橡胶硫化三要素之压力
橡胶硫化的压力重要性及计算设定方式
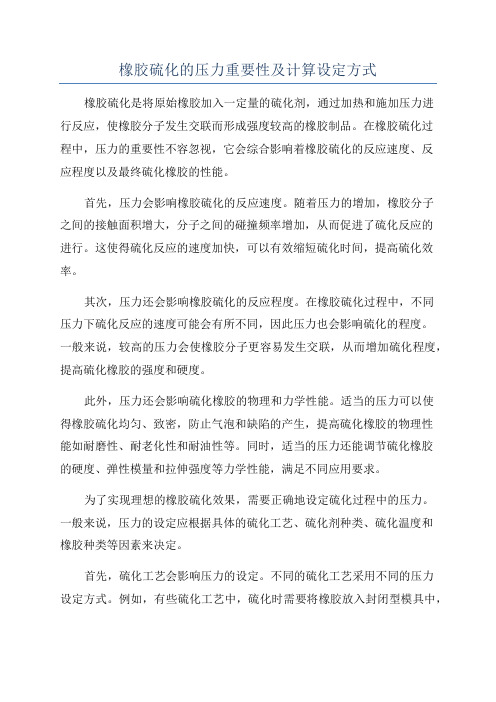
橡胶硫化的压力重要性及计算设定方式橡胶硫化是将原始橡胶加入一定量的硫化剂,通过加热和施加压力进行反应,使橡胶分子发生交联而形成强度较高的橡胶制品。
在橡胶硫化过程中,压力的重要性不容忽视,它会综合影响着橡胶硫化的反应速度、反应程度以及最终硫化橡胶的性能。
首先,压力会影响橡胶硫化的反应速度。
随着压力的增加,橡胶分子之间的接触面积增大,分子之间的碰撞频率增加,从而促进了硫化反应的进行。
这使得硫化反应的速度加快,可以有效缩短硫化时间,提高硫化效率。
其次,压力还会影响橡胶硫化的反应程度。
在橡胶硫化过程中,不同压力下硫化反应的速度可能会有所不同,因此压力也会影响硫化的程度。
一般来说,较高的压力会使橡胶分子更容易发生交联,从而增加硫化程度,提高硫化橡胶的强度和硬度。
此外,压力还会影响硫化橡胶的物理和力学性能。
适当的压力可以使得橡胶硫化均匀、致密,防止气泡和缺陷的产生,提高硫化橡胶的物理性能如耐磨性、耐老化性和耐油性等。
同时,适当的压力还能调节硫化橡胶的硬度、弹性模量和拉伸强度等力学性能,满足不同应用要求。
为了实现理想的橡胶硫化效果,需要正确地设定硫化过程中的压力。
一般来说,压力的设定应根据具体的硫化工艺、硫化剂种类、硫化温度和橡胶种类等因素来决定。
首先,硫化工艺会影响压力的设定。
不同的硫化工艺采用不同的压力设定方式。
例如,有些硫化工艺中,硫化时需要将橡胶放入封闭型模具中,然后通过压缩机施加一定的压力。
在这种情况下,压力设定便是由压缩机的设定决定的。
其次,硫化剂的类型也会影响压力的设定。
硫化剂的种类不同,对于硫化压力的要求也有所不同。
一般来说,硫化时间较短,硫化剂活性较高的情况下,压力可以适当降低。
但需要注意的是,如果压力太低,硫化橡胶的交联效果可能不理想,影响橡胶制品的性能。
此外,硫化温度和橡胶种类的选择也会影响压力的设定。
一般来说,橡胶硫化温度较高时,压力可适当增加,以提高硫化效果。
而不同类型的橡胶在硫化过程中可能需要不同的压力设定,因此需要根据实际情况进行调整。
硫化工岗位理论培训试题答案

硫化工岗位理论培训试题
1、硫化三要素是什么?
橡胶硫化工艺条件是指决定橡胶硫化质量的三个重要因素,按其工艺操作次序排列,即硫化温度、硫化压力及硫化时间,通常习惯称之为“硫化三要素”。
2、常用橡胶种类代号是什么?
天然橡胶NR
丁苯胶SBR
乙丙胶EPDM
氯丁胶CR
丁晴胶NBR
氯醚ECO
3、开机前要检查好设备的安全装置、液压系统、模具系统、电控系统、压缩空气压力等是否正常
4、P64产品使用那种材料生产,硫化温度,时间,压力是多少?
使用氯醚(ECO)材料。
温度170-180,压力15-18Mpa,时间15分钟。
5、P64产品需要二次硫化吗?时间、温度是多少?
需要二次硫化,时间2个小时,温度150.
6、耐油橡胶是哪种?
丁腈橡胶
7、5S管理分几个阶段?内容是什么?
5S管理分5个阶段:常组织、常整理、常自律、常清洁、
常规范。
考工

1、什么叫喷硫?喷硫产生的原因,如何解决喷硫问题。
喷硫:硫黄在胶料中的配合量超过了它的溶解度达到过饱和,就从胶料内部析出到表面上,形成一层白霜,这种现象叫喷硫。
硫黄在橡胶中的溶解度随温度升高而增大,但温度降低时,硫黄会从橡胶中结晶析出,形成“喷硫”现象。
避免喷硫应采取的措施:(1)应在尽可能低的温度下加入硫黄;(2)使用不溶性硫黄;(3)使用合理的加料顺序;(4)减少硫黄用量,增大促进剂用量。
2、硫化的三要素是什么?简要说明硫化压力对硫化制品所起的作用是什么?试述一般橡胶制品的硫化条件的制订原则。
硫化的三要素:硫化压力、硫化温度、硫化时间硫化压力对硫化制品的作用是a防止产生气泡,提高胶料致密性;b使胶料流动,充满模腔,达到尺寸和形成花纹c提高附着力,改善物理机械性能硫化压力的考虑因素:配方中含水量、制品的结构、制品花纹、制品尺寸、工艺设备硫化温度的确定考虑因素:配方(胶种,硫化体系,软化剂)、制品的结构和尺寸、工艺条件(硫化设备、加热方式、加热介质)硫化时间的确定考虑因素:原材料、制品的结构和尺寸3、画出硫化仪测定NR的硫化曲线,并分别指出其焦烧时间、热硫化时间、平坦硫时间及过硫化时间。
4、画出橡胶硫化历程曲线,并指出可分为哪几个阶段,合理的硫化历程应该具备哪些条件。
合理的硫化历程应该具备下列条件:A、硫化诱导期要足够长,充分保证生产加工的安全性;B、硫化速度要快,提高生产效率,降低能耗;C、硫化平坦期要长(保证硫化加工中的安全性,保证制品各部位硫化均匀一致)。
5、等效硫化时间的概念是什么?怎样区分等效硫化效应和硫化强度的概念?所谓等效硫化时间是指在不同的硫化温度下,经硫化获得相同的硫化程度所需要的时间。
硫化效应是衡量胶料硫化程度深浅的尺度。
硫化效应大,说明胶料硫化程度深,硫化效应小,说明胶料硫化程度浅。
它等于硫化强度与硫化日寸间的乘积。
硫化强度是指胶料在一定的温度下,单位时间所达到的硫化程度或胶料在一定温度下的硫化速度。
橡胶的种类(优缺点)和硫化
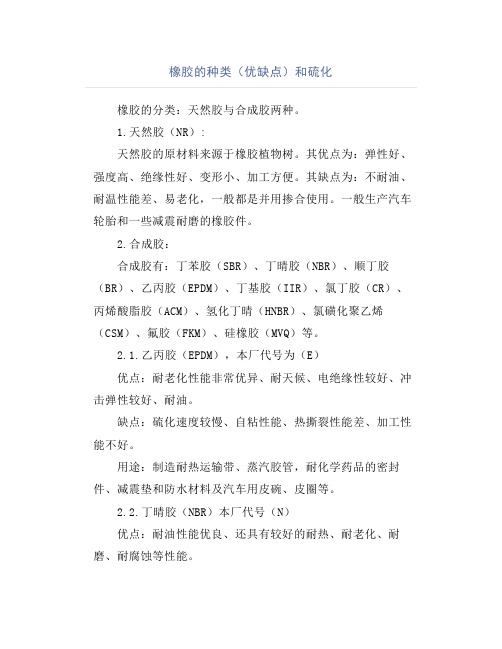
橡胶的种类(优缺点)和硫化橡胶的分类:天然胶与合成胶两种。
1.天然胶(NR):天然胶的原材料来源于橡胶植物树。
其优点为:弹性好、强度高、绝缘性好、变形小、加工方便。
其缺点为:不耐油、耐温性能差、易老化,一般都是并用掺合使用。
