常见的镀膜术语和镀膜形式
镀膜是什么

镀膜是什么简介镀膜是一种表面处理技术,通过在物体表面上涂覆一层薄膜,以提高其性能和耐用性。
镀膜可以应用于各种材料和物体上,包括金属、塑料、陶瓷等。
它被广泛应用于工业、科学研究和日常生活中。
镀膜的目的镀膜主要有以下几个目的:1.增加耐腐蚀性:某些金属容易被氧化或腐蚀,通过镀上膜可以保护物体表面,延长使用寿命。
2.增加硬度和耐磨性:一些物体在使用过程中会受到磨损,镀膜可以提供额外的保护层,增加物体的硬度和耐磨性。
3.改善外观:镀膜可以改变物体的外观,包括颜色、光泽和质感,使其更具吸引力。
4.增加导电性和导热性:某些表面处理技术可以在物体表面形成导电或导热层,提高其导电性或导热性。
5.改善光学性能:镀膜可以改善物体的光学性能,如透过率、折射率和反射率,以满足特定的需求。
镀膜的常见类型常见的镀膜类型包括:1.金属镀膜:金属镀膜是将金属材料沉积在物体表面,常见的金属包括铬、镍、铜和铝等。
金属镀膜可以提供耐腐蚀和外观改善的功能。
2.阳极氧化膜:阳极氧化是将物体浸入电解液中,通过施加电流形成一层氧化膜。
这种膜能够提升耐耗性和硬度,常见于铝和钛等金属上。
3.真空蒸发膜:真空蒸发是将固态材料加热至其熔点,使其蒸发并沉积在物体表面。
这种方法常用于制作光学镜片和涂层等。
4.溅射膜:溅射是通过向固态材料加高能粒子施加电子束或离子束,使其从源材料中脱离并沉积于物体表面。
这种方法广泛应用于制造电子器件和薄膜太阳能电池等。
5.化学镀膜:化学镀膜是通过在物体表面形成一层化学反应产生的薄膜。
这种方法常用于改善物体的耐腐蚀性和外观。
镀膜的应用镀膜技术在许多领域有着广泛的应用,包括但不限于以下几个方面:1.汽车工业:镀膜可以应用于汽车的表面保护和外观改善。
例如,镀膜可以增加汽车车身的抗腐蚀能力,降低氧化和褪色的风险,并改善车身的光泽度。
2.建筑工业:镀膜可以用于建筑物外墙的涂料和涂层,以提高抗风化、耐腐蚀和防污能力。
此外,有些镀膜可以反射阳光,以提高建筑物的能效。
cvd或pvd镀膜原理
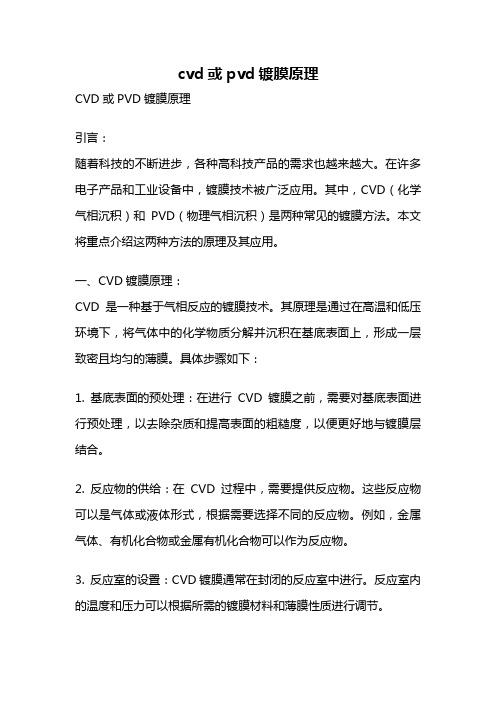
cvd或pvd镀膜原理CVD或PVD镀膜原理引言:随着科技的不断进步,各种高科技产品的需求也越来越大。
在许多电子产品和工业设备中,镀膜技术被广泛应用。
其中,CVD(化学气相沉积)和PVD(物理气相沉积)是两种常见的镀膜方法。
本文将重点介绍这两种方法的原理及其应用。
一、CVD镀膜原理:CVD是一种基于气相反应的镀膜技术。
其原理是通过在高温和低压环境下,将气体中的化学物质分解并沉积在基底表面上,形成一层致密且均匀的薄膜。
具体步骤如下:1. 基底表面的预处理:在进行CVD镀膜之前,需要对基底表面进行预处理,以去除杂质和提高表面的粗糙度,以便更好地与镀膜层结合。
2. 反应物的供给:在CVD过程中,需要提供反应物。
这些反应物可以是气体或液体形式,根据需要选择不同的反应物。
例如,金属气体、有机化合物或金属有机化合物可以作为反应物。
3. 反应室的设置:CVD镀膜通常在封闭的反应室中进行。
反应室内的温度和压力可以根据所需的镀膜材料和薄膜性质进行调节。
4. 反应过程:在反应室内,反应物会在高温下分解,并与基底表面上的活性位点发生反应,生成新的化合物。
这些化合物在基底表面沉积,逐渐形成一层均匀的薄膜。
5. 薄膜性质的调节:通过调节反应室内的温度、压力和反应物的浓度,可以控制薄膜的成分、结构和性质。
这些参数的调节可以实现对薄膜的硬度、抗腐蚀性、电学性能等特性的控制。
6. 后处理:在CVD过程结束后,需要对镀膜进行后处理,以去除残余的反应物和提高薄膜的质量。
这可以通过热处理、溶剂洗涤或化学处理等方法来实现。
二、PVD镀膜原理:PVD是一种基于物理过程的镀膜技术。
其原理是通过蒸发或溅射源,将固体材料转化为气体或离子态,并沉积在基底表面上,形成一层致密且均匀的薄膜。
具体步骤如下:1. 蒸发源或溅射源的选择:PVD镀膜过程需要使用蒸发源或溅射源来提供镀膜材料。
蒸发源可以是电子束蒸发源或电阻加热蒸发源,而溅射源可以是直流或射频溅射源。
pcb镀膜工艺技术
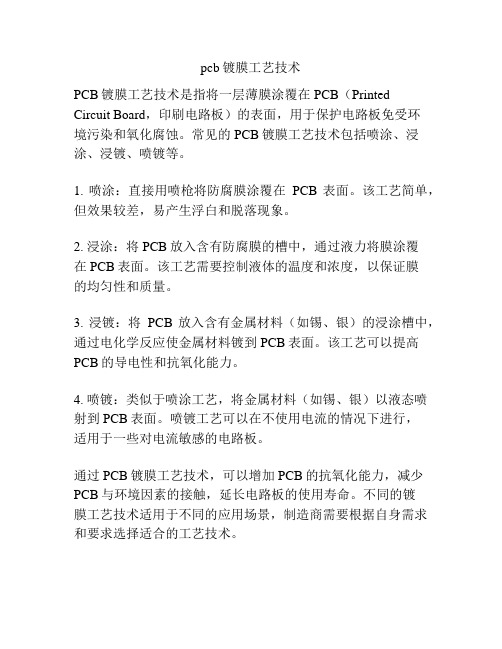
pcb镀膜工艺技术
PCB镀膜工艺技术是指将一层薄膜涂覆在PCB(Printed
Circuit Board,印刷电路板)的表面,用于保护电路板免受环
境污染和氧化腐蚀。
常见的PCB镀膜工艺技术包括喷涂、浸涂、浸镀、喷镀等。
1. 喷涂:直接用喷枪将防腐膜涂覆在PCB表面。
该工艺简单,但效果较差,易产生浮白和脱落现象。
2. 浸涂:将PCB放入含有防腐膜的槽中,通过液力将膜涂覆
在PCB表面。
该工艺需要控制液体的温度和浓度,以保证膜
的均匀性和质量。
3. 浸镀:将PCB放入含有金属材料(如锡、银)的浸涂槽中,通过电化学反应使金属材料镀到PCB表面。
该工艺可以提高PCB的导电性和抗氧化能力。
4. 喷镀:类似于喷涂工艺,将金属材料(如锡、银)以液态喷射到PCB表面。
喷镀工艺可以在不使用电流的情况下进行,
适用于一些对电流敏感的电路板。
通过PCB镀膜工艺技术,可以增加PCB的抗氧化能力,减少PCB与环境因素的接触,延长电路板的使用寿命。
不同的镀
膜工艺技术适用于不同的应用场景,制造商需要根据自身需求和要求选择适合的工艺技术。
镀膜基础必学知识点

镀膜基础必学知识点
以下是关于镀膜基础知识点的一些必学内容:
