PMC生产计划与物料控制实务
PMC生产计划和物料控制

协
(如通用原则物料)允许库存旳最高存量。
同
共
最高存量=一种生产周期旳天数每天使用量+安
进
全存量
三、材料计划与存量管制
安全存量VS最高存量VS最低存量
凝
聚
最低存量
真
知
,
最低存量是指生产淡季固定时期内,能确保配合
协
生产所需旳物料库存数量旳最低界线。
同
共
最低存量=购备时间每天使用量+安全存量
凝
A类物资 品种少,占用资金多,是管理旳要点,必须计算每种
聚
真
物资旳订货量,尽快缩短供给间隔期。选择最优旳订购批量,
知
力求收库存压缩到最低楼上水平
,
协
C类物资 品种繁多,占用资金小,能够适应集中大量订货,以
同 共
简化订购工作,节省订购费用;统计、检验定额控物也却能够
进
采用A类为粗略旳方式。力求简便宜行。以提升管理效率。
各分类必须相斥, 各分类必须涉及分 全部分类之基准,
真
凡能归类者仅能归 类之一切物料,物 必须符合逻辑之基
知 , 协 同
入该类,绝无归入 他类可能,故互斥 之目旳在于互斥之
不能归入某一类者, 本原则 定可归入另一类, 故周延旳目旳为不
共
目旳在于不致于发 致漏掉。
进
生发生反复。
二、物料工程管理
物料分类/编号
知
号时,必要时 符号或数字, 择易记性之文
,
应考虑须能配 必须有足够之 字、符号或数
协
合制成机械。 数量,能够代 字,并应有暗
同
以免将来重编 表全部个别物 示性及联想性,
共
料,以应付将 以便记忆
生产计划与物料控制PMC实务

第六节:制造业生产方案控制三种模式
• 预期滚动方案系统/推进式〔push〕生产控制系统/拉 动式〔pull〕生产控制系统;
〔1〕世界五百強企業〔德資〕,施耐德電氣Schneider推进 式生产控制系统;
〔2〕预期滚动方案编制程序/特点/运作-----有效控制急 单/插单/多单模式;
〔11〕上海某公司〔小型〕供给商配送系统物料广告牌实物 图片实例分析;
〔12〕华强三洋供给商驻厂代表配送/退料/换料广告牌实物 图片实例分析;
〔13〕供给商JIT直送工位管理方法;
〔14〕华晨宝马供给商〔物料看板〕集货配送〔Milk-Run 〕管理方法;
〔15〕精益采购〔JIT采购〕——即时化采购流程的设计/特 征/优势/方式;
〔3〕传统推进式与准时化生产拉动式流程图范例解析; 〔4〕深圳华为精美生产方案管理手册实例分析;
第二章: 生产方案控制 ----均衡化/柔性化生产方案和生产
• 第一节:生产方案控制流程七途径---讲师/学员点评某公 司现场诊断
〔1〕东莞诺基亚拉動生产計划控制流程實例分析;
〔2〕青岛海尔生产方案总体方案控制流程實例分析;
• 上海大金空调/盾安空调/格力空调/上海通用汽車/成都丰田/华晨宝马 /海南马自达/比亚迪汽車/长安汽車.郑州日产/北京ABB等多家知名企 业/曾驻厂辅导〔局部 〕东莞诺基亚/北京索爱/惠州TCL/南京/成都 爱立信/蒂森克虏伯/华强三洋/三菱电机〔广州〕/四川长虹电器/空调 /新飞电器/苏泊尔/夏新电子.厦华集團/惠州德赛/飞利浦〔上海〕/苏 州飞利浦/中兴通讯/武汉烽火科技/中国长城计算机〔深圳〕/东莞汤 姆逊〔电器〕/ 顺德美的日用集团/阿波罗卫浴/TOTO顺德乐华陶瓷 〔arrow〕/得而达水龙头〔Delta〕/科勒卫浴/迈瑞生物医疗/东莞伟 易达/美泰玩具/恒安纸业〔心相印〕/森马/真维斯〔旭日集团〕香港 启桓贸易行/溢达纺织/晶苑制衣集团/东莞台達電子/富士康集團/康佳 集团。
PMC生产计划与物料控制实战操作

PMC生产计划与物料控制实战操作概述生产计划与物料控制(PMC)是一种重要的生产管理方法,它将生产计划和物料控制结合起来,以确保生产过程的顺利进行。
本文将介绍PMC的基本概念、实施步骤和实战操作,帮助您更好地理解和应用PMC。
什么是PMCPMC是生产计划和物料控制的缩写,它是一种管理方法,旨在通过制定有效的生产计划和物料控制策略,实现生产过程的优化和优化资源的利用。
PMC的目标是通过合理安排生产计划,控制物料采购和库存,确保按时交付产品,提高生产效率和效益。
PMC的重要性PMC在生产管理中起着重要的作用,它能够:1.提高生产效率:通过合理安排生产计划,避免生产过程的浪费和闲置,提高生产效率。
2.减少库存成本:通过合理控制物料采购和库存,减少库存成本和积压风险。
3.提高产品质量:通过合理安排生产计划和物料控制,确保产品质量得到保证。
4.提高客户满意度:通过按时交付产品,提高客户满意度,增强企业竞争力。
PMC的实施步骤PMC的实施包括以下几个步骤:1.制定生产计划:根据需求和资源情况,制定生产计划,确定生产任务和完成时间。
2.物料需求计划:根据生产计划,确定所需物料的种类和数量,制定物料需求计划。
3.物料采购和库存控制:根据物料需求计划,进行物料采购,并合理控制物料库存,以确保按时交付产品。
4.生产调度与监控:根据生产计划和物料控制情况,进行生产调度和监控,保障生产进度和质量。
5.生产计划与物料控制优化:根据实际情况和经验,不断优化生产计划和物料控制策略,提高生产效率和品质。
PMC实战操作示例下面将以某公司生产一款手机为例,介绍PMC的实战操作:1.制定生产计划:根据市场需求和资源情况,制定月度生产计划,确定生产任务和完成时间。
2.物料需求计划:根据生产计划,确定所需的各类物料种类和数量,制定物料需求计划表。
3.物料采购和库存控制:根据物料需求计划,进行物料采购,并及时将物料入库,确保物料的及时供应和库存充足。
PMC生产计划与物料控制

PMC生产计划与物料控制生产计划与物料控制是一个公司运作中非常重要的环节,它们直接影响到产品的质量、交货时间和成本控制。
在一个项目管理委员会(PMC)中,生产计划和物料控制是核心工作之一。
本文将从生产计划和物料控制的主要内容、重要性和有效实施的方法等方面进行阐述。
首先,生产计划是确定实际生产需求并制定合理的生产时间表的过程。
它通常包括从原材料采购到产品出厂等各个环节的安排和协调。
生产计划的目标是合理安排生产资源,确保产品按时交付,既满足客户需求,又最大限度地提高效率和降低成本。
物料控制是管理和控制生产过程中所需物料的供应和使用的活动。
它包括物料的采购、入库、库存管理和物料使用等环节。
物料控制的目标是确保物料的供应和使用的准确性、及时性和经济性,以满足生产计划的需求。
生产计划和物料控制的重要性不言而喻。
首先,它们直接影响到产品的质量。
通过合理的生产计划和物料控制,可以避免因物料短缺或过剩导致的生产异常和产品不合格的问题。
其次,它们关系到交货时间。
一个良好的生产计划和物料控制可以确保产品按时交付,避免客户投诉和滞销的风险。
最后,它们对成本控制至关重要。
