KANBAN
kanban及kanban管理

kanban及kanban管理Kanban(Taiichi Ohno在Toyota(丰田汽车)任副总裁时的系统开发)是一个卡,设计用于防止过量生产并且保证关键部件在每一工艺步骤都有详细说明,反过来定单(Kanban在日语里意为”可视的录制”)。
Kanban过程是一个补充系统,设计用于控制每一生产工序中的产量。
Kanban 是卡片包含所有信息必需做在产品在各个阶段沿它的道路对完成并且哪个零件是需要的在随后过程。
Kanban是个日语名词,表示一种挂在或贴在盛装在制品的容器上或一批零件上的标签或卡片,或流水线上各种颜色的小球或信号灯、电视图象等。
看板是揭示牌,可以作为交流厂内生产管理信息的手段。
看板卡片包含相当多的信息并且可以反复使用。
看板通常是装在透明的长方形乙烯封套中,为得是在工厂环境中保护卡片不受损坏。
常用的看板有两种:生产看板(或生产通知看板)和运送看板(或取货看板).生产看板指在一个工厂内,指示某工序加工制造规定数量工件所用的看板。
运送看板是指后道工序的操作者按看板上所列件号,到前到工序(或协作厂)领取的看板。
Replenishment Kanban是补货看板;补货看板是一种补货的管理方法,现场库存与供应商及第三方物流已形成一条专门的货物供应链的前提下,进行补货看板管理;它根据现场库存的耗用速度与耗用时数量,以及制定的补货点规则,计算出补货的数量和参数,参数包括货品种类规格,补货时间,运货方式,运货地点等,并打印出此补货看板,再将此投入到供应链循环中,快速进行被货;也可以这样认为,补货由看板来进行管理,一旦库存量少于一定水平,便向供应商或第三方物流发出送货指令,及时进行补货,这样可以减少现场库存的货品屯积,甚至实现零库存管理,又能达到满足生产的要求;简单说来……看板就是一种可视的拉动系统,能够方便地在正好对某个物品发生需求的时候传递信息。
当流程工作站之间无法实现连续流动时,通常我们用看板和超市的模式实现拉动式生产。
敏捷项目管理中的Kanban方法解析与应用
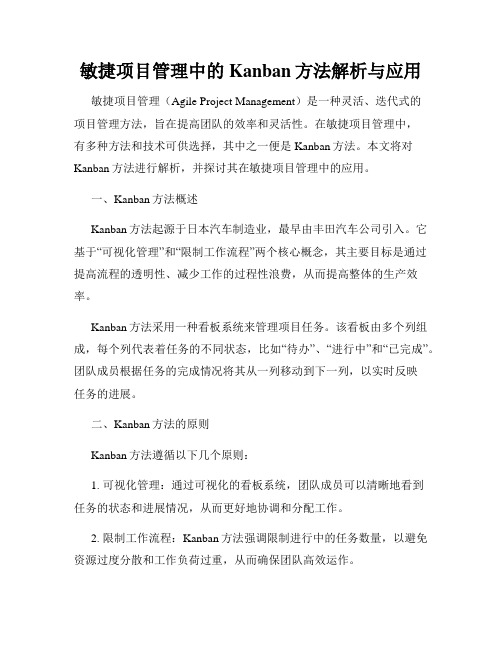
敏捷项目管理中的Kanban方法解析与应用敏捷项目管理(Agile Project Management)是一种灵活、迭代式的项目管理方法,旨在提高团队的效率和灵活性。
在敏捷项目管理中,有多种方法和技术可供选择,其中之一便是Kanban方法。
本文将对Kanban方法进行解析,并探讨其在敏捷项目管理中的应用。
一、Kanban方法概述Kanban方法起源于日本汽车制造业,最早由丰田汽车公司引入。
它基于“可视化管理”和“限制工作流程”两个核心概念,其主要目标是通过提高流程的透明性、减少工作的过程性浪费,从而提高整体的生产效率。
Kanban方法采用一种看板系统来管理项目任务。
该看板由多个列组成,每个列代表着任务的不同状态,比如“待办”、“进行中”和“已完成”。
团队成员根据任务的完成情况将其从一列移动到下一列,以实时反映任务的进展。
二、Kanban方法的原则Kanban方法遵循以下几个原则:1. 可视化管理:通过可视化的看板系统,团队成员可以清晰地看到任务的状态和进展情况,从而更好地协调和分配工作。
2. 限制工作流程:Kanban方法强调限制进行中的任务数量,以避免资源过度分散和工作负荷过重,从而确保团队高效运作。
3. 反馈机制:Kanban方法鼓励团队成员在任务完成后进行回顾和反馈,以不断改进工作流程和提高工作效率。
三、Kanban方法在敏捷项目管理中的应用Kanban方法在敏捷项目管理中有如下应用:1. 任务管理与优先级划分:通过Kanban看板,团队成员可以清晰地了解项目的任务和优先级,从而更好地管理和分配任务。
同时,团队成员可以根据任务的重要性和紧急程度进行优先级划分,确保高价值任务得到及时处理。
2. 工作流程控制与优化:Kanban方法可以帮助团队发现工作流程中的瓶颈和问题,及时调整和优化工作流程,提高工作效率和质量。
团队成员可以通过可视化的看板,追踪任务的进展和周期,从而更好地掌控工作状态。
3. 团队协作与沟通:Kanban方法通过可视化的看板和任务拆分,促进团队成员之间的沟通和协作。
KANBAN管理系统综述

Receiving post
Kanban card for product 1
Kanban card for product 2
Storage area
O2
Fabrication
cell
O1
O3
O2
Empty containers Full containers
Assembly line 1 Assembly line 2
实行KANBAN系统的结果
•客户的满意 •优化整个工业系统的库存 •使用简单,没有数据处理 •操作者参与到生产管理中 •生产部员工增强了质量意识和销售观念
六个方面产生良好的影响:
1、展示改善成绩,让参与者有成就感、自豪感 2、营造竞争的氛围 3、营造现场活力的强有力手段。 4、明确管理状况,营造有形及无形的压力,有利于工作的推进。 5、树立良好的企业形象。(让客户或其他人员由衷地赞叹公司的管理水平) 6、展示改善的过程,让大家都能学到好的方法及技巧。
• 若每箱內各有22个零件,則箱子(看板)数量为多少?
