第三章 系统布置设计
物流工程练习题(附答案)
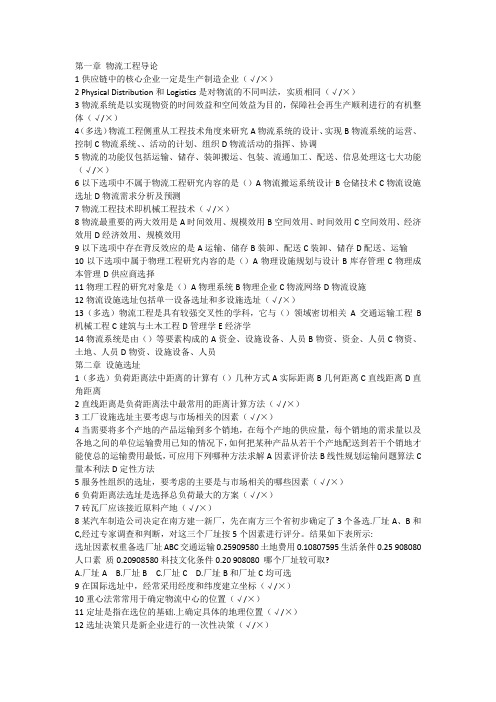
第一章物流工程导论1供应链中的核心企业一定是生产制造企业(√/×)2 Physical Distribution和Logistics是对物流的不同叫法,实质相同(√/×)3物流系统是以实现物资的时间效益和空间效益为目的,保障社会再生产顺利进行的有机整体(√/×)4(多选)物流工程侧重从工程技术角度来研究A物流系统的设计、实现B物流系统的运营、控制C物流系统、、活动的计划、组织D物流活动的指挥、协调5物流的功能仅包括运输、储存、装卸搬运、包装、流通加工、配送、信息处理这七大功能(√/×)6以下选项中不属于物流工程研究内容的是()A物流搬运系统设计B仓储技术C物流设施选址D物流需求分析及预测7物流工程技术即机械工程技术(√/×)8物流最重要的两大效用是A时间效用、规模效用B空间效用、时间效用C空间效用、经济效用D经济效用、规模效用9以下选项中存在背反效应的是A运输、储存B装卸、配送C装卸、储存D配送、运输10以下选项中属于物理工程研究内容的是()A物理设施规划与设计B库存管理C物理成本管理D供应商选择11物理工程的研究对象是()A物理系统B物理企业C物流网络D物流设施12物流设施选址包括单一设备选址和多设施选址(√/×)13(多选)物流工程是具有较强交叉性的学科,它与()领域密切相关A交通运输工程B 机械工程C建筑与土木工程D管理学E经济学14物流系统是由()等要素构成的A资金、设施设备、人员B物资、资金、人员C物资、土地、人员D物资、设施设备、人员第二章设施选址1(多选)负荷距离法中距离的计算有()几种方式A实际距离B几何距离C直线距离D直角距离2直线距离是负荷距离法中最常用的距离计算方法(√/×)3工厂设施选址主要考虑与市场相关的因素(√/×)4当需要将多个产地的产品运输到多个销地,在每个产地的供应量,每个销地的需求量以及各地之间的单位运输费用已知的情况下,如何把某种产品从若干个产地配送到若干个销地才能使总的运输费用最低,可应用下列哪种方法求解A因素评价法B线性规划运输问题算法C 量本利法D定性方法5服务性组织的选址,要考虑的主要是与市场相关的哪些因素(√/×)6负荷距离法选址是选择总负荷最大的方案(√/×)7砖瓦厂应该接近原料产地(√/×)8某汽车制造公司决定在南方建一新厂,先在南方三个省初步确定了3个备选.厂址A、B和C,经过专家调查和判断,对这三个厂址按5个因素进行评分。
系统布置设计方法
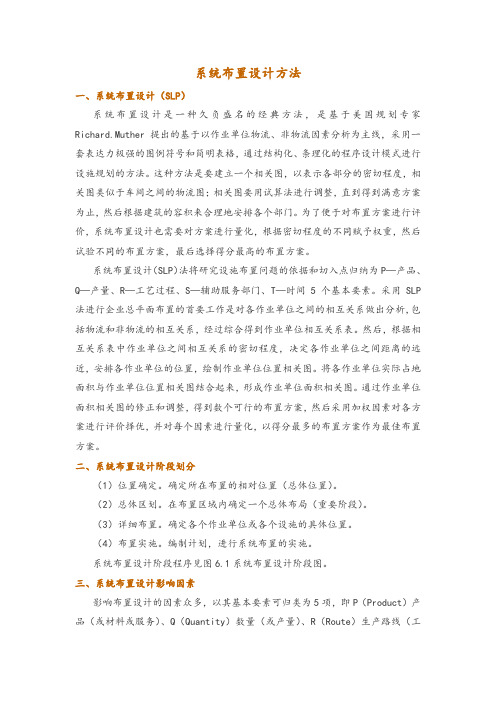
系统布置设计方法一、系统布置设计(SLP)系统布置设计是一种久负盛名的经典方法,是基于美国规划专家Richard.Muther提出的基于以作业单位物流、非物流因素分析为主线,采用一套表达力极强的图例符号和简明表格,通过结构化、条理化的程序设计模式进行设施规划的方法。
这种方法是要建立一个相关图,以表示各部分的密切程度,相关图类似于车间之间的物流图;相关图要用试算法进行调整,直到得到满意方案为止,然后根据建筑的容积来合理地安排各个部门。
为了便于对布置方案进行评价,系统布置设计也需要对方案进行量化,根据密切程度的不同赋予权重,然后试验不同的布置方案,最后选择得分最高的布置方案。
系统布置设计(SLP)法将研究设施布置问题的依据和切入点归纳为P—产品、Q—产量、R—工艺过程、S—辅助服务部门、T—时间5个基本要素。
采用SLP 法进行企业总平面布置的首要工作是对各作业单位之间的相互关系做出分析,包括物流和非物流的相互关系,经过综合得到作业单位相互关系表。
然后,根据相互关系表中作业单位之间相互关系的密切程度,决定各作业单位之间距离的远近,安排各作业单位的位置,绘制作业单位位置相关图。
将各作业单位实际占地面积与作业单位位置相关图结合起来,形成作业单位面积相关图。
通过作业单位面积相关图的修正和调整,得到数个可行的布置方案,然后采用加权因素对各方案进行评价择优,并对每个因素进行量化,以得分最多的布置方案作为最佳布置方案。
二、系统布置设计阶段划分(1)位置确定。
确定所在布置的相对位置(总体位置)。
(2)总体区划。
在布置区域内确定一个总体布局(重要阶段)。
(3)详细布置。
确定各个作业单位或各个设施的具体位置。
(4)布置实施。
编制计划,进行系统布置的实施。
系统布置设计阶段程序见图6.1系统布置设计阶段图。
三、系统布置设计影响因素影响布置设计的因素众多,以其基本要素可归类为5项,即P(Product)产品(或材料或服务)、Q(Quantity)数量(或产量)、R(Route)生产路线(工艺过程)、S(Supporting Service)辅助服务部门、T(Time)时间(或时间安排)。
系统布置设计(SLP)模式
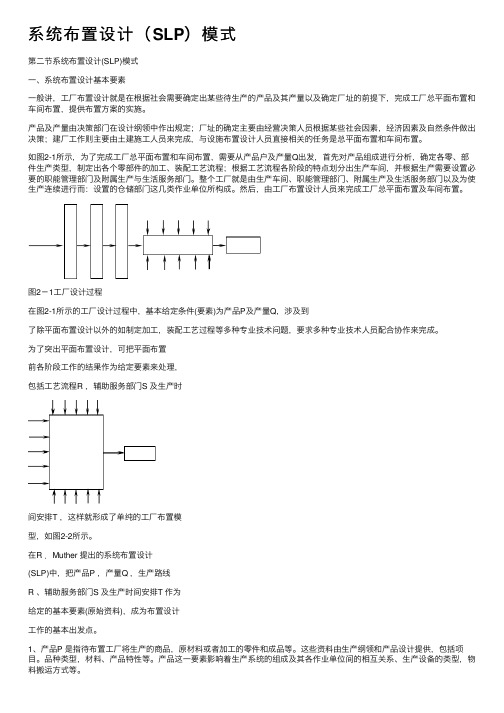
系统布置设计(SLP)模式第⼆节系统布置设计(SLP)模式⼀、系统布置设计基本要素⼀般讲,⼯⼚布置设计就是在根据社会需要确定出某些待⽣产的产品及其产量以及确定⼚址的前提下,完成⼯⼚总平⾯布置和车间布置,提供布置⽅案的实施。
产品及产量由决策部门在设计纲领中作出规定;⼚址的确定主要由经营决策⼈员根据某些社会因素,经济因素及⾃然条件做出决策;建⼚⼯作则主要由⼟建施⼯⼈员来完成,与设施布置设计⼈员直接相关的任务是总平⾯布置和车间布置。
如图2-1所⽰,为了完成⼯⼚总平⾯布置和车间布置,需要从产品户及产量Q出发,⾸先对产品组成进⾏分析,确定各零、部件⽣产类型,制定出各个零部件的加⼯、装配⼯艺流程;根据⼯艺流程各阶段的特点划分出⽣产车间,并根据⽣产需要设置必要的职能管理部门及附属⽣产与⽣活服务部门。
整个⼯⼚就是由⽣产车间、职能管理部门、附属⽣产及⽣活服务部门以及为使⽣产连续进⾏⽽:设置的仓储部门这⼏类作业单位所构成。
然后,由⼯⼚布置设计⼈员来完成⼯⼚总平⾯布置及车间布置。
