组合式机床电气控制设计
-某组合机床的电气控制系统 设计.

输出部分
输出部分
点数
接触器
12
总计
12
注:照明不需要接入PLC,只需要选择开关就可以。
所以选用FX2N―32MR加扩展单元FX2N―32ER,FX2N―32MR含有32个 I/O点(16入,16出),FX2N―32ER为含有32点扩展单元。 下面是电器元件选择。
代号 M1 M2 M3 M4 M5
名称
接触器的线圈通过接110V电压与PLC的输出端和COM端相连。按 钮和开关与输入端和COM端相连。
3.4 元器件选型
首先是PLC的选择。统计组合机床PLC输入元器件、执行元器件及 I/O点数:
输入部分
输入部分 动力头工作方式选择按钮 SB
冷却泵选择开关SA 行程开关SQ 按钮SB 总计
点数
6
2 6 4 18
3.3 I/O分配
图3-5 照明灯
因采用PLC控制,需分配其I/O点,它决定着系统如何工作。
输入地址 号
信号名称
输出地址号 信号名称
X0
左动力头正转
启动按钮
X1
左动力头反转
启动按钮
Y0
M1主轴正转
(KM1)
Y1
M1主轴反转
(KM9)
X2
左动力头停车
Y2
按钮
M3工进正转 (KM3)
X3
左动力头冷却
Y3
成,可靠性高。PLC还配备了自检和监控功能,能自诊断出自身的故 障,并随时显示给操作人员,还能动态的监视控制程序的执行情况,为 现场调试和维护提供了方便。
总之,PLC在性能上均优越于继电接触式控制系统,特别是控制速 度快,可靠性高,设计施工周期短,调试方便,控制逻辑修改方便,而 且体积小,功耗低。
四工位组合机床PLC电气控制系统设计

第一部分设计任务与调研 (1)第二部分设计说明 (4)第三部分设计成果 (13)第四部分结束语 (21)第五部分致谢 (21)第六部分参考文献 (22)第一部分设计任务与调研1、毕业设计的主要任务设计一台由双面钻床、双面铳床组合夹紧放松,在一次半自动循环中,工件经过钻、铳两个工位进行加工,两个工位各完成一道加工工序,在加工而成的较型壳体零件的粗加工为对象的四工位组合机床的PLC电气控制系统。
2、设计的思路、方法设计思路,依托电工实训中心和自动化设备维修实训中心的钻床、铳床、PLC 等实训设备,充分运用所学专业知识和实践技能,详细制定设计方案和阶段进度计划,通过程序设计、模拟调试,建立正确的设讣思路,掌握正确的设计方法,修订完善,设计出能实现铳、钻双面四工位加工系统功能的组合机床PLC电气控制系统。
设计方法,利用文献检索、图书馆借阅、手册查询、设备选型、PLC编程、PLC 实训室程序调试;分析工艺与控制流程、分析控制要求与方式、分析系统设汁的原则和方法、确定PLC输入输出设备和I/O点数及选择PLC机型、硬件系统设计、软件程序设计、绘制控制系统接线图、电器元件的选择、程序调试。
3、本课题相关的资料4、调研的目的和总结4. 1调研的目的起初的组合机床于1911年在美国制成,用于加工汽车零件。
1953年,美国 福特汽车公司和通用汽车公司与美国机床制造厂协商,确定了组合机床通用部件 标准化的原则。
初期,各机床制造厂都有各自的通用部件标准。
为了提高不同制 造厂的通用部件的互换性,便于用户使用和维修。
1973年,国际标准化组织(ISO ) 公布了第一批组合机床通用部件标准。
1975年,中国第一机械工业部颁布了中 国的第一批组合机床通用部件标准。
二十世纪70年代以来,随着可转位刀具、 密齿铳刀、锤孔尺寸自动检测和刀具自动补偿技术的发展,组合机床的加工精度 也有所提高。
铳削平面的平面度可达0. 05毫米/ 1000亳米,表面粗糙度可低达 2. 5〜0.63微米;镇孔精度可达IT7〜6级,孔距精度可达0. 03〜0. 02微米。
组合机床的电气控制系统设计

电气控制与PLC 课程设计说明书题目:某组合机床的电气控制系统设计专业班级:自动1206姓名:陈文浩学号:指导教师:任胜杰1 系统概述组合机床是以通用部件为基础,配以按工件特定形状和加工工艺设计的专用部件和夹具,组成的半自动或自动专用机床。
组合机床一般采用多轴、多刀、多工序、多面或多工位同时加工的方式,生产效率比通用机床高几倍至几十倍。
由于通用部件已经标准化和系列化,可根据需要灵活配置,能缩短设计和制造周期。
因此,组合机床兼有低成本和高效率的优点,在大批、大量生产中得到广泛应用,并可用以组成自动生产线。
组合机床一般用于加工箱体类或特殊形状的零件。
加工时,工件一般不旋转,由刀具的旋转运动和刀具与工件的相对进给运动,来实现钻孔、扩孔、锪孔、铰孔、镗孔、铣削平面、切削内外螺纹以及加工外圆和端面等。
有的组合机床采用车削头夹持工件使之旋转,由刀具作进给运动,也可实现某些回转体类零件(如飞轮、汽车后桥半轴等)的外圆和端面加工。
随着PLC控制技术日益成熟并得到越来越广泛的应用,利用原有的继电器—接触器控制电路设计PLC控制系统,或直接进行PLC控制系统的设计,都能很好地满足组合机床自动化控制的要求。
本次设计的要求如下:##图如图所示为某一组合机床的示意图,左面为1#箱体移动式动力头。
主轴电机M1为、1440转/分钟,1#箱体的进给电机为M3为、1450转/分钟,工进与快进采用电磁铁YV1(DC24V,10W)进行切换;右面为2#箱体移动式动力头。
主轴电机M2为、1440转/分钟,2#箱体的工作进给电机为M4,为、1450转/分钟,工进与快进采用电磁铁YV2(DC24V,10W)进行切换。
SQ1为左动力头的原位限位,SQ3为左动力头的快进限位,SQ5为左动力头的工进限位,SQ2为右动力头的原位限位,SQ4为右动力头的快进限位,SQ6为右动力头的工进限位,具体要求如下:1.左、右两动力头均要求快进→工进→快退的工作循环。
组合镗床的电气控制线路设计探讨