工作中心(Work Center)的 看板数量的计算(1)
如果此物料的供应点不是瓶颈,其物料补充周期与物料 数量无关
触发数量=下道日消耗数量*物料补充周期
看板数量=触发数量
工作中心(Work Center)的 看板数量的计算(2)
如果此物料的供应点不是瓶颈,其物料补充周期与物料 数量有关(近似成正比)
看板(容器)数量之决定2
N=
前置期期间的平均需求+安全库存 标准容器的零件容量
(dL+S)(1+x)
=
c
看板(容器)数量之决定3
考虑前提: 1. 各工作中心的生产速率相同 2. 补充时间:看板离开材料到新材料挂上该看板入库
JIT看板Kanban管理
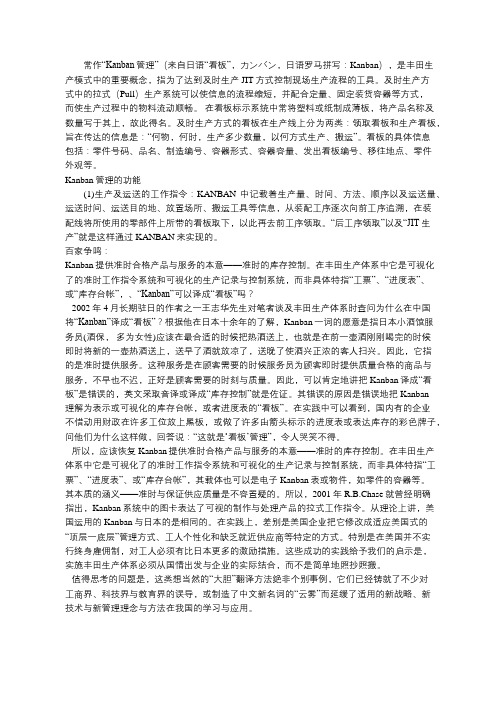
常作“Kanban管理”(来自日语“看板”,カンバン,日语罗马拼写:Kanban),是丰田生产模式中的重要概念,指为了达到及时生产JIT方式控制现场生产流程的工具。
及时生产方式中的拉式(Pull)生产系统可以使信息的流程缩短,并配合定量、固定装货容器等方式,而使生产过程中的物料流动顺畅。
在看板标示系统中常将塑料或纸制成薄板,将产品名称及数量写于其上,故此得名。
及时生产方式的看板在生产线上分为两类:领取看板和生产看板,旨在传达的信息是:“何物,何时,生产多少数量,以何方式生产、搬运”。
看板的具体信息包括:零件号码、品名、制造编号、容器形式、容器容量、发出看板编号、移往地点、零件外观等。
Kanban管理的功能(1)生产及运送的工作指令:KANBAN中记载着生产量、时间、方法、顺序以及运送量、运送时间、运送目的地、放置场所、搬运工具等信息,从装配工序逐次向前工序追溯,在装配线将所使用的零部件上所带的看板取下,以此再去前工序领取。
“后工序领取”以及“JIT生产”就是这样通过KANBAN来实现的。
百家争鸣:Kanban提供准时合格产品与服务的本意——准时的库存控制。
在丰田生产体系中它是可视化了的准时工作指令系统和可视化的生产记录与控制系统,而非具体特指“工票”、“进度表”、或“库存台帐”,、“Kanban”可以译成“看板”吗?2002年4月长期驻日的作者之一王志华先生对笔者谈及丰田生产体系时查问为什么在中国将“Kanban”译成“看板”?根据他在日本十余年的了解,Kanban一词的愿意是指日本小酒馆服务员(酒保,多为女性)应该在最合适的时候把热酒送上,也就是在前一壶酒刚刚喝完的时候即时将新的一壶热酒送上,送早了酒就放凉了,送晚了使酒兴正浓的客人扫兴。
因此,它指的是准时提供服务。
这种服务是在顾客需要的时候服务员为顾客即时提供质量合格的商品与服务,不早也不迟,正好是顾客需要的时刻与质量。
因此,可以肯定地讲把Kanban译成“看板”是错误的,英文采取音译或译成“库存控制”就是佐证。
Kanban (看板)
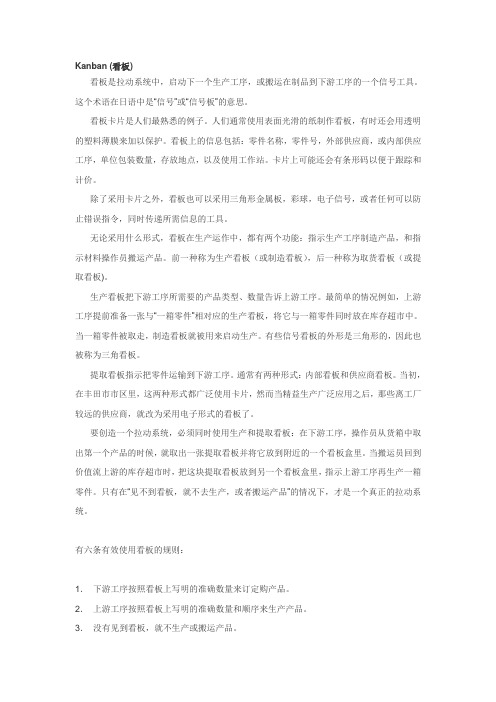
Kanban (看板)看板是拉动系统中,启动下一个生产工序,或搬运在制品到下游工序的一个信号工具。
这个术语在日语中是“信号”或“信号板”的意思。
看板卡片是人们最熟悉的例子。
人们通常使用表面光滑的纸制作看板,有时还会用透明的塑料薄膜来加以保护。
看板上的信息包括:零件名称,零件号,外部供应商,或内部供应工序,单位包装数量,存放地点,以及使用工作站。
卡片上可能还会有条形码以便于跟踪和计价。
除了采用卡片之外,看板也可以采用三角形金属板,彩球,电子信号,或者任何可以防止错误指令,同时传递所需信息的工具。
