变换触媒钝化新方案
变换操作
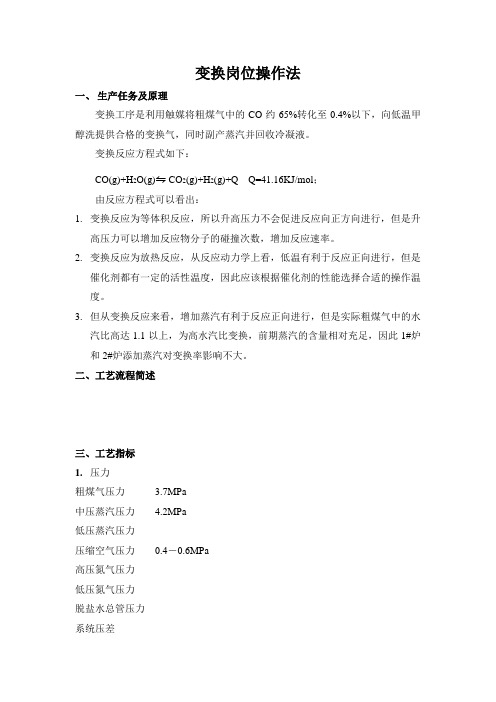
变换岗位操作法一、生产任务及原理变换工序是利用触媒将粗煤气中的CO约65%转化至0.4%以下,向低温甲醇洗提供合格的变换气,同时副产蒸汽并回收冷凝液。
变换反应方程式如下:CO(g)+H2O(g)⇋ CO2(g)+H2(g)+Q Q=41.16KJ/mol;由反应方程式可以看出:1.变换反应为等体积反应,所以升高压力不会促进反应向正方向进行,但是升高压力可以增加反应物分子的碰撞次数,增加反应速率。
2.变换反应为放热反应,从反应动力学上看,低温有利于反应正向进行,但是催化剂都有一定的活性温度,因此应该根据催化剂的性能选择合适的操作温度。
3.但从变换反应来看,增加蒸汽有利于反应正向进行,但是实际粗煤气中的水汽比高达1.1以上,为高水汽比变换,前期蒸汽的含量相对充足,因此1#炉和2#炉添加蒸汽对变换率影响不大。
二、工艺流程简述三、工艺指标1.压力粗煤气压力 3.7MPa中压蒸汽压力 4.2MPa低压蒸汽压力压缩空气压力0.4-0.6MPa高压氮气压力低压氮气压力脱盐水总管压力系统压差2、温度粗煤气温度出工段变换气温度40o C1#变换炉进口温度260±5o C 1#变换炉出口温度380±5o C2#变换炉进口温度240±5o C 2#变换炉出口温度430±5o C3#变换炉进口温度220±5o C 3#变换炉出口温度260±5o C4#变换炉进口温度200±5o C 4#变换炉出口温度200±5o C四、设备五、控制要点1.精心控制变换炉进口温度,注意床层温度变化情况,能够对异常情况作出正确的判断并及时处理;2.细心观察炉温变化,总结规律和影响因素,避免炉温波动过大,损坏催化剂;3.严格控制各工艺指标,保证系统安全、稳定生产;4.生产负荷变化时,做到及时调整,保证炉温稳定和出口达标;5.加强各处导淋排放,控制变换炉进口温度在露点温度30o C以上,防止液体水进入床层,损坏触媒;6.控制各蒸发冷凝器液位、压力正常,稳定各点温度并外送合格蒸汽,同时防止超温或蒸汽倒流现象发生;7.根据前后工段的生产情况,选择合适的调节手段,控制变换系统稳定正常运行;8.沉着冷静,针对突发情况作出正确判断并及时处理;9.遵循一定的路线按时对整个变换系统进行巡检,准确掌握各个设备的使用和运行情况;六、原始开车1、开车前应具备的条件:①各设备、管道安装到位,系统吹扫、清洗干净,气密合格氮气置换合格;②各处盲板抽堵正常;③仪表控制设施安装正确,DCS调试完毕;④安全设施全部到位,安全阀已经校检;⑤相关公用工程具备使用条件;⑥各泵盘车正常备用;⑦变换炉催化剂装填完毕,具备充压条件;2、升温硫化(厂家提供)3、开车①根据变换炉床层温度判断是否需要电炉升温;②检查升温硫化及置换管线上各盲板是否完全关闭,关闭各分离器出口阀门、导淋和放空;③往E-20108上段壳程通入溴化锂冷却水,给V-20101建立一定液位;开启P-20101、P-20102、P-20103,给E-20102、E-20104、E-20105、E-20107、E-20111建立一定液位,用管网蒸汽对各个蒸发冷凝器进行预热;开启P-20107给V-20103建立一定液位;利用脱盐水给S-20102和E-20108下段建立一定液位后,开启P-20104、P-20105往E-20103壳程通入冷却水;E-20109壳程通入循环冷却水;开启P-20101给E-20106通入冷却水;利用管网蒸汽对各个蒸汽添加管线暖管(打开导淋);④缓慢打开界区阀XV1001的旁路均压阀,对系统前后进行均压;⑤均压结束后,打开XV1001界区阀,调节PV201018开度,控制系统压力,对变换炉床层进行升温,同事注意排放各处冷凝液,调节蒸汽用量,严格控制升温速率,防止超温飞温现象发生;(接气后给S-20104通入脱盐水,同时往C-20101通入气提蒸汽)⑥根据工艺指标调节个参数,待出口变换气分析合格后想后工段送气,并关闭PV201018;七、开停车1.长期停车①通知调度变换长期停车,请相关工段做好相应的处理;②根据气量的减少,逐渐减少蒸汽和水的添加量直到完全切断蒸汽和水;③依次停下P-20104、P-20105、P-20103、P-20102、P-20101、P-20106、P-20107、P-20108八台泵并排净泵内的液体;同时关闭蒸发冷凝器的压力控制阀PV1034、PV1035、PV1036、PV1037、PV1020,排净蒸发冷凝器内的水,关闭各自的液位调节阀;④关闭粗煤气界区阀XV1001;⑤关闭变换气去低温甲醇洗界区阀HV1001;⑥将系统卸至常压,然后用干煤气或者惰性气体(N2)保压;2. 短期停车①停车前4小时适当的提高各变换炉的温度;②通知调度变换停车,请相关工段做好相应的处理;③根据气量的减少逐步减少蒸汽和水的添加量直至切断蒸汽和水的添加;④依次停下P-20104、P-20105、P-20103、P-20102、P-20101、P-20106、P-20107、P-20108八台泵;同时关闭蒸发冷凝器的压力控制阀PV1034、PV1035、PV1036、PV1037、PV1020,根据蒸发冷凝器内的液位,关闭各自的液位调节阀;⑤关闭粗煤气界区阀XV1001;⑥关闭变换气去低温甲醇洗界区阀HV1001;⑦整个系统做保温保压处理;⑧注意排净各蒸汽以及工艺气管线上各处的导淋。
1_直转甲烷化触媒升温还原方案
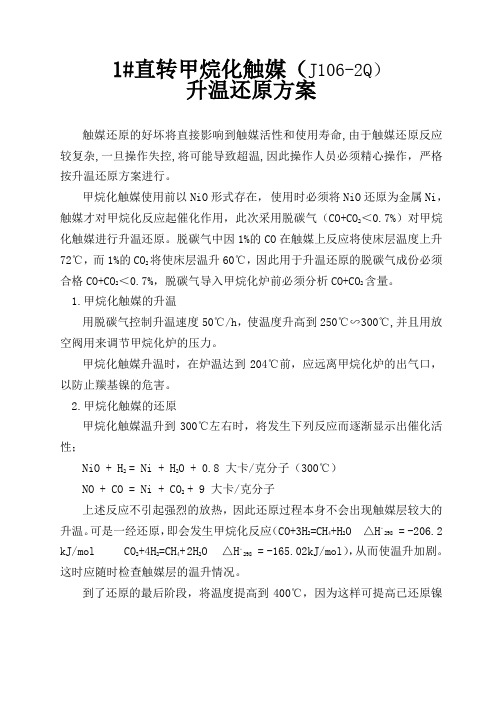
1#直转甲烷化触媒(J106-2Q)升温还原方案触媒还原的好坏将直接影响到触媒活性和使用寿命,由于触媒还原反应较复杂,一旦操作失控,将可能导致超温,因此操作人员必须精心操作,严格按升温还原方案进行。
甲烷化触媒使用前以NiO形式存在,使用时必须将NiO还原为金属Ni,触媒才对甲烷化反应起催化作用,此次采用脱碳气(CO+CO2<0.7%)对甲烷化触媒进行升温还原。
