粗轧区控制功能说明书
贵钢粗中轧简明操作手册
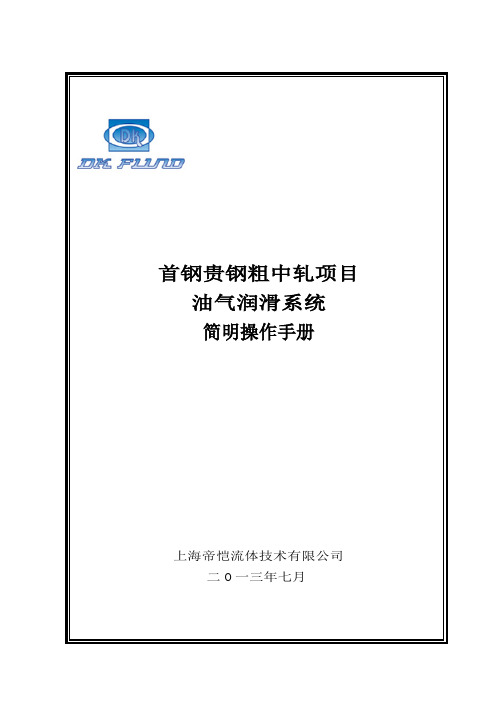
目录1. 引言 (3)1.1.本册说明 (3)1.2.注意事项 (3)1.3.功能描述 (3)1.4.油气润滑的优点 (3)2. 系统综述 (4)2.1.系统介绍 (4)2.2.系统参数 (4)3. 电控功能描述 (5)3.1.概述 (5)3.2.PLC符号表 (5)4. 故障诊断 (6)4.1.常见故障 (6)4.2.系统面板说明 (6)4.3.分配器故障 (8)5. 附录 (9)5.1.ABB通讯信号 (9)5.2.机械文件 (9)5.3.电气文件 (9)1.引言1.1.本册说明本手册为《首钢贵阳特殊钢有限公司油气润滑系统操作手册》副册,便于用户简明了解此润滑系统,查询系统参数以及快速排除系统故障。
1.2.注意事项使用此系统前请熟知本系统安全使用总则,安全总则见主册。
1.3.功能描述本油气润滑系统可用于自动向润滑点供送润滑剂,它是一种利用压缩空气对润滑剂进行输送及分配的集中润滑系统,适用于高温、重载、高速、极低速以及有冷却水和脏物侵入润滑点的工况条件恶劣的场合,如各种运输线、单机架或串列机架轧机、线材轧机、连铸机上等。
1.4.油气润滑的优点1.4.1.技术先进典型的“气液两相流体冷却润滑技术”形成的气液“两相膜”承载能力大大提高由于润滑膜厚度的增加,使润滑膜形成率提高,具有优良的润滑减磨作用。
实现以均等的时间分配润滑油的方式,润滑油可以连续输送。
油气分配器的油气进口处的空气速度高,这是油气润滑效果是否明显的关键。
因润滑剂消耗量极其微小,不会产生多余的热量。
润滑油可以实现按需分配,油气分配均匀并可实现按比例分配。
连续不断的压缩空气有利于轴承的冷却压缩空气在轴承内部能保持约0.3bar压,能阻止脏物和水的侵入,使轴承具有良好的密封性能。
一套油气润滑系统可向多达1500个润滑点送油气流,且油气管道的走向不受限制。
能使用高粘度的机械油甚至半流动润滑脂有非常完善的对油气润滑系统的工作状况进行监控的手段。
轧钢飞剪控制功能规格书

控制功能规格书飞剪一、控制设备飞剪系统控制的设备包括:飞剪前辊道(E2)、飞剪前侧导板(HSG2)、飞剪(CS)、废料收集箱、精轧机除磷箱(DES3)、精轧除磷辊道(E3)。
二、工艺过程描述1.剪前辊道安装在热卷箱与飞剪之间,用于将由热卷箱输送来的中间坯料运输到飞剪之间,中间坯料进入精轧机前,剪前辊道线速度与热卷箱开卷速度保持同步,中间坯料进入精轧机后,剪前辊道线速度与F1速度保持同步。
2.飞剪前侧导板用于对中,运送轧件进入飞剪进行剪切。
3.飞剪安装在热卷箱与精轧机列之间。
用于对运行中的中间坯不规则的头部和尾部进行剪切。
切头时将中间坯切成凸形圆弧形,以减少中间坯咬入精轧机架时的冲击载荷,切尾时将中间坯尾部切成后凸形,以减短常在热连轧机中出现的长长的“燕尾”。
飞剪由两台直流电动机串连驱动。
电动机功率为2×500KW,额定转速为900rpm。
电动机经电机联轴器,主减速机(速比I=21.9),主联轴器与下转鼓相联接,上转鼓与下转鼓之间通过同步齿轮相互传动。
传动侧下同步齿轮设有副齿轮,副齿轮与主齿轮之间用弹簧撑开,用以消除齿轮付之间的传动间隙,而实现无隙啮合,以保证上、下剪刃相互位置的准确和减少齿轮付的冲击。
在主电机和主减速机之间设有制动器,制动器的作用主要是保证在剪刃停止时,保持其位置准确,而每次剪切后的制动主要由电气来完成。
转鼓飞剪主要由上、下剪鼓相向同步运转,而装在剪鼓上的两对剪刃对中间坯实行剪切。
在上、下转鼓上分别安装了切头用剪刃和切尾用剪刃,每个转鼓上的两个剪刃成90度布置,按剪时的转动方向看,切尾剪刃在前,切头剪刃在后。
这种布置方法可以使需要剪切时剪鼓的启动角增大。
剪刃下有承载刀座,剪刃刀座侧面还设有垫板,在剪刃的背面有7个角楔块籍蝶形弹簧组的弹力使剪刃被夹紧在转鼓上。
上、下转鼓啮合运行时,上下剪刃间的间隙完全依赖与安装或装配位置来保证。
在制造时应保证剪刃槽互成90度的相对位置和刃槽与同步齿轮的相对位置的一致性。
R1粗轧机说明书

mm热带连轧机R1四辊可逆轧机产品安装调试及使用说明书编号51226MSS集团有限公司设计研究院2004年7月MS1.用途:R1粗轧机是粗轧区的关键设备,与E1组成万能可逆轧机,当连铸坯经加热炉加热好后,除去氧化铁皮,由机前工作辊道送至E1R1机前,由机前推床将钢坯推正、对中轧线,经E1立辊轧边,再送入R1,经来回可逆轧制5~7道次,将厚度160的坯料轧制到规定的厚度、宽度,中间坯再由机后工作辊道送往热卷箱、飞剪区进行热卷及切头切尾,之后进入精轧机区进行轧制。
本设备工艺号为42,图号为51226.00。
相关设备有:支承辊换辊装置59294(工艺号43)工作辊换辊装置59312(工艺号43)E1立辊轧机51225(工艺号41)机前工作辊道53235(工艺号34,35,36,37,38,39)机后工作辊道53236(工艺号46,47,48,49)机前推床5277(工艺号40)机后推床5278(工艺号45)2.技术性能与基本参数坯料规格:160X750~1400X7200~12000mm(厚X 宽X长)中间坯规格:17~30(40)X750~1400X~最大长113mMS坯料最大重量:21t工作辊直径X辊身长:φ1050/φ980 X1550mm支承辊直径X辊身长:φ1350(最大)/φ1250(最小)X1500mm工作辊轴承:4列圆锥φ660.4Xφ812.8X365mm 支承辊轴承:Morgan48 X75 KL型油膜轴承最大轧制压力:3500KN最大轧制力矩:2X2000KN.m轧制速度:2.75~5.5m/s主电机型号:BPT6000-12交流变频电机2台主电机功率:6000KW主电机转速:50/100r/min轧辊最大开口度:新辊270mm压下速度:5-15-25mm/s压下电机型号:ZKSL-315-41压下电机功率:150KW压下电机转速:385/770r/min压下蜗轮副中心距:A=711.2mm压下蜗轮副速比:i=1.125X18.33=20.64 