2000KN包边液压机技术说明
2000KN压力试验机
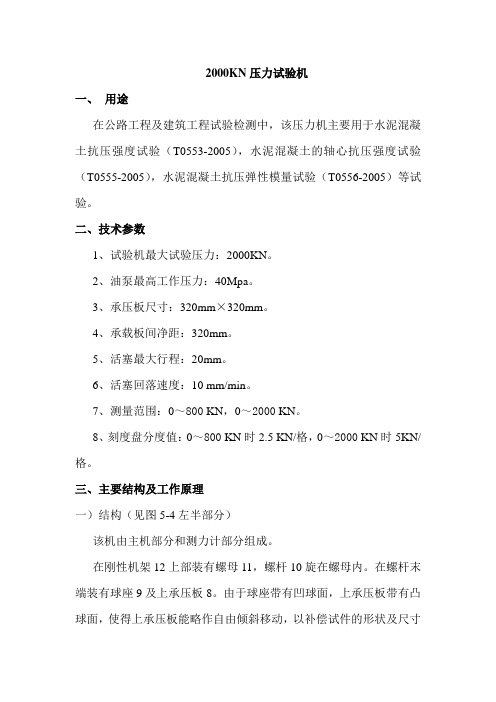
2000KN压力试验机一、用途在公路工程及建筑工程试验检测中,该压力机主要用于水泥混凝土抗压强度试验(T0553-2005),水泥混凝土的轴心抗压强度试验(T0555-2005),水泥混凝土抗压弹性模量试验(T0556-2005)等试验。
二、技术参数1、试验机最大试验压力:2000KN。
2、油泵最高工作压力:40Mpa。
3、承压板尺寸:320mm×320mm。
4、承载板间净距:320mm。
5、活塞最大行程:20mm。
6、活塞回落速度:10 mm/min。
7、测量范围:0~800 KN,0~2000 KN。
8、刻度盘分度值:0~800 KN时2.5 KN/格,0~2000 KN时5KN/格。
三、主要结构及工作原理一)结构(见图5-4左半部分)该机由主机部分和测力计部分组成。
在刚性机架12上部装有螺母11,螺杆10旋在螺母内。
在螺杆末端装有球座9及上承压板8。
由于球座带有凹球面,上承压板带有凸球面,使得上承压板能略作自由倾斜移动,以补偿试件的形状及尺寸误差。
因此,在试件受压时,可以自动调整上承压板与试件受压面接触吻合。
根据试件尺寸,转动手轮13,就可以调节上承压板与下承压板之间的距离(即净距)。
油缸1固定在机架的下部,在油缸的内壁上嵌有复合圈3和橡胶密封圈4,防止在高压时活塞和油缸间过多的油液溢出,油缸左后测装有一溢油管,直接让溢出的油流回油箱,以保持机器四周的洁净。
1-工作油箱;2-螺钉;3-复合圈;4-橡胶密封圈;5-遮屑板;6-油塞;7-下承压板;8-上承压板;9-球座;10-螺杆;11-螺母;12-机架;13-手轮;14-弹簧;15-测力体;16-电气箱;17-分油阀;18-回油阀;19-进油阀;20-测力油缸;21-电机;22-液压泵。
2、测力计部分(见图5-4右半部分)测力系统由荷载指示机构、加载系统、测力机构、操作部分组成。
1)加载系统加载系统由液压泵22、电机21、测力油缸20、分油阀17组成,他们分别紧固在机架下部测力计的槽钢上储油箱装在油泵后侧,储油箱底部装有放油螺塞,储油箱内部装有滤油器。
2000kN四柱液压机液压系统工作原理

2000kN四柱液压机液压系统工作原理作者殷洪福2000kN四柱液压机是一台宽工作台的压力机,工作台尺寸为2000mm(左右)×1500mm(前后)。
这台机的设计目标是大尺寸薄板零件的拉深、翻边、冲裁工艺。
这台机的液压系统有几个特点:1.设置高压、低压两个可以根据工艺力的大小而自动切换的油源;2.上下油缸可以单独运行,也可以差动运行;3.主油缸的柱塞内包含顶出油缸,可以进行上顶出(脱模)操作。
为说明液压系统的工作原理,以设备的典型运作过程(凹模在上方、凸模在下方的反向拉深工艺过程)为例。
图示液压系统是完成一次工作循环之后的状态。
下一次工作循环从系统升压开始。
系统工作原理说明如下。
1.系统升压先导式溢流阀12原处于卸荷状态,高压油源失效。
低压油源仍处于供油状态。
将手动换向阀11的手柄推到位置Ⅰ,控制油路X1升压,使溢流阀12恢复正常工作状态,高压油源恢复供油,系统压力升高至设定数值。
2.滑块快速下降将手动换向阀9的手柄拉到位置Ⅲ,支承滑块的油缸4的下腔回油路接通,滑块在自重的作用下,快速下降,直至上模(凹模)接触工件。
滑块在下降过程中一方面将上油缸3的柱塞向下拉,使上油缸3内腔产生负压,造成正向打开液控单向阀(大流量的充液阀)2的趋势;另一方面压迫油缸4下腔的油,使之压力升高,压力油通过控制油路X2迫使液控单向阀2彻底打开(正反向都处于开启状态),于是,充液过程开始,油箱1内的油通过大直径油管被吸进上油缸3。
与此同时,另一部分来自两个油源的油通过换向阀9进入上油缸3。
有一个问题需要说明:滑块快速下降主要靠自重作用,但是,自重作用并不可靠,如果滑块下降受阻(或许是因为滑块与立柱之间的滑动付力学异常),就可能发生下降不顺甚至卡死的现象。
这种现象通常不会发生。
然而,这种现象一旦发生,就会进入如“工作行程”那样的过程,滑块被上油缸3的柱塞强迫下降,系统依然正常工作。
单向节流阀13的作用是增加油缸4下腔回油路上的阻力,以求提高控制油路X2的压力,以便打开液控单向阀2。
2000T框架液压机
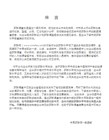
4.5充液系统
充液箱、充液阀等
4.6 管路系统
管路、管架等。
4.7 润滑系统
稀油润滑站、润滑油管等。
4.8 平台护栏
梯子、平台、围板等。
4.9 电气系统
电气箱、操作按钮站、电线电缆等。
4.10 随机附件
地脚螺栓、调整垫铁等。
JB3818-1999《液压机技术条件》
JB3915-1985《液压机安全技术条件》
GB/T3766-2001《液压系统通用技术条件》
JB/T7343-1994《单双动薄板冲压液压机》
JB/T8609-1997《锻压机械焊接件技术条件》
