常用超声波探伤标准要求
超声探伤2级探伤标准
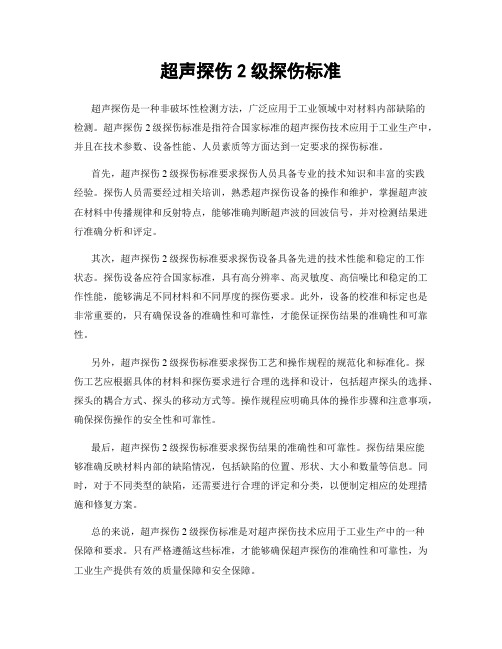
超声探伤2级探伤标准超声探伤是一种非破坏性检测方法,广泛应用于工业领域中对材料内部缺陷的检测。
超声探伤2级探伤标准是指符合国家标准的超声探伤技术应用于工业生产中,并且在技术参数、设备性能、人员素质等方面达到一定要求的探伤标准。
首先,超声探伤2级探伤标准要求探伤人员具备专业的技术知识和丰富的实践经验。
探伤人员需要经过相关培训,熟悉超声探伤设备的操作和维护,掌握超声波在材料中传播规律和反射特点,能够准确判断超声波的回波信号,并对检测结果进行准确分析和评定。
其次,超声探伤2级探伤标准要求探伤设备具备先进的技术性能和稳定的工作状态。
探伤设备应符合国家标准,具有高分辨率、高灵敏度、高信噪比和稳定的工作性能,能够满足不同材料和不同厚度的探伤要求。
此外,设备的校准和标定也是非常重要的,只有确保设备的准确性和可靠性,才能保证探伤结果的准确性和可靠性。
另外,超声探伤2级探伤标准要求探伤工艺和操作规程的规范化和标准化。
探伤工艺应根据具体的材料和探伤要求进行合理的选择和设计,包括超声探头的选择、探头的耦合方式、探头的移动方式等。
操作规程应明确具体的操作步骤和注意事项,确保探伤操作的安全性和可靠性。
最后,超声探伤2级探伤标准要求探伤结果的准确性和可靠性。
探伤结果应能够准确反映材料内部的缺陷情况,包括缺陷的位置、形状、大小和数量等信息。
同时,对于不同类型的缺陷,还需要进行合理的评定和分类,以便制定相应的处理措施和修复方案。
总的来说,超声探伤2级探伤标准是对超声探伤技术应用于工业生产中的一种保障和要求。
只有严格遵循这些标准,才能够确保超声探伤的准确性和可靠性,为工业生产提供有效的质量保障和安全保障。
常用超声波探伤标准要求
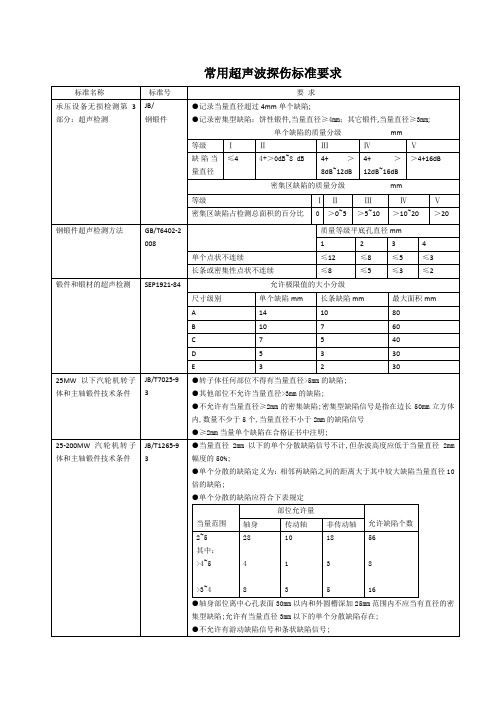
50~200MW汽轮发电机转子锻件技术条件
JB/T1267-93
●不允许有当量直径≥连续性缺陷信号和游动缺陷信号;
●当量直径小于2mm的缺陷不计,允许2~4mm缺陷存在,但相邻两缺陷的距离不小于其中较大缺陷直径的7倍;
●单个分散的缺陷应符合下表规定
允许极限值的大小分级
●不允许有游动信号和条状缺陷信号;
50~200MW汽轮发电机无中心孔转子锻件技术条件
JB/T8706-1998
●当量直径小于mm的缺陷不计,不允许有当量直径等于或大于mm连续缺陷信号和流动缺陷信号;
●在锻件中心φ150 mm范围内,不允许有当量直径大于mm100 MW以下转子锻件,不允许有当量直径大于mm的单个缺陷和大于或等于当量直径mm的密集缺陷信号;
≥3~4
3
1
4
8
总数
15
6
9
30
50MW以下汽轮发电机无中心孔转子锻件技术条件
JB/T 8705-1998
●小于当量直径2 mm的缺陷不计;
●不允许有连续性缺陷信号及游动信号;
●在中心φ150 mm范围内不允许有当量直径大于4 mm的缺陷和大于或等于当量直径mm的密集缺陷信号;
●外圆槽深加25 mm范围内不允许有当量直径大于4 mm的缺陷,其它区域允许有当量直径2~5mm分散的单个缺陷存在,但相邻两个缺陷的距离不小于其较大缺陷直径的5倍;
当量范围
部位允许量
允许缺陷个数
轴身
传动轴
非传动轴
2~5
其中:
>4~5
>3~4
28
4
8
10
1
3
超声波探伤国家标准
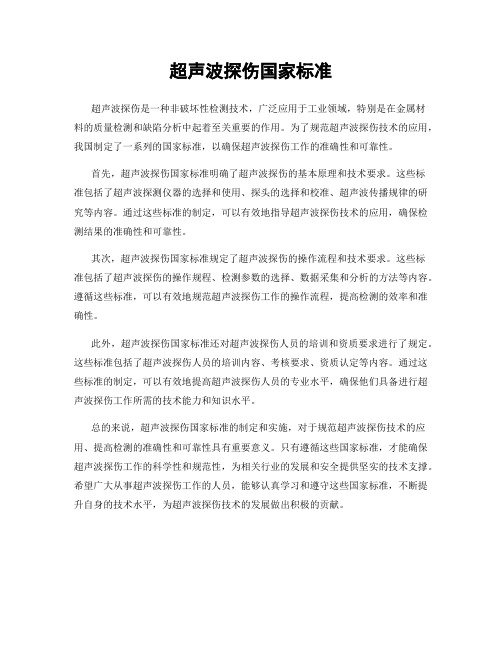
超声波探伤国家标准
超声波探伤是一种非破坏性检测技术,广泛应用于工业领域,特别是在金属材
料的质量检测和缺陷分析中起着至关重要的作用。
为了规范超声波探伤技术的应用,我国制定了一系列的国家标准,以确保超声波探伤工作的准确性和可靠性。
首先,超声波探伤国家标准明确了超声波探伤的基本原理和技术要求。
这些标
准包括了超声波探测仪器的选择和使用、探头的选择和校准、超声波传播规律的研究等内容。
通过这些标准的制定,可以有效地指导超声波探伤技术的应用,确保检测结果的准确性和可靠性。
其次,超声波探伤国家标准规定了超声波探伤的操作流程和技术要求。
这些标
准包括了超声波探伤的操作规程、检测参数的选择、数据采集和分析的方法等内容。
遵循这些标准,可以有效地规范超声波探伤工作的操作流程,提高检测的效率和准确性。
此外,超声波探伤国家标准还对超声波探伤人员的培训和资质要求进行了规定。
这些标准包括了超声波探伤人员的培训内容、考核要求、资质认定等内容。
通过这些标准的制定,可以有效地提高超声波探伤人员的专业水平,确保他们具备进行超声波探伤工作所需的技术能力和知识水平。
总的来说,超声波探伤国家标准的制定和实施,对于规范超声波探伤技术的应用、提高检测的准确性和可靠性具有重要意义。
只有遵循这些国家标准,才能确保超声波探伤工作的科学性和规范性,为相关行业的发展和安全提供坚实的技术支撑。
希望广大从事超声波探伤工作的人员,能够认真学习和遵守这些国家标准,不断提升自身的技术水平,为超声波探伤技术的发展做出积极的贡献。
超声波探伤检测标准
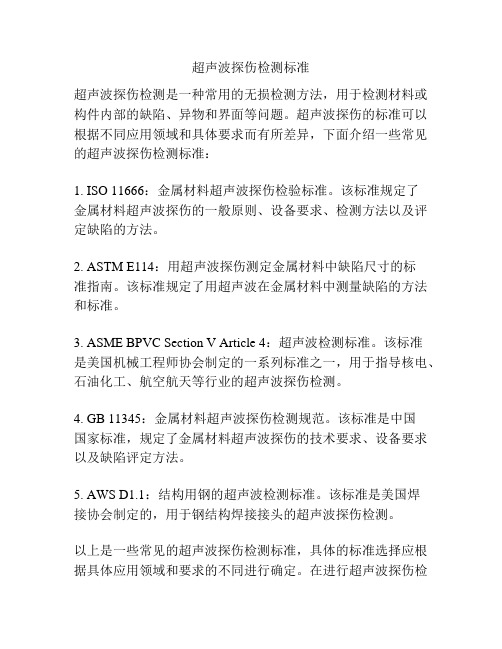
超声波探伤检测标准
超声波探伤检测是一种常用的无损检测方法,用于检测材料或构件内部的缺陷、异物和界面等问题。
超声波探伤的标准可以根据不同应用领域和具体要求而有所差异,下面介绍一些常见的超声波探伤检测标准:
1. ISO 11666:金属材料超声波探伤检验标准。
该标准规定了
金属材料超声波探伤的一般原则、设备要求、检测方法以及评定缺陷的方法。
2. ASTM E114:用超声波探伤测定金属材料中缺陷尺寸的标
准指南。
该标准规定了用超声波在金属材料中测量缺陷的方法和标准。
3. ASME BPVC Section V Article 4:超声波检测标准。
该标准
是美国机械工程师协会制定的一系列标准之一,用于指导核电、石油化工、航空航天等行业的超声波探伤检测。
4. GB 11345:金属材料超声波探伤检测规范。
该标准是中国
国家标准,规定了金属材料超声波探伤的技术要求、设备要求以及缺陷评定方法。
5. AWS D1.1:结构用钢的超声波检测标准。
该标准是美国焊
接协会制定的,用于钢结构焊接接头的超声波探伤检测。
以上是一些常见的超声波探伤检测标准,具体的标准选择应根据具体应用领域和要求的不同进行确定。
在进行超声波探伤检
