大锻件 第4部分 锻造用钢锭及铸锭技术
第一章锻造用原材料准备

利用高速旋转的砂轮片与坯料之间发生剧烈的摩擦并产生高热 使金属软化甚至局部溶化,在磨削作用下切断坯料。
下料特点:小尺寸坯料,设备简单,操作方便,下料长度精确, 却面平整,无毛刺及斜口,切割不受坯料硬度显著,但砂轮片消 耗较大。
砂轮锯结构
F
电机功率:5~10KW
锯片线切割速度50~60m/s
砂轮片厚4~6mm
三、钢锭的主要缺陷 五种
1.偏析 1)定义:钢锭各处成分和杂质分布不均匀的现象。
分为枝晶偏析和区域偏析。
2)偏析消除 区域偏析:反复镦粗-拔长。 枝晶偏析:锻造、再结晶、高温扩散、锻后热处理消除。
2.夹杂 1)定义:不溶解于金属基体的非金属化合物,称之为
夹杂。常见的夹杂物主要有硫化物、氧化物、硅酸盐等。
3.气体 钢中常见的气体主要有:氧、氢、氮等。其中氧与
氮以其化合物形式存在,钢液中气体含量较多时,会形成 气泡。
氢的危害最为严重,含量较高形成白点和氢脆缺陷。 减轻钢中气体含量措施:加强脱氧、炉外精炼、真空除气。
4.缩孔和缩松 缩孔的形成:收缩引起,得不到补缩时变产生缩孔或 缩松。 减轻的措施:设计冒口、增加变形量及其锻比。
中心等轴晶区 表面细等轴晶游离,枝晶熔断, 液面上凝壳晶体的沉积形成。
3.存在三个不 均匀性
物理性能不均匀:缩孔、气孔、裂纹 结晶组织不均匀:粗细不均 化学成分不均匀:偏析
表面清理:打磨溅疤等表面缺陷。
4.钢锭清理
碳钢 冒口占钢锭18~25%。
切除冒口和底部
底部占钢锭5~7%
合金钢 冒口占钢锭25~30%。 底部占钢锭7~10%
1-1 锻造用钢锭及型材 一、模铸钢锭的内部结构
冒口区:占钢锭重量18~25%。 1.结构组成 锭身区:有用部分。
冶金工程概论4连铸部分
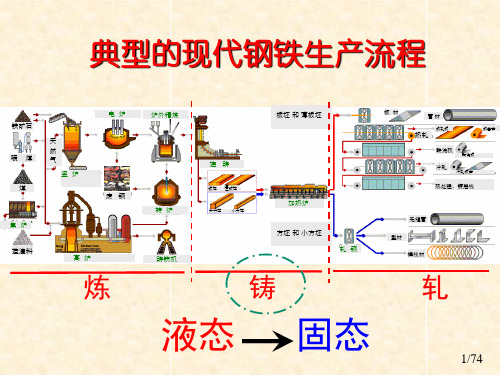
结晶器的振动:
结晶器的上下往复运行,“脱模” 的作用。 坯壳与铜板间的粘附力因结晶器振动而减小,防止了在
初生坯壳表面产生过大应力而导致裂纹的产生或引起更 严重的后果。 当结晶器向下运动时,因为“负滑脱”作用,可“愈合” 坯壳表面裂痕,并有利于获得理想的表面质量。 根据结晶器振动的运动轨迹将振动方式分为非正弦振动 和正弦振动两大类。
保护渣粘度测定方法
1. 将配制好的保护渣粉末混匀。 2. 将炉温恒定在1350℃,称取140g渣料加入
坩埚,10min后渣料均匀熔化; 3. 将Mo转头下降到熔渣表面充分预热; 4. Mo转头下端距离石墨坩埚底部10mm,搅
拌一段时间,使炉渣尽可能均匀; 5. 以5℃·min-1的速度降低炉温,将测得频率
5. 角部的传热为二维,开始凝固最快,最早收缩,最
早形成气隙。角部的传热始终小于其他部位,致使
角部区域坯壳最薄,这也是产生角部裂纹和发生漏
钢的薄弱环节。
28/74
连铸工艺和设备
29/74
钢包回转台
将从精炼跨接受的钢包回 转到浇注跨,为连铸机提 供钢水,实现多炉连浇, 提高连铸机作业率。
由底座、回转臂、驱动装 置、回转支撑、事故驱动 控制系统、润滑系统和锚 固件6部分组成。
[1] 覆盖钢水绝热保温; [2] 隔绝空气,防止钢水二次氧化; [3] 吸收上浮到钢渣界面上的非金属夹杂物; [4] 降低拉坯阻力,润滑铸坯和结晶器作用; [5] 流入坯壳和结晶器间隙内的液态渣形成
渣膜,以控制铸坯向结晶器传热速度, 保持坯壳均匀生长。
21/74
保护渣的渣层结构
纵向渣层结构:
➢绝热保温 ➢防止钢液二次氧化 ➢吸收夹杂物
与零点频率值比较得到保护渣粘度数值; 6. 系统连续采集数据即可得到粘度-温度曲
大型锻件锻造工艺过程

大锻件一般应用在大型机械的关键部位,由于工作环境恶劣,受力复杂多变,因此,在生产过程中对大型锻件的质量要求很高。
大锻件由钢锭直接锻造成形,生产大型锻件时,即使采用最先进的冶金技术,钢锭内部也不可避免存在微裂纹、疏松、缩孔、偏析等缺陷,严重影响锻件的质量,为了消除这些缺陷,提高锻件质量,就必须改进锻造工艺,选用合理的锻造工艺参数。
大锻件锻造不仅要满足所需零件形状和尺寸,而且重要的是破碎铸态组织、细化晶粒、均匀组织、锻合缩孔、气孔和缩松等缺陷,提高锻件内部质量。
钢锭尺寸愈大,钢锭中的缺陷也愈严重,锻造改善缺陷愈困难,进而增加了锻造难度。
在锻造过程中,镦粗和拔长是最基本的工序,也是不可缺少的工序,对于具有特殊外形的锻件来说,胎模锻造也较为常用。
一、镦粗工艺在大型锻件的自由锻生产中,镦粗是一个非常主要的变形工序。
镦粗工艺参数的合理选择,对大锻件的质量起着决定性的作用。
反复的镦拔不但可以提高坯料的锻造比,同时也可以破碎合金钢中的碳化物,达到均匀分布的目的;还可以提高锻件的横向力学性能,减小力学性能的异向性。
大型饼类锻件和宽板锻件都是以镦粗为主要变形,且镦粗的变形量很大,但是目前该类锻件的超声波探伤废品率很高,主要因为内部出现了横向内裂层缺陷,然而现行的工艺理论对此不能解释。
为此,从90年代开始,中国学者经过长时间的认真研究,从主变形区以及被动变形区理论出发,对镦粗理论进行深入研究。
提出了平板镦粗时刚塑性力学模型的拉应力理论以及静水应力力学模型的切应力理论,与此同时还进行了大量的定性物理模拟实验,并利用广义滑移线法和力学分块法来求解分析工件内部的应力状态,大量数据证明了该理论的合理性和正确性,揭示了利用普通平板镦粗圆柱体时其内部应力的分布规律,进而提出了锥形板镦粗新工艺,建立了方柱体镦粗的刚塑性力学模型。
二、拔长工艺拔长是大型轴类锻件锻造过程中必须的一道工序,也是影响锻件质量的主要工序,通过拔长工序使坯料截面积减小,长度增加,同时也起到打碎粗晶、锻合内部疏松与孔洞、细化铸态组织等作用,从而获得均质致密的高质量锻件。
锻造知识培训讲义

锻造知识培训讲义§钢锭知识及钢锭冶炼1、钢锭是将冶炼钢液在一定温度下注入钢锭模中凝固而成的。