通过优化生产计划和物料控制,可以降低物料的采购成本、减少库存成本和提高生产效率,从而实现成本的控制。
为了有效实施生产计划和物料控制,需要以下几点注意事项。
首先,需要准确地评估市场需求和客户订单,以制定合理的生产计划。
其次,需要与供应链密切合作,建立稳定的供应商关系,确保物料供应的准确性和及时性。
再次,需要建立合理的库存管理和物料使用机制,避免物料积压和浪费。
最后,需要建立有效的协调和沟通机制,使生产部门、采购部门和销售部门之间能够及时共享信息和协调工作。
总之,生产计划与物料控制是一个公司运作中非常重要的环节。
通过合理的生产计划和物料控制,可以保证产品的质量、交货时间和成本控制。
因此,公司应高度重视并有效实施生产计划和物料控制工作,以提升竞争力和实现可持续发展。
pmc生产计划与物料控制3篇

pmc生产计划与物料控制第一篇:PMC生产计划的基本概念和流程在制造业中,PMC是一个非常重要的部门,它负责制定生产计划和控制物料流动,保证生产可以有序进行。
那么 PMC生产计划的基本概念是什么呢?PMC生产计划本质上是一种很复杂的系统,它包含了以下几个要素:1.产品计划:按照市场需求、库存状况等信息来确定生产计划的产品种类和数量。
2.资源计划:包括人力、机器、材料等的利用计划,计算出每个资源需要的数量和时间分配。
3.时间计划:根据产品计划和资源计划,制定出生产的具体时间表,以保证生产的顺利进行。
4.成本计划:根据生产计划和资源计划,计算出生产成本。
根据这些要素,PMC生产计划通常包括以下几个步骤:1.市场需求预测和销售计划:通过市场调研和销售数据来预测未来市场需求,并制定销售计划。
2.产能分析和资源规划:分析公司的产能和资源状况,制定资源规划和机器升级计划等。
3.产品计划:根据市场需求和资源状况,制定具体产品计划。
4.生产时间计划:根据产品计划和资源计划,制定生产时间表。
5.物料计划:根据生产时间表,制定相应的物料计划,保证各项物料准备充足。
6.检查和修正:不断监控生产过程,及时调整生产计划,并在需要时修改销售计划。
以上就是 PMC生产计划的基本概念和流程,它是保障企业生产顺利进行和经济效益的重要手段。
在实际操作过程中,PMC生产计划需要与财务、采购、生产等部门密切合作,确保整个生产系统的有序运行。
第二篇:物料控制的主要任务和方法在制造业中,物料控制是 PMC部门的主要工作之一,它是指对生产物料的进、出、存情况进行控制,以确保生产过程能够顺利进行。
那么物料控制的主要任务和方法是什么呢?物料控制的主要任务包括以下几个方面:1.物料采购:根据生产计划和物料计划,制定采购计划,及时采购所需物料。
2.物料储存:对采购来的物料进行分类、标记、存储等工作,以便于生产过程中的提取和使用。
3.物料配送:根据生产计划和物料需求,制定物料配送计划,确保所需物料及时送达。
生产计划和物料控制(PMC)实操技法班
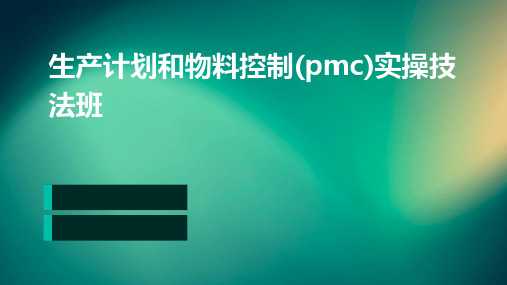
案例二:某电子企业的mrp系统实施
总结词
通过实施mrp系统,实现物料需求的有效计划和控制。
详细描述
该电子企业面临物料需求预测不准确、库存积压严重等问题,通过引入mrp系统 ,实现物料需求的有效计划和控制,提高采购效率和准确性,降低库存成本和缺 货风险,提升企业的竞争力。
案例三:某化工企业的供应商协同管理
MRP系统的实施与应用
要点一
总结词
实践操作,解决问题
要点二
详细描述
实施MRP系统需要先进行系统规划,明确目标、范围和资 源需求。然后进行系统分析,了解现有业务流程和数据基 础。接着进行系统设计,包括数据库设计、用户界面设计 、系统功能设计等。最后进行系统实施和运行维护,确保 系统的稳定性和可靠性。应用MRP系统可以解决生产计划 和物料控制中的各种问题,如库存积压、缺料、生产进度 延迟等。
处理。
盘点流程优化
03mc实操技法案例分享
案例一:某制造企业的生产计划优化
总结词
通过采用先进的生产计划方法,优化生产流程,提高生产效 率。
详细描述
该制造企业面临生产计划不准确、交货延误等问题,通过引 入生产计划管理软件,采用拉动式生产方式,优化排程和调 度,提高生产计划的准确性和及时性,减少库存积压和浪费 ,最终实现生产效率的提高。
重要性
有效的PMC管理能够确保生产计 划的顺利执行,提高生产效率和 产品质量,降低库存成本和缺货 风险,提升企业的整体竞争力。
pmc的基本原则和目标
基本原则
以市场需求为导向,以生产计划为核 心,对物料需求进行准确预测和计划 ,确保生产进度的稳定性和连续性。
目标
实现生产计划的准确性和及时性,确 保物料供应的稳定性和可靠性,优化 库存结构和管理,降低生产成本和库 存成本。
PMC(生产计划与物料控制)教程
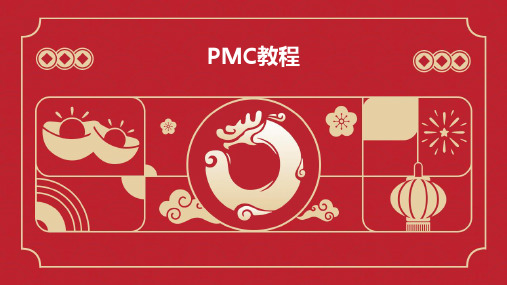
物料采购与跟催
总结词
物料采购与跟催是确保物料按时、按量供应的关键环节,需 要与供应商建立良好的合作关系,并密切关注物料供应情况 。
详细描述
根据物料需求计划,与供应商协商确定采购合同,明确采购 数量、交货时间和地点等条款。在采购过程中,需要定期跟 催供应商,确保物料按时到货。对于到货的物料,需要进行 质量检验,确保符合生产要求。
03 物料控制
CHAPTER
物料需求计划的制定
总结词
物料需求计划是物料控制的核心,它决定了企业生产所需的原材料、零部件和辅料的数量、质量和时 间。
详细描述
制定物料需求计划需要综合考虑销售预测、生产计划、库存状况以及原材料的采购周期等因素。通过 计算得出每种物料的总需求量,再根据实际库存进行调整,最终确定每种物料的采购数量和时间。
强化信息沟通与协作
加强各部门之间的信息沟通与协作, 确保信息的准确性和及时性,从而提 高生产计划与物料控制的协同效率。
05 PMC的实操技巧
CHAPTER
产能评估与资源分配
产能评估
准确评估现有设备和工人的生产能力,了解 瓶颈环节,为后续生产计划提供依据。
资源分配
根据产品特性和生产需求,合理分配人力、物料、 设备等资源,确保生产顺利进行。
监控生产计划执行情况
通过实时监控和数据分析,了解生产计 划的执行情况,及时发现和解决问题。
优化生产计划
通过不断优化生产流程、改进工艺、 提高设备利用率等方式,降低生产成
本,提高生产效率。
调整生产计划
根据市场需求变化、企业内部变化或 其他不可抗力因素,及时调整生产计 划,确保计划的适应性。
应急预案
制定应急预案,应对突发事件对生产 计划的影响,确保生产活动的连续性 和稳定性。
生产计划和物料控制(PMC)

物料收发制度及执行
制定库存量考核方案
仓库呆料处理制度
帐物一致相关制度
*
第三室:材料计划和存量控制