1. 镀膜的定义:镀膜是指在材料表面上通过化学或物理方法将一层物
质覆盖在其上,以改变材料的性质或外观。
2. 镀膜的目的:镀膜的主要目的是保护基材、增强其性能并改善外观。
3. 镀膜的分类:根据镀膜方法的不同,镀膜可以分为化学镀膜、物理
镀膜和电化学镀膜等。
4. 化学镀膜:化学镀膜是利用化学反应在基材表面生成一层无机或有
机物质的方法。
常见的化学镀膜有磷化、化学镀铜、化学镀镍等。
5. 物理镀膜:物理镀膜是利用物理原理将薄膜材料蒸发或溅射到基材
上形成膜层的方法。
常见的物理镀膜有蒸发镀膜、溅射镀膜和离子镀
膜等。
6. 电化学镀膜:电化学镀膜是利用电解液中的金属离子通过电化学反
应沉积在基材上形成膜层的方法。
常见的电化学镀膜有电镀铜、电镀镍、电镀铬等。
7. 镀膜的性能:镀膜可以提高基材的硬度、耐腐蚀性、耐磨性、导电
性等性能,从而延长其使用寿命。
8. 镀膜的应用:镀膜广泛应用于各个行业,如电子、机械、汽车、航
空航天等领域,常见的镀膜应用包括电子元器件镀膜、汽车零部件镀膜、模具镀膜等。
以上是镀膜基础必学知识点的一些内容,希望对你有所帮助。
汽车镀膜名词解释
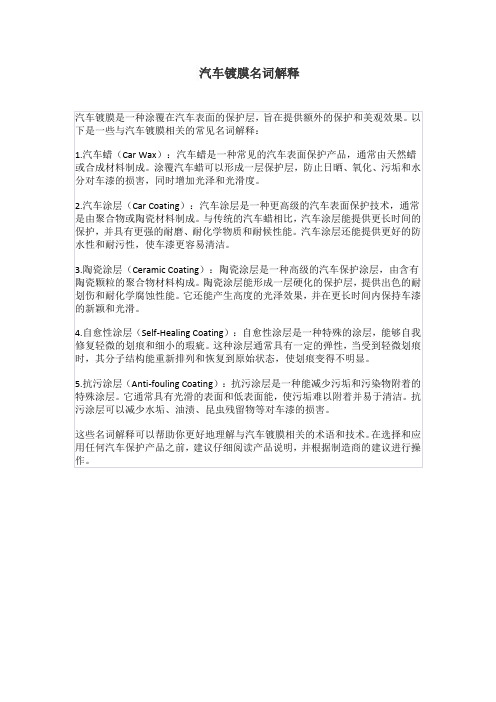
5.抗污涂层(Anti-fouling Coating):抗污涂层是一种能减少污垢和污染物附着的特殊涂层。它常具有光滑的表面和低表面能,使污垢难以附着并易于清洁。抗污涂层可以减少水垢、油渍、昆虫残留物等对车漆的损害。
这些名词解释可以帮助你更好地理解与汽车镀膜相关的术语和技术。在选择和应用任何汽车保护产品之前,建议仔细阅读产品说明,并根据制造商的建议进行操作。
2.汽车涂层(Car Coating):汽车涂层是一种更高级的汽车表面保护技术,通常是由聚合物或陶瓷材料制成。与传统的汽车蜡相比,汽车涂层能提供更长时间的保护,并具有更强的耐磨、耐化学物质和耐候性能。汽车涂层还能提供更好的防水性和耐污性,使车漆更容易清洁。
3.陶瓷涂层(Ceramic Coating):陶瓷涂层是一种高级的汽车保护涂层,由含有陶瓷颗粒的聚合物材料构成。陶瓷涂层能形成一层硬化的保护层,提供出色的耐划伤和耐化学腐蚀性能。它还能产生高度的光泽效果,并在更长时间内保持车漆的新颖和光滑。
汽车镀膜名词解释
汽车镀膜是一种涂覆在汽车表面的保护层,旨在提供额外的保护和美观效果。以下是一些与汽车镀膜相关的常见名词解释:
1.汽车蜡(Car Wax):汽车蜡是一种常见的汽车表面保护产品,通常由天然蜡或合成材料制成。涂覆汽车蜡可以形成一层保护层,防止日晒、氧化、污垢和水分对车漆的损害,同时增加光泽和光滑度。
电镀专业术语介绍
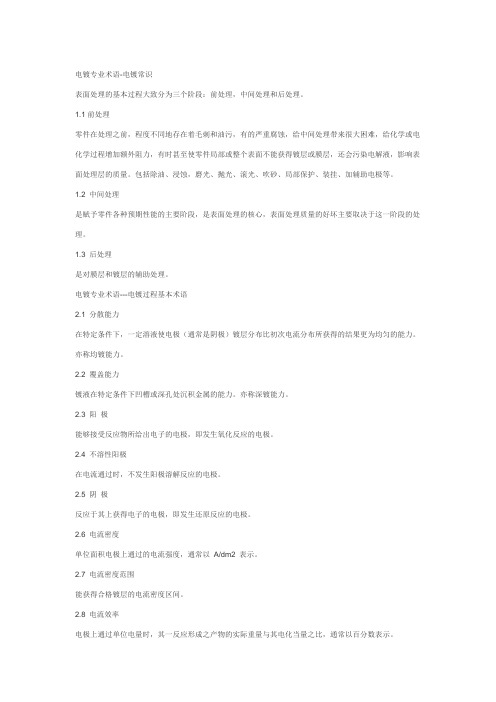
电镀专业术语-电镀常识表面处理的基本过程大致分为三个阶段:前处理,中间处理和后处理。
1.1前处理零件在处理之前,程度不同地存在着毛刺和油污,有的严重腐蚀,给中间处理带来很大困难,给化学或电化学过程增加额外阻力,有时甚至使零件局部或整个表面不能获得镀层或膜层,还会污染电解液,影响表面处理层的质量。
包括除油、浸蚀,磨光、抛光、滚光、吹砂、局部保护、装挂、加辅助电极等。
1.2 中间处理是赋予零件各种预期性能的主要阶段,是表面处理的核心,表面处理质量的好坏主要取决于这一阶段的处理。
1.3 后处理是对膜层和镀层的辅助处理。
电镀专业术语---电镀过程基本术语2.1 分散能力在特定条件下,一定溶液使电极(通常是阴极)镀层分布比初次电流分布所获得的结果更为均匀的能力。
亦称均镀能力。
2.2 覆盖能力镀液在特定条件下凹槽或深孔处沉积金属的能力。
亦称深镀能力。
2.3 阳极能够接受反应物所给出电子的电极,即发生氧化反应的电极。
2.4 不溶性阳极在电流通过时,不发生阳极溶解反应的电极。
2.5 阴极反应于其上获得电子的电极,即发生还原反应的电极。
2.6 电流密度单位面积电极上通过的电流强度,通常以A/dm2 表示。
2.7 电流密度范围能获得合格镀层的电流密度区间。
2.8 电流效率电极上通过单位电量时,其一反应形成之产物的实际重量与其电化当量之比,通常以百分数表示。
2.9 阴极性镀层电极电位的代数值比基体金属大的金属镀层。
2.10 阳极性镀层电极电位的代数值比基体金属小的金属镀层。
2.11 阳极泥在电流作用下阳极溶解后的残留物。
2.12 沉积速度单位时间内零件表面沉积出金属的厚度。
2.13 初次电流分布在电极极化不存在时,电流在电极表面上的分布。
2.14 活化使金属表面钝化状态消失的作用。
2.15 钝化在一定环境下使金属表面正常溶解反应受到严重阻碍,并在比较宽的电极电位范围内使金属溶解反应速度降到很低的作用。
2.16 氢脆由于浸蚀,除油或电镀等过程中金属或合金吸收氢原子而引起的脆性。
镀膜工艺技术

镀膜工艺技术镀膜工艺技术是一种将膜物质涂覆在工件表面的方法,使工件具有特定的性能或外观效果的技术。
镀膜工艺技术广泛应用于电子、航空航天、光学、汽车等领域。
一、镀膜工艺技术的分类根据涂覆物的不同,镀膜工艺技术可以分为化学镀膜、物理镀膜和电化学镀膜三种。
1. 化学镀膜技术化学镀膜是利用化学反应将膜物质溶解在化学溶液中,通过反应物分子在工件表面形成一层薄膜,从而改善工件表面的性能。
常用的化学镀膜技术有镀金、镀铬、镀镍等。
2. 物理镀膜技术物理镀膜是利用物理方法将膜物质蒸发或溅射到工件表面,形成一层薄膜。
常见的物理镀膜技术有真空蒸发、物理气相沉积等。
