催化工艺说明
催化裂化工艺介绍

1。
0催化裂化催化裂化是原料油在酸性催化剂存在下,在500℃左右、1×105~3×105Pa 下发生裂解,生成轻质油、气体和焦炭的过程.催化裂化是现代化炼油厂用来改质重质瓦斯油和渣油的核心技术,是炼厂获取经济效益的重要手段。
催化裂化的石油炼制工艺目的:1)提高原油加工深度,得到更多数量的轻质油产品;2)增加品种,提高产品质量。
催化裂化是炼油工业中最重要的一种二次加工工艺,是重油轻质化和改质的重要手段之一,已成为当今石油炼制的核心工艺之一。
1。
1催化裂化的发展概况催化裂化的发展经历了四个阶段:固定床、移动床、流化床和提升管。
见下图:固定床移动床流化床提升管(并列式)在全世界催化裂化装置的总加工能力中,提升管催化裂化已占绝大多数。
1。
2催化裂化的原料和产品1。
2。
0原料催化裂化的原料范围广泛,可分为馏分油和渣油两大类。
馏分油主要是直馏减压馏分油(VGO),馏程350—500℃,也包括少量的二次加工重馏分油如焦化蜡油等,以此种原料进行催化裂化称为馏分油催化裂化。
渣油主要是减压渣油、脱沥青的减压渣油、加氢处理重油等。
渣油都是以一定的比例掺入到减压馏分油中进行加工,其掺入的比例主要受制于原料的金属含量和残炭值.对于一些金属含量低的石蜡基原有也可以直接用常压重油为原料。
当减压馏分油中掺入渣油使通称为RFCC。
以此种原料进行催化裂化称为重油催化裂化。
1。
2.1产品催化裂化的产品包括气体、液体和焦炭。
1、气体在一般工业条件下,气体产率约为10%-20%,其中含干气和液化气。
2、液体产物1)汽油,汽油产率约为30%-60%;这类汽油安定性较好。
2)柴油,柴油产率约为0—40%;因含较多芳烃,所有十六烷值较低,由重油催化裂化得到的柴油的十六烷值更低,这类柴油需经加氢处理。
3)重柴油(回炼油),可以返回到反应器内,已提高轻质油收率,不回炼时就以重柴油产品出装置,也可作为商品燃料油的调和组分。
4)油浆,油浆产率约为5%—10%,从催化裂化分馏塔底得到的渣油,含少量催化剂细粉,可以送回反应器回炼以回收催化剂。
催化裂化工艺流程ppt

催化剂对裂解过程的促进作用
提供活性中心
催化剂表面具有特殊的活性中 心,能够吸附和活化重质烃分 子,使其更容易发生裂解反应
。
降低反应活化能
催化剂可以降低裂解反应的活化 能,使反应更容易进行。
促进反应选择性
催化剂可以促进特定结构的烃分子 发生裂解反应,提高产品的选择性 。
产品的主要性质及用途
乙烯和丙烯
催化裂化工艺流程ppt
xx年xx月xx日
contents
目录
• 概述 • 工艺流程 • 催化裂化反应原理 • 工艺特点 • 应用和发展 • 安全和环保
01
概述
催化裂化是什么
1
催化裂化是一种将重质烃转化为轻质烯烃和芳 烃的石油化工过程。
2
催化裂化催化剂通常为酸性催化剂,如硅酸铝 、沸石等。
3
催化裂化工艺可分为固定床、流化床和移动床 三种类型,其中流化床工艺最为常用。
THANKS
谢谢您的观看
三废处理
对工艺流程中产生的废水、废气、废渣进行分类处理,实现资源化再利用。 例如,将废气中的二氧化碳进行捕获和封存,实现减排目标;将废水进行深 度处理后再次利用;将废渣进行资源化利用等。
绿色催化裂化工艺流程的探索
不断探索新的催化裂化工艺流程,采用绿色催化剂、提高反应转化率和能量 利用率等措施,实现工业生产与环境保护的有机结合。
产品收率和质量调整
通过调整催化剂种类和反应条件,可以改变产品的收率和质 量。这使得催化裂化工艺具有很强的适应性,能够根据市场 需求灵活调整产品结构。
05
应用和发展
在石油工业中的地位
01
石油工业作为国家经济发展的重要支柱,催化裂化工艺在其中扮演着至关重要 的角色。
QSY-高效催化氧化工艺介绍

QSY-高效催化氧化工艺介绍一、QSY-高效催化氧化工艺技术与产品介绍QSY-高效催化氧化深度处理污水技术是自主研发创新的高效、广谱深度污水处理专有专利技术(专利号:20170249910.2)不仅能对尾水深度处理,实现中水回用,而且可以用于生化前预处理。
广泛适用于印染、化纤、化工、制药、农药、电泳、电镀、焦化、造纸以及工业园区、市政污水的深度处理,提标改造,具有高效、广谱、低成本及稳定性好的优势。
(1)QSY-高效催化氧化深度处理污水技术技术背景:根据水质分析结果,特别是含有化纤、印染、制药、化工等废水的综合污水,经生化处理后,水中残留的污染因子主要为杂环类、多键、多碳等有机化合物和微生物分泌的溶解性生物排泄物。
这类特征污染因子的化学和生物稳定性较高,不仅难以生物降解而且对微生物具有较高的抑制和毒害作用,因此采用常规的混凝、过滤等深度处理技术效果不明显。
本技术是基于水质的特点而研发的,其技术原理是:A、通过催化还原催化氧化,改变了水中特征污染物的键价特性,降低其反应条件;B、通过改变和破坏水中特征污染物的分子结构,提高其化学反应的活性;C、通过改变特征污染物分子的电荷和电负性,改变其亲水性,以提高凝聚性能。
(2)本技术核心为QSY-高效催化氧化专用催化剂:QSY-高效催化氧化是由催化还原催化氧化组成的技术,具有催化还原—催化氧化多功能作用。
利用QSY高效催化剂形成催化还原+催化氧化体系,组成多电源催化系统,拥有多相电极,液相传质效率高,大大提高了电流效率、单位时空效率,对特征污染因子进行还原、氧化,实现降解。
催化剂(Catalyst)由CA1和CA2组成,CA1催化材料:多电位差多金属复合新型催化剂,CA2催化材料:多金属(POM)纳米材料制备的新型催化剂。