GB/T5226.1-2002《机械安全 机械电气设备第1部分:通用技术条件》
工作 100T 230mm/s
800T 37mm/s
2000T 14mm/s
回程 300mm/s
─ 工作台距地面高 700mm
5.11 液压机设有机械下顶式安全栓,光电安全保护装置,安全维修平台、围板,顶部设有标高指示灯,移动按钮站设有双手操作按钮,液压系统设有过载保护装置和液压安全支撑保险回路。
5.12 液压系统设有油位指示,油液冷却和过滤系统,油液冷却选用水冷却。
5.13 滑块导轨润滑采用稀油集中润滑,设有集油盒,自动润滑器设有故障报警装置。
─动力电源: 三相四线制380V
─电压波动范围 380V±10%
─液压机功率 ~370kW
应快、内泄小、动作灵敏可靠、流量大、抗污染能力强,使用维护方便,寿命长等优点。
本机冷却过滤系统油泵选用CB-B低压齿轮泵。
2000kN压力机主要技术指标
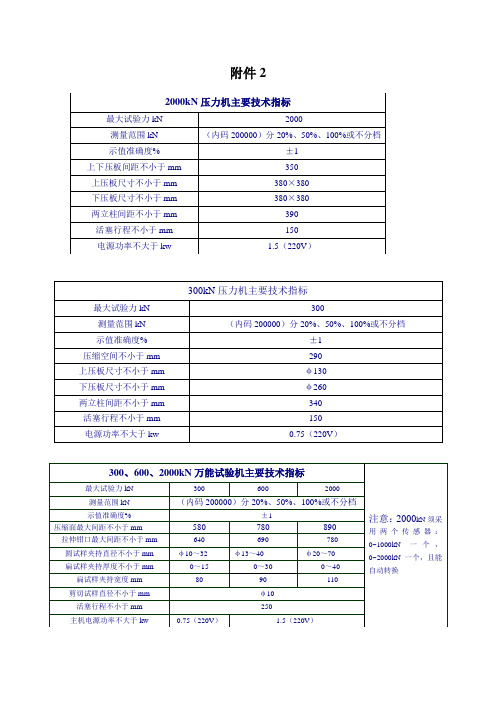
640
690
780
圆试样夹持直径不小于mm
φ10~32
φ13~40
φ20~70
扁试样夹持厚度不小于mm
0~15
0~30
0~40
扁试样夹持宽度mm
80
90
110
剪切试样直径不小于mm
φ10
活塞行程不小于mm
250
主机电源功率不大于kw
0.75(220V)
1.5(220V)
5kN抗折试验机主要技术指标
附件2
2000kN压力机主要技术指标
最大试验力kN
2000
测量范围kN
(内码200000)分20%、50%、100%或不分档
示值准确度%
±1
上下压板间距不小于mm
350
上压板尺寸不小于mm
380×380
下压板尺寸不小于mm
380×380
两立柱间距不小于mm
390
活塞行程不小于mm
150
电源功率不大于kw
1.5(220V)
300kN压力机主要技术指标
最大试验力kN
300
测量范围kN
(内码200000)分20%、50%、100%或不分档
示值准确度%
±1
压缩空间不小于mm
290
上压板尺寸不小于mm
φ130
下压板尺寸不小于mm
φ260
两立柱间距不小于mm
340
活塞行程不小于mm
150
电源功率不大于kw
0.75(220V)
最大试验力kN
大于或等于5
测量范围
(内码200000)全程不分档
示值准确度%
±1
2000吨油压机安全技术操作规程
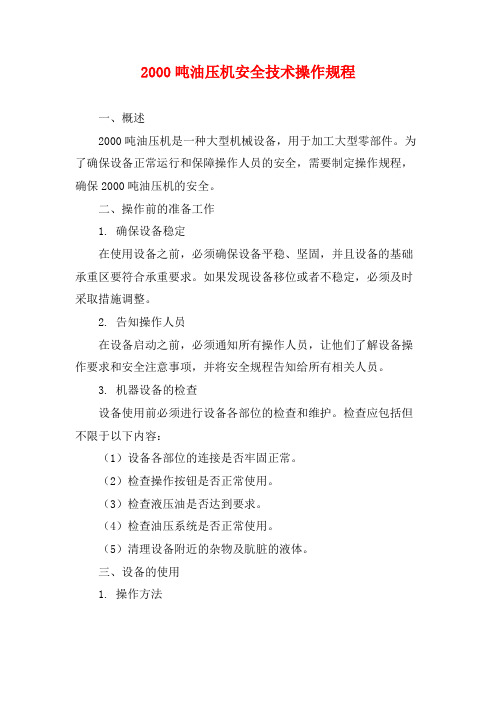
2000吨油压机安全技术操作规程一、概述2000吨油压机是一种大型机械设备,用于加工大型零部件。
为了确保设备正常运行和保障操作人员的安全,需要制定操作规程,确保2000吨油压机的安全。
二、操作前的准备工作1. 确保设备稳定在使用设备之前,必须确保设备平稳、坚固,并且设备的基础承重区要符合承重要求。
如果发现设备移位或者不稳定,必须及时采取措施调整。
2. 告知操作人员在设备启动之前,必须通知所有操作人员,让他们了解设备操作要求和安全注意事项,并将安全规程告知给所有相关人员。
3. 机器设备的检查设备使用前必须进行设备各部位的检查和维护。
检查应包括但不限于以下内容:(1)设备各部位的连接是否牢固正常。
(2)检查操作按钮是否正常使用。
(3)检查液压油是否达到要求。
(4)检查油压系统是否正常使用。
(5)清理设备附近的杂物及肮脏的液体。
三、设备的使用1. 操作方法(1)正确选用模具,调整模具间隙,并严格按照工艺要求进行操作。
(2)按照先小力后大力,慢进快压的原则进行操作过程中的升降和压制。
(3)在压制过程中,应严格避免超负荷及超限操作。
(4)操作人员应该按照操作规程要求,正确操作,严禁随意调整设备压力和移动。
2. 操作要求(1)设备启动和停止时,应按照生产工艺程序进行操作,保证整个操作流程的正常稳定。
(2)设备操作过程中,必须始终保持高度警觉,不得擅自离开操作处。
(3)设备在操作中发生异常时,应立即停机停电查明原因,修正故障后方可继续操作。
(4)作业人员要保持清晰头脑,不得饮酒参与作业,严防事故发生。
(5)在设备运行中,操作人员应该保持沉着冷静,小心谨慎,保持工作区域清洁,防范事故发生。
四、注意事项1. 禁止超负荷操作设备在使用时,要严禁超负荷操作和掉落重物。
只有当设备操作正确、相互配合稳定、员工严格遵循操作规程时,才能正常运行设备。
2. 设备保护设备在使用前应仔细检查并确认一切正常,同时设备使用人员要随时检查设备的工作状态,一旦发现设备异常状态,应停止设备进行修理。
2000KN压力试验机操作规程
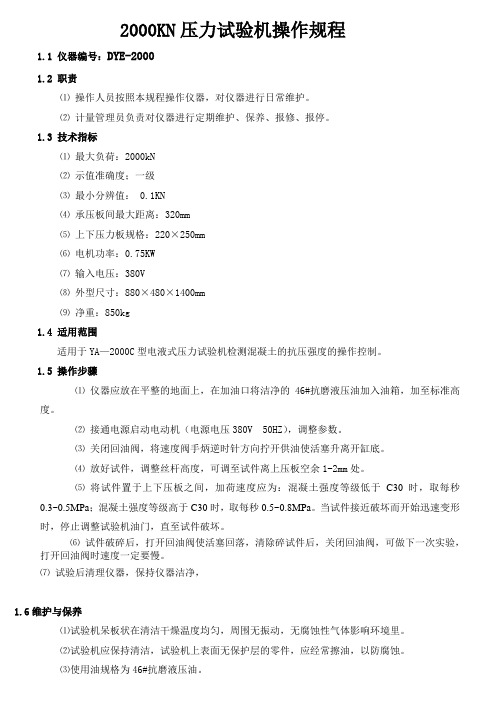
2000KN压力试验机操作规程1.1 仪器编号:DYE-20001.2 职责⑴操作人员按照本规程操作仪器,对仪器进行日常维护。
⑵ 计量管理员负责对仪器进行定期维护、保养、报修、报停。
