丰田生产方式和4S(新人教育用)中文(完整版)
丰田生产方式
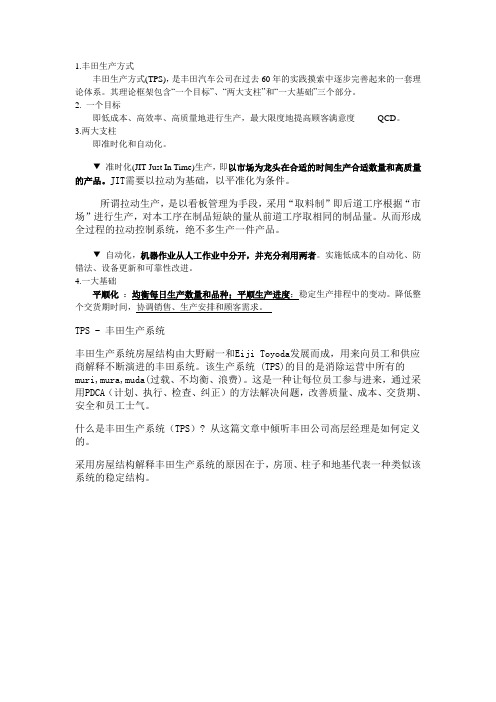
1.丰田生产方式丰田生产方式(TPS),是丰田汽车公司在过去60年的实践摸索中逐步完善起来的一套理论体系。
其理论框架包含“一个目标”、“两大支柱”和“一大基础”三个部分。
2. 一个目标即低成本、高效率、高质量地进行生产,最大限度地提高顾客满意度------- QCD。
3.两大支柱即准时化和自动化。
▼准时化(JIT-Just In Time)生产,即以市场为龙头在合适的时间生产合适数量和高质量的产品。
JIT需要以拉动为基础,以平准化为条件。
所谓拉动生产,是以看板管理为手段,采用“取料制”即后道工序根据“市场”进行生产,对本工序在制品短缺的量从前道工序取相同的制品量。
从而形成全过程的拉动控制系统,绝不多生产一件产品。
▼自动化,机器作业从人工作业中分开,并充分利用两者。
实施低成本的自动化、防错法、设备更新和可靠性改进。
4.一大基础平顺化:均衡每日生产数量和品种;平顺生产进度;稳定生产排程中的变动。
降低整个交货期时间,协调销售、生产安排和顾客需求。
TPS - 丰田生产系统丰田生产系统房屋结构由大野耐一和Eiji Toyoda发展而成,用来向员工和供应商解释不断演进的丰田系统。
该生产系统 (TPS)的目的是消除运营中所有的muri,mura,muda(过载、不均衡、浪费)。
这是一种让每位员工参与进来,通过采用PDCA(计划、执行、检查、纠正)的方法解决问题,改善质量、成本、交货期、安全和员工士气。
什么是丰田生产系统(TPS)? 从这篇文章中倾听丰田公司高层经理是如何定义的。
采用房屋结构解释丰田生产系统的原因在于,房顶、柱子和地基代表一种类似该系统的稳定结构。
今天,丰田生产系统还在不断的发展。
丰田人开始称丰田生产系统为“员工思考的系统”来代替原有名称。
丰田系统总是不断的改进。
丰田生产系统(TPS)是精益企业的运营蓝图大多数成功实施精益的组织都采用丰田生产系统作为他们的运营蓝图。
他们学习并理解该系统,重新命名使其结合自身情况为其所用,同时尽可能采用纯粹的丰田方式。
丰田生产方式(ToyotaProductionSysterm,TPS)又称精益生产方式

丰田生产方式(ToyotaProductionSysterm,TPS)又称精益生产方式1 绪论1.1 课题背景许多年来,美国和一些主要工业化国家也抱怨自己的制造业衰落了,而且经常因此而指责中国制造业的发展。
但是,近年Robert McGuckin 博士的最新的研究披露,现在不能证实各国的制造业存在着这种缓慢下滑趋势。
例如在美国,无论他们认为制造业发展是好还是“下滑”的时候,其制造业都至少每年为本国创造了1600万个就业岗位,它占全美就业的14%,而包括德国、法国与日本等发达国家也存在相似的状况。
世界很多大型企业都在学习丰田管理模式的基础上,建立了各自的管理系统,以试图实现标杆超越,像通用电气公司、福特公司、克莱斯勒公司等世界著名企业都加入了这一行列。
但是,令人惊异的是,尽管丰田管理模式已为全球所认同和接受,真正成功的企业却并不多,如今位于日本的丰田公司每天都要接受数以万计的企业高级管理者参观,这些参观者将他们看到的管理方式带到本国后,并没有得到意想的效果,为此,很多人认为丰田管理模式的成功根源于其独特的文化因素。
但事实并非如此,例如同是日本公司的尼桑和本田却并没有达到丰田的标准,而丰田本身却将其独特的管理模式带到了全世界,这其中的代表就是位于美国肯塔基州的丰田乔治城汽车生产厂,该厂自1988年7月开始在1300英亩的厂址上进行批量生产,年生产能力为200000辆Camry轿车,相当于以往美国从日本进口同类型轿车的总量,1991年秋天丰田美国公司引入了全新的Camry轿车,1992年该类型车的供应量为40000辆,销售额将增加20%。