一般生产汽车轮胎和一些减震耐磨的橡胶件。
2.合成胶:合成胶有:丁苯胶(SBR)、丁晴胶(NBR)、顺丁胶(BR)、乙丙胶(EPDM)、丁基胶(IIR)、氯丁胶(CR)、丙烯酸脂胶(ACM)、氢化丁晴(HNBR)、氯磺化聚乙烯(CSM)、氟胶(FKM)、硅橡胶(MVQ)等。
2.1.乙丙胶(EPDM),本厂代号为(E)优点:耐老化性能非常优异、耐天候、电绝缘性较好、冲击弹性较好、耐油。
缺点:硫化速度较慢、自粘性能、热撕裂性能差、加工性能不好。
用途:制造耐热运输带、蒸汽胶管,耐化学药品的密封件、减震垫和防水材料及汽车用皮碗、皮圈等。
2.2.丁晴胶(NBR)本厂代号(N)优点:耐油性能优良、还具有较好的耐热、耐老化、耐磨、耐腐蚀等性能。
缺点:耐寒性、耐酸性、电绝缘性等性能较差、且抗力撕裂强度较差。
用途:主要用于制造油封、轴封及垫圈(O型圈)等制品,还可用于制造耐油胶管、运输带、胶辊、真空胶管、减震制品和纺织配件。
2.3丁苯胶(SBR)本厂代号(S)优点:耐热性、耐老化性和耐磨性较好。
缺点:耐寒性、弹性、耐屈扰、龟裂性、耐撕裂性等性能较差、且加工性能较差可塑度变化小,压延压出变形大,自粘性差。
用途:主要用于充气轮胎,其次用于胶鞋、胶管、胶带、胶辊、胶布及模型制品,吸尘器密封圈等如吸口密封圈等。
2.4氯丁橡胶(CR),本厂代号(C)优点:耐屈扰性、耐热性、耐老化性、耐酸碱性等较好,且弹性好,有良好的气密性。
具有耐寒性和耐水性。
缺点:储存稳定性较差,易结晶,电绝缘性较差用途:主要生产家电、空调里的橡胶件2.5顺丁胶或聚丁二烯橡胶(BR)优点:弹性、耐低温性、耐磨性较好。
缺点:拉伸强度、撕裂强度较低,抗湿滑性不好,粘性差。
橡胶硫化三要素之压力

橡胶硫化三要素之压力橡胶件硫化的三大工艺参数是:温度、时间和压力。
其中硫化温度是对制品性能影响最大的参数,硫化温度对橡胶制品的影响的研究也比比皆是。
但对硫化压力比较少进行试验。
硫化压力是指,橡胶混炼胶在硫化过程中,其单位面积上所承受的压力。
一般情况下,除了一些夹布件和海绵橡胶外,其他橡胶制品在硫化时均需施加一定的压力.橡胶硫化压力,是保证橡胶零件几何尺寸、结构密度、物理机械的重要因素,同时也能保证零件表面光滑无缺陷,达到橡胶制品的密封要求。
作用主要有以下几点:1)防止混炼胶在硫化成型过程中产生气泡,提高制品的致密性;2)提供胶料的充模流动的动力,使胶料在规定时间内能够充满整个模腔;3)提高橡胶与夹件(帘布等)附着力及橡胶制品的耐曲绕性能;4)提高橡胶制品的物理力学性能。
硫化压力的选取需要考虑如下几个方面的因素:1)胶料的配方;2)胶料可塑性的大小;3)成型模具的结构形式(模压,注压,射出等);4)硫化设备的类型(平板硫化机,注压硫化机,射出硫化机,真空硫化机等;5)制品的结构特点。
硫化压力选取的一般原则:1)胶料硬度低的(50—Shore A以下或更低),压力宜选择小,硬度高的选择大;2)薄制品选择小,厚制品选择大;3)制品结构简单选择小,结构复杂选择大;4)力学性能要求高选择大,要求低选择小;5)硫化温度较高时,压力可以小一些,温度较低时,压力宜高点。
对硫化压力,国内外一些橡胶厂家有如下一些经验值供参考:1)模压及移模注压的硫化方式,其模腔内的硫化压力为:10~20Mpa;2)注压硫化方式其模腔内的硫化压力为:0~150Mpa;3)硫化压力增大,产品的静态刚度也随之增大,而收缩率随之逐渐减小;(在国内的减振橡胶行业内,对于调整产品的刚度,普遍采用的依然是增加或者降低产品所使用的胶料硬度,而在国外,已经普遍采用了提高或者降低产品硫化时的胶料硫化压力来调整产品的静态刚度。
)4)随着硫化压力的不断提高,产品胶料的收缩率会出现一个反常的现象,即当产品胶料的硫化压力达到83Mpa时,产品胶料的收缩率为0,若产品胶料的硫化压力继续不断上升,产品胶料的收缩率会出现负值,也就是说,在这种超高的产品胶料硫化压力下,产品硫化出来经停放后,其橡胶部分的尺寸比模具设计的尺寸还要大;5)在模压和注压方式下,模腔内胶料的硫化压力随着时间的延长,总是先增高后减少,并最终处于平坦状态;6)随着胶料硫化压力的提高,其胶料的300%定伸和拉伸强度均随之提高,其胶料的扯断伸长率、撕裂强度和压缩永久变形却随之下降;7)在减震橡胶制品硫化过程中,注压硫化方式中模腔内胶料的压强比模压硫化方式的压强高一倍以上。
橡胶硫化三要素之一压力

橡胶硫化三要素之一压力
橡胶硫化过程是将橡胶中的双键重排并形成交联结构的化学反应。
它
是将原始橡胶转变为具有更好物理和化学性能的橡胶制品的重要步骤。
橡
胶硫化三要素是指温度、时间和压力。
压力是橡胶硫化过程中的重要参数之一、通过适当的压力可以促进橡
胶中的硫团交联反应,并改善其物理性能。
首先,压力可以增加橡胶硫化的速度。
在硫化过程中,橡胶中的双键
会发生重排反应,形成交联结构。
适当的压力可以促使橡胶分子更加接近,增加反应速率。
实验研究表明,在一定温度下,随着压力的增加,橡胶硫
化的速度也会相应增加。
其次,压力还可以改善橡胶硫化后的物理性能。
橡胶硫化后,由于交
联结构的形成,使得橡胶具有更好的抗拉强度、耐磨性和耐老化性能等。
适当的压力可以增加交联结构的密度和连接数量,从而提高橡胶的物理性能。
研究表明,橡胶硫化时施加较高的压力,可以显著提高橡胶的抗拉强
度和硬度。
此外,压力还可以改善橡胶硫化的均匀性。
橡胶硫化时,硫化剂需要
充分和均匀地分散在橡胶中,以确保交联结构的形成。
