过程审核评分表
制造过程审核检查表

4
1、文件与工装、刀具、模具、检具其中任意 一项未符合最终版本各扣1分。
3
1、包装方案未按照和客户达成一致的包装方 案扣3分。
1、包装上未有客户标识扣1分。
4
2、包装上未有产品名称标识扣1分。 3、包装上未有产品零件号扣1分。
4、包装上未有产品数量标识扣1分。
3
1、无安全库存资料扣2分。 2、安全库存资料不完善扣1分。
1、物料未按要求区域划分待检区、合格区、
不合格区或划分不合理扣1分。
5
2、划分标识不明确扣1分。 3、每批次产品无编码标识扣1分。
4、每批次产品无厂家标识扣1分。
5、每批产品无炉批号扣1分。
第 1 页,共 4 页
文件编号: OK
检具精度能否满足要求,检具 3 得到了有效的验证,检测,
并有有效期标签
4
库存管理程序,来料的安全库 存
三: 生产工位 按照控制计划审核生产过
1 程,设备参数与文件一致
2 产出产品的追溯方案
3 RPN的改进
偶发事件的应急方案,人 4 员,设备,备用工装,检
具,刀具,模具 关键特性是否都在控制方式 5 之内
明确的产品状态及分析报
6
告,红盒子,黄盒子,绿盒 子及调机品,首末件,存储
2
1分。 2、控制计划版本与版本记录不相符不正确扣
1分
1、无工装夹具扣2分。
8
2、工装夹具与清单不相符扣2分。 3、过程责任者不明确扣2分。
4、过程责任者未经培训考核就上岗扣2分
1、未采用SPC统计过程控制扣2分。
5
2、未采用防错过程控制扣2分.
3、未采用全检的控制方式扣1分
5
1、来料未按要求进行检验扣3分。 2、未有检验报告扣2分。
VDA6.3-2010_过程风险评分表
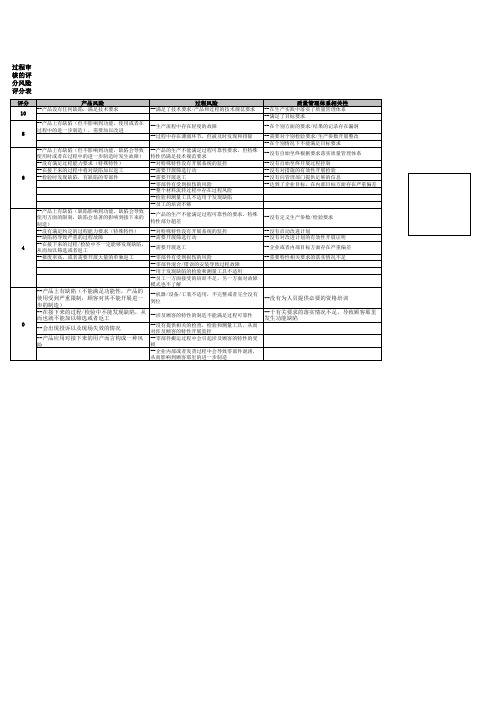
4
--产品上有缺陷(缺陷影响到功能,缺陷会导致 使用方面的限制,缺陷会显著的影响到接下来的 制造) --没有满足约定的过程能力要求(特殊特性) --缺陷将导致严重的过程故障 --在接下来的过程/检验中不一定能够发现缺陷, 从而加以筛选或者返工 --报废率高,或者需要开展大量的单独返工
--没有定义生产参数/检验要求 --没有启动改进计划 --没有对改进计划的有效性开展证明 --企业或者内部目标方面存在严重偏差 --重要特性相关要求的落实情况不足
过程审核的评分风险评分表
评分 10 产品风险
--产品没有任何缺陷,满足技术要求 --产品上有缺陷(但不影响到功能,使用或者在 过程中的进一步制造),需要加以改进
过程风险
--满足了技术要求/产品和过程的技术规范要求 --生产流程中存在轻度的故障 --过程中存在薄弱环节,管理体系 --满足了目标要求 --在个别方面的要求/结果的记录存在漏洞 --需要对个别检验要求/生产参数开展整改 --在个别情况下不能满足目标要求 --没有自始至终根据要求落实质量管理体系 --没有自始至终开展过程控制 --没有对措施的有效性开展检验 --没有向管理部门提供足够的信息 --达到了企业目标,在内部目标方面存在严重偏差
8
6
--产品上有缺陷(但不影响到功能,缺陷会导致 使用时或者在过程中的进一步制造时发生故障) --没有满足过程能力要求(特殊特性) --在接下来的过程中将对缺陷加以返工 --检验时发现缺陷,有缺陷的零部件
--产品的生产不能满足过程可靠性要求,但特殊 特性仍满足技术规范要求 --对特殊特性没有开展系统的监控 --需要开展筛选行动 --需要开展返工 --零部件有受到损伤的风险 --整个材料流转过程中存在过程风险 --检验和测量工具不适用于发现缺陷 --员工的培训不够 --产品的生产不能满足过程可靠性的要求,特殊 特性部分超差 --对特殊特性没有开展系统的监控 --需要开展筛选行动 --需要开展返工 --零部件有受到损伤的风险 --零部件混合/错误的安装导致过程故障 --用于发现缺陷的检验和测量工具不适用 --员工一方面接受的培训不足,另一方面对故障 模式也不了解
VDA6.3过程审核评分矩阵表(标准模板)