三、QSY-高效催化氧化工艺流程及说明工艺流程(1)将污水泵入催化还原反应系统,对多键、多碳、硝基、偶氮类等污染物进行开环断链,水分子按照磁力线的方向重新排列,降低有机物活性点与药剂分子的反应屏障;(2)再经催化氧化反应系统,达到无选择地与废水中的有机污染物进行催化氧化反应;能将污染物分解为二氧化碳、水或小分子有机物;(3)之后进QSY-稳定反应器进行进一步的催化氧化,提高废水中残留的、难降解的、水溶性小分子污染物的混凝性、沉降性;(4)稳定反应器出水进入高效沉淀池进行固液分离,出水清澈透明。
催化氧化工艺rto

催化氧化工艺RTO
催化氧化工艺RTO是一种废气处理技术,利用催化剂在高温、高压的条件下与氧气反应,将有机物氧化成CO2和H2O。
其工作原理如下:
1. 废气进入预热器,经过预热后进入催化燃烧室。
2. 废气在催化剂的作用下与氧气反应,在高温下氧化成CO2和H2O。
3. 氧化后的气体进入热交换器,通过热交换器将废气中的热量传递给进入的新鲜空气,使新鲜空气被加热。
4. 加热后的新鲜空气进入再生燃烧器,与废气中未经氧化的有机物反应,产生热量。
5. 再生燃烧后的废气通过热交换器,将热量传递给进入的废气,使废气被加热。
6. 加热后的废气进入再生室,通过热交换器将废气中的热量传递给进入的新鲜空气,使新鲜空气被加热。
7. 经过热交换后的废气再次进入催化燃烧室,与氧气反应,反复循环直至废气得到完全氧化。
催化燃烧RTO的优点包括高效节能、无二次污染等,被广泛应用于各种工业废气的处理上,如石化行业尾气净化、化工行业有机溶剂回收、食品加工过程中异味气体的去除等。
催化裂化工艺流程
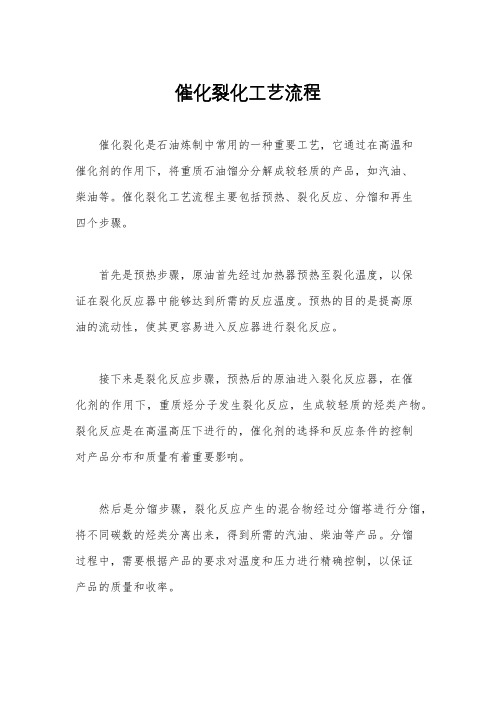
催化裂化工艺流程
催化裂化是石油炼制中常用的一种重要工艺,它通过在高温和
催化剂的作用下,将重质石油馏分分解成较轻质的产品,如汽油、
柴油等。
催化裂化工艺流程主要包括预热、裂化反应、分馏和再生
四个步骤。
首先是预热步骤,原油首先经过加热器预热至裂化温度,以保
证在裂化反应器中能够达到所需的反应温度。
预热的目的是提高原
油的流动性,使其更容易进入反应器进行裂化反应。
接下来是裂化反应步骤,预热后的原油进入裂化反应器,在催
化剂的作用下,重质烃分子发生裂化反应,生成较轻质的烃类产物。
裂化反应是在高温高压下进行的,催化剂的选择和反应条件的控制
对产品分布和质量有着重要影响。
然后是分馏步骤,裂化反应产生的混合物经过分馏塔进行分馏,将不同碳数的烃类分离出来,得到所需的汽油、柴油等产品。
分馏
过程中,需要根据产品的要求对温度和压力进行精确控制,以保证
产品的质量和收率。
最后是再生步骤,裂化反应产生的催化剂在经过一段时间的使
用后会失活,需要进行再生。
再生过程包括焙烧和再生氢化两个步骤,通过高温气体的通入和催化剂的洗涤,使催化剂重新获得活性,可以继续用于裂化反应。
总的来说,催化裂化工艺流程是一个复杂的过程,需要对原油
的性质、催化剂的选择、反应条件的控制等方面进行精确的把握。
只有在各个步骤都能够得到合理的设计和操作,才能够得到高质量
的裂化产品。
同时,随着石油资源的日益枯竭和环保要求的提高,
对催化裂化工艺的研究和改进也变得日益重要,希望在未来能够有
更多的突破和创新,为炼油行业的发展做出更大的贡献。
催化工艺流程概述

工艺流程概述4.1 工艺原理催化裂化工艺是指原料油〔常压渣油〕,在高温催化剂的作用下发生催化裂化反响生成裂解油气,并通过精馏、吸收、解吸等手段将裂解油气别离为干气、液化气、稳定汽油、柴油、回炼油、油浆的过程。
4.1.1反响系统预提升段:使催化剂在提升管中下部能够形成“柱塞流〞,具有较好的速度与密度,以利于与原料的充分接触。
进料喷嘴:在适宜的原料油预热温度下,通过原料雾化蒸气的作用,将原料油雾化成小液滴,以便与催化剂充分接触。
提升管反响器:是原料油与高温催化剂接触进展催化裂化的场所。
提升官反响器的构造特点使其可以比拟好的控制反响时间,防止返混、减少二次反响。
粗旋快分和油气快速导出技术是提升管出口处油气—催化剂别离装置,用以减少油气、催化剂的接触时间,防止二次反响,减少过度裂化和热裂化。
汽提段:经粗旋别离后的催化剂下落至汽提段处,与汽提蒸汽逆向接触,置换出催化剂颗粒间和催化剂本身所携带的油气,从而到达提高轻质油收率,降低干气、焦炭产率的目的。
再生器的主要作用是烧去待生催化剂外表的积炭,恢复催化剂的活性,并提供原料发生裂解反响所需的热量。
本装置再生器采用快速――喘流床串联的方式,催化剂采用两段再生。
辅助燃烧室:以瓦斯气〔柴油〕为燃料,主风分一、二次风进入。
一次风进入燃烧室提供燃烧需要的氧,二次风通过夹套冷却炉膛,一、二次风混合后,控制炉膛出口温度,辅助燃烧室只在开工时供再生器升温用,正常生产时只作为主风的通道。
主风分布管:主要是使主风能够沿整个床层截面均匀分布,从而创造一个良好的流化条件和烧焦条件。
大孔分布板:用以分隔烧焦罐与二段再生器,是一再催化剂上升至二段再生器的通道,同时为二段再生器,提供均匀分布的再生气,为二段再生强化烧焦提供保证。
旋风别离器:催化剂自二密相进入稀相时,携带有局部催化剂,含有催化剂的烟气以切线反向进入旋风别离器,在升气管与壳体之间形成旋转的外涡流,由上而下直到锥体底部,悬浮在烟气流中催化剂在离心力的作用下,一面被甩向器壁,一面随烟气流旋转向下,最后落入到灰斗,经料腿返回再生器密相。
(工艺流程)催化工艺流程简述