测时,还需要考虑材料的特性、检测设备的性能以及操作人员的技术水平等因素。
JBT10061-1999超声波探伤仪通用技术条件
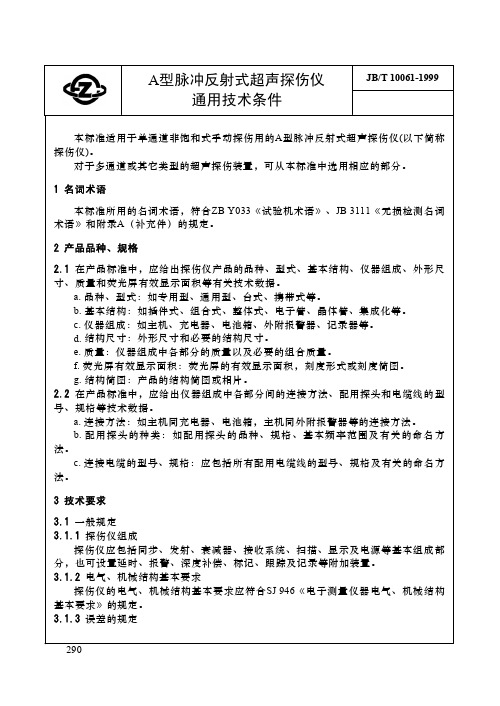
本标准适用于单通道非饱和式手动探伤用的探伤仪。
)对于多通道或其它类型的超声探伤装置,可从本标准中选用相应的部分。
—JB/T 100611999291探伤仪工作误差的给出原则及其表示方法,应符合《电子测量仪器误差的一般SJ 943规定》中的有关规定。
凡表中规定工作特性的项目,必须给出额定工作条件下的的误差2极限,在此前提下,必要时部分项目可以按影响量、影响特性等不同范围分段给出。
3.14环境要求探伤仪按使用条件的环境分组,应符合《电子测量仪器环境试验总纲》的规SJ 2075定,并在产品标准中注明产品隶属的组别。
3.2电性能 3.2.1衰减器总衰减量:不小于。
a. 60dB衰减误差:在探伤仪规定的工作频率范围内,衰减器每的工作误差不超出±b. 12dB。
1dB 3.2.2垂直线性误差不大于%。
83.2.3 动态范围不小于。
26dB 3.2.4水平线性误差不大于%。
23.2.5工作频率窄频带探伤仪的基本频率档级应在下列数值中选取:a. 、、()、、()、()、、()、、、、、、(0.4) 0.51 1.252 2.25 2.545(8) 10(12) 15、、:202530MHz 宽频带探伤仪的基本频率范围应在下列数值中选取:b. 、、()、、、、()、、()、、()、、()、(0.4) 0.50.81 1.52 2.25 2.53581012、()、、、。
1518202530MHz 注:括号内的数值为非优选数值。
3.2.6 电噪声电平在产品标准中应给出电噪声电平的最大值。
3.2.7 接收系统最大使用灵敏度在产品标准中应给出下列技术数据:窄频带探伤仪应给出各工作频率档级所对应的中心频率下的最大使用灵敏度;a. 宽频带探伤仪应给出频带上限、下限及中心频率所对应的使用灵敏度。
b. 3.2.8接收系统频带宽度在产品标准中应给出窄频带探伤仪-频带宽度的最小值。
3dB 3.2.9阻塞范围在产品标准中应给出接收系统阻塞范围的最大值。
超声波探伤方法和探伤标准
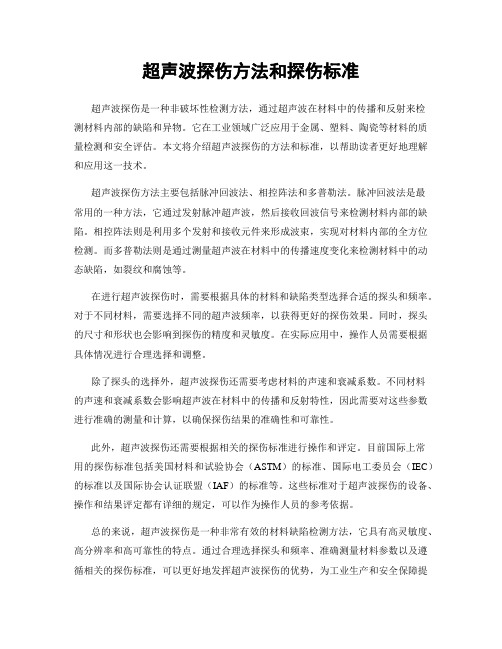
超声波探伤方法和探伤标准超声波探伤是一种非破坏性检测方法,通过超声波在材料中的传播和反射来检测材料内部的缺陷和异物。
它在工业领域广泛应用于金属、塑料、陶瓷等材料的质量检测和安全评估。
本文将介绍超声波探伤的方法和标准,以帮助读者更好地理解和应用这一技术。
超声波探伤方法主要包括脉冲回波法、相控阵法和多普勒法。
脉冲回波法是最常用的一种方法,它通过发射脉冲超声波,然后接收回波信号来检测材料内部的缺陷。
相控阵法则是利用多个发射和接收元件来形成波束,实现对材料内部的全方位检测。
而多普勒法则是通过测量超声波在材料中的传播速度变化来检测材料中的动态缺陷,如裂纹和腐蚀等。
在进行超声波探伤时,需要根据具体的材料和缺陷类型选择合适的探头和频率。
对于不同材料,需要选择不同的超声波频率,以获得更好的探伤效果。
同时,探头的尺寸和形状也会影响到探伤的精度和灵敏度。
在实际应用中,操作人员需要根据具体情况进行合理选择和调整。
除了探头的选择外,超声波探伤还需要考虑材料的声速和衰减系数。
不同材料的声速和衰减系数会影响超声波在材料中的传播和反射特性,因此需要对这些参数进行准确的测量和计算,以确保探伤结果的准确性和可靠性。
此外,超声波探伤还需要根据相关的探伤标准进行操作和评定。
目前国际上常用的探伤标准包括美国材料和试验协会(ASTM)的标准、国际电工委员会(IEC)的标准以及国际协会认证联盟(IAF)的标准等。
这些标准对于超声波探伤的设备、操作和结果评定都有详细的规定,可以作为操作人员的参考依据。
总的来说,超声波探伤是一种非常有效的材料缺陷检测方法,它具有高灵敏度、高分辨率和高可靠性的特点。
通过合理选择探头和频率、准确测量材料参数以及遵循相关的探伤标准,可以更好地发挥超声波探伤的优势,为工业生产和安全保障提供可靠的技术支持。
希望本文所介绍的超声波探伤方法和标准能够对读者有所帮助,促进这一技术的应用和发展。
超声波探伤标准GB11345-89

13.5 反射波幅位于Ⅲ区的缺陷, 无论其指示长度如何, 均评定为Ⅳ级.13.6 不合格的缺陷, 应予返修, 返修区域修后, 返修部位及补焊受影响的区域, 应按原探伤条件进行复验,复探部位的缺陷亦应按12 章评定.14 记录与报告14.1 检验记录主要内容: 工件名称、编号、焊缝编号、坡口形式、焊缝种类、母材材质、规格、表面情况、探伤方法、检验规程、验收标准、所使用的仪器、探头、耦合剂、试块、扫描比例、探伤灵敏度. 所发现的超标缺陷及评定记录, 检验人员及检验日期等. 反射波幅位于Ⅱ区, 其指示长度小于表 6 的缺陷也应予记录.14.2 检验报告主要内容: 工件名称、合同号、编号、探伤方法、探伤部位示意图、检验范围、探伤比例收标准、缺陷情况、返修情况、探伤结论、检验人员及审核人员签字等.14.3 检验记录和报告应至少保存7 年.14.4 检验记录和报告的推荐格式见附录 F.附录A标准试块的形状和尺寸( 补充件)注: 尺寸公差±0.1; 各边垂直度不大于0.05;C 面尺寸基准面, 上部各折射角刻度尺寸值见表A1,下部见表A2.附录B对比试块的形状和尺寸( 补充件)B1 对比试块的形状和尺寸见表B1.注: ①尺寸公差±0.1mm; ②各边垂直度不大于0.1; ③表面粗糙度不大于 6.3 μm; ④标准孔与加工面的平行度不大于0.05.附录C串列扫查探伤方法( 补充件)C1 探伤设备C1.1 超声波探伤仪的工作方式必须具备一发一收工作状态.C1.2 为保证一发一收探头相对于串列基准线经常保持等距离移动, 应配备适宜的探头夹具, 并适用于横方型及纵方型两种扫查方式.C1.3 推荐采用, 频率2-2.5Mhz, 公称折射角45°探头, 两探头入射点间最短间距应小于20mm.C2 仪器调整C2.1 时基线扫描的调节采用单探头按标准正文9.1 的方法调节, 最大探测范围应大于 1 跨距声程.C2.2 灵敏度调整在工件无缺陷部位, 将发、收两探头对向放置, 间距为 1 跨距, 找到底面最大反射波见图C1及式C1,调节增益使反射波幅为荧光屏满幅高度的40%,并以此为基准波高. 