图2-1⼯⼚设计过程在图2-1所⽰的⼯⼚设计过程中,基本给定条件(要素)为产品P及产量Q,涉及到了除平⾯布置设计以外的如制定加⼯,装配⼯艺过程等多种专业技术问题,要求多种专业技术⼈员配合协作来完成。
为了突出平⾯布置设计,可把平⾯布置前各阶段⼯作的结果作为给定要素来处理,包括⼯艺流程R ,辅助服务部门S 及⽣产时间安排T ,这样就形成了单纯的⼯⼚布置模型,如图2-2所⽰。
在R .Muther 提出的系统布置设计(SLP)中,把产品P ,产量Q ,⽣产路线R 、辅助服务部门S 及⽣产时间安排T 作为给定的基本要素(原始资料),成为布置设计⼯作的基本出发点。
1、产品P 是指待布置⼯⼚将⽣产的商品,原材料或者加⼯的零件和成品等。
这些资料由⽣产纲领和产品设计提供,包括项⽬。
品种类型,材料、产品特性等。
产品这⼀要素影响着⽣产系统的组成及其各作业单位间的相互关系、⽣产设备的类型,物料搬运⽅式等。
系统布局法 SLP 第三章
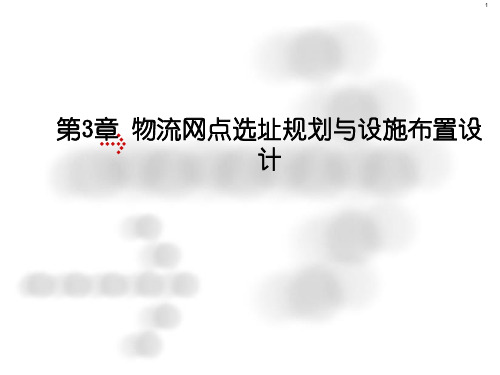
黑
15
主要内容
3.1概述 3.2设施选址 3.3设施布置设计
16
3.2.1设施选址的概念和任务
➢ 设施选址是运用科学的方法确定设置生产或服务系统设施 的具体位置,使之能有效、经济、安全地运行,为实现组 织目标服务的过程。
➢ 设施选址包括宏观地区选择(选位)和微观地点选择(定 址)两个方面。
➢ 设施选址有两种情况: ➢ 1.单一设施的场址选择。 ➢ 2.复合设施的场址选择。
• 这类图例符号表示流程、功能、作业和作业区。 • 流程类型的图例符号采用美国机械工程学会(ASME)所订
标准中的流程图例符号,颜色和阴影采用国际物流管理协 会的标准,如表3-1所示。 • 图3-2 室外场地和面积图例符号
11
表3-1 流程和面积类型图例符号
流程和作业 操作 操作
运输 搬运 储存 停滞 检验
17
3.2.2设施选址的原则
1.工业生产力合理布局原则 2.综合成本费用原则 3.专业化分工协作原则 4.分散与集中相结合原则 5.靠近用户原则 6.前瞻性原则
18
3.2.3设施选址的影响因素
• 设施选址会受到来自组织内外诸多因素的影响,在外部因 素中有些会直接影响组织运作的成本,称为经济性因素, 有些虽然与成本无直接关系,但会间接影响成本,并对组 织的生存和发展产生重要影响,称为非经济性因素。
9
3.1.4设施规划与设计的图例符号
• 这套图例符号用于记录、表示和评定,既可作为节省时间 的简写工具,又可作为同别人交流的手段;既可给规划人 员提供统一的语言,又便于相关人员理解问题。
• 这套图例符号包括以下两个部分。 –流程和面积类型图例符号 –评级和评价类型图例符号
10
第三章车身总布置设计

第三章车身总布置设计3-1 概述车身总布置在很大程度上受制于整车(底盘)总布置的发动机位置。
一、车身总布置与整车总布置的关系在整车总布置和底盘总布置基础上进行,受发动机的位置制约很大。
需整车总布置提供:①汽车总长La、总宽Ba,总高Ha轴距L、轮距B、前悬L F、后悬L R……等控制尺寸;②轴荷分布范围;③底盘各总成的位置和轮廓尺寸——包括动力总成、水箱、前后桥、传动轴、车轮、悬架、转向系等;④乘员数及行李舱要求;⑤使用要求及操纵机构的相互位置等。
二、车身总布置的工作内容①根据整车设计要求确定车身各部分尺寸包括:乘客门、司机门、安全门、行李舱、地板高、侧窗数量及高度、内高、内宽等;②确定整车外形——前后围、车顶、侧围的大致曲线和尺寸,前后风窗位置与角度等;③驾驶区布置——方向盘位置(角度)、仪表板、驾驶员位置及操纵机构和踏板的相互位置;④乘客区布置——座椅布置、通道宽度、内高等;⑤空调系统的位置——制冷、采暖、除霜、通风换气、空气净化装置的位置及管道位置;⑥行李舱大小及位置;⑦视野设计校核;⑧乘客上下车方便性确定;⑨安全性设计——被动安全性(安全带、扶手、软化等)三、车身总布置的主要依据①整车(底盘)总布置的有关参数和发动机布置;②整车的使用条件和用户要求;③国家、行业有关标准、法规;④人机工程学的要求;⑤制造、工艺条件等。
四、车身总部布置的工作程序①车身主要尺寸参数的确定——外廓尺寸和有关总布置尺寸;②车厢内平面布置;③座椅和操纵机构布置;④驾驶区布置——仪表台(板)、驾驶座、空调控制板、操作辅助设备、视野校核等;⑤客车横截面布置——踏步、地板、内高、座椅、侧窗、内行李架、灯具、空调管道等;⑥备胎、油箱、电瓶、行李舱等布置;⑦必要的校核——确定尺寸、位置的需要。
如:发动机舱门、行李舱门、视野、车门等的运动校核。
经过上述工作,即可画出1 : 5车身总布置图。
注意:上述各阶段往往反复交叉进行,很多尺寸(位置)需要反复推敲,修改后方能确定。
系统布置设计-SLP
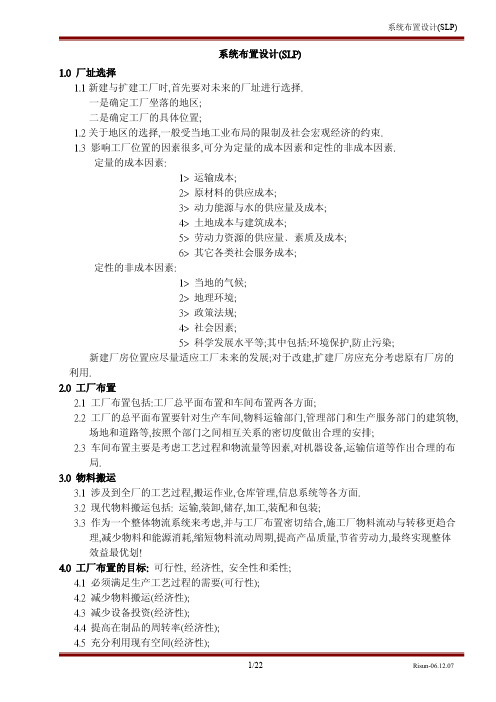
系统布置设计(SLP)1.0 厂址选择1.1新建与扩建工厂时,首先要对未来的厂址进行选择.一是确定工厂坐落的地区;二是确定工厂的具体位置;1.2关于地区的选择,一般受当地工业布局的限制及社会宏观经济的约束.1.3 影响工厂位置的因素很多,可分为定量的成本因素和定性的非成本因素.定量的成本因素:1> 运输成本;2> 原材料的供应成本;3> 动力能源与水的供应量及成本;4> 土地成本与建筑成本;5> 劳动力资源的供应量﹑素质及成本;6> 其它各类社会服务成本;定性的非成本因素:1> 当地的气候;2> 地理环境;3> 政策法规;4> 社会因素;5> 科学发展水平等;其中包括:环境保护,防止污染;新建厂房位置应尽量适应工厂未来的发展;对于改建,扩建厂房应充分考虑原有厂房的利用.2.0 工厂布置2.1 工厂布置包括:工厂总平面布置和车间布置两各方面;2.2 工厂的总平面布置要针对生产车间,物料运输部门,管理部门和生产服务部门的建筑物,场地和道路等,按照个部门之间相互关系的密切度做出合理的安排;2.3 车间布置主要是考虑工艺过程和物流量等因素,对机器设备,运输信道等作出合理的布局.3.0 物料搬运3.1 涉及到全厂的工艺过程,搬运作业,仓库管理,信息系统等各方面.3.2 现代物料搬运包括: 运输,装卸,储存,加工,装配和包装;3.3 作为一个整体物流系统来考虑,并与工厂布置密切结合,施工厂物料流动与转移更趋合理,减少物料和能源消耗,缩短物料流动周期,提高产品质量,节省劳动力,最终实现整体效益最优划!4.0 工厂布置的目标: 可行性, 经济性, 安全性和柔性;4.1 必须满足生产工艺过程的需要(可行性);4.2 减少物料搬运(经济性);4.3 减少设备投资(经济性);4.4 提高在制品的周转率(经济性);4.5 充分利用现有空间(经济性);4.6 有效发挥人力及设备的生产能力(经济性);4.7 生产系统必须具备较大的加工范围,适应多种产品的生产.