工艺流程简述1、反应-再生部分原料油由装置外原料油储罐进入本装置原料油罐(V2201),经原料油泵(P2201/A、B)升压与轻柴油(E2211/A、B)、循环油浆(E2207)换热,换热后温度至200℃左右,与回炼油混合后分四路经原料油雾化喷嘴进入提升管反应器(R2101A),回炼油浆经原料油喷嘴上方单独的—组喷嘴进入提升管反应器,在此与高温再生催化剂接触并迅速升温、汽化,催化剂沿提升管向上流动的同时,原料不断进行反应,生成汽油、轻柴油、液化气、干气、中段油、回炼油、油浆等气相产物,同时生成的焦炭覆盖在催化剂表面,使其裂化活性、选择性逐步降低,成为待生催化剂,反应油气与待生催化剂经提升管反应器出口粗旋迅速分离。
进入沉降器(R2101)之后,夹带有少量催化剂的油气经单级旋风分离器分离催化剂后,离开沉降器进入分馏塔(T2201)。
为促进氢转移等二次反应和减少热裂化反应,降低干气、焦炭产率,提高轻质油品收率,在提升管中上部(第一反应区出口)设置有常压直馏汽油、自产粗汽油或除氧水作为反应终止剂的注入点,以增加操作灵活性和弹性。
积炭的待生催化剂自粗旋料腿及沉降器单级旋风分离器料腿进入汽提段,在此与过热蒸汽逆流接触,以置换催化剂所携带的油气,汽提后的催化剂经待生立管、待生塞阀、待生立管套筒进入再生器(R2102)的密相床,在690℃的再生温度、富氧、CO助燃剂存在的条件下进行逆流完全再生,催化剂活性得到恢复后,经再生立、斜管及再生滑阀进入提升管反应器底部,在予提升蒸汽(干气)的提升下,完成催化剂加速、分散过程,然后与雾化原料接触循环使用。
再生过程的过剩热量由内取热器取走恒定热量后,仍然过剩的热量由外取热器(R2103)取走。
再生器的部分催化剂由外取热入口管进入外取热器壳程,在流化风的作用下,呈密相向下流动在流经翅片管束间降温冷却,冷却后的催化剂经外取热器返回管由提升风提升返回再生器密相床层中部,外取热器流化风、提升风由增压机(B2103/A、B)提供。
中石化催化剂制作工艺

中石化催化剂制作工艺一、原料准备催化剂的制造首先需要准备相应的原料,包括载体、活性组分以及其他辅助物质。
载体的选择需要根据具体应用场景和催化剂性能要求来确定,活性组分则需根据催化剂的设计和制备方法进行选择和确定。
此外,还需准备适量的水、有机溶剂等辅助物质。
二、配料混合在原料准备充分后,需要进行配料混合。
这一步骤中,需要将活性组分、载体、水、有机溶剂等按照一定的比例和顺序加入到反应釜中,并进行充分的搅拌和混合。
配料混合的作用是使活性组分与载体充分分散并均匀分布,以确保催化剂的物理化学性能达到预期要求。
三、浸渍沉淀浸渍沉淀是催化剂制备过程中的关键步骤之一。
在此步骤中,将含有活性组分的溶液与载体进行浸渍,使活性组分充分渗透到载体的表面和内部。
随后,通过控制温度、pH值等条件,使活性组分在载体表面发生化学反应并沉淀下来,形成一层均匀的薄膜。
这一步骤对于催化剂的性能具有重要影响。
四、干燥焙烧在浸渍沉淀完成后,需要对催化剂进行干燥焙烧。
这一步骤的作用是去除催化剂中的水分和有机溶剂,同时使催化剂的物理化学性质得到进一步稳定。
干燥焙烧的条件(如温度、气氛等)需要根据具体的催化剂类型和应用场景来确定。
五、活化处理活化处理是催化剂制备过程中的最后一步。
在此步骤中,催化剂需要在一定温度和压力条件下进行还原或氧化反应,以激活催化剂的活性组分并提高其催化性能。
活化处理的方式和条件需根据催化剂的具体类型和应用场景来确定。
六、包装存储活化处理完成后,需要对催化剂进行包装存储。
包装存储的作用是保护催化剂不受外界环境的影响,保持其性能稳定。
包装材料应具有一定的密封性和强度,能够有效保护催化剂免受机械损伤和氧化腐蚀等不利因素的影响。
同时,存储环境也应保持干燥、通风良好且无有害气体存在。
在整个催化剂制作工艺过程中,每个步骤都需要严格控制质量和安全,并密切关注可能出现的问题和异常情况。
对于出现的问题应及时采取措施加以解决,以确保最终产品的质量和性能达到预期要求。
不同催化裂化工艺简介

1.MGG和ARGGMGG和ARGG是采用专用催化剂和相应的工艺操作条件,通过提升管反应器最大量生产低碳烯烃(主要是丙烯)和高辛烷值汽油的催化裂化工艺。
典型工艺条件:MGG反应温度530℃、剂油比7.8、回炼比0.15;ARGG反应温度530℃、剂油比8、反应时间3~4s、回炼比0.1~0.3。
工艺特点:(1)油气兼顾,既大量生产液化石油气又大量生产高辛烷值汽油。
以石蜡基原油的(VGO)为例,MGG工艺技术液化石油气产率可达34%,汽油产率46%,汽油(RON)92~94,诱导期500~1000min。
ARGG的(LPG)产率达25%~30%(其中丙烯含量为40%),汽油产率41%。
(2)原料广泛,可以加工多种原料油,如蜡油、掺渣油、常压渣油或原油等重质原料油。
(3)采用活性高、选择性好、抗金属污染能力强、具有特殊反应性能的RMG、RAG系列催化剂。
(4)适宜的工艺操作条件与专用催化剂配合实现了正常裂化和过裂化的有效控制,在转化率远高于一般催化裂化情况下,汽油安定性好,焦炭和干气无明显增加。
(5)操作灵活,可根据市场变化的需要,通过改变工艺条件来调节汽油、轻柴油和液化石油气的产品分布。
2.DCC-Ⅰ及DCC-ⅡDCC-Ⅰ工艺是以蜡油为原料,在CRP-1专用催化剂及相应操作条件下,用提升管加床层反应器最大量生产丙稀的催化裂化工艺。
在采用较低操作压力、适量注汽、适当空速及540~560℃操作条件下,丙烯产率可达13%~23%,丁烯产率10%~17%,乙烯产率3.5%~6%。
DCC-Ⅱ工艺是以重质油为原料,在CIP-1专用催化剂及较缓和操作条件下,用提升管反应器多产丙烯和异构烯烃,同时兼顾生产汽油的催化裂化工艺。
最大异构烯烃兼顾汽油方案,原料油特性因数为12.6,反映温度505℃下,丙烯产率可达12.52%,异丁烯产率11.23%,异戊烯产率8.67%,汽油产率40.98%,汽油辛烷值(RON)95.8。