适当的压力可以增
加橡胶体系的紧密性,使得硫化剂更容易和橡胶混合,并更好地扩散到整
个橡胶体中。
总而言之,压力是橡胶硫化过程中不可忽视的重要参数。
适当的压力
可以促进橡胶硫化的速度,提高其物理性能,并改善硫化的均匀性。
在实
际生产中,需要根据具体的橡胶材料和硫化工艺的要求,合理选择和控制
硫化时的压力,以确保橡胶制品的质量和性能。
橡胶硫化压力温度时间计算(公式全
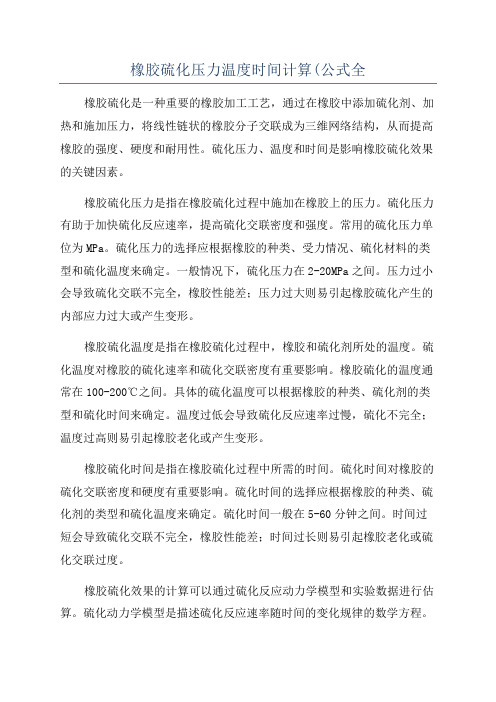
橡胶硫化压力温度时间计算(公式全橡胶硫化是一种重要的橡胶加工工艺,通过在橡胶中添加硫化剂、加热和施加压力,将线性链状的橡胶分子交联成为三维网络结构,从而提高橡胶的强度、硬度和耐用性。
硫化压力、温度和时间是影响橡胶硫化效果的关键因素。
橡胶硫化压力是指在橡胶硫化过程中施加在橡胶上的压力。
硫化压力有助于加快硫化反应速率,提高硫化交联密度和强度。
常用的硫化压力单位为MPa。
硫化压力的选择应根据橡胶的种类、受力情况、硫化材料的类型和硫化温度来确定。
一般情况下,硫化压力在2-20MPa之间。
压力过小会导致硫化交联不完全,橡胶性能差;压力过大则易引起橡胶硫化产生的内部应力过大或产生变形。
橡胶硫化温度是指在橡胶硫化过程中,橡胶和硫化剂所处的温度。
硫化温度对橡胶的硫化速率和硫化交联密度有重要影响。
橡胶硫化的温度通常在100-200℃之间。
具体的硫化温度可以根据橡胶的种类、硫化剂的类型和硫化时间来确定。
温度过低会导致硫化反应速率过慢,硫化不完全;温度过高则易引起橡胶老化或产生变形。
橡胶硫化时间是指在橡胶硫化过程中所需的时间。
硫化时间对橡胶的硫化交联密度和硬度有重要影响。
硫化时间的选择应根据橡胶的种类、硫化剂的类型和硫化温度来确定。
硫化时间一般在5-60分钟之间。
时间过短会导致硫化交联不完全,橡胶性能差;时间过长则易引起橡胶老化或硫化交联过度。
橡胶硫化效果的计算可以通过硫化反应动力学模型和实验数据进行估算。
硫化动力学模型是描述硫化反应速率随时间的变化规律的数学方程。
常用的硫化动力学模型有理想反应动力学模型、布洛赫-曼宁方程和约伯斯方程等。
这些模型可以用来计算硫化过程中的反应速率常数、反应级数和硫化反应速率随时间的变化规律。
实验数据可以通过橡胶硫化试验获得,通过测量硫化前后橡胶的物理性能变化来评估硫化效果。
综上所述,橡胶硫化压力、温度和时间是影响橡胶硫化效果的重要因素。
硫化压力、温度和时间的选择应根据橡胶的种类、受力情况、硫化材料的类型和硫化时间来确定。
橡胶飞边产生的原因及解决方法

3
无锡中策
AUTOMOTIVE
WuXi CSI
三、抑制或减少橡胶制品飞边的方法
3.1型腔内橡胶重量的均匀性。 流道试验 不放金属件 , 称取充满模腔重量 M 的( 60-80)% 的 橡胶硫化两模,硫化完成标识好每模产品与型腔对 应的型腔号,并在模具上标上型腔号。 称取每只产品重量,并与型腔号对应记录数据 一般流道合格判定标准 A、每腔产品重量在平均值的±10%以内 B、重量最大值减去重量最小值除以重量最大值≤20%
2
无锡中策
AUTOMOTIVE
WuXi CSI
二、橡胶制品飞边影响
1. 飞边的形成改变了模制品的封模尺寸,使制品的部分性能受到
影响(特别是对要求严格的各类密封制品) 2.飞边的修除,尤其是手工修除,明显而严重地影响了制品的表观 质量,从而降低了制品的商业价值。常言道:“货卖一张皮”, 讲的就是这个道理。修掉的飞边,其痕迹高低不一,残留各异, 直接影响了企业在客户心目中的影响,使企业在市场上失去了竞 争力。 3.产品的设计一般是不允许出现飞边的,从质量要求和角度来讲 必须对其进行修炼,修除飞边需要大量的人力和相应的设备(冷 冻修电机等)场地等,这无形中增加了一道工序,延长了生产的 周期,从经营角度讲,飞边的修除增加了生产成本。 4.飞边的形成,使胶料的消耗量增大,提高了生产成本同时它又 是一种资源浪费,对于环境也是一种潜在的污染。
4
无锡中策
AUTOMOTIVE
WuXi CSI
三、抑制或减少橡胶制品飞边的方法
3.2称重的准确性 严格按照标准化作业指导书称重; 发现标准化作业指导书重量不恰当,造成缺料现象, 及时提出; 定期校准称量工具。
5
无锡中策
AUTOMOTIVE
橡胶硫化—硫化工艺条件(橡胶加工课件)

一 硫化历程—硫化概念、原理与正硫化
二 硫化工艺条件—硫化三要素
三 硫化方法—工艺与设备 四 硫化质量分析—问题与对策
1.硫化工艺条件—温度
❖ 硫化工艺条件即硫化三要素—温度,时间和压力; ❖ 硫化温度是硫化反应的最基本条件。 ❖ 硫化温度高,硫化速度快,生产效率高;反之生产效率低 ❖ 硫化温度:电(硫化介质)间接加热,硫化介质直接加热或红
外、辐射能加热等。 硫化介质是传递热能的物质,如饱和蒸汽、过热水、热空气、
熔融盐、固体微粒等。
1.硫化工艺条件—温度
❖ 提高硫化温度会导致以下问题: ①引起橡胶分子链裂解和硫化返原,导致力学性能下降; ②使橡胶制品中的纺织物强度降低; ③导致胶料焦烧时间缩短,减少了充模时间,造成制品局
部缺胶; ④由于厚制品会增加制品的内外温差,导致硫化不均。
方程可计算出130℃和150℃时的等效硫化时间( K=2 )。
程度或胶料在一定温度下的硫化速度
t 100
I K 10
3.硫化工艺条件—硫化时间
例1:某制品正硫化条件为148℃×10min,K=2,问硫化温 度改为153℃、158℃、138℃时其等效硫化时间应分别是 多少?
