265m2烧结机工艺梳理
265m烧结机使用说明书

产品使用说明书项目名称:265M2带式烧结机唐山冶金矿山机械厂设计中心2011年3月目录一. 机器的用途二. 机器的技术性能三. 机器的外形图四. 机器的传动系统五. 机器的结构六. 机器的润滑系统七. 机器的安装调整和试运转八. 机器的维护及安全技术一. 机器的用途:265m2烧结机适用于大型黑色冶金烧结厂的烧结作业,它是抽风烧结过程中的主体设备,它可将不同成分、不同粒度的精矿粉、富矿粉烧结成块,并部分消除矿石中所含的硫、磷、砷等有害杂质。
二. 机器的技术性能三. 机器的外形图(见烧结机总图)四. 机器的传动系统机器的传动系统由YTSP200L2-6型2x22kw电动机,高速级减速机、低速级减速机、悬挂系统、头部星轮组成,以推动台车运行。
五. 机器的结构1.265m2烧结机由下列各主要部分组成:(1)铺底料装置(2)圆辊给料(3)辊式布料器(4)柔性传动装置(5)头部星轮装置(6)吸风装置(7)台车装配(8)头部机架(9)中部机架及轨道(10)尾部机架(11)头尾密封罩(12)台车装配(13)平台部(14)尾部移动装置(15)1号2号灰箱(16)台车吊具(17)干油集中润滑系统(18)隔热装置(19)篦条压平装置(20)疏料平料装置2.由于带式烧结机在我国各黑色冶金烧结厂已被广泛采用,它的一般结构及工作原理都是烧结工作者所共知,故本说明对265m2烧结机结构简述如下。
(1)铺底料装置安装在头部骨架上,位于台车的上方,用以完成在台车上的铺底料工作。
本装置由上料槽、中料槽、闸门调整装置、摆动漏斗等组成。
上料槽用两点销子,两点压力传感器支撑在厂房上,水平方向的支撑靠4组止振拉杆装置。
摆动漏斗通过两侧的支撑轴和轴承座安装在烧结机骨架上,它是用来调节台车上的铺底料层厚度,漏斗的排出侧侧板是双层结构,外侧闸门可上下调整,其动作由手动蜗轮装置实现,铺底料厚度在20—50mm范围内调节。
(2)辊式布料器通过圆辊的的物料落在由9个φ128mm圆辊组成的倾角38°滚动斜面上,继而装到台车上,并能使物料在料层厚度上得到合理分布。
265m2烧结吊装汇编

烧结主厂房钢结构吊装方案一、工程概况山东莱钢永锋钢铁公司5#265m²烧结机工程烧结主厂房由山东冶金设计院有限责任公司设计,根据项目部分工我单位进行烧结主厂房钢结构工程的吊装工作。
二、编制依据由甲方提供的设计院设计的烧结主厂房钢结构系统施工图《钢结构工程施工及质量验收规范》GB50205-2001以往相关工程的工作经验三、施工准备1.工程特点烧结主厂房轴线跨度为18.000m,最高点处(屋脊处)35.400m,屋脊处高度。
烧结主厂房01线-2线为机尾框架部分,吊车梁分布于BD跨01线-15线。
根据现场实际勘察,只能采用单面跨外吊车站位的方法进行吊装。
现场场地狭小,并与土建,设备安装等专业处于交叉作业状态。
施工项目多,涉及的专业多。
要求施工单必须充分做好构件进场、劳动力、施工机具、周转材料等的组织、协调与调配工作,以确保施工项目按计划、有顺序的进行。
整体结构较复杂。
因此对投入该工程的施工机械的性能、劳动力的素质等要求较高。
高空作业和交叉作业多,专业配合多。
在施工中要科学组织、精心施工,认真编制重点项目的施工方案和作业设计,以使施工正常有序的进行。
安装精度要求高,质量要求高。
烧结钢结构焊接质量及安装质量要求高,必须选用高素质,有经验的管理人员和施工操作人员投入施工,充分利用以往类似工程的施工经验并在施工中加大质量检查力度,严把质量关,确保工程施工质量。
综合以上施工特点,对于该工程的施工必须合理组织、统筹安排、综合考虑,采用科学合理的施工管理办法、手段进行施工、确保施工质量、施工进度,并最大限度的控制成本。
2.烧结主厂房钢结构工程施工内容主要包括:01线-2线的钢结构框架框架,框架柱总高度34.5m。
建筑檐高34.8m。
机尾框架部分总共分为三层平台第一层平台高度为10.6m,第二层平台15.2m,第三层平台20.6m。
机尾框架部分最重构件为框架柱接近30吨。
吊车梁分布于01线-15线共计30根吊车梁。
八钢265m2烧结机生产操作要点

2008年第3期新疆钢铁总l07期八钢265m2烧结机生产操作要点杨恒元朱晓华(宝钢集团八钢公司炼铁分公司)摘要:介绍八钢公司l号265m2烧结机投产后.为适合原燃料供应及生产工艺要求.生产过程控制中的操作原则与要点。
以及影响目前生产稳定发展的因素。
关键词:烧结机;操作;混合料;焦粉;生石灰中图分类号:TF046.4文献标识码:B文章编号:1672--4224(2008)03—0001--021前言随着烧结生产设备规模的扩大。
单位生产能力的提高.大烧结机相对于小烧结机生产。
对生产过程控制的稳定性要求更高。
因为,滞后时间的延长,缓回的周期也就加长。
生产操作的稳定不仅受到烧结原燃料供应量及质量的影响。
还与烧结生产组织管理思路、操作指导方针和过程控制参数范围的合理设置有很大关系。
从八钢l号265m2烧结机投产一年多的生产运行状况来看,不能以组织小烧结生产的思路、经验来指导大烧结生产,面对出现的新问题,必须严格生产操作制度.规范操作。
2八钢265m2烧结机生产操作特点2.1关于焦粉的配加操作焦粉配加原则:八钢265m2烧结机生产工艺一个显著特点就是烧结内循环返矿、烟道及小格散料、除尘灰等都集中到配料矿槽定量配加。
内循环料在烧结过程中始终处于循环状态。
不应参与烧结配料计算。
但是,实际中内返料基本上是经过烧结过程的物料。
原有的水、炭含量已发生改变,内返料配加量的改变必然影响到焦炭配比的调整。
焦粉作为一种新料,要参与烧结配料计算过程。
因此焦粉的配料调整关系必须随着总料量的改变而做调整。
操作要点:由于配料调整滞后时间的延长,同时265m2烧结机生产工艺取消了热筛工艺环节.烧结过程对混合料水分及炭波动造成的后果比较敏感。
因此对焦粉的配量调整应谨慎执行.要充分考虑混合料水分、风量等对含炭量的相互制约关系.否则.将会引起~些操作事故的发生。
如烧结过程恶化。
返料增加.成品率下降,环冷机过红料等现象。
目前,正常生产状况下焦炭调整指导方针是.每次调整以0.2个配比为限.90r a i n后再进行下一次调整。
莱钢265m2烧结机低碳厚料层烧结生产实践

合理 , 使各层烧结反应都处于最佳状态 , 而均匀地 进行。 另外 , 将六辊布料器 的传动方式进行改造。将 原 来 四台减 速机链 条传 动改 为单 减 速机 齿 轮传 动 , 六辊与齿轮箱 的连接 , 采用花键联轴器连接。不但 降低 了设备故 障 率而且节 约 用 电 , 台车 上布 料 偏析 明显趋 于合理 , 料 的偏 析程 度 可 以通 过调 整 六辊 布 的转速 加 以控 制 。
新 和设 备 改造 , 行低碳 厚料 层烧 结技 术应 用 , 进 取得 了较 好 的效果 。
关键 词 : 低碳厚 料层 烧 结 ; 小球 烧 结 ; 偏析 布料 ; 温烧 结 低
2 1 偏析 布料 .