脱碳气中因1%的CO在触媒上反应将使床层温度上升72℃,而1%的CO2将使床层温升60℃,因此用于升温还原的脱碳气成份必须合格CO+CO2<0.7%,脱碳气导入甲烷化炉前必须分析CO+CO2含量。
1.甲烷化触媒的升温用脱碳气控制升温速度50℃/h,使温度升高到250℃∽300℃,并且用放空阀用来调节甲烷化炉的压力。
甲烷化触媒升温时,在炉温达到204℃前,应远离甲烷化炉的出气口,以防止羰基镍的危害。
2.甲烷化触媒的还原甲烷化触媒温升到300℃左右时,将发生下列反应而逐渐显示出催化活性;NiO + H2 = Ni + H2O + 0.8 大卡/克分子(300℃)NO + CO = Ni + CO2 + 9 大卡/克分子上述反应不引起强烈的放热,因此还原过程本身不会出现触媒层较大的升温。
可是一经还原,即会发生甲烷化反应(CO+3H2=CH4+H2O △H。
298 = -206.2 kJ/mol CO2+4H2=CH4+2H2O△H。
298 = -165.02kJ/mol),从而使温升加剧。
这时应随时检查触媒层的温升情况。
到了还原的最后阶段,将温度提高到400℃,因为这样可提高已还原镍的比率。
已还原的触媒不得漏入空气,否则有迅速燃烧而失活的危险。
甲烷化触媒升温还原进度表3.升温还原操作注意事项(1)当温度至204℃以前时,要防止羰基镍的危害。
(2)温度由430℃回复到300℃时,在CO+CO2<20PPM即可投入正式运行。
(3)当甲烷化炉出现超温现象,应及时切断气源,用蒸汽降温。
触媒还原操作规程
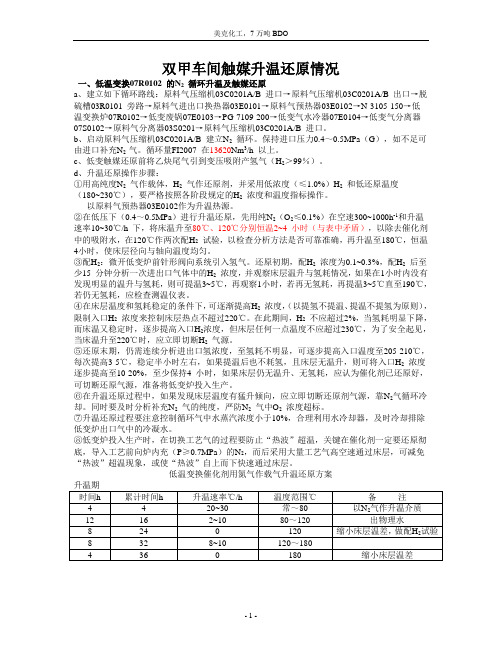
双甲车间触媒升温还原情况一、低温变换07R0102 的N2循环升温及触媒还原a、建立如下循环路线:原料气压缩机03C0201A/B 进口→原料气压缩机03C0201A/B 出口→脱硫槽03R0101 旁路→原料气进出口换热器03E0101→原料气预热器03E0102→N-3105-150→低温变换炉07R0102→低变废锅07E0103→PG-7109-200→低变气水冷器07E0104→低变气分离器07S0102→原料气分离器03S0201→原料气压缩机03C0201A/B 进口。
b、启动原料气压缩机03C0201A/B 建立N2循环。
保持进口压力0.4~0.5MPa(G),如不足可由进口补充N2 气。
循环量FI2007 在13620Nm3/h 以上。
c、低变触媒还原前将乙炔尾气引到变压吸附产氢气(H2>99%)。
d、升温还原操作步骤:①用高纯度N2气作载体,H2气作还原剂,并采用低浓度(≤1.0%)H2和低还原温度(180~230℃),要严格按照各阶段规定的H2浓度和温度指标操作。
以原料气预热器03E0102作为升温热源。
②在低压下(0.4~0.5MPa)进行升温还原,先用纯N2(O2≤0.1%)在空速300~1000h-1和升温速率10~30℃/h 下,将床温升至80℃、120℃分别恒温2~4 小时(与表中矛盾),以除去催化剂中的吸附水,在120℃作两次配H2试验,以检查分析方法是否可靠准确,再升温至180℃,恒温4小时,使床层径向与轴向温度均匀。
③配H2:微开低变炉前针形阀向系统引入氢气。
还原初期,配H2浓度为0.1~0.3%,配H2后至少15 分钟分析一次进出口气体中的H2浓度,并观察床层温升与氢耗情况,如果在1小时内没有发现明显的温升与氢耗,则可提温3~5℃,再观察1小时,若再无氢耗,再提温3~5℃直至190℃,若仍无氢耗,应检查测温仪表。
④在床层温度和氢耗稳定的条件下,可逐渐提高H2浓度,(以提氢不提温、提温不提氢为原则),限制入口H2浓度来控制床层热点不超过220℃。
转化系统停车及催化剂钝化程序
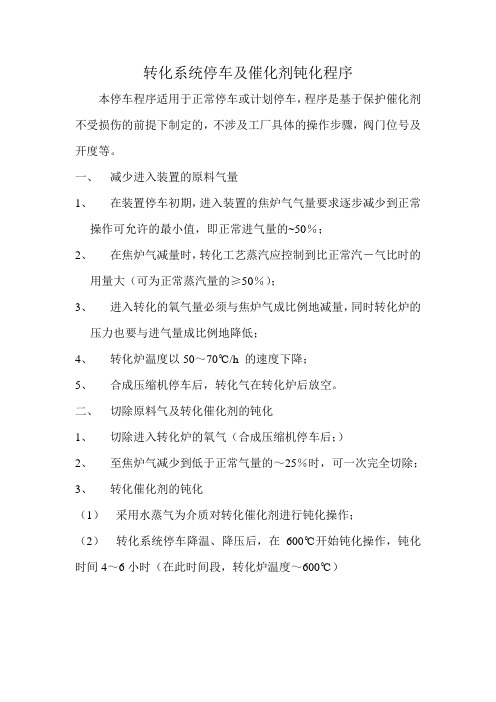
转化系统停车及催化剂钝化程序
本停车程序适用于正常停车或计划停车,程序是基于保护催化剂不受损伤的前提下制定的,不涉及工厂具体的操作步骤,阀门位号及开度等。
一、减少进入装置的原料气量
1、在装置停车初期,进入装置的焦炉气气量要求逐步减少到正常
操作可允许的最小值,即正常进气量的~50%;
2、在焦炉气减量时,转化工艺蒸汽应控制到比正常汽-气比时的
用量大(可为正常蒸汽量的≥50%);
3、进入转化的氧气量必须与焦炉气成比例地减量,同时转化炉的
压力也要与进气量成比例地降低;
4、转化炉温度以50~70℃/h 的速度下降;
5、合成压缩机停车后,转化气在转化炉后放空。
二、切除原料气及转化催化剂的钝化
1、切除进入转化炉的氧气(合成压缩机停车后;)
2、至焦炉气减少到低于正常气量的~25%时,可一次完全切除;
3、转化催化剂的钝化
(1)采用水蒸气为介质对转化催化剂进行钝化操作;
(2)转化系统停车降温、降压后,在600℃开始钝化操作,钝化时间4~6小时(在此时间段,转化炉温度~600℃)
4、转化催化剂钝化要点
(1)当转化出口水蒸气中基本不含不凝性气体时,可认为钝化操作已结束;
(2)钝化过程应密切关注转化炉的床层温度变化;
(3)由于转化炉直径较大,气流沿整个转化炉截面分布不易均匀,(超温、混合器运转异常等现象即为转化炉气流分布不均匀的表现特征)需根据钝化时床层温度的变化调整钝化时间;
(4)“钝化”完成后可用N2或空气吹除系统中的水蒸气,并进一步降温;若采用空气置换降温,应在~200℃,逐渐缓慢加空气,严格观察温升情况,防止超温事故发生。
(5)“钝化”完成后,转化催化剂在温度降到常温后才可暴露在空气里。
干法脱硫转化问答
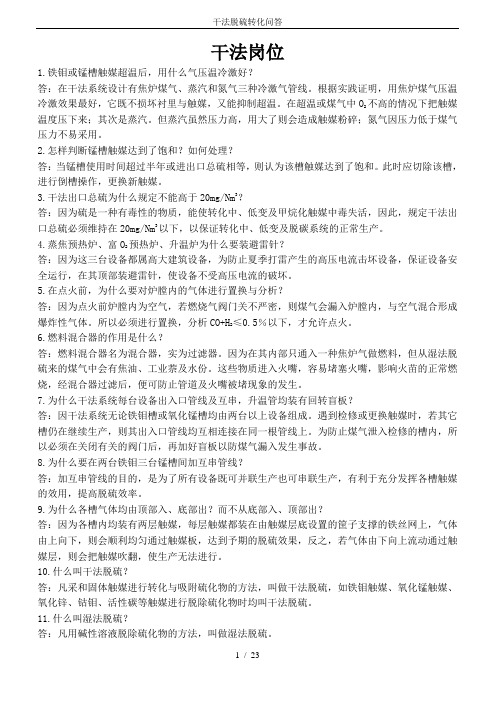
干法岗位1.铁钼或锰槽触媒超温后,用什么气压温冷激好?答:在干法系统设计有焦炉煤气、蒸汽和氮气三种冷激气管线。
根据实践证明,用焦炉煤气压温不高的情况下把触媒冷激效果最好,它既不损坏衬里与触媒,又能抑制超温。