3. 电化学镀膜技术电化学镀膜是利用电解溶液中的阳离子在阳极处发生离子化,经过电场作用,将离子在阴极处还原,形成一层薄膜。
常见的电化学镀膜技术有镀锌、镀铜、镀锡等。
二、镀膜工艺技术的应用1. 保护性镀膜镀膜可以在工件表面形成一层保护性膜,防止工件与外界环境接触,延长其使用寿命。
例如,汽车零部件镀锌可以防止钢铁零件锈蚀,延长其使用寿命。
2. 装饰性镀膜镀膜可以使工件表面具有金属质感或其他特殊效果,提高其装饰性。
例如,首饰镀金可以使首饰更加闪亮、美观。
3. 功能性镀膜镀膜可以赋予工件特定的功能,如增加工件的导电性、耐磨性或降低摩擦系数等。
例如,光学镀膜可以使镜片具有优良的透光性和抗反射性能。
三、镀膜工艺技术的发展趋势1. 绿色环保化随着环保意识的提高,镀膜工艺技术向着绿色环保化的方向发展。
例如,采用无铬镀膜工艺替代传统的六价铬镀膜,可以减少对环境的污染。
2. 高效节能化工艺技术的不断创新,使得镀膜过程中的能源消耗大大减少,提高了工艺的效率和节能性。
3. 自动化智能化镀膜工艺技术在自动化和智能化方面的应用越来越广泛,大大提高了生产效率和产品质量。
例如,采用机器人来进行膜物质的涂覆,可以保证涂覆的均匀性和一致性。
总之,镀膜工艺技术是一项重要的表面处理技术,具有广泛的应用前景。
常用电镀技术的术语

常用电镀技术术语电镀技术常用术语一、电镀层种类1、硬铬在严格控制温度与电流密度(较装饰镀铬高)的条件下,从镀铬液中获得的硬度较高、耐磨性好的硬铬层。
2、乳色铬通过改变镀铬溶液的工作条件,获得的孔隙少、具有较高抗蚀能力、而硬度较低的乳白色铬镀层。
二、氧化及钝化1、阳极氧化通常指铝或铝合金制品或零件,在一定的电解液中和特定的工作条件下作为阳极,通过直流电流的作用,使其表面生成一层抗腐蚀的氧化膜的处理过程。
2、磷化钢铁零件在含有磷酸盐的溶液中进行化学处理,使其表面生成一层难溶于水的磷酸盐保护膜的处理过程。
3、发蓝钢铁零件在一定的氧化介质中进行化学处理,使其表面生成一层蓝黑色的保护性氧化膜的处理过程。
4、化学氧化在没有外电流作用下,金属零件与电解质溶液作用,使其表面上生成一层氧化膜的处理过程。
5、电化学氧化以浸入一定的电解质溶液中的金属零件作为阳极,在直流电作用下,使其表面生成氧化膜的电化学处理过程。
6、化学钝化在没有外电流作用下,金属零件与电解质溶液作用,使其表面上生成一层钝化膜的处理过程。
7、电化学钝化以浸入一定电解质溶液中的金属零件作为阳极,在直流电作用下,使其表面生成一层钝化膜的处理过程。
三、电解1、电解在外电流通过电解液时,在阳极和阴极上分别进行氧化和还原反应,将电能变为化学能的过程。
2、阳极电解以零件作为阳极的电解过程。
3、阴极电解以零件作为阴极的电解过程。
四、镀前处理1、化学除油在含碱的溶液中,借助皂化和乳化作用,除去零件或制品表面油垢的过程。
2、有机溶剂除油利用有机溶剂对油垢的溶解作用,除去零件或制品表面油垢的过程。
3、电化学除油(即电解除油)在含有碱的溶液中,以零件作为阳极或阴极,在电流作用下,除去零件或制品表面油垢的过程。
4、化学酸洗在含酸的溶液中,除去金属零件表面的锈蚀物和氧化物的过程。
5、化学抛光金属零件在一定组成的溶液中和特定条件下,进行短时间的浸蚀,从而将零件表面整平,获得比较光亮的表面的过程。
常用的镀膜方法

常用的镀膜方法
1.溅射镀膜法
溅射镀膜法是利用高能离子束轰击样品表面,产生的微小粒子将目标表面的物质释放出来,再沉积至基底表面,形成薄膜。
溅射镀膜法因其可在高真空下进行,所以适用于制备金属、半导体、氧化物及其他无机化合物薄膜。
此外,该技术还可用于制备具有特定性质的晶体结构薄膜,例如具有分子化合物的多层体系。
溅射镀膜法是当前常用的薄膜制备方法之一。
2.磁控溅射镀膜法
磁控溅射镀膜法也是一种广泛使用的薄膜制备方法,其原理同溅射镀膜法相似。
区别在于磁控溅射镀膜法使用磁场来控制离子束,从而增强溅射效率,提高沉积速度。
该技术适用于制备高品质的多层结构、重金属、氧化物和非晶态薄膜等。
3.化学气相沉积法
化学气相沉积法是通过将含有金属有机物等原料的气体送入反应室中,利用化学反应在基片表面上生长薄膜。
该技术适用于大面积,均一薄膜的制备。
化学气相沉积法可用于制备二氧化硅、硅胶、氮化硅、碳化硅等材料的薄膜。
4.热蒸发镀膜法
热蒸发镀膜法是利用高温加热金属或化合物材料,使之蒸发并沉积在基底表面。
该方法简便、容易操作,广泛应用于制备单层和多层金属薄膜,如铬、钼、铜、银和铝等金属薄膜。
此外,该技术还可用于制备非晶态薄膜,例如氧化铝薄膜、TiO2薄膜等。
5.电化学沉积法
电化学沉积法是将金属投入含有所需离子的溶液中作为阴极,通电后,溶液中的阳离子被还原成金属沉积在阴极表面上。
该技术操作简单,可制备所需厚度的纯金属或合金薄膜,并可控制薄膜的粗糙度。
电化学沉积法适用于制备黄金、银、铜等高纯度金属薄膜,也可用于制备复杂的多层材料和表面修饰。
镀膜工作原理
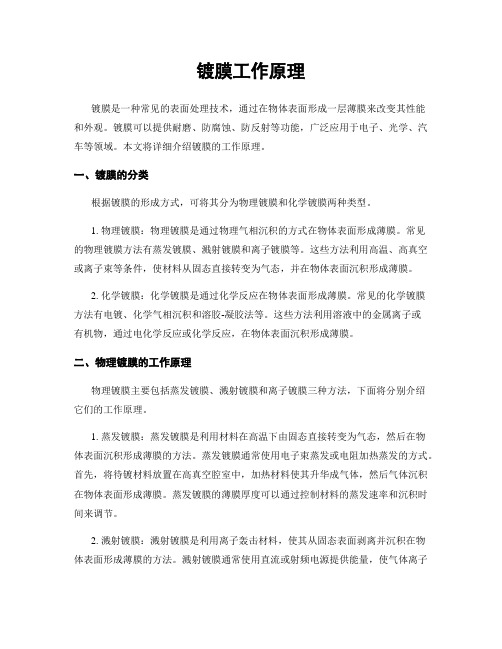
镀膜工作原理镀膜是一种常见的表面处理技术,通过在物体表面形成一层薄膜来改变其性能和外观。
镀膜可以提供耐磨、防腐蚀、防反射等功能,广泛应用于电子、光学、汽车等领域。
本文将详细介绍镀膜的工作原理。
一、镀膜的分类根据镀膜的形成方式,可将其分为物理镀膜和化学镀膜两种类型。
1. 物理镀膜:物理镀膜是通过物理气相沉积的方式在物体表面形成薄膜。
常见的物理镀膜方法有蒸发镀膜、溅射镀膜和离子镀膜等。