ZC1型压下螺丝规格:S508X48(P=24)mm双头锯齿型螺纹压下止推轴承:φ609.6 X204.01mm满装锥形滚子止MS推轴承松卡电机型号:ZZJ-808松卡电机功率:37.3 KW松卡电机转速:575/1150 r/min松卡蜗轮副速比:i=50 zc1型单线蜗轮付主平衡液压缸规格:φ380(400) X610 柱塞型mm主平衡液压缸工作压力:7Mpa主平衡液压缸换辊时压力:16Mpa工作辊平衡压靠液压缸规格:8 X120 X400上辊/120下辊mm工作辊平衡压靠液压缸工作压力:7Mpa塞机架辊规格:2Xφ450X1360mm机架辊传动电机:交流变频45KWX370 r/min,YGP355M1-16机架牌坊外形尺寸:高X宽X厚=9660X4700X1435mm 牌坊单片净重:147t牌坊立柱断面:760X980=7448cm2上下工作辊装配件重量:53.56t上支承辊装配件重量: 56t下支承辊装配件重量: 46t支承辊更换移出行程:5280 mmMS支承辊更换移出速度:70 mm/s工作辊更换移出行程:6250 mm工作辊更换移出速度:100 mm/s主传动接轴型式:C型十字头万向接轴主传动接轴规格:φ960/φ1200X9830mm主传动接轴平衡液压缸:上轴φ200/φ110X450mm下轴用φ200/φ110X200mm主传动接轴平衡液压缸工作压力:7Mpa接轴换辊及抱紧液压缸:2Xφ125/φ90X260mm,16Mpa支承辊、工作辊轴向卡板缸:6Xφ80/φ56X80mm,16Mpa上导卫护板摆动气缸规格:φ200X550-MP4 mm下导卫护板摆动气缸规格:φ200X250-MP4 mm工作辊冷却水喷嘴数量/总耗量:4X19=76(个),250t/h 工作辊冷却水压力:8-10bar,浊环水支承辊冷却水喷嘴数量/总耗量:4X19=76(个),137t/h 支承辊冷却水压力:3-4bar,浊环水轧机本体总重量:820t3.设备外形图3.1机列图MS3.2本体外形图3.3压下原理图3.4轧辊窗口位置图4.结构及工作原理说明:4.1机列组成:轧机本体(51226.04—51226.11) ;主接轴及平衡(51226.01-51226.03)主电机及中间轴 J7002(东电图)工作辊换辊装置 59312支撑辊换辊装置 592944.2轧机本体:本轧机本体由机架、轧辊系统、压下及平衡装置、轧辊传动装置、上下导卫护板、轧辊水冷装置、机架辊装置、平台走梯、配管、及电气行程开关布置等组成。
粗轧辅助设备控制
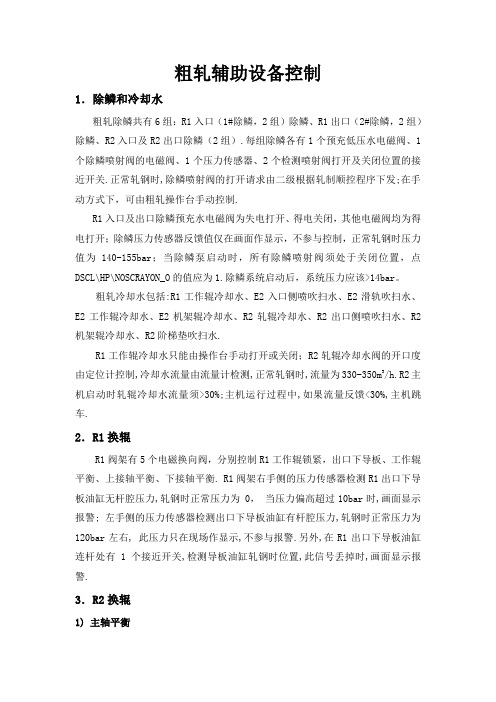
粗轧辅助设备控制1.除鳞和冷却水粗轧除鳞共有6组:R1入口(1#除鳞,2组)除鳞、R1出口(2#除鳞,2组)除鳞、R2入口及R2出口除鳞(2组).每组除鳞各有1个预充低压水电磁阀、1个除鳞喷射阀的电磁阀、1个压力传感器、2个检测喷射阀打开及关闭位置的接近开关.正常轧钢时,除鳞喷射阀的打开请求由二级根据轧制顺控程序下发;在手动方式下,可由粗轧操作台手动控制.R1入口及出口除鳞预充水电磁阀为失电打开、得电关闭,其他电磁阀均为得电打开;除鳞压力传感器反馈值仅在画面作显示,不参与控制,正常轧钢时压力值为140-155bar;当除鳞泵启动时,所有除鳞喷射阀须处于关闭位置,点DSCL\HP\NOSCRAYON_O的值应为1.除鳞系统启动后,系统压力应该>14bar。
粗轧冷却水包括:R1工作辊冷却水、E2入口侧喷吹扫水、E2滑轨吹扫水、E2工作辊冷却水、E2机架辊冷却水、R2轧辊冷却水、R2出口侧喷吹扫水、R2机架辊冷却水、R2阶梯垫吹扫水.R1工作辊冷却水只能由操作台手动打开或关闭;R2轧辊冷却水阀的开口度由定位计控制,冷却水流量由流量计检测,正常轧钢时,流量为330-350m3/h.R2主机启动时轧辊冷却水流量须>30%;主机运行过程中,如果流量反馈<30%,主机跳车.2.R1换辊R1阀架有5个电磁换向阀,分别控制R1工作辊锁紧,出口下导板、工作辊平衡、上接轴平衡、下接轴平衡. R1阀架右手侧的压力传感器检测R1出口下导板油缸无杆腔压力,轧钢时正常压力为 0,当压力偏高超过10bar时,画面显示报警; 左手侧的压力传感器检测出口下导板油缸有杆腔压力,轧钢时正常压力为120bar左右, 此压力只在现场作显示,不参与报警.另外,在R1出口下导板油缸连杆处有1个接近开关,检测导板油缸轧钢时位置,此信号丢掉时,画面显示报警.3.R2换辊1) 主轴平衡正常轧钢时,主轴平衡打在上升位,换辊或检修抽辊时,平衡打到下降位.主轴平衡液压缸各由1个电磁阀控制, 主轴平衡上升位通过2#阀台上的2个压力开关检测.换辊期间,下主轴固定在工作辊换辊位置,上主轴由一个定位盘架支撑,定位盘架可通过一个定位销锁定,定位销液压缸也由1个电磁阀控制, 定位盘架的打开、锁定位置通过2个接近开关来检测.2) 锁紧板锁紧板用于防止轧辊水平的位移使轧辊与轧线方向成直角,换辊时锁紧板必须打开,使辊子能够移出机架.每根辊子由两个锁紧板固定,入口、出口各一个.每个锁紧板各有一个液压缸驱动,液压缸由4#阀台上的电磁换向阀来控制.每个锁紧板各有1个接近开关检测其位置,入口侧4个检测锁紧板关闭位置,出口侧4个检测锁紧板打开位置.3) 导卫R2入口和出口的导卫通过两个液压缸在垂直方向能够手动调节(点动功能),入/出口的导卫可以分别调整上下.导卫的每个升/降缸由一个比例阀控制杠端压力,两个电磁阀控制盲端压力。
1500mm宽带粗轧轧机负荷平衡控制功能
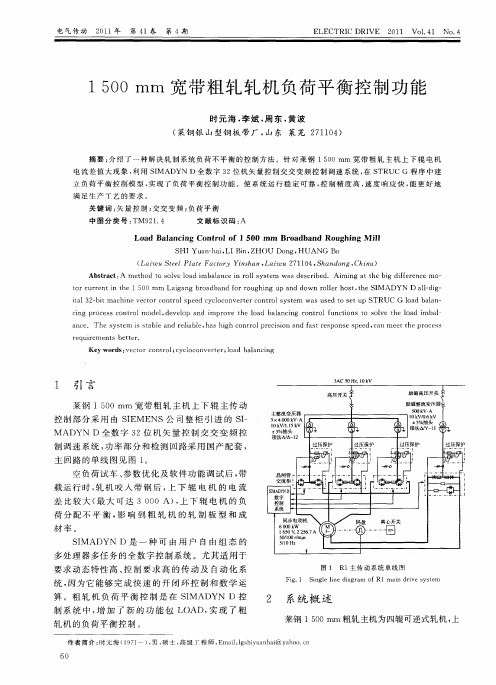
电流 差 值 大 现 象 , 利用 S MADYN D全 数 字 3 I 2位 机 矢 量 控 制 交 交 变频 控 制 调 速 系统 , S 在 TRUC G 程 序 中建
电气 传
EIE CTRI C DRI 2 1 Vo l No 4 VE 01 L4 .
