图解法在合模装置设计中的应用
第四节 注射机合模装置

• B.自锁作用
• C.运动速度
• D.模板间距、锁模力和合模速度的调节困难 • E.曲肘机构容易磨损,加工精度要求也高
• 综上所述,液压合模装置和液压---机械式合
模装置都具有各自的特点,这些特点都是相 对的,同时也不是不可改变的。因此,在中 小型注射机上,上述各种形式都有应用。不 过相对来说,液压—机械式多一些;而大中 型则相反,液压式采用较多。
高度范围较大。
• 移动模板可以在行程范围内任意位置停留,因此,
调节模板间的距离十分简便。
• 调节油压,就能调节锁模力的大小。 • 锁模力的大小可以直接读出,给操作带来方便。 • 零件能自润滑,磨损小。 • 在液压系统中增设各种调节回路,就能方便地实现
注射压力、注射速度、合模速度以及锁模力等的调 节,以更好地适应加工工艺的要求。
• 2、 液压合模装置
• 合模装置是依靠液体的压力实现模具的启闭和锁紧
作用的。
• 直压式合模装置
• 模具的启闭和锁紧都是在一个油缸的作用下完成的,
这是最简单的合模装置。
• 这种合模装置存在一些问题,并不十分符合注射机
对合模装置的要求。
• 合模初期,模具尚未闭合,合模力小;为了缩短循
环周期,这时的移模速度应快才好。但因油缸直径 甚大,实现高ຫໍສະໝຸດ 有一定困难。第四节 合模装置
• 合模装置是保证成型模具可靠的闭锁 开启并取出制
品的部件。一个完善的合模装置,应该具备下列三 个基本条件:
• 第一、足够的锁模力,使模具在熔料压力(即模腔
压力)作用下,不致有开缝现象发生。
• 第二、足够的模板面积、模板行程和模板间的开距,
以适应不同外形尺寸制品的成型要求。
• 第三、模板有合适的运动速度,应是闭模时先快后
合模导向机构的设计课件

2.定位----模具闭合时,保证动、定模按照 正确的位置闭合。 对导柱导套间隙有要求
3.承受侧压→充模过程中可能有单向侧压力
应有一定强度刚度,如侧压力较大时 应增设锥面定位机构
三、导向机构的形式: 1.导柱、导套导向(见上图) 2. 锥面定位
(通常采用导柱、导套导向)
(二)导柱导向机构
导柱导向机构的主要零件是导柱和导套。 一、导柱
两种导柱的结构特点
1. 带头导柱和有肩导柱的前端都设计为锥形,便于导向。
2. 两种导柱都可以在工作部分带有贮油槽图3.图4所示。 带贮油槽的导柱可以贮存润滑油,延长润滑时间。
3. 装在模具另一侧的导套安装孔可以和导柱安装孔采用 同一尺寸,一次加工而成,保证了严格的同轴,如下 图3所示。
4. 有肩导柱工作部分因某种原因挠曲时,容易从模板中 卸下更换,带头导柱则比较困难,如图4所示。
1. 导柱的结构形式 带头导柱——简单,小批量磨损少则无需 导套。 有肩导柱——较复杂,用于大批量精度要 求高时。
A: 带头导柱或(直形导柱)如图
B:有肩导柱(或阶梯形导柱)
除安装部分的凸肩外,使安装的配合 部分直径比外伸的工作部分直径大如下 图b.C所示。
b ■c 用于固定板太薄的场合,不常用.
■ 二、导套
■1.导套的结构形式 带头导套——用于精度较高合,
如下图所示 直导套——用于简单模具
如右图所示
2.导套设计要求
①导柱孔做成通孔,利于排出孔内空气及残渣废料、如模 板较厚、导柱孔必须做成盲孔时、可在盲孔侧面打一 小孔排气
②导套用与导柱相同材料或铜合金等耐磨材料制造、导套 硬度应低于导柱、以↓磨损、防导柱或导套拉毛,导套
作业:
1、合模导向装置的作用是什么? 2、导向装置选用和设计的原则有哪些? 3、导柱的结构形式有哪几种?各自用在
合模装置的设计2

合模装置的设计2肘杆式合模装置是利用各种形式的肘杆机构,在合模时,使合模系统形成预应力,进而对模具实现锁紧的一种合模装置。
例如图13所示的单曲肘机构,当压力油进入油缸的活塞杆端,使活塞下移,从而带动肘杆机构并推动模板向前运动。
当运动至图(13-2a)所示状态时,即模具的分型面刚接触,而肘杆机构尚未成一线排列时,动模板将受到变形阻力的作用,只有在合模油缸的工作油继续升压,并足以克服系统的变形阻力,才能使肘杆成为图(13b)所示的一线排列。
此时,合模系统因发生弹性变形(△lp)而对模具实现预紧,此预紧力pcm即为合模力。
当肘杆机构伸直并对模具实现预紧后,即使工作油的压力卸去,只要合模系统保持着原变形,其合模力是不会随之改变的。
在模具合紧后,如所有受力构件都遵守胡克定律以及不考虑接触点处的非线性变形,则受拉力作用的构件(即拉杆)的变形应为:△lp=3.2调模装置的选择在注塑机合模部分的技术参数中,存有最小模厚和最轻模厚。
调模装置就是用作调节移动模板和前紧固模板之间的距离,以适应环境不必的模具厚度。
对于液压――曲肘式合模装置来说,调模装置也就是调整再分模力的装置。
对调模装置的要求是调模要方便,便于操作;轴向位移准确、灵活、受力均匀;安全可靠,调节行程应有限位和过载保护措施。
目前,使用的调模装置形式很多,常见的几种形式有:1将颤抖模板设计成与两块女团出来的板,其厚度(h)调节器。
2将肘杆设计成长度可调的形式。
3将整个肘杆机构设计成轴向边线可移动的结构。
本次设计选用形式1的调模装置,其结构如图3-7。
此结构的动模板是由左、右两块并用螺纹方式连接起来,通过旋动调节螺母,使动模板厚度b发生变化,从而实现模具高度和合模力的调整。
其特点是调模比较方便,但增加了模板和机器的长度,此式多用于中小型机器上。
图3-7调模装置3.3挖空装置的设计为了取出模内制品,在各类的合模装置上均需设置顶出装置。