这些方法利用高温、高真空或离子束等条件,使材料从固态直接转变为气态,并在物体表面沉积形成薄膜。
2. 化学镀膜:化学镀膜是通过化学反应在物体表面形成薄膜。
常见的化学镀膜方法有电镀、化学气相沉积和溶胶-凝胶法等。
这些方法利用溶液中的金属离子或有机物,通过电化学反应或化学反应,在物体表面沉积形成薄膜。
二、物理镀膜的工作原理物理镀膜主要包括蒸发镀膜、溅射镀膜和离子镀膜三种方法,下面将分别介绍它们的工作原理。
1. 蒸发镀膜:蒸发镀膜是利用材料在高温下由固态直接转变为气态,然后在物体表面沉积形成薄膜的方法。
蒸发镀膜通常使用电子束蒸发或电阻加热蒸发的方式。
首先,将待镀材料放置在高真空腔室中,加热材料使其升华成气体,然后气体沉积在物体表面形成薄膜。
蒸发镀膜的薄膜厚度可以通过控制材料的蒸发速率和沉积时间来调节。
2. 溅射镀膜:溅射镀膜是利用离子轰击材料,使其从固态表面剥离并沉积在物体表面形成薄膜的方法。
溅射镀膜通常使用直流或射频电源提供能量,使气体离子化,然后加速离子轰击靶材,使靶材表面的原子或分子剥离,并沉积在物体表面。
溅射镀膜的薄膜厚度可以通过控制离子轰击能量和时间来调节。
3. 离子镀膜:离子镀膜是利用离子束轰击物体表面,使其表面原子或分子离开并沉积在物体表面形成薄膜的方法。
离子镀膜通常使用离子源产生离子束,并通过加速器将离子束加速到一定能量,然后轰击物体表面。
离子束轰击物体表面时,会激发表面原子或分子,使其从物体表面剥离,并沉积在物体表面形成薄膜。
常用的镀膜方法

常用的镀膜方法
镀膜是一种将金属或其他材料涂覆在另一种材料表面的工艺。
它可以提高材料的耐腐蚀性、硬度、光泽度和美观度。
以下是常用的几种镀膜方法。
1. 电镀
电镀是将金属离子通过电解沉积在基材表面的一种方法。
它可以制造出高质量、均匀的镀层,适用于各种金属和非金属材料。
电镀可以分为镀铬、镀镍、镀铜、镀锌等。
2. 热浸镀
热浸镀是将金属材料浸入熔融的金属中,使其表面形成一层金属涂层的方法。
它可以提高材料的耐腐蚀性和硬度,适用于钢铁、铜、铝等材料。
常见的热浸镀方法有热浸锌、热浸铝、热浸锡等。
3. 喷涂
喷涂是将涂料喷射到基材表面形成一层涂层的方法。
它可以提高材料的耐腐蚀性、防火性和美观度,适用于各种材料。
常见的喷涂方法有喷漆、喷粉、喷油漆等。
4. 化学镀
化学镀是利用化学反应在基材表面形成一层金属涂层的方法。
它可
以制造出高质量、均匀的镀层,适用于各种材料。
常见的化学镀方法有化学镀铜、化学镀镍、化学镀铬等。
5. 气相沉积
气相沉积是将金属蒸发后沉积在基材表面形成一层金属涂层的方法。
它可以制造出高质量、均匀的镀层,适用于各种材料。
常见的气相沉积方法有物理气相沉积、化学气相沉积等。
镀膜方法有很多种,每种方法都有其适用范围和特点。
在选择镀膜方法时,需要根据材料的性质和要求来选择最合适的方法。
光学镀膜基础知识

光学镀膜基础知识
光学镀膜是一种在物体表面上形成一层薄膜,以改变光在物体表面上的反射、透射和吸收的特性的技术。
它可以提高光学元件的透光率、抗反射能力和耐刮擦性能,同时还可以改变光的颜色和光谱特性。
以下是光学镀膜的基础知识:
1. 光学镀膜类型:有透射镀膜、反射镀膜和滤光镀膜等不同类型的光学镀膜。
2. 镀膜材料:常用的镀膜材料包括金属、氧化物、硫化物和氟碳化物等。
不同的材料可以实现不同的功能,如增强透射、减少反射、调节色彩等。
3. 镀膜原理:基本的镀膜原理是利用光学干涉的现象。
通过控制镀膜材料的厚度,可以实现不同波长光的干涉效果,从而达到改变光的传输和反射性能的目的。
4. 镀膜性能评价:光学膜层的性能评价常包括透射率、反射率、满足特定光学要求的光谱特性等。
5. 常见的光学镀膜技术:包括真空蒸发、溅射镀膜、离子镀膜等不同的技术。
每种技术都有其特点和适用性,选择合适的技术可以获得高质量的光学镀膜。
6. 应用领域:光学镀膜广泛应用于光学元件、光学仪器、电子
设备、眼镜等领域。
它可以改善光学仪器的性能,提高成像和传输质量,也可以实现特定的光学效果和功能。
总之,光学镀膜是一门复杂而重要的技术,通过掌握光学镀膜的基本知识,可以更好地理解和应用光学元件。
镀膜工艺方案

镀膜工艺方案背景介绍镀膜工艺是一种将金属材料或其他表面涂覆上薄膜的工艺。
镀膜工艺可以提高材料的表面硬度、耐腐蚀性、防磨损性、光学透过率等性能,从而改善材料的性能。
应用广泛,如在电子、航天、航空、医疗器械、机械制造等行业都有着非常广泛的应用。
镀膜工艺分类根据不同的镀膜材料和特点,可以将镀膜工艺大致分为以下几类:1.金属镀膜:包括镀铬、镀镍、镀金等常见的金属镀膜。
2.合金镀膜:包括合金化铬、合金化硝酸镍等。
3.陶瓷/氧化物涂层:包括氮化硅、碳化钨等。
4.光学镀膜:包括各种光学薄膜。
5.生物医用镀膜:如生物医用涂层。
主要工艺流程镀膜工艺的主要流程包括:基材表面处理、预处理、表面处理、镀膜、后处理等。
1.基材表面处理:对金属或其他材料进行清洗、去污、去油等处理,以保证表面无杂质,有利于后续工艺的进行。
2.预处理:对表面进行一些物理和化学处理,以提高表面的粗糙度。
3.表面处理:将表面经过活化处理,使其能够与膜材料结合到一起,实现膜材料的粘附。
4.镀膜:将膜材料通过各种方法,如物理气相沉积、化学气相沉积、电化学沉积等,沉积到基材上。
5.后处理:对镀膜进行检验、包装以及质量控制等相应的处理过程。
选择合适的镀膜工艺方案选用合适的镀膜工艺方案,不仅可以大幅提高材料的性能,还可以降低成本,提高生产效率,具有非常重要的意义。