当前程度
6.1.2 E P6 #DIV/0!
6.1.3
6.1.4
6.2.4
6.2.5
6.6.1
6.6.2
6.6.3
###### ###### ###### ###### ######
###### ###### ###### ###### ###### ######
###### ###### ######
6.1.2
6.1.3
6.1.4
6.2.4
6.2.5
6.6.1
6.6.2
6.6.3
过程分析中的子要素的分析评估(1-n的平均数) 6.1.1 6.1.2
当前程度
6.1.3
目标程度
6.1.4
最高程度
6.1.5
当前程度
6.2.1
6.2.2
6.2.3
当前程度
6.2.4
目标程度
6.2.5
最高程度
6.2.6
当前程度 当前程度
n.e. 当前程度 目标程度 最高程度 当前程度
#DIV/0!
######
EPzR
######
5.2
5.3
5.4*
5.5*
5.6
5.7
n.e.
当前程度
目标程度
最高程度
当前程度
E P5
#DIV/0!
工序落实程度[%]
运输和零部件处置
E1 #DIV/0! E2 #DIV/0! E3 #DIV/0! E4 #DIV/0! E5 #DIV/0! E6 #DIV/0! E7 #DIV/0! E8 #DIV/0! E9 #DIV/0! E10 #DIV/0!
###### ###### ###### ######
体系审核审核打分表

10
8
6
4
0
0 有相关检具的MSA记录
e、相关专业人员是否具有资格?
10 8 6 4
30
是否按照规定有效实施了相关的进货检验和试 验?(抽查所有关键重要外协、外包件)
10
8
6
4
是否按照规定有效实施了相关的过程检验和试
31 验?(抽查所有过程产品的关键重要特性) 10 8 6 4
(达产审核时不审)
是否按照规定有效实施了相关的出厂检验和试
32 验?(包括年度的型式试验)(达产审核时不 10 8 6 4
审)
★ 从合格品库中抽取至少3种关键、重要外协 33 (包括外包)件进行现场检验、试验。
20 16 12 8
34
在生产演示生产至少300件产品中,每道工序 按作业指导书的要求进行检测。
20 16 12
8
0 10 有专业测试项目及人员资格证明
0 10 有试生产记录
批量生产条件下的生产文件和检验文件是否具 15 备且齐全?体现的技术要求与产品图纸、标准 10 8
是否一致?(允许高于标准要求)
6
4
0
10
生产、检验文件齐全,技术要求与检验规格, 操作指导书书保持一致
16 是否已具备所要求的批量生产能力?
二、过程控制文件
10 8
6
4
0
10
查FD128车活塞孔SPC,cpk=1.37,具备批量 生产能力
对于待检、已收、退货和待处理的零部件或原 42 材料,是否有分区存放的隔离制度?合格品的 10 8
存放环境如何?先进先出吗?
6
4
0
公司划有各个产品状态的区域,对不良品和合
VDA6.3-10版过程审核检查表
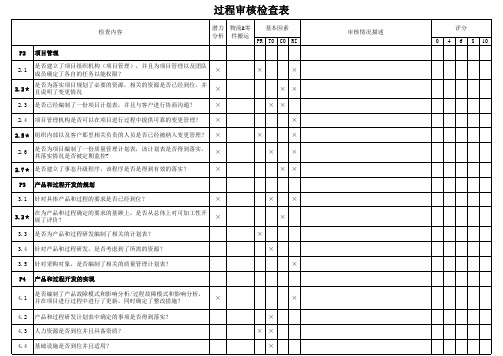
P2 项目管理
检查内容
潜力 物流&零 基本因素 分析 件搬运
PR TO CO RI
2.1
是否建立了项目组织机构(项目管理),并且为项目管理以及团队 成员确定了各自的任务以能权限?
×
2.2*
是否为落实项目规划了必要的资源,相关的资源是否已经到位,并 且说明了变更情况
×
×
×
××
2.3 是否已经编制了一份项目计划表,并且与客户进行协商沟通?
×
6.2.2 对生产工艺流程是否进行了放行,并且对设置数据进行了采集?
×
×
×
6.2.3* 使用的生产设备是否可以满足客户对具体产品提出的要求?
×
×
6.2.4* 在生产环节是否对特殊的特征进行了控制管理?
×
×
6.2.5
对于报废零件、返工零部件以及设置用零部件,是否单独放置并相 应加以了标记?
×
6.2.6
×
5.4* 针对采购对象,是否获得了必要的审批
×
×
5.5* 针对采购对象约定的质量是否得到保障?