在超温或煤气中O2温度压下来;其次是蒸汽。
但蒸汽虽然压力高,用大了则会造成触媒粉碎;氮气因压力低于煤气压力不易采用。
2.怎样判断锰槽触媒达到了饱和?如何处理?答:当锰槽使用时间超过半年或进出口总硫相等,则认为该槽触媒达到了饱和。
此时应切除该槽,进行倒槽操作,更换新触媒。
3.干法出口总硫为什么规定不能高于20mg/Nm3?答:因为硫是一种有毒性的物质,能使转化中、低变及甲烷化触媒中毒失活,因此,规定干法出口总硫必须维持在20mg/Nm3以下,以保证转化中、低变及脱碳系统的正常生产。
预热炉、升温炉为什么要装避雷针?4.蒸焦预热炉、富O2答:因为这三台设备都属高大建筑设备,为防止夏季打雷产生的高压电流击坏设备,保证设备安全运行,在其顶部装避雷针,使设备不受高压电流的破坏。
5.在点火前,为什么要对炉膛内的气体进行置换与分析?答:因为点火前炉膛内为空气,若燃烧气阀门关不严密,则煤气会漏入炉膛内,与空气混合形成≤0.5%以下,才允许点火。
爆炸性气体。
所以必须进行置换,分析CO+H26.燃料混合器的作用是什么?答:燃料混合器名为混合器,实为过滤器。
因为在其内部只通入一种焦炉气做燃料,但从湿法脱硫来的煤气中会有焦油、工业萘及水份。
这些物质进入火嘴,容易堵塞火嘴,影响火苗的正常燃烧,经混合器过滤后,便可防止管道及火嘴被堵现象的发生。
7.为什么干法系统每台设备出入口管线及互串,升温管均装有回转盲板?答:因干法系统无论铁钼槽或氧化锰槽均由两台以上设备组成。
遇到检修或更换触媒时,若其它槽仍在继续生产,则其出入口管线均互相连接在同一根管线上。
为防止煤气泄入检修的槽内,所以必须在关闭有关的阀门后,再加好盲板以防煤气漏入发生事故。
中温变换催化剂的升温还原原操作说明
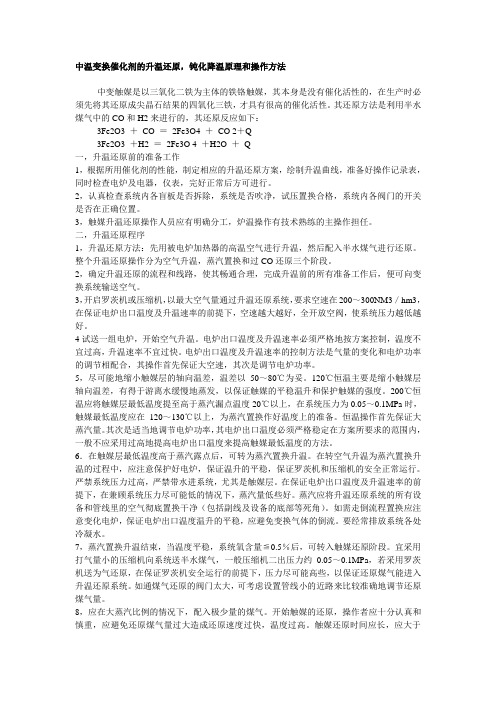
中温变换催化剂的升温还原,钝化降温原理和操作方法中变触媒是以三氧化二铁为主体的铁铬触媒,其本身是没有催化活性的,在生产时必须先将其还原成尖晶石结果的四氧化三铁,才具有很高的催化活性。
其还原方法是利用半水煤气中的CO和H2来进行的,其还原反应如下:3Fe2O3 +CO =2Fe3O4 +CO 2+Q3Fe2O3 +H2 =2Fe3O 4 +H2O +Q一,升温还原前的准备工作1,根据所用催化剂的性能,制定相应的升温还原方案,绘制升温曲线,准备好操作记录表,同时检查电炉及电器,仪表,完好正常后方可进行。
2,认真检查系统内各盲板是否拆除,系统是否吹净,试压置换合格,系统内各阀门的开关是否在正确位置。
3,触媒升温还原操作人员应有明确分工,炉温操作有技术熟练的主操作担任。
二,升温还原程序1,升温还原方法:先用被电炉加热器的高温空气进行升温,然后配入半水煤气进行还原。
整个升温还原操作分为空气升温,蒸汽置换和过CO还原三个阶段。
2,确定升温还原的流程和线路,使其畅通合理,完成升温前的所有准备工作后,便可向变换系统输送空气。
3,开启罗茨机或压缩机,以最大空气量通过升温还原系统,要求空速在200~300NM3/hm3,在保证电炉出口温度及升温速率的前提下,空速越大越好,全开放空阀,使系统压力越低越好。
4试送一组电炉,开始空气升温。
电炉出口温度及升温速率必须严格地按方案控制,温度不宜过高,升温速率不宜过快。
电炉出口温度及升温速率的控制方法是气量的变化和电炉功率的调节相配合,其操作首先保证大空速,其次是调节电炉功率。
5,尽可能地缩小触媒层的轴向温差,温差以50~80℃为妥。
120℃恒温主要是缩小触媒层轴向温差,有得于游离水缓慢地蒸发,以保证触媒的平稳温升和保护触媒的强度。
200℃恒温应将触媒层最低温度提至高于蒸汽漏点温度20℃以上,在系统压力为0.05~0.1MPa时,触媒最低温度应在120~130℃以上,为蒸汽置换作好温度上的准备。
触媒钝化方案

催化剂的钝化1 钝化机理由于硫化态的催化剂在卸出变换炉后,很快会与空气中的氧气反应并放出大量的热量,这样会造成催化剂烧坏并使扒卸工作困难,故硫化态的催化剂在卸出之前需要进行钝化:使硫化态的催化剂依次和水蒸汽、空气在控制下缓慢反应以使其成为氧化态。
CoS+H2O→CoO+H2S ⊿H=+13.5 KJ/molMoS2+3H2O→MoO3+2H2S+H2⊿H=+48.3 KJ/mol2MoS2+7O2→2MoO3+4SO2-Q2CoS+3O2→2CoO+2SO2-Q由于硫化态的催化剂与氧气反应会放出大量的热量而使反应难以控制,故使其先和水蒸汽反应(吸热),以使大多数催化剂变为氧化态,然后剩余的催化剂再和空气反应(放热)便可在催化剂床层温度可控的条件下缓慢全部氧化。
2除硫钝化前的工作:(1)首先按短期停车方案将变换系统处理完成后,用0.4Mpa氮气进行系统置换,T2001出口取样分析CO+H2<0.5%为合格。
(2)系统由PV2005泄压至0.2MPa左右保压。
(3)将需要钝化的变换炉隔离。
3 催化剂的除硫和降温:(1)拆除升温流程各阀上的盲板,循环系统充氮至0.4MPag开C2001系统氮气循环,启动电加热炉F2001。
(2)打通入升温系统的低压蒸汽,处于备用状态。
(3)待加热炉F2301出口温度接近催化剂床层温度时,配入0.5Mpag、 158ºC 的低压蒸汽进行除硫,将PV2005设定0.4MPa保压放空。
(4)除硫过程中因反应床温出现下降可减小蒸汽量通过调节电加热炉F2001出口温度维持床温的稳定。
(5)分析循环气中H2S含量小于80ppm为除硫结束。
3氧化(钝化):(1)除硫结束后,可停止向氮气循环系统加蒸汽。
当电加热炉F2001出口气温度降至150℃时停F2001。
由F2001出口处工厂空气线向循环气中加入空气进行钝化反应。
床层温度控制在270℃以内,逐量提高氧气浓度(即加大空气量)使催化剂逐渐钝化。
变换岗位操作规程
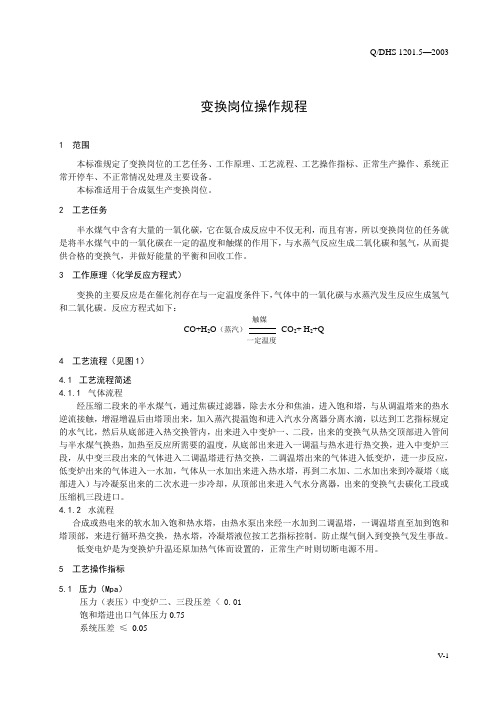