灵敏度分别提高8dB、14dB 和20dB 代表判废灵敏度、定量灵敏度和评定灵敏度.C3 检验程序C3.1 检验准备a. 探伤面对接焊缝的单面双侧;b. 串列基准线如发、收两探头实测折射角的平均值为β或K 值平均为K. 在离参考线( 参考线至探伤截面的距离L'-0.5P) 的位置标记串列基准线, 见图C2 及式C2.0.5P=δtg β(C1)或0.5P= δK (C2)C3.2 初始探伤C3.2.1 探伤灵敏度不低于评定灵敏度.C3.2.2 扫查方式采用横方形或纵方形串列扫查, 扫查范围以串列基准线为中心尽可能扫查到整个探伤截面, 每个探伤截面应扫查一遍.C3.2.3 标记超过评定线的反射波, 被判定为缺陷时, 应在焊缝的相应位置作出标记.C3.3 规定探伤C3.3.1 对象只对初始检验标记部位进行探伤.C3.3.2 探伤灵敏度为评定灵敏度.C3.3.3 缺陷位置不同深度的缺陷, 其反射波均出现在相当于半跨距声程位置见图C3. 缺陷的水平距离和深度分别为:(C3)(C4)C3.3.4 缺陷以射波幅在最大反射波探头位置, 以40%线为基准波高测出缺陷反射波的dB数作为缺陷的相对波幅, 记为SL±----dB.C3.3.5 缺陷指示长度的测定采用以评定灵敏度为测长灵敏度的绝对灵敏度法测量缺陷指示长度. 即进行左右扫查( 横方形串列扫查), 以波幅超过评定线的探头移动范围作为缺陷指示长度.C4 缺陷评定所有反射波幅度超过评定线的缺陷均应按标准正文第12 章的规定予以评定, 并按第13 章的规定对探伤结果作等级分类.附录D距离---- 波幅(DAC)曲线的制作( 补充件)D1 试件D1.1 采用标准附录B对比试块或其他等效形式试块绘制DAC曲线.D1.2 R 小于等于W2/4 时, 应采用探伤面曲率与工件探伤面曲率相同或相近的对比试块.D2 绘制步骤DAC曲线可绘制在坐标纸上( 称DAC曲线), 亦可直接绘制在荧光屏前透明的刻度板上( 称DAC曲线板).D2.1 DAC 曲线的绘制步骤如下:a. 将测试范围调整到探伤使用的最大探测范围, 并按深度、水平或声程法调整时基线扫描比例;b. 根据工件厚度和曲率选择合适的对比试块, 选取试块上民探伤深度相同或接近的横孔为第一基准孔, 将探头置于试块探伤面声束指向该孔, 调节探头位置找到横孔的最高反射波;c. 调节" 增益" 或" 衰减器" 使该反射幅为荧光屏上某一高度( 例如满幅的40%)该波高即为" 基准波高", 此时,探伤系统的有效灵敏度应比评定灵敏度高10dB;d. 调节衰减器, 依次探测其他横孔, 并找到最大反射波高, 分别记录各反射波的相对波幅值(dB);e. 以波幅(dB) 为纵坐标, 以探沿距离( 声程、深度或水平距离) 为横坐标, 将c、d 记录数值描绘在坐标纸上;f. 将标记各点连成圆滑曲线, 并延长到整个探测范围, 最近探测点到探距离O点间画水平线, 该曲线即为Φ3mm横孔DAC曲线的基准线;g. 依据标准正文表 3 规定的各线灵敏度, 在基准线下分别绘出判废线、定量线、评定线, 并标记波幅的分区;h. 为便于现场探伤校验灵敏度, 在测试上述数据的同时, 可对现场使用的便携试块上的某一参考反射体进行同样测量, 记录其反射波位置和反射波幅(dB) 并标记在DAC曲线图上.D2.2 DAC 曲线的绘制步骤如下:a. 同D2.1a;b. 依据工件厚度和曲率选择合适的对比试块, 在试块上所有孔深小于等于探测深度的孔中, 选取能产生最大反射波幅的横孔为第一基准孔;c. 调节" 增益" 使该孔的反射波为荧光屏满幅高度的80%,将其峰值标记在荧光屏前辅助面板上. 依次探测其它横孔, 并找到最大反射波, 地峰值点标记在辅助面板上, 如果做分段绘制, 可调节衰减器分段绘制曲线;d. 将各标记点连成圆滑曲线, 并延伸到整个探测范围, 该曲线即为Φ3mm横孔DAC曲线基准线; 定量灵敏度下, 如分别将灵敏度提高或降低6dB, 该线将分别代表评定或判废线.(A 级检验DAC基准线即为判废线);e. 将灵敏度提高(8-50mm提高到10dB,50-300mm提高10dB或8dB), 该线表示定量线. 在定量灵敏度下, 如分别将灵敏度提高或降低6dB, 该线将分别代表评定或判废线.(A 级检验DAC基准线即为判废线);f. 在作上述测试的同时, 可对现场使用的便携式试块上的某一参考反射体作同样测, 并将其反射波位置和峰值标记在曲线板上, 以便现场进行灵敏度校验.附录E声能传输损耗差的测定( 补充件)工件本身反射波幅度有影响的两个主要因素是材料的材质衰减和工件表面粗糙度及耦合情况的表面声能损失.超声波的材质衰减对普通碳钢或低合金网板材, 在频率低于3MHz声程不超过200mm时, 可以忽略不记, 或者一般来说衰减系数小于0.01dB/mm 时, 材质衰减可以不予考虑, 标准试块和对比试块均应满足这一要求.受检工件探伤时, 如声程较大, 或材质衰减系数超过上述范围, 在确定缺陷反射波幅时, 应考虑作材料衰减修整, 如被检工件表面比较粗糙还应考虑表面声能损失问题.E1 横波超声材质衰减的测量E1.1 制作与受检工件材质相同或相近, 厚度约40mm表面粗糙度与对比试块RB相同的平面型试块图E1.E1.2 采用工件检验中使用的斜探头按深度1:1 调节仪器时基扫描.E1.3 另选用一只与该探头尺寸、频率、角度相同的斜探头, 两探头按图E1 所示方向置于平板试块上, 两探头入射点间距离为1P,仪器调为一发一收状态, 找到接以最大反射波幅, 记录其波幅值Hi(dB).E1.4 将两探头拉开到距离为2P,找到最大反射波幅, 记录其波幅值H2(dB).E1.5 实际探伤中超声波总是往返的, 故双程的衰减系数αH可用下式计算:(E1)S1=40/COSβ+l' (E2)S2=80/COSβ+l'0 (E3)(E4)式中L0---- 晶片到为的距离, 作为简化处理亦可取l'0=l0, mm;△------ 声程S1、S2不考虑材质衰减时大平面的反射波幅dB 差, 可用公式计算或从该探头的D·G·S 曲线上查得,dB;由于S2 近拟为S1 的2 倍, 在声程大于 3 倍近场长度N时, △约为6dB.E1.6 如果在图E1 试块和RB对比试块的侧面测得波幅HZ,相差不过1dB, 则可不考虑工件的材质衰减.E2 传输损失差的测定E2.1 采用工件检验中使用的斜探头, 按深度比例调节仪器时基扫描.E2.2 选用另一与该探头尺寸、频率、角度相同的斜探头, 两探头按图E2 所示方向置于对比试块侧面上, 两探头入射点间距离为1P, 仪器调为一发一收状态.E2.3 在对比试块上, 找到接收波最大反射波幅, 记录其波幅值H1(dB).E2.4 在受检工件板材上( 不通过焊缝) 同样测出接收波最大反射波幅, 记录其波幅值H2(dB).E2.5 传输损失差△V为:△V=H1-H2-△1- △2 (E5)式中△1---- 声程S1、S2 不考虑材质衰减时大平面的反射波幅dB 差, 可用公式计算或从探头的D·G·S 曲线上查得,dB;S1---- 在对比试块中的声程,mm;S2---- 在工件板材中的声程,mm;△2-- 试块中声程S1 时与工件中声程S2 时的超声材质衰减差值,dB.