组合镗床的电气控制线路设计探讨组合镗床是一种先进的机床,可以完成钻、铣、镗等多种加工工艺,拥有较高的加工精度和效率,广泛应用于制造业。
其中,电气控制系统是组合镗床的重要组成部分,它不仅关乎整个机床的稳定性和可靠性,还影响到加工质量、效率和安全。
本文将探讨组合镗床的电气控制线路设计及其相关问题。
1. 电气控制系统的组成组合镗床的电气控制系统主要由以下几部分组成:(1)主控制系统:由数控装置、伺服驱动器、编码器、 PLC等组成,负责控制整个机床的加工运行和动作精度。
(2)机床操作面板:由触摸屏或按键、指示灯、紧急停止按钮等组成,负责人机交互和调整机床参数。
(3)电气控制柜:包括主控制器、运动控制卡、开关电源、变频器、抗干扰滤波器、继电器等电气元件,负责将电气信号转化为机械运动。
(4)电动驱动设备:主要包括电机、减速器、传动装置等,负责提供动力和传递力量。
(5)电路保护和安全保护设备:包括断路器、熔断器、漏电保护器、接地保护器、安全门、安全光幕等,负责保护人员和设备的安全。
2. 电气控制线路设计(1)主控制系统的设计主控制系统是组合镗床的“大脑”,它的设计关键在于选型和配合。
首先要选择性能稳定、操作简单、功能强大的数控装置,如常见的数控系统有FANUC、Siemens、Mitsubishi等。
其次,要根据不同的加工需求选配合适的伺服驱动器和编码器,保证机床的位置控制和运动精度。
最后,根据加工工件的不同形状和要求,编写相应的控制程序并进行调试和优化。
(2)电气控制柜的设计电气控制柜是机床电气控制系统的核心部分,它需要满足以下几个设计要点:①电气元件选型:选用具有高性能、低噪声、耐腐蚀性等特点的电气元件,如开关电源、继电器、接触器等,并根据实际负载来选定电气元件的额定电流和电压。
②电气布线设计:布线需要考虑电气安全和实用性,应避免电缆搭绕、交叉等情况,合理规划布线路径和接线方式,并对布线进行标识和保护。
③电气运行与调试:在电气控制柜内部的布线完成后,组合镗床的电气工程师需要进行电气调试和运行测试,以验证电气控制系统的性能和可靠性。
组合机床的电气控制

第六节组合机床的电气控制组合机床是针对特定工件,采用多刀、多面、多工序、多工位同时加工,是由通用部件和专用部件组成的具有工作自动循环功能的高效率专用机床。
它的动力部件采用电动机驱动或采用液压系统驱动,电气控制线路是将各个部件的工作组合成一个统一的循环系统,是典型的机电或机电液一体化的自动化加工设备。
组合机床的通用部件有:动力部件,如动力头和动力滑台;支承部件,如滑座、床身、立柱和中间底座;输送部件,如回转分度工作台,回转鼓轮、自动线工作回转台及零件输送装置;控制部件,如液压元件、控制板、按钮台及电气挡板;其它部件,如机械扳手、排屑装置和润滑装置等。
通用部件已标准化、系列化和通用化。
一、组合机床的主要结构及运动形式双面钻孔组合机床用于在工件两相对表面上钻孔,机床的结构简图如图所示。
1-侧底座2-刀具电动机3-工件及定位夹位夹紧装置4-主轴箱及钻头5-动力滑台机床由动力滑台提供进给运动,电动机拖动主轴箱的刀具主轴提供切削主运动。
两液压动力滑台对面布置,安装在标准侧底座上,刀具电动机固定在滑台上,中间底座上装有工件定位夹紧装置。
机床工作的自动循环过程如图3-14a所示。
工作时,工件装入夹具(定夹位夹紧装置),按动起动按钮SB6,开始工件的定位和夹紧,然后两面的动力滑台同时进行快速进给,工作进给和快速退回的加工循环,同时刀具电动机也起动工作,冷却泵在工进过程中提供切削液,加工循环结束后,动力滑台退回到原位,夹具松开并拔出定位销,一次加工的工作循环结束。
二、组合机床的拖动特点及控制要求1)机床的动力滑台和工件的定位夹紧装置均由液压系统驱动,定位夹紧装置的动作由定位销液压缸和夹紧液压缸完成,三位四通电磁换向阀控制液压缸活塞运动方向的切换。
电磁阀线圈YV5-1与YV5-2控制定位销液压缸活塞运动方向,YV1-1与YV1-2控制夹紧液压缸活塞运动方向,YV2-1、YV2-2,YV4-1为左机滑台油路中电磁换向阀线圈,YV3-1、YV3-2,YV6-1为右机滑台油路中电磁换向阀线圈,各工步电磁阀线圈通电状态如表3-4所示。
组合机床电气控制课程设计

目录第一章绪论 (1)第二章设计方案 (3)2.1 左、右两动力头进给电机 (3)2.2电动机控制电路 (3)2.3液压泵电动机 (4)2.4液压动力滑台控制 (4)2.5主电路及照明电路 (6)2.6保护与调整环节 (6)2.7继电器电气原理简图 (8)第三章I/O分配表 (10)第四章组合机床电气控制电路图 (11)第五章课程设计的具体内容 (12)5.1单循环自动工作 (12)5.1.1单循环自动工作循环图 (12)5.1.2单循环自动工作功能表 (12)5.1.3单循环自动工作梯形图 (12)5.2左铣单循环工作 (13)5.2.1左铣单循环功能表 (13)5.2.2左铣单循环梯形图 (13)5.3右铣单循环工作梯形图 (13)5.4公用程序 (13)5.5回原位程序 (14)5.6手动程序 (15)5.7 PLC梯形图总体结构图 (15)5.8面板设计 (16)第六章系统调试 (17)第七章设计心得 (18)第八章参考文献 (19)第一章绪论对于机械—电气结合控制的组合机床,电气控制系统起着重要的神经中枢作用。
传统的组合机床采用的继电器—接触器控制系统,接线复杂、故障率高、调试和维护困难。
随着PLC控制技术日益成熟并得到越来越广泛的应用,利用原有的继电器—接触器控制电路设计PLC控制系统,或直接进行PLC控制系统的设计,都能很好地满足组合机床自动化控制的要求。
本次设计的要求如下:组合机床结构示意图组合机床工作循环图组合机床采用两个动力头从两个侧面分别加工,左、右动力头的电动机均为2.2kw,进给系统和工件夹紧都用液压系统驱动,液压泵电动机的功率为3kw,动力头和夹紧装置的动作由电磁阀控制。