顶出装置设计是否完善,将对制品质量和产量都有较大影响。
复合模的构造

复合模的构造复合模的构造1.复合模的基本构造(如下图所示)模板的加工方式上下模座在模具比较在大的情况下,模座上有外导柱(小型模具可以不要外导柱,)导柱的单边间隙在0.01—0.02,这样才能起到良好的导正作用.模座与夹板联接起来需要樏栓,因此模座上也有螺栓沉头孔彧螺丝孔;有时模座和夹板也需要合销来固定,因此,模座上也有合销孔,另外,下模座上一定要有漏料孔.有时弹簧行程不够的情况下,在模座也会有钻弹簧孔.上下夹板: 主要是用来固定, 夹持, 保护冲头的作用.夹板上冲头孔的单边间隙取-0.03.在有内导柱的情`下,夹板上有导柱或导柱孔;与模座联接固定合销孔, 螺栓沉头孔或螺丝孔;联接脱板的等高套筒过孔,限制脱板行程的弹簧孔或优力胶孔;固定冲头的螺丝孔,固定销孔(比较在的冲头).内外脱板: 脱料板的作用主要是脱料和保护冲头.脱料板的单边间隙取+0.015,为紧配合,因此在有脱料板的情况下,冲头可以不用合销.在有内导柱的情况下,外脱板上有导柱孔(导柱孔正面要倒R角);脱板上有等高套筒螺丝孔,冲头过孔等.(4) 公母模: 冲孔下料之功用.在割公母共享时,必须注意下料的毛边方向.一般采用如下左图之割法,而不采用如下右图之割法,此两种割法,下料之毛边方向刚好相反,而复合模的毛边方向为向下.此种加工方式:毛边向下此种加工方式:毛边向上(5) 在有内导柱的情况下,母模上有内导柱或内导柱孔(导柱孔正面要倒R角).模板上有螺栓沉头孔合销孔定位销(块) 漏料孔等.2.复合模上的主要零件及标准件导柱导柱有外导柱和内导柱(亦称辅助导柱),它们的功用都是在上下模运动时起到导正的作用.导柱的头部要做R角,导柱孔的正面孔要倒R角,这样在上下模运动时便于导正.导柱可装在上模,也可装在下模,根据冲压时取放材料之方便而定.内导柱的端部在一般的情况下沉于夹板上,而不沉于模座上,这与加工组装之经济性和方便性有关.导柱必须垂直.假若导柱的垂直度不够(导柱孔割斜等),往往会产生以下两种不良之后果: A 冲头产品毛刺加大B 脱料不顺导柱长度的确定:当还没有开始加工时,导柱已达到直线接触,直线部分为5mm 左右即可,但最小不能不于3mm.要注意防呆,也就是讲在有四根导柱的情况下,千万不能把四根导柱做成前后左右完全对称,以防组模时装反,要把其中一根导柱(一般为右下角的一根)向一边偏3-5mm.合销合销的作用:A 固定作用,把模板固定在想象的尺寸上;B 帮助强度,尤其是在折弯模上.是否要合销,要看其作用,在有脱料的情况下,冲头上可以不要合销,因为脱料板的间隙为+0.015.但当脱料板的间隙很大时,冲头上仍然要用合销.在其它模板上要有合销消孔.(3) 螺栓:其作用就是把各个模板联接锁紧起来.螺栓孔位置螺栓长度螺栓间距螺栓孔及沉头孔尺寸见资料<>等高套筒等高套筒的固定方法使用等高套筒,等高套筒在于控制脱料板的活动部分之尺寸高度(须要配合脱料板牙孔规格).在等高套筒的活动范围内,各模板必须加工消孔,闭模时螺丝头不可凸出模板面(螺丝头部要低于模板面之距离不得小于3.0mm)弹簧优力胶: 在于将活动板或零件给予适当的压力.★在选择弹簧时,必须考虑弹簧的行程和弹性(即倔强系数K).弹簧在装配时,一般可装在脱板和夹板之间,但在弹簧行程不够时,也可在模座上和脱板之间(夹板为过孔,同时夹板也对弹簧起到一种保护作用).弹簧在装配时一定先给一定的预压,否则,弹簧根本不能起到应有的作用.弹簧的种类一般以其颜色来区分: 黄色----轻小荷重蓝色----轻荷重红色----中荷重绿色----重荷重咖啡色----极重荷重弹簧的预压量:当弹簧未动作时,必须先行压缩1.0---2.0mm定位销: 其作用是将材料固定,使尺寸得以准确加工定位销按形状可分为圆形异形(也称定位块);按活动方式可分为固定式和活动式.圆形定位销,一般做Φ3.0—5.0.冲子(冲头)冲子一定要躲在脱板里,至少低于脱板1.0mm冲子的最好固定方式是用螺丝锁紧.对于剪单边的冲子,必须有靠壁,即剪单边冲头有一个根部根部的长度至少为5.0mm,而且根部要倒R角(R1.0—2.0),其目的是为了防止冲子在剪切时逃向一侧.冲子的长度: 冲子在冲孔下料时,必须在吃到材料时再冲下1.5---3.0mm附: 1 刀口问题刀口在线割时都留有一定的直线部分,直线部分的最佳值为3t(t 为材料厚度).但在冲铝制口时,线割时刀口部分绝不能留直线部分,因为铝的熔点比较低,在冲压过程中产生大量的热,废料铝因长时间受热而稍有熔化即熔结在刀口上,久而久之,刀口被破坏,模具报废,因此,在制造冲铝制品模具时,刀口部分决不可留直线部分.2 冲压材料规格的确定材料尺寸规格的确定,以产品展开尺寸单边加大来确定材料和尺寸规格.一般地,左右单边加大 2.5---3.2mm,前后单边加大2.0—2.5mm.第二篇展开图的画法一,对于冲压模具的设计,第一道工序就是要画展开图.一般地,展开图的画法有以下几:内寸法所谓内寸法即是:料内+料内+补偿量(△L)例:如右图展开长度L=( a - t) + ( b –t )+△L=( a - t) + ( b –t )+λ* t 其中"λ"为材料的展开系数,它与材质料厚有关.一般地,料厚在1.20以下,展开系数"λ"为1/3上下,但△L小数的第二位一定要圆整为"0"或"5".例: 材质为SECC, t=1.0mm △L=1/3*1.0 取△L=0.35t=0.8mm △L=1/3*0.8 取△L=0.25中立面法所谓中立面法,即是产品在折弯时,内侧受到压缩,外侧受到拉伸,但总有一个面不受到压缩,也不受到拉伸,此面即为中立面,其长度即为产品之展开长度,此种方法适用于折弯半径在0.5mm以上. 