在选择合适的镀膜工艺方案时,我们应该考虑以下几个因素:1.材料的特性:根据材料的特性,我们可以选择合适的镀膜材料以及合适的镀膜工艺。
2.镀膜各项性能的要求:比如硬度、耐腐蚀性、光学透过率等,我们要根据实际的要求进行对应的选择。
3.生产效率和成本控制:我们要平衡生产效率和成本控制,选择适合自己实际情况的工艺方案。
结论镀膜工艺方案是一个相对复杂的技术问题,在实际应用中需要根据实际情况做出合理的选择。
我们在进行镀膜工艺设计的时候,应该充分考虑到各种因素,以达到最佳的效果。
真空镀膜技术的一般术语
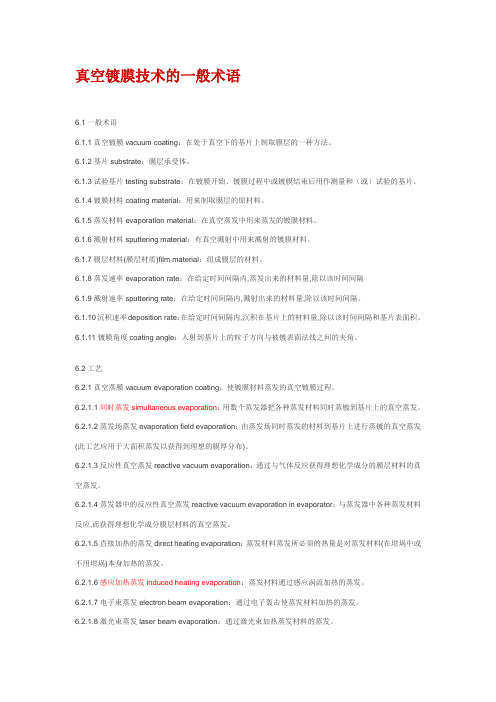
真空镀膜技术的一般术语6.1一般术语6.1.1真空镀膜vacuum coating:在处于真空下的基片上制取膜层的一种方法。
6.1.2基片substrate:膜层承受体。
6.1.3试验基片testing substrate:在镀膜开始、镀膜过程中或镀膜结束后用作测量和(或)试验的基片。
6.1.4镀膜材料coating material:用来制取膜层的原材料。
6.1.5蒸发材料evaporation material:在真空蒸发中用来蒸发的镀膜材料。
6.1.6溅射材料sputtering material:有真空溅射中用来溅射的镀膜材料。
6.1.7膜层材料(膜层材质)film material:组成膜层的材料。
6.1.8蒸发速率evaporation rate:在给定时间间隔内,蒸发出来的材料量,除以该时间间隔6.1.9溅射速率sputtering rate:在给定时间间隔内,溅射出来的材料量,除以该时间间隔。
6.1.10沉积速率deposition rate:在给定时间间隔内,沉积在基片上的材料量,除以该时间间隔和基片表面积。
6.1.11镀膜角度coating angle:入射到基片上的粒子方向与被镀表面法线之间的夹角。
6.2工艺6.2.1真空蒸膜vacuum evaporation coating:使镀膜材料蒸发的真空镀膜过程。
6.2.1.1同时蒸发simultaneous evaporation:用数个蒸发器把各种蒸发材料同时蒸镀到基片上的真空蒸发。
6.2.1.2蒸发场蒸发evaporation field evaporation:由蒸发场同时蒸发的材料到基片上进行蒸镀的真空蒸发(此工艺应用于大面积蒸发以获得到理想的膜厚分布)。
6.2.1.3反应性真空蒸发reactive vacuum evaporation:通过与气体反应获得理想化学成分的膜层材料的真空蒸发。
6.2.1.4蒸发器中的反应性真空蒸发reactive vacuum evaporation in evaporator:与蒸发器中各种蒸发材料反应,而获得理想化学成分膜层材料的真空蒸发。
离子镀膜分类

离子镀膜分类离子镀膜是一种常见的表面处理技术,通过将金属离子沉积到基材表面上,形成一层薄膜,以改善基材的性能和外观。
离子镀膜可以分为金属离子镀膜和非金属离子镀膜两大类。
一、金属离子镀膜金属离子镀膜是指将金属离子沉积到基材表面上,以增加其硬度、耐磨性和耐腐蚀性。
常见的金属离子镀膜技术有镀铬、镀镍、镀银等。
1. 镀铬镀铬是将铬离子沉积到基材表面上的过程。
镀铬可以提高基材的硬度和耐腐蚀性,使其具备更好的耐磨性和耐高温性能。
镀铬常用于汽车零部件、家电产品和装饰品等领域。
2. 镀镍镀镍是将镍离子沉积到基材表面上的过程。
镀镍可以增加基材的硬度和耐腐蚀性,同时还能提升其光泽度和装饰性。
镀镍广泛应用于汽车零部件、厨具、首饰等领域。
3. 镀银镀银是将银离子沉积到基材表面上的过程。
镀银可以使基材具备良好的导电性和抗氧化性能,同时还能提升其外观质感和装饰效果。
镀银常用于电子元器件、餐具、首饰等领域。
二、非金属离子镀膜非金属离子镀膜是指将非金属离子沉积到基材表面上,以改善其特定性能。
常见的非金属离子镀膜技术有氮化、氧化和碳化等。
1. 氮化氮化是将氮离子沉积到基材表面上的过程。
氮化可以增加基材的硬度、耐磨性和耐腐蚀性,改善其表面光洁度和抗氧化性能。
氮化常用于刀具、模具和机械零部件等领域。
2. 氧化氧化是将氧离子沉积到基材表面上的过程。
氧化可以形成一层氧化膜,提高基材的耐磨性、耐腐蚀性和绝缘性能。
氧化常用于铝制品、不锈钢和电子元器件等领域。
3. 碳化碳化是将碳离子沉积到基材表面上的过程。
碳化可以增加基材的硬度和耐磨性,改善其耐腐蚀性和导热性能。
碳化常用于刀具、轴承和机械零部件等领域。
离子镀膜技术在工业生产和科研领域中具有广泛的应用。
通过选择不同的离子镀膜技术,可以根据基材的不同需求,提升其性能和外观质量。
离子镀膜的发展也为许多产业提供了新的发展机遇,推动了相关行业的进步和创新。
随着科技的不断进步,离子镀膜技术也将不断完善和发展,为各行各业带来更多的机遇和挑战。
镀膜技术常用名词及英文对照

镀膜技术常用名词及英文对照1、真空镀膜:vacuum coating在处于真空条件下的基片上制取膜层的一种方法。
2、基片:substrate被镀膜的基体材料我们称之为基片,通常也叫做工件或试片。
3、镀膜材料:coating material用来制取膜层的材料,通常称之为靶材。
4、蒸发材料:evaporation material在真空蒸发中用来蒸发的镀膜材料。
5、溅射材料:sputtering material在真空溅射中用来溅射的镀膜材料。
