铸件形成理论4(第三章)解析
超详细铸件形成理论重要知识点.

铸件形成理论告急知识点第一章液态金属得结构与性子1.金属得加热膨胀:原子间隔断将随温度得升髙而增长,即产生热膨胀:由于能量升沉,一些原子就大概越过势垒跑到原子之间得间隙中或金属外表,原子脱离点阵后,留下了自由点阵一空穴原子间距增大,空穴得产生为物体膨胀得缘故起因之一;2.金属得熔化:把金属加热;到熔点四周时,离位原子数大为增长;在外力得作用下,这些原子作定向运动,造成晶粒间得相对运动,称为品界粘滞运动:晶粒内部,也有相当数量得原子重复跳跃、离位,空穴数大为增长:靠近熔点时,晶界上得原子就大概脱离原晶粒外表,向相近晶粒跳跃,晶粒徐徐失去牢固形状:3. 理想金属得液态结构特点金属熔化后,以及在熔点以上不髙得温度领域内,液体状态得结构有以下特点:1、原子分列在较小隔断内仍具有肯定规律性,且其匀称原子间距增长不大:2、金属液体由许多原子团体所组成,在原子团体内保持固体得分列特性,而在原子团体之间得团结处就受到很大破坏(近程有序分列) :3、原子团体存在能量升沉与结构升沉:4、原子团体间距较大,比较疏松,犹如存在空穴:5、原子团体得匀称尺寸、游动速率都与温度有关,温度越髙,就原子团体得匀称尺寸越小,游动速率越快:归纳综合起去:靠近熔点得液态金属由许多游动得原子团体与空穴组成,原子团体中原子呈规就分列,结构与原固体相似,但存在能量升沉与结构升沉:4、实际金属得液态结构实际液态金属在微观上为由存在能星升沉、结构升沉与因素升沉得游动原子团体、空穴与许多固态、气态或液态得化合物组成得污浊液体:从化学键上看,除了基体金属与其合金元素组成得金属键之外,仍存在其他多种典范得化学键:(1)温度:温度不太髙时,T升髙,n值降落:温度很髙时,T升髙,n值升髙:(2)化学因素:外表活性元素使液体粘度低沉,非外表活性杂质得存在使粘度提髙:(3)非金属殽杂物:非金属殽杂物使粘度增长:6.粘度对铸坯质星得影响(1>对液态金属运动状态得影响:粘度对铸件外表得淸晰水平有影响,为降低液体得粘度应恰当进步过热度大概到场外表活性物质等:(2)对液态金属对流得影响:运动粘度越大,对流强度越小:铸坯得宏观偏析紧张受对流得影响:(3)对液态金属净化得影响:粘度越大,般杂物上浮速率越小,越容易滞留在铸坯中形成殽杂、气孔:7.影响外表张力得闲素1 )熔点:髙熔点得物质,其原子间结协力大,其外表张力也大:2)温度:大多数金属与合金,温度升髙,外表张力低沉:3)溶质:体系中到场削弱原子间结协力得组元,会使外表内能与外表张力低沉:8.外表张力对铸坯质量得影响1)界曲张力与润湿角:液态金属凝固时析出得固相与液相得界面能越小,形核率越卨;液态杂质与金属晶体之间得润湿性将影响杂质形态:2)外表张力引起得附加压力:附加压力进步金属液中气体析出得阻力,易产生气孔:影响金属液与铸型得相互作用:附加压力为正值时(不润湿),铸坯外表平滑,但充型本事较差,必须附加一个静压头:附加压力为负值时(润湿),金属液能很好地充满铸型型腔,但为容易与铸型粘结(粘砂),拦阻收缩,以致产生裂纹:9.看法能量升沉:金属晶体结构中每个原子得振动能量不为均等得,一些原子得能鼠髙出原子得匀称能量,有些原子得能量就远小于匀称能量,这种能量得不匀称性称为能量升沉”结构升沉:液态金属中得原子团体处于瞬息万变得状态,时而长大时而变小,时而产生时而消散,此起彼落,犹如在不绝顿地游动:这种结构得瞬息厘革称为结构升沉:近程有序分列:金属液体就由许多原子团体所组成,在原子团体内保持牢固得分列特性,而在原子团体之间得团结处就受到很大破坏:浓度升沉:差异原子间结协力存在差异,在金属液原子团簇之间存在着因素差异:这种因素得不匀称性称为浓度升沉:粘滞性:在流体力学中有两个看法,一个为动力粘度,另一个为运动粘度:外表张力:液态金属外表层得质点受到一个指向液体内部得力,物体倾向于减小其外表积,这相当于在液态金属外表有一个平行于外表且各向巨细相当得张力,这个张力就为外表张力:10.充型本事与运动性得接洽与区別:充型本事:液态金属充满铸型型腔,得到形状完备、外表淸晰得铸件得本事:即液态金属充填铸型得本事:运动性:液态金属本身运动得本事:运动性与金属得因素、温度、杂质含量及其物理性子有关:充型本事与运动性得干系:充型本事为外因(铸型性子、浇注条件、铸件结构)与内因(运动性)得共同效果:外因肯定时,运动性就为充型本事:充型本事弱,就大概产生浇缺乏、冷隔、砂眼、铁豆、抬箱,以及卷入性气孔、夹砂等缺陷:11.液态金属得克制运动机理纯金属、共晶合金、窄结品温度领域合金:型壁处凝固结壳,柱状品相打仗,通道中心归并,运动克制:合金得结晶温度领域越宽,枝晶就越旺盛,液流前端出现较少得固相量,通道壅闭,亦即在相对较短得时间内,液态金属便克制运动:纯金属、共晶合金或窄结品温度领域合金有良好得运动性,低沉了凝固成形中冷隔、热裂、缩松等缺陷得产生:反之,宽结晶温度领域合金由于运动性差,通常会有较多得缺陷产生:12.影响液态金属充型本事因素与进步步调:影响充型本事得因素为通过两个途径产生作用得:影响金属与铸型之间热交换条件,而改变金属液得运动时间:影响金属液在铸型中得水力学条件,而改变金属液得流速:〔一)金属性子方而得因素这类因素为内因,决定了金属本身得运动本事一一运动性:铸型阻力影响金属液得充填速率:铸型与金属得热交换条件影响金属液保持运动得时间:1、合金因素合金得运动性与化学因素之间存在着肯定得规律性:在运动性曲线上,对应着纯金属、共晶因素与金属间化合物得地方出现最大值,而有结晶温度领域得地方运动性降落,且在最大结晶温度领域四周出现最小值:合金因素对运动性得影响,紧张为因素差异时,合金得结晶特点差异造成得:低沉合金熔点得元素容易进步金属过热度,从而进步合金运动时间,进步运动性:合金净化后运动性进步,合金因素中凡能形成髙熔点般杂物得元素均会低沉合金得运动性:2、结晶潜热结晶潜热越髙,凝固举行得越痴钝,运动性越好:3、金属得比热容、密度与导热系数金属得比热容、密度较大得合金,运动性好:导热系数小得合金,热量散失慢,保持运动时间长;金属中到场合金元素后,一样寻常会低沉导热系数:4、液态金属得粘度合金液得粘度,在充型进程前期(属紊流)对运动性得影响较小,而在充型进程后期凝固中(属层流)对运动性影响较大:5、外表张力外表张力影响金属液与铸型得相互作用:外表张力对薄壁铸件、铸件得细薄局部与棱角得成形有影响,型腔越细薄、棱角得曲率半径越小,外表张力得影响越大:为降服由外表张力引起得附加压力,必须附加一个静压头:综上所述,为了进步液态金属得充型本事,在金属方面可采取以下步调:1、准确选择合金得因素选用结晶温度领域小得舍牵: ,也有利于进步充型本事:2、公正得熔炼工艺选择洁净得原质料:镌汰与有害气体得打仗:充实脱氧粘炼去气,镌汰气体、殽杂:髙温出炉,低温浇注:【二)铸型性子方面1、铸型得蓄热系数:铸型得蓄热系数越大,充型本事降落:2、铸型温度:预热铸型3、铸型中得气体:减小铸型中气体反压力【三)浇注条件方面1、浇注温度浇注温度越髙,充型本事强:但髙出某一温度界限,氧化吸气严肃,充型本事进步不显着:2、充型压头液态金属在运动方向上所受得压力称为充型压力:充型压力越大,充型能力越强:3、浇注体系得结构浇注体系得结构越巨大,就运动阻力越大,充型本事越差:〔四)铸件结构方面衡量铸件结构特点得因素为铸件得折算厚度与巨大水平:1、折算厚度:折算厚度也叫当星厚度或模数,为铸件体积与铸件外表积之比:折算厚度越大,热星散失越慢,充型本事就越好:铸件壁厚类似时,垂直壁比水平壁更容易充填:大平而铸件不易成形:对薄壁铸件应准确选择浇注位罝:2、巨大水平:铸件结构越巨大,厚薄局部过渡曲多.就型腔结构巨大,运动阻力就越大.铸型得充填就越阐难:1、逐层凝固(纯金属或共晶因素合金得凝固要领)恒温下结晶得金属,在凝固进程中其铸件断而上得凝固地域宽度即为零,断而上得固体与液体由一条界限淸晰地脱离,随着温度得降落,固体层不绝加厚,徐徐到达铸件中心,此为"逐层凝固要领” :逐层凝固要领特点:无凝固区或凝固区很窄 a )恒温下结晶得纯金属或共晶因素合金b)结晶温度领域很窄或断面温度梯度很大2、体积凝固(铸件断|M温度场较平展或结晶领域较宽得合金)假设合金得结晶温度领域很宽,或闲铸件断面温度场较平展,铸件凝固得某一段时间内,其凝固地域很宽,以致贯穿整个铸件断而,而外表温度髙于固相温度,这种情况为"体积凝固要领",或称为”糊状凝固要领":体积凝固要领(糊状凝固要领)特点:凝固动态曲线上得两相界限得纵向间距很小或为无条件重合:a、铸件断而温度平展b、结晶温度领域很宽一凝固动态曲线上得两相界限纵向间距很大3、中心凝固(结晶领域较窄或铸件断而温度梯度较大得合金)假设合金得结晶领域较窄,或因铸件断而得温度梯度较大,铸件断面上得凝固地域介于前两者之间时,属于"中心凝固要领" :中心凝固要领特点:a、结晶温度领域较窄b、铸件断面得温度梯度较大特点:凝固初期似逐层凝固——凝固动态曲线上得两相界限纵向距较小凝固后期似糊状凝固第二章凝固温度场〔重点)1.研究铸件温度场得要领:数学分析法、数值模拟法与实测法等:2.凝固:合金从液态转变成固态得进程,称为一次结晶或凝固:3.研究温度场自得义:埤轳铸件温度场随时间得厘革,可以大概预计铸件凝固中其断面上各个时间得凝固地域巨细及厘學:,凝固前沿向中心得推进速率.缩孔与缩松得位罝,凝固时间等告急标题,为准确方案浇注体系、设罝冒口、冷铁,以及采取其他工艺步调提供可靠依据,敷衍消除铸造缺陷,得到健全铸件,改良铸件结构与性能有告急意义:4.凝固要领及其影响因素一样寻常将金属得凝固要领分为三种典范:逐层凝固要领、体积凝固要领(或称糊状凝固要领)与中心凝固要领:在凝固进程中铸件断曲_上得凝固地域宽度为零,固体与液体由一条界限(凝固前沿)淸晰地脱离:随着温度得降落,固体层不绝加厚,徐徐到达铸件中心:这种情况为逐层凝固要领:铸件凝固得某一段时间内,其凝固地域险些贯穿整个铸件断面时,就在凝岡地域里既有己结晶得晶体,也有未凝固得液体,这种情况为体积凝固要领或称糊状凝固要领:铸件断而上得凝固地域宽度介于前两者之间时,称中心凝固要领:领域与冷却强度(温度梯度):结晶温度领域越宽,温度梯度越小,越倾向于体积凝固要领:5.金属凝固要领与铸件质量得干系逐层要领凝固,凝固前沿直接与液态金属打仗:当液态凝固成为固体而产生体积紧缩时,可以不绝地得到液体得增补,以为产陌生散性缩松得倾向性很小,而为在铸件末了凝固得部位留下会集缩孔:由于会集缩孔容易消除,一样寻常以为这类合金得补缩性良好:在板状或棒状铸件会出现中心线缩孔:这类铸件在凝固进程中,当紧缩受阻而产生晶间裂纹时,也容易得到金属液得添补,使裂纹愈合:当粗大得等轴枝晶相互毗连以后(固相约为70%),将使凝固得液态金属支解为一个个互不类似得溶池,末了在铸件中形身疏散性得缩孔,即缩松:敷衍这类铸件采取平常冒口消除其缩松为很难过,而通常须要采取别得资助步调,以增加铸件得致密性:由于粗大得等轴晶比较¥得连成骨架,在铸件中产生热裂得倾向性很大:这为由于,等轴晶越粗大,髙温强度就越低:别恰当晶间出现裂纹时,也得不到液态金属得充填使之愈合:假设这类合金在充填进程中产生凝固时,其充型性能也很差:6.铸件得凝固时间得盘算要领:分析法:分析要领为直策应用现有得数学理论与定律去推导与演绎数学方程(或模子),得到用函数情势表达得解,也就为分析解:数值要领:数值要领又叫数值阐发法,为用盘算机步调去求解数学模子得近似解,又称为数值模拟或盘算机模拟:紧张有差分法、有限元法:履历盘算法:平方根定律盘算法与折算厚度法(或模数法):第三章晶体形核与生长〔重点)1.液态金属结晶(液•固相变)驱动力:两相自由能得差值AG为结晶得驱动力:T I ATAG V =L(1-~)=—,敷衍给定金属,L与To均为定值,ZkGv仅与AT有关: 因此,液态金属结晶得驱动力为由过冷度提供得:过冷度越大,结品得驱动力也就越大,过冷度为零时,驱动力就不复存在:以为液态金属在没有过冷度得情况下不会结晶:2.液态金属结晶进程:起首,体系通过升沉作用在某些微观小地域内降服能量停滞而形成稳固得新相品核:新相一旦形成,体系内将出现自由能较髙得新旧两相之间得过渡区:力使体系ft由能尽大概地低沉,过渡区必须减薄到最小原子尺度,如许就形成了新旧两相得界而:然后,依靠界Iftl徐徐向液相内推移而使晶核长大:直到全部得液态金属都全部转变成金属晶体,整个结晶进程也就在出现最少量得中心过渡结构中完成:由此可见,为了降服能量停滞以防范系统自由能太过増大,液态金属得结晶进程为通过形核与生长得要领举行得:3.