钢锭的形状通常是截头锥体,上部较大,下部较小,截面形状有方形、圆形、扁方形、多角形。
其结构及内部组织如下图。
缩孔正偏析形偏析倒形偏析负偏析在冒口部位,一般有缩孔、疏松等冶金缺陷;在锭身部位从外向内有细晶粒层、柱状粗晶和等轴粗晶;在底部有夹渣物沉积(主要是密度较重的金属和非金属夹渣物)。
由于钢锭冒口和底部存在严重的缺陷,不能作为锻件的一部分,对于冲大孔后芯棒拔长和扩孔锻件,底部可以适当利用。
2、钢锭的冶金缺陷缩孔:钢锭凝固后,在上端形成的孔洞及缩管;主要由于钢锭在冷凝收缩时钢液不足补缩不良造成的,锻造切除不干净会形成裂缝与折叠;减小和消除的措施主要是采用发热冒口、绝热冒口、改善钢液补缩条件,使缩孔上移到冒口处,锻造时切除。
疏松:钢锭中上部海绵状组织结构,包括中心疏松和一般疏松;主要由于钢锭在冷凝晶间冷缩形成的显微空隙与针孔,此处夹杂聚集力学性能较差;减小和消除的措施提高加热温度,通过锻造压实。
枝晶偏析(微观树枝状偏析):树枝状晶与晶间物理、化学及杂质分布的不均一性;主要由于钢锭在冷凝时的选择性结晶及溶解度的变化造成;减小和消除的措施是通过高温扩散、锻造变形和热处理均匀化来消除。
区域偏析(宏观偏析):钢锭内各处化学成分及杂质分布的不均一性,如锭心的V型正偏析、离心的倒V 型正偏析以及底部的锥形负偏析区;主要由于钢锭在冷凝结晶过程中的选择性结晶、溶解度变化,各处密度差异造成,区域偏析会造成锻造裂纹及力学性能不均匀等缺陷;减小和消除的措施是降低钢液中的S、P等偏析元素的含量,采用多炉合浇及冒口补浇工艺和采用振动浇注。
硫化物夹杂:内生非金属夹杂物FeS、MnS等低熔点物质,分布在枝晶间及区域偏析处,塑性好,易变形;偏析严重,硫含量高,片状或密集分布危害大,形成应力集中开裂,形成热脆,降低力学性能;减小和消除的措施是炼钢时充分脱硫,减少偏析,充分锻压变形改善夹杂物的形状与分布。
大锻件的锻造工艺

大锻件的锻造工艺大锻件通常由大铸锭直接锻压成形。
大铸锭内部通常存在严重的偏析、缩孔、夹杂与晶粒粗大等铸造缺陷,且随着大锻件的规格不断增大,铸造缺陷越来越严重。
因此,改形与改性是大锻件锻造的两大关键任务。
大锻件一般采用自由锻成形。
根据锻造方式的不同,大锻件的自由锻工艺分为镦粗和拔长两类。
镦粗镦粗是使坯料高度减小、横截面积增加的锻造工艺。
除了饼类锻件的成形主要应用镦粗工序之外,许多重要轴类锻件的成形也常采用镦粗工序。
镦粗的主要目的是增大坯料横截面积,提高拔长的锻造比,改善锻件的横向力学性能和减少力学性能的异向性。
镦粗方法有普通平砧镦粗、凹形砧镦粗、锥形板镦粗与M形板镦粗等。
Array 1.普通平砧镦粗普通平砧面镦粗是最早采用的镦粗工艺。
传统的理论认为,镦粗过程中锻件中心点处于三向压应力状态,镦粗有利于压实心部孔隙缺陷,且不会在心部产生新的裂纹缺陷。
但是在实际生产中却发现,大型饼类锻件在经历大变形量的普通平砧镦粗工艺后,超声波探伤不合格率仍较高,主要原因是其内部出现横向裂纹缺陷。
显然,普通平站镦粗过程中锻件中心部位并不是一直处于三向压应力状态。
为此,从主动和被动塑形变形区等概念出发,于20世纪90年代初提出了普通平站镦粗圆柱体的两个新理论——刚塑性力学模型的拉应力理论和静水应力力学模型的切应力理论。
采用有限元数值模拟的方法,定量地分析了普通平站徽粗过程中圆柱体中心点部位应力场的演变规律,结果表明,原始高径比大于1.6的圆柱体毛坯中心点在镦粗过程中出现了两向拉应力状态,随着压下率的增大,圆柱体毛坯中心点的拉应力先增大后减小,并达到临界压下率时拉应力转变为压应力,且该临界压下率随着原始高径比的减小而减小。
对于原始髙径比为2.33 的圆柱体而言,该临界压下率为35%,对应的锻件瞬时高径比为1.129。
因此,开坯时,压下率应该大于40%,但是每次压下率应该在材料容许的塑性范围之内。
所以,圆柱体毛坯的原始高径比最好为2〜2. 2。
大钢锭定向凝固技术研究

条件后尽量小,以减少投资。
设: 平均浇注温度 TP = 1 560℃ ; 脱模温度 TI = 1 100℃ ; 平均熔点 Tm = 1 510℃ 。
于是钢锭从浇注到脱模散失的热量为:
Qi = WI[Hm + CP △Tm + CP ( Tm - TI ]
( 4)
冷板整个凝固过程吸收热量为:
QB = WB[CP △TB ]
图 4 有限元模拟过程图 Figure 4 The diagram of finite
element simulation process
图 5 测试点 Figure 5 Test point
图 6 模拟和测试结果对比 Figure 6 Result comparison between simulation and test
长期以来,对这些缺陷形成机理的研究与探 索推动了凝固理论的发展。而定性与定量地分析 钢锭的凝固过程,则涉及到“三传”和“三场”等前 沿学科的理论。对凝固过程中正、负偏析及缩松 形成机理的 研 究 也 是 一 个 前 沿 课 题[4]。 尽 管 如 此,科技人员在试图改善大钢锭缺陷的研究、试验 及生产实践中认识了许多定量或定性的规律,为 定向凝固工艺的研究与应用打下了基础。如:
在试验中,我们仅对锭模周边的材料进行了 更换,A 锭模周边有保温材料,B 锭周边为铸铁, 以便于充分了解定向凝固钢锭本体的原始质量状 况并观察不同边界条件下定向凝固钢锭内部结构 以 及 钢 锭 内 部 偏 析 和 夹 杂 物 分 布 的 变 化 状 况。 A、B 两支钢锭各重 5 600 kg,同炉钢水材质为 45# 钢( 平炉冶炼) ,在相同条件下浇注而成。炉后成 分如表 1 所示。
本研究课题正是在重大技术装备需求不断递 增的背景,在多学科前沿理论研究成果的支持 下展 开 的,它 对 揭 示 钢 锭 偏 析 形 成 机 理,改 进 工 艺,提高质量,降低成本有着极为重要的意义。