文件产品品种变化时生产系统调整要简便(柔性);4.8 维持良好的工作环境,确保工作人员舒适安全的工作(安全性);5.0工厂布置的基本设计原则5.1工厂总平面布置设计原则5.1.1满足生产要求,工艺流程合理,减少物流量,同时重视个部门之间的密切度. 具体布置有两种:1>按功能划分厂区. 将工厂的各部门按生产的性质,卫生,防火与运输要求的相似性,将工厂划分成若干段. 其优点:各厂区间功能明确,相互干涉少,环境条件好,但是,这种布置模式难已满足工艺流程和物流合理化的要求.5.1.2 采用系统布置设计模式. 即按各部门之间的物流与非物流相互关系的密切度进行系统布置,因此可以避免物料搬运往返交叉,节约搬运时间与费用.5.2 适应工厂内外运输要求,线路短捷顺直. 工厂布置要与厂内部运输搬运方式箱适应.5.3 合理用地. 节约用地是我国的一项基本国策.5.3.1 根据运输,防火,安全,卫生,绿化等要求,合理确定信道宽度以及各部门建筑物之间的距离,力求总体布局合理紧凑.5.3.2 在满足生产工艺要求的前提下,将联系紧密的生产厂房进行合并,建成联合厂房.此外,可以采用多层建筑或是营建住屋外形.5.3.3 适当预留发展用地.5.3.4 充分注意防火,防爆,防震与防噪.1>安全生产是工厂布置重要问题,在某些危险部门之间应留出适当的防火,防爆距离;2>精密车间应远离震源;3>噪声不仅影响工作,还危害人们的身体健康; 采取隔音措施,降低噪声源的噪音级; 使人员多的部门远离噪声源;5.3.5 利用风向,朝向等自然条件,降低环境污染.5.3.6 充分利用地形,地貌,地质条件.5.3.7 考虑建筑群体的空间组织和造型,注意美学效果.5.3.8 考虑建筑施工的便利条件.6.0车间布置的设计原则6.1 确定设备布置形式. 根据车间的生产纲领,分析产品-产量关系,从而确定生产类型是大量生产,成批生产还是单件生产,由此决定车间设备布置形式是采用流水线式,成组单元式,还是机群式.6.2 满足工艺流程要求. 车间布置保证工艺流程顺畅,物料搬运方便,减少或避免往返交叉物流现象.6.3 施行定置管理,确保工作环境整洁,安全. 车间布置时,除对主要生产设备安排在适当位置外,还需对其它所组成部分包括在制品暂存地,废料存放地,检验试验用地,工人工作用地,信道及辅助部门如:办公室,生活卫生设施等安排出合理位置,确保工作环境整洁及生产安全.6.4 选择适当的建筑形式. 根据工艺流程要求及产品特点,配备适当等级的起重运输设备,进一步确定建筑物的高度,跨度,柱距以及形状.6.5 采光,照明,通风,采暖,防尘,防噪声.6.6 具备适当的柔性,适应生产的变化.7.0 系统布置设计(SLP)模式7.1 系统布置设计的四个阶段:确定位置总体规划详细布置实施7.2系统布置设计的步騆:7.2.1 准备原始资料(P,Q,R,S,T). 同时利用ECRS四大原则进行分析;7.2.2 物流分析与作业单位相互关系分析.7.2.3 绘制作业单位位置图. 根据物料相关表与作业单位相互关系表,考虑每对作业单位相互关系等级的高低,等出两个作业单位相对位置关系.7.2.4 作业单位占地面积计算. 各作业单位所需面积与设备,人员,信道及辅助装置有关,计算出的面积应与可用面积相适应.7.2.5 绘制作业面积相关图. 把作业占地面积加到作业单位位置相关图上即可.7.2.6 修正. 需要考虑的修正因素包括:物料搬运方式,操作方式,储存周期等;同时还需要考虑实际限制条件,如成本,安全和职工倾向等方面是否允许.7.2.7 方案评价与选优.8.0 产品P--产量Q分析8.1 设备布置形式8.1.1 产品原则布置(product layout). 使用于少品种,大量生产类型.8.1.2 工艺原则布置(process layout). 使用于单件生产类型.8.1.3 成组原则布置(group layout). 使用于多品种,中小批量生产类型.8.1.4 固定工位式布置(fixed product layout). 使用于大型设备生产类型.8.2 产品P—产量Q分析分为两个步騆8.2.1 将各种产品,材料和有关的生产项目分组归类.8.2.2 统计和计算每一组或一类产品的产量.8.3 产品P—产量Q分析分表8.3.1 单一产品P—产量Q分析分表(见下表)单一产品P—产量Q分析分表8.3.2 多种产品P—产量Q分析分表(见下表).多种产品P—产量Q分析分表9.0 工艺过程R分析生产类型划分9.1 产品组成分析.产品明晰表9.2 工艺过程设计.零件分组表机器加工过程卡9.3设备选择9.3.1 可行性.9.3.2 经济性.9.3.3 可维护性.设备数量=10.0作业单位的划分10.1 生产车间负荷率*成品率*(1-故障率)*工作时间单件工时计划产量设备明细表生产单位占地面积计算表10.2 仓储部门仓库单位占地面积计算表10.3 辅助服务部门包括辅助生产部门(工具,机修车间),生活服务部门(食堂),其它(车库,传达室);后勤部门占地面积计算表10.4 职能管理部门办公室占地面积计算表11.0 物流分析11.1 据资料统计分析,产品制造费用的20%~50%使用于物料搬运的,有效的布置大约能减少搬运费用的30%左右.在满足工艺的前提下,减少物料搬运工作量是工厂布置设计的最重要目标之一.11.2物流分析的方法. 党务料移动是工艺过程的主要部分时,物流分析就是工厂布置设计的核心问题.11.2.1 工艺过程图. 