×
×
5.6 是否按实际需要对进厂的货物进行储存?
×
5.7
针对各具体的任务,相关的人员是否具备资质,是否定义了责权关 系?
×
P6 过程分析/生产
6.1 什么是过程的输入?(过程进入)
6.1.1* 是否在研发和批量生产之间进行了项目交接?
×
××
2.4 项目管理机构是否可以在项目进行过程中提供可靠的变更管理? ×
×
2.5* 组织内部以及客户那里相关负责的人员是否已经被纳入变更管理? ×
2.6
是否为项目编制了一份质量管理计划表,该计划表是否得到落实, 其落实情况是否被定期监控?
新版VDA6.3过程审核实例(含评分矩阵)
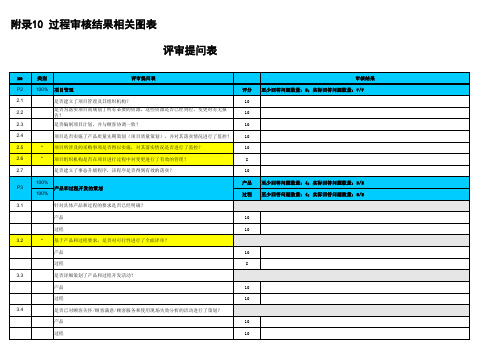
审核结果
是否对质量和过程数据进行了收集和分析? 毛坯铸造 滚齿 热处理 磨削 修整 机加 冲压 注塑 分装 总装 * 一旦与产品和过程要求不符,是否进行了原因分析,是否验证了纠正措施的有效性? 毛坯铸造 滚齿 热处理 磨削 修整 机加 冲压 注塑 10 10 10 10 10 10 10 10 10 8 8 10 10 10 10 10 10 10
评审提问表 10 10
审核结果
8 8 10 10 10 10 10 8 10 10
是否根据需要确定产量/生产批量,并且有目的地运往下道工序? 毛坯铸造 滚齿 热处理 磨削 修整 机加 冲压 注塑 分装 总装 是否根据要求对产品/零部件进行适当存储,所使用的运输设备/包装方式是否与产品 /零部件的特点相适应? 毛坯铸造 8 8 8 10 8 8 10 10 8 10 10
类别 机加 冲压 注塑 分装 总装
评审提问表 10 10 10 10 10
审核结果
生产设备/工具的维护保养是否受控? 毛坯铸造 滚齿 热处理 磨削 修整 机加 冲压 注塑 分装 总装 * 通过使用的监视和测量设备,是否能够有效地监控质量? 毛坯铸造 滚齿 热处理 磨削 修整 机加 冲压 注塑 分装 总装 6 8 8 10 10 10 8 10 10 10 10 8 8 10 10 10 10 10 10 8
NO 工序4 工序5 工序6 工序7 工序8 工序9 工序10 6.5.2 工序1 工序2 工序3 工序4 工序5 工序6 工序7 工序8 工序9 工序10 6.5.3 工序1 工序2 工序3 工序4 工序5 工序6 工序7 工序8
类别 磨削 修整 机加 冲压 注塑 分装 总装
评审提问表 10 10 10 10 10 10 10
VDA6.3-2016过程审核检查表及评分矩阵
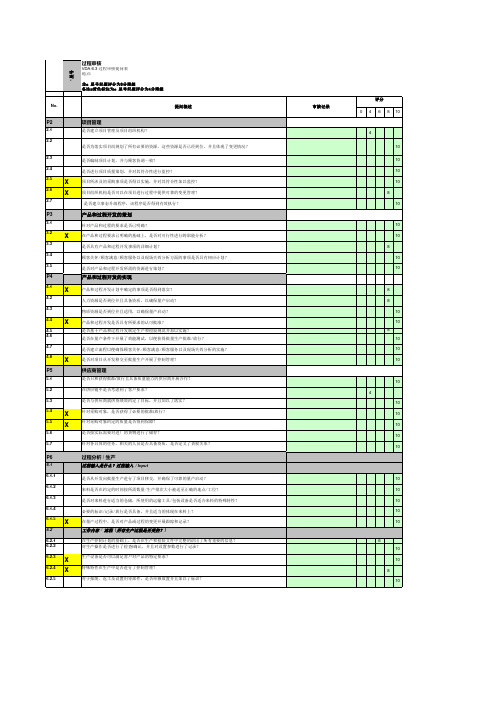
10 10 10
10 10 10 10
10 10 10 0
10 10 10 10
10 10 10 10 10
审核记录
评分 0 4 6 8 10
4 10 10 10 10
8 10
10 10 8 10 10
8 8
10 10 8 10 10 10
10 4
10 10 10 10 10
10 10 10 10 10
6 10 10
8 10
6.3
x 6.3.1
6.3.2
6.3.3
6.4
x 6.4.1
6.4.2
x 6.4.3
产品和过程开发计划中确定的事项是否得到落实? 人力资源是否到位并且具备资质,以确保量产启动? 物质资源是否到位并且适用,以确保量产启动? 产品和过程开发是否具有所要求的认可批准? 是否基于产品和过程开发制定生产和检验规范并加以实施? 是否在量产条件下开展了效能测试,以便获得批量生产批准/放行? 是否建立流程以便确保顾客关怀/顾客满意/顾客服务以及现场失效分析的实施? 是否对项目从开发移交至批量生产开展了控制管理? 供应商管理 是否只和获得批准/放行且具备质量能力的供应商开展合作? 在供应链中是否考虑到了客户要求? 是否与供应商就供货绩效约定了目标,并且加以了落实? 针对采购对象,是否获得了必要的批准/放行? 针对采购对象约定的质量是否得到保障? 是否按实际需要对进厂的货物进行了储存? 针对各具体的任务,相关的人员是否具备资质,是否定义了责权关系?