0 前言
节 能降耗 , 质 高 效 不 仅 仅 是 为 了降 低 成 本 , 优 也 是环保 的客 观要 求 , 别是 针 对我 国钢铁 工业 这 特
出 l , } 全
21 1 第 期 0年 1 四 1 月
莱钢 2 5 2 结 机低 碳 厚 料 层烧 结 生产 实践 6 烧 m
王 炜
( 东莱钢股 份 炼铁 厂 莱芜 山 210 ) 714
摘
要: 莱钢股份炼铁厂 4 25 2 号 6m 烧结机从 自身的实际情况 出 , 出了以低碳厚料层烧结为核心 , 小 发 提 将 球 烧 结 、 温烧 结 、 低 蒸汽预 热 、 偏析 布 料 等一 系列 新技 术 融 为一 体 , 结合 自己的 思路 进 行 技 术 创 并
一
烧 结混 合料 往 台车上 布料 时 , 层 与 中层 的粒 上 度组 成差 不 多 , 下 层 大 颗粒 将 会 增 加 , 样 下 层 但 这
耗 能大 户 的现 状 , 具 有 现 实 意 义 。据 统 汁 , 更 我
酒钢265m2烧结机混合料系统工艺优化生产实践温辉吴小平
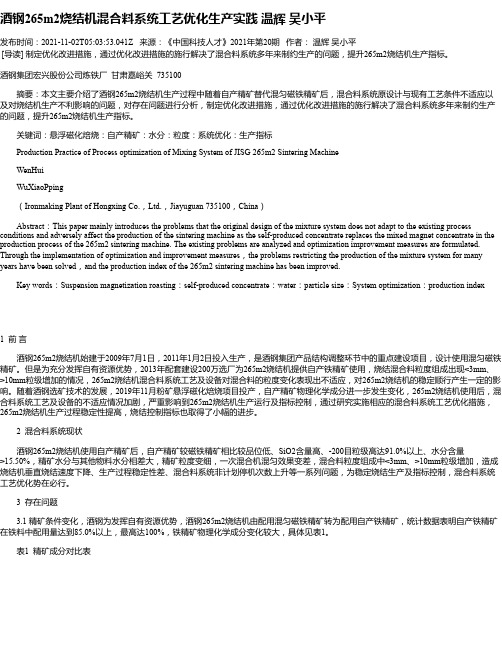
酒钢265m2烧结机混合料系统工艺优化生产实践温辉吴小平发布时间:2021-11-02T05:03:53.041Z 来源:《中国科技人才》2021年第20期作者:温辉吴小平[导读] 制定优化改进措施,通过优化改进措施的施行解决了混合料系统多年来制约生产的问题,提升265m2烧结机生产指标。
酒钢集团宏兴股份公司炼铁厂甘肃嘉峪关 735100摘要:本文主要介绍了酒钢265m2烧结机生产过程中随着自产精矿替代混匀磁铁精矿后,混合料系统原设计与现有工艺条件不适应以及对烧结机生产不利影响的问题,对存在问题进行分析,制定优化改进措施,通过优化改进措施的施行解决了混合料系统多年来制约生产的问题,提升265m2烧结机生产指标。
关键词:悬浮磁化焙烧:自产精矿:水分:粒度:系统优化:生产指标 Production Practice of Process optimization of Mixing System of JISG 265m2 Sintering Machine WenHuiWuXiaoPping (Ironmaking Plant of Hongxing Co.,Ltd.,Jiayuguan 735100,China)Abstract:This paper mainly introduces the problems that the original design of the mixture system does not adapt to the existing process conditions and adversely affect the production of the sintering machine as the self-produced concentrate replaces the mixed magnet concentrate in the production process of the 265m2 sintering machine. The existing problems are analyzed and optimization improvement measures are formulated. Through the implementation of optimization and improvement measures,the problems restricting the production of the mixture system for many years have been solved,and the production index of the 265m2 sintering machine has been improved. Key words:Suspension magnetization roasting:self-produced concentrate:water:particle size:System optimization:production index1 前言酒钢265m2烧结机始建于2009年7月1日,2011年1月2日投入生产,是酒钢集团产品结构调整环节中的重点建设项目,设计使用混匀磁铁精矿。
265m~2烧结机高料层烧结技术

的点火时间加长 , 可以降低点火温度 , 改善烧结矿的 转鼓 强度 , 减少 烧 结矿 的粉末 。
2 )厚料层 烧结 过程 中的蓄热 作用 得 到加 强 , 相
对 的可 以降低 燃料 的用 量 , 强 了烧 结 过程 中 的 氧 增 化气 氛 。
3 )减 少燃 烧过 程不 均匀 所带 来 的影 响 , 改善 烧
台车的速度来增加产量 , 首先必须提高垂直烧结速
度。
合料 、 强化制粒 、 配加蛇纹石等措施 , 成功 的实现 了
料 层为 7 0mm的 高料层 烧结 。 5
3 实施 高料层烧 结采取的措 施
为成 功 实 现 料 层 高 度 为 70 m 的 高 料 层 烧 5 m 结 , 份炼 铁 厂 25m 烧 结 机采用 了一 系 列措 施来 股 6 改善 料层 的透 气性 及提 高垂 直烧结 速度 。
水能 够均匀 的遍 布 于混 合 料 内 , 混 合 料充 分 的润 使
日益枯 竭 的现状 及 烧 结 技术 的发 展 趋 势 来 看 , 施 实
性基本公式测算 , 料层的通风量大约降低 1 %。因 5 此, 实施 高 料层 烧结 时 , 须相 应 的改善 料层 的透气 必 性, 以保 证烧 结 的顺 利进行 , 证烧结 矿 的产量 及质 保
量。
2 2 烧 结 速度减 慢 .
5 3
秦 立 国 。 :6 结机 高料 层烧 结技 术 等 25m 烧
长, 其成 球效 果就越 好 。 因此 , 二次混 合机 的倾 角 将
第 6期 ( 总第 10期 ) 5
表 1 添加 0 5 . %蛇纹石时料层厚度对烧结指标的影响
由原来 的 18 调整 为 .。使混 合 造球 时 间延 长 了 .。 15 , 大约 1mi, 善 了混 合 料 的 成球 性 , n改 也就 是 改 善 了 混合 料 的透气 性 。 3 113 喷加雾 化水 . ..