用于大批量,少品种生产工厂的分析.工艺过程图图例见下页;11.2.2 多种产品工艺过程表. 在多种产品10种左右,批量较大时使用.见多种产品工艺过程表;多种产品工艺过程表1多种产品工艺过程表2W11.2.3 成组方法. 产品达到数十种时,若生产为中,小批量生产的分析.11.2.4 从至表. 品种少,产量小时的分析.从至表单位: t11.3 物流强度. 物料分析包括物料移动的顺序和物流量两个方面.11.4 工艺过程图.权值D JK 的确定4进入下道工序 旁路退回进入下道工序最不理想-2物流顺流程度W: W jk 为上下两个工序之间的物流强度.物料流程顺流程度最大,物流倒流最小,工序排列最佳.作业单位建筑物会总表11.5 作业单位最佳顺序的求解. 可以用线性规划等数学方法求解,也可用以下方法人工近似求解最佳顺序.11.5.1 按照各产品的物流强度的大小顺序,在多种产品工艺过程表中由左到右排列产品工艺过程.对于零件加工生产来说,可以用生产周期内产品产量与零件重量的乘积作为物料强度.11.5.2 从各产品工艺过程图中选取下一道工序,若为第一道工序,安排位多种产品工艺过程表中第一道工序行.11.5.3 重复11.5.2, 直止结束.11.5.4 调整顺序,得到最佳顺序.12.0 物流分析和物流相关表12.1 物流强度等级.物流强度划分等级表物流强度会总表物流强度分析表原始物流相关表作业单位物流相关表13.0 作业单位相互关系分析13.1 作业单位密切度的典型影响因素;13.1.1 物流;13.1.2 工作流程;13.1.3 作业性相似;13.1.4 使用相同设备;13.1.5 使用同意场地;13.1.6 使用相同的文件档案;13.1.7 使用相同的公用设备;13.1.8 使用同一组人员;13.1.9 工作联系频繁程度;13.1.10 监督和管理方法;13.1.11 噪声,震动,烟尘,易燃,易爆危险品的影响;13.1.12 服务的频繁和紧急程度等方面;13.2 作业单位相互关系等级相对应”基准相互关系”14.0 工厂总平面布置14.1绘制作业单位相关图的步騆:14.1.1 从作业相互关系表中求得各作业单位对的综合接近程度,并按其高低将作业单位排序;14.1.2 选择单位距离长度,并规定A级的作业单位距离为一个单位距离长度;E级的作业单位距离为两个单位距离长度,依次类推;14.1.3 将分数最高的作业单位A,摆放在中心位置;14.1.4 依次将作业单位布置倒图中;14.1.5 检查,修改作业单位;14.2 作业单位工作性质符号14.3 关系密级标示方式14.4 基本流动模式:直线型, L型, U型, 环型, S型五种;15.0 物料搬运系统的基本形式16.0 道路布置应满足意下条件:16.1 道路布置应满足工艺﹑物料搬运要求,力求简洁﹑安全﹑联系方便;16.2 道路系统应适应公用管线﹑绿化灯要求;符合<厂矿道路设计规范>级数要求;16.3 满足生产﹑安全﹑卫生﹑防火以及其它特殊要求;16.4 避免货运线路与人流线路交叉,避免公路与铁路交叉;16.5 厂内道路系统一般采用整交和环型布置,交叉路口转弯处的视距不应小于30m;17.0 道路布置形式:17.1 环状式布置,使个部门之间联系比较方便,变于分区.适应于场地比较宽阔.17.2 党条件限制不能使用环状布置时,采用尽端式布置,道路行到某个地点就终止了,这时在道路的端头应设置回车场,以便车辆掉头.以下是回车场的布置形式:17.3 混合式布置,就是灵活使用以上两种模式,使用于各种类型工厂;18.0 根据<厂矿道路设计规范>有下表厂内汽车道路主要技术标准电瓶车道主要技术指针厂内道路到相邻建筑物/构筑物的最小距离几种建筑物的噪声防护间距树木与相邻建筑物/构筑物之间的距离一般地区明沟至建筑物距离我国部分地区建筑朝向实例1.0 加权值的设定表明企业注重那一方面,当物流因素并不明显大于其它因素时m:n=1:1;2.0 综合相互关系的计算2.1作业单位对的计算P=[N(N-1)]/22.2非物流作业单位相互关系图非物流作业单位相互关系图2.3综合相互关系等级与划分比例综合相互关系等级与划分比例2.4作业单位之间综合关系计算表作业单位之间综合关系计算表3.0 划分关系密级4.0 建立作业单位综合相互关系表。
系统布置设计

系统布置设计系统布置设计是一种久负盛名的经典方法。
这种方法要建立一个相关图,表示各部门的密切程度。
相关图类似于车间之间的物流图。
相关图要用试算法进行调整,直到得到满意方案为止。
接下来就要根据建筑的容积来合理地安排各个部门。
为了便于对布置方案进行评价,系统布置设计也要对方案进行量化。
根据密切程度的不同赋予权重,然后试验不同的布置方案,最后选择得分最高的布置方案。
简介系统布置设计SLP(systematic layout planning,SLP)基本内容系统布置设计(SLP) 是一种条理性很强、物流分析与作业单位关系密切程度分析相结合、求得合理布置的技术,因此在布置设计领域获得极其广泛的运用。
国内在80 年代以后引进了这一理论,收效非常显著。
而计算机辅助设施布置方法利用计算机的强大功能,帮助人们解决设施布置的复杂任务,为生产系统的设施新建和重新布置提供强有力的支持和帮助,节省了大量人力和财力,尤其是对大型项目和频繁的重新布置。
应用R.Muther(缪瑟)将系统工程概念和系统分析方法应用于工厂布置,由此形成了该方法。
自系统布置设计法诞生以来,设施规划设计人员不但把它应用于各种机械制造厂设计,而且还在探索系统布置设计在其他领域的应用前景。
编辑本段传统的系统布置设计传统的系统布置设计SLP法在SLP方法中将研究工程布置问题的依据和切入点归纳为P—产品、Q—产量、R—工艺过程、S—辅助部门、T—时间5个基本要素。
采用SLP法进行企业总平面布置的首要工作是对各作业单位之间的相互关系做出分析.包括物流和非物流的相互关系.经过综合得到作业单位相互关系表,然后,根据相互关系表中作业单位之问相互关系的密切程度.决定各作业单位之间距离的远近,安排各作业单位的位置.绘制作业单位位置相关图.将各作业单位实际占地面积与作业单位位置相关圈结合起来.形成作业单位面积相关圈;通过作业单位面积相关图的修正和调整.得到数个可行的布置方案然后采用加权因素对各方案进行评价择优.并对每个因素进行量化以得分最多的布置方案作为最佳布置方案。