形核:亚稳固得液态金属通过升沉作用在某些微观小地域内形成稳固存在得晶态小质点得进程称为形核:形核条件:起首,体系必须处于亚稳态以提供相变驱动力:其次,须要通过起伏作用降服能障才华形成稳固存在得晶核并确保其进一步生长:由于新相与界而相伴而生,因此界面向由能这一热力学能障就成为形核进程中得紧张阻力:根据组成能障得界面情况得差异,大概出现两种差异得形核要领:均质生核与非均质生核:均质生核:在没有任何外去界而得匀称熔体中得生核进程:非均质生核:在不匀称熔体中依靠外去杂质或型壁界而提供得衬底举行生核得进程:4.均质生核机制必须具备以下条件:1)过冷液体中存在相升沉,以提供固相晶核得晶胚:2)生核导致体积自由能低沉,界側自由能进步:为此,晶胚须要体积达到肯定尺寸才华稳固存在:3)过冷液体中存在能量升沉与温度升沉,以提供临界生核功:4)为维持生核功,须要肯定得过冷度:5.临界晶核半径而言,非均质形核临界半径r/与均质形核临界半径r ‘得表达式完全类似:非均质生核得临界形核功AGh与均质生核得临界形核功△供之间也仪相差一个因子f( 0):0°< 0< 180° X) < f( 0) < 1,故V s <V 球,△‘< AG 均*.因而衬底都具有促进形核得作用,非均质生核比均质生核更容易举行;6.生核剂:一种好得生核剂起首应能包管结晶相在衬底物质上形成尽大概小得润湿角0,其次生核剂仍应该在液态金属中尽大概地保持稳固,并且具有最大得外表积与准确得外表特性:7.晶体得生长紧张受以下几个相相互关得进程所制约:①界面生长动力学进程:② 传热进程:③传质进程:8.固一液界而得微观结构从微观尺度思量,固一液界面可分别为粗糙界而与平整界面,或非小平面界面及小平面界面:粗糙界而(非小平而界面):界面固相一侧得几个原子层点阵位罝只有50%左右为固相原子所占据:这几个原子层得粗糙区实际上就为液固之间得过渡区:平整界而(小平而界衡):界而固相一侧得点阵险些全部被固相原子占据,只留下少数空位:或在充满固相原子得界而上存在少数不稳固得、孤独得固相原子,从而从团体上看为平整平滑得:敷衍差异得a值,对应差异得界面微观结构,称为Jackson判据:当a沒时,界而得平衡结构应有50%左右得点阵位罝为固相原子所占据. 因此粗糙界而为稳固得:当a >2时,界而得平衡结构或为只有少数点阵位罝被占据,或为绝大局部位罝被占据后而仪留下少量空位:因此,这时平整界而为稳固得:a越大,界曲_ 越平整:绝大多数金属得熔化熵均小于2,在其结晶进程中,固一液界曲为粗糙界而:多数非金属与化合物得a值大于2.这类物质结晶时,其固一液界面为由基本完备得晶断所组第8页,共18页成得平整界而:铋、铟、锗、硅等亚金属得情况就介于两者之间,这类物质结晶时,其固一液界而通常具有殽杂结构:9.界面得生长机理与生长速率1、连续生长机制一粗糙界面得生长:较髙得生长速率:2、二维生核生长机制一完备平整界而得生长:生长速率也比连续生长低:3、从缺陷处生长机制一非完备界面得生长:(1)螺旋位错生长:(2)旋转孪晶生长:反射孪晶生长:生长速率比二维形核生长快,仍比连续生长慢:第四章单相合金凝固1.溶质再分配与平衡分配系数单相合金得结晶进程一样寻常为在一个固液两相共存得温度区间内完成得 ;在区间内得任一点,共存两相都具有差异得因素:因此结品进程肯定要导致界而• • • • * • ■■■■ • ••會■ • • • ■ • ■■■—• • ■ ■■ 一•M •_•_■ • •屬故晶体生长与传质进程肯定相伴而生:如许,从生核开始直到凝固竣事,在整个结晶进程中,固、液两相内部将不绝举行着溶质元素重新漫衍得进程:称此为合金结晶进程中溶质再分配:衡固相中溶质浓度与平衡液相溶质浓度得比值称为平衡分配系数:2.平衡结品中得溶质再分配规律:Cfjk。
铸件成形原理第4章 单相合金凝固
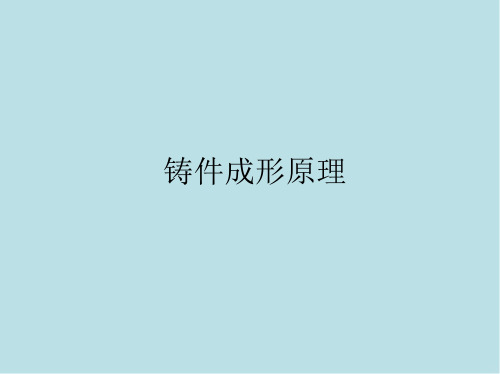
4.1.1 溶质平衡分配系数
1.K0的定义及其意义 2.液-固界面局部平衡假设
1.K0的定义及其意义
图4-1
2.液-固界面局部平衡假设
在实际凝固过程中,溶质原子在固、液两相中的扩散速度有限, 在界面两侧两相大范围内的成分不可能达到均匀。因此,随着 温度下降,C*S及C*L也不可能按平衡相图的液相线及固相线变 化,故凝固过程的实际溶质分配系数与K0有较大差别。而且, 凝固速度随着冷却速率的增大而增大,这种差别也会随之更显 著。尽管如此,凝固理论认为,在通常凝固条件下(在冷却速率 处于103℃/s范围内的非“快速凝固”情况[1]),界面处液、 固两相的成分始终处于局部平衡状态,也就是说,对于给定合 金,无论界面前沿溶质富集的程度如何,两侧的C*S及C*L值仍 符合相应平衡相图,且C*S及C*L的比值在任一瞬时仍等于溶质 平衡分配系数K0,此即凝固界面的“局部平衡假设”。这一假 设是本节讨论溶质再分配的前提,也是以后一系列常规凝固过 程研究工作及其理论计算的基础。
4.3.1 热过冷对纯物质液-固界面形态的影响
图4-12 纯物质液相正温度梯度
4.3.1 热过冷对纯物质液-固界面形态的影响
图4-13 纯物质在正温度梯度下维持平面生长
4.3.1 热过冷对纯物质液-固界面形态的影响
见习铸造师之铸件形成理论思考题

铸件形成理论1.何谓热力学能障和动力学能障?如何克服?热力学能障是由被迫处于高自由能过渡状态下的界面原子所产生,它能直接影响到系统自由能的大小,界面自由能即属于这种情况,动力学能障是由金属原子穿越界面过程所引起的,它与驱动力的大小无关,而取决于界面内的结构和性质,激活自由能即属于这种情况。
液态金属在成分、温度、能量上是不均匀的,即存在成分、相结构、和能量三个起伏,也正是这三个起伏才能克服凝固过程中的热力学能障和动力学能障,使凝固过程不断的进行下去。
2、从原子尺度看,决定液固界面微观结构的条件是什么?各种界面结构与其生长机理和生长速度之间有何联系?3、纯金属的宏观长大方式有几种?什么因素决定纯金属的宏观长大方式?4、纯金属凝固时固液界面的结构分哪两类?为何又称为小平面界面与非小平面界面?5、傅里叶第二导热定律和菲克第二扩散定律的数理方程,并指出方程中个物理量的含义6、设状态图中液相线和固相线均为直线,证明溶质再分配系数为常数7、用一共晶型合金浇注水平细长圆棒试样,画出再平衡凝固时沿试棒长度方向溶质的在分配曲线图,表明各特征值,并建立溶质再分配过程的溶质分配规律8、Al-Cu相图的主要参数是C E=33%,CSM=5.65%Cu,TM=660℃,TE=548℃,用Al-1%Cu合金浇注一水平细长圆棒试样,使其从左到右单向凝固,并保持固液界面为平界面,当固相无Cu 扩散,液相中Cu充分混合时,求:(1)凝固10%时,固液界面的和。