无论采用什么形式,看板在生产运作中,都有两个功能:指示生产工序制造产品,和指示材料操作员搬运产品。
前一种称为生产看板(或制造看板),后一种称为取货看板(或提取看板)。
生产看板把下游工序所需要的产品类型、数量告诉上游工序。
最简单的情况例如,上游工序提前准备一张与“一箱零件”相对应的生产看板,将它与一箱零件同时放在库存超市中。
当一箱零件被取走,制造看板就被用来启动生产。
有些信号看板的外形是三角形的,因此也被称为三角看板。
提取看板指示把零件运输到下游工序。
通常有两种形式:内部看板和供应商看板。
当初,在丰田市市区里,这两种形式都广泛使用卡片,然而当精益生产广泛应用之后,那些离工厂较远的供应商,就改为采用电子形式的看板了。
要创造一个拉动系统,必须同时使用生产和提取看板:在下游工序,操作员从货箱中取出第一个产品的时候,就取出一张提取看板并将它放到附近的一个看板盒里。
当搬运员回到价值流上游的库存超市时,把这块提取看板放到另一个看板盒里,指示上游工序再生产一箱零件。
只有在“见不到看板,就不去生产,或者搬运产品”的情况下,才是一个真正的拉动系统。
有六条有效使用看板的规则:1.下游工序按照看板上写明的准确数量来订定购产品。
2.上游工序按照看板上写明的准确数量和顺序来生产产品。
3.没有见到看板,就不生产或搬运产品。
4.所有零件和材料都要附上看板。
JIT与Kanban对库存管理的影响

实施难度比较
技术要求
JIT需要较高的技术支撑,如生产计划、物流配送等方面的 技术;而Kanban则相对简单,主要依靠看板管理。
人员要求
JIT需要一支专业的管理团队,具备较高的管理素质和技能 ;而Kanban则相对对人员要求较低,操作简单易行。
成本投入
JIT需要较大的初期投入,包括技术研发、设备购置等方面的费 用;而Kanban则成本较低,主要涉及看板制作和人员培训。
jit与kanban对库存 管理的影响
目录
CONTENTS
• JIT(准时制)生产方式简介 • Kanban生产方式简介 • JIT对库存管理的影响 • Kanban对库存管理的影响 • JIT与Kanban的比较与选择 • 实际应用案例分析
01 JIT(准时制)生产方式 简介
JIT的核心理念
未来发展趋势
JIT与IoT技术的结合
随着物联网技术的发展,JIT将与IoT技术深度融合,实现 实时监控、智能调度和自动化配送等功能。
Kanban的数字化转型
随着数字化转型的推进,Kanban将逐渐实现数字化管理 ,通过数字化看板和数据分析,提高库存管理效率和准确 性。
混合库存管理模式
未来库存管理模式将趋向于混合模式,即结合JIT和 Kanban的优势,根据企业实际情况选择合适的库存管理 模式,实现库存管理的最优解。
03 JIT对库存管理的影响
降低库存成本
减少库存持有成本
01
JIT通过及时生产减少库存量,从而降低库存持有成本。
降低库存损耗
02
JIT生产方式能够快速响应市场需求变化,避免因需求预测不准
确而导致的库存积压和损耗。
降低库存管理成本
03
kanban研发流程

kanban研发流程
看板(Kanban)研发流程是一种基于精益和敏捷原则的方法论,用于管理和优化软件开发过程。
以下是看板研发流程的一般步骤:
1. 确定价值流:价值流是指从需求提出到产品交付的整个过程。
识别和理解价值流可以帮助团队明确工作流程和关键环节。
2. 可视化工作:使用看板将工作流程和任务以可视化的方式展示出来。
看板通常以列的形式表示不同阶段或状态的工作,例如待办事项、进行中、已完成等。
