铸造工艺毕业设计
压铸工艺与模具设计毕业论文

压铸工艺与模具设计毕业论文一、选题的依据及意义本课题来源于江铃汽车集团公司骨干企业,江铃汽车集团公司车厢饰件厂的全资子公司,江铃有色金属压铸厂。
该公司成立于2002年5月。
工厂总投入资金为四千万元人民币,自建立起就本着高起点,现代化的原则,工厂以生产铝合金压铸件及其加工为主,已为江铃汽车、奇瑞汽车及中华汽车配套生产变速器及发动机零部件,产品已出口欧洲,工厂还可生产路灯灯罩、电梯踏板、电机壳体等其它铝合金压铸件。
产品图如下所示:压力铸造是近代金属加工工艺中发展较快的一种少无切削的特种铸造方法。
它是将熔融金属在高压高速下充填铸型,并在高压下结晶凝固形成铸件的过程。
高压高速是压力铸造的主要特征。
常用的压力为数十兆帕,填充速度(浇口速度)约为16~80米/秒,金属液填充模具型腔的时间极短,约为0.01~0.2秒。
压力铸造特点如下:一、优点:(1)可以制造形状复杂、轮廓清晰、薄壁深腔的金属零件。
(2)压铸件的尺寸精度较高,可达IT11~IT13级,有时可达IT9级,表面粗糙度达Ra0.8~3.2um,有时达Ra0.4um,互换性好。
(3)材料利用率高。
(4)可以将其他材料的嵌件直接嵌铸在压铸件上。
(5)压铸件组织致密,具有较高的强度和硬度。
(6)可以实现自动化生产。
二、缺点:(1)由于高速充填,快速冷却,形腔中气体来不及排出,致使压铸件常有气孔及氧化夹杂物存在,从而降低了压铸件质量。
(2)压铸机和压铸模质量昂贵,不适合小批量生产。
(3)压铸件尺寸受到限制。
(4)压铸合金种类受到限制。
在此之上还发展出多种特殊压铸工艺,以解决压铸件的气孔和疏松问题。
迄今为止主要有真空压铸、充氧压铸、精速密压铸、半固态压铸等。
由于用这种方法生产产品具有生产效率高,工序简单,铸件公差等级较高,表面粗糙度好,机械强度大,可以省去大量的机械加工工序和设备,节约原材料等优点,且其缺点可以通过特殊压铸得到有效的克服,所以现已成为我国铸造业中的一个重要组成部分。
熔模铸造毕业设计

熔模铸造毕业设计熔模铸造毕业设计熔模铸造是一种先进的金属铸造技术,也是我毕业设计的主题。
在这篇文章中,我将探讨熔模铸造的原理、应用以及我在毕业设计中的研究内容。
一、熔模铸造的原理熔模铸造是一种通过制作熔模来铸造复杂形状的金属零件的方法。
它的原理是先制作出一个与所需零件形状相同的模具,然后通过加热模具,使模具内的熔融金属填充进去,并冷却凝固,最后获得所需的零件。
熔模铸造的核心在于熔模的制作。
一般来说,熔模可以使用多种材料制作,如石膏、陶瓷、蜡等。
其中,蜡模是最常用的材料,因为它具有良好的可塑性和热稳定性。
通过制作蜡模,可以实现复杂形状的零件铸造。
二、熔模铸造的应用熔模铸造在工业生产中有广泛的应用。
它可以用于制造各种复杂形状的零件,如汽车发动机缸体、航空发动机叶片等。
相比于其他铸造方法,熔模铸造具有以下优势:1. 高精度:熔模铸造可以实现高精度零件的制造,因为模具的制作和熔模的填充过程可以控制得很精确。
2. 节约材料:相比于其他铸造方法,熔模铸造可以节约材料。
因为熔模铸造是通过填充熔融金属来制造零件,不需要额外的材料。
3. 良好的表面质量:熔模铸造可以获得良好的表面质量,因为熔模的表面光滑,可以直接影响到最终零件的表面质量。
三、我的毕业设计内容在我的毕业设计中,我选择了熔模铸造技术,并以某种特定的零件为研究对象。
我的研究内容主要包括以下几个方面:1. 熔模材料的选择:在研究中,我将对不同材料的熔模进行比较,包括蜡模、陶瓷模等。
通过对比它们的性能和成本,选择最适合的熔模材料。
2. 熔模制作工艺的优化:在研究中,我将对熔模的制作工艺进行优化,以提高熔模的质量和生产效率。
我将尝试不同的工艺参数,如温度、压力等,以找到最佳的制作工艺。
3. 铸造过程的模拟与分析:在研究中,我将使用计算机模拟软件对熔模铸造过程进行模拟与分析。
通过模拟,我可以预测铸造过程中可能出现的问题,如气孔、缩松等,并提前采取相应的措施。
4. 零件性能的测试与评估:在研究中,我将对熔模铸造获得的零件进行性能测试与评估。
铸造毕业设计

铸造毕业设计铸造毕业设计毕业设计的题目为“某铝合金零件的铸造工艺优化”。
该零件是一种重要的结构部件,需要具有高强度和优异的耐腐蚀性能。
目前,该零件的铸造工艺存在一些问题,例如出现缺陷率较高、机械性能不稳定等。
该毕业设计旨在通过对铸造工艺的优化,解决上述问题,提高零件的质量和性能。
首先,我们将对原有的铸造工艺进行分析和评估。
通过对原有工艺参数的收集和整理,以及相关文献的回顾和研究,我们将得到关于原有铸造工艺的全面了解。
然后,我们将使用实验和仿真等手段,对原有工艺进行性能测试和缺陷分析。
这些测试可以包括金相显微镜观察、拉伸试验、硬度测试等。
在分析和评估的基础上,我们将制定一套铸造工艺优化方案。
这个方案将包括选择合适的铸造材料、优化铸造工艺参数、设计合理的浇注系统和冷却系统等。
我们将使用实验和数值模拟等方法,对不同方案进行比较和评估。
最终,我们将选取最优方案,并进行试验验证。
根据选取的最优方案,我们将进行具体的工艺优化和工艺参数的优化。
优化的过程中,我们将充分考虑原材料的性能和加工工艺的可行性。
我们可以采用多种方法进行优化,例如改变浇注温度和速度、调整合金成分、设计合理的冷却方法等。
通过实验和模拟,我们将评估不同参数对零件性能的影响,找到最佳的工艺参数组合。
最后,我们将对优化后的铸造工艺进行验证。
通过制造一批优化后的零件,并对其进行全面的性能测试和缺陷分析,我们将评估新工艺的效果。
这些测试可以包括金相显微镜观察、拉伸试验、硬度测试等。
同时,我们还可以对新工艺进行成本分析和可行性评估,为企业提供参考。
通过这个毕业设计,我将掌握铸造工艺优化的方法和技能,提高自己的实践能力和工程素质。
同时,我也将为相关企业的研发和技术创新提供有益的建议和支持。
铸造工艺毕业设计说明书

轮毂的铸造工艺及其热芯盒模具设计摘要随着社会的发展,机动车辆在生产和生活中的越来越广泛。
缸盖是机动车辆中的重要部件,其壳体的结构及加工精度直接影响轮毂的正常工作,因此研究轮毂的加工方法和工艺的编制是十分必要和有意义的。
本设计是对前轮毂零件进行铸造毛坯工艺设计。
根据零件的使用条件、结构特点、生产批量,结合工厂现有设备等进行铸造工艺分析,确定了铸造方法、造型及造芯方法、凝固原则及浇注位置、分型面、砂箱中铸件数量、砂型数量等,完成了砂芯、浇注系统、冒口及冷铁、相关工装设备等设计。
本设计采用壳芯盒法制芯,根据芯子的形状及重量选用763射芯机进行射芯,采用酚醛树脂砂作为制芯材料。
接着对壳芯盒本体进行设计,芯盒本体的设计主要包括芯盒的结构及分盒面的选择,射砂口的设计,芯盒材料的选择,芯盒中砂芯的数目,排气装置的设计以及芯盒顶出机构的设计。
关键字:砂型铸造,工艺分析,工艺设计,壳芯工装设计The Casting Technology and Hot Core BoxMold Design of HubABSTRACTAlong with social development, motor vehicle used in production and life is increasingly wide. Hub is an important vehicle component and its interior structure and processing precision directly affect the hub normal work. Study hub cast processing methods and techniques of preparation is necessary and meaningful.This design is the casting technology design for front hub in vehicle. According to the application conditions, structural features, production batch and existing equipment, it determines the method of casting, modeling, core making, solidification principles and pouring position, parting surface, the quantity of casting and mold etc. It completes the design of sand core, pouring system, riser, chill and related equipment etc.This design uses the shell core box making core. According to the shape and weight it choose 763 shoot core machine shoot core and use phenolic resin sand as the core making material. Then design the shell core box body, the core box body design mainly includes the core box structure and box surface selection, sand jetting port core box design, choice of materials, core box of sand core in number, exhaust design and installation of the core box lifting mechanism design.KEY WORDS:sand casting,technology analysis,technology design,Shell core fixture design目录前言 (1)第一章铸造工艺设计 (2)§1.1 零件概述 (2)§1.1.1 零件信息 (2)§1.1.2 技术要求 (2)§1.2 铸造工艺方案的确定 (3)§1.2.1 造型、造芯方法及铸型种类的确定 (3)§1.2.2 浇注位置和分型面的确定 (3)§1.2.3 砂箱中铸件数目的确定 (6)§1.3 工艺参数的选择 (6)§1.3.1 铸造收缩率 (6)§1.3.2 机械加工余量、铸件的尺寸和重量偏差 (7)§1.3.3 拔模斜度的确定 (8)§1.3.4 铸造圆角的确定 (8)§1.3.5 最小铸出口及槽 (8)§1.4 浇注系统的设计 (8)§1.4.1 浇注系统的概述 (8)§1.4.2 浇注系统类型的选择 (9)§1.4.3 浇注系统的设计与计算 (10)§1.4.4 出气孔的设计 (13)§1.5 砂芯的设计 (13)§1.5.1 砂芯的概述 (13)§1.5.2 砂芯数量的确定 (13)§1.5.3 芯头的设计 (13)§1.5.4 壳芯的制备 (14)§1.6 冒口及冷铁的设计 (15)§1.6.1 冒口的设计 (15)§1.6.2 冷铁的设计 (15)第二章铸造工艺装备设计 (16)§2.1 模板 (16)§2.1.1 模样的设计 (16)§2.1.2 模底板的设计 (16)§2.2 壳芯工装设计 (17)§2.2.1 壳芯的概述 (17)§2.2.2 壳芯工艺 (17)§2.2.3 壳芯盒的材料 (18)§2.2.4 壳芯工装设计 (19)结论 (23)参考文献 (24)致谢 (25)前言近年来,能源,环境和安全问题受到普遍关注,汽车行业尤为突出。
高锰钢锤头铸造工艺及工装设计毕业设计答辩PPT
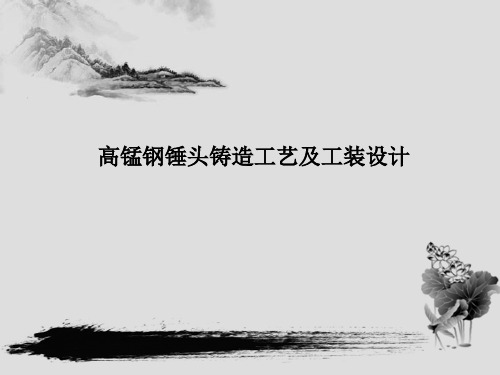
壹 简介 贰 铸造工艺方案确定 叁 工艺设计 肆 华铸CAE模拟分析 伍 铸造工艺装备设计 陆 热处理工艺
一、简 介
高锰钢锤头是矿山、水泥等行业破碎物 料的易耗件,也是锤式破碎机核心零件之 一,锤头在破碎机高速运转时直接打碎物 料,工作环境恶劣,质量要求高,尤其是 锤头头部需要较高的耐磨性和抗冲击性。 其结构如下图所示。
下模样图
下模板图
3.热芯盒的设计
材料:HT200
芯盒内腔尺寸按公式: :Ab=(Ac±At)(1+εt) 计算
4.砂箱的设计
采用整铸式机器造型用 砂箱,材质为HT200
采用Z1410A顶箱 震压造型机,其 最大内框尺寸为 1200×800×350
六、热处理工艺
水韧处理定义:将钢加热到Acm以上保温一 段时间,使铸态组织中的碳化物溶解、共 析类型组织进行奥氏体化,铸态组织全部 消除,得到化学成分均匀的单相奥氏体组 织,然后快速冷却得到过冷的奥氏体固溶 体组织。
1.加热温度
对于不含其他合金元素的常规成分的高锰 钢的水韧处理温度以1050℃~1100℃最为 合适。
2.保温时间
适宜的保温时间与铸件壁厚有关,经 查阅资料得,保温时间取1~2h最好。
3.冷却
采用水淬冷却,并且时间要快,因为 冷却速度不足会在奥氏体中析出碳化物。
谢 谢!
二、铸造工艺方案确定
铸造工艺方案的确定主要有以下内容: 1.工艺性分析 2.造型材料的选择 3.造型、造芯方法的选择 4.分型面和浇注位置的确定
分型面的选择有两种方案,如图所示:
三、工艺设计
主要内容: 1.工艺参数的确定
机械加工余量:由于高锰钢硬度大,难于加工,因此不设定 加工余量。 铸造收缩率:由于高锰钢线收缩较大,常规的Mn13的线收缩 率为2.4%~3.0%,本次设计取3.0%。
低压铸造工艺设计毕业论文
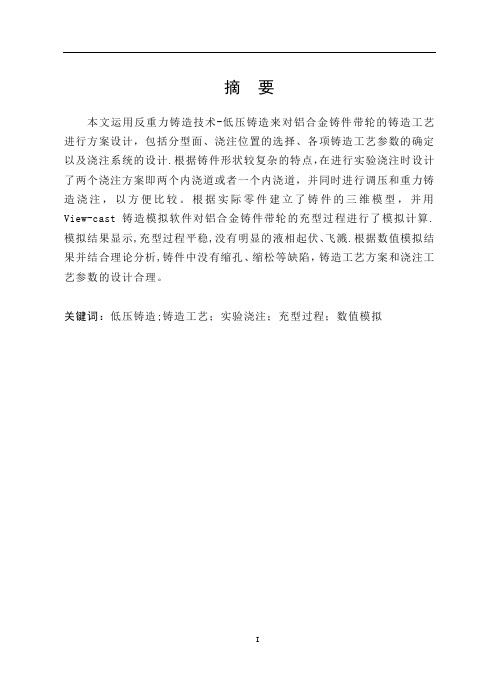
摘要本文运用反重力铸造技术-低压铸造来对铝合金铸件带轮的铸造工艺进行方案设计,包括分型面、浇注位置的选择、各项铸造工艺参数的确定以及浇注系统的设计.根据铸件形状较复杂的特点,在进行实验浇注时设计了两个浇注方案即两个内浇道或者一个内浇道,并同时进行调压和重力铸造浇注,以方便比较。
根据实际零件建立了铸件的三维模型,并用View-cast铸造模拟软件对铝合金铸件带轮的充型过程进行了模拟计算.模拟结果显示,充型过程平稳,没有明显的液相起伏、飞溅.根据数值模拟结果并结合理论分析,铸件中没有缩孔、缩松等缺陷,铸造工艺方案和浇注工艺参数的设计合理。
关键词:低压铸造;铸造工艺;实验浇注;充型过程;数值模拟AbstractIn this paper,anti—gravity casting technology,low pressure casting technology was used to complete the design of the casting of an aluminum alloy casting wheel,which include choice of Sub-surface and casting position,determining all of the parameters of the casting process,and the design of the casting system。
For the complex shape of the casting,when conducting experiments was designed to use two runners and one ingate for casting in one time, and at the same time,surge and gravity casting was used to make it easier to compare. For sand shell moulding, the mode of same time freezing was generally used. Build the Three-dimensional model of the casting, then simulate and calculate the filling process of casting。
迷宫圈铸造工艺设计

毕业论文毕业设计论文设计(论文)题目:迷宫圈铸造工艺及工装设计下达日期:2007 年 4 月28 日开始日期:2007 年 4 月28 日完成日期:2007 年 6 月8 日指导教师:韩小峰学生专业:材料成型与控制技术班级:材料0402班学生姓名:刘雄飞教研室主任:材料工程系附件二陕西工业职业技术学院毕业设计(论文)任务书一、设计(论文)内容及要求:(一)设计(论文)内容1. 撰写铸造技术发展现状的研究文章;2. 维美德西安造纸机械有限公司实习;3. 编制铸件(附零件图)铸造工艺规程,绘制铸造工艺图,填写铸造工艺过程卡片;4. 绘制铸件图和铸型装配图;5. 设计铸造工艺装备,绘制模样、模板、砂箱和芯盒等设计图;6. 撰写设计说明书(论文)。
(二)要求1.通过企业实习,熟悉铸造工艺过程,结合生产实际完成本次设计任务;2. 工程图用AutoCAD软件绘制并打印;3. 说明书(论文)按照学院统一格式,使用word文档并打印。
4. 提交资料包括:(1)毕业设计任务书;(2)铸造技术发展现状的研究文章;(3)“四图一卡”,即绘制铸造工艺图;铸件图;铸型装配图;模样、模板、砂箱和芯盒等铸造工装图;(4)设计说明书(论文)。
所有提交的资料包括打印文件和电子文件。
二、技术指标:1.生产类型:大批大量生产2.生产及质量要求:满足产品图纸的各项技术要求;工艺出品率较高,废品率5%以下;生产效率高;对工人技术水平要求较低,操作简便。
3.生产工艺要求:树脂砂型铸造;机械化造型;所用工装自行设计;冲天炉及中频感应电炉熔炼;生产的原材料均经过检验,符合材料质量保证单要求。
4.技术水平要求:尽量采用先进技术,创新项目应符合国家环保及安全生产要求。
三、主要参考资料:[1] 曹瑜强.铸造工艺及设备.北京:机械工业出版社,2005年7月.[2]刘喜俊.铸造工艺学.北京:机械工业出版社,1999年10月.[3]丁根宝.铸造生产基础.北京:机械工业出版社,1994年10月.[4] 王晓江.铸造合金及其熔炼.北京:机械工业出版社,1999年7月.[5] 中国机械工程学会铸造分会编.铸造手册.北京:机械工业出版社,2003年10月.陕西工业职业技术学院毕业设计(论文)任务书摘要本文是迷宫圈铸造工艺流程,该铸件是西安维美德生产造纸机上一个附属部件,要求有一定的机械强度,没有特殊的技术要求,根据迷宫圈的产量和生产条件,选用呋喃树脂自硬砂造型、造芯,其工艺流程包括:铸造工艺设计、金属熔炼、工装设计。
熔模铸造毕业设计说明书
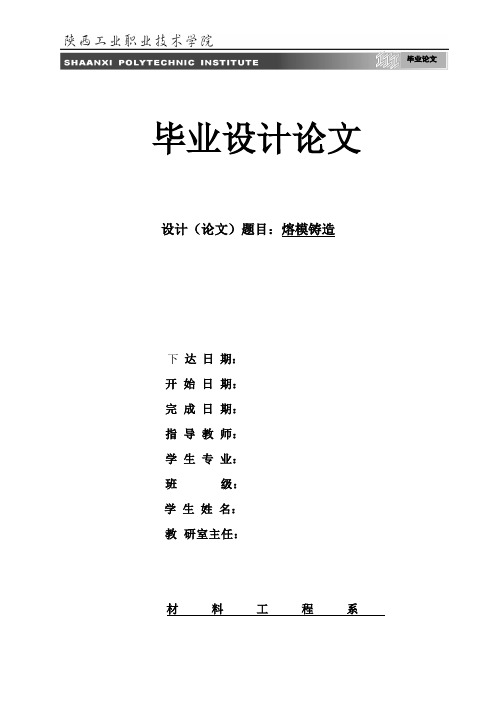
毕业论文毕业设计论文设计(论文)题目:熔模铸造下达日期:开始日期:完成日期:指导教师:学生专业:班级:学生姓名:教研室主任:材料工程系陕西工业职业技术学院毕业设计(论文)任务书一、设计(论文)内容及要求:(一)设计(论文)内容1. 撰写熔模技术发展现状的研究文章;2. 编制铸件(附零件图)铸造工艺规程,绘制铸造工艺图,填写铸造工艺过程卡片;3. 绘制铸件图和总装图;4. 设计熔模压型模具,绘制模具零件图;5. 撰写设计说明书(论文)。
(二)要求1.通过理论学习,熟悉熔模工艺过程,结合生产实际完成本次设计任务;2. 工程图用AutoCAD软件绘制并打印;3. 说明书(论文)按照学院统一格式,使用word文档并打印。
4. 提交资料包括:(1)毕业设计任务书;(2)熔模铸造技术发展现状的研究文章;(3)“四图一卡”,即绘制铸造工艺图;铸件图;零件图;铸型装配图;铸造工艺卡;(4)设计说明书(论文);所有提交的资料包括打印文件和电子文件。
二、技术指标:1.生产类型:大批大量生产2.生产及质量要求:满足产品图纸的各项技术要求;工艺出品率较高,废品率5%以下;生产效率高;对工人技术水平要求较低,操作简便。
3.生产工艺要求:熔模铸造;所用熔模模具自行设计;4.技术水平要求:尽量采用先进技术,创新项目应符合国家环保及安全生产要求。
陕西工业职业技术学院毕业设计(论文)任务书进程计划表摘要本设计是通过熔模铸造的方法来铸造管接头,先分析铸件,进行工艺设计,确定了主要参数,进行压型设计,绘制出铸件工艺图,进行熔模制造-型壳制造-脱蜡焙烧-熔炼浇注-后处理分析,结合具体零件,通过具体分析,最后有针对性的制定出材料为锡青铜的管接头熔模铸造工艺方案。
根据现实生产的应用,表明:熔模铸造适用于实际生产中管接头的铸造。
关键词:熔模铸造,锡青铜,工艺流程ABSTRACTThis design is through investment casting methods to cast pipe joints, first analysis of castings, for process design, to determine the main parameters for pressure-type design, the casting process to map out plans to carry out melt-mold making - Shell Manufacturing - Dewaxing roasting - Melting Pouring - post-processing analysis of specific parts, through a specific analysis, and finally to develop targeted materials bronze fittings of Investment Casting Process.Applications based on the realities of production, indicating that: the application of investment casting in the actual production of the control valve body casting.Key word:Melt mold casting, gun metal, technical process目录毕业设计任务书中文摘要英文摘要一、概述 (1)1、定义 (1)2、熔模铸造的特点 (1)3、发展历史 (2)4、应用范围 (2)二、熔模工艺设计 (4)1、零件图 (4)2、铸件结构工艺性分析 (4)3、确定工艺方案和工艺参数 (5)4、浇注系统 (7)5、绘制铸造工艺图 (10)三、压型设计 (11)1、装配图 (11)2、压型分类 (11)3、分型面选择 (12)4、型体设计 (13)5、压型排气 (16)6、压型冷却 (17)7、压型工作图设计 (17)8、注蜡孔的设计 (19)四、熔模的制造 (20)1、熔模 (20)2、模料的选取和配制 (20)3、制熔模 (21)4、制模组 (23)五、型壳的制造 (26)1、型壳服役性能的要求 (26)2、制造型壳的耐火材料及黏结剂 (26)3、制造型壳用涂料及配制 (27)4、制壳工艺 (31)六、脱蜡与焙烧 (34)1、脱蜡 (34)2、焙烧 (35)七、熔炼与浇注 (36)1、材料的选择 (36)2、选择炉型 (37)3、熔炼准备 (38)4、配料 (40)5、熔炼工艺 (42)八、铸件的后处理 (44)1、型壳的清理 (44)2、切割浇冒口 (46)参考文献 (47)致谢 (48)一、概述1、定义熔模铸造又称“失蜡铸造”,通常是在可熔模样的表面涂上数层耐火材料,待其硬化干燥后,加热将其中模样熔去,而获得具有与模样形状相应空腔的型壳,再经过焙烧,然后在型壳温度很高的情况下进行浇注,而获得铸件的一种方法,由于获得的铸件具有较高的尺寸精度和表面光洁度,故又称“熔模精密铸造”。
大学本科机械专业泵盖铸造工艺毕业设计
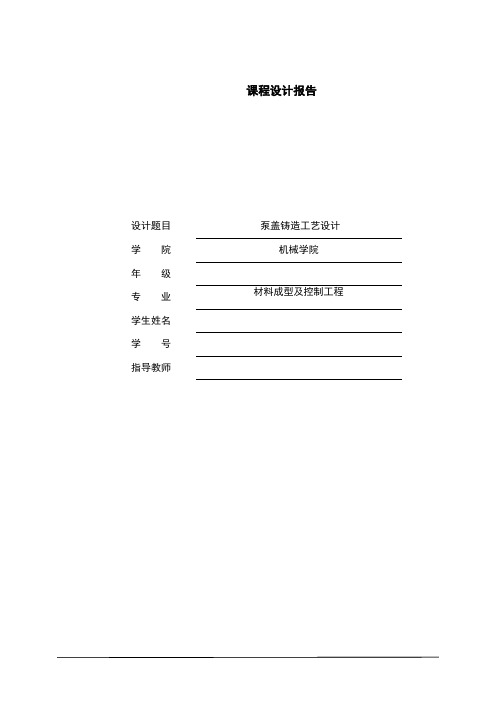
课程设计报告设计题目泵盖铸造工艺设计学院机械学院年级材料成型及控制工程专业学生姓名学号指导教师目录1 设计任务 (1)1.1设计任务 (1)1.2 设计的技术要求12 铸造工艺方案的确定 (2)2.1 零件结构分析 (2)2.2 分型面的确定 (3)2.3.加工余量和铸造圆角 4 2.4工艺参数的确定 5 2.5.1工艺补正量 6 2.5.2分型负数 6 2.5.3砂芯设计 62.5.4铸件毛胚质量 73. 浇注系统(包括冒口)的选择 (7)3.1浇注系统和冒口7 4铸造工艺图 (11)5 铸造工艺卡 (13)6 参考文献 (14)1 设计任务1 1设计任务泵盖铸造工艺设计图11 2设计的技术要求设计应达到的技术要求:实际主要用于零件的外部,起密封,阻挡灰尘的作用,故其在机器中只是起辅助作用,对机器的稳定运行影响不是很大,其在具体加工的时候,精度要求也不是很高,加工起来也十分容易。
依据图纸要满足下列要求:1、材质灰铁150、未注铸造圆角均为R3;2、铸件表面不得有沙眼、缩孔等缺陷;3、泵盖底部Φ132表面Ra为3.2,Φ100表面Ra为6.3,二者之间台阶Ra1.6。
Φ14中心孔内表面Ra为1.6,Φ25中心孔内表面Ra为6.3,其余为Ra12.5;4、两个圆柱孔分别为中心大圆柱Φ25H9基本尺寸为Φ25mm,公差带为H8的孔;中心小圆柱Φ14H92铸造工艺方案的确定2.1零件结构分析名称:泵盖材料: HT150生产批量:大批量生产图2泵盖立体图3泵盖零件2.2分型面的确定在生产中考虑选择分型面时应注意以下原则:1、应使铸件全部或大部置于同一半型内,以保证铸件精度。
如果做不到上述要求,必须尽可能把铸件的加工面和加工基准放在同一半型内。
2、应尽量减少分型面的数目。
分型面越少,铸件精度容易保证且砂箱数目少减少工人劳动量。
3件精度。
4填砂、紧实、起模、下芯都不方便,劳动强度大。
56就本次的泵盖而言:将铸件大部分---重要部分(泵盖圆盘底部)置于下部且分型面为最大截面。
HT150阀体的铸造工艺设计-毕业论文

---文档均为word文档,下载后可直接编辑使用亦可打印--- 摘要本文通过对灰铸铁阀体的铸造工艺方案的设计,包括浇注位置、分型面的选择,砂芯和各项铸造工艺参数的确定以及浇注系统、砂箱、芯盒、模板的设计。
根据铸件小的特点,分为一箱四件,并采用封闭式的浇注系统的方法。
通过对凝固过程的温度场和铸造缺陷的分析,对工艺进行改进,然后绘制屏分析铸造工艺图与合箱图,将数据具体化,有效地调整工艺参数,减少可能出现的铸造缺降,保证工艺的可靠性。
最后设汁出合理的铸造工艺方案。
关键词:阀体;铸造工艺设计;浇注系统;铸造工艺图.AbstractIn this paper, the casting process design of gray iron valve cover, including casting location, parting surface selection, sand core and casting process parameters determination and casting system, sand box, core box, template design. According to the characteristics of small castings, it is divided into four parts in one box, and the method of closed casting system is adopted. By analyzing the temperature field of solidification process and casting defects, the process was improved, and then the screen was drawn to analyze the casting process diagram and box diagram, and the data was materialized to effectively adjust the process parameters, reduce the possible casting loss and ensure the reliability of the process. Finally, a reasonable casting process plan was established.Key words: valve cover; Casting process design; Casting system; Casting process drawing.目录一绪论 (6)1.1概述 (7)1.2铸造行业的历史 (8)1.3国内铸造行业的现状 (8)1.4铸造工艺(技术)发展展望 (9)1.5本课题的研究内容 (10)二铸件结构的工艺性 (10)2.1零件的设计 (10)2.2铸造工艺对铸件结构的要求 (12)三铸造工艺方案的设计 (13)3.1造型和造芯方法的选择 (13)3.2浇注位置的确定 (14)3.3分型面的选择 (15)3.4砂箱中铸件的数量及排列方式 (16)四铸造工艺参数及砂芯的设计 (16)4.1铸造工艺参数的确定 (16)4.2砂芯的设计 (21)五浇注系统的设计 (22)5.1浇注系统类型的选择 (22)5.2浇注系统尺寸的确定 (22)5.3直浇道的设计 (25)5.4横浇道的设计 (25)5.5内浇道的设计 (26)5.6浇口杯的设计 (27)5.7冒口的设计 (27)5.8冷铁的设计 (27)六铸造工艺装备设计 (27)6.1模样的设计 (27)6.2模板的设计 (28)6.3芯盒的设计 (31)6.4砂箱的设计 (32)七铸件的落砂、清理及后处理 (35)7.1铸件的冷却 (35)7.2落砂 (35)7.3表面清理 (35)7.4铸件的矫形 (35)7.5铸件的缺陷修补 (36)7.6铸件的内应力消除 (36)结论与展望 (36)参考文献 (38)小结引言重力铸造是指金属液在地球重力作用下注入铸型的工艺,也称浇铸。
砂型铸造模具毕业设计
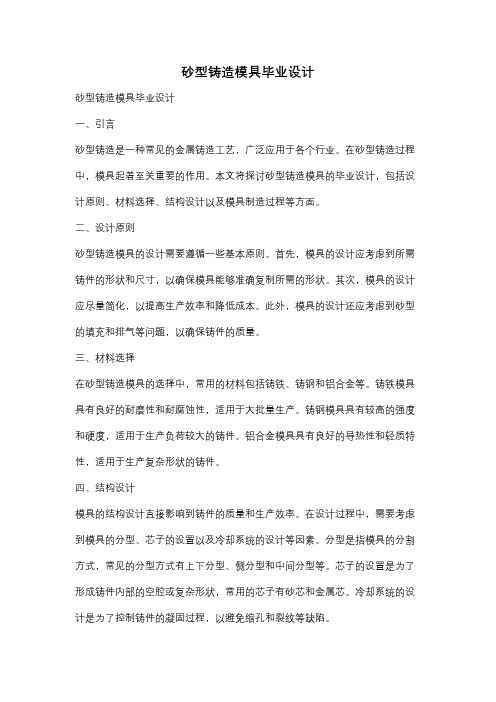
砂型铸造模具毕业设计砂型铸造模具毕业设计一、引言砂型铸造是一种常见的金属铸造工艺,广泛应用于各个行业。
在砂型铸造过程中,模具起着至关重要的作用。
本文将探讨砂型铸造模具的毕业设计,包括设计原则、材料选择、结构设计以及模具制造过程等方面。
二、设计原则砂型铸造模具的设计需要遵循一些基本原则。
首先,模具的设计应考虑到所需铸件的形状和尺寸,以确保模具能够准确复制所需的形状。
其次,模具的设计应尽量简化,以提高生产效率和降低成本。
此外,模具的设计还应考虑到砂型的填充和排气等问题,以确保铸件的质量。
三、材料选择在砂型铸造模具的选择中,常用的材料包括铸铁、铸钢和铝合金等。
铸铁模具具有良好的耐磨性和耐腐蚀性,适用于大批量生产。
铸钢模具具有较高的强度和硬度,适用于生产负荷较大的铸件。
铝合金模具具有良好的导热性和轻质特性,适用于生产复杂形状的铸件。
四、结构设计模具的结构设计直接影响到铸件的质量和生产效率。
在设计过程中,需要考虑到模具的分型、芯子的设置以及冷却系统的设计等因素。
分型是指模具的分割方式,常见的分型方式有上下分型、侧分型和中间分型等。
芯子的设置是为了形成铸件内部的空腔或复杂形状,常用的芯子有砂芯和金属芯。
冷却系统的设计是为了控制铸件的凝固过程,以避免缩孔和裂纹等缺陷。
五、模具制造过程模具的制造过程包括模具设计、模具加工和模具调试等环节。
在模具设计中,需要使用CAD软件进行三维建模,并根据设计原则和结构设计进行模具设计。
在模具加工过程中,需要使用数控机床进行模具零件的加工,然后进行装配和调试。
模具调试是为了验证模具的合理性和准确性,以确保模具能够满足生产要求。
六、模具使用与维护模具的使用和维护对于保证铸件质量和提高模具寿命至关重要。
在使用过程中,需要注意模具的正确安装和调试,以确保模具能够正常工作。
同时,还需要定期对模具进行清洁和润滑,以防止模具表面的氧化和磨损。
对于长期不使用的模具,还需要进行防腐处理,以延长模具的使用寿命。
QT500—7球墨铸铁熔炼工艺设计毕业论文

QT500-7球墨铸铁熔炼工艺设计摘要合金熔炼是铸造生产中的重要环节。
当前,铸造生产中的废品约有50% 与熔炼有关,熔炼铁液的成本约占铸件成本的25%~30% ,合金熔炼对铸件质量和成本有着很大的影响。
我们应该针对不同的铸件材质及技术要求选择不同的熔炼方法。
本设计题目为QT500-7球墨铸铁熔炼工艺设计,体现了球墨铸铁熔炼的设计要求、内容及方向,有一定的设计意义。
通过对该牌号球墨铸铁的设计,进一步加强了设计者熔炼工艺设计的基础知识,为设计其它牌号铸铁的熔炼做好了铺垫和吸取了更深刻的经验。
本设计运用铸造合金熔炼的基础知识,首先分析了QT500-7球墨铸铁的成分及性能要求,为选取熔炼设备及炉料做好了准备;然后选取熔炼设备,计算炉料的比例用量;最后设定球化、孕育方法,确定浇注温度参数,进行质量检测及分析。
本设计着重点在于使用冲天炉-感应电炉双联熔炼球墨铸铁。
由冲天炉熔化铁液并进行化学成分含量的初步确定;在感应电炉中高温精炼,调整铁液的化学成分至规定的范围;进一步清除非金属夹杂物和降低气体含量;提高铁液温度至符合出炉球化要求;最终球化及孕育处理,出炉检测。
关键词:球墨铸铁双联熔炼球化处理孕育处理QT500-7 Ductile Iron Smelting Process DesignAbstractAlloy melting is an important part in casting production. At present, about 50% of the waste in the foundry production is related to the smelting. The cost of the molten iron is about 25% - 30% of the cost of the casting. We should choose different smelting methods fordifferent casting materials and technical requirements.This design topic is QT500-7 nodular cast iron smelting process design, reflects the design requirements, content and direction of ductile iron smelting, there is a certain design significance. Through the design of this type of ductile iron, further strengthen the designers of the basic knowledge of smelting process design for the design of other grades of cast iron to pave the way and draw a more profound experience.The design and use of casting alloy melting of basic knowledge,the first analysis of the QT500-7 nodular cast iron composition and performance requirements for the selection of smelting equipment and charge ready; then select smelting equipment, calculation burden ratio; finally set the ball, inoculation method, to determine the parameters of casting temperature, quality detection and analysis.This design is focused on the use of cupola induction furnace duplex melting of nodular cast iron. By cupola melting iron liquid and preliminary identification of chemical components; in the induction furnace high temperature refining, adjustment of the liquid metal chemical composition to the specified range; further clear non metallic inclusions and reduce the gas content; improve the temperature of molten metal to meet released the ball of the requirements; and eventually the ball and inoculation treatment, detection of released.Key words: Ductile iron, Tecastiron, Spheroidize, Inoculation treatment目录摘要 IAbstract II1 绪论 11.1球墨铸铁的出现 11.2国内外球墨铸铁的发展 11.3球墨铸铁的应用 21.4熔炼工艺及发展 31.5课题来源及意义 42 熔炼工艺方案的确定 52.1熔炼技术要求及分析 52.1.1技术要求 52.1.2材料性能及分析 52.2工艺方案 63 冲天炉熔炼工艺设计 83.1冲天炉熔炼特性及原理 83.1.1冲天炉熔炼概述 83.1.2冲天炉熔炼的技术要求 83.1.3冲天炉的燃烧过程原理 103.2炉料的计算 133.2.1球墨铸铁原铁液的配比要求 13 3.2.2QT500-7原始资料的确定 133.2.3确定元素增减率及增减后成分 14 3.2.4确定配料比并校核 143.2.5炉料计算 153.3熔炼工艺及参数 163.3.1装炉 163.3.2炉前控制 163.3.3铁液出炉 163.3.4脱硫处理 163.4熔炼过程的化学反应 174电炉熔炼工艺设计 204.1感应电炉的熔炼特点 204.1.1感应电炉构造及工作原理 204.1.2感应电炉熔炼的优缺点及其应用 20 4.2熔炼工艺及参数 214.2.1二次脱硫 214.2.2脱磷处理 214.2.3精炼调整 224.3球化工艺 224.3.1球化剂 224.3.2QT500-7球化剂的选用 244.3.3 QT500-7的球化处理工艺 244.3.4球化剂加入量的确定 264.4孕育工艺 274.4.1孕育剂 274.4.2孕育处理工艺 284.5出液浇注 294.5.1浇注温度对性能的影响 29 4.5.2球铁的浇注温度 295质量检验及分析 305.1质量检测 305.1.1炉前三角试片检验法 30 5.1.2火苗判断法 305.1.3炉前快速金相法 305.1.4炉前光谱分析法 305.2缺陷分析 305.2.1球化不良 315.2.2球化衰退 325.2.3石墨漂浮 326 结论 34致谢 36参考文献 371 绪论铸造是机电装备制造业中铸件生产的工艺过程。
铸造毕业设计

铸造毕业设计铸造毕业设计一、引言铸造是一门古老而重要的制造工艺,它通过将熔化的金属或合金倒入模具中,经过冷却凝固后得到所需的零件或产品。
作为一名铸造专业的毕业生,毕业设计是我们展示自己专业技能和知识的重要机会。
本文将探讨铸造毕业设计的重要性、设计内容和实施过程。
二、重要性1.学术意义毕业设计是对我们在大学学习期间所掌握的理论知识和实践技能的综合运用。
通过设计一个完整的铸造项目,我们可以巩固和运用所学的知识,提高自己的学术水平。
2.职业发展毕业设计是我们进入职业生涯的敲门砖。
通过设计一个切实可行的铸造项目,我们可以展示自己的能力和潜力,吸引潜在雇主的注意,增加就业机会。
三、设计内容1.项目选择在开始毕业设计之前,我们需要选择一个适合的铸造项目。
这个项目应该具有一定的挑战性,能够充分展示我们的技术和创新能力。
同时,项目的规模和复杂度也要与我们的时间和资源相匹配。
2.材料选择铸造过程中,材料的选择对最终产品的质量和性能有重要影响。
我们需要根据项目的要求和所学的材料知识,选择适合的金属或合金。
同时,还需要考虑到材料的可获得性和成本等因素。
3.模具设计模具是铸造过程中的关键环节,它决定了最终产品的形状和尺寸。
我们需要根据项目的要求和所学的模具设计知识,设计出合适的模具。
模具的设计应该考虑到材料的收缩率、浇注系统的设计等因素,以确保最终产品的质量。
4.工艺设计铸造工艺是铸造过程中的核心环节,它决定了最终产品的组织结构和性能。
我们需要根据项目的要求和所学的铸造工艺知识,设计出合适的工艺方案。
工艺的设计应该考虑到金属的熔化温度、浇注温度、冷却速度等因素,以确保最终产品的质量。
四、实施过程1.准备工作在开始实施毕业设计之前,我们需要进行一些准备工作。
这包括收集和整理相关的文献资料,了解和研究已有的铸造技术和工艺,以及准备所需的实验设备和材料等。
2.实验设计在实施毕业设计时,我们需要进行一系列的实验来验证和优化我们的设计方案。
铸造工艺毕业设计

铸造工艺毕业设计【篇一:铸造工艺毕业论文】毕业论文题目浅谈铸造工艺与品质检查姓名所在系别专业班级学号指导教师日期摘要:为了提高铸件的可靠性、适用性;提高产品在市场上的竞争能力,对铸件质量的要求不断提高。
铸件质量的概念也发生了相应的变化,“质量”的含义至少包含两个方面的内容:一是产品质量,即铸件满足用户要求的程度;或按其用途在使用中应取得的功效,这功效是反映铸件结构特征、材质的工作特性和物理力学特性的总和,是评价铸件质量水平和技术水平的基本指标。
二是工程质量,指的是铸制毛坯和铸制零件的生产过程对产品质量的保证程度,即铸件在具体使用条件下的可靠性。
这一指标在相当大的程度上决定于前述的功效指标,还与稳定性、耐用性和工艺性等指标有关。
标准是由国家承认的标准制订单位批准的对各种产品(铸件)规格、材料规格、试验方法、术语定义或推荐的工艺方法的规定。
我国的国家标准是由国家技术监督局批准并颁行的,有关铸件质量的各种标准一经接纳、贯彻与实施,可取得明显的效果和效益。
国际标准是由国际标准化组织批准并颁行的。
我国是国际标准化组织的主要成员国之一,按国家现行的政策,国际标准可以等效地视为国家标准。
关键词:铸件质量;提高铸件品质;稳定性;耐用性目录引言 (3)第一章铸件质量标准 (4)1.1 铸件精度标准 (4)第二章铸件缺陷分类 (6)2.1铸件缺陷 (6)2.2废品与铸件质量 (11)2.3 修补与缺陷防止 (11)第三章铸造过程中的质量控制技术................................. 错误!未定义书签。
3.1影响铸件质量的因素 (12)3.2 技术准备过程的质量控制 (13)3.2.1质量标准的制定 (13)3.2.2铸件设计 (14)3.2.3铸造工艺、工装设计及验证 (15)3.3生产工艺过程的质量控制 (15)3.3.1原材料的质量控制 (15)3.3.2设备及工装的质量控制 (16)3.3.3 工艺过程的质量控制 (16)第四章铸件质量检测技术与缺陷诊断方法 (17)4.1铸件外观质量检测 (17)4.1.1 铸件形状和尺寸检测 (17)4.2 铸件内在质量检测 (17)4.3 铸件质量无损检测技术 (18)结论 ......................................................................... 18 参考文献???????????????????????????????..19 答谢。
压铸模毕业设计-范文

摘要压力铸造是目前成型有色金属铸件的重要成型工艺方法。
压铸的工艺特点是铸件的强度和硬度较高,形状较为复杂且铸件壁较薄,而且生产率极高。
压铸模具是压力铸造生产的关键,压铸模具的质量决定着压铸件的质量和精度,而模具设计直接影响着压铸模具的质量和寿命。
因此,模具设计是模具技术进步的关键,也是模具发展的重要因素。
根据零件的结构和尺寸设计了完整的模具。
设计内容主要包括:浇注系统设计、成型零件设计、抽芯机构设计、推出机构设计以及模体结构设计。
根据铸件的形状特点、零件尺寸及精度,选定了合适的压铸机,通过准确的计算并查阅设计手册,确定了成型零件以及模体的尺寸及精度,在材料的选取及热处理要求上也作出了详细说明,并在结合理论知识的基础上,借助于计算机辅助软件绘制了各部分零件及装配体的立体图和工程图,以保障模具的加工制造。
根据有关资料,采用扁平侧面浇注系统,降低了浇注时金属液对型芯的冲击,确定了铸造工艺参数:铸件加工余量取0.1~0.75mm,收缩率为0.4~0.7﹪,脱模斜度为25′~45′。
模具整体尺寸为900×640×835mm,符合所选压铸机安装空间。
抽芯采用斜滑块机构,拼合形式为两瓣式。
推出机构采用4根端面直径26mm的圆截面推杆,推杆兼复位杆作用。
经计算,推杆受力符合要求。
通过电脑模拟显示,模具能够正常工作,开启灵活。
关键词:压力铸造;压铸模具;锌合金铸件;底盘座AbstractDie-casting molding technology is playing a key role in non-ferrous metal structure forming processes. Die-casting process’s features are the stren gth and hardness of die casting on high, thin-walled castings with complex shape can be cast, and the production is efficient. The die-casting die is the key for the process of die casting, its quality decides the quality and accuracy of castings, and the design of the die-casting die affects its quality and operating life directly. Therefore, designing the die-casting die is the key to technological progress; it is also an important factor in the development of mold.Based mainly on parts of the design integrity of the structure and size, it scheme out the required spare parts. Design elements include: design of gating system, forming part design, core-pulling mechanism design, the ejector design and the mold body structure design. According to the shape of features , parts size and accuracy, the author selected the appropriate die casting machine, through the exactly calculate and consult design handbooks, confirm the size and accuracy of the forming part and mold body structure, it also makes particular instruction on the material selection and the requirements of the heat treatment, with theoretical basis, plotting out pictorial drawing and casting drawing of the parts by using computer software to ensure the manufacture of die-casting die.Based on the datum, use flat side gating system which can reduce pouring molten metal on the impact of cores, it ensure the technological parameter of the mold: the allowance of the casting was 0.1~0.75mm, shrinkage rate was 0.4~0.7﹪, draft angle was 25′~45′. The size of the die-casting mold was 900×640×835mm, which satisfy the space of the die casting machine which is chosen. The core-pulling mechanism of the mold was optional side slider core-pulling mechanism, Introduced organizations selected two push plate. The diameter of the ejector pin with a cylindrical head was 26mm, and was also used as return pin. The stress of the ejector pin was conformance to the requirement by calculate. The simulation by computer shows that the mold works function normally, and it can dexterous and quickly to open.Keywords: die casting; die-casting mold; zinc alloy castings; subbase目录摘要 (I)Abstract (II)第1章绪论 (1)1.1课题意义 (1)1.1.1 压力铸造的特点 (1)1.1.2压铸模具设计的意义 (2)1.2压铸发展历史、现状及趋势 (2)1.2.1压铸的发展历史 (2)1.2.2我国压铸产业的发展 (3)1.2.3压铸产业的发展趋势 (4)1.3毕业设计内容 (5)第2章压铸模具的整体设计 (7)2.1 铸件工艺性分析 (7)2.1.1 铸件立体图及工程图 (7)2.1.2 铸件分型面确定 (8)2.1.3 浇注位置的确定 (8)2.2 压铸成型过程及压铸机选用 (9)2.2.1 卧式冷室压铸机结构 (9)2.2.2 压铸成型过程 (10)2.2.3压铸机型号的选用及其主要参数 (11)2.3 浇注系统设计 (11)2.3.1 带浇注系统铸件立体图 (11)2.3.2 内浇口设计 (12)2.3.3 横浇道设计 (12)2.3.4 直浇道设计 (14)2.3.5 排溢系统设计 (14)2.4 压铸模具的总体结构设计 (15)第3章成型零件及斜滑块结构设计 (18)3.1 成型零件设计概述 (18)3.2浇注系统成型零件设计 (18)3.3 铸件成型零件设计 (20)3.3.1 成型收缩率 (20)3.3.2 脱模斜度 (21)3.3.3 压铸件的加工余量 (21)3.3.4铸件成型尺寸的计算 (21)3.4 成型零件装配图 (24)3.5 斜滑块机构设计 (25)3.5.1 侧抽芯系统概述 (25)3.5.2 斜滑块机构基本结构 (26)3.5.3 斜滑块的拼合形式 (27)3.5.4 斜滑块的导滑形式 (27)3.5.5 斜滑块尺寸设计 (27)3.5.6 斜滑块抽芯机构表面粗糙度和材料选择 (29)3.5.7 弹簧限位销设计 (29)3.5.8 斜滑块抽芯机构立体图和装配图 (29)第4章推出机构和模体设计 (31)4.1 推出机构设计 (31)4.1.1 推出机构概述 (31)4.1.2 推杆设计 (31)4.1.3 推板导向及限位装置设计 (33)4.1.4 复位机构设计 (33)4.1.5 推出、复位零件的表面粗糙度、材料及热处理后的硬度 (35)4.1.6 推出机构装配工程图及立体图 (35)4.2 模体设计 (37)4.2.1 模体设计概述 (37)4.2.2 模体尺寸 (38)4.2.3模板导向的尺寸 (38)4.2.4模体构件的表面粗糙度和材料选择 (39)4.3 模具总装图及工作过程模拟 (39)4.3.1 模具总装立体图 (39)4.3.2 模具工作过程模拟图 (39)第5章结论 (42)参考文献 (43)致谢 (45)附录 (46)第1章绪论1.1课题意义1.1.1 压力铸造的特点高压力和高速度是压铸中熔融合金充填成型过程的两大特点。
- 1、下载文档前请自行甄别文档内容的完整性,平台不提供额外的编辑、内容补充、找答案等附加服务。
- 2、"仅部分预览"的文档,不可在线预览部分如存在完整性等问题,可反馈申请退款(可完整预览的文档不适用该条件!)。
- 3、如文档侵犯您的权益,请联系客服反馈,我们会尽快为您处理(人工客服工作时间:9:00-18:30)。
铸造工艺毕业设计
铸造工艺毕业设计
在现代工业生产中,铸造工艺是一项非常重要的技术。
通过铸造,我们可以将
熔化的金属或合金倒入模具中,经过冷却凝固后得到所需的零件或产品。
铸造
工艺的优劣直接影响到产品的质量和性能,因此,对于铸造工艺的研究和改进
具有重要意义。
在我的毕业设计中,我选择了铸造工艺作为研究对象。
我将通过实验和理论分析,探讨如何提高铸造工艺的效率和质量。
首先,我将对不同材料的熔化过程
进行研究。
不同材料的熔化温度和熔化速度存在差异,因此,了解不同材料的
特性对于选择合适的熔化工艺具有重要意义。
其次,我将研究模具的设计和制造。
模具是铸造工艺中的关键环节,它决定了
最终产品的形状和尺寸。
通过优化模具的设计和制造工艺,可以提高产品的精
度和一致性。
我将使用CAD软件进行模具的设计,并通过数控加工来制造模具,以提高制造效率和精度。
另外,我还将研究铸造过程中的凝固行为。
凝固过程对于产品的组织结构和性
能具有重要影响。
通过理论分析和实验研究,我将探讨凝固速度、凝固形貌以
及凝固缺陷的形成机理。
通过对凝固行为的深入研究,可以为优化铸造工艺提
供理论依据。
此外,我还将研究铸造过程中的温度控制和气体控制。
温度控制对于凝固速度
和产品性能具有重要影响。
我将研究如何通过控制熔体温度和模具温度来控制
凝固速度,以及如何通过控制熔体中的气体含量来减少气孔和夹杂物的形成。
最后,我将对铸造工艺进行优化。
通过对上述各个环节的研究,我将提出一套
完整的铸造工艺优化方案。
该方案将包括材料选择、模具设计、凝固行为控制以及温度和气体控制等方面的内容。
通过优化铸造工艺,可以提高产品的质量和性能,降低生产成本,提高生产效率。
总结起来,我的毕业设计将围绕铸造工艺展开研究。
通过对熔化过程、模具设计、凝固行为、温度和气体控制等方面的研究,我将提出一套完整的铸造工艺优化方案。
这将对于提高产品质量和性能,降低生产成本,提高生产效率具有重要意义。
通过毕业设计的研究,我将深入了解铸造工艺的各个环节,为将来从事相关工作打下坚实的基础。