6、膜层材料:film material称之为膜层介质,指组成膜层的材料。
7、蒸发速率:evaporation rate在给定的时间间隔内,蒸发出来的材料量,除以该时间间隔。
8、溅射速率:sputtering rate在给定的时间间隔内,溅射出来的材料量,除以改时间间隔。
9、沉积速率:deposition rate在给定的时间间隔内,沉积在基片上的材料量,除以改时间间隔。
10、镀膜角度:coating angle入射到基片上的粒子方向与被镀表面法线之间的夹角。
11、真空蒸镀:vacuum evaporation coating在真空条件下,使镀膜材料蒸发的真空镀膜过程。
12、同时蒸发:simultaneous evaporation用数个蒸发器把各种蒸发材料同时蒸镀到基片上的真空蒸发。
13、蒸发场蒸发:evaporation field evaporation由蒸发场同时蒸发材料到基片上进行蒸镀的真空蒸发。
14、反应型真空蒸发:reactive vacuum evaporation通过与气体反应获得理想化学成分膜层材料的真空蒸发15、感应加热蒸发:induced heating evaporation蒸发材料通过高频感应涡流加热的蒸发16、电子束蒸发:electron beam evaporation通过电子束轰击使蒸发材料加热的蒸发17、激光束蒸发:laser beam evaporation通过激光束加热蒸发材料的蒸发18、间接加热蒸发:indirect heating evaporation通过热传导或热辐射的方式传递热给蒸发材料的蒸发19、闪蒸:flash evaporation将极少量的蒸发材料间断的做瞬时的蒸发20、真空溅射:vacuum sputtering在真空中,惰性气体离子从靶材表面上轰出原子(分子)或原子团的过程21、反应性真空溅射:reactive vacuum sputtering通过与气体的反应获得理想化学成分膜层材料的真空溅射22、偏压溅射:bias sputtering在溅射过程中,将偏压施加于基片以及膜层的溅射23、直流二级溅射:direct current diode sputtering通过两个电极间的直流电压,使气体自持放电并把靶作为阴极的溅射24、非对称性交流溅射:asymmtric alternate current sputtering通过两个电极间的非对称性交流电压,使气体自持放电并把靶作为吸收较大正离子流的电极。
电镀术语
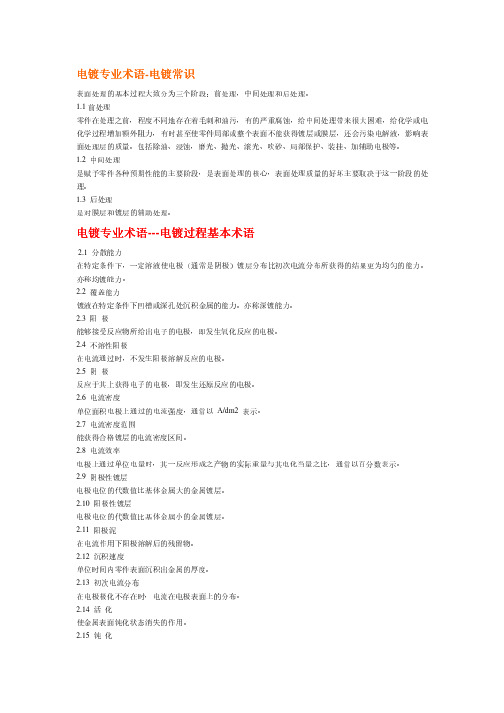
电镀专业术语-电镀常识表面处理的基本过程大致分为三个阶段:前处理,中间处理和后处理。
1.1前处理零件在处理之前,程度不同地存在着毛刺和油污,有的严重腐蚀,给中间处理带来很大困难,给化学或电化学过程增加额外阻力,有时甚至使零件局部或整个表面不能获得镀层或膜层,还会污染电解液,影响表面处理层的质量。
包括除油、浸蚀,磨光、抛光、滚光、吹砂、局部保护、装挂、加辅助电极等。
1.2 中间处理是赋予零件各种预期性能的主要阶段,是表面处理的核心,表面处理质量的好坏主要取决于这一阶段的处理。
1.3 后处理是对膜层和镀层的辅助处理。
电镀专业术语---电镀过程基本术语2.1 分散能力在特定条件下,一定溶液使电极(通常是阴极)镀层分布比初次电流分布所获得的结果更为均匀的能力。
亦称均镀能力。
2.2 覆盖能力镀液在特定条件下凹槽或深孔处沉积金属的能力。
亦称深镀能力。
2.3 阳极能够接受反应物所给出电子的电极,即发生氧化反应的电极。
2.4 不溶性阳极在电流通过时,不发生阳极溶解反应的电极。
2.5 阴极反应于其上获得电子的电极,即发生还原反应的电极。
2.6 电流密度单位面积电极上通过的电流强度,通常以A/dm2 表示。
2.7 电流密度范围能获得合格镀层的电流密度区间。
2.8 电流效率电极上通过单位电量时,其一反应形成之产物的实际重量与其电化当量之比,通常以百分数表示。
2.9 阴极性镀层电极电位的代数值比基体金属大的金属镀层。
2.10 阳极性镀层电极电位的代数值比基体金属小的金属镀层。
2.11 阳极泥在电流作用下阳极溶解后的残留物。
2.12 沉积速度单位时间内零件表面沉积出金属的厚度。
2.13 初次电流分布在电极极化不存在时,电流在电极表面上的分布。
2.14 活化使金属表面钝化状态消失的作用。
2.15 钝化在一定环境下使金属表面正常溶解反应受到严重阻碍,并在比较宽的电极电位范围内使金属溶解反应速度降到很低的作用。
2.16 氢脆由于浸蚀,除油或电镀等过程中金属或合金吸收氢原子而引起的脆性。
真空镀膜的三种形式
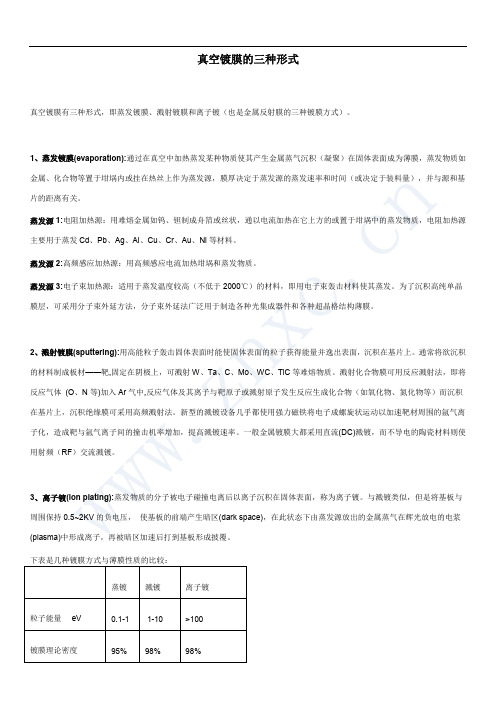
真空镀膜的三种形式真空镀膜有三种形式,即蒸发镀膜、溅射镀膜和离子镀(也是金属反射膜的三种镀膜方式)。
1、蒸发镀膜(evaporation):通过在真空中加热蒸发某种物质使其产生金属蒸气沉积(凝聚)在固体表面成为薄膜,蒸发物质如金属、化合物等置于坩埚内或挂在热丝上作为蒸发源,膜厚决定于蒸发源的蒸发速率和时间(或决定于装料量),并与源和基片的距离有关。
蒸发源1:电阻加热源:用难熔金属如钨、钽制成舟箔或丝状,通以电流加热在它上方的或置于坩埚中的蒸发物质,电阻加热源主要用于蒸发Cd、Pb、Ag、Al、Cu、Cr、Au、Ni等材料。
蒸发源2:高频感应加热源:用高频感应电流加热坩埚和蒸发物质。
蒸发源3:电子束加热源:适用于蒸发温度较高(不低于2000℃)的材料,即用电子束轰击材料使其蒸发。
