注塑工艺培训
注塑工艺基础知识培训
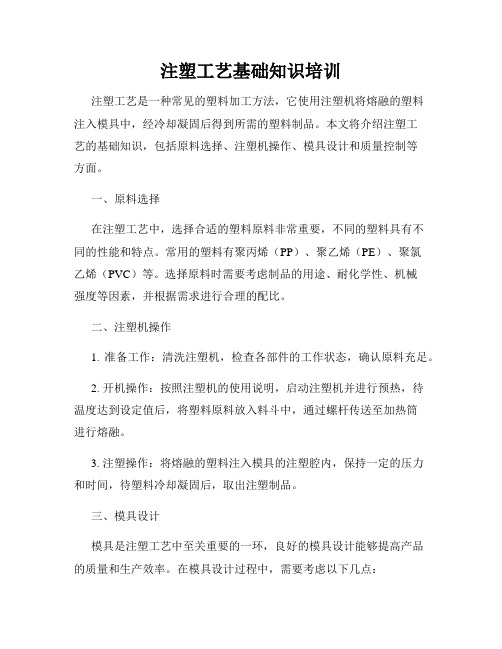
注塑工艺基础知识培训注塑工艺是一种常见的塑料加工方法,它使用注塑机将熔融的塑料注入模具中,经冷却凝固后得到所需的塑料制品。
本文将介绍注塑工艺的基础知识,包括原料选择、注塑机操作、模具设计和质量控制等方面。
一、原料选择在注塑工艺中,选择合适的塑料原料非常重要,不同的塑料具有不同的性能和特点。
常用的塑料有聚丙烯(PP)、聚乙烯(PE)、聚氯乙烯(PVC)等。
选择原料时需要考虑制品的用途、耐化学性、机械强度等因素,并根据需求进行合理的配比。
二、注塑机操作1. 准备工作:清洗注塑机,检查各部件的工作状态,确认原料充足。
2. 开机操作:按照注塑机的使用说明,启动注塑机并进行预热,待温度达到设定值后,将塑料原料放入料斗中,通过螺杆传送至加热筒进行熔融。
3. 注塑操作:将熔融的塑料注入模具的注塑腔内,保持一定的压力和时间,待塑料冷却凝固后,取出注塑制品。
三、模具设计模具是注塑工艺中至关重要的一环,良好的模具设计能够提高产品的质量和生产效率。
在模具设计过程中,需要考虑以下几点:1. 结构设计:合理的模具结构能够保证注塑制品的形状和尺寸精度,同时方便模具的装卸和维护。
2. 冷却系统设计:冷却时间对注塑周期有着重要影响。
优化冷却系统的设计,能够提高生产效率并避免制品缺陷。
3. 模具材料选择:模具需要具有足够的硬度和耐磨性,常见的模具材料有H13、S7等。
四、质量控制在注塑工艺中,质量控制是保证产品质量的关键。
以下是一些常用的质量控制措施:1. 注塑机参数控制:根据产品要求,合理设置注塑机的温度、压力、注塑速度等参数,保证制品的质量。
2. 模具维护:定期对模具进行检查和维护,及时修复损坏的部件,避免因模具问题引起的质量缺陷。
3. 制品检测:对注塑制品进行外观检查、尺寸测量等多项检测,确保产品符合设计要求。
总结:通过本文的培训,我们了解了注塑工艺的基础知识,包括原料选择、注塑机操作、模具设计和质量控制等方面。
合理运用这些知识,可以提高注塑制品的质量和生产效率,为塑料制品加工行业的发展做出贡献。
注塑成型工艺培训
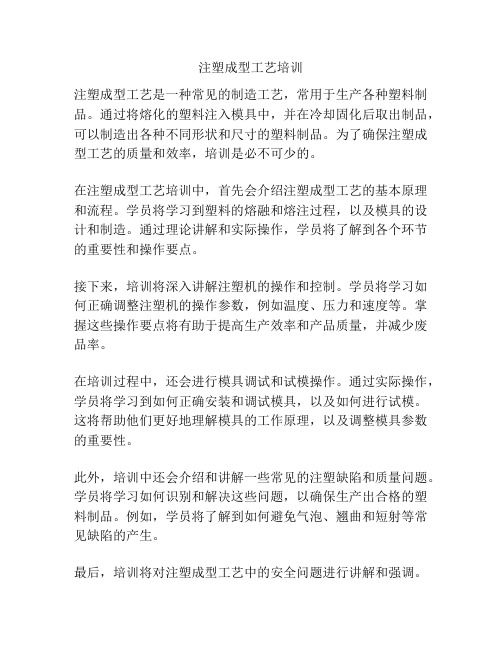
注塑成型工艺培训注塑成型工艺是一种常见的制造工艺,常用于生产各种塑料制品。
通过将熔化的塑料注入模具中,并在冷却固化后取出制品,可以制造出各种不同形状和尺寸的塑料制品。
为了确保注塑成型工艺的质量和效率,培训是必不可少的。
在注塑成型工艺培训中,首先会介绍注塑成型工艺的基本原理和流程。
学员将学习到塑料的熔融和熔注过程,以及模具的设计和制造。
通过理论讲解和实际操作,学员将了解到各个环节的重要性和操作要点。
接下来,培训将深入讲解注塑机的操作和控制。
学员将学习如何正确调整注塑机的操作参数,例如温度、压力和速度等。
掌握这些操作要点将有助于提高生产效率和产品质量,并减少废品率。
在培训过程中,还会进行模具调试和试模操作。
通过实际操作,学员将学习到如何正确安装和调试模具,以及如何进行试模。
这将帮助他们更好地理解模具的工作原理,以及调整模具参数的重要性。
此外,培训中还会介绍和讲解一些常见的注塑缺陷和质量问题。
学员将学习如何识别和解决这些问题,以确保生产出合格的塑料制品。
例如,学员将了解到如何避免气泡、翘曲和短射等常见缺陷的产生。
最后,培训将对注塑成型工艺中的安全问题进行讲解和强调。
学员将学习如何正确使用和维护注塑设备,以及如何预防事故和伤害的发生。
正确的操作和安全意识是注塑成型工艺中不可或缺的一部分。
通过注塑成型工艺的培训,学员将掌握基本的注塑技能和操作要点。
他们将能够独立操作注塑设备,并解决一些常见的问题和质量缺陷。
这将有助于提高生产效率和产品质量,为企业带来更高的竞争力。
在注塑成型工艺的培训过程中,学员还将学习到更高级的技术和知识。
例如,他们将了解到注塑成型中的材料选择和配方设计。
不同的塑料材料具有不同的特性和应用,学员需要了解每种材料的特点,以便正确选择和使用。
此外,学员还将学习到一些高级的注塑工艺技术,例如多组分注塑和热流道注塑。
多组分注塑可以将不同的材料注入同一个模具中,从而制造具有不同颜色或功能的制品。
热流道注塑可以提高注塑成型的效率,减少废品率,并增加产品的一致性。
注塑成型工艺知识培训

注塑成型工艺知识培训注塑成型工艺是一种常用的塑料加工方法,广泛应用于制造各种塑料制品。
为了提高员工的工作技能和质量意识,培训注塑成型工艺知识是非常重要的。
首先,培训应着重介绍注塑成型的基本原理和流程。
注塑成型是将塑料通过加热熔化,并通过高压注射进入模具的空腔中,然后冷却硬化成型的过程。
培训中应详细介绍每个环节的作用和关键点,包括塑料的熔化和注射、模具的设计和制造、注塑机的操作等。
其次,培训要重点讲解常见的注塑缺陷及其原因。
注塑过程中可能会出现短斑、气泡、翘曲等缺陷,这些缺陷严重影响产品的质量。
培训中应指导员工如何通过调整注塑工艺参数和模具结构,以及加强质量检查来避免这些缺陷的产生。
此外,培训还应介绍相关的质量管理知识。
注塑生产需要严格遵循质量管理体系,如ISO 9001标准等。
员工应了解质量规范和标准,学习如何正确操作和使用检测仪器,以确保产品的质量符合要求。
在培训中还可以引入一些案例分析和实际操作。
通过案例分析,员工可以学习分析问题的能力和解决问题的方法。
通过实际操作,员工可以熟悉注塑设备的使用和调整参数的技巧。
最后,培训还应包括注塑成型工艺的维护和安全知识。
员工需要学习如何正确保养和维修注塑设备,以确保设备的正常运行和延长使用寿命。
同时,员工还应了解注塑过程中的安全问题,如防护措施、操作规范等,以确保自身和他人的安全。
通过注塑成型工艺知识培训,可以提高员工的专业技能和质量意识,提高产品的质量和生产效率。
同时,注塑企业也应不断关注新技术和新工艺的发展,不断提升自身的竞争力。
继续进行注塑成型工艺知识培训,可以涉及以下相关内容:(1)材料选择和特性:注塑成型工艺的关键之一是材料的选择。
不同的塑料材料具有不同的特性和特点,因此在进行注塑成型前需要根据产品的要求选择合适的材料。
在培训中,可以介绍常见的塑料材料,包括聚丙烯(PP)、聚乙烯(PE)、聚氯乙烯(PVC)等,并讲解它们的特性、用途和加工注意事项。
注塑培训资料课件

合模装置工作原理
模具在合模装置的作用下 关闭,并承受注射压力和 模具锁紧力。
塑料材料基础
塑料分类
热塑性塑料和热固性塑料。
常用塑料
聚乙烯、聚丙烯、聚氯乙烯、聚酯等。
塑料性能
密度、熔点、流动性、收缩率等。
注塑工艺与参数
02
注射阶段
注射阶段
在注塑过程中,注射阶段是至关重要的环节,它涉及到塑料颗粒的熔 化和注入模具型腔的过程。
缩痕会影响产品外观和性能,其产生 原因可能包括塑料收缩率大、模具冷 却不均匀、注塑参数设置不当等。
翘曲问题
总结词
翘曲是指注塑件形状扭曲、不平 整的现象。
详细描述
翘曲会导致产品装配困难、外观质 量差等问题。翘曲产生的原因可能 包括塑料收缩率大、模具温度和注 塑参数设置不当等。
解决方案
优化模具设计,如增加加强筋、改 进冷却系统等;调整注塑参数,如 注射速度、注射压力和模具温度; 选用收缩率较小的塑料。
其他常见问题
总结词
其他常见问题包括气泡、喷射痕、熔接痕等。
详细描述
气泡是指在塑料内部或表面出现的气泡;喷射痕是指塑料在流动过程中,由于流动中断等 原因形成的条纹状痕迹;熔接痕是指塑料熔体在流动过程中,因汇合处未完全融合而形成 的线状痕迹。
解决方案
优化模具设计和注塑参数,改善塑料在模具内的流动和冷却;调整塑料干燥条件;选用合 适的塑料材料。
安全与环保
05
注塑安全操作规程
注塑机操作前安全检查
确保机器正常运转,检查安全门、防护罩等是否完好,确保无安 全隐患。
注塑机操作中注意事项
操作过程中,应保持注意力集中,避免分心或疲劳操作,同时遵循 安全操作规程,避免发生意外事故。
注塑安全教育培训资料(2篇)
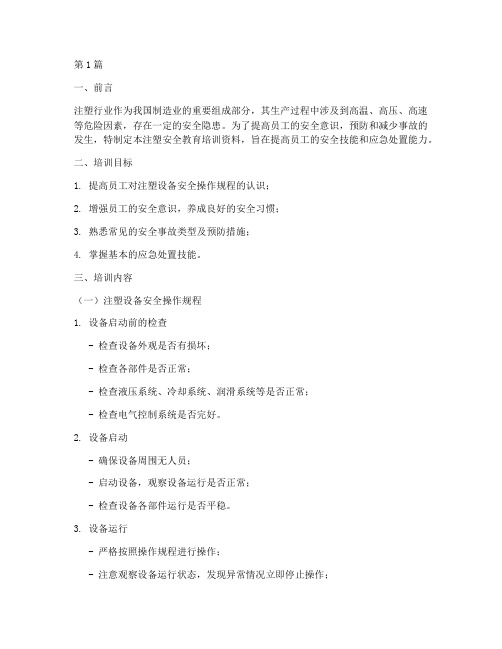