3. 定义工作项:将需求或任务拆分为可管理的工作项,并将其记录在看板上。
每个工作项应包含清晰的描述、负责人和预计完成时间等信息。
4. 限制在制品(WIP):为了避免工作拥塞和多任务并行导致的效率下降,采用在制品限制原则。
通过限制同时进行的工作项数量,确保团队专注于高优先级的任务。
5. 流动原则:鼓励工作项的快速流动,从一个阶段到另一个阶段,减少等待和阻塞。
通过解决瓶颈和优化流程,加速价值的交付。
6. 每日站会:团队成员在每日站会上更新工作进展,分享障碍和问题,并共同协商解决方案。
站会帮助促进沟通和协作,确保团队成员之间的信息流通。
7. 持续改进:通过观察和分析看板上的工作流程,识别潜在的改进机会。
团队可以定期回顾和调整流程,以提高效率和质量。
看板研发流程强调可视化、限制 WIP、流程优化和持续改进,有助于团队更好地管理工作、提高协作效率,并实现高质量的产品交付。
看板的作用及其使用规则
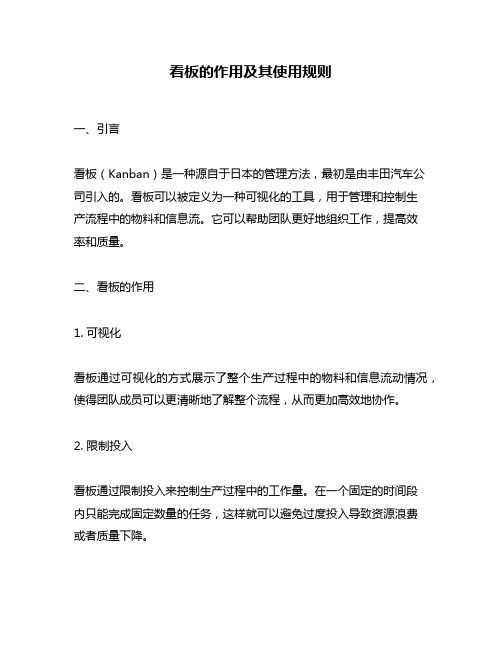
看板的作用及其使用规则一、引言看板(Kanban)是一种源自于日本的管理方法,最初是由丰田汽车公司引入的。
看板可以被定义为一种可视化的工具,用于管理和控制生产流程中的物料和信息流。
它可以帮助团队更好地组织工作,提高效率和质量。
二、看板的作用1. 可视化看板通过可视化的方式展示了整个生产过程中的物料和信息流动情况,使得团队成员可以更清晰地了解整个流程,从而更加高效地协作。
2. 限制投入看板通过限制投入来控制生产过程中的工作量。
在一个固定的时间段内只能完成固定数量的任务,这样就可以避免过度投入导致资源浪费或者质量下降。
3. 管理存货看板可以帮助管理存货,并确保库存水平始终保持在最佳状态。
通过实时监控库存水平和订单需求,可以及时调整生产计划以满足客户需求。
4. 提高效率看板可以帮助团队更好地组织工作,使得任务分配更加合理化、协同更加顺畅、交付更加及时。
这些都有助于提高生产效率和质量。
5. 改善流程看板可以帮助团队识别生产过程中的瓶颈,从而改善流程。
通过实时监控生产过程中的物料和信息流动情况,可以及时发现问题并采取措施加以解决。
三、看板的使用规则1. 看板必须可视化看板必须是一种可视化的工具,它应该能够清晰地展示整个生产过程中的物料和信息流动情况。
这样才能帮助团队更好地协作,提高效率和质量。
2. 看板必须限制投入看板通过限制投入来控制生产过程中的工作量。
在一个固定的时间段内只能完成固定数量的任务,这样就可以避免过度投入导致资源浪费或者质量下降。
3. 看板必须管理存货看板可以帮助管理存货,并确保库存水平始终保持在最佳状态。
通过实时监控库存水平和订单需求,可以及时调整生产计划以满足客户需求。
4. 看板必须提高效率看板可以帮助团队更好地组织工作,使得任务分配更加合理化、协同更加顺畅、交付更加及时。
这些都有助于提高生产效率和质量。
5. 看板必须改善流程看板可以帮助团队识别生产过程中的瓶颈,从而改善流程。
通过实时监控生产过程中的物料和信息流动情况,可以及时发现问题并采取措施加以解决。
KANABN管理方法资料
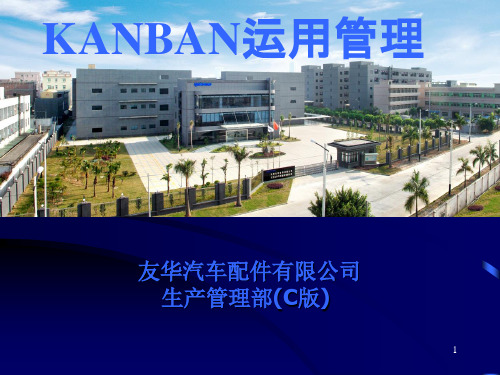
28
看板与ERP接轨
• • • • • • 根据看板发出信息,作成ERP订单. 按部品的包装单位打印出ERP现品票(条码). 看板+ERP订单+ERP现品票 装订好送供方. 供方生产包装时,贴上ERP现品票. 友华汽车收货时,条码机扫描入帐(入ERP系统) IQC检查,入出仓库等采用条码机扫描.