设计要求如下:(1)两台铣削动力头分别由两台笼型异步电动机拖动,单向旋转,无须电气变速和停机制动控制,但要求铣刀能进行点动对刀。
(2)液压泵电动机单向旋转,机床完成一次半自动工作循环后按下总停机按钮时才停机。
关于数控机床的电气控制改进组合式机床电气控制设计

关于数控机床的电气控制改进组合式机床电气控制设计组合式加工机床由于具有较高的灵敏性,经常用来在工业生产中加工大型工件,比如轧钢机的大型部件,组合式加工机床的优势之一是可以灵活的进行移动移位加工,因此组合式加工机床比目前市面上存在的固定机床更加适合加工大型的工件,主要原因是由于越大越沉重的工件加工时越不容易翻转或移动,因此导致加工效率降低,而是用组合式加工机床可以有效解决上述问题,提供工作效率和工作质量。
组合式加工机床的主要部件包括主轴箱、床身导轨以及立柱等构成,而且需要根据实际生产情况,设计组合式加工机床的电气控制系统,然后进行分析、改进以及完善等工作,以保证组合式加工机床的工作效率。
1 电气控制柜的设计在本设计中,组合式加工机床的电气柜中装配的电子设备主要包括:LG变频器(两个),欧姆龙CQM1H型可编程逻辑控制器(PLC)一个。
主轴电机使用18.5kw容量的变频器进行控制,而主轴箱走刀电机和主轴箱快速电机以及立柱行走电机使用5.5kW容量的变频器控制。
而且在操作站与组合式加工机床的电器柜之间的传输方式使用了总线式传输方式,并且使用插头连接手控操作站、床身分线盒和控制柜,因此不但大量的减少了控制电缆的数量,而且方便工作人员进行维护、检修和移动等工作。
电器柜的柜门上分别安装了电源启动/停止控制按钮以及两个电机转速显示表,方便工作人员对主回路电源进行控制。
在电器柜的内部,通过空气开关、变压器、继电器以及接触器等大量电器设备进行多级保护。
为了防止PLC被电路故障或其他原因损坏,因此,接触器需要通过继电器对PLC进行控制。
2 可编程逻辑控制器(PLC)程序设计可编程逻辑控制器(Programmable Logic Controller,简称PLC),是一种通过进行数字运算实现具体操作的电子系统,是现代工业的核心控制部件。
本设计采用可编程逻辑控制器是OMRON(欧姆龙)公司的CQM1H型PLC控制器,可编程逻辑控制器(PLC)在组合式加工机床控制电路中,主要不但需要接收来自限位开关的信号、按钮控制信号、空气开关监控信号、电机过载信号、变频器保护信号等来自外部的信号,还需要接受指示信号、输入变频器控制信号以及输出变频器控制信号等。
六工位组合机床PLC电气控制系统设计毕业设计论文
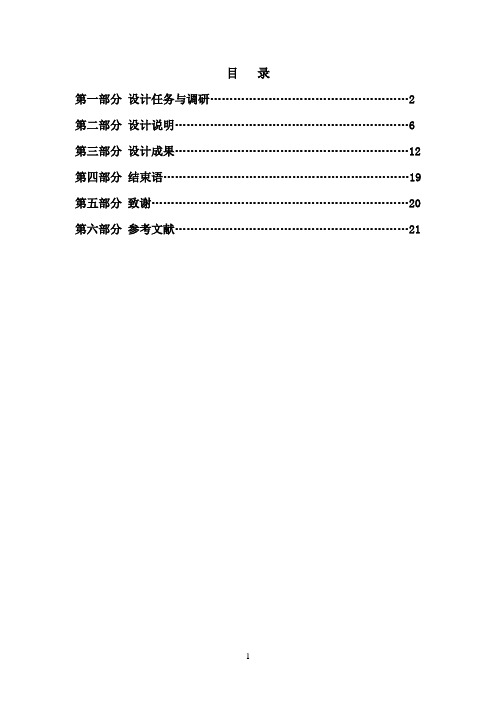
目录第一部分设计任务与调研 (2)第二部分设计说明 (6)第三部分设计成果 (12)第四部分结束语 (19)第五部分致谢 (20)第六部分参考文献 (21)第一部分设计任务与调研1、毕业设计的主要任务设计一台能完成设计一台能完成装卸、打中心孔、钻孔、倒角、扩孔以及铰孔加工六工位组合机床的PLC电气控制系统。
的PLC电气控制系统。
六工位组合机床完成装卸、打中心孔、钻孔、倒角、扩孔以及铰孔加工。
具体加工过程为:回转工作台上升→在工位Ⅰ拆卸和装夹零件→回转工作台回转到工位Ⅱ下降→工位Ⅱ对零件进行打中心孔→回转工作台上升回转到工位Ⅲ下降→工位Ⅲ钻孔加工→回转工作台上升回转到工位Ⅳ下降→工位Ⅳ倒角加工→回转工作台上升回转到工位Ⅴ下降→工位Ⅴ扩孔加工→回转工作台上升回转到工位Ⅵ下降→工位Ⅵ铰孔加工,如此循环实现对不同零件、不同工位的同步加工。
六工位组合机床完成装卸、打中心孔、钻孔、倒角、扩孔以及铰孔加工。
因为各控制对象所处地理位置比较集中,各个工位之间相隔60°,且相互之间的动存在一定的顺序关系,所以采用集中式控制系统,用一台PLC控制多台设备。
各电动机和工作台的运动在工艺上都应具备必要的配合和联锁。
2、设计的思路、方法与步骤2.1 思路依托电工实训中心和自动化设备维修实训中心的铣床、钻床、镗床、PLC等实训设备,充分运用所学专业知识和实践技能,详细制定设计方案和阶段进度计划,通过程序设计、模拟调试、修订完善,设计出能实现六工位加工系统功能的组合机床PLC电气控制系统。
2.2方法:文献检索、图书馆借阅、手册查询、设备选型、PLC编程、PLC 实训室程序调试。
2.3步骤:分析工艺与控制流程、分析控制要求与方式、分析系统设计的原则和方法、确定PLC输入输出设备和I/O点数及选择PLC机型、硬件系统设计、软件程序设计、绘制控制系统接线图、电器元件的选择、程序调试。
3、本课题相关资料3.1组合机床概述组合机床是机械制造业中的主要加工工具, 因为绝大多数机械零件都是由机床加工而成的。
组合机床的电气控制系统设计
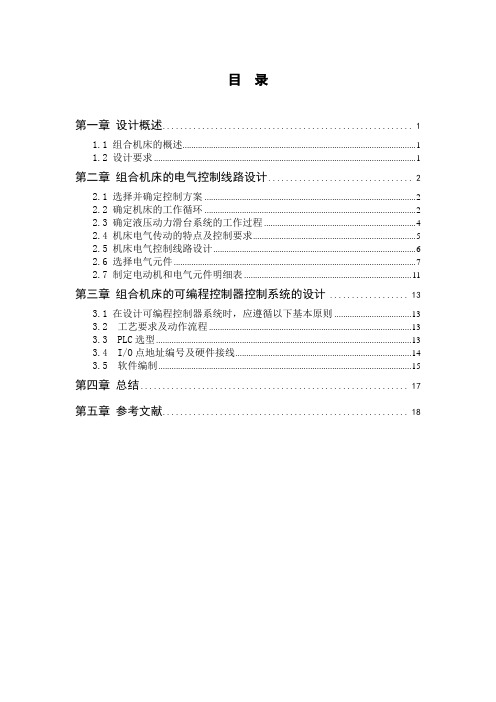
目录第一章设计概述 (1)1.1 组合机床的概述 (1)1.2 设计要求 (1)第二章组合机床的电气控制线路设计 (2)2.1 选择并确定控制方案 (2)2.2 确定机床的工作循环 (2)2.3 确定液压动力滑台系统的工作过程 (4)2.4 机床电气传动的特点及控制要求 (5)2.5 机床电气控制线路设计 (6)2.6 选择电气元件 (7)2.7 制定电动机和电气元件明细表 (11)第三章组合机床的可编程控制器控制系统的设计 (13)3.1 在设计可编程控制器系统时,应遵循以下基本原则 (13)3.2 工艺要求及动作流程 (13)3.3 PLC选型 (13)3.4 I/O点地址编号及硬件接线 (14)3.5 软件编制 (15)第四章总结 (17)第五章参考文献 (18)第一章设计概述1.1 组合机床的概述组合机床通常是采用多刀、多面、多工序、多工位同时加工,由通用部件和专用部件组成的工序集中的高效率专用机床。