第1篇一、前言注塑行业作为我国制造业的重要组成部分,其生产过程中涉及到高温、高压、高速等危险因素,存在一定的安全隐患。
为了提高员工的安全意识,预防和减少事故的发生,特制定本注塑安全教育培训资料,旨在提高员工的安全技能和应急处置能力。
二、培训目标1. 提高员工对注塑设备安全操作规程的认识;2. 增强员工的安全意识,养成良好的安全习惯;3. 熟悉常见的安全事故类型及预防措施;4. 掌握基本的应急处置技能。
三、培训内容(一)注塑设备安全操作规程1. 设备启动前的检查- 检查设备外观是否有损坏;- 检查各部件是否正常;- 检查液压系统、冷却系统、润滑系统等是否正常;- 检查电气控制系统是否完好。
2. 设备启动- 确保设备周围无人员;- 启动设备,观察设备运行是否正常;- 检查设备各部件运行是否平稳。
3. 设备运行- 严格按照操作规程进行操作;- 注意观察设备运行状态,发现异常情况立即停止操作;- 避免在设备运行时进行维修或调整。
4. 设备停止- 停止设备运行;- 关闭电源;- 清理设备,保持设备清洁。
(二)常见安全事故类型及预防措施1. 机械伤害- 预防措施:穿戴防护手套、眼镜等个人防护用品;避免身体部位进入设备运行区域;设备运行时不得进行维修或调整。
2. 火灾- 预防措施:保持设备周围清洁,防止易燃物堆积;定期检查电气线路,防止短路;配备灭火器,并定期检查其有效性。
3. 烫伤- 预防措施:穿戴防护手套、眼镜等个人防护用品;保持设备周围清洁,防止烫伤事故发生。
4. 中毒- 预防措施:保持车间通风良好,防止有害气体积聚;定期检测有害气体浓度,确保在安全范围内。
(三)应急处置技能1. 火灾应急处置- 立即切断电源,防止火势蔓延;- 使用灭火器进行灭火;- 疏散人员,确保人员安全。
2. 烫伤应急处置- 立即用冷水冲洗烫伤部位;- 用干净的布料覆盖烫伤部位;- 立即就医。
3. 中毒应急处置- 立即将中毒人员移至通风良好处;- 采取必要的急救措施,如人工呼吸等;- 立即就医。
注塑工艺培训
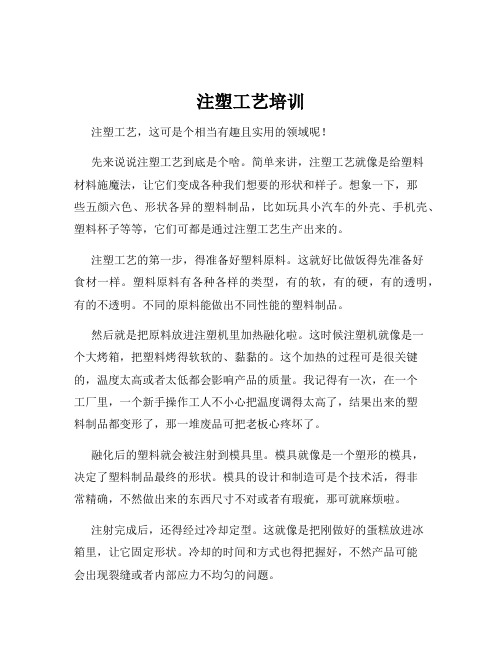
注塑工艺培训注塑工艺,这可是个相当有趣且实用的领域呢!先来说说注塑工艺到底是个啥。
简单来讲,注塑工艺就像是给塑料材料施魔法,让它们变成各种我们想要的形状和样子。
想象一下,那些五颜六色、形状各异的塑料制品,比如玩具小汽车的外壳、手机壳、塑料杯子等等,它们可都是通过注塑工艺生产出来的。
注塑工艺的第一步,得准备好塑料原料。
这就好比做饭得先准备好食材一样。
塑料原料有各种各样的类型,有的软,有的硬,有的透明,有的不透明。
不同的原料能做出不同性能的塑料制品。
然后就是把原料放进注塑机里加热融化啦。
这时候注塑机就像是一个大烤箱,把塑料烤得软软的、黏黏的。
这个加热的过程可是很关键的,温度太高或者太低都会影响产品的质量。
我记得有一次,在一个工厂里,一个新手操作工人不小心把温度调得太高了,结果出来的塑料制品都变形了,那一堆废品可把老板心疼坏了。
融化后的塑料就会被注射到模具里。
模具就像是一个塑形的模具,决定了塑料制品最终的形状。
模具的设计和制造可是个技术活,得非常精确,不然做出来的东西尺寸不对或者有瑕疵,那可就麻烦啦。
注射完成后,还得经过冷却定型。
这就像是把刚做好的蛋糕放进冰箱里,让它固定形状。
冷却的时间和方式也得把握好,不然产品可能会出现裂缝或者内部应力不均匀的问题。
注塑工艺还有很多细节需要注意。
比如说注塑机的压力控制,压力太大,可能会把模具压坏;压力太小,塑料又不能充分填充模具。
还有注射速度、保压时间等等,每一个环节都像是一场精密的舞蹈,需要各个动作配合得恰到好处。
在实际操作中,还得时刻关注产品的质量。
有时候,可能会出现一些表面瑕疵,比如气泡、流痕、缩痕等等。
这时候就得像医生看病一样,找出问题的根源,然后对症下药。
我曾经在一家注塑工厂里参观,看到工人们全神贯注地操作着机器,眼睛紧紧盯着产品,那种专注和认真的神情让我印象深刻。
他们就像是一群魔法师,用自己的技术和经验,把一堆塑料变成了一件件精美的制品。
总之,注塑工艺虽然看似复杂,但只要掌握了其中的窍门,就能像变魔术一样,制造出各种各样的塑料制品。
注塑培训资料
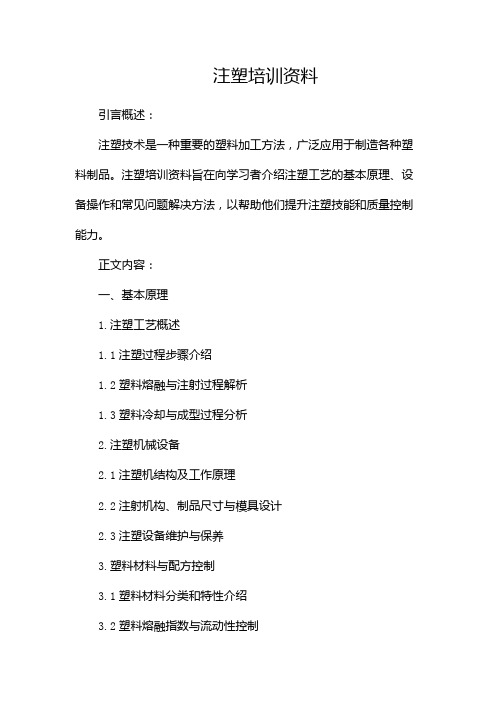
注塑培训资料引言概述:注塑技术是一种重要的塑料加工方法,广泛应用于制造各种塑料制品。
注塑培训资料旨在向学习者介绍注塑工艺的基本原理、设备操作和常见问题解决方法,以帮助他们提升注塑技能和质量控制能力。
正文内容:一、基本原理1.注塑工艺概述1.1注塑过程步骤介绍1.2塑料熔融与注射过程解析1.3塑料冷却与成型过程分析2.注塑机械设备2.1注塑机结构及工作原理2.2注射机构、制品尺寸与模具设计2.3注塑设备维护与保养3.塑料材料与配方控制3.1塑料材料分类和特性介绍3.2塑料熔融指数与流动性控制3.3配方设计及其对制品质量的影响二、设备操作1.注塑模具安装与调试1.1模具安装的步骤和注意事项1.2模具调试的原则和方法2.注塑机操作技巧2.1注塑机开机前的准备工作2.2注塑机操作面板及参数设置2.3操作中的常见问题及解决方法3.温度和压力控制3.1注塑过程中温度的控制与意义3.2注塑过程中流道压力的控制与优化3.3温度和压力异常的判断和处理三、质量控制1.注塑制品缺陷与分析1.1常见的注塑制品缺陷类型1.2缺陷产生的原因与分析方法1.3预防和解决制品缺陷的措施2.注塑制品检测与测试2.1检测设备与方法概述2.2注塑制品物理性能测试2.3检测结果分析及质量控制措施3.注塑工艺参数的优化3.1注塑工艺参数的选择和调整3.2工艺参数优化的试验方法与流程3.3注塑工艺参数优化的实例和经验总结四、安全与环保1.注塑操作的安全措施1.1注塑设备安全使用规范1.2塑料材料储存和处理的安全注意事项1.3紧急事故处理与应急措施2.注塑过程的环保问题2.1废水、废气、废渣的处理与回收利用2.2资源节约和能耗优化措施五、未来发展趋势1.自动化与智能化1.1注塑生产线自动化控制1.2智能注塑机的应用前景2.环保和可持续发展2.1生物降解塑料的应用前景2.2注塑技术对环境的影响与改进方向3.新材料和新工艺3.1高性能塑料的研发和应用3.2先进注塑工艺的研究与实践总结:注塑培训资料涵盖了注塑技术的基本原理、设备操作、质量控制、安全与环保以及未来发展趋势等重要内容。
注塑技术培训资料
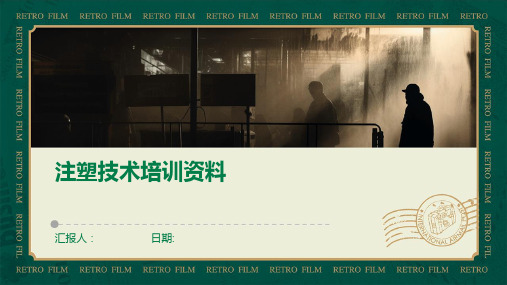
成型过程中的注意事项及维护保养方法
温度控制 压力调整 循环时间控制 维护保养
注塑过程中需严格控制模具和原材料的温度,以获得最佳的成 型效果。同时,定期检查加热元件、冷却系统等是否正常工作
。
根据产品需求和模具结构,合理调整注射压力、保压压力等参 数,以保证注塑件的质量和稳定性。
优化注射、保压、冷却等环节的时间,以提高生产效率。
操作步骤
根据生产计划,准备好原料、模具和 机器,调整注射成型参数,进行生产 。
注射压力、注射速度、保压时间等参数的设置与调整
01
02
03
注射压力
根据产品大小和模具情况 设定适当的注射压力,一 般不超过1500bar。
注射速度
根据产品厚度和模具结构 设定适当的注射速度,一 般不超过150mm/s。
保压时间
定期对注塑机、模具等设备进行保养,包括润滑、清洁、紧固 等措施,以延长设备的使用寿命。
成型后的产品检验及质量评估方法
外观检测
尺寸检测
观察注塑件是否有气孔、缩孔、流痕等缺 陷,以及尺寸是否符合要求。
使用测量工具对注塑件的尺寸进行精确测 量,包括长度、宽度、高度等参数。
性能测试
质量评估
根据产品需求,对注塑件进行相应的性能 测试,如耐温性、耐冲击性、耐磨损性等 。
具有较好的强度和耐冲击 性,适用于机械零件和家 电制品等领域。
塑料的收缩率及影响因素
塑料的收缩率
塑料制品的收缩率是指其尺寸在熔融状态下与冷却后的差异,不同的塑料品种和 加工条件下的收缩率会有所不同。
收缩率的影响因素
塑料的收缩率主要受到其结晶度、分子量、添加剂和加工条件等因素的影响。
选材原则及注意事项
由于冷却不均匀或其他因素,可 能导致成型件变形。解决方法是 优化冷却系统设计和成型条件,
注塑工艺员培训计划