29
36
四 确 认 供 应 商 是 否 把 看 板 挂 在 相 应 的 部 品 上
三 确 认 看 板 的 数 量 及 纳 期
二 确 认 部 品 上 有 没 有 贴 现 品 票
一 确 认 供 应 商 有 没 有 带 看 板
37
仓库人员要把部 品与看板一一对 应入库看板数量 需要与实物相符
一目了然
38
部 品 出 时 从 相 对 应 的 部 品 上 取 下 看 板
15
KANBAN运用的流程图:
生產管理
看 板
(調達)
发注确定
看 板
指示日 纳入日 IQC确认
A
3
4 5
制造
供 给 材 料
KANBAN
供 应 商
调达依赖
看 板
1
6
看 板
2
KANBAN
受入IQC检查后 看板和物整理入 库
7
16
有关纳入日和指示日(A):
17
KANBAN方式(纳入指示KANBAN)
1.标准状态
看板总枚数与交货周期有关系
12
KANBAN枚数的算出和决定(2):
KANBAN枚数=日生产要数量*(L/T+安全日数) 捆包单位 L/T=生产L/T(加工时间+停滞时间)+KANBAN 回收的L/T 日生产要数量=月生产数量/稼动日数
JIT采购名词解释

JIT采购名词解释JIT采购,即“Just-In-Time”采购,是一种在生产或供应过程中,根据需求进行即时采购和交付的方法。
它旨在通过减少库存和准确控制供应链来提高效率,并确保产品及时到达客户手中。
下面是对JIT采购中常见的一些名词的解释。
1. JIS(Just-In-Sequence):正按顺序及时供货。
JIS是JIT的一种扩展,它要求按特定的顺序及时供应零部件,以保证生产线上的顺序不被打乱。
2. Kanban(看板):一种用于JIT生产的控制方法,它通过可视化信号(通常是卡片)来控制生产和补给。
当库存低于设定量时,卡片被触发,表示需要进行补给。
3. Takt Time(节拍时间):是指JIT生产中所需完成一个产品的时间间隔。
它是根据需求和制造能力来计算的,以确保产量与需求之间的平衡。
4. Andon(安灯):一种用于JIT生产中的可视化指示装置,用于通知问题、停工或其他异常情况。
当生产线上发生问题时,工人可以按下按钮或者其他装置来触发安灯指示,以便快速解决问题。
5. Poka-yoke(防错):一种用于JIT生产的错误预防方法。
它通过设计产品或工艺,以防止错误的发生或捕获错误,以提高生产质量和效率。
6. Bottleneck(瓶颈):在JIT生产中,指阻碍生产流程的狭窄部分。
通过识别并消除瓶颈,可以提高整个生产过程的效率和产量。
7. Value Stream Mapping(价值流图):用于分析价值流程的方法。
通过绘制出整个价值流程,并标注出各个环节的价值和非价值活动,可以帮助找到和消除浪费,并优化生产过程。
8. Kaizen(改善):一种长期持续改进的方法。
JIT采购中,Kaizen意味着与供应商和合作伙伴紧密合作,持续改进产品质量、交货时间和成本效益。
9. Lean Manufacturing(精益生产):一种以减少浪费为目标的生产方法。
JIT采购通常与精益生产原则相结合,以提高生产效率、降低成本和提高产品质量。
了解敏捷开发中的Scrum和Kanban方法
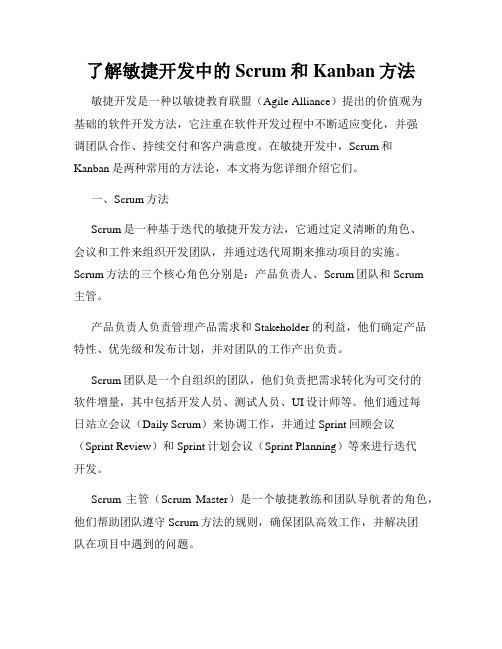
了解敏捷开发中的Scrum和Kanban方法敏捷开发是一种以敏捷教育联盟(Agile Alliance)提出的价值观为基础的软件开发方法,它注重在软件开发过程中不断适应变化,并强调团队合作、持续交付和客户满意度。
在敏捷开发中,Scrum和Kanban是两种常用的方法论,本文将为您详细介绍它们。
一、Scrum方法Scrum是一种基于迭代的敏捷开发方法,它通过定义清晰的角色、会议和工件来组织开发团队,并通过迭代周期来推动项目的实施。
Scrum方法的三个核心角色分别是:产品负责人、Scrum团队和Scrum主管。
产品负责人负责管理产品需求和Stakeholder的利益,他们确定产品特性、优先级和发布计划,并对团队的工作产出负责。
Scrum团队是一个自组织的团队,他们负责把需求转化为可交付的软件增量,其中包括开发人员、测试人员、UI设计师等。
他们通过每日站立会议(Daily Scrum)来协调工作,并通过Sprint回顾会议(Sprint Review)和Sprint计划会议(Sprint Planning)等来进行迭代开发。
Scrum主管(Scrum Master)是一个敏捷教练和团队导航者的角色,他们帮助团队遵守Scrum方法的规则,确保团队高效工作,并解决团队在项目中遇到的问题。
在Scrum中,项目被划分为多个固定长度的迭代周期,称为Sprint。
每个Sprint都有一个明确的目标和计划,团队在Sprint中完成工作,并在Sprint结束时产生一个可交付的软件增量。
二、Kanban方法Kanban是一种基于流程管理的敏捷开发方法,它通过可视化工作流程和限制在制品数量来提高工作效率并控制工作负载。
Kanban方法的核心概念是看板、工作项和工作流程管理。
看板是一个可视化的工作面板,用于显示工作流程、工作项和工作状态。
通常,看板分为待办、进行中和已完成等列,并使用卡片或贴纸来表示每个工作项。
工作项是指需要执行的单个任务或工作,可以是一个用户故事、一个缺陷修复或一个功能开发等。
表上作业法名词解释

表上作业法名词解释
表上作业法(Kanban)是一种管理工具和方法,主要用于优化工作流程和提高生产效率。
它最初由日本汽车制造商丰田开发并应用于其生产线,后来被广泛应用于各个行业和组织。
表上作业法的核心概念是通过可视化工作流程,使团队成员能够清晰地了解任务的状态、进展和优先级。
这通常通过一个表格或面板来实现,其中包含列代表不同的任务状态,行代表不同的任务。