酒钢265m 2烧结机工艺设计特点及生产实践

矗薯
眦。 EU =。 m 。 a :
付旭 刚 , 更新 , 何 刘树林 , 李文彬 , 贾 强
( 酒钢宏 兴股份公 司 选烧 厂。 甘肃 嘉峪关 7 50 ) 3 10
摘
要: 介绍了酒钢 25m 烧 结机的工 艺、 6 2 设计特点 , 以及投产 半年 以来 的生产运行 情况。通过必 要的设备 消缺 、
整改 、 工艺改进和强化措施 , 较快 的实现了达 产达效 。 关键词 : 烧结工艺 ; 设计 特点 ; 生产实践 中图分类 号 :F 2 . T 14 5 文献标识码 : A
料仓 , 加工方式采用对辊破碎机、 四辊破碎机开路破 碎流程 , 粒度质量标准为 ≥ . m粒度范围≤基准 50m 值 ± .% , 40 基准值根据原料结构及阶段性指标完成
情 况进行 调整 。 () 剂 。熔 剂 主要包 括轻 烧 白云石 、 3熔 生石灰 粉 、
中采纳 国内外先进经验 、 成熟技术和可靠设备 , 结合 自身原料条件 、 供料条件及生产组织模式 , 在建设阶
( 含铁原料。含铁原料主要包括磁铁精矿 、 1 ) 进 口粉矿、 黑鹰山精矿、 高碱 度烧结矿返矿及 酸性 返 矿 ; 精矿 来 自酒 钢储 运综合 料场 , 铁 经综 运皮 带运 输 至配料室 13 18 精矿仓 , 0 — 0# 酸性返矿、 高碱度烧结
矿返 矿 由汽 车运输 至地 矿 槽 、 过 皮带 运 输 至 相 应 通
品存储与外供 、 烧结矿取样与检验以及环冷机余热
回收利 用等 内容 。
2 1 1 原料 的接 受与贮存 ..
碱度烧结矿产量 已不能满足 日 益增产铁产量要求 , 为进一步增加烧结矿产量 , 降低炼铁成本 , 酒钢宏兴
265m2烧结机工艺梳理
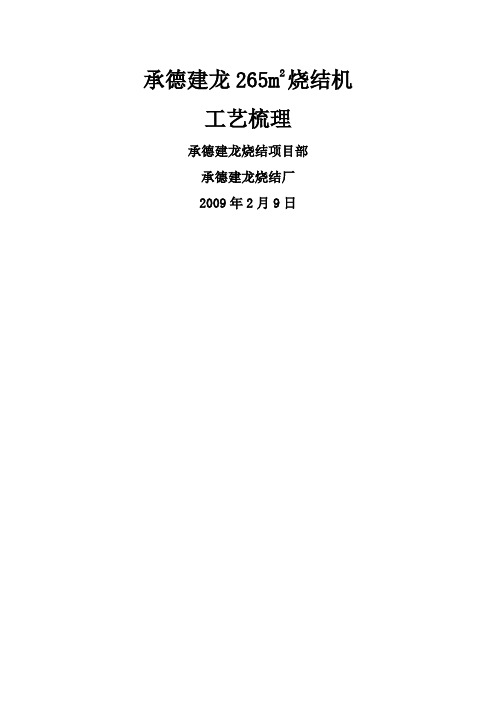
承德建龙265m2烧结机工艺梳理承德建龙烧结项目部承德建龙烧结厂2009年2月9日目录第一章工艺概述第二章一次上料及燃料破碎第三章配料第四章混合、制粒第五章烧结第六章冷却第七章整粒筛分第八章主抽风机、电除尘第九章布袋除尘第十章气力输灰第十一章水泵站第十二章水处理间、余热利用附件1:烧结机系统起重设备性能参数第一章工艺概述1、本资料统计范围:承德建龙烧结厂265m2烧结作业区管辖区域。
2、工艺流程2.1整个烧结系统分为配料、混料、烧结、环冷、风机、除尘6个作业工作区域。
如图所示2.2烧结工艺有一次含铁料受料、燃料破碎、配料、混合、外滚燃料制粒、烧结、冷却、成品整粒、抽风除尘和冷返矿循环等组成;2.3含铁料、燃料、熔剂、除尘灰和冷返矿经配料和混合后,通过两段混合机进行润湿混匀、制粒,混合料经布料、点火后抽风烧结,烧结矿热破后进入环式冷却机冷却,与回收环冷散料经整粒分出部分10-20mm的烧结矿用作铺底料,小于5mm的冷返矿与回收烧结散料一起返回到配料室参加配料,5mm~10mm和大于20mm的做为成品矿直接由胶带运输机送往高炉或落地贮存。
3.铁矿石烧结(数据来源《技术处进厂原料内控标准》)3.1燃料3.1.1固体燃料:焦粉固定炭含量大于78%,含硫≤0.75%,灰份≤18%,含水≤10%,粒度小于40mm;3.1.2气体燃料:烧结机点火燃料为高炉煤气,热值约为3.2238MJ/m3,车间接点压力≥6000Pa,正常用量21201m3/h,最大用量26501 m3/h。
3.2熔剂3.1.1.2熔剂3.1.1.2.1白云石技术要求3.1.1.2.2生石灰技术要求3.1.1.3.含铁原料技术要求3.1.1.4氧化铁皮技术要求4、原料验收与供料进厂各种原燃料必须严格按公司有关规定,进行数、质量检验和验收。
并将检验和验收有关数据记入相关报表台帐内。
根据生产作业计划、现场原料库存量,及时组织进料工作。
上料工根据各配料矿槽铁矿粉、外矿粉、氧化铁皮、除尘灰、白灰粉、云石粉、焦沫的料位信息,及时组织向烧结供料。
265烧结机自动化控制方案

2.1 电控部分
1
原料系统: 原料系统:
当操作本系统的事故停止按钮,或使本系统的配料式输送 当操作本系统的事故停止按钮, 机停止运转、或使正在运转中的任意一台定量给料机停止运转 机停止运转、 必须同时停止所有的定量给料机和带式输送机。 时,必须同时停止所有的定量给料机和带式输送机。 因配料中原料品种改变, 因配料中原料品种改变,或因同一品种而必须变更配料仓 时,则要按一定的时间间隔顺序启停定量给料机,该时间间隔 则要按一定的时间间隔顺序启停定量给料机, 就是启、 就是启、停的定量给料机之间的距离与配料带式输送机运行速 度的比值。 度的比值。 安装了定量称量给料机的矿仓,当定量称量给料机上负荷 安装了定量称量给料机的矿仓, 低于设定值下限时,即启动振动器运转, 低于设定值下限时,即启动振动器运转,负荷恢复正常即停止 运转、振动器运转时,机旁开关须接通, 运转、振动器运转时,机旁开关须接通,且定量称量给料机要 处于运转状态。 处于运转状态。 矿仓下使用容积配料的圆盘给料机时, 矿仓下使用容积配料的圆盘给料机时,仓壁振动器则按 15~30min的时间间隔定周期振动 每次震动1~2min。 15~30min的时间间隔定周期振动,每次震动1~2min。 的时间间隔定周期振动,
HAIHUI automation
2.1 电控部分
顺序停止: 顺序停止: 1)在生产过程中停机时,为了把在设备上的物料 在生产过程中停机时, 都运走或排空、则把系统物料流动最上游的设备首 都运走或排空、 先停止,经过一定的时间间隔之后,待物料都运走 先停止,经过一定的时间间隔之后, 或排空,下游机群则同时停止。 或排空,下游机群则同时停止。 2)生产过程停机也可采用另一种顺序停止程序, 生产过程停机也可采用另一种顺序停止程序, 即停机时,先停物料流动最上游的给料设备, 即停机时,先停物料流动最上游的给料设备,并顺 物料流动方向,顺次序往下游停止各设备运转。 物料流动方向,顺次序往下游停止各设备运转。但 这种方式比1 要复杂。 这种方式比1)要复杂。
265m2烧结机一次混合机给料系统粉尘治理论文

265m2烧结机一次混合机给料系统粉尘治理【摘要】在烧结生产中,一次混合机是烧结生产工艺中的重要设备,它承担着对混合料进行润湿、混匀及制粒的重任,是当前进料系统普遍采用的皮带机-漏斗给料方式,使混合料的水分、粒度、料温及混合料的成分均匀分布并制粒,为烧结机提供适宜的混合料。
本文主要讲述了山东钢铁莱芜分公司炼铁厂265m2烧结机一次混合机给料系统存在的问题,主要是产生大量蒸汽和粉尘,现场环境恶劣。
针对当前状况分析,在综合分析的基础上进行了实施改造,有效改善了生石灰消化现场环境,实现了清洁生产。
【关键词】烧结机;混合机;给料系统0.前言圆筒混合机是烧结生产的一个主要设备,承担着重要的运输给料系统,是烧结机生产工艺中的重要设备之一。
在山东钢铁莱芜分公司炼铁厂生产中,一、二次圆筒混合机进料系统普遮采用皮带机一漏斗给料方式。
这种给料方式容易造成粉尘污染,不易控制,降低了烧结生产工艺的良性发展。
随着全球市场经济的快速发展,在烧结厂的烧结原料作业中,不论一次混合还是二次混合均选用圆筒混合机,随着烧结机向大型化方向快速发展,与之相配套圆筒混合机的规格也相应增大,结构也有了很大发展。
圆筒混合机混料原理新型圆筒混合机结构是由简体、滚圈、支承装置(包括托辊及轴承)、止推挡辊、传动装置、喂料与喷水装置、润滑装置、底座组成。
工作时能过运输机械(一般为皮带运输机)将由各种原料组成的混合料入混合机内.混合机筒体成倾斜安装,筒体回转时物料在摩擦力的作用下,随筒体回转方向向上运行,到一定高度,由于自重物料,又落下来,并沿筒体轴倾斜方向移动。
物料的颗粒在上升抛落的每一个循环过程中,具有不同的运动轨迹。
物料经过多次提升和抛落,在向排料端螺旋状前进的运动中,使物料中的各种成分及水分逐渐分布均匀。
在生石灰消化过程中,产生大量蒸汽和粉尘,现场环境恶劣,由于粉尘中含有cao成分以及水蒸汽,会造成布袋除尘器糊堵,电除尘器极板易挂泥导致腐蚀严重,除尘效果较差,因此对当前烧结机给料系统改造势在必行。
7月份265m2烧结生产技术分析总结

烧结分厂(20m2)烧结作业区7月份生产技术分析总结二、、生产指标完成情况分析:(1)、烧结矿产量。
6月26日-7月12日,烧结物料主要是混匀料,生产情况较好。
7月12日-7月26日,烧结物料中使用了配加20%含瓦斯灰的烧结料(主要是以瓦斯灰、返矿和除尘灰混匀的料)。
由于返矿、瓦斯灰和除尘灰只混了一遍,混匀效果不好,给烧结配碳量的操作带来了很大难度。
在配碳量不变的情况下,烧结矿亚铁含量在 6.5——11.9%之间波动。
而且有时候将配料配碳量调至最小300克(7月30日配料做工作后可降至200克),在烧结机机尾断面观察,焦炭依然较大,已经无调节手段,这都对烧结矿产量、转股指数和亚铁含量的控制都产生了很大难度,烧结矿产量较前期下降了约90吨/天。
针对这一系列难题,烧结作业区采取了相应的对策,从管理、操作技术上克服生产困难,一是加强培训,对职工进行布料和焦炭加减以及焦炭判断岗位培训和现场示范性培训,进一步提高操作工实际操作能力;二是针对瓦斯灰混匀程度,制定焦炭过大的应对措施;三是加强管理,控制加减料次数,减少生产波动,目前加减料次数基本控制在4次以内;四是加强布料和料层控制,保证布料平整,料层厚度基本控制在370-410mm,较6月份提高了约60mm;五是加强信息沟通,要求看火工及时和配料、制粒工的信息沟通,稳定水、碳。
通过一系列措施,对稳定烧结生产起到了积极作用,7月份各项生产指标均完成计划任务。
三、目前存在的问题:1、7月份由于按照分公司生产技术科要求,配加瓦斯灰组织生产。
但是由于瓦斯灰、返矿和除尘灰只混了一遍,混匀效果不好,烧结过程中焦炭控制难度虽有改善,但没有根本解决,没有消除瓦斯灰对生产的不利影响。
2、自7月26日停用造球盘后,特别是第一周,水分控制差,不但影响了产量,而且由于物料忽干忽湿,台车糊炉箅子现象严重。
截止8月2日,作业区已经组织将炉箅子糊的严重的2#烧结机台车炉箅子全部清理。
目前物料水分较前期控制有所好转。
烧结生产线工艺流程
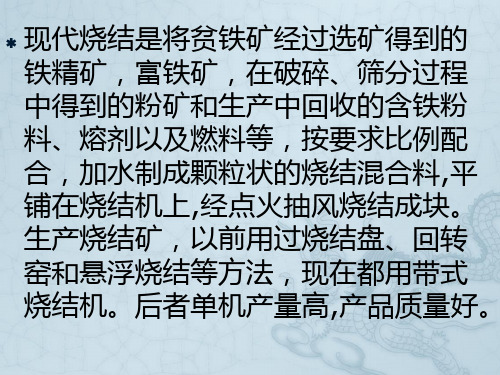
固体燃料
无烟煤是煤中固定碳含量最高, 挥发份最少的煤。对固体燃料 化学成分要求:固定碳含量高, 灰分、挥发份、含硫低。
固体燃料的运输及破碎
265m2烧结机使用燃料由原料 厂通过皮带机运至烧结区域燃 料破碎室料斗内,经电子皮带 秤直接拖出供三台Φ900×700 四辊破碎机破碎,成品由皮带 机运至配料室。
灰尘由仓式泵气力输送至灰尘仓。
配料室排料系统
混匀矿采用Φ2800圆盘给料机 排料,配料电子秤称重;
燃料和熔剂及冷返矿直接用配 料电子秤拖出;
生石灰的排料、称量及消化通 过叶轮给料机、螺旋秤及消化 器完成。
配料室排料系统
灰尘经叶轮给料机、螺旋、加 湿机、配料电子秤称重;
以上几种原料按设定比例经称 量后给到混合料的胶带机上, 送往一次混合室。
二次混合机为了提高混合料温度, 混合机配一套蒸汽预热装置。
混合机组成
根据烧结工艺的要求,该设备配 有一套喷水装置,以保证物料达 到一定湿度,从而有利于混合和 造球。为了便于观察物料混合情 况,给水法兰设置在排料端,给 水阀门由烧结工艺配置,用来调 节给水量的大小。
烧结室
烧结机的有效抽风面积为 265m2,台车宽度3.5m,栏 板 高 度700mm。经点火炉点 火后开始烧结,烧结终结的热 烧结饼经机尾卸至 Φ2000×3740mm的单辊破碎 机。
配
料
配料是按烧结矿的质量指标要求和 原料成分将各种烧结料按一定比例 配合在一起的工序过程。
265m烧结机采用单列配料室,共 设14个矿槽(为称重矿槽),其中 混匀矿5个、灰尘仓1个、冷返矿2 个、燃料2个、石灰石2个、生石灰 2 个。
配料
配料目前一般有两种方法,即容 积配料法和质量配料法。
265烧结机说明书

265m2带式抽风烧结机技术说明书甘肃酒钢集团西部重工股份有限公司技术中心2010年9月甘肃酒钢集团西部重工股份有限公司技术中心目录1、技术性能参数----------------------------------32、主要结构及特点--------------------------------43、安装要求--------------------------------------124、操作、维护及检修------------------------------145、易磨损零件表----------------------------------20甘肃酒钢集团西部重工股份有限公司技术中心1、技术性能甘肃酒钢集团西部重工股份有限公司技术中心2、主要结构及特点烧结机是烧结车间的主要设备之一,它由给料系统、驱动装置、台车、风箱及端部密封装、尾部移动装置、骨架及辊道等主要部件组成,以下介绍烧结机主要结构及特点。
2.1 给料系统给料系统位于烧结机头部、铺底料料槽、混合料料槽固定在厂房梁上,中间料槽则固定在头部骨架上。
给料系统主要由篦条压辊,铺底料装料装置、混合料给料装置、九辊布料器、疏料装置、料层厚度控制装置和平料装置等组成。
2.1.1篦条压辊为使布料前台车上篦条平整和铺底料厚度均均,台车进入水平段后篦条压辊将篦条压平,然后进入给料段。
2.1.2铺底料给料装置铺底料装置含铺底料料槽、中间料槽、摆动漏斗等部件。
铺底料料槽有效容积50m3可装料约90t,料槽为钢结构焊接件。
经筛选后合格的铺底料由皮带机送入料槽,料槽一侧用铰接支在厂房梁上,另一侧通过压力传感器支在厂房梁上,通过压力传感器反映料槽内的料量,以控制皮带机,对该料槽给料。
中间料槽位于铺底料料槽与摆动漏斗之间起过渡作用。
中间料槽设有扇形闸门,由手动蜗轮操纵闸门的开口度,控制料流量。
甘肃酒钢集团西部重工股份有限公司技术中心摆动漏斗位于台车上方,悬挂安装在头部骨架上,上接中间料槽。
最终265烧结机施工方案

2#265㎡烧结机纠偏、更换机头弯轨及链轮齿板施工方案建设单位意见:批准:审核:编制:莱钢建设建筑安装分公司机电工程部2014年6月21日目录一、编制依据 (3)二、工程概况 (3)三、施工安排 (3)四、施工进度计划 (4)五、施工准备与资源配置计划 (4)六、施工方法及工艺要求 (6)七、质量管理计划 (11)八、安全管理计划 (11)九环境管理计划 (13)2#265㎡烧结机纠偏、更换机头弯轨及链轮齿板一、编制依据编制依据明细表二、工程概况烧结机现运行多年来,跑偏严重,主要是头轮齿板磨损、压溃严重;机头、机尾弯道磨损,偏离安装尺寸;移动摆架移动不畅;烧结机台车存在尺寸累积误差;水平轨及尾部弯道都有不同程度的磨损等问题。
2#烧结机弯轨冲击和磨损现象严重,台车在运料过程中在转弯处经常发生碰撞,弯道的磨损超过局部已超过20mm,且根据烧结机技术要求弯道磨损超过5mm应报废。
头轮齿板经现场测量发现南面链轮齿板的磨损已达到20mm,北面链轮齿板的磨损已达15 mm,根据技术要求链轮齿板磨损达到5mm应报废。
故机头弯轨及链轮齿板均需更换,同时设备安装完成后精度的调整是重点。
三、施工安排四、施工进度计划五、施工准备与资源配置计划5.1施工人员计划为了保证施工顺利完成,并做到安全文明施工,我单位组织技术水平高、经验丰富的职工进行施工,成立施工领导小组,实行统一指挥,合理组织,确保施工任务保质保量完成。
5.2 施工机具计划主要施工机具表六、施工方法及工艺要求6.1准备工作(1)、机具、备件清点倒运到现场:轨道、螺栓、垫片、支座、加固用钢板、测量用钢管和机具等。
(2)、烧结机台车吊出,设置挂设中心线支架。
6.2烧结机纠偏1、基准线的定位由于原施工时的定位基准不好查找,同时跑偏严重,应重新定位烧结机中心线。
中心基准的定位有两种方法,一是以头尾链轮两侧齿板间对称中心作烧结机的纵向中心线;二是风箱上部固定滑道底座的中心线。
唐钢265烧结机[1]
![唐钢265烧结机[1]](https://img.taocdn.com/s3/m/b89cd8d6c1c708a1284a44fe.png)
唐钢265m2烧结机工艺设计及设备特点范勤芳(唐山钢铁公司设计研究院) 摘 要 介绍了唐钢265m2烧结机的工艺和设备特点。
主要包括:成品整粒系统改造、取消热矿振动筛、余热回收系统及设备改造的特点。
关键词 烧结机 工艺 设备1 前 言 唐钢烧结厂原有2台180m2烧结机,年生产能力约342万t,是唐钢二铁厂两座1260m3高炉配套建设的项目。
随着二铁厂2560m3高炉的投产(已于1998年9月26日投产出铁),三座高炉烧结矿的消耗量达594万t a。
烧结厂的生产能力远远不能满足高炉的需要。
为此,新建了一台265m2烧结机,作业率90.4%,利用系数为1.2t (m2・h)设计能力为251.86万t a。
265m2烧结机的设计宗旨为:不新征地,在现有烧结厂区内进行,尽量利用原有设施及设备,以降低工程投资;装备水平不低于现有的两台180m2烧结机。
2 工艺设计的主要特点2.1 成品整粒系统改造265m2烧结机不再建设新的成品整粒系统,将原有1号、2号烧结机的整粒系统进行改造,使其满足三台烧结机的需要。
1)改造前整粒系统状况原有2台180m2烧结机整粒系统均设有冷破碎和4级筛分。
二、三、四次筛分均采用2.5×8.5m冷矿振动筛,且均为双列布置,一个系列生产,一个系列备用。
2)1号烧结机整粒系统改造 对1号烧结机整粒系统进行改造的目的是供收稿日期:1999—07—01 联系人:范勤芳(063000)河北 唐山钢铁公司设计研究院265m2烧结机使用。
将其中一个系列的三台2.5×8.5m冷矿振动筛改为3.0×9.0m冷矿振动筛,另一个系列不变。
正常生产时以改造的系列为主,原有2.5×8.5m冷矿振动筛系列备用。
3)2号烧结机整粒系统扩建扩建2号烧结机成品整粒系统的№1a、№2a 冷矿筛分室,以满足原有1号、2号烧结机成品整粒系统的需要。
充分利用旧有设备,将更换下来的三台2.5×8.5m冷矿振动筛作为原有1号、2号烧结机整粒系统的一个系列,使之构成三个系列,两个系列生产,一个系列备用。
265m2烧结机-皮带

一、原料管理班1、铁料接受:为了满足烧结生产的用料需求,各种含铁原料在原料场按比例配矿混匀后,以单一品种混匀矿用带式输送机运往配料室,并通过B=1200重型移动卸矿车分别向混匀矿槽给料。
为了保证生产的稳定顺行,保证配料当发生临时性设备故障时与生产不相互干扰,配料室共设置五个混匀料仓,每个料仓的容积是325m3,正常生产时使用三个料仓下料,另外两个做为备用料仓。
为了提高料仓的使用寿命及仓内下料料流的顺畅,在料仓的锥形部分镶有衬板,衬板的材质为含油尼龙。
铁料接受所属的设备其技术规格如表1-2等所示。
表1-4 B=1200重型卸矿车性能及技术参数表2、熔剂受矿槽:熔剂包括白云石和生石灰两种原料。
生产中熔剂的加入不仅能使烧结矿获得一定的碱度,而且在强化烧结的过程中它起着关键性的作用。
熔剂受矿槽主要接受3—0mm的白云石,采用自卸汽车卸料。
为了满足生产的需要,共设4个容积为25m3矿槽,矿槽内镶有含油尼龙衬板。
通过矿槽下部的GZG80-140F型振动给料机进行卸料,并由PL-8皮带机将其送往配料室的熔剂矿槽。
熔剂受矿槽所属的设备其技术规格如下表:表2-3 GZG80-140F振动给料机设备性能及技术参数表3、焦粉、白云石粉接受:确保入厂白云石粉、焦粉的质量和数量符合烧结生产要求。
4、无烟煤接受:固体燃料是生产的重要保障,它的是否连续供应直接关系着生产的稳定顺行。
为了满足生产的需要,无烟煤接受共设三个料仓,每个料仓的容积为124 m3,燃料由汽车运至燃料受矿槽,燃料进料粒度为15—0mm 。
料仓内壁镶有含油尼龙衬板。
料仓里的燃料将通过两条胶带机运往燃料破碎室进行破碎,破碎后将供应生产需要。
其所属设备技术规格如下表所示:表4-3 RP-2皮带机性能及技术参数表二、1、混匀矿圆盘给料机:为了保证和稳定烧结生产的各种质量技术指标,保证混匀矿、熔剂、燃料的正常配比下料,混匀矿采用Φ2800圆盘给料机给料,并经配料电子秤称重;燃料、熔剂及冷返矿直接用配料电子秤拖出;生石灰的排料、称量及消化通过叶轮给料机、LXG-H-400螺旋秤及消化器完成;灰尘经叶轮给料机、螺旋给料机、DSZ-80加湿机、配料电子秤称重,以上几种原料按设定比例经配料室的自动控制系统称量计算后输送到混合料的胶带机上运往一次混合室进行混匀。
265 m2烧结机主传动系统更换

265 m2烧结机主传动系统更换摘要:烧结机主传动系统改造,对关键工序涨紧环无键连接新技术的应用进行详细解说。
对各主传动各轴承采用多点自动润滑系统,效果良好。
关键词:涨紧环悬挂减速机润滑某265m2烧结机主传动悬挂减速机运行多年后,小齿轮打齿、大齿轮磨损严重,需进行更换。
在传动形式上,进行了改造,由原先的电动机-定转矩联轴器-减速机-万向轴-平面二次包络蜗杆减速机(左、右)-悬挂减速机改为现在的两个调频电动机-PR减速机(左、右)-慢速悬挂减速机,总功率保持不变。
1、265m2烧结机涨紧环主要构造及工作原理265m2烧结机的头轮主轴与柔性传动装置的大齿轮连接,采用3组涨紧环组合使用的大型涨紧环装置,其一组涨紧环的主要规格如下:型号:Z5 400*495(JB/T 7934-1999)规格:内径φ400mm、外经φ495mm、环体宽度187mm传递转矩:最大535N.m传递轴向力:最大2670KN涨紧环与轴接触压力(p):158MPa涨紧环与轮毂接触压力(p’):高强螺栓紧固力矩(M):930N.mZ5型涨紧环的构造见图1,它由内环、前外环、后外环及前锥形环、后锥形环5部分所组成。
内、外环用弹簧钢经验各热处理及磨光加工制成、每个环上都有一个开口处,类似活塞涨圈,当夹紧开口处闭合后才能装入。
2、安装程序及方法2.1清洗大齿轮与轴颈在安装涨紧环以前,将大齿轮及轴颈全部清洗干净,仔细检查各个部位,用油石打磨干净各种小毛刺及尖角,清洗后用四氯化碳对轴颈及齿轮孔内作脱脂处理。
2.2检查主轴及大齿轮孔的装配尺寸设计规定轴为400h7,公差为0/-0.057mm,孔为400H8,公差为+0.089/0mm,其最大间隙仅0.146mm,实测结果平均间隙为0.14~0.15mm,此间隙是比较小而紧的。
2.3吊装大齿轮大齿轮重量为5.8t,安装时用4个手拉葫芦吊装(见图3),上部用1号手拉葫芦(10~15t)起吊,在上方用2号手拉葫芦(5~10t)作为平衡链,另外2个(3、4号)手拉葫芦(每个3~5t),向头轮侧同时拉动,所有在大齿轮上的绑扎部位都用麻布及木块保护。
- 1、下载文档前请自行甄别文档内容的完整性,平台不提供额外的编辑、内容补充、找答案等附加服务。
- 2、"仅部分预览"的文档,不可在线预览部分如存在完整性等问题,可反馈申请退款(可完整预览的文档不适用该条件!)。
- 3、如文档侵犯您的权益,请联系客服反馈,我们会尽快为您处理(人工客服工作时间:9:00-18:30)。
建龙265m2烧结机工艺梳理建龙烧结项目部建龙烧结厂2009年2月9日目录第一章工艺概述第二章一次上料及燃料破碎第三章配料第四章混合、制粒第五章烧结第六章冷却第七章整粒筛分第八章主抽风机、电除尘第九章布袋除尘第十章气力输灰第十一章水泵站第十二章水处理间、余热利用附件1:烧结机系统起重设备性能参数第一章 工艺概述1、本资料统计围:建龙烧结厂265m 2烧结作业区管辖区域。
2、工艺流程2.1整个烧结系统分为配料、混料、烧结、环冷、风机、除尘6个作业工作区域。
如图所示一次冷筛分二次冷筛分5-10mm图2-1 工艺流程图抽风烟囱排入大气<5mm<10mm 10-20mm成品烧结矿上高炉>20mm散料和灰尘配 料混 合制 粒烧损电除尘灰尘冷却烧 结热破碎点火空气煤气<3mm生石灰<3mm<5mm灰尘冷返矿<3mm轻烧白云石铺底料蒸汽水<20mm <3mm细破碎粗破碎<8mm<8mm 一 次 配 料<8mm 燃料0-40mm铁矿粉杂料滚燃料2.2 烧结工艺有一次含铁料受料、燃料破碎、配料、混合、外滚燃料制粒、烧结、冷却、成品整粒、抽风除尘和冷返矿循环等组成;2.3 含铁料、燃料、熔剂、除尘灰和冷返矿经配料和混合后,通过两段混合机进行润湿混匀、制粒,混合料经布料、点火后抽风烧结,烧结矿热破后进入环式冷却机冷却,与回收环冷散料经整粒分出部分10-20mm的烧结矿用作铺底料,小于5mm的冷返矿与回收烧结散料一起返回到配料室参加配料, 5mm~10mm和大于20mm的做为成品矿直接由胶带运输机送往高炉或落地贮存。
3. 铁矿石烧结(数据来源《技术处进厂原料控标准》)3.1 燃料3.1.1 固体燃料:焦粉固定炭含量大于78%,含硫≤0.75%,灰份≤18%,含水≤10%,粒度小于40mm;3.1.2气体燃料:烧结机点火燃料为高炉煤气,热值约为3.2238MJ/m3,车间接点压力≥6000Pa,正常用量21201m3/h,最大用量26501 m3/h。
3.2熔剂3.1.1.2熔剂3.1.1.2.1白云石技术要求3.1.1.2.2生石灰技术要求3.1.1.3.含铁原料技术要求3.1.1.4氧化铁皮技术要求3.1.5 高炉返矿:高炉返矿粒度大于5mm部分≤10%。
4、原料验收与供料进厂各种原燃料必须严格按公司有关规定,进行数、质量检验和验收。
并将检验和验收有关数据记入相关报表台帐。
根据生产作业计划、现场原料库存量,及时组织进料工作。
上料工根据各配料矿槽铁矿粉、外矿粉、氧化铁皮、除尘灰、白灰粉、云石粉、焦沫的料位信息,及时组织向烧结供料。
杜绝出现亏、错、混、断、溢料现象。
5、原燃料的储存与使用各种原料必须严格按指定位置卸料储(堆)存,严禁混料。
同类、同品种原料,化学成份差别较大的原料,堆与堆之间必须有明显的分界线,不允许搭界堆放。
必须严格按生产计划(配比)用料,不得任意停用或大幅度调整原燃料用量或配比。
变更用量须报请技术中心批准或由技术中心下达。
确因工作需要,某个矿槽需更换另一品种物料时,必须将矿仓的物料用空以后,方可进另一种物料。
保持各矿槽料位在1/3~2/3。
上料工要掌握生产用料情况,经常观察矿槽料位变化,发现仓存料低于1/3,要及时通知汽车(铲车)供料,防止因亏料而影响生产。
注:料场面积(准等腰梯形):(上底66.8m+下底112.6m)×高154.3m÷2=14612m2折21.9亩6、烧结矿技术标准第二章一次上料及燃料破碎1.工艺方法1.1 一次受料系统汽车受矿槽主要接受来自汽车卸料的含铁原料及杂料,采用Ф2800mm圆盘给料机给料,并进行一次受料(各料种单一运输),给到主运输胶带机上通过移动可逆胶带机向各配料矿槽给料;1.2 燃料受矿槽和破碎室燃料受矿槽主要接受来自汽车卸料的焦粉,通过大倾角胶带机运至破碎系统分配仓(2个)。
燃料破碎室设有二个燃料破碎系统,同时进行燃料粗破碎和细破碎。
燃料采用对辊粗碎与四辊细碎组成的开路破碎系统,以保证获得合格的成品粒度,共2个系列,从而保证作业率。
粗、细破碎均布置在本工序,每个系统能力为40~45t/h。
,每个仓下设有给料闸门、给料胶带机和电磁除铁器,将需破碎的燃料给至2台Φ1200×1000对辊破碎机,进行粗破碎,将燃料破碎至12~0mm。
每台对辊破碎机下有一条胶带机,将经过粗破碎的燃料给至Φ1200×1000四辊破碎机,进行细破碎,燃料破碎至3~0mm。
3~0mm合格燃料由胶带机分别送至配料室燃料配料槽和外滚燃料及制粒室燃料矿槽。
矿槽上均采用固定可逆胶带机向各配料槽给料。
燃料破碎系统有一台出现故障,可以使用另一台组织生产;1.3生石灰和轻烧白云石采用外设压缩空气将汽车罐车送来的生石灰和轻烧白云石送至配料矿槽;1.4 冷返采用皮带运输到2个配料矿槽;1.5自循环灰尘采用气力输送方式运输到2个配料矿槽。
2.技术要求2.1 一次受料系统一次受料运输皮带运输能力为800t/h,上料时按照配料各料种需求保证用料平衡。
2.2 燃料破碎系统2.2.1 进入对辊破碎机的焦粉粒度小于40mm;2.2.2 给料量适当,满足破碎粒度质量要求;2.2.3 四辊破碎后粒度要求达到3mm以下,合格率达到90%(可调)以上;2.2.4 粒度达不到要求时,应及时车辊或更新辊皮。
3. 主要设备性能参数3.1 一次受料矿槽(10个):仓容50m3/个;3.2 汽车受矿槽Ф2800mm圆盘给料机设备技术参数见表1;3.3 一次受料运输皮带(H-2):运输能力800 t/h,皮带宽度1.2m、带速1.60m/s、全长463m、配用电机功率160kW;3.4 一次燃料受料矿槽(2个):仓容34.8m3/个(已核实的数据);对辊下料仓容积0.7m3、四辊下料仓容积1.16m3;3.5 破碎系统分配仓:每个仓有效容积为150m³;3.6 燃料用永磁带式除铁器技术参数表2;3.7 Φ1200×1000对辊破碎机见表3;3.8 φ1200×1000四辊破碎机见表4。
Φ1200×1000对辊破碎机表3第三章配料1.工艺方法含铁料、燃料、熔剂、冷返矿、除尘灰在配料室集中配料后送至一次混合机。