例:如右图展开长度L=a + b + 1= a + b +θ*R(θ为折弯角度,单位为弧度)θ=n*π/180一般情况下,中立面在靠内侧1/3—1/2处,料厚在1.2mm以上, 接近1/2处.Z字形法此种方法主要适用于"两折一次成型"的折弯,其计算方法为"两次展开加一次系数",展开仍以内寸法.例: 如右图展开长度L=( a – t ) + ( b – t )+ ( m - 2t ) + △L反折压平展开长度L= a + b - △L 如下图所示: △L之值可参考下表. 注:画展开图时,一定要定基准点,对于对称的图形,其基准点定在其对称中心,另外,展开图模具图之尺寸采用坐标式标注.画展开图时,其展开尺寸尽量短一点,切不可过长,因为,尺寸过短时,只要在折弯处倒R角即可修正其长度,但过长时,则无法补救,修模很困难.对于压线折弯,会造成正常殿开尺寸过短,差距在0.8mm以内,因此在此种情况下,其展开尺寸要稍加在一点,另外,如果材料短时, 亦可把压线冲子的头部倒一R角即可修正其长度,如下图所示: 压线冲子二,展开图面的要求:图面要求:展开图中必须包含产品图中的所有内孔,内部成型和外部成型的展开的像素.展开图的毛刺面必须向下.展开图中除圆孔外所有像素必须串联成复线.所有冲裁尖角均要倒圆角R=0.3.冲凸和冲桥形10. 11. 14. 15. 应进行局部剖视(剖视方向只能向左或向上).有较复杂折弯(小折,抽孔等如图3~9. 12. 13. 16~18)时应画出局部断面图表示成形以后的断面形状,并用英文注解"PRODUCT IMAGE……."在展开主视图中的表示方法同剖视一样,(在展开图上的长度是展开后的长度,所以小折弯不能画成剖视图的形式,只能画成对应视意图.注:a. 压平成形只画一条压平线, 最外型线放在BEND层如图(17.15)b. Z折如果是一次成型, 则只画两条折线如图(7. 8)c. 以上列出类型除压平(17. 18) 外, 均指一次成型.展开计算原理:板料在弯曲过程中外层受到拉应力,内层受到压应力,从拉到压之间有一既不受拉力也不受压力的过渡层------中性层,中性层在弯曲过程中的长度和弯曲前一样,保持不弯,所以中性层是计算弯曲件展开长度的基准,中性层位置与变形程直度有关,当弯曲半径较大,折弯角度较小时,弯曲程度较小,中性层位置是靠近板料厚的中心处,当弯曲半径变小,折弯角度增大时,变形程度随之增大,中性层位置逐渐向弯曲中心的内侧移动,中性层到板料内侧的距离用"λ"表示计算方法(一)展开的基本公式: 展开长度=料内+料内+补偿量R=0, θ=90Oλ=1/4TL=(A-T)+(B-T)+λ*π/2=(A-T)+(B-T)+T/4*π/2=A+B-2T+ KK=λ*π/2=0.4TR≠0 θ=900L=(A-T-R)+(B-T-R)+(R+λ)*π/2当R≥5T时λ=1/2T3T<r<="" 3t<λTR=0 θ≠900λ=1/3TL=(A-T*Tan (a/2))+(B-T*Tan (a/2))+T/3*a (a单位为rad,下同) R≠0 θ≠900L=(A- (T+R)* Tan (a/2))+(B-(T+R)* Tan (a/2)+(R+λ)*a当R≥5T时λ=1/2T3T<r<="" 3t<λTZ折(1)当C≥5T时,一般分两次成型,按两个900 折弯计算L=A-T+C-2T+B+2K当3T<c<5t时(一次成型)< p="">L=A-T+C-2T+B+K当C≤3T时(一次成型)L=A-T+C-2T+B+1/2KZ折(2)C≤3T时(一次成型)L=A-T+C-T+B+D+K第三篇设计一,冲模设计应注意的问题为便于冲模设计者在设计模具时,全方位考虑问题,以减少不必要的修改次次数及时间,现特提出以下几点,希望设计时能参照以下内容进行思考,设计.1.拿到产品图时,首先应了解产品所需毛边方向.2.了解产品材质类型及厚度,以决定间隙大小.3.了解产品的加工产量,以决定具的结构.4.该产品的模具应在哪条线冲制,该线对模具的要求.5.对于需攻牙或反转的产品,应考虑设计攻牙治具或反转治具.6.对于所有跑ROBOT的模具在两冲床之间须有空站(攻牙,治具,反转治具能代替空站)7.在设计连续模时,必须要有检知开关装置及最后一站必须顺利脱料.8.在第一工程图面OK出图后,应填写请购单,注明材料规格,数量,以便资材备料.9.试模OK后,设计者应立即做移交清册(需向钳工索取试模记录)10.试模期间,设计者需参与试模.11.冲模设计自主检表见(附件3)二,下料,切边,冲孔注意事项1.切边线冲孔或下料冲孔其外侧距模板边缘应有45-50mm之距离.以确保模具强度,此距离并非任何厚度之冲材均适用,相对而言冲材越厚边距越大.2.冲ψ2以下小孔(spot凸点除外),下模需加装模套(衬套),以避免模板堵屑难以处理.其剥板与夹板皆须考虑B型ψ4行之,W/C时剥板滑配,夹板紧配.3.冲小孔时,冲头零件请购时可多请2-3支,以防冲头断裂时可更换.4.ψ2以下之孔时,在冲头上方加装止付螺丝, 以便线上更换.5.下规条在摆设时须主废料取出方便,并应防止人为疏忽而造成屑孔遮蔽,导致模板爆裂.另折弯,箱曲,抽型等模具.其规条最佳摆放位置为折块下方.6.切边冲头在刀口对面须要有挡块,以避免单边切料时,对面产生刀口重叠现象.7.冲孔当冲压件须有各种形状之孔时即可用冲孔冲完成,一般间隙设定冲子(±0),夹板(0.005-0.01),剥板(0.015-0.02),下模(冲制料厚50%).