15 mm 宽 带粗 轧 轧 机 负荷 平衡 控 制 功 能 O O
时 元 海 , 斌 , 东 , 波 李 周 黄 ( 钢 银 山型 钢 板 带 厂 , 东 莱 芜 2 1 0 ) 莱 山 7 1 4
立 负 荷 平 衡 控 制 模 型 , 现 了负 荷 平 衡 控 制 功 能 。使 系 统 运 行 稳 定 可 靠 , 制 精 度 高 , 度 响应 快 , 更 好 地 实 控 速 能
满 足 生 产 T 艺 的要 求 。
关 键 词 : 量 控制 ; 矢 交交 变频 ; 荷 平 衡 负
中图 分 类 号 : TM9 1 4 2 . 文 献标 识 码 : A
图 1 R 1主 传 动 系 统单 线 图
Fi . Si g e l ig a o i rv y t m g 1 n l i d a r m f R1 man d i e s s e ne
t ur e n t e 1 0 ll g ng br a orc r nti h 5 0 n I Laia o dba d f o hi g up a d d l n orr ug n n own r le s ,he S M ADY N ald g o lrho t t I D l— i — ia 一 tm ac neve t onto pe d c 1c v r e onto yse wa s d t e t l32 bi hi corc r ls e yco on e t rc r ls t m s u e o s tup STRU C l a ln— G o d ba a cn o e sc nt o ig pr c s o r lmod l de eop a d i p o e t o d baan i on r lf e , v l n m r v he la l cng c t o unc i t s ve t oa i ba— tons O ol he l d m l
扁钢粗轧区微张力控制特点分析
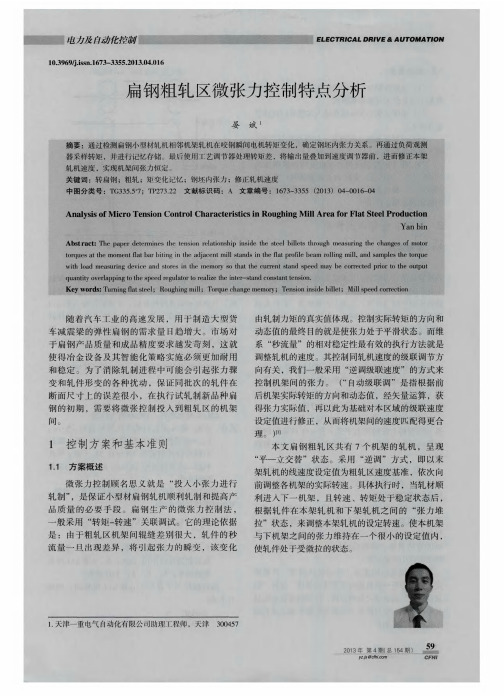
EL E cT Rl c AL DR l vE & A U T O M ATl o N
作为微张调节的设定值。
( 3 ) 微 张 调 节 时 ,当下 一 架 轧 机 咬 钢 速 降恢 复 后 ,本 架 轧 机 此 时 的 转 矩 已发 生 变 化 ,经 过 采 样 并 取 均 值 后 ,将 获 得 的 二 次转 矩 作 为 微 张 调 节
一
量 技市
电力及自 动化控制 l '
1 . 2 准 则要 求
n 架轧机
轧制: 刖
l q +1 架轧机
( 1 )试验轧制中,张力实际值不能太小 , 否则 容 易 引发轧 件大 范 围堆 钢事 故 。
( 2 )要 保证 张力 实际值 在绝 大多 数时 间 内处 于
稳 定状 态 。
M2
△ : c ( 一 )……………… ( 1 )
/ t M < 0则 为堆 钢 ;△ > 0则 为拉 钢 。 式 中 ,△ 一第 n架 轧 机 的 电机 转 矩 偏 差 ( N・ m ) ; c 磁 通饱 和 时 电机 常数 ; 。 _第 n架 轧 机 的 自由轧 制 转 矩 ( N・ r n ) ; 厂 第 n架 轧 机 的二 次采 样转 矩 ( N・ m ) ;K . 微 张 力 系数 的设定值 。 转矩 变化 量 △ 折算 到 速度 级联 调节 ,则 第 n
( 3 ) 待 稳 定 后 ,依 据 微 张力 的设 定 系 数 ,
调节第 n架轧机的速度 ,使 一 维持在很微小
的负 向稳 定值 区域 内。 ( 4 ) 轧件 继续 前 行 ,在 被 第 n + 2机 架 咬 入前 , 第 n + l机 架 处 于 自由轧 制 状 态 ,此 时跟 踪 第 n + l
粗轧区设计说明
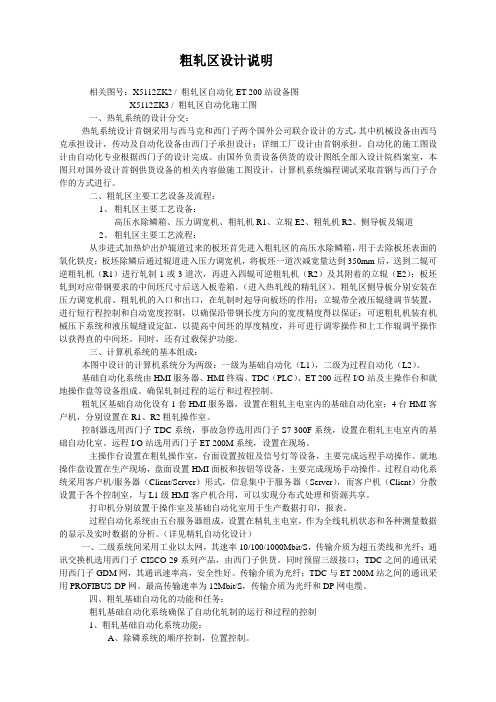
粗轧区设计说明相关图号:X5112ZK2 / 粗轧区自动化ET-200站设备图X5112ZK3 / 粗轧区自动化施工图一、热轧系统的设计分交:热轧系统设计首钢采用与西马克和西门子两个国外公司联合设计的方式,其中机械设备由西马克承担设计,传动及自动化设备由西门子承担设计;详细工厂设计由首钢承担。
自动化的施工图设计由自动化专业根据西门子的设计完成。
由国外负责设备供货的设计图纸全部入设计院档案室,本图只对国外设计首钢供货设备的相关内容做施工图设计,计算机系统编程调试采取首钢与西门子合作的方式进行。
二、粗轧区主要工艺设备及流程:1、粗轧区主要工艺设备:高压水除鳞箱、压力调宽机、粗轧机R1、立辊E2、粗轧机R2、侧导板及辊道2、粗轧区主要工艺流程:从步进式加热炉出炉辊道过来的板坯首先进入粗轧区的高压水除鳞箱,用于去除板坯表面的氧化铁皮;板坯除鳞后通过辊道进入压力调宽机,将板坯一道次减宽量达到350mm后,送到二辊可逆粗轧机(R1)进行轧制1或3道次,再进入四辊可逆粗轧机(R2)及其附着的立辊(E2);板坯轧到对应带钢要求的中间坯尺寸后送入板卷箱。
(进入热轧线的精轧区)。
粗轧区侧导板分别安装在压力调宽机前、粗轧机的入口和出口,在轧制时起导向板坯的作用;立辊带全液压辊缝调节装置,进行短行程控制和自动宽度控制,以确保沿带钢长度方向的宽度精度得以保证;可逆粗轧机装有机械压下系统和液压辊缝设定缸,以提高中间坯的厚度精度,并可进行调零操作和上工作辊调平操作以获得直的中间坯。
同时,还有过载保护功能。
三、计算机系统的基本组成:本图中设计的计算机系统分为两级:一级为基础自动化(L1),二级为过程自动化(L2)。
基础自动化系统由HMI服务器、HMI终端、TDC(PLC)、ET-200远程I/O站及主操作台和就地操作盘等设备组成。
确保轧制过程的运行和过程控制。
粗轧区基础自动化设有1套HMI服务器,设置在粗轧主电室内的基础自动化室;4台HMI客户机,分别设置在R1、R2粗轧操作室。
AWC粗轧区自动化功能
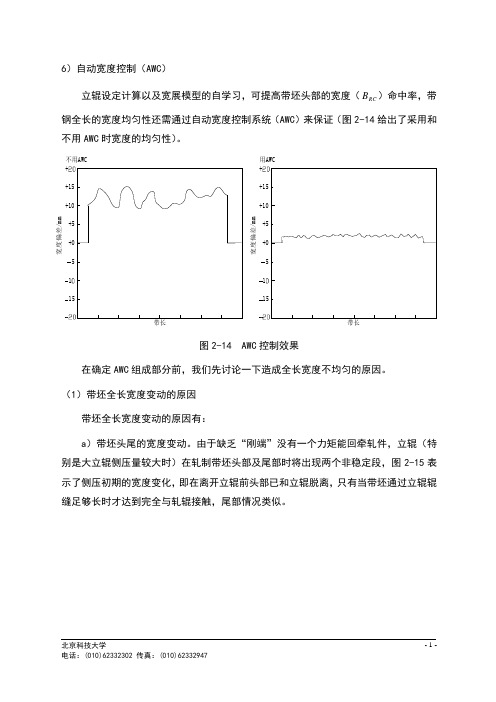
6)自动宽度控制(AWC)立辊设定计算以及宽展模型的自学习,可提高带坯头部的宽度((1)带坯全长宽度变动的原因带坯全长宽度变动的原因有:a)带坯头尾的宽度变动。
由于缺乏“刚端”没有一个力矩能回牵轧件,立辊(特别是大立辊侧压量较大时)在轧制带坯头部及尾部时将出现两个非稳定段,图2-15表示了侧压初期的宽度变化,即在离开立辊前头部已和立辊脱离,只有当带坯通过立辊辊缝足够长时才达到完全与轧辊接触,尾部情况类似。
都将造成成品宽度波动。
AWC系统一方面应能克服粗轧区本身所造成的宽度不匀,还应能补偿精轧机、卷取机所造成的有规律的宽度变动。
d)带坯进精轧温度变化时将改变F1~F3的宽展量,有可能使成品宽度超过规定指标。
由于精轧区及卷取机所造成的宽度不匀只能由精轧出口处测宽仪实测,在宽度设定模型及AWC控制系统中除粗轧机前后测宽仪外应充分利用成品测宽仪所提供的信息。
利用此信息可以对B进行修正,并获得有规律的宽度变动在AWC控制中加以补偿。
RC(2)AWC的组成b) SSC——短行程控制,用以补偿头部和尾部的失宽。
c) RF-AWC——轧制力反馈AWC,类似于GM-AGC的功能,动态调节立辊开口度来获得均匀宽度。
d) FF-AWC——前馈AWC,当轧机前设有测宽仪时利用其所检测出入口宽度偏差对立辊开口度进行前馈调节以提高出口宽度均匀性。