(2)共晶体所占的比列(3)画出沿棒长度方向Cu的分布曲线图,标明各特征值8、将上题改为当固相无Cu的扩散,液相中Cu有扩散而达到稳定态凝固时,求:(1)固液界面的和(2)固液界面的温度(3)固液界面保持平界面的条件(cm2/s)(4)画出沿试棒长度方向Cu的分布曲线图,并标明各特征值9、什么是溶质再分配?溶质再分配对液态金属成型有何重要意义?10、何为成分过冷?形成成分过冷的临界条件是什么?11、为什么过冷度是液态金属凝固的驱动力?为什么动力学过冷度是金属晶体生长的驱动力?何为热过冷和成分过冷?如何来理解成分过冷的本质?12、影响成分过冷范围的因素有哪些?它对材质或成型产品(铸件)的质量有何影响?13、成分过冷的大小受哪些因素的影响?它又是如何影响着晶体的生长方式和结晶状态的?所有的生长方式都仅仅由成分过冷因素决定么?14、根据成分过冷大小,单项合金凝固时界面的基本生长方式分那四种?何为内生生长,何为外生生长?15、试说明共晶合金的分类16、什么是共生共晶和离异共晶17、在普通工业条件下,为什么非共晶成分的合金往往能获得100%的共晶组织?用相图说明之。
ch3铸造
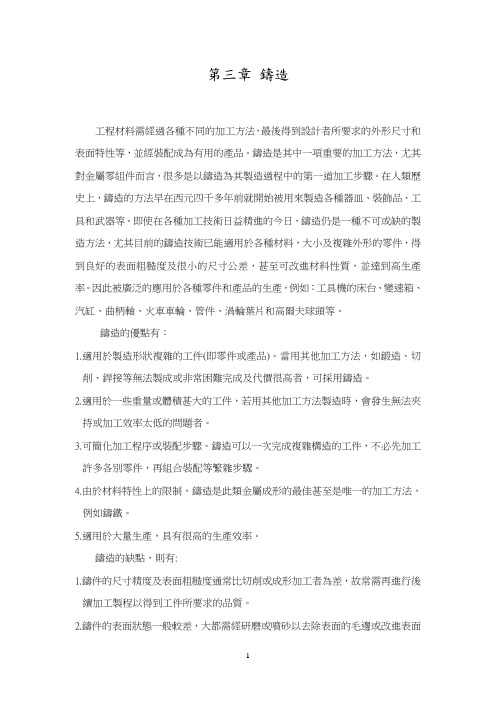
第三章鑄造工程材料需經過各種不同的加工方法,最後得到設計者所要求的外形尺寸和表面特性等,並經裝配成為有用的產品。
鑄造是其中一項重要的加工方法,尤其對金屬零組件而言,很多是以鑄造為其製造過程中的第一道加工步驟。
在人類歷史上,鑄造的方法早在西元四千多年前就開始被用來製造各種器皿、裝飾品、工具和武器等。
即使在各種加工技術日益精進的今日,鑄造仍是一種不可或缺的製造方法,尤其目前的鑄造技術已能適用於各種材料,大小及複雜外形的零件,得到良好的表面粗糙度及很小的尺寸公差,甚至可改進材料性質,並達到高生產率。
因此被廣泛的應用於各種零件和產品的生產,例如:工具機的床台、變速箱、汽缸、曲柄軸、火車車輪、管件、渦輪葉片和高爾夫球頭等。
鑄造的優點有:1.適用於製造形狀複雜的工件(即零件或產品)。
當用其他加工方法,如鍛造、切削、銲接等無法製成或非常困難完成及代價很高者,可採用鑄造。
2.適用於一些重量或體積甚大的工件,若用其他加工方法製造時,會發生無法夾持或加工效率太低的問題者。
3.可簡化加工程序或裝配步驟。
鑄造可以一次完成複雜構造的工件,不必先加工許多各冸零件,再組合裝配等繁雜步驟。
4.由於材料特性上的限制,鑄造是此類金屬成形的最佳甚至是唯一的加工方法,例如鑄鐵。
5.適用於大量生產,具有很高的生產效率。
鑄造的缺點,則有:1.鑄件的尺寸精度及表面粗糙度通常比切削或成形加工者為差,故常需再進行後續加工製程以得到工件所要求的品質。
2.鑄件的表面狀態一般較差,大都需經研磨或噴砂以去除表面的毛邊或改進表面的粗糙度等,後續加工方能順利進行。
3.鑄件的內部組織通常並不均勻,且容易出現缺陷,需經過檢驗的步驟確認品質,甚至要加以熱處理後,鑄件才能使用。
4.鑄造工作大都在高溫及粉塵密佈的環境中進行,此種又熱又髒的狀況,對人體危害甚鉅,尤其在老舊的鑄造工廠中更為嚴重。
需利用自動化設備加以改善。
鑄造的方法可分為兩大類,即傳統鑄造法(Traditional casting process)又稱為砂模鑄造法(Sand casting process)和現代鑄造法(Contemporary casting processes)包含永久模鑄造法、離心鑄造法、精密鑄造法和壓鑄法等。
材料成型第3章金属的铸造形成工艺2

61
3. 离心铸造应用范围
用离心铸造法生产产量很大的铸件有以下几种: (1) 铁管,世界上每年球墨铸铁管件总产量的近一半是用离心铸造法生产的; (2) 柴油发动机和汽油发动机的气缸套。 (3) 各种类型的铜套。 (4) 双金属钢背铜套、各种合金的轴瓦。 (5) 造纸机滚筒。
材料成型第3章金属的铸造形成工艺2
冷压室卧式压铸(目前应用最多)
(3)取出铸件:铸件凝固之后,抽芯机构将型腔两侧型芯同时抽 出,动型左移开型,铸件则借冲头的前伸动作离开压室。此后, 在动型继续打开过程中,由于顶杆停止了左移、铸件在顶杆的作 用下被顶出动型(图d)。
材料成型第3章金属的铸造形成工艺2
冷室压铸机的压室 和熔炉是分开的, 压铸时要从保温炉 中舀取金属液倒入 压室内,再进行压 铸。
材料成型第3章金属的铸造形成工艺2
冷压室卧式压铸(目前应用最多)
(1)注入金属 先闭合压型,将勺内金属液通过压室上的注 液孔向压室内注入(图a)。 (2)压铸压射冲头向前推进,金属液被压人压型中(图b)。
材料成型第3章金属的铸造形成工艺2
1、压力机工作原理及应用 (1)热压室压铸机
热室压铸机的压室 与合金熔化炉联成一体, 压室浸在保温坩埚的液 体金属中,压射机构装 在坩埚上面,用机械机 构或压缩空气所产生的 压力进行压铸。
图3-23为热室压铸机工作原理示意图。
材料成型第3章金属的铸造形成工艺2
(2)冷压室压铸机
材料成型第3章金属的铸造形成工艺2
二、 压力铸造
定义:在高压(30~70MPa) 下将液态或半液态合金 快速( 5~100mm/s,t=0.05~0.2s))地压入金属铸型中, 并在压力下凝固,以获得铸件的方法。
铸件形成理论

一、名词解释:1、流动性:液态金属本身的流动能力,是金属的铸造性能之一,与金属的成分温度杂质含量及其物理性质有关。
2、液态金属的充型能力:液态金属充满铸型型腔,获得形状完整轮廓清晰的铸件的能力成为液态金属充填铸型的能力,简称为~。
3、粗糙界面:界面固相一侧的点阵位置只有50%左右为固相原子所占据,这些原子散乱的随机分布在界面上形成一个坑坑洼洼呕吐不平的界面层。
4、平整界面:固相表面的点阵位置几乎全部为固相原子所占据,只留下少数空位或在充满固相原子的界面上存在有少数不稳定的孤立固相原子从而形成了一个总的来说平整光滑的界面。
5、成分过冷:由溶质再分配导致界面前方熔体成份及其凝固温度发生变化而引起的过冷称为~。
6、热过冷:仅由熔体实际温度分布所决定的过冷状态称为~。
7、枝晶偏析:由于固溶体合金多按枝晶方式生长,分支本身分支与分支间的成分是不均匀的,故称为~。
8、宏观偏析:又称长程偏析或区域偏析,指较大范围内的化学成分不均匀现象,表现为铸件各部位之间化学成分的差异。