如试块图E1 按E1 测量材质衰减系数小于0.01dB/mm, 此项可以不予考虑.附录F焊缝超声波探伤报告和记录( 参考件)焊缝超声波探伤报告焊缝超声波探伤记录附加说明:本标准由中华人民共和国机械电子工业部提出.本标准由全国无损检测标准化技术委员会归口.本标准由哈尔滨焊接研究所负责起草, 主要参加单位: 哈尔滨锅炉厂、劳动人事部锅炉压力容器检测研究中心.本标准主要起草人李生田、李家鳌、康纪黔、张泽丰、王梅屏.。
超声波探伤标准
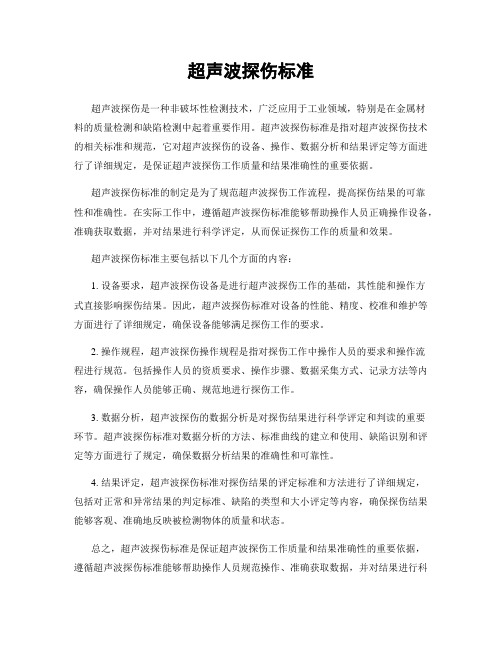
超声波探伤标准超声波探伤是一种非破坏性检测技术,广泛应用于工业领域,特别是在金属材料的质量检测和缺陷检测中起着重要作用。
超声波探伤标准是指对超声波探伤技术的相关标准和规范,它对超声波探伤的设备、操作、数据分析和结果评定等方面进行了详细规定,是保证超声波探伤工作质量和结果准确性的重要依据。
超声波探伤标准的制定是为了规范超声波探伤工作流程,提高探伤结果的可靠性和准确性。
在实际工作中,遵循超声波探伤标准能够帮助操作人员正确操作设备,准确获取数据,并对结果进行科学评定,从而保证探伤工作的质量和效果。
超声波探伤标准主要包括以下几个方面的内容:1. 设备要求,超声波探伤设备是进行超声波探伤工作的基础,其性能和操作方式直接影响探伤结果。
因此,超声波探伤标准对设备的性能、精度、校准和维护等方面进行了详细规定,确保设备能够满足探伤工作的要求。
2. 操作规程,超声波探伤操作规程是指对探伤工作中操作人员的要求和操作流程进行规范。
包括操作人员的资质要求、操作步骤、数据采集方式、记录方法等内容,确保操作人员能够正确、规范地进行探伤工作。
3. 数据分析,超声波探伤的数据分析是对探伤结果进行科学评定和判读的重要环节。
超声波探伤标准对数据分析的方法、标准曲线的建立和使用、缺陷识别和评定等方面进行了规定,确保数据分析结果的准确性和可靠性。
4. 结果评定,超声波探伤标准对探伤结果的评定标准和方法进行了详细规定,包括对正常和异常结果的判定标准、缺陷的类型和大小评定等内容,确保探伤结果能够客观、准确地反映被检测物体的质量和状态。
总之,超声波探伤标准是保证超声波探伤工作质量和结果准确性的重要依据,遵循超声波探伤标准能够帮助操作人员规范操作、准确获取数据,并对结果进行科学评定,从而保证探伤工作的质量和效果。
因此,在超声波探伤工作中,必须严格遵循超声波探伤标准的要求,确保探伤工作的准确性和可靠性。
常用超声波探伤标准要求[参考资料]
![常用超声波探伤标准要求[参考资料]](https://img.taocdn.com/s3/m/d0e40316af45b307e87197c1.png)
●≥2mm当量单个缺陷在合格证书中注明。
25-200MW汽轮机转子体和主轴锻件技术条件
JB/T1265-93
●当量直径2mm以下的单个分散缺陷信号不计,但杂波高度应低于当量直径2mm幅度的50%。
冶金设备制造通用技术条件(锻钢件超声波探伤方法)
YB/T036.10-1992
●密集缺陷:在钢中距离50mm的范围内,有5个以上大于或等于探伤灵敏度基准的缺陷波,称密集缺陷。
●条状缺陷:当缺陷反射波幅大于或等于探伤灵敏度基准波幅,长度大于或等于30mm的连续性缺陷,称条状缺陷。
标准号
要求
模锻锤和大型机械锻压机用模块技术条件
GB11880-89
●允许存在个别的、分散的、不大于当量直径¢2mm的冶金缺陷。
●在100cm2的面积内,当量直径¢2~¢4 mm的冶金缺陷不超过3个,其中¢3~¢4 mm的冶金缺陷只允许有1个。
●允许有2-4个小于当量直径¢2mm的冶金缺陷的密集区,但每区不得超过10cm3,每区之间距不得小于150mm。
●距中心孔表面75mm以外部位,允许有3个小于当量直径1.6mm的密集缺陷区,但密集区在任何方向的尺寸均应不大于20mm,并且任何两缺陷区间距离应不小于120mm。
●不允许有游动缺陷信号和条状缺陷信号。
50MW以下汽轮发电机转子锻件技术条件
JB/T7026-93
●小于当量直径2mm的缺陷不计。
●不允许有当量直径≥2mm的密集型缺陷密集型缺陷信号,连续性缺陷信号,及游动信号。
●允许有当量直径2~5mm分散的单个缺陷存在,但相邻两个缺陷的距离不小于其较大缺陷直径的5倍,总数量不得超过56个。
超声波探伤作业指导书
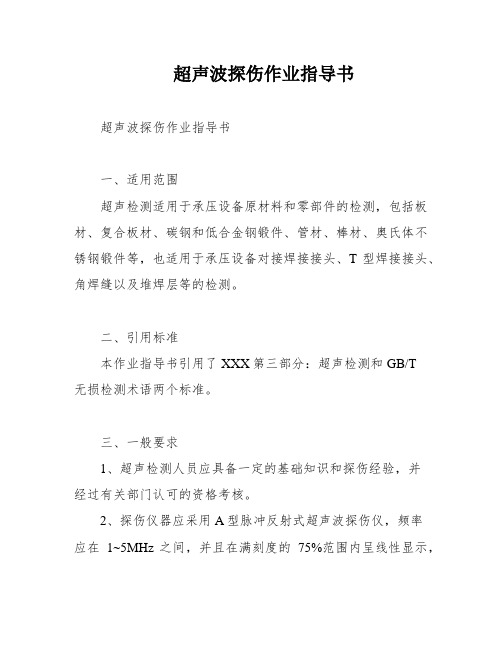
超声波探伤作业指导书超声波探伤作业指导书一、适用范围超声检测适用于承压设备原材料和零部件的检测,包括板材、复合板材、碳钢和低合金钢锻件、管材、棒材、奥氏体不锈钢锻件等,也适用于承压设备对接焊接接头、T型焊接接头、角焊缝以及堆焊层等的检测。
二、引用标准本作业指导书引用了XXX第三部分:超声检测和GB/T无损检测术语两个标准。
三、一般要求1、超声检测人员应具备一定的基础知识和探伤经验,并经过有关部门认可的资格考核。
2、探伤仪器应采用A型脉冲反射式超声波探伤仪,频率应在1~5MHz之间,并且在满刻度的75%范围内呈线性显示,垂直线性误差不得超过5%。
仪器的水平线性、分辨力和衰减器的精度等指标应符合JB/T 的规定。
3、探头应符合以下要求:①纵波直探头的晶片直径应在10~30mm之间,工作频率1~5MHz,误差不得超过±10%。
②横波斜探头的晶片面积应在100~400mm²之间,K值一般取1~3.③纵波双晶直探头晶片之间的声绝缘必须良好。
4、仪器系统的性能应符合以下要求:①在达到所探工件的最大检测声程时,其有效灵敏度余量不得小于10dB。
②仪器与探头的组合频率与公称频率误差不得大于±10%。