新的Camry轿车属于中等家庭车系列,占有美国所有轿车市场l/3的市场份额,价格平均为$18500,税前平均利润为17%,显然,其经营绩效是十分瞩目的。
各国长期经济发展的经验证明,制造业对于提高国家生产率和国民的生活水平有至关重要的决定性作用。
由于制造业在国家经济发展中的这些重要作用使美国、英国、德国、墨西哥与比利时等国过半数的制造公司在2004年都优先支持满足顾客需求的制造技术革新与改进,他们都在为计算机、数据采集装置和B9C等顶层自动化进行投资(TPS 咨询公司,2004)。
图解 丰田生产方式

图解丰田生产方式丰田生产方式的体系和基本思想:丰田生产方式的目的是消除浪费和创造高质量、高收益。
在销售产品时,必须在总成本上加上利润,这就是销售价格,由此可以明白,提高利润的方式有以下三种:1.提高销售价格2.多产多卖3.降低成本丰田生产方式的特点就是为了实现降低成本的目的,不仅在制造成本中,而且在丰田独特的生产结构中消除七种浪费。
Step1 在经济增长无望的时代,降低成本。
Step2 丰田在其生产组织结构中彻底消除浪费。
通过准时化消除时间上的浪费,通过自动化提高产品质量。
Step3 通常企业在降低成本时,都考虑降低制造成本,制造成本包括材料费、劳务费、经费三部分。
丰田七种浪费:以减少无效生产时间的浪费为中心目标,对生产结构加以改善。
1、生产过量的浪费。
2、不合格产品的浪费。
3、停工等活的浪费。
4、动作的浪费。
5、运输的浪费。
6、加工本身的浪费。
7、库存的浪费。
高收益的秘密在于生产方式的思想丰田推行“在实行量产化的同时,也坚持以人为中心的生产方式”。
从销售价格中减去成本就是利润,销售价格是由顾客决定的。
通过彻底消除3MU来确立高质量、高收益体制:3MU的对立面就是效率,以效率高的姿势和跑法,保持一定的节奏跑的人,似乎最终取得胜利的几率较高。
制造产品也可以通过技术上的差别来降低成本,提高质量,3MU就是muri(超负荷的人员或设备)、muda(浪费)、mura(不均衡)。
我们需要培养一种发现浪费的眼光。
作业效率=生产量总工时数/(作业工时数-非作业工时数)×100%。
工时数是指人×作业时间。
在经济高度增长和销售不断增长的时期,在成长的光芒下很难发现浪费,从现状来看,任何一个企业都没有富余产品,引起这种生产过剩的浪费的原因是无视顾客的需求数量,任意提高生产数量的表面效率。
表面效率的提高会引起生产过剩的浪费,结果只是增加了库存。
因为是仔细观察事物,所以要仔细看整体,否则就不能有效改善,此时,瞄准目的技术非常重要,作为清除浪费的基本思想,可以把作业分为浪费作业、纯作业、附加作业。
S-4__丰田生产方式--改善
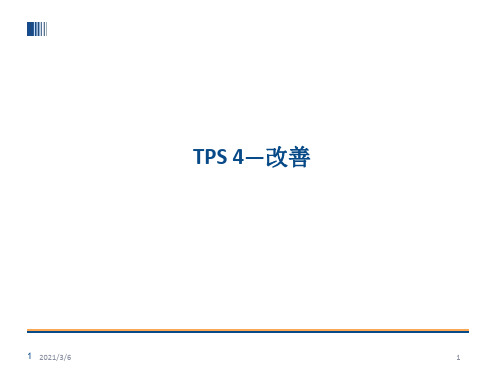
8 2021/3/6
8
产品发货状态表
9 2021/3/6
9
4. 通过“目视化管理”共同认识作业
丰田在各种作业中都运用到了“目视化管理”。如果用眼睛看一下, 谁都容易明白,就可以形成共同的认识,这样作业中的浪费和错误就可 以被消除。
一旦发生问题,立刻赶往现场,观察发生了问题的东西,仔细检查问 题发生状况,这样“三现主义”就植根了。这是把从古到今一直被流传 的“百闻不如一见”在实践中作为企业的体质而建立起来的思想。
技能不只是指作业的熟练程度,而是要使员工拥有问题意识,不断改善工序的 作业,接受教育训练,养成解决问题的能力。同时还融入了关于培养部下的能力、 团队合作的能力等内容。
无论自动化和人工智能化多么发达,丰田都认为只有人才能做好。
6 2021/3/6
6
技能工教育的观点
所谓技能工教育
① 实际作业能力(作业熟练 程度等) ② 改善工序作业等解决问题 的能力 ③ 培育部下的能力 ④ 团队合作的能力
④指定席和自由席
指定席是指在悬挂牌上涂上印记,把产品放入悬挂牌所指定的地方的方法。 自由席是指在生产中产生不一致的产品时,为了吸收不一致的产品,可以放上某样东西。