1.3 技术指标⑴最大负荷:2000kN⑵ 示值准确度;一级⑶ 最小分辨值: 0.1KN⑷ 承压板间最大距离:320mm⑸ 上下压力板规格:220×250mm⑹电机功率:0.75KW⑺输入电压:380V⑻外型尺寸:880×480×1400mm⑼净重:850kg1.4 适用范围适用于YA—2000C型电液式压力试验机检测混凝土的抗压强度的操作控制。
1.5 操作步骤⑴仪器应放在平整的地面上,在加油口将洁净的46#抗磨液压油加入油箱,加至标准高度。
⑵接通电源启动电动机(电源电压380V 50HZ),调整参数。
⑶关闭回油阀,将速度阀手炳逆时针方向拧开供油使活塞升离开缸底。
⑷放好试件,调整丝杆高度,可调至试件离上压板空余1-2mm处。
⑸将试件置于上下压板之间,加荷速度应为:混凝土强度等级低于C30时,取每秒0.3~0.5MPa;混凝土强度等级高于C30时,取每秒0.5~0.8MPa。
当试件接近破坏而开始迅速变形时,停止调整试验机油门,直至试件破坏。
⑹试件破碎后,打开回油阀使活塞回落,清除碎试件后,关闭回油阀,可做下一次实验,打开回油阀时速度一定要慢。
⑺试验后清理仪器,保持仪器洁净,1.6维护与保养⑴试验机呆板状在清洁干燥温度均匀,周围无振动,无腐蚀性气体影响环境里。
⑵试验机应保持清洁,试验机上表面无保护层的零件,应经常擦油,以防腐蚀。
⑶使用油规格为46#抗磨液压油。
YH32 2000C千牛四柱液压机说明书

千牛四柱液压机YH32-2000C型 20000 书明用说使YH32-2000C-SM千牛力: 20000称公:出厂编号合肥合锻机床股份有限公司液压机┃┃第1 页使用说明书┃目录┃共1 页一、机器的参数主要技术参数机器外形图00010005 地基图图二、原理0002液压原理图0004 电气原理图三、机器的用途、特点四、机器结构概述五、液压元件六、液压系统七、电气系统八、机器的安装与试车机器的安装加油试车前的准备故障及消除方法九、机器的维护保养十、安全操作规程十一、附图主活塞油缸主柱塞油缸滑块仰视图移动台俯视图总装配图液压原理图基础图液压机┃┃第1 页使用说明书┃主要技术参数┃共1 页序备20000KN1MPa液体压225滑块行3mm1500行开口高425005000左工作台有56前3000工作台面距地面高6007空mm/s>1508工94-1010回10mm地面以上高118240机外970012左右地占面积尺寸13 7565 前后14机器总功率110KW液压机┃┃第1 页使用说明书┃机器的用途特点┃共1 页本机为四柱液压机,主要用于金属材料挤压成型,也可实现金属及非金属的压制、成型和拉伸等工艺。
本机有独立的动力系统和电气系统,采用按钮集中控制,可实现调整、半自动两种工作方式。
本机的行程可在设计范围内调节,能完成定压成形和定程成形两种工艺方式,定压成形工艺方式具有加压延时及自动回程动作。
液压系统采用二通插装阀,结构紧凑,安装维修方便, 动作灵敏可靠,传动率高,密封性好。
液压机┃┃第1 页使用说明书┃机器结构概述┃共 1 页本机由机身、主油缸、滑块行程限位装置及电气系统等部件组成。
滑块通过四立柱导向,在油缸驱动下作上、下直线运动。
压机的液压系统布置在油箱上部,电气柜位于主机左侧,本机设有活动按钮站供操作者操作。
1 、机身:机身为四柱式结构,由上横梁、滑块、下横梁及四根立柱组成,通过螺母紧固,组成一封闭式刚性框架,滑块与主缸活塞杆连接,以立柱为导向作上下移动,滑块上设有加油孔定时加油,以便润滑运动部位.滑块下平面和工作台上平面开有T 形槽,供安装模具用。
包边液压机技术条件

008(GEN-2)包边液压机技术协议二〇〇八年五月四日包边液压机技术协议甲方:济南青年汽车有限公司乙方:济南青年汽车有限公司(甲方)委托乙方按照甲方提出的技术要求设计和制造200吨框架式包边液压机,经双方协商制订本技术协议。
一、名称、公称力、数量框架式包边液压机、 2000KN 、 3台二、设备的主要用途及工作条件本机是根据需要而设计的专用设备,主要适用于乘用车四门两盖的包边工艺。
压机允许的工作环境温度:10—40℃;供水压力:0.25MPa;空气压力:0.5—0.6MPa;入口水温≤30℃;出口水温:≤45℃;动力电采用380∨±10%/50Hz三相四线制,压力波动范围380V±10%,50Hz。
控制电采用220∨/50Hz,线圈电压24∨,环境湿度≤70%。
三、该设备的主要结构:采用整体框架式结构,主要构件如上横梁、立柱、下横梁、滑块、移动工作台均为钢板焊接结构。
所有焊接件均采用二氧化碳气体保护焊施焊,焊缝打磨平整、无焊渣和流疤、机身外观平整无明显凹凸现象。
大件焊接后经高温回火炉退火消除内应力,粗加工后经高温回火炉进行二次退火,以保证彻底消除残余应力,确保焊接件永不变形,精度保持性高。
滑块采用可拆卸斜楔式四角八面导轨导向。
上平台围栏周边封闭。
设有移动式工作台两个,左右移动。