大钢锭定向凝固技术研究

p r i n c i p l e o f m a i n p a r a me t e r s H / D 和 / o f d i r e c t i o n a l s o l i d i i f c a t i o n s t e e l i n g o t .I t d i s c u s s e s t h e e l e me n t s t o i n i f u —
Che n Xi a o c i
Ab s t r a c t : T h i s p a p e r i n t r o d u c e s t h e b a s i c t h e o r y o f d i r e c t i o n a l s o l i d i i f c a t i o n t e c h n o l o g y a n d s t a t e s t h e c a l c u l a t i o n
的 因素 进 行 了讨 论 , 阐 明 了定 向凝 固钢 锭 工 艺 参 数 对 实 现 自然 精 炼 的作 用 。
锻造用钢锭和锻圆通用技术要求

锻造用钢锭和锻圆通用技术条件1 适用范围本标准适用于锻造用钢锭和锻圆的通用外采及验收,如有特殊产品另行规定。
钢锭与锻圆的区别:钢锭:订货时按照一一对应的工作令、图号按件数进行采购或根据批量常规产品相关技术要求采购的钢锭,具有固定的相关钢锭参数;锻圆:订货时不按照图号要求,而是按批次、按重量采购,形状均为轴类,截面规格有要求,长度方向尺寸范围较宽。
2 规范性引用文件GB/T1979-2001 结构钢低倍组织缺陷评级图GB/T10561-2005 钢中非金属夹杂物含量的测定-标准评级图显微检验法SEP1584的第2版发蓝断口检测法检验钢中宏观非金属夹杂物GB/T222-2006 钢的成品化学成分允许偏差JB/T5000.15-1998 重型机械通用技术条件锻钢件无损探伤JB/T1266-2002 25MW~200MW汽轮机转盘及叶轮锻件技术要求3 技术要求3.1 材料化学成分应符合钢锭和锻圆成分表1规定。
3.2 材料用钢锭冶炼方法:采用电炉+精炼真空脱气进行冶炼。
有要求时,可用电渣重熔钢锭、真空碳脱氧或按专用技术协议。
3.3 化学成份允许偏差按GB/T222标准规定。
34CrMo、34CrNi3Mo、34CrMo1A化学成分允许偏差按JB/T1266-2002执行。
[H]、[O]、[N]成品检测值不允许超出要求值上限的10%。
3.4 锻造比的要求:锻圆锻造比≥3;3.5 锻圆直径方向允许偏差0~10mm,长度方向允许偏差0~40mm。
3.6 锻圆超声波探伤检验,结果均应符合JB/T5000.15-1998中Ⅲ级要求。
钢锭要保证锻件探伤合格,标准符合JB/T5000.15-1998的Ⅲ级。
3.7 钢锭锭身比例要确保大于等于82%。
3.8 表面质量钢锭和锻圆表面不得有肉眼可见的重皮、裂纹、折叠、结疤、夹层、锻伤、夹渣等有害缺陷。
如有上述缺陷必须清除,其清除深度不得超过尺寸下偏差的要求。
决不允许对材料进行补焊处理。
钢锭
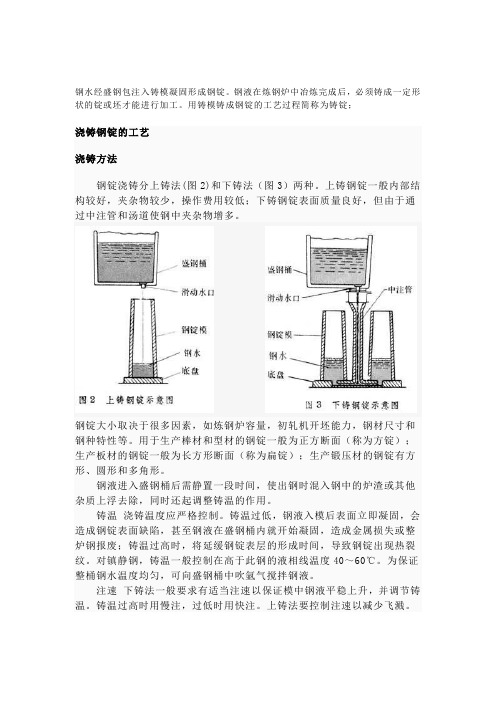
钢水经盛钢包注入铸模凝固形成钢锭。
钢液在炼钢炉中冶炼完成后,必须铸成一定形状的锭或坯才能进行加工。
用铸模铸成钢锭的工艺过程简称为铸锭;浇铸钢锭的工艺浇铸方法钢锭浇铸分上铸法(图2)和下铸法(图3)两种。
上铸钢锭一般内部结构较好,夹杂物较少,操作费用较低;下铸钢锭表面质量良好,但由于通过中注管和汤道使钢中夹杂物增多。
钢锭大小取决于很多因素,如炼钢炉容量,初轧机开坯能力,钢材尺寸和钢种特性等。
用于生产棒材和型材的钢锭一般为正方断面(称为方锭);生产板材的钢锭一般为长方形断面(称为扁锭);生产锻压材的钢锭有方形、圆形和多角形。
钢液进入盛钢桶后需静置一段时间,使出钢时混入钢中的炉渣或其他杂质上浮去除,同时还起调整铸温的作用。
铸温浇铸温度应严格控制。
铸温过低,钢液入模后表面立即凝固,会造成钢锭表面缺陷,甚至钢液在盛钢桶内就开始凝固,造成金属损失或整炉钢报废;铸温过高时,将延缓钢锭表层的形成时间,导致钢锭出现热裂纹。
对镇静钢,铸温一般控制在高于此钢的液相线温度40~60℃。
为保证整桶钢水温度均匀,可向盛钢桶中吹氩气搅拌钢液。
注速下铸法一般要求有适当注速以保证模中钢液平稳上升,并调节铸温。
铸温过高时用慢注,过低时用快注。
上铸法要控制注速以减少飞溅。
浇铸时大气中的氧将进入钢锭,使钢液二次氧化而降低钢的质量。
浇铸高质量钢时,需用惰性气体氩保护与空气接触的钢流,用合成固体渣粉保护模中上升的钢液面。
镇静钢锭锭身凝固时所造成的体积收缩需用帽头内钢液来补充,因此可适当延长帽头浇铸时间。
一般帽头注速比锭身注速慢一倍左右。
钢锭的缺陷在铸锭过程中由于操作不当或注速、铸温控制不当,会使铸成的锭有种种缺陷。
常见的缺陷为:钢锭表面的结疤、重皮和纵、横裂纹,内部的残余缩孔、皮下气泡、疏松和偏析,混入钢中的耐火物和炉渣、灰尘造成的夹杂等。
这些缺陷能大大降低钢锭的成坯率,甚至使整个钢锭报废。
钢锭的分类钢锭一般情况下大致可区分为以下几类:1)未净钢钢锭只经过了最基本(最低限)的脱氧处理。
大锻件锻造方法简介
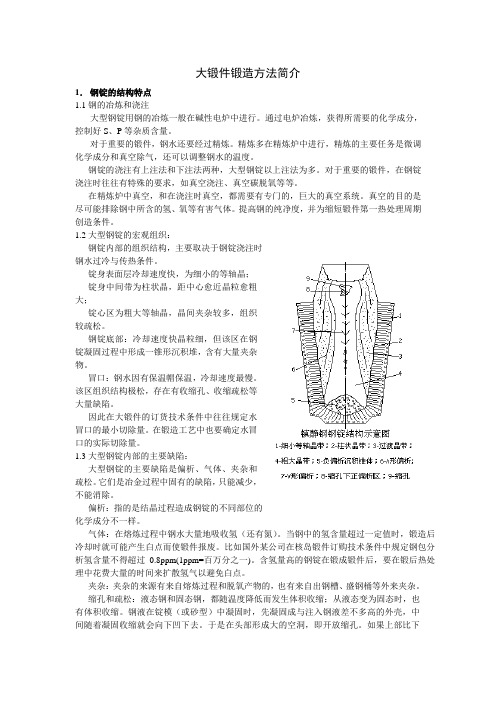
大锻件锻造方法简介1.钢锭的结构特点1.1钢的冶炼和浇注大型钢锭用钢的冶炼一般在碱性电炉中进行。
通过电炉冶炼,获得所需要的化学成分,控制好S、P等杂质含量。
对于重要的锻件,钢水还要经过精炼。
精炼多在精炼炉中进行,精炼的主要任务是微调化学成分和真空除气,还可以调整钢水的温度。
钢锭的浇注有上注法和下注法两种,大型钢锭以上注法为多。