③仪器与直探头组合的始脉冲宽度(在基准灵敏度下):对于频率为5MHz的探头,宽度不大于10mm;对于频率为2.5MHz的探头,宽度不大于15mm。
④直探头的远场分辨力应不小于30dB,斜探头的远场分辨力应不小于6dB。
⑤仪器与探头的系统性能应按JB/T 9124和JB/T 的规定进行测试。
四、探伤时机及准备工作1、探伤一般应安排在最终热处理后进行。
若因热处理后工件形状不适于超声探伤,也可将探伤安排在热处理前,但热处理后仍应对其进行尽可能完全的探伤。
2、工件在外观检查合格后方可进行超声探伤,所有影响超声探伤的油污及其他附着物应予以清除。
3、探伤面的表面粗糙度Ra应为6.3μm。
五、探伤方法1、为确保检测时超声波声束能扫查到工件的整个被检区域,探头的每次扫查覆盖率应大于探头直径的15%。
超声波探伤检测标准

超声波探伤检测标准摘要:1.超声波探伤检测标准的概述2.超声波探伤的原理3.超声波探伤的优点4.超声波探伤检测标准的制定与实施5.超声波探伤检测标准的发展趋势正文:一、超声波探伤检测标准的概述超声波探伤检测标准是一种非破坏性检测技术,广泛应用于各种材料和零部件的检测中。
超声波探伤技术利用超声波在材料中的传播特性,检测材料内部的缺陷、裂纹等问题,以评估其质量和安全性。
在实际应用中,为了保证超声波探伤检测的准确性和可靠性,需要制定一系列的技术标准和规范。
二、超声波探伤的原理超声波探伤的原理是利用超声波在材料中的传播速度和衰减特性,检测材料内部的缺陷、裂纹等问题。
超声波在传播过程中,如果遇到材料内部的缺陷或界面,会产生反射、散射等现象,这些现象会被探头接收并转换为电信号。
通过分析这些电信号的特征,可以判断材料内部是否存在缺陷,以及缺陷的性质、位置、大小等。
三、超声波探伤的优点超声波探伤技术具有许多优点,使其成为非破坏性检测的主要方法之一。
首先,超声波探伤可以检测到材料内部的缺陷,而不会破坏材料的表面和结构。
其次,超声波探伤可以检测到各种不同类型的缺陷,包括裂纹、夹杂、气孔等。
此外,超声波探伤还具有较高的检测速度和灵敏度,可以有效地提高检测效率和准确性。
四、超声波探伤检测标准的制定与实施为了保证超声波探伤检测的准确性和可靠性,需要制定一系列的技术标准和规范。
这些标准和规范包括超声波探伤的设备标准、检测方法标准、数据处理和分析标准等。
超声波探伤检测标准的制定和实施,有助于确保检测结果的可靠性和一致性,提高检测技术的应用水平和效果。
五、超声波探伤检测标准的发展趋势随着超声波探伤技术的不断发展和应用,超声波探伤检测标准也在不断完善和更新。
超声波探伤检验标准
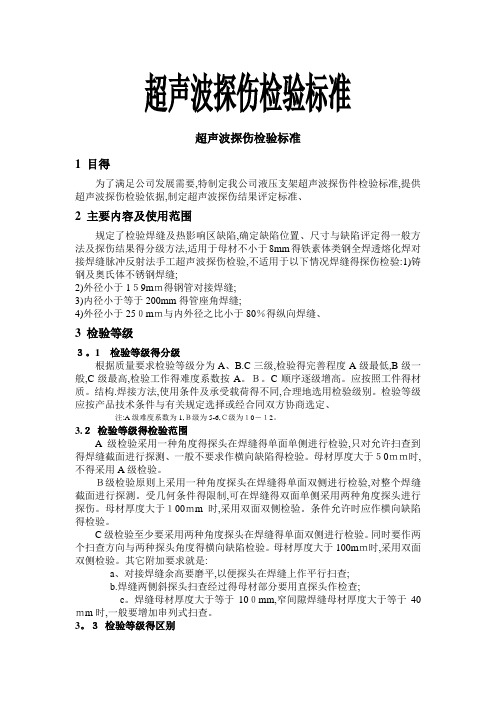
超声波探伤检验标准超声波探伤检验标准1 目得为了满足公司发展需要,特制定我公司液压支架超声波探伤件检验标准,提供超声波探伤检验依据,制定超声波探伤结果评定标准、2 主要内容及使用范围规定了检验焊缝及热影响区缺陷,确定缺陷位置、尺寸与缺陷评定得一般方法及探伤结果得分级方法,适用于母材不小于8mm得铁素体类钢全焊透熔化焊对接焊缝脉冲反射法手工超声波探伤检验,不适用于以下情况焊缝得探伤检验:1)铸钢及奥氏体不锈钢焊缝;2)外径小于159mm得钢管对接焊缝;3)内径小于等于200mm得管座角焊缝;4)外径小于250mm与内外径之比小于80%得纵向焊缝、3 检验等级3。
1检验等级得分级根据质量要求检验等级分为A、B.C三级,检验得完善程度A级最低,B级一般,C级最高,检验工作得难度系数按A。
B。
C顺序逐级增高。
应按照工件得材质。
结构.焊接方法,使用条件及承受载荷得不同,合理地选用检验级别。
检验等级应按产品技术条件与有关规定选择或经合同双方协商选定、注:A级难度系数为1,B级为5-6,C级为10-12。
3.2检验等级得检验范围A级检验采用一种角度得探头在焊缝得单面单侧进行检验,只对允许扫查到得焊缝截面进行探测、一般不要求作横向缺陷得检验。
母材厚度大于50mm时,不得采用A级检验。
B级检验原则上采用一种角度探头在焊缝得单面双侧进行检验,对整个焊缝截面进行探测。
受几何条件得限制,可在焊缝得双面单侧采用两种角度探头进行探伤。
母材厚度大于100mm时,采用双面双侧检验。
条件允许时应作横向缺陷得检验。
C级检验至少要采用两种角度探头在焊缝得单面双侧进行检验。
同时要作两个扫查方向与两种探头角度得横向缺陷检验。
母材厚度大于100mm时,采用双面双侧检验。
其它附加要求就是:a、对接焊缝余高要磨平,以便探头在焊缝上作平行扫查;b.焊缝两侧斜探头扫查经过得母材部分要用直探头作检查;c。
焊缝母材厚度大于等于100mm,窄间隙焊缝母材厚度大于等于40mm时,一般要增加串列式扫查。
超声波探伤检验标准
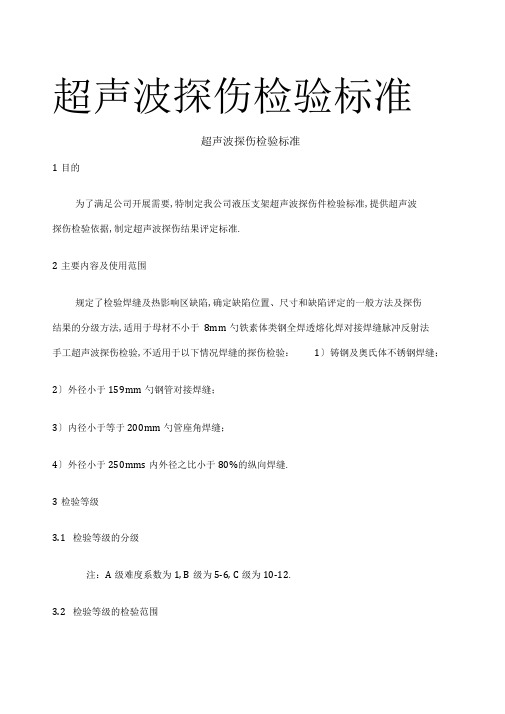
超声波探伤检验标准超声波探伤检验标准1目的为了满足公司开展需要,特制定我公司液压支架超声波探伤件检验标准,提供超声波探伤检验依据,制定超声波探伤结果评定标准.2主要内容及使用范围规定了检验焊缝及热影响区缺陷,确定缺陷位置、尺寸和缺陷评定的一般方法及探伤结果的分级方法,适用于母材不小于8mm勺铁素体类钢全焊透熔化焊对接焊缝脉冲反射法手工超声波探伤检验,不适用于以下情况焊缝的探伤检验:1〕铸钢及奥氏体不锈钢焊缝;2〕外径小于159mm勺钢管对接焊缝;3〕内径小于等于200mm勺管座角焊缝;4〕外径小于250mms内外径之比小于80%的纵向焊缝.3检验等级3.1检验等级的分级注:A级难度系数为1, B级为5-6, C级为10-12.3.2检验等级的检验范围A级检验采用一种角度的探头在焊缝的单面单侧进行检验,只对允许扫查到的焊缝截面进行探测.一般不要求作横向缺陷的检验.母材厚度大于50mnW,不彳#采用A级检验.B级检验原那么上采用一种角度探头在焊缝的单面双侧进行检验,对整个焊缝截面进行探测.受几何条件的限制,可在焊缝的双面单侧采用两种角度探头进行探伤.母材厚度大于100mm寸,采用双面双侧检验.条件允许时应作横向缺陷的检验.C级检验至少要采用两种角度探头在焊缝的单面双侧进行检验.同时要作两个扫查方向和两种探头角度的横向缺陷检验.母材厚度大于100mm寸,采用双面双侧检验.其它附加要求是:a.对接焊缝余高要磨平,以便探头在焊缝上作平行扫查;b.焊缝两侧斜探头扫查经过的母材局部要用直探头作检查;c.焊缝母材厚度大于等于100mm窄间隙焊缝母材厚度大于等于40mnW, 一般要增加用列式扫查.3.3检验等级的区别A、B、C三种检验等级之间有所区别,现将其探头种类数、面数、侧数、板厚等方面的区别简单列于表一中:结合本公司产品结构特点,及焊后焊缝特性,规定超声波探伤检当等级主要采用A级, 以B级辅助,特殊情况时选用C级检验.4初始检验4.1一般要求4.1.1探头移动区应去除焊接飞溅、铁屑、油垢及其他外部杂质,探伤外表应平整光滑, 便于探头的自由扫查,具外表粗糙度不应超过 6.3小解必要时应进行打磨,超声波探伤检验应在焊缝及探伤外表经外观检查合格且满足以上要求后进行.4.1.2检验前,探伤人员应了解受检工件的材质、结构、曲率、厚度、焊接方法、焊缝种类、坡口形式、焊缝余高及反面沉淀、沟槽等情况.4.1.3探伤灵敏度应不低于评定线灵敏度.4.1.4扫查速度不应大于150mm/s相邻两次探头移动间隔保证至少有探头宽度10%勺重叠.4.2平板对接焊缝的检验4.2.1为探测纵向缺陷,斜探头垂直于焊缝中央线放置在探伤面上,做锯齿型扫查〔如图一〕.探头前后移动的范围应保证扫查到全部焊缝截面及热影响区. 在保持探头垂直焊缝做前后移动的同时,还应做10° ~15°的左右转动.图一:锯齿形扫查4.2.2为探测焊缝及热影响区的横向缺陷应进行平行和斜平行扫查.a.B级检验时,可在焊缝两侧边缘使探头与焊缝中央线成10° ~20.做斜平行扫查〔如图二〕图二:斜平行扫查b.C级检验时,可将探头放在焊缝及热影响区上做两个方向的平行扫查〔如图三〕,焊缝母材厚度超过100mm寸,应在焊缝的两面做平行扫查或者采用两种角度探头〔45°和60°或45°和70°并用〕做单面两个方向的平行扫查,亦可用两个450探头做串列式平行扫查.图三:平行扫查c.对电渣焊缝还应增加与焊缝中央线成45°的斜向扫查.4.2.3为确定缺陷的位置、方向、形状、观察缺陷动态波形或区分缺陷讯号与伪讯号,可采用前后、左右、转角、环绕等四种探头根本扫查方式〔如图四〕图四:四种根本扫查方法4.3曲面工件对接焊缝的检验4.3.1探伤面为曲面时,应采用4.2条的方法进行检验,C级检验时,受工件几何形状限制,横向缺陷探测无法实施时,应在检验记录中予以注明.4.3.2环缝检验时,比照试块的曲率半径为4.3.3纵缝检验时,比照试块的曲率半径与探伤面曲率半径之差应小于10%4.4其他结构焊缝的检验4.4.1一般原那么a.尽可能采用平板焊缝检验中已经行之有效的各种方法;b.在选择探伤面和探头时应考虑到检测各种类型缺陷的可能性, 并使声束尽可能垂直于该结构焊缝中的主要缺陷.4.4.2T型接头4.4.2.1.腹板厚度不同时,选用的折射角见表二,斜探头在腹板一侧做直射法和一次反射法探伤见图五位置2.表二:腹板厚度与选用的折射角图五:型接头图六:T型接头4.4.2.2采用折射角45.〔K1〕探头在腹板一侧做直射法和一次反射法探测焊缝及腹板侧热影响区的裂纹〔如图六〕.4.4.2.3为探侧腹板和翼板间未焊透或翼板侧焊缝下层状撕裂等缺陷,可采用直探头〔图五位置1〕或斜探头〔图六位置3〕在翼板外侧探伤或采用折射角450〔K1〕探头在翼板内侧做一次反射法探伤〔图五位置3〕.4.4.3角接接头角接接头探伤面及折射角翼板按图七和表二选择.图七:角接接头4.4.4管座角焊缝4.4.4.1根据焊缝结构形式,管座角焊缝的检验有如下五种探测方式,可选择其中一种或几种方式组合实施检验.探测方式的选择应由合同双方商定,并重点考虑主要探测对象和几何条件的限制〔图八、九〕图八:管座角焊缝图九:管座角焊缝a.在接管内壁外表采用直探头探伤〔图八位置1〕b.在容器内外表用直探头探伤〔图九位置1〕c.在接管外外表采用斜探头探伤〔图九位置2〕d.在接管内外表采用斜探头探伤〔图八位置3,图九位置3〕e.在容器外外表采用斜探头探伤〔图八位置2〕4.4.44.4.5直探头检验的规程a.推荐采用频率2.5MHZ直探头或双晶探头,探头与工件接触面的尺寸W应小于2个5b.灵敏度可在与工件同曲率的试块上调节, 也可采用计算法或DGS®线法,以工件底面回波调节,具检验等级评定见表三表三:直探头检验等级评定5规定检验5.1一般要求5.1.1规定检验只对初始检验中标记的部位进行检验.5.1.2探伤灵敏度应调节到评定灵敏度.5.1.3对所有反射波幅超过定量线的缺陷均应确定其位置,最大反射波幅所在区域和缺陷指示长度.5.2最大反射波幅的测定5.2.15.2.2最大反射波幅A与定量线SL的dB差值记为SL±dB.5.3位置参数的测定5.3.1缺陷位置以获得缺陷最大反射波的位置来表示,根据相应的探头位置和反射波在荧光屏上的位置来确定如下全部或局部参数.a.纵坐标L代表缺陷沿焊缝方向的位置.以检验区段编号为标记基准点〔即原点〕建立坐标.坐标正方向距离L表示缺陷到原点之间的距离〔如图十〕图十:纵坐标L示意图c.横坐标q代表缺陷离开焊缝中央线的垂直距离, 可由缺陷最大反射波位置的水平距离或简化水平距离求得.5.3.2缺陷的深度和水平距离〔或简化水平距离〕两数值中的一个可由缺陷最大反射波在荧光屏上的位置直接读出,另一数值可采用计算法、曲线法、作图法或缺陷定位尺求出.5.4尺寸参数的测定应根据缺陷最大反射波幅确定缺陷当量值①或测定缺陷指示长度A L o5.4.1缺陷当量①,用当量平底孔直径表示,主要用于直探头检验,可采用公式计算、GS曲线、试块比照或当量计算尺确定缺陷当量尺寸.5.4.2缺陷指示长度A L的测定推荐采用如下二种方法.a.当缺陷反射波只有一个高点时,用降低6dB相对灵敏度法测长〔如图十一〕图十一:相对灵敏度测长法b.在测长扫查过程中,如发现缺陷反射波峰值起伏变化;有多个高点,那么以缺陷两端反射波极大值之间探头的移动长度确定为缺陷指示长度,即端点峰值法〔如图十二〕图十二:端点峰值测长法6缺陷评定6.1超过评定线的信号应注意其是否具有裂纹等危害性缺陷特征,如有疑心时应采取改变探头角度、增加探伤面、观察动态波形、结合结构工艺特征做判定,如对波型不能准确判断时,应辅以其他检验做综合判定.6.2最大反射波幅位于II区的缺陷,其指示长度小于10mm寸按5mnif.6.3相邻两缺陷各向间距小于8mm寸,两缺陷指示长度之和作为单个缺陷的指示长度.7超声波探伤检验结果的等级分类7.1最大反射波幅位于II区的缺陷,根据缺陷指示长度按下表的规定予以评级.表四:缺陷等级分类注:为坡口加工侧母板厚,母材板厚不同时,以较薄侧板为准2.管座角焊缝6为焊缝截面中央线高度.7.2最大反射波幅不超过评定线的缺陷,均评为1级.7.3最大反射波幅超过评定线的缺陷,检验者判定为裂纹等危害性缺陷时,无论其波幅和尺寸如何,均评为IV级.7.4反射波幅位于I区的非裂纹性缺陷,均评为I级7.5反射波幅位于田区的缺陷,无论其指示长度如何,均评定为IV级.7.6不合格的缺陷,应予返修,返修区域修补后,返修部位及补焊受影响的区域,应按原探伤条件进行复验.8本公司缺陷评定等级8.1被探伤焊缝的坡口深度范围内的缺陷参与评定.8.2缺陷的长度评定等级一般选取表四中的AII级.8.3当辅以B级或C级检验时,相应选取标准亦暂时按II级执行.8.4假设之前本公司的相关规定与本标准内容相悖时,以本标准为准.9其他9.1本标准主要引用GB/T11345-89的相关内容,结合本公司实际情况而定9.2本标准由质量治理限制中央负责起草,并负责解释、更新.9.3本标准自签发之日起生效.。
超声波探伤级别标准
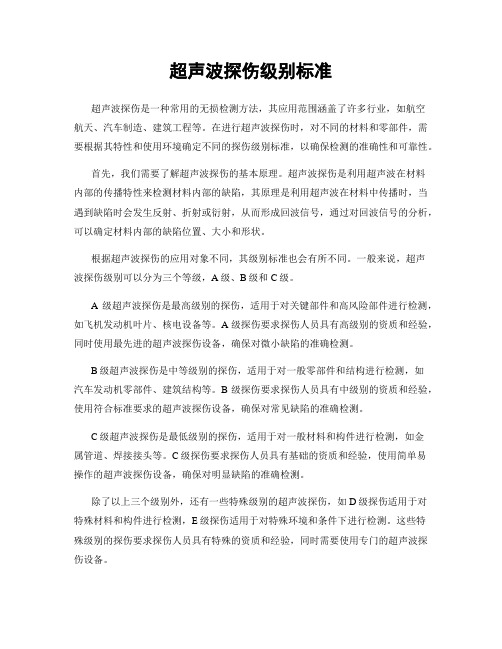
超声波探伤级别标准超声波探伤是一种常用的无损检测方法,其应用范围涵盖了许多行业,如航空航天、汽车制造、建筑工程等。
在进行超声波探伤时,对不同的材料和零部件,需要根据其特性和使用环境确定不同的探伤级别标准,以确保检测的准确性和可靠性。
首先,我们需要了解超声波探伤的基本原理。
超声波探伤是利用超声波在材料内部的传播特性来检测材料内部的缺陷,其原理是利用超声波在材料中传播时,当遇到缺陷时会发生反射、折射或衍射,从而形成回波信号,通过对回波信号的分析,可以确定材料内部的缺陷位置、大小和形状。
根据超声波探伤的应用对象不同,其级别标准也会有所不同。
一般来说,超声波探伤级别可以分为三个等级,A级、B级和C级。
A级超声波探伤是最高级别的探伤,适用于对关键部件和高风险部件进行检测,如飞机发动机叶片、核电设备等。
A级探伤要求探伤人员具有高级别的资质和经验,同时使用最先进的超声波探伤设备,确保对微小缺陷的准确检测。
B级超声波探伤是中等级别的探伤,适用于对一般零部件和结构进行检测,如汽车发动机零部件、建筑结构等。
B级探伤要求探伤人员具有中级别的资质和经验,使用符合标准要求的超声波探伤设备,确保对常见缺陷的准确检测。
C级超声波探伤是最低级别的探伤,适用于对一般材料和构件进行检测,如金属管道、焊接接头等。
C级探伤要求探伤人员具有基础的资质和经验,使用简单易操作的超声波探伤设备,确保对明显缺陷的准确检测。
除了以上三个级别外,还有一些特殊级别的超声波探伤,如D级探伤适用于对特殊材料和构件进行检测,E级探伤适用于对特殊环境和条件下进行检测。
这些特殊级别的探伤要求探伤人员具有特殊的资质和经验,同时需要使用专门的超声波探伤设备。
总的来说,超声波探伤级别标准的确定需要根据实际情况和要求来进行评估和选择。
在进行超声波探伤时,必须严格按照相应级别标准的要求进行操作,确保检测的准确性和可靠性,从而保证材料和构件的安全可靠性。
同时,探伤人员需要不断提升自身的技术水平和经验,以适应不同级别标准的要求,为超声波探伤工作的开展提供更加可靠的保障。
不锈钢板超声波探伤标准

不锈钢板超声波探伤标准一、探伤设备1.超声波探伤仪:应采用数字式超声波探伤仪,其性能应符合国家相关标准要求。
2.探头:应选用频率为2.5MHz至5MHz的直探头或斜探头。
3.耦合剂:应选用粘度适中、对工件无腐蚀作用的耦合剂。
4.试块:应采用标准试块,以校正探伤灵敏度和校准探头。
二、探伤条件1.环境温度:应在10℃至35℃之间进行探伤。
2.相对湿度:应小于75%。
3.探伤表面状态:应清除工件表面的油污、锈迹等杂质,确保表面光滑。
三、探伤方法1.预扫查:在探伤前,应对工件进行一次全面的扫查,以了解工件的形状、尺寸和材料状况。
2.正式探伤:应按照GB/T 11345-2013标准进行操作,采用直探头或斜探头对工件进行纵向和横向扫查。
扫查速度不应超过150mm/s。
3.缺陷定位:当发现缺陷时,应进行缺陷定位,记录缺陷的位置和大小。
4.缺陷定量:应对缺陷进行定量,确定缺陷的面积和深度。
四、缺陷判别1.对于单个缺陷,应判定其是否超过允许值。
2.对于密集型缺陷,应判定其是否为裂纹等危险性缺陷。
3.对于无法判断的缺陷,应进行进一步的分析和检测。
五、探伤记录1.应记录探伤过程中的所有数据,包括缺陷的位置、大小、形状等。
2.应记录探伤的时间、环境温度和湿度等信息。
3.应记录探伤人员的姓名和操作过程等信息。
六、探伤结果1.应根据探伤记录,对工件进行评级,确定其质量等级。
2.对于不合格的工件,应进行返修或报废处理。
3.对于合格的工件,可以进行后续加工或使用。
七、安全要求1.操作人员应经过专业的培训,熟悉超声波探伤仪的操作流程和安全规范。
2.在操作过程中,应注意避免探头和工件的过度摩擦和冲击,防止发生意外事故。
3.在处理高温工件时,应注意防止烫伤和火灾事故的发生。
4.在进行探伤前,应对工件进行全面的检查,防止因工件质量问题造成意外事故。
5.在操作过程中,应注意保持环境的整洁和安全,防止因杂乱或危险物品导致的意外事故。
6.在使用耦合剂时,应注意不要将耦合剂溅入眼睛或口中,防止造成伤害。
焊缝超声波探伤标准

焊缝超声波探伤标准焊接是制造业中常见的一种连接工艺,而焊缝的质量直接关系到焊接件的使用性能和安全性。
为了确保焊缝质量,超声波探伤技术被广泛应用于焊接质量检测中。
本文将介绍焊缝超声波探伤的标准和要点。
一、超声波探伤原理。
超声波探伤是利用超声波在材料中的传播特性来检测材料内部缺陷的一种无损检测技术。
当超声波遇到材料内部的缺陷时,会发生反射、散射或透射,通过对超声波的接收和分析,可以确定材料内部的缺陷类型、位置和大小。
二、焊缝超声波探伤标准。
1. 超声波探伤设备。
进行焊缝超声波探伤时,应选择适当的超声波探伤设备,包括超声波发射探头、接收探头、超声波检测仪器等。
设备的选择应符合相关标准要求,并经过校准和检定。
2. 探伤方法。
焊缝超声波探伤可以采用直接接触法、浸润法或者接触耦合法。
在选择探伤方法时,应根据具体情况和标准要求进行合理选择,并保证探伤过程中与焊缝的充分接触。
3. 探伤参数。
探伤参数包括超声波频率、波束角、增益、脉冲重复频率等。
在进行焊缝超声波探伤时,应根据焊缝的材料、厚度、几何形状等特点,合理选择探伤参数,并进行相应的调节和优化。
4. 探伤结果评定。
根据焊缝超声波探伤的标准,对探伤结果进行评定和判定。