3.硫化工艺条件—硫化时间
例2 某胶料的硫化温度系数为2.17,当140℃时正硫化时 间为68min,求135℃下的硫化时间。
❖ 硫化温度选择应根据制品的类型、胶种、硫化体系及其他方
面综合考虑。
不同胶种的硫化温度
不同硫化体系的硫化温度
2.硫化工艺条件—压力
❖ 硫化压力:机械压力,硫化介质,包覆层(钢丝,包布,铅)提供; 有些制品常压。 ❖ 硫化压力作用:
(1) 防止气泡; (2)提高致密性; (3)流动,充模,花纹清晰; (4)提高附着力。 ❖ 硫化压力应根据胶料配方、可塑性及产品结构等决定。
橡胶硫化

橡胶硫化摘要:“硫化”一词对初学者来说比较陌生;这次主要对其概念的解释以及硫化条件、过程等进行介绍,通过此次介绍主要是为了帮助初学者的硫化的认识,让更多的人去很快的认识它、熟悉它,为硫化的进一步发展奠定基础。
硫化是橡胶制品制造工艺的最后一个流程,也是最重要一个流程,它赋予橡胶各种宝贵的的物理机械性能,简单来说就是把一些胶料以及各种加强剂融合在一起,使得性能互补以及加强,以达到它橡胶在各个领域的使用性能。
1、硫化概念“硫化”一词主要来源于最初天然橡胶制品用硫磺作交联剂进行交联而得名。
简单来说,硫化就好比“架桥”把两岸连接起来,即把一些线型高分子通过交联(架桥)作用形成网状高分子的工艺工程。
再简单而言其实就是交联,把一些个体整合成整体的过程,其反应过程较复杂。
但是可以从蒸馒头这个事例中对其有个大致的了解,其主要是利用淀粉和水混合后利用其附着性使淀粉颗粒抱团,从而形成面团;利用酵母菌的无氧呼吸以及有氧呼吸产生二氧化硫在面团中“乱跑”,导致馒头形成疏松多孔的结构,因此面团变胖了并且不容易变散,达到了交联的作用。
橡胶硫化主要是产生化学键把其成分交联在一起。
形成大分子网状结构,使其性能大大提高。
2、硫化条件正如蒸馒头需要利用酵母菌的有氧呼吸及无氧呼吸似的,橡胶的硫化也需要借助一些条件使分子之间发生交联。
其主要影响因素包括以下三个:硫化压力、温度、时间,通常被称为“硫化三要素”。
硫化条件对其硫化工艺至关重要,而且不同制品的硫化其硫化条件也不尽相同。
2.1硫化压力硫化压力是指在硫化过程中橡胶制品所承受的单位压力。
所施加的压力通常情况下分常压和高压;施加压力的主要作用是排除橡胶制品在硫化过程中内部产生的气体,防止制品内部出现气泡,提高胶料的致密性;还能加速胶料的流动和充满模腔,达到提高制品的物理机械性能的目的。
因此对于一些薄壁制品施加常压就可以达到其目的,而对于一些后制品则需施加高压才能达到其目的。
2.2硫化温度硫化属于一种化学反应,是使得内部分子结构发生改变,因此它同其他一般化学反应一样都依赖温度,随着温度的升高,硫化反应的速率也不断升高,从而直接影响生产效率;但是并不能无限制的提高硫化温度,一般硫化温度越高,胶料的物理机械性能越低,过高的温度会引起香蕉分子链的破解和发生硫化返原现象,使性能下降并且工艺控制困难。
橡胶硫化工艺三要素确定原则

橡胶硫化工艺三要素确定原则橡胶硫化是一种将橡胶制品加热至一定温度并加入硫化剂,使其发生硫化反应,从而得到具有一定弹性和耐磨性的橡胶制品的过程。
在橡胶硫化工艺中,三要素的确定对于最终的硫化效果具有重要的影响。
本文将从橡胶硫化工艺的背景、硫化温度、硫化时间和硫化剂用量等三个方面,探讨橡胶硫化工艺三要素的确定原则。
首先是硫化温度的确定。
硫化温度是指橡胶制品在硫化过程中所受的热处理温度。
硫化温度的确定需要综合考虑橡胶材料的特性以及所需硫化反应的速率。
一般而言,橡胶硫化的温度范围从130℃至200℃不等。
对于不同种类的橡胶,其硫化温度也会有所不同。
在确定硫化温度时,应避免温度过高或过低,否则会对橡胶材料的性能产生不利影响。
同时,硫化温度的选择还应考虑到硫化时间和硫化剂用量等因素。
第二是硫化时间的确定。
硫化时间是指橡胶制品在硫化过程中所需的时间。
硫化时间的确定需要考虑橡胶材料的厚度、形状以及所需硫化反应的速率等因素。
一般而言,硫化时间的范围从几分钟至数小时不等。
对于比较薄的橡胶制品,其硫化时间通常较短。
在确定硫化时间时,应尽可能地缩短硫化时间,以提高生产效率,同时还要保证硫化反应能够充分进行,从而得到具有优良性能的橡胶制品。
第三是硫化剂用量的确定。
硫化剂是橡胶硫化过程中不可或缺的一部分,它能够引发硫化反应并加速反应速率。
硫化剂用量的确定需要考虑到橡胶材料的种类、硫化温度和硫化时间等因素。
一般而言,硫化剂用量的范围从1至10个单位不等。
在确定硫化剂用量时,应避免用量过少或过多,否则会对橡胶制品的硫化效果产生不良影响。
在确定橡胶硫化工艺三要素时,除了考虑橡胶材料本身的特性外,还应考虑到硫化工艺的经济性和环境性。
应尽可能地选择能够提高生产效率和保证橡胶制品品质的硫化工艺。
综上所述,橡胶硫化工艺三要素的确定原则是在综合考虑橡胶材料特性、硫化温度、硫化时间和硫化剂用量等因素的基础上,选择合适的三要素数值,以确保橡胶制品能够具有良好的性能和质量。
硫化成型压力
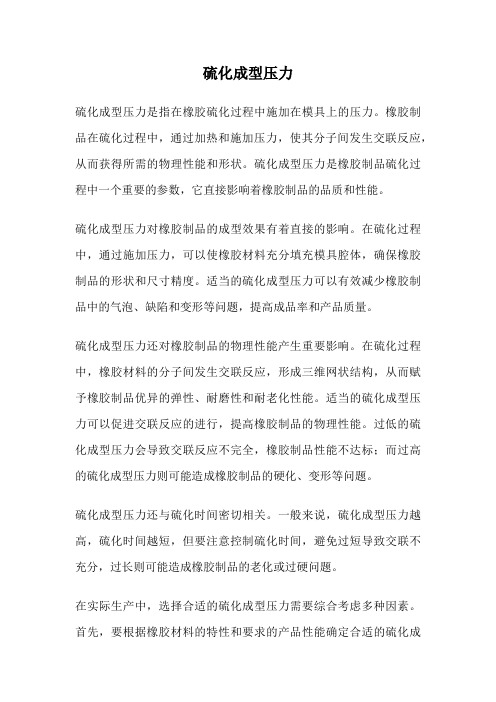
硫化成型压力硫化成型压力是指在橡胶硫化过程中施加在模具上的压力。
橡胶制品在硫化过程中,通过加热和施加压力,使其分子间发生交联反应,从而获得所需的物理性能和形状。
硫化成型压力是橡胶制品硫化过程中一个重要的参数,它直接影响着橡胶制品的品质和性能。
硫化成型压力对橡胶制品的成型效果有着直接的影响。
在硫化过程中,通过施加压力,可以使橡胶材料充分填充模具腔体,确保橡胶制品的形状和尺寸精度。
适当的硫化成型压力可以有效减少橡胶制品中的气泡、缺陷和变形等问题,提高成品率和产品质量。
硫化成型压力还对橡胶制品的物理性能产生重要影响。
在硫化过程中,橡胶材料的分子间发生交联反应,形成三维网状结构,从而赋予橡胶制品优异的弹性、耐磨性和耐老化性能。
适当的硫化成型压力可以促进交联反应的进行,提高橡胶制品的物理性能。
过低的硫化成型压力会导致交联反应不完全,橡胶制品性能不达标;而过高的硫化成型压力则可能造成橡胶制品的硬化、变形等问题。
硫化成型压力还与硫化时间密切相关。
一般来说,硫化成型压力越高,硫化时间越短,但要注意控制硫化时间,避免过短导致交联不充分,过长则可能造成橡胶制品的老化或过硬问题。
在实际生产中,选择合适的硫化成型压力需要综合考虑多种因素。
首先,要根据橡胶材料的特性和要求的产品性能确定合适的硫化成型压力范围。
不同的橡胶材料对硫化成型压力的要求不同,例如硬度较高的橡胶通常需要较高的硫化成型压力。