对于重要的锻件,在钢锭浇注时往往有特殊的要求,如真空浇注、真空碳脱氧等等。
在精炼炉中真空,和在浇注时真空,都需要有专门的,巨大的真空系统。
真空的目的是尽可能排除钢中所含的氢、氧等有害气体。
提高钢的纯净度,并为缩短锻件第一热处理周期创造条件。
1.2大型钢锭的宏观组织:钢锭内部的组织结构,主要取决于钢锭浇注时钢水过冷与传热条件。
锭身表面层冷却速度快,为细小的等轴晶;锭身中间带为柱状晶,距中心愈近晶粒愈粗大;锭心区为粗大等轴晶,晶间夹杂较多,组织较疏松。
钢锭底部:冷却速度快晶粒细,但该区在钢锭凝固过程中形成一锥形沉积堆,含有大量夹杂物。
冒口:钢水因有保温帽保温,冷却速度最慢。
该区组织结构极松,存在有收缩孔、收缩疏松等大量缺陷。
因此在大锻件的订货技术条件中往往规定水冒口的最小切除量。
在锻造工艺中也要确定水冒口的实际切除量。
1.3大型钢锭内部的主要缺陷:大型钢锭的主要缺陷是偏析、气体、夹杂和疏松。
它们是冶金过程中固有的缺陷,只能减少,不能消除。
偏析:指的是结晶过程造成钢锭的不同部位的化学成分不一样。
气体:在熔炼过程中钢水大量地吸收氢(还有氮)。
当钢中的氢含量超过一定值时,锻造后冷却时就可能产生白点而使锻件报废。
比如国外某公司在核岛锻件订购技术条件中规定钢包分析氢含量不得超过0.8ppm(1ppm=百万分之一)。
含氢量高的钢锭在锻成锻件后,要在锻后热处理中花费大量的时间来扩散氢气以避免白点。
夹杂:夹杂的来源有来自熔炼过程和脱氧产物的,也有来自出钢槽、盛钢桶等外来夹杂。
缩孔和疏松:液态钢和固态钢,都随温度降低而发生体积收缩;从液态变为固态时,也有体积收缩。
锻钢和轧钢的制造方法

锻钢和轧钢的制造方法工模具钢及锻钢的制造方法如图6-6所示。
钢液浇入钢锭模中凝固成钢锭。
工模具钢的钢锭质量通常为0.5~10t,需重熔精炼时则成为VAR或ESR等的母材钢锭。
将这些钢锭加热到约1200℃的高温进行保温,这个过程称为热扩散处理(Soaking),目的是通过元素扩散来达到均匀化。
之后,用锻压机进行锻造。
日本国内的锻压机最大加压能力约为15000t。
其锻造目的归纳如下:图6-6 工模具钢及锻钢的制造方法1)将钢锭锻造成便于进一步锻造及轧制的坯料,或直接精锻成最终产品。
2)细化钢锭的粗大凝固组织。
3)减轻钢锭的中心偏析,压合细小缺陷。
将钢锭初始横截面积与锻造后横截面积的比值称作锻造比。
随锻造比的增加,凝固组织逐渐破碎成微细组织,微小缺陷也得到消除,从而使韧性和延展性提高。
一般来说,锻造比超过5之后韧性几乎达到饱和,所以将此作为最低锻造比。
锻造时,将钢锭沿轴向压缩的镦锻以及沿轴向伸长的锻造均能实现。
通过两个方向的锻造,可以使最终产品的力学性能,尤其是韧性和塑性等各向异性得到改善。
另外,在实际锻造操作中,还需要考虑钢锭的加热温度和时间、脱碳层和氧化皮厚度、锻造加载方式以及最终精锻温度等,并应根据不同钢种来决定最佳条件。
轧制产品的横截面积较小,可以用钢锭来轧制。
对可以进行连续铸造的钢种,也可用连铸钢坯加热后轧制成最终产品。
这一过程如图6-7所示。
轧制过程和锻造一样,可通过减小横截面积来改善凝固组织,从而实现微细化。
其特点是可利用孔型来简单地制得各种尺寸的产品。
图6-7 轧钢的制造方法钢材经锻造或轧制达到所需形状和尺寸后,若为工模具钢,则需要进行球化退火处理。
其目的是降低硬度,改善切削性,以便进行机械加工,还可作为淬火和回火的预备组织,以便淬火回火后球状碳化物均匀分散,保证耐磨性和韧性的平衡。
为得到最佳退火组织,有时还对其前身组织进行正火。
各种模具钢的退火条件已在第4章进行了介绍。
钢锭模铸锭介绍
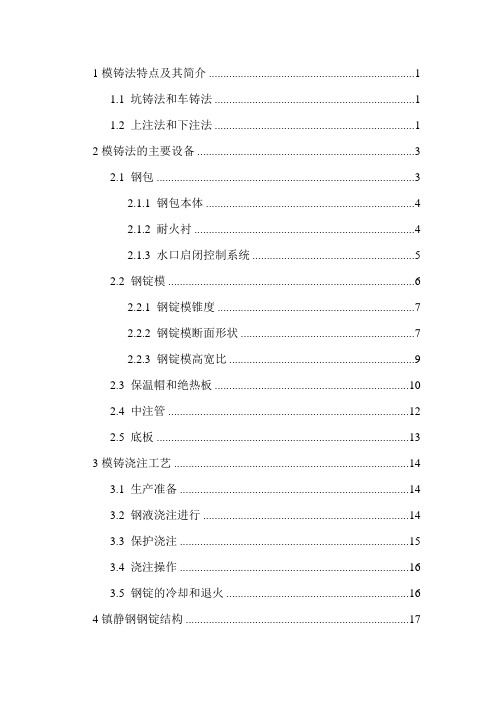
1模铸法特点及其简介 (1)1.1 坑铸法和车铸法 (1)1.2 上注法和下注法 (1)2模铸法的主要设备 (3)2.1 钢包 (3)2.1.1 钢包本体 (4)2.1.2 耐火衬 (4)2.1.3 水口启闭控制系统 (5)2.2 钢锭模 (6)2.2.1 钢锭模锥度 (7)2.2.2 钢锭模断面形状 (7)2.2.3 钢锭模高宽比 (9)2.3 保温帽和绝热板 (10)2.4 中注管 (12)2.5 底板 (13)3模铸浇注工艺 (14)3.1 生产准备 (14)3.2 钢液浇注进行 (14)3.3 保护浇注 (15)3.4 浇注操作 (16)3.5 钢锭的冷却和退火 (16)4镇静钢钢锭结构 (17)4.1 镇静钢钢锭结构 (17)4.2 镇静钢钢锭的偏析状况 (18)5 镇静钢钢锭常见缺陷 (19)6 钢锭的检查与精整 (20)7 模铸工艺的发展 (20)8 参考文献 (21)钢锭模铸锭介绍1 模铸法特点及其简介钢锭模铸锭(模铸)钢的浇注,就是把在炼钢炉中或炉外精炼所得到的合格钢水,经过钢包(又称盛钢桶)及中间钢包等浇注设备,注入到一定形状和尺寸的钢锭模或结晶器中,使之凝固成钢锭或钢坯。
钢锭(坯)是炼钢生产的最终产品,其质量的好坏与冶炼和浇注有直接关系,是炼钢生产过程中质量控制的重要环节。
目前采用的浇注方法有钢锭模铸钢法(模铸法)和连续铸钢法(连铸法)两种。
模铸法是将盛钢桶内的钢水注入到具有一定形状和尺寸的钢锭模中,把液态的钢水变成固态的钢锭。
钢锭经过初轧开坯轧制成钢坯,然后再进一步轧制成各种钢材。
模铸法可分为以下几种。
1.1 坑铸法和车铸法坑铸法是将钢锭模摆放在铸坑内的底板上进行浇注,浇注作业全在铸锭跨内进行。
此法生产效率低,劳动条件差,因此仅在一些中小型的炼钢车间采用。
车铸法是将钢锭模摆放在铸车的底板上进行浇注,除在铸锭跨内进行浇注钢液外,其他作业如脱模、整模等均在另外的厂房内进行,从而克服了坑铸法的缺点。
大型锻钢件用真空钢铸锭技术要求