四、执行标准JIS B 6403-1994 《单动簿板冲压液压机1级精度》GB/T5226.1-1996 《工业机械电气设备通用技术条件》JB/T3818-1999 《液压机技术条件》JB9967-1999 《液压机噪声限值》JB3915-1985 《液压机安全技术条件》GB/T3766-833 《液压系统通用技术条件》JB/T1829—1997 《锻压机械通用技术条件》JB/T8609—1997 《锻压机械焊接技术条件》GB17120—1997 《锻压机械安全技术条件》其它按照国家、企业相关标准执行。
四柱液压机说明书

四柱液压机说明书1、主液压泵(恒功率输出液压泵),2、齿轮泵,3、电机,4、滤油器,5、7、8、22、25、溢流阀,6、18、24、电磁换向阀,9、21、电液压换向阀,10、压力继电器,11、单向阀,12、电接触压力表,13、19、液控单向阀,14、液动换向阀,15、顺序阀,16上液压缸,17、顺序阀,20、下液压缸,23节流器,26、行程开关四柱万能液压机的启动:电磁铁全断电,主泵卸荷。
主泵(恒功率输出)→电液换向阀9的M型中位→电液换向阀21的K型中位→T四柱万能液压机的启动:电磁铁全断电,主泵卸荷。
主泵(恒功率输出)→电液换向阀9的M型中位→电液换向阀21的K型中位→T液压缸16活塞快速下行:2YA、5YA通电,电液换向阀9右位工作,道通控制油路经电磁换向阀18,打开液控单向阀19,接通液压缸16下腔与液控单向阀19的通道。
进油路:主泵(恒功率输出)→电液换向阀9→单向阀11→液压缸16上腔回油路:液压缸16下腔→电液换向阀9→电液换向阀21的K型中位→T液压缸活塞依靠重力快速下行:大气压油→吸入阀13→液压缸16上腔的负压空腔液压缸16活塞接触工件,开始慢速下行(增压下行):液压缸活塞碰行程开关2XK使5YA断电,切断液压缸16下腔经液控单向阀19快速回油通路,上腔压力升高,同时切断(大气压油→吸入阀13→上液压缸16上腔)吸油路。
进油路:主泵(恒功率输出)→电液换向阀9→单向阀11→液压缸16上腔回油路:液压缸16下腔→顺序阀17→电液换向阀9→电液换向阀21的K型中位→T四柱液压机的启动保压:液压缸16上腔压力升高达到预调压力,电接触压力表12发出信息,2YA断电,液压缸16进口油路切断,(单向阀11和吸入阀13的高密封性能确保液压缸16活塞对工件保压,利用液压缸16上腔压力很高,推动液动换向阀14下移,打开外控顺序阀15,防止控制油路使吸入阀1误动而造成液压缸16上腔卸荷)当液压缸16上腔压力降低到低于电接触压力表12调定压力,电接触压力表12又会使2YA通电,动力系统又会再次向液压缸16上腔供应压力油……。
WAW-2001 2000kn液压万能试验机技术指标
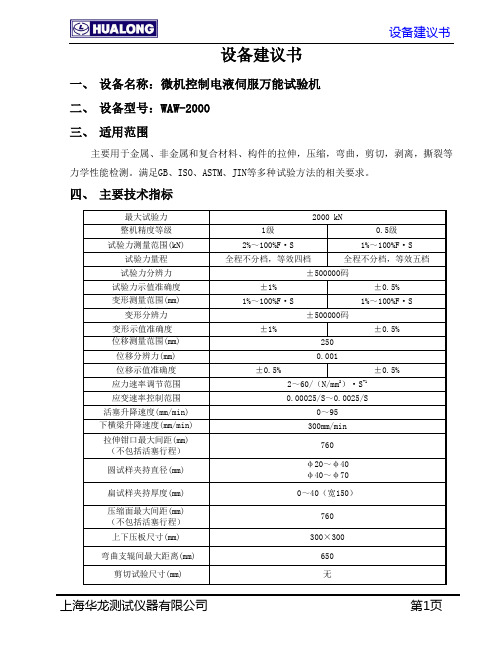
设备建议书一、设备名称:微机控制电液伺服万能试验机二、设备型号:WAW-2000三、适用范围主要用于金属、非金属和复合材料、构件的拉伸,压缩,弯曲,剪切,剥离,撕裂等力学性能检测。
满足GB、ISO、ASTM、JIN等多种试验方法的相关要求。
四、主要技术指标最大试验力2000 kN整机精度等级1级0.5级试验力测量范围(kN) 2%~100%F·S 1%~100%F·S 试验力量程全程不分档,等效四档全程不分档,等效五档试验力分辨力±500000码试验力示值准确度±1% ±0.5%变形测量范围(mm) N) ((((mm 1%~100%F·S 1%~100%F·S变形分辨力±500000码变形示值准确度±1% ±0.5% 位移测量范围(mm) 250位移分辨力(mm) 0.001位移示值准确度±0.5% ±0.5% 应力速率调节范围2~60/(N/mm2)·S-1应变速率控制范围0.00025/S~0.0025/S活塞升降速度(mm/min) 0~95下横梁升降速度(mm/min) 300mm/min拉伸钳口最大间距(mm)(不包括活塞行程)760圆试样夹持直径(mm) υ20~υ40 υ40~υ70扁试样夹持厚度(mm) 0~40(宽150)压缩面最大间距(mm)(不包括活塞行程)760 上下压板尺寸(mm) 300×300弯曲支辊间最大距离(mm) 650 剪切试验尺寸(mm) 无活塞行程(mm) 250 两立柱间有效宽度(mm) 680主机外形尺寸及极限高度(mm) 1200 x 880 x 30003260控制台外形尺寸(mm) 琴台式伺服油源,1100x990x1200电源电压:380V±10%;功率:5.5(kw)重量(Kg) 5500五、产品配置●控制系统:华龙Auto CTS-550一台●伺服阀:意大利ATOS伺服阀或美国MOOG阀一只●油泵:德国液压油泵一台●负荷传感器:高精度轮幅式负荷传感器一只●位移传感器:抽出式数字位移传感器一只●电子引伸计:北京钢院,标距50mm,延伸率50%,精度0.03% 一只●计算机:品牌计算机(17″液晶显示器)一台●打印机:HP A4彩色喷墨打印机一台●计算机软件:Hualong TestWorld测控软件一套●拉伸夹具(圆钳口两付八件,平钳口一付四件)一套●弯曲试验装置(压棍直径Φ50mm,两支座间距30~650mm)(选配)一套●压缩装置(上、下压板各一付,300×300mm)一套●随机工具一套六、设备简介该系列机型获得了四项中华人民共和国专利:专利号专利类型专利内容ZL 02 2 15727.1 实用新型专利试验机四立柱可调机构ZL 02 3 77170.4外观设计专利万能材料试验机(四立柱式)ZL 02 3 77171.2外观设计专利编码式位移传感器ZL 02 2 77147.7外观设计专利试验机用琴台式油源机柜由主机、液压源、华龙Auto CTS-550控制器、计算机和HuaLong TestWorld测控软件等组成。