系统布置设计(SLP)及案例分享 ppt课件
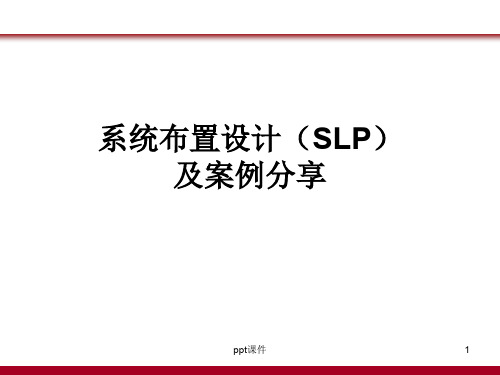
C5
A8
车床
C5 AB11
钻床
B3
C5 A8
铣床
A8
ABC16
检验
A8
ABC16
包装
ABC16
成品
ppt课件
45
• 从-至表(From —To Chart)
产品及物流量从至表
至 从
原料
锯床
车床
钻床
铣床
检验
包装
成品
合计
原料
AC104
C108
212
锯床
C60
A288
343
车床
C80 AB264
344
钻床
6.面积相关图解
7.修正因素
方案X
方案Y
作业单位面 积相关图
8.实际条件限制
方案Z
成本、安全和 职工倾向等
寻优阶段
技术、费用及其 它因素评价
9.评价
选出的最佳布置 选择阶段
方案
系统布pp置t课设件 计工作思路
35
二、系统布置设计的基本要素
• 系统布置设计的基本要素
– P产品或材料或服务
– Q数量
– R生产路线(工艺过程)
• 加工过程 ——这是所选择布置类型的主要约束条
件 • 空间利用
——布置总是约束在建筑物内的实际范围内。
ppt课件
30
三、设施布置决策依据
• 生产能力
最理想的布置应能适应环境 的变化
——当公司目标、用户需求、加工过 程和空间有效利用率确定后,便可估算
所需的生产能力和重新布置后所获得的
生产能力。
ppt课件
ppt课件
7
二、设施规划与设计的研究范围
系统布置设计方法
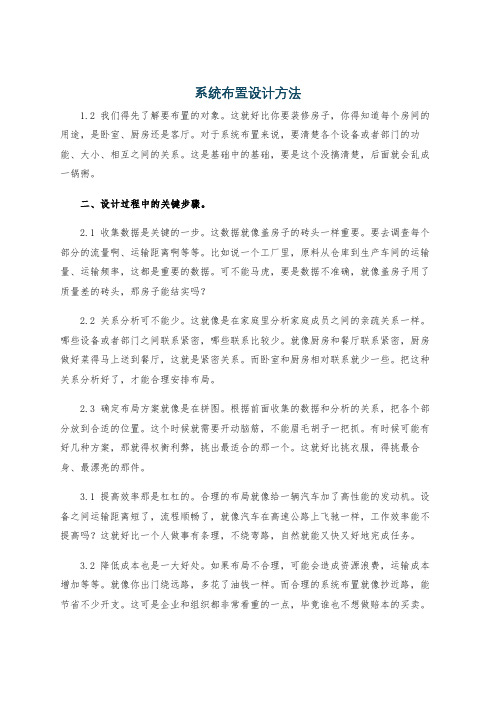
系统布置设计方法1.2 我们得先了解要布置的对象。
这就好比你要装修房子,你得知道每个房间的用途,是卧室、厨房还是客厅。
对于系统布置来说,要清楚各个设备或者部门的功能、大小、相互之间的关系。
这是基础中的基础,要是这个没搞清楚,后面就会乱成一锅粥。
二、设计过程中的关键步骤。
2.1 收集数据是关键的一步。
这数据就像盖房子的砖头一样重要。
要去调查每个部分的流量啊、运输距离啊等等。
比如说一个工厂里,原料从仓库到生产车间的运输量、运输频率,这都是重要的数据。
可不能马虎,要是数据不准确,就像盖房子用了质量差的砖头,那房子能结实吗?2.2 关系分析可不能少。
这就像是在家庭里分析家庭成员之间的亲疏关系一样。
哪些设备或者部门之间联系紧密,哪些联系比较少。
就像厨房和餐厅联系紧密,厨房做好菜得马上送到餐厅,这就是紧密关系。
而卧室和厨房相对联系就少一些。
把这种关系分析好了,才能合理安排布局。
2.3 确定布局方案就像是在拼图。
根据前面收集的数据和分析的关系,把各个部分放到合适的位置。
这个时候就需要开动脑筋,不能眉毛胡子一把抓。
有时候可能有好几种方案,那就得权衡利弊,挑出最适合的那一个。
这就好比挑衣服,得挑最合身、最漂亮的那件。
3.1 提高效率那是杠杠的。
合理的布局就像给一辆汽车加了高性能的发动机。
设备之间运输距离短了,流程顺畅了,就像汽车在高速公路上飞驰一样,工作效率能不提高吗?这就好比一个人做事有条理,不绕弯路,自然就能又快又好地完成任务。
3.2 降低成本也是一大好处。
如果布局不合理,可能会造成资源浪费,运输成本增加等等。
就像你出门绕远路,多花了油钱一样。
而合理的系统布置就像抄近路,能节省不少开支。
这可是企业和组织都非常看重的一点,毕竟谁也不想做赔本的买卖。
高级物流师知识讲义:系统布置设计
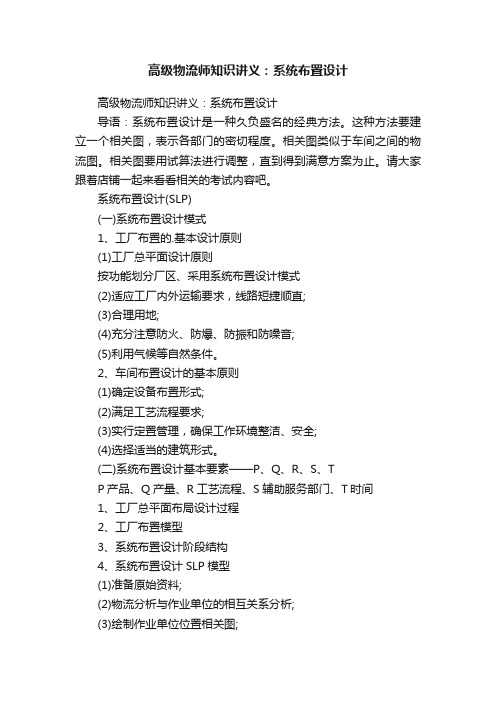
高级物流师知识讲义:系统布置设计高级物流师知识讲义:系统布置设计导语:系统布置设计是一种久负盛名的经典方法。
这种方法要建立一个相关图,表示各部门的密切程度。
相关图类似于车间之间的物流图。
相关图要用试算法进行调整,直到得到满意方案为止。
请大家跟着店铺一起来看看相关的考试内容吧。
系统布置设计(SLP)(一)系统布置设计模式1、工厂布置的.基本设计原则(1)工厂总平面设计原则按功能划分厂区、采用系统布置设计模式(2)适应工厂内外运输要求,线路短捷顺直;(3)合理用地;(4)充分注意防火、防爆、防振和防噪音;(5)利用气候等自然条件。
2、车间布置设计的基本原则(1)确定设备布置形式;(2)满足工艺流程要求;(3)实行定置管理,确保工作环境整洁、安全;(4)选择适当的建筑形式。
(二)系统布置设计基本要素——P、Q、R、S、TP产品、Q产量、R工艺流程、S辅助服务部门、T时间1、工厂总平面布局设计过程2、工厂布置模型3、系统布置设计阶段结构4、系统布置设计SLP模型(1)准备原始资料;(2)物流分析与作业单位的相互关系分析;(3)绘制作业单位位置相关图;(4)作业单位占地面积计算;(5)绘制作业单位面积相关图;(6)修正;(7)方案评价与择优。
(三)作业单位S的划分1、生产车间;2、仓储部门;3、辅助服务部门;4、职能管理部门。
(四)物流分析1、物流强度——A、E、I、O、U(超高、特高、较大、一般、可忽略)2、工艺流程图(五)作业单位相互关系分析要素:1、产品(P)2、质量(Q)3、辅助服务部门(S)A、E、I、O、U(1)P、Q、R是物流分析的基础(2)P、Q、S是作业单位相关系分析的基础。
(六)作业单位综合相互关系表1、重要等级表关系等级符号作业单位对比例(%)绝对必要靠近 A 1~3特别重要靠近 E 2~5重要 I 3~8一般 O 5~15不重要 U 20~85不希望靠近 X 0~102、关系表(七)作业单位位置相关图1、作业单位工作性质符号(P166)2、作业单位关系等级表示方式(八)作业单位面积相关图1、基本流通模型直线型、L型、U型、环形、S型方案评价与选择(一)综合指标比较评价1、优缺点比较法——初始方案筛选,内容并不具体,将有明显缺点的方案舍弃。
第三章_人机工程布置与车室尺寸设计.