6.4.4
6.4.5 6.5
6.5.1
6.5.2
x 6.5.3
6.5.4
6.6
6.6.1
6.6.2
6.6.3
汽车产品VDA 过程审核检查表及评分标准
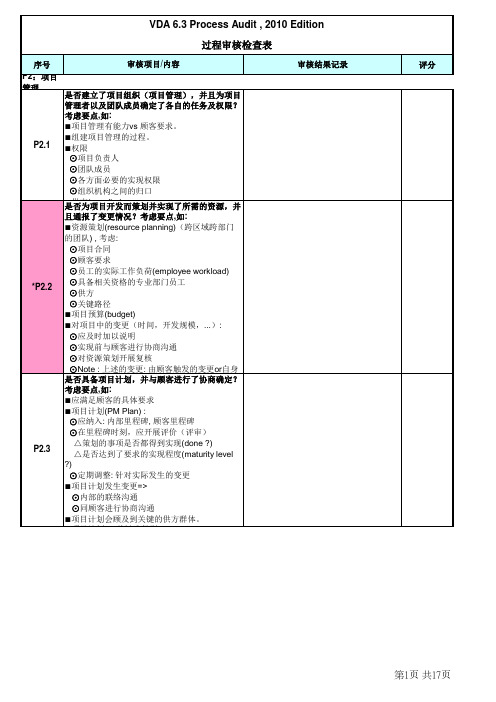
⊙试运行计划(trailling plan), 必须包含 △材料 △零件 △分总成(subassemblies) △生产制造过程: 原型件(prototype) + 试生产
阶段 (pre-production)
⊙测试、检查和检验设备策划(equipment planning)
⊙项目负责人 ⊙团队成员 ⊙各方面必要的实现权限 ⊙组织机构之间的归口 是 ■供否方为(项su目pp开lie发r) 而策划并实现了所需的资源,并 且通报了变更情况?考虑要点,如: ■资源策划(resource planning)(跨区域跨部门 的团队) , 考虑: ⊙项目合同 ⊙顾客要求 ⊙员工的实际工作负荷(employee workload) ⊙具备相关资格的专业部门员工 ⊙供方 ⊙关键路径 ■项目预算(budget) ■对项目中的变更(时间,开发规模,...): ⊙应及时加以说明 ⊙实现前与顾客进行协商沟通 ⊙对资源策划开展复核 ⊙Note : 上述的变更: 由顾客触发的变更or自身 是否具备项目计划,并与顾客进行了协商确定? 考虑要点,如: ■应满足顾客的具体要求 ■项目计划(PM Plan) : ⊙应纳入: 内部里程碑, 顾客里程碑 ⊙在里程碑时刻,应开展评价(评审)
prototype ⊙试生产阶段pilot run ⊙系列生产阶段serial production
是否在系列生产条件下进行了试生产,以获得生 产批准/放行?考虑要点,如: ■必须开展试生产/ 生产测试
⊙生产因素和影响进行评价=> 整改 (corrections)
⊙批量生产过程中,避免瓶颈以及质量损失
⊙质量管理计划(QM Plan, i.e. control plan) 人力资源是否到位并且具备资格?考虑要点,如: ■过程[人力资源策划]
过程审核报告(评分表)

XXXX有限公司过程审核报告SJ/JL-083-B/0123456123456符合率(%)1.策划2.落实E DE1234561234561.策划2.落实101010101010E PE12345678910101010E Z1.11.21.31.41.52.12.22.32.42.52.62.73.13.23.33.43.54.14.24.34.44.54.61010101010101010101010101010101010101010101010E 1E 2E 3E 4E 5E 6E 7E 8E 9E 10B2要素中对照质量体系的评分(工序1-n 的平均值)1.1 1.2 1.3 1.4 1.52.1 2.2 2.3 2.4 2.5 2.6 2.73.1 3.2 3.3 3.4 3.54.1 4.2 4.3 4.4 4.5 4.6101010101010101010101010101010101010101010101012345610110101010E KB2要素中按产品组的符合率E PG (%)(E X -E n 的平均值)按产品组计算的总符合率批量生产前批产开始时/以后注:未进行评分的提问用nb 填入过程审核评分表昆山博富新材料科技股份有限公司100100人员/素质生产设备/工装nb100100运输/搬运/贮存/包装A 产品诞生过程1 产品开发(设计)2 过程开发ES 1(%)B 批量生产2 生产(对各道工序评分)工序1:工序3:缺陷分析,纠正措施,持续改进(KVP)100工序2:#DIV/0!E PG (%)1 分供方/原材料#DIV/0!工序6:#DIV/0!工序7:#DIV/0!工序4:#DIV/0!工序5:ES 2(%)ES 3(%)ES 4(%)100#DIV/0!工序8:#DIV/0!工序9:产品组#DIV/0!工序10:#DIV/0!3 服务/顾客满意程度85100工序产品组符合率EP(%)已评要素数E P (%)=E DE +E PE +E Z +E PG +E K=保存期:三年。
VDA6.3过程审核-2010 检查表-评分矩阵-中英文版
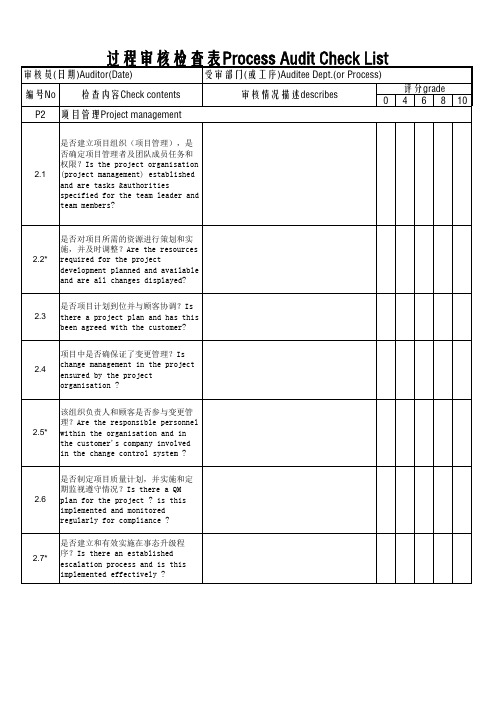