12 2021/3/6
12
目视管理(2)
指示灯
没有声音:正在运行中(正常),绿灯亮
有音乐:发生异常(缺少零件、产生不合 格产品等)时,作业人员按警报按钮,该
4
5S
放置场所管理、通道的区划线、危险标志、符合夹具工具形状,有利于养成用 眼观察的意识
5
进展状况
确认看现场的什么东西就能明白生产紧张状况,各道工序的看板和现货量,, 存货状况,生产管理牌,日程计划表
TPS丰田生产方式中文版完整版精品课件(二)

TPS丰田生产方式中文版完整版精品课件(二)- TPS丰田生产方式简介TPS是丰田生产方式(Toyota Production System)的缩写,是一种以精益生产为核心的生产方式。
TPS的目标是实现高效率、高质量、低成本的生产,从而提高企业竞争力。
- TPS的五大原则TPS的核心是五大原则:价值流思维、精益思维、流程改善、人员培养、标准化作业。
这五大原则相互关联、相互支持,是TPS成功的关键。
- 价值流思维价值流思维是指从客户的角度出发,以价值流为基础,通过精益生产的方式,最大限度地提高价值流的流畅度和效率。
价值流思维的核心是消除浪费,从而提高生产效率和质量。
- 精益思维精益思维是指以最小化浪费为目标,通过精细化生产、精益化管理、精益化设计等手段,实现高效率、高质量、低成本的生产。
精益思维的核心是通过不断改进,不断提高生产效率和质量。
- 流程改善流程改善是指通过价值流分析、流程分析等手段,找出生产过程中的瓶颈和浪费,从而对生产流程进行优化和改进。
流程改善的核心是通过精益生产的方式,实现流程的优化和改进,从而提高生产效率和质量。
- 人员培养人员培养是指通过培训、教育、激励等手段,提高员工的技能和素质,使其能够更好地适应精益生产的要求。
人员培养的核心是通过培训和激励,提高员工的工作积极性和创造力,从而推动生产的不断改进。
- 标准化作业标准化作业是指通过制定标准化流程、标准化操作等手段,确保生产过程的稳定性和可控性。
标准化作业的核心是通过制定标准化流程和操作,实现生产过程的可控和稳定,从而提高生产效率和质量。
- TPS的优点TPS的优点在于可以实现高效率、高质量、低成本的生产,从而提高企业的竞争力。
TPS可以帮助企业消除浪费,提高生产效率和质量,从而实现生产成本的降低和产品质量的提高。
- TPS的应用TPS已经被广泛应用于汽车制造、电子制造、机械制造等领域。
许多企业通过引进TPS的理念和方法,实现了生产效率和质量的提高,从而提高了企业的竞争力。
TPS丰田生产方式中文版(完整版)

1)自主保全 ・・・ 由制造部门实施
・第一阶段
・第二阶段
①・清扫
①・小改善
②・日常点检
②・定期换油
③・定期点检
③・定期更换
④・小维护、调整 ④・小修理(更换部件)
⑤・小停顿的恢复作业
・把握设备的功能、性能。 ・明白正常和异常。 ・掌握保全的知识和技能。
2)专业保全 ・・・由保全专业部门实施
・预防保全 ・・・ 有计划的实施 ・事后保全 ・・・ 缩短修理时间(KY训练、备齐备件)
1
TPS: Toyota Production System
丰田生产方式
・制造方法:彻底地实行JIT和自働化 ・通过TOTAL・TPS 推进成本降低
使现场充满活力
TOYOTA ENGINEERING CORPORATION 丰田ENGINEERING株式会社
2007. 10
HORIKIRI OZAWA SUZUKI
生产改善活动 生产活动
・工序改善 ・物流改善
自主研究会、生产会议
原来的TPS
业务范围 的扩展
16
・〔3〕:TOTAL-TPS的具体开展
・
1:现场的活性化 2:现场的可视化 3:作业改善
・每天的改善活动 ・营造有工作意义
的现场
4:物流改善
5:品质改善
7:改善的推进方法
8:制造工序的评价
6:新产品投产业务
成本
制造经费 加工费、物流费
②