2000KN压力试验机

JYE-2000压力试验机操作规程一、机器使用前,要将油箱注油至油标所示的位置。
二、打开箱体后盖,检查测力活塞杆与下连接架定位动块的中心是否对准(特别是位移安装后的首次使用更要做到)。
三、试验人员在试验前,应对试验的最大承载力有所估计,以便选用相应的测量范围。
检查调整转向阀至适当位置,以获取准确的数据。
四、按试件大小及下压板的定位刻线,将试件放置于下压板中心,并旋转手轮上压板调至离试件2-5mm的位置。
五、接通电源,按下启动电钮,关闭回油阀缓缓打开送油阀使活塞浮起。
六、旋转调零钮,使主动针对准零位,并将被动针拨至零位。
七、操作送油阀进行加荷试验,加荷速度应平稳均匀,当指针不再上升时,表示试件已达到最大承载或试件已破碎,应缓缓打开回油阀卸荷。
八、记录被动针所示试件的抗压力值,一组试验即告结束。
九、依此顺序,可继续进行各组试验。
十、试验最后结束,打开回油阀,关闭送油阀,切断电源,清扫机器。
JYE-2000压力试验机维护保养规程一、试验机应保持清洁,对无保护表面应经常擦油防锈,不用时应用机罩覆盖。
二、一年应更换一次液压油,使用频繁应半年更换一次,更换的油必须洁净。
三、由于气候的变化,所用油料略有不同,当环境温度为15±50C时,采用GB443N46(相当于30#)机械油,当环境温度为25±50C时,采用GB443-84N68机械油。
四、首次使用前,必须按要求彻底清除机器内部为防止搬运损坏而设置的各种坚固物,严格按操作步骤进行认真的检查,谨慎操作,严禁违章操作。
五、试验操作时,下压板上升高度严禁超过50mm。
六、严禁先关机后卸荷,严禁在加荷时操作转换阀换档,严禁在高压时突然停机再开机,以免损坏机件,影响精度。
天锻2000C说明书..
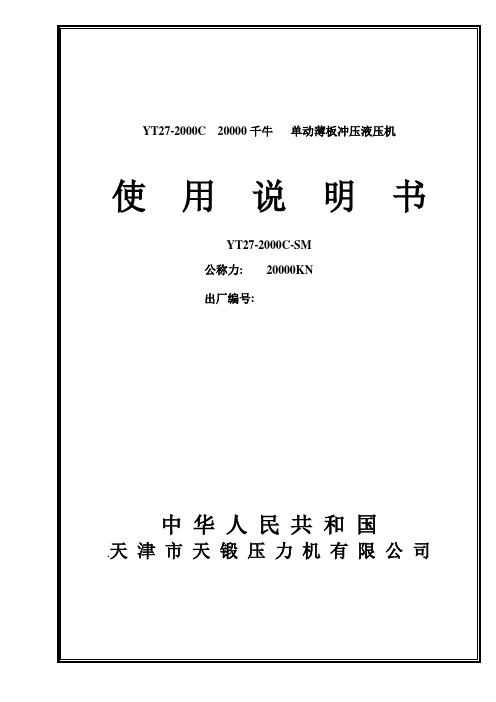
目录一、外观图二、用途和特点三、主要技术规格四、结构概述五、液压系统概述六、电气系统概述七、安装与试车八、维护保养和安全操作九、故障和消除方法十、易损件表附图1、移动工作台俯视图2、滑块仰视图3、主缸结构图4、侧缸结构图5、顶出缸结构图6、液压垫缸结构图7、 30A插装阀块示意图8、 30B插装阀块示意图9、 30C插装阀块示意图10、JTDB32DYF7/6-10插装阀块示意图11、JTDB80ZS6-10b插装阀块示意图12、JTDB32YS2/2-10c插装阀块示意图13、JTDB16YL/4-10插装阀块示意图附以下产品图1、总装配图 (0000 1/3)2、液压原理图 (0000 2/3) (共2张)3、电气原理图 (0000 3/3))(共22张)4、操纵板接线图(6000 1/5)5、分线盒线号布置图(6000 2/5)6、互连图(6000 3/5)7、电气布置图(6000 4/5)8、动力机构接线图(6000 5/5)9、基础图 (0100)YT27-2000C 使用说明书YT27-2000C-SM 共33页第3页一、外观图YT27-2000C使用说明书YT27-2000C-SM 共33页第4页二、用途和特点本机主要适用于金属板件的拉伸、弯曲、翻边、成型和复杂箱体及大曲面零件拉伸及成形等工艺。
本机具有以下特点:1、本机的控制系统有定压和定程两种工作方式,通过操纵面板上的选择开关切换。
工作方式包括微调整、寸动、半自动和全自动四种工艺动作。
2、本机的液压控制系统采用插装式集成阀,先导电磁阀采用进口德国力士乐公司产品,主泵采用进口德国力士乐公司公司产品,提高了动作的可靠性及使用寿命,同时减少了噪音和液压冲击。
3、本机的电气控制系统采用了日本OMRON公司生产的PLC可编程控制器,可实现机床各种工艺动作循环。
该系统使控制更为灵活,动作准确可靠。
4、本机的机身采用组合框架式结构,机身有足够的强度和刚度,机械精度保持性好。
2000吨油压机安全技术操作规程(最新版)

2000吨油压机安全技术操作规程(最新版)The safety operation regulations are the guiding documents for the safe operation of the post.It stipulates the specific details of the safe operation methods of the post.( 操作规程)单位:_______________________部门:_______________________日期:_______________________本文档文字可以自由修改2000吨油压机安全技术操作规程(最新版)1.油压机操作人员需经培训后方可上岗操作,并应熟悉油压机的一般性能和结构,其它人员禁止操作。