它的电气控制线路是将各个部件组合成一个统一的循环系统。
在组合机床上可以完成钻孔、扩孔、铰孔、镗孔、攻螺纹、铣削及磨削等工序。
组合机床用于大批量生产。
组合机床的控制系统大多采用机械、液压或气动、电气相结合的控制方式。
其中,电气控制又起中枢连接的作用。
因此,应分析组合机床电气控制系统与机械、液压或气动部分的相互关系。
1.2 设计要求设计两面加工组合机床的电气控制线路及其可编程控制器的控制系统。
要求如下:1)能按照本组最终要求合理设计继电器电气原理图,PLC电气原理图,再做成控制板,最后连线试验。
2)要求上交1份设计说明书,2张图纸,测试结果。
第二章组合机床的电气控制线路设计2.1 选择并确定控制方案组合机床组成部件不是一成不变的,它将随着生产力的向前发展而不断更新,因此与相适应的电气控制线路也随着更新换代,目前主要有以下两种:1)机械动力滑台控制线路机械动力滑台和液压动力滑台都是完成进给运动的动力部件,两者区别仅在于进给的驱动方式不同。
三面铣组合机床的电气控制系统设计
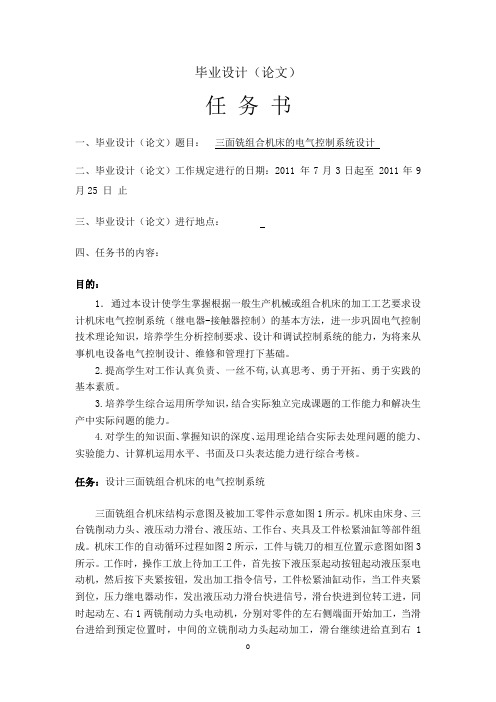
年月 日
教研室主任签名:
年月日
学生签名:
年月日
摘要
组合机床(transfer and unit machine)组合机床是以通用部件为基础,配以按工件特定形状和加工工艺设计的专用部件和夹具,组成的半自动或自动专用机床。
组合机床一般采用多轴、多刀、多工序、多面或多工位同时加工的方式,生产效率比通用机床高几倍至几十倍。由于通用部件已经标准化和系列化,可根据需要灵活配置,能缩短设计和制造周期。因此,组合机床兼有低成本和高效率的优点,在大批、大量生产中得到广泛应用,并可用以组成自动生产线。
关键词:电气控制系统、液压控制系统、三面铣组合机床
1.工件的加工过程及行程开关的安装位置图
2.
液压元件动作表
元件
工序
YV1
YV2
YV3
YV4
YV5
KP1
原位
—
(+)
—
—
—
—
夹紧
+
—
—
—
—
+
快进
(+)
—
+
—
—
+
工进
(+)
—
+
—
+
+
死挡铁停留
(+)
—
+
—
+
+
快退
(+)
—
—
+
—
+பைடு நூலகம்
松开
—
+
—
—
—
—
3.
夹紧过程:
按下按钮SB4检查右1铣头工作是否正常
组合式机床电气控制设计

组合式机床电气控制设计组合式机床电气控制设计【摘要】本文阐述了组合式机床相关知识和PLC的相关概念,论证了组合式机床电气设计的基本理论和过程,并结合PLC编程程序来进行设计。
【关键字】组合式机床;电气设计;PLC编程1、组合式机床的相关知识1.1组合式机床的概念组合式机床是集机电于一体的、自动化程度较高的成套技术装备,它是由一些通用部件及少量的专用部件组成的自动化或者半自动化的专用机床。
它的特征是高效率、高质量、低成本、经济实用,因而被广泛应用于工程机械、交通、能源、轻工业等行业。
1.2组合式机床的加工方式组合式机床加工方式一般为多轴、多刀、多工序、多面或多工位同时加工,它的生产效率是通用机床的几倍甚至几十倍。
组合式机床一般用来加工箱体类或形状特殊的零件,基本上加工物固定不动,由刀具的各方位的旋转以及刀具与工件的相对运动来实现钻孔、扩孔、铰孔、铣削平面、切削内外螺纹等工序。
随着技术日臻成熟,出现了一种新型的组合式机床,它利用原有的继电接触式控制电路加上PLC控制系统,来完成多位主轴箱、可换主轴箱等的自动更换,达到任意改变工作循环控制和驱动系统的目的。
2、可编程控制器及应用2.1可编程控制器(PLC)概述PLC是一种专门在工业环境下产生的数字运算操作的电子装置。
它采用可以编制程序的存储器,在其内部进行存储和执行逻辑运算、顺序运算、计时、计数和算术运算等操作的指令,并能通过数字信号或模拟信号来进行输入和输出,从而控制各种类型的机械或生产过程。
PLC还有一些相关的外围设备与其配合,形成一个整体,这样易于功能性的`扩展。
2.2有关组合式机床的电气控制设计的实现方式组合式机床的电气控制,理论上讲,可以采用继电接触式电气控制系统、单片机控制系统和PLC控制系统来实现。
但PLC控制系统是实际工程中比较经济、有效、性能优越的控制方案。
下面做以简单的比较:(1) 控制逻辑继电接触式控制系统采用线路的串联、并联以及串并联的硬接线逻辑,它的连线复杂、体积大、功耗大,不易改革,所以在灵活性和扩展性存在缺陷;而PLC采用逻辑存储,它只有输入端和输出端的外围设备需要线路连线,逻辑控制是由程序来完成并存储在PLC的内存当中,改变程序就可以改变逻辑控制,所以PLC的灵活性和扩展性更强。
四工位组合机床的电气控制电路设计
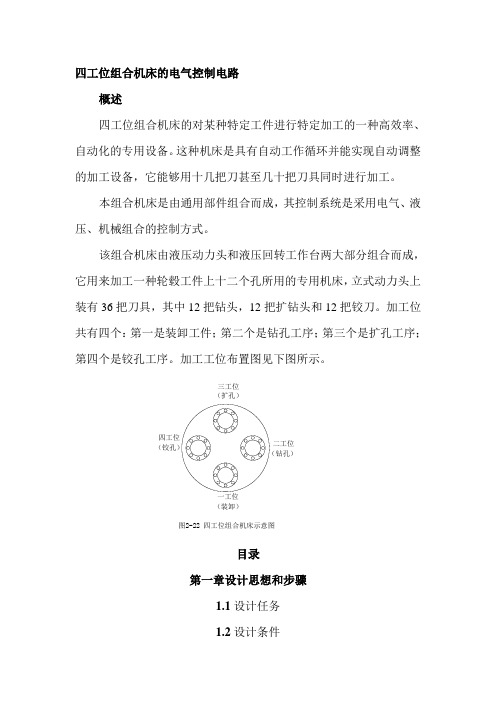
四工位组合机床的电气控制电路概述四工位组合机床的对某种特定工件进行特定加工的一种高效率、自动化的专用设备。
这种机床是具有自动工作循环并能实现自动调整的加工设备,它能够用十几把刀甚至几十把刀具同时进行加工。
本组合机床是由通用部件组合而成,其控制系统是采用电气、液压、机械组合的控制方式。
该组合机床由液压动力头和液压回转工作台两大部分组合而成,它用来加工一种轮毂工件上十二个孔所用的专用机床,立式动力头上装有36把刀具,其中12把钻头,12把扩钻头和12把铰刀。
加工位共有四个:第一是装卸工件;第二个是钻孔工序;第三个是扩孔工序;第四个是铰孔工序。
加工工位布置图见下图所示。