根据探伤结果,判断焊缝内部是否存在缺陷,确定缺陷的类型、位置和大小,并进行相应的等级评定。
5. 报告和记录。
对焊缝超声波探伤的整个过程进行记录和报告,包括探伤设备的选择和校准、探伤方法和参数的选择、探伤结果的评定等内容,确保探伤过程的可追溯性和可复制性。
三、注意事项。
1. 操作人员应具备专业的超声波探伤技术知识和操作技能,严格按照相关标准和要求进行操作。
2. 探伤设备应定期进行维护和保养,确保设备的正常工作状态。
3. 在进行焊缝超声波探伤前,应对焊缝进行清洁和表面处理,保证探伤的准确性和可靠性。
四、结论。
焊缝超声波探伤是一种有效的焊接质量检测方法,对焊接件的质量和安全性具有重要意义。
严格按照相关标准和要求进行焊缝超声波探伤,可以有效地发现焊缝内部的缺陷,保证焊接件的质量和可靠性。
常用超声波探伤标准要求
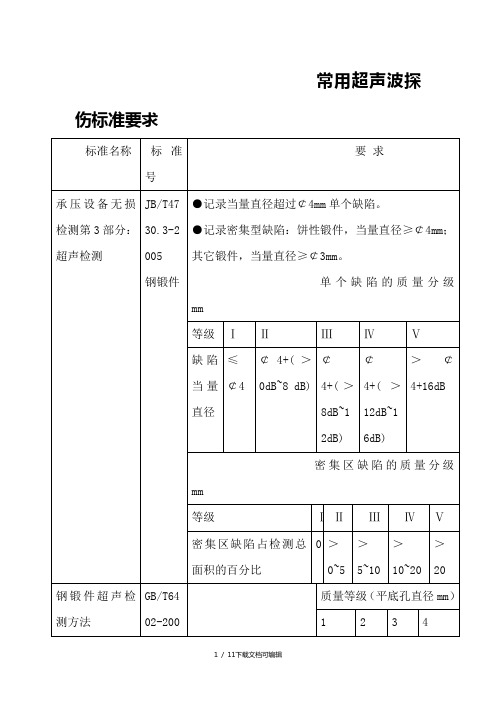
允许极限值的大小分级
当量范围
部位允许量
总数
轴身
传动轴
非传动轴
¢2~¢3
12
5பைடு நூலகம்
5
22
>¢3~¢4
3
1
4
8
总数
15
6
9
30
●在应力较大区域不允许有当量直径大于3mm的单个缺陷缺陷和≥2mm当量直径的密集缺陷信号。
300~600MW汽轮发电机转子锻件技术条件
JB/T7178-93
●其他部位不允许当量直径>3mm的缺陷。
●不允许有当量直径≥2mm的密集缺陷。(密集型缺陷信号是指在边长50mm立方体内,数量不少于5个,当量直径不小于2mm的缺陷信号)
●≥2mm当量单个缺陷在合格证书中注明。
25-200MW汽轮机转子体和主轴锻件技术条件
JB/T1265-93
●当量直径2mm以下的单个分散缺陷信号不计,但杂波高度应低于当量直径2mm幅度的50%。
●不允许有当量直径≥1.6mm连续性缺陷信号和游动缺陷信号。
●允许有当量直径1.6~3.55mm的缺陷存在,但相邻两个缺陷的距离不小于其较大缺陷直径的10倍,总数量不得超过30个。
●在应力较大区域,不允许有当量直径大于2mm的缺陷,和≥1.6mm当量直径的密集缺陷信号。
锻钢件无损检测
JB/T5000-15-2007
标准号
要求
模锻锤和大型机械锻压机用模块技术条件
GB11880-89
●允许存在个别的、分散的、不大于当量直径¢2mm的冶金缺陷。
●在100cm2的面积内,当量直径¢2~¢4 mm的冶金缺陷不超过3个,其中¢3~¢4 mm的冶金缺陷只允许有1个。
超声波、磁粉探伤要求

3、焊缝及热影响区打磨
探伤时无焊接药皮
超声波、磁粉、渗透探伤的适用范围及要求
超声波探伤
除焊缝外,表面光洁度均不低于12.5um;形状尽量简单
磁粉探伤
渗透(着色)探伤
铸钢件
1、应在正火后进行
2、合适尺寸范围:25-400mm
1、只适合铁磁性材料;
2、只适合检测距表面3mm的开口及不开口的气孔、夹渣、裂纹及缺陷;
3、表面应干净,无污物及氧化皮锈蚀。
1、只能检测开口缺陷;
2、适用于金属、非金属材料;
3、不适合多孔结构;
4、表面应干净;5、铸Fra bibliotek表面至少经打磨
锻件
1、探伤应在热处理后进行;
2、最小厚度25mm。即厚度小于25mm对小于φ2缺陷不易检出
轴类
以下三种情况不适宜
1、细长轴类横向缺陷
2、离开心部与轴线平行的缺陷
3、直径40mm以下
焊缝
1、板厚应≥8mm;
超声波探伤轨头核伤判伤标准

超声波探伤轨头核伤判伤标准
一、核伤尺寸
核伤尺寸是判断轨头核伤严重程度的重要指标之一。
根据超声波探伤结果,可以测量出核伤的直径和深度。
一般情况下,核伤直径大于1mm或深度大于2mm时,应判定为重伤。
对于直径小于1mm或深度小于2mm的核伤,应根据实际情况进行判定。
二、核伤深度
核伤深度是判断轨头核伤严重程度的另一个重要指标。
根据超声波探伤结果,可以测量出核伤的深度。
一般情况下,核伤深度大于2mm时,应判定为重伤。
对于深度小于2mm的核伤,应根据实际情况进行判定。
三、核伤位置
核伤位置也是判断轨头核伤严重程度的重要指标之一。
如果核伤位于轨头的关键部位,如轨颚、轨底等,则应判定为重伤。
如果核伤位于非关键部位,则应根据实际情况进行判定。
四、核伤数量
核伤数量也是判断轨头核伤严重程度的重要指标之一。
如果轨头上有多个核伤,则应判定为重伤。
如果只有一个或少数几个核伤,则应根据实际情况进行判定。
五、表面裂纹
表面裂纹也是轨头损伤的一种表现形式。
如果超声波探伤结果显示轨头表面存在裂纹,则应根据裂纹的长度、深度和位置进行判定。
如果裂纹较长、较深或位于关键部位,则应判定为重伤。
如果裂纹较短、较浅或位于非关键部位,则应根据实际情况进行判定。
- 1、下载文档前请自行甄别文档内容的完整性,平台不提供额外的编辑、内容补充、找答案等附加服务。
- 2、"仅部分预览"的文档,不可在线预览部分如存在完整性等问题,可反馈申请退款(可完整预览的文档不适用该条件!)。
- 3、如文档侵犯您的权益,请联系客服反馈,我们会尽快为您处理(人工客服工作时间:9:00-18:30)。
常用超声波探伤标准要求
•不允许有当量直径》2mm 的密集缺陷。
(密集型缺陷信号是指在边长 50mm 立方 体内,数量不少于5个,当量直径不小于 2mm 的缺陷信号) • > 2mm 当量单个缺陷在合格证书中注明。
•当量直径2mm 以下的单个分散缺陷信号不计,但杂波高度应低于当量直径 2mm 幅度的50%
•单个分散的缺陷定义为: 相邻两缺陷之间的距离大于其中较大缺陷当量直径 10
倍的缺陷。
•单个分散的缺陷应符合下表规定
•轴身部位离中心孔表面 30mm 以内和外圆槽深加
1.6m m 的密集型缺陷。
允许有当量直径 3mm 以下的单个分散缺陷存在。
•不允许有游动缺陷信号和条状缺陷信号。
标准名称 标准号 承压设备无损检测第 3 JB/T4730.3-
•记录当量直径超过0 4mm 单个缺陷 部分:超声检测 2005 •记录密集型缺陷:饼性锻件,
当量直径》0 4mm 其它锻件,当量直径》0 3mm
钢锻件
单个缺陷的质量分级
mm
等级
密集区缺陷占检测总面积的百分比
I
V
钢锻件超声检测方法 0 > 0~5
> 5~10
>10~20
V > 20
体和主轴锻件技术条件 3
•其他部位不允许当量直径 >3mm 的缺陷
锻件和锻材的超声检测 25MW 以下汽轮机转子 25-200MW 汽轮 机转子 JB/T1265-9 体和主轴锻件技术条件
3。