每个任务都被表示为卡片或贴纸,上面包含任务的相关信息,比如任务名称、负责人和截止日期等。
通过使用表上作业法,团队成员可以更好地协作和沟通。
他们可以直观地看到当前任务的状态,避免重复工作和资源浪费。
团队成员可以根据任务的优先级和工作量,自行决定接下来的工作,同时也能够更好地进行任务分配和调整。
此外,表上作业法还强调持续改进和反馈。
团队成员可以定期开会或站会,讨论任务的进展和遇到的问题,以及如何通过调整工作流程来提高效率。
这种持续的反馈和改进可以帮助团队不断优化工作流程,提高工作效率和质量。
总而言之,表上作业法是一种简单而有效的工作管理方法,通过可视化工作流程和任务状态,帮助团队成员更好地协作、沟通和优化工作流程,从而提高生产效率和质量。
它已经在各个行业和组织中得到广泛应用,并被证实是一种有效的管理工具。
看板KANBAN-精益生产的高级工具

看板KANBAN-精益生产的高级工具看板KANBAN是精益工具里较为高端的一个工具,这里的看板不是指工作场地的显示和记录状况的白板,看板在这里是一种触发信号,而且尤其是指拉动方式里的触发信号。
较为复杂,却意义重大。
看板作为拉动的实施工具,作为准时生产JIT的实现方式,起的是个触发的作用。
两箱系统(two-binsystem)是很好的个入门方式。
典型应用于生产区域的小零件(比如螺丝螺帽等)的货架上,这样的小零件的缺货会影响生产区域的装配作业,而如何补货也是个棘手的问题。
两箱系统的做法是,将零件盒中间加一层隔板,前后各放一袋零件,拆前面的一袋开始用,在后面的一袋下方放一块红色的牌子,标有零件号,也就是看板。
当第一袋用完,从后面的第二袋到前方的时候,第二箱底部的红色看板即呈现,则手工将此红牌插在货架上。
因而便于补货人员在定期巡视时可以查看到什么料缺了而需要补货。
执行这个两箱系统的时候,需要对每个料号的零件的体积和最小起订量、以及单位生产使用量进行一定的计算和平衡,也对物料补给员的巡视时间进行相应的匹配(比如是每两小时巡视一次、还是每天一次)。
而这种实物看板也可以由电子看板来替代。
这种典型的看板的应用,是一种触发信号,对于在生产现场的最低库存和保证不断货的顺畅供应间的平衡下的一个补货的触发信号。
也有做法是把这样的小零件的现场货架外包给供应商,供应商每天有人来负责检查巡视缺货状况,并予以补充。
这种两箱系统的看板方法,促成了生产现场的小零件和使用方和补充方的良性互动,从而得以取得不断货和最低库存间的均衡。
对于工序间的WIP在制品、半成品、原材料的搬运中,看板也是有典型的运用。
为配合JIT的准时生产,只生产需要的量,当生产指令从生产线末端朝前方传递,同一条生产线上的内部看板为不增加额外的浪费而可以省略,因同一条生产线在拉动生产中趋向于单件流,所以每个工位只有一件WIP在制品,当完工的在制品被下一工序取走,即触发此工位的生产指令。
项目 看板方法

项目看板方法
看板方法(Kanban)是一种用于项目管理和团队协作的工作流程策略。
它是由丰田汽车公司在20世纪50年代开发的,旨在优化生产流程并降低浪费。
看板方法通过可视化任务流程,让团队成员了解工作进展,发现问题并及时解决。
它的核心思想是限制工作在不同阶段的数量,避免过度负荷和优化流程效率。
基本的看板方法包括:
1. 看板板:使用物理或数字的看板板,将项目任务细分为不同的列,代表不同的工作阶段,如待办、进行中和已完成等。
2. 任务卡片:将每个任务写在一个卡片上,并将其放置在适当的列中,以表示其当前状态。
任务卡片通常包含任务名称、描述、负责人和截止日期等信息。
3. 限制工作在进程的数量:每个列中的任务数量应限制为适当数量,以避免工作过程负荷过重,促进流程的平稳进行。
4. 拉动式工作流:当一个任务完成时,下一个任务才能开始。
这种工作方式有助于减少资源浪费和阻塞。
5. 可视化工作流程:通过实时更新看板板,团队成员可以随时了解工作进展和团队负荷。
6. 持续改进:团队应定期审查看板板,分析瓶颈和延迟,并寻找改进工作流程的机会。
看板方法的优势包括提高团队透明度、增加协作和沟通效率、减少工作阻塞、集中精力解决优先任务以及促进工作流程的持续改进。
总体而言,看板方法是一个简单而有效的项目管理工具,适用于各种团队和项目。
看板管理的概念

看板管理的概念什么是看板管理?看板管理(Kanban)源自于日本工业界,在项目管理中被广泛应用。
它是一种通过可视化工作流程、限制工作在执行过程中的数量和优化工作流程的方法。
看板管理通过在一个可视化的看板上显示任务的状态和进度,使团队能够更好地跟踪和管理工作流程。
看板管理的原则1. 可视化工作流程看板管理的核心理念是通过可视化工作流程来使整个团队了解工作的状态。
通常,一张看板由多个列组成,每个列代表一个阶段或状态。
工作事项以卡片的形式在看板上进行移动,以表示其在工作流程中的进展。
2. 限制工作量看板管理通过限制在执行过程中的任务数量,来促使团队专注于重要的任务。
通过限制任务数量,团队能够集中精力完成当前的工作,而不会过度承载。
这种方法可以提高工作质量,并确保团队能够按时交付。
3. 持续优化看板管理是一种持续改进的方法,团队应该不断寻求改进工作流程的途径。
通过跟踪工作流程中的瓶颈和延迟,团队能够发现问题并修复它们,以提高效率和生产力。
同时,团队还应该鼓励成员提供反馈,以进一步优化工作流程。
看板管理的好处1. 可视化和透明通过看板管理,整个团队都能清楚地看到所有任务的状态和进度。
这种透明度有助于团队成员了解工作优先级和分工,从而更好地协作和协调工作。
2. 提高交付速度看板管理通过限制工作流程中的任务数量,使团队能够集中精力完成当前的任务。
这有助于减少工作的堆积和延误,从而提高交付速度。
3. 识别瓶颈和问题通过看板管理,团队能够快速识别瓶颈和问题,以便及时采取措施解决。