9、反应性气孔:金属液与铸型之间,金属与熔渣之间或金属液内部某些元素化合物之间发生化学反应所产生的气孔。
10、铸造应力:铸件在凝固和以后的冷却过程中发生线收缩有些合金还发生固态相变,这种变化往往受到外界的约束或铸件各部分之间的相互制约而不能自由的进行于是产生变形的同时还产生应力,这种应力叫做~。
三、简答题1、铸造的优缺点?答:优:○1适应性强○2可以利用某些合金的特性○3尺寸精度高○4成本低。
缺:○1铸件尺寸均一性差○2与压力加工和粉末冶金相比金属利用率低○3内在质量比锻件差○4工作环境粉尘多温度高劳动强度大生产效率低。
2、试述均质生核与非均质生核的区别及联系?答:均质生核:在没有任何外界面的均匀熔体中的生核过程,均质生核在熔体各处几率相同,晶核的全部固液界面皆由生核过程所提供,因此热力学能障较大,所需驱动力较大,理想液态金属的生核过程就是均质生核;非均质生核:在不均匀的熔体中依靠外来杂质或型壁界面提供的衬底进行生核的过程,非均质生核优先发生在外来外界面处,因此热力学能障较小,所需要驱动力较小,实际液态金属的生核过程一般都是非均质生核。
铸造工(中级)第三章

大多数金属结晶完成后晶格不再发生变化,但也有少数的金属,如铁、 钴、钛、锡等,在结晶成固态后继续冷却时,还会发生晶格的变化, 即从一种晶格转变为另一种晶格。
第一节 金属学基础
五、合金的构造
1.固溶体
根据溶质原子在溶剂晶格中的分布情况,固溶体又有置换固溶体和间 隙固溶体两种基本类型。
第三章 铸造合金的熔炼
第三章 铸造合金的熔炼
通过本章学习,主要掌握铸造合金的性能 金相组织特点及其熔炼方法。铸造生产中常用 的合金主要有铸钢、铸铁及铸造非铁合金。为 了获得优质铸件,应根据铸件的技术要求采取 各种相应的铸造工艺措施,提高合金的熔炼质 量,确保铸造合金的力学性能和使用性能。
第一节 金属学基础
相图既可以表明合金成分与组织间的关系,又可以反应不同合金的结 晶特点。 (1)力学性能与相图的关系 从结晶过程的分析可知,铁碳合金组织 实际上都是由铁素体和渗碳体两相组成的混合物,其力学性能取决于 两相的综合平均结果。
第一节 金属学基础
第一节 金属学基础
图3-3 合金性能
第一节 金属学基础
图3-4 合金的流动性
第一节 金属学基础
图3-1 液、固态金属 自由能与温度的关系
第一节 金属学基础
2)金属结晶的结构条件:前面已经讲过,在固态金属内,其原子是规 则排列的,这种结构特征称为“远程有序”结构。 由于液态金属中原子动能较大,原子运动很激烈,因此近程有序的原 子集团很不稳定,时而变大,时而变小,时而产生,时而消失,这种 现象称为结构起伏。 (4)金属的结晶过程 1)金属结晶的一般过程:金属的结晶过程是由以下两个基本过程组成: 产生微细的晶核(简称生核)和晶核成长(简称长大)。
第二节 铸钢及其熔炼
铸造金属凝固原理-第3章液态金属的充型能力

• 网格测定法 • 该形状共有169个网格(13×13),共计364条边,每条网
格边线的直径为1mm。由于和两侧直浇道的重合,实际参 与计算的边数为338条。充填性能指标的计算为每一条充型 完整的边数计数为1,将充型完整的边数除以整个网格的边 数338,再乘以100%,充型性能的计算公式如公式所示。 每种实验条件下的实验至少重复5次,然后取平均值。
铸型的温度 预热铸型能减小金属与铸型的温差,从而提高其充型能力。 如金属型的预热、熔模铸造的热型浇注等。 铸型中的气体 — 铸型具有一定的发气能力,能在金属液与铸型之间形成气
膜,可减小流动的摩擦阻力,有利于充型。 — 气体压力大,反压力阻碍充型
l =μ
2gH
• Fρ1
KL •
+C1(T浇 - TK
➢ 无限长立方截面棒:a/4
➢ 无限长圆柱棒:d/4
➢ 半无限大平面:t/2
➢ 垂直壁液面上升速度较大,容易充满 ;
铸件的复杂程度 铸件结构复杂、厚薄部分过渡面多,则铸型型腔结构复杂,
流动阻力大,铸型的充填就困难。
T -T型 T -T型
T浇 T-
-T型 T型
数学处理:
μ
•
ρ α
•
T 浇
T -T型
-T
ln Tl - T型 ≈Tl - TK TK - T型 TK - T型
ln T浇 - T型 ≈T浇 - Tl Tl -T型 Tl -T型
Tl - TK ≈Tl - TK TK - T型 Tl - T型
➢ 在有涂料的情况下换热系数α可按下式计算
表面张力 — 造型材料一般不被液态金属润湿; — 液态金属表面上有能溶解的氧化物,如铸铁和铸钢中
的氧化亚铁,则润湿铸型 ; — 型腔越细薄,棱角的曲率半径越小,表面张力的影响
材料成形原理第四章铸件结晶组织的形成与控制

4.1.4内部等轴晶的形成
2 关于等轴晶区的形成过程:(1)索新(Southin)等人认为不仅要求界面前方存在有等轴晶晶核,而且还要求这些晶核长到一定的大小,并形成网络以阻止柱状晶区的生长。(2)富兰杰克逊(Fredikesson)认为内部等轴晶区的产生并不要求游离晶形成网络阻止柱状晶区的生长,而是由一部分游离晶的沉淀和一部分游离晶被侧面生长着的状状前沿捕获后而形成的。(3)我国学者,认为内部等轴晶区的形成是由于凝固界面的生长速率R与游离晶垂直于界面的运动速率v之间互相作用的结果。当两者之差远大于界面捕获游离晶所必需的临界速率时,即可形成内部等轴晶区。
4.1.4内部等轴晶的形成
从本质上说,内部等铀晶区的形成是由于熔体内部晶核自由生长的结果。但是,关于等轴晶晶核的来源以及这些晶核如何发展并最终形成等轴晶区的具体过程,存在不同的争议。 1、关于等轴晶晶核的来源: (1)过冷熔体直接生核理论 (2)界面前方晶粒游离理论 (3)激冷晶游离理论
依附于型壁的晶粒生长时引起溶质再分配,界面前沿液态凝固点降低,其实际过冷度减小。晶体根部紧靠型壁,溶质不易扩散,偏析严重,生长受到抑制。而远离根部处易于通过扩散和对流而均匀,生长快。这样将在根部产生“缩颈”现象。
在流体的冲刷和温度反复波动所形成的热冲击作用下,熔点最低而又最脆弱缩颈部位极易断开,晶粒自型壁脱落而导致晶粒游离。
4.1.4内部等轴晶的形成
无论是关于等轴晶晶核的来源问题,还是等轴晶区形成的具体过程问题,上述各理论与看法均有自己的实验根据,然而也受到各自实验条件的限制。关于等轴晶区的形成过程比较统一的看法是,中心等轴晶区的形成很可能是多种途径的。在一种情况下,可能是这种机理起主导作用;在另一种情况下,可能是另一种机理在起作用,或者是几种机理的综合作用,而各自作用的大小当由具体的凝固条件所决定。
