厚背板钻孔工艺研究
背钻孔的工艺

背钻孔的工艺
背钻孔的工艺是一种特殊的钻孔技术,主要用于在PCB板的背面进行钻孔,打通连接或清除残留材料。
以下是背钻孔的工艺流程:
1.在PCB板的正面上布置需要背钻的孔位,并在背面标记对应的
位置。
2.将PCB板放在背钻机上,并固定好。
3.使用数控钻床或激光钻床,将钻头从PCB板的背面开始钻孔,
直到打通到PCB板的正面。
4.在背钻过程中,需要控制钻孔深度和孔径大小,以免对PCB板
造成损坏。
5.完成背钻后,使用抛光机器等设备将孔口抛光,以获得更好的
连接效果。
在背钻孔的工艺中,还需要注意以下问题:
1.选择合适的钻头和加工参数,以保证加工效果和质量。
2.注意PCB板的厚度和材料,以避免加工过程中出现问题。
3.在背钻孔前,需要对PCB板进行定位和固定,以确保钻孔位置
的准确性。
4.在背钻孔过程中,需要控制好钻头的进给速度和旋转速度,避
免对PCB板造成过大的冲击和损伤。
5.在背钻孔后,需要进行清洗和检查,去除残留物和不合格品,
以保证产品的质量和可靠性。
总之,背钻孔的工艺需要精确控制加工的位置、深度和精度等参数,
以确保钻孔的质量和稳定性。
同时,还需要注意安全和环保问题,采取相应的防护措施和废弃物处理措施。
PCB生产中背钻工艺详解
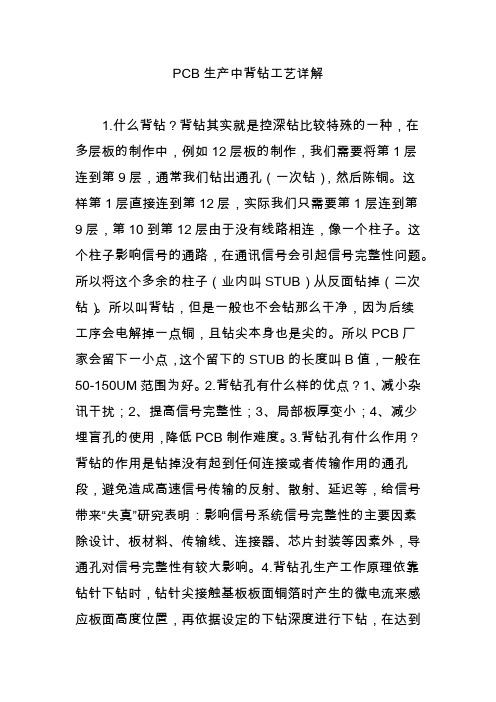
PCB生产中背钻工艺详解1.什么背钻?背钻其实就是控深钻比较特殊的一种,在多层板的制作中,例如12层板的制作,我们需要将第1层连到第9层,通常我们钻出通孔(一次钻),然后陈铜。
这样第1层直接连到第12层,实际我们只需要第1层连到第9层,第10到第12层由于没有线路相连,像一个柱子。
这个柱子影响信号的通路,在通讯信号会引起信号完整性问题。
所以将这个多余的柱子(业内叫STUB)从反面钻掉(二次钻)。
所以叫背钻,但是一般也不会钻那么干净,因为后续工序会电解掉一点铜,且钻尖本身也是尖的。
所以PCB厂家会留下一小点,这个留下的STUB的长度叫B值,一般在50-150UM范围为好。
2.背钻孔有什么样的优点?1、减小杂讯干扰;2、提高信号完整性;3、局部板厚变小;4、减少埋盲孔的使用,降低PCB制作难度。
3.背钻孔有什么作用?背钻的作用是钻掉没有起到任何连接或者传输作用的通孔段,避免造成高速信号传输的反射、散射、延迟等,给信号带来“失真”研究表明:影响信号系统信号完整性的主要因素除设计、板材料、传输线、连接器、芯片封装等因素外,导通孔对信号完整性有较大影响。
4.背钻孔生产工作原理依靠钻针下钻时,钻针尖接触基板板面铜箔时产生的微电流来感应板面高度位置,再依据设定的下钻深度进行下钻,在达到下钻深度时停止下钻。
如图二,工作示意图所示5.背钻制作工艺流程?a、提供PCB,PCB上设有定位孔,利用所述定位孔对PCB进行一钻定位并进行一钻钻孔;b、对一钻钻孔后的PCB进行电镀,电镀前对所述定位孔进行干膜封孔处理;c、在电镀后的PCB上制作外层图形;d、在形成外层图形后的PCB上进行图形电镀,在图形电镀前对所述定位孔进行干膜封孔处理;e、利用一钻所使用的定位孔进行背钻定位,采用钻刀对需要进行背钻的电镀孔进行背钻;f、背钻后对背钻孔进行水洗,清除背钻孔内残留的钻屑。
6. 如有电路板有孔要求从第14层钻到12层要如何解决呢?1、如该板在第11层有信号线,在信号线的两端有通孔连接到元件面和焊锡面,在元件面上将会插装元器件,如下图所示,也就是说,在该线路上,信号的传输是从元件A通过第11层的信号线传递到元件B。
高厚径比微型孔对接钻加工方法探究
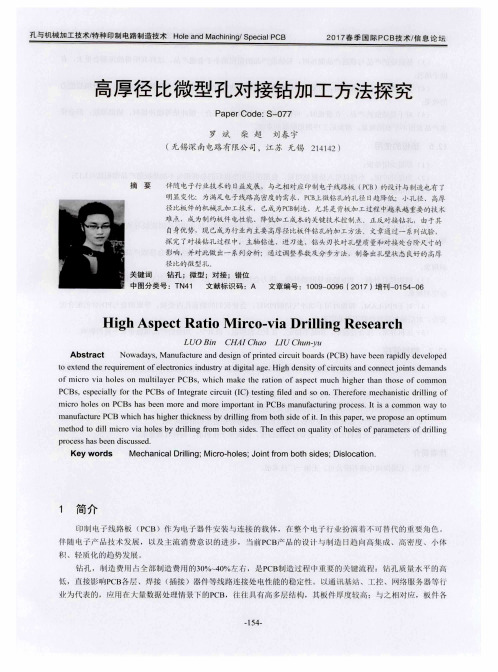
罗 斌 柴 超 刘春 宇
( 无锡 深 南电路 有 限公 司,江苏 无锡 2 1 4 1 4 2)
摘 要
伴 随 电子行 业 技 术 的 日益 发展 ,与之 相 对 应 印 制 电子 线路 板 ( P C B )的设 计 与 制造 也 有 了 明显 变化 : 为满 足 电子 线路 高 密度 的需 求 ,P C B k _ 微 钻 孔 的孔 径 日趋 降 低: 小 孔 径 、 高厚 径 比板件 的机 械孔 加 工 技 术 , 已成 为P C B @ J 造 , 尤其 是 背板 加 工过 程 中越 来 越 重要 的技 术 难 点 , 戍 为制 约板 件 电性 能 、降 低加 工成 本 的 关键技 术控 制 点 。正 反 对接 钻孔 , 由于其
mi c r o h o l e s 0 1 1 P CBs h a s b e e n mo r e a n d r n o r e i mp o r t a n t i n PCBs ma n u f a c t u r i n g p r o c e s s .I t i s a c o mmo n wa y t o
! 皇 丰 几 加 工 技 术 / 特种 印 制 电 路 制 造 技 术 H o l e a n d M a c h i n i n g / S p e c i a l P C B
2 0 1 7 春季国际 P C B 技术 / 信息论坛