大型锻钢件用真空钢铸锭技术要求1范围本文件规定了大型锻钢件用真空钢锭的冶炼和铸锭的质量要求、设备及仪器要求、人员要求、安全环保要求、原材料及冶金辅具、吊具要求、冶炼和铸锭工艺流程、冶炼工艺、真空铸锭工艺、记录、检验规则和试验方法以及质量证明书。
本文件适用于大型锻钢件用50吨及以上真空钢锭(以下简称为“钢锭”)的冶炼和铸锭。
2规范性引用文件下列文件中的内容通过文中的规范性引用而构成本文件必不可少的条款。
其中,注日期的引用文件,仅该日期对应的版本适用于本文件;不注日期的引用文件,其最新版本(包括所有的修改单)适用于本文件。
GB/T223(所有部分)钢铁及合金化学分析方法GB/T2272硅铁GB/T2988高铝砖GB/T3649钼铁GB/T3795锰铁GB/T3863工业氧GB/T3864工业氮GB/T4139钒铁GB/T4223废钢铁GB/T4336碳素钢和中低合金钢多元素含量的测定火花放电原子发射光谱法(常规法)GB/T4842氩GB/T5683铬铁GB/T6414铸件尺寸公差、几何公差与机械加工余量GB/T6516电解镍GB/T11170不锈钢多元素含量的测定火花放电原子发射光谱法(常规法)GB/T11261钢铁氧含量的测定脉冲加热惰气熔融-红外线吸收法GB∕T20118_一般用途钢丝绳GB/T20123钢铁总碳硫含量的测定高频感应炉燃烧后红外吸收法(常规方法)GB/T20124钢铁氮含量的测定脉冲加热惰气熔融-红外线吸收法GB/T20125低合金钢多元素含量的测定电感耦合等离子体原子发射光谱法GB/T22589镁碳砖YB/T042冶金石灰YB/T192炼钢用增碳剂YB/T5049滑板砖YB/T5051硅钙合金YB/T5217萤石YB/T5296炼钢用生铁AQ2001炼钢安全规程3术语和定义GB/T5611界定的以及下列术语和定义适用于本文件。
真空钢锭vacuum ingot通过电炉粗炼、钢包精炼加真空脱气处理、真空浇注(模铸滴流脱气或模铸滴流脱气加真空碳脱氧)的钢锭。
大型锻造钢锭的生产技术

大型锻造钢锭的生产技术Christian Redl, Rainer Tarmann, Johannes Obitz, Matthias Pfennig,Harald Holzgruber白彦贵译(奥地利因泰克特种冶炼公司,奥地利布鲁克8600)摘要:目前对大型钢锭的需求特别是在能源市场上不断地增加,因此,对于生产大型钢锭的技术和设备存在巨大需求。
本文介绍了大型钢锭不同的生产技术、所需的设备和最新的项目。
关键词:钢锭浇铸;真空钢锭浇铸;锻造钢锭;氢含量PRODUCTION TECHNOLOGIES FOR LARGEFORGING INGOTSMatthias Pfennig, Harald Holzgruber(INTECO special melting technologies GmbH, Bruck/Mur 8600, Austria)Abstract:The required ingot sizes especially for the energy market are steadily increasing nowadays. Therefore it exists a huge demand for the equipment and technology to produce these large ingots. This paper shall give an overview about different production technologies, the required equipment and recent projects.Key words:Ingot Casting, Vacuum Ingot Casting, Forging Ingots, Hydrogen Content1 前言虽然连续浇铸从上个世纪七十年代以来非常成功,在钢铁生产中,模铸钢锭一直占有重要地位。
锻造用钢锭技术条件

锻造用钢锭技术条件1,电炉钢锭(外购)技术条件1.1钢的化学成分符合国家标准,偏差应符合GB222。
1.2钢锭尾部圆弧与锭身应圆滑过渡,不得有台阶。
锭尾不得带有汤道把子。
1.3锭身不得有裂纹。
裂纹必须修磨,修磨处应圆滑过渡,修磨处深宽比为1:6,裂纹深度>15mm的钢锭不得镦粗使用,>20mm应判废。
1.4钢锭飞边毛刺应清理,外部粘结的砖块等非金属应清理掉。
结疤、重皮、表面气孔应清理掉。
深度<2mm的缺陷可不予清理。
1.5有接注。
冒口上涨、注入钢渣、混入绝热板等杂物的钢锭应予判废。
2电渣钢锭技术条件2.1钢的化学成分符合国家标准,偏差应符合GB222。
2.2锭型工艺参数见表12.3钢锭表面不允许有结疤、裂纹、气孔及夹渣(渣沟)。
2.4 钢锭表面裂纹清理:重量小于2吨的钢锭,清理深度单边不得大于10mm,大于2吨的钢锭单边清理深度应小于15mm,统同一截面相对两边深度之和<30mm,单边>10mm 不得镦粗使用。
2.5 清理深宽比为1:6,并圆滑过渡。
2.6 下列情况宽不清理:(1)φ400-500mm锭渣沟深度<3mm;(2)φ600-700mm锭渣沟深度<5mm;(3)φ600mm以上合工钢、冷轧辊钢、不锈钢锭渣沟深度应小于4mm。
2.7 深度<10mm渣沟,允许修磨,修磨深宽比为1:6,圆滑过渡。
渣沟深度>10mm的钢锭不可用于镦粗。
2.8 切头、切尾范围见表2,在此范围的缺陷可不清理。
2.9 钢锭报废标准(1)清理缺陷超深者(见2.4条);(2)钢锭高度小于700mm者;(3)高度重量允许偏差±2%,超正偏差部分不计产量,超负偏差不能按原合同交接。
2.10 减斤处理(1)缺陷位置超过切头、切尾长度者;(2)缩孔长度超过允许缩孔深度者(见表3);减斤长度=缩孔深度-允许缩孔深度表3(3)补缩阶段化入余头或未补缩者减斤长度为100-120mm,中间阶段化入余头报废。