夹板与垫板如无特别要求,一般圆孔均彩钻订加工,有夹持作用者线割单边+0.005,有排屑作用者单边+0.5.8.引导孔一般采用于连续模,目的在于确定料带在一Pitch上冲制时不至于偏离,其顶端为圆锥状,可以导正料带,一般间隙下模(±0)引导冲单0.015,使用时应注意引导冲直线部漏出剥板是否正确.9.抽芽孔,一般分为两种做法,如下解说:9.1 一次抽芽孔时,其凸破点之余料,常因磁性问题导致余料附眷于母模面, 冲子或是因为凸破刀口不锋利而致废料留于成品上.所以一般一次抽之做法很少使用.9.2一冲孔二抽孔作法虽然二次,但可以保证成品或模板上无余炎问题,此做法比一次要好很多.9.3抽芽孔冲子与母模间隙单边为材料70%9.4抽芽冲子因R角及凸破点问题,故长度比冲孔冲头加长3mm.9.5.一般使用芽孔规范(见附件4)10.热处理.模具上所使用之钢材无论材,均有一定的规范,以保证模具寿命,一般热处理均将前置动作完成,避免热处理后难以加工. (热处理硬度规范见附件5)三, 展开图面要求1.图面要求a.展开图面中必须含产品图中的所有内孔,内部成型和外部成型的展开的像素b.展开图面的毛刺面必须向下.c.所有冲裁尖角(除特殊要求外)均要倒圆角(R=0.3)d.展开图中除圆孔外所有圆元必须串联成复线e.冲凸和冲桥形应进行局部剖视(剖视方向只能向左或向上),有较复杂折弯时应尽量出局部断面图表示成形以后的断面形状,并用英文批注为:PRODCT IMAGE…" 在展开主视图中的表示方法同剖视一样(在展开图上的长度是展开后是长度,所以小折弯不能画成的形式,只能画为对应示意图)2.折线画法(详见第一章展开图的画法11.说明:第四条,第五条,第六条均见组立部份四,注意事项抽芽抽芽孔尺寸计算原理为体积不变原理,即抽芽孔前后材料体积不变, ABCD 四边形面积=GFEA 所围成的面积,一般抽孔高度不深取H=3P (P 为螺纹距离,) R=EF见图因为T*AB=(H-EF)*EF+π*(EF)2/4所以AB={H*EF+(π/4-1)*EF}T所以预冲孔径=D-2AB当T≤0.5时,取EF=100%T0.5< p="">当R≥4mm时材料厚度T=1.2~1.4 取Hmax=4TT=0.8~1.0取Hmax=5TT=0.7~0.8取Hmax=6TT≤0.6 取Hmax=8T当R<4mm时,请示上级附件一. 常见抽芽预冲孔径一览表型料厚0.60.81.01.21.51.6M31.51.82.02.2M41.82.02.22.43.23.6#6-321.51.82.02.22.83.61.以上攻牙形式均为无屑式抽芽高度一般均取H=3P, 为P螺纹距离(牙距) 卷圆压平L=A-T+B-T+4K=A+B-2T+4*0.4T=A+B-0.4T(上式中:取K=0.4T)图三:900折弯处尺寸为A+0.5K图四:卷圆压平时,可视工程排配的情况考虑是否在折成900前压线位置为A-T侧冲压平L=A-T+B-T+4K=A+B-2T+4*0.4T=A+B-0.4T图三:900折弯尺寸为A+2K图四:侧冲压平时,在折成900前必须压线,压线位置为A-0.5K13.综合计算如图:L= 料内+ 料内+ 补偿量= A + B + C + D+ 中性层弧长( AA+ BB + CC )(中性层弧长均按"中性层到板料内侧距离λ=T/3计算:个人设计流程一,观察产品图先熟悉产品结构,了解产品材料材质厚度及其生产量以决定模具结构和模板材质!二,展开产品图展开方法: 1, 内寸法:主要用于直角折边2, 中立面法:主要用于折异形和有内R 的折边3, 反折压平法:用于反折压平展开图展开后,检察确定无误后,即可根据产品外形结构来排工序! 三,工序设计1,细致考虑此产品结构需几个工程,定出程数思考要领:一工程一般为下料,就是复合模了,还可以加入一些冲孔,补强等补强设在一工程可以防止拉料导致产品变形.抽牙和沙拉分一次和二次成型,由于一次成型效果不很好,所以最好使用二次成型,可以在一工程预冲抽牙孔或沙拉孔;后面的工程一般都是折弯模,根据产品外形确定折弯方法即可.确定好每一工程以后,下一步骤就是开模了四,开模步骤:1,插入展开图或半成品图2,根据产品展开尺寸和规格模板尺寸确定实际模板大小3,确定五金零件位置及大小,确定模具结构4,弄清楚每块模板上孔的大小,位置,画模板图5,后期处理:标注尺寸文字注解插入图框过程中需注意的问题:复合模: 1,冲剪模模板边缘距剪切边缘之距离应为40MM以上2,冲子需切入下模一个料厚以上3,计算剥料力和弹簧类型及数量,决定行程长,防止脱料不顺4,漏料孔的大小要足够防止漏料不顺5,间隙问题考虑周全以防止过紧,过松和产品毛边折弯模:1,根据产品结构决定折弯方向,是向上还是向下2, 折弯块要有挡块或用折弯块固定槽以防止因产品抗折而出现"折不起"的现象3, 要求严格的产品需设计滚轮折弯块之R角需研磨光滑以防止产品裂痕和擦伤4, 在折弯时如遇到抽牙和折边无法避位时需设计滑块需注意问题当然远远不止这些,还有很多需要通过工作实践去思考,研究,解决!第四篇备料第一条模具各站工作步骤与方法一.备料可分为画线,铣床点孔或图面钉孔,基三种各有不同.1.画线,用于一般模具其模具内小孔少,为避免小孔破孔用.2.铣床点孔,用于模具内小多且无法于画线台上一次完成的模板.3.图面钉孔,模具内无小孔,但需注意图面比例是否正确.4.ψ2.40以下的孔径,彩细孔放电,但模板表面必须利用ψ1之中心钻,把中心定出约1m/m利用放电加工.5.