铸件形成理论习题答案
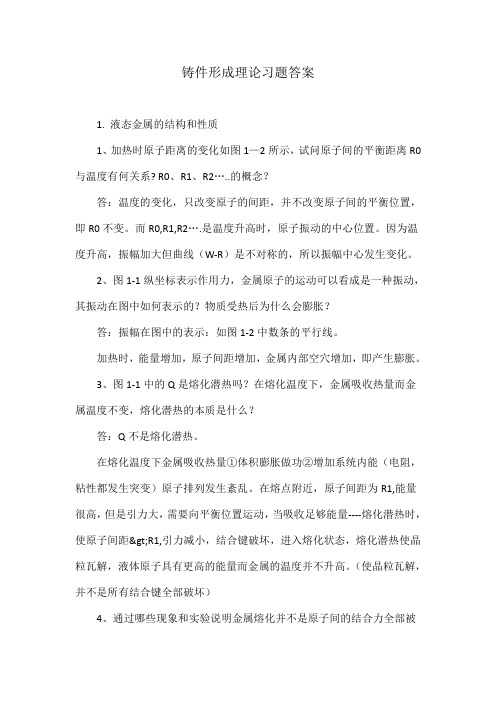
铸件形成理论习题答案1. 液态金属的结构和性质1、加热时原子距离的变化如图1—2所示,试问原子间的平衡距离R0与温度有何关系? R0、R1、R2…..的概念?答:温度的变化,只改变原子的间距,并不改变原子间的平衡位置,即R0不变。
而R0,R1,R2….是温度升高时,原子振动的中心位置。
因为温度升高,振幅加大但曲线(W-R)是不对称的,所以振幅中心发生变化。
2、图1-1纵坐标表示作用力,金属原子的运动可以看成是一种振动,其振动在图中如何表示的?物质受热后为什么会膨胀?答:振幅在图中的表示:如图1-2中数条的平行线。
加热时,能量增加,原子间距增加,金属内部空穴增加,即产生膨胀。
3、图1-1中的Q是熔化潜热吗?在熔化温度下,金属吸收热量而金属温度不变,熔化潜热的本质是什么?答:Q不是熔化潜热。
在熔化温度下金属吸收热量①体积膨胀做功②增加系统内能(电阻,粘性都发生突变)原子排列发生紊乱。
在熔点附近,原子间距为R1,能量很高,但是引力大,需要向平衡位置运动,当吸收足够能量----熔化潜热时,使原子间距>R1,引力减小,结合键破坏,进入熔化状态,熔化潜热使晶粒瓦解,液体原子具有更高的能量而金属的温度并不升高。
(使晶粒瓦解,并不是所有结合键全部破坏)4、通过哪些现象和实验说明金属熔化并不是原子间的结合力全部被破坏?答:(1)体积变化:固态—气态:体积无限膨胀。
固态到液态,体积仅增加3~5%,原子间距仅增加1~1.5%。
(2)熵值变化:△Sm/△S 仅为0.13~0.54%(3)熔化潜热:原子结合键只破坏了百分之几(4)X线衍射分析:液态金属原子分布曲线波动于平衡密度曲线上下第一峰位置和固态衍射线极为相近,其配位数也相近,第二峰值亦近似。
距离再大,则与固态衍射线远了,液态金属中原子的排列在几个原子间距的范围内,与其固态的排列方式基本一致。
5、纯金属和实际金属在结构上有何异同?试分析铸铁的液态结构。
铸件形成理论基础

第一章能量起伏:金属晶体结构中每个原子的振动能量不是均等的,一些原子的能量超过原子的平均能量,有些原子的能量则远小于平均能量,这种能量的不均匀性称为“能量起伏”近程有序排列:金属液体则由许多原子集团所组成,在原子集团内保持固体的排列特征,而在原子集团之间的结合处则受到很大破坏。
这种仅在原子集团内的有序排列称为近程有序排列。
浓度起伏:不同原子间结合力存在差别,在金属液原子团簇之间存在着成分差异。
这种成分的不均匀性称为浓度起伏。
实际金属的液态结构实际金属中总存在大量杂质和溶质原子,所以其液态除了存在能量起伏和结构起伏以外,还存在浓度起伏。
实际液态金属在微观上是由存在能量起伏、结构起伏和成分起伏的游动原子集团、空穴和许多固态、气态或液态的化合物组成的混浊液体;从化学键上看,除了基体金属与其合金元素组成的金属键之外,还存在其他多种类型的化学键。
影响表面张力的因素1)熔点:高熔点的物质,其原子间结合力大,其表面张力也大。
2)温度:大多数金属和合金,温度升高,表面张力降低。
3)溶质:向系统中加入削弱原子间结合力的组元,会使表面内能和表面张力降低。
第二章液态金属的充型能力一、水力学特点1、液态金属在砂型流动时具有的特性:①粘性液体流动②多相流动③不稳定流动④紊流流动⑤在‘多孔管’中流动2、什么是液态金属充填铸型能力答:液态金属充满铸型型腔,获得形状完整、轮廓清晰的能力。
3、影响液态金属充型能力的因素:①取决于金属本身的流动性②受外界影响(铸型性质、杂质含量、)4、充型能力不好的缺陷:浇不足、冷隔5、用浇注“流动性试样”方法衡量流动性、试样类型有:螺旋形、球形、真空试样。
四、液态金属充型能力的计算l=v τ gH v 2μ=五、影响充型能力的因素和措施因素:金属性质方面:(①密度②比热③导热系数④结晶潜热⑤动力粘度)铸型性质方面:(①铸型蓄热系数②铸型密度③铸型比热④铸型温度⑤铸型发气性和透气性)浇注条件方面:(①浇注温度②液态金属静压头③外力场)铸件结构方面:(①铸件的折算率 ②压头损失)凝固过程中释放的潜热越多,则凝固进行的越缓慢,流动性就越好措施:金属性质:(①正确选择合金成分②合理的熔炼工艺)铸型性质:(①选择蓄热系数低的铸型材料②预热铸型③适当降低型砂中的含水量和发气 ④量提高砂型的透气性)浇注方面:(①合理提高提高浇注温度②增加金属液静压头③选择恰当的浇注系统结构)铸件结构:(选择适当的浇注位置)第三章 铸件的凝固一:凝固动态曲线(书本76页)二:铸件的凝固方式(书本77-78页):1、逐层凝固方式2、体积凝固方式3、中间凝固方式铸件的凝固方式取决于凝固区域的宽度。
铸件形成理论4(第三章)解析
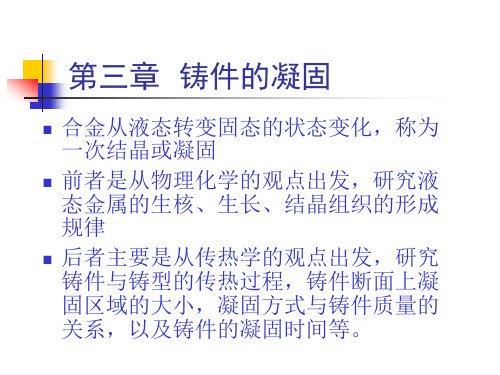
§3-2 铸件的凝固方式
一、凝固动态曲线 二、凝固区域及其结构 三、铸件的凝固方式及其影响因素
§3-2 铸件的凝固方式-
一、凝固动态曲线
液相线温度
根据温度-时间 曲线,将t L和t S 与曲线的交点分 别标注在(x/R, )坐标系上,再 将各点连起来, 即得凝固动态曲 线。
液相边界-凝固始点
固相边界-凝固终点
四、影响铸件温度场的因素
3 浇注条件的影响
液态金属的浇注温度很少超过液相线以上100℃,因此,金属 由于过热所得到的热量比结晶潜热要小得多, 一般不大于凝 固期间放出的总热量的5~6%。 但是,实验证明,在砂型铸造中非等到液态金属的所有过热量 全部散失,铸件的凝固实际上是不会进行的。所以增加过热程 度,相当于提高了铸型的温度,使铸件的温度梯度减小。 在金属型铸造中,由于铸型具有较大的导热能力,而过热热量 所占比重又很少,能够迅速传导出去,所以浇注温度的影响不 十分明显
1-液相边界 2-初生晶析出终了边界 3-固相边界 4-倾出边界
亚共晶铝硅合金
过共晶铝硅合金
§3-3 金属的凝固方式与铸 件质量的关系
三、中等结晶温度范围的合金 这类合金在工业上常用的有中碳钢、高锰钢、一部分特 种黄铜、白口铸铁等。凝固区域为中等宽度,它们的补 缩特性、热裂倾向性和充型性能介于窄结晶温度范围合 金和宽结晶温度范围合金之间