图2-22 四工位组合机床示意图 一工位(装卸)四工位(铰孔) 三工位(扩孔)二工位(钻孔)目录第一章设计思想和步骤1.1设计任务1.2设计条件1.3设计要求1.4设计思想及步骤第二章四工位的电路设计2.1主电路设计2.2变压器设计2.3控制电路设计第三章四工位机床的工作台电路设计3.1液压回转工作台的控制电路设计3.2液压动力头控制电路设计3.3指示灯电路设计3.4总电路设计第四章PLC电路设计4.1 PLC控制设计4.2电路元件选择4.3明细表第五章总结5.1参考文献5.2设计小结第一章设计思想和步骤1.1设计任务1.1设计任务1:根据条件与要求设计出KA-KM电路。
2:根据设计的KA-KM电路做一张J-C电路图。
3:根据KA-KM列出输入状态表。
4:根据KA-KM列出输出状态表。
5:根据KA-KM列出中间元件状态表。
6:根据KA-KM列出定时器状态表。
7:根据上表绘制梯形图。
8:根据梯形图编制程序。
9:作出现场接线图。
10:编写说明书。
1.2设计条件(一)组合机床的启动工作状态回转台抬起→回转抬回转→回转台反靠→回转台夹紧→动力头快进→动力头工进→延时停留→动力头快退。
(二)液压回转工作台回转控制状态液压回转工作台是靠控制液压系统的油路来实现工作台转位动作,而液压系统的动作循环是靠电气电路控制。
电气控制及PLC课程设计 双面卧式组合机床控制系统设计说明书
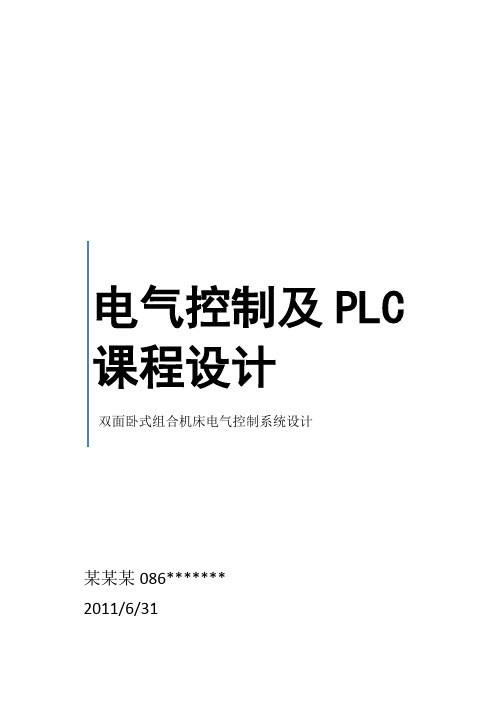
电气控制及PLC 课程设计双面卧式组合机床电气控制系统设计某某某086*******2011/6/31目录一、机床电气控制系统的原理图1.主电路图2.PLC的I/O接线图二、控制系统程序1.I/O地址表2.梯形图3.语句表三、电气元件清单四、机床操作说明书M 13~FR 1KM 1FU 1M 23~FR 2KM 2FU 2M 33~FR 3KM 3FU 3M 43~FR 4KM 4FU 4380VL 2L 1L 3QS PE 液压泵电机左主轴电机右主轴电机冷却电机总开关及保护总停启动工作方式左机接通右机接通夹具夹紧夹具松开冷却电机左滑台快进左滑台快退右滑台快进右滑台快退左主轴电机右主轴电机左滑台原位左滑台工进左滑台终点右滑台原位右滑台工进右滑台终点松开信号夹紧信号油泵电机夹具夹紧夹具松开冷却电机左主轴电机右主轴电机左滑台快进左滑台工进左滑台快退右滑台快进右滑台工进右滑台快退运行指示灯半自动指示灯调整指示灯左原位指示灯右原位指示灯左滑台工作指示灯右滑台工作指示灯一、机床电气控制系统的原理图 1、主电路图2、PLC 的I/O 接线图二、控制系统程序1、I/O地址表2、梯形图3、语句表0 LD M80021 ZRST S0 S30 6 SET S08 STL S09 LD X00110 OR Y00011 ANI X00012 SET Y00013 SET Y01414 LD X00015 RST Y00016 LD X00017 RST Y01418 LD X00319 SET Y02120 LDI X00321 RST Y02122 LD X00423 SET Y02224 LDI X00425 RST Y02226 LD X00227 OUT Y01628 LDI X00229 OUT Y01530 LD X01631 OUT Y01732 LD X02133 OUT Y02034 LD X00235 MPS36 AND X01437 OUT Y00438 MRD 39 AND X01540 OUT Y00541 MRD42 AND X00743 OUT Y00344 MRD45 AND Y00046 AND X00647 ANI X02548 OUT Y00249 MRD50 AND Y00051 AND X00552 OUT Y00153 MRD54 AND Y00055 AND X01056 ANI X02057 OUT Y00658 OUT Y00759 MRD60 AND Y00061 AND X01262 ANI X02363 OUT Y01164 OUT Y01265 MRD66 AND Y00067 AND X01168 ANI X01669 OUT Y01070 MPP71 AND Y00072 AND X01373 ANI X02174 OUT Y01375 LDI X00276 AND Y00077 LD X01678 ORI X00379 ANB80 LD X02181 ORI X00482 ANB83 AND X00584 SET S2186 STL S2187 SET Y00188 LDI X00289 SET Y01590 LD X01691 OUT Y01792 LD X02193 OUT Y02094 LD X02495 SET S2297 STL S2298 LD X00399 SET Y004 100 OUT Y006 101 OUT Y007 102 LS X004 103 SET Y005 104 OUT Y011 105 OUT Y012 106 LD X016 107 OUT Y017 108 LD X021 109 OUT Y020 110 LD X017 111 ORI X003112 LD X022113 ORI X004114 ANB115 SET S23117 STL S23118 OUT Y003119 LD X003120 OUT Y007121 LD X004122 OUT Y012123 LD X02124 ORI X003125 LD X023126 ORI X004127 ANB128 OUT T0 K20 131 LD T0132 SET S24134 STL S24135 LD X003136 OUT Y010137 LD X004138 OUT Y013139 LD X016140 ORI X003141 LD X021142 ORI X004143 ANB144 SET S25146 STL S25147 RST Y001148 RST Y004149 RST Y005150 OUT Y002151 LD X016152 OUT Y017 153 LD X021 154 OUT Y020 155 LD X025 156 SET S0 158 RET三、电气元件清单四、机床操作说明书1、自动1)按下操作台上“启动”按钮,使泵站工作(指示灯亮)。
