汽车塑料外饰件的设计文档
浅谈汽车外饰塑料件设计缺陷
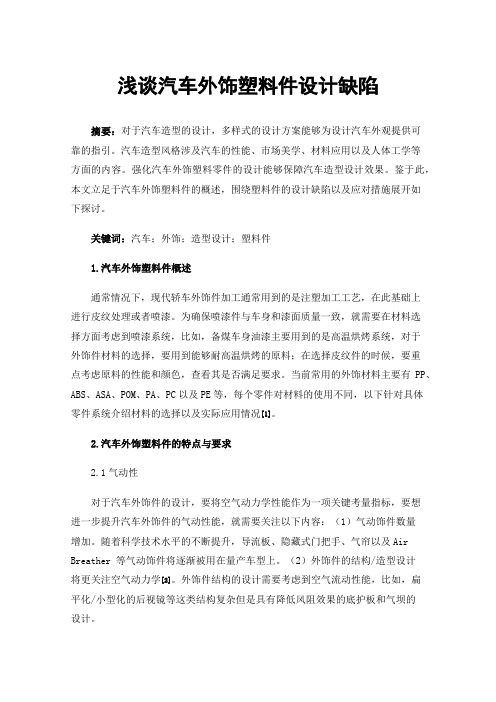
浅谈汽车外饰塑料件设计缺陷摘要:对于汽车造型的设计,多样式的设计方案能够为设计汽车外观提供可靠的指引。
汽车造型风格涉及汽车的性能、市场美学、材料应用以及人体工学等方面的内容。
强化汽车外饰塑料零件的设计能够保障汽车造型设计效果。
鉴于此,本文立足于汽车外饰塑料件的概述,围绕塑料件的设计缺陷以及应对措施展开如下探讨。
关键词:汽车;外饰;造型设计;塑料件1.汽车外饰塑料件概述通常情况下,现代轿车外饰件加工通常用到的是注塑加工工艺,在此基础上进行皮纹处理或者喷漆。
为确保喷漆件与车身和漆面质量一致,就需要在材料选择方面考虑到喷漆系统,比如,备煤车身油漆主要用到的是高温烘烤系统,对于外饰件材料的选择,要用到能够耐高温烘烤的原料;在选择皮纹件的时候,要重点考虑原料的性能和颜色,查看其是否满足要求。
当前常用的外饰材料主要有PP、ABS、ASA、POM、PA、PC以及PE等,每个零件对材料的使用不同,以下针对具体零件系统介绍材料的选择以及实际应用情况[1]。
2.汽车外饰塑料件的特点与要求2.1气动性对于汽车外饰件的设计,要将空气动力学性能作为一项关键考量指标,要想进一步提升汽车外饰件的气动性能,就需要关注以下内容:(1)气动饰件数量增加。
随着科学技术水平的不断提升,导流板、隐藏式门把手、气帘以及Air Breather 等气动饰件将逐渐被用在量产车型上。
(2)外饰件的结构/造型设计将更关注空气动力学[2]。
外饰件结构的设计需要考虑到空气流动性能,比如,扁平化/小型化的后视镜等这类结构复杂但是具有降低风阻效果的底护板和气坝的设计。
2.2装饰性Panoz 与 Feynlab 合作将一种记忆聚合物涂层应用于油漆中,这种材料的使用能够在受热时恢复原始结构,从而将表面划痕除去。
这种涂层通常用来处理漩涡痕迹或者轻微划痕。
车漆自修复技术用到的是一种特殊的涂层保护剂,这种密度较高的透明合成树脂,将其以网状结构涂在汽车油漆外层,能够增强汽车表层抗划伤能力,即便出现划痕,基于超强的网状树脂也能够快速修复划痕。
汽车塑料件设计要求方案
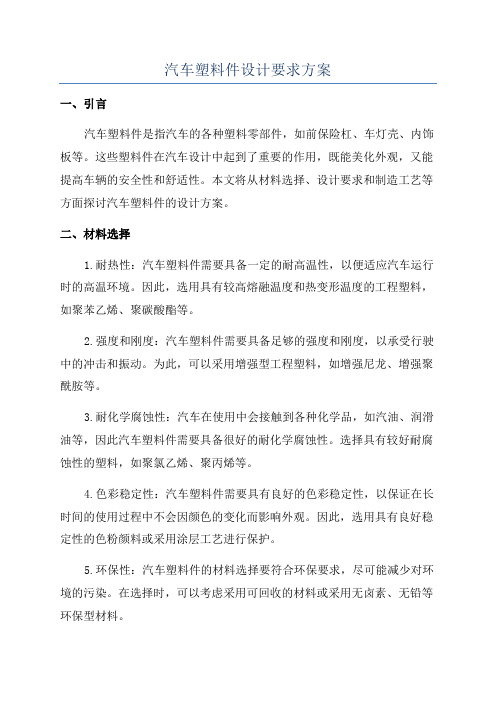
汽车塑料件设计要求方案一、引言汽车塑料件是指汽车的各种塑料零部件,如前保险杠、车灯壳、内饰板等。
这些塑料件在汽车设计中起到了重要的作用,既能美化外观,又能提高车辆的安全性和舒适性。
本文将从材料选择、设计要求和制造工艺等方面探讨汽车塑料件的设计方案。
二、材料选择1.耐热性:汽车塑料件需要具备一定的耐高温性,以便适应汽车运行时的高温环境。
因此,选用具有较高熔融温度和热变形温度的工程塑料,如聚苯乙烯、聚碳酸酯等。
2.强度和刚度:汽车塑料件需要具备足够的强度和刚度,以承受行驶中的冲击和振动。
为此,可以采用增强型工程塑料,如增强尼龙、增强聚酰胺等。
3.耐化学腐蚀性:汽车在使用中会接触到各种化学品,如汽油、润滑油等,因此汽车塑料件需要具备很好的耐化学腐蚀性。
选择具有较好耐腐蚀性的塑料,如聚氯乙烯、聚丙烯等。
4.色彩稳定性:汽车塑料件需要具有良好的色彩稳定性,以保证在长时间的使用过程中不会因颜色的变化而影响外观。
因此,选用具有良好稳定性的色粉颜料或采用涂层工艺进行保护。
5.环保性:汽车塑料件的材料选择要符合环保要求,尽可能减少对环境的污染。
在选择时,可以考虑采用可回收的材料或采用无卤素、无铅等环保型材料。
三、设计要求1.外观设计:汽车塑料件是汽车的重要组成部分,其外观设计要与整车风格相协调。
注重形状的流线化、曲线的柔和、比例的协调等,以提高整体的美观性。
2.强度和刚度:对于需要承受冲击的塑料件,要注重强度和刚度的设计,以确保其在受力时不会发生变形和破裂。
3.安装和拆卸便捷性:汽车塑料件需要便于安装和拆卸,以方便维修和更换。
因此,在设计时要考虑到拆卸和装配的方便性,并采用合适的固定件和连接件。
4.密封性:对于需要防水和密封的汽车塑料件,要注重密封性的设计,以避免水汽渗入和气体泄漏。
5.耐久性:汽车塑料件需要具备一定的耐久性,以承受车辆长期使用带来的磨损和老化。
因此,在设计时要考虑到材料的耐候性和耐磨性,并采取适当的保护措施。
汽车装饰件塑料模具设计论文(doc 39页)
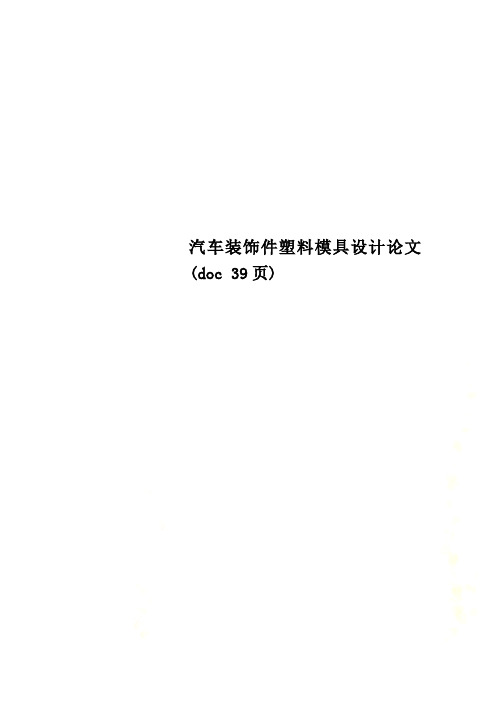
汽车装饰件塑料模具设计论文(doc 39页)第一章绪论1.1 塑料成型模具在工业生产中的地位在现代制造业的发展进程中,模具的地位及其重要性日益受到人们的重视。
在塑料材料、和制品设计及加工工艺确定后,塑料模具的质量与产量具有决定性作用,模具成本对制品的成本也有很大影响。
在现代塑料制品生产中,合理的加工工艺、高效的设备和先进的模具,被称为塑料制品的“三大支柱”。