2.油压机使用前,应按规定检查高压泵、压力表、各种阀、密封圈等辅助设备是否正常。
3.油压机开机前,应检查相关辅助工具、模具是否完好配套。
检查设备接地(零)是否牢固可靠,操纵系统是否灵敏好用,压力表是否准确无误。
4.进行试车检查,确认无问题后方可进行作业。
5.油压机各油缸工作时,严禁超过最大压力工作。
6.切料滑块、压料缸、推料缸严禁超过最大伸出行程使用。
禁止活塞头压到缸口导套上,避免造成损坏。
7.切料时,注意物料不要压在推料滑座的上面,以防把滑座及活塞杆压弯。
8.压头回程时要提高到一定的高度,严防工件顶住压头。
9.作业中如发现设备有异常现象或管路系统漏油时,应立即停压并将压头落实,切断电源后方可进行检修。
10.滑块运行时,不允许人员进入机身两侧和前面,以防不测。
11.操作员在开始切料之前、调整物料位置重新开机之前和发现有人进入非安全区时,应按响警铃进行警示。
12.油压机工作平台上,严禁上人工作,确实需要时必须采取防范措施或停机。
13.多人操作时,要有专人开机,并相互协调配合进行操作。
14.工作完毕,应将相关辅助工具、模具整理好并放到指定地方,清理清扫作业现场,关闭电源。
YE—2000液压式压力机操作指南
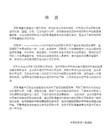
度盘的选用:试验人员在试验前对试样所承受的最大试验力有所估计,以便选用相应的测量范围,才能得到准确的数据。
砣的悬挂:本试验机采用摆锤的形式,根据测量范围不同,而悬挂不同重量的砣。
指针零点的调整:试验前必须将指针调至零位置,才能避免测力读数的误差。
平衡砣的调整:调整平衡活塞,使摆杆保持铅垂位置。
送油阀、回油阀及试验力速度指示器的使用:试验时应根据试验力范围选用试验力速度指示器的指示速度。
缓冲阀的使用调整:缓冲阀的用途是:当试验破坏后,使摆杆缓慢下降,避免产生冲击现象。
检验规程:
接好电源线,按电源“总开”按扭,指示灯亮。
根据试样选用负荷测量范围,在摆杆上挂上或取下砣,并调整转换受柄。
灌油与排油:
放电:
润滑:测力计内主轴两端之滚轴,平时不应注油润滑,以免日久产生油泥防碍测量机构的灵敏度。如果是使用年限较长的必须拆卸内部时,可用汽油冲洗后,放入极少量优质稀薄的润滑油,但应足以能防止其锈蚀,装好后用标准力计重新校验。
油泵的初次运转及试车:
试验机的保养:
试验机各部分应经常擦拭干净,对没有喷漆的表面擦拭干净后,用棉纱占少量的机油再擦一遍,以防止生锈,雨季期间应更注意擦拭,不用时,用不罩起以防尘土浸入。
试验力速度指示器:
高压油泵与电动机:
操作部分:
缓冲阀:装设在回油阀体内,其用途,当试样破坏后,油路系统中油压立即下降,因而摆杆皮砣就要以很大速度回落,为了防止这种快落而采用了缓冲阀。
液压传动系统:
试验机操作方法:
试验结果是否正确,除要求试验机本身必须达到规定的精确度外,还要求试验人员必须熟悉试验机的操作方法,现将本试验机的使用操作方法叙述如下:
YES-2000压力机使用说明书
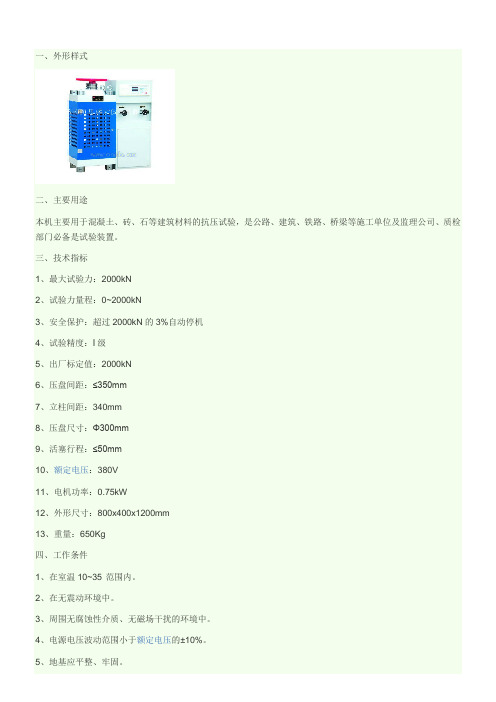
一、外形样式
二、主要用途
本机主要用于混凝土、砖、石等建筑材料的抗压试验,是公路、建筑、铁路、桥梁等施工单位及监理公司、质检部门必备是试验装置。
三、技术指标
1、最大试验力:2000kN
2、试验力量程:0~2000kN
3、安全保护:超过2000kN的3%自动停机
4、试验精度:Ι级
5、出厂标定值:2000kN
6、压盘间距:≤350mm
7、立柱间距:340mm
8、压盘尺寸:Φ300mm
9、活塞行程:≤50mm
10、额定电压:380V
11、电机功率:0.75kW
12、外形尺寸:800x400x1200mm
13、重量:650Kg
四、工作条件
1、在室温10~35°范围内。
2、在无震动环境中。
3、周围无腐蚀性介质、无磁场干扰的环境中。
4、电源电压波动范围小于额定电压的±10%。
5、地基应平整、牢固。
- 1、下载文档前请自行甄别文档内容的完整性,平台不提供额外的编辑、内容补充、找答案等附加服务。
- 2、"仅部分预览"的文档,不可在线预览部分如存在完整性等问题,可反馈申请退款(可完整预览的文档不适用该条件!)。
- 3、如文档侵犯您的权益,请联系客服反馈,我们会尽快为您处理(人工客服工作时间:9:00-18:30)。
2000KN框架式包边液压机技术说明徐州达一锻压设备有限公司2000KN框架式包边液压机主要技术性能一、机器主要用途和工作条件1.1机器的主要用途:本液压机为框架式高性能、高精度单动薄板冲压液压机,公称力为2000KN,主要用于车门、引敬盖、引进(或行李箱盖)的包边成型等工艺。
本机配有超负荷保险装置,确保生产的安全和平稳。
要求机床结构设计合理,有足够的静态、动态刚度,并采用先进技术,保证系统具有良好的动态品质。