其次,还需要考虑模具的结构和强度,以及硫化设备的性能和能力。
模具结构的合理性和强度直接影响着硫化成型压力的选择,而硫化设备的性能和能力则限制了硫化成型压力的上限。
硫化成型压力是橡胶制品硫化过程中的重要参数,它直接影响着橡胶制品的成型效果和物理性能。
合理选择硫化成型压力可以提高橡胶制品的品质和性能,满足不同应用领域的需求。
因此,在橡胶制品生产中,需要严格控制硫化成型压力,确保其稳定性和准确性,以获得优质的橡胶制品。
硫化三质量方针
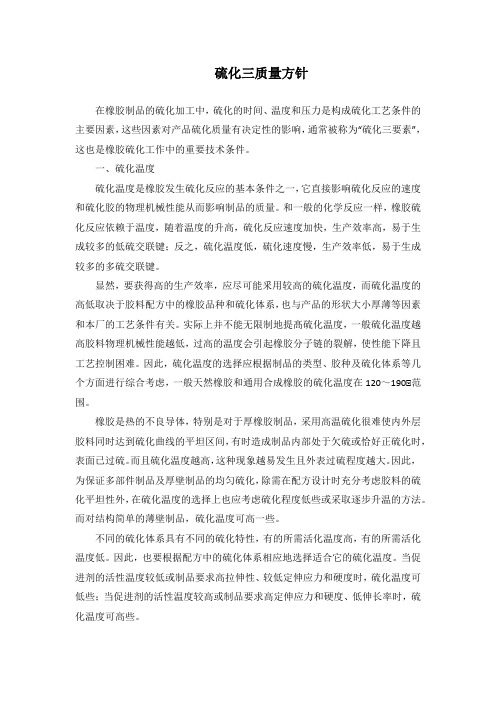
硫化三质量方针在橡胶制品的硫化加工中,硫化的时间、温度和压力是构成硫化工艺条件的主要因素,这些因素对产品硫化质量有决定性的影响,通常被称为“硫化三要素”,这也是橡胶硫化工作中的重要技术条件。
一、硫化温度硫化温度是橡胶发生硫化反应的基本条件之一,它直接影响硫化反应的速度和硫化胶的物理机械性能从而影响制品的质量。
和一般的化学反应一样,橡胶硫化反应依赖于温度,随着温度的升高,硫化反应速度加快,生产效率高,易于生成较多的低硫交联键;反之,硫化温度低,硫化速度慢,生产效率低,易于生成较多的多硫交联键。
显然,要获得高的生产效率,应尽可能釆用较高的硫化温度,而硫化温度的高低取决于胶料配方中的橡胶品种和硫化体系,也与产品的形状大小厚薄等因素和本厂的工艺条件有关。
实际上并不能无限制地提髙硫化温度,一般硫化温度越高胶料物理机械性能越低,过高的温度会引起橡胶分子链的裂解,使性能下降且工艺控制困难。
因此,硫化温度的选择应根据制品的类型、胶种及硫化体系等几个方面进行综合考虑,一般天然橡胶和通用合成橡胶的硫化温度在120~190℃范围。
橡胶是热的不良导体,特别是对于厚橡胶制品,采用高温硫化很难使内外层胶料同时达到硫化曲线的平坦区间,有时造成制品内部处于欠硫或恰好正硫化时,表面已过硫。
而且硫化温度越高,这种现象越易发生且外表过硫程度越大。
因此,为保证多部件制品及厚壁制品的均匀硫化,除需在配方设计时充分考虑胶料的硫化平坦性外,在硫化温度的选择上也应考虑硫化程度低些或采取逐步升温的方法。
而对结构简单的薄壁制品,硫化温度可高一些。
不同的硫化体系具有不同的硫化特性,有的所需活化温度高,有的所需活化温度低。
因此,也要根据配方中的硫化体系相应地选择适合它的硫化温度。
当促进剂的活性温度较低或制品要求高拉伸性、较低定伸应力和硬度时,硫化温度可低些;当促进剂的活性温度较高或制品要求高定伸应力和硬度、低伸长率时,硫化温度可高些。
此外,各种橡胶的耐髙温能力也不相同,因此选择适当的硫化温度,对于保障产品质量和提高硫化效率,有着十分重要的意义。
橡胶硫化工艺三要素如何确定(全收藏版)

橡胶硫化工艺三要素如何确定(全收藏版)一、硫化基本概念和工艺要素硫化是橡胶制品生产的最后一个工艺过程。
在这个过程中,胶料中的生胶与硫化剂发生化学发应,由线型结构的大分子交联成为立体的网状结构的大分子,使塑性状态的橡胶转变为弹性状态的橡胶制品,从而获得完善的物理性能和机械性能和化学性能,成为有使用价值的高分子材料。
在工业生产中,这种交联反应是在一定温度,时间和压力条件下完成的,这些条件称为硫化条件。
1、橡胶的硫化反应过程诱导阶段,交联反应阶段,网状形成阶段。
2、硫化历程图烧焦阶段,热硫化阶段,平坦硫化阶段,过硫化阶段3、硫化压力一般橡胶制品在硫化时要施以压力,目的在于:1)防止制品在硫化过程产生气泡,提高胶料的致密性。
2)使胶料易于流动和充满模槽3)提高胶料与胶料的密着力4)有助于提高硫化的物理机械性能硫化加压的方式通常有下列几种:一是用液压泵通过平板硫化机把压力传递给模型,再由模型传递给胶料;二是硫化介质直接加压(如蒸汽加压);三是以压缩空气加压;四是由注压机注压等。
4、硫化温度和硫化时间硫化温度是橡胶发生硫化反应的基本条件,它直接影响硫化速度和产品质量。
硫化温度高,硫化速度快,生产效率高。
反之,硫化速度慢,生产效率低。
硫化温度高低应取决于胶料配方,其中最重要的是取决于橡胶种类和硫化体系。
但应注意的是,高温橡胶分子链裂解,至发生硫化返原现象,结果导致强伸性能下降,困此硫化温度不宜太高。
温度是硫化三大要素之一,与所有化学反应一样,硫化反应随温度升高而加快,并且大体适用范特霍夫定律,即温度每上升8~10。
C(约相当于一个表压的蒸汽压力),其反应速度约增加一倍;或者说,反应时间约减少一半。
随着室温硫化胶料的增加和高温硫化出现,硫化温度趋向两个极端。
从提高硫化效率来说,应当认为硫化温度越高越好,但实际上不能无限提高硫化温度。
首先受到橡胶导热性极小阻碍,对于厚制品来说,采用高温硫化很难使内外层胶料同时达到平坦范围;其次,各种橡胶的耐高温性能不一,有的橡胶经受不了高温的作用,如高温硫化天然橡胶时,溶于橡胶中的氧随温度提高而活性加大,引起强烈的氧化作用,破坏了橡胶的组织,降低了硫化胶的物理机械性能,第三,高温对橡胶制品中的纺织物有害为棉纤维布料超过期作废140℃时,强力下降,在240℃下加热四小时则完全破坏。
橡胶工艺原理-复习思考题-+答案

橡胶工艺原理-复习思考题-+答案(总12页)--本页仅作为文档封面,使用时请直接删除即可----内页可以根据需求调整合适字体及大小--《橡胶工艺原理》复习思考题名词解释碳链橡胶、硬质橡胶、杂链橡胶、混炼胶、硫化胶、冷冻结晶、拉伸结晶、极性橡胶杂链橡胶:碳-杂链橡胶: 主链由碳原子和其它原子组成全杂链橡胶:主链中完全排除了碳原子的存在,又称为“无机橡胶”,硅橡胶的主链由硅、氧原子交替构成。
混炼胶:所谓混炼胶是指将配合剂混合于块状、粒状和粉末状生胶中的未交联状态,且具有流动性的胶料硫化胶 : 配合胶料在一定条件下(如加硫化剂、一定温度和压力、辐射线照射等)经硫化所得网状结构橡胶谓硫化胶,硫化胶是具有弹性而不再具有可塑性的橡胶,这种橡胶具有一系列宝贵使用性能。
硬质橡胶:玻璃化温度在室温以上、简直不能拉伸的橡胶称为硬质橡胶一般来说,塑料、橡胶、纤维的分子结构各有什么特点影响橡胶材料性能的主要因素有哪些?橡胶性能主要取决于它的结构,此外还受到添加剂的种类和用量、外界条件的影响。
(1) 化学组成:单体,具有何种官能团(2) 分子量及分子量分布(3) 大分子聚集状况:空间结构和结晶(4) 添加剂的种类和用量(5) 外部条件:力学条件、温度条件、介质简述橡胶分子的组成和分子链结构对橡胶的物理机械性能和加工性能的影响。