材料、零部件费
4
〔2〕:从TPS到TOTAL-TPS的发展
TPS的发展
2007th
Profit 利润、利益
TPS的基本(2个支柱)
①・JIT(Just in Time) ②・自働化(Jidouka)
丰田生产模式

丰田生产模式的几个基本思想
六、库存的浪费
• 必要的库存系制造业的传统观念与作法,为了避免可 能造成生产停滞,库存视为理所当然;
• 丰田生产方式则认为库存是生产问题的根源,更是最 大的浪费所在;
• 因为库存需要建造仓库作为存放场所,然后需要工作 人员使用搬运机械设备将物品搬运至仓库,设置仓储 人员管理或作防锈处理,从仓库领用时生锈或有所损 伤时,又需整修作业等等,都造成增加人员设备及许 多额外提高成本的恶果;
•
15、一年之计,莫如树谷;十年之计 ,莫如 树木; 终身之 计,莫 如树人 。2021 年7月下 午9时4 9分21. 7.2121:49July 21, 2021
•
16、提出一个问题往往比解决一个更 重要。 因为解 决问题 也许仅 是一个 数学上 或实验 上的技 能而已 ,而提 出新的 问题, 却需要 有创造 性的想 像力, 而且标 志着科 学的真 正进步 。2021 年7月21 日星期 三9时4 9分2秒 21:49:0 221 July 2021
•
4、All that you do, do with your might; things done by halves are never done right. ----R.H. Stoddard, American poet做一切事都应尽力而为,半途而废永远不行6.17.20216.17.202110:5110:5110:51:1910:51:19
丰田生产模式的几个基本思想
二、产品成本分析
产品成本依制造方法和运输方式等不同而有所改变, 但大致可以分为两部分。
一是每个企业均相同的成本,如材料成本、零部件的 单价、能源单价、劳动单价、设备费折旧等。
丰田生产方式

实施做法
要活用Science SQC,理解的来应用是比较重要的,所以要整备Y 研修的Case,把研修毕业者作为SQC专门的人员或是专门的顾问, 这样来资格化。让他们作为各个现场•公司的推进Leader来进行实 际的指导,能够盘旋上升的展开。
Science SQC
科学的Approach 科学的SQC 管理SQC 有体系的组织的推进 Science SQC 解决问题的攀登 技术方法
这样进行改善的组织框架的建立,对于改善而有干劲 的人的培养是最重要课题。
顾客的要求越来越高
拿精度再 高一点 的来 再便宜些
每天 我用 多少 就送 多少
顾客的要求
明年的要求 还要更高的
作业标准和标准作业的不同
标准作业和作业标准是两个完全不同的方面,其主要的不 同之处如下。
作业标准
就是所谓的进行各个作业的标准。为了生产出顾客所要求 的质量,是以作业的经济条件为目标而规定的内容。例如 切削加工时的切削条件,钻头的种类等以及加热处理时的 加热的温度与时间,还有冷却条件以及冷却液等这些方面。 在制作作业标准上是有很多方法的,作为简易的方法像左 图表中的作业标准。
IT与TQM的关连上,丰田就是「满足顾客的焦点的IT化」 和「人改善可能的IT化」「实际成绩、评估、 Process可 视的IT化」。 ● 满足顾客的焦点就是从CS到CD(Customer Delight:超 过 顾客希望的惊讶),再进一步从车这一硬件的提供到 发 展到关于车生涯价值(Life Time Value)的软件服务。 ●改善就是在日常活动中随着反覆的进行改善与革新, 持续的进行改善。 ● 可视的IT化,因为Business Process的可视化以及信息 共 有环境中可以进行共同协作等。 同一种产品应该是许多公司都在生产,参加市场竞争的。 这样如果公司不同制作方法也是不同,所以成品的质量 方面(Q)、成本(C)、交期(D)各个公司也是有强有弱的。 即使质量好而成本过高、交期不好的话,顾客也会离去 的。QDC的综合力顾客是从各个方面来评价,竞争力弱 的公司,就自然会被淘汰。