1.2 机器工作条件:1.2.1、设备工作区域温度:0~40℃1.2.2、供电电压为:380V三相四线制,电压波动范围:380V±10%,50HZ。
1.2.3、液压系统使用介质:YB—N46#抗磨液压油。
二、机身主要构成机身主要由上梁、滑块、移动工作台、立柱、下梁、拉杆等组成2.1 机身2.1.1、机身采用分体式框架结构。
机床的机身采用优质Q235碳素钢板焊接结构,主要结构件采用CO2气体保护焊,箱型焊接结构、筋板及焊接坡口对称布置,焊接工艺性好,焊缝经打磨无焊渣和流疤现象;再经抛丸处理;焊后经过去应力振动时效处理,使其不产生变形,上横梁、立柱、滑块、工作台(T型槽/顶杆孔位置及大小需由甲方书面确认)以及下横梁采用液压预紧螺母组成密闭式框架结构,整个机身外观平整,无明显凸凹现象;机架经Inventor有限元分析,对机架的应力、位移变形及安全率做全面的分析,使整个机架刚性更强固、耐用。
2.1.2、滑块采用四角八面导轨导向并衬有低摩擦系数的耐磨材料,调整精度高,刚性好,调整后不易发生精度跑偏现象,此外导轨经淬火硬化处理,硬度在HRC45以上,耐磨性能良好,使用寿命长。
2.1.3、上横梁、立柱、工作台、滑块、下横梁等焊接大件采用CO2气体保护焊。
箱型焊接结构、筋板及焊接坡口对称布置,焊接工艺性好,各大构件焊接完成后消除内应力。
2.1.4、立柱内侧装有四角八面导轨,导轨下端装有接油盒以消除油污染。
2.1.5、四根拉杆材料为45#钢,两端有螺纹与螺母相联接,采用液压预紧螺母锁紧框架。
2.2 滑块2.2.1、滑块为钢板焊接箱形结构,滑块底面板为整块钢板,滑块上平面与主缸活塞杆连接,滑块下平面加工有T型槽,滑块四角装有可调导轨,与立柱上的导轨组成四角八面导滑,由于四角八面导轨间隙调整方便,保证了导向精度,且刚性好,抗偏载能力强,间隙可调。
导轨热处理硬度HRC45以上,导滑板材料采用铜合金。
2.2.2、滑块行程控制采用无触点行程开关,行程开关采用日本OMRON公司产,确保性能可靠。
2.2.3、滑块具有行程上、下限的安全极限开关,确保滑块在行程范围内安全工作。
2.2.4、滑块的压力调压范围为公称压力15%-100%。
系统压力显示采用耐震压力表显示。
滑块的压力控制采用远程调压控制,压力显示采用耐震压力表显示。
2.2.5、设有上死点滑块支撑锁紧机构,以便在进行设备检修及换模时确保安全。
滑块支撑锁紧机构操作方式为手动单独操作,与主机其它动作互锁。
2.2.6、加装液压安全支撑,从而有效保护操作人员以及机台、模具的安全。
2.3 移动工作台2.3.1、压机设有两个工作台,移出方式为左右移出,移入重复定位精度±0.05mm,驱动方式为电机加减速机驱动,工作台移动速度为50mm/sec。
2.3.2、移动工作台台体为钢板焊接结构,焊接采用二氧化碳气体保护焊,焊接完成后消除内应力。
2.3.3、移动工作台提升和夹紧采用液压式,由四组提升夹紧缸完成;移动工作台的移进、移出及落下夹紧定位时,均与液压机动作联锁,并设有定位检测开关。
2.3.4、配有移动工作台下平面和下横梁上平面的贴和检测装置(对角布置,不少于2个),当间隙大于0.3mm时,主机不许工作,并有报警装置。
2.3.5、移动工作台上面板加工有T型槽。
T形槽尺寸由用户方提供。
2.3.6、移动工作台电缆收线方式采用卷线轮方式。
2.3.7、移动工作台的操作位置在主操作台上。
操作方式为手动操作,与主机互锁,即只有滑块回程到上限位时移动工作台才允许工作。
2.4、主油缸主油缸采用双缸结构,油缸通过螺母安装固定在上横梁上。
缸体采用优质碳素钢锻件,活塞杆表面经淬火精研磨处理,硬度在HRC45以上,使用寿命长;油缸内表面经过强滚压工艺,液压油缸具有足够的强度和钢度。
油缸密封采用优质进口材料密封组件,确保主缸密封可靠,延长使用寿命。
三、液压部分液压传动装置由动力控制系统,各种泵、阀和液压油箱等组成。
对主机提供动力并实现对主机的控制。
主油箱在上平台上,液压控制阀块在油箱上平面上有序排列。
3.1 液压系统采用二通插装式逻辑阀,这是目前最适合于大型液压机传动的一种阀门形式,该阀通油量大、抗污染能力强,控制灵活、性能可靠,响应快、控制方式灵活等一系列优点。
3.2 本系统的充液回路选用常闭式充液阀,滑块快下时靠箱吸油,快速下降速度由油缸下腔油路的插阀控制调节。
3.3 液压管路系统密封可靠,不渗不漏;管路连接方式采用法兰连接,管路布置整齐,并采用抗震管夹和耐震压力表,管路及油箱内部均进行良好的除锈保洁处理,在用户进行二次安装时,所有控制管路连接及控制阀体连接螺钉均涂止退胶,以防螺钉松动。
3.4主缸调压范围为公称压力15%-100%无机可调,压力测量元件采用压力传感器,通过触摸屏可对压力进行数字显示及设定。
辅助系统压力显示采用耐震压力表显示。
主缸的压力控制采用远程调压控制。
3.5主油泵采用南通启东高压柱塞泵,电机采用山东华力公司等产品。
3.6液压系统中设有独立的水冷却系统,当油温达到40℃时冷却系统自动开始工作,确保油温在正常工作范围,压机能够正常连续工作。