铁粉和杂料采用Φ2500圆盘给料机排料,配料电子秤称重;燃料和冷返矿直接用配料电子秤拖出;灰尘和生石灰、轻烧白云石采用配料电子秤及加湿器消化器完成。
以上几种原料按设定比例经称量后给到配合料的胶带机上。
2.技术要求2.1 配料要求2.1.1 采用自动配料时,电子称精度不得低于0.5%,下料量误差不得超过1%。
具体参数:含铁料±1.0kg/m;焦粉±0.05kg/m;熔剂±0.5kg/m;槽返±0.5kg/m;2.1.2 每2小时对含铁料下料量校定一次,每1小时对焦粉、熔剂下料量校定一次检查自动配料系统称量误差,超出围时,应及时查明原因处理;2.1.3矿槽存量应在1/2以上;2.1.4 由作业区根据原料性质及生产要求确定配料方案(包括上料料层、熔剂配比、燃料配比等);2.1.5 在正常生产时,根据看火岗位的要求,调整燃料用量;2.1.6 根据原料成份变化和烧结矿碱度波动,及时调整熔剂(白云石、生石灰)上料量;2.1.7 生石灰加水提前充分消化(打成潮泥状),配料粉尘和白云石加湿机加水标打潮即可;2.1.8根据槽存平衡稳定使用冷返矿(料仓料位控制在30%~80%);2.1.9调整返矿时,应适当调整燃料用量;2.1.10上料、缓料时,料头、料尾对齐;2.1.11正常生产产能控制围7500~7800t/d,料批kg/m、小时上料量可利用计算公式自行推出料批kg/m=上料量kg/(3600s×皮带转速m/s);2.1.12 配料计算公式2.1.12.1 混合料成分计算①各种原料代入成分干配比=湿配比×(1-水分%)TFe =干配比×TFe%SiO2 =干配比×SiO2%CaO =干配比×CaO%MgO =干配比×MgO %残存=干配比×(1-烧损%)注:烧损即某种物料在烧结过程中氧化增重或二氧化碳、水等成分的散失。
②混合料成分计算混合料成分为各各种物料代入成分之和残存 =∑残存物料 Tfe =∑TFe量SiO2 =∑SiO2量 CaO =∑CaO量2.1.12.2 配料计算①首先计算出已知配比各料的干配比、残存,化学成分同上,但计算燃料代入SiO2、CaO时注意以下问题:SiO2 =湿配比×(1-H2O%)×Ac×50%CaO =湿配比×(1-H 2O%)×Ac ×16% 残存=湿配比×(1-H 2O%)×Ac注:如不特给燃料灰分(Ac )中SiO 2、 CaO 比例,按SiO 2、 CaO 为50%、16%计算,残存按SiO 2的二倍计算。
② 计算出白灰有效CaO 和配比白灰干配比 =)H2O%1(CaO CaO -R SiO2-⨯⨯∑∑有效注:白灰有效CaO :即是根据烧结矿碱度要求扣除中和本身SiO 2后,剩余的CaO 含量,其表达式为:CaO 有效 =CaO -R ×SiO 2式中CaO 、SiO 2是熔剂中的含量。
③烧结矿各成分计算烧结矿Tfe =残存∑TFe R =残存烧结矿残存烧结矿÷÷SiO2CaO④白灰配比差计算公式 白灰配比差(%) =有效差值)差值(配比调整值CaO CaO R SiO ∑∑-⨯⨯2(适用配比变化)白灰配比差(%) =新有效矿矿新CaO CaO SiO R -⨯2 (适用碱度变化)白灰配比差(%) = 有效差差CaO CaO SiO R ∑∑-⨯2 (适用成分变化)3.主要设备性能参数3.1配料矿仓设备性能参数见表1。
3.2 铁矿粉及杂料配料电子秤主要技术参数:3.2.1 胶带宽度:1000mm;3.2.2配料秤长度:3055mm(头尾轮间距),下料点距尾轮800mm;3.2.3 电动机功率:~4.0kW(可由制造厂确定)不调速;3.2.4物料堆比重:2.0~2.2 t/m33.2.5 物料水分:~8%3.2.6称量围:10~180t/h3.2.7给料方式:圆盘给料机给料3.2.8数量:7台3.2.9称量精度:在额定量程10-100%围为实际给料量的±0.5%3.3 燃料配料电子秤主要技术参数:3.3.1胶带宽度:800mm3.3.2配料秤长度:3055mm(头尾轮间距),下料点距尾轮800mm3.3.3电动机功率:~3.0kW(可由制造厂确定) 变频调速3.3.4物料堆比重:0.8~1.0t/m33.3.5物料水分:~10%3.3.6称量围: 3~30t/h3.3.7给料方式:给料闸门拖料3.3.8数量:2台3.4 冷返矿配料电子秤主要技术参数:3.4.1 胶带宽度:1000mm3.4.2 配料秤长度:3055mm(头尾轮间距),下料点距尾轮800mm3.4.3 电动机功率:~4.0kW(可由制造厂确定)变频调速3.4.4 物料堆比重:1.7t/m33.4.5 物料水分:03.4.6 称量围: 50~180t/h3.4.7 给料方式:给料闸门拖料3.4.8数量:2台3.5 生石灰、白云石、灰尘全密封式配料电子秤主要技术参数:3.5.1 胶带宽度:1000mm3.5.2 配料秤长度:3055mm(头尾轮间距),下料点距尾轮800mm3.5.3 电动机功率:~4.0kW(可由制造厂确定)变频调速3.5.4 物料堆比重:1.0 t/m3 (生石灰)、1.6 t/m3(白云石)、1.7 t/m3(灰尘) 3.5.5 称量围: 10~65t/h3.5.6 给料方式:给料闸门给料3.5.7 供货数量:5台3.5.8 36袋压力式仓顶除尘器技术参数见表2型号:BXHS-500(非标)型;生石灰消化能力:20t/h;消化效率:95%;型式:双轴结构;介质:生石灰;进口物质:生石灰,出口物质:消石灰;电机型号:Y2-160M-4 11KW 380V;减速机型号:ZQ40-40-IV-Z;水压要求:>0.25Mpa,50~60℃;生石灰输送用压气:压气量:60m /min,压力:0.5~0.6MPa;生石灰消化用水:最大耗水量:20t/h;供货数量:3台;安装地点:配料室;快速加热器:数量1套。