丰田生产方式

丰田生产方式概述学号:06083007姓名:杜栋丰从以前的一般的汽车生产公司到今天的全世界排行第一位的汽车生产厂商,其生产方式是助其成功的一大方面,如今,各个制造业都认识到丰田生产方式是先进的生产方式,大家都在学习。
丰田生产方式分为几个主要的部分,准时制(Just in Time),均衡生产,标准时作业,丰田的持续性改善和优质生产等等。
准时制(JIT)生产是指:在所需要的时刻,按所需要的数量生产所需要的产品的生产模式,其目的是加速半成品的流转,将资金的积压减少到最低的限度,从而提高企业的生产效益。
它是一种全方位的系统管理工程。
准时制生产遵循着以下5个基本原则:1)物流准时原则。
要求在需要的时间段内,一般指15分钟至30分钟内,所有的物按照需要的规格、规定的质量水平和需要的数量,按规定的方式送到生产现场,或在指定的地点能提取货物。
2)管理的准时原则。
要求在管理过程中,能够按照管理的需要,遵照管理规定的要求收集、分析、处理和应用所需的信息和数据,并作为指令来进行生产控制。
3)财务的准时原则。
要求在需要时候,及时按照需要的金额调拨并运用所需的周转资金,保证企业的财务开支适应生产运行的需求。
4)销售的准时廊组。
要求在市场需求的供货时间内,组织货源和安排生产,按照订单或合向要求的品种和数量销售和交付产品,满足顾客的需求。
5)准时生产原则。
企业通过实施劳动组织柔性化来坚持多机床操作和多工序管理的生产方式,通过培训使操作工掌握一专多能的技艺,形成一支适应性强、技术水平高和富有创造性的工作团队,以保证各项特殊要求的生产任务能出色和按时地完成。
并且在生产组织上实行工序间“一个流”的原则或成品/半成品储备量逐年下降的原则,最终实现“零库存”的管理目标。
同时,在生产准备工作和生产调度也必须适应多品种混流生产的要求,实现柔性化生产。
均衡生产,是指在完成计划的前提下,产品的实物产量或工作量或工作项目,在相等的时间内完成的数量基本相等或稳定递增。
丰田生产方式用语说明(日语版)
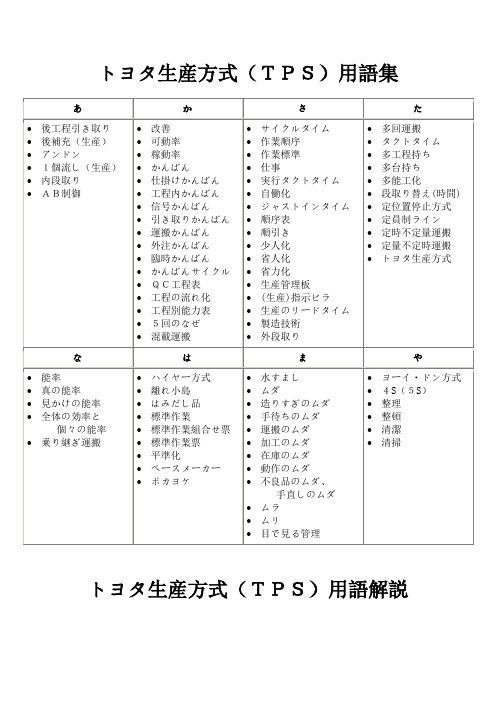
作業者一人が、受け持ち工程を決められた作業順序で作業して一巡するのに要する時間をいう。
作業順序 Working Sequence
標準作業の3要素1つで、作業者が一番効率的に良品の生産ができる作業の順序をいう。
作業標準 Operation Standards
標準作業を現場で正しく運営していく上で、工程図、品質チェック標準、QC工程表や安全標準などをベースとして、質・量・コスト・安全などを確保できるように各作業のやり方や条件を標準化したものの総称である。代表的なものとして、作業要領書・作業指導書・品質チェック要領書・刃具取り替え作業要領書などがある。
設備とその保全によってもたらされる信頼性に相当する。これは常に100%が理想である。
稼動率 Rate of Operation
後工程に必要な(売れに結びついた)生産量を加工するのに、その設備能力でフル操業した時の、定時能力に対する需要の割合をいう。
売れ行きによって、稼動率は決まるものである。
かんばんKanban
混載運搬 MIXED-Load Conveyance
1台の車両に、多種類の部品を積載して運搬する方法をいう。
この混載運搬により、運搬効率を低下させずに(運搬車両のトータルとしての運行回数を増やさずに)、多回運搬ができ前後工程の在庫量を少なくすることができる。また生産変動に対し運行回数の増減も容易になる。
工場が受注してから、製品の出荷にいたるまでの時間をいう。
A:該当製品の生産指示情報の滞留時間
B:該当製品の材料仕掛から完成にいたるまでの時間(加工時間+停滞時間)