为了沉积高纯单晶膜层,可采用分子束外延方法,分子束外延法广泛用于制造各种光集成器件和各种超晶格结构薄膜。
2、溅射镀膜(sputtering):用高能粒子轰击固体表面时能使固体表面的粒子获得能量并逸出表面,沉积在基片上。
通常将欲沉积的材料制成板材——靶,固定在阴极上,可溅射W、Ta、C、Mo、WC、TiC等难熔物质。
溅射化合物膜可用反应溅射法,即将反应气体(O、N等)加入Ar气中,反应气体及其离子与靶原子或溅射原子发生反应生成化合物(如氧化物、氮化物等)而沉积在基片上,沉积绝缘膜可采用高频溅射法。
新型的溅镀设备几乎都使用强力磁铁将电子成螺旋状运动以加速靶材周围的氩气离子化,造成靶与氩气离子间的撞击机率增加,提高溅镀速率。
一般金属镀膜大都采用直流(DC)溅镀,而不导电的陶瓷材料则使用射频(RF)交流溅镀。
3、离子镀(ion plating):蒸发物质的分子被电子碰撞电离后以离子沉积在固体表面,称为离子镀。
与溅镀类似,但是将基板与周围保持0.5~2KV的负电压,使基板的前端产生暗区(dark space),在此状态下由蒸发源放出的金属蒸气在辉光放电的电浆(plasma)中形成离子,再被暗区加速后打到基板形成披覆。
常见的镀膜术语和镀膜形式

由于镀膜技术发展迅速,本人了解的有限,所以仅仅对日常中的一些镀膜说说,而且这些镀膜是本人比较了解的。
这些内容都是比较通用的,如果各家自己叫的,因为本人不可能对各家的都了解,如果是本人不了解的,就不叙述了。
我们拿起一个光学产品,上面往往有些标示,把产品规格写出来。
但是对于望远镜和摄影镜头来说,往往还有其他的一些东西,常见的是对镀膜的说明,比如:COATING,FULL Y COATING,MULIT-COA TING,FULL Y MULIT-COA TING等。
下面我就一一为大家说明一下。
COATING:这个标示的意思是,本产品内包含镀膜镜片。
我个人的看法:这个产品不要购买,因为,这个产品十有八九只是前后2个表面镀膜了。
这样做的目的是降低成本。
如果它所有表面镀膜了,一般不会这样标示的,而是采用下面要说的标示。
FULL Y COATING(缩写FC):这个标示的意思是,本产品所有和空气接触的表面都镀膜了。
但是,这个镀膜正常情况下一般是单层膜。
因为只要有一个面是多层膜,它就不会这样标示,而是采用下面的标示。
MULIT-COATING(缩写MC):这个标示的意思是,本产品至少有一个和空气接触面是多层镀膜。
通常有这个标示的,如果表面没有多层镀膜,一般都会镀单层膜的,因为既然镀了一个多层,成本的考虑上,没必要再节约其他的单层镀膜了。
FULL Y MULIT-COA TING(缩写FMC):这个表示的意思是,本产品所有和空气接触的面都有多层镀膜。
从上面的叙述中,我们提取几个关键词:和空气接触的面,镀膜,多层镀膜。
下面逐一解释。
和空气接触的面:通常使用的光学产品都是在空气中,镜片之间也是空气,所以我特别提到和空气接触的面。
与之相对应的就当然有一个:不和空气接触的面。
不和空气接触的面,在通常使用中,就只有胶合镜片的胶合面。
这个面在惯例上,是不需要镀膜的。
当然,也有些厂家出于某些考虑,也镀,但是一般是镀单层的。
我曾经加工过一个镜片,据说是给松下公司的,就有一个胶合面要镀单层的AL2O3。
- 1、下载文档前请自行甄别文档内容的完整性,平台不提供额外的编辑、内容补充、找答案等附加服务。
- 2、"仅部分预览"的文档,不可在线预览部分如存在完整性等问题,可反馈申请退款(可完整预览的文档不适用该条件!)。
- 3、如文档侵犯您的权益,请联系客服反馈,我们会尽快为您处理(人工客服工作时间:9:00-18:30)。
由于镀膜技术发展迅速,本人了解的有限,所以仅仅对日常中的一些镀膜说说,而且这些镀膜是本人比较了解的。
这些内容都是比较通用的,如果各家自己叫的,因为本人不可能对各家的都了解,如果是本人不了解的,就不叙述了。
我们拿起一个光学产品,上面往往有些标示,把产品规格写出来。
但是对于望远镜和摄影镜头来说,往往还有其他的一些东西,常见的是对镀膜的说明,比如:COATING,FULL Y COATING,MULIT-COA TING,FULL Y MULIT-COA TING等。
下面我就一一为大家说明一下。
COATING:这个标示的意思是,本产品内包含镀膜镜片。
我个人的看法:这个产品不要购买,因为,这个产品十有八九只是前后2个表面镀膜了。
这样做的目的是降低成本。
如果它所有表面镀膜了,一般不会这样标示的,而是采用下面要说的标示。
FULL Y COATING(缩写FC):这个标示的意思是,本产品所有和空气接触的表面都镀膜了。
但是,这个镀膜正常情况下一般是单层膜。
因为只要有一个面是多层膜,它就不会这样标示,而是采用下面的标示。
MULIT-COATING(缩写MC):这个标示的意思是,本产品至少有一个和空气接触面是多层镀膜。
通常有这个标示的,如果表面没有多层镀膜,一般都会镀单层膜的,因为既然镀了一个多层,成本的考虑上,没必要再节约其他的单层镀膜了。
FULL Y MULIT-COA TING(缩写FMC):这个表示的意思是,本产品所有和空气接触的面都有多层镀膜。
从上面的叙述中,我们提取几个关键词:和空气接触的面,镀膜,多层镀膜。
下面逐一解释。
和空气接触的面:通常使用的光学产品都是在空气中,镜片之间也是空气,所以我特别提到和空气接触的面。