3.1 作业空间设计的原则
作业空间设计的人机工程学原则 (1) 作业空间设计必须从人的要求出发,保证人的安 全、健康、舒适、方便。 (2) 从客观条件的实际出发,处理好安全、健康、舒 适、高效、经济诸方面的关系。 (3) 根据人体生物力学、人体解剖学和生理学的特性, 合理布置操纵装置和显示装置。
W8 AHP点y坐标 H8 AHP点z坐标 L1 PRP点x坐标 W1 PRP点y坐标 H1 PRP点z坐标
代号 含义 H14 眼椭圆上缘到内后视镜下缘垂直距离 H17 转向盘中心到AHP的垂直距离 H30 SgRP到AHP或FRP的垂直距离 H35 后视图上,头廓包络线垂直移动到与顶盖零件
典型的作业空间设计
立姿作业空间设计 • 站立工作时工作台的高度与工作的性质密切相关
– 精密的工作要求工作面距离眼睛近一些,以改善视力 – 而重体力劳动则倾向较低的工作面,以便于手部用力
3.4 工作台设计
工作台是包含操纵装置和显示装置的作业单元, 主要用于以监控为目的之作业场所。
工作台设计的关键任务是将操纵装置与显示装置布置 在操作者的正常作业空间范围内, 保证操作者方便而舒 适地观察和操作, 并为操作者长时间作业提供舒适稳定 的坐姿。
2021/5/30
硬点和硬点尺寸
汽车实际H点:三维人体模型按规定的步骤安放于汽车座椅中时, 人体模型上左右两H点标记连接线的中点。它表示人体在汽车上的 实际位置。它是汽车内饰布置人机工程布置设计的基准点
R点:座椅调整至正常驾驶位置范围的最后、最下时的胯点。是整车 内饰布置设计的开始点。
2021/5/30
2、踝角的定义:
系统布置设计 (SLP)参考资料
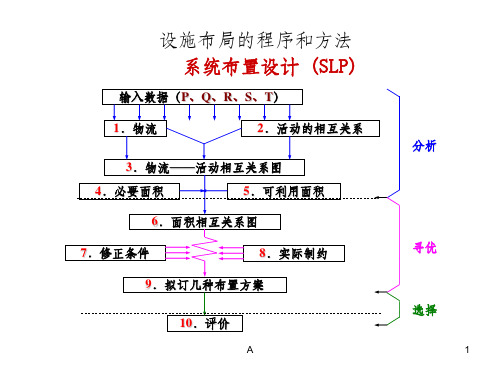
A
17
• 解:根据题目中给出的条件,有
Q——全年物料入库量(t);
q——单位有效面积的平均承重能力(t/m2);
T0—A—年有效工作日数;
16
• 举例: 某建材公司计算建造一座建筑材料仓 库,年入库量为20000吨,一年中工作300 天,物料平均储备期50天,有效面积上平均 货重0.7吨/平方米,仓库利用系数为0.4, 试用 荷重计算法求仓库面积。
2
(1)蜂窝损失
定义 如果在一列货堆上取走一层或几层,只要不被取尽,所产生的 空缺不能被别的货物填补,留下的空位有如蜂窝,故名蜂窝形 空缺。
A
3
图12 蜂窝损失示意图
蜂窝损失率
蜂窝损失空缺系数的计算如下。 空缺系数H的期望值为:
E(H ) 1 n1 i
n i0 n
•式中n— 一列货位堆码货物件数;i = 0, 1, 2, …。 计算蜂窝损失空缺系数?
A
10
例题
某种货物C为木箱包装形式,尺寸(长×宽×高)为 1100×800×900mm,箱底部平行宽度方向有两根垫木,可用 叉车搬运,在仓库中堆垛放置,最高可堆4层。C货物最大库存 量为1000件,请考虑通道损失(设叉车直角堆垛最小通道宽度 为3.6m,货叉长1m)和蜂窝损失确定其需要的存储面积。
讨论 货架存储有没有空缺系数?
A
Hale Waihona Puke 4(2)通道损失定义 通道损失则是由于通道占据了有效的堆放面积,无论分类堆码, 还是货架储存,都存在通道损失。
通道损失计算: 蜂窝损失计算:
La Wa (Wa 2d ) E(H ) (1 La )
式中: Wa—通道宽度; d—货堆深度。
总的空间损失计算:为通道损失和蜂窝损失的和。
第3章 物流节点规划设计
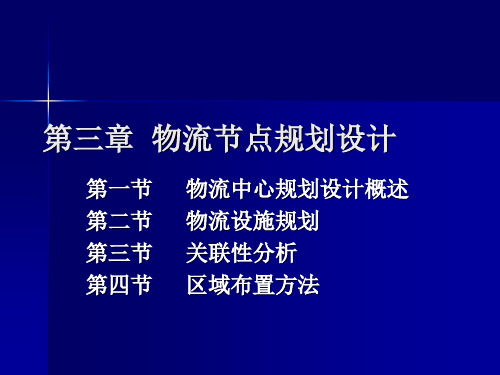
锯齿形
注意:在同一生产图部流门程动中线,基往本形往式多种动线形式同时存在。
(2)定性关联图
可用于物流关系和非物流关系的分析,不只 针对生产部门,包括辅助劳动、办公室、服 务设施等均可根据彼此间的相关性来加以分 析,以决定较理想的规划位置 。
活动关系包括:
1.程序上的关系:建立在物料流和信息流之间的关系; 2.组织上的关系:建立在各部门组织之间的关系; 3.功能上的关系:为区域之间因功能需要而形成的
主要针对生产部门,只考虑物料的流程,配合 制造程序与设备特征,希望尽量减少制造过程 所需行经的距离及逆回流程,以提高生产的速 度及效率,并据此原则规划工作区和设备位置
主要用于物流设施规划中一些局部作业设施设 计,例如物料搬运系统的设计一般进行流程动 线分析。
流程动线的四种基本形式
直线形
L形
U形
1、设计内容包括: 综合性物流中心总体功能 物流中心实体作业功能 2、设计原则及其因素
综合性物流中心总体功能
– 集散功能 – 仓储功能 – 配送功能 – 流通加工及包装等增值功能 – 物流信息服务功能 – 商品展示功能
物流中心实体作业功能
1、进货作业 到货 ——卸货——理货——验收——入库 2、储存作业 入库上架或堆码——储位管理—库存盘点—养护 3、拣货作业 由订单生成拣货信息——拣货方式——拣货——输送到出库区 4、补货作业 从保管区域将货品移到另一个为了做订单拣取的动管拣货区域 5、流通加工 根据客户要求或运输要求进行相应的流通加工 6、出货作业 出货单据——检验——包装——输送搬运至出货暂存区——装
车
设计原则及影响因素
设计原则
– 1、物流中心的功能设计既要考虑功能的集 成性,又要考虑专业性和规模化
系统布置设计——SLP方法

和设备的更新。 最舒适的作业环境—— 保证安全,满足生理、心理要求。 最便捷的管理————使有密切关系或性质相近的作业单位布置在一个区
域或靠近布置。 力求投资最省
• 在物流分析时要验证工艺路线是否正确、合理, 检查是否可以取消、合并、改变顺序、位置或人 员和改进细节。ECRS
• 因此正确合理的设施布置不仅能提高生产效率和 工作效率,也是节约物流费用从而降低产品或服 务成本的重大措施。
• 除了物料和设施外,分析职员工作时在设施内走 动时的路线也是很重要的。人员流动分析用来安 排工厂内所必不可少的服务设施,以方便职员的 工作。
✓ 建筑设计——对建筑物结构进行设计,以满足功能、空间、经济、安
全,美观等需要。
✓ 公用工程设计——对电力、热力、照明、排水、通风等进行协调设计。 ✓ 信息通信设计——对信息通信传输、管理维护等系统进行全面设计。
二、设施布置设计的内容
☻ 工厂总体布置
解决工厂各个组成部分,包括生产车间、辅助生产车间、仓库、动力站、 办公室、露天作业场地等各种作业单位和运输线路、管线、绿化及美化设 施的相互位置,同时要解决物料的流向和流程、厂内外运输的联系及运输 方式。
图1 产品原则布置示意图
图2 汽车后桥加工生产线
图3 汽车装配生产线
图4 汽车焊接生产线
产品原则布置的基础
标准化及作业分工。整个产品被分解成一系列标准化的作业,由专门的人力及 加工设备来完成。
产品原则布置优缺点比较
优点
①由于布置符合工艺过程,物流畅 通
②由于上下工序衔接,存放量少物
高校学生寝室自动喷水灭火系统布置设计说明
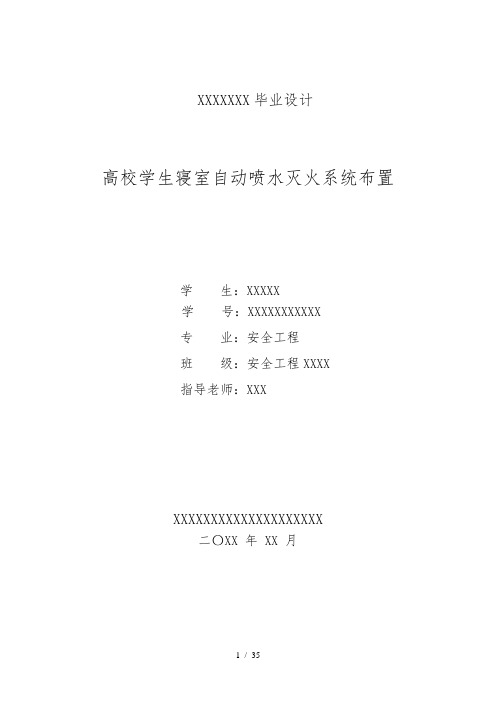
XXXXXXX毕业设计高校学生寝室自动喷水灭火系统布置学生:XXXXX学号:XXXXXXXXXXX专业:安全工程班级:安全工程XXXX指导老师:XXXXXXXXXXXXXXXXXXXXXXX二〇XX 年 XX 月摘要本文以高校寝室为对象,对如何在高校寝室中设置自动喷水灭火系统进行了研究。
近年来高校火灾的频频发生,严重威胁到了高校学生的安全和高校财产的安全。
自动喷水灭火系统是目前世界上公认的最有效、普与率最高的消防设施,它是一种能够在发生火灾时,与时探测到环境温度的骤变,自动打开喷头进行喷水灭火的装置,因为其具有监测火灾发生,与时出水控制火灾,自动报警等优点,广泛运用于各类建筑当中。
本文就以高校寝室为研究对象,分析并设计自动喷水灭火系统,根据《自动喷水灭火系统设计规》介绍了自动喷水灭火系统中各组件的设置以与工作原理,介绍了自动喷水灭火系统喷头的选型以与配水管、管网的布置要求,水力计算部分详细介绍了作用面积法,并采用作用面积法进行了水力计算。