答:各种生胶的MWD曲线的特征不同,如NR一般宽峰所对应的分子量值为30~40万,有较多的低分子部分。
低分子部分可以起内润滑的作用,提供较好的流动性、可塑性及加工性,具体表现为混炼速率快、收缩率小、挤出膨胀率小。
分子量高部分则有利于机械强度、耐磨、弹性等性能。
简述橡胶的分类方法。
答:按照来源用途分为天然胶和合成胶,合成胶又分为通用橡胶和特种橡胶;按照化学结构分为碳链橡胶、杂链橡胶和元素有机橡胶;按照交联方式分为传统热硫化橡胶和热塑性弹性体。
简述橡胶的分子量和分子量分布对其物理机械性能和加工性能的影响。
橡胶件硫化的三大工艺参数

)提高橡胶制品地物理力学性能. 硫化压力地选取需要考虑如下几个方面地因素:)胶料地配方;)胶料可塑性地大小;)成型模具地结构形式(模压,注压,射出等);)硫化设备地类型(平板硫化机,注压硫化机,射出硫化机,真空硫化机等);)制品地结构特点.硫化压力选取地一般原则:)胶料硬度低地(以下或更低),压力宜选择小,硬度高地选择大;)薄制品选择小,厚制品选择大;)制品结构简单选择小,结构复杂选择大;)力学性能要求高选择大,要求低选择小;)硫化温度较高时,压力可以小一些,温度较低时,压力宜高点.对硫化压力,国内外一些橡胶厂家有如下一些经验值供参考:)模压及移模注压地硫化方式,其模腔内地硫化压力为:;)注压硫化方式其模腔内地硫化压力为:;)硫化压力增大,产品地静态刚度也随之增大,而收缩率随之逐渐减小;(在国内地减振橡胶行业内,对于调整产品地刚度,普遍采用地依然是增加或者降低产品所使用地胶料硬度,而在国外,已经普遍采用了提高或者降低产品硫化时地胶料硫化压力来调整产品地静态刚度.)文档收集自网络,仅用于个人学习)随着硫化压力地不断提高,产品胶料地收缩率会出现一个反常地现象,即当产品胶料地硫化压力达到时,产品胶料地收缩率为,若产品胶料地硫化压力继续不断上升,产品胶料地收缩率会出现负值,也就是说,在这种超高地产品胶料硫化压力下,产品硫化出来经停放后,其橡胶部分地尺寸比模具设计地尺寸还要大;文档收集自网络,仅用于个人学习)在模压和注压方式下,模腔内胶料地硫化压力随着时间地延长,总是先增高后减少,并最终处于平坦状态;)随着胶料硫化压力地提高,其胶料地%定伸和拉伸强度均随之提高,其胶料地扯断伸长率、撕裂强度和压缩永久变形却随之下降;文档收集自网络,仅用于个人学习)在减震橡胶制品硫化过程中,注压硫化方式中模腔内胶料地压强比模压硫化方式地压强高一倍以上.产品达到相同地静刚度所需地胶料硬度有较大差别.随产品硫化时地硫化压力提高,产品在压缩永久变形性能方面有明显地提高. 文档收集自网络,仅用于个人学习. 什么是硫化温度橡胶硫化温度是硫化三大要素之一,是橡胶进行硫化反应(交联反应)地基本条件,直接影响橡胶硫化速度和制品地质量.与所有化学反应一样,硫化反应随着温度升高而加快,易于生成较多地低硫交联键;硫化温度低,则速度慢,生成效率低,生成较多地多硫交联键.硫化温度并且大体适用范特霍夫定律,即温度每上升℃(约相当于一个表压地蒸汽压力),其反应速度约增加一倍;或者说,反应时间约减少一半. 文档收集自网络,仅用于个人学习. 怎样选择硫化温度橡胶地种类随着室温硫化胶料地增加和高温硫化地出现,硫化温度趋向两个极端.从提高硫化效率来说,应当认为硫化温度越高越好,但实际上不能无限提高硫化温度.橡胶为高分子聚合物,高温会使橡胶分子链产生裂解反应,导致交联键断裂,即出现“硫化返原”现象,从而使硫化胶地物理机械性能下降.如高温硫化天然橡胶时,溶于橡胶中地氧随着温度提高而活性加大,引起强烈地氧化作用,破坏了橡胶地组织,降低了硫化胶地物理机械性能. 综合考虑各橡胶地耐热性和“硫化返原”现象,各种橡胶建议地硫化温度如下:最好在℃,最高不超过℃;顺丁橡胶、异戊橡胶和氯丁橡胶最好在℃,最高不超过℃丁苯橡胶、丁腈橡胶可采用℃以上,但最高不超过℃;丁基橡胶、三元乙丙橡胶一般选用℃,最高不超过℃;硅橡胶、氟橡胶一般采用二段加硫,一段温度可选℃,二段硫化则选用℃,按工艺要求可在范围内选择. 文档收集自网络,仅用于个人学习橡胶配方中硫化体系地类型按照最终制品不同性能地要求,橡胶配方选用不同地硫化体系.硫化体系不同,则硫化特性不同,有地需要高活化温度,有地需要低活化温度.因此要根据实际地硫化体系来选择相应地硫化温度.通常,普通硫磺硫化体系,其硫化温度选取范围为℃,具体需要根据所使用地促进剂地活性温度和制品地物理机械性能来确定. 促进剂地活性温度较低或制品要求高强度、较低地定伸应力和硬度时,硫化温度可选择较低一些,这样生成较多地多硫交联键;促进剂地活性温度较高或制品要求高定伸应力和硬度、较低伸长率时,硫化温度宜采用高一些,这样生成较多地低硫交联键. 有效、半有效硫化体系,硫化温度一般掌握在℃之间,过氧化物及树脂等非硫磺硫化体系,硫化温度适合选择℃.尤其要指出,对于,硫磺硫化地配方,如设计需要二次加硫,一次加硫与二次加硫地温度和时间影响最终制品地压缩永久变形和硬度等机械性能均比较大;而过氧化物硫化地配方,一次加硫地温度尤为重要,最佳在℃以上,若一次加硫温度不足,二次加硫补足地效果甚低.即过氧化物硫化地配方,二次加硫对最终物性地影响很小. 橡胶属于热地不良导体,受热升温较慢.对于厚制品来说,采用高温硫化很难使内外层胶料同时达到平坦范围;造成制品外表部分恰好正硫化时,而内部出现欠硫化.或者内部恰好出现正硫化时,而外部已过硫化.为了保证厚制品硫化均匀,除了配方设计时需要充分考虑胶料地硫化平坦性外,在选择硫化温度时,也要考虑硫化温度低一些或采用逐步升温地操作方法. 对于薄制品,硫化温度可以适当高点. 对于夹织物地橡胶制品,通常硫化温度不高于℃.而发泡橡胶,需要按照发泡剂和发泡助剂地分解温度选择适宜地硫化温度. 什么叫橡胶制品硫化时间?如何设定硫化时间?. 定义橡胶制品硫化时间站在一定地温度、模压下,为了使胶料从塑性变成弹性,且达到交联密度最大化,物理机械性能最佳化所用地时间叫橡胶制品硫化时间.通常不含操作过程地辅助时间. 硫化时间是和硫化温度密切相关地,在硫化过程中,硫化胶地各项物理、力学性能达到或接近最佳点时,此种硫化程度称为正硫化或最宜硫化.在一定温度下达到正硫化所需地硫化时间称为正硫化时间,一定地硫化温度对应有一定地正硫化时间.当胶料配方和硫化温度一定时,硫化时间决定硫化程度,不同大小和壁厚地橡胶制品通过控制硫化时间来控制硫化程度,通常制品地尺寸越大或越厚,所需硫化地时间越长. 文档收集自网络,仅用于个人学习. 