C:該当製品の完成品の最初の1個(台)ができてから、後工程が引き取る数の完成品が出来あがるまでの時間(運搬数×該当製品の生産タクト)
丰田生产方式
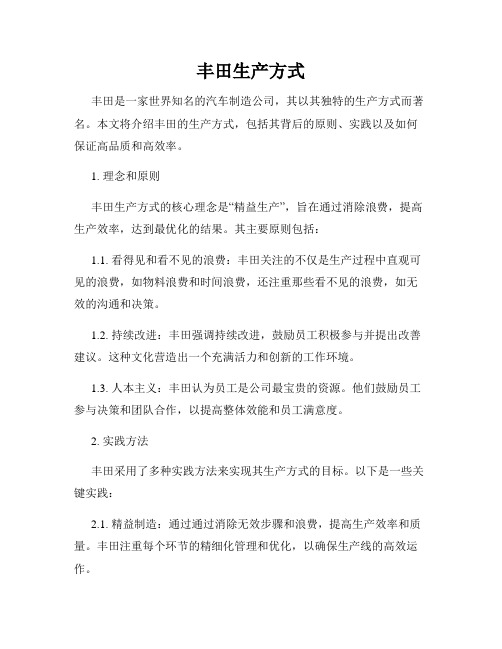
丰田生产方式丰田是一家世界知名的汽车制造公司,其以其独特的生产方式而著名。
本文将介绍丰田的生产方式,包括其背后的原则、实践以及如何保证高品质和高效率。
1. 理念和原则丰田生产方式的核心理念是“精益生产”,旨在通过消除浪费,提高生产效率,达到最优化的结果。
其主要原则包括:1.1. 看得见和看不见的浪费:丰田关注的不仅是生产过程中直观可见的浪费,如物料浪费和时间浪费,还注重那些看不见的浪费,如无效的沟通和决策。
1.2. 持续改进:丰田强调持续改进,鼓励员工积极参与并提出改善建议。
这种文化营造出一个充满活力和创新的工作环境。
1.3. 人本主义:丰田认为员工是公司最宝贵的资源。
他们鼓励员工参与决策和团队合作,以提高整体效能和员工满意度。
2. 实践方法丰田采用了多种实践方法来实现其生产方式的目标。
以下是一些关键实践:2.1. 精益制造:通过通过消除无效步骤和浪费,提高生产效率和质量。
丰田注重每个环节的精细化管理和优化,以确保生产线的高效运作。
2.2. 拉动制造:丰田采用拉动制造方式,根据客户需求来触发生产。
这种方式减少了库存和过度生产的问题,同时提高了交付效率。
2.3. 金工系统:丰田实施了严格的金工系统,以确保生产过程中的标准化和一致性。
这种系统有助于提高质量和工作效率,并最大限度地减少变动。
3. 丰田生产方式的优势丰田生产方式以其独特的优势而闻名于世。
以下是一些显著的优势:3.1. 灵活性:由于丰田生产方式的灵活性,公司能够快速做出响应,根据市场需求进行调整和变化。
这使得丰田能够更好地适应竞争激烈的市场环境。
3.2. 高质量:丰田通过严格的质量控制和工艺优化,确保产品高质量。
这种高品质有助于树立公司的声誉,并实现长期的客户忠诚度。
3.3. 高效率:通过消除浪费和优化生产过程,丰田能够达到更高的生产效率。
这使得公司能够提供更具竞争力的产品和服务,并实现更高的利润率。
总结:丰田生产方式是丰田公司成功的关键之一。
丰田4S管理培训教材

提高信任感和满意度
异常减少 品质提高 满意度提高
对策
寻找解决对策
TOYOTAL&F
“发现浪费”→“改善” 可以发现浪费的组织架构 4S
这一循环不断往复。
平均化生产
后续工序
标准作业
T P S 的 2 根 支 柱
Just/in/time 仅对“需要的产品”、“在必要的时间”、生产和搬运“必要 的量”。
TOYOTAL&F
制定4S日历
TOYOTAL&F
1. 丰田的生产方式和4S
2. 4S的实践
3. 维持4S的关键,另外一个S“教育”
TOYOTA L&F
检查你的公司的“教育”度 □①把不需要的物品扔掉后,会马上发生大量堆积。 □②工具使用完毕后,丢在那里不管。 □③物品不是什么时候不见了 □④钻头和美工刀的放置方法会影响其锋利程度 □⑤材料和零部件的堆积易发生倾倒 □⑥厕所肮脏 □⑦机械和设备沾满油污和粉尘,乌黑一片。 □⑧无论怎么劝说,都不戴安全帽和防护眼镜 □⑨作业场所和通道上布满烟屁股和垃圾 □⑩无法打招呼
在制造业中,只有“加工”是具有附加价值的作业=正式作业 只有正式作业才能得到回报。
TOYOTAL&F
所谓浪费:所有不能提高附加价值的工作。 浪费的种类 7种浪费
最严重的浪费 ①制造过剩 (会诱发其它浪费的 产生) ②拿在手里 ③搬运 ④加工过程自身存在的 浪费 ⑤库存 ⑥动作 ⑦不合格产品/修理
子啊丰田公司,在生产中, 把 ,在物流过程中把 定位为“最严重的浪费”。
自动化(带人字部的自动化) 发生异常时停止、人和机械的分离、在工序中控制质量
TOYOTAL&F
4S是基本中的基本,是进行改善最为重要的基础工作。