催化剂工艺流程介绍
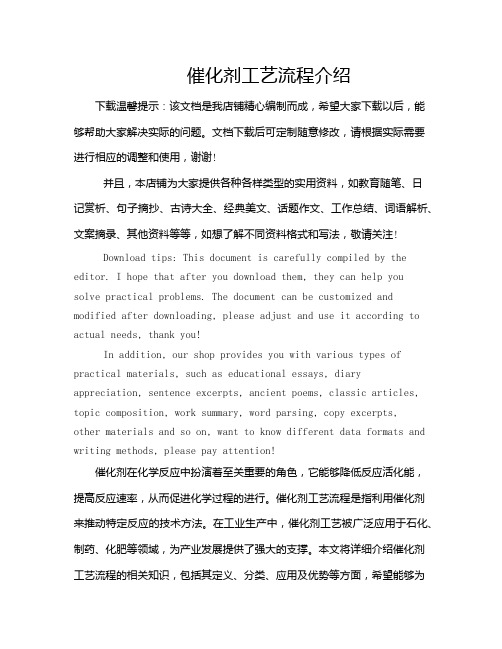
催化剂工艺流程介绍下载温馨提示:该文档是我店铺精心编制而成,希望大家下载以后,能够帮助大家解决实际的问题。
文档下载后可定制随意修改,请根据实际需要进行相应的调整和使用,谢谢!并且,本店铺为大家提供各种各样类型的实用资料,如教育随笔、日记赏析、句子摘抄、古诗大全、经典美文、话题作文、工作总结、词语解析、文案摘录、其他资料等等,如想了解不同资料格式和写法,敬请关注!Download tips: This document is carefully compiled by the editor. I hope that after you download them, they can help yousolve practical problems. The document can be customized and modified after downloading, please adjust and use it according to actual needs, thank you!In addition, our shop provides you with various types of practical materials, such as educational essays, diary appreciation, sentence excerpts, ancient poems, classic articles, topic composition, work summary, word parsing, copy excerpts,other materials and so on, want to know different data formats and writing methods, please pay attention!催化剂在化学反应中扮演着至关重要的角色,它能够降低反应活化能,提高反应速率,从而促进化学过程的进行。
绿色催化技术与工艺

绿色催化技术与工艺绿色催化技术与工艺是一种以可持续发展为基础,旨在减少环境污染和资源浪费的催化技术和工艺。
它通过使用高效的催化剂和优化的反应条件,实现废弃物的降解、有机化合物的合成以及能源转化等过程。
下文将重点介绍绿色催化技术的原理和应用。
一、绿色催化技术的原理绿色催化技术的原理可以概括为以下几点:1. 使用高效催化剂:绿色催化技术使用高效催化剂来提高反应的速率和选择性。
这些催化剂通常具有高催化活性、良好的稳定性和循环使用能力。
2. 优化反应条件:绿色催化技术通过优化反应条件,如温度、压力和反应物比例,以提高反应效率和产物选择性。
同时,减少或消除有毒和有害物质的使用,从而减少环境污染。
3. 推动能源转化:绿色催化技术利用催化反应实现能源转化,如利用太阳能和可再生能源的催化合成、催化分解和催化转换等。
这种方式有助于减少对传统化石能源的依赖,降低碳排放并实现可持续发展。
二、绿色催化技术的应用绿色催化技术在多个领域都有广泛的应用,以下是其中的几个典型应用:1. 废弃物处理:绿色催化技术可以实现废弃物的有效降解和转化。
例如,通过催化反应将工业废水中的有机污染物转化为无害的物质,从而减少对环境的污染。
2. 有机合成:绿色催化技术在有机合成领域具有重要的应用价值。
通过选择合适的催化剂和反应条件,可以实现高效、选择性和环境友好的有机化合物的合成。
3. 能源转化:绿色催化技术在能源转化领域发挥着重要作用。
例如,利用催化技术将生物质转化为生物燃料,实现能源的可持续转化和利用。
4. 环境保护:绿色催化技术可以通过降低能源消耗和有毒物质的使用,减少对环境的负面影响。
这有助于保护生态环境和提高可持续发展水平。
综上所述,绿色催化技术是一种可持续发展的催化技术和工艺。
通过使用高效催化剂和优化反应条件,它实现废弃物的降解、有机化合物的合成和能源的转化。
绿色催化技术在废弃物处理、有机合成、能源转化和环境保护等领域具有广泛的应用前景。
催化工艺流程简述

催化工艺流程简述在化工工业中,催化技术是一种重要的生产方式。
催化技术利用催化剂来降低化学反应的能量需求,提高反应速率,从而增加产量和改善选择性。
本文将简要介绍催化工艺的基本流程。
1. 催化反应的基本原理催化反应是指在催化剂的作用下,底物分子之间发生相互作用,进而产生新的分子,同时催化剂在反应过程中不消耗。
催化剂通常可以提供合适的反应活化能,选择性地促进目标产物的生成。
2. 催化反应的影响因素催化反应的效率受多种因素影响,如催化剂的选择、反应条件、底物浓度和反应温度等。
合适的催化剂选择是催化反应成功的关键,不同的催化剂适用于不同的化学反应。
3. 催化工艺的基本流程3.1 催化剂的制备催化剂通常通过物理或化学方法合成。
物理方法包括沉淀法、共沉淀法等;化学方法则包括浸渍法、沉积法等。
合成的催化剂需要具有良好的活性、选择性和稳定性。
3.2 反应设备的选择催化反应通常在特定的反应器内进行。
反应器种类多样,如流动床反应器、固定床反应器等。
反应器的选择取决于反应条件、催化剂形态以及反应产物的要求。
3.3 反应条件的控制反应条件包括温度、压力、底物浓度等因素。
合理的反应条件可以提高反应速率、产率和选择性。
反应过程中需要不断监控和调整反应条件,以确保反应的正常进行。
3.4 产品分离和纯化反应结束后,需要对反应混合物进行分离和纯化。
通常采用蒸馏、结晶、萃取等方法对产物进行提纯。
高纯度的产品对后续工艺和市场需求至关重要。