ψ2以下的孔径(含2),如孔娄众多且集中,则采用细孔放电,避免人为因素导致线割破孔,步骤同上,如零散之ψ2孔应试眷提长各人能力,采用ψ1.2钻头钻孔,如无法达成则细孔放电.6.ψ3以上的孔径(含ψ3),一律采用ψ1.5-ψ2钻头钻孔,单边约留0.4-0.5做线割用即可,小的导型孔亦比照办理7.其它大的导型孔或ψ孔,视工作物状况,钻头选择不应大于3m/m.8.一般圆孔之穿线孔皆为ψ中心,但ψ径大于25以上穿线孔则选择为ψ径外圆往里推5m/m,取为穿线孔中心.圆往里推5m/m,取为穿线孔中心.二.沈头孔1. M5螺丝,先ψ5.3孔M5沉头铣刀钻7m/m深2. 1/4"与M8螺丝,先孔ψ7孔M6沉头刀钻8m/m深3. 5/16"与M8螺丝,先孔ψ8.5孔M8沉头铣刀钻10mm深4. 3/8"与M10螺丝,先孔ψ孔10.5孔M10沉头铣刀钻12mm深5. 1/2"与M12螺丝,先孔ψ12.5孔M12沉头铣刀钻14mm深6.步骤: a.先孔b.沉头c.倒角三攻芽1.M4螺丝攻,模板ψ3.2-3.4先孔,手绞垂直度和逃屑情形.2.M5螺丝攻,模板ψ4.1-4.3先孔,手绞垂直度和逃屑情形.3.M6螺丝攻,模板ψ5-5.3先孔,手绞垂直度和逃屑情形.4.M8螺丝攻,模板ψ6.8-7先孔,可在旋臂钻床上绞孔亦应注意逃屑情形.5.M10螺丝攻,模板ψ8.5-8.8先孔,可在旋臂钻床上绞孔亦应注意逃屑情形.6.M12螺丝攻,模板ψ10.5-10.7先孔,可在旋臂钻床上绞孔亦应注意逃屑情形.7.M16螺丝攻,模板ψ14-14.2先孔,手可在旋臂钻床上绞孔亦应注意逃屑情形.8.M20螺丝攻,模板ψ17.5先孔,可在旋臂钻床上绞孔亦应注意逃屑情形.9.3/16螺丝攻,模板ψ4先孔,手绞并应注意垂直度和逃屑情形.10.1/4螺丝攻,模板ψ5.4先孔,手绞并注意垂直度和逃屑情形.11.5/16 螺丝攻,模板ψ6.8先孔,可在旋臂上绞孔,并应注意垂直度和逃屑情形.12 3/8 螺丝攻,模板ψ8.3先孔,可在旋臂上绞孔,并应注意垂直度和逃屑情形.13.5/16 螺丝攻,模板ψ10.5先孔,可在旋臂上绞孔,并应注意垂直<></c<5t时(一次成型)<></r</r。
5.4合模装置

2019年4月17日
合模类型的比较
合模形式与能耗 一般而言合模装置决定了注射机的总能耗。 液压式远大于肘杆式。 合模形式与成本 中小型的液压式高于肘杆式的。 合模形式的调整与维护 液压式的通过改变工作油的压力,可以方便 地调整,并易于读取。肘杆式则需要设置特 殊的调整装置和测力装置
三、顶出装置
顶出的作用?
2019年4月17日
顶出装置的种类
1)机械式顶出装置 2)液压式顶出装置 3)气动式顶出装置
2019年4月17日
液压式顶出装置最常用
顶出位置可选,行程可调,顶出次数可随意。 力量足够,速度合适。
2019年4月17日
四、合模类型的比较
考虑因素: 合模形式与制品尺寸精度在合模力相同和 工艺条件相似条件下,制品的尺寸精度在 很大程度上取决于合模装置的刚性。就一 般而言,肘杆式合模装置的刚性大于液压 式。但液压式的稳定性好。精密注射常用 液压式。
2019年4月17日
单曲肘合模装置
2019年4月17日
特点:
结构简单,外形尺寸小,制造容易。 增力作用小(10倍左右)承载能力受结构 限制作用大。 主要用于1000kN以下小型机上。
Ψ
P1
α
Po
2019年4月17日
P2
β
Pm
2 )双曲肘合模装置( 又称对称型)
组成:模板,拉杆,双曲肘机构,顶出和 调模装置,移动油缸等。 特点: 增力作用大 机械机构复杂 模板行程较短
2019年4月17日
解决双曲肘机构行程短的方案:
改变肘杆的运动方向将后杆向外侧翻转 将固定模板和肘杆连接交节改为活动交节
合模导向及抽芯机构设计
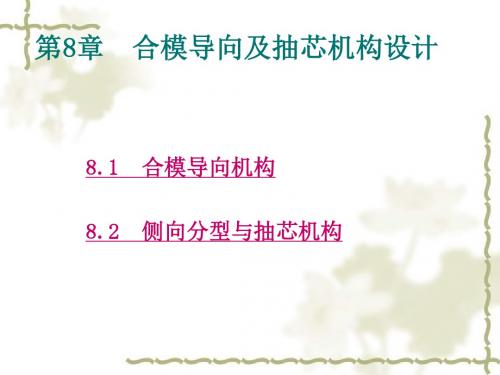
s1
r R
式中 S——抽芯距; S1——抽芯距极限尺寸; R——塑件外形; r——塑件外形小径;
s2
图5-61 半模抽芯距
5.3.2
斜导柱分型与抽芯机构
(一).斜导柱分型与抽芯机构 特点:结构简单、制造方便、安全可靠、应用 广泛等特点。 工作原理如图5-62所示 1.斜导柱的设计 (1)斜导柱的结构如图 (2)斜导柱倾斜角a的确定 斜导柱倾斜角a与斜导柱所受的弯曲离抽拔力 开模力等有关的重要参数,从受力图上可知如图564。
[σ]—许用弯曲应力 因斜导柱断面为圆形,故断面系数为 d 3 3
W 32 0.1d
(5-15)
代入(5-11)式即可计算斜导柱直径:
d 3 M PI 3 0.1 0.1
(5-16)
5.3.2
斜导柱分型与抽芯机构
2.滑块与导滑槽的设计 (1)侧型芯与滑块的连接形式(如图5-66) (2)侧型芯的结构(如图5-67) (3)滑块限位肩的位置(如图5-68) (4)滑块的导滑形式 滑块与导滑槽的配合形式(如图5-69) 锥面定位的滑块导滑槽(如图5-70) (5)滑块长度与导滑槽长度 注意:滑块长度与导滑槽长度之比一般为3:2滑块的 滑动长度应大于滑块高度,否则易歪斜,造成运动不 畅或卡滞(如图5-71)局部延长导滑板(如图5-72)
行程
1 2 3 4 5 6
行程
行程
1 2 3
1 2 3
图5-73 滑块的定位装置
a)
b)
c)
d)
图5-74 楔紧块的形式
e)
f)
g)
α
α′
图5-75 楔紧块的楔角
5.设计中的一些其它问题
(1)斜导柱倾斜角必须与滑块上斜孔 的斜角一致(如图5-76),滑块斜孔直径一 般比斜导柱直径大0.5-0.8毫米斜导柱伸入 滑块深度要合适(如图5-77)。 (2)滑块与导滑槽的配合关系一般采用 H7/f7或h7/e6。