变换岗位操作规程1 范围本标准规定了变换岗位的工艺任务、工作原理、工艺流程、工艺操作指标、正常生产操作、系统正常开停车、不正常情况处理及主要设备。
本标准适用于合成氨生产变换岗位。
2 工艺任务半水煤气中含有大量的一氧化碳,它在氨合成反应中不仅无利,而且有害,所以变换岗位的任务就是将半水煤气中的一氧化碳在一定的温度和触煤的作用下,与水蒸气反应生成二氧化碳和氢气,从而提供合格的变换气,并做好能量的平衡和回收工作。
3 工作原理(化学反应方程式)变换的主要反应是在催化剂存在与一定温度条件下,气体中的一氧化碳与水蒸汽发生反应生成氢气和二氧化碳。
反应方程式如下:触媒CO+H2O(蒸汽)CO2+ H2+Q一定温度4 工艺流程(见图1)4.1 工艺流程简述4.1.1 气体流程经压缩二段来的半水煤气,通过焦碳过滤器,除去水分和焦油,进入饱和塔,与从调温塔来的热水逆流接触,增湿增温后由塔顶出来,加入蒸汽提温饱和进入汽水分离器分离水滴,以达到工艺指标规定的水气比,然后从底部进入热交换管内,出来进入中变炉一、二段,出来的变换气从热交顶部进入管间与半水煤气换热,加热至反应所需要的温度,从底部出来进入一调温与热水进行热交换,进入中变炉三段,从中变三段出来的气体进入二调温塔进行热交换,二调温塔出来的气体进入低变炉,进一步反应,低变炉出来的气体进入一水加,气体从一水加出来进入热水塔,再到二水加、二水加出来到冷凝塔(底部进入)与冷凝泵出来的二次水进一步冷却,从顶部出来进入气水分离器,出来的变换气去碳化工段或压缩机三段进口。
4.1.2 水流程合成或热电来的软水加入饱和热水塔,由热水泵出来经一水加到二调温塔,一调温塔直至加到饱和塔顶部,来进行循环热交换,热水塔,冷凝塔液位按工艺指标控制。
防止煤气倒入到变换气发生事故。
低变电炉是为变换炉升温还原加热气体而设置的,正常生产时则切断电源不用。
5 工艺操作指标5.1 压力(Mpa)压力(表压)中变炉二、三段压差< 0.01饱和塔进出口气体压力0.75系统压差≤0.05蒸汽压力≥ 0.85补气软水压力> 0.80热水泵出口压力> 饱和塔进口气体压力0.25.2 温度(℃)饱和塔出口气体温度> 125变换炉一段进口温度> 375冷凝塔出口气体温度< 35变换炉触煤层温度:一段480±10(视触媒活性情况而定)活性温度波动范围≤±10中变二段出口温度< 4505.3 成份半水煤气中O2含量≤ 0.5%合格> 0.8%减量> 1.2%切气变换气中CO含量:中变气:8%—13%一低变气:4%—6%二低变气:≤ 1.0%循环热水中总固体含量:≤ 500mg/l5.4 液位(液位计高度)热水塔液位1/2~2/3冷凝塔液位1/2~2/3水封液位> 2/35.5 电机:电流及温升按铭牌规定值6 正常生产操作6.1 触煤层温度的控制触煤层温度要控制在活性温度之内,温度波动范围为±10℃,触煤温度主要根据触煤层某一最灵敏的温度的变化情况进行调整,使其在活性温度范围内。
变换工艺原理

变换工艺原理变换工艺原理粗煤气变换装置是将粗煤气中的CO与水蒸汽反应生成氢气和二氧化碳,以满足合成气对甲烷合成要求H2/CO=3.1-3.3,同时回收变换反应热量,最后将煤气冷却送入低温甲醇洗装置其化学方程式为:H2O + CO CO2 + H2 +23.4MJ/Kmol反应的特点是一个可逆的气固相催化反应,正反应为放热反应,反应前后气体体积不变,反应热效值随温度增高而缓慢降低。
煤气中除含有CO以外,还含有CO2、H2、H2O、N2、CH4、有机硫等气体。
在一定工艺条件下,可能发生下列反应:2CO=C+CO2 CO+2H2=CH3OHCO+3H2=CH4+H2O 3H2+N2=2NH3为什么要硫化,主要反应方程式?钴钼耐硫催化剂的常态为氧化态,不具有高活性,使用前必须先进行硫化,使其呈硫化态,才具有高活性。
钴钼催化剂的硫化工业上常采用CS2作硫化机,硫化反应方程式:CS2+4H2 = 2H2S+CH4MoO3+2H2S +H2= MoS2+H2OGoO+H2S = GoS+H2O正常生产中,在一定反应温度和水汽比范围内,当H2S浓度低于平衡所需的最低H2S浓度时,会出现反硫化而使催化剂失活,反应方程式:MoS2+2H2O = MoO2+H2S在预变换炉中装填除氧剂的目的进变换系统的粗煤气中含有0.39%(V)的O2,这些少量的氧气将会与变换反应催化剂的活性组分或载体发生硫酸盐化反应,使催化剂迅速失活。
装填除氧剂后有效地脱除原料气中的氧等毒物,保护催化剂,延长催化剂的使用寿命。
除氧剂:1.9m3/台,总量7.6m3,使用位置是预变炉上层。
催化剂:预变炉 6.4m3/台,主变换炉27.9m3/台,总量是81.4m3。
使用位置是预变炉下层,主变炉。
换热器:在开停车时要注意换热器管/壳层的压差,防止出现高于0.5MPa。
防止损坏换热器。
变换炉:开车前,首先将变换炉床层以50℃/h的速率升温到260℃-280℃,并且向变换炉导气时要缓慢。
甲醇钝化下载知识
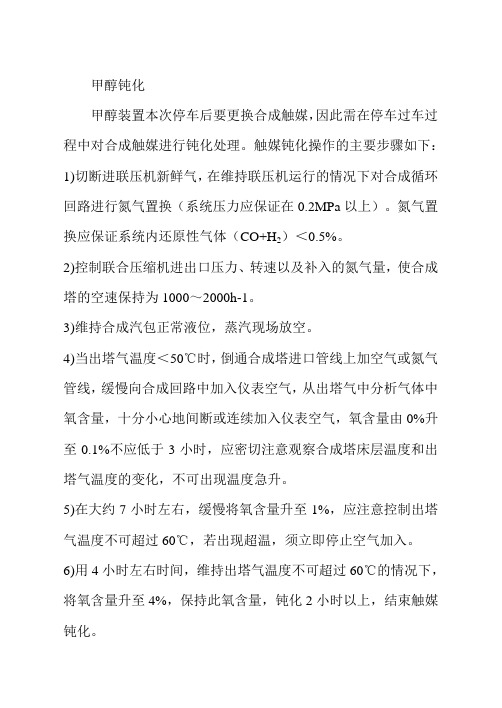
甲醇钝化甲醇装置本次停车后要更换合成触媒,因此需在停车过车过程中对合成触媒进行钝化处理。
触媒钝化操作的主要步骤如下:1)切断进联压机新鲜气,在维持联压机运行的情况下对合成循环回路进行氮气置换(系统压力应保证在0.2MPa以上)。
氮气置换应保证系统内还原性气体(CO+H2)<0.5%。
2)控制联合压缩机进出口压力、转速以及补入的氮气量,使合成塔的空速保持为1000~2000h-1。
3)维持合成汽包正常液位,蒸汽现场放空。
4)当出塔气温度<50℃时,倒通合成塔进口管线上加空气或氮气管线,缓慢向合成回路中加入仪表空气,从出塔气中分析气体中氧含量,十分小心地间断或连续加入仪表空气,氧含量由0%升至0.1%不应低于3小时,应密切注意观察合成塔床层温度和出塔气温度的变化,不可出现温度急升。