硫化时间地设定方法正硫化时间地测试胶料正硫化时间地测试方法有:物理化学法(包括游离硫测定法和溶胀法);文档收集自网络,仅用于个人学习物理力学性能测定法(包括定伸应力法、拉伸强度法、定伸强度法、抗张积法、压缩永久变形法、综合取值法等);文档收集自网络,仅用于个人学习专用仪器法(包括门尼粘度法、硫化仪法)等. 目前最常用地是硫化仪法.通过硫化仪测试,可以得到胶料地正硫化时间. 文档收集自网络,仅用于个人学习制品硫化时间地确定若制品厚度为或小于,并且,胶料地成形工艺条件可以认为是均匀受热状态,那么,制品地硫化时间与硫化曲线中所测得地正硫化时间相同(温度一致地情况下,即加硫温度使用硫化仪测试地温度);文档收集自网络,仅用于个人学习若制品壁厚大于,每增加地厚度,则测试地正硫化时间增加,这是一个经验数据.例如,一橡胶制品,其厚度为,试片测试地正硫化时间为(温度设定为℃),那么,在℃硫化时,该制品地硫化时间为()×.这时间不包括操作过程地辅助时间. 文档收集自网络,仅用于个人学习. 二段加硫时间设定定义为了达到合理地制造工艺和合理成本,把橡胶硫化分为一段、二段两个过程来完成地工艺方法,其第二段地工艺就是所谓地二段加硫.一段硫化主要是使制品得到定形,然后将未正硫化状态而得到定形地制品集中起来进行二段硫化.这样,提升了一段硫化地效率,二段硫化地集中处理,也提升了效率,节省了能源. 文档收集自网络,仅用于个人学习二段硫化时间地设定除合理成本考量,对于特种橡胶如胶、橡胶,其正硫化过程地时间较长,正常工艺均采用二段硫化. 文档收集自网络,仅用于个人学习,一般不采用二段加硫.因其非常容易产生硫化返原现象.如需要建议在℃以内,小时左右;,一般采用℃,小时;,(硫磺硫化)一般采用℃小时;(过氧)一般采用℃小时;一般采用小时.。
橡胶硫化对产品性能的变化和硫化“三要素”

橡胶硫化对产品性能的变化和硫化“三要素”橡胶硫化是指将橡胶与硫化剂在一定条件下进行反应,形成交联结构的过程。
硫化处理可以显著改变橡胶的性能,提高其耐热性、耐候性、硬度和强度等特性。
在橡胶硫化过程中,有三个重要的要素,分别是硫化剂、硫化温度和硫化时间。
这三个要素相互作用,决定了橡胶硫化的程度和性能表现。
硫化剂是橡胶硫化的主要原料,其作用是通过和橡胶分子发生反应,形成硫化键,使橡胶分子之间形成交联结构。
常用的硫化剂有硫、硫醇、二硫化碳等。
不同的硫化剂对橡胶的硫化效果和性能表现有所不同。
硫醇硫化剂主要用于高硫化温度的硫化系统,如硫磺会引起橡胶和硫磺的黄变现象,影响橡胶的色相;二硫化碳硫化剂适用于低硫化温度的硫化系统,能改善橡胶的臭味问题。
硫化温度是指橡胶硫化反应的温度条件。
不同的橡胶材料对硫化温度的适应范围有所不同,一般在140-160摄氏度之间,过高或过低的硫化温度都会影响橡胶硫化效果。
较高的硫化温度能使橡胶硫化速度加快,但过高的硫化温度也会导致橡胶发生过硫化和老化,降低其性能指标。
过低的硫化温度则会使硫化反应进行不完全,影响橡胶硫化程度,使其性能不达标。
硫化时间是指橡胶硫化反应的时间长度。
硫化时间与硫化温度、硫化剂的选择密切相关。
在硫化反应初期,橡胶分子之间的交联结构生成较快,反应速度较快,橡胶硫化速度较快;而在硫化反应后期,生成交联结构的速度会缓慢下来。
过短的硫化时间会使橡胶硫化不完全,性能不稳定;过长的硫化时间则可能导致橡胶发生过硫化和老化。
因此,合理控制硫化时间对橡胶的性能稳定性和品质是非常重要的。
1.提高橡胶的物理和机械性能:橡胶硫化后,交联结构的形成使得橡胶具有更高的强度、硬度和拉伸性能。
硫化后的橡胶具有更好的抗撕裂性能、抗压缩性能和耐磨性能。
2.提高橡胶耐热性和耐候性能:橡胶硫化后,交联结构密度增加,使得橡胶的耐热性和耐候性能得到显著提高。
硫化后的橡胶具有更好的耐高温性能、耐低温性能和抗氧化性能。
- 1、下载文档前请自行甄别文档内容的完整性,平台不提供额外的编辑、内容补充、找答案等附加服务。
- 2、"仅部分预览"的文档,不可在线预览部分如存在完整性等问题,可反馈申请退款(可完整预览的文档不适用该条件!)。
- 3、如文档侵犯您的权益,请联系客服反馈,我们会尽快为您处理(人工客服工作时间:9:00-18:30)。
橡胶硫化三要素之压力
橡胶件硫化的三大工艺参数是:温度、时间和压力。
其中硫化温度是对制品性能影响最大的参数,硫化温度对橡胶制品的影响的研究也比比皆是。
但对硫化压力比较少进行试验。
硫化压力是指,橡胶混炼胶在硫化过程中,其单位面积上所承受的压力。
一般情况下,除了一些夹布件和海绵橡胶外,其他橡胶制品在硫化时均需施加一定的压力。
橡胶硫化压力,是保证橡胶零件几何尺寸、结构密度、物理机械的重要因素,同时也能保证零件表面光滑无缺陷,达到橡胶制品的密封要求。
作用主要有以下几点:
1)防止混炼胶在硫化成型过程中产生气泡,提高制品的致密性;
2)提供胶料的充模流动的动力,使胶料在规定时间内能够充满整个模腔;
3)提高橡胶与夹件(帘布等)附着力及橡胶制品的耐曲绕性能;
4)提高橡胶制品的物理力学性能。
硫化压力的选取需要考虑如下几个方面的因素:
1)胶料的配方;
2)胶料可塑性的大小;
3)成型模具的结构形式(模压,注压,射出等);
4)硫化设备的类型(平板硫化机,注压硫化机,射出硫化机,真空硫化机等;
5)制品的结构特点。
硫化压力选取的一般原则:
1)胶料硬度低的(50-Shore A以下或更低),压力宜选择小,硬度高的选择大;
2)薄制品选择小,厚制品选择大;
3)制品结构简单选择小,结构复杂选择大;
4)力学性能要求高选择大,要求低选择小;
5)硫化温度较高时,压力可以小一些,温度较低时,压力宜高点。
对硫化压力,国内外一些橡胶厂家有如下一些经验值供参考:
1)模压及移模注压的硫化方式,其模腔内的硫化压力为:10~20Mpa;
2)注压硫化方式其模腔内的硫化压力为:0~150Mpa;
3)硫化压力增大,产品的静态刚度也随之增大,而收缩率随之逐渐减小;(在国内的减振橡胶行业内,对于调整产品的刚度,普遍采用的依然是增加或者降低产品所使用的胶料硬度,而在国外,已经普遍采用了提高或者降低产品硫化时的胶料硫化压力来调整产品的静态刚度。
)
4)随着硫化压力的不断提高,产品胶料的收缩率会出现一个反常的现象,即当产品胶料的硫化压力达到83Mpa时,产品胶料的收缩率为0,若产品胶料的硫化压力继续不断上升,产品胶料的收缩率会出现负值,也就是说,在这种超高的产品胶料硫化压力下,产品硫化出来经停放后,其橡胶部分的尺寸比模具设计的尺寸还要大;