(4)减斤重量=减斤长度×单位长度重量单位长度重量见表4。
大型锻件第1部分 绪论
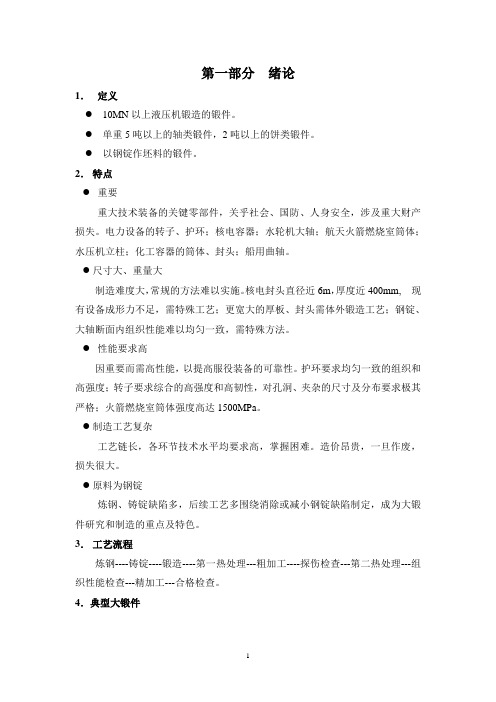
第一部分绪论1.定义●10MN以上液压机锻造的锻件。
●单重5吨以上的轴类锻件,2吨以上的饼类锻件。
●以钢锭作坯料的锻件。
2.特点●重要重大技术装备的关键零部件,关乎社会、国防、人身安全,涉及重大财产损失。
电力设备的转子、护环;核电容器;水轮机大轴;航天火箭燃烧室筒体;水压机立柱;化工容器的筒体、封头;船用曲轴。
●尺寸大、重量大制造难度大,常规的方法难以实施。
核电封头直径近6m,厚度近400mm, 现有设备成形力不足,需特殊工艺;更宽大的厚板、封头需体外锻造工艺;钢锭、大轴断面内组织性能难以均匀一致,需特殊方法。
●性能要求高因重要而需高性能,以提高服役装备的可靠性。
护环要求均匀一致的组织和高强度;转子要求综合的高强度和高韧性,对孔洞、夹杂的尺寸及分布要求极其严格;火箭燃烧室筒体强度高达1500MPa。
●制造工艺复杂工艺链长,各环节技术水平均要求高,掌握困难。
造价昂贵,一旦作废,损失很大。
●原料为钢锭炼钢、铸锭缺陷多,后续工艺多围绕消除或减小钢锭缺陷制定,成为大锻件研究和制造的重点及特色。
3.工艺流程炼钢----铸锭----锻造----第一热处理---粗加工----探伤检查---第二热处理---组织性能检查---精加工---合格检查。
4.典型大锻件支撑辊高速钢工作辊高中压联合转子低压转子水轮机大轴核电接管段核电整体顶盖船用70曲轴曲拐舵轴发电机主轴核电蒸发器管板煤液化容器筒节5.世界大锻件生产及工艺装备的现状6.我国大锻件生产和工艺装备的现状及存在的问题我国大锻件生产和工艺装备的现状表5~表7列出了我国大锻件生产和工艺装备的现状。
与发达国家的差距(1)钢水精炼和真空处理等新的冶金技术利用率低。
我国钢水除气率近40%~60%,国外已近100%。
(2)钢水纯净度低;以转子为例,国外S〈0.003%,P〈0.005%,H〈1.0ppm;我国S〈0.006%,P〈0.006%,H〈1.4~1.8ppm。
(3)铸锭技术水平低,锻件尺寸肥头大耳,因此,钢锭利用率低,仅50%~55%,国外已达60%。
冶炼钢锭浇铸工艺

冶炼钢锭浇铸工艺冶炼钢锭是一种重要的工艺过程,用于将原料转化为高强度、耐用的钢材。
本文将介绍冶炼钢锭的浇铸工艺,包括工艺流程、设备和材料的选择,以及注意事项等方面。
一、工艺流程冶炼钢锭的浇铸工艺一般包括以下几个步骤:1. 原料准备:根据需要冶炼的钢种选择合适的原料,通常包括铁矿石、废钢、合金等。
原料需经过粉碎、筛分等处理,以保证均匀混合。
2. 熔炼炉装料:将准备好的原料按照一定比例装入熔炼炉中。
常见的熔炼炉有电炉、转炉、氧气顶吹炉等。
3. 加热熔化:通过电能、燃料或氧气等方式对熔炼炉进行加热,使原料完全熔化。
熔炼过程中需要控制温度、炉内气氛等参数,以保证冶炼效果。
4. 炉内调质:在熔炼过程中,可以添加合适的合金元素和脱氧剂等,以调整钢液的成分和性能。
5. 钢液浇注:将熔化好的钢液从熔炼炉中流出,倒入浇铸模具中。
浇注时需要控制流速、温度等参数,以保证钢液充分填充模具,并获得均匀的凝固结构。
6. 凝固冷却:钢液在模具中逐渐冷却凝固,形成钢锭。
冷却过程中需要控制冷却速度,以避免产生缺陷。
7. 处理后工艺:冷却后的钢锭需要进行去毛边、修整等处理,以达到规定的尺寸和形状要求。
8. 检验和质量控制:对冶炼钢锭进行化学成分分析、机械性能测试等,确保产品质量符合标准要求。
二、设备和材料选择冶炼钢锭的设备选择主要考虑生产规模、钢种要求和经济效益等因素。
常见的设备有电炉、转炉、氧气顶吹炉等。
对于大型钢厂,通常采用转炉或氧气顶吹炉进行冶炼;而小型钢厂则多采用电炉进行冶炼。
材料选择方面,要根据冶炼钢锭的要求选择合适的原料。
铁矿石作为最主要的原料,应选择高品位、低硫低磷的铁矿石。
废钢可以作为回收利用的原料,但需要经过分类、清洁等处理。
合金则根据冶炼需要选择合适的合金元素。
三、注意事项1. 安全操作:冶炼钢锭的过程涉及高温、高压等危险因素,操作人员必须佩戴防护设备,并按照操作规程进行操作。
2. 温度控制:钢液的浇注温度、冷却速度等参数对钢锭的质量具有重要影响,需要进行严格控制。
锻造用钢锭与型材PPT课件

传统的铣削是通过镗杆进行加工, 而现代 铣削加 工,多 由各种 功能附 件通过 滑枕完 成,已 有替代 传统加 工的趋 势,其 优点不 仅是铣 削的速 度、效 率高, 更主要 是可进 行多面 体和曲 面的加 工,这 是传统 加工方 法无法 完成的 。因此 ,现在 ,很多 厂家都 竞相开 发生产 滑枕式 (无镗 轴)高速 加工中 心,在 于它的 经济性 ,技术 优势很 明显, 还能大 大提高 机床的 工艺水 平和工 艺范围 。同时 ,又提 高了加 工精度 和加工 效率。 当然, 需要各 种不同 型式的 高精密 铣头附 件作技 术保障 ,对其 要求也 很高。
工艺特点
• 注温:一般比熔点高8)化学原因
偏析:比重差异\选择性结 晶、溶解度变化
夹杂:钢中非金属化合物 内生夹杂 外来夹杂
2)物理原因
气体:O H N
缩孔
蔬松 气泡
都是由于物理收缩 引起的缺陷
裂纹
4.型材的常见缺陷
• 型材:是经过塑性变形后的材料,轧材、挤 棒、锻坯等。
高速铣削给落地式铣镗床带来了结构 上的变 化,主 轴箱居 中的结 构较为 普遍, 其刚性 高,适 合高速 运行。 滑枕驱 动结构 采用线 性导轨 ,直线 电机驱 动,这 种结构 是高速 切削所 必需的 ,国外 厂家在 落地式 铣镗床 上都已 采用, 国内同 类产品 还不