5.4 合模装置

合模力
Pcm
D
4
2
p0 10
1
(5 - 12)
式中:Pcm — 锁模力(KN) p。— 油压(MPa) D — 活塞直径(cm)
14/60
移模速度
Q V 2 D /4
(5 - 13)
式中:Q — 合模时对油缸的供油量(升/分) V — 移模速度(米/秒)
15/60
② 增压式合模装置
27/60
⑦ 液压—抱合螺母式合模装置
图5-42 液压—抱合螺母式合模装置 6-移模油缸 5抱合螺母 4-移动模板 3-阳模 2-阴模 1-锁紧油缸
28/60
5.4.2.3 液压—机械式合模装置
液压-机械式合模装置由液 压系统和肘杆机构两部分组成。 最常用的是移模油缸或稳压油 缸与肘杆机构组成的串接式合 模装置,兼有液压式和机械式 合模装置速度快、自锁、节能 等优点。
Lt L1 L2 Lm H3 H3 A nFt F1 F2 Fm 48J 1 48J 2
杆长比
L1 L2
E 2 F L1 1 0 2 2A
38/60
图5-46 F —α关系曲线
39/60
活塞杆推力
sin F0 P2 sin
式中:
Lt —— 拉杆长度
Lt —— 拉杆变形量
Lc —— 受压零件的总长度
Lc —— 受压零件的总变形量
37/60
锁模力
F
EL1 1 cos 0 L2 1 cos 0 Lt L1 L2 Lm H3 H3 nFt F1 F2 Fm 48J 1 48J 2
液压控制系统的主要回路
合模装置

前者以缩短冷却时间为主要方向,后者主要提高开 闭模速度。一般而言,肘杆式的易实现高速平稳 变速。液压式升压时间长,动作切换次数多。 合模形式与能耗 一般而言合模装置决定了注射机的总能耗。液压式 远大于肘杆式。 合模形式与成本 中小型的液压式高于肘杆式的。 合模形式的调整与维护 液压式的通过改变工作油的压力,可以方便地调整, 并易于读取。肘杆式则需要设置特殊的调整装置 和测力装置
当曲肘机构合紧处于一直线排列时: 总变形 Pcm Pcm L0 L p L k ZC p C k
1 1 Pcm ( ) ZC p C k
即: Pcm=C* ∆Lo 式中:C为系统的总刚度 Ck
Pcm C
1/C= 1/(Z*Cp)+1/
在注射时,由于有胀模力的存在,使得最终的 琐紧力(Pz)比合模力(Pcm)要大。
L p
ZEF p
也可写为: Pcm Z * C p * L p 式中:Lp-----拉杆长度 Fp------拉杆截面积 ∆ Lp------拉杆变形
Pcm-----合模力 E------ 拉杆材料弹性模量 Z------拉杆数 Cp-----拉杆刚度,Cp=E*Fp/Lp 同理受压杆的变形:
第一节合模装置工作过程的特征
一基本的概念: 合模力(Pcm):合模终结时,模板对模具形成的 锁紧力 锁模力(Pz):在合模终结当熔料注入模腔时,模 板对模具形成的锁紧力。 变形力(Pc):在锁紧模具过程中,机构由于变形 而产生的内力。 移模力(Pm):在启闭模时,对动模板的作用力
胀模力:因熔料模腔压力作用,而产生欲 使模具分开的力。 二 液压式合模装置基本特征 依靠液体压力经油缸活塞直接实现模具的 合紧。 2 3 Pcm D0 P0 10 1 合模力: 4 Pcm----合模力(kN) Ds -----合模油缸直径(m) Po-----工作油压力(MPa)
连续模 级进模 金典结构及各零件的加工方法和作用《图解》

上垫脚上模座上垫板上夹板下模板下垫板下模座下垫脚连续模上面各模板的功用在前面已经基本介绍过,综合为表九:一、上垫脚组装螺丝(1):螺丝①在上垫脚板(上托板)正面沉头,由垫脚正面攻牙深15.0-20.0左右。
用来锁上垫脚板和垫脚使之紧固。
而上垫脚板、上垫脚和模具之间的联结是靠螺丝(2)来实现的。
其加工方式是上垫脚板沉头、上垫脚钻通孔、上模座正面攻牙。
上垫脚上通常有两种孔:正面攻牙孔和钻通孔;就是锁螺丝(1)和通过螺丝(2)的。
二、压料脱料顶料、脱料组件(7)(8)(9)(10)(75):这种脱料形式在复合模中已经提到,只是复合模用的是空板,这里用的是塞打螺丝(9)固定。
其组装和工作方式是:在上垫脚板反面攻牙,来锁塞打螺丝或是套筒螺丝组件。
通过调整塞打螺丝来实现打板(75)对弹簧(8)或优力胶(9)的预压。
弹簧(7)或优力胶(8)是平放在打板(75)和上垫脚板之间的,打板是靠塞打螺丝(9)来防止其横向位移的,而塞打螺丝在打板上是过孔,加工方式是钻出。
打杆在各板的加工方式均为钻出。
当上下合模时,脱料背板顶起打杆(10)通过打板(75)对弹簧(8)实现压缩;当上下分模时弹簧(7)的反作用力就会通过打板释放,将打杆(10)向下顶出,将力传递到脱料背上,从而实现了合模时的压料和分模时脱料的作用。
顶料脱料组件(42)(43)(44):这种压料、卸料方式是通过等高套筒螺丝组件在分模合模时的上下行程来压缩释放弹簧(43)的力,用止符螺丝(42)来调节弹簧的预压和承载弹簧力。
加工方法是:上模座正面攻止符螺丝牙,底孔钻穿;上垫板钻D+10孔,在上垫板和上模座中放弹簧(43);上夹板和脱料背板钻套筒过孔D+4;脱料板正面攻牙。
此种压料脱料方式有时会在螺丝的杯头上放置弹簧豆;或是加垫片用螺丝杯头来导正弹簧。
三、上模的固定:上模螺丝(11):其功用是紧固上模各板,使之联结,加工方式是:上模座正面钻沉头;上垫板钻D+1螺丝过孔;上夹板正面攻牙,常用螺丝大小:M8、M10.合模销(51):防止上模各板的横向位移,保护冲头。