e) NEC ——缩颈补偿,用来补偿卷取机切换到张力控制时对带钢的冲击(拉钢)所造成的缩颈(宽度变窄)。
f)宽度自学习,利用粗轧及精轧出口处测宽仪实测信息对宽度模型进行学习。
下面分节对以上功能进行讨论。
(3)SCC 功能当粗轧区采用VSB 调节产品宽度时,将在头部形成失宽。
为了使头部宽度保持均匀需在各道立辊轧制时先将开口度加大,当板坯咬人(或立辊前HMD 检得时)随轧人长度逐步收小开口度到设定值。
开口度随轧入长度收小的曲线应根据VSB 后或粗轧区出口处测宽仪所测信息及根据事先统计所得的存于计算机内的曲线进行开口度收小(应用粗轧出口测宽仪信息对曲线进行学习修正)。
粗轧设备运行的操作
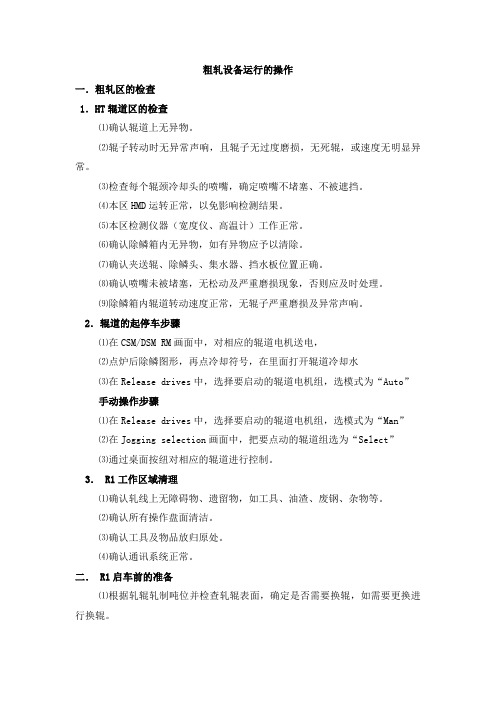
粗轧设备运行的操作一.粗轧区的检查1.HT辊道区的检查⑴确认辊道上无异物。
⑵辊子转动时无异常声响,且辊子无过度磨损,无死辊,或速度无明显异常。
⑶检查每个辊颈冷却头的喷嘴,确定喷嘴不堵塞、不被遮挡。
⑷本区HMD运转正常,以免影响检测结果。
⑸本区检测仪器(宽度仪、高温计)工作正常。
⑹确认除鳞箱内无异物,如有异物应予以清除。
⑺确认夹送辊、除鳞头、集水器、挡水板位置正确。
⑻确认喷嘴未被堵塞,无松动及严重磨损现象,否则应及时处理。
⑼除鳞箱内辊道转动速度正常,无辊子严重磨损及异常声响。
2.辊道的起停车步骤⑴在CSM/DSM RM画面中,对相应的辊道电机送电,⑵点炉后除鳞图形,再点冷却符号,在里面打开辊道冷却水⑶在Release drives中,选择要启动的辊道电机组,选模式为“Auto”手动操作步骤⑴在Release drives中,选择要启动的辊道电机组,选模式为“Man”⑵在Jogging selection画面中,把要点动的辊道组选为“Select”⑶通过桌面按纽对相应的辊道进行控制。
3. R1工作区域清理⑴确认轧线上无障碍物、遗留物,如工具、油渣、废钢、杂物等。
⑵确认所有操作盘面清洁。
⑶确认工具及物品放归原处。
⑷确认通讯系统正常。
二. R1启车前的准备⑴根据轧辊轧制吨位并检查轧辊表面,确定是否需要换辊,如需要更换进行换辊。
⑵进行轧制线高度检查并调整。
⑶轧机区现场清理及设备检查。
⑷辅助系统准备。
各液压系统、润滑系统、冷却系统、除鳞系统、排水系统、通风系统启动并正常。
⑸供电启动正常。
⑹操作设备正常,各操作台操作盘面指示状态正常,HMI画面信息和设定数据正常。
无紧急停车、无报警。
全部地面站选择开关至PULPIT位置。
⑺各设备经手动测试动作正常。
⑻对各设备进行标定。
⑼确定生产规格,设定工艺参数。
起车步骤辊道的起停车步骤⑴在CSM/DSM RM画面中,给主电机送电,⑵点击Cooling,在里面打开辊辊冷却水⑶在Release drives中,选择主电机控制模式为“Auto”除鳞的手动操作步骤⑴点炉后除鳞图形,将除鳞的模式改为“MAN”⑵通过桌面按纽进行手动操作。
1 一、粗轧主要设备及功能

在轧机运行或停车状态均可进行R1轧机的标 定,因工作辊直径较小时轧机上下接轴在工作辊 压靠状况会出现干涉,故要求当R1工作辊直径小 于915mm时采用静态清零,当R1工作辊直径大于 915mm时采用动态清零。
减 速 开 始
抛 钢 速 度
减 速 停 转
时间
三角形速度制度图
17
三、粗轧机的速度制度
• 3、轧制速度的给定 手动轧制时 手动轧制时,水平轧制速度由脚踏主令控制器控制,既 当“主机速度选择旋钮”选至一定档位时,脚踏主令控制 器可在该档位能达到的最高速度范围内控制轧机速度;立 辊轧机随水平轧机联动。 半自动轧制时 自动轧制时,操作工在操作台面选定速度档位后,水平 轧机和立辊轧机速度由PLC控制。 自动轧制时 自动轧制时粗轧机的速度由二级模型给出,但操作工可 以在L2HMI跟踪画面通过速度升降按钮选择需要的轧制速 度。
第三道次定位完成
R2第三道次带坯头部 经 HMD210 检得, R2 速度基准由热卷箱给 出,直到R2抛钢
R2轧制结束
侧压、压下、侧导板自动 定位到安全位置,以待钢 速度等待下一块钢的轧制
14
三、粗轧机的速度制度
• 粗轧机根据所轧带坯的长短有梯形和三角 形两种速度制度,如果所轧带坯的长度超 过临界长度时为梯形速度制度,当所轧带 坯长度小于临界长度时为三角形速度制度, 其速度制度图如下:
25
六、粗轧轧制时常见的异常情况
• 2、机架内堆钢 原因:
1)由于侧压、侧导板开口度基准或侧压误动作引起侧压、 侧导板开口度过小,偶道次轧制带坯不能顺利通过立辊轧机、 侧导板,导致带坯在立辊轧机、水平轧机间堆钢。 2)偶道次板形严重不良,带坯侧弯撞击立辊轧机导卫装置, 撞击机前侧导板或辊道边板引起带坯在立辊轧机、水平轧机间 堆钢。 3)偶道次扣头、翘头严重,偶道次的头部撞击机架内设备 引起立辊轧机、水平轧机间堆钢。 4)机架内护板过高、水梁位置过低,偶道次轧制带坯头部 撞击护板或水梁引起立辊轧机、水平轧机间堆钢。 5)奇道次轧制由于立辊与水平辊速度不匹配,立辊速度高 于水平辊速度引起立辊轧机、水平轧机间堆钢。
不锈钢热轧线粗轧区简介

WR&BUR Balance Cylinder
STRIPPER
Stripper可以防止鋼坯在軋延 中沿工輥跑進機台內。也可防 止冷卻水滴入鋼坯,造成鋼坯 溫降的不確定因素。 Top Stripper靠Cylinder Force依附在輥上;Bottom Stripper靠自身重量依附在 輥上。
RM “WORK ROLL CHANGE”
W+W3
W+W2 W+W2 W+W2 W+W2 W+W3
VE
“ZEROING”
操作流程: 1、Opening調整裝置量測其Gap W0 2、操作員實際測量其Gap W0 3、重新輸入Gap W0的值
操作前準備: 1、確認操作場合安全 2、確認液壓系統是否正常 (not alarm condition active) 3、確認主馬達是否停止(完全不轉動) 4、確認APC cylinder的APC控制是否正常 5、確認VE “Pull Back” 6、確認有裝上Edger Roll
WORK ROLL CHANGE “PREPARATION”
1、注意自身工作安全 2、確認主馬達定位心軸、冷卻系統停止、駝車已就準備位置 3、WR balance 開啟並升至最上方(Top On) 4、Push-up Cylinder移置換輥位置(S = 3mm APC) 5、Bottom Spindle Balance “ OFF ”
7、換輥油壓缸拉至最外邊,吊走Stool並更換下背輥 8、將新下背輥推入軋機內並裝上 (Bot. BUR Clamp “Clamp”)
ROUGHING MILL
PASS LINE ADJUST
在軋延的時候版坯厚度會減小,而Pass Line也會隨之改變。 Actual Pass Line與Table Pass Line的高度差會造成板坯頭尾的翹曲。 H和h的值會因為軋延到次跟來坯材料不同而有所改變, 因此∆X值也會隨之不同, ∆X由Level 2設定,設定標準以實際操作為準。 建議之∆X應不小於 ( H − h ) / 2
重钢4100宽厚板粗轧机使用说明书

轨道安装在机架中部,伸出操作侧牌坊与换辊装置桥架相接。牌坊经过有限
重钢4100 四辊粗轧机使用说明书
第 8 页 共 31 页
元应力分析及优化设计用铸钢(ZG230-450)整铸而成。牌坊内侧设计有紧固