受审部门(或工序)Auditee Dept.(or Process)
编号No
检查内容Check contents
P2 项目管理Project management
审核情况描述describes
0
评分grade 4 6 8 10
是否制定项目质量计划,并实施和定 期监视遵守情况?Is there a QM 2.6 plan for the project ? is this implemented and monitored regularly for compliance ?
是否建立和有效实施在事态升级程
2.7*
序?Is there an established escalation process and is this
是否建立项目组织(项目管理),是 否确定项目管理者及团队成员任务和 权限?Is the project organisation 2.1 (project management) established and are tasks &authorities specified for the team leader and team members?
implemented effectively ?
是否对项目所需的资源进行策划和实 施,并及时调整?Are the resources 2.2* required for the project development planned and available and are all changes displayed?
是否项目计划到位并与顾客协调?Is 2.3 there a project plan and has this
过程审核的评分标准

0
--产品上有缺陷(不能满足功能性,产品的 --机器/设备/工装不适用,不完整或者完全没有 使用受到严重限制,顾客对其不能开展进一 到位 步的制造) --在接下来的过程/检验中不能发现缺陷,从 --涉及顾客的特性的制造不能满足过程可靠性 而也就不能加以筛选或者返工
--没有提供相关的检查,检验和测量工具,从而 对涉及顾客的特性开展监控 --零部件搬运过程中会引起涉及顾客的特性的受 --产品应用对接下来的用户而言构成一种风险 损 --企业内部或者发货过程中会导致零部件混淆, 从而影响到顾客那里的进一步制造
--没有为人员提供必要的资格培训 --于有关要求的落实情况不足,导致顾客那里 发生功能缺陷
--会出现投诉以及现场失效的情况
过程审核的评分风险评分表
评分 10 产品风险
--产品没有任何缺陷,满足技术要求 --产品上有缺陷(但不影响到功能,使用或者在 过程中的进一步制造),需要加以改进
过程风险
--满足了技术要求/产品和过程的技术规范要求 --生产流程中存在轻度的故障 --过程中存在薄弱环节,但被及时发现和排除
质量管理体系相关性
8
6
--产品上有缺陷(但不影响到功能,缺陷会导致 使用时或者在过程中的进一步制造时发生故障) --没有满足过程能力要求(特殊特性) --在接下来的过程中将对缺陷加以返工 --检验时发现缺陷,有缺要求,但特殊 特性仍满足技术规范要求 --对特殊特性没有开展系统的监控 --需要开展筛选行动 --需要开展返工 --零部件有受到损伤的风险 --整个材料流转过程中存在过程风险 --检验和测量工具不适用于发现缺陷 --员工的培训不够 --产品的生产不能满足过程可靠性的要求,特殊 特性部分超差 --对特殊特性没有开展系统的监控 --需要开展筛选行动 --需要开展返工 --零部件有受到损伤的风险 --零部件混合/错误的安装导致过程故障 --用于发现缺陷的检验和测量工具不适用 --员工一方面接受的培训不足,另一方面对故障 模式也不了解
VDA 过程审核检查表及评分标准

审核结果记录
评分
第5页 共17页
序号 P4.6
审核项目/内容
是否在不同阶段应用了生产控制计划,并由此编制出了生 产、测试和检验文件?考虑要点,如: ■生产控制计划Production control plan 包括:
⊙构件 ⊙组件 ⊙部件 ⊙零件和材料 ⊙与产品相关的生产过程。 ■生产控制计划(control plan) : ⊙原型件阶段(如果顾客提出要求的话)prototype ⊙试生产阶段pilot run ⊙系列生产阶段serial production 本问题与产品开发无关!