高厚径 比微 型孑 L 对 接钻 加工方法探究
LUO Bi n CH A1 Ch a o LI U Ch u n -  ̄ t
Ab s t r a c t
No wa d a y s , Ma n u f a c t u r e a n d d e s i g n o f p r i n t e d c i r c u i t b o a r d s( P CB ) h a v e b e e n r a p i d l y d e v e l o p e d
厚板沉孔开制方法的创新-

方案序号
方案名称
基本描述
1
手工割制法
2
直板定位自动旋转切割法
人工控制手把割枪割制 通过直板确定半自动切割机切割轨迹
3
模具定位自动旋转切割法
通过制作特定模具确定半自动切割机切割轨迹
制表人:冉瑞恒
制表日期:2016年协调公司操作能力极强的技工手工切割,凭多年的切割经验,合理控制火焰 温度及焰枪倾角,沿划定的路线进行切割,切割完成之后补焊打磨,得到合格的 沉孔;
七、对策实施
引弧点确定实物图1
引弧点确定实物图2
七、对策实施
确定引弧点效果检查:小组对手工切割后的缝隙进行了检查,同时校核了切 割尺寸,切割质量符合预期要求,其中引弧点准确落在预定位置上。小组采取抽 样检查的方式测量由本次切割产生的马牙深度,测量后的数据如下:
手 工 割 制 实 景 图
方案二:直板定位自动旋转切割法
在厚板上铺设一块辅助板,辅助板上开一个300mm的大孔,大孔中心与预开 沉孔中心重合,沿大孔直径焊接一块6*30mm的直板,在直板上与两孔中心重合处 钻一个直径8mm的小孔,将半自动切割机摇杆插入小孔中,调整切割焰枪倾斜角 度(45°)和火焰温度,使切割机沿小孔中心做圆周运动,移除辅助板,将直板 覆盖处部分采用手工切割,得到完整沉孔,之后补焊打磨得到合格的喇叭孔;
切割稳定 性
切割效率
切割质 量
结论
1
手工切割法
难度大、对 技能要求极 高
不实用
切割投入 小返修投 入大
随意性大、 不稳定
效率低下
外观及 尺寸差
不选用
孔易偏
2
直板定位自动旋转 切割法
操作简易
较实用 投入较小
切割稳定
背钻工艺详解
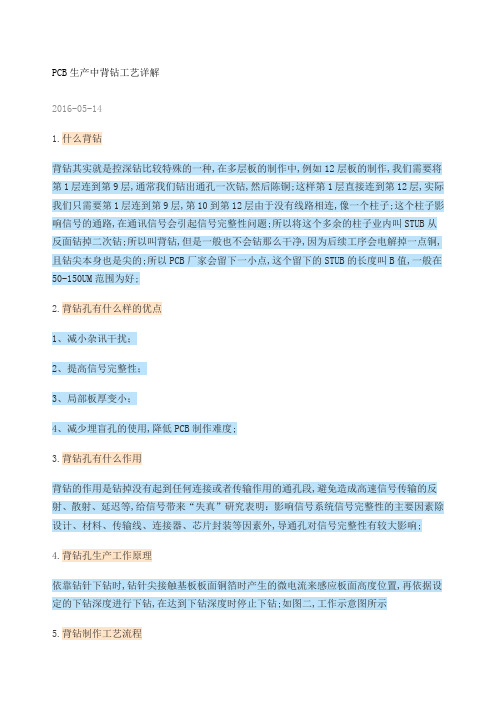
PCB生产中背钻工艺详解2016-05-141.什么背钻背钻其实就是控深钻比较特殊的一种,在多层板的制作中,例如12层板的制作,我们需要将第1层连到第9层,通常我们钻出通孔一次钻,然后陈铜;这样第1层直接连到第12层,实际我们只需要第1层连到第9层,第10到第12层由于没有线路相连,像一个柱子;这个柱子影响信号的通路,在通讯信号会引起信号完整性问题;所以将这个多余的柱子业内叫STUB从反面钻掉二次钻;所以叫背钻,但是一般也不会钻那么干净,因为后续工序会电解掉一点铜,且钻尖本身也是尖的;所以PCB厂家会留下一小点,这个留下的STUB的长度叫B值,一般在50-150UM范围为好;2.背钻孔有什么样的优点1、减小杂讯干扰;2、提高信号完整性;3、局部板厚变小;4、减少埋盲孔的使用,降低PCB制作难度;3.背钻孔有什么作用背钻的作用是钻掉没有起到任何连接或者传输作用的通孔段,避免造成高速信号传输的反射、散射、延迟等,给信号带来“失真”研究表明:影响信号系统信号完整性的主要因素除设计、材料、传输线、连接器、芯片封装等因素外,导通孔对信号完整性有较大影响;4.背钻孔生产工作原理依靠钻针下钻时,钻针尖接触基板板面铜箔时产生的微电流来感应板面高度位置,再依据设定的下钻深度进行下钻,在达到下钻深度时停止下钻;如图二,工作示意图所示5.背钻制作工艺流程a、提供PCB,PCB上设有定位孔,利用所述定位孔对PCB进行一钻定位并进行一钻钻孔;b、对一钻钻孔后的PCB进行电镀,电镀前对所述定位孔进行干膜封孔处理;c、在电镀后的PCB上制作外层图形;d、在形成外层图形后的PCB上进行图形电镀,在图形电镀前对所述定位孔进行干膜封孔处理;e、利用一钻所使用的定位孔进行背钻定位,采用钻刀对需要进行背钻的电镀孔进行背钻;f、背钻后对背钻孔进行水洗,清除背钻孔内残留的钻屑;6. 如有电路板有孔要求从第14层钻到12层要如何解决呢1、如该板在第11层有信号线,在信号线的两端有通孔连接到元件面和焊锡面,在元件面上将会插装元器件,如下图所示,也就是说,在该线路上,信号的传输是从元件A通过第11层的信号线传递到元件B;图42、按第1点所描述的信号传输情况,通孔在该传输线路的作用等同于信号线,如果我们不进行背钻,则信号的传输路线如图五所示;3、从第2点所描述的图中,我们可以看到,在先好传输过程中,焊锡面到11层的通孔段其实并没有起到任何的链接或者传输作用;而这一段通孔的存在则容易造成信号传输的反射、散射、延迟等,因此背钻实际上就是钻掉没有起到任何链接或者传输作用的通孔段,避免造成信号传输的反射、散射、延迟,给信号带来失真;由于钻孔深度存在一定的公差控制要求,以及板件厚度公差,我们无法100%满足客户绝对的深度要求,那么对于背钻深度的控制是深一点好还是浅一点好我们对工艺的看法是宁浅勿深,图六;7. 