团队可以通过观察卡片在工作流程中的积压情况,识别潜在的瓶颈,并采取相应的措施,以确保工作顺利进行。
4. 提高团队协作通过可视化工作流程和透明度,看板管理能够提高团队的协作和沟通效率。
团队成员能够更好地了解其他成员的工作进展,并更好地协调和合作。
5. 具有灵活性和可调整性看板管理能够灵活地适应不同的项目和工作流程。
团队可以根据具体需求自定义看板的列和卡片,并根据工作情况进行调整。
KANBAN-SYSTEM-看板系统
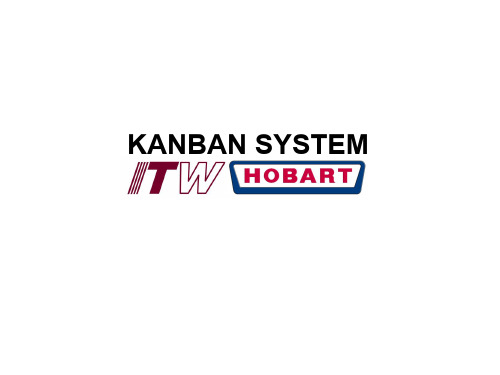
Kanban Card
物料号码: 742301 物料描述: C44B 水箱
KB方式 本卡数量
C KB 1
1
8 10
前序加工
区号: 010 工位: W
后序加工
区号: 030 工位: C2
3/10
Hobart Food Equipment Co.,Ltd
Kanban Card
物料号码: 742312
物料描述: C44B门钩焊件
F KB 1
1
2
3
供应商:
SEW T ianjin FAX:
物料送达
区号: 090 工位: WH
2/3
Hobart Food Equipment Co.,Ltd
Kanban Card
物料号码: 274232-C
物料描述: C44B穿线管
KB方式 本卡数量
C TB 30
供应商:
廊坊裕隆 FAX:
物料送达
两箱定配制:适用于低值物料。以一个 KanBan显示该物料的存储和再订购信息, 第二箱数量为固定数量。
KanBan的形式说明
以卡代料形式,适用于各种形 式的物料
以独特运载车,托盘形式,多 适用于内部加工物料。
以特殊的包装形式,多适用于 外购物料的运输。
供应商物料存储形式,多适用 于80供应商。
KB方式 本卡数量
C TB 50
前序加工
区号: 010 工位: W
后序加工
区号: 030 工位: C2
1/1
Hobart Food Equipment Co.,Ltd
Kanban Card
物料号码: 742321 物料描述: C44B门焊件
看板管理名词解释

看板管理名词解释看板管理是一种透过可视化和简化流程来管理和改进工作流程的方法。
它起源于日本的丰田汽车公司,经过多年的发展和应用,已逐渐被广泛应用于各种行业和组织中。
下面将对与看板管理相关的一些重要名词进行解释。
1. 看板(Kanban)看板是看板管理的核心工具,它是一种信息传递和控制系统,通过卡片、标志或图表等形式,清晰显示工作的状态、进度和需求。
看板提供了一个可视化的方式来跟踪工作、识别和解决问题,并促进团队沟通和协作。
2. 限制存货(Limited WIP)限制存货是看板管理的一个重要原则,它指的是在工作流程中限制同时进行的工作数量,以避免任务积压和资源浪费。
通过限制存货,可以更好地控制工作的负荷和优先级,提高生产效率和交付速度。
3. 工作流(Workflow)工作流是指完成一个任务所需经过的各个步骤和活动。
看板管理将工作流程可视化,使团队成员可以清楚地了解任务的进度和状态,从而更好地协调和分配任务,并及时解决问题。
4. 任务卡片(Task Card)任务卡片是在看板上表示一个任务或工作项的信息单元。
它通常包含任务的名称、描述、执行人、相关信息和状态,用于跟踪任务的进度和状态。
任务卡片可以移动和调整其位置来反映任务的变化和优先级。
5. 上限(Work-In-Progress Limit)上限是指在某个步骤或阶段中同时进行的任务数量的最大限制。
通过设置上限,可以防止任务的积压和资源的过度分散,从而提高任务的处理效率和交付速度。
6. 周期时间(Cycle Time)周期时间是指完成一个任务所需的时间,从任务开始到完成的时间间隔。
通过记录和分析周期时间,可以识别工作流程中的瓶颈和延迟,进而改进工作流程和增加生产效率。
7. 价值流图(Value Stream Map)价值流图是一种绘制工作流程的图表,通过显示任务和信息的流动路径和时间,帮助团队识别和消除浪费和瓶颈。
通过优化价值流,可以减少不必要的工作和等待时间,提高工作效率和交付质量。
kanban看板管理实践精要

kanban看板管理实践精要Kanban看板管理是一种敏捷项目管理和工作流程管理方法,它通过可视化工作流程,帮助团队更好地管理工作、提高效率。
Kanban看板可以用物理形式展示在墙上,也可以通过电子工具实现。
这篇文章将介绍Kanban看板管理的精要,包括原理、核心概念和实践步骤。
一、Kanban看板管理的原理Kanban看板管理起源于日本的产线管理方法,它的原理包括以下几个重要的方面:1.可视化工作流程:Kanban看板通过将工作流程可视化,让团队成员清晰地了解每个任务的状态和进度。
每个任务作为一个卡片,卡片按照任务的不同阶段进行分组,可以看到任务是在哪个阶段,以及每个阶段的工作量。
2.限制在制品数量:Kanban看板通过限制每个阶段的任务数量,避免了任务的过度堆积和工作负荷过大。
只有当前阶段的任务完成,后续的任务才能进入到下一个阶段。
3.优化工作流程:Kanban看板通过持续的改进来优化工作流程。
团队可以根据实际情况,结合反馈和经验,不断调整每个阶段的任务数量、工作流程等细节,以提高工作的效率和质量。
二、Kanban看板管理的核心概念在Kanban看板管理中,有几个核心概念非常重要:1.卡片(Cards):每个任务都以卡片的形式表示,卡片上包含任务名称、描述、负责人等信息。
卡片在不同阶段之间流动,代表任务在各个阶段的进展情况。
2.列(Columns):Kanban看板的每一列代表一个任务的阶段,例如“待办”、“进行中”、“测试”、“已完成”等。
团队成员可以将卡片从一列移到另一列,表示任务的进展。
3.限制在制品数量(WIP Limits):每个列都有一个限制在制品数量,表示该列可以容纳的任务数量。