与之相对应的就当然有一个:不和空气接触的面。
不和空气接触的面,在通常使用中,就只有胶合镜片的胶合面。
这个面在惯例上,是不需要镀膜的。
当然,也有些厂家出于某些考虑,也镀,但是一般是镀单层的。
我曾经加工过一个镜片,据说是给松下公司的,就有一个胶合面要镀单层的AL2O3。
镀膜:指在镜片表面通过某些方法,沉积若干化学物质。
镀膜本身是一个很广泛的概念,它本身就包含了多层镀膜,但是在日常使用中,我们通常说的是单层镀膜,而且因为生产上单层镀膜一般用的是氟化镁,所以没有特别说明,镀膜一般是指单层的氟化镁。
多层镀膜:指在镜片表面通过某些方法,沉积2层或以上的不同化学物质。
我们日常中使用了很多多层镀膜,比如数码相机中的红外截止滤镜,就是镀了30层以上的膜。
但是日常中说的多层镀膜,一般是指多层减反膜。
这里需要说一下,如果多层镀膜控制不好的话,镜片的反射率可能比单层膜还差。
再说说蓝膜,红膜,绿膜,宽带膜等。
蓝膜:蓝膜一般是单层的,镀膜的时候,中心波长控制在570左右,整个玻璃就呈现蓝色。
反射曲线如下:
红膜:红膜倒是不折不扣的多层膜,因为我实在用一层镀不出来,但是红膜在天文中被人骂的狗血淋头,也是有原因的。
因为红膜实在反射了太多的光线了。
而且在实际使用中有偏色。
我们先看一个比较好的红膜。
其实很简单,就是把红色光线反射出来了。
不过,我想一般地摊上的红膜不会有上面的曲线的,上面的曲线实际是红外截止膜的前半段,使用了30多层。
但是实际的红膜我没见过曲线,所以不好说。
但是看到红膜亮晶晶的,可以看出,不会是好镀膜。
绿膜:多层绿膜现在比较流行,原因是多方面的。
第一:一般的绿膜确实是真正的减反膜,对光线的透过率还是可以的,第二:厂家控制起来容易些,因为人眼对绿色比较敏感,当厂家镀膜发生漂移时,实际效果看起来差别不大。
下面是一个多层绿膜,用了4层
可以看到,在550NM左右,有一个反射峰,我们看到的绿色主要是那里呈现出来的。
宽带膜;宽带膜其实是一个非常模糊的概念。
到底多宽叫宽带?反射率在多少以下才算?可见光一般是按400~700NM算的,整个可见光也就300NM,多宽算宽带呢?按一般望远镜厂的指标,带宽200NM之内,反射率1%以下,就算宽带了。
如果带宽到250NM,反射率1%以下,可以算超宽带。
上面我们默认宽带膜是减反膜,其实宽带膜也可以是高反膜。
不过,我们还是按约定俗成的说法。
同时,按一般的镀膜设计和控制水平,如果带宽做到200NM,反射率1%以下,一般4~5层可以搞定。
如果做到250NM,没有个6~7层是搞不定的。
下面是一个超宽带的镀膜,用了6层,虽然理论上达到了300NM,但是实际控制中,能做到260NM就可以了。
估计有人已经看到了,上面一直讨论的镀膜,其实是单个镜片表面的镀膜。
而实际使用中,不可能只有一个面的,整个望远镜或镜头有很多个表面组成的。
这样,我们就要谈谈镜头里大家经常提到的T*(ZEISS),HFT(ROLLEI)和SMC(PENTAX)了。
从我掌握的资料来看,T*和HFT的功能类似,都是针对色彩还原而特别设计的,而且它考虑的是整个镜头的透过率。
色彩还原在国际上有一个专门的CCI指数进行标定的。
具体CCI 指数如何计算出来的,我们可以不考虑,先了解一下什么是CCI指数。
彩色贡献指数(Color Contribution Index)
彩色贡献指数(CCI)是评价镜头彩色平衡特性的重要指标,通常以摄影镜头对彩色胶片感红层(R)、感绿层(G)、感蓝层(B) [RGB三原色] 的各层的相对贡献率来表示。
ISO-CCI值是摄影镜头色贡献指数的国际标准, 其含义是摄影镜头光谱透过率分布(从370nm~680nm)满足感光载体(彩色胶卷)的光谱感光需求,能按绝大多数人的喜好再现被摄物的色彩。
要保证这一点,并不是要求在可见光区(370nm~680nm)的光谱范围内透过率一致。
而是分为三个波段(即蓝光、绿光和红光),它们有不同的透过率要求。
根据ISO 6728-1983的规定:色彩平衡的摄影镜头的标准彩色贡献指数各分量B/G/R分别为0/5/4。
允许误差标准是:-4~+3/3~5/2~5。
彩色贡献指数的方法将镜头的色彩还原特性数值化,从而具有表示简单明了的特点,也便于用来比较。
从上面可以看出,镜头不是对所有光线一样的透过率是最好的,考虑到接收器,需要不同的透过率。
而整个镜头除了镀膜外,还有镜片对光线的吸收不一样,这样,就需要将整个镜头一起考虑。
T*和HFT并不是单个表面的镀膜指标,而是整个镜头一起考虑的,也许某个面的曲线不是很漂亮,但是,为了整个镜头的CCI,它可能需要牺牲了。
同样道理,就算每个面的曲线都非常漂亮,最后整体的CCI指数也许出问题了。
这样的情况,本人就碰到过,当时是给某日本公司的相机提供镜头,在检测后发现CCI指数出问题了,拍出来的图片偏蓝,最后解决方法是,将某个面的曲线故意做出问题,最后CCI指数检测顺利通过。
还有PENTAX的SMC镀膜,从公开的资料看,其核心似乎是:7层镀膜,0.2%反射率,这个和T*和HFT就不是一样了,做0.2%的反射率不是很难的,说白了,SMC也就是一个比较好的减反膜。
上面的说法主要用在望远镜里,但是还是要注意,望远镜里的棱镜,正常情况下是不镀膜的。
有的高档望远镜里的棱镜镀过膜,但是是什么镀膜,就难说了。
我以前见过CANON外发的棱镜,全表面镀单层减反膜。
另外,最近在望远镜业内出现了“相位膜”,也是镀在棱镜上的,据称可以提高透过率2%。
前面文章里所说的镀膜,均是不考虑棱镜镀膜的,请注意。