背钻孔板技术特征有哪些1多数背板是硬板2层数一般为8至50层3板厚:以上4厚径比较大5板尺寸较大6一般首钻最小孔径>=7外层线路较少,多为压接孔方阵设计8背钻孔通常比需要钻掉的孔大9背钻深度公差:+/10如果背钻要求钻到M层,那么M层到M-1M层的下一层层的介质厚度最小8.背钻孔板主要应用于何种领域呢背板主要应用于通信设备、大型服务器、医疗电子、军事、航天等领域;由于军事、航天属于敏感行业,国内背板通常由军事、航天系统的研究所、研发中心或具有较强军事、航天背景的PCB制造商提供;在中国,背板需求主要来自通信产业,现逐渐发展壮大的通信设备制造领域;在Allegro中实现背钻文件输出1.首先选中背钻Net,定义长度;在菜单栏中点Edit-Properties,打开对话框Edit property,如下图:2.在菜单中点:Manufacturing→NC→ Backdrill Setup and Analysis,如下图:3.背钻可以从top层开始,也可以从Bottom层开始;高速信号上的连接管脚和VIA都需要做背钻;设置如下:4.钻孔文件如下:5.将背钻钻孔文件和背钻钻孔深度的表格一起打包发给PCB厂,背钻深度表格需手动填写相关的一些属性Properties1,BACKDRILL_MAX_PTH_STUBnet:在constraint manager里面需要给背钻的网络赋予BACKDRILL_MAX_PTH_STUB属性,只有设置了属性,软件才会识别为这个网络需要考虑背钻;在constraintmanager→net→general properties →worksheet→backdrill项,选择需要的项目并单击鼠标右键,在弹出的快捷菜单中选择change命令,输入maximum stub的值即可;Stub的计算原则为top和bottom两面的stub都会被计入到最大的stub长度里面;2,BACKDRILL_EXCLUDE属性:定义了这个属性后,相关的目标就不进行背钻,此属性可以赋给symbol,pin,via,甚至可以在建库的时候就附上属性;3,BACKDRILL_MIN_PIN_PTH属性:确保最小的通孔金属化的深度4,BACKDRILL_OVERRIDE属性:用户自定义backdrill的范围,这也是比较有用的一个方法,尤其是针对结构简单,背钻深度一致的设计;5,BACKDRILL_PRESSFIT_CONNECTOR属性:这是针对压接件的设置属性,一般情况下,背钻会识别压接器件,不会从器件面背钻,如果要求两面背钻,压接器件必须赋予BACKDRILL_PRESSFIT_CONNECTOR属性;用于压接器件,要求单面或者双面背钻背钻时,指定这个参数后,背钻深度不会进入压接器件必需的有效连接区域;值<value1:value2>,其中values=pin contact range,这个值必须从压接器件厂家得到;针对背钻的属性都设置完成后,就是对背钻的分析了,启动菜单命令:manufacture→NC backdrill setup and analysis,启动背钻界面分析窗口,选择new pass set,设置一些背钻的参数,分析之后会产生报告,有冲突的地方都会有详细说明;如果分析没有问题,那么背钻的设置就全部完成了, 需要在后处理的光绘输出阶段如NC-Drill legend和NC Drill的窗口中选择include backdrill,然后执行生成背钻钻孔孔位图和钻孔文件;注意PCB板厂的背钻深度工艺能力需要与厂家沟通;。
关于改善小孔背钻堵孔的研究
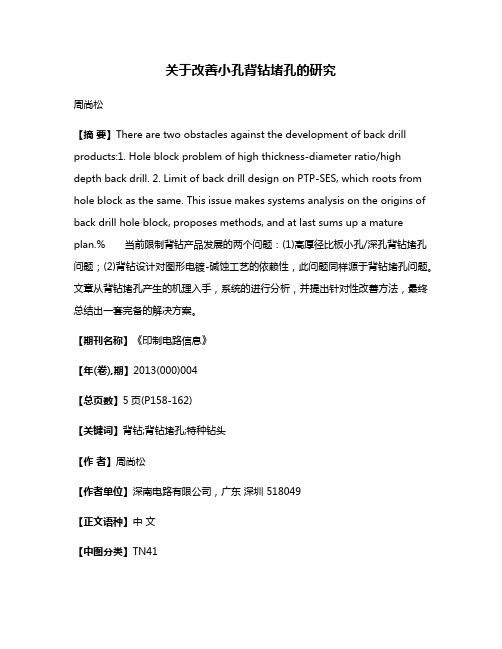
关于改善小孔背钻堵孔的研究周尚松【摘要】There are two obstacles against the development of back drill products:1. Hole block problem of high thickness-diameter ratio/high depth back drill. 2. Limit of back drill design on PTP-SES, which roots from hole block as the same. This issue makes systems analysis on the origins of back drill hole block, proposes methods, and at last sums up a mature plan.% 当前限制背钻产品发展的两个问题:(1)高厚径比板小孔/深孔背钻堵孔问题;(2)背钻设计对图形电镀-碱蚀工艺的依赖性,此问题同样源于背钻堵孔问题。
文章从背钻堵孔产生的机理入手,系统的进行分析,并提出针对性改善方法,最终总结出一套完备的解决方案。
【期刊名称】《印制电路信息》【年(卷),期】2013(000)004【总页数】5页(P158-162)【关键词】背钻;背钻堵孔;特种钻头【作者】周尚松【作者单位】深南电路有限公司,广东深圳 518049【正文语种】中文【中图分类】TN411 前言背钻是指在常规钻孔完成电镀后,使用较大直径钻头进行一定深度的钻孔加工,以去除部分电镀层,从而获得如图1所示的孔型结构。