5)在大约7小时左右,缓慢将氧含量升至1%,应注意控制出塔气温度不可超过60℃,若出现超温,须立即停止空气加入。
6)用4小时左右时间,维持出塔气温度不可超过60℃的情况下,将氧含量升至4%,保持此氧含量,钝化2小时以上,结束触媒钝化。
7)最后用3~4小时,边放空边进仪表空气,将系统全部置换为仪表空气,并维持循环,直至床层温度降至常温。
9)停联合压缩机,关闭甲醇水冷器进出口循环水阀门,由甲醇分离器出口专门的钝化放空管将系统泄至常压。
10)有关注意事项:A.由于有空气的介入,整个钝化过程中,特别是泄压时气体均不能排至火炬,应由位于甲醇分离器出口管线上的专用放空管现场放空,以防止可能发生爆炸事故。
B.钝化过程中,如合成塔出塔气温度超过60℃,应立即停止加入仪表空气,若仍不能降温,则应将系统卸至微正压,连续充入氮气置换。
甲醇钝化下载知识。
QDB-04宽温变换催化剂

Co-Mo系耐硫变换催化剂介绍简介1.1Co-Mo系变换催化剂的发展历程Co-Mo系催化剂最早是在炼油行业中使用,属炼油行业加氢催化剂。
国内最早研究开发此催化剂用于变换工艺的有三家:上海化工研究院、湖北化工研究所、齐鲁石化研究院。
上世纪八十年代初上海化工研究院研制出了Co-Mo系变换催化剂,化工部命名的牌号是B301。
该催化剂系混捏法生产,外观为圆柱形,生产工艺复杂,成本较高。
但该催化剂开创了国内Co-Mo系耐硫变换催化剂的先河,在当时为中、小氮肥的节能降耗做出了很大贡献。
八十年代后期,湖北所吸收了丹麦技术研制出了B302Q.B303Q,在国内首先采用了r-Al2O3球形载体,首先采用了无焙烧工艺即浸泽工艺,制造工艺大为简化,生产成本进一步降低,从而推动了Co-Mo系变换催化剂的迅速发展。
九十年代中期,齐鲁院开发出了中石化命名的Qcs-01、Qcs-02、Qcs-03,在国内首先采用了钛复合载体,使Co-Mo 系耐硫变换催化剂的稳定性、活性助剂、硫化性能大为改进。
目前国内生产该催化剂的厂家已发展有十多家。
1.2我公司采用的Co-Mo系变换催化剂我公司采用的Co-Mo系耐硫变换催化剂型号为K8-11和QDB-04,K8-11为德国巴斯夫公司生产,采用混捏法制备工艺,以MgO、AL2O3、SiO2为复合载体。
在CO含量高、汽/气比低、压力高、床层温度高的情况下,抑制CH4化副反应方面性能更优越。
QDB-04为青岛联信化学有限公司生产,在齐鲁院技术的基础上有所发展,以镁铝尖晶石为载体,含有多元复合助剂,在高温低硫的条件下使用时,与同类催化剂相比,更能显示其优越的催化性能。
两种催化剂性能相近均为新型耐硫变换催化剂,均含有特殊载体,都有良好的低温、宽温、宽硫特性,都有较强抗毒性能,较高的选择性。
下面就以QDB-04为例对Co-Mo系耐硫变换催化剂做详细介绍。
2.Co-Mo系耐硫变换催化剂QDB-04的物理性能表1QDB-04的物理性能项目物理性能CoO%MoO3%外形尺寸mm堆密度Kg/L1.8±0.2 8±1.0φ3.5-4.5 0.8-1.0≧130破碎强度N/cm比表面积m2/g 孔容cm3/g颜色磨损率%钾流失率%≧100≧0.25红色或绿色≦2.0≦1.0(正常使用1年)3.Co-Mo系耐硫变换催化剂QDB-04的主要使用条件表2QDB-04的主要使用条件项目使用条件压力MPa温度℃最佳使用温度℃起活温度℃初期最佳入口温度℃耐热温度℃~5.0 190-500 240-450180高于露点205502-4 1000-4500耐热时间h干气空速h-1最佳装填高径比汽气比0.8-1.5~1.44.Co-Mo系耐硫变换催化剂QDB-04的突出优点4.1添加特殊助剂并使用活性载体,由于助剂、活性载体与活性组分三者的协同效应,提高了催化剂的变换活性,特别是提高了催化剂在高温低硫下的变换活性及稳定性。
中变催化剂钝化方案

中变催化剂钝化方案
中变催化剂的钝化温度和使用活性温度有密切关系,也就是说还原态的催化剂使用活性温度低,那么钝化温度也要低,如B113型催化剂在250℃就有很好的活性,钝化温度控制在250~350℃。
中变催化剂钝化温度比较好控制,但由于使用了一段时间后避免不了床层结块及偏流等因素,不容易彻底钝化,中变催化剂按下面过程进行,钝化过程中可能有放硫现象,不可避免造成局部环境污染。
1、系统停车后,用过热蒸汽或氮气进行吹扫,在吹扫过程中使床层温度达到钝化指标250~350℃,出口CO+H2<0.5%以下。
2、在载体气中配入空气,初始氧含量控制在0.2~0.5%,严格控制温度在钝化温度范围。
3、随着钝化过程的进行,在此氧含量下,温度有所下降,逐渐增加氧含量,当氧含量达到3%时,如温度有所下降,逐步减少载体气量,增加空气量,当系统全部切换为空气时,床层温度不再上涨,视为钝化以结束,将床层温度降到60℃左右,等待催化剂的卸出。
钝化过程严格控制,不能超温,避免烧坏催化剂和设备损坏。
催化剂钝化进度表。
3精脱硫岗位操作问答
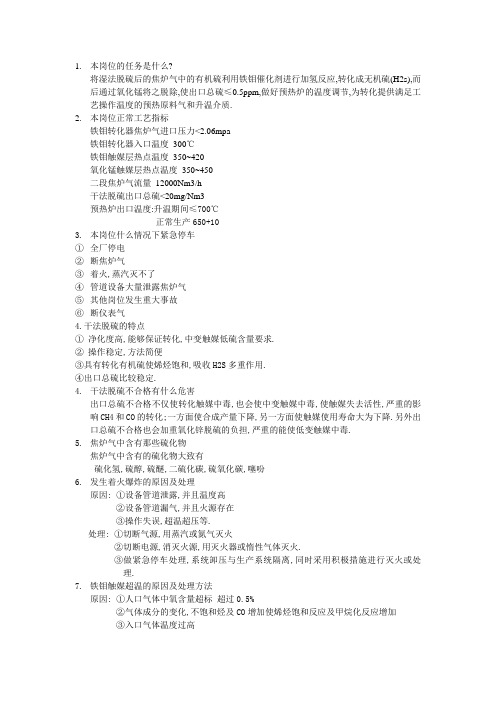