组合机床的电气控制

组合机床的电气控制组合机床是一种同时具备多种机床功能的多工位机床,它将不同的切削、成形、加工功能集成在一个床身上,基本上可以实现薄板焊接、钻铣、刨磨、车削、磨齿等多种加工工艺。
在组合机床中,电气控制系统是整个设备的重要组成部分之一,它对机床性能和加工过程至关重要。
本文将从组合机床的电气控制设计、电气元器件选配、电气系统安装、电气调试和维护维修等方面详细介绍组合机床的电气控制技术。
一、组合机床的电气控制设计组合机床的电气控制系统设计应该根据机床功能特点和加工需求进行综合考虑,尤其是在电气控制方案上,必须坚持“适度简化、合理选配”的原则。
整个电气控制系统应当建立在确定了各项机床构件和机床各种运动要求的基础之上,合理选配各种元器件,将机床的硬件参数与控制程序组合起来,通过合理的电气连线和安装方式来实现对机床的全面控制。
二、电气元器件的选配组合机床的电气控制元器件为电机、传感器、执行机构等。
首先,应根据各项机床构件和要求进行电机的选型和调参,确保其性能稳定。
其次,传感器也是组合机床中不可缺少的元器件,可以实现对机床运动和加工精度的测控,如编码器、位置传感器等可用来对机床位置和转角进行精确定位,在加工过程中能按照加工要求更加准确地控制机床运动。
执行机构包括电磁阀、气缸、水平/垂直伺服机械手臂等,能够实现机床各项运动和加工功能的切换、刹车、自动上下料等功能。
三、电气系统的安装与调试组合机床的电气系统安装应根据基础设计任务的实际要求,尽早进行基础设施(如电气箱、电缆支架等)的安装。
安装中应根据电气元器件的特点进行布局设计,以达到安全、简单、实用的目的。
此外,在机床加工后,还应进行电气系统调试,最好由专业技术人员实施,以确保电气系统能够安全有效地工作,并在出现故障时能及时进行修理。
四、电气系统的维护维修组合机床的日常运行维护应重视电气部分的检修,检修时要注意安全防范措施,以免发生电气伤害。
一般来说,应每隔一定时间进行一次设备维护,以检查电气设备的运行情况,如电气部分的清洁、预防性维护、视觉检查和检测各项所需的指标等。
组合机床的电气控制系统设计

组合机床的电气控制系统设计组合机床是一种集铣削、钻孔、镗削、攻丝等多种加工功能于一体的机床。
电气控制系统是组合机床的关键部分之一,它负责控制机床的运动、加工参数以及自动化程度等。
本文将从电气控制系统的设计和组成方面进行探讨。
1.总体设计思路在组合机床的电气控制系统设计中,首先需要确定总体设计思路。
一般情况下,可以采用PLC(可编程逻辑控制器)作为主控制器,通过与其他外围设备的通信来实现对整个系统的控制。
此外,还可以附加使用触摸屏、计算机等设备作为人机界面,方便操作员进行参数设置和故障排除等操作。
2.电机驱动系统设计组合机床中的各个运动部件(如主轴、进给运动等)需要通过电机进行驱动。
在电机驱动系统设计中,需要根据不同的运动要求选择合适的电机及其驱动器,并结合具体的机械结构进行匹配。
3.传感器选择和布置传感器在电气控制系统中的作用是对机床的运动状态、工件加工状态、刀具磨损等进行监测和反馈,以实现自动化控制。
在传感器的选择上,需要综合考虑其精度、稳定性、可靠性以及适应环境的能力。
在布置上,需要合理安装传感器,确保其能够准确获取相关信息。
4.自动化控制设计自动化控制是组合机床电气控制系统的重要部分。
通过自动化控制,可以减少操作员的劳动强度,提高产品质量和生产效率。
在自动化控制设计中,需要根据不同的加工要求,设置相应的控制程序,实现自动换刀、自动测量、自动刀具磨损补偿等功能。
5.安全保护和故障诊断设计在组合机床的电气控制系统设计中,安全保护和故障诊断是非常重要的考虑因素。
安全保护包括电气隔离、急停按钮、门禁系统等措施,在确保操作员人身安全的基础上,对机床进行有效的保护。
故障诊断则需要设计合理的电气故障监测系统,通过报警、自动停机等方式及时发现和排除故障,保证机床的正常运行。
总之,组合机床的电气控制系统设计需要综合考虑机床的运动要求、加工要求、自动化程度以及安全保护和故障诊断等因素。
通过合理的设计,可以实现机床的高效、稳定和安全运行。
组合机床的电气与PLC控制系统设计
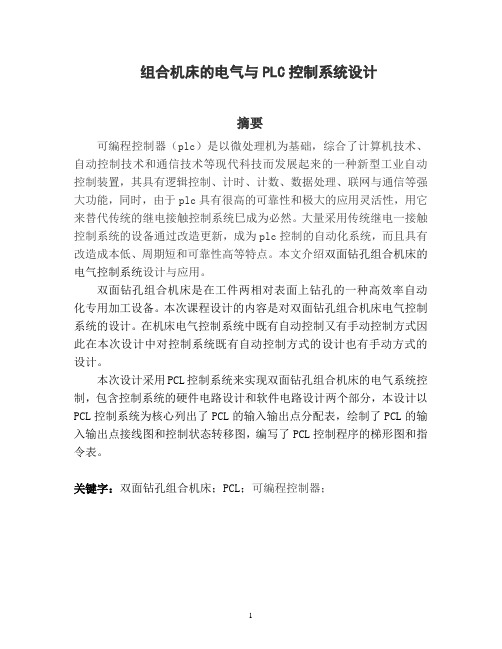
组合机床的电气与PLC控制系统设计摘要可编程控制器(plc)是以微处理机为基础,综合了计算机技术、自动控制技术和通信技术等现代科技而发展起来的一种新型工业自动控制装置,其具有逻辑控制、计时、计数、数据处理、联网与通信等强大功能,同时,由于plc具有很高的可靠性和极大的应用灵活性,用它来替代传统的继电接触控制系统巳成为必然。
大量采用传统继电一接触控制系统的设备通过改造更新,成为plc控制的自动化系统,而且具有改造成本低、周期短和可靠性高等特点。
本文介绍双面钻孔组合机床的电气控制系统设计与应用。
双面钻孔组合机床是在工件两相对表面上钻孔的一种高效率自动化专用加工设备。
本次课程设计的内容是对双面钻孔组合机床电气控制系统的设计。
在机床电气控制系统中既有自动控制又有手动控制方式因此在本次设计中对控制系统既有自动控制方式的设计也有手动方式的设计。
本次设计采用PCL控制系统来实现双面钻孔组合机床的电气系统控制,包含控制系统的硬件电路设计和软件电路设计两个部分,本设计以PCL控制系统为核心列出了PCL的输入输出点分配表,绘制了PCL的输入输出点接线图和控制状态转移图,编写了PCL控制程序的梯形图和指令表。