此流程的设计初衷是通过切除部分层次连接铜层,以满足不同层次的电气连接需求。
随着当前设计的小型化、集成化要求日益提高,产品设计时逐渐开始将此方法应用于高速产品上,通过切除部分多余的铜层,以降低高速信号传导时,有效信号的丢失及噪声的干扰。
常见的如系统板上的BGA背钻,其特点是孔径小(通常<0.3 mm)、厚径比高(>8:1)、背钻深度大(>2.0 mm)。
12层厚铜印制板钻孔工艺改进

12层厚铜印制板钻孔工艺改进唐文锋 程 剑 谢超峰 周 刚 曾祥福(广东科翔电子科技有限公司,广东 惠州 516081)中图分类号:TN41 文献标识码:A 文章编号:1009-0096(2019)03-0063-04Improvement of drilling technology for 12-layerthick copper PCBTang Wenfeng Chen Jian Xie Chaofeng Zhou Gang Zeng Xiangfu1 背景描述为了提高PCB线路的电流承载能力,在不能增加线宽条件下只能相应提高导体厚度即铜厚。
本文对一款厚铜板从工程资料优化,重点对压合、钻孔、电镀等工艺跟进研究,改善了孔偏、孔粗过大、孔烧焦,内层孔环崩缺、被拉出,钉头等不良,使厚铜板成品后通过相关可靠性测试符合品质要求。
此板为12层内/外层铜厚140 μm(4 oz)的厚铜板,第一次试样共投12 PNL,钻孔后发现有孔偏、孔粗过大(见图1)、孔烧焦,内层孔环崩缺、被拉出,钉头(图2)现象等问题存在,报废了9 PNL。
现针对第一次打样存在的问题展开研究。
2 试验方案设计(1)内层照相底片资料的更改:此板制作难点主要在钻孔,试板主要是针对钻孔进行资料更改与跟进。
为了能够减少钻孔时钻针与内层铜皮摩擦产生大量热量而导致孔粗、树脂缩陷等品质问题,对内层照相底片上部分铜皮掏掉,具体掏铜皮标准是:对于PTH(镀通孔)孔钻孔孔径Ф≥0.9 mm,内层独立Pad及带有隔离环的Pad,把中间铜皮掏空,掏空铜皮标准是钻孔孔径Ф-0. 6 mm。
如:钻孔孔径Ф0.9 mm要掏掉铜皮的直径为0.9-0.6=0.3 mm; Ф1.3 mm 要掏掉铜皮的直径为1.3-0.6=0.7 mm;依次类推。
NPTH(非镀通孔)孔孔径不变。
如图3所示。
(2)更改钻孔孔径:为了增加孔铜的结合力,同时借签行业经验参考将孔铜厚度就做到70 μm左右,增加孔铜厚度的同时还要保证孔径OK,就要加大钻孔孔径,钻孔孔径修改标准:对于PTH孔钻孔孔径Ф<1.0 mm,在现有MI要求孔径的基础上再加0.05 mm,如:0.4 mm改成0.45 mm,0.5 mm改成0.55 mm,0.55改成0.6 mm,依次类推。
背钻工艺详解

PCB生产中背钻工艺详解2016-05-141.什么背钻背钻其实就是控深钻比较特殊的一种,在多层板的制作中,例如12层板的制作,我们需要将第1层连到第9层,通常我们钻出通孔(一次钻),然后陈铜。
这样第1层直接连到第12层,实际我们只需要第1层连到第9层,第10到第12层由于没有线路相连,像一个柱子。
这个柱子影响信号的通路,在通讯信号会引起信号完整性问题。
所以将这个多余的柱子(业内叫STUB)从反面钻掉(二次钻)。
所以叫背钻,但是一般也不会钻那么干净,因为后续工序会电解掉一点铜,且钻尖本身也是尖的。
所以PCB厂家会留下一小点,这个留下的STUB的长度叫B值,一般在50-150UM范围为好。
2.背钻孔有什么样的优点1、减小杂讯干扰;2、提高信号完整性;3、局部板厚变小;4、减少埋盲孔的使用,降低PCB制作难度。
3.背钻孔有什么作用背钻的作用是钻掉没有起到任何连接或者传输作用的通孔段,避免造成高速信号传输的反射、散射、延迟等,给信号带来“失真”研究表明:影响信号系统信号完整性的主要因素除设计、材料、传输线、连接器、芯片封装等因素外,导通孔对信号完整性有较大影响。
4.背钻孔生产工作原理依靠钻针下钻时,钻针尖接触基板板面铜箔时产生的微电流来感应板面高度位置,再依据设定的下钻深度进行下钻,在达到下钻深度时停止下钻。
如图二,工作示意图所示5.背钻制作工艺流程a、提供PCB,PCB上设有定位孔,利用所述定位孔对PCB进行一钻定位并进行一钻钻孔;b、对一钻钻孔后的PCB进行电镀,电镀前对所述定位孔进行干膜封孔处理;c、在电镀后的PCB上制作外层图形;d、在形成外层图形后的PCB上进行图形电镀,在图形电镀前对所述定位孔进行干膜封孔处理;e、利用一钻所使用的定位孔进行背钻定位,采用钻刀对需要进行背钻的电镀孔进行背钻;f、背钻后对背钻孔进行水洗,清除背钻孔内残留的钻屑。
6. 如有电路板有孔要求从第14层钻到12层要如何解决呢1、如该板在第11层有信号线,在信号线的两端有通孔连接到元件面和焊锡面,在元件面上将会插装元器件,如下图所示,也就是说,在该线路上,信号的传输是从元件A通过第11层的信号线传递到元件B。
厚板和薄板的钻孔刀具消耗论证