尤其是模具对于实现塑料制品的加工工艺要求、塑料使用要求及塑件外观的造型要求,都起着无可替代的作用。
1.2注塑模在国内外的发展随着全球经济的发展,新的技术革命不断取得新的进展和突破,技术的飞跃发展已经成为动世界经济增长的重要因素。
市场经济的不断发展,促使工业产品越来越向多品种、小批量、高质量、低成本的方向发展,为了保持和加强产品在市场上的竞争力,产品的开发周期、生产周期越来越短,于是对制造各种产品的关键工艺装备—模具的要求越来越苛刻。
一方面企业为追求规模效益,使得模具向着高速、精密、长寿命方向发展;另一方面企业为了满足多品种、小批量、产品更新换代快、赢得市场的需要,要求模具向着制造周期短、成本低的快速经济的方向发展。
计算机、激光、电子、新材料、新技术的发展,使得快速经济制模技术如虎添翼,应用范围不断扩大,类型不断增多,创造的经济效益和社会效益越来越显著。
在注塑模具方面,2006年,注塑模具比例进一步上升,热流道模具和气辅模具水平进一步提高,注塑模具在量和质方面都有较快的发展,我国最大的注塑模具单套重量已超过50吨,最精密的注塑模具精度已达到2微米。
在CAD/CAM 技术得到普及的同时,CAE技术应用越来越广,CAD/CAM/CAE一体化得到发展,模具新结构、新品种、新工艺、新材料的创新成果不断涌现,专利数量增多。
在模具产品结构改善和水平提高方面,软件所起的作用功不可没。
据了解,moldflow软件在提高我国注塑水平方面确实起到了很大的作用。
现在,用户对软件的集成化、智能化、网络化等方面的要求越来越高,相信moldflow软件能不断发展来满足用户的要求。
JT1-9902-2013汽车外饰塑料零件通用技术条件

汽车外饰塑料零件通用技术条件JT1-9902-2013共 4 页重庆长安汽车股份有限公司2013年3月12日汽车外饰塑料零件通用技术条件JT1-9902-2013编制 赖 礼 汇校核 陈 雷审定 王 晓批准 曹 渡更改记录规范编号制定/修订者制定/修订日期批准日期JT1-9902-2013 赖礼汇2013-3-11 曹渡2013-3-12JT1-9902-2013汽车外饰塑料零件通用技术条件1 范围本技术条件规定了前格栅、前罩装饰件、扰流板、防擦条、侧围护板、轮罩衬板、保险杠、三角窗外盖板、后牌照灯盖、发动机装饰罩盖等等外饰塑料零件的基本性能要求及试验方法。
本技术条件适用于长安汽车股份有限公司所开发的所有轿车车型。
2 规范性引用文件SAE J2527 汽车外饰材料加速老化实验标准:可控辐照度氙弧灯SJ-NW-15 塑料件涂装要求规范SJ-NW-16 塑料镀铬件性能要求规范SJ-NW-57 汽车塑料内饰件耐刮擦实验方法及结果判定SJ-NW-101 汽车塑料内饰件耐刮擦实验方法(划格法)3 要求3.1 除非另外规定,否则应符合本技术条件的要求,并按经规定程序批准的图样与技术文件制造。
喷漆零件除了满足本技术条件外,还应满足SJ-NW-15的要求。
电镀零件除了满足本技术条件外,还应满足SJ-NW-16的要求。
3.2 外观要求:所有零件外观应与经确认后的样品一致。
1)产品外观面不允许有裂纹、变形、银纹、波纹、烧焦、飞边、毛刺、气泡、浇口痕迹、顶杆印痕、熔接痕和收缩痕等不可接受表面缺陷。
2)喷涂或镀铬的产品,表面涂层或镀层均匀一致、色泽均匀,外观表面不允许有目视可见的麻点、起泡、漏镀、变色、脱落及其他不可接受缺陷。
3)产品A面上的分模线应小于0.1mm;非主视外观面分模线的痕迹小于0.2mm。
且必须经过长安公司技术部门的认可。
4)零件表面的颜色和花纹应与经规定程序批准的色板或样品一致。
皮纹要清晰、色泽均匀,皮纹类型、纹理方向、纹理深度以及皮纹范围应与长安公司所要求的一致,由于因脱模方向引起的非主要表面皮纹深度变化要均匀,不允许出现皮纹拉伤。
塑胶模具设计-汽车前保险杠
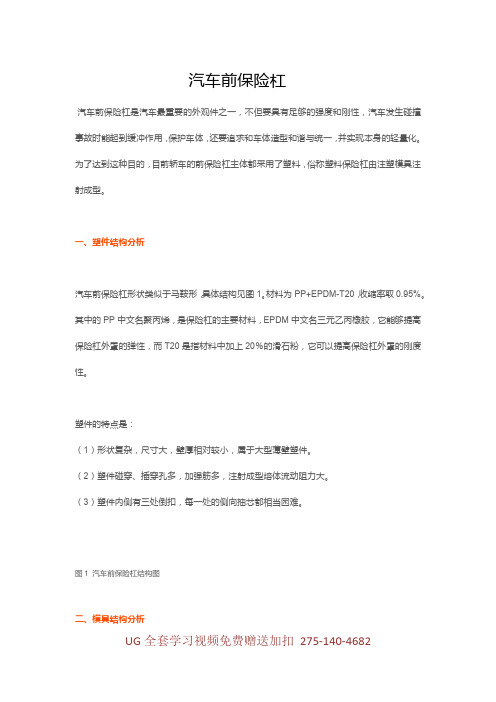
汽车前保险杠汽车前保险杠是汽车最重要的外观件之一,不但要具有足够的强度和刚性,汽车发生碰撞事故时能起到缓冲作用,保护车体,还要追求和车体造型和谐与统一,并实现本身的轻量化。
为了达到这种目的,目前轿车的前保险杠主体都采用了塑料,俗称塑料保险杠由注塑模具注射成型。
一、塑件结构分析汽车前保险杠形状类似于马鞍形,具体结构见图1。
材料为PP+EPDM-T20,收缩率取0.95%。
其中的PP中文名聚丙烯,是保险杠的主要材料,EPDM中文名三元乙丙橡胶,它能够提高保险杠外罩的弹性,而T20是指材料中加上20%的滑石粉,它可以提高保险杠外罩的刚度性。
塑件的特点是:(1)形状复杂,尺寸大,壁厚相对较小,属于大型薄壁塑件。
(2)塑件碰穿、插穿孔多,加强筋多,注射成型熔体流动阻力大。
(3)塑件内侧有三处倒扣,每一处的侧向抽芯都相当困难。
图1汽车前保险杠结构图二、模具结构分析前保险杠主体注塑模具采用内分型面,通过热流道,并由顺序阀控制进胶。
两侧倒扣采用大斜顶套横向斜顶加直顶的结构,最大外形尺寸2500×1560×1790mm,模具结构详见图2。
图2前保险杠注塑模具结构图1.定模固定板;2.承板;3.热流道板;4.定位圈;5.一级热射嘴;6.气阀;7.阀针;8.二级热射嘴;9.动模固定板;10.方铁;11.推杆固定板;12.推杆底板;13.支撑柱;14.动模方导柱;15.推杆;16.动模板;17.支撑脚;18.定模方导柱;19.定目板;20.斜推杆;21、29.转销;22、28.斜顶;23、34.导轨;24、27.动模镶件;25、26.直顶;30.斜推杆;31、39.护杆;32、33、40、41.导向柱;35、36、37.推杆;38.定位块;42.耐磨块;43.侧抽芯;44.弹簧;45.限位块1、成型零件设计本模具的3D图见图3,模具设计时采用了先进的内分型面技术,详见图4。
其优点是分型夹线隐藏在保险杠的非外观面上,在汽车上装配后看不到,不会影响外观。
JLYY-JT 191-06汽车内外饰塑料件通用技术条件
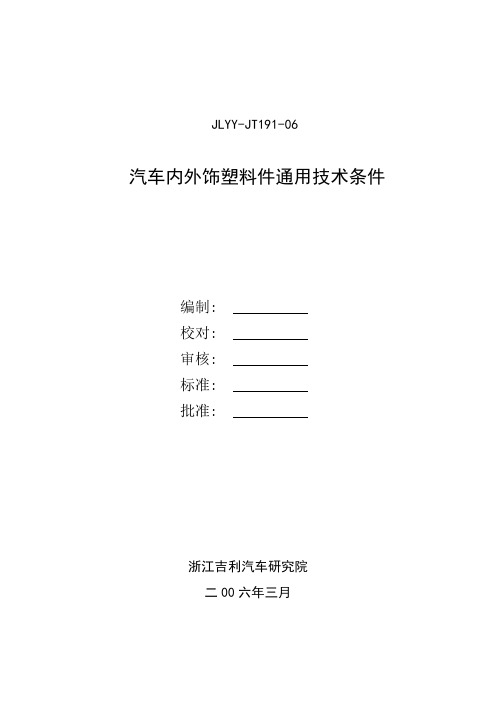
JLYY-JT191-06汽车内外饰塑料件通用技术条件编制:校对:审核:标准:批准:浙江吉利汽车研究院二00六年三月前言本标准对于吉利汽车塑料件的技术要求、试验方法做出具体规定。
本标准结合本企业的具体情况编制。
本标准由浙江吉利汽车研究院有限公司提出。
本标准由浙江吉利汽车研究院有限公司车身设计部负责起草。
标准主要起草人:王琪本标准首次发布日期:2006年4月1日;实施日期:2006年5月1日。
1范围本标准规定了塑料件(不包括涂层、电镀、发泡件)的要求、试验设备、仪器及环境、试验方法、检验规则、标记、运输及贮存。
本标准适用于乘用车产品的内外饰塑料件(以下简称产品)。
2规范性引用标准下列文件中的条款通过本标准的引用而成为本标准的条款。
凡是注日期的引用文件,其随后所有的修改单(不包括勘误的内容)或修改版均不适用于本标准,然而,鼓励根据本标准达成协议的各方研究是否可使用这些文件的最新版本。
凡是不注日期的引用文件,其最新版本适用于本标准。
GB/T 250-1995 评定变色用灰色样卡GB/T 3077-1999 合金结构钢GB 8410-1994 汽车内饰材料燃烧特性GB/T 16422.2-1999 塑料实验室光源暴露试验第2部分:氙弧灯JLYY-JT139-04 汽车塑料件及合成橡胶制品标记的规定JTYY-JT146-04 汽车内饰材料气味性试验方法3要求3.1 一般要求3.1.1在自然光线的阳光下产品的光泽应在样品的光泽等级范围之内。
3.1.2 零件的表面应没有污迹、划伤、裂纹、扭曲变形及表面皮纹磨损,也不应有任何影响装配和外观的缺陷。
3.1.3 产品的尺寸、公差、质量、纹理、颜色、标识、材料应按照图样要求。
3.2 性能要求性能要求按表1的规定。
4试验设备、仪器、环境4.1 试验设备4.1.1 环境箱:各个部位达到并维持与所规定的等级相一致的温度,而且符合规定的温度误差要求,最大相对湿度为20%。
在结构上,能够使样品在任何部位均不被热源直接辐射。
汽车塑料件设计要求方案
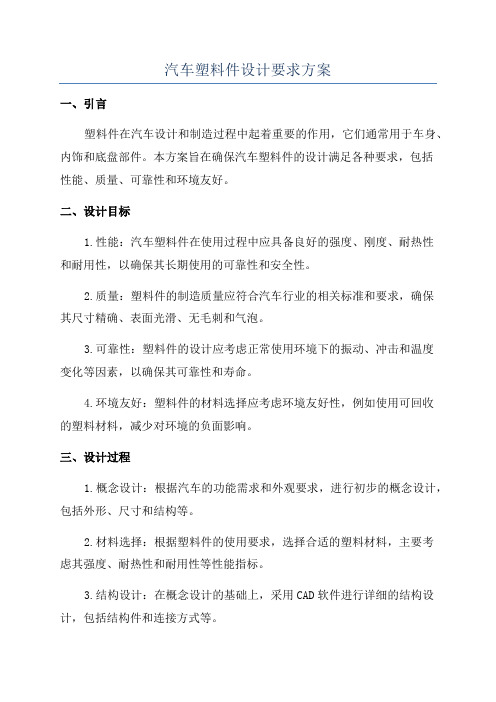
汽车塑料件设计要求方案一、引言塑料件在汽车设计和制造过程中起着重要的作用,它们通常用于车身、内饰和底盘部件。
本方案旨在确保汽车塑料件的设计满足各种要求,包括性能、质量、可靠性和环境友好。
二、设计目标1.性能:汽车塑料件在使用过程中应具备良好的强度、刚度、耐热性和耐用性,以确保其长期使用的可靠性和安全性。
2.质量:塑料件的制造质量应符合汽车行业的相关标准和要求,确保其尺寸精确、表面光滑、无毛刺和气泡。
3.可靠性:塑料件的设计应考虑正常使用环境下的振动、冲击和温度变化等因素,以确保其可靠性和寿命。
4.环境友好:塑料件的材料选择应考虑环境友好性,例如使用可回收的塑料材料,减少对环境的负面影响。
三、设计过程1.概念设计:根据汽车的功能需求和外观要求,进行初步的概念设计,包括外形、尺寸和结构等。
2.材料选择:根据塑料件的使用要求,选择合适的塑料材料,主要考虑其强度、耐热性和耐用性等性能指标。
3.结构设计:在概念设计的基础上,采用CAD软件进行详细的结构设计,包括结构件和连接方式等。
4.模具设计:根据结构设计的CAD模型,进行模具的设计和制造,确保塑料件的生产过程中能够精确复制设计要求。
5.实验验证:利用模具制备出样品进行实验验证,包括强度测试、耐热性测试和可靠性测试等,以确保设计要求的满足。
6.优化改进:根据实验结果,对设计进行优化改进,以提高塑料件的性能和可靠性。
四、质量控制1.原材料检验:对进货的塑料材料进行检验,包括外观、尺寸和性能测试等,确保原材料的质量符合设计要求。
2.生产过程控制:在塑料件生产过程中,采用严格的控制措施,确保良品率和尺寸精度的控制。
3.产品验收:对塑料件进行全面的验收,包括外观、尺寸和功能测试等,确保产品质量符合客户的要求。
4.售后服务:建立健全的售后跟踪服务体系,及时解决客户的问题和反馈,确保客户满意度。
五、环境友好1.材料选择:优先选择可回收的塑料材料,减少对环境的污染。
2.工艺改进:改进生产工艺,减少废料产生和能源消耗,提高生产效率。
汽车外饰件(塑料)总成技术条件
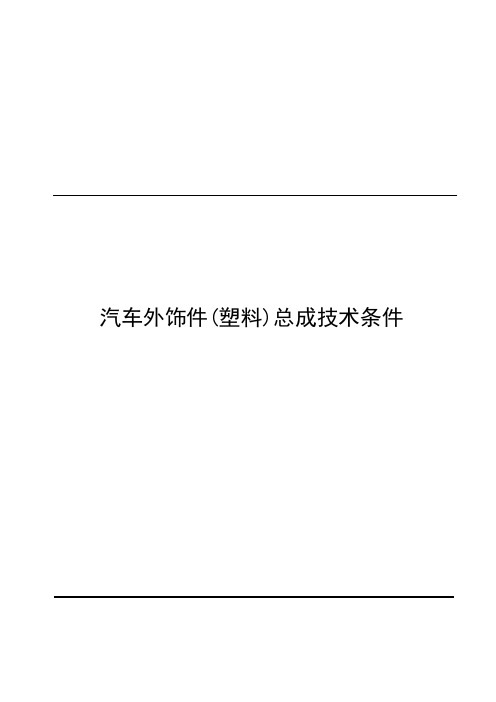
汽车外饰件(塑料)总成技术条件前言为满足设计、生产和检验的需要,保证产品质量,制定了本标准。
本标准根据有关国家标准和行业标准,同时参照国内外汽车生产企业的先进经验而编制的。
本标准规定了本公司设计开发的汽车塑料外饰件的技术要求、试验方法、检验规则、标志、包装、运输和贮存等内容。
汽车外饰件(塑料)总成技术条件1 范围本标准规定了汽车外饰件的技术要求、试验方法、检验规则、标志、包装、运输和贮存的内容。
本标准适用于本公司设计开发的汽车塑料外饰件总成(以下简称外饰件)。
2 引用标准下列标准所包含的条文,通过在本标准中引用而构成为本标准的条文。
本标准出版时,所示版本均为有效。
所有标准都会被修订,使用本标准的各方应探讨使用下列标准最新版本的可能性。
GB/T 1033—1986 塑料密度和相对密度试验方法GB/T 1040—1992 塑料拉伸性能试验方法GB/T 1634.1—2004 塑料负荷变形温度的测定第1部分:通用试验方法GB/T 1843—1996 塑料悬臂梁冲击试验方法GB/T 2828.1—2003 计数抽样检验程序第1部分:按接收质量限(AQL)检索的逐批检验抽样计划GB 8410—1994 汽车内饰材料阻燃特性GB/T 9341—2000 塑料弯曲性能试验方法GB/T 9342—1988 塑料洛氏硬度试验方法QC/T 15—1992 汽车塑料制品通用试验方法QC/T 17—1992 汽车零部件耐候性试验一般规则QC/T 625—1999 汽车用涂镀层和化学处理层Q/J B070—2006 汽车塑料件涂漆技术条件Q/J B071—2006 汽车产品零部件标识规定Q/J B124—2006 汽车SMC件总成技术条件3主要外饰件材料选用要求3.1 汽车主要外饰件材料选用(推荐)见表1。
表1 汽车主要外饰件材料选用(推荐)4 技术要求4.1 外饰件应按经规定程序批准的图样、数学模型及技术文件制造,并应符合本标准的规定。
汽车内外饰塑料产品结构设计介绍
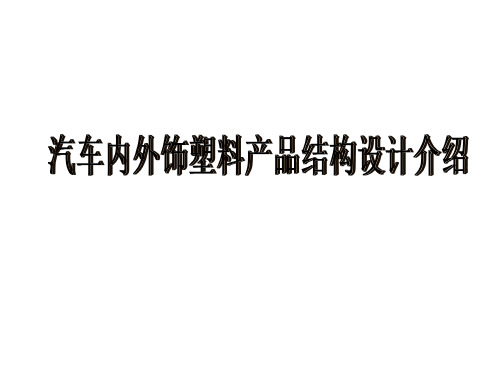
第一章 概述
“细节决定成败”已经成为大家的共识。对于汽车来说,细节 更是决定着产品的品质、品牌和品位,内外饰就是其中的“细节” 之一。因为内外饰是顾客购车或使用最先、最直接感知的部分,其 设计水平、做工质量很大程度上影响着顾客的购车决定。
内饰—仪表板
普力马
外饰—前脸
过去相当长的一段时间里,汽车内外饰都只是作为汽车钣金 装饰件,20世纪80年代以来,随着人们对节能、安全、舒适的要 求不断提高,汽车内外饰设计在整车轻量化,主、被动安全等方 面占据越来越重要的地位。
开模方向
脱模方向确定后,产品的加强筋、卡扣、凸起等结构尽可能设 计成与开模方向一致,以避免抽芯减少拼缝线,延长模具寿命。
一、脱模方向 (2)脱模方向原则
内饰A面 内孔脱模方向
内孔脱模以尺寸小的一端为准, 以保证与内孔配合零件的尺寸 及配合间隙,脱模方向为尺寸 扩大的方向取得
外形尺寸以大端为准,脱模斜 度向尺寸缩小的方向取得,保 证零件与周围的配合间隙,同 时要保证零件的工艺美观要求;
分模线
不能放到表 面上
对于具体的产品,其分型面的选择和设计存在多种方案,因 此必须遵守一定的规则才能选择和设计出合理的分型面,并简化 模具的结构降低成本。而对于不同的产品其分型面的选择和设计 还需要根据具体的情况作针对性的分析,并且不一定都能满足上 述的规则,因此应该根据设计保证主要的方面作必要变更。
二、分型线
(3)设计原则
① 保证产品的外观质量和精度。 ② 保证模具零件成型时的刚性。 ③ 分型面应该有利于侧向抽芯。 ④ 分型面应该有利于塑件脱模。 ⑤ 分型面的选择和设计应该有利于加工制造。 如: 1.主分型面为平面的情况,分型面设计时 要考虑方便于磨床加工。2.主分型面为复杂曲面, 分型面设计时要考虑方便于NC加工,避免EDM加工。
某车型的塑料侧围外板设计

1 侧围外板功能分析
侧I 吲 外 板最 童 要的功 能之一 就 是体现 车辆 侧
域 的造 特 I,冈此 美学功 能 为其最 重 要 的
A 往 装饰 板
装 饰板 ( 前
; 侧 窗玻 璃
功能 之 一 , 婴 涉及造 特征 的体现 以 及各部 件 的 良好 的遮蔽 、 配搭 接美 观等 ;侧 罔外 板是 乘 员感 乍辆 的第 一 部件 , 也是 乘员 卜下 车时最 易触
碰部 件 , 此 *要 一定 的 刚度 ,避免造 成 按 压
图 1塑 料侧 围外板 分件示 意
3 塑料侧围外板材料选择
刚度 小足造 成 乘 员抱 怨 ,因此 支撑 刚度 为侧 外 扳的 乃一
塑料侧 『 韦 1 外 板 在 材 料 选 择 方而 需 要 兼 顾 刚 功能 ;侧 罔外 板下 部 门槛 区域足 乘 性 、成本 、注 塑 艺 、抗 老化和 尺寸稳 定 性等 ; 员I 下 乍l J 1 『 弈 易踩踏 部 位 ,因此需 具 备 的一定 的 常规 P P 材料具 有 良好 的注 流 动性 ,同时 也具 备
( )、A 朴 装饰板 ( 后 )和B 柱 装饰板 ;对 门槛 合 美观 ,采 用大 间隙 配合 ,通 过加 装装 饰条进 行 韦 1 外 板和 域 因为踩 刚度 要求 较高 , 时 该 区域 同样 卡 H 二 次遮 蔽 ;对于 配合 问 隙敏感 域 如侧 『 刈 宽度较 小 , 此拆 分为侧 包 同装饰 板 ;最后 形 后 保 险杠 等 ,为保 征间隙 面差 和 同定 可 靠性 ,通 成侧 结 构 f 最 大 的部 件 为后 侧 同装饰 板 。符部 过设 置 独 安装 支架将 塑料 侧 同外 板 的翻边 和保
汽车内外饰设计_1
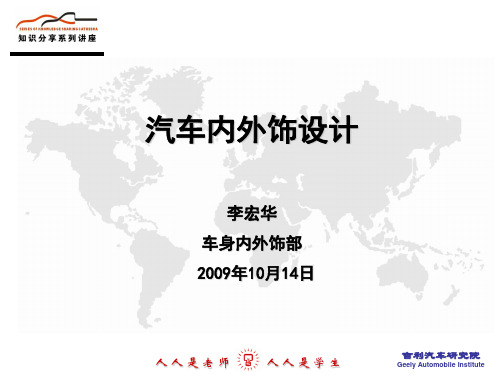
注:红色标注部分是 与内外饰相关的。
13
吉利汽车研究院
Geely Automobile Institute
四、内外饰常用材料及工艺
内外饰常用材料及工艺:
零部件
仪表板
车门 侧围 顶盖
地毯 行李舱隔板
装饰板
材料 PP+EPDM-TD20 PVC表皮+PU发泡+(PP+EPDM-TD20) ABS/PVC表皮+PU发泡+(PP+EPDM-TD20)
工艺 注塑成型 搪塑成型 吸塑成型 注塑成型 注塑成型 模压成型
模压成型
模压成型
吉利汽车研究院
Geely Automobile Institute
四、内外饰常用材料及工艺
零部件 行李舱左、右侧装饰板和行
李舱门内装饰板
行李舱地毯 备胎盖板
后围内装饰板 背门
前/后保险杠 散热器面罩
缓冲块 前/后保险杠支架 后保险杠装饰板
一、汽车内外饰简介
8 9 10 11 12
17
16
15
14
13
4
序
名
号
称
8 左侧围内饰装置
9
顶盖内饰装置
10 右侧围内饰装置
11 右后车门内饰装置
12 行李舱内饰装置
13 左后车门内饰装置
14 左前车门内饰装置
15
地毯内饰装置
16 右前车门内饰装置
17 发动机舱内饰装置
吉利汽车研究院
Geely Automobile Institute
15
材料 PE/PET 两厢车:改性PP(如PP/PE) PE/PET纤维毡 硬质板材,如中密度板 PP/PE或者PP+EPDM-TD20 PP/PE或者PP+EPDM-TD20 PP+EPDM-TD10
汽车外饰烫印塑料件设计开发
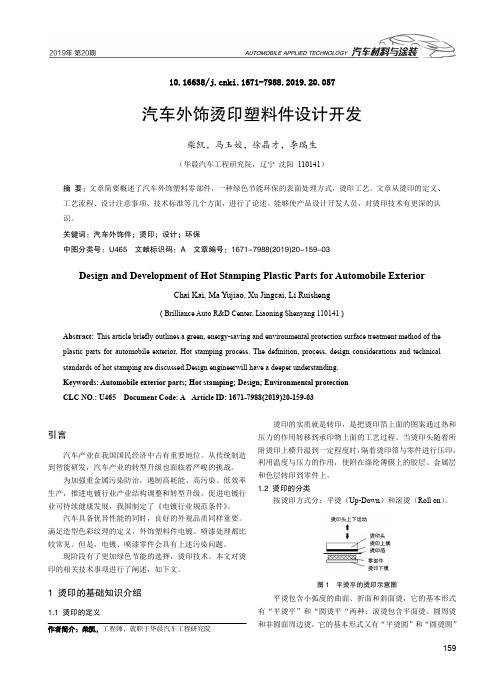
15910.16638/ki.1671-7988.2019.20.057汽车外饰烫印塑料件设计开发柴凯,马玉姣,徐晶才,李瑞生(华晨汽车工程研究院,辽宁 沈阳 110141)摘 要:文章简要概述了汽车外饰塑料零部件,一种绿色节能环保的表面处理方式,烫印工艺。
文章从烫印的定义、工艺流程、设计注意事项、技术标准等几个方面,进行了论述。
能够使产品设计开发人员,对烫印技术有更深的认识。
关键词:汽车外饰件;烫印;设计;环保中图分类号:U465 文献标识码:A 文章编号:1671-7988(2019)20-159-03Design and Development of Hot Stamping Plastic Parts for Automobile ExteriorChai Kai, Ma Yujiao, Xu Jingcai, Li Ruisheng( Brilliance Auto R&D Center, Liaoning Shenyang 110141 )Abstract: This article briefly outlines a green, energy-saving and environmental protection surface treatment method of the plastic parts for automobile exterior, Hot stamping process. The definition, process, design considerations and technical standards of hot stamping are discussed.Design engineerwill have a deeper understanding. Keywords: Automobile exterior parts; Hot stamping; Design; Environmental protection CLC NO.: U465 Document Code: A Article ID: 1671-7988(2019)20-159-03引言汽车产业在我国国民经济中占有重要地位。
CVTC 52020-2012 外饰塑料件技术要求

上汽商用车技术中心企业标准CVTC 52020-2012外饰塑料件技术要求Performance requirements for exterior plastic parts2012-12-30发布 2012-12-30实施 上汽商用车技术中心标准化技术委员会发布CVTC 52020-2012前 言本标准按照GB/T 1.1—2009给出的规则起草。
本标准由上海汽车集团股份有限公司商用车技术中心车身及造型部提出。
本标准由上海汽车集团股份有限公司商用车技术中心标准化技术委员会归口。
本标准起草部门:车身及造型部。
本标准主要起草人:宁贵欣CVTC 52020-2012外饰塑料件技术要求警告:使用本标准的人员应有正规实验室工作的时间经验。
本标准并没有指出所有可能的安全问题。
使用者有责任采取适当的安全和健康措施,并保证符合国家有关法规规定的条件。
1 范围本标准规定了汽车外饰塑料零件的试验准备、技术要求及试验方法以及在图纸及文件中的表示。
本标准适用于上汽商用车技术中心开发设计的车辆上所用的外饰塑料零件。
注:汽车外饰塑料零件包括外饰总成件或者各种金属件、装饰件或者功能件中的塑料子零件以及塑料组成部分。
对于需要进行表面处理(喷漆、电镀等)塑料零件不需要进行本标准中所有试验。
各种表面处理的技术要求参见相关的表面处理标准。
本标准不能替代法律法规。
2规范性引用文件下列文件对于本文件的应用是必不可少的。
凡是注日期的引用文件,仅注日期的版本适用于本文件。
凡是不注日期的引用文件,其最新版本(包括所有的修改单)适用于本文件。
ASTM D523 镜面光泽度试验方法ISO 4892-1 塑料实验室光源暴晒方法ISO 4892-2 塑料实验室光源暴晒方法ISO 7724-1 色漆和清漆颜色测量方法SAE J1545 外饰件颜色测量方法SAE J2527 汽车外饰材料加速老化试验方法3试验准备3.1 试验设备3.1.1 设备标定所有的试验设备应该能够正常工作并在标定的有效期内。
车辆塑料外壳设计方案
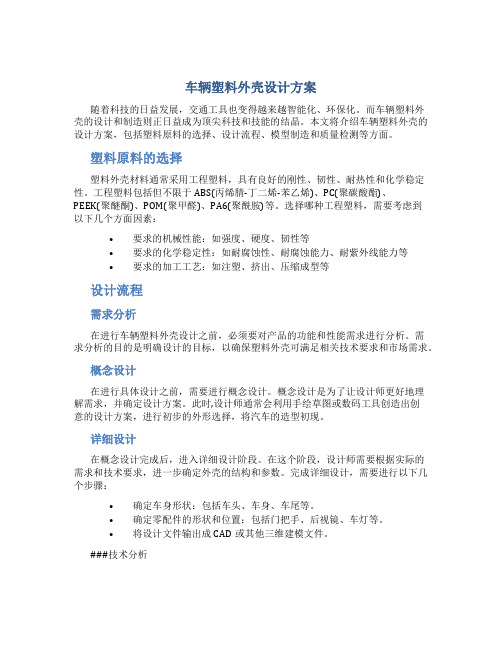
车辆塑料外壳设计方案随着科技的日益发展,交通工具也变得越来越智能化、环保化。
而车辆塑料外壳的设计和制造则正日益成为顶尖科技和技能的结晶。
本文将介绍车辆塑料外壳的设计方案,包括塑料原料的选择、设计流程、模型制造和质量检测等方面。
塑料原料的选择塑料外壳材料通常采用工程塑料,具有良好的刚性、韧性、耐热性和化学稳定性。
工程塑料包括但不限于ABS(丙烯腈-丁二烯-苯乙烯)、PC(聚碳酸酯)、PEEK(聚醚酮)、POM(聚甲醛)、PA6(聚酰胺)等。
选择哪种工程塑料,需要考虑到以下几个方面因素:•要求的机械性能:如强度、硬度、韧性等•要求的化学稳定性:如耐腐蚀性、耐腐蚀能力、耐紫外线能力等•要求的加工工艺:如注塑、挤出、压缩成型等设计流程需求分析在进行车辆塑料外壳设计之前,必须要对产品的功能和性能需求进行分析。
需求分析的目的是明确设计的目标,以确保塑料外壳可满足相关技术要求和市场需求。
概念设计在进行具体设计之前,需要进行概念设计。
概念设计是为了让设计师更好地理解需求,并确定设计方案。
此时,设计师通常会利用手绘草图或数码工具创造出创意的设计方案,进行初步的外形选择,将汽车的造型初现。
详细设计在概念设计完成后,进入详细设计阶段。
在这个阶段,设计师需要根据实际的需求和技术要求,进一步确定外壳的结构和参数。
完成详细设计,需要进行以下几个步骤:•确定车身形状:包括车头、车身、车尾等。
•确定零配件的形状和位置:包括门把手、后视镜、车灯等。
•将设计文件输出成CAD或其他三维建模文件。
###技术分析在进行详细设计时,还需要对设计方案进行技术分析,以保证这些设计最终可以顺利实现并符合相应的技术标准。
这些技术分析包括:•结构分析和强度分析。
•分析塑料是否可以承受设计要求的负荷和应力。
•检查各个组件是否与其他系统相兼容。
模型制造完成设计后,设计师需要将三维模型文件传到模型厂商处进行加工。
生产车辆塑料外壳需要进行多个步骤,包括模型制造、注塑成型、后处理和表面处理等。
车身注塑件设计指南

车身注塑件设计指南目次前言 (III)1 范围 (1)2 规范性引用文件 (1)3 定义 (1)4 注塑件及其工艺概述 (1)4.1 注塑件简述 (1)4.2 注射成型简述 (2)4.3 注塑模具简述 (2)5 注塑件设计程序和原则 (2)5.1 塑料制品设计的一般程序 (2)5.2 塑料制品设计的一般原则 (3)5.3 车身注塑件材料的选用原则 (3)6 车身注塑件中典型结构的设计要点和工艺特点 (4)6.1 壁厚设计 (4)6.2 主出模方向和脱模角度确定 (8)6.3 模具分型面位置选择 (10)6.4 加强筋和支撑结构设计 (14)6.5 凸台(柱位) (18)6.6 圆角 (20)6.7 孔 (21)6.8 侧面凸凹和侧孔 (24)6.9 嵌件 (27)7 注塑件与车身的连接方式 (34)7.1 塑料件与车身钣金件的连接方式 (34)7.2 塑料件与塑料件的连接方式 (36)8 注塑件尺寸公差 (38)8.1 公差等级表 (38)8.2 公差等级选用 (38)参考文献 (39)附录A (规范性附录) 注塑件尺寸公差 (40)前言为了对公司车身内外饰设计开发中注塑件的设计提供参考,特编制此设计指南。
本设计指南的编制来源于参考文献以及公司多年积累的设计经验,并参照国内外汽车设计公司及汽车生产企业的先进经验编制而成的,规定了车身注塑件的设计特点。
由于车身注塑件用途、结构形式、选用材料千差万别,工艺水平也在不断提高,文中部分推荐参数将会有所不同,因此在设计过程中,具体的设计方法还需要工程师斟酌思考。
本指南适用于各种类型汽车的注塑件设计。
本指南由公司产品管理部提出并归口。
本指南起草单位:车身设计部。
车身注塑件设计指南1 范围本指南从注塑工艺及模具方面,结合内外饰件在车身上的安装特点进行阐述,提出车身注塑件设计时所要注意的工艺、结构要求以及对注塑件设计的限制。
本指南适用于车身内外饰中的注塑件设计,供设计时参考。
- 1、下载文档前请自行甄别文档内容的完整性,平台不提供额外的编辑、内容补充、找答案等附加服务。
- 2、"仅部分预览"的文档,不可在线预览部分如存在完整性等问题,可反馈申请退款(可完整预览的文档不适用该条件!)。
- 3、如文档侵犯您的权益,请联系客服反馈,我们会尽快为您处理(人工客服工作时间:9:00-18:30)。
汽车塑料外饰件的设计
二.汽车外饰件简介
汽车外饰件主要指前后保险杠、轮口、进气格栅、散热器面罩、防擦条等通过螺栓和卡扣或双面胶连接在车身上的部件。
在车身外部主要起装饰保护作用,及开启等功能。
汽车外饰件在车身上主要位置及大致形状见图一。
1.前保险杠,后保险杠,散热器面罩,前后轮口,侧饰条,防擦条,后视镜,进气格栅,背门饰板,车门外开手柄,扰流板,行李箱手柄
三.汽车塑料外饰件设计标准
由于汽车的特殊功能,外饰件设计必须坚持标准化,系列化,通用化的“三化”设计原则,同时满足合理性,先进性,维修方便性,可靠性,经济性,制造工艺性“六性”要求。
3.1产品“三化”设计
根据设计车型将要投放国家地区的不同,设计过程中必须全面贯彻执行当地的法规标准。
在造型设计之初产品设计师须学习了解相关法规标准并以此为依据进行设计。
这主要包括前保险杠上牌照安装孔间距尺寸规定,是否需欲留雾灯安装孔,外部突出物表面圆角及开口尺寸等相关要求。
另外有关散热器面罩迎风面积是否满足发动机,空调制冷要求,需在设计发布前得到相关部门认可。
充分考虑系列化产品的发展,零件安装固定尽量采用统一的螺栓螺母及卡扣等连接件,或通用其他车型的固定件,提高零件通用化程度,保证维修安装的方便性。
3.2材料的确定
3.2.1材料种类确定
塑料的种类繁多,目前汽车上广泛采用的主要是一些TPO,PP,ABS,PA6/PA66。
根据汽车外饰件不同的功能,使用工况,大致如下:
汽车外饰件材料一览表
3.2.2材料标准确定
同一类材料执行不同材料标准,其试验项目,成品性能,模具设计均有差异。
根据产品将要投放国家地区的不同,汽车材料工程师可确定材料具体执行的标准,或请原材料供应商提供相关资料。
现代轿车外饰件一般多为注塑喷漆或皮纹件,喷漆件为保证与车身颜色及漆面质量的一致,在选材时必须考虑喷涂系统。
例如北美车身油漆多采用高温烘烤系统,外饰件选材时相应亦须选择可高温烘烤的原料。
皮纹件选材时须特别考虑原料的颜色及耐候性能是否满足设计要求。
四.汽车塑料外饰件安装
外饰件一般均通过螺栓卡扣等连接件与车身本体或相邻件诸如翼子板或车门等相连。
为保证汽车外型的美观和防盗,所有外饰件安装点设计尽量隐藏在四门两盖内,但同时为方便维修拆卸,设计时更需考虑在更换零件时尽可能少拆或不拆周边零件。
车身外饰件安装方式和安装点数量与外饰件形状、外形尺寸及其功能有直接关系。
4.1安装方式
最简单的安装即用螺栓、螺母。
大部分外饰件均用此方式,如图二所示P点。
在设计安装面时应考虑安装工具所占空间,并尽量采用相同和常见的标准件,方便调整及维修。
一些小型非开启件常采用销定位胶粘接的连接方式,如防擦条(图一零件6)。
采用双面胶粘接的件为使零件与车身装配后配合紧密,设计时预先在零件上留出一凹槽面定的粘胶位置,为保证粘接强度,双面胶粘双面胶厚度一般为1mm至1.2mm,宽8mm至10mm,零件上凹槽为双面胶厚度的一半,如右图为防擦条基本结构。
有些外饰件如散热器面罩(图一零件8),侧饰条(图一零件5)常无法用螺栓连接,又不宜采用胶粘接的形式,则常常利用零件自身结构与其他件相连,或通过卡扣直接装在车身上。
如图二所示保险杠和散热器面罩的配合。
两件可在分装线上先分装成一体或由供应商直接提供分总成。
4.2安装点数量
外饰件安装点数量与零件的大小有直接关系,其安装点位置直接影响装配质量,主要是间隙和面差。
其中前后保险杠又是外饰件中最主要也是最直接影响整车效果的零件。
以前保险杠为例,上下左右安装点是支撑整个零件的核心,至少保证上部中间两点,左右各一点,下部不可少于四点。
同时为防止零件下沉,中部及侧边需有支撑支架或托板,见图二。
五.汽车塑料外饰件结构设计
塑料件设计不仅要满足使用要求,而且要符合塑料的成型工艺特点,并且尽可能使模具结构简单。
这样,可使成型工艺稳定,保证制品的质量,又可使生产成本降低。
外饰件的结构设计主要包括形状、壁厚、脱模角度、加强筋、支撑面、圆角、孔等。
5.1零件的形状
在造型师进行零件造型的同时,产品设计师更多考虑的则是零件的可制造性,可靠性等细节。
5.1.1可制造性
首先需分析确定零件的脱模方向,检查零件所有断面是否存在无法脱模的负角,尽量避免侧壁凹槽或与脱模方向垂直的孔,这样可简化模具结构,见图三。
零件边缘设计的好坏直接影响模具结构和制件的质量。
图四是一些设计中常常碰到的典型断面。
5.1.2可靠性
尽量避免零件局部突出过大的悬臂结构,如图二前保险杠上部两安装点M区域刚性较差,装配后零件易变形。
设计之初最好考虑两安装点连成一体或加宽凸缘,如图虚线所示,或背面加筋等方法解决。
在与车身要求有配合的边界加凸缘可以减少零件的变形量,提高配合精度,保证质量,见图二A-A、B-B断面所示。
5.2零件的壁厚
零件的壁厚一般力求均匀,否则会因固化或冷却速度不同而引起收缩不均匀,产生内因力,导致零件产生翘曲变形或缩孔。
图二散热器面罩基本断面,a为原结构,b为改进后结构,保持了料厚均匀一致,为提高模具寿命将局部不可见面削去。
汽车外饰件一般壁厚取2.5+0.25mm,大型件如保险杠取3+0.25mm至3.5+0.25mm。
为避免壁厚的变化影响零件表面质量,设计时特别强调料厚变化需保证足够的过渡区,如下图示。
T2-T1=T3
如果T3 1.0mm, D=25mm
如果T3 2.0mm, D=75mm
如果T3 2.5mm, D=100mm 推荐方案错误设计
5.3脱模角度
塑料件设计必须考虑脱模角度,避免脱模角度为零或负角。
脱模角度越大,零件越容易脱模,但容易造成零件厚度不均,影响制造精度。
图二散热器面罩断面,基本壁厚为3mm,如果脱模角度选择3︒,其最大壁厚处达7mm,最终零件表面会收缩,变形,并且浪费材料,减少迎风面积,甚至影响水箱冷却。
一般脱模角度与零件深度有关,最小和最大脱模角度可参考表二。
但皮纹件脱模角度相对非皮纹件需大些,具体与皮纹深度有关,一般每0.025皮纹深度需1︒脱模角度,皮纹深度增加时脱模角度随之加大。
表二:零件深度与脱模角度关系
5.4 加强筋
塑料件特别是大型零件如果仅仅有一定的壁厚是无法保证制件的形状和尺寸的,更谈不上一定的强度。
因此必须在一些如孔,大曲面或安装点处加筋,以提高强度和刚性。
外饰件主要表面(CLASSA)一般不宜加筋,次表面(CLASSB)加筋时根部壁厚也不可大于壁厚的3/4,对表面质量要求低或非可见表面(CLASS C&D),其相关尺寸见下图:
有时由于结构的限制,需在主要表面(CLASSA)背后布置安装点等,如图五为轮口安装点结构,此时为防止表面缩印,安装点壁厚尽量薄或局部开口,由于安装时此部位应力集中,为防止断裂,常加一些小筋。
5.5支撑面
若用整个面作为零件的支撑面,稍有变形就会影响与车身的配合。
因此实际常采用凸边或局部凸起的支角作为支撑面,而且对一些需紧密配合的零件设计时常采用如右图所示结构。
5.6圆角
外饰件表面不可有尖锐的楞线,凸出车身的外饰件圆角必须按相关标准设计,如我国GB11566《轿车外部突出物》对其有严格规定。
一般零件最小圆角取R0.5,但零件分型面避免有圆角,否则将增加制造成本和难度。
5.7孔
外饰件孔形状应尽量简单,孔与壁之间应保持一定距离,孔至边界最小至少是孔径的1.5倍。
6.结束语
现代汽车开发设计是汽车发展的核心,其本身又是一个技术高度密集的产业,强调各专业人员的团
队协作。
作为汽车设计的一部分,塑料外饰件的设计亦不例外,更是造型师,产品工程师,材料工程师,零件供应商以及方方面面各专业合作的结晶。
本人作为产品工程师,在多年的设计工作中更是深有体会,以上几个方面是本人在设计中积累的一点经验和体会,希望与各位交流探讨。