⊙生产计划 ⊙负责生产的厂区 ■特殊特性(SCs) ⊙在FMEA中 ⊙通过措施进行了保障。 ■证明(evidence) : 措施的有效性
审核结果记录
评分
第4页 共17页
序号 P4.2
审核项目/内容
产品和过程开发计划中确定的事项是否得到了有效实现? 考虑要点,如: ■考虑产品的使用条件(English version : installation requirement) ■产品开发的方法(e.g. QFD, DOE, FMEA …) 得到了应用
⊙包括那些顾客没有明确说明的要求(例如法律法 规要求) ■考虑: ⊙经验(教训) ⊙未来的期望 ■规范: 报价审批过程 ⊙相关负责/参与的部门确认顾客要求的可行性
△采购 △开发 △生产计划 △生产 △质量管理策划 △物流... ■报价阶段: 考虑产能(capacity) ■必须考虑到来自P7“顾客支持/顾客满意度/服务”的要 求
VDA 6.3 Process Audit , 2010 Edition
过程审核检查表
序号 P2:项目 管理
P2.1
审核项目/内容
制造过程审核检查表

26
员工是否严格按作业指导书作业?
27
现场的照明是否充足,是否适合作业\检查等操作?
28
现场产品标示看板等是否清楚标示产品相关生产信息,记录是否与产品相符
29
每天工作计划安排清晰,各生产岗位数量与安排一致;
30
生产计划安排是否与当班生产设备等吻合?
31
对特性有关的测量系统是否有进行MSA分析?
32
测量工具是否
不符合项目编号
20160304 ZTQR01092 AO
制造过程审核检查表
审核员:
日期:
审核过程:
陪同人员:
1、评分标准:10分---完全符合要求,不存在偏差; 8分---绝大部分符合要求,有少量偏差; 6分---部分符合要求,有较大偏差;
4分----少部分符合要求,偏差严重; 0分---完全不符合要求;
制程的物料、半成品、成品、合格品、不合格品等是否按规定要求标识清楚?
22
当制程的工作环境条件有规定要求时,是否按规定要求来实施控制?
23
是否有执行首件确认并做相应的记录?是否有按控制计划的安排执行制程检验并作记录?
24
发生变更后是否有进行验证和批准?
制造过程控制
25
作业指导书是否受控?是否为最新版?是否与现场作业相符?
序号 审核项目
审核内容
得分
审核情况描述
1
所有操作人员是否具备了相应的资格和能力?
2
员工对本岗位的作业指导书的要求是否清楚?
3
特殊岗位人员是否进行了资格鉴定?
4
员工是否明确工作职责,是否知道如何清楚的与上下级沟通各种情况?
5
人员素质 当发生质量异常时,员工是否知道如何反馈?