厚板和薄板的钻孔刀具消耗论证厚板和薄板的钻孔刀具消耗论证引言:钻孔是一项常见的加工工艺,广泛应用于各个行业的制造过程中。
在进行钻孔加工时,选择合适的刀具对于提高加工效率和质量至关重要。
本文将对厚板和薄板的钻孔刀具消耗进行论证,分析两者之间的差异以及影响因素。
一、厚板钻孔刀具消耗1. 厚板特点厚板通常指材料厚度大于等于3mm的金属板材,其硬度和韧性较高,需要较大的力量才能进行钻孔。
由于材料厚度大,切削阻力也相应增加。
2. 刀具选择在钻孔厚板时,需要选择适合高负荷和高强度切削任务的刀具。
常见的刀具类型包括实心钻头、硬质合金钻头、涂层钻头等。
这些刀具通常采用较大直径和坚固耐用的设计。
3. 切削参数为了保证高效率和稳定性,在进行厚板钻孔时需要调整合适的切削参数。
切削速度、进给速度和切削深度等参数需要根据具体材料和刀具选择进行调整。
4. 刀具消耗由于厚板钻孔的高负荷和切削阻力大,刀具消耗较快。
主要表现为磨损、断裂和变形等。
这些现象会导致钻孔质量下降,增加生产成本。
二、薄板钻孔刀具消耗1. 薄板特点薄板指材料厚度小于3mm的金属板材,相比于厚板,薄板的硬度和韧性较低,容易进行钻孔加工。
由于材料薄,切削阻力相对较小。
2. 刀具选择在钻孔薄板时,通常选择细长的刀具,如中心钻、麻花钻等。
这些刀具能够提供较好的稳定性和精度,并减少振动和变形。
3. 切削参数与厚板不同,在进行薄板钻孔时需要注意控制合适的切削参数。
过大的进给速度或过深的切削深度可能会导致振动、变形和切削质量下降。
4. 刀具消耗相对于厚板,薄板钻孔的刀具消耗较低。
薄板的切削阻力小,刀具磨损相对较少。
然而,由于薄板的材料特性,刀具容易出现断裂和损坏的情况。
三、影响钻孔刀具消耗的因素1. 材料特性材料硬度、韧性以及热导率等特性都会对钻孔刀具消耗产生影响。
硬度高的材料会加速刀具磨损,而韧性差的材料容易导致刀具断裂。
2. 切削参数选择合适的切削参数可以减少刀具消耗。
pcb背板制作工艺技术
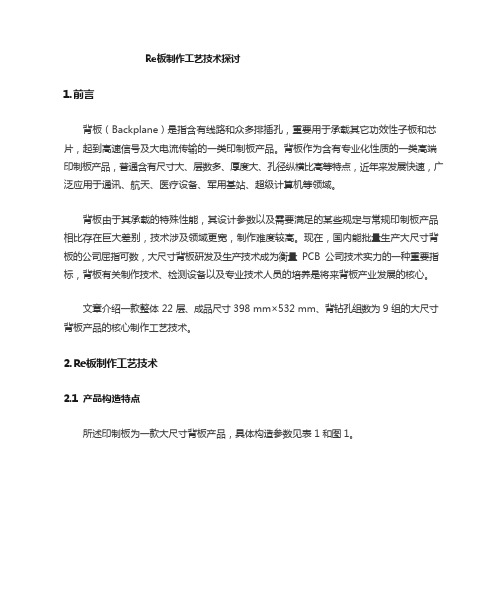
Re板制作工艺技术探讨1.前言背板(Backplane)是指含有线路和众多排插孔,重要用于承载其它功效性子板和芯片,起到高速信号及大电流传输的一类印制板产品。
背板作为含有专业化性质的一类高端印制板产品,普通含有尺寸大、层数多、厚度大、孔径纵横比高等特点,近年来发展快速,广泛应用于通讯、航天、医疗设备、军用基站、超级计算机等领域。
背板由于其承载的特殊性能,其设计参数以及需要满足的某些规定与常规印制板产品相比存在巨大差别,技术涉及领域更宽,制作难度较高。
现在,国内能批量生产大尺寸背板的公司屈指可数,大尺寸背板研发及生产技术成为衡量PCB 公司技术实力的一种重要指标,背板有关制作技术、检测设备以及专业技术人员的培养是将来背板产业发展的核心。
文章介绍一款整体 22 层、成品尺寸 398 mm×532 mm、背钻孔组数为 9 组的大尺寸背板产品的核心制作工艺技术。
2.R e板制作工艺技术2.1产品构造特点所述印制板为一款大尺寸背板产品,具体构造参数见表 1 和图 1。
图 1 大尺寸背板层压构造图2.2工艺流程设计根据本款背板产品的构造特点,并结合实际PCB 生产制作工艺,拟定其生产工艺流程以下。
开料→内层图形→OPE冲孔→内层AOI→棕化→压合→外层钻孔→沉铜→全板电镀→外层图形→图形电镀→背钻孔→外层蚀刻→外层AOI→丝印阻焊→沉镍金→成型→成型后测试→FQC→FQA→包装2.3工艺制作难点分析及解决办法2.3.1镀锡+分段背钻技术(1)难点描述。
背钻孔是将一种电镀导通后的通孔,使用控深钻孔办法除去一部分孔铜,只保存一部分孔铜而形成的孔,背钻孔的核心作用是在高速信号传输过程中,减少多出孔铜对信号的反射干扰,以确保信号传输的完整性。
现在,背钻孔是成本较低的能够满足高频、高速线路板性能的制作办法。
但实际实施过程中,由于背钻本身的特点及其电路边构造规定等工艺难点,易出现孔内铜丝、堵孔、断钻等品责问题。
背钻孔生产工作原理
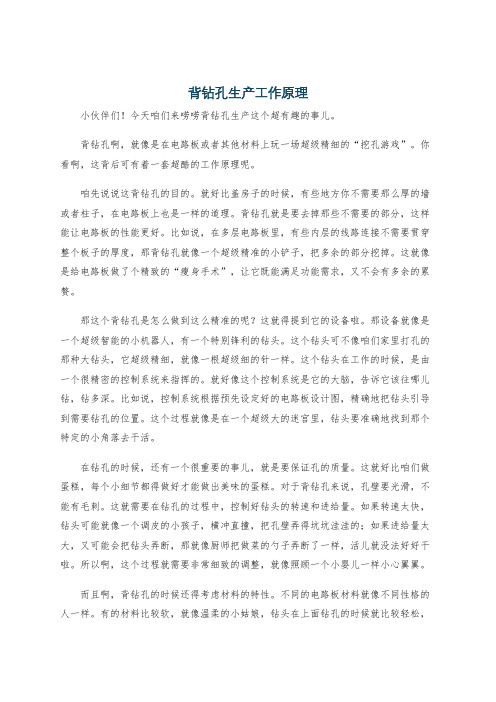
背钻孔生产工作原理小伙伴们!今天咱们来唠唠背钻孔生产这个超有趣的事儿。
背钻孔啊,就像是在电路板或者其他材料上玩一场超级精细的“挖孔游戏”。
你看啊,这背后可有着一套超酷的工作原理呢。
咱先说说这背钻孔的目的。
就好比盖房子的时候,有些地方你不需要那么厚的墙或者柱子,在电路板上也是一样的道理。
背钻孔就是要去掉那些不需要的部分,这样能让电路板的性能更好。
比如说,在多层电路板里,有些内层的线路连接不需要贯穿整个板子的厚度,那背钻孔就像一个超级精准的小铲子,把多余的部分挖掉。
这就像是给电路板做了个精致的“瘦身手术”,让它既能满足功能需求,又不会有多余的累赘。
那这个背钻孔是怎么做到这么精准的呢?这就得提到它的设备啦。
那设备就像是一个超级智能的小机器人,有一个特别锋利的钻头。
这个钻头可不像咱们家里打孔的那种大钻头,它超级精细,就像一根超级细的针一样。
这个钻头在工作的时候,是由一个很精密的控制系统来指挥的。