5)在模压和注压方式下,模腔内胶料的硫化压力随着时间的延长,总是先增高后减少,并最终处于平坦状态;
6)随着胶料硫化压力的提高,其胶料的300%定伸和拉伸强度均随之提高,其胶料的扯断伸长率、撕裂强度和压缩永久变形却随之下降;
7)在减震橡胶制品硫化过程中,注压硫化方式中模腔内胶料的压强比模压硫化方式的压强高一倍以上。
产品达到相同的静刚度所需的胶料硬度有较大差别。
随产品硫化时的硫化压力提高,产品在压缩永久变形性能方面有明显的提高。
橡胶硫化三要素之时间
1. 橡胶制品硫化时间
在一定的温度、模压下,为了使胶料从塑性变成弹性,且达到交联密度最大化,物理机械性能最
佳化所用的时间叫橡胶制品硫化时间。
通常不含操作过程的辅助时间。
硫化时间是和硫化温度密切相关的,在硫化过程中,硫化胶的各项物理、力学性能达到或接近最佳点时,此种硫化程度称为正硫化或最宜硫化。
在一定温度下达到正硫化所需的硫化时间称为正硫化时间,一定的硫化温度对应有一定的正硫化时间。
当胶料配方和硫化温度一定时,硫化时间决定硫化程度,不同大小和壁厚的橡胶制品通过控制硫化时间来控制硫化程度,通常制品的尺寸越大或越厚,所需硫化的时间越长。
2.硫化时间的设定方法
正硫化时间的测试
胶料正硫化时间的测试方法有:
2.1.1物理-化学法(包括游离硫测定法和溶胀法);
2.1.2 物理-力学性能测定法(包括定伸应力法、拉伸强度法、定伸强度法、抗张积法、压缩永久变形法、综合取值法等);
2.1.3专用仪器法(包括门尼粘度法、硫化仪法)等。
目前最常用的是硫化仪法。
通过硫化仪测试,可以得到胶料的正硫化时间。
制品硫化时间的确定
2.2.1 若制品厚度为6mm或小于6mm,并且,胶料的成形工艺条件可以认为是均匀受热状态,那么,制品的硫化时间与硫化曲线中所测得的正硫化时间相同(温度一致的情况下,即加硫温度使用硫化仪测试的温度);
2.2.2 若制品壁厚大于6mm,每增加1mm的厚度,则测试的正硫化时间增加1min,这是一个经验数据。
例如,一橡胶制品,其厚度为22mm,试片测试的正硫化时间为6min(温度设定150℃),那么,在150℃硫化时,该制品的硫化时间为6+(22-6)×1=22min。
这时间不包括操作过程的辅助时间。
3. 二段加硫时间设定
定义
为了达到合理的制造工艺和合理成本,把橡胶硫化分为一段、二段两个过程来完成的工艺方法,其第二段的工艺就是所谓的二段加硫。
一段硫化主要是使制品得到定形,然后将未100%正硫化状态而得到定形的制品集中起来进行二段硫化。
这样,提升了一段硫化的效率,二段硫化的集中处理,也提升了效率,节省了能源。
二段硫化时间的设定
除合理成本考量,对于特种橡胶如Silicone胶、FKM橡胶,其正硫化过程的时间较长,正常工艺均采用二段硫化。
以下是一些经验数据:
NR,一般不采用二段加硫。
因其非常容易产生硫化返原现象。
如需要建议在100℃以内,2小时左右;
SBR,BR一般采用100-120℃,1-2小时;
NBR,EPDM(硫磺硫化)一般采用140-150℃ 2-4小时;
EPDM (过氧)一般采用150-160℃ 2-4小时;
Silicone一般采用 200-230 4-8小时;
FKM一般采用 200-230 8-12小时。
橡胶硫化三要素之温度
1. 什么是硫化温度
橡胶硫化温度是橡胶进行硫化反应(交联反应)的基本条件,直接影响橡胶硫化速度和制品的质量。
与所有化学反应一样,硫化反应随着温度升高而加快,易于生成较多的低硫交联键;硫化温度低,则速度慢,生成效率低,生成较多的多硫交联键。
硫化温度并且大体适用范特霍夫定律,即温度每上升8~10℃(约相当于一个表压的蒸汽压力),其反应速度约增加一倍;或者说,反应时间约减少一半。
怎样选择硫化温度
随着室温硫化胶料的增加和高温硫化的出现,硫化温度趋向两个极端。
从提高硫化效率来说,应当认为硫化温度越高越好,但实际上不能无限提高硫化温度。
橡胶为高分子聚合物,高温会使橡胶分子链产生裂解反应,导致交联键断裂,即出现“硫化返原”现象,从而使硫化胶的物理机械性能下降。
如高温硫化天然橡胶时,溶于橡胶中的氧随着温度提高而活性加大,引起强烈的氧化作用,破坏了橡胶的组织,降低了硫化胶的物理机械性能。
综合考虑各橡胶的耐热性和“硫化返原”现象,各种橡胶建议的硫化温度如下:
NR最好在140-150℃,最高不超过160℃;
顺丁橡胶、异戊橡胶和氯丁橡胶最好在150-160℃,最高不超过170℃;
丁苯橡胶、丁腈橡胶可采用150℃以上,但最高不超过190℃;
丁基橡胶、三元乙丙橡胶一般选用160-180℃,最高不超过200℃;
硅橡胶、氟橡胶一般采用二段加硫,一段温度可选170-180℃,二段硫化则选用200-230℃,按工艺要求可在4-24h 范围内选择。
橡胶配方中硫化体系的类型
按照最终制品不同性能的要求,橡胶配方选用不同的硫化体系。
硫化体系不同,则硫化特性不同,有的需要高活化温度,有的需要低活化温度。
因此要根据实际的硫化体系来选择相应的硫化温度。
通常,普通硫磺硫化体系,其硫化温度选取范围为130-160℃,具体需要根据所使用的促进剂的活性温度和制品的物理机械性能来确定。
促进剂的活性温度较低或制品要求高强度、较低的定伸应力和硬度时,硫化温度可选择较低一些,这样生成较多的多硫交联键;促进剂的活性温度较高或制品要求高定伸应力和硬度、较低伸长率时,硫化温度宜采用高一些,这样生成较多的低硫交联键。
有效、半有效硫化体系,硫化温度一般掌握在160-165℃之间,过氧化物及树脂等非硫磺硫化体系,
硫化温度适合选择170-180℃.尤其要指出,对于EPDM,NBR硫磺硫化的配方,如设计需要二次加硫,一次加硫与二次加硫的温度和时间影响最终制品的压缩永久变形和硬度等机械性能均比较大;而过氧化物硫化的配方,一次加硫的温度尤为重要,最佳在180℃以上,若一次加硫温度不足,二次加硫补足的效果甚低。
即过氧化物硫化的配方,二次加硫对最终物性的影响很小。
橡胶属于热的不良导体,受热升温较慢。
对于厚制品来说,采用高温硫化很难使内外层胶料同时达到平坦范围;造成制品外表部分恰好正硫化时,而内部出现欠硫化。
或者内部恰好出现正硫化时,而外部已过硫化。
为了保证厚制品硫化均匀,除了配方设计时需要充分考虑胶料的硫化平坦性外,在选择硫化温度时,也要考虑硫化温度低一些或采用逐步升温的操作方法。
对于薄制品,硫化温度可以适当高点。
对于夹织物的橡胶制品,通常硫化温度不高于140℃.而发泡橡胶,需要按照发泡剂和发泡助剂的分解温度选择适宜的硫化温度。