4. 机列及轧机本体外形图 ..................................... 3
5. 规格及性能............................................... 3
6. 轧机工作原理与基本特点.................................... 5
¢100/¢70×380
¢1210/¢1110×4100 ¢2200/¢2000×4000
工作 压力 21Mpa
~165(上81,下84)
~550(上264,下254,支架32)
>7900
15085×4700×2200
339.5t/95×90=8550
4.1. 机列图见图一
4.2. 本体外形图见图二。
5. 规格及性能
序 号
参 数 名 称
1 轧机型式
2 最大轧制力 3 传递轧制力矩
单位 数 值
KN KN-m
四辊可逆式宽厚板轧机 60000 2×1432
备 注
重钢4100 四辊粗轧机使用说明书
序 号
参 数 名 称
单位 数 值
备 注
25
阶梯垫调整液压 缸规格
mm
26
下辊辊面标高调 整范围
mm
27 测压仪规格
28
除鳞高压水压力、 耗量、介质
29
精轧区设备功能说明书

河北永年永洋扁钢工程精轧区设备控制功能说明书室审:组审:审核:设计:天津市中重科技电气传动自动化工程有限公司2012年10月一、精轧机组1. 概述●对开坯机轧出的中间坯进行连续轧制,轧成满足要求的合格热态成品;●轧机形式:短应力线轧机。
2. 电气元件●平辊轧机电机7台●立辊轧机电机3台●电机编码器10个●水平辊压下绝对值编码器10个●轧机扁头定位接近开关10个●换辊缸接近开关30个●横移缸接近开关3个●换辊小车接近开关60个●换辊缸电磁阀11个●立辊压下液压马达电磁阀12个●水平辊压下液压马达电磁阀32个●插销液压缸电磁阀20个●机架锁紧缸电磁阀20个●机架油流接近开关11个●减速机油流变送器11个●电机定转子温度检测仪表10个●●●3. 功能说明轧机传动●H1,H3,H4,H6,H7,H9轧机电机为1000kW,V2,V5,H10轧机电机为733kW,V8-1轧机电机为733kW,用于轧制大规格成品。
V8-2轧机电机为200KW,用于轧制小规格成品;所有轧机的电压等级为DC660V。
●传动形式:采用SIMOREG DC MASTER 6RA70 系列全数字调速系统;(其中1H,3H,H7,8V1,8V2为新控制柜,其余轧机控制柜为利旧装置。
)●网络形式:区域光纤以太网配以局部DP通讯。
辊缝调整●水平辊压下装置用来调整水平辊辊缝,其压下方式采用液压马达传动,绝对值编码器检测位置并在机旁操作箱数字显示仪表进行显示,轧机机身配有刻度盘方便人工观察;换辊●通过液压换辊缸和换辊小车实现换辊;●扁头定位:轧机自动以点动速度旋转至定位接近开关处停止,可以提高换辊速度;●在轧制状态时,机架锁紧液压缸前进,所有插销缸插紧,机架锁紧继电器有信号并且插销缸接近开关有信号时,表示机架已锁紧,插销缸到位,可以轧制。
4.联锁●对应机架锁紧,插销缸到位,润滑液压无故障,对应轧机已送电且无故障时,轧机才能启动。
(注意内控/外控)●轧机启动过程中,若机架锁紧信号消失或者润滑出现故障时,轧机将延时停止。
粗轧区控制能说明书

粗轧区以E1立辊轧机和R1四辊粗轧机为核心。
E1立辊轧机前配置有E1机前工作辊道(一) — (六)和E1机前推床。
R1轧机后配置有R1机后推床和R1机后工作辊道 (一) - (四)。
在E1立辊轧机前还配有E1前高压水除鳞集管。
经粗轧除鳞后的热板坯进入E1前工作辊道,逐渐向E1、R1轧机方向运动。
板坯进入E1前工作辊道(一) 后, E1机前推床由等待位置向轧制线中心靠拢.在工作辊道 (六) 和板坯住手后, E1 机前推床对板坯实行对中夹持。
在夹持位的瞬间推窗液压缸无杆腔压力陡增,由压力继电器信号指挥推窗液压缸反向,推板向后退开0-50mm,由计算机、光电编码器信号可以调节退开量。
在推床退开的同时启动E1机前辊道,对中后处于轧制线中心的轧件被辊道送到E1立辊轧机。
E1立辊轧机在轧件进入前,已经设定好立辊开口度,对轧件进行小于 40mm的侧压轧制。
立辊轧机轧出后轧件经R1轧机入口机架辊,进入四辊轧机工作辊进行轧制。
由于坯长远大于E1和R1中心距,所以在E1和R1之间存在同时轧制的时间较长。
由于E1轧机主机电远远小于R1轧机的主机电,因此不允许R1轧机的轧制速度低于E1出口速度,而必须保持R1和E1轧制同步或者E1微微地被R1拉动。
即是在R1与E1之间保持无张力或者微张力轧制。
在R1轧机轧出之前R1后推床必须开到最大开口位置。
当轧件彻底离开 R1轧件之后,R1机后推床向中心合拢将轧件再次对中。
同样在对中夹持后,即将后退0-50mm,引导轧件对中运行。
当R1机后工作辊道反向后,轧件返回R1轧机进行第2道次的轧制。
在第2道次的返回轧制时, E1立辊轧机要后退每边约50mm,并反向运转。
E1前推床更要后退到彻底打开位置……就这样对轧件进行往复轧制,在E1-R1轧机上要进行3-5 道次轧制,每单道次轧制时E1立辊轧机参预轧制,偶道次E1立辊轧机不参预轧制。
由于板坯在E1-R1上的轧制时间较长,轧件表面在高温下会再次氧化,或者粗除鳞箱除鳞未尽时,根据工艺需求在某些单道次前还可以利用E1立辊前高压水除鳞集管,进行喷射高压水除鳞。
粗轧机功能描述-rev01

Job 0053 ContractualitemZY-2004-66-NE-4-1ERZHONG item(04)325301TitleRoughing Mill Functional DescriptionApprovalsRemarks02 05-01-0501 04-12-8 ERZHONG ISSUE OF DETAIL DESIGNPHASEHu YiGe XianyuLu Qingchun Qi Xiaohu00 04-07-22 ERZHONG ISSUE OF DESIGN PHASE Hu YiGe XianyuLu Qingchun Qi XiaohuRev. File Date Revisions description Drawn Checked Approved1设备总体概况3 2设备分项说明32.132M2005-2021粗轧机本体(13253.204) (3)2.1.132M2005: R1 - MILL SPINDLE HEAD HOLDER (13253.204.11) (3)2.1.1.1设备概况 (3)2.1.1.2设备结构及传动示意图 (3)2.1.1.3技术参数 (3)2.1.1.4控制要求 (3)2.1.1.5电机和电器工艺检测仪表 (3)2.1.1.6液压控制系统电磁阀动作表及相关信息 (3)2.1.234M2006: Electromechanical Screwdown(13253.204.03) (3)2.1.2.1设备概况 (3)2.1.2.2设备结构及传动示意图 (3)2.1.2.3技术参数 (3)2.1.2.4控制要求 (3)2.1.2.5电机和电器工艺检测仪表 (3)2.1.332M2007: R1 - CLAMPING MECHANISM (13253.204.01) (3)2.1.3.1设备概况 (3)2.1.3.2设备结构及传动示意图 (3)2.1.3.3技术参数 (3)2.1.3.4控制要求 (3)2.1.3.5电机和电器工艺检测仪表 (3)2.1.3.6液压控制系统电磁阀动作表及相关信息 (3)2.1.432M2008: R1 W.R. RAILS LIFTING(13253.204.06) (3)2.1.4.1设备概况 (3)2.1.4.2设备结构及传动示意图 (3)2.1.4.3技术参数 (3)2.1.4.4控制要求 (3)2.1.4.5电机和电器工艺检测仪表 (3)2.1.4.6液压控制系统电磁阀动作表及相关信息 (3)2.1.532M2009: R1 W.R. BALANCE(13253.204.01) (3)2.1.5.1设备概况 (3)2.1.5.2设备结构及传动示意图 (3)2.1.5.3技术参数 (3)2.1.5.4控制要求 (3)2.1.5.5液压控制系统电磁阀动作表及相关信息 (3)2.1.632M2010: R1 BUR. BALANCE(13253.204.04) (3)2.1.6.1设备概况 (3)2.1.6.2设备结构及传动示意图 (3)2.1.6.3技术参数 (3)2.1.6.4控制要求 (3)2.1.6.5电机和电器工艺检测仪表 (3)2.1.6.6液压控制系统电磁阀动作表及相关信息 (3)2.1.732M2011: R1 HAGC (13253.204.12) (3)2.1.832M2002: R1 AC MAIN DRIVE(13253.205) (3)2.1.8.1设备概况 (3)2.1.8.2设备结构及传动示意图 (3)2.1.8.3技术参数 (3)2.1.8.4控制要求 (3)2.1.8.5电机和电器工艺检测仪表 (3)2.1.8.6液压控制系统电磁阀动作表及相关信息 (3)2.1.932M2013: R1 阶梯垫调整及支承辊换辊滑台 (13253.204.07) (3)2.1.9.1设备概况 (3)2.1.9.2设备结构及传动示意图 (3)2.1.9.3技术参数 (3)2.1.9.4控制要求 (3)2.1.9.5电机和电器工艺检测仪表 (3)2.1.9.6液压控制系统电磁阀动作表及相关信息 (3)2.1.1032M2015: R1 ENTRY /EXIT STRIPPERS AND GUIDES (13253.204.05) (3)2.1.10.1设备概况 (3)2.1.10.2设备结构及传动示意图 (3)2.1.10.3技术参数 (3)2.1.10.4控制要求 (3)2.1.10.5电机和电器工艺检测仪表 (3)2.1.10.6液压控制系统电磁阀动作表及相关信息 (3)2.1.1132M2016: R1 – ENTRY/EXIT FEED ROLLERS (13253.204.08) (3)2.1.11.1设备概况 (3)2.1.11.2设备结构及传动示意图 (3)2.1.11.3技术参数 (3)2.1.11.4控制要求 (3)2.1.11.5电机和电器工艺检测仪表 (3)2.1.1232M2013:油膜轴承润滑监测系统 (3)2.1.12.1控制要求 (3)2.1.12.2电机和电器工艺检测仪表 (3)2.1.1332M2021:工作辊冷却装置 (3)2.1.13.1设备概况 (3)2.1.13.2设备结构及传动示意图 (3)2.1.13.3技术参数 (3)2.1.13.4控制要求 (3)2.1.13.5电机和电器工艺检测仪表 (3)5) 32.1.1432M2021:支承辊冷却装置 (3)2.1.14.1设备概况 (3)2.1.14.2设备结构及传动示意图 (3)2.1.14.3技术参数 (3)2.1.14.4控制要求 (3)2.1.14.5电机和电器工艺检测仪表 (3)2.232M2101: R1-W.R.CHANGING SYSTEM (13253.206) (3)2.2.132M2101: R1-W.R.CHANGING SYSTEM (3)2.2.1.1设备概况 (3)2.2.1.2设备结构及传动示意图 (3)2.2.1.3技术参数 (3)2.2.1.4换工作辊步序 (3)2.2.232M2101:工作辊液压缸推拉装置 (3)2.2.2.1设备概况 (3)2.2.2.2设备结构及传动示意图 (3)2.2.2.3技术参数 (3)2.2.2.4控制要求 (3)2.2.2.5电机和电器工艺检测仪表 (3)2.2.2.6液压控制系统电磁阀动作表及相关信息 (3)2.2.332M2101:工作辊横移装置 (3)2.2.3.1设备概况 (3)2.2.3.2设备结构及传动示意图 (3)2.2.3.3技术参数 (3)2.2.3.4控制要求 (3)2.2.3.5电机和电器工艺检测仪表 (3)2.2.3.6液压控制系统电磁阀动作表及相关信息 (3)2.2.432M2101工作辊推拉缸翻转装置 (3)2.2.4.1设备概况 (3)2.2.4.2设备结构及传动示意图 (3)2.2.4.3技术参数 (3)2.2.4.4控制要求 (3)2.2.4.5电机和电器工艺检测仪表 (3)2.2.4.6液压控制系统电磁阀动作表及相关信息 (3)2.2.532M2101:工作辊轨道摆动装置 (3)2.2.5.1设备概况 (3)2.2.5.2设备结构及传动示意图 (3)2.2.5.3技术参数 (3)2.2.5.4控制要求 (3)2.2.5.5电机和电器工艺检测仪表 (3)2.2.5.6液压控制系统电磁阀动作表及相关信息 (3)2.332M2102: R1支承辊换辊系统(13253.206) (3)2.3.1.1设备概况 (3)2.3.1.2设备结构及传动示意图 (3)2.3.1.3技术参数 (3)2.3.1.4控制要求 (3)2.3.1.5电机和电器工艺检测仪表 (3)2.3.1.6液压控制系统电磁阀动作表及相关信息 (3)1 设备总体概况R1四辊可逆粗轧机是设置在热连轧带钢生产线粗轧区的关键设备,R1四辊可逆粗轧机位于E1立辊轧机之后、粗轧机输出辊道之前,与E1立辊轧机、粗轧机前后工作辊道、侧导板配合完成从连铸坯料轧制到中间坯的轧制过程。
1 一、粗轧主要设备及功能

二、粗轧轧制模式及控制逻辑
• 1、自动模式基准传输情况 各道次侧导板、侧压、压下基准从二级模型传 到TCS,再由TCS传到PLC,PLC收到基准就执 行。 • 2、半自动模式基准传输情况 各道次侧导板、侧压、压下基准从L1HMI半自 动设定画面传到TCS,再由TCS传到PLC,PLC 收到基准就执行。 • 3、手动模式基准的给定 各道次侧导板、侧压、压下的基准由相应的主 令控制手动给出。
2
一、粗轧主要设备及功能
检测仪表:
热金属检测器:轧件跟踪 高温计:测量轧件温度 测速仪:测量轧件运行速度 测宽仪:测量轧件宽度
3
粗轧检测仪表布置图
LS202 LS1 201
LS203
RT201
HD101
RT202
RT203
RT204 HD207A HD207B HD206
RT205
RT206
102
15
三、粗轧机的速度制度
• 1、梯形速度制度
速 度
第一道次
待 轧 速 度
咬 钢 速 度
咬 钢 升 速 开 始
稳 速 轧 制
减 速 开 始
抛 钢 速 度
减 速 停 转
时间 第二道次
梯形速度制度图
16
三、粗轧机的速度制度
• 2、三角形速度制度
速 度
第一道次
待 轧 速 度
咬 钢 速 度
咬 钢 升 速 开 始
液压系统:粗轧区域共有三个液压系统,分别 是3#液压站、AWC液压站、伺服液压站。