这个限制的引入可以避免任务过多导致资源的滥用和效率的降低。
4.流动图(Flowchart):Kanban看板可以用流动图的形式展示工作流程,用箭头表示任务的流动路径。
流动图可以帮助团队成员更好地理解工作的流程和关系。
- 1、下载文档前请自行甄别文档内容的完整性,平台不提供额外的编辑、内容补充、找答案等附加服务。
- 2、"仅部分预览"的文档,不可在线预览部分如存在完整性等问题,可反馈申请退款(可完整预览的文档不适用该条件!)。
- 3、如文档侵犯您的权益,请联系客服反馈,我们会尽快为您处理(人工客服工作时间:9:00-18:30)。
QUALITY (质量)
昆山嘉得隆电子有限公司生产每日良率&DPPM 1 2
4
3
15
16
17
18 19
20
21
22
23
24
25 26 27 28 29
30 31
TARGET(目标)
YIELD (良率)
DPPM (百万缺陷
105
10410310210110099989796959493929190898887868584838281807978777675
Month(月份)
WORST(非常差)
BLEW AVE.(差)
MEET(合格
9
10
11
12
1
2
3
4
5
6
7
8
Y I E L D (良率)
昆山嘉得隆电子有限公司生产每月良率&DPPM 统计
%
昆山嘉得隆电子有限
Laird Kunshan
COS
良率&DPPM 统计表YEA
MEET CUSTOMER
5
6
7 8 9 10 11 12 13
14
5
8
9 10
11
12
13
14 15 16 17 18 19 20 21
22
23
24
25
MATERIAL U VARIANCE DL EFFICIEN
Y
40 6.039 5.838 5.637 5.436 5.235 5.034 4.833 4.632 4.431 4.230 4.029 3.828 3.627 3.426 3.225 3.024 2.823 2.622 2.421 2.220 2.019 1.818 1.617 1.416 1.215 1.0140.8130.6120.4110.210
0.0
Month(月份)
GOOD(优秀)
EXCELLENT(非常棒)
CURRENT STATUS(当前状态)
3
DPPM(百万缺陷率)
MONTHLY GOAL(月度目标)
ROOT CAUSE(根本原因)3
1
CORRECTIVE ACTIONS(改善措施)T(合格)
1
2
34567
昆山嘉得隆电子有限公
M A T E R I A L U S A G E V A R I A N C E (材料用量差异)
1
22
良率&DPPM 统计表
%
子有限公司生产材料差异&效率统计
shan Site Workshop Operat
莱尔德昆山工厂车间运营
COST (成本)
YEAR(年份)
1
2
3
4
5
6
7
25
26
27
28
29
30
31 TARGET(目标)
IAL USAGE NCE
CIENCY(员工效率)
每
##105##104##103##
102##
101##100##
99##98##97##96##
95##94##93##92##
91##90##
89##
88##87##
86##859984988397
8296819580947993
78927791
7690
75
1
2
3
)
CURRENT STATUS(当前状态)2
3
MONTHLY GOAL(月度目标)ROOT CAUSE(根本原因)10
11
12
CORRECTIVE ACTIONS(改善措施)1
PERFORMANCE BOARD OWNER
(绩效板责任人)
QUALITY (质量)
BEN FANG
DL EFFICIENCY(员工效率)
1
O T R & O T P (需求准时交付率 & 承诺准时交付率)
78
9
有限公司生产每月材料差异&效率统计
% %
DELIVERY (交货)
昆山嘉得隆电子有限公司生产每日OTR&OTP统计
DATE(日期)
Month(月份)
DELIVERY (交货)
ANG
COST (成本)
ANDY LI
10
11
12
CURRENT STATUS(
2
3
4
5
6
7
8
9
3
2
1
CORRECTIVE ACTION 3
2
1
ROOT CAUSE(根MONTHLY GOAL(月
Board
SAFETY (安全)
5
6
7
8
9
10
4
6 7
8 9
10
11 12
13
14
15
16 17
25
26 27 28
29
30
31 TARGET(目标)
REPORTABLE (可报告事故)
NEAR MISS (险承事件)
ISS
3029282726252423222120191817161514131211109876543210
Month(月份)
10
SCORPION ZHENG
SAFETY (安全)
JANE WANG
CHAMPION(监
1
2
3
4
5
6
7
8
9
昆山嘉得隆电子有限公司生产每月险承事件&可
R E P O R T A B L E (可报告事故)&N E A R M I S S (险承事件)
ATUS(当前状态)
CTIONS(改善措施)
SE(根本原因)
OAL(月度目标)
全)
12
11
1
2
3
4
5
17 18
19
20
21
22
23
24
25
目标)
LY
善措施)
险承事件&可报告事故统计
MONTHLY GOAL(月度目标)
ROOT CAUSE(根本原因)
1
2
3
CORRECTIVE ACTIONS(改善措施)
1
2
3
CURRENT STATUS(当前状态)1112
ON(监督人)LAWRENCE LIU。