- 1、下载文档前请自行甄别文档内容的完整性,平台不提供额外的编辑、内容补充、找答案等附加服务。
- 2、"仅部分预览"的文档,不可在线预览部分如存在完整性等问题,可反馈申请退款(可完整预览的文档不适用该条件!)。
- 3、如文档侵犯您的权益,请联系客服反馈,我们会尽快为您处理(人工客服工作时间:9:00-18:30)。
即使看着很忙,拼命动作, 也不能变成工作
所谓働く就是通过改进工程 提高工作质量 达到减少浪费提高效率
区别每个动作是 会产生价值呢 还是会造成浪费 从而通过改善浪费 把「动き」转化为「働き」
「动き=浪费」的例子 ・找东西 ・货物的重复堆放 ・东西的取出放回
1.丰田生产方式和4S
何为浪费 : 所有不能增加附加价值的东西
重犯罪也不断减少
407,141
348,867 293,874
246,117 227,773
(件) 202,106 187,181
100,000
0 1994 1995 1996 1997 1998 1999 2000
如果4S做好、就会防止重大错失的发生
16/65
以丰田生产方式为准的4S的理解
1.丰田生产方式和4S 2.4S的实践 3.4S维持的钥匙、另外一个S「躾」
品质提高 满意度提高
臭东西从源头 切断
対策
7/65
1.丰田生产方式和4S
「浪费的发现」 「改善」
持续循环
能看到浪费的制度
4S
4S是基本中的基本
平准化生产
拉动式生产
标准作业
等
T P
及时化
S 「把必要的东西」「在必要的时间」 生产、搬运「必要的量」
的
2
根 支
自働化(带人字傍的自动化)
柱 异常停止、人和机器的分离、品质在工程内保证
29
V
M 19
T 12 45 39
D
8 24
Q
35 88 H 56
Z 21
S 18
9
J 72 40
2.4S的实践
1S:整理
1S的实际体验测试
1S后
1 23 17
9 20 36
6 32
要 26 33
3 37 13 28 24 38
的
7
39
34
11
18
35
10
21
东西 15
2 27 30 25
4 31 14
与作业有关的浪费
ቤተ መጻሕፍቲ ባይዱ
正味作业 付帯作业
浪费
种类
意味
正味作业 会产生附加价值的作业
制造业的例 加工部品
付帯作业
在当前的作业条件下虽然没有 付加価値但是必须做的作业业
去把部品拿过来 组合到机器上
浪费
现在立即停止也没影响的作业
找部品、等待、 部品的反复组装
在制造业只有「加工」是有附加价值的作业=正味作业 只有正味作业能取得报酬
22 16
8
5 29 12 19 40
G
S
F
T 55 81 70 48
不P
A
H
R 80
U
Z 84
要
的K O
C
I 65
V 72
W
东西 Q
L
B
J
X 45 56 72
D
N
E
M 60 92
Y 88
19/65
丰田式4S
“整理・整顿・清扫・清洁中有利润的源头”
1.丰田生产方式和4S
何为浪费 : 所有不能增加附加价值的东西 「働く」和「动く」
「働く」と「动く」
「働く」是以减少浪费、增加附加价值、为目的高效率的 工作(即“动く”)
「动く」是指不增加附加价值,仅仅动作而已
不改善,增加工作量 ⇒ 劳动强化 通过改善把「动き」变成「働き」 ⇒ 合理化
是要的部品呢 还是不要品呢
不知道
不知道异常 =作业品质的悪化
13/65
1.丰田生产方式和4S 4S如果做不好:②工作就不好开展
不知道什么地方有什么东西
来回找东西产生多余的作业
工作不好开展 =浪费多
14/65
1.丰田生产方式和4S 4S如果做不好:③危険
货物占据了道路
叉车和人交错时危険
导致事故的发生
5/65
1.丰田生产方式和4S
何为浪费 : 所有不能增加附加价值的东西
浪费的种类 最严重的浪费
东西做的太多
在库太多
需要很多仓库・空间
需要很多管理人
需要很多搬运人
需要很多栈板・保管容器
需要管理用的 指示票・程序
需要很多搬运车・叉车・台车
浪费会引发更多的浪费!!