四、润滑系统滑块的润滑装置均采用电脑程控不回收自动润滑南京贝奇尔或华润技术。
供油量、供油时间间隔设定后,自动进行润滑。
立柱上设有润滑油废油回收装置。
润滑系统和主机动作设有互锁,润滑系统有故障,主机报警并停止工作。
五、电气控制5.1、电气控制系统采用PLC可编程序控制器。
电气系统的设计与制造贯彻GB5226.1—2002《机械安全机械电气设备第一部分通用技术条件》,电气系统由动力电路和控制电路组成,并有完备的保护电路和漏电保护开关。
动力电路为380V、50HZ,担负着油泵电机的起、停和保护。
控制部分的核心功能由“PLC”可编程序控制器来承担。
电气控制系统采用日本欧姆龙可编程序控制器(简称PLC)。
控制部分的核心功能由“PLC”可编程序控制器来承担,输出口采用隔离继电器驱动负载,保护PLC不易被损坏。
通过彩色触摸屏进行各数据的显示及预置值设定处理与存储。
画面为人机交互式,可在触摸屏幕上非常方便地对主缸的压力、各种时间参数进行数字设定,清晰的显示压力和时间参数、及阀的工作状态等;可以存储数十套模具的相关参数,操作简便;并设有智能化故障显示诊断功能及故障部位,并发讯功能且与液压机动作联锁。
5.2、电器线路采用防油耐腐蚀优质铜芯线,电气系统有独立的电气控制柜。
柜内配有漏电保护、通风设施。
5.3、主操作面板:压机安装有操作按钮站。
并有各种操作按钮及指示灯。
操作面板要求中文永久标示,耐腐蚀,方便操作。
5.4、大功率电机起动采用星三角降压,依先后次序逐个起动。
5.5、设备设有可移动操作按钮站。
位于机器的前,以方便操作。
5.6、机身上预留AC36V;AC220V,10A;AC380A,10A电源插座各两个,机身四角设有急停按钮,立柱内侧装有照明灯。
5.7、所有按钮、指示灯、转换开关等均采用法国施耐德产品,接近开关采用日本OMRON 公司产品,性能稳定可靠。
5.8、电气控制柜为独立式,设置于地面,电控系统采用可编程控制器控制,PLC控制的压力和工作方式为调整、无压力下行、半自动和连续四种动作及紧急停止、紧急返回功能。
应能满足主油泵启动、停止及相关的互联锁要求。
5.9、设备应有独立的按钮站,按钮站设所需的开关、指示色灯、紧急停止按钮;主按钮站上应有液压油温、包边压力计数字显示,主油泵电流显示表和触摸显示屏等。
5.10、主操作面板设置于压机前面右立柱的侧面,而副操作面板设置于对角的后部立柱侧面。
六、压机操作方式和工艺动作6.1、压机工作方式: 定压或定程。
6.2、压机设调整、无压力下行、半自动,自动四种操作方式。
用转换开关转换。
6.2.1、调整:按压相应按钮产生相应动作,手松动作停。
此动作无快速。
6.2.2、无压力下行:按压相应按钮滑块下行,不加压。
6.2.3、半自动循环:按压双手下行按钮,压机连续完成快降-慢降-加压(到设定值)-回程一个循环动作。
6.2.4、自动:按压自动按钮,根据设定循环时间,自动循环工作6.3、压机能完成下列工艺动作:6.3.1、设备单周期连续工作循环为:人工将产品放至模具上产品输送装置→启动设备开机运行按钮(自动)→模具内产品定位挡块自动升起到位→输送装置启动完成将产品输送入模具内→到位后输送装置停机→模具顶件器和定位挡块自动下降→下降都到位后自动启动油压机一个工作循环周期→油压机一个工作循环周期完成后自动启动模具顶件器上升→模具顶件器上升到位后启动模具上产品输送装置产品送出→送出到位后自动停止输送装置→人工卸下产品,完成循环。
6.3.2、设备连续工作循环为:设备外传送带将产品送至模具上产品输送装置→设备自动识别到位启动模具内产品定位挡块升起到位→模具上输送装置启动完成将产品输送入模具内→到位后输送装置停机→模具顶件器和定位挡块自动下降→下降都到位后自动启动油压机一个工作循环周期→油压机一个工作循环周期完成后自动启动模具顶件器上升→模具顶件器上升到位后启动模具上产品输送装置产品送出到设备外传送带→送出到位后自动停止输送装置→等待下一件产品输送进来(注:产品未取走时,自动启动不能运行)。
6.3.4、油压机一个工作循环周期:油压机滑块自锁解除→滑块快速下降→滑块快速下降到位后慢速下降→滑块慢速下降到位后加压、保持→完成后滑块快速上升→滑块快速上升到位后慢速上升→滑块慢速上升到位后停止、自锁。
七、设备安全保护措施7.1、静止及急停按钮:发生异常时按“静止”按钮, 压力机工作全部停止,按“急停”按钮,包括电机均停止运行。
压机设有四个急停按钮, 操作控制面板上一个,另外三个分别设在另三个立柱上;在任何状态和情况下,按压其中任何一个急停按钮,压机立即停止。
7.2、双手操作按钮。
7.3、液压双支承保险回路:为防止滑块失控下行, 在活塞式主油缸下腔设置液压支承保险阀回路,确保安全。
设置液压联锁安全回路,确保支承保险阀不打开时,主缸活塞就无法下行。
7.4、超载保护:液压系统中设有液压安全阀,确保压机不会超载工作而损坏压机。
7.5、机器顶部设有维修平台、梯子和机器高位警示灯,确保维修人员安全。