4. 催化工艺的应用领域催化技术在石油化工、化学合成、环境保护等领域有着广泛的应用。
例如,在石油加工中,催化裂化技术可以将原油转化为高附加值的产品;在化学合成中,催化剂可以帮助合成特定的有机化合物;在环境保护中,催化反应可以降解有机废水和废气等。
5. 结语催化工艺是一种高效、绿色的生产方式,对化工产业的发展具有重要意义。
通过不断优化催化技术,可以提高产物质量,减少能耗和废物排放,实现可持续发展。
希望本文对催化工艺的基本流程有所帮助。
干式过滤+吸附脱附催化燃烧工艺说明
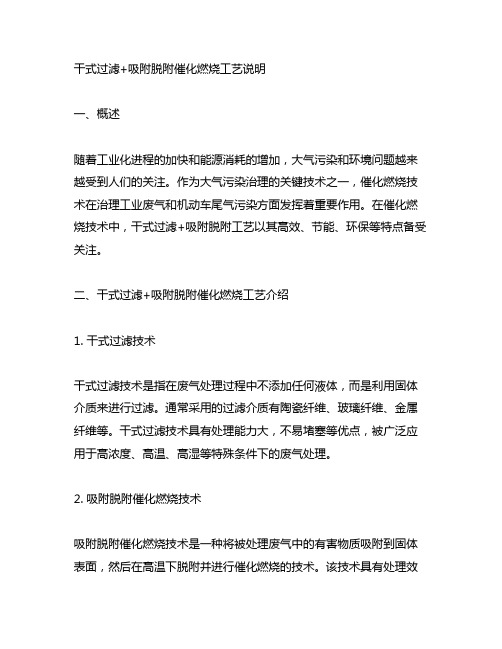
干式过滤+吸附脱附催化燃烧工艺说明一、概述随着工业化进程的加快和能源消耗的增加,大气污染和环境问题越来越受到人们的关注。
作为大气污染治理的关键技术之一,催化燃烧技术在治理工业废气和机动车尾气污染方面发挥着重要作用。
在催化燃烧技术中,干式过滤+吸附脱附工艺以其高效、节能、环保等特点备受关注。
二、干式过滤+吸附脱附催化燃烧工艺介绍1. 干式过滤技术干式过滤技术是指在废气处理过程中不添加任何液体,而是利用固体介质来进行过滤。
通常采用的过滤介质有陶瓷纤维、玻璃纤维、金属纤维等。
干式过滤技术具有处理能力大,不易堵塞等优点,被广泛应用于高浓度、高温、高湿等特殊条件下的废气处理。
2. 吸附脱附催化燃烧技术吸附脱附催化燃烧技术是一种将被处理废气中的有害物质吸附到固体表面,然后在高温下脱附并进行催化燃烧的技术。
该技术具有处理效率高、能耗低、操作稳定等优点,特别适用于有机废气和恶臭气体的处理。
三、干式过滤+吸附脱附催化燃烧工艺应用案例以XX石化公司为例,该公司在废气处理中采用了干式过滤+吸附脱附催化燃烧工艺。
通过在废气处理装置中设置干式过滤器和吸附脱附催化燃烧装置,成功地实现了废气中有害物质的过滤和催化燃烧,使排放浓度大幅度降低,达到了国家和地方的环保标准要求。
四、干式过滤+吸附脱附催化燃烧工艺的优势及发展趋势1. 优势干式过滤+吸附脱附催化燃烧工艺具有处理效率高、设备运行成本低、操作维护简单等优点。
特别是在工业废气和恶臭气体处理领域,该工艺表现出较大的优势。
2. 发展趋势随着环保意识的提高和环保政策的不断完善,干式过滤+吸附脱附催化燃烧工艺将会在更多领域得到推广应用。
随着技术的不断进步和成本的逐渐降低,该工艺在设备结构、催化剂选择、运行参数优化等方面也将得到进一步完善。
五、结论干式过滤+吸附脱附催化燃烧工艺作为废气处理领域的前沿技术,具有很大的发展潜力。
通过不断的研究和实践,优化改进,使得该技术可以更好地满足不同领域废气处理的需求,为保护环境、改善空气质量做出更大的贡献。
催化裂化工艺技术手册

催化裂化工艺技术手册第一章催化裂化工艺概述1.1 催化裂化的定义和作用催化裂化是一种重要的炼油工艺,主要用于将重质石油原料分解为轻质燃料和高附加值的化工产品。
通过催化剂的作用,在高温下将长链烃分子裂解成短链烃分子,以提高产品质量和产率。
1.2 催化裂化工艺的发展历程催化裂化工艺的应用可以追溯到20世纪初。
随着石油行业的不断发展,催化裂化技术也得到了广泛应用。
从传统催化裂化到流化床催化裂化,再到现代的超轻质催化裂化,工艺不断创新和改进,以满足市场需求。
1.3 催化裂化的工艺流程和原理催化裂化的工艺流程包括加热炉和裂解器两个主要部分。
在加热炉中,通过加热将石油原料加热至适宜的温度,然后送入裂解器进行裂解反应。
裂解反应在催化剂的作用下进行,在高温和压力下,长链烃被裂解成短链烃。
第二章催化剂的选择和性能2.1 催化剂的种类和特点常用的催化剂包括酸性催化剂和贵金属催化剂。
酸性催化剂主要是用来促进分子内结构重排和骨架碳裂解反应,贵金属催化剂则用于催化氢化反应,减少不饱和化合物。
2.2 催化剂的性能参数选择合适的催化剂对于提高催化裂化的效果至关重要。
催化剂的性能参数包括比表面积、孔径分布、酸性、稳定性等。
这些参数直接影响到催化反应的速率和选择性。
第三章催化裂化装置的设计和运行3.1 催化裂化装置的主要设备催化裂化装置主要包括加热炉、裂解器、分馏塔等组成。
加热炉用于将石油原料加热至裂解温度,裂解器是催化裂化反应的主要场所,分馏塔用于分离裂解产物。
3.2 催化裂化装置的操作注意事项催化裂化装置的正常运行需要注意以下几个方面:保持适宜的反应温度和压力,注意催化剂的再生和投料,控制氢气和催化剂的用量,合理处理废气和废水。
第四章催化裂化产品的特性和应用4.1 轻质燃料的生产和应用催化裂化可以将重质石油原料转化为轻质燃料,如汽油、柴油和液化石油气。
这些轻质燃料在交通运输、工业生产和日常生活中广泛应用。
4.2 高附加值化工产品的生产和应用除了轻质燃料,催化裂化还可以生产一系列高附加值的化工产品,如石蜡、石油焦等。
催化工艺流程简述

催化工艺流程简述1、反应-再生部分原料油由装置外原料油储罐进入本装置原料油罐(V2201),经原料油泵(P2201/A、B)升压与轻柴油田22114、B)、循环油浆(E2207)换热,换热后温度至200℃左右,与回炼油混合后分四路经原料油雾化喷嘴进入提升管反应器(R2101A),回炼油浆经原料油喷嘴上方单独的一组喷嘴进入提升管反应器,在此与高温再生催化剂接触并迅速升温、汽化,催化剂沿提升管向上流淌的同时,原料持续进行反应,生成汽油、轻柴油、液化气、干气、中段油、回炼油、油浆等气相产物,同时生成的焦炭覆盖在催化剂表面,使其裂化活性、选择性逐步降低,成为待生催化剂,反应油气与待生催化剂经提升管反应器出口粗旋迅速分离。
进入沉降器(R2101)之后,夹带有少量催化剂的油气经单级旋风分离器分离催化剂后,离开沉降器进入分馏塔(T2201)。