而且、「只多生产这么点没关系」「这么点在 库没关系」这样漫不经心的想法、会阻碍改善意识萌芽的产生
在丰田正常理所当然→这样就形成了只管理异常的体制
12/65
1.丰田生产方式和4S 「容易发现异常」・・・例
管理广告牌的作用
・在现地点能够一目了然 的判断工程是否异常
・能看见生产的进度
12/65
1.丰田生产方式和4S 4S没做好:①异常不容易发现
工厂的作业场脏乱
螺栓掉了 = 异常
螺栓掉了也没有察觉到
4/65
1.丰田生产方式和4S
何为浪费 : 所有不能增加附加价值的东西 浪费的种类 7种浪费
最严重的浪费 ①制作太多的浪费
(会引发其他的浪费)
②等待的浪费
③搬运的浪费
浪
费
④加工的浪费
⑤在库的浪费
⑥动作的浪费
⑦不良品・返修的浪费
丰田把生产方面的 东西制造的太多 、
物流方面的 在库太多
总结为「最严重的浪费」
6/65
1.丰田生产方式和4S 何为浪费 : 所有不能增加附加价值的东西
「把问题点暴露出来」+「进行対策」
看不到问题点
・・・ 不想让他人知道
以
往
方
没有改善意识
・・・打算私自处理
式
改善没有进展
・・・隐藏问题点
把臭东西用
盖子盖住
対応
丰
田
问题点要让他人知道 、暴露出来
方
式
进行对策
信頼和满意度的提高
异常逐渐减少
17/65
2.4S的实践
1S:整理
1S的实际体验测试
1S前
1
O
5 11
17 31 G 20
38
3
A
W
55
L 81 14
E 28 70 37
36
6 10
X
22 26 33
B
P 60 30
R
C 15 92
4
32
Y
I 27
18/65
48 25 84 N
7 16 13 80
F
U
2 65
K 34 72 23
4S是最基本最重要的“型”
惯
4S不仅仅是「美化运动」
11/65
1.丰田生产方式和4S
「容易发现异常」这里的异常是
正常 和 异常
区别
作业的进展状况 人的动作
东西的放置方法 放置场所
情报的流通
等正确的基准处于明确的状态=正常
「正常」如果没有定义出来, 「正常」还是「异常」不知道
和这个基准不一致的就是异常
15/65
1.丰田生产方式和4S 如果小的犯罪放置、会引发大的犯罪
破窗户理论
把引擎盖打开的废车在住宅地放置一个星期
前挡风玻璃砸坏
前挡风玻璃和保持原状
结果
车变的破破烂烂・・・
紧接着玻璃被打碎、很多 部品被盗。
结果
车和以前一样・・・
完全没变
纽约市进行消除地下铁的乱写乱画、强化 轻犯罪的管治
500,000 400,000 300,000 200,000
10/65
1.丰田生产方式和4S
4S是基本中的基本、是改善的重要基础工事
4S
+ 1S
整理
躾
通过4S的彻底实施
要・不要区分开不要的废弃
整顿
按使用方便去放置
清扫
清扫干净
清洁
维持
规定
①能够发现异常
的 事
②工作容易进行
能
③不会使人・东西受伤
够
正
确
遵
守 并
成为全部改善的基础
养 成
丰田生产方式是改善的“型”
习