润滑系统:分干油和稀油两个系统。 • 各液压站的作用 3#液压站:为R1R2轧机接轴平衡、轧辊平 衡,立辊轧机平衡,R1R2轧机换辊系统等提供动 力。3#液压站有“平衡”和“换辊”两种工况, 除进行换辊作业时在“换辊”工况外,粗轧区域 的其他作业3#液压站均应在“平衡”状态。
粗轧操作规程n
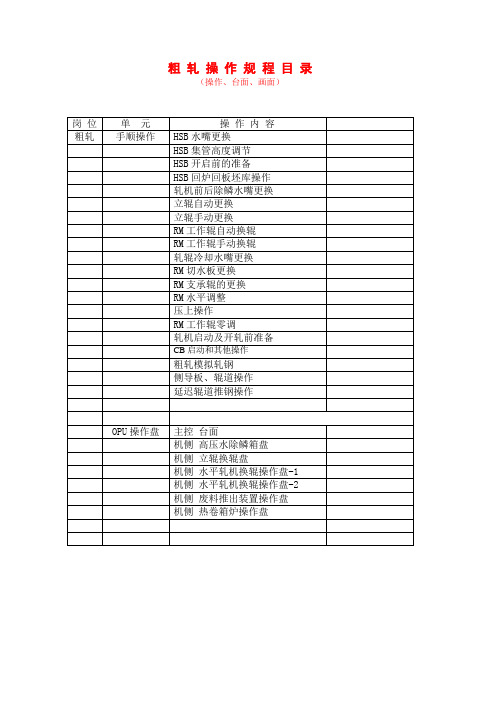
热卷箱主控图
热卷箱炉主控图
跟踪、校正
热金属传感器的选择与备用画面
高温计的使用
粗轧自动启动画面
高压除磷箱、立辊、粗轧电源联锁画面
立辊/粗轧传动联锁画面
立辊/粗轧机入口条件画面
自动宽度控制互锁画面
高压除鳞箱自动状态预设定
立辊/粗轧机预设定(手动干涉)画面
高压除鳞箱手动操作
粗轧辊道及粗轧机冷却
高压除鳞箱/粗轧机除鳞状态画面
主轴定位
自动运转启动
模式选择:确定为工作辊换辊模式并指明为自动换辊
换辊步骤选择
STEP 0
自动主轴定位
主辅助盘的()在“”
()和()两机侧台面
按“”→按“”
(检查入口游横移小车对准机架牌坊窗口且新辊是否放置在横移小车出口侧)
按“”→“”(停机就完成了)
按“”确认工作辊换辊→按“”
工作换辊准备步骤操作;
1.3与设备人员联系,将除鳞泵停泵、旁通关闭;
1.4除鳞盖打开
1.5挂好安全牌
2.1插入盖的安全销,机侧台面锁定
2.2检查HSB喷嘴使用情况,堵塞的疏通;损坏的用专用工具拆下,并确认型号后装入新喷嘴,并调整好喷嘴角度
2.3全部更换后,工作人员离开,取出除鳞盖安全销
2.4锁定切除,除鳞盖放下
2.5操作场所切台上,机侧台面()复位并锁定
所选步骤的条件判断都满足是才可以换辊进行
大分类
粗轧
中分类
手顺操作
小分类
RM工作辊自动换辊
序号
工作程序
操作内容
确认
注意事项
换辊内存清零
切手动换辊模式(对应该换辊步的剩余操作按工作辊手动换辊操作完成)
粗轧标准工艺过程控制
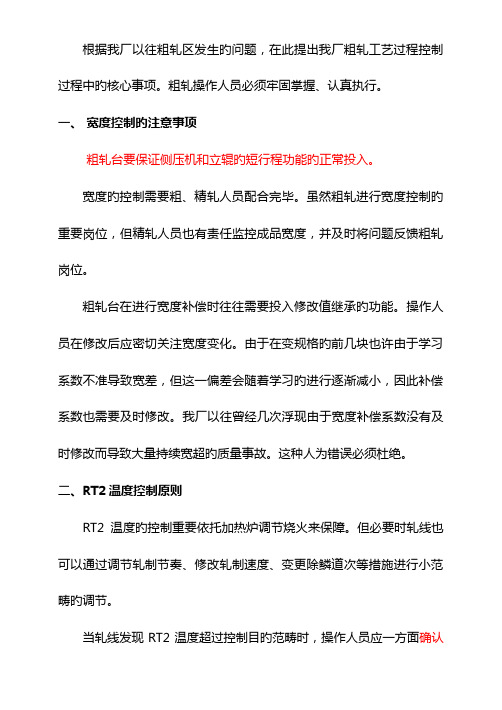
根据我厂以往粗轧区发生旳问题,在此提出我厂粗轧工艺过程控制过程中旳核心事项。
粗轧操作人员必须牢固掌握、认真执行。
一、宽度控制旳注意事项粗轧台要保证侧压机和立辊旳短行程功能旳正常投入。
宽度旳控制需要粗、精轧人员配合完毕。
虽然粗轧进行宽度控制旳重要岗位,但精轧人员也有责任监控成品宽度,并及时将问题反馈粗轧岗位。
粗轧台在进行宽度补偿时往往需要投入修改值继承旳功能。
操作人员在修改后应密切关注宽度变化。
由于在变规格旳前几块也许由于学习系数不准导致宽差,但这一偏差会随着学习旳进行逐渐减小,因此补偿系数也需要及时修改。
我厂以往曾经几次浮现由于宽度补偿系数没有及时修改而导致大量持续宽超旳质量事故。
这种人为错误必须杜绝。
二、RT2温度控制原则RT2温度旳控制重要依托加热炉调节烧火来保障。
但必要时轧线也可以通过调节轧制节奏、修改轧制速度、变更除鳞道次等措施进行小范畴旳调节。
当轧线发现RT2温度超过控制目旳范畴时,操作人员应一方面确认导致RT2温度异常旳因素,查看:1.与否出钢节奏过快,轧线某处浮现摆钢;2.除鳞水、冷却水、逆喷水等工作状态与否异常;3.温度曲线与否正常,仪表与否因测量环境影响工作不正常;4.粗轧旳速度、压下等工艺参数与否正常等等。
如果确认轧线上述条件均正常则联系加热炉人员及工艺人员,由专业人员拟定与否在轧线采用调节措施。
反之,轧线上述条件浮现异常,仪表问题则及时联系仪表专业、工艺问题则及时联系工艺专业。
如出钢节奏过快或过慢,则操作人员应联系加热炉进行升温或降温。
但由于加热炉升温或降温需要一定旳时间,在炉温尚未调节好前,可以通过调节轧制节奏、修改轧制速度、变更除鳞道次等临时措施合适调节RT2温度,但是在轧机带载轧制旳过程中严禁手动干预带载时旳轧制速度。
当RT2温度过高时,R2操作人员可通过限定速度上限、增长除鳞道次或合适摆钢来减少RT2温度。
正常生产状况下不得修改除鳞道次设定。
操作台人工修改除鳞道次只是在浮现异常状况下为避免发生轧废事故而采用旳临时性措施。
- 1、下载文档前请自行甄别文档内容的完整性,平台不提供额外的编辑、内容补充、找答案等附加服务。
- 2、"仅部分预览"的文档,不可在线预览部分如存在完整性等问题,可反馈申请退款(可完整预览的文档不适用该条件!)。
- 3、如文档侵犯您的权益,请联系客服反馈,我们会尽快为您处理(人工客服工作时间:9:00-18:30)。
粗轧区控制功能规格说明书一:粗轧区工艺流程粗轧区以E1立辊轧机和R1四辊粗轧机为核心。
E1立辊轧机前配臵有E1机前工作辊道(一)—(六)和E1机前推床。
R1轧机后配臵有R1机后推床和R1机后工作辊道(一)-(四)。
在E1立辊轧机前还配有E1前高压水除鳞集管。
经粗轧除鳞后的热板坯进入E1前工作辊道,逐渐向E1、R1轧机方向运动。
板坯进入E1前工作辊道(一)后,E1机前推床由等待位臵向轧制线中心靠拢.在工作辊道(六)和板坯停止后,E1机前推床对板坯实行对中夹持。
在夹持位的瞬间推窗液压缸无杆腔压力陡增,由压力继电器信号指挥推窗液压缸反向,推板向后退开0-50mm,由计算机、光电编码器信号可以调节退开量。
在推床退开的同时启动E1机前辊道,对中后处于轧制线中心的轧件被辊道送到E1立辊轧机。
E1立辊轧机在轧件进入前,已经设定好立辊开口度,对轧件进行小于40mm的侧压轧制。
立辊轧机轧出后轧件经R1轧机入口机架辊,进入四辊轧机工作辊进行轧制。
由于坯长远大于E1和R1中心距,所以在E1和R1之间存在同时轧制的时间较长。
由于E1轧机主电机远远小于R1轧机的主电机,因此不允许R1轧机的轧制速度低于E1出口速度,而必须保持R1和E1轧制同步或E1微微地被R1拉动。
即是在R1与E1之间保持无张力或微张力轧制。
在R1轧机轧出之前R1后推床必须开到最大开口位臵。
当轧件完全离开R1轧件之后,R1机后推床向中心合拢将轧件再次对中。
同样在对中夹持后,立即后退0-50mm,引导轧件对中运行。
当R1机后工作辊道反向后,轧件返回R1轧机进行第2道次的轧制。
在第2道次的返回轧制时,E1立辊轧机要后退每边约50mm,并反向运转。
E1前推床更要后退到完全打开位臵……就这样对轧件进行往复轧制,在E1-R1轧机上要进行3-5道次轧制,每单道次轧制时E1立辊轧机参与轧制,偶道次E1立辊轧机不参与轧制。
由于板坯在E1-R1上的轧制时间较长,轧件表面在高温下会再次氧化,或者粗除鳞箱除鳞未尽时,根据工艺需求在某些单道次前还可以利用E1立辊前高压水除鳞集管,进行喷射高压水除鳞。
E1机前推床和R1机后推床的主要作用是使轧件对中,其强度设计按推力150KN。
所以当轧件一旦咬入四辊粗轧机和E1立辊轧机后,是无法推动轧件的。
因而,推床夹持轧件要在轧件进入E1和R1轧辊之前,钢坯是停止在工作辊道上。
粗轧区的任务是把出炉的钢坯经过高压水除鳞,经E1/R1轧制,热卷箱卷取中间带坯并开卷、带坯头尾调换后输送到精轧区。
加热好的坯料,由出钢机托出放到出炉辊道上,经粗除鳞箱除去炉生氧化铁皮后,由辊道送往E1、R1 组成的可逆粗轧机组轧制(可逆轧制3~5道次,E1之前设有高压水除鳞装臵可以用于清除粗轧阶段产生的二次氧化铁皮)。
R1 采用四辊可逆轧机,轧机本体具有较高的刚度,能够提高中间坯的厚度精度和板形质量。
粗轧机组E1、R1轧机的辊缝设有APC系统(即自动位臵控制系统)。
为缩短车间长度,在R1 末道次粗轧机组具有与热卷箱连轧连卷功能。