XS_ZY_120A塑料注射成型机合模装置的设计

文章编号:1005-2895(2001)04-0033-03XS -ZY -120A 塑料注射成型机合模装置的设计高秀兰 (宝鸡文理学院机械工程系,陕西宝鸡721007) 摘 要:介绍了XS -Z Y -120A 型塑料注射成型机合模装置的设计,主要包括其主要功能结构、工作原理、模板距离调节机构、推出机构及其液压系统,并分析了其优缺点。
关 键 词:塑料注射机;液压—单曲肘合模装置;推出机构中图分类号:T Q 320.66+2 文献标识码:B收稿日期:2001-07-02作者简介:高秀兰(1965-),女,陕西扶风县人,宝鸡文理学院讲师,工学学士,主要研究方向为机械设计,CA D/CA M.1 引 言在塑料注射成型机中,合模装置的设计是否合理,关系到成型模具能否可靠地闭锁、开启;方便、可靠地取出塑料制品;以及塑料注射成型机生产率的提高。
可见,合模装置的设计在塑料注射成型机的设计中占据着比较重要的地位。
2 XS -ZY -120A 型塑料注射成型机的工作原理注射成型机的示意图如图1所示。
注射成型机的注射过程由三个阶段组成:呈粒状的塑料原料被输送机送到料斗9中,再落入料斗出口处的螺杆8内,然后被螺杆连续均匀地向前输送。
螺杆在输送物料的过程中,逐渐压实物料,并在料筒外加热和螺杆剪切热的作用下,将物料加热到粘流态。
粘流态的塑料被螺杆推送到螺杆头部积聚,压力逐渐升高。
当此压力升高到一定值时,压力阀换向,注射油缸11的活塞退回,带动螺杆后退,对螺杆头部物料进行计量。
螺杆退回到一定位置,其头部的熔料增多到所需的注射量时,限位开关动作,使螺杆停止后退和转动,预塑完毕。
同时,合模机构在合模油缸的推动下移动动模5使模具闭合,整个注射座也前移,使喷嘴对准模具的主浇道口。
然后,注射油缸切换,带动螺杆按要求的注射压力和注射速度将熔料注入到模腔内。
注射完毕,就完成了第一阶段工作。
第二阶段是保压。
在熔料充满模腔后,螺杆仍然不图1 注射成型机示意图1-顶杆固定板 2-顶出底板 3-动模安装板4-顶杆 5-动模 6-定模 7-定模安装板8-螺杆 9-料斗 10-电机 11-注射油缸停地转动,不断向模腔内补充制品冷却收缩所需要的物料,保持熔料一定的压力,防止模腔中熔料可能产生的反流。
- 1、下载文档前请自行甄别文档内容的完整性,平台不提供额外的编辑、内容补充、找答案等附加服务。
- 2、"仅部分预览"的文档,不可在线预览部分如存在完整性等问题,可反馈申请退款(可完整预览的文档不适用该条件!)。
- 3、如文档侵犯您的权益,请联系客服反馈,我们会尽快为您处理(人工客服工作时间:9:00-18:30)。
作者简介:刘俊萍(1957-),女,山东章丘人,副教授,本科,研究方向:塑料成型机械。
收稿日期:2008-11-24;修回日期:2009-02-040引言采用注射方法成型塑料制品的过程中,合模装置是个很重要的部件,它的作用是保证成型模具可靠地闭合、开启、顶出制品。
合模装置性能的好坏,直接关系到塑料制件的质量和数量。
锁模装置的种类较多,主要有液压式(直压式)和肘杆式(机械式)两大类型。
肘杆式又分单曲肘式和双曲肘式,双曲肘合模装置以其结构对称、增力作用大、模具承受的合模力均匀对称,在国内外注射机上得到广泛应用;目前的一些大型注射机上也用这种合模装置。
双曲肘机构按曲肘的铰链数可分为四孔型和五孔型;按曲肘排列位置又分为斜排列和直排列。
目前采用最多的是五孔斜排列形式,具有较紧凑的结构[1]见图1。
1问题的提出和解决合模装置设计过程中,会遇到一些比较棘手的问题,看起来是数学计算问题,但是解其过程却很复杂。
通过对问题的思考和分析,采用图解法与计算法相结合的方法,可使问题得到圆满解决。
1.1求机构最大初始角设计中的动模板行程S m 为给定的见图2,综合考虑机构具有较小的轴向尺寸、较大的增力作用、较高的运动速度和平稳变速后,确定了各杆件的尺寸和合模时机构的位置,即L 1、L 2、L 4、L 5、γ、e 、e D 均已确定,现在需要求出开模时的最大初始角αmax 。
机构在某一位置时,模板行程S m 可表达为:S m =L 1+L 2 cos θmin -L 1cos αmax +L 22-L 21sin 2αmax %姨姨姨cos θmax .(1)其中:sin θ=eL 1cos α+L 22-L 21sin 2α%姨%.(2)模板行程S=315mm 为已知,如何求得机构的最大起始角αmax ,如将S 代入式(1)求αmax 是很困难的。
这里采用AutoCAD 作图解决,可以很快初步确定αmax ,作图过程见图2。
具体做法如下:1)按比例绘制出合模状态下的机构简图。
2)将行程315mm 分为5等分,从闭模状态开始逐个画出各杆件对应的确定位置,最后达到开模位置,可得杆1的两个极限位置的夹角,即是最大起始角αmax ,同时也得到了移模油缸的行程S 0与不同位置对应的诸多角度。
3)把αmax 代入式(2)计算出θ,再代入式(1)计算出S m 。
4)如果计算出的S m 与已知的行程相等,说明作图得到的αmax 为真实的最大初始角;如果二者不等,可在作图得到的αmax 値左右调整α,重新计算θ,再代入式(1)计算S m ,直至与给定的行程相符为止。