采购必备的条件和依据 1、条件 根据不同的物料、供应商使用不同的采购方式 信息共享 采购要懂生产计划,供应链(SCM)管理 针对核心物料进行供应商生产计划库存监控 仓库库存管理 2、依据 库存 采购周期 在途量扣除 采购周期 本次订货量
异常协调
包装发货
第四室:生产计划控制管理
月度主排产计划/周计划依据 市场提供的交货进度控制表 工程提供的模具明细 车间提供的工装及设备产能 财务提供的销售与库存状况分析资料 战略物料状况 IE提供的机种分组产能负荷 未来月度的人手
第四室:生产计划控制管理
工艺路线 环境因素 采购中的物料 客户优先顺序的规律 未来6月的设备 下月维修保养计划
第二室:生产计划和物料控制管理流程
生产计划和物料管理的十四流程
生产订单处理流程
生产计划与生产过程控制流程
生产辅料损耗控制流程
采购物料交期管理制度
供应商选择、评估、考核流程
工程更改流程
新材料、配件确认
供应物料品质管理方法
*
第二室:生产计划和物料控制管理流程
生产计划和物料管理的十四流程
物料备料与催料流程
第三室:材料计划和存量控制
库存管理九大指标 库存周转率 及时发货率 帐物相符率 月均库存量 年均库存量 库存物料数量准确率 库存物料质量完好率 仓库面积容积利用率 运输质量保证率
第四室:生产计划控制管理
一般控制流程
市场部销售供货信息
生产计划
物料需求计划
协商交货期
产出计划
PMC生产计划与物料控制教材
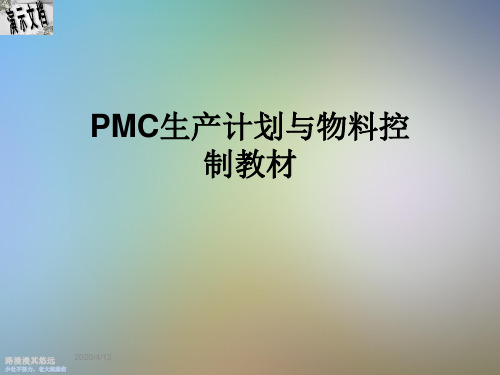
•
2.6 预期型计划
• 在预期生产情形下, 由于生产所必需的数据资料 在开发阶段已作准备,因而 进入生产阶段即开始正式营 业活动时,就没有必要每次 都制作数据库,要计划的仅 是生产品种、数量及交货期 。
•计划立案日分别为5月25日 、6月25日、7月25日,时间 相隔为1个月。
•计划制订比计划执行日提前 的日数称之为计划工作日程
•1.1 PMC定义的两项内容 •1.2 PMC管理任务与目标 •1.3 PMC的组织结构建议 •1.4 PMC的未来管理功能
路漫漫其悠远
•
企业管理混乱的根源
• 缺乏标准化 • 组织不良 • 缺乏计划性 • 控制工作不良
路漫漫其悠远
•
生产工厂常见的问题(一)
1. 订货规格常不相同,图面设计及生产准备无法 标准化,且估价不够准确。
•投入 •人员 •资金 •材料 •计划 •政策 •程序
•项目管理
•项目 •控制
•组织 • 人员 • 资源 • 工作活动
•信息系统
•产出
•产品 •服务 •活动 •数据
•*当第三物流管理模式成为企业首选时,PMC之对外 管理功能将转向“如何与物流配送中心协调沟通”。
•订单信息
路漫漫其悠远
•企业 •指令交流
零组件别 三日/日
日
路漫漫其悠远
•
大日程生产计划(例)
•产品别:×××
项目
月份 一月份 二月份
三月份
四月份
五月份
设计图样
材料计划
采购计划
程序计划
工数计划
外包计划
设备计划
资源管理计划
日程计划
缴交生产计划
路漫漫其悠远
•
生产计划及物料控制(pmc)课件
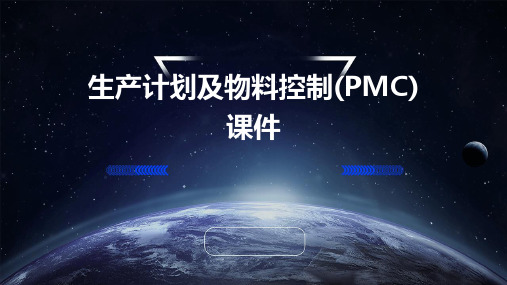
定期对生产计划执行情况进行 评估和总结,不断优化生产计 划管理流程。
03
物料需求计划
物料清单的编制
01
02
03
确定产品结构
根据产品图纸、技术要求 和工艺流程,确定产品的 物料组成和结构。
编制物料清单
根据产品结构,逐层展开, 列出所有零部件的名称、 规格、数量等详细信息。
维护物料清单
随着产品更新换代或工艺 改进,及时更新物料清单, 确保其准确性。
02
生产计划管理
生产计划的制定与调整
根据市场需求、产品 特点、产能和供应链 状况制定生产计划。
建立灵活的生产计划 调整机制,以应对突 发事件和紧急订单。
定期评估生产计划, 根据实际生产和市场 需求变化进行调整。
生产计划的关键指标
生产效率
衡量生产线的产出与投 入之比,反映生产过程
的效率。
准时交货率
生产执行系统的应用
生产过程管理
生产执行系统可以对生产过程进行实时监控和管 理,确保生产进度和质量符合要求。
质量管理
生产执行系统可以对生产过程中的质量进行检测 和控制,及时发现和解决质量问题。
设备管理
生产执行系统可以对生产设备进行监控和维护, 确保设备的正常运行和使用寿命。
供应链管理系统的应用
供应商管理
PMC能够协调各个部门的工作,确保生产过程中的各个环节顺畅进行,提高整体的 生产效率。
PMC通过合理的生产计划和物料控制,能够减少库存积压和浪费,降低企业的库存 成本。
PMC的发展历程与趋势
PMC起源于20世纪初的制造业,随 着信息技术的发展和市场竞争的加剧 ,PMC在制造业中的地位逐渐提升 。
未来,随着物联网、大数据、人工智 能等新技术的应用,PMC将更加智能 化、自动化和精细化,进一步提高制 造业的生产效率和竞争力。
生产计划与物料控制PMC实务.doc

生产计划与物料控制PMC实务------------------------------------------------------------------------------------------------------------------------------------------课-程-背-景:生产计划和物料控制(PMC)部门是一个企业“心脏”,掌握着企业生产及物料运作的总调度和命脉,统筹营运资金、物流、信息等动脉,直接涉及影响生产部、生产工程部、采购、货仓、品控部、开发与设计部、设备工程、人力资源及财务成本预算控制等,其制度和流程决定公司盈利成败。
因此PMC部门和相关管理层必须充分了解:物料计划、请购、物料调度、物料控制(收、发、退、借、备料等)、生产计划与生产进度控制,并谙熟运用这门管理技术来解决问题,学习PMC课程从计划价值流切入剖析工厂制造成本和缩短制造周期,提高物流过程循环效率(库存、资金的周转率)及客户满意率;为降低或消除物流过程中的非增值活动。
--------------------------------------------------------------------------------培-训-收-益:1、建立制定完善的生产与物控运作体系à提升准时交货和降低库存成本2、预测及制定合理的短、中、长期销售计划à达成公司策略管理目标3、对自身的生产能力负荷预先进行详细分析并建立完善产品数据机制à协助公司建立产品工程数据4、生产前期做好完整的生产排程和周生产计划à提高备料准确率,保持生产顺畅5、配合生产计划做到良好物料损耗控制和备料à完善降低物料损耗机制和停工待料工时6、对生产进度及物料进度及时跟进和沟通协调à缩短生产周期,提高企业竞争力--------------------------------------------------------------------------------课-程-大-纲:如何做好生产计划/物料控制实操技法班第一室:銷售計划/生産計划/物料計划协调接口管理1、生産計划角色和定位---订单总导演/总指挥生产计划制度和流程决定公司盈利成败2、銷售計划/生産計划/物料計划架构/职能分工中兴通讯销售计划/生产计划/物料计划接口职能图/资源图实例分析美的集团连续滚动周计划负荷分析和三天生产计划不能变职能图东莞诺基亚公司銷售計划/生産計划/物料計划组织架构生産計划/物料控制五大职能----欠料分析跟进/备料功能/呆料预防处理--------3、怎样建立/完善计划体系-----一级主生产计划/二级生产计划做好生产计划必须具备五大信息条件及九方面专业技能-一级主生产计划制订和执行流程- APS系统二级主生产计划制订和执行流程--4、主生产计划链接体系----指挥与协调保障功能销售预测与生产计划的衔接与平衡生产计划准时生产计划VS市场业务部VS客户“三赢”规则一汽大众锁定一周生产计划不能变控制流程實例分析有效控制扦单、急单、补单/加单五种措施(范例)-----中山某有限公司5、销售预测与主生产计划(MPS)月/周生产计划/物料計划(MRP)链接流程- order managemen/APS系统銷售预测計划/生产计划变化反馈和预测库存控制协调管理一级主生产计划产供销平衡制度-上海某医疗公司-銷售計划流程――销售预测流程/销售计划流程/备货计划流程/生产计划流程6、制造业生产计划控制三种模式――预期滚动计划系统/推进式(push)生产控制系统/拉动式(pull)生产控制系统7、不同产品销售策略决定不同五大計划(銷售計划/生産計划/物料計划/采购計划/库存計划)深圳华为精美计划管理手册实例分析-某著名企業产品策略手册实例分析小结:不同产品的物流策略决定不同五大計划(銷售計划/生産計划/物料計划/采购計划/库存計划)第二室銷售計划/生产计划控制流程--- order management-(包括项目计划)1、銷售预测計划/主生产计划(MPS)与月/周生产计划控制流程七途径---讲师/学员点评某公司现场诊断通过市场调查/信息反馈提高订单预测准确率三大做法提升编制銷售预测計划编制准确性六大步骤华润集团华晶銷售预测計划编制六大步骤實例分析滚动銷售预测計划微调制度化降低预测库存成本原理分析青岛海尔新产品项目计划总体方案控制流程實例分析-- order management苏州西门子月/周/日项目计划时间节点协调流程實例分析--- MIS系统苏州西门子项目计划时间节点考核制度實例分析富士康集团ERP—SAP/R3系统主生产计划流程案例分析--- order management大金空调(日资公司)計划控制流程實例分析----MES系统青岛海尔月/周/日项目计划协调流程實例分析----MES系统富士康集团(台湾)公司月度滚动产能负荷分析/三天生产计划不能变的滚动产能负荷分析實例分析苏州西门子生产计划(拉动)三天生产计划不能变的滚动产能负荷分析實例分析2、透过准时化生产机制解决订单频繁变更三种方法-- Production plan change management顺德美的日用集团扦单、急单、补单/加单/生産計划紧急控制流程實例分析-- Production plan change management飞利浦扦单/急单計划紧急控制流程案例分析- Production plan change management飞利浦周删改生产计划控制基本流程案例分享第三室一级主生产计划/二级生产计划进度控制---- order delivery management1、缩短产品周期流程-- lead time reduction西门子产品周期缩短流程价值流案例分享某公司缩短产品周期电脑系统(用友)流程主界面实例分析2、月/周生产计划产能连续滚动负荷分析制度化中国某著名公司月度主排产计划制定十三依据中国某著名公司三天生产计划依据制定九依据3、周生产计划要点、内容及编制演练----月/周生产计划排程表制定与执行重点演练--上海某公司五张订单月/周生产计划排程表制定个案演练4、分析产能负荷七要素方面---人力负荷/机器负荷……广州某配件公司2007/04月产能负荷会实录文件分析产能负荷分析表实例-----广州某汽车配件公司5、生产进度监控三个阶段---事前/事中/事后--信息化在生产管理中运用5.1如何统计分析生产数据----MIS系统5.2通过生产数据采集计算机系统图监控计划与进度---东莞某公司MES系统5.3现场运用LED/条形码同步监控生产进度实物展示分析---事中管理6、协调沟通处理生产异常问题-- 八条改善措施(NCR goods management )7、产销失调原因与对策--跨部门生产进度控制七步骤8、飞利浦(上海)各部门异常工时/各部门产能损失图案例分析--------生产绩效管理9、中国某公司生产能力效率表/综合效率分析-------生产绩效管理深度案例:中国某著名公司生产计划各相关部门控制流程(共46页)第四室物流计划跟进与存量管制0.物流计划流程七步骤----某公司学员现场诊断(学员与讲师互动点评)产品交期短/物料采购周期长物流计划流程定期缩短供货商lead time工作制度化流程-- Real Lead time monitoring在銷售预测不准条件下避免预测采购导致库存量提升工作流程物料采购周期长再请购计划(PR)流程--- Reorder point management扦单、急单、补单/加单/生産計划紧急update物料计划流程解析上海西门子ERP—SAP/R3系统RUN-MRP流程主界面分析北京某公司Normal Order/ CONSIGNMENT/VMI/JIT/Buffer Control四种采购工作流程三菱电机(广州)有限公司(欧洲全资)ERP—SAP/R3系统采购订单管理流程主界面实例分析—1、供货商交期管制十大之道-- lead time reduction2、采购物料交期跟催监控三张表格/工具偉創力(美資)在采购物料欠料分析跟进表實例分析某世界五百強企業采購物料预防欠料表案例/中国某企業采购备料齐套表实例分析某世界五百強企業(美資)采購物料跟踪表案例研討――捷普科技中国某著名家电民營企業ERP-ORACLE系统物料查询/跟进主界面实例分析1物料短缺八大原因和七种预防对策2物料管理相辅相成十四流程-- warehouse management2.1物料管理精髓三个盲点和八大死穴--――伟创力(Flextronics)美資公司呆料预防/处理制度实例2.2某公司物料工程更改流程分析2.3一汽马自达公司补料/损耗控制案例分析--降低内循环成本美的/ /精工集团(日资)补料/损耗控制案例分析4、存量管制-- inventory management需求预测、物料计划与库存控制四大策略欧普照明公司需求预测与库存控制职能图现场分析青岛海尔公司需求预测变化和库存相应调整控制流程實例分析远期采购批量与预测库存、需求预测原理长虹采购订单模式实例分析----大陆标准/通用物料采购TCL远期采购库存模式实例分析---海外lean time长物料采购安全存量VS最高存量VS.最低存量定义安全存量三种设定方法ABC控制法-- warehouse management施耐德電氣ABC控制法實例分析库存量根据生产淡旺波峰调整两套方法ABB根据生产淡旺波峰库存量调整三阶段實例分析使用条形码及与供货商进行电子数据交换(EDI)降低库存量方法库存量降低五大方法九大库存指标管理/考核库存周转率定量计算提高库存周转率的途径深圳某实业有限公司物料周转速度/周转率/存料率简例透过现场诊断学员公司库存现状运用六种存量管制模式设置恰当库存管理方法----降低外循环成本-透过供应链管理控制:MTO /ROP 需求量少/供应商要求MOQ等外循环成本库存武汉某著名公司优化供应链管理實例分析-减少外循环库存成本.某著名电讯公司透过打破常规实现“零库存”故事尾声:当头棒喝—捅破窗纸1、学习/兴奋两天,回到公司后……结合公司实际情况-2、通过学员成果发表--体会分享/经验回顾/讲师点评3、实践/活用所学五步骤--------------------------------------------------------------------------------讲-师-资-历:雷老师,香港理工大学MBA,香港生产力促进局特约讲师,美国管理学会(AMA)授权专业培训师,中山大学EMBA班特邀实战型讲师。
生产计划与物料控制PMC

第二部分:生产管理(pmc)的组织结构
1.制造管理与生产管理的职能分离 2.生产管理的职能定位及追求的目标 3.pmc(生产管理)=PC(计划管理)+MC(物料管理) 4.PC的职责、MC的职责、PC与MC间规范流程 5.传统的pmc结构不适应于生产管理的有效运作 6.规范的pmc组织结构分析案例 第三部分:主生产计划(MPS)运作 1.需求的确定流程,需求=预测+订单 2.预测是生产计划顺利执行的前提和基础 3.合同评审关键管理因素 4.预测与产销计划 5.预测模式及实务预测方法 6.如何组织生产规划会议协调生产计划 7.主生产计划(MPS)周期滚动规则 8.主生产计划的作用 9.没有规则和约定生产计划方式,生产计划将形同虚设
5
第四部分:主生产计划的编排
1.主生产计划编排流程及组织要求 2.主生产计划的基本形式 3.某工厂季/月/周生产计划编排案例剖析 4.周生产计划制定时须考虑四个关键因素 5.计划变更后的信息沟通流程 6.生产计划适用的基本表格形式 7.生产进度的控制方法 8.生产进度失控后的应对处理案例 9.如何应对插单和紧急订单案例 第二篇:物料需求规划与库存控制 第一部分:物料需求规划基本概念 1.MRP的基本原理及逻辑流程 2.BOM的基本形式和作用 3.毛需求与净需求的展算方式 4.现有库存量、现有库存可用量、库存可用量、在途库存量的区别 5.何谓ATP量?ATP量作用是什么? 6.供应链(SCM)基本理念及操作案例 7.ERP/MRPⅡ/ERP/ERPⅡ之间相互关系 8.ERP实施中基本步骤及实施中的八大忠告
9
● 导师简介
蔡老师:培训师、咨询师中国企业家联合会高级讲师,课程研发方向为供应 链管理,2002年获得美国生产与库存管理协会颁发的CPIM证书。曾在跨国企 业、世界500强企业主管过生产计划、供应链流程改进、国际采购、库存控 制等部门。在MRPII/ERP系统、仓库管理、库存控制、生产计划、采购谈判、 物流配送方面具有丰富的实战经验和管理理念,为圣戈班、海沃斯、柯达、 皇家飞利浦、第一医药、联合汽车、UT斯康达、金创集团等几十家大型企业 提供过供应链咨询和培训;为《供应链管理分析师》课程和《物流紧缺人才》 课程编写教材和考试大纲,并开展培训和阅卷。 【研究方向】生产计划、仓储管理、库存控制、供应链管理、物流配送、物 流项目管理、采购管理、企业采购实战、采购谈判技巧等; 【代表客户】宏旭模具、森中电器、湘大兽药、强田液体、西达实业、顶味 食品、富佳家俱、合安防护、佳特设备、纳博特斯克、上兴设备、福州惠宝、 庄信万丰、新洲包装等。
生产计划与物料控制PMC实务培训报告

生产计划与物料控制PMC实务培训报告一、培训目的和背景本次培训的目的是帮助员工提高生产计划与物料控制(PMC)实务的能力,加强生产计划和物料供应管理的技巧和知识,从而提高企业的生产效率和准时交付率。
通过此次培训,我们希望员工能够掌握PMC的基本概念和原则,了解目前常用的生产计划和物料控制方法和工具,并能够应用于实际工作中。
二、培训内容和方式1.生产计划概述本节主要介绍了生产计划的定义和作用,重点强调了合理的生产计划对企业生产流程的顺畅运行和产品质量的控制有着重要的作用。
同时,介绍了生产计划的主要内容和要素,并包括制定生产计划的基本步骤和方法。
2.需求预测与销售计划需求预测和销售计划是制定生产计划的重要前提,本节课主要介绍了需求预测的方法和模型,以及销售计划的制定过程和要点。
通过实际案例分析,帮助员工了解如何进行需求预测和销售计划,并且进行了相应的练习。
3.计划编制与调整本节课介绍了生产计划的编制和调整方法,并结合实际案例进行了分享和讨论。
重点强调了制定生产计划的准确性和可行性,以及在生产过程中及时调整计划的重要性。
通过此部分的学习,员工能够更好地完成生产计划的编制和调整工作。
4.物料控制概述物料控制是PMC工作的核心内容,本节课主要介绍了物料控制的定义和作用,重点强调了合理的物料控制对企业生产流程和库存管理的重要性。
同时,介绍了物料控制的主要方法和工具,并进行了实际案例分析。
5.库存管理与优化本节课介绍了库存管理的基本原则和方法,并结合实际案例进行了分享和讨论。
重点强调了合理的库存水平对企业成本和交付能力的影响,以及如何通过库存管理和优化来降低成本和提高交付能力。
三、培训效果和总结通过本次培训,员工对生产计划与物料控制的基本概念和原则,以及常用的方法和工具有了更深入的了解。
培训效果良好,员工们积极参与讨论和练习,对培训内容表示满意。
总结来说,生产计划与物料控制(PMC)是企业生产管理中非常重要的环节,对企业的生产效率和准时交付能力有着直接的影响。
生产计划与物料控制PMC实务.doc
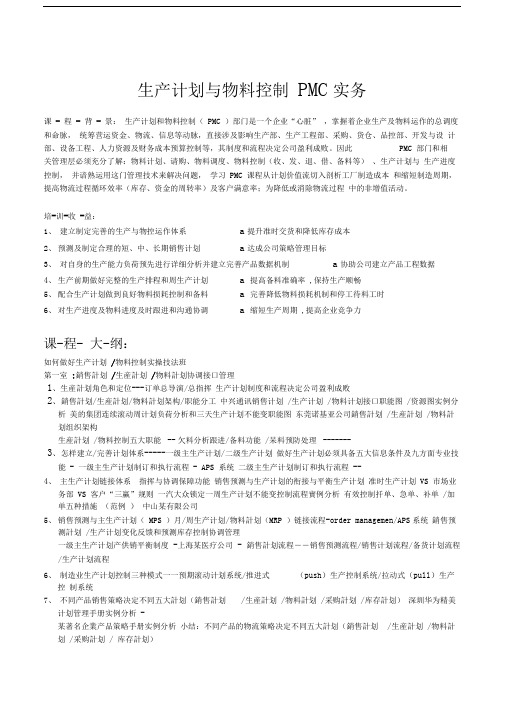
生产计划与物料控制PMC实务课- 程- 背- 景:生产计划和物料控制(PMC )部门是一个企业“心脏” ,掌握着企业生产及物料运作的总调度和命脉,统筹营运资金、物流、信息等动脉,直接涉及影响生产部、生产工程部、采购、货仓、品控部、开发与设计部、设备工程、人力资源及财务成本预算控制等,其制度和流程决定公司盈利成败。
因此PMC 部门和相关管理层必须充分了解:物料计划、请购、物料调度、物料控制(收、发、退、借、备料等)、生产计划与生产进度控制,并谙熟运用这门管理技术来解决问题,学习PMC 课程从计划价值流切入剖析工厂制造成本和缩短制造周期,提高物流过程循环效率(库存、资金的周转率)及客户满意率;为降低或消除物流过程中的非增值活动。
培-训-收-益:1、建立制定完善的生产与物控运作体系a提升准时交货和降低库存成本2、预测及制定合理的短、中、长期销售计划a达成公司策略管理目标3、对自身的生产能力负荷预先进行详细分析并建立完善产品数据机制a协助公司建立产品工程数据4、生产前期做好完整的生产排程和周生产计划 a 提高备料准确率,保持生产顺畅5、配合生产计划做到良好物料损耗控制和备料 a 完善降低物料损耗机制和停工待料工时6、对生产进度及物料进度及时跟进和沟通协调 a 缩短生产周期,提高企业竞争力课-程- 大-纲:如何做好生产计划/物料控制实操技法班第一室:銷售計划/生産計划/物料計划协调接口管理1、生産計划角色和定位---订单总导演/总指挥生产计划制度和流程决定公司盈利成败2、銷售計划/生産計划/物料計划架构/职能分工中兴通讯销售计划/生产计划/物料计划接口职能图/资源图实例分析美的集团连续滚动周计划负荷分析和三天生产计划不能变职能图东莞诺基亚公司銷售計划/生産計划/物料計划组织架构生産計划/物料控制五大职能-- 欠料分析跟进/备料功能/呆料预防处理-------3、怎样建立/完善计划体系-----一级主生产计划/二级生产计划做好生产计划必须具备五大信息条件及九方面专业技能- 一级主生产计划制订和执行流程- APS 系统二级主生产计划制订和执行流程--4、主生产计划链接体系指挥与协调保障功能销售预测与生产计划的衔接与平衡生产计划准时生产计划VS 市场业务部VS 客户“三赢”规则一汽大众锁定一周生产计划不能变控制流程實例分析有效控制扦单、急单、补单/加单五种措施(范例)中山某有限公司5、销售预测与主生产计划(MPS )月/周生产计划/物料計划(MRP )链接流程-order managemen/APS系统銷售预测計划/生产计划变化反馈和预测库存控制协调管理一级主生产计划产供销平衡制度-上海某医疗公司- 銷售計划流程――销售预测流程/销售计划流程/备货计划流程/生产计划流程6、制造业生产计划控制三种模式一一预期滚动计划系统/推进式(push)生产控制系统/拉动式(pull)生产控制系统7、不同产品销售策略决定不同五大計划(銷售計划/生産計划/物料計划/采购計划/库存計划)深圳华为精美计划管理手册实例分析-某著名企業产品策略手册实例分析小结:不同产品的物流策略决定不同五大計划(銷售計划/生産計划/物料計划/采购計划/ 库存計划)第二室銷售計划/ 生产计划控制流程--- order management- (包括项目计划)1、銷售预测計划/主生产计划(MPS)与月/周生产计划控制流程七途径---讲师/学员点评某公司现场诊断通过市场调查/ 信息反馈提高订单预测准确率三大做法提升编制銷售预测計划编制准确性六大步骤华润集团华晶銷售预测計划编制六大步骤實例分析滚动銷售预测計划微调制度化降低预测库存成本原理分析青岛海尔新产品项目计划总体方案控制流程實例分析-- order management 苏州西门子月/周/日项目计划时间节点协调流程實例分析--- MIS 系统苏州西门子项目计划时间节点考核制度實例分析富士康集团ERP—SAP/R3 系统主生产计划流程案例分析--- order management 大金空调(日资公司)計划控制流程實例分析MES 系统青岛海尔月/周/日项目计划协调流程實例分析--- MES 系统富士康集团(台湾)公司月度滚动产能负荷分析/三天生产计划不能变的滚动产能负荷分析實例分析苏州西门子生产计划(拉动)三天生产计划不能变的滚动产能负荷分析實例分析2、透过准时化生产机制解决订单频繁变更三种方法-- Production plan change management顺德美的日用集团扦单、急单、补单/加单/生産計划紧急控制流程實例分析-- Production plan change management飞利浦扦单/急单計划紧急控制流程案例分析- Production plan change management 飞利浦周删改生产计划控制基本流程案例分享第三室一级主生产计划/二级生产计划进度控制order delivery management1、缩短产品周期流程-- lead time reduction 西门子产品周期缩短流程价值流案例分享某公司缩短产品周期电脑系统(用友)流程主界面实例分析2、月/周生产计划产能连续滚动负荷分析制度化中国某著名公司月度主排产计划制定十三依据中国某著名公司三天生产计划依据制定九依据3、周生产计划要点、内容及编制演练-----月/周生产计划排程表制定与执行重点演练--上海某公司五张订单月/周生产计划排程表制定个案演练4、分析产能负荷七要素方面---人力负荷/机器负荷 ....广州某配件公司2007/04月产能负荷会实录文件分析产能负荷分析表实例广州某汽车配件公司5、生产进度监控三个阶段---事前/事中/事后--信息化在生产管理中运用5.1如何统计分析生产数据--- MIS 系统5.2通过生产数据采集计算机系统图监控计划与进度---东莞某公司MES 系统5、3现场运用LED/条形码同步监控生产进度实物展示分析---事中管理6、协调沟通处理生产异常问题-- 八条改善措施(NCR goods management )7、产销失调原因与对策--跨部门生产进度控制七步骤8、飞利浦(上海)各部门异常工时/各部门产能损失图案例分析------- 生产绩效管理9、中国某公司生产能力效率表/综合效率分析 ---- 生产绩效管理深度案例:中国某著名公司生产计划各相关部门控制流程(共46 页)第四室物流计划跟进与存量管制0.物流计划流程七步骤某公司学员现场诊断(学员与讲师互动点评)产品交期短/物料采购周期长物流计划流程定期缩短供货商lead time 工作制度化流程-- Real Lead time monitoring 在銷售预测不准条件下避免预测采购导致库存量提升工作流程物料采购周期长再请购计划(PR )流程--- Reorder point management扦单、急单、补单/加单/生産計划紧急update 物料计划流程解析上海西门子ERP—SAP/R3 系统RUN-MRP 流程主界面分析北京某公司Normal Order/ CONSIGNMENT/VMI/JIT/Buffer Control 四种采购工作流程三菱电机(广州)有限公司(欧洲全资)ERP—SAP/R3 系统采购订单管理流程主界面实例分析—1、供货商交期管制十大之道-- lead time reduction 2、采购物料交期跟催监控三张表格/工具偉創力(美資)在采购物料欠料分析跟进表實例分析某世界五百強企業采購物料预防欠料表案例/ 中国某企業采购备料齐套表实例分析某世界五百強企業(美資)采購物料跟踪表案例研討一一捷普科技中国某著名家电民營企業ERP-ORACLE 系统物料查询/ 跟进主界面实例分析1 物料短缺八大原因和七种预防对策2物料管理相辅相成十四流程--warehouse ma nageme nt2. 1物料管理精髓三个盲点和八大死穴--――伟创力(Flextronics )美資公司呆料预防/处理制度实例2.2 某公司物料工程更改流程分析2. 3 一汽马自达公司补料/损耗控制案例分析--降低内循环成本美的/ /精工集团(日资)补料/损耗控制案例分析4、存量管制-- inventory management 需求预测、物料计划与库存控制四大策略欧普照明公司需求预测与库存控制职能图现场分析青岛海尔公司需求预测变化和库存相应调整控制流程實例分析远期采购批量与预测库存、需求预测原理长虹采购订单模式实例分析- 大陆标准/通用物料采购TCL 远期采购库存模式实例分析---海外lean time 长物料采购安全存量VS 最高存量VS. 最低存量定义安全存量三种设定方法ABC 控制法-- warehouse management 施耐德電氣ABC 控制法實例分析库存量根据生产淡旺波峰调整两套方法ABB 根据生产淡旺波峰库存量调整三阶段實例分析使用条形码及与供货商进行电子数据交换(EDI)降低库存量方法库存量降低五大方法九大库存指标管理/考核库存周转率定量计算提高库存周转率的途径深圳某实业有限公司物料周转速度/周转率/存料率简例透过现场诊断学员公司库存现状运用六种存量管制模式设置恰当库存管理方法-- 降低外循环成本谢谢观赏-透过供应链管理控制:MTO /ROP 需求量少/供应商要求MOQ 等外循环成本库存武汉某著名公司优化供应链管理實例分析-减少外循环库存成本.某著名电讯公司透过打破常规实现“零库存”故事尾声:当头棒喝—捅破窗纸1、学习/兴奋两天,回到公司后……结合公司实际情况-2、通过学员成果发表--体会分享/经验回顾/讲师点评3、实践/活用所学五步骤讲-师-资-历:雷老师,香港理工大学MBA ,香港生产力促进局特约讲师,美国管理学会(AMA)授权专业培训师,中山大学EMBA 班特邀实战型讲师。
生产计划与物料控制PMC

第二部分:物料需求计划的制定 1.通用性、常规性材料需求计划的制定 2.中长期采购周程(超过2个月)的物料需求计划的制定 3.中长期生产周程零件、半成品需求计划制定 4.零件生产与外协加工生产计划的制定 5.工作指派方法与自制部品生产进度的控制 6.物料采购计划的滚动规则(与供应商约定规则) 7.物料进度跟催 案例分享:企业实际排产案例、制造业生产计划体系案例 集体讨论:应对计划变动频繁的一些工作技巧和方法 第三部分:物料采购 1..实用的订购方法 a.固定订购批量法(Fixed Order Quantity) b.经济订购批量法(EOQ法) c.固定时订购法(Fixed Period Requirements) d.净需求订购法(Lot For Lot) e.复仓法与订购点法 2.库存的分类 3.衡度库存合理性的指标:库存周转率和库存周转期计算和分析 4.物料在库天数分析和计算 5.库存积压资金的原因分析 6.降低库存的有效途径(安全库存的设置,库存的分类管理,缩短采购周期,提高预测准确性等十几 种具体方法) 7.广东某电子厂降低300万美元库存行动计划案例 8.某工厂材料库存周转率分析案例 9.库存控制基本组织保障要求
3
第二部分:生产管理(pmc)的组织结构
1.制造管理与生产管理的职能分离 2.生产管理的职能定位及追求的目标 3.pmc(生产管理)=PC(计划管理)+MC(物料管理) 4.PC的职责、MC的职责、PC与MC间规范流程 5.传统的pmc结构不适应于生产管理的有效运作 6.规范的pmc组织结构分析案例 第三部分:主生产计划(MPS)运作 1.需求的确定流程,需求=预测+订单 2.预测是生产计划顺利执行的前提和基础 3.合同评审关键管理因素 4.预测与产销计划 5.预测模式及实务预测方法 6.如何组织生产规划会议协调生产计划 7.主生产计划(MPS)周期滚动规则 8.主生产计划的作用 9.没有规则和约定生产计划方式,生产计划将形同虚设
- 1、下载文档前请自行甄别文档内容的完整性,平台不提供额外的编辑、内容补充、找答案等附加服务。
- 2、"仅部分预览"的文档,不可在线预览部分如存在完整性等问题,可反馈申请退款(可完整预览的文档不适用该条件!)。
- 3、如文档侵犯您的权益,请联系客服反馈,我们会尽快为您处理(人工客服工作时间:9:00-18:30)。
实际需工 作日
•3
•600ו2
•=6天á7天(余1天)
•A单 实际需工作日=•9•62×0••0320
•=14天>12天(-2天)
•C单 实际需工作日=
•600
•3
•75× •2
•D单 实际需工作日=
•900
•3
•130ו2
•=5.4天á10天(余4天) •=5天á14天(余9天)
PMC生产计划与物料控制实务
学习改变命运,知 识创造未来
PMC生产计划与物料控制实务
•4.优先率排程要领与演练
优先管制的前提资料:
①.作业前置时间; ②.订单规定的时间; ③.作业标准工时。
至出货剩余的天数(Number of days will need)
•优先率 =
•(Priority Ratio工)作所必需的天数(Number of day work to be done)
学习改变命运,知 识创造未来
PMC生产计划与物料控制实务
•4.优先率排程要领与演练
例:2007年第一季
•
•一月
•二月
•三月
•产品A
•查库存余额 •
•期初余 额
•减需求 量
•期末余 额
•5000
•一月 •8000 •5000 •3000
•3000
•二月 •3000 •3000
•0
•6000
•三月 •0
= 130-(10+10+12+9+8)
= 130-49=81天
不足天数=113-81=32天
总实际加必工须天考数虑(加加班班(后4h)=/天81)可+4增0=加1天2••81数21>=1•4103天 (计划可行)
学习改变命运,知 识创造未来
PMC生产计划与物料控制实务
•4.优先率排程要领与演练
3.生产计划初排 :
学习改变命运,知 识创造未来
PMC生产计划与物料控制实务
•4.优先率排程要领与演练
•1.计算优先率 :
学习改变命运,知 识创造未来
PMC生产计划与物料控制实务
•4.优先率排程要领与演练
优先率管制表
•产品种 类
•E
•优先顺序 •1
•优先率 •0.62
•物料状况 •20
•B
•2
•0.82
•22
•A
•3
•1.生产计划管理概述
•多种少量生产方式特性剖析
• 项目 •1.标准化
•2.生产计划方 式
•3.生产管制方 式
•4.异常管理方 式
•设备使用 •6.人员调配
•
具体内容
•较困难
•1.紧急订单多
•2.交期短
•3.数量变更频繁
•4.生产变换次数多
•1.作业指示为略图、样品与口头指示
•2.以分散式调配工作
•产能负荷管理方式概要表
•经过产能计算及负荷计划的比较分析后,可从资料中掌握产能与负 荷的差异状况,并决定是否需要调整余力 ,或通过外包、加班、增加
人手等方式来应付订单生产能量,此即产能需求计划之目的。
•项目\判断
•方式1
•方式2
•方式3
•分 析
•产能>负荷
•产能<负荷
•产能=负荷
•状 况 •对 策
•6000 •-6000
学习改变命运,知 识创造未来
PMC生产计划与物料控制实务
•4.优先率排程要领与演练
• 采购前置时间:10天,订单规定的时间3/1-1/1= 42天
• 作业标准工时:6000/110 ≈ 55天
• 此一订单:
• 优先率 =• 42(至发生需要天数×)100%
•
•65(55+10)(工作所需之天数
•4.优先率排程要领与演练
种类
长期生产计划 (1-3年)
主要作用
年度财务预算、固定资产(设备等)和不动产(厂 房等)的投入、预定开发新产品类别及预定淘汰目 前还在生产产品类别、生产布局规划等
中期生产计划 (月计划)
短期生产计划 (周计划)
评价在未来数月里,生产能力、供应商及采购部门 能否对应,各部门人员是否不足(或富余)
对最终产品制定生产指令,既要确保准时出货给客 户,又要产品库存量最小化。同时为其它车间(生 产最终产品以外)、仓库、采购等部门提供制定生 产指令、交货指令的参考依据
学习改变命运,知 识创造未来
PMC生产计划与物料控制实务
2.制造业生产计划的模式
• 制造业生产排程方法简介:
•
• ①.甘特图法; • ②.PSI生产—发货—库存; • ③.瓶颈排程法; • ④.反向排程法; • ⑤.滚动排程法; • ⑥.优先率法。
学习改变命运,知 识创造未来
PMC生产计划与物料控制实务
PMC生产计划与物料控制实务
•1.生产计划管理概述
•生管(PMC)的工作职 责:
•1).协调销售计划; •2).分析产能负荷; •3).制定生产计划; •4).督促物料进度; •5).生产数据统计; •6).控制生产进度; •7).生产异常协调。
•生管(PMC)的工作目 标:
•1).客户订单如期出货; •2).生产物料及时上线; •3).优化的流程任务安排, •4).最低库存成本。
• 学员自检:如何计算生产节拍?
学习改变命运,知 识创造未来
PMC生产计划与物料控制实务
•3.产能负荷分析
•生产能力的预估
•■生产能力分析五方面
•规格和流程
•材料前置时间
学习改变命运,知 识创造未来
•设备
•场地
•总标准时间/ •制程标准时间 •(人力负荷能力)
PMC生产计划与物料控制实务
•3.产能负荷分析
PMC生产计划与物料控制实务
•4.优先率排程要领与演练
■生产计划排程的优先五规则
•先 •到 •加工时间最短(能缩短平均滞留时间)
•先 •用
•交期宽裕最小(使延迟最小)
•︹ •最
•后续加工时间最长(减少延误)
•常 •用
•后续作业数最多(减少制程干扰)
•︺
学习改变命运,知 识创造未来
PMC生产计划与物料控制实务
•3.产能负荷调整困难
•4.进度掌握较困难
•1.制品库存吸收比较难
•2.短交期造成零组件之大量库存
•3.加班多,支援需求亦多
•4.外包频繁
•5.生产异常多,生产管理较难
•以泛用设备为主
•以多能工为主
PMC生产计划与物料控制实务
•1.生产计划管理概述
•通过生产分析制定多种少量 •订货式生产管理对策
•
•
• 学员分组研讨:PMC的胜任素质模型?
学习改变命运,知 识创造未来
PMC生产计划与物料控制实务
2.制造业生产计划的模式
1.计划性生产模式:
①.少样多量,专用制程设备 ②.规格、式样、交期,大部分由生
产者决定 ③.先产后销,预测比较准确 ④.专案工程,高科技产品居多
•2.订单性生产模式:
•①.多种少量,泛用设备 •②.客户决定规格、式样、交期多 •③.先销后产,预测不易 •④.消费产品,工业用产品居多
PMC生产计划与物料控制实务
壹.少量多样的生产计划与管制
1、生产计划概述与模式 2、产能负荷分析与平衡 3、优先率生产计划要领与演练 4、滚动生产计划要领与演练 5、急单插单的处理技巧 6、少量多样化的解决对策
学习改变命运,知 识创造未来
PMC生产计划与物料控制实务
学习改变命运,知 识创造未来
•由于订货的产品种类多,且数量大 小不一,其新开发的产品多,工作经 常会有变化,亦即生产工作转换次 数增多是其特性,因此缩短生产准 备时间是其管理重点
要项
•1 •订货生产形态
•2 •生产变更方式
•3 •多种少量生产
•4 •交期管理
•5 •产销配合方式
•6 •事务管理
学习改变命运,知 识创造未来
•
生产分析
•1 •产品分析
•2 •管理分析
•1 •变更次数分析
•2 •变更时间分析
•1 •产品ABC分析 •2 •模组化分析 •3 •零组件共用性分析 •1 •生产周程分析 •2 •前置分析 •3 •自制外包分析 •1 •产能负荷分析
•3.产能负荷分析
• 产能负荷分析的步骤:
• ①.依产品别、制程别计算出负荷。 • ②.依机械(人员)别、制程别作负荷合计。 • ③.进行负荷、能力的比较、分析。 • ④.对负荷、能力进行调整,使之一致。
• 产能负荷分析的关键:
• ①.瓶颈工序决定最大产能。 • ②.市场节拍、固有节拍和生产节拍平衡。
•4.优先率排程要领与演练
• 扔给大家的问题:
• 同时接到10个订单,您依据什么原则排订单?
• 1).交货期先后原则; • 2).客户分类原则; • 3).产能平衡原则; • 4).工艺流程原则。
• 这四个排订单的原则难道是最好的吗?
学习改变命运,知 识创造未来
PMC生产计划与物料控制实务
•4.优先率排程要领与演练
•0.9
•仓存500PCS.余22
•C
•4
•1.0
•24
•D
•5
•1.25
•21
学习改变命运,知 识创造未来
PMC生产计划与物料控制实务
•4.优先率排程要领与演练
2.初步分析:
总计至出货天数=28+15+20+22+28=113天
总工作天数=31+18+20+16+45=130天
总实际加工天数 = 总工作天数-总采购天数