1.本岗位的任务是什么?将湿法脱硫后的焦炉气中的有机硫利用铁钼催化剂进行加氢反应,转化成无机硫(H2s),而后通过氧化锰将之脱除,使出口总硫≤0.5ppm,做好预热炉的温度调节,为转化提供满足工艺操作温度的预热原料气和升温介质.2.本岗位正常工艺指标铁钼转化器焦炉气进口压力<2.06mpa铁钼转化器入口温度300℃铁钼触媒层热点温度350~420氧化锰触媒层热点温度350~450二段焦炉气流量12000Nm3/h干法脱硫出口总硫<20mg/Nm3预热炉出口温度:升温期间≤700℃正常生产650+103.本岗位什么情况下紧急停车①全厂停电②断焦炉气③着火,蒸汽灭不了④管道设备大量泄露焦炉气⑤其他岗位发生重大事故⑥断仪表气4.干法脱硫的特点①净化度高,能够保证转化,中变触媒低硫含量要求.②操作稳定,方法简便③具有转化有机硫使烯烃饱和,吸收H2S多重作用.④出口总硫比较稳定.4.干法脱硫不合格有什么危害出口总硫不合格不仅使转化触媒中毒,也会使中变触媒中毒,使触媒失去活性,严重的影响CH4和CO的转化;一方面使合成产量下降,另一方面使触媒使用寿命大为下降.另外出口总硫不合格也会加重氧化锌脱硫的负担,严重的能使低变触媒中毒.5.焦炉气中含有那些硫化物焦炉气中含有的硫化物大致有硫化氢,硫醇,硫醚,二硫化碳,硫氧化碳,噻吩6.发生着火爆炸的原因及处理原因: ①设备管道泄露,并且温度高②设备管道漏气,并且火源存在③操作失误,超温超压等.处理: ①切断气源,用蒸汽或氮气灭火②切断电源,消灭火源,用灭火器或惰性气体灭火.③做紧急停车处理,系统卸压与生产系统隔离,同时采用积极措施进行灭火或处理.7.铁钼触媒超温的原因及处理方法原因: ①人口气体中氧含量超标超过0.5%②气体成分的变化,不饱和烃及CO增加使烯烃饱和反应及甲烷化反应增加③入口气体温度过高处理: ①联系调度,把气体中氧降为0.5%以下,同时打开铁钼冷激气,用焦炉气,氮气或蒸汽进行压温,必要时减量生产或停车.②开预热器付线或加冷激降低入口温度8.本岗位巡回检查内容①检查本岗位所有设备,管道,阀门的运行泄露,阻力及异常情况.②排放油分离器,燃料混合器,燃烧气管线,焦炉气管线的冷凝水③检查升温炉,预热炉的燃烧情况9.原料焦炉气中含有的成分氢气甲烷一氧化碳二氧化碳氧气烃类硫化物10.铁钼触媒反应原理是什么铁钼转化器主要是将有机硫加氢转化为H2S并使烯烃加氢饱和反应如下11.铁钼触媒使用一段时间后为什么要再生.铁钼触媒再生的主要原因是恢复触媒的活性.正常生产中在铁钼触媒中会发生副反应.CS2+2H2=2H2S+C C2H4=CH4+C 2CO=CO2+C 另外一些有机杂质如焦油,萘等也能附载在催化剂表面,使触媒活性下降,所以使用一段时间后必须再生,才能使触媒活性增加.12.干法出口总硫高是什么原因造成的,应如何处理原因:①干法触媒床层温度低②触媒硫容饱和③负荷过大④气体成分不符合工艺要求,铁钼触媒中毒⑤湿法脱硫出口H2S控制的太高处理:①关干法各冷激,关预热器付线阀,提高干法触媒床层温度②分析触媒硫容饱和后,开启备用槽,将原槽切除生产系统进行降温钝化后,更换新触媒.③减负荷生产④联系调度使气体成分符合工艺条件,同时适当提高床层温度⑤联系调度让湿法脱硫将H2S降至200mg/Nm3以下.13.干法床层温度低,原因是什么①入铁钼温度低预热器管内转化气温度太低,而导致管外焦炉气温度也低②气量小,空速低③冷激阀内漏或冷激气加得太多④焦炉气成分有问题,如氧含量太低,含有机硫及烯烃太少⑤油水分离器没及时排放,至使焦炉气带水,油等14.干法各槽超温会有什么危害触媒超温回烧坏触媒,使触媒丧失活性,甚至永久失活,严重时结块不好卸出.另外超温太高,设备管道阀门因超过钢材使用温度而损坏,触媒超温不仅破坏了生产工艺条件,而且也严重地影响生产正常进行.15.铁钼触媒为什么使用时必须硫化因为铁钼触媒在出厂时是以氧化态即Fe.MnO2,Fe2O3,MnO存在,在未硫化前,对有机硫化合物就有一定活性,但不稳定,比硫化态活性低,所以在使用时必须硫化.。
精选变换工艺技术方案

φ3.5-4.0条形氧化态为浅绿色0.76-0.86>140
主要使用条件
压力,MPa温度,C干气空速, h-1水/气, mol/mol最佳装填高度(高/径)
1.010210-580100060000.32.00.81.5
动设备: 1#冷凝液泵:耐腐蚀多级离心泵 2#冷凝液泵:耐腐蚀多级离心泵存在问题: 目前,国内变换炉制造厂家有南化机、锦西化机、大连金重等,其中南化机制造的海南高温变换炉φ4600×100×10270 T=477℃,P=4.2MPa为最大,但压力比较低。
四、公用工程
副产蒸汽:
蒸汽品质
主要使用条件
压力,MPa温度,C最佳使用温度,C起活温度,C初期最佳入口温度,C耐热温度C耐热时间,h干气空速, h-1水/气, mol/mol最佳装填高度(高/径)
6.0190-500220-450180高于露点20C5502-4100060001.40.81.5
项 目
K8-11G
小结:中温变换是最早的流程。由于当时没有低变触媒,因此全用中变触媒。此时的进口半水煤气温度约在300度左右,而热点温度在480~500度。这个流程几个流程中最耗能的。该流程出口的CO大约在3%左右。当低变触媒研发成功后,首次出现的是中串低工艺,该工艺前面是很大的中变炉,当作主要的变换场所,而后面连接的低变炉的最主要的作用就是将中变炉出口CO由3~5%降到1%左右。中低低流程中变炉减小,而增大了低变炉的容积,因此就会更节能。全低变就是全部采用低变触媒,因此进口温度就可降到180~210度,而热点将达到240~280度。耐硫变采用耐硫触媒,使催化剂有较强的抗硫性能,变换出口CO<0.60%,满足后工序的生产要求。
转化器触媒翻倒实施方案
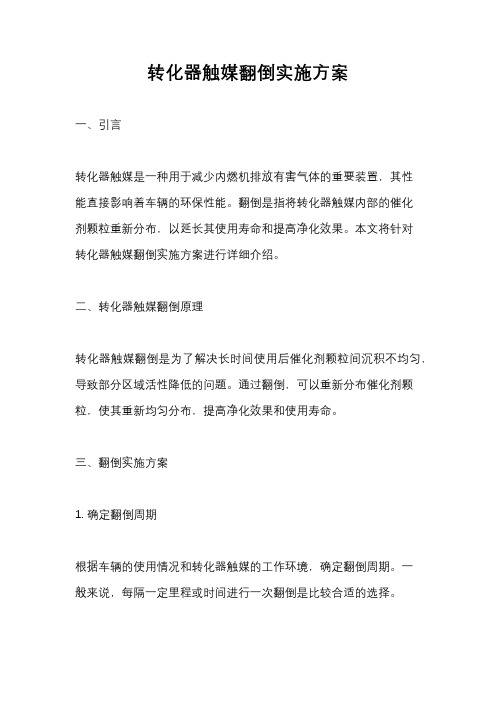
转化器触媒翻倒实施方案一、引言转化器触媒是一种用于减少内燃机排放有害气体的重要装置,其性能直接影响着车辆的环保性能。
翻倒是指将转化器触媒内部的催化剂颗粒重新分布,以延长其使用寿命和提高净化效果。
本文将针对转化器触媒翻倒实施方案进行详细介绍。
二、转化器触媒翻倒原理转化器触媒翻倒是为了解决长时间使用后催化剂颗粒间沉积不均匀,导致部分区域活性降低的问题。
通过翻倒,可以重新分布催化剂颗粒,使其重新均匀分布,提高净化效果和使用寿命。
三、翻倒实施方案1. 确定翻倒周期根据车辆的使用情况和转化器触媒的工作环境,确定翻倒周期。
一般来说,每隔一定里程或时间进行一次翻倒是比较合适的选择。
2. 确定翻倒方法目前常用的翻倒方法有机械翻倒和化学翻倒两种。
机械翻倒是指通过特殊设备将转化器触媒内部的催化剂颗粒进行重新分布,而化学翻倒则是通过特殊溶液将催化剂颗粒溶解后重新沉积。
根据实际情况选择合适的翻倒方法。
3. 实施翻倒操作在进行翻倒操作时,需要严格按照操作规程进行,确保操作的安全和准确性。
同时,需要注意保护环境和自身安全,避免对周围环境和人员造成不良影响。
四、翻倒效果评估完成翻倒后,需要对转化器触媒的净化效果进行评估。
通过排放检测和性能测试,验证翻倒后的转化器触媒是否达到预期的净化效果和性能要求。
五、翻倒后的维护和保养翻倒完成后,需要对转化器触媒进行维护和保养,确保其长期稳定运行。
定期检查和清洁转化器触媒,及时发现并解决问题,可以延长其使用寿命并保持良好的净化效果。
六、结语转化器触媒翻倒是保障车辆环保性能的重要环节,正确的翻倒实施方案可以有效提高转化器触媒的净化效果和使用寿命,对保护环境和人类健康具有重要意义。
希望本文所述的翻倒实施方案能够为相关行业提供参考,推动环保技术的不断进步和应用。
净化题库

1什么是催化剂?能够增加反应速度,而反应前、后本身的性质保持不变的物质叫催化剂。
1.写出净化车间各炉催化剂还原前后的主要成份?1)中变催化剂,还原前Fe2O3,还原后Fe3O4;2)低变催化剂,还原前CoO、MoO3,硫化后CoS、MoS2;3)甲烷化催化剂,还原前NiO,还原后Ni。
2中变触媒在使用前,为什么要进行升温还原?因为中变触媒在运输和贮存过程中是以Fe2O3的形式存在的,而我们生产时,变换CO的主要活性成份是Fe3O4。
要想把Fe2O3变成具有变换活性的Fe3O4,在使用前就必须进行还原。
由于在制造、运输和存放时,触媒里含有少量水份,在使用前,用提高温度的办法,使水份蒸发掉。
在还原过程中,温度在180℃时还原反应才能进行,250℃以上时,反应较明显、剧烈。
所以中变触媒在使用前要进行升温和还原。
3中变触媒在还原时为什么要加蒸汽?加多少为宜?因为用干煤气进行还原,会使中变触媒过度还原。
使还原好的触媒(Fe3O4),过度还原生成氧化亚铁、金属铁,并且而生成碳化铁,造成触媒结构变化,失活、粉化、阻力增大。
为防止过度还原最有效的方法就是:从还原开始就通入一定量的水蒸汽。
一般不低于10%。
随着变换反应的增加,水蒸汽的比例可相应增大。
4写出变换、甲烷化主要反应方程式?i.变换:CO+H2O(g)==CO2+H2ii.2)甲烷化:CO+3H2==CH4+H2O(g)CO2+4H2==CH4+2H2O(g)5中变触媒在卸出之前为什么要钝化?因为在生产状态下,中变触媒是以还原态的Fe3O4形式存在的,它遇氧易被氧化,当温度在60℃以上时,遇空气能剧烈燃烧,使触媒烧结及损坏设备;因温度剧升也使人无法进入设备内卸触媒。
想继续使用的触媒无法再用。
因中变炉内壁是耐火泥捣固的,即使不想再用的触媒也不能用水浇。
所以为防止触媒氧化,在卸出前要进行钝化处理。
6写出中变触媒还原反应方程式?3Fe2O3+H2==2Fe3O4+H2O(g)3Fe2O3+CO==2Fe3O4+CO27写出甲烷化还原反应方程式?NiO+H2==Ni+H2O(g)NiO+CO==Ni+CO28写出低变触媒硫化反应方程式?CoO+H2S==CoS+H2O(g)MoO3+2H2S+H2==MoS2+3H2O(g)9中变、低变反应及钝化、还原反应温升大约是多少?1)每变换1%CO温升大约6℃;2)变触媒纯化每1%O2温升大约160℃;3)中变触媒还原每1%CO温升大约14℃;4)中变触媒还原每1%H2温升大约3℃5)甲烷化反应触媒的温升大约是多少?6)每反应1%的CO触媒的温升约72℃;7)每反应1%的CO2触媒的温升约60~64℃;8)每反应1%的O2触媒的温升约165℃。
触媒反应的机理与应用

触媒反应的机理与应用触媒反应是指在化学反应中,通过添加一种物质——触媒,来加速化学反应过程的方法。
触媒反应具有很多的优点,如节省能源、降低反应物成本、提高反应的选择性和效率等。
由于它具有这些优点,所以在现代化学产业中有着广泛的应用。
一、触媒反应的机理触媒反应的本质是通过改变反应物的自由能,来降低化学反应的活化能,从而提高反应速率的过程。
触媒的加入可以在很短的时间内改变反应物的自由能,而且在反应过程中不会被消耗,因此可以反复利用。
触媒能够降低化学反应的活化能,是因为它能够提供一条新的反应路径,使得反应物可以通过这条路径快速地转化为产物。
在触媒反应中,通常会形成一种中间体,这种中间体又被称为触媒活性中心,它是触媒参与反应的关键。
在触媒反应中,触媒与反应物之间存在着物理吸附和化学吸附的两种吸附方式。
物理吸附是指触媒与反应物之间的吸引力是由于物理力量的作用,如范德华力。
而化学吸附是指触媒与反应物之间的吸引力是由于化学键的形成而产生的。
在化学吸附中,触媒分子在吸附到反应物表面上后,会发生变化,形成一个化学键。
这种化学键可以使得反应物在触媒的帮助下,转化为更稳定的中间体。
而这个中间体会通过再次与触媒发生化学反应,最终生成产物。
二、触媒反应的应用领域触媒反应在现代化学产业中有着广泛的应用。
以下就是一些常见的触媒反应应用:1. 催化裂化反应催化裂化反应是指使用高温和高压的条件将石油原料中的长链烃分子破裂成较短链的低碳烃。
这种反应需要使用一种催化剂,通常使用的是沸石催化剂。
沸石催化剂具有很强的酸性,可以加速石油原料的破裂反应。
通过催化裂化反应,可以获得高质量的汽油和柴油等烃类。
2. 氧化反应氧化反应是指将一种物质中的氧元素转移给另一种物质的化学反应。
氧化反应在有机合成和化工生产中都有广泛应用。
例如,在制备一些精细化学品时,需要使用氧化反应来合成反应所需的中间体。
此外,氧化反应还可以用来处理废水中的有机物质。
3. 氢化反应氢化反应是指将一种物质与氢气反应生成另一种物质的化学反应。
变换-净化工艺流
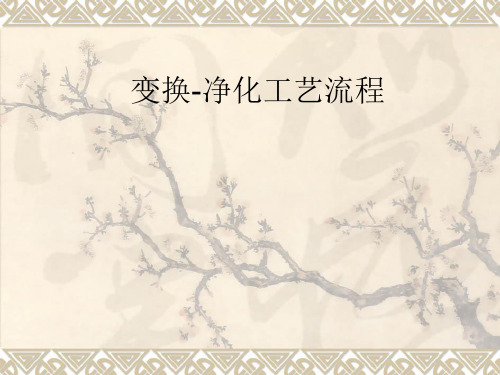
2.2.3 物理化学综合吸收法 环丁砜法、常温甲醇法等。
3. 低温甲醇洗工艺特点
3.1 吸收能力大
甲醇在低温下,对CO2、H2S、COS的溶解 度较大,据计算,在3.1MPa的压力下,1m3甲 醇溶液能吸收CO2 160~180m3,而1m3NHD溶 液仅能吸收CO2 40~55m3,甲醇对CO2的吸收 能力是NHD溶液的4倍左右,在吸收等量酸性气 体时低温甲醇洗的甲醇溶液循环量小,装置设 备数量较少,总能耗较低。
P2012A/B 二硫化碳计量泵
久泰能源内蒙古有限公司100万吨/年 甲醇项目变换工段工艺流程图
制图 弋朝山 审核 卫东升
2.4 流程讲述
2.4.1 变换系统 将气化送来的水煤气进行部分变换,将一部分一氧化碳在触媒的作用下,与水蒸气反
应,使CO与H2比例满足甲醇合成需要后送入低温甲醇洗工段。
2.4.2 热回收系统 热回收系统主要任务是将气化系统送来的高温水煤气进行降温,用废锅回收其中的热
催化剂主要成份为:CoO和MoO3。由于催化剂是以氧化物形式存在,活性很低,当转化为 金属硫化物时才具有很高的活性,所以在催化剂使用之前必须硫化。
硫化过程主反应为:
MoO3+2H2S+H2==MoS2+3H2O+48.15 KJ/mol (1)
CoO+H2S==CoS+H2O+13.40 KJ/molE2007E206HV2009
H PDIA
2002
TI 2015
E2009
CWR
E2010 CW
锅炉给水去甲醇合成 脱盐水
C2001
TI 2016
- 1、下载文档前请自行甄别文档内容的完整性,平台不提供额外的编辑、内容补充、找答案等附加服务。
- 2、"仅部分预览"的文档,不可在线预览部分如存在完整性等问题,可反馈申请退款(可完整预览的文档不适用该条件!)。
- 3、如文档侵犯您的权益,请联系客服反馈,我们会尽快为您处理(人工客服工作时间:9:00-18:30)。
变换触媒氧化降温方案
变换氧化降温任务是将变换炉通入空气,使一、二、三段高活性触媒Fe3O4表面氧化生成Fe2O3,可以从炉内卸出,筛去粉末后装入变换炉还原后重新使用。
为了仍能重新利用变换触媒,在触媒卸出前必须将其彻底钝化,根据以往经验和公司的装备情况,特制定以下中变触媒钝化降温方案。
一、钝化组织机构
总负责人:
负责人:
设备负责人:
工艺负责人:
电气负责人:
仪表负责人:
分析负责人:
操作工:
二、设备的准备工作:
1、
2、低变进出口加盲板,且挂标志牌。
3、变换饱和塔出口加一个“U”型汞柱测压表。
脱硫准备1#罗茨鼓风机,给钝化触媒时提供空气,拆除罗茨风机进口管加消音器,出口加装盲板,配置Ф325管道利用大近路管线至静电除焦进口,使之与脱硫塔以前的系统和进气系统隔离(脱硫净氨塔加满水形成水
封)。
4、配热交进口大阀降温进路阀,煤气付线阀关死挂禁动牌。
5、低变触媒保护用氮气10瓶。
6、操作记录报表,记录本。
三、停车后的工作
1、停车后变换系统立即打开低变近路阀,关其进、出口阀门,然后中低变系统分别进行卸压,待压力卸完后,低变炉进、出口阀加盲板,低变内加氮气保护。
2、压缩2台压缩机拆除一二段活门(一二段各4只),作为钝化空气的通道(一台阻力大)。
3、脱硫系统置换、配管道、加盲板和净氨塔加水。
四、变换蒸汽置换降温(约3~4小时)
1、变换系统加蒸汽静止置换,向前置换至压缩二段出口,向后置换至碳化进口放空(该放空钝化降温期间应长开),到CO+H2≤0.5%为止;
2、然后打开三段后放、热交后放及系统后放空变换进入蒸汽降温阶段。
降温速率为每小时50℃,当触媒层温度降至230℃~250℃左右时,变换转入空气钝化阶段。
六、空气钝化(30小时)
待确认脱硫、变换、二出管线、三进管线、压缩机蒸汽置换合格后,通知脱硫岗位开启1#罗茨鼓风机,打开4#压缩机的一进阀门和二出阀门,其余阀门全部关闭,将空气引人变换岗位关闭热交前的进
口大阀(汞柱应在200~220mmHg高)
蒸汽加入量调至2000kg/h,慢慢向系统内配入空气(第一次配空气约开三圈半) 。
根据汞柱的高度,触媒床层氧化温度会逐渐升高,要及时调节蒸汽与空气的配比,氧化温升速率不超过100℃/h。
氧化前期(15小时左右),热点温升120℃左右时,加大蒸汽用量,待热点温度下降110℃左右,再适当增加空气减少蒸汽用量,如此反复多次。
钝化15小时后,热点温升应控制在150℃左右时,反复加大蒸汽用量,待热点温度下降150℃左右,再适当增加空气减少蒸汽用量,如此反复多次,直至一台大罗茨机负荷加满停止加入蒸汽,降温阀门全开,炉温不再上涨反而逐步下降,钝化过程热点温度最高不能超过550℃。
分析变换炉出口氧含量20%左右,然后启动压缩机,向变换系统补空气,缓慢升压,同时注意温度变化,若温度再次上涨,则继续添加蒸汽,直至压力等于0.4MPa,温度不再发生变化视为钝化结束。
钝化结束后调整各段冷激阀门炉温降至200℃以下停罗茨机、压缩机,钝化降温结束(该降温过程约需2~4小时)。
五、降温置换注意事项
1、调度要合理指挥,要求脱硫、压缩岗位安排专人操作罗茨鼓风机、压缩机,水处理、锅炉要保证供水供汽。
锅炉岗位要专人看管蒸汽压力。
2、各岗位操作人员应认真操作,按时做好各项纪录。
3、置换时要打开各付线,排污倒淋,做到置换要彻底,不留死
角。
4、中变触媒降温时,热水饱和塔要建立热水循环,,并排出热水,补充冷水。
同时防止填料和塔器内壁发生着火现象。
5、各塔液位应控制在1/2—2/3处,并经常排放各处倒淋。
6、试配空气时要密切注意温度变化,,防止触媒层温度过高,最高温度不得超过550℃,防止触媒结疤,烧坏箅子。
7、试配空气和试配蒸气不能同时进行,调配间隔应大于10分钟,视触媒层温度变化情况再决定下一次调控参数。
8、在钝化期间要时刻注意蒸汽压力的变化,加大蒸汽用量和关小蒸汽阀门要提前与锅炉岗位联系。
9、各位操作人员要事前熟悉流程,在操作中要勤联系,勤检查,做好本次氧化降温和置换工作。
10、空气降温触媒床层温度降至120℃时不准加入蒸汽。
******化工有限责任公司
2009、5、16。