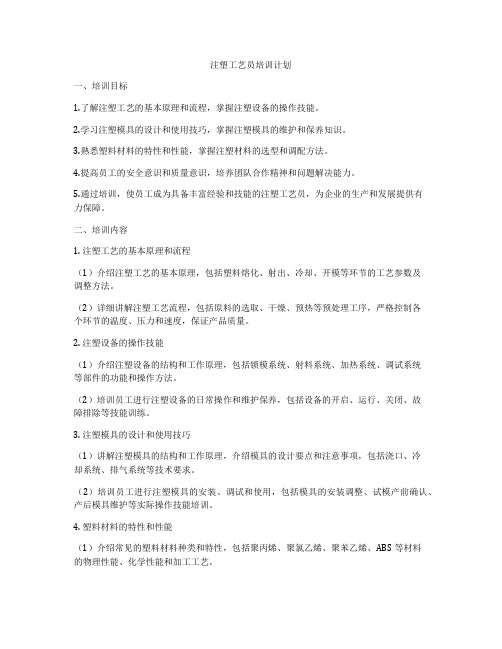
注塑工艺员培训计划一、培训目标1.了解注塑工艺的基本原理和流程,掌握注塑设备的操作技能。
2.学习注塑模具的设计和使用技巧,掌握注塑模具的维护和保养知识。
3.熟悉塑料材料的特性和性能,掌握注塑材料的选型和调配方法。
4.提高员工的安全意识和质量意识,培养团队合作精神和问题解决能力。
5.通过培训,使员工成为具备丰富经验和技能的注塑工艺员,为企业的生产和发展提供有力保障。
二、培训内容1. 注塑工艺的基本原理和流程(1)介绍注塑工艺的基本原理,包括塑料熔化、射出、冷却、开模等环节的工艺参数及调整方法。
(2)详细讲解注塑工艺流程,包括原料的选取、干燥、预热等预处理工序,严格控制各个环节的温度、压力和速度,保证产品质量。
2. 注塑设备的操作技能(1)介绍注塑设备的结构和工作原理,包括锁模系统、射料系统、加热系统、调试系统等部件的功能和操作方法。
(2)培训员工进行注塑设备的日常操作和维护保养,包括设备的开启、运行、关闭、故障排除等技能训练。
3. 注塑模具的设计和使用技巧(1)讲解注塑模具的结构和工作原理,介绍模具的设计要点和注意事项,包括浇口、冷却系统、排气系统等技术要求。
(2)培训员工进行注塑模具的安装、调试和使用,包括模具的安装调整、试模产前确认、产后模具维护等实际操作技能培训。
4. 塑料材料的特性和性能(1)介绍常见的塑料材料种类和特性,包括聚丙烯、聚氯乙烯、聚苯乙烯、ABS等材料的物理性能、化学性能和加工工艺。
(2)培训员工进行塑料材料的选型和调配,包括挑选适合的原料、根据产品要求进行原料的调配和混合等实际操作技能训练。
5. 安全和质量管理(1)讲解注塑生产中的安全风险和事故预防知识,包括设备操作安全、模具更换安全、原料使用安全等方面的培训。
(2)培训员工进行注塑产品的质量检测和控制,包括产品外观缺陷的判断和处理、产品尺寸精度的检测和控制等技能培训。
6. 团队合作和问题解决能力(1)组织团队合作的培训活动,包括团队协作、沟通协调、决策执行等方面的培训,培养员工的团队合作精神。
注塑成型工艺培训PPT课件
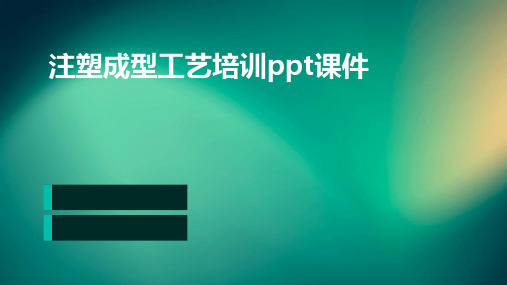
THANKS FOR WATCHING
感谢您的观看
确保原料干燥、无杂质。
加入料筒
将塑料加入料筒,并确保填充均匀。
塑料加热融化
加热料筒
使塑料在料筒内加热至熔点。
控制温度
保持温度稳定,避免过热或不足。
模具闭合与注射
模具闭合
确保模具紧密闭合,防止塑料溢出。
注射塑料
在高压下将融化的塑料注入模具型腔。
压力保持与冷却
压力保持
保持注射压力,使塑料充分填充型腔。
模具
用于形成塑料制品 的形状和尺寸。
注塑机的分类
立式注塑机
塑料原料从模具上方注 入,适合小型制品的生
产。
卧式注塑机
塑料原料从模具侧面注 入,适合大型制品的生
产。
全自动注塑机
配备机械手和自动化控 制系统,实现塑料制品
的连续生产。
多色注塑机
可以同时注入多种颜色 的塑料原料,适合生产
多色制品。
注塑机的维护与保养
在电子行业中,注塑成型工艺用于制造 各种塑料电子元件和部件,如连接器、 插头、插座等。
02 注塑成型设备
注塑机的结构
射嘴
连接射台和模具, 是塑料熔体的入口。
料筒
储存塑料原料,并 对其进行加热和熔 化。
射台
用于安装和固定模 具,并将塑料熔体 注入模具型腔。
螺杆
旋转时将塑料原料 推向射嘴,并将其 熔化。
制品表面出现银纹或光泽不良
总结词
制品表面出现银纹或光泽不良是由于塑料在熔融流动过程中发生降解或氧化,或者由于 模具温度过高所导致。
详细描述
制品表面出现银纹可能是由于塑料在高温下长时间受热发生降解,导致表面出现银色的 条纹;光泽不良可能是由于模具温度过高,导致塑料表面烧焦或产生其他颜色。
注塑成型技术培训---上下模
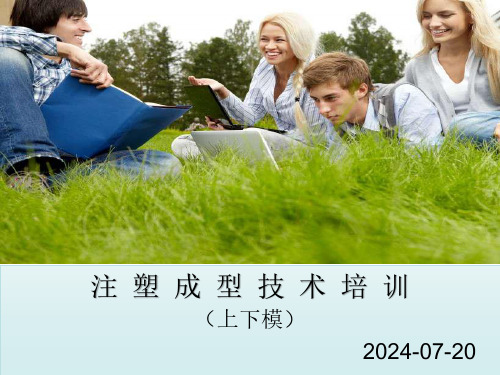
7.点动行车下行按键至挂钩能从吊环取出,吊环拧下慢速松 掉行车移走行车到指定的位置。
8.开模前先把锁模块拆除,固定于模具上并拧紧螺丝,防止 螺丝掉入水口箱内。(如图 6)
图4 图5 图6
上模步骤
8.根据模具要求装上辅助设备:如顶针保护开关,模温设备、 顶针强拉、中子抽芯、防撞微等,装好后,将模具合至1.5MM,关 机台马达,并告诉专业调机人员作是否正常。(如图 7)
9.先检查模具有无异常和要在开模前须按装的设备,如模具 内置抽芯和顶针强制复位结构,如确认没有,方可慢速开模。如 有由专业调机人员现场指导并开模。
注塑成型技术培训
(上下模) 2024-07-20
Catalog
01 上模准备事项ห้องสมุดไป่ตู้
02 上模步骤事项
03 下模步骤事项
04
过程安全事项
上模前准备
目的:规范上下模作业流程和技术要求,预防安全事故发生
准备:
1.确认该套模具的产品所使用的原料是否烘烤好 2.确认该套模具是否要保养(白色、颜色浅、防火料等) 3.确认该机台是否满足生产产品(机台吨位、机器性能等) 4.查找生产该套模具的相关工艺参数文件 5.准备上模所使用的工具(内六角、吊环、开口扳手等) 6.上模前必须穿戴安全用品:安全帽、安全鞋、手套 7.检查模具是否装有顶针保护开关及顶杆行程是否有效 8.上模前使用气枪吹模具运水是否畅通
10.移除相关工具,把机台周边“5S”做好。地面不有油水, 废弃物导致滑倒摔伤。
注塑培训资料

注塑培训资料注塑工艺是一种常见的塑料加工方法,广泛应用于电子、汽车、家具等行业。
而要想在注塑领域有所发展,必须掌握相关的知识和技能。
因此,接受专业的注塑培训就显得尤为重要。
以下是一份关于注塑培训资料的详细介绍,希望能够帮助您更好地了解这一领域。
一、培训内容1. 注塑基础知识在注塑培训中,学员将会学习注塑的基础知识,包括注塑工艺原理、机器构造、原料性能等方面的内容,为后续学习打下坚实基础。
2. 模具设计和制造模具是注塑加工的重要工具,学员将学习模具设计的基本原理与方法,以及模具材料的选择和制造工艺。
3. 操作技能培训通过注塑模拟机的实际操作,学员将掌握注塑机的开关机操作、模具更换、参数调整等技能,提高实际操作水平。
4. 质量管理与质量控制培训将涵盖注塑产品的质量管理体系、质量控制方法,帮助学员提高产品质量,降低次品率。
二、培训形式1. 理论讲授培训机构将安排专业讲师进行注塑相关理论知识的讲解,让学员全面了解注塑加工的基本原理。
2. 实践操作通过实际操作练习,学员将可以亲自操作注塑模拟机进行模具更换、参数调整等操作,提高技能水平。
3. 案例分析培训中将结合实际案例进行分析,帮助学员了解注塑过程中可能出现的问题及解决方法,提高学员的应变能力。
三、培训机构推荐1. 塑胜培训学院塑胜培训学院是一家专业的塑料加工培训机构,拥有经验丰富的讲师团队和先进的培训设备,致力于为学员提供优质的注塑培训服务。
2. 创新塑业教育创新塑业教育是一家专业的注塑培训机构,拥有一流的师资团队和培训设施,注重培养学员的实际操作能力和解决问题的能力。
四、培训结语通过本份注塑培训资料的介绍,相信您对注塑培训有了更深入的了解。
选择一家专业的培训机构进行注塑培训,不仅可以提高自身的技能水平,还能为个人的职业发展打下坚实基础。
希望您能够在未来的注塑领域取得更大的成就!。
注塑培训计划方案模板范文

一、培训目的为提高公司注塑生产线员工的技能水平,确保产品质量和生产效率,特制定本培训计划。
通过系统培训,使员工掌握注塑工艺流程、设备操作、故障排除及质量控制等方面的知识和技能。
二、培训对象公司注塑生产线全体员工,包括操作工、维修工、质检员等。
三、培训时间2023年1月至2023年12月,每月开展一次培训,共计12次。
四、培训内容1. 注塑工艺流程(1)注塑工艺的基本概念及原理(2)注塑模具的结构及分类(3)注塑机的结构及分类(4)注塑工艺参数的设定及调整2. 设备操作与维护(1)注塑机的操作步骤及注意事项(2)注塑模具的安装、调试及维护(3)设备故障的判断与排除3. 质量控制(1)产品质量标准及检验方法(2)常见质量问题的分析及解决措施(3)如何提高产品良率4. 安全生产(1)注塑生产过程中的安全隐患及预防措施(2)紧急事故的应对及处理方法五、培训方式1. 讲师授课:邀请公司内部有丰富经验的工程师和外部专家进行授课。