关键字:双面钻孔组合机床;PCL;可编程控制器;目录第1章设计目的要求和概述 (3)1.1 设计目的 (3)1.2 双面钻孔组合机床的概述 (3)1.3设计要求与任务分配 (3)第2章双面钻孔组合机床的控制要求 (5)2.1 双面钻孔组合机床的工作流程 (5)2.2电动机控制要求 (5)2.3 机床动力滑台、工件定位装置、夹紧装置控制要求 (6)第 3 章 PLC的简介与选择 (8)3.1 PLC (8)3.2 PLC简介 (8)3.3 PLC的结构及基本配置 (8)3.4 PLC选择 (9)第4章双面钻孔机床左机钻孔顺序动作PLC控制 (10)4.1 双面钻孔组合机床的左机钻孔自动控制PLC输入输出点分配 (10)4.2状态继电器的分配 (10)第5章双面钻孔组合机床的PLC控制实现 (14)5.1 并行分支状态转移 (14)5.2 PLC控制考虑上双面钻孔组合机床的手动方式控制 (14)第6章总结 (21)参考文献 (22)第1章设计目的要求和概述1.1 设计目的1、培养学生综合分析和解决本专业的一般工程技术问题的独立工作能力,拓宽和深化学生的知识。
(参考)组合机床电气控制课程设计说明书

目录第一章绪论 (1)第二章设计方案 (3)2.1 左、右两动力头进给电机 (3)2.2电动机控制电路 (3)2.3液压泵电动机 (4)2.4液压动力滑台控制 (4)2.5主电路及照明电路 (6)2.6保护与调整环节 (6)2.7继电器电气原理简图 (8)第三章I/O分配表 (10)第四章组合机床电气控制电路图 (11)第五章课程设计的具体内容 (12)5.1单循环自动工作 (12)5.1.1单循环自动工作循环图 (12)5.1.2单循环自动工作功能表 (12)5.1.3单循环自动工作梯形图 (12)5.2左铣单循环工作 (13)5.2.1左铣单循环功能表 (13)5.2.2左铣单循环梯形图 (13)5.3右铣单循环工作梯形图 (13)5.4公用程序 (13)5.5回原位程序 (14)5.6手动程序 (15)5.7 PLC梯形图总体结构图 (15)5.8面板设计 (16)第六章系统调试 (17)第七章设计心得 (18)第八章参考文献 (19)第一章绪论对于机械—电气结合控制的组合机床,电气控制系统起着重要的神经中枢作用。
传统的组合机床采用的继电器—接触器控制系统,接线复杂、故障率高、调试和维护困难。
随着PLC控制技术日益成熟并得到越来越广泛的应用,利用原有的继电器—接触器控制电路设计PLC控制系统,或直接进行PLC控制系统的设计,都能很好地满足组合机床自动化控制的要求。
本次设计的要求如下:组合机床结构示意图组合机床工作循环图组合机床采用两个动力头从两个侧面分别加工,左、右动力头的电动机均为2.2kw,进给系统和工件夹紧都用液压系统驱动,液压泵电动机的功率为3kw,动力头和夹紧装置的动作由电磁阀控制。
设计要求如下:(1)两台铣削动力头分别由两台笼型异步电动机拖动,单向旋转,无须电气变速和停机制动控制,但要求铣刀能进行点动对刀。
(2)液压泵电动机单向旋转,机床完成一次半自动工作循环后按下总停机按钮时才停机。
组合机床的电气控制系统设计
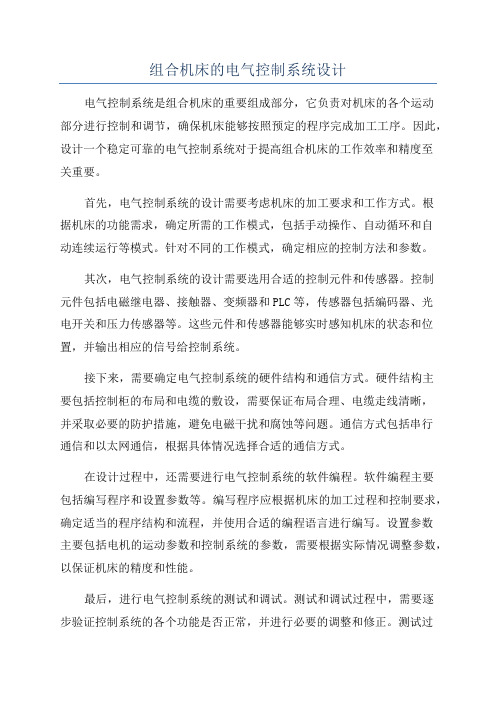
组合机床的电气控制系统设计电气控制系统是组合机床的重要组成部分,它负责对机床的各个运动部分进行控制和调节,确保机床能够按照预定的程序完成加工工序。
因此,设计一个稳定可靠的电气控制系统对于提高组合机床的工作效率和精度至关重要。
首先,电气控制系统的设计需要考虑机床的加工要求和工作方式。
根据机床的功能需求,确定所需的工作模式,包括手动操作、自动循环和自动连续运行等模式。
针对不同的工作模式,确定相应的控制方法和参数。
其次,电气控制系统的设计需要选用合适的控制元件和传感器。
控制元件包括电磁继电器、接触器、变频器和PLC等,传感器包括编码器、光电开关和压力传感器等。
这些元件和传感器能够实时感知机床的状态和位置,并输出相应的信号给控制系统。
接下来,需要确定电气控制系统的硬件结构和通信方式。
硬件结构主要包括控制柜的布局和电缆的敷设,需要保证布局合理、电缆走线清晰,并采取必要的防护措施,避免电磁干扰和腐蚀等问题。
通信方式包括串行通信和以太网通信,根据具体情况选择合适的通信方式。
在设计过程中,还需要进行电气控制系统的软件编程。
软件编程主要包括编写程序和设置参数等。
编写程序应根据机床的加工过程和控制要求,确定适当的程序结构和流程,并使用合适的编程语言进行编写。
设置参数主要包括电机的运动参数和控制系统的参数,需要根据实际情况调整参数,以保证机床的精度和性能。
最后,进行电气控制系统的测试和调试。
测试和调试过程中,需要逐步验证控制系统的各个功能是否正常,并进行必要的调整和修正。
测试过程中,应关注机床的各个运动部分的动作是否准确、平稳,并确保整个系统的稳定性和可靠性。
综上所述,设计组合机床的电气控制系统需要考虑机床的加工要求和工作方式,并选用合适的控制元件和传感器。
还需要确定电气控制系统的硬件结构和通信方式,并进行软件编程、测试和调试,以确保控制系统的稳定性和可靠性。
电气控制系统的良好设计和运行将直接影响组合机床的工作效率和加工精度。
- 1、下载文档前请自行甄别文档内容的完整性,平台不提供额外的编辑、内容补充、找答案等附加服务。
- 2、"仅部分预览"的文档,不可在线预览部分如存在完整性等问题,可反馈申请退款(可完整预览的文档不适用该条件!)。
- 3、如文档侵犯您的权益,请联系客服反馈,我们会尽快为您处理(人工客服工作时间:9:00-18:30)。
组合式机床电气控制设计
组合式机床电气控制设计,是为大家精心的关机床电气控制设
计的论文,欢迎各位机电一体化的同学阅读!