就好像这个控制系统是它的大脑,告诉它该往哪儿钻,钻多深。
比如说,控制系统根据预先设定好的电路板设计图,精确地把钻头引导到需要钻孔的位置。
这个过程就像是在一个超级大的迷宫里,钻头要准确地找到那个特定的小角落去干活。
在钻孔的时候,还有一个很重要的事儿,就是要保证孔的质量。
这就好比咱们做蛋糕,每个小细节都得做好才能做出美味的蛋糕。
对于背钻孔来说,孔壁要光滑,不能有毛刺。
这就需要在钻孔的过程中,控制好钻头的转速和进给量。
如果转速太快,钻头可能就像一个调皮的小孩子,横冲直撞,把孔壁弄得坑坑洼洼的;如果进给量太大,又可能会把钻头弄断,那就像厨师把做菜的勺子弄断了一样,活儿就没法好好干啦。
所以啊,这个过程就需要非常细致的调整,就像照顾一个小婴儿一样小心翼翼。
而且啊,背钻孔的时候还得考虑材料的特性。
不同的电路板材料就像不同性格的人一样。
有的材料比较软,就像温柔的小姑娘,钻头在上面钻孔的时候就比较轻松,但是也得小心别太用力把它弄伤了;有的材料比较硬,那就像个倔强的小硬汉,这时候钻头就得更有耐心,慢慢地去攻克它。
厚板工艺的好工具—I穿孔的详解

厚板工艺的好工具—I穿孔的详解在如今随着大型化装备和以切割焊接代替钢板铸造的趋势下,中厚板在制造企业中的应用越来越广,利用火焰切割机切割中厚板的过程中存在着穿孔耗时严重影响切割效率,作为生产结构件的头道工序,研究如何效率地切割具有重要意义。
标签:厚板工艺;穿孔随着这些年的城市基建的着力改造,地铁的修建,对于盾构机、压路机等机械产品要求数量越来越多。
这些大型机械中的中厚板的结构件通常都采用火焰切割机来进行切割,但是这种切割方式会存在一个问题,那就是在切割过程中进行预热穿孔操作会需要大量的时间。
通常的解决方案会有以下几种:·原先采用钻床进行钻孔,然后再进行切割;·采用钻切复合机器进行切割;·通过手动添加拐角,将引线手动移动拐角上进行切割;·通过连割工艺减少穿孔;以上四种方案均存在某些问题方案一:在钻床上进行钻孔,将零件的孔都给钻出来,这样在火焰机床上再进行切割需要对板材进行准确定位,同时需要考虑到切割过程中的变形导致的预穿孔的位移。
方案二:这种切割可以通过先钻孔,再切割,可以一个零件一个零件的进行切割,但是这种切割需要对应的钻切复合机,同时考虑到单个钻孔这样的效率比较低,完成切割零件的时间较长。
方案三:在零件图中添加对应的拐角,在排料之后拐角也做对应的切割,同时通过手动移动将引入线移动到上个零件的拐角上,这样切割的时候可以减少穿孔,直接短预热就可以切了,但是这种添加了拐角之后的零件,在排料的时候会影响利用率。
方案四:这种通过添加连割工艺,在进行切割的时候,就能够减少穿孔次数,但是需要对零件的引线进行手动调整,同时对部分零件是无法进行连割工艺的。
通过这几种方案,我们可以看出对于切割厚板来说都存在适用性的一个问题,我们在XSuperNEST的套料引擎中学到了一种新的切割工艺——I穿孔。
这种工艺在切割厚板的时候,可以通过预先额外切割出小的圆孔,作为下个零件的预热穿孔,同时这些小圆孔是在基于排料之后,在零件的空隙部分产生的,不会影响到零件的排料利用率。
厚覆盖层钻孔施工工艺浅析
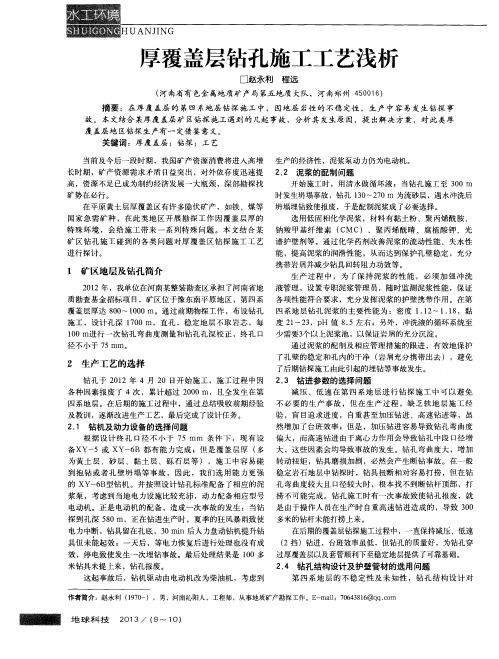
验 ,盲 目追 求进 度 , 自重甚 至加 压钻 进 、高速 钻进 等 ,虽
然 增加 了 台班 效率 ;但 是 ,加压 钻进 容易导 致 钻孔 弯 曲度
2 . 1 钻机及动力设备的选择 问题
根 据 设 计 终 孔 口径 不 小 于 7 5 mm 条件 下 ,现 有 设 偏 大 ,而高 速钻 进 由于离 心力 作用会 导致 钻孔 中段 口径 增
厚覆盖层钻孔施工工艺浅 析
口赵永利 程远
( 河南省 有 色金 属地质矿产局 第五地质 大队,河南郑州 4 5 0 0 1 6 )
摘要 :在厚覆 盖层 的 第四 系地 层钻探 施工 中,因地层 岩 性的不 稳定性 ,生产 中容 易发生钻探 事
故 。本文结合 某厚覆 盖层矿 区钻探施工遇到 的几起 事 故,分析其 发生原 因,提 出解决方 案 ,对 此类厚 覆盖层 地 区钻探 生产有一 定借 鉴意 义。 关键词 :厚覆盖层 ;钻探 ;工艺
进行 探讨 。
能 ,提 高 区地层及钻孔简介
携带岩 屑并减 少钻具 回转阻 力功 效等 。 生 产过 程 中 ,为 了保 持 泥 浆 的性 能 , 必须 加 强冲 洗
2 0 1 2年 ,我单 位在河南 某整装 勘查 区承担 了河 南省地 液管 理 ,设置 专职 泥浆 管理 员 ,随 时监 测泥浆 性 能 ,保 证 质勘 查基 金招 标项 目,矿 区位 于豫东 南平 原地 区 ,第 四系 各项 性 能符合 要求 ,充 分发挥 泥浆 的护 壁携 带作 用 。在第 覆 盖层 厚达 8 0 0 ~1 0 0 0 m。通过前 期物 探工作 ,布 设钻 孔 四 系地 层 钻孔 泥 浆的 主要 性 能 为 :密 度 1 . 1 2 ~1 . 1 8,黏 施 工 ,设 计孔 深 l 7 0 0 m,直 孔 ,稳 定地 层 不取 岩 芯 ,每 度 2 1 ~2 3 ,p H值 8 . 5左右 ;另外 ,冲洗 液 的循环 系统至 1 0 0 m进 行一 次 钻孔 弯 曲度测 量和 钻孔 孔深 校 正 ,终孔 口 少 需要3 个以上 泥浆池 ,以保证岩 屑的充 分沉淀 。