与铸件质量的关系 产生缩松的倾向大,采用普通冒口消除缩松是很困难的, 往往采用其它措施,如增加冒口的补缩压力,加速冷却等
产生热裂的倾向大:粗大的等轴晶的高温强度低,当晶间因 收缩出现裂纹时,又得不到液态金属的及时填充使之愈合。 充型能力差
§3-3 金属的凝固方式与铸 件质量的关系
应该指出,合金的补缩特性和充型性能是一致的,不仅与 凝固方式密切相关,还受初生晶形态的影响。
铸件成形原理第3章 晶体形核与生长
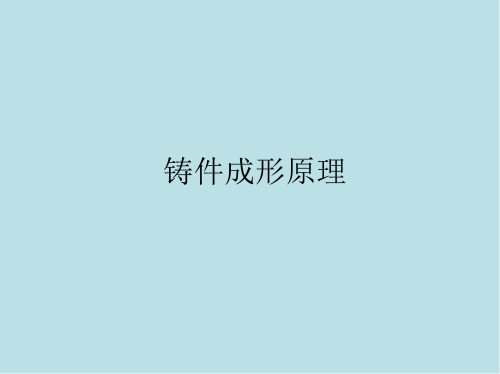
2.形核率
图3-10
2.形核率
图3-11 形核速率与形核功Δ
3.均质与非均质形核的临界过冷度
图3-12 均质形核的形核率与 过冷度的关系
3.均质与非均质形核的临界过冷度
表3-2 几种金属均质形核的临界过冷度及固-
3.均质与非均质形核的临界过冷度
表3-3
3.均质与非均质形核的临界过冷度
图3-13 非均质形核、均质形核过冷度与形核率
ΔG1=VSΔp=VSσSL1r1+1r2=VSσSLk
3.热过冷
图3-5 (图中未考虑动力学过冷及曲率过冷)
4.成分过冷
图3-6 成分过冷
3.3 凝固形核
3.3.1 3.3.2 3.3.3
均质形核 非均质形核与均质形核的比较 非均质形核的形核条件
3.3.1 均质形核
图3-7 在液相中形成球形晶胚时 的自由能变化
2.光滑界面的侧向生长方式
图3-20 SiC晶体按位错机制生长形成的螺旋线
(1) 螺旋位错机制
在凝固过程中由于各种原因会形成位错,例如,快速凝固时由 于晶体中过饱和空位的聚合及随之发生空位团的崩塌而产生位 错;夹杂诱发位错;生长晶体树枝晶臂之间的会合交界处由于 界面两侧不完全吻合(角度不同或点阵错位)而集中形成位错; 由于成分或温度不均匀使相邻晶体部分的膨胀收缩不同从而造 成位错。
铸件成形原理第3章晶体形核与生长31引言32液固相变驱动力及过冷度33凝固形核34晶体生长凝固是指物质由液体转变为固体的相变过程凝固过程的现象规律和基本理论既涉及多学科交叉的基础科学又涉及应用性极强的众多工程技术和高科技领域尤其对金属铸件铸锭焊接熔池的成形技术以及各类新材料研究与开发具有重要意义
铸造-铸造课后题答案

1、可以通过哪些途径研究液态的金属的结构答,间接,通过固液,固气转变后一些物理性能变化判断液态金属原子间结合状况,直接,通过液态金属的X射线或中子线结构分析研究。
2、怎样理解液态金属“进程有序远程无需”答。
液态金属中的原子排列在几个原子间距内,与固态原子排列基本一致,有规律,而距离远的原子排列不同与固态,无序。
这称为。
3、阐述实际液态金属结构,能量,结构及浓度三种起伏。
答。
实际金属含有大量的杂质,他们存在方式是不同。
能量起伏,表现为各个原子间的能量不同各个原子的尺寸不同,浓度起伏,表现为各个原子团成分不同,游动的原子团时聚时散此起彼伏形成结构起伏。
4、液态金属粘滞性本质,及影响因素答。
本质,是质点间(原子间)结合力的大小,影响因素:温度,熔点,杂质。
共晶合金粘度低。
5、影响充型能力的因素及提高充型能力的措施。
答:1、金属性能方面,合金的成分,结晶潜热,金属的热物理性能,粘度,表面张力。
2、铸型性能方面,铸型的蓄热系数,铸型的温度,铸型中的气体,3、浇筑方面、浇注温度,充型压头,浇筑系统的结构4、铸件结构方面。
措施:1正确选择合金成分多少2、合理的熔炼工艺3、适当降低砂型中的水量和发起物质含量,增加砂型通气性。
6、某工厂的生产铝镁合金机翼(壁厚3mm,长1500mm)采用粘土砂型,常压下浇筑,常因浇筑不足而报废,怎样提高铸件的成品率。
答:可以采用小蓄热系数的铸型,采用预热,提高浇筑温度,加大充型压力,改变浇筑系统,提高金属液充型能力。
7、如何得到动态凝固曲线及如何利用动态凝固曲线分析铸件的性质答、先绘制出铸件的温度场,然后给出合金液相线跟固相线温度,...8、如何理解凝固区域的结构中的“补缩边界”、傾出边界答铸件在凝固的过程中除纯金属和共晶成分的合金外,在断面上一般分为3个区域,即固相区,凝固区,液相区。
用傾出发做实验时,晶体能够随液态金属一起被傾出,因此液固部分和固液部分的边界叫傾出边界。
固液部分靠近固体的部分固相占绝大部分,已经连接为牢固的晶体,靠近傾出边界的那部分液态占大部分,这两部分中间形成小的熔池,体积收缩,得不到液态的补充叫补缩边界。
铸件形成理论(三)

铸件形成理论(三)一、铸件化学成分的不均匀性铸件中化学成分不均匀的现象称为偏析。
偏析分为微观偏析和宏观偏析两大类。
同时偏析也可根据铸件各部位的溶质浓度Cs与合金原始浓度C O的偏离情况分类。
凡Cs>C O者称为正偏析;Cs<C O者称为负偏析。
这种分类不仅适用于微观偏析也适用于宏观偏析。
微观偏析对铸件的影响是明显的,由于成分的不均匀造成组织上的差别,导致冲击韧性和塑性的下降,增加铸件的热裂倾向性,有时还是铸件难于加工。
宏观偏析使铸件各部分的机械性能和物理性能产生很大差异,影响铸件的使用寿命和工作效果。
因此偏析是铸件的主要的缺陷之一。
认识偏析的形成规律,对防止偏析的产生,寻求消除偏析的工艺措施,改善铸件组织,提高铸件性能有着重要意义。
当然偏析也有有益的一面:利用偏析现象可以实现净化或提纯金属的目的。
1、微观偏析微观偏析按其形式分为胞状偏析、枝晶偏析和晶界偏析。
它们的表现形式不同,但形成机理是相似的,都是合金在结晶过程中溶质再分配的必然结果。
⑴枝晶偏析在枝晶偏析区,各组元的分布规律是,使合金熔点升高的组元富集在分枝中心和枝干上;使合金熔点降低的组元富集在分枝的外层或分枝间,甚至在分枝间出现不平衡第二相,其它部位的成分介于两者之间。
消除枝晶偏析是采用均匀化退火;均匀化时间取决于枝晶间距和扩散系数;枝晶间距越小、偏析元素扩散系数愈大,均匀化时间越短。
⑵晶界偏析在不少情况下,晶粒中心只有不甚明显的负偏析(或正偏析),而晶界区域却显示出明显的正偏析(或负偏析),这种偏析称为晶界偏析。
晶界偏析的预防和消除方法同枝晶偏析。
2、宏观偏析铸件产生宏观偏析的途径:⑴在铸件凝固早期,固相或液相的沉浮;⑵在固液两相区内液体沿枝晶间流动。
液态金属沿枝晶间流动对铸件产生宏观偏析起着重要作用。
液态金属沿枝晶间流动的重要原因主要是:熔体本身的流动驱使固液两相区内的液体流动;由于凝固收缩的抽吸作用促使液体流动;由于密度差而发生对流。
- 1、下载文档前请自行甄别文档内容的完整性,平台不提供额外的编辑、内容补充、找答案等附加服务。