iatf16949过程审核评分表
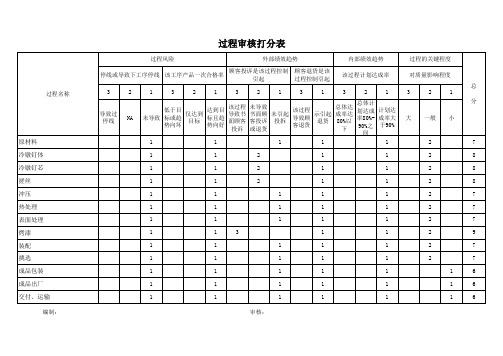
未导致 书面顾 客投诉 或退货
未引起 投拆
该过程 导致顾 客退货
示引起 退货
总体达 成率达 80%以
下
总体计 划达成 率80%90%之
间
计划达 成率大 于90%
大
一般
小
分
1
1
1
1
1
2
7
1
1
2
1
1
2
8
1
1
2
1
1
2
8
1
1
2
1
1
2
8
1
1
1
1
1
2
7
1
1
1
1
1
2
7
1
1
1
1
1
2
7
1
1
3
1
1
2
9
ห้องสมุดไป่ตู้
1
1
1
1
1
2
7
1
1
1
1
1
2
7
1
1
1
1
1
1
6
1
1
1
1
1
1
6
1
1
1
1
1
1
6
审核:
过程风险
外部绩效趋势
内部绩效趋势
过程的关键程度
停线或导致下工序停线
该工序产品一次合格率
顾客投诉是该过程控制 引起
顾客退货是该 过程控制引起
该过程计划达成率
对质量影响程度
总
3
2
1
3
2
1
3
汽车行业VDA6.3过程审核检查表及评分标准
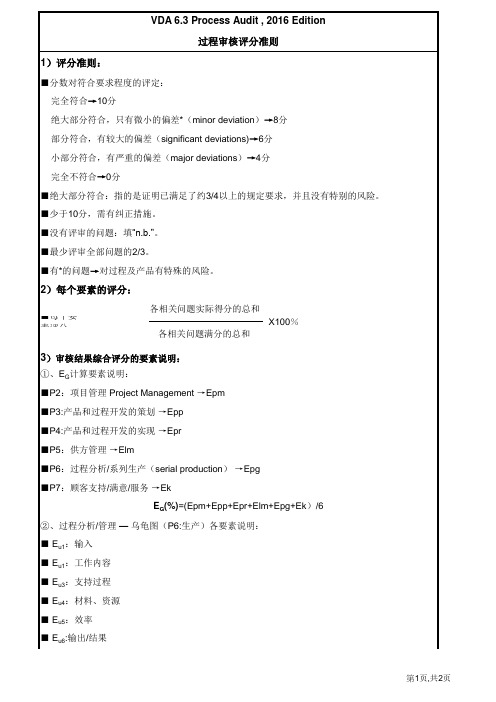
第2页,共2页
完全不符合→0分
■绝大部分符合:指的是证明已满足了约3/4以上的规定要求,并且没有特别的风险。
■少于10分,需有纠正措施。
■没有评审的问题:填“n.b."。
■最少评审全部问题的2/3。
■有*的问题→对过程及产品有特殊的风险。
2)每个要素的评分:
■每个要 素评分
各相关问题实际得分的总和
X100% 各相关问题满分的总和
3)审核结果综合评分的要素说明: ①、EG计算要素说明: ■P2:项目管理 Project Management →Epm ■P3:产品和过程开发的策划 →Epp ■P4:产品和过程开发的实现 →Epr ■P5:供方管理 →Elm ■P6:过程分析/系列生产(serial production) →Epg ■P7:顾客支持/满意/服务 →Ek
过程审核评分准则
■ Eu7:零件运输(Transport/Parts Handling) 4)审核结果的综合评分Overall Assessment:
总符合率EG(%) EG>=90
对过程的评定 符合
级别名称 A
80=<EG<90
有条件符合
B
EG<80
不符合
C
■审核结果的综合评分-降级规则
如果EG≥90%, 且P2…P7、E1…En、EU1…Eu7都>80%,评为A级;反之,则评为B级(A→B)
VDA 6.3 Process Audit , 2016 Edition
过程审核评分准则
1)评分准则:
过程审核评分表

必须定义和规范质量数据和过程参数(设定值),这些数据对于证明产品一致性来说是必要的。
记录实际数据(实际值),用于展示对目标要求的符合性。
这些数据必须确保可用以评价。
对异常情况进行记录(班次日志/设备日志)。
收集的数据要与产品和过程相关,数据来源是实际的、易获取的、可查的、可存档的。
要考虑追溯性要求。
对收集的数据进行分析,并启动相应的改进措施。
潜在的改进必须根据质量、成本、服务的先前问题来持续开展。
导致过程或产品发生偏离的事件,及其相关措施,被体现在相应的风险分析(例如FMEA)当中。
●缺陷收集卡
●控制图
●特殊特性
●过程参数(温度,时间,压力...)
●生产数据采集
●故障信号(例如停线,断电,程序故障报警)●参数变化
●失效类型/失效频率
●失效成本(不符合)
●报废/返工
●隔离通知/拣选行动
●节拍时间,周期时间
●SPC●柏拉图分析
●因果图
●风险分析(FMEA、FTA…)。
过程审核检查表、计划表
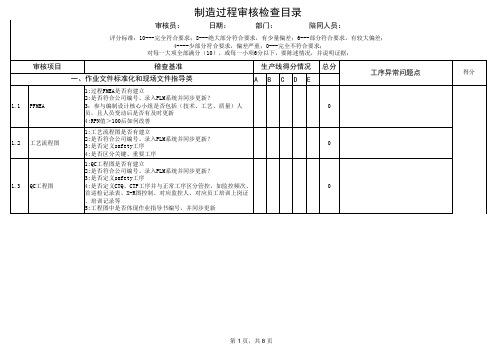
0
测量的需求
测量工具是否有合
6.2 6.3 6.4
格标识,测量工具 完好、准确? 作业员\检查员是 否按规定频率和样 本数量使用指定工 具检查? 测量记录完整,准 确、有效?