本设计将作图得到的αmax 带回式(2)、式(1),经计算得到S m =314.82mm ,相对误差仅为0.057%,所以图解法在合模装置设计中的应用刘俊萍(太原理工大学机械工程学院,山西太原030024)【摘要】合模装置是塑料注塑成型设备中的重要机械设备,作用是保证成型模具可靠地闭紧、开启、顶出制品。
在注塑机合模装置的设计中,采用AutoCAD 作图和计算相结合的方法来解决较为复杂的数学问题,从而达到高效和准确之目的。
【关键词】合模装置;图解法;分析【中图分类号】TB21【文献标识码】A 【文章编号】1003-773X (2009)03-0003-02图2运动行程与各参数的图解图第24卷第3期(总第108期)机械管理开发2009年6月Vol.24No.3(SUM No.108)MECHANICAL MANAGEMENT AND DEVELOPMENTJun .20093··第24卷第3期(总第108期)机械管理开发2009年6月CAD的作图精度完全能够满足设计要求。
1.2求移模油缸最大推力p0max[2]肘杆、动模板、定模板、后固定模板、拉杆组成了一个封闭框架,合模时,移模油缸通过肘杆机构推动动模板前移,当动模与定模接触时,两肘杆尚未伸直为一直线,此时的α0称临界角。
肘杆继续运动,各构件产生弹性变形,动模板、肘杆受压,拉杆受拉。
机构变形力PC=f(α)为肘杆机构在锁紧模具过程中,因系统发生弹性变形而形成的实际锁紧力,它取决于合模机构变形量的大小,与杆件尺寸有关,呈二次抛物线。
封闭框架形成的预紧力可保证塑料熔体充模后动、定模不分离,从而使制品具有较高的精度。
变形力是移模油缸的负荷,合模时油缸推动肘杆机构,因机构有增力作用,产生移模力P m=f(α)克服变形力将模具锁紧,移模力Pm=f(α)是双曲线,移模力应大于变形力,这是肘杆机构正常工作的条件。
如果给定一组油缸推力值,就可画出一组移模力曲线(见图3),理论上只要P m=f(α)在PC=f(α)上方都可保证机构正常工作;但是过大的油缸推力不但使结构增大和移模速度减慢,同时还易造成超载事故;因此应求出油缸理论最大推力,再考虑机构效率,最后确定油缸实际推力。
合模时的油缸推力将随机构的放大能力的改变而改变,α′为移模力和变形力相等时所对应的角度,在α′~α0区间,由于变形力的增长速率大于机构放大后的移模力的增长速率,因此油缸推力P0从零逐渐增大。
而在α′~0区间侧相反,放大后的移模力的增长速率大于变形力的增长速率,油缸推力逐渐减小直至为零。
因此油缸推力有一个最大值,就在P C和P m相切的′之处。
计算式为:%PC =0.5L1·(1+λ)C·(α2-α2).%(3)由机构的放大倍数:M=PmP=L5sin(α+γ+φ+θ)cosθL1(1+λ)cosφsinα.(4)可得移模力:Pm=PL5sin(α+γ+φ+θ)cosθL1(1+λ)cosφsinα.(5)令PC=Pm,可得油缸推力:P=L21C(1+λ)2cosφsinα(α2-α2)2L5sin(α+γ+θ+φ)cosθ.(6)其中:sinφ=ed-L5sin(γ+α+θ)L4.(7)要得到P0的最大值,对式(6)求导,令d P/dα=0得到α′后,再代入式(6)求得P0max,但其计算过程复杂。
如果采用作图方法,只要寻找到两条曲线的切点,即可解决此问题,大大降低了难度。
具体过程如下:1)按比例分别绘制出Pc=f(α)和Pm=f(α)两条曲线。
2)将移模力曲线Pm=f(α)放在Pc=f(α)曲线的正上方,横座标严格对齐,上下移动Pm=f(α)曲线,两曲线相切处对应的角度即为要求的α′,代回式(6)求出P0max。
3)在初步确定的α′左右,再选出几个角度带入(6)式计算,直到求出真正的P0max。
2结束语以上两个实例虽是针对某一独特设计,但是这种借助CAD作图和计算相结合的方法,却是可以借鉴的,能为解决设计计算中出现的一些较复杂的数学问题,提供一种方法和思路:1)这种方法简单直观,可以化繁为简,能很快将寻找目标锁定在较小的范围内,省去了复杂的数学运算,从而提高效率。
2)在找到初步目标后,可以结合计算的方法,进行调整计算,使最后结果更加准确,从而满足设计要求。
参考文献[1]北京化工大学,华南理工大学.塑料机械设计[M].北京:化学工业出版社,1995.[2]邱宣怀.机械设计[M].北京:高等教育出版社,1997.图3P C-P m-P o关系图The Graphical Method Application in Close-Mold Device DesignLIU Jun-ping(College of Mechanical Engineering,Taiyuan University of Technology,Taiyuan030024,China)〔Abstract〕The close-mold device is the important set in the injection mold,it is used to ensure the process of closing,opening and ejecting the products.In the process of designing closed-mold device,the paper integrates AutoCAD with calculation to solve some complex mathematic problems and reach high efficiency and accuracy.〔Key words〕Closed-mold device;Graphical method;Analysis4··。