- 1、下载文档前请自行甄别文档内容的完整性,平台不提供额外的编辑、内容补充、找答案等附加服务。
- 2、"仅部分预览"的文档,不可在线预览部分如存在完整性等问题,可反馈申请退款(可完整预览的文档不适用该条件!)。
- 3、如文档侵犯您的权益,请联系客服反馈,我们会尽快为您处理(人工客服工作时间:9:00-18:30)。
厚背板钻孔工艺研究焦其正;王小平;纪成光【摘要】文章主要研究了厚背板压接孔钻孔工艺以及高精度背钻残桩控制方法.通过对比不同类型钻孔工艺的出刀面孔径精度,确定采用等大对钻方法可以满足孔位精度控制要求,同时采用导电控深铣方式控制对钻阶梯.通过对比分析试板测试分区背钻、板厚测量等比例背钻以及内层导电背钻等工艺方法,确定采用内层导电背钻,成功控制背钻残桩<0.25 mm.【期刊名称】《印制电路信息》【年(卷),期】2019(027)001【总页数】6页(P9-14)【关键词】背板钻孔;等大对钻;内层导电背钻【作者】焦其正;王小平;纪成光【作者单位】生益电子股份有限公司,广东东莞 523127;生益电子股份有限公司,广东东莞 523127;生益电子股份有限公司,广东东莞 523127【正文语种】中文【中图分类】TN410 背景随着5 G和IPV6等网络与通讯技术不断向大容量、低延迟,高速度传输的方向发展,作为网络传输的核心器件背板,也不断向高密度、超高速,高稳定性方向发展,这些性能要求引起的显著变化就是,高频高速材料(R5775及以上级别)的使用;尺寸超大1143 mm到1270 mm(45 in~50 in);超厚(最大10 mm~13 mm);层数超多(最大60~80层);压接器孔数剧增(最大7~12万/单元)。
上述变化对背板PCB的核心制程钻孔提出了严苛要求和巨大挑战,因为背板的主要功能器件为通过压接器连接不同的功能模块和网络,其线路板上的主要的功能模块为压接器的压接孔。
压接孔必须通过钻孔制作出来(如图1)。
因此背板的钻孔制作难度也就越来越大。
这主要体现在以下几个方面:(1)板厚度大,钻刀刃长,容易产生断刀报废的风险。
(2)板尺寸大,压接器数量多,孔位精度差极易产生压接跪针的风险。
(3)板厚度高,出刀面偏位几率高,容易产生背钻孔残铜问题,引起短路失效。
(4)为了减小残桩(stub)对高速信号传输的影响,背钻stub控制要求越来越高。
图1 背板钻孔典型缺陷由于以上制作难点,因此必须开发可行的适合背板的钻孔技术和方法,满足背板不断发展提出的要求。
1 工艺方法研究1.1 压接孔钻孔制作工艺针对厚度超高的背板钻孔,在分析现有钻孔技术的基础上提出几种钻孔方法进行对比试验。
针对表1钻孔方式,选取一个板厚9.0 mm的试板进行钻孔工艺测试,通过试板确定最佳的钻孔方法,试板基本要求及结果分析如表2。
表1 厚背板钻孔方式?表2 厚背板不同钻孔方式测试结果备注:孔径精度按照±0.075 mm(3 mil)计算,A/A1/A2为钻带A部分读孔结果,B/B1/B2为钻带B部分读孔结果(读孔机分段读孔)。
?从不同钻孔方式钻孔试板孔位精度结果(表2)来看:目前仅有采用等大对钻方式钻孔可以满足出刀面孔位精度满足Cpk≥1.0的要求,同时无超出0.10 mm(4 mil)的孔(保证无背钻偏孔)。
因此为了保证背钻无偏孔残铜,只能采用等大对钻方式钻孔。
同时等大对钻还可以保证无披锋毛刺(需打磨修理),以及粉尘堵孔的问题(见图2)。
图2 厚板常规钻孔品质问题对于等大对钻工艺存在的问题为对钻交界位置阶梯的问题。
出现阶梯主要由于两个原因导致:(1)两面定位孔偏差,板正反两面钻孔需相同定位孔重复打定位,由于两次打定位,因定位孔偏移会导致两面孔位偏移,最终形成阶梯。
(2)单面钻深大,反面对钻时交界位置的导向作用导致偏位,最终形成阶梯。
对于以上原因分析,结合钻孔设备的发展与新功能的应用,可以采用CCD钻孔方式改善,即采用X-RAY打靶机钻出的孔作为CCD标靶孔,此标靶孔仅供CCD抓靶(无需打销钉定位,对孔无损伤),抓靶后自动计算零位。
同时两面钻孔均采用导电控深方式控制55%板厚的钻深,通过此方法减小单面钻孔深度,也可以改善对钻阶梯大小(图3)。
图3 等大对钻基本原理示意图通过采用导电控深对钻+CCD钻孔方式进行等大对钻,对钻阶梯可以由常规对钻最大0.10 mm减小到≤0.05 mm,(见图4)。
图4 对钻阶梯改善结果通过厚背板钻孔方法的研究得到以下结论:(1)对比多种钻孔方式,采用等大对钻方法最优,可以保证两面孔位精度均满足要求(压接面±0.75 mm以内,非压接面背钻无偏孔残铜,同时无披锋毛刺;(2)采用导电控深+CCD钻孔方式进行等大对钻,可以控制对钻阶梯≤0.05 mm。
1.2 背钻stub控制能力研究1.2.1 背钻Stub对信号的影响由于网络和结构设计的复杂性不断提升,目前的信号传输经常会出现从表层到板中某一层的传输回路。
基本上很少有完全的在两个表层之间传输信号设计(图5)。