1:满足测量工具按需配置, 2:量具在制定的校检期内, 3:测试工具完好无损, 4:测试记录应保持齐全完整, 5:对于关键的控制点,按要求进行测量,并做过程能力分析控制 图
0
验证数据、不回用的处理流程节点责任人
得分
0
第 3 页,共 8 页
审核项目
制造过程审核检查目录
审核员:
日期:
部门:
陪同人员:
评分标准:10---完全符合要求;8---绝大部分符合要求,有少量偏差;6---部分符合要求,有较大偏差; 4----少部分符合要求,偏差严重;0---完全不符合要求;
对每一大项全部满分(10),或每一小项6分以下,要陈述情况,并说明证据;
三、生产设备、工装、夹具、封样件
A B C D E 总分
工序异常问题点
3.1
设备、工装定期点 检保养,检验器具 定期校验、封样件 校验记录
1:设备是否定期进行保养(记录) 2:设备是否有相关的点检保养制度,以及相关的操作流程 3:点检记录的规范以及完整性 4:工装是否定期检定,并且在有效检定期内使用 5:计量器具、封样件是否在有效期内、是否有校验记录
对每一大项全部满分(10),或每一小项6分以下,要陈述情况,并说明证据;
审核项目
稽查基准
是否有措施保证标 1:班组是否有明确的要求规定巡检频率 1.10 准化作业的执行? 2:过程巡检工作班组是否有专人执行,
(如过程监查) 3:过程检查是否按规定检查,并留有记录
过程审核评分表
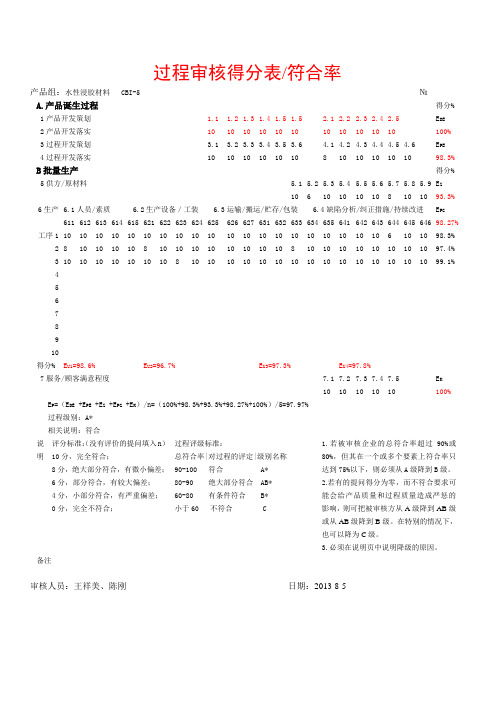
过程审核得分表/符合率产品组:水性浸胶材料 CBI-5 №A.产品诞生过程得分%1产品开发策划2产品开发落实1.1 1.2 1.3 1.4 1.5 1.5 2.1 2.2 2.3 2.4 2.5 E DE 10 10 10 10 10 10 10 10 10 10 10 100%3过程开发策划4过程开发落实3.1 3.2 3.3 3.4 3.5 3.6 4.1 4.2 4.3 4.4 4.5 4.6 E PE10 10 10 10 10 10 8 10 10 10 10 10 98.3%B批量生产得分% 5供方/原材料 5.1 5.2 5.3 5.4 5.5 5.6 5.7 5.8 5.9 E Z10 6 10 10 10 10 8 10 10 93.3% 6生产 6.1人员/素质 6.2生产设备/工装 6.3运输/搬运/贮存/包装 6.4缺陷分析/纠正措施/持续改进E PG98.27%611 612 613 614 615 621 622 623 624 625 626 627 631 632 633 634 635 641 642 643 644 645 646工序1 10 10 10 10 10 10 10 10 10 10 10 10 10 10 10 10 10 10 10 10 6 10 10 98.3%2 8 10 10 10 10 8 10 10 10 10 10 10 10 10 8 10 10 10 10 10 10 10 10 97.4%3 10 10 10 10 10 10 10 8 10 10 10 10 10 10 10 10 10 10 10 10 10 10 10 99.1%45678910得分% E U1=98.6% E U2=96.7% E U3=97.3% E U4=97.8%7服务/顾客满意程度7.1 7.2 7.3 7.4 7.5 E K10 10 10 10 10 100%E P=(E DE +E PE +E Z +E PG +E K)/n=(100%+98.3%+93.3%+98.27%+100%)/5=97.97%过程级别:A*相关说明:符合说明评分标准:(没有评价的提问填入n)10分,完全符合;8分,绝大部分符合,有微小偏差;6分,部分符合,有较大偏差;4分,小部分符合,有严重偏差;0分,完全不符合;过程评级标准:总符合率|对过程的评定|级别名称90-100 符合 A*80-90 绝大部分符合 AB*60-80 有条件符合 B*小于60 不符合 C1.若被审核企业的总符合率超过90%或80%,但其在一个或多个要素上符合率只达到75%以下,则必须从A级降到B级。