【摘要】本文阐述了组合式机床相关知识和PLC的相关概念,论证了组合式机床电气设计的基本理论和过程,并结合PLC编程程序来进行设计。
【关键字】组合式机床;电气设计;PLC编程
1、组合式机床的相关知识
1.1组合式机床的概念
组合式机床是集机电于一体的、自动化程度较高的成套技术装备,它是由一些通用部件及少量的专用部件组成的自动化或者半自动化的专用机床。
它的特征是高效率、高质量、低成本、经济实用,因而被广泛应用于工程机械、交通、能源、轻工业等行业。
1.2组合式机床的加工方式
组合式机床加工方式一般为多轴、多刀、多工序、多面或多工
位同时加工,它的生产效率是通用机床的几倍甚至几十倍。
组合式机床一般用来加工箱体类或形状特殊的零件,基本上加工物固定不动,由刀具的各方位的旋转以及刀具与工件的相对运动来实现钻孔、扩孔、铰孔、铣削平面、切削内外螺纹等工序。
随着技术日臻成熟,出现了一种新型的组合式机床,它利用原
有的继电接触式控制电路加上PLC控制系统,来完成多位主轴箱、可
换主轴箱等的自动更换,达到任意改变工作循环控制和驱动系统的目的。
2、可编程控制器及应用
2.1可编程控制器(PLC)概述
PLC是一种专门在工业环境下产生的数字运算操作的电子装置。
它采用可以编制程序的存储器,在其内部进行存储和执行逻辑运算、顺序运算、计时、计数和算术运算等操作的指令,并能通过数字信号或模拟信号来进行输入和输出,从而控制各种类型的机械或生产过程。
PLC还有一些相关的外围设备与其配合,形成一个整体,这样易于功能性的扩展。
2.2有关组合式机床的电气控制设计的实现方式
组合式机床的电气控制,理论上讲,可以采用继电接触式电气
控制系统、单片机控制系统和PLC控制系统来实现。
但PLC控制系统是实际工程中比较经济、有效、性能优越的控制方案。
下面做以简单的比较:
(1) 控制逻辑继电接触式控制系统采用线路的串联、并联以及串并联的硬接线逻辑,它的连线复杂、体积大、功耗大,不易改革,所以在灵活性和扩展性存在缺陷;而PLC采用逻辑存储,它只有输入
端和输出端的外围设备需要线路连线,逻辑控制是由程序来完成并存储在PLC的内存当中,改变程序就可以改变逻辑控制,所以PLC的灵活性和扩展性更强。
(2) 控制速度继电器接触式控制系统的是根据触点的动作来
实现的,工作频率低,继电器越多,反应的速度越慢,还容易出现触点抖动和拉弧问题;而PLC是由指令控制电路来实现,速度快,并且PLC内部有严格的同步,不会出现抖动和拉弧问题。
(3) 定时控制和计数控制继电接触式控制系统利用时间继电
器的延时来进行定时控制,它本身精度不高,受环境影响大,还有一些结构复杂的时间继电器,使维护难度加大;而PLC使用集成电路作为定时器,时基脉冲由晶体震荡器产生,精度相当高并且定时时间长、范围广。
(4) 可靠性和维护性继电接触式控制系统机械触点多,连线也多,触点容易受损,造成可靠性和维护性差。
PLC采用微电子技术,配有自检和监控功能,不但可靠性得到保证,还可以诊断出自身的故障并随时显示,以及能动态的监视控制程序的执行情况,为现场调试和维护提供了方便。
3、结合PLC系统的电气控制的设计
3.1设计原则
利用继电接触式和PLC控制系统相结合的方法,会对设计产生事半功倍的效果。
PLC的硬、软件再配以继电接触式的控制系统,不但能完善机床电气设备控制系统的设计,更能对控制线路进行准确地分析和精准地维护。
设计的继电接触式控制系统和PLC控制系统,应同时遵循以下基本原则:(1)最大限度地满足被控制对象的控制要求,包括功能要
求、性能要求;(2)在满足控制要求的前提下,力求控制系统简单、经济、节约能源;(3)力求控制系统安全、可靠、使用与维修方便。
3.2电气控制设计的流程
根据控制对象的用途、基本结构、运动形式、工艺过程、工作
环境和控制要求,确定控制方案;绘制组合机床的电气原理图、控制
系统的PLC I/O接线图和梯形图,写出指令程序清单;选择电器元件,列出电器元件明细表。
4、组合式加工机床设计举例
我们以一个组合式加工机床中的电气柜为例,简要介绍一下:
此电气柜主要的电子设备主要有:LG变频器(两个),欧姆龙某款可编程逻辑控制器(PLC)一个。
变频器:其中一个为容量18.5kw的变频器进行主轴的控制,一个容量为5.5kW的变频器来控制主轴箱的走刀电机和快速电机以及立柱行走电机的控制。
4.1变频器参数调整
LG变频器根据需要设置分为“功能组1、功能组2、驱动组、
输入/输出组(I/O组)、选项组、外部组、应用组”,将这七组参数
设置成出厂时的默认数据,并且提供相关功能,方便需求不同而进行调整。
4.2变频器基本参数的设置
LG变频器是组合式数控加工机床电气控制系统的核心部件,它决定着组合式数控加工机床的工作性能,在设置变频器的基本参数时,应该首先对参考变频器的型号来对电机功率进行设置和选择。
4.3特定功能的应用
组合式加工机床中立柱的传动轴和主轴箱的传动轴是不同的,在工作中,为了实现电机对不同的传动轴的选择,来满足工作需要,所以要通过对第二电机进行参数设置,来进行控制。
第二参数功能具体的配置和使用方法如下:首先任意选择一个多功能端口,设置对应的I/O参数,并保持端口在激活状态,然后启用第二电机功能操作。
在对参数进行设置时,具体包括:“第二电机加速时间、减速时间、转折频率、电压、频率方式、第二电机正转矩补偿、第二电机反转矩补偿、电子热保护等级(一分钟)、电子热保护等级(连续)、第二电机额定电机电流”。
4.4其他设置
在操作站与组合式加工机床的电器柜之间的传输方式设置为总线式,并且使用插头连接手控操作站、床身分线盒和控制柜,这样可以减少大量的控制电缆数量,方便工作人员进行维修和移动。
电器柜的柜门上设置了电源ON/OFF按钮,用于电源的开关控制,还有两个电机转速显示表,方便工作人员对主回路电源进行控制。
在电器柜的内部,通过设置空气开关、变压器、继电器以及接触器等大量电气设备进行多级保护。
5、总结
可编程控制器的发展特点是更加适应于现代工业的需要。
从控制规模上来说,这个时期发展了大型机和超小型机;从控制能力上来说,诞生了各种各样的特殊功能单元,用于压力、温度、转速、位移
等各式各样的控制场合;从产品的配套能力来说,生产了各种人机界面单元、通信单元,使应用可编程控制设备的配套更加容易。
PLC系统之所以在组合式机床电气控制设计中得到广泛应用,在于它的灵活性和扩展性强、控制速度快、精度高、具有较高可维护性。
生产中,有了PLC系统,就可以高效率、高质量地完成生产任务。
内容仅供参考。