2. 案例分析:结合实际生产案例,分析问题、探讨解决方案。
3. 实操训练:现场操作设备,让员工亲身体验注塑工艺流程。
4. 考试考核:培训结束后,对员工进行理论知识与实践操作考核。
六、培训进度安排1. 第一阶段(1-3月):注塑工艺流程及设备操作培训2. 第二阶段(4-6月):质量控制及安全生产培训3. 第三阶段(7-9月):注塑模具维护及故障排除培训4. 第四阶段(10-12月):综合培训及考核七、培训评估与反馈1. 评估方式:培训结束后,对员工进行理论知识与实践操作考核,评估培训效果。
2. 反馈方式:收集员工对培训内容的意见和建议,及时调整培训方案。
八、培训保障措施1. 设备保障:确保培训过程中设备正常运行,满足实操训练需求。
2. 师资保障:邀请公司内部及外部专家进行授课,保证培训质量。
3. 考核保障:对培训效果进行评估,确保培训目标的实现。
九、培训经费预算根据培训内容、师资、场地等需求,预计培训经费为XX万元。
注塑生产工艺知识培训课程
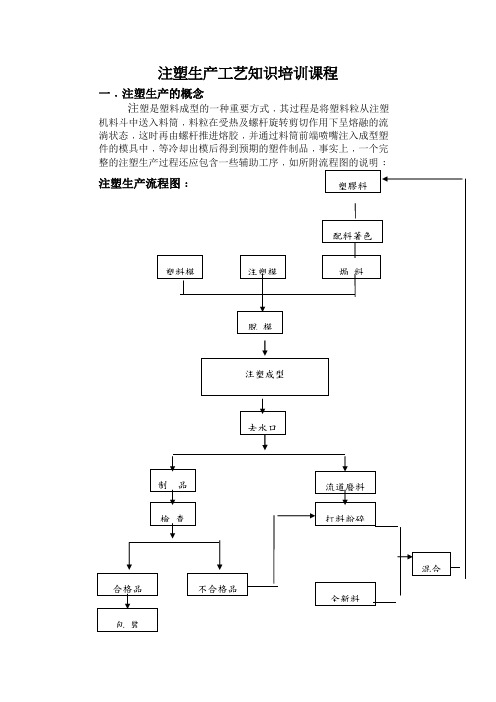
注塑生产工艺知识培训课程一﹒注塑生产的概念注塑是塑料成型的一种重要方式﹐其过程是将塑料粒从注塑机料斗中送入料筒﹐料粒在受热及螺杆旋转剪切作用下呈熔融的流淌状态﹐这时再由螺杆推进熔胶﹐并通过料筒前端喷嘴注入成型塑件的模具中﹐等冷却出模后得到预期的塑件制品﹐事实上﹐一个完整的注塑生产过程还应包含一些辅助工序﹐如所附流程图的说明注塑生产流程图﹕**注塑生产可使用半自动与全自动两种生产形式﹐而手动形式只是在调机时使用.二﹒注塑生产的条件﹕获得优良注塑的先决条件(1)﹒性能可靠的注塑机﹒(2)﹒满足使用要求的辅助设备﹒(干燥机﹒冻水机﹑混料机等)(3)﹒选择适用的塑料﹒(4)﹒优良的注塑模具﹒(5)﹒高素养的调机技术人员﹒1﹒注塑机目前我厂生产车间注塑机要紧为震雄机器厂有限公司生产的机器﹐下表列出有(1)注塑机基本结构注塑机包含﹕注射系统﹑锁模系统及注塑模具三大部分构成﹒各部分的作用列述如下﹕a)注射系统是注塑机最重要的部分﹐包含加料装置(料斗)﹑料筒﹑螺杆及喷嘴等部分﹐其作用是使塑料均匀地塑化﹐并在很快速度与较高压力下通过螺杆的剪切塑化推动射入模具﹒b)锁模系统在注塑机上实现锁合模具﹐开启模具与顶出制件的机构﹐现用注塑机为液压--双曲肘型﹒c)注塑模具(另述)2﹒生产辅助设备﹕(1)干燥器由于塑料高分子大都含有亲水基因﹐易吸水致成型产生银丝﹑气泡﹑水纹等缺陷﹒故基本上都需要干燥﹐根据材料的性质特点来选择相应的焗料条件(请参见附件(1)<<常用塑料材料干燥条件>>)(2)冻水机(WATER CHILLER)通过操纵冷却水温度(通常使用零上10℃左右)来操纵模具的工作温度﹐本厂现时用的型号为﹕20ST-05W(恒星工业冷水机)(3)碎料机将脱离的流道或者报废塑件打碎成为水口料以回用于生产﹐打料时注意不一致种类的料分开不能杂合﹐环境要保持干净﹐防受污染﹒(4)混料机将按配比秤量后的塑料原料﹐水口料(若需要加入)及色粉/色种通过机械搅拌﹐混合均匀﹐以使成型塑件着色﹐强度一致﹒附录(1)附录(2)*** 塑料差色时注意的几个问题﹕1﹒PE﹑PP﹑PVC﹑GPPS﹑PMMA﹑SAN﹑PC﹑PBT染不透明色时需加入钛白粉﹒2﹒PVC﹑GPPS﹑SAN﹑PMMA﹑PC染透明或者珠光色时不得加入钛白粉﹐锌钡白或者其它无机物﹒3﹒需注意多种色剂用于PE﹑PP﹑PVC时会发生不一致程度的迁移现象﹐选用时注意﹒4﹒由于ABS﹑SAN类中有A(丙烯月青)组份﹐而月青氨基(-CN)会引起着色不理想(色不稳固﹐不够鲜艳)﹐另一方面﹐A组份会使熔体粘度增大﹐摩擦剪切热较多﹐因此对色剂的耐热性要求较高﹒5﹒PMMA及PC因含有酯基而易水解﹐故混色后在成型前完全给予干燥﹒6﹒PA中含有极性很强的酉先胺基﹐吸水性强﹐故混色后在成型前亦务必完全进行烘焗﹒7﹒因PVC(特别是软PVC)中含有大量的增塑剂﹐热稳固剂等添加剂会使着色鲜艳性差﹐而且添加剂的析出易使色剂渗出发生迁移现象﹐另外﹐PVC在高温下分解出的氯化氢(HCL)也会使色剂颜色发生变化﹒三﹑啤塑(注射)成型原理概述(一)﹒成型过程的描述a.塑料原料粒通过注塑机(啤机)料斗进入料筒﹔b.料粒在料筒中受热力及螺杆剪切力的塑化作用熔化成流态﹔c.流态溶胶在注射机螺杆推动下以较高压力与较快速度通过一个狭小喷射嘴射入闭合的模具型腔内﹔d.经模具的散热冷却(过程中施以保压等操纵)﹐熔体凝固硬化﹔e开启模具﹐在顶处系统作用下﹐得到与模具型腔一致的胶件﹒总之﹕注射过程包含加料﹑塑化﹑注射﹑保压﹑冷却与脱模等步骤﹒(二)﹒成型前的准备工作1﹒对原料粒的干燥处理胶粒高分子含亲水基因﹐易吸湿而使胶件产生银纹﹑夹水纹﹑气泡等缺陷﹒通常说来结晶性塑料(PE﹑PP﹑POM等)较非结晶性塑料(PMMA﹑PC等)吸水性小﹒2﹑料筒的清洗﹕更换新的塑料需在注射成型前清洗残留在料筒内的旧料﹐以保证性能﹒料筒清洗剂﹕适用于温度在180℃〜280℃的各类热塑性塑料﹒3﹑脱模剂的选用为帮助顺利脱模﹐生产上可用雾化脱模剂操纵最佳使用量﹒(三)﹑注塑机操作程序1﹑利用注塑油缸液压活塞将螺杆向前推进﹐由螺杆端部将溶胶推出喷嘴﹐注塑入模﹒2﹑注塑模内充满塑料并在注塑压力下固化﹒3﹑螺杆旋转﹐在不断将料斗落下料粒曳入料筒的同时﹐螺杆后退让料筒中的料在外热及剪切摩擦热下进行塑化﹒最后将塑化好的溶胶定量地输送并﹒贮存到螺杆端部﹐等待下一轮注射﹒4﹑开模取出固化了的塑件﹐合模准备下一轮注射﹒以上1﹑2﹑3﹑4是连续﹑周期性进行的﹒(四)﹑注塑工艺注塑成型要紧工艺参数﹕温度﹑压力﹑时间﹒准确而稳固的注塑工艺是保证塑件质量的充要前提﹒调整工业条件时﹕按照压力──时间──温度顺序﹐不应同时变更两个或者两个以上参数﹒1﹑温度注塑成型工艺需操纵的温度有﹕1﹒料筒温度2﹒喷嘴温度3﹒模具温度其中料筒温度与喷嘴温度要紧影响塑化与流淌﹔模具温度﹒要紧影响流淌与冷却定型﹒a. 料筒温度通常自后至前逐步升高﹐以使均匀塑化﹒b﹒喷嘴温度通常略低于料筒最高温度﹐防止喷嘴发生“流涎”现象但亦不能太低,,以防早凝堵塞﹒c﹒模具温度模具温度的选择与塑料特性﹑制品结构﹑尺寸性能要求均有关系2﹑压力﹕注射成型过程中需操纵的压力有﹕a注射压力﹑b塑化压力(背压)﹒a﹒注射压力﹕注射压力是指螺杆顶部对熔胶施加的压力﹐其作用是克服熔胶自料筒流向型腔的流淌阻力﹐使熔体具有一定的充模速度并对熔体进行压实地﹒注射压力的大小与塑料品种﹑注塑机类型﹑制品结构及其它工艺参数有关﹒b﹒塑化压力(背压)﹕螺杆顶部熔胶在螺杆转动后退受到的压力﹐亦称背压﹒背压通过调节液压缸的溢流阀来调节﹐增大背压﹐能够提高熔体温度﹐使温度均匀﹐但会减小塑化速率﹐延长成型周期﹐可能导致塑料降解﹒通常宜取低背压(0.5Mpa不超过2Mpa)3﹑时间(成型周期)─充模时间注射时间──-保压时间──成型周期──闭模冷却时间────────总冷却时间其它时间(开模﹑脱模等)其中﹕a.注射时间与冷却时间是基本构成部分﹐注射时间与冷却时间的多少对塑件质量有决定性影响﹒b.充模时间通常不长﹐不超过10S﹒c.保压时间较长﹐与胶件壁厚有关﹐通常以塑件收缩最小取最佳保压时间﹒d.冷却时间要紧取决于制件的壁厚﹑模具温度﹑塑料热性能及结晶性能等﹒*注射速度的操纵﹕注射速度通过调节单位时间内向注射油缸供油多少来实现﹒A﹑低速注射﹕需较高注射压力(因熔胶粘度﹑流淌阻滞大的原因)a.优点﹕流速平稳﹐剪切速度小﹐塑件内应力低﹐尺寸较稳固﹐亦有助于避免缩水凹陷﹒b 缺点﹕充模时间延长﹐制件易分层与出现熔结痕(即夹水纹)﹐影响外观﹐亦使机械强度大大降低﹒B﹑高速注射﹕a.优点﹕快速充满型腔﹐料温与粘度下降很小﹐可使用低的注射压力能改善制件光泽度﹑平滑度﹐改善夹水纹﹑缩水等现象﹒b.缺点﹕“自由喷射”的涡流混入空气使制件有气纹﹐气泡(透明件明显)﹔排气不顺而“困气”烧焦﹑泛黄﹐脱模困难﹔速度紊乱易使透明件不透明﹐增加了内应力胶件易变形翘曲等﹒四. 注射成型常见问题及改善方法✧塑料或者着色剂热稳固性差﹒O 操纵料温﹑模温﹑保证稳固的结晶情况﹒✧结晶性塑料结晶度的差异﹒✧制件造型或者浇口形状的影响﹒✧五﹑塑料制件结构的认识(一)﹑制件结构方面在设计阶段应考虑的问题1﹑确定分型面──即以制件最大轮廓直径处设分型面﹐以分型面为界限设计脱模斜度﹒分型面形状越简单越好﹐除了考虑模具造价费用原因﹐复杂的分型面因加工精度影响易导致啤塑披锋等缺陷﹒2﹑凹割处理───从结构上改进应使模具制造简单﹐如尽可能使用碰穿位代替行位(滑块)﹐这样也提高了动作的可靠性﹒如图一所示﹐a)结构需侧抽芯(走行位)﹐b)改进后可使用整体式凸/凹模结构﹒3﹑制件的顶出──a﹒制件顶出系统通常设在动模内(即后模且大部分是凸模)﹐若预见制件粘前模﹐应采取措施改善﹐如增大前模出模斜度﹐加倒扣位强行令胶件留在后模等﹒b﹒顶针痕迹应设置在不影响胶件外观位置﹐如要求较高则需考虑其它顶出方式﹐如顶板顶出等﹒4﹑浇口开设的位置──要顾及制件形状﹐可能出现的熔接痕及批除水口对外观的影响﹒5﹑模具镶件──镶嵌界限线应可能设计成与塑件本体形成台阶﹐以减弱可能对外观的影响﹒6﹑出模斜度──a﹒为使制件顺利出模﹐内外壁应有足够脱模斜度﹐脱模斜度通常0.5∘~1.0∘.b﹒制品结构复杂﹐脱模斜度就取大些﹒c﹒斜度取法﹕通常内孔以小端为基准﹐斜度由扩大方向取得﹔而外形以大端为基准﹐斜度由缩小方向取得(如图二所示)﹒d﹒由于顶出系统设在后模﹐故应使胶件留在后模即要求制品内表面脱模斜度小于外表面脱模斜度﹐即图二中α>β﹒e﹒当侧面(壁)不同意有脱模斜度的精密制件模具需使用侧面走滑块形式﹐将无斜度的面做在滑块上﹒7﹑壁厚──模型的冷却时间是由最大壁厚决定的﹐壁太厚会浪费料﹐增加成本及延长啤塑时间﹐另外也增加了产生缩凹的倾向﹔壁太薄﹐啤塑易走料不到﹐及强度刚度不够﹔壁厚薄不一﹐因固化冷却速度不一致导致收缩不均匀﹐并造成内应力而导致胶件变形翘曲等等﹒8﹑圆角连接──将内角做圆角连接﹐避免应力集中及提高强度﹐并能改善熔料的流淌性﹒9﹑消除尖角利边──针对玩具制品的安全标准要求﹐在设计阶段应改善避免胶件存在有可接触之尖角﹑利边等﹒(二)﹑针对不一致侧重要求的结构形式A﹑注重外观的结构设计从结构设计上应重点考虑避免缩水痕﹐其它如模具结构对制件外观的影响如分型线﹑镶拼线﹑浇口(冷料穴﹑垃圾位等)的痕迹﹒*改善缩水痕的结构设计1﹒统一壁厚﹕通过设计工艺孔等手段减薄特别厚的部位使壁厚均匀﹐壁厚变化不宜超过20%﹐(参见﹕图三﹑图四)﹒2﹒把大的加强筋变成几条小加强筋(见图五)﹒3﹒把厚壁改为加强筋支持的薄壁﹐加强筋处于受力方向位置(如图六)4﹒制品表面越光亮缩水痕越明显﹐哑光面有掩饰缩水痕作用B﹑在结构上保证制件尺寸精度影响塑料制品尺寸的要紧因素﹕a)模具制造误差(占50%)b)成型条件变化(占30%)c)材料批量间及批量内误差(占20%)1﹒塑件上某些高精度尺寸不能靠模具成型达到﹐如与金属轴配合的轴孔尺寸﹐应当用金属轴套以嵌件形式嵌入胶件﹒(需注意设计上消除嵌件位应力的开裂)﹒2﹒根据模具结构﹐制件的尺寸分为两类﹕a)由模具零件直接决定的尺寸﹒此类尺寸都在型芯或者型腔的单方面﹐精度只受模具零件加工精度的影响﹒b)由两个以上模具零件相对位置决定的尺寸﹒此类尺寸较难操纵﹐如过分型面尺寸受飞边(披锋)影响﹐圆筒形胶件壁厚受型芯与型腔同轴度的影响(偏心)等﹒C﹑在结构上确保制件强度(一). 确保制件强度的原则﹕1﹒勿使制件壁太薄﹒2﹒去除尖角﹒(二). 增加制件强度的措施﹕1﹒设加强筋﹕加强筋能有效地达到增加制品的刚度与强度的目的﹐比单纯增加壁厚能有效利用材料﹑缩短啤塑成型周期﹐更具有经济性(参考图七)﹒另外﹐大平面增设加强筋还有防止翘曲变形的作用﹒设置加强筋应注意﹕a)加强筋高度不要超过壁厚的3倍﹔b)加强筋底部的宽度不能超过壁厚的2/3﹔c)加强筋上设计2∘〜5∘的出模斜度;d)两条筋间的距离不得小于两倍壁厚﹒2﹒圆角连接﹕尖角处易开裂﹐原因是熔料在尖角处的流态急剧变化产生大的应力残留﹐除了镶拼型芯与分型面等模具结构的原因之外﹐结构上均应考虑使用圆角﹑圆弧过渡避免应力集中﹐提高强度﹒圆角大小的确定﹕设壁厚为T﹐圆角半径为R﹐则R/T≧0.253﹒自攻螺丝孔柱的强度﹕如(图八)所示﹐在不引起缩水的前提下﹐尽可能加粗凸台(司筒成型壁厚)以增加强度﹒D﹑简化结构便于模具制造1.制件使用镶拼的部分不要设计成圆角(如图九)所示﹒2.制件外表面镶拼部分与型腔不要成一个平面﹐应设有一台阶掩饰镶拼痕线(如图十所示).3.成型孔太细长难以成型﹐因细针型芯易受注射压力或者折断﹒应改进为细针根部加圆角并将下半段放粗(对螺丝孔有导向作用),(如图十一所示)﹒另外﹐孔径与深度也有一定关系﹐对注射成型参考数据﹕通孔﹕h≦10d不通孔﹕h≦4〜5d否则成型针易弯变形或者折断﹒4.制品上的凹槽不要设计成薄刃﹑薄壁形状﹐刀口状型芯难加工﹐且易损坏﹒5.制品上的凸字﹐模具上容易雕刻﹐反之则很困难﹒E﹑防止变形的制件结构材料力学证明﹕某些形状抵抗因外部载荷或者残余加工应力而产生的变形的能力优于其它形状﹒1.盒﹑盒类制品上口易变形﹐须设边框增强﹐(如图十二所示)﹒2.箱体类制品底部的变形﹐用凹凸变形或者加框方法加强﹐(如图十三所示)﹒3.不对称的制件因收缩不均匀﹐容易变形﹐在结构上考虑改为接近对称形状﹒如图十四所示)﹒4.变形的要紧原因是收缩不均匀与应力作用所致﹐应尽可能简化设计﹐使形状简单﹐壁厚均匀﹒F﹑防止开裂的结构改进1.制件的应力往往集中在尖角或者缺口部位﹒防止开裂的首要条件就是保持制件外形的连续性﹐将尖角改为圆角﹐缺口改为圆弧过渡﹒(如图十五所示)﹒2.孔与孔之间的距离太近或者孔距离制件边缘太近会减弱强度﹐易出现开裂﹐故应有一定要求(如图十六所示)3.孔口是应力集中区﹐最易开裂﹐故应加框筋加强﹒(如图十七﹑十八所示)﹒4.需喷油制件﹐由于涂料开油水的作用容易应力开裂﹐需注意相应位置用圆角连接(如图十九所示)﹒G﹑结构的改进以减少成型故障1﹒浇口设在制品厚壁部位容易成型﹐当料流同厚壁部向薄壁处流淌时﹐注射压力损耗小﹐并有利于保压﹒(如图二十所示)2﹒透明制件的侧壁务必有足够的脱模斜度﹐以免侧壁拖花﹒3﹒模拟熔料流淌状态﹐推断融合线位置﹐以确保浇口正确的开设位置(如图二十一所示)﹐杯类制件的浇口应开设在杯底部﹒4﹒简化制品形状﹐定模中尽量不要有高度大或者细长的型芯﹒5﹒有尖角的制件脱模困难﹐脱模时易刮伤胶件﹐应改善结构消除尖角(如图二十二所示)﹒6﹒制件外侧的孔﹑凹槽﹑文字标记等对制件来说都形成凹割﹐需用横抽芯的模具成型(即需走侧行位)﹐抽芯模具结构比较复杂﹐而且成型稳固性差﹐易发生故障﹐故从结构上考虑改进﹕如上下型芯斜面贴紧(碰穿)形成孔或者将圆孔改成U型孔以简化模具结构﹐(如图二十三所示)﹒另外﹐制件里面的凸筋同样形成凹割﹐需在内侧抽芯(走内行位)﹐模具结构更复杂﹐(如图二十四所示)将相应底面改为通孔形式﹐利用碰穿成型﹐可避免走内行位﹒H﹑考虑到二次加工的结构改进1﹒喷油﹑印刷制件结构a﹒尽可能取大的脱模斜度﹐提高模腔的光洁度﹐脱模剂类物质会造成喷油不上油或者易甩油﹒b﹒喷漆面上的不能有飞边﹑熔接线﹐且制件结构应设计成能分散内应力形状﹐如使用圆角过渡,水口开设位置应尽可能减小水纹影响﹐应力集中的位置喷油后在开油水作用下易发生开裂.2﹒粘结制件的结构a﹒与喷油件设计条件相同﹐脱模斜度要大﹒b﹒粘合面的缩凹﹐会影响粘结效果﹐须保证粘结面平整﹒溶剂脱水粘结时﹐部分溶剂残留于缩凹部位会使塑件表面出现裂纹﹒c﹒粘结件装配须设计有空隙﹐以保证紧贴与储存胶水(如图二十五所示)﹒3﹒烫印(烫金)制件的结构a﹒烫印面背面不能有引起缩凹的加强筋﹐凸台等厚壁不均匀形状﹐烫印面应平整﹐不能翘曲﹐否则凹处烫金不到(漏印)﹒b﹒在熔接线烫印﹐花纹容易剥落﹐结构上应考虑把融合线移到别处﹒c﹒与喷油件要求条件相同﹒d﹒烫印面的背面要有利支持﹐烫印压力不足﹐图案易剥落﹒4﹒电镀制件结构a﹒同喷油制件设计要求b﹒塑件上不应有熔结线﹒C﹒电镀面上不应有分型线与型芯镶嵌线﹒d﹒避免盲孔﹐残留在盲孔内的镀涂不易清洗干净﹒e﹒凹槽深度不宜超过槽宽的1/3﹐凹槽越深越难电镀(所需电压高)且镀层质量差﹒f﹒镀件壁不能太薄(应≧1.5)﹐否则电镀中因刚性差易变形﹐镀层结合力也差﹒g﹒电镀工艺有锐角变厚的现象﹐电镀中锐角边引起尖端放电﹐造成边角镀层隆起﹐圆角半径至少在R0.3mm以上﹒(如图二十六所示)﹒h﹒平板形塑件难电镀﹐镀件中心部分镀层薄﹐越靠近边缘镀层越厚﹐整个镀层不均匀﹒应将平面改成略带圆弧面或者将平面制成哑光面﹐以改善镀层光泽的均匀性﹒5﹒安装铭牌的制件结构a﹒需用粘结剂粘结铭牌﹐塑件结构上应设有粘结剂干燥孔(如图二十七所示)﹒b﹒为使铭牌与塑件面接触紧贴﹐在塑件粘结面应留有凹槽(如图二十八所示)﹒6﹒热烫焊有关的制件结构a﹒热烫焊焊脚位应加圆角R以保证强度﹐焊脚高度不够﹐堆焊少﹐会影响强度﹒被烫焊件厚度至少1.0mm﹐焊脚长度=被烫件厚度+1.5 ~ 2.5mm.(如图二十九所示)b﹒烫焊要求烫焊中及烫焊后不移动﹐可参考(图三十所示)结构形式定位﹒六﹑啤塑生产模具常见问题及处理方法(一)﹑模具啤塑过程中粘模☆粘模的要紧原因如下﹕1﹑出模斜度不够──视情况尽可能加大脱模斜度﹐并应保证型腔﹑型芯足够的光洁度﹒2﹑模温太高──调整模温﹒☆强制塑件粘动模(后模)由于通常模具的顶出机构都设在动模(后模)内﹐由于定模(前模)型腔复杂等原因出现塑件粘前模的情况﹒解决方法﹕在后模型芯位开凹槽倒扣位﹐需不影响外观﹐强制塑件粘在后模上﹒☆型腔砂磨抛光方向与塑件出模方向一致﹒残留粗的砂痕影响出模与制件外观质量﹒☆分型面向内翻口﹐塑件粘模或者出模拖花改善﹕修平﹐省光滑﹐但注意不能回口﹒☆高度大的制件粘模﹒由于高度大的制件会牢牢的吸附在型芯上﹒形成负压﹐造成出模困难且易损坏﹒需改善顶出机构﹐如利用压缩空气吹出﹐或者在型芯顶杆增加排气位置﹒(二)﹑模具变形☆模具变形要紧原因﹕1﹑模具整体刚性差﹒2﹑注射压力太大﹒☆新模试模发生涨模﹐经常是由于一开始就使用高压注塑所致﹐需特别注意试模时注射压力取低在根据情况逐步调高﹒☆涨模模具的修理: 型芯与型腔配合严密但刚性不足的模具,用模具外周加框加固修理.☆连续生产中发生涨模: 要紧是由于型芯温度升高,同型腔温差越来越大,热膨胀将模具卡死冷却模具后即可开启模具.☆杯形制件模具变形: 要紧由于模具定位不可靠,杯形制件型芯高度大,在料流不平衡冲击下(高压达50mPa),易变形或者偏位.☆改善: 高度大的模具应使用台阶或者锥面配合的二次定位机构,而不能用导柱等导向零件代替定位零件.(三)﹑模具生锈☆模具生锈要紧原因1﹑模腔表面粘附腐蚀性物质2﹑模腔表面霜雾☆防止模具生锈的措施1﹑生产中的模具防锈塑料制件啤塑生产中﹐型腔表面会形成一层分解生成物﹐特别是PVC﹑赛钢(POM)等塑料﹐这些分解生成物会磨耗腐蚀模具而致生锈﹒故需定期定班地清洁擦拭干凈模具(可用酒精).2﹑停产后的模具保护清洁模具﹐喷防锈剂﹔长期不用的模具需在模腔及主流道孔涂黄油以防生锈﹒3﹑防止出现模腔结霜停机时应首先闭运水管﹐擦凈模具表面﹐防止冷凝生成霜雾﹒(四)﹑模具咬粘☆滑动部位零件咬粘的原因﹕滑动部位零件受到过大的力﹐发生变形或者移位☆滑动零件咬粘的防止﹕设计刚性好的滑动零件﹐可靠的定位结构与对滑动零件用淬硬等﹒高度大的模具要用镀面定位的模具结构﹐定位部分与导向部分的角度一致易发生卡死﹐定位部分角度应比导向部分大一些(参见图一)﹒(五)﹑模具顶出机构故障☆细顶杆弯曲/折断细顶杆应设计成下半段直径放粗的台阶形以增加强度﹐特别形状的成型顶针﹐如矩形截面针易断﹐应多备几支﹒☆复位机构干扰横抽芯的模具﹐在其复位之前﹐顶杆务必先复位﹐否则闭模时滑块与顶杆碰撞(干扰)损坏模具﹒应使用可靠安全装置﹒☆制品粘在顶杆上﹐不能自动落下﹐需使用半自动啤﹐手工取出胶件﹒☆成型顶针(包含司筒顶针)成型胶件结构的部分往往有方向性﹐需留意定位问题﹐以免成型后影响外观及出现装配问题﹒(六)﹑模腔踫花☆型腔踫花的常见原因之一﹕是由于全自动成型中塑件留在型腔内闭模﹐故在模具方面应保证塑件的可靠脱模﹒☆防止型腔踫花﹕模具成型零件应热处理淬硬或者镀硬铬﹒(七)﹑模具损坏☆模具开裂模具刚性差﹐超过疲劳极限时﹐发生开裂﹒箱体类制件角部最易发生开裂﹒修复用烧焊或者镶嵌的方法﹒☆型芯(针)折断塑件孔成型针过长﹐受到不平衡的成型压力或者脱模力﹐冲击会弯曲或者是从根部折断﹒成型针根部设计圆角可避免应力集中﹐不易折断﹐其材料宜用弹簧钢﹐并应预有备件﹒☆型腔损坏轻微的损坏(伤痕)可用踏平的方法修理, 严重的损坏或者把损坏的部分钻去或者割去,把损坏的部分做成镶件嵌入修得, 但制品表面会留有镶拼线痕. (参见图二)☆分型面的修理分型面往往因粘有飞边或者垃圾而压出凹痕(塌陷), 修理的方法用踏平或者焊补后修整.而用磨削分型面虽能修理凹痕, 但型腔高度变化影响尺寸;关于结构复杂的模具,如存在碰穿位置的, 此种修理方法更需特别留意, 做同时执修.(八)膜具焊补的问题☆焊补后模具开裂要紧原因是焊补时热应力造成, 应先将模具充分预热, 焊补后缓慢冷却.☆补焊区变硬, 制品表面局部光泽差原因: 补焊材料与模具材质不一致, 导致热传导差异, 此种情况有的时候镶拼件修复也会出现.﹒☆关于烧焊后的针孔, 假焊, 清晰的焊接轮廓线应重视补焊前后的热处理.(九)冷却水循环通道中的问题☆冷却水接头处渗水要紧原因是接头密封圈未装到位, 或者长期工作老化出现裂痕.☆冷却水从模腔或者模板渗出1.加工失误, 致使冷却水通道与其它孔击穿.2.模具加工过程中, 改变设计的补充加工,造成水孔壁击穿.3.设计冷却水道时要考虑四周留有充分壁厚.4.模具‘O ’型密封圈未装正或者选用规格太小有间隙☆冷却水渗漏的修补接头渗漏查修较易, 其它渗漏需用焊补修复. 假如无法修复, 只能重新设计冷却水道.模具一旦发生微细裂纹, 冷却水管内的水沿裂纹流到模腔表面, 影响生产, 这种渗漏是很难修理的.(十)流道中的问题主流道粘模原因:1.主流道斜度不够( 通常应2°~ 4°) ;2.主流道内划花, 主流道应设计成可更换的浇口套形式, 选用优质钢单独加工与热处理淬硬再行研磨.;3.喷嘴温度过低;4.主流道与分流道连接圆角太小, 主流道从分流道连接处脱落;5.喷嘴与模具浇口套之间溢料使主流道在浇口套内. 浇口套凹球面半径应大于喷嘴凸球面半径, 主流道直径应大于喷嘴直径,这样喷嘴同浇口套才能紧密贴合.塑料螺丝孔经d为塑料螺丝公称直径D的0.85系数(用塑料疏牙螺丝)。
注塑工艺人员培训计划

注塑工艺人员培训计划一、培训目的注塑工艺作为一种重要的塑料加工工艺,在现代工业生产中发挥着不可替代的作用。
而合格的注塑工艺人员是保证注塑生产工艺稳定、产品质量可控的基础。
因此,开展注塑工艺人员的培训工作,对于提高注塑工艺人员的专业技能和工作水平,提高企业的生产效率和产品质量,具有非常重要的意义。
二、培训对象本次培训对象为公司现有注塑工艺人员,包括注塑工艺师、注塑操作工、注塑调试工等。
三、培训内容1. 塑料材料的特性和分类1.1 塑料材料的种类和特点1.2 塑料材料的加工性能和应用1.3 塑料材料的成型温度和压力控制2. 注塑工艺的基础知识2.1 注塑成型原理2.2 注塑模具结构和腔型设计2.3 注塑机的结构和工作原理2.4 注塑工艺参数的设定和调整3. 注塑生产过程中的常见问题及解决方法3.1 成型缺陷分析与改善3.2 注塑机故障排除与维护3.3 注塑模具使用和保养4. 注塑生产安全和质量管理4.1 注塑生产现场的安全规范和操作流程4.2 产品质量控制和质量管理标准5. 其他相关知识5.1 注塑模具设计原理5.2 注塑设备的选型和购置原则5.3 注塑工艺的节能减排技术四、培训形式本次培训采取理论学习和实际操作相结合的形式进行。
具体包括专业讲座、现场操作演示、案例分析等教学方式。
五、培训计划培训时间:共计3个月1. 第一阶段(1个月)1.1 了解塑料材料的特性和分类1.2 学习注塑工艺的基础知识1.3 熟悉注塑生产过程中的常见问题及解决方法2. 第二阶段(1个月)2.1 学习注塑生产安全和质量管理知识2.2 掌握注塑模具设计原理2.3 开展实际操作演示和案例分析3. 第三阶段(1个月)3.1 进行现场操作实习3.2 进行模具使用和保养维护实训3.3 进行产品质量控制实战演练备注:培训结束后进行总结和答疑,对培训效果进行评估和反馈。
六、培训师资培训师资来源于公司内部的注塑工艺技术人员和外部的注塑专业技术人员。
注塑成型工艺培训资料

注塑成型工艺培训资料汇报人:日期:•注塑成型工艺概述•注塑机结构与工作原理•模具设计与制造技术目录•塑料原材料选择与性能特点•注塑成型工艺参数设置与调整方法•注塑产品质量控制与缺陷分析方法01注塑成型工艺概述是一种塑料加工方法,将熔融状态的塑料注入模具中,冷却后获得所需形状的制品。
注塑成型用于执行注塑成型的设备,通常由注射装置、合模装置、液压系统、电气控制系统等组成。
注塑机将塑料颗粒加热至熔融状态,形成流体。
通过注塑机的注射装置,将熔融状态的塑料注入模具的型腔中,并充满整个型腔。
塑料在模具中冷却,由流体状态转变为固态。
开模后,制品从模具中脱出,完成整个注塑过程。
塑料熔融注射与充填冷却与固化脱模与取出注塑成型工艺应用领域家电制造日用品行业家电零部件如洗衣机桶、冰箱门等。
日常用品如餐具、玩具、文具等。
汽车制造电子行业其他行业汽车零部件如仪表盘、门板、座椅等。
电子元件、连接器、外壳等。
医疗器械、建筑、包装等。
02注塑机结构与工作原理包括注射螺杆、料筒、喷嘴等部件,用于将塑料熔体注入模具型腔。
注射装置包括动模板、定模板、拉杆、合模油缸等部件,用于将模具闭合,实现制品成型。
合模装置包括液压泵、油缸、液压阀等部件,用于控制注塑机的动作和实现模具的开关模。
液压系统包括电脑控制板、操作面板、温度控制仪表等部件,用于控制注塑机的各个动作和工艺参数。
电气控制系统注塑机结构组成注塑机工作原理塑料熔体注入模具型腔注射螺杆在液压系统的作用下,将塑料熔体从料筒中推出,通过喷嘴注入模具型腔。
模具闭合合模装置中的动模板在液压系统的作用下,向定模板靠近,将模具闭合。
保压与冷却模具闭合后,注射螺杆继续向前推进,保持一定的压力,使塑料熔体充满整个型腔。
同时,模具进行冷却,使塑料熔体固化成型。
开模与顶出冷却完成后,液压系统控制模具打开,制品被顶出。
操作人员需经过专业培训,熟悉注塑机的结构、工作原理和操作规程。
严格遵守操作规程安全操作工艺参数调整设备维护与保养操作人员需佩戴防护用品,避免接触高温和高压的部位。
注塑工艺培训计划
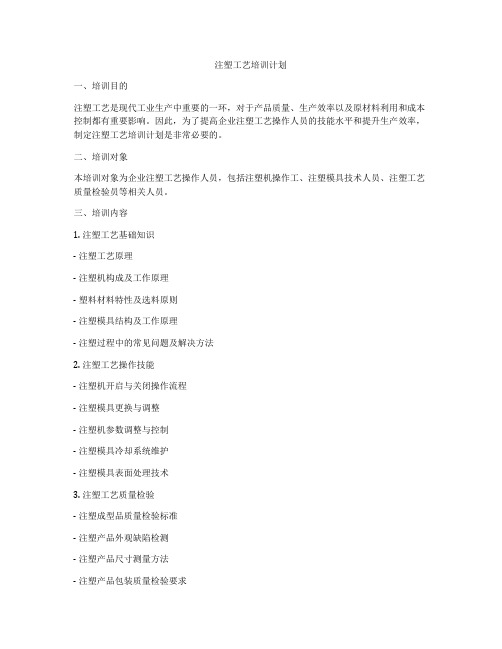
注塑工艺培训计划一、培训目的注塑工艺是现代工业生产中重要的一环,对于产品质量、生产效率以及原材料利用和成本控制都有重要影响。
因此,为了提高企业注塑工艺操作人员的技能水平和提升生产效率,制定注塑工艺培训计划是非常必要的。
二、培训对象本培训对象为企业注塑工艺操作人员,包括注塑机操作工、注塑模具技术人员、注塑工艺质量检验员等相关人员。
三、培训内容1. 注塑工艺基础知识- 注塑工艺原理- 注塑机构成及工作原理- 塑料材料特性及选料原则- 注塑模具结构及工作原理- 注塑过程中的常见问题及解决方法2. 注塑工艺操作技能- 注塑机开启与关闭操作流程- 注塑模具更换与调整- 注塑机参数调整与控制- 注塑模具冷却系统维护- 注塑模具表面处理技术3. 注塑工艺质量检验- 注塑成型品质量检验标准- 注塑产品外观缺陷检测- 注塑产品尺寸测量方法- 注塑产品包装质量检验要求4. 注塑工艺安全生产- 注塑机安全操作规程- 注塑模具使用安全要求- 塑料材料危害防护措施- 废品及废料处理及回收利用5. 注塑工艺改进和优化- 注塑工艺流程分析及改进方法- 注塑模具结构改进方案- 注塑机参数优化调整- 注塑成型周期缩短技术四、培训方式1. 理论授课通过讲解PPT课件、视频资料等方式进行注塑工艺基础知识及操作技能的理论学习。
2. 实操训练安排岗位训练,实际操作注塑机及模具,指导操作员熟练掌握操作技能。
3. 质量检验组织举行注塑产品外观缺陷检测、尺寸测量及包装质量检验的实际操作培训。
4. 安全生产培训通过安全生产教育课程、事故案例分析等方式进行安全生产知识培训。
五、培训方法1. 理论结合实践通过讲解理论知识的同时,引导学员进行实际操作,边学习边实践,加深印象,提高学员的学习兴趣和学习效果。
2. 班组学习根据操作工、模具技术人员等不同岗位,分别进行班组学习,加强针对性培训。
3. 组织考核设立理论学习考试、技能操作考核、质量检验考核等多种形式的考核方式,对学员进行全面的考核评估。
注塑成型工艺培训资料
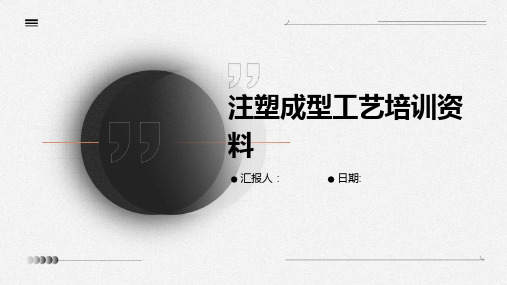
02
注塑成型前的准备
塑料材料的选取与检验
总结词
塑料材料的选取与检验是注塑成型工艺的第一步,对于最终制品的质量、成本 和生产效率具有重要影响。
详细描述
在选取塑料材料时,需要考虑制品的使用场合、受力情况、外观要求以及成本 等因素。同时,需要对塑料材料进行检验,确保其符合相关标准和要求,例如 密度、收缩率、流动性等。
构进行合理设定。
冷却时间
冷却时间对于确保注塑件充分冷却 和减少残余应力至关重要,应根据 产品要求和模具结构进行合理设定 。
周期时间
周期时间是整个注塑成型过程的时 间,需综合考虑注射时间、冷却时 间、取出产品等因素。
04
注塑成型后的处理及检验
塑料件的取出与处理
塑料件的取出
在注塑机完成注塑成型后,应立即将 塑料件从模具中取出,以避免塑料件 在高温下变形或产生水口。
注塑机的选取与调试
总结词
注塑机的选取与调试是注塑成型工艺的 关键环节,对于制品的质量和生产效率 具有重要影响。
VS
详细描述
在选取注塑机时,需要考虑制品的形状、 尺寸、材料特性以及生产效率等因素。同 时,需要对注塑机进行调试,确保其工作 状态良好,例如注射压力、注射速度、模 具温度等参数的调整。此外,还需要对制 品的尺寸和外观进行检测,确保其符合相 关标准和要求。
废弃物回收和处理
对于注塑制品的废弃物,应采取有效的回收和处理措施,以减少对环境的污染。同时,应积极推广可循环利用的 塑料材料,实现资源的有效利用。
感谢观看
THANKS
05
02
加料
将塑料原料加入注塑机中,经过加热熔融后 形成熔体。
04
保压
在注射后,对模具进行保压,以防止 制品产生收缩和变形。
- 1、下载文档前请自行甄别文档内容的完整性,平台不提供额外的编辑、内容补充、找答案等附加服务。
- 2、"仅部分预览"的文档,不可在线预览部分如存在完整性等问题,可反馈申请退款(可完整预览的文档不适用该条件!)。
- 3、如文档侵犯您的权益,请联系客服反馈,我们会尽快为您处理(人工客服工作时间:9:00-18:30)。
3.4:注塑成型缺陷分析、实例分析
料花、顶白、混色
1 料花 2 3 混色
实例分析之料花:产品图观察导致料花原因有材料含水分过高、材料过于混杂及螺杆不干净、无背压等等导致的。 解决措施:1、增加材料烘烤时间。2、加大塑化背压。3、减少螺杆送退位置。4、放慢射出速度。 5、降低成型温度。6、清晰螺杆。7、跟换新材料。 实例分析之顶白:产品顶白是有产品冷却时间不够、产品太过于饱满、顶出速度过快、产品脱模角度不够、 后模模仁有倒扣、产品壁厚太薄等等导致的。 解决措施:1、增加冷却时间。2、降低射出速度及保压压力、保压时间、塑化背压、成型温度。3、降低 顶出速度。4、增加脱模角度。5、后模抛光/省模。6、增加顶针数量。7、增加产品壁厚。8、优化模具运水。 实例分析之混色:产品混色是有材料过于混杂、炮筒及烘料筒没有清洗干净这些主要原因造成的混色。 解决措施:1、降低成型温度。2、放慢射出第一段的填充速度。3、清洗螺杆及料筒。4、跟换材料。 (工艺调整只能起到降低混色成度,不能完全有效的消除混色。最好是清洗螺杆及更换材料最为有效。)
2.1注塑基本理论知识
1、何谓跑道效应
面试官常问的问题
(沿着跑道可以高运动以及有规律的运动节奏称之为跑道效应。)在 填充完较薄部位之前,流体快速通过型腔的较厚部位,便会发生跑道效 应出现包风。 2、何谓内应力 (当物体没有外部因素作用时,物体内部依然保持自相抗衡的应力称 之为内力.)当塑料熔体进入快速冷却的模腔时,制品表面的降温速率 远比内层快,表层迅速地冷却而固化,由于凝固的塑料导热性差,制品 内部凝固很缓慢,当浇口封闭时,不能对中心冷却收缩进行补料,那么, 内层会因收缩处于拉伸状态,而表层则处于相反状态的压应力,这种应 力在开模后来不及消除而留在制品里,我们称之为残余应力或内应力。
3.8注塑成型缺陷原因分析
原因分析
现象 模具方面 1.浇口、流道太小 2.排气不良 3.型腔内有杂物 设备方面 1.注塑机吨位太小 2.喷嘴中有异物 工艺方面 1.成型温度太低 2.注射速度及保压压力 过低 3. 保压时间太短 4.模温过低 1成型温度过高 2.射出速度、熔胶量、 保压时间、保压压力过 高。 3.模温太高 1.注射速度及保压压力 过低 2. 保压时间过短 3.成型周期太短 1.收缩 率过大 1.厚壁不一致 材料方 面 1.流动 性不 足 产品设计 1.壁厚太薄
3.6:注塑成型缺陷分析、实例分析
堵孔、结合线
此处组装 是容易破 裂已经用 彩笔简单 的描绘出 来了 此处 有熔接痕
此处容 易堵孔
实例分析:产品产品结合线是由于脱模剂喷的过多,如果不打脱模剂那么产品容易拉白,进水口和出水口容易堵孔 已知数据:1、经过产品解剖得知产品堵孔,是因为活动镶件使用时间过长,活动镶件有磨损。2、不喷脱模剂就拉 白,喷了脱模剂就有结合线。3、材料是PP+碳酸钙 解决措施:1、活动镶件建议在原有基础上在做大尺寸(0.05mm左右),或者重新配。2、熔接痕是因为脱模剂喷的 过多,影响了产品的融合,才导致产品有裂痕及产品在组装的容易破裂。建议此处在省模、抛光。3、将活动镶件更 改成自动绞牙,先绞牙后后抽芯那么可以消除型腔内部的真空,因此也可以缓解产品拉白的现象。同时可以增加生产 效率。
2
3.3:注塑成型缺陷分析、实例分析
包风、跑道效应
跑道效应 跑道效应表明存在不非平衡 流动路径,并常常产生不必 要的熔接线和气穴。
塑料流体(红色箭头)沿边缘快速 流动,困住一团气泡(蓝色圆圈)。
实例分析:根据以上图片可以清晰的看到有包风以及飞边的存在。 解决措施之飞边:1、重新调模、检查高压锁模。2、确认注塑机锁模板 是否平行。3、重新配模。 解决措施之包风:1、将模温适当提高。2、成型温度也可适当提高。 3、熔体填充至包风处开始将填充速度放慢,大约在流量总值的5%左右 。(因为产品壁厚比较薄所以将模温和成型温度提高,这样塑胶熔体长 时间内可以不被凝固,同时对末端的慢速填充是十分有利。)
2.2注塑基本理论知识
三天不看书智商输给猪
3、何谓压力 (物体流动时所受到的阻力称之为压力)压力在物理方面指垂直作用在物体表面 上的力。受力物是物体的支持面,作用点在接触面上,方向垂直于接触面。 4、何谓流量 (单位时间内所经过的流动体积称之为流量,流量的大小就速度的快慢)单位时 间内,通过河、渠或管道某一横截面的流体的量。一般指体积流量,以每秒立方 米来表示。 5、何谓背压 (指注塑机螺杆储料时后退的反向压力称之为背压)在塑料塑化过程中,熔料不断 移向料筒前端(计量室内),且越来越多,逐渐形成一个压力,推动螺杆向后退。 为了阻止螺杆后退过快,确保熔料均匀压实,需要给螺杆提供一个反方向的压力, 这个反方向阻止螺杆后退的压力称为 背压 。
2.4注塑基本理论知识
最大计量容量
滞留时间准则滞留时间 = 塑胶进入料筒到离开喷嘴的 时间 PE,PP,PS: 最少 30 秒 (大于 40 秒为好)PA, POM, PBT: 最少 60 秒 (75 秒为好) 一般允许的滞留时间 4 ~ 6 分钟: PC+ABS, PC+ASA, PBT+PC及阻燃材 料; 4 ~ 8 分钟:ABS, PC, PC-HT, PET, PBT 4 ~ 10 分钟:PA
产品筋 位意识图
实例分析:根据以上图片可以清晰的看到有熔接线的存在。 解决措施:1、提高模前模温度。2、提高熔体温度。3、先以较高的速度填充至产品结合处在将填充速度放慢。4、在 在熔接线处增加排气槽,当有必要时还需要加开溢料槽(排渣口)。5、更改产品设计,在产品结合线处的背部增加 筋位如意识图所示,利用跑道效应让熔体有先填充熔接线,那么熔接就会完全消失掉。
缺料
溢边
1.模板变形 2.模具分型面配合 尺寸有误差 3.排气槽尺寸过大 4.分型面有杂物 1.浇口、流道太小 2.模具运水设计不 合理
1.锁模力不足 2.模板不平行,格 林柱及铰臂磨损 严重 1.注塑机吨位太小 2.喷嘴中有异物
缩水
3.9注塑成型缺陷原因分析
原因分析
现象 模具方面 1.浇口尺寸太大 2.型腔尺寸不准 3.型心松动 4.模具运水不合理 1.浇口太小 2.排气不良 3.浇口位置不对 4.浇口数目过多 1.浇口位置不当 2.顶出设计不合理 使制品受力不均 设备方面 工艺方面 1.射出速度保压 压力过高 2.料筒温度过高 3.保压时间过长 4.背压过足 1.料温过低 2.模温过低 3.注塑速度太慢 1.前后模温比例 失调 2.保压时间太短 3.冷却时间太短 4.背压过大 1.原料流 动性差 1.产品结构不合 理 材料方面 产品设计
演讲资料
张 演 建 讲 辉
注塑演讲大纲
1:注塑机基本结构 2: 注塑工艺基本理论知识 3:注塑成型缺陷分析、实例分析
4:模具结构及初步认识
5:注塑周边辅机及应用 6:电气电路基本知识 7:注塑机的发展历程
1.1:注塑机基本结构
设备基本概述
注塑机构造:卧式 、立式、角式。其中 立式、卧式是最常见 成型设备
尺寸过大
熔接痕
1.材料收 缩过大
1.厚薄不均 2.结构不合理
反翘
3.10注塑成型缺陷原因分析
原因分析
现象 模具方面 1.排气不良 2.浇口位置不当 3.浇口尺寸太小 1.流道口太小 2.浇口太小 3.排气不良 4.型腔面不光 1. 脱模斜度不够 2.光洁度不够 3.顶针数量不够 设备方面 1.机台吨位太小 工艺方面 1.射出速度过快 2.保压压力太低 3.保压时间太短 4.料温过高 1.料温、模温过低 2. 2.收缩率 过大 1.材料除 湿程度不 够 产品设计 1.壁厚太厚
合模中
合模完
合模要点:慢速合模→快速合模→低压保护→高压锁模。 慢速合模是缓解快速模所产生的冲击力。快速合模是为了增加生产效率。低压保护是防止压模时将损耗降到最低 。低压保护知识要点:当后模具导柱进入前模导套时就开始低压保护,低压保护压力一般0-15par低压保护位置0. 05mm-2mm之间。 开模要点:慢速开模→中度开模→快速开模→低速开模。 慢速开模是为了排除型腔内部真空气体及防止产品拉伤等。中速开模是缓解快速开模所产生冲击力。快速开模是 为了增加生产效率。低速开速是消除快速开模后所残余的冲击力。
3.2:注塑成型缺陷分析、实例分析
波纹、流痕
波纹低熔体或模具温度在加上以慢速填充时候所发生的波纹 (振动纹)是在浇口附近出现的一种圆形波纹状表面缺陷。 流痕材料在浇口附近冻结。低熔体或模具温度,以冷料进入型 腔。导致未完全固化的材料呈现出流动形态就叫流痕。
1 实例分析:根据示图2可以清晰看胶口部位有波纹的成型缺陷。 已知数据:浇口是以直接进胶模式进胶,胶口直径约为14.8m m.材料是:PC。前模普通水,后模栋水16度,产品壁厚14.5 mm,产品单重约:900ɡ。波纹的空制在图1的红色圆圈内,就 可以了。 解决措施:1、提升前模温度到90度。2、先以很慢很慢的速 度填充至型腔内,大约填充至整个产品的0.5%-1.5%左右,在 以中低速填充至图2的红色线圈位置,最后再以中高速填充至 整个产品体积的85%-90%左右切换慢速填充,慢速填充至98% 左右开始VP压力切换。
3.7:注塑成型缺陷分析、实例分析
反翘 1
有较为明 显的翘曲
1.23mm
2
1.57mm
实例分析:产品往前模方向翘曲是由壁厚不均匀、冷却不均匀、残余应力等问题导致。 已知数据:经过产品解剖得知制品壁厚不均匀,前模一端尺寸:1.57㎜ 后模一端尺寸:1.23㎜。 前后模的冷 却水路 没有,只有中子有运水。材料为普通PP材料。 解决措施:1、检查中子是否有偏移及松动,中子松动及偏移导致制品壁厚不均匀,引起收缩不均匀,最后出 现产品翘曲。2、后模接模温,前模接模温,利用模温中和产品往前方向模翘曲。3、降低射出速度,速度 过快也会影响型芯偏移。
2、导杆支座;8、注射座;10、座移油缸
止逆环是装在螺杆头与螺杆之间,止逆环是防止熔体逆 流的,在螺杆往前注射的时候,止逆环端面与垫圈接触 使螺杆头部形成封闭的空间,当机器塑化时,此时止逆 环与垫圈松开了,使熔体通过螺杆头流入计量室。