在高速信号传输中,过孔无效孔铜(stub,见图6)对信号传输存在严重的干扰。
严重时甚至导致信号失真,或者无法传输。
因此从电子结构设计者到线路板制造商都在寻找减小甚至消除stub长度对信号影响的控制方法。
目前PCB制造业主流解决方案为设计背钻流程,专门用来去除无效孔铜,其原理就是利用深度控制钻孔方式将PTH孔无效孔铜部分钻掉[图6(b)]。
此方法简单高效,同时也存在深度控制精度差(stub长度值),稳定性差(stub长度一致性)的问题。
因此迫切需要提升背钻stub控制的制作能力。
即将stub值控制得越小越好,越稳定越好。
例如全部控制在0.05~0.25 mm(2~10 mil)以内。
图5 信号传输典型模式图6 Stub示意图随着5G通讯及下一代互联网技术的进步与发展,网络传输不断向高频高速方向发展,这就对信号传输的质量和稳定性提出越来越高的要求,而随着频率的不断提高,stub的影响也越来越明显(详见图7所示),因此必须不断提升信号传输的重要影响因素stub的控制能力和水平。
背板由于网络复杂性的提高,过孔背钻的深度也越来越大,钻深经常达到板厚的50%~80%,通常最大钻深达到5~7 mm。
因此常规背钻工艺方法无法满足任意钻深stub均控制在0.25 mm以内的要求。
目前背钻stub控制能力差,且随着钻深的增加,stub长度控制能力不断增加,例如钻深2.5 mm以下stub可以控制在0.25 mm以内,钻深达到4 mm,stub仅能控制在0.35 mm以内,钻深达到5 mm,stub仅能控制在0.40 mm以内。
并且stub控制的一致性也越来越差。
出现这种随着钻深的增加,stub控制能力越差的主要原因在于介质厚度偏差越来越大。
这种介厚偏差的变化目前的设计和PCB制作工艺无法避免。
因此就需要寻找减小和消除介质厚偏差对stub控制的影响的背钻工艺方法。
1.2.2 不同背钻工艺原理目前结合背钻钻机的基本原理,开发出以下三种背钻工艺,通过特殊的背钻方法提高背钻stub控制能力:分区背钻,自动测量板厚等比例背钻,内层导电背钻。
三种工艺的基本原理如下。
(1)分区背钻。
利用叠层设计资料中的铜厚叠加原理,模拟计算分析板厚分布规律,对整板进行板厚分区,依据分区对板厚进行测量,在分区测量的基础上,对每个分区内的板厚和被尊深度进行单独计算与补偿,减小和消除板面不同区域介质厚度差异导致的背钻深度不一致。
(2)自动测量板厚等比例背钻。
板厚测量等比例背钻法,其基本原理如图9。
针对板厚测量目前主要有接触式和非接触式两种方式,由于测量位置与板面背钻孔位置一一对应才能更准确反映实际板厚,非接触式目前还不成熟(大部分停留在样品和测试阶段),接触式普通方法仅能分区测量,因此结合Schmoll钻机的mapping功能,开发出smart mapping方法进行准确的单点测量(需背钻的孔的位置),其测量的基本方法有两种,一种为仅测量台面法,一种为台面和板面相结合的测量方法(图9),通过试板对比台面和板面相结合的方法测量准确度更高,因此试板采用此方法。
(3)内层导电背钻。
内层导电背钻主要有两种方法两次背钻法和3D背钻法,两种方法的基本原理分别如图10、图11。
图7 stub对信号影响示意图内层导电两次背钻基本原理是将基准面设计在距离不可钻穿层的上方更近的位置(一般距离为0.5 mm~1.0 mm),通过减少介质厚度的偏差提高stub的控制能力。
第一次背钻去除参考层与表层的导通,第二次背钻以参考层为基准面进行背钻。
3D背钻的参考层设计思路与两次背钻相同,实现方法略有差异,主要差异为3D 背钻在一钻时精确测量每个需背钻孔位置的表层到参考层的介质厚度。
背钻深度计算时进行深度补偿,消除表层到参考层的介厚的影响。
通过一个板厚7 mm,背钻深度从2~5 mm的尺寸610 mm×914.4 mm的背板进行能力对比测试,三种背钻工艺能力水平测试结果如表3、图12和图13。
(1)3D背钻与两次背钻制作能力接近,3D略优于两次背钻,3D背钻和两次背钻能力明显高于自动测量等比例背钻;(2)按照CP≥1.67计算3D背钻能力为0.75 mm两次背钻为±0.75 mm,自动测量等比例背钻制作能力为±0.14 mm。
图8 板厚分区背钻原理示意图图9 自动测量等比例背钻基本原理图10 内层导电两次背钻原理示意图图11 3D背钻原理示意图2 结论及推广应用通过以上厚背板钻孔制作工艺研究得出以下结论。
表3 三种工艺制作能力对比分析5±5 2.79 2.63 1.52 5±3 1.67 1.58 0.91图12 不同背钻工艺能力对比结果图13 三种背钻工艺对比(1)为了满足压接孔孔位精度以及背钻位置精度控制要求,目前最佳的钻孔方式为导电控深等大对钻方式;(2)等比例背钻,内层导电背钻均可以提升背钻stub控制能力,为了满足stub<0.25 mm(10 mil)要求,最佳工艺方法为内层导电背钻。
通过本项目的开展,显著提升厚背板钻孔制作能力,为高端背板技术能力的提升和市场开拓打下良好的基础,满足背板制作技术发展不断提出的要求,促进高频高速背板技术能力的提升。