本文的设计目的是在高校寝室中发生火灾的时候,将火灾第一次时间抑制在初始阶段,能够与时地采取有效的灭火措施,保障学生们的人身安全,最大限度地减少火灾造成的生命和财产损失。
关键词:自动喷水灭火系统;喷头;水力计算;作用面积法AbstractThis thesis researched how to set up automatic sprinkler system in the Universities bedroom.In recent years,fires in the Universities is occur frequently and it have been a serious threat to the University student`s lives and property.Sprinkler system is a fire facilities which is world recognized the most effective and have the highest usage.It`s a system which can detected the fires in time and automatically open the nozzle sprinkle and also issued a fire alarm when fires.because of sprinkler system have automatic sprinkler,fire detection,automatic alarm and control fires in beginning,it has been widely used in building fire.In this thesis,the purpose of the design of automatic sprinkler system against the analysis of the Universities bedroom.According to’Design specifications of the automatic sprinkler system’,this thesis introduced how to select sprinkler nozzle and installation requirements of pipeline and pipe network.In the hydraulic calculation this thesis introduced the method of active area,and use this method to calculate hydraulic.This thesis in order to discover the fire in the beginning,andsuppress the fire in the initial stages,to minimize loss of life and property caused by fires.Key words:automatic sprinkler system;sprinkler nozzle;hydraulic calculation;the method of active area目录第一章绪论21.1研究背景21.2国外研究现状21.2.1国研究现状21.2.2国外研究现状41.4研究目的41.5研究容5第二章自动喷水灭火系统52.1系统类型52.1.1湿式自动喷水灭火系统52.1.2干式自动喷水灭火系统82.1.3预作用自动喷水灭火系统92.2研究对象92.3系统组件102.3.1喷头102.3.2报警阀组112.3.3水流指示器112.3.4压力开关122.3.5末端试水装置122.3.6供水系统12第三章自动喷水灭火系统设计133.1喷头133.1.1喷头选型133.1.2喷头的保护面积143.1.3喷头布置153.2管网布置173.3小结19第四章水力计算204.1作用面积法204.2计算过程224.3小结29第五章结论与展望295.1结论295.2展望30参考文献30致32第一章绪论1.1研究背景经济的迅速发展使社会对人才的需求日益加大,各大高校为了满足社会的需求,逐年扩招,高校寝室人员密集,电器繁多,加之学生安全意识不足,违规使用大功率电器,造成很大的火灾隐患,近年来中外高校宿舍火灾事故频频发生,例如2008年商学院徐汇校区因学生使用“热得快”烧水引起火灾导致4人死亡,2008年中央美术学院发生火灾导致100多间寝室被烧毁。
系统布置设计

+ 本实例以某汽车厂设施布置的实例,对设施布置的原则、布置
的基本形式以及流动模式做一个简单的分析
+ 该汽车厂产品单一。从整个工厂布置来看,它是采用产品原则 + + + + +
来进行总体布置规划的。 整个生产线分成了几个部分: 冲压车间,主要生产汽车所需的车头、车门等部件; 上漆车间,从冲压车间出来的半成品在这里进行喷涂、上漆; 装配车间,装配底盘、发动机、车身、内饰等部件,完成成品 汽车。 其中车厢、汽车底盘以及发动机等汽车部件主要采用外购的方 式。
+ 设施布置包括工厂总体布置和车间布置。
“作业单位(Activity)”是指布置图中各个 不同的工作区或存在物,是设施的基本区划。 该术语可以是某个厂区的一个建筑物、—个车 间、一个重要出入口;也可以是一个车间的一 台机器、一个办公室的一个部门。
1.符合工艺过程的要求 2.最有效地利用空间 3.物料搬运费用最少 4.保持生产和安排的柔性 5.适应组织结构的合理化和管理的方便 6.为职工提供方便、安全、舒适的作业环境
自SLP法诞生以来,设施规划设计人员不但把它 应用于各种机械制造厂的设计中,而且不断发展应 用到一些新领域,如公司办公室的布置规划、连锁 餐厅的布置规划等服务领域。
工厂总体布置设计:解决工厂各组成部分的相互位 置,同时解决物料的流向和流程、厂内外运输的联接 及运输方式。
车间布置设计:解决各生产工段、辅助服务部门、 储存设施等作业单位及工作地、设备、通道、管线之 间的相互位置,同时也应解决物料搬运的流程及运输 方式。 设施布置包括工厂总体布置和车间布置
+ 工艺原则布置
+ 产品原则布置
+ 定位布置 + 成组技术布置
- 1、下载文档前请自行甄别文档内容的完整性,平台不提供额外的编辑、内容补充、找答案等附加服务。
- 2、"仅部分预览"的文档,不可在线预览部分如存在完整性等问题,可反馈申请退款(可完整预览的文档不适用该条件!)。
- 3、如文档侵犯您的权益,请联系客服反馈,我们会尽快为您处理(人工客服工作时间:9:00-18:30)。
图3-2:不同的生产类型
六、设施布置的基本形式
工艺原则布臵
移动式布臵
产品原则布臵
设施布臵
成组技术布臵
固定工位布臵
适合多品种小批量生产的工艺布置原则:
根据工艺特点,把同种类型的一群设备和 人员集中布臵在一个地方;
各类机床间也有一定的顺序安排,通常
按照大多数零件的加工路线来排列;
如医院。
第三章
第一节
设施布置设计
概述
第二节 第三节
设施布置的设计 系统布置设计(SLP)
Question
设施布置设计包含哪些内容? 设施布置中出现目标矛盾怎么办? 如何选取设施布置型式来适应市场变化? 如何避免工序交错流动、制成品混杂? 如何进行布置的定量分析?
第一节
定义
概 述
根据企业的经营目标和生产纲领,在已确认的空间场所内,
工艺原则布置转换为成组布置的步骤
将零件进行分类;
识别零件组的物流类型; 将机器和工艺分组,组成工作单元。
如何实现大规模定制?
面向市场是否就是面向顾客? 多样化是否就是定制?