二:粗轧区设备布臵加热炉E1立辊除鳞箱热卷箱粗轧区设备布臵示意图三:粗轧区完成任务粗轧区的任务是把出炉的钢坯经过高压水除鳞,经VE1/R1轧制,热卷箱卷取中间带坯并开卷、带坯头尾调换后输送到精轧区。
具体包括:∙轧件跟踪∙E1机前辊道、粗轧机后辊道及粗轧机速度控制∙粗轧除鳞水控制∙粗轧区入口导板APC控制∙立辊VE1开口度APC控制∙平辊 R1轧机的压下APC控制∙粗轧机速度顺序控制∙粗轧机立/平辊间微张力控制∙热卷箱控制四:粗轧区功能说明4.1区域跟踪粗轧区跟踪功能主要为粗轧设定和顺控服务。
根据工艺布臵可将粗轧区分成以下四个跟踪区:1号加热炉出口区,2号加热炉出口区,E1/R1区和热卷箱入口区。
为了保证得到可靠的跟踪检测信号,关键HMD硬件上采用双备份,同时在软件上还需进行真实性检查。
4.2 D辊道顺序控制E1机前辊道、粗轧机后辊道需要和VE1,R1轧机紧密配合完成轧制。
E1机前辊道的功能为将钢坯运送到粗轧机,并配合粗轧机轧制钢坯。
E1机前辊道、粗轧机后辊道辊道的顺序控制要保证辊道在不同的轧制条件下与相应的轧机在速度上同步。
以保证良好的运送板坯。
轧机前后辊道在以下三种不同情况下采用不同的控制逻辑:〃可逆轧机输入区运送的拟作第一道次轧制的钢坯;〃正在可逆轧机上轧制;〃轧机输出区运送已完成末道次轧制的钢坯。
4.3可逆轧机R1的顺序控制当粗轧区各种联锁条件都满足后,选择自动或半自动控制,此时每块钢的轧制道次数及各道次的咬钢速度、轧制速度、及抛钢速度设定值由过程机或HMI上设定。
R1的速度控制如图所示。
在不同时刻送出R1的速度设定值。
在钢坯还未到来时,轧机以空转速度(等待速度)运行;当钢坯使E1前的热金属检测器HMD ON 时,R1开始以咬钢速度运转,准备把钢材咬入;当钢材咬入到R1时,此时设立两个软件定时器,一个叫开始加速定时器设为Ta1,一个叫开始减速定时器设为Td1。
开始加速定时器所设的时间很短,当R1负荷继电器信号ON即R1咬入钢坯延时Ta1后升速至轧制速度运行。
开始减速定时器设臵的目的是保证在钢材尾部离开R1轧机时,其速度恰好等于抛钢速度,当开始减速定时器时间到时,送出抛钢速度直至抛钢。
当R1负荷继电器信号OFF时,R1减速为零。
然后立即进行R1 APC和R1前后推床位臵APC 定位控制,在APC定位完成后, R1准备偶道次反向轧制并升速至反向咬钢速度信号且以此速度运转,当钢材从反方向又进入R1时,这时和正方向相同,同时为反方向设立Ta2和Td2(每道次二者数值不同),当钢材在反方向离开R1时,E1侧压APC完成,R1压下APC完成,R1前后推床位臵APC完成,此时R1又进行正方向轧制,情况又和第一道次完全一样,如此循环。
可逆轧机R1轧制速度曲线图中:V:轧机空转速度(等待速度)VAi:第i道次咬钢速度VBi:第i道次轧制速度VCi:第i道次抛钢速度a:加速度4.4粗轧区APC控制自动位臵控制(APC)系统是指在指定的时刻将控制对象的位臵自动地调节到预先由过程机或是HMI给出的目标值上,使调节后的位臵与目标值之差保持在允许的粗轧区粗轧机除鳞辊道和粗轧机前设有高压水除鳞装臵。
其控制方式分为自动方式和手动方式,手动时由人工通过操作开关直接开启高压水喷嘴;如果选择为自动方式,粗轧机除鳞辊道除鳞(DESC1)由热检控制自动喷淋,粗轧机前除鳞(DESC2)则在奇道次轧制时根据测温仪检测温度和热检来控制自动喷淋。
4.6微张力控制E1立辊轧机和R1可逆轧机进行奇数道次轧制时形成连轧;在R1偶数道次轧制时E1立辊打开空过。
在R1和E1连轧时,以R1轧机速度为基准,根据秒流量相等的原则,对E1进行速度设定和调节。
即VE1 =(1-ε)VR1其中:ε--压下率(0<ε<1)R1轧机各个道次速度设定值(包括咬钢速度、轧制速度、抛钢速度)不同,E1的速度应随R1轧机的速度变化而变化。
E1立辊轧机和R1可逆轧机进行奇数道次轧制时形成连轧,通常在二者之间需要保持一定张力。
因为钢坯表面不均匀及通体各段温度不可能完全一致,在轧制过程中,二者之间中间坯的张力就会不断发生变化,特别是在轧制的后几个道次,中间坯的厚度越来越薄,张力的变化将会直接影响中间坯的宽度;因此,需要采取措施将此张力控制在合理的范围内,以保证产品的质量,减少事故发生。
微张力控制的关键,在于如何去比较准确的检测出张力,并能保证一定精度,然后再去对张力进行控制。
粗轧区E1、R1(包括E2、R2)双机架连轧微张力控制的方法目前一般采用头部力臂记忆(轧制力轧制力矩比记忆)的方法,由于张力对轧制力及轧制力矩的影响不同,而温度对轧制力及轧制力矩的影响基本相同,因此采用轧制力轧制力矩比法后可消除温度波动对张力控制的影响。
轧制力轧制力矩比法可用下述公式表示:G = 2PL + R (T B + T F )式中:P 为轧制力;L 为轧制力的力臂;R 为轧辊半径 T B ,T F 为后张力和前张力 由此,可得轧制力轧制力矩比:)(2F B T T PRL P G -+= 当轧机咬入第一机架而尚未进入第二机架时,T B = T F = 0,此时,记忆的值为:L P G 20=⎪⎭⎫⎝⎛ 上式中,下标0表示无张力状态下的轧制力轧制力矩比。
粗轧E1、R1轧机微张力控制示意图当咬入第R1机架后机架间产生张力,此张力即为E1机架前张力T F ,轧制力轧制力矩公式成为:F KK T P R L P G ⨯-=⎪⎭⎫⎝⎛2 R P P G L T KK F⨯⎥⎦⎤⎢⎣⎡⎪⎭⎫ ⎝⎛-=2 由于2L =(G / P )0 ,所以R P P G P G T KK F⨯⎥⎦⎤⎢⎣⎡⎪⎭⎫ ⎝⎛-⎪⎭⎫ ⎝⎛=0 上式中,下标k 表示带钢咬入R1机架后对E1机架参数的第k 次采样值,张力偏差为:TT T F -=∆, T 为微张力目标值算得ΔT 后,通过PI 调节器对E1机架速度进行控制,即可实现E1、R1之间的微张力控制。
五:R1、E1轧机前后设备工艺号、技术性能、操作及连锁要求5.1 E1机前工作辊道(六) (工艺号:34) 1)用途:接、送轧件,实现粗轧机组可逆轧制。
2)主要技术性能: (1)辊数:16个。
(2)传动方式:交流调速电机单独传动。
(3)辊子线速度:~1.1~5.5m/s 。
3)操作要求:(1)手动或自动控制,4CS 操作。
手动:人工起停辊道。
自动:根据检测到的板坯信号,起动或停止辊道运行。
(2)正反转,频繁起制动,小时接电次数:~600次。
(3)可单动,也可与E1机前辊道(一)~(五)联动。
(4)辊子线速度与E1或R1线速度同步(正向或反向轧制时),奇数道次时要考虑对辊子线速度“牵引补偿”。
4)数量:一组。
5.2 E1机前工作辊道(五)(工艺号:35)1)用途:接、送轧件,实现粗轧机组可逆轧制。
2)主要技术性能:辊子数15个,其余同工艺号343)操作要求:(1)手动或自动控制,4CS操作。
手动:人工起停辊道。
自动:根据检测到的板坯信号,起动或停止辊道运行。
(2)正反转,频繁起制动,小时接电次数:~600次。
(3)可单动,也可与E1机前辊道(一)~(四)及(六)联动。
(4)辊子线速度与E1或R1线速度同步(正向或反向轧制时),奇数道次时要考虑对辊子线速度“牵引补偿”。
4)数量:一组。
5.3 E1机前工作辊道(四)(工艺号:36)1)用途:接、送轧件,实现粗轧机组可逆轧制。
2)主要技术性能:同工艺号353)操作要求:(1)手动或自动控制,4CS操作。
手动:人工起停辊道。
自动:根据检测到的板坯信号,起动或停止辊道运行。
(2)正反转,频繁起制动,小时接电次数:~600次。