为促进氢转移等二次反应和减少热裂化反应,降低干气、焦炭产率,提升轻质油品收率,在提升管中上部(第一反应区出口)设置有常压直馏汽油、自产粗汽油或除氧水作为反应终止剂的注入点,以增加操作灵活性和弹性。
积炭的待生催化剂自粗旋料腿及沉降器单级旋风分离器料腿进入汽提段,在此与过热蒸汽逆流接触,以置换催化剂所携带的油气,汽提后的催化剂经待生立管、待生塞阀、待生立管套筒进入再生器(R2102)的密相床,在690℃的再生温度、富氧、CO助燃剂存在的条件下进行逆流完全再生,催化剂活性得到复原后,经再生立、斜管及再生滑阀进入提升管反应器底部,在予提升蒸汽(干气)的提升下,完成催化剂加速、分散过程,然后与雾化原料接触循环使用。
再生过程的过剩热量由内取热器取走恒定热量后,仍旧过剩的热量由外取热器(R2103)取走。
再生器的部分催化剂由外取热入口管进入外取热器壳程,在流化风的作用下,呈密相向下流淌在流经翅片管束间降温冷却,冷却后的催化剂经外取热器返回管由提升风提升返回再生器密相床层中部,外取热器流化风、提升风由增压机(B2103/A、B)提供。
催化裂化的基本工艺流程(一)
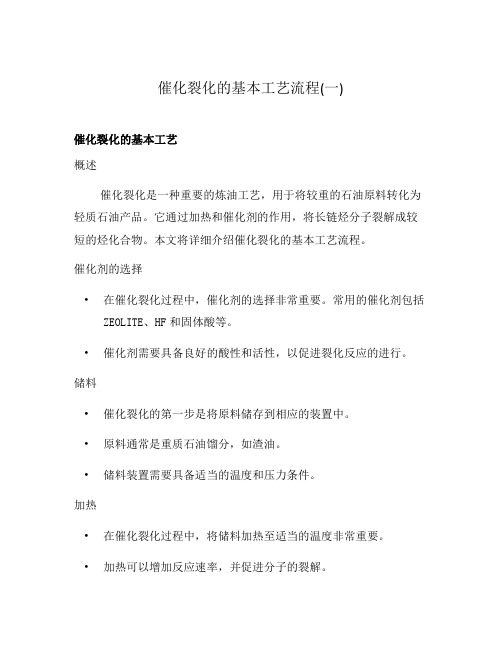
催化裂化的基本工艺流程(一)催化裂化的基本工艺概述催化裂化是一种重要的炼油工艺,用于将较重的石油原料转化为轻质石油产品。
它通过加热和催化剂的作用,将长链烃分子裂解成较短的烃化合物。
本文将详细介绍催化裂化的基本工艺流程。
催化剂的选择•在催化裂化过程中,催化剂的选择非常重要。
常用的催化剂包括ZEOLITE、HF和固体酸等。
•催化剂需要具备良好的酸性和活性,以促进裂化反应的进行。
储料•催化裂化的第一步是将原料储存到相应的装置中。
•原料通常是重质石油馏分,如渣油。
•储料装置需要具备适当的温度和压力条件。
加热•在催化裂化过程中,将储料加热至适当的温度非常重要。
•加热可以增加反应速率,并促进分子的裂解。
•加热的温度通常在高温热解范围内。
裂化反应•裂化反应是催化裂化过程的核心步骤。
•在高温和催化剂的作用下,长链烃分子断裂成较短的烃化合物。
•裂化反应通常需要一定的时间来完全进行。
分离•裂化反应生成的产物是混合物,需要进行分离。
•分离可以根据不同组分的沸点差异进行,如常用的蒸馏分离法。
•分离过程可以产生不同类型的轻质石油产品,如汽油、煤油和液化石油气。
冷凝•在分离过程中,需要对产物进行冷凝。
•冷凝是将蒸气转化为液体的过程,通过降低温度,使烃化合物从气态转化为液态。
•冷凝可以通过冷凝器等设备实现。
催化剂再生•催化剂在裂化反应中会逐渐失活,需要进行再生。
•催化剂再生是将失活的催化剂恢复其活性和酸性的过程。
•再生方式可以有燃烧再生、化学再生等。
总结催化裂化是一项复杂而重要的工艺,在石油炼制中具有重要的地位。
本文对催化裂化的基本工艺流程进行了详细的介绍,包括储料、加热、裂化反应、分离、冷凝和催化剂再生等环节。
通过合理选择催化剂和控制工艺参数,可以实现高效的石油产品转化和利用。
催化裂化工艺的优势提高产能•催化裂化工艺可以将重质石油原料转化为轻质石油产品,提高产能。
•通过裂化反应,可以将较长的烃分子裂解成较短的烃化合物,使得石油原料能够充分利用。
催化裂解工艺(DCC)

催化裂解工艺(DCC)1.工艺原理:催化裂解工艺(DCC)是以重质油为原料、利用择形催化反应制取气体烯烃的新技术。
其中催化裂解Ⅰ型(DCC-Ⅰ)以生产最大量丙烯为主要目的,催化裂解Ⅱ型(DCC-Ⅱ)以生产最大量异丁烯和异戊烯、兼产丙烯和高辛烷值优质汽油为目的。
它们所加工的原料可以是蜡油、蜡油掺渣油或二次加工油以及常压渣油,实现了炼油工艺向石油化工的延伸,开创了一条以重质油为原料直接制取低碳烯烃的新途径,达到国际先进水平。
由于目的产品不同,DCC-Ⅰ和DCC-Ⅱ两者采用的反应器型式、催化剂类型和工艺操作条件都不相同,其差别列于表1。
从表1可见,DCC-Ⅱ的反应时间、反应温度、剂油比及注水量均低于DCC-Ⅰ。
表1:DCC-Ⅰ和DCC-Ⅱ工艺的主要差别DCC-ⅠDCC-Ⅱ反应器型式提升管十床层提升管催化剂CRP CIP反应温度,℃540-580500-530剂油比9-156-9注水量,m%15-256-10产品分布,m%H2~C211.91 5.59C3~C442.2234.49C5+汽油26.6039.00柴油 6.609.77重油 6.07 5.84焦炭 6.00 4.31损失0.60 1.00合计100.00100.00烯烃产率,m%丙烯21.0314.29总丁烯14.0314.65异丁烯 5.13 6.13总戊烯--9.77异戊烯-- 6.77异丁烯/总丁烯0.360.42异戊烯/总戊烯--0.69汽油性质RONC99.396.4MONC84.782.5催化裂解利用择形催化反应原理,将重质原料油选择性裂化成低碳气体烯烃,其丙烯产率是常规FCC的3倍以上。
异丁烯和异戊烯产率也达到FCC的3倍以上。
催化裂解工艺开辟了一条制取低碳烃的新途径。
1.1催化裂解的一般特点①催化裂解是碳正离子反应机理和自由基反应机理共同作用的结果,其裂解气体产物中乙烯所占的比例要大于催化裂化气体产物中乙烯的比例。
②在一定程度上,催化裂解可以看作是高深度的催化裂化,其气体产率远大于催化裂化,液体产物中芳烃含量很高。
催化工艺流程

催化工艺流程催化工艺是一种通过催化剂来促进化学反应的方法,它在工业生产中具有重要的应用价值。
催化工艺可以提高反应速率,减少反应温度和压力,降低反应副产物的生成,提高产品纯度等。
下面将以催化裂化工艺为例,阐述催化工艺的流程。
催化裂化是一种将石油原料转化为高附加值产品的重要工艺。
它通过在高温和高压条件下,利用催化剂将重质石油组分裂解成较轻的烃类化合物。
催化裂化工艺流程主要包括预热、进料、裂化反应、分离和再生等几个步骤。
首先是预热步骤。
石油原料从储罐进入预热器,通过换热器和热交换器进行预热,提升进料温度至裂化反应所需的温度。
预热的目的是降低反应所需的热能输入,并避免因突然变化的温度对设备造成损害。
接下来是进料步骤。
经过预热的石油原料进入主反应器,同时通过氢气进料装置加入适量的氢气。
氢气的加入可以降低催化剂的积碳和结焦,延长催化剂的使用寿命。
在进料过程中,还需要控制进料的流量和温度,以保持反应条件的稳定性。
然后是裂化反应步骤。
在主反应器中,石油原料通过与催化剂接触,发生裂化反应。
裂化反应的条件通常为高温和高压,并且需要催化剂的存在才能进行。
催化剂可以通过吸附、解离和再结合等过程促进石油原料的裂化,生成较轻的烃类化合物。
裂化反应后,需要进行产品的分离步骤。
主反应器出口的混合物经过冷凝和分离,得到不同碳数和性质的烃类产品。
分离过程中常见的设备有分馏塔、凝结器、冷却器等。
分馏塔通过热平衡和物质选择性,实现不同产品的分离和纯度的控制。
最后是催化剂的再生步骤。
催化剂经过多次使用后会积聚废炭和降低活性,需要进行再生以恢复催化剂的活性。
催化剂的再生通常包括在高温和高压条件下进行的氢气燃烧和氨气脱附等步骤。
再生后的催化剂可以循环使用,降低了生产中的成本。
综上所述,催化裂化工艺流程是一个复杂而高效的过程,通过控制进料、反应条件、分离和再生等步骤,可以生产出高附加值的烃类产品。
催化工艺的成功应用,不仅提高了化工产业的效率和产品质量,也减少了能源消耗和环境污染。
- 1、下载文档前请自行甄别文档内容的完整性,平台不提供额外的编辑、内容补充、找答案等附加服务。
- 2、"仅部分预览"的文档,不可在线预览部分如存在完整性等问题,可反馈申请退款(可完整预览的文档不适用该条件!)。
- 3、如文档侵犯您的权益,请联系客服反馈,我们会尽快为您处理(人工客服工作时间:9:00-18:30)。
1、中高浓度有机废气。例如溶剂废气:苯类、酮类等。
直接式焚烧
工艺流程示意图
光催化氧化工艺
概 念 就是光催化剂在光的作用下发生催化作用,使有机物产生分解,如聚 合物分解为简单分子甚至氧化为CO2、H2O 光催化剂:一种在光的照射下,自身不起变化,却可以促进化学反应 的物质。利用光能转换成为化学反应所需的能量,产生催化作用,使 周围的氧气及水分子激发成极具氧化力的自由基或负离子。
催化燃烧
可分为: 预热式:废气温度低于起燃温度 自身热平衡式:废气温度高于起燃温度
吸附—催化燃烧:有机废气的流量大,浓度低,温度低、
采用催化燃烧需要消耗大量燃料时,可先采用吸附浓缩处理
催化剂
催化剂的作用: 降低反应的活化能,降低反应温度,提升反应速率
催化剂寿命:8000H,低于此值能保证90%的催化燃烧效率
成分:有机组分的起燃温度和热值对工艺有影响,物质的爆炸极限浓度需要 衡量,进炉膛的气体控制浓度在25%LEL以下。苯类 280℃,乙酸乙酯350℃, 醋 酸 丁 酯 410℃ , 热 值 能 确 定 辐 热 系 统 的 功 率 。 是否含有硫,卤素,重金属等使催化剂中毒的元素,颗粒物含量情况等。 工作周期:选择备用吸附床,一般设备工作8H不用,超过16H一定要用备用 床。
技术原理 通过引风机将废气送入净化装置换热器换热,再送入到 加热室,通过加热装置,使气体达到催化反应温度,再通 过催化床内催化剂作用,使有机气体分解成二氧化碳和热 能。
①
适用范围
中、高浓度的有机废气,最佳浓度2500—3000mg/m³ ,理 论最低浓度可低至200mg/m³ 主要针对烃类、苯类、酮类、醚类、酯类、醇类、酚类
催化燃烧工艺组合 4.蓄热式催化净化( RCO) 蓄热式催化净化(RCO)
工艺流程示意图
催化燃烧工艺组合 蓄热式催化净化(RCO)
工艺原理图
蓄热式热力氧化(RTO)
技术原理
将高温氧化与蓄热技术相结合的一种有机废气处理技术。
适用范围
适用于中高浓度的有机废气 适用于涂装线、印刷、化学合成工艺(ABS合成)、石油炼化工艺各种产生有机 废气的场所。
安装要求:场地大小是否受限,平面与高度。
催化燃烧工艺组合 活性炭吸附—蒸汽脱附—催化燃烧 (VOC-XC) 适用范围
适用于常温、大风量、中低浓度,易挥发的有机废 气,主要包括一些有机溶剂如苯类、酮类、醛类、 醚类、烷烃及其混合类等。浓度小于 1000mg/m³ 。
技术原理
根据吸附(效率高)和催化燃烧(节能)两个基本 原理设计的,即吸附浓缩-催化燃烧法。
催化燃烧的常见基础参数
选择催化燃烧时主要考量的基础参数有5个如下
风量:决定设备型号大小。 浓度:决定是回收还是燃烧还是需要加浓缩吸附再处理 ,理论起燃浓度 200mg/m³ ,最佳自平衡浓度2500mg/m³ -3000mg/m³ 无需辅热(以催化燃烧 为例)。
温度:温度太高不能直接进活性炭(耐温极限 80 ℃ )浓缩,可以选择沸石 (150℃)。
技术原理
利用特殊波长的光(一般为紫外线),在光催化剂、 水汽、氧气的作用下产生臭氧及自由基对VOCs进 行氧化分解。
光催化氧化工艺组合 前处理+光催化氧化+后处理
根据废气不同的性质,光规划氧化工艺前端需要进行相关前处理工作,以满 足 光 催 化 氧 化 的 使 用 要 求 如除尘、吸附、洗涤等预处理工艺,同时前处理系统还发挥浓度缓冲的作用。 根据对公司目前的废气特性特点的了解,我们采用建议使用复合洗涤塔进行 前处理;复合洗涤塔涵盖生物处理、除尘、洗涤缓冲的作用。一方面通过洗涤 作用将废气中漆尘进行去除,同时利用水的吸收相转化作用将废气中有机物 转移部分到废水中;同时利用微生物的作用对传质入水相的废气进行分解。 该前处理工序能将废气中漆尘、二甲苯、酮类、酯类等去除相当一部分;设 计去除率可达60%。 预处理后的废气进入到光催化氧化系统中,简单分子的酮类、醇类直接分解 为二氧化碳和水,对酯类等物质进行分解为简单分子(如有机酸和醇),该 过程同时去除恶臭气味。 最后出气中可将分解后的尾气进行洗涤塔洗涤,将转化后的可溶有机物清除。
经济性简析
造 价 分 析 : 直接催化燃烧炉体和附属加热混合机构,构成催化燃烧整体设备,按 目前的废气信息进行估算,造价接近 100万,加上附属设施、施工及 其 它 材 料 , 预 计 在 壹 佰 贰 拾 万 以 上 。 如果加入浓缩工艺,采用活性炭浓缩器 + 脱附装置,整体造价将会接 近200万;如采用工艺先进可靠的转轮浓缩装置,造价将飙升至300万 以 上 。 采用光催化氧化工艺,配合前后处理附属设施,其设备造价在 100 万 以内,包含附属设施及施工等,估算造价在120万以内。 催 化 燃 烧 运 行 费 用 分 析 除去风机动力外,直接催化氧化工艺预计装机功率在 500 千瓦左右, 根据目前了解的生产工况,我们预计定常功率应不少于 200千瓦,按 年运行2500小时计算,电额外消耗在50万度;催化剂的装填量在3立 方左右,按设计寿命8000小时计算,三年左右更换一次,费用约50万 元 若采用传统活性炭浓缩,预计年更换活性炭约10吨,若采用活性炭纤 维 蜂 窝 材 料 预 计 年 更 换 量 约 4-5 吨 , 每 吨 费 用 在 3 万 元 左 右 若采用沸石转轮,则10年左右无须更换
催化燃烧工艺组合 活性炭吸附—蒸汽脱附—催化燃烧
工艺流程图
催化燃烧工艺组合 活性炭吸附—蒸汽脱附—催化燃烧
技术特点 采用吸附浓缩 +催化燃烧组合工艺,整个系统实 现了净化、脱附过程闭循环,系统一次性投资较 高。 设计时在活性炭达到80-95%饱和之前即开始脱 附。可自动/手动切换阀门。活性炭更换周期约为 50次吸脱附过程。
有机废气处理技术 简析
燃烧处理技术
燃烧的分类
直接燃烧 热力燃烧
两者的区分:是否添加燃料,热力燃烧有多种,常见的有催化燃烧和蓄热燃 烧等。 直接燃烧经济,常外加燃料汽油或天然气,缺点是燃烧不完全,产生NOx, 大量的有害气体和烟尘,以及热辐射。 催化燃烧,是典型的气-固相催化反应,其实质是活性氧参与深度氧化作用。 在催化燃烧过程中,催化剂的作用是降低反应的活化能,同时使反应物分子 富集于催化剂表面,以提高反应速率。又称无焰燃烧,燃烧完全,温度要求 不高,200-450℃。 蓄热燃烧,利用蓄热陶瓷体维持足够的炉温,有机废气通过蓄热体时发生燃 烧,燃烧后产生的热量重新传导到蓄热体中维持炉膛高温,在800℃左右维持 燃烧 对进气有要求,不能含有硫,卤素,重金属等使催化剂中毒的元素,而且有 时需要消耗辅助燃料。缺点是工艺复杂。
炉内正常温度 400 ℃ , 500 ℃ 将报警,并通过 补冷风进行降温,温度达600℃时停机,同时设计 泄压阀保证安全。
活性炭属性
活性炭
粒状:风阻大 蜂窝状:风阻小
适宜高风量低浓度VOC
第一次脱附时活性炭吸附效率降低较多,以后降低效率平缓,高质量蜂窝活 性炭纤维吸脱附周期为50次左右;普通活性炭制品在20-30次不等 避免高温脱附,高温会使活性炭吸附效率严重下降,穿透时脱附,脱附温度 要大于吸附质沸点15-20℃。
陶瓷蓄热式
直接式焚烧(ZS)
技术原理
利用辅助燃料燃烧所发生热量,把可燃的有害气体的温度提 高到反应温度,从而发生氧化分解。
适用范围 技术特点 利用热力法燃烧方式氧化分解恶臭气体,在适当的温度 下,提供充足的燃烧氧气和一定驻留时间,高效除臭,高 净化率。同时该设备主机工作稳定,不存在堵塞现象。
工作原理 炉体在进行废气处理之前,先将燃烧室、蓄热床进行预热;预热完毕后,将废 气源接入设备。有机废气在配套风机作用下,首先经预热的蓄热陶瓷体1进行 热交换,废气经过一次提温后进入加热区,在加热区废气得到第二次提温, 此时废气温度达到800℃左右废气直接燃烧,生成二氧化碳与水排出并释放热 能;处理后的洁净气体再经过蓄热陶瓷体 2进行蓄热由风机排出。经排风机进 口测温棒进行温度检测后达到设定温度时,进行阀门切换由蓄热陶瓷体2进入 废气、由蓄热陶瓷体1排出,如此循环往复。
沸石
优质沸石吸附器耐高温好,吸附性能优异,以进口沸石转轮的实用纪录,其 循环使用时间一般均大于35000小时,但造价高。目前国内产的沸石吸附器, 其效能与活性炭纤维相差不大,且吸附饱和值低
沸石转轮吸附—焚烧
VOC浓缩净化装置的基本原理图
VOC浓缩净化装置内部结构基 本原理图
催化燃烧工艺组合 低温催化氧化VOC-CH
光催化剂在光照条件(可以是不同波长的光照)下所起到催化作用的 化学反应,统称为光催化反应。
光催化一般是多种相态之间的催化反应。
光催化氧化工艺适用条件
适用范围
ቤተ መጻሕፍቲ ባይዱ
适用于常温、大风量、低浓度,易挥发的恶臭有机 废气,主要包括一些有机溶剂如苯类、酮类、醛 类、醚类、烷烃、甲硫醇、氨、硫化氢、苯乙烯 及其混合类等。进气浓度适宜低于300mg/m³ 。
②
催化燃烧工艺组合 低温氧化催化VOC-CH
技术特点 高浓度时耗能仅为风机功率,浓度较低时自动间歇补偿加热。
催化起燃温度为300—500℃。
催化燃烧工艺组合 蓄热式催化净化(RCO)
技术原理
将低温催化氧化与蓄热技术相结合的一种有机废气净化技术
适用范围
适用与涂装线及烘房有机废气处理,化学工业、化学合成工艺(ABS合 成),石油炼化工艺等各种产生有机废气的场所。