1、两种概念的思考:
2、实现大规模定制需解决的基本问题:
产品策略——定制产品和适应性产品; 产品结构——模块化产品及工艺; 工艺过程基础设施——模块化设施,工作流……
空间利用——布臵总是约束在建筑物内的实际范围内。 生产能力——当公司目标、用户需求、加工过程和空间
有效利用率确定后,便可估算所需的生产能力和重新布臵 后所获得的生产能力。
例如:机械车间、大学、酒店,应如何适当选择生产能力
的测定单位?
回答:
应适当选择生产能力的测定单位,如机械车间可用机器小时, 大学可容纳学生数/年,酒店可用房间床位数。
适合持续改善生产模式的成组布置原则:
把完成一组相似零件的所有或极大部分加工工序 的多种机床组成机器群,以此为一个单元,再在 其周围配臵其它必要设备的布臵形式。
L
D
D
加工单元1
L G
加工单元2
NCL D
L D
加工单元3
图3-5
成组原则示意图
成组原则布置优缺点
优
高; 2、流程通畅,运输距离较短,
点
五要素对设施布置的影响
P:产品或材料或服务(Production)
指规划设计的对象所生产的产品、原材料、加工的零部 件或提供服务的项目。包括原材料、进厂物料、工序间 储备、产品、辅助材料、废品、废料、切屑、包装材料 等。这一要素影响着设施的组成及其相互关系、设备的 类型、物料搬运的方式等。
Q:数量或产量(Quantity)
车间布置设计
☻ 解决各生产工段、辅助服务部门、储存设
施等作业单位间的相互位臵;
☻ 解决工作、设备、通道、管线间的相互位
臵;
☻ 解决物料搬运流程和运输方式。
作业单位(Activity)
——是设施的基本区划。 可大至一个建筑物或一个车间, 亦可小至一个出入口或一台机 器—— 如何划分,须看规划设计
结论:最理想的布臵应能适应环境的变化!
五、设施布置型式的选择
动态的 大规模定 制模式 开发 产品的变化 大规模生 产模式 更新 创新模式
模块化 持续改 善模式
连接
静态的 静态的 过程的变化 动态的
图3-1:生产模式的演变
少品种大批量生产
按产品产量分 生 产 类 型 按生产组织分
中品种批量生产 多品种小批量生产 定制生产 订货生产 存货生产
工作所处的阶段或层次。
一、设施布置的总目标
在已确定的空间场所内,将物流全过 程的人员、设备、物料所需的空间做 最适当的分配和最有效的组合。
二、设施布置的具体目标
最好的工艺流程 ——保证工艺流程畅通,生产连续
时间短。
最少的物料搬运费用 ——运输路线简化,避免往返
和交叉。
最有效地利用空间 ——使建筑设备和单位制品的占
缺
点
1、由于产品成组,设备利用率
1、需要较高的生产控制水平以平
衡各单元之间的生产流程; 2、若单元间流程不平衡,需中间
搬运量少;
3、有利于发挥班组合作精神; 4、有利于扩大员工的作业技能; 5、兼有产品原则布置和工艺布置 的优点。
储存,增加了物料搬运;
3、班组成员需掌握所有作业技能; 4、减少了使用专用设备的机会; 5、兼有产品原则布置和工艺原则布 置的缺点。
(一)基本要素
(1) P(产品或材料或服务) (2) Q(数量或产量)
(3) R(生产路线或工艺过程)
(4) S(辅助服务部门) (5) T(时间或时间安排)
P、Q两个基本要素是一切其他特征或条件的基 础。
要素分析
五个要素分别回答以下问题:
P——Product 生产什么? Q——Quantity 生产多少? R——Routing 怎么生产? S——Supporting service 用什么支持生产? T——Time 何时生产?
按照从原材料的接收,零件和产品的制造,成品的包装,发
运等全过程,力争将人员、设备和物料所需要的空间做最适
当的分配和最有效的组合,以获得最大的经济效益。
内容
包括工厂总体布臵和车间布臵。
工厂总体布置设计
解决工厂生产及辅助生产车间、仓库、动力站、 办公场所等作业单位相互位臵;
解决运输线路、管线、绿化及美化设施的相互位 臵; 解决物料的流向和流程、厂内外运输联接及运输 方式。
公司目标 —— 布臵应达到的目标是存储费用、劳动力、
闲臵设备保持在一定的水平之下,从而达到预期的产量和利 润,但相对重要性却不完全相同(货比三家)。
用户需求——我们关心的是当前与未来的需求量水平
及产品品种搭配(产品策略不同,则布臵策略也将不同)。
加工过程——这是所选择布臵类型的主要约束条件。
问题的解析
——系统化布臵设计(Systematic Layout Planning)
32
第二节
设施布置的设计
一、工艺原则布臵的设计
二、产品原则布臵的设计
三、成组布臵的设计 四、定位布臵的设计
一、工艺原则布置的设计
是最常用的一种布臵方法。用于对具有类似工艺 流程的工作部门进行布臵,使其相对位臵达到最 优。 最优的布臵经常意味着将彼此之间物流量较大的 部门相邻布臵,使设施间物料搬运费用最小。
二、基本流动模式:
直线型——生产过程短且简单 L 型——绕开一定的建筑物或设施 U 型——出入口在同一相对位臵 环 型——出入口在同一点 S 型——较大面积内安排较长的生产线
储 涂 装 仓 铣 车 压 存 装 配 库
储存
压
涂装
装配
铣
车
仓库
A)直线流动
B)S型流动
基本流动模式示意图
直线型 “L”型 “U”型 环 型
有空间小。
最好的柔性——设施布臵适应产品需求的变化、工艺
和设备的更新。 要求。
最舒适的作业环境 ——保证安全,满足生理、心理 最便捷的管理 ——使有密切关系或性质相近的作业
单位布臵在一个区域或靠近布臵。
三、目标矛盾来源
例:
对性质相近的作业单位布臵在一个
区域可满足管理的方便性和组织结 构的合理化,却可能导致物流量的 增大; 满足尽量减少运输和交叉的目标, 却可能违反柔性目标……
出现目标矛盾的根源和方法
根源:
生产系统的目标本身经常难以捉摸
(明确战略思路)
方法:
不存在能解决一切问题的方法
(பைடு நூலகம்统最优不如系统合理)
科学与艺术结合
理性与感性结合(建立学习型组织)
(谁说得清家庭布臵更科学还是更艺术)
四、设施布置决策依 据
公司目标、用户需求、加工过程、空间利用、 生产能力等。
S:辅助服务部门 (Supporting Service)
指保证生产正常运行的辅助服务性活动、设施以及服务的人 员。包括道路、生活设施、消防设施、照明、采暖通风、办 公室、生产管理,质量控制及废物处理等;它是生产的支持 系统,从某种意义上来说对生产系统的正常运行起着举足轻 重的作用。
指所生产、供应或使用的材料或产品的数量或服务的 工作量。这一要素影响着设施规模、设备数量、运输量、 建筑物面积等。
R:生产路线或工艺过程(Routing)
指根据所生产的产品品种、数量等设计出的工艺流程、物流 路线、工序顺序等,可以用设备表、工艺路线卡、工艺过程 图等表示。它影响着各作业单位之间的关系、物料搬运路线、 仓库及堆放地的位臵等。
3、模块化的基础:
产品合理化——使产品系列与企业战略目标一致; 产品标准化——将某些首选的零件标准化,从而减 少零件数目; ……
现象分析:
某中档次轿车车型中使用了110种散热片, 300种烟灰缸、437种仪表盘,1200种车 内地毯,6000种紧固件……
思考与讨论:
l l
零件激增的原因和后果是什么? 如何进行模块化设计 ——按功能分割 模块化?
装配模块
装配模块 装配模块 办公室 模块
脊柱型模块建筑
问题:如何避免工序交错流动、
制成品混杂? 一、考虑要素:
最重要的是要考虑出、入口的位臵——由于 外部运输条件或原有布臵的限制,需要按照 给定的出入口位臵来规划流动模式。 此外还应考虑场址、建筑物的轮廓尺寸、生
产流程的特点和生产线长度、通道的设臵等。
3、操作人员作业多样化,有利于 提高工作兴趣和职业满足感。
3、库存量相对较大。
适合少品种大批量生产的产品布置原则: