PCB电路板制作常见的问题及改善方法汇总
pcb设计常见问题和改善措施

pcb设计常见问题和改善措施PCB设计是电子制造中不可或缺的一环,它直接关系到整个电子产品的稳定性和性能表现。
然而,很多初学者在设计PCB时常常会遇到一些问题。
本文将探讨常见的PCB设计问题及改善措施。
一、布局问题1.过于密集的布局如果布局过于密集,会导致信号串扰(crosstalk)和噪声(noise)的产生。
为了解决这个问题,可以采用分层设计,将多层电路板分为几个逻辑分区。
在每个分区内,则可以使用自己的供电和接地系统。
2.容易混淆的引脚映射在复杂的PCB设计中,引脚映射关系可能会让人感到混乱,容易出错。
这种情况下,我们应该简化引脚映射,并且尽量减少不同部件的互相干扰。
3.热点问题一些元器件非常容易发热,并产生很强的电磁干扰。
这些元器件应该被单独布局,并且应该和其他元器件保持一定的距离。
二、管理问题1.缺乏模块化设计模块化设计可以帮助我们在有需要时,快速更换某个元器件或调整局部电路。
如果缺乏模块化设计,则在维护或更新时需要耗费更多的时间和资金。
模块化设计可以使得整个系统更加灵活和可靠。
2.不合理的基本布局规则设计PCB时,应该遵循一些基本的布局规则。
例如,元器件应该遵循一定的大小和形状,以方便插入和插拔。
又如,元器件的布局和尺寸应该考虑到过孔和贴片的芯片之间的兼容性。
三、电气问题1.传输线匹配问题传输线的匹配非常重要,否则会导致信号的反射和损耗。
设计师应该使用合适的电路板布线工具,并根据电路需求寻找适当的线材。
2.串扰与干扰问题当多根传输线靠近时,它们之间的耦合可能会导致信号干扰。
此时,我们可以分析信号之间的相关性,并使用合适的工具进行干扰分析和排除。
3.接地问题良好的接地系统可以有效地减少噪声和电磁干扰对电子器件的影响。
我们应该确保供地面和接地面的区域大小合适,并且不应忽略单点接地的规则。
综上所述,设计PCB时需要注意的许多问题必须受到严格的重视和更正。
采用科学的设计思路和正确的工具可以帮助我们解决问题,实现PCB优化设计的目标。
PCB板设计常见问题及建议
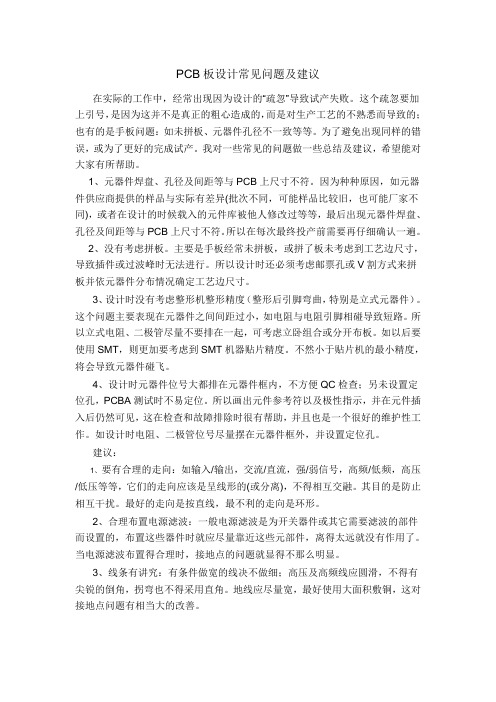
PCB板设计常见问题及建议在实际的工作中,经常出现因为设计的“疏忽”导致试产失败。
这个疏忽要加上引号,是因为这并不是真正的粗心造成的,而是对生产工艺的不熟悉而导致的;也有的是手板问题:如未拼板、元器件孔径不一致等等。
为了避免出现同样的错误,或为了更好的完成试产。
我对一些常见的问题做一些总结及建议,希望能对大家有所帮助。
1、元器件焊盘、孔径及间距等与PCB上尺寸不符。
因为种种原因,如元器件供应商提供的样品与实际有差异(批次不同,可能样品比较旧,也可能厂家不同),或者在设计的时候载入的元件库被他人修改过等等,最后出现元器件焊盘、孔径及间距等与PCB上尺寸不符。
所以在每次最终投产前需要再仔细确认一遍。
2、没有考虑拼板。
主要是手板经常未拼板,或拼了板未考虑到工艺边尺寸,导致插件或过波峰时无法进行。
所以设计时还必须考虑邮票孔或V割方式来拼板并依元器件分布情况确定工艺边尺寸。
3、设计时没有考虑整形机整形精度(整形后引脚弯曲,特别是立式元器件)。
这个问题主要表现在元器件之间间距过小,如电阻与电阻引脚相碰导致短路。
所以立式电阻、二极管尽量不要排在一起,可考虑立卧组合或分开布板。
如以后要使用SMT,则更加要考虑到SMT机器贴片精度。
不然小于贴片机的最小精度,将会导致元器件碰飞。
4、设计时元器件位号大都排在元器件框内,不方便QC检查;另未设置定位孔,PCBA测试时不易定位。
所以画出元件参考符以及极性指示,并在元件插入后仍然可见,这在检查和故障排除时很有帮助,并且也是一个很好的维护性工作。
如设计时电阻、二极管位号尽量摆在元器件框外,并设置定位孔。
建议:1、要有合理的走向:如输入/输出,交流/直流,强/弱信号,高频/低频,高压/低压等等,它们的走向应该是呈线形的(或分离),不得相互交融。
其目的是防止相互干扰。
最好的走向是按直线,最不利的走向是环形。
2、合理布置电源滤波:一般电源滤波是为开关器件或其它需要滤波的部件而设置的,布置这些器件时就应尽量靠近这些元部件,离得太远就没有作用了。
电路板(PCB)制造出现各种问答及改善方法
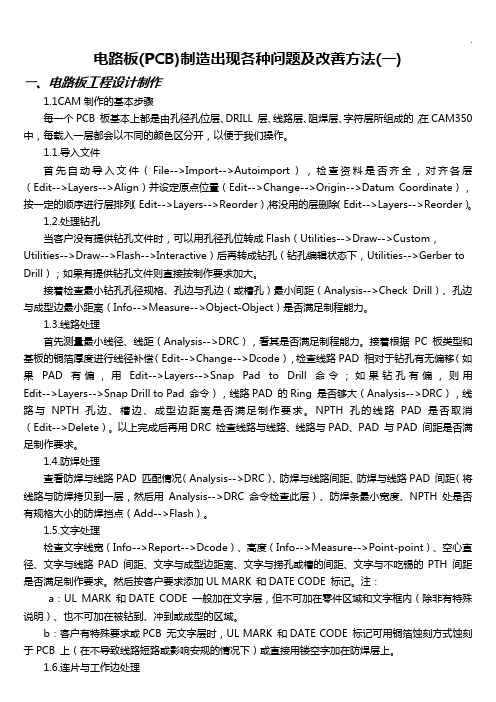
电路板(PCB)制造出现各种问题及改善方法(一)一、电路板工程设计制作1.1CAM制作的基本步骤每一个PCB 板基本上都是由孔径孔位层、DRILL 层、线路层、阻焊层、字符层所组成的,在CAM350 中,每载入一层都会以不同的颜色区分开,以便于我们操作。
1.1.导入文件首先自动导入文件(File-->Import-->Autoimport),检查资料是否齐全,对齐各层(Edit-->Layers-->Align)并设定原点位置(Edit-->Change-->Origin-->Datum Coordinate),按一定的顺序进行层排列(Edit-->Layers-->Reorder),将没用的层删除(Edit-->Layers-->Reorder)。
1.2.处理钻孔当客户没有提供钻孔文件时,可以用孔径孔位转成Flash(Utilities-->Draw-->Custom,Utilities-->Draw-->Flash-->Interactive)后再转成钻孔(钻孔编辑状态下,Utilities-->Gerber to Drill);如果有提供钻孔文件则直接按制作要求加大。
接着检查最小钻孔孔径规格、孔边与孔边(或槽孔)最小间距(Analysis-->Check Drill)、孔边与成型边最小距离(Info-->Measure-->Object-Object)是否满足制程能力。
1.3.线路处理首先测量最小线径、线距(Analysis-->DRC),看其是否满足制程能力。
接着根据PC 板类型和基板的铜箔厚度进行线径补偿(Edit-->Change-->Dcode),检查线路PAD 相对于钻孔有无偏移(如果PAD 有偏,用Edit-->Layers-->Snap Pad to Drill 命令;如果钻孔有偏,则用Edit-->Layers-->Snap Drill to Pad 命令),线路PAD 的Ring 是否够大(Analysis-->DRC),线路与NPTH 孔边、槽边、成型边距离是否满足制作要求。
PCB制作设计过程中出现的问题及解决办法
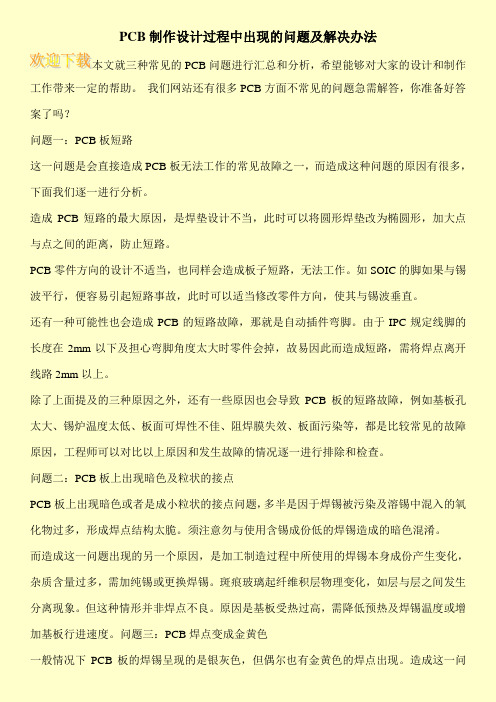
PCB制作设计过程中出现的问题及解决办法本文就三种常见的PCB问题进行汇总和分析,希望能够对大家的设计和制作工作带来一定的帮助。
我们网站还有很多PCB方面不常见的问题急需解答,你准备好答案了吗?问题一:PCB板短路这一问题是会直接造成PCB板无法工作的常见故障之一,而造成这种问题的原因有很多,下面我们逐一进行分析。
造成PCB短路的最大原因,是焊垫设计不当,此时可以将圆形焊垫改为椭圆形,加大点与点之间的距离,防止短路。
PCB零件方向的设计不适当,也同样会造成板子短路,无法工作。
如SOIC的脚如果与锡波平行,便容易引起短路事故,此时可以适当修改零件方向,使其与锡波垂直。
还有一种可能性也会造成PCB的短路故障,那就是自动插件弯脚。
由于IPC规定线脚的长度在2mm以下及担心弯脚角度太大时零件会掉,故易因此而造成短路,需将焊点离开线路2mm以上。
除了上面提及的三种原因之外,还有一些原因也会导致PCB板的短路故障,例如基板孔太大、锡炉温度太低、板面可焊性不佳、阻焊膜失效、板面污染等,都是比较常见的故障原因,工程师可以对比以上原因和发生故障的情况逐一进行排除和检查。
问题二:PCB板上出现暗色及粒状的接点PCB板上出现暗色或者是成小粒状的接点问题,多半是因于焊锡被污染及溶锡中混入的氧化物过多,形成焊点结构太脆。
须注意勿与使用含锡成份低的焊锡造成的暗色混淆。
而造成这一问题出现的另一个原因,是加工制造过程中所使用的焊锡本身成份产生变化,杂质含量过多,需加纯锡或更换焊锡。
斑痕玻璃起纤维积层物理变化,如层与层之间发生分离现象。
但这种情形并非焊点不良。
原因是基板受热过高,需降低预热及焊锡温度或增加基板行进速度。
问题三:PCB焊点变成金黄色一般情况下PCB板的焊锡呈现的是银灰色,但偶尔也有金黄色的焊点出现。
造成这一问。
电路板(PCB)制造出现各种问答及改善方法
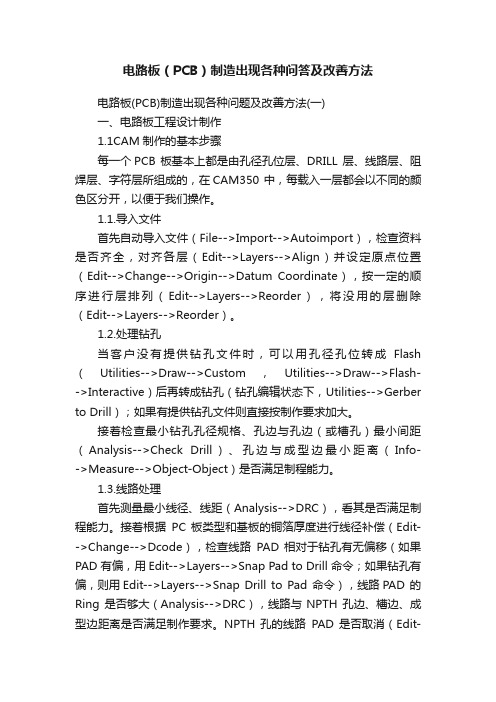
电路板(PCB)制造出现各种问答及改善方法电路板(PCB)制造出现各种问题及改善方法(一)一、电路板工程设计制作1.1CAM制作的基本步骤每一个PCB 板基本上都是由孔径孔位层、DRILL 层、线路层、阻焊层、字符层所组成的,在CAM350 中,每载入一层都会以不同的颜色区分开,以便于我们操作。
1.1.导入文件首先自动导入文件(File-->Import-->Autoimport),检查资料是否齐全,对齐各层(Edit-->Layers-->Align)并设定原点位置(Edit-->Change-->Origin-->Datum Coordinate),按一定的顺序进行层排列(Edit-->Layers-->Reorder),将没用的层删除(Edit-->Layers-->Reorder)。
1.2.处理钻孔当客户没有提供钻孔文件时,可以用孔径孔位转成Flash (Utilities-->Draw-->Custom,Utilities-->Draw-->Flash-->Interactive)后再转成钻孔(钻孔编辑状态下,Utilities-->Gerber to Drill);如果有提供钻孔文件则直接按制作要求加大。
接着检查最小钻孔孔径规格、孔边与孔边(或槽孔)最小间距(Analysis-->Check Drill)、孔边与成型边最小距离(Info-->Measure-->Object-Object)是否满足制程能力。
1.3.线路处理首先测量最小线径、线距(Analysis-->DRC),看其是否满足制程能力。
接着根据PC 板类型和基板的铜箔厚度进行线径补偿(Edit-->Change-->Dcode),检查线路PAD 相对于钻孔有无偏移(如果PAD 有偏,用Edit-->Layers-->Snap Pad to Drill 命令;如果钻孔有偏,则用Edit-->Layers-->Snap Drill to Pad 命令),线路PAD 的Ring 是否够大(Analysis-->DRC),线路与NPTH 孔边、槽边、成型边距离是否满足制作要求。
pcb常见缺陷原因与措施

焊点氧化
长时间存储可能导致焊点氧化,引起接触不良 或开路。
结构变化
长时间存储可能导致PCB结构变化,如弯曲或变形。
04
检测与修复过程中的常见缺陷 原因
检测设备故障或精度不足
设备老化
设备长时间使用可能导致 部件磨损,影响检测精度 。
设备维护不当
定期维护和保养不到位, 可能导致设备故障。
设备校准问题
制定操作规范
制定详细的操作规范和作业指导书,确保员工严格按照规范进行操 作。
建立激励机制
建立员工激励机制,鼓励员工积极学习和提高自己的技能水平。
加强运输和存储环节的管理和监控
确保运输安全
选择具有良好信誉和稳定运输能力的物流公司,确保 产品在运输过程中不受损坏或丢失。
加强存储管理
制定存储管理规定和操作规范,确保产品存储环境良 好,避免产品在存储过程中受损或变质。
进行定期检查
对存储和运输环节进行定期检查,及时发现和处理可 能出现的问题。
06
针对不同类型缺陷的具体应对 措施建议
针对原材料问题的应对措施建议
严格控制原材料质量
对供应商进行评估和选择,确保原材料的质 量稳定可靠。
加强原材料检验
对进料进行严格检验,确保符合设计要求和 相关标准。
建立原材料追溯体系
对原材料进行标识和追溯,以便及时发现和 解决问题。
设备校准不准确,导致检 测结果偏差。
修复技术不当或材料问题
修复方法选择不当
针对不同缺陷应采用不同的修复方法 ,选择不当可能导致修复效果不佳。
材料质量问题
修复工艺问题
修复过程中工艺控制不当,如温度、 压力、时间等参数控制不准确,可能 导致修复失败。
PCB十大质量问题与对策
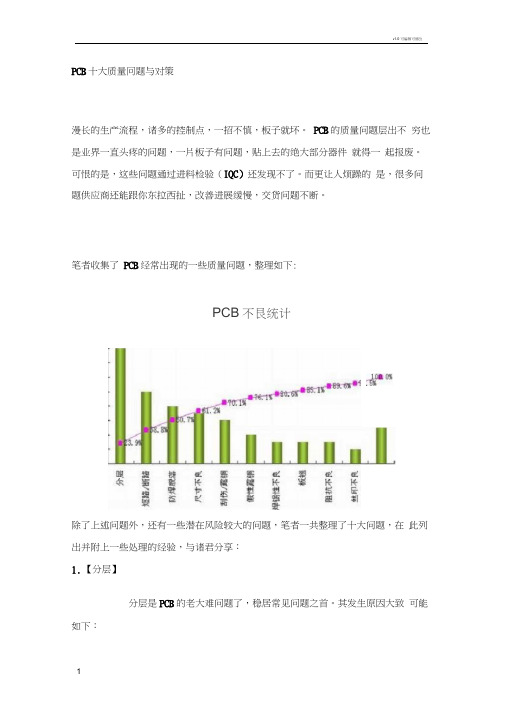
PCB十大质量冋题与对策漫长的生产流程,诸多的控制点,一招不慎,板子就坏。
PCB的质量问题层出不穷也是业界一直头疼的问题,一片板子有问题,贴上去的绝大部分器件就得一起报废。
可恨的是,这些问题通过进料检验(IQC)还发现不了。
而更让人烦躁的是,很多问题供应商还能跟你东拉西扯,改善进展缓慢,交货问题不断。
笔者收集了PCB经常出现的一些质量问题,整理如下:PCB不艮统计除了上述问题外,还有一些潜在风险较大的问题,笔者一共整理了十大问题,在此列出并附上一些处理的经验,与诸君分享:1.【分层】分层是PCB的老大难问题了,稳居常见问题之首。
其发生原因大致可能如下:(1)包装或保存不当,受潮;(2)保存时间过长,超过了保存期,PCB板受潮;(3)供应商材料或工艺问题;(4)设计选材和铜面分布不佳。
受潮问题是比较容易发生的,就算选了好的包装,工厂内也有恒温恒湿仓库,可是运输和暂存过程是控制不了的。
笔者曾“有幸”参观过一个保税仓库,温湿度管理是别指望了,房顶还在漏水,箱子是直接呆在水里的。
不过受潮还是可以应对的,真空导电袋或者铝箔袋都可以不错地防护水汽侵入,同时包装袋里要求放湿度指示卡。
如果在使用前发现湿度卡超标,上线前烘烤一般可以解决,烘烤条件通常是120度,4耳如果是供应商处材料或工艺发生问题,那报废的可能性就比较大了。
常见的可能原因包括:棕(黑)化不良,PP或内层板受潮,PP胶量不足,压合异常等。
为了减少这种情况的问题发生,需要特别关注PCB供应商对对应流程的管理和分层的可靠性试验。
以可靠性试验中的热应力测试为例,好的工厂通过标准要求是5次以上不能分层,在样品阶段和量产的每个周期都会进行确认,而普通工厂通过标准可能只是2次,几个月才确认一次。
而模拟贴装的IR测试也可以更多地防止不良品流出,是优秀PCB厂的必备。
当然设计公司本身的PCB设计也会带来分层的隐患。
例如板材Tg的选择,很多时候是没有要求的,那PCBT为了节约成本,肯定选用普通Tg的材料,耐温性能就会比较差。
电路板PCB制造出现各种问题及改善方法

制作要求。然后按客户要求添加 ULMARK 和 DATECODE 标记。注:
a:ULMARK 和 DATECODE 一般加在文字层, 但不可加在零件区域和文字框内 (除非有特殊说明) 、
也不可加在被钻到、冲到或成型的区域。
b:客户有特殊要求或 PCB 无文字层时, ULMARK 和 DATECODE 标记可用铜箔蚀刻方式蚀刻于
模拟和数字元件应放置在它们自己的专门 PCB 区域。电源应放置在板边沿或者角落和模拟与数字
区域之间。
电源布线对噪声性能也是关键。数字元件 (特别是高速大功率数字元件 )不能放置、也不能靠近模拟
返回电流流回电源的通路。 这就是数字元件不应放置在靠近承载模拟电流的线或到模拟和混合信号元件
的电源线。注意,电源承载信号电流,因为它们重新充电板上的旁路电容器。返回电流必须通过分离地
ADC 模拟电源最好采用线性电压稳压器。
·假若任何数字电路供电电源和 ADC 输出驱动器电源是同一电源,并有信号线到板的另外区域,则 这两个电源平板之间用电容器。把这些电容器放置在紧靠信号线处。
?1.12.1 ,检查用户的文件 用户拿来的文件,首先要进行例行的检查:
1,检查磁盘文件是否完好;
2,检查该文件是否带有病毒,有病毒则必须先杀病毒;
和 ADC 数字输出驱动器的电源平板。
·ADC 数字芯核电源用模拟电源,但 ADC 数字驱动器不能用模拟电源。
·ADC 数字输出驱动器电源可以是 ADC 输出驱动元件的相同电源。
·把所有模拟元件和连线放置在模拟电源平板之上,把所有数字元件和连线放置在数字电源平板之
上。
·每个平板用分离的电源。 ADC 数字输出电源,可以来自任何一个电源,但应该用串联扼流圈去耦。
PCB常见缺陷原因与措施

PCB常见缺陷原因与措施引言Printed Circuit Board(PCB)是电子产品中不可或缺的组成部分。
而PCB在制造的过程中常常会出现各种缺陷,严重影响到电子产品的性能和质量。
本文将介绍PCB常见的缺陷原因,并提出相应的解决措施,以帮助读者更好地了解和解决PCB制造过程中的问题。
一、焊点问题1. 缺陷原因•锡焊不良:焊料不完全熔化、焊料过量或者焊料流动不顺畅都会导致焊点的质量下降。
•冷焊:焊接温度过低,导致焊料与焊盘间粘附力不足,形成冷焊现象。
•焊接过热:焊接温度过高,导致焊料流动过快,造成焊点高度不均匀、焊缝过大。
•焊接气泡:在焊接过程中,焊料中的挥发性成分产生气泡,导致焊点质量下降。
2. 解决措施•控制焊接温度:根据焊接材料的要求,合理设定焊接温度,以充分熔化焊料。
•控制焊接时间:根据焊接材料和焊接面积,控制焊接时间,确保焊料充分流动且均匀。
•检测焊接质量:通过焊接质量检测设备,对焊点进行检测,发现问题及时修复。
•提高焊接技术:通过培训和实践,提高焊接工人的技术水平,降低焊接缺陷率。
二、线路板污染问题1. 缺陷原因•灰尘和异物:制造环境不洁净,灰尘和其他杂物会污染线路板表面,影响电路连接质量。
•油污和氧化物:线路板表面受到油污和氧化物的污染,导致线路板表面粗糙、电路导通不良。
2. 解决措施•清洁环境:确保生产车间的清洁和通风,定期清理灰尘和杂物,防止其附着到线路板上。
•使用防护层:在制造过程中,使用防护层覆盖线路板表面,防止油污和氧化物的污染。
•采用合适的清洁剂:在清洗线路板时,选择合适的清洁剂,去除油污和氧化物,确保线路板表面干净和平滑。
•加强质检:建立完善的质检体系,对线路板进行全面检查,及时发现并处理污染问题。
三、连线问题1. 缺陷原因•线路断开:线路横截面积不足、线路受到外力破坏等原因导致线路断开,造成电路不通。
•线路短路:线路之间存在不必要的电气连接,造成电路短路。
•线路错位:线路连接错误,导致电气信号传输错误。
PCB电路板制作常见的问题及改善方法汇总
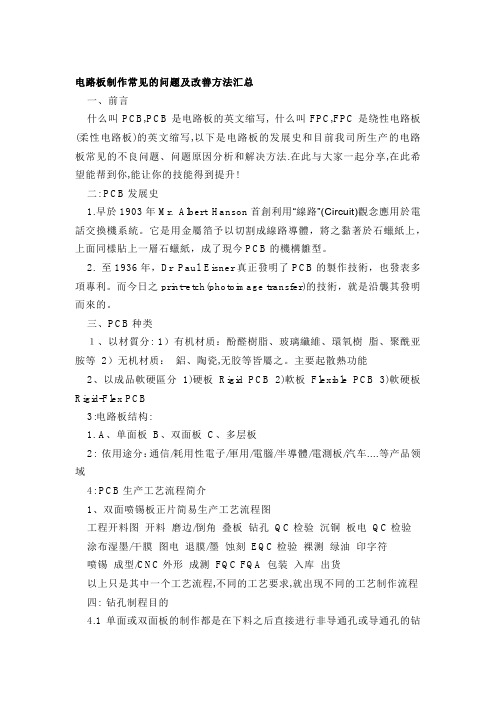
电路板制作常见的问题及改善方法汇总一、前言什么叫PCB,PCB是电路板的英文缩写, 什么叫FPC,FPC是绕性电路板(柔性电路板)的英文缩写,以下是电路板的发展史和目前我司所生产的电路板常见的不良问题、问题原因分析和解决方法.在此与大家一起分享,在此希望能帮到你,能让你的技能得到提升!二: PCB发展史1.早於1903年Mr. Albert Hanson首創利用“線路”(Circuit)觀念應用於電話交換機系統。
它是用金屬箔予以切割成線路導體,將之黏著於石蠟紙上,上面同樣貼上一層石蠟紙,成了現今PCB的機構雛型。
2. 至1936年,Dr Paul Eisner真正發明了PCB的製作技術,也發表多項專利。
而今日之print-etch(photoimage transfer)的技術,就是沿襲其發明而來的。
三、PCB种类1、以材質分: 1)有机材质:酚醛樹脂、玻璃纖維、環氧樹脂、聚酰亚胺等2)无机材质:鋁、陶瓷,无胶等皆屬之。
主要起散熱功能2、以成品軟硬區分1)硬板Rigid PCB 2)軟板Flexible PCB 3)軟硬板Rigid-Flex PCB3:电路板结构:1. A、单面板B、双面板C、多层板2: 依用途分:通信/耗用性電子/軍用/電腦/半導體/電測板/汽车....等产品领域4: PCB生产工艺流程简介1、双面喷锡板正片简易生产工艺流程图工程开料图开料磨边/倒角叠板钻孔QC检验沉铜板电QC检验涂布湿墨/干膜图电退膜/墨蚀刻EQC检验裸测绿油印字符喷锡成型/CNC外形成测FQC FQA 包装入库出货以上只是其中一个工艺流程,不同的工艺要求,就出现不同的工艺制作流程四: 钻孔制程目的4.1单面或双面板的制作都是在下料之后直接进行非导通孔或导通孔的钻孔, 多层板则是在完成压板之后才去钻孔。
传统孔的种类除以导通与否简单的区分外,以功能的不同尚可分:零件孔,工具孔,通孔(Via),盲孔(Blind hole),埋孔(Buried hole)(后二者亦为via hole的一种).近年电子产品'轻.薄.短.小.快.'的发展趋势,使得钻孔技术一日千里,机钻,雷射烧孔,感光成孔等.4.2流程:上PIN→钻孔→检查全流程线路板厂,都会有钻孔这麽一道工序。
pcb板常见问题与维修
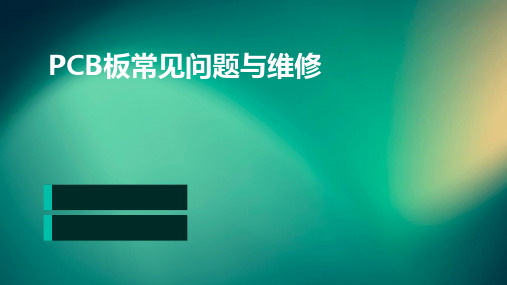
目录
• PCB板常见问题 • PCB板维修方法 • PCB板维修工具 • PCB板维修注意事项
01 PCB板常见问题
短路
总结词
短路是指在PCB板上,两个不应 该导通的电路之间出现了导通现 象。
详细描述
短路可能由多种原因引起,如污 染物、湿气、焊锡桥、元件放置 不当等。短路可能导致电路功能 异常、设备过热甚至烧毁。
在维修过程中,应记录所做的更改和 修复,以便于后续的维护和管理。
遵循维修步骤
按照正确的维修步骤进行操作,避免 因操作不当导致电路板损坏或安全事 故。
THANKS FOR WATCHING
感谢您的观看
环境注意事项
适宜的温度和湿度
维修PCB板时应确保工作 环境的温度和湿度适宜, 避免过高的温度或湿度影 响维修效果。
远离磁场干扰
在维修过程中应尽量远离 磁场干扰,以免影响电子 元件的正常工作。
防静电措施
采取适当的防静电措施, 以防止静电对电子元件造 成损坏。
操作注意事项
熟悉电路原理
记录维修过程
在维修之前,应对PCB板的电路原理 有一定的了解,以便更好地进行故障 诊断和维修。
焊盘脱落维修
总结词
焊盘脱落是指PCB板上的导电焊盘与线路断开,导致电路中断。
详细描述
焊盘脱落维修需要重新连接脱落的焊盘与线路,可以使用焊锡进行焊接,或者使用导电胶进行粘接。 在修复过程中要小心不要损坏周围的元件和线路。
铜箔翘起维修
总结词
铜箔翘起是指PCB板上的铜箔层发生翘曲或 脱落现象。
详细描述
焊盘脱落
总结词
焊盘脱落是指PCB板上的导电焊盘与线路或元件分离,导致 电路断开。
pcb品质提升改善方案

pcb品质提升改善方案一、目前PCB品质问题的“病根儿”咱PCB(印制电路板)啊,就像电子产品的小血管和骨架,要是品质不好,那整个电子产品都得闹脾气。
现在咱这PCB有不少问题呢。
比如说,线路短路就像小路上突然堵了大石头,电流过不去;还有开路,这就好比路中间突然断了,电流也没法跑。
另外,焊接不良就像盖房子的时候砖头没粘好,随时可能掉链子。
二、具体的“治病良方”1. 原材料的严格把关。
供应商这块儿得好好挑选,不能随便找个“路人甲”供应商。
就像找对象一样,得找个靠谱的。
得看看他们的口碑咋样,以前生产的原材料质量好不好,有没有经常出岔子。
原材料一到货,咱就得像检查宝贝一样仔细检查。
不能只看表面,得深入检查内部结构,看看有没有隐藏的“小毛病”。
比如说,检查铜箔的厚度是不是均匀,玻纤布有没有破损啥的。
要是发现有问题的原材料,坚决不要,不能让它混进咱们的生产队伍。
2. 生产流程的精细管理。
设计环节是PCB的“灵魂规划”。
咱得找那些经验丰富的设计师,他们就像建筑大师一样,设计出来的线路布局要合理,间距要合适,不能让线路之间太拥挤,容易打架(短路)。
而且,设计好之后得反复检查,多找几个人看看,说不定谁就能发现一个隐藏的小漏洞。
生产设备要像对待宠物一样精心照顾。
定期给它们做个“体检”,擦擦油、紧紧螺丝啥的。
要是设备老了或者病了,生产出来的PCB肯定也有问题。
比如说,钻孔机要是钻头钝了,钻出来的孔就可能不标准,这就会影响后续的工序。
在生产过程中,每个工序都得设置“小关卡”。
就像玩游戏闯关一样,上一个工序合格了才能进入下一个工序。
比如说,蚀刻完了要检查线路是不是蚀刻完整了,没蚀刻好的就不能进入下一道工序。
而且每个工序的工人得是熟练工,不能是刚上手的新手,这就好比让一个刚学做饭的人去做满汉全席,肯定做不好。
3. 人员培训与激励。
得给咱的员工好好培训。
不能让他们稀里糊涂地干活。
要让他们知道PCB每个环节的重要性,就像告诉士兵他们守卫的是非常重要的阵地一样。
pcb常见缺陷原因与措施

pcb常见缺陷原因与措施以pcb常见缺陷原因与措施为题,对pcb常见缺陷进行分析,并提出相应的解决措施。
一、常见pcb缺陷及其原因1. 焊盘剥落:焊盘剥落是pcb制造中常见的缺陷,主要原因包括焊接温度不合适、焊盘表面处理不当以及焊接压力不均等。
这些问题会导致焊盘与基板之间的粘附力不足,造成焊盘剥落。
2. 焊接短路:焊接短路是pcb制造中的另一个常见问题,主要原因是焊接过程中,焊料过多或焊接位置不准确,导致电路之间产生短路。
此外,焊接过程中的静电也是引起焊接短路的重要原因之一。
3. 焊接开路:焊接开路是pcb制造中的常见问题,主要原因是焊接温度不够高或焊接时间不足,导致焊料未完全熔化,无法与基板形成牢固的连接。
此外,焊盘与焊盘之间的距离也会影响焊接质量,距离过大会导致焊接开路。
4. 焊盘错位:焊盘错位是pcb制造中常见的缺陷,主要原因是焊盘布局设计不合理或制造过程中的误操作。
焊盘错位会导致焊接位置不准确,影响电路的连接性能。
5. 焊盘过度露铜:焊盘过度露铜是pcb制造中的常见缺陷,主要原因包括蚀刻不当、工艺参数设置错误以及材料选择不当等。
过度露铜会导致焊盘的机械强度下降,容易引起焊盘剥落或焊接开路。
二、常见pcb缺陷的解决措施1. 控制焊接温度和时间:合理控制焊接温度和时间是防止焊盘剥落、焊接短路和焊接开路的关键。
通过调整焊接参数,确保焊料能够充分熔化并与基板形成牢固的连接。
2. 加强焊盘表面处理:焊盘表面处理对焊盘的粘附性有很大影响。
通过选择合适的表面处理方法,如喷锡、化学镀金等,可以提高焊盘的附着力,减少焊盘剥落的风险。
3. 控制焊接压力和位置:合理控制焊接压力和位置是防止焊盘错位的关键。
通过调整焊接设备的参数,确保焊接位置准确,避免焊盘错位。
4. 优化焊接工艺:通过优化焊接工艺,如优化焊接温度曲线、调整焊接速度等,可以减少焊接短路和焊接开路的发生。
此外,加强对焊接操作人员的培训,提高他们的技术水平和操作规范性,也是防止焊接缺陷的重要手段。
PCB制程问题的分析与改善对策
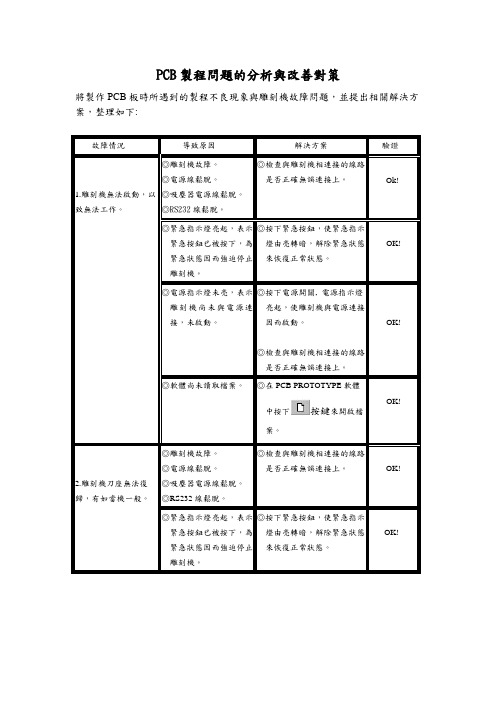
PCB製程問題的分析與改善對策
將製作PCB板時所遇到的製程不良現象與雕刻機故障問題,並提出相關解決方案,整理如下:
故障情況導致原因解決方案驗證
1.雕刻機無法啟動,以致無法工作。
◎雕刻機故障。
◎電源線鬆脫。
◎吸塵器電源線鬆脫。
◎RS232線鬆脫。
◎檢查與雕刻機相連接的線路
是否正確無誤連接上。
Ok!
◎緊急指示燈亮起,表示
緊急按鈕已被按下,為
緊急狀態因而強迫停止
雕刻機。
◎按下緊急按鈕,使緊急指示
燈由亮轉暗,解除緊急狀態
來恢復正常狀態。
OK!
◎電源指示燈未亮,表示
雕刻機尚未與電源連
接,未啟動。
◎按下電源開關,電源指示燈
亮起,使雕刻機與電源連接
因而啟動。
◎檢查與雕刻機相連接的線路
是否正確無誤連接上。
OK!
◎軟體尚未讀取檔案。
◎在PCB PROTOTYPE軟體
中按下按鍵來開啟檔
案。
OK!
2.雕刻機刀座無法復歸,有如當機一般。
◎雕刻機故障。
◎電源線鬆脫。
◎吸塵器電源線鬆脫。
◎RS232線鬆脫。
◎檢查與雕刻機相連接的線路
是否正確無誤連接上。
OK!
◎緊急指示燈亮起,表示
緊急按鈕已被按下,為
緊急狀態因而強迫停止
雕刻機。
◎按下緊急按鈕,使緊急指示
燈由亮轉暗,解除緊急狀態
來恢復正常狀態。
OK!。
pcb板的创作与设计中遇到的问题及解决方法

pcb板的创作与设计中遇到的问题及解决方法【知识】主题:PCB板的创作与设计中遇到的问题及解决方法导语:PCB板作为电子产品中不可或缺的一部分,在创作和设计的过程中常常面临各种问题。
本文将从深度和广度的角度,全面评估PCB 板创作和设计中遇到的问题,并提供解决方法,以帮助读者更深入地理解和解决这些技术挑战。
一、PCB板创作与设计中常见问题1.1 接线布局错误导致的电路故障在PCB板创作和设计过程中,接线布局是一个非常关键的环节。
错误的接线布局可能会导致电路故障,甚至无法正常工作。
常见的问题包括相互干扰的信号线、电源线或地线不合理分布等。
这些问题可能会导致信号串扰、电源噪声以及辐射干扰等一系列问题。
解决方法:1. 仔细规划信号线、电源线和地线的布局,尽量避免它们的交叉和相互干扰。
2. 使用屏蔽罩或地平面屏蔽技术来减少干扰。
3. 使用合适的阻抗匹配和终端电阻来降低信号串扰。
1.2 高频电路设计困难在高频电路设计中,信号的频率和速度非常高,要求非常高的板线布局和元件参数选择。
许多设计师在高频电路设计中面临困难,如信号完整性、匹配网络、信号衰减等问题。
解决方法:1. 了解高频电路设计常用的技术和规范,如微波电路设计、EMC设计等。
2. 使用仿真工具进行模拟和验证,如SPICE、ADS等,以确保信号完整性和匹配网络性能。
3. 仔细选择高频器件和元件参数,根据实际需求进行调整。
1.3 PCB板材料选择问题PCB板材料的选择直接影响到电路性能、散热效果和可靠性。
常见的问题包括材料热传导性能不佳、介电常数过大等,这些问题可能会导致电路性能下降、工作温度过高等问题。
解决方法:1. 根据实际需求选择合适的PCB板材料,考虑其热传导性能、介电常数、机械强度等因素。
2. 注意材料的可靠性和供货渠道,选择知名品牌或可靠的供应商。
1.4 PCB板制造工艺问题PCB板的制造工艺是保证电路性能和可靠性的重要环节。
常见的问题包括线路走线粗细不一致、焊盘大小不合适等,这些问题可能会导致焊接不良、导线过热等问题。
电路板(PCB)制造出现各种问题及改善方法

电路板(PCB)制造出现各种问题及改善方法(一)一、电路板工程设计制作制作的基本步骤每一个PCB 板基本上都是由孔径孔位层、DRILL 层、线路层、阻焊层、字符层所组成的,在CAM350 中,每载入一层都会以不同的颜色区分开,以便于我们操作。
.导入文件首先自动导入文件(File-->Import-->Autoimport),检查资料是否齐全,对齐各层(Edit-->Layers-->Align)并设定原点位置(Edit-->Change-->Origin-->Datum Coordinate),按一定的顺序进行层排列(Edit-->Layers-->Reorder),将没用的层删除(Edit-->Layers-->Reorder)。
.处理钻孔当客户没有提供钻孔文件时,可以用孔径孔位转成Flash (Utilities-->Draw-->Custom,Utilities-->Draw-->Flash-->Interactive)后再转成钻孔(钻孔编辑状态下,Utilities-->Gerber to Drill);如果有提供钻孔文件则直接按制作要求加大。
接着检查最小钻孔孔径规格、孔边与孔边(或槽孔)最小间距(Analysis-->Check Drill)、孔边与成型边最小距离(Info-->Measure-->Object-Object)是否满足制程能力。
.线路处理首先测量最小线径、线距(Analysis-->DRC),看其是否满足制程能力。
接着根据PC 板类型和基板的铜箔厚度进行线径补偿(Edit-->Change-->Dcode),检查线路PAD 相对于钻孔有无偏移(如果PAD 有偏,用Edit-->Layers-->Snap Pad to Drill 命令;如果钻孔有偏,则用Edit-->Layers-->Snap Drill to Pad 命令),线路PAD 的Ring 是否够大(Analysis-->DRC),线路与NPTH 孔边、槽边、成型边距离是否满足制作要求。
PCB设计中常见问题及调试技巧综述研究

PCB设计中常见问题及调试技巧综述研究PCB(Printed Circuit Board)设计是电子产品开发过程中重要的一环。
在PCB设计中,常常会遇到一些常见问题,如电磁兼容性、电路布局、信号完整性等问题。
本文将综述PCB设计中常见问题,并提供一些调试技巧。
一、电磁兼容性问题电磁兼容性是指电路板设计的电磁波及干扰对设备造成的影响。
在PCB设计中,常见的电磁兼容性问题有:1. 电源和信号线干扰:在电路板布局中,应避免信号线与电源线靠得太近,以减少串扰。
同时,对于高频信号线,应使用差分传输线来减少干扰。
2. 地线布局:地线是整个电路板中最重要的一条线路,正确地布局地线可以有效地减少电磁干扰。
一般来说,应尽量缩短地线的长度,避免出现回流环路。
3. 屏蔽设计:在高频电路中,应考虑采用屏蔽材料来减少电磁辐射。
合理设置屏蔽罩和屏蔽框可以有效地降低干扰。
4. 组态设计:在多层PCB设计中,可以考虑将干扰源放在一层,将受干扰的线路放在另一层,通过屏蔽层来隔离。
调试技巧:使用电磁兼容性测试仪器进行测试,如频谱分析仪、电磁场探测器等。
二、电路布局问题电路布局是PCB设计中至关重要的一步。
良好的电路布局可以确保信号完整性和电磁兼容性。
以下是一些常见的电路布局问题和解决技巧:1. 良好的信号完整性:如数据线、时钟线等,应保证布局对称,长度平等,并避免与电源线、高电流回路靠近。
2. 连接器位置:连接器的位置应根据外部接口进行合理布局,尽量避免长距离连接线,以减少信号传输的损耗。
3. 良好的热管理:布局要考虑散热问题,尽量避免热源与敏感部件(如低噪声放大器、放大器等)靠近。
4. 解耦电容和滤波电容的选择和布局:解耦电容应尽量靠近电源和地线,以降低功率噪声;滤波电容应根据实际需要选择合适的数值和布局。
调试技巧:通过布线规则的审查和信号完整性分析,如时序分析、电源噪声分析等工具。
三、信号完整性问题信号完整性是指信号在传输过程中是否能够保持其原有的形态和特性。
- 1、下载文档前请自行甄别文档内容的完整性,平台不提供额外的编辑、内容补充、找答案等附加服务。
- 2、"仅部分预览"的文档,不可在线预览部分如存在完整性等问题,可反馈申请退款(可完整预览的文档不适用该条件!)。
- 3、如文档侵犯您的权益,请联系客服反馈,我们会尽快为您处理(人工客服工作时间:9:00-18:30)。
电路板制作常见的问题及改善方法汇总一、前言什么叫PCB,PCB是电路板的英文缩写, 什么叫FPC,FPC是绕性电路板(柔性电路板)的英文缩写,以下是电路板的发展史和目前我司所生产的电路板常见的不良问题、问题原因分析和解决方法.在此与大家一起分享,在此希望能帮到你,能让你的技能得到提升!二: PCB发展史1.早於1903年Mr. Albert Hanson首創利用“線路”(Circuit)觀念應用於電話交換機系統。
它是用金屬箔予以切割成線路導體,將之黏著於石蠟紙上,上面同樣貼上一層石蠟紙,成了現今PCB的機構雛型。
2. 至1936年,Dr Paul Eisner真正發明了PCB的製作技術,也發表多項專利。
而今日之print-etch(photoimage transfer)的技術,就是沿襲其發明而來的。
三、PCB种类1、以材質分: 1)有机材质:酚醛樹脂、玻璃纖維、環氧樹脂、聚酰亚胺等2)无机材质:鋁、陶瓷,无胶等皆屬之。
主要起散熱功能2、以成品軟硬區分1)硬板Rigid PCB 2)軟板Flexible PCB 3)軟硬板Rigid-Flex PCB3:电路板结构:1. A、单面板B、双面板C、多层板2: 依用途分:通信/耗用性電子/軍用/電腦/半導體/電測板/汽车....等产品领域4: PCB生产工艺流程简介1、双面喷锡板正片简易生产工艺流程图工程开料图开料磨边/倒角叠板钻孔QC检验沉铜板电QC检验涂布湿墨/干膜图电退膜/墨蚀刻EQC检验裸测绿油印字符喷锡成型/CNC外形成测FQC FQA 包装入库出货以上只是其中一个工艺流程,不同的工艺要求,就出现不同的工艺制作流程四: 钻孔制程目的4.1单面或双面板的制作都是在下料之后直接进行非导通孔或导通孔的钻孔, 多层板则是在完成压板之后才去钻孔。
传统孔的种类除以导通与否简单的区分外,以功能的不同尚可分:零件孔,工具孔,通孔(Via),盲孔(Blind hole),埋孔(Buried hole)(后二者亦为via hole的一种).近年电子产品'轻.薄.短.小.快.'的发展趋势,使得钻孔技术一日千里,机钻,雷射烧孔,感光成孔等.4.2流程:上PIN→钻孔→检查全流程线路板厂,都会有钻孔这麽一道工序。
看起来钻孔是很简单,只是把板子放在钻机上钻孔,其实那是只是表面的动作,而实际上钻孔是一道非常关键的工序。
如果把线路板工艺比着是“人体”,那麽钻孔就是颈(脖子),很多厂因为钻孔不能过关而面对报废,导致亏本。
就此,凭着个人的钻孔工作经验和方法,同大家浅析钻孔工艺的一些品质故障排除。
在制造业中的不良品都离不开人、机、物、法、环五大因素。
同样,在钻孔工艺中也是如此,下面把钻孔用鱼骨图分列出影响钻孔的因素。
在众多影响钻孔加工阶段,施于各项不同的检验方法.4.3钻孔常见不良问题,原因分析和改善方法钻孔前基板检验:A、品名、编号、规格、尺寸、铜铂厚B、不刮伤C、不弯曲、不变形D、不氧化或受油污染E、数量F、无凹凸、分层剥落及折皱(2)、钻孔中操作员自主检验1.钻孔品质检验项目有A、孔径B、批锋C、深度是否贯穿D、是否有爆孔E、核对偏孔、孔变形F、多孔少孔G、毛刺H、是否有堵孔J、断刀漏孔K、整板移位2.断钻咀产生原因:(1)主轴偏转过度(2)数控钻机钻孔时操作不当(3)钻咀选用不合适(4)钻头的转速不足,进刀速率太大(5)叠板层数太多(6)板与板间或盖板下有杂物(7)钻孔时主轴的深度太深造成钻咀排屑不良发生绞死(8)钻咀的研磨次数过多或超寿命使用。
(9)盖板划伤折皱、垫板弯曲不平(10)固定基板时胶带贴的太宽或是盖板铝片、板材太小(11)进刀速度太快造成挤压所致(12)特别是补孔时操作不(13)盖板铝片下严重堵灰(14)焊接钻咀尖的中心度与钻咀柄中心有偏差解决方法:(1)应该通知机修对主轴进行检修,或者更换好的主轴。
(2)A、检查压力脚气管道是否有堵塞B、根据钻咀状态调整压力脚的压力,检查压力脚压紧时的压力数据,正常为7.5公斤。
C、检查主轴转速变异情况及夹嘴内是否有铜丝影响转速的均匀性。
D、钻孔操作进行时检测主轴转速变化情况及主轴的稳定性。
(可以作主轴与主轴之间对比)E、认真调整压力脚与钻头之间的状态,钻咀尖不可露出压脚,只允许钻尖在压脚内3.0mm处F、检测钻孔台面的平行度和3、孔损产生原因:(1)断钻咀后取钻咀造成(2)钻孔时没有铝片或夹反底版(3)参数错误(4)钻咀拉长(5)钻咀的有效长度不能满足钻孔叠板厚度需要(6)手钻孔(7)板材特殊,批锋造成解决方法:(1)根据前面问题1,进行排查断刀原因,作出正确的处理(2)铝片和底版都起到保护孔环作用,生产时一定要用,可用与不可用底版分开方向统一放置,上板前在检查一次。
(3)钻孔前,必须检查钻孔深度是否符合,每支钻咀的参数是否设置正确。
(4)钻机抓起钻咀,检查清楚钻咀所夹的位置是否正确再开机,开机时钻咀一般不可以超出压脚。
(5)在钻咀上机前进行目测钻咀有效长度,并且可用生产板的叠数进行测量检查。
(6)手动钻孔切割精准度、转速等不能达到要求,禁止用人手钻孔。
(7)在钻特殊板设置参数时,根据品质情况进行适当选取参数,进刀不宜太快。
4.孔位偏、移,对位失准产生原因:(1)钻孔过程中钻头产生偏移(2)盖板材料选择不当,软硬不适(3)基材产生涨缩而造成孔位偏(4)所使用的配合定位工具使用不当(5)钻孔时压脚设置不当,撞到销钉使生产板在产生移动(6)钻头运行过程中产生共振(7)弹簧夹头不干净或损坏(8)生产板、面板偏孔位或整叠位偏移(9)钻头在运行接触盖板时产生滑动(10)盖板铝片表面划痕或折痕,在引导钻咀下钻时产生偏差。
(11)没有打销钉(12)原点不同(13)胶纸未贴牢(14)钻孔机的X、Y轴出现移动偏差(15)程序有问题解决方法(1)A、检查主轴是否偏转B、减少叠板数量,通常按照双面板叠层数量为钻头直径的6倍而多层板叠层数量为钻头直径的2~3倍。
C、增加钻咀转速或降低进刀速率;D、检查钻咀是否符合工艺要求,否则重新刃磨;E、检查钻咀顶尖与钻咀柄是否具备良好同中心度;F、检查钻头与弹簧夹头之间的固定状态是否紧固;G、检测和校正钻孔工作台板的稳定和稳定性。
(2)选择高密度0.50mm的石灰盖板或者更换复合盖板材料(上下两层是厚度0.06mm的铝合金箔,中间是纤维芯,总厚度为0.35mm)。
(3)根据板材的特性,钻孔前或钻孔后进行烤板处理(一般是145℃±5℃,烘烤4小时为准)(4)检查或检测工具孔尺寸精度及上定位销的位置是否有偏移。
(5)检查重新设置压脚高度,正常压脚高度距板面还有0.80mm为钻孔最佳压脚高度(6)选择合适的钻头转速。
(7)清洗或更换好的弹簧夹头。
(8)面板未装入销钉,管制板的销钉太低或松动,需要重新定位更换销钉(9)选择合适的进刀速率或选抗折强度更好的钻头。
(10)更换表面平整无折痕的盖板铝片(11)按要求进行钉板作业(12)记录并核实原点(13)将胶纸贴与板边成90度直角,(14)反馈通知机修调试维修钻机(15)查看核实,通知工程进行修改5、孔大、孔小、孔径异形产生原因:(1)钻咀规格错误(2)进刀速度或转速不恰当所致(3)钻咀过度磨损(4)钻咀重磨次数过多或退屑槽长度底低于标准规定。
(5)主轴本身过度偏转。
(6)钻咀崩尖,钻孔孔径变大(7)看错孔径(8)换钻咀时未测孔径(9)钻咀排列错误(10)换钻咀时位置插错(11)未核对孔径图(12)主轴放不下刀,造成压刀(13)参数中输错序号解决方法(1)操作前应进行检查钻头尺寸及控制系统是否指令发生错误。
(2)调整进刀速率和转速至最理想状态(3)更换钻咀,并限制每支钻咀钻孔数量。
通常按照双面板(每叠四块)可钻3000~3500孔;高密度多层板上可钻500个孔;对于FR-4(每叠三块)可钻3000个孔;而对较硬的FR-5,平均减小30%。
(4)限制钻头重磨的次数及重磨尺寸变化。
对于钻多层板每钻500孔刃磨一次,允许刃磨2~3次;每钻1000孔可刃磨一次;对于双面板每钻3000孔,刃磨一次,然后钻2500孔;再刃磨一次钻2000孔。
钻头适时重磨,可增加钻头重磨次数及增加钻头寿命。
通过工具显微镜测量,在两条主切削刃全长内磨损深度应小于0.2mm。
重磨时要磨去0.25mm。
定柄钻头可重磨3次;铲形钻头重磨2次。
(5)反馈给维修进行动态偏转测试仪检查主轴运行过程的偏转情况,严重时由专业的供应商进行修理。
(6)钻孔前用20倍镜检查刀面,将不良钻咀刃磨或者报废处理(7)多次核对、测量(8)在更换钻咀时可以测量所换下钻咀,对已更换钻咀进行测量所钻第一个孔(9)排列钻咀时要数清楚刀库位置(10)更换钻咀时看清楚序号(11)在备刀时要逐一核对孔径图的实际孔径(12)清洗夹咀,造成压刀后要仔细测量及检查刀面情况(13)在输入刀具序号时要反复检查6、漏钻孔产生原因:(1)断钻咀(标识不清)(2)中途暂停(3)程序上错误(4)人为无意删除程序(5)钻机读取资料时漏读取解决方法:(1)对断钻板单独处理,分开逐一检查(2)在中途暂停后再次开机,要将其倒退1-2个孔继续钻孔(3)判定是工程程序上错误要立即通知工程更改(4)在操作过程中,操作员尽量不要随意更改或删除程序,必要时通知工程处理(5)在经过CAM读取文件后,换机生产,通知机修处理7、披锋产生原因:(1)参数错误(2)钻咀磨损严重,刀刃不锋利(3)底板密度不够(4)基板与基板、基板与底板间有杂物(5)基板弯曲变型形成空隙(6)未加盖板(7)板材材质特殊解决方法:(1)在设置参数时,严格按参数表执行,并且设置完后进行检查核实。
(2)在钻孔时,控制钻咀寿命,按寿命表设置不可超寿命使用(3)对底板进行密度测试(4)钉板时清理基板间杂物,对多层板叠板时用碎布进行板面清理。
(5)基板变形应该进行压板,减少板间空隙(6)盖板是起保护和导钻作用。
因此,钻孔时必须加铝片。
(对于未透不可加铝片钻孔)(7)在钻特殊板设置参数时,根据品质情况进行适当选取参数,进刀不宜太快。
8、孔未钻透(未贯穿基板)产生原因:(1)深度不当(2)钻咀长度不够(3)台板不平(4)垫板厚度不均(5)断刀或钻咀断半截,孔未透(6)批锋入孔沉铜后成形成未透(7)主轴夹嘴松动,在钻孔过程中钻咀被压短(8)未夹底板(9)做首板或补孔时加两张垫板,生产时没更改解决方法:(1)检查深度是否正确.<分总深度和各个主轴深度>(2)测量钻咀长度是否够.(3)检查台板是否平整,进行调整(4)测量垫板厚度是否一致,反馈并更换垫板(5)定位重新补钻孔(6)对批锋来源按前面进行清查排除,对批锋进行打磨处理(7)对主轴松动进行调整,清洗或者更换索嘴。