多见,仅在中小规格机床上采用线性 导轨。 高速加 工还对 环境、 安全提 出了更 高的要 求,这 又产生 了宜人 化生产 的概念 ,各厂 家都非 常重视 机床高 速运行 状态下 ,对人 的安全 保护与 可操作 性,将 操作台 、立柱 实行全 封闭式 结构, 既安全 又美观 。
现在,又开发了一种可更换式主轴 系统, 具有一 机两用 的功效 ,用户 根据不 同的加 工对象 选择使 用,即 电主轴 和镗杆 可相互 更换使 用。这 种结构 兼顾了 两种结 构的不 足,还 大大降 低了成 本。是 当今卧 式镗铣 床的一 大创举 。电主 轴的优 点在于 高速切 削和快 速进给 ,大大 提高了 机床的 精度和 效率。
- 1、下载文档前请自行甄别文档内容的完整性,平台不提供额外的编辑、内容补充、找答案等附加服务。
- 2、"仅部分预览"的文档,不可在线预览部分如存在完整性等问题,可反馈申请退款(可完整预览的文档不适用该条件!)。
- 3、如文档侵犯您的权益,请联系客服反馈,我们会尽快为您处理(人工客服工作时间:9:00-18:30)。
第四部分锻造用钢锭及铸锭技术一、 大型钢锭的组织结构及类型1.大型钢锭的组织结构z 激冷层:锭身表面的细小等轴晶区。
厚度仅6~8mm ;因过冷度较大,凝固速 度快,无偏析;有夹渣、气孔等缺陷。
z 柱状晶区:位于激冷层内侧;由径向呈细长的柱状晶粒组成;由于树枝状 晶沿温度梯度最大的方向生长,该方向恰为径向,因此形成了柱状晶区;其凝固速度较快,偏析较轻,夹杂物较少;厚度约50~120mm 。
z 分枝树枝晶区:从柱状晶区向内生长;主轴方向偏离柱状晶,倾斜,并出现 二次以上分枝;温差较小,固液两相区大,合金元素及杂质浓度较大。
z A 偏析区:枝状晶间存在残液,比锭内未凝固的钢液密度小,向上流动,形成A 偏析;在偏析区合金元素和杂质富集,存在较多的硫化物,易产生偏析裂纹。
z 等轴晶区:位于中心部位;温差很小,同时结晶,成等轴晶区。
钢液粘稠, 固相彼此搭桥,残液下流形成V 偏析,疏松增多。
z 沉积锥区:位于等轴晶区的底端;由顶面下落的结晶雨、熔断的枝状晶形成的自由晶组成,显示负偏析;等轴的自由晶上附着大量夹杂物,其组织疏松,且夹杂浓度很大;应切除。
z 冒口区:最后凝固的顶部;因钢液的选择性结晶,使后凝固的部分含有大量的低熔点物质,最后富集于上部中心区,其磷、硫类夹杂物多;若冒口保温不良,顶部先凝固,因无法补缩形成缩孔;质量最差,应予切除。
2. 大型钢锭的类型z 普通钢锭高径比:=+dD H 2 1.8~2.5;通常,10吨以下的钢锭:2.1~2.3,10吨以上的钢锭:1.5~2;锥度:=%100-D Hd 3~4% ; 横断面为8棱角形。
大钢锭为16,24,32棱角。
z 短粗型钢锭高径比: 0.5~2;锥度: 8~12%。
高宽比减小,锥度加大有利于钢锭实现自下而上顺序凝固,易于钢水补缩,中心较密实;有利于夹杂上浮,气体外溢,减少偏析;锭身较短,钢水压力小,侧表面不易产生裂纹;锥度大,易脱模;可增加拔长锻比。
z 短冒口钢锭对于中、低碳钢,中、低合金结构钢的大型空心锻件,可使用普通锭模,但采用短冒口,以减少冒口钢水。
z 细长型钢锭高径比:大于3.5;锥度:5~8%;用于不需镦粗的轴类件,可减少火次,钢锭利用率达70~75%。
z 空心钢锭用于锻造大型筒类、环类等空心锻件,对于容器制造具有重要意义; 在钢锭模内置入薄壁钢管,浇铸后形成空腔;可显著提高钢锭利用率,大幅减少火次;心部冷却速度明显提高,结构致密,偏析减轻。
国内已成功浇成150吨锭。
z多锥度钢锭下部锥度大,中部次之,上部锥度小。
内部较致密。
z电渣重熔钢锭圆截面,小锥度;高径比:约2.5;钢水洁净,组织致密,结构合理;钢锭利用率高;国内已具备浇铸400吨级钢锭的能力。
二、铸锭工艺1.钢水注入钢包,经脱氧后浇注成钢锭的炼钢工序。
2.铸锭中钢液发生的物理化学变化z大气环境下浇注,钢液发生二次氧化,产生氧化物夹杂,吸入水蒸气、氢气。
z钢液与耐火材料接触,形成外来夹杂。
z在钢锭模内完成液态到固态的转变。
z固态钢收缩。
3.普通铸锭法z大气环境浇注。
z大型钢锭普遍采用上注法,钢液飞溅易产生表面气孔,钢锭表面凸凹不平。
z德国梯森·亨利希冶金公司发明下注法,浇注过435吨钢锭,质量高。
z为防止二次氧化,可采用惰性气体保护。
4.真空铸锭法z钢液通过中间包浇入置于真空室钢锭模的方法。
z普通真空铸锭z真空吹氩铸锭z采用除气设备,在浇注中除气。
z避免了二次氧化,减少了非金属夹杂物。
z可利用真空条件下的碳氧反应,进行真空碳脱氧操作,对于低硅的NiCrMo、NiCrMoV钢意义重大,减少夹杂,显著改善偏析,钢锭质量明显提高。
三、大型钢锭的缺陷1.偏析大锻件要求极少的缺陷和性能的均匀化,但铸锭的物理化学过程,特别是选择性结晶的结果,却使缺陷不可避免。
不同元素于不同温度下在固液两相中的溶解度不同,由不同温度梯度形成的结晶差别,凝固过程中的收缩及各种化学反应过程等都将会引起偏析,即成分在宏观、微观区域的不均匀分布。
z A偏析形貌与成分分布:位于分枝树枝晶区和等轴晶区之间。
与半径的比例关系,锭顶部为0.51~0.54,中部为0.38~0.42,底部为0.26~0.28。
纵断面上表现为不连续的八字形条纹,横断面上表现为以同心圆分布的斑点,斑点直径从几毫米到几十毫米。
呈线状。
偏析外侧轮廓清晰平滑,内侧轮廓模糊粗糙。
锭底部细小,顶部粗大。
扫描电镜观察发现。
A偏析线内存在1微米左右的洞穴,密度明显降低。
偏析线处P 、Mn 、Si 、Mo 浓度远大于平均值,而其周围浓度低于平均值,成分偏析特征明显。
形成机理:理论一:A 偏析应在凝固前沿形成,位于固液两相区,该处固相率为30%~35%,是准固相区和准液相区的界面。
理论二:富集溶质的钢液比原始钢液密度小,在凝固前沿上浮,形成偏析线。
偏析线的斜度由上浮速度和凝固前沿推进的径向速度共同决定。
