克莱斯勒标准 CS-腐蚀-2004 零部件和系统的腐蚀性能要求
通用汽车技术标准
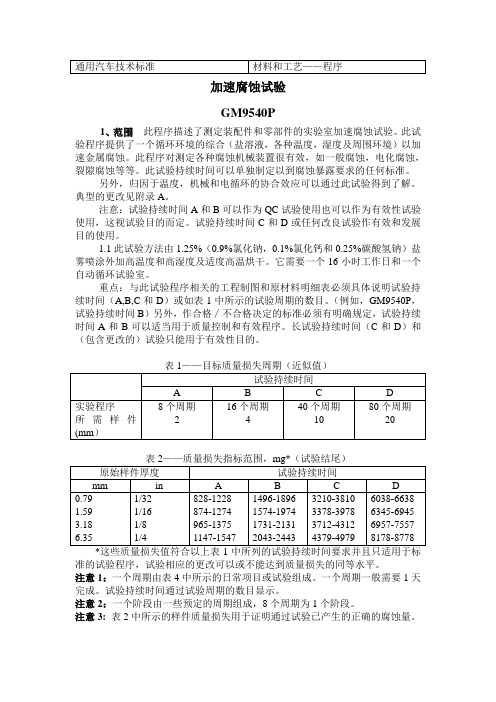
加速腐蚀试验GM9540P1、范围此程序描述了测定装配件和零部件的实验室加速腐蚀试验。
此试验程序提供了一个循环环境的综合(盐溶液,各种温度,湿度及周围环境)以加速金属腐蚀。
此程序对测定各种腐蚀机械装置很有效,如一般腐蚀,电化腐蚀,裂隙腐蚀等等。
此试验持续时间可以单独制定以到腐蚀暴露要求的任何标准。
另外,归因于温度,机械和电循环的协合效应可以通过此试验得到了解。
典型的更改见附录A。
注意:试验持续时间A和B可以作为QC试验使用也可以作为有效性试验使用,这视试验目的而定。
试验持续时间C和D或任何改良试验作有效和发展目的使用。
1.1此试验方法由1.25%(0.9%氯化钠,0.1%氯化钙和0.25%碳酸氢钠)盐雾喷涂外加高温度和高湿度及适度高温烘干。
它需要一个16小时工作日和一个自动循环试验室。
重点:与此试验程序相关的工程制图和原材料明细表必须具体说明试验持续时间(A,B,C和D)或如表1中所示的试验周期的数目。
(例如,GM9540P,试验持续时间B)另外,作合格∕不合格决定的标准必须有明确规定,试验持续时间A和B可以适当用于质量控制和有效程序。
长试验持续时间(C和D)和(包含更改的)试验只能用于有效性目的。
准的试验程序,试验相应的更改可以或不能达到质量损失的同等水平。
注意1:一个周期由表4中所示的日常项目或试验组成。
一个周期一般需要1天完成。
试验持续时间通过试验周期的数目显示。
注意2:一个阶段由一些预定的周期组成,8个周期为1个阶段。
注意3: 表2中所示的样件质量损失用于证明通过试验已产生的正确的腐蚀量。
2、参考标准GM4465P GM9508P GM9102P ASTM B1173、设备和试验原料3.1试验设备3.1.1盐雾湿度箱。
湿度箱要按照GM9540P和表3的规定。
(部件上的水雾或可见水滴在达到平衡之后要持续不断)。
3.1.2盐雾喷涂。
盐雾溶液要按照表3中的规定。
溶液要喷成雾状(例如,从一个塑料瓶喷到试验样品和样件上)。
汽车零部件及材料试验室循环腐蚀试验方法-中国汽车工程学会标准

汽车零部件及材料试验室循环腐蚀试验⽅法-中国汽车⼯程学会标准《汽车零部件及材料实验室循环腐蚀试验⽅法》编制说明(标准征求意见稿)A. ⼯作简况1. 任务来源本标准依据中国汽车⼯程学会2015年10⽉16⽇印发中汽学函[2015]76号《中国汽车⼯程学会技术标准起草任务书》,任务书编号2015-1制定,标准名称《汽车零部件及材料实验室循环腐蚀试验⽅法》。
本标准主要完成单位:中国第⼀汽车股份有限公司技术中⼼,美国Q-Lab 公司中国代表处,重庆长安汽车股份有限公司等。
2. 主要⼯作过程2.12015年7⽉由中国第⼀汽车股份有限公司技术中⼼向中国汽车⼯程学会(以下简称中汽学会)提出制定《汽车零部件及材料实验室循环腐蚀试验⽅法》标准的申请,当年8⽉成⽴了标准⼯作组,提出规划并进⾏分⼯。
2.2⼯作组于2015年9⽉召开标准讨论会,确认撰写⼤纲和章节⽬录。
会后组织实验室循环腐蚀试验与户外腐蚀对⽐试验,并对对⽐试验⼯作进⾏分⼯,确定样品提供单位、实验室循环腐蚀试验单位和户外腐蚀测试试验单位。
2.3先后有10家主机⼚的参与单位,根据汽车⽣产的实际⼯艺提供了试验样品。
试验⼀共收到21种试验样品,其中有效试验样品19种(样板信息见表10)。
这19种试验样品经过对分层膜厚和总厚度的测试和记录,筛选外观合格的最终的样板数量是4257⽚。
样品准备的截⽌时间是2017年2⽉。
2.4经本标准的主要起草单位⼈员,分别是王纳新、王振尧、孙杏蕾、瞿华盛和张恒。
在各个参加单位准备样品期间,讨论通过了本标准的试验⽅案和实施路线。
⾸先,确定本标准的试验分两部分:⼏种实验室的循环腐蚀试验⽅法和验证实验室试验的户外腐蚀试验。
其中,户外腐蚀试验分为两类,⼀类是户外加速腐蚀试验,⼀类是户外⾃然腐蚀试验。
其次,通过⽐对试验和筛选,主要起草⼈员讨论决定:(1)户外加速腐蚀试验分别在2个不同的试验场进⾏,⼀个是中国船舶重⼯集团公司第七⼆五研究所厦门分部的试验场,在厦门海边,属于⾃然加速腐蚀,总的试验时间是2年;另⼀个是海南热带汽车试验有限公司的试验场,在海南琼海,⼈⼯喷洒盐⽔,属于⼈⼯加速腐蚀,总的试验时间也是2年。
c4h防腐国际标准

c4h防腐国际标准
C4H防腐国际标准的主要目的是确保在各种恶劣的环境中使用的金属制品和设备能够
持久耐用、防腐防锈,并能够在长期使用中保持其正常功能。
此标准是由国际标准化组织(ISO)制定的,已经成为了全球范围内的一个通用标准。
C4H防腐国际标准包含了多个层面的要求,包括金属材料的制备、设备的设计、表面
处理以及其它相关问题。
以下是对C4H防腐国际标准的一些重要内容的简述:
1. 材料。
该标准规定,金属制品应该使用符合特定化学成分、机械性能和耐腐蚀性
能要求的材料。
在选择材料时,应该考虑使用条件、腐蚀介质以及所处环境等诸多因素。
2. 设备设计。
该标准要求在设计设备时应该考虑使用环境的特点,采用防腐、防锈
的设计措施。
例如,在接触腐蚀介质的管道和容器壁上应该采用特殊的金属保护层,以防
止腐蚀和漏油等问题的发生。
3. 表面处理。
该标准要求在金属制品的表面处理方面应该采用一系列的措施,包括
清洗、脱脂、除锈、去除氧化物以及镀层处理等。
这些措施旨在提高制品的耐腐蚀性能,
从而延长其使用寿命。
4. 保护层。
该标准规定,金属制品表面所需的保护层应该选用具有较高的抗腐蚀性
能的防腐涂料,以保证表面能够防腐防锈,并且能够在长期使用中维持其正常功能。
此外,保护层应该按照涂装厚度、时间和涂层结构等参数加以控制,以确保其作用效果。
总之,C4H防腐国际标准的制定和实施,为各行业的金属制品和设备的防腐防锈问题
提供了标准和指导,有助于提高其使用寿命、降低维护成本,并且更好地满足了客户对质
量和可靠性的要求。
汽车零部件及材料实验室循环腐蚀试验方法
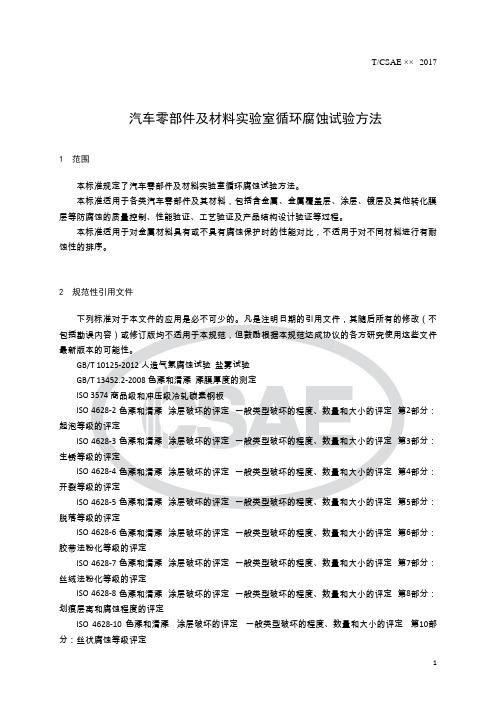
6.4 测定质量损失
T/CSAE ××-2017
试验结束后,应立即取出参比试样,除掉试样背面的保护膜,使用物理或化学方法去除腐蚀产 物。除锈操作的具体步骤可参考GB/T 10125-2012中5.2.3章节,例如,在23 ℃±2 ℃下于20%±5% (质量分数)分析纯级别的柠檬酸二铵(NH4)2HC6H5O7水溶液中充分浸泡。浸泡后,在室温下用 水清洗试样,再用乙醇清洗,干燥后称重。除锈操作的亦可参考ISO 8407中的规定,例如,用 50%(体积分数)的盐酸溶液(密度1.18 g/mL),其中加入3.5 g/L的六次甲基四胺缓蚀剂,浸泡 试样除去腐蚀产物,之后用清水在室温下清洗,然后再用乙醇清洗,最后干燥。
5.2.2 箱内至少放置两个盐溶液收集器,一个靠近喷嘴,一个远离喷嘴。收集器用玻璃等惰性材料 制成漏斗形状,直径为100 mm,收集面积约80 cm2,漏斗管插入带有刻度的容器中,要求收集的是 盐溶液,而不是从试样或其他部位滴下的液体。
5.2.3 通过喷嘴喷淋的溶液,喷淋量可调,且均匀喷淋在试样上。试验箱的形状和尺寸应能使箱内 溶液的收集速度为:在8.1章节表1的第1步至第3步中的12分钟喷淋时间内,盐溶液平均沉降率在80 cm2的水平面积为39 mL~79 mL。
a) 试样划刻线以外部分的外观,如气泡、生锈、开裂、脱落、粉化、丝状腐蚀等;
b) 试样划刻线部位的外观、划痕层离程度、划痕腐蚀程度等;
c) 质量变化;
d) 显微形貌变化。
7
T/CSAE ××-2017 11 试验报告 11.1 试验报告必须写明采用的评价标准和得到的试验结果。如有必要,应有每个试样的试验结 果,每组相同试样的平均试验结果和试样的照片。 11.2 根据试验目的及要求,试验报告可包括如下内容:
汽车耐腐蚀标准

汽车耐腐蚀标准
汽车耐腐蚀标准是指汽车在不同环境条件下对氧化、腐蚀、污染物等的抵抗能力。
不同国家和地区有不同的汽车耐腐蚀标准,其中一些常见的标准包括:
1. ISO 9223:国际标准化组织(ISO)制定的标准,用于评估
汽车所处环境的腐蚀性能,根据大气条件将腐蚀分为6个等级。
2. ASTM B117:美国材料和试验协会(ASTM)制定的标准,用于评估汽车材料和涂层的耐腐蚀性能,通过在盐雾环境中暴露的测试来确定性能。
3. JIS D0205:日本工业标准制定的标准,用于评估汽车防腐
性能的测试方法,包括盐雾、湿热和酸性雨水等环境条件的测试。
4. GB/T 1771-2017:中国国家标准,用于评估汽车及其部件的
耐腐蚀性能,并制定了不同环境条件下的相关测试方法和要求。
这些标准对于汽车制造商和相关行业来说都非常重要,可以帮助确保汽车在各种环境条件下具有良好的耐腐蚀性能,延长汽车的使用寿命,并提高安全性能。
c4h防腐国际标准

c4h防腐国际标准C4H防腐国际标准是指一种防止金属腐蚀的国际标准,该标准涵盖了材料选择、处理方法、施工要求和质量控制等方面。
本文将详细介绍C4H 防腐国际标准的相关内容。
C4H防腐国际标准主要适用于金属结构、设备、管道和储罐等的防腐处理。
其目的是延长金属材料的使用寿命,减少腐蚀所造成的损坏和安全隐患。
该标准的实施可以保证防腐工程的质量和可靠性,提高设备的可靠性和维护成本的降低。
首先,C4H防腐国际标准要求在材料选择方面首先考虑使用铝、镍、镍合金、铜、铜合金等抗腐蚀性能较好的材料。
对于常用结构钢材,要求进行防腐处理,如热浸镀锌、喷涂涂料等。
对于不同的工作环境和介质,要根据《C4H防腐国际标准》规定的化学物质腐蚀性指数对材料的耐腐蚀性能进行评估和选择。
其次,在处理方法方面,C4H防腐国际标准要求采用合适的表面处理方法,如脱脂、除锈、钝化等,以确保金属表面清洁、平整和有效的防腐效果。
在钢结构和设备表面处理中,可以采用喷砂、喷丸、机械抛光等方法,去除表面的锈蚀、油污等杂质,以提高防腐涂层的附着力和稳定性。
此外,施工要求是C4H防腐国际标准的另一个重要方面。
标准要求施工单位采用科学的施工工艺和合理的施工方法,确保防腐工程的质量和可靠性。
施工单位应根据工程要求和标准规定,选择适当的涂层材料和施工工艺,并严格按照施工规程和操作手册进行操作。
同时,还要注意施工现场的环境控制,确保施工环境温度、湿度等条件符合涂料施工要求。
最后,质量控制是C4H防腐国际标准的关键环节。
标准要求施工单位建立并实施质量控制体系,包括材料进场检验、施工过程控制、工程验收等。
施工单位应对涂层材料进行质量检验,并记录和保留相应的检验报告。
在施工过程中,要进行现场质量控制和监督,确保施工质量和进度符合标准要求。
综上所述,C4H防腐国际标准是一项关于防止金属腐蚀的国际标准,该标准涵盖了材料选择、处理方法、施工要求和质量控制等方面。
它在金属结构、设备、管道和储罐等的防腐处理中具有重要的指导作用,可以提高工程质量、延长设备使用寿命,并确保设备的可靠性和安全性。
GM4350M-2004通用汽车零件涂装要求标准
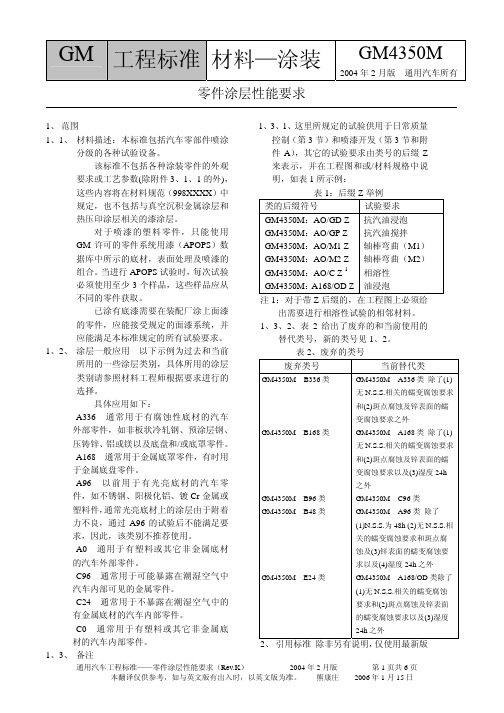
GM工程标准材料—涂装GM4350M2004年2月版—通用汽车所有零件涂层性能要求1、范围1、1、材料描述:本标准包括汽车零部件喷涂分级的各种试验设备。
该标准不包括各种涂装零件的外观要求或工艺参数(除附件3、1、1的外),这些内容将在材料规范(998XXXX)中规定,也不包括与真空沉积金属涂层和热压印涂层相关的漆涂层。
对于喷漆的塑料零件,只能使用GM许可的零件系统用漆(APOPS)数据库中所示的底材,表面处理及喷漆的组合。
当进行APOPS试验时,每次试验必须使用至少3个样品,这些样品应从不同的零件获取。
已涂有底漆需要在装配厂涂上面漆的零件,应能接受规定的面漆系统,并应能满足本标准规定的所有试验要求。
1、2、涂层一般应用以下示例为过去和当前所用的一些涂层类别,具体所用的涂层类别请参照材料工程师根据要求进行的选择。
具体应用如下:A336 通常用于有腐蚀性底材的汽车外部零件,如非板状冷轧钢、预涂层钢、压铸锌、铝或镁以及底盘和/或底罩零件。
A168 通常用于金属底罩零件,有时用于金属底盘零件。
A96 以前用于有光亮底材的汽车零件,如不锈钢、阳极化铝、镀Cr金属或塑料件,通常光亮底材上的涂层由于附着力不良,通过A96的试验后不能满足要求,因此,该类别不推荐使用。
A0 通用于有塑料或其它非金属底材的汽车外部零件。
C96 通常用于可能暴露在潮湿空气中汽车内部可见的金属零件。
C24 通常用于不暴露在潮湿空气中的有金属底材的汽车内部零件。
C0 通常用于有塑料或其它非金属底材的汽车内部零件。
1、3、备注1、3、1、这里所规定的试验供用于日常质量控制(第3节)和喷漆开发(第3节和附件A),其它的试验要求由类号的后缀Z来表示,并在工程图和或/材料规格中说明,如表1所示例:表1:后缀Z举例类的后缀符号试验要求GM4350M:AO/GD ZGM4350M:AO/GP ZGM4350M:AO/M1 ZGM4350M:AO/M2 ZGM4350M:AO/C Z 1GM4350M:A168/OD Z抗汽油浸泡抗汽油搅拌轴棒弯曲(M1)轴棒弯曲(M2)相溶性油浸泡注1:对于带Z后缀的,在工程图上必须给出需要进行相溶性试验的相邻材料。
国外石化腐蚀标准与资料介绍
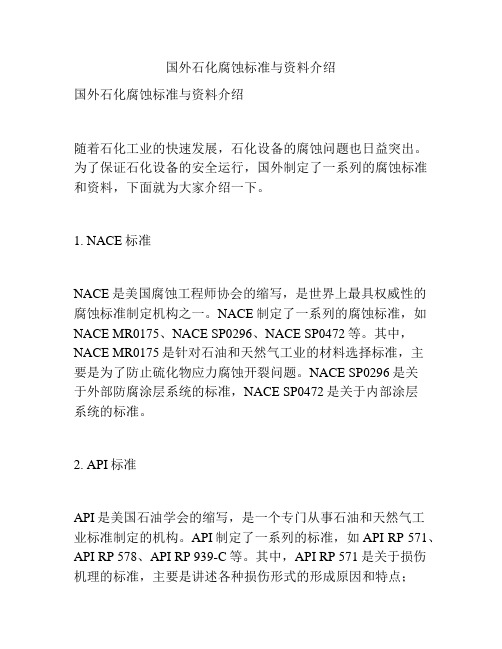
国外石化腐蚀标准与资料介绍国外石化腐蚀标准与资料介绍随着石化工业的快速发展,石化设备的腐蚀问题也日益突出。
为了保证石化设备的安全运行,国外制定了一系列的腐蚀标准和资料,下面就为大家介绍一下。
1. NACE标准NACE是美国腐蚀工程师协会的缩写,是世界上最具权威性的腐蚀标准制定机构之一。
NACE制定了一系列的腐蚀标准,如NACE MR0175、NACE SP0296、NACE SP0472等。
其中,NACE MR0175是针对石油和天然气工业的材料选择标准,主要是为了防止硫化物应力腐蚀开裂问题。
NACE SP0296是关于外部防腐涂层系统的标准,NACE SP0472是关于内部涂层系统的标准。
2. API标准API是美国石油学会的缩写,是一个专门从事石油和天然气工业标准制定的机构。
API制定了一系列的标准,如API RP 571、API RP 578、API RP 939-C等。
其中,API RP 571是关于损伤机理的标准,主要是讲述各种损伤形式的形成原因和特点;API RP 578是关于焊接人员资格认证的标准;API RP 939-C是关于材料选择和耐蚀性评估的标准。
3. ASTM标准ASTM是美国材料与试验协会的缩写,是一个从事材料和产品标准制定的机构。
ASTM制定了一系列的标准,如ASTM G1、ASTM G31、ASTM G48等。
其中,ASTM G1是关于化学分析和金相检查的标准;ASTM G31是关于电化学腐蚀测试方法的标准;ASTM G48是关于晶间腐蚀测试方法的标准。
4. ISO标准ISO是国际标准化组织的缩写,是一个从事国际标准制定的机构。
ISO制定了一系列的标准,如ISO 8501-1、ISO 8502-3、ISO 12944-5等。
其中,ISO 8501-1是关于表面清洁度等级的标准;ISO 8502-3是关于表面粗糙度测量方法的标准;ISO 12944-5是关于涂层系统设计和表面处理的标准。
整车零部件防腐技术条件

制动硬管总 镀锌 Fe/Ep·Zn18,橄榄绿,按 QC/T 625-1999 的规定;盐雾试验在
成
120h 以上,无腐蚀现象。
制动管
40
路装置 制动软管总 金属接头及支架表面处理 Fe/Ep•Zn12•c1B,按 QC/T 625-1999 执行,
盐雾试验要求大于 240h,其余金属件 96h 以上中性盐雾试验后均不
Q/JLY J721060-2009
表 1(续)
序号 所属系统
零部件名称
防腐设计要求
下摆臂焊接 焊接完毕后表面应进行阴极电泳涂漆处理,按 QC/T 484-1999 TQ6 执
总成
行,耐盐雾试验大于 240h,试验后零件表面无起泡、腐蚀等异常现象。
前悬架
30
下摆臂 下摆臂球头 黑色亚光电泳漆,盐雾试验大于 240h 无腐蚀现象,铆接部位除外;
时。
43
粘贴式平衡块
表面镀锌并喷罩光漆或喷塑,耐盐雾试验 480h 无红锈。
45
钢轮平衡块
表面喷塑均匀,盐雾试验 480h 无红锈。
Fe/Ep·Cr10,按 QC/T 625-1999 执行,酸性盐雾试验(CASS)48h
46
车轮螺母
后外表面腐蚀等级 8 级以上。
横拉杆:表面黑色电泳漆,按 QC/T 484-1999 TQ6 规定执行,盐雾试
镀锌,盐雾试验 72h,不出现白锈。
共7页 第1页
GEELY
CE-1/2 整车零部件防腐技术条件
Q/JLY J721060-2009
表 1(续)
序号 所属系统
零部件名称
防腐设计要求
3
车身车Leabharlann 铰链镀锌,盐雾试验 96h,不出现白锈。
汽车及其零件的腐蚀和防护

汽车及其零部件的腐蚀与防护汽车在日常生活中变得越来越重要。
但现在汽车制造所用的材料仍以金属为主,而金属材料普遍存在腐蚀问题,它不仅破坏了汽车的外观,还直接影响到汽车质量和汽车寿命,同时带来环境污染、交通事故的发生,以及材料与能源的浪费。
可以说,汽车的防护越来越重要,汽车金属零部件表面的防腐是其中的重中之重.我们要对汽车进行防护,必须先了解汽车零部件被腐蚀的原因,一般来说有以下几种:(1)结构设计不合理,如有焊接疤痕;(2)有害物质的侵蚀(如酸碱盐等);(3)机械损伤后的腐蚀;(4)材料方面存在的问题;(5)防护工艺上存在的问题;(6)环境因素造成的腐蚀(如湿度较大,日光及风化等);(7)电化学腐蚀。
日常生活中,汽车主要容易受到腐蚀的部位如下:1.汽车表面(汽车暴露在潮湿的空气里,表面自然是最容易受到侵蚀的部位);2.汽车底盘(汽车底盘也是受到侵蚀的重点部位,日常生活中车底盘与水接触得较多,最容易生锈。
底盘终年不见阳光,湿气还会从底盘细小的孔洞中渗入而锈蚀车身,使油漆剥落。
);3.刹车系统(刹车系统失效是因刹车油容易和水融合,水蒸气在制动罐上大量积存,很容易进入制动液内,对刹车片及其部件有一定的腐蚀);4.汽车音响系统(音箱与CD容易受潮);5.汽车坐椅(汽车坐椅是和人体接触最多的部位,即使是真皮坐椅,在一些阴暗的部位,也容易受到潮气侵蚀。
);6.车载电脑系统(车载电脑系统也是容易被潮气侵蚀的重要部件且价格颇贵,应是车主应重点保护的对象。
);7.轴承(因为长期承受高强度的机械运动受力而磨损较为严重)。
基于这些,我们要重点对这些部位进行防护。
提高汽车防腐能力的建议:①从结构方面避免腐蚀,②选用抗腐蚀性能优良的材料,③采用先进完善的防腐工艺。
下面介绍汽车金属零部件表面常用的几种表面处理方式:①电化学处理:主要是电镀和阳极氧化;②涂装:喷涂和电泳;③化学处理:磷化、钝化、发黑等;④热处理方式:热浸镀、热喷涂、热烫印和化学热处理等;⑤真空法处理:蒸发镀、溅射镀及离子镀等。
不同品牌汽车的零部件及材料加速腐蚀试验方法及评价对标分析
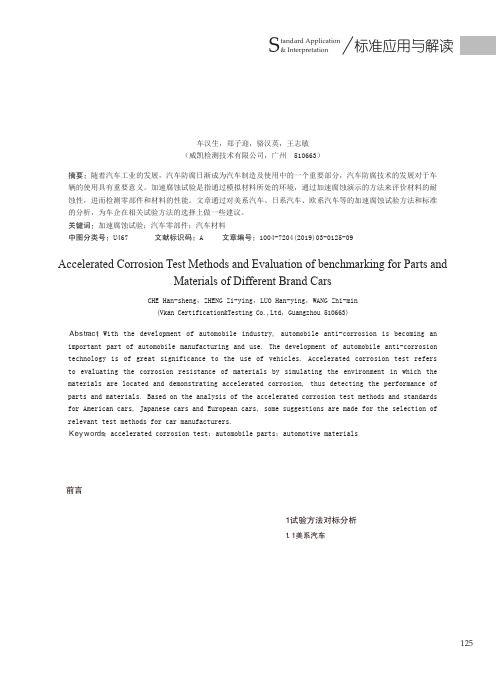
0 h 3 min
1c’
3 h 3 min
2 h 54 min
1a’ 5 h 57 min
0 h 3 min
2a
6 h 0 min
0 h 30 min
2b
6 h 30 min
2 h 0 min
3a
8 h 30 min 15 h 30 min
3a
24 h 0 min
—
重复步骤 1a-3a 4 次(不含第 1 次)
环。 盐 溶 液 成 分: 氯 化 钠 NaCl:0.9 %, 无 水 氯 化 钙
CaCl2:0.1 %,碳酸氢钠 NaHCO3:0.075 %。 1.2 欧系汽车 1.2.1 PSA 汽车 1)试验标准,D13 5486-2012,《材料和覆盖层 循
环加速腐蚀试验》。 2)具体测试条件: 喷雾阶段(如表 2) 过渡阶段(如表 3) 热循环阶段(如表 4) 盐溶液成分:氯化钠:5 %,通过 0.005 mol/L 的硫
辆的使用具有重要意义。加速腐蚀试验是指通过模拟材料所处的环境,通过加速腐蚀演示的方法来评价材料的耐
蚀性,进而检测零部件和材料的性能。文章通过对美系汽车、日系汽车、欧系汽车等的加速腐蚀试验方法和标准
的分析,为车企在相关试验方法的选择上做一些建议。
关键词:加速腐蚀试验;汽车零部件;汽车材料
中图分类号:U467
S 标准应用与解读 tandard Application & Interpretation
1.1.2 通用汽车 1) 试 验 标 准:GMW14872-2013,《 实 验 室 循 环 腐 蚀试验》。 2)具体测试条件 室温阶段:温度 25±3 ℃,相对湿度 45 %± 1 0 % R H , 持续时间 8 h; 高湿阶段:温度 49±2 ℃,相对湿度约 100 %RH, 持续时间 8 h; 干燥阶段:温度 60±2 ℃,相对湿度≤ 30 %RH,持 续时间 8 h; 盐溶液成分:氯化钠:0.9 %,氯化钙:0.1 %,碳酸 氢钠:0.075 %; 总 试 验 时 间: 根 据 样 品 的 安 装 部 位, 依 据 GMW14872 的表 A1 和 A2 规定的测试周期。见图 5 试验 流程和图 6 测试周期。 3)标准特点 喷雾方式与传统盐雾不一样,每循环喷淋 1-4 次, 通过手动或自动喷头直接喷射到样品表面,直到润湿为 止。 测试过程中需要加入标准板“coupon”控制腐蚀速率, 具体见图 7 和 8。 除了常规的汽车零部件,有些特殊的部位需要增加 环境应力,例如高温、冷凝液或泥浆等。以汽车排气管 为例,该部件的循环腐蚀测试方法,应依据标准 GMW 14872-2013 Option 4 进行试验。每个循环包含 3 个试验 阶段: 室温阶段:温度 25±3℃,相对湿度 45 %± 10 %RH,持续时间 8 h,该阶段内对样品和标准板进行 4 次盐雾喷洒,前 2 次喷洒间隔 1 h,在第 2 次喷洒结 束 0.5 h 后,对样品进行 4 h 的 482 ℃的高温试验,高温 试验结束 0.5 h 后,对样品和标准板进行 2 次间隔 1 小时 的盐雾喷洒(标准板不随样品进行高温试验); 高湿阶段:温度 49±2 ℃,相对湿度约 100 %RH, 持续时间 8 h; 干燥阶段:温度 60±2 ℃,相对湿度≤ 30 %RH,持
汽车零部件镀镍、铬技术条件

汽车零部件镀镍、铬技术条件1范围本标准规定了各型汽车的零部件经电镀装饰镍、铬及镀硬铬后的质量要求,以及电镀前后的检验规则和试验方法。
本标准适用于各型汽车金属和塑料零件的防护装饰性镀铬、镀硬铬。
2规范性引用文件下列文件中的条款通过本标准的引用而成为本标准的条款。
凡是注日期的引用文件,其随后所有的修改单(不包括勘误的内容)或修订版均不适用于本标准,然而,鼓励根据本标准达成协议的各方研究是否可使用这些文件的最新版本。
凡是不注日期的引用文件,其最新版本适用于本标准。
GB/T 4955-1997 金属覆盖层金属覆盖层厚度测量阳极溶解库仑法GB/T 6461-2002 金属基体上金属和其它无机覆盖层经腐蚀试验后的试样和试件的评级GB/T 10125-1997 人造气氛腐蚀试验盐雾试验GB/T 11379-1989 金属覆盖层金属用铬电镀层3术语和定义下列术语和定义适用于本标准。
3.1电镀在电流通过电解质溶液的条件下,在作为阴极的金属制品表面或表面具有导电层的非金属表面上形成与基体牢固结合的金属覆盖层的过程。
3.2主要表面指零件上电镀前和电镀后的某些表面,该表面上的镀层对于工件的外观和使用性能是起主要作用的。
4电镀分类4.1外观件——镀装饰铬组装后十分容易见到,装饰价值很高的部分。
包括:格栅组件,后牌照灯饰板,标牌,车门外扣手,内门拉手,车轮螺母,紧固螺栓,安全带扣手,手刹按钮等。
4.2耐磨件——镀硬铬增加表面硬度,提高耐磨性的部分。
包括:减震活塞拉杆,发动机活塞环刮片环外园等。
5零件电镀前的质量要求5.1金属零件电镀前的质量要求5.1.1有配合公差要求的零件,应留有适当的加工余量。
5.1.2焊接件的焊点、焊缝均要求饱满、圆滑,无气孔、无漏焊、假焊、焊裂、焊穿、无药皮、飞溅、焊瘤。
焊缝应清理至无氧化皮、无溶渣。
5.1.3零件表面不得有经前处理和机械研磨都无法除去的缺陷,如严重的碰凹、碰伤、严重锈蚀、热轧氧化皮、裂纹等。
c4m防腐等级标准

c4m防腐等级标准防腐等级c4,腐蚀面积小于或等于5%,发黑发白斑都算腐蚀。
1、C4防腐要求较高,C4级别常用于高盐度的工业区、化工区、沿海区域、桥梁、化工厂、电厂、船厂、海船等,它最主要的应用环境是高盐度、高湿度环境。
2、热镀锌厚度:普通:单点高于70μ,单点高于85μ加厚:单点高于90μ,单点高于110μ。
c4防腐等级标准根据《ISO12944腐蚀环境判定标准》,将大气环境对裸露钢板的腐蚀程度分为以下五个级别——C1、C2、C3、C4、C5、C5m,其中C1、C2、C3为轻防腐,水性涂料多为醇酸或丙烯酸涂料C3、C4防腐级别的水性涂料多为环氧或聚氨酯涂料对于C5或C5M,目前水性涂料难以达到防腐要求。
应用于C3-C5M级别的防腐涂料通常性能要求高,户外型产品还具有较高的耐候要求,因此涂料配方中经常需要添加紫外线吸收剂、光稳定剂等耐候助剂。
一、C1级别的防腐要求比较低,涂膜干膜厚度一般在60u,中等要求的干膜厚度在120u左右,高等级要求的在180u左右。
C1级别的水性防腐涂料应用环境多是加热的内部,建筑内部,空气洁净的环境,如办公室、商店、学校和宾馆等。
二、C2级别的防腐要求也比较低。
多为大气污染较低,未加热的、低频凝结发生的环境,如库房、体育馆等。
三、C3级别属于中等的防腐类别,它多应用于城市。
它的主要应用环境是高湿度和有些污染空气的生产场所,如普通的工业厂房,酒厂等。
四、C4级别常用于高盐度的工业区、化工区、沿海区域、桥梁、化工厂、电厂、船厂、海船等,它*主要的应用环境是高盐度、高湿度环境。
五、C5级别应用于高盐度和恶劣大气的工业区域,有冷凝和高湿的建筑。
在防腐领域,C5级别的要求是比较高的。
六、C5M级别要求则更高,常见于海洋、高盐度的沿海离岸地带。
从环境上来说是处于高湿度、高污染的建筑物,如海上钻井平台、航标塔等。
c4防腐等级标准参考ISO12944-2-1998,标准中规定了大气环境的6类大气腐蚀性级别,C1 非常低,C2低,C3中等,C4高,C5-1很高(工业),C5-M很高(海洋)。
Q SQR04.028-2005 整车金属零部件涂层技术规范(试行)
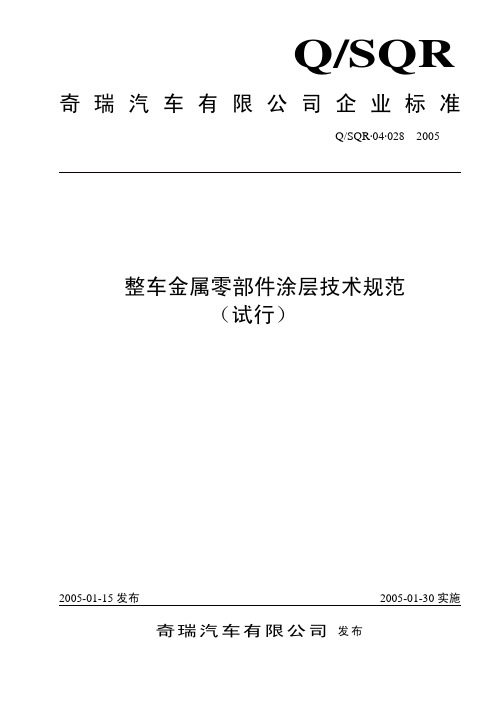
外观
厚度,um 耐盐雾时间,h
粘附强度
Q/SQR·04·028—2005
镀层表面细致,均匀,无裂痕、气泡、毛细孔、褶皱、麻点、 目测
粗糙、脱落、污物、变色及局部无镀层等表面缺陷存在
≥3
≥8
≥15
GB/T 4956
48
96
144
240
⑶
GB6458
无起泡等现象
*
*-将试样放置在(220±10)℃下存放 30 分钟,接着浸在温度为 15℃~25℃的水中。然后将零件 取出,观察表面有无起泡等现象。 ⑶ 盐雾试验后判断标准参照 7.1.2
3.1 涂层的定义: 涂层:覆盖于零部件表面用于保护零部件外观和功能,包括油漆涂层和镀层。油漆涂层分为喷漆、 电泳、喷塑和粉末喷涂等;镀层包括镀锌、镀铬等。
3.2 外部、内部区域定义: 外部区域:以车门、风窗---密封条为界,位于车身外部或某些开启零件内部。 内部区域:以密封条为界,位于驾驶舱或行李舱内。
I
Q/SQR·04·028—2005
整车金属零部件涂层技术规范
1 范围
本技术规范确定了整车金属零部件涂层的技术要求。本技术规范由范围、规范性引用文件、术语、 涂层腐蚀定义、零部件腐蚀等级定义和技术要求、判断标准、注意事项等部分组成。
2 规范性引用文件
下列文件中的条款通过本技术规范的引用而成为本技术规范的条款。凡是注日期的引用文件,其随
6 技术要求 6.1 油漆涂层性能要求(见表 6)
3
项目
外观
膜厚, 喷漆
um
电泳
粉末(稳定杆)
附着力,级
抗石击,级 耐盐雾试验时间
表6
性能要求
FS-1
FS-2 FS-3 FS-4 FS-5
cs-cscorrosion车辆系统好部件的腐蚀要求

1一般1.1目的本标准规定了相关的功能和外观的车辆部件和系统目标的腐蚀。
它也描述了工程开发的腐蚀试验的要求(ED),设计验证(DV),产品验证(PV),和持续一致性(CC)测试。
组件级ED和DV实验室测试可以免测,提供了一份完成的由腐蚀工程师签字的完整系统和连接设计审核文件。
1.2本标准范围本标准适用于克莱斯勒集团有限责任公司的车辆和零部件。
它可能被引用在其他系统的标准或性能标准的建立。
本标准的要求,除了那些包含在任何适用的材料或工艺标准。
1.3限制使用这个标准可以通过复制适当的性能要求2节中给出了本标准第4节中为下列工程文件的测试要求的应用:预源码包- CATIA / NX模型或性能标准(PF)-设计验证计划和报告(DVP&R)产品保证计划(PAP)定义/缩写/缩写1.4的位置定义/缩写或缩写可以在本标准第5节的发现。
2腐蚀性能要求2.1外观要求外观要求的定义如下:2.1.1 I类表面外观定义:I类外观项目被定义为外表面的项目是客户随时可见而不打开任何封板或在车内平视视角的表面。
要求:在服务5年无腐蚀。
2.1.2 II类表面外观。
定义:第二类外观项目被定义为这些项目是在打开关闭的面板后可见的,例如门的门框和硬件,-门或舱盖排水槽,或卡车后挡板包围,燃料填充开门。
不在眼前车内项目,但通常是客户在正常的操作和维护的过程中可见的。
要求:服务5年无腐蚀。
2.1.3发动机舱的外观。
定义:发动机舱的外观项目是指那些发动机舱的物品,客户在正常的使用和维修活动的过程可见的。
要求:服务2年无腐蚀。
2.1.4车底外观。
定义:当汽车被提升机提升后那些客户随时可见车底项目。
要求:在服务1年的腐蚀允许最小(小于1%总底部腐蚀)。
2.1.5外观内饰定义:这些内部的金属部件,客户在正常的使用和维护过程中直接可见的。
要求:在服务5年无腐蚀2.2功能要求:定义:功能需求是指物理,电气,机械或属性描述项的功能,例如,结构,输出,或使用。
车身密封-防腐设计(白车身)

车身密封-防腐介绍(白车身)车身防腐性能是决定车身使用寿命的重要指标。
由于车身在行驶中经常受到高速石子的撞击,还经历潮湿和酸碱环境,要使整车满足设计任务书的要求,必须要分析车身各个部件在使用中的腐蚀风险,从结构设计和材料选择开始,确保防腐材料在整车(白车身)零部件上的可实施性。
一.PSA的防腐目标●保证零件16年的安全运行(售后15年+1年商品化前的整车库存)判断的标准:60个CAV循环●保证13年无穿孔(售后12年+1年商品化前的整车库存),按照国标QC/T 484—1999,车身耐腐蚀性要求是8无穿孔年。
判断的标准:60个CAV循环●客户可见的零件6年无红锈腐蚀现象(售后5年+1年商品化前的整车库存)判断的标准:30个CAV循环二.车身防腐区域划分2.1、通常将车身分为4个级别-0级:没有要求区域-1级:腐蚀较弱区域-2级:一般要求区域-3级:强腐蚀要求区域2.2、对于外观腐蚀风险划分为3个等级-A级:弱风险区-B级:一般风险区-C级:强风险区2.3、车身腐蚀等级图示部件说明要求等级涂层镀锌层电泳层抗石击Ⅰ-地板部件1-前地板总成:K2B-地板:-横梁:-外(前,前闭板)-侧围内部-通道/横梁加强板:侧围外部侧围内部-通道:333310/1010/100/010/100/010/101515/R8/R15/R8/R15OONONO/N2-后地板总成:K2C-地板:-横梁:-侧围内部-侧围外部-纵梁:-加强板:-外部-侧围内部3133310/100/010/1010/1010/100/01581515/R158NNNONNⅡ-风窗挡板:K3A-挡板: 3 10/10 10 NO:有抗石击要求N:无抗石击要求三.防腐密封定义3.1、通用涂层定义:防腐原理:以牺牲性材料保护钢板。
试验证明:10um/10um的双面镀锌钢板暴露在大气中,5年才出现红锈,而0.7的裸板暴露在大气中是3年穿孔。
根据镀锌工艺,镀锌分为热镀锌(G)和电镀锌(EZ),电镀锌成本高于热镀锌,通常G10/10的防腐效果等同于EZ7.5/7.5。
汽车防腐蚀标准

汽车防腐蚀标准
汽车防腐蚀标准指的是汽车制造和出厂时需要满足的防止金属部件受到腐蚀损害的技术规范和要求。
以下是一些常见的汽车防腐蚀标准:
1. ISO 9223:这是一项国际标准,用于评估大气环境条件对金
属腐蚀的影响。
汽车制造商可以根据ISO 9223将汽车设计和
制造以适应不同的环境条件。
2. ISO 12944:这个标准涵盖了对车身进行防腐蚀处理的技术
要求。
它包括金属表面处理、防腐蚀涂层的选择和涂覆工艺等方面的要求。
3. ASTM B117:这个标准规定了进行盐雾腐蚀测试的方法。
汽车制造商可以使用这个标准来评估和比较不同材料和涂层的耐腐蚀性能。
4. JASO标准:这个标准是日本汽车标准组织(JASO)制定的,主要适用于日本汽车制造商。
它包括了涂层材料的选择、涂覆工艺和腐蚀测试等方面的要求。
除了以上的标准,汽车制造商还可以根据其自身的要求和市场需求,制定自己的防腐蚀标准。
这些标准通常会包括涂层的厚度要求、防腐蚀性能的测试要求等。
汽车制造商会进行严格的质量控制,确保汽车在使用过程中不受到腐蚀损害。
重型汽车零部件耐腐蚀能力的评定——中性盐雾试验评级方法

墼: 型丛
Aut om obi e t I T s e
重型汽 车零部件耐腐蚀ຫໍສະໝຸດ 能力的评定 中性 盐 雾 试 验 评 级方 法
— —
向 红
( 西重 型汽车 有 限公司 , 陕西 西 安 70 0 ) 陕 120 摘 要 :重型汽 车在 市场 上部 分零 部件 出现 多处涂层 缺 陷 ,影 响外观 及使 用性 能 ,形成腐 蚀 ,导致 本
评级 》和 ( C T 4 4 19 汽车 油漆 涂层 》针对 于 Q / 8 —9 9
1 、概 述 :
耐腐 蚀性 评 级标准 ( B 6 6 .0 2 金 属基 体上 G /4 12 0
试板的评级 而 标准 中没 有对 汽车零 部件 评级 ;试板
,
的评 级标准 直接 用 于汽车 零部 件 的评 级会 产生 很大偏
h a y d t u o p rsno c re p n i g sa a d o e a s sme .I t i he i.wih r fr n e t ee a t e v - u y a t a t o r s o d n tnd r s fr t se s nt n s t ss h h t e e e c o r lv n
Ke wo d : Co tn e e t, e ra ats r yt s, o o i nr ssa c , o t v l ai n t ai gme o y rs ai gd fcs n ut ls l p a t c r so e it e c ai e au t ,her tn t d e n ng o h
关键 词 :涂层缺 陷 ;中性 盐雾试 验 ;耐腐 蚀 能力 ;涂层评 定 ;评级 方法 He v - a y dut u o pa t -- he a s s m e fc r o i n r ss a e y a t r s--t s e s nto o r s o e i t nc - - o ut a a ts a e tr tng m e ho fne r l l pr y t s a i t ds s
- 1、下载文档前请自行甄别文档内容的完整性,平台不提供额外的编辑、内容补充、找答案等附加服务。
- 2、"仅部分预览"的文档,不可在线预览部分如存在完整性等问题,可反馈申请退款(可完整预览的文档不适用该条件!)。
- 3、如文档侵犯您的权益,请联系客服反馈,我们会尽快为您处理(人工客服工作时间:9:00-18:30)。
D AIMLER C HRYSLER CORPORATION No: CS-CORROSION Characteristic Standard Date Published: 2004-06-22 Category Code: A-5 Change: B EASL Req.: NoRESTRICTED: NoCORROSION REQUIREMENTS - SYSTEMS AND COMPONENTS1.0 GENERAL1.1 PurposeThis standard describes corrosion-related functional and appearance objectives for systems and components, which were agreed to by the Product Quality Committee at the meeting of August 26, 2002. It also describes the corrosion test requirements for engineering development (ED), design verification (DV), product validation (PV), and continuing conformance (CC) testing.1.2 Coverage of this StandardThis standard applies to vehicles and service parts built by the Chrysler Group of DaimlerChrysler Corporation (DCC). It may be referenced within other system standards or performance standards. The requirements of this standard are in addition to those contained within any applicable material or process standards.1.3 Limitations on UsageThis standard may be applied by copying the appropriate performance requirements given in Section 3.0 and the test requirements given in Section 5.0 of this standard into to the following engineering documents:- Pre-source package- CATIA model or Performance standard (PF)- Design Verification Plan & Report (DVP&R)- Product Assurance Plan (PAP)This standard may be released directly on a CATIA model if no PF exists, or if the PF cannot be revised to include these requirements in time to meet program requirements.1.4 Location of Definitions/ Abbreviations/ AcronymsDefinitions/ Abbreviations/ Acronyms can be found in Section 6.0 of this standard.2.0 CORROSION PERFORMANCE REQUIREMENTS2.1 Appearance RequirementsAppearance requirements are defined in terms of a maximum allowable corrosion rating after a given length of service. The definition of the corrosion rating system appears in section 5.0 of this standard. 2.1.1 Class I Surface AppearanceDefinition:Class I appearance items are defined as exterior surface items that are readily visible to the customer without opening any closure panels, except as defined in paragraph 2.1.4, or that are in plain view within the vehicle interior.Requirements:- 1 year in service with a corrosion rating of 0, and- 5 years in service with a maximum allowable corrosion rating of 1.2.1.2 Class II Surface Appearance.Definition:Class II appearance items are defined as those items that are visible upon opening closure panels, e.g. - Door jambs and hardware,- Liftgate or decklid drain troughs, or truck tailgate surrounds,- Fuel filler door opening.Class II appearance items also includes interior items that are not in plain view, but are commonly visible to the customer in the course of normal ownership and maintenance activities.Requirements:- 1 year in service with a maximum allowable corrosion rating of 1, and- 5 years in service with a maximum allowable corrosion rating of 2.2.1.3 Underhood Appearance.Definition:Underhood appearance items are defined as those underhood items that are readily visible to the customer in the course of normal ownership and maintenance activities.Requirements:- 1 year in service with a maximum allowable corrosion rating of 1, and- 5 years in service with a maximum allowable corrosion rating of 2.2.1.4 Underbody Appearance.Definition:Those underbody items that are readily visible to the customer when viewed from outside of the vehicle, with the vehicle on the ground (i.e. not on a hoist or lift), with the eye at a distance of not more than 5 meters and at a height of not less than 1 meter from the ground shall be subject to this requirement. Consideration shall be given to the position of the front wheels when assessing the visibility of chassis components, with regard for the showroom appearance of those items that may be visible with the wheels turned.Requirement;- 1 year in service with a maximum allowable corrosion rating of 1, and- 5 years in service with a maximum allowable corrosion rating of 2 only for those items that are in plain view directly through the face of the wheels, except brake rotors;.2.2 Functional RequirementsDefinition:Functional requirements are defined as those physical, electrical, or mechanical attributes that describe the function of an item, e.g., structure, output, or serviceability. Design life is defined as the required period of time that the item must retain its functional requirements. This may be less than the life of the vehicle if it is intended that the part be serviced or replaced. The responsible engineering department shall define the functional requirements and design life of the item under test.Requirement:- 10 years in service with no loss of function due to corrosion, unless the design life is otherwise specified. - For fasteners; 10 years in service with a maximum allowable corrosion rating of 3.3.0 CORROSION TESTING - GENERAL3.1 Compliance to Material and Process Standard requirementsPrior to corrosion testing of an item according to this standard, the engineer must verify that the materials and processes used meet the requirements of the applicable DaimlerChrysler Material and Process Standards or other industry specifications; otherwise, the test results shall be considered inconclusive. Examples of requirements found within material or process standards are;- Coating thickness- Coating composition- Resistance to salt spray- Resistance to humidity- Cycle cracking- Ultraviolet exposureNOTE: Corrosion and other environmental tests are included as characterization tests within materialand process standards. In this case, such tests are used for material or process characterization and do not directly correlate to in-service corrosion performance.3.2 Full-Vehicle Corrosion TestingFull-vehicle corrosion testing according to LP 461H-117 is preferred at all levels of the product creation process because corrosion performance of an item is dependent upon its position on the vehicle. Where both full-vehicle and laboratory methods are prescribed, the full vehicle method shall be the preferred test.In the Engineering Development (ED) phase testing may be conducted on a mule or other program vehicle. Information may also be drawn from previous tests conducted on similar vehicles.In the Design Verification (DV) phase, testing conducted on an S0 level vehicle is preferred. If an S0 vehicle is not available a full-vehicle test on an earlier-level vehicle may be substituted.In the Product Validation (PV) phase, only full-vehicle testing performed on an S0 (or later) level vehicle is permitted because the position of the item on the vehicle must be considered.3.3 Laboratory TestingIn the ED and DV phases laboratory testing may be utilized if full vehicle testing is not possible. However, THE ENGINEER MUST CONSIDER environmental factors that affect corrosion which may be absent in the laboratory test. Some examples are:- Splash- High temperature- Road blast- Mud packing- Water poolingThe laboratory test method may be altered in order to consider these or other environmental factors with the concurrence of the design engineer and the Corrosion Prevention Group, Body Materials Engineering.Laboratory testing is not permitted in the PV phase because the influence of component location on the vehicle must be included in the test.Results of full-vehicle corrosion testing supercede those of laboratory corrosion testing.3.4 Continuing Conformance (CC) or Quality Control TestingCC or quality control testing shall be based upon the requirements defined within the specified DaimlerChrysler standards (MS or PS) or other industry specifications. Performance testing done prior to the CC phase demonstrates that the chosen materials and processes fulfill the functional requirements of a particular item in a particular application. CC testing demonstrates continuing conformance of the materials and processes to the requirements of their specifications. Such requirements may be environmental tests such as resistance to salt spray or humidity. It is important to recognize that these are characterization tests that DO NOT DIRECTLY CORRELATE TO IN-SERVICE CORROSION PERFORMANCE. Refer to CS-9801 for general quality requirements.4.0 CORROSION TESTING - SPECIFIC REQUIREMENTSBecause corrosion severity varies with component location on the vehicle, five groups have been defined to facilitate specification of the appropriate test requirements. The acceptance criteria for the following test requirements shall be as specified in Section 3.0. Where both laboratory and full-vehicle test requirements are given, the tests shall be considered as alternates, although the full-vehicle test shall be the preferred method. The following test requirements are summarized in Table 1.NOTE: Certain exceptions to the following test requirements appear in section 5.6 of this standard.4.1 Systems or components that are located on the exterior surface or directly on the underbody of the vehicle.4.1.1 One year appearance requirement (if applicable; see Section 2.0)- Laboratory testing: 15 cycles SAE J2334 – immersion method- PG testing: 3 weeks LP-461H-1174.1.2 Five year appearance requirement (if applicable; see Section 2.0)- Laboratory testing: 60 cycles SAE J2334 – immersion method- PG testing: 12 weeks LP-461H-1174.1.3 Ten year functional requirement- Laboratory testing: 120 cycles SAE J2334 – immersion method- PG testing: 24 weeks LP-461H-1174.1.4 Fifteen year functional requirement (if required)- Laboratory testing: 180 cycles SAE J2334 – immersion method- PG testing: 36 weeks LP-461H-1174.2 Systems or components that are located on secondary exterior surfaces, such as door jambs, etc., or in the underhood area, but not directly exposed to road spray and splash;4.2.1 One year appearance requirement (if applicable; see Section 2.0)- Laboratory testing: 8 cycles SAE J2334 – spray method- PG testing: 3 weeks LP-461H-1174.2.2 Five year appearance requirement (if applicable; see Section 2.0)- Laboratory testing: 30 cycles SAE J2334 – spray method- PG testing: 12 weeks LP-461H-1174.2.3 Ten year functional requirement- Laboratory testing: 60 cycles SAE J2334 – spray method- PG testing: 24 weeks LP-461H-1174.2.4 Fifteen year functional requirement (if required)- Laboratory testing: 90 cycles SAE J2334 – spray method- PG testing: 36 weeks LP-461H-1174.3 Systems or components that are located within the cavities of doors with moving glass.4.3.1 Appearance requirements – NOT APPLICABLE4.3.2 Ten year functional requirement- Laboratory testing: 60 cycles SAE J2334 – spray method- PG testing: 24 weeks LP-461H-1174.4 Systems or components that are located on the floor of the interior of the vehicle. NOTE: These are minimum requirements, which may be extended or increased in the case of convertible, Jeep(TM), or other activity vehicles at the initiative of the releasing group.4.4.1 One year appearance requirement (if applicable; see Section 3.0)- Laboratory testing: 5 cycles SAE J2334 – spray method- PG testing: Not applicable4.4.2 Five year appearance requirement (if applicable; see Section 3.0)- Laboratory testing: 20 cycles SAE J2334 – spray method- PG testing: Not applicable4.4.3 Ten year functional requirement- Laboratory testing: 40 cycles SAE J2334 – spray method- PG testing: Not applicable4.5 Systems or components that are located within the vehicle interior, but not on the floor. NOTE: These are minimum requirements, which may be extended or increased in the case of convertible, Jeep(TM), or other activity vehicles at the initiative of the releasing group.4.5.1 One year appearance requirement- Laboratory testing: Humidity test per ASTM D1735, 24 hours- PG testing: Not applicable4.5.2 Five year appearance requirement- Laboratory testing: Humidity test per ASTM D1735, 120 hours- PG testing: Not applicable4.5.3 Ten year functional requirement- Laboratory testing: Humidity test per ASTM D1735, 240 hours- PG testing: Not applicable4.6 Special CasesThe SAE J2334 and LP-461H-117 test methods are either not sufficient or not appropriate for the following components;- Brake rotors- Aluminum heat exchangers- Stainless steel underhood and underbody components- Aluminum body panels- Decorative trim- ExhaustAny corrosion requirements that appear within applicable DaimlerChrysler performance standards (PF) for these components take precedence. Contact the Corrosion Prevention Group, Body Materials Engineering for specific advice regarding these components.TABLE 1: CORROSION TEST REQUIREMENTSpara. designlevel criteria laboratorytestduration Full-vehicletestduration MAXIMUMcorrosion rating4.1 ED, DV 1 yr.appearance (1)J2334(immersion)15 cy. CPG 3 wks. class I: 0class II: 15yr. appearance(1) J2334(immersion) 60 cy. CPG 12 wks. class I: 1class II: 210 yr. function J2334(immersion)120 cy. CPG 24 wks. 415yr. function(1) J2334(immersion)180 cy. CPG 36 wks. 4PV 1yr.appearance N/A N/A CPG 3 wks. class I: 0class II: 15yr. appearance N/A N/A CPG 12 wks. class I: 1class II: 210 yr. function N/A N/A CPG 24 wks. 415yr.function(1)N/A N/A CPG 36 wks. 44.2 ED, DV 1 yr.appearance(1) J2334(spray)*** 8 cy.***CPG 3wks. 15yr. appearance(1) J2334(spray)30 cy. CPG 12 wks. 210 yr. function J2334(spray)60 cy. CPG 24 wks. 415yr. function(1) J2334(spray)90 cy. CPG 36 wks. 4PV 1yr.appearance(1)N/A N/A CPG 3 wks. 1 5yr.appearance(1)N/A N/A CPG 12 wks. 2TABLE 1: CORROSION TEST REQUIREMENTSpara. designlevelcriteria laboratorytestduration Full-vehicletestduration MAXIMUMcorrosion rating10 yr. function N/A N/A CPG 24 wks. 415yr.function(1)N/A N/A CPG 36 wks. 44.3 ED, DV 1 yr.appearanceN/A N/A N/A N/A n.a.5yr.appearanceN/A N/A N/A N/A n.a.10 yr. function J2334(spray)60 cy. CPG 24 wks. 4PV 1yr.appearanceN/A N/A N/A N/A n.a.5yr.appearanceN/A N/A N/A N/A n.a.10 yr. function N/A N/A CPG 24 wks. 44.4 ED,DV,PV 1 yr.appearance(1) J2334(spray)5 cy. N/A N/A Class I: 0Class II: 15yr. appearance(1) J2334(spray)20 cy. N/A N/A Class I: 1Class II: 210 yr. function J2334(spray)40 cy. N/A N/A 44.5 ED,DV,PV 1 yr.appearance(1) Humidity 24 hrs. N/A N/A Class I: 0Class II: 15yr. appearance(1) Humidity 120 hrs. N/A N/A Class I: 1Class II: 210 yr. function Humidity 240 hrs. N/A N/A 4 NOTE 1: Only if requiredJ2334 (immersion): Cyclic corrosion test per SAE J2334 with full immersion in salt water solutionJ2334 (spray): Cyclic corrosion test per SAE J2334 with salt water solution by hand sprayerCPG: DCC Chelsea, MI Proving Grounds full-vehicle corrosion test per LP 461H-117Humidity: Humidity test per ASTM D17355.0 DEFINITIONSThe corrosion performance of an item under corrosion test is assessed according to the rating system described in Table 2.TABLE 2: CORROSION RATING SYSTEMRATING DEFINITION0 Nocorrosion1 Light paint blistering and / or light rust, powder or blush (discoloration of surface).2 Medium paint blistering and / or medium rust; light scale (irregular surface with pieces or layers of oxide that do not fall off with light tapping).3 Heavy paint blistering and / or heavy rust (scabbing), rust bleed; medium scale / flake (small pieces of oxide that fall off with light tapping).4 Severe red rust, scabbing, rust bleed, paint peeling; heavy flake (layers or chunks of oxide that fall off with light tapping).TABLE 2: CORROSION RATING SYSTEMRATING DEFINITION5 Perforation / broken / loss of function.Road Blast: The abrasion or erosion due to stones and grit thrown by the tires of the vehicle. Road blast can significantly add to the effects of corrosion in causing loss of function.ED, DV, PV, CC: The various stages of the product creation process; defined further in DCC “PAP4CDS manual”.SO: The program vehicle build level characterized by utilization of design-intent materials and processes, but not necessarily production tooling; defined further in DCC “PAP4CDS manual”.6.0 GENERAL INFORMATIONThree asterisks “***” after the section/paragraph header denotes multiple technical changes to the section/paragraph. A triple asterisk before and after a string of text (***text***) identifies a single change.Certain important information relative to this standard has been included in separate standards. To assure the items submitted meet all of DaimlerChrysler requirements, it is mandatory that the requirements in the following standards be met.CS-9800 - Application of this standard, the subscription service, and approved sourcesCS-9003 - Regulated substances and recyclabilityWithin Engineering Standards, the Regulatory (Government-mandated) requirements are designated by <S>, <E> and <H> which correspond to Safety, Emission and Homologation Shields respectively. The DCC-mandated requirements are designated by <D>, <A> and <T> and correspond to the Diamond, Appearance and Traceability symbols respectively.For specific information on this document, please refer to the contact person shown in the "Publication Information" Section of this document. For general information on obtaining Engineering Standards and Laboratory Procedures, see CS-9800 or contact the Engineering Standards Department atengstds@.7.0 REFERENCESCS-9800CS-9801CS-9003LP 461H-117PF-8500Chrysler Corporation Product Assurance Planning Manual (84-231-1232)Chrysler, Ford, and General Motors manual, Quality System Requirements QS - 9000 DaimlerChrysler, “Product Assurance Testing” manualASTM D1735SAE Recommended Practice J2334, “Cosmetic Corrosion Test”8.0 ENGINEERING APPROVED SOURCE LISTNot applicable.9.0 PUBLICATION INFORMATIONContact/Phone No: M.L.Stephens, (248) 576-7452Alternate Contact/Phone No: A.K. Desai, (248) 576-7455Dept. Name & Dept. No. /Tech Club/Organization: Body Materials Engineering, Dept. 5820 / Scientific Laboratories & Proving GroundsDate Standard Originally (Initially Issued): 2000-12-07Date Published: 2004-06-22Change Notice:Description of Change: Editorial; corrected typographical error in Table 1.# # # # #。