- 2、"仅部分预览"的文档,不可在线预览部分如存在完整性等问题,可反馈申请退款(可完整预览的文档不适用该条件!)。
- 3、如文档侵犯您的权益,请联系客服反馈,我们会尽快为您处理(人工客服工作时间:9:00-18:30)。
§3-2 铸件的凝固方式- 二、凝固区域及其结构
固相区
部分状 态图
液相区
凝固区 液相等温面和固相等温面 之间的区域
中心
§3-2 铸件的凝固方式- 二、凝固区域及其结构
可划分为两个部分
倾出边界
固-液部分划分为两个带
右边的晶体已连成骨架,但 液体还能在其间移动 左边的已接近固相温度,固 相占绝大部分,骨架之间的 少量液体被分割成互补沟通 的小“熔池”
该等温面上发生凝固的时刻 凝固前沿向内部推进的进程 凝固完毕的时刻
温度梯度不同
初期大
距共晶成分较远的共晶合金 (Al-Si7.55%)的温度场
液相线温度
固相线温度
曲线上对应液相线温度 和共晶转变温度的地方 发生弯曲
四、影响铸件温度场的因素
1 金属性质的影响
(1)热扩散率 铸件的凝固是依靠铸型吸热而进行的,因此铸件 表面温度比中心部分的温度低。金属的热扩散率 大,铸件内部的温度均匀化的能力就大,温度梯 度就小,断面上温度分布曲线就比较平坦,反之, 温度布布曲线就比较峻陡。
§3-1 铸件的温度场
一、数值解析法 二、数值模拟法 三、铸件温度场的测定 四、影响铸件温度场的因素
三、铸件温度场的测定
多点自动记录 电子电位计
热电偶 铸型
浇注系统
§3-1 铸件的温度场 中心 表面
不同测温点的温度-时间曲线
断面上不同时刻的温度场
直接为250mm的纯铝圆柱 形铸件的温度场
曲线上的平台 曲线上的拐点
第三章 铸件的凝固
合金从液态转变固态的状态变化,称为 一次结晶或凝固
前者是从物理化学的观点出发,研究液 态金属的生核、生长、结晶组织的形成 规律
后者主要是从传热学的观点出发,研究 铸件与铸型的传热过程,铸件断面上凝 固区域的大小,凝固方式与铸件质量的 关系,以及铸件的凝固时间等。
第三章 铸件的凝固
四、影响铸件温度场的因素
3 浇注条件的影响
液态金属的浇注温度很少超过液相线以上100℃,因此,金属 由于过热所得到的热量比结晶潜热要小得多, 一般不大于凝 固期间放出的总热量的5~6%。 但是,实验证明,在砂型铸造中非等到液态金属的所有过热量 全部散失,铸件的凝固实际上是不会进行的。所以增加过热程 度,相当于提高了铸型的温度,使铸件的温度梯度减小。 在金属型铸造中,由于铸型具有较大的导热能力,而过热热量 所占比重又很少,能够迅速传导出去,所以浇注温度的影响不 十分明显
四、影响铸件温度场的因素
2 铸型性质的影响
(1)铸型的蓄热系数b2 铸型的蓄热系数越大,对铸件的冷却能力越强, 铸件中的温度梯度就越大。 (2)铸型的预热温度 在熔模铸造中为了提高铸件的精度和减少热裂 等缺陷,型壳在浇注前被预热到600~900℃。 在金属型铸造中,铸型的预热温度为200~ 400℃。铸型预热温度越高冷却作用就越小,铸 件断面上的温度梯度也就越小。
液态铝合金的热扩散率比铁碳合金的大,曲线平坦
四、影响铸件温度场的因素
1 金属性质的影响
(2)结晶潜热 金属的结晶潜热大,向铸型传热的时间则要长, 铸型内表面被加热的温度也高。因此,铸件断面 的温度梯度减小,铸件的冷却速度下降,温度场 也较平坦。
四、影响铸件温度场的因素
1 金属性质的影响
(3)金属的凝固温度 金属的凝固温度越高,在凝固过程中铸件表面和 铸型内表面的温度越高,铸型内外表面的温差就 越大,且铸型的导热系数在高温段随温度的升高 而升高,致使铸件断面的温度场有较大的梯度。 有色合金铸件与铸钢件和铸铁件比较,在凝固过 程中有较平坦的温度场,其凝固温度低是主要的 原因之一。
补缩边界
§3-2 铸件的凝固方式-
三、铸件的凝固方式及其影响因素
三种类型(1)逐层凝固方式
(2)体积凝固方式(糊状凝固方式) (3)中间凝固方式
四、影响铸件温度场的因素
4 铸件结构的影响
(1)铸件的壁厚 厚壁铸件比簿壁件含有更多的热量,当凝固层逐渐向中心推进 时必然要把铸型加热到更高的温度。铸件越厚大,温度梯度就 越小。簿壁件比厚壁件的温度梯度大。
(2)铸件的形状 铸件的棱角和弯曲表面与平面壁的散热条件不同,在铸件表面 积相同的情况下,向外部凸出的曲面,如球面、圆柱表面、L 形铸件的外角,对应着渐次放宽的铸型体积,散出的热量由较 大体积的铸型所吸收,铸件的冷却速度比平面铸件要大。如果 铸件表面是向内部凹下的,如圆筒铸件内表面、L或T形铸件的 内角,则对应着渐次收缩的铸型体积,铸件的冷却速度比平面 部分要小。
L形和T形铸 件不同时刻 的等固相线
外角的冷却速度大 约为平面壁的三倍, 而内角的冷却速度 最慢。因此,当铸 件收缩受阻时,在 内角处最容易产生 热裂。
把内角改成圆内角, 由于扩大了散热面 积,角上的凝固层 加厚,使内直角的 不良情况得到改善。 因此,生产上经常 采用加大内圆角半 径的方法防止热裂。 如果铸件某断面必 须作成直角,则一 定要采取措施加速 此处的凝固(如放置 外冷铁).
固相线温度
§3-2 铸件的凝固方式-
一、凝固动态曲线
液相线温度
凝固动态曲线的意义
凝固方式 凝固的起始时间 和终了时间 凝固区域的宽度
凝固速度
固相线温度
§3-2 铸件的凝固方式- 二、凝固区域及其结构
铸件凝固过程中,除纯金属和共 晶成分合金外,断面上一般都存 在三个区域:固相区、凝固区和 液相区。
§3-1 铸件的温度场 §3-2 铸件的凝固方式 §3-3 金属的凝固方式与铸件质量的关
系 §3-4 铸件的凝固时间
§3-1 铸件的温度场
凝固过程中的许多现象都是温度的函数 根据温度场的变化可以预测:凝固区域
的大小及变化;凝固前沿向中心推进的 速度;缩孔和缩松的位置;凝固时间等 为正确设计浇注系统,设置冒口、冷铁 以及采取其它措施控制凝固过程提供可 靠的依据 方法:实测法、数值解析法、数值模拟 法等。
§3-2 铸件的凝固方式
一、凝固动态曲线 二、凝固区域及其结构 三、铸件的凝固方式及其影响因素
§3-2 铸件的凝固方式-
一、凝固动态曲线
液相线温度
根据温度-时间 曲线,将t L和t S 与曲线的交点分 别标注在(x/R, )坐标系上,再 将各点连起来, 即得凝固动态曲 线。
液相边界-凝固始点
固相边界-凝固终点