理论三:当以下热力学条件满足时,含碳量为0.7%的钢即形成A 偏析 75.81.1≤⋅R εε---冷却速度;R---凝固前沿的凝固速度。
显然,冷却和前沿凝固速度越低,上式越容易满足,A 偏析越容易产生。
影响因素:化学成分对A 偏析的影响:对于CrNiMo(V)钢,C 、S 、P 在偏析区富集,认为S 是引起偏析的主要原因,要减轻A 偏析,须将S 降至0.002%以下。
Mo 可抑制偏析发生,Mo 钢几乎无偏析。
低Si 钢因凝固前沿的固相率低,枝晶间钢液的密度与原始钢液相差很小,不足以上浮形成偏析。
反之,高Si 则易产生偏析。
凝固速度对A 偏析的影响:钢锭外表面凝固速度快,无偏析现象;随固相线向内推进,凝固速度逐渐降低,当降至0.8mm/min 时,出现A 偏析;进一步向内推进,因纵向凝固速度的影响,疏松尺寸渐大,面积也增加,A 偏析不明显。
对力学性能的影响:偏析区的力学性能明显降低,正火碳钢偏析区与表面区塑性指标 δ、Ψ、αk 的比列于下图。
淬火回火低合金钢偏析区与表面区塑性指标 δ、Ψ、αk 的比列于下表。
由图表可见,偏析区的力学性能均比表面区低;偏析区的横向力学性能比纵向更低;抗拉强度越高,偏析区力学性能降低的幅度越大。
当MPa b 441=σ时,纵向δ、Ψ、αk 分别降低5%、6%、12%,横向δ、Ψ、αk 分别降低20%、25%、70%。
当MPa b 735=σ时,纵向δ、Ψ、αk 分别降低8%、11%、20%,横向δ、Ψ、αk 分别降低31%、43%、29%。
z V偏析形貌:位于上部等轴晶区,但冒口与锭身交接处中心顶部一般无偏析。
成V形条纹,周期性分布。
疏松与空隙与其同时存在,说明它们有共同的形成条件。
属最后凝固的正偏析区。
S化物夹杂富集。
形成机理:实验表明,凝固后期在钢锭上部中心区形成了加速凝固区,因其出现凝固收缩导致了V偏析的产生。
凝固开始时,因钢锭仅受底部冷却的影响,纵向凝固速度较慢。
其后,由于纵向与横向凝固速度叠加的结果,纵向凝固速度加快,凝固曲线出现拐点,形成凝固壳体。
此后,因壳底部加厚,侧面凝固速度成为主要影响因素,从而形成一狭长的U形熔池,底部变尖成V形。
池内为浓缩钢液。
凝固壳内钢液的固相率分布不均,下部大而上部小,当下部钢液顺序凝固时,体积收缩,吸引上部低固相率的浓缩钢液向下流动,填补了下部的凝固收缩间隙,并形成V偏析。
影响因素:主要影响因素是钢锭模的高径比H/D、锥度、冒口的温度等。
高径比H/D越小,横向凝固速度的影响越小,越不容易形成狭长的U形熔池,可减轻或避免V偏析的产生,同时也可减少疏松缺陷。
下图中某110T钢锭高径比H/D为1.06,135T钢锭的H/D为1.41;两者的锥度基本相同。
图中表明,135T 钢锭的横向凝固速度明显大于110T钢锭。
解剖结果表明,135T钢锭的V偏析要严重得多。
钢锭锥度越大越不容易产生V偏析。
实际上当锥度为2%~10%时存在发生V 偏析的可能;当锥度大于25%时,V偏析则不会发生。
锥度过小会阻碍凝固的锭身下滑,甚至可能沿锭肩部撕裂。
冒口温度高有利于形成正的温度梯度,使钢液沿温度梯度方向结晶,可抑制等轴晶的形成及自冒口内下沉,避免V偏析的发生。
对力学性能的影响:V偏析区强度增高,塑性和韧性降低。
碳偏析造成FATT升高。
偏析程度越严重,影响就越大。
V偏析使锻件的均质化处理困难。
热处理难度更大。
z沉积锥的负偏析钢锭底部轴心处溶质浓度低的自由晶区称为沉积区或沉积锥。
沉积锥含有大量的非金属夹杂物,又称夹杂沉积区。
沉积锥底部为柱状晶,上部为等轴晶,呈圆锥台状,上平面中心呈凹形。
形成机理:钢锭顶面下落的结晶雨、侧壁被熔断或折断的枝状自由晶落入底部,形成了含有较多固相颗粒的粘稠区,使夹杂物难以上浮。
由于钢液具有温度差,钢液将形成自然对流,将已上浮的夹杂物带回底部粘稠区,并被阻滞在其中,凝固后形成富集夹杂的等轴晶区。
由于非金属夹杂富集,加之熔断或折断的树枝晶本身部分合金含量也低,即形成负偏析区。
沉积锥合金含量低,以氧化物为主的夹杂物多,应切除,切除率一般为15%,因沉积锥高度不稳定,切除后仍会发现超标夹杂。
采用VCD(真空碳氧反应)法二次炼钢,强化冒口保温措施,采用耐侵蚀的耐火材料可使切除率降低至8%~12%,从而使钢锭的利用率提高至60%。
z微观偏析指枝晶偏析,即枝晶干与枝晶间的成分不均匀现象。
是钢液凝固过程中不可避免的现象。
z偏析的危害,解剖75吨钢锭可见化学成分的不均匀性:最大正偏析在锭身上部的V 偏析内,最大负偏析在底部沉积锥。
C 、S 、P 偏析程度均较大。
C 偏析更易导致热处理工艺制定的困难。
大气浇注与真空浇注相比,前者偏析更严重。
C 在水口端为0.26%,而在在冒口端达0.51%。
热处理时,冒口端可能淬裂,而水口端因冷速不够而不达标。
C 的零偏析点位于锭身的30%处。
偏析率为:CoC C C C min max −=Δ 其它元素的偏析,其偏析率与C 偏析成正比,其中C 、N 、S 偏析最强烈,V 、Sn 、As 、P 、Cu 次之,Si 、Ni 、Cr 、Mo 偏析最轻微。
微观偏析中,P 、S 、C 、Mo 最强烈,Mn 、Si 、Ni 较弱。
危害:加热温度只能取上限。
因各部位成分不同,完成珠光体转变所需时间不同,从十几小时到几十小时。
为保证各部位都实现转变,需延长加热时间。
冒口C 高,有淬裂危险,水口C 低,需加大冷却速度,为保证实现均匀性要求,须在同一锻件上采用不同的回火温度。
偏析区因C 、S 、P 的的富集而脆化,在锻造和热处理时会因拉应力的作用开裂。
H 和夹杂在偏析区富集会加剧脆化倾向。
偏析区的力学性能降低。
z 减轻偏析的措施改进熔炼技术,尽量降低P 、S 含量。
采用VCD 技术及真空浇注技术。
改进锭模形状,控制凝固条件。
加冒口发热剂或用电渣加热冒口。