24米箱梁模板设计.doc
铁路客专双线简支箱梁定额

24米双线简支箱梁预制 有桥面防水保护层
24米双线简支箱梁预制 无桥面防水保护层
32米双线简支箱梁预制 有桥面防水保护层 2322-Ⅱ 直线
32米双线简支箱梁预制 无桥面防水保护层 2322-Ⅱ 直线
24米双线简支箱梁支架施工 有桥面防水保护层
24米双线简支箱梁支架施工 无桥面防水保护层
32米双线简支箱梁支架施工 有桥面防水保护层
32米双线简支箱梁支架施工 无桥面防水保护层
24米双线简支箱梁移动模架施工 有桥面防水保护层
24米双线简支箱梁移动模架施工 无桥面防水保护层
32米双线简支箱梁移动模架施工 有桥面防水保护层
32+48+32m预应力砼连续梁 有桥面防水防护层
32+48+32m预应力砼连续梁 无桥面防水防护层
48+80+48m 预应力砼连续梁 有桥面防水防护层
48+80+48m 预应力砼连续梁 无桥面防水防护层。
预制箱梁预制作业指导书
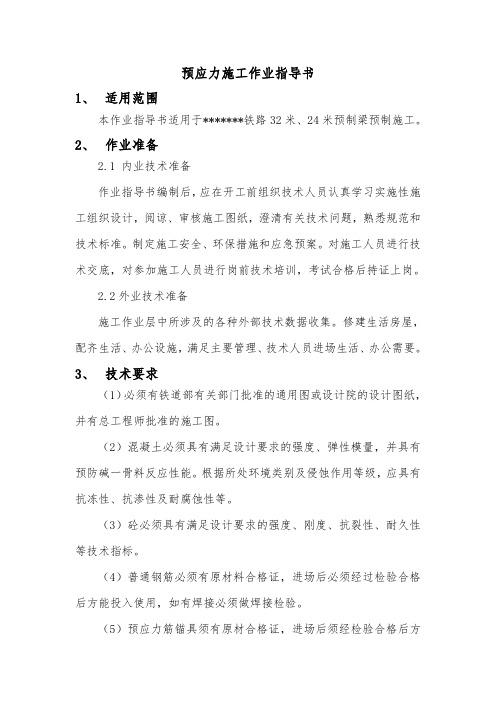
预应力施工作业指导书1、适用范围本作业指导书适用于*******铁路32米、24米预制梁预制施工。
2、作业准备2.1 内业技术准备作业指导书编制后,应在开工前组织技术人员认真学习实施性施工组织设计,阅谅、审核施工图纸,澄清有关技术问题,熟悉规范和技术标准。
制定施工安全、环保措施和应急预案。
对施工人员进行技术交底,对参加施工人员进行岗前技术培训,考试合格后持证上岗。
2.2外业技术准备施工作业层中所涉及的各种外部技术数据收集。
修建生活房屋,配齐生活、办公设施,满足主要管理、技术人员进场生活、办公需要。
3、技术要求(1)必须有铁道部有关部门批准的通用图或设计院的设计图纸,并有总工程师批准的施工图。
(2)混凝土必须具有满足设计要求的强度、弹性模量,并具有预防碱一骨料反应性能。
根据所处环境类别及侵蚀作用等级,应具有抗冻性、抗渗性及耐腐蚀性等。
(3)砼必须具有满足设计要求的强度、刚度、抗裂性、耐久性等技术指标。
(4)普通钢筋必须有原材料合格证,进场后必须经过检验合格后方能投入使用,如有焊接必须做焊接检验。
(5)预应力筋锚具须有原材合格证,进场后须经检验合格后方能投入使用。
4、施工程序与工艺流程4.1 施工程序在钢筋车间预制好半成品钢筋后,在胎膜架上绑扎染体钢筋,利用门吊将梁体钢筋移至台座底模上,再立钢模板、安装上面板钢筋,浇筑混凝土。
4.2 工艺流程 (见下页图)5、施工要求5.1 钢筋制安5.1.1 钢筋加工5.1.1.1 钢筋下料及质量要求梁场技术部门根据施工图纸发下料单,下料人员根据下料单进行试弯,试弯合格并负责人签认后开始正常下料,根据供料尺寸的情况统筹安排以减小钢筋的损耗,构造筋下料切断刀口平齐,两端头不应弯曲。
5.1.1.2 钢筋加工钢筋下料、弯曲成型、检查钢筋绑扎成型梁体钢筋安装、检查端模安装穿胶管侧模安装、检查桥面钢筋安装、检查桥面附属件成型安装混凝土灌注养护脱模初张拉梁体出生产台位吊至终张拉台位终张拉压浆、封锚、桥面施工出厂检验、后期修补发运桥梁底模、端模修整、检查支座板安装、检查原材料检验合格联接铁件安装、检查侧模修整、喷涂水泥、砂石料、减水剂检验合格混凝土拌合抽拔纵、横向张拉制孔器、泄水孔模具取料、做砼试件、养护砼试件强度试验砼试件强度试验砼试件强度弹模试验及龄期取料、做试件、养护后张梁制梁工艺流程图(1)在进行弯曲成型前,应先熟悉加工钢筋规格、形状和各部尺寸及弯曲顺序。
24米箱梁设计制作及安装

24米箱梁设计制作及安装箱梁是一种常用的桥梁结构,其结构形状呈矩形或梯形,被称为箱梁。
箱梁在桥梁工程中应用广泛,其优点是具有较高的承载能力和刚度,适用于跨越较大跨度的桥梁。
箱梁在桥梁工程中承担着重要的作用,设计与制作质量直接关系到桥梁的使用寿命和安全性。
本文将介绍24米箱梁的设计、制作和安装过程。
1.设计首先,对桥梁的设计要进行合理规划和计算,确定箱梁的截面形状、尺寸和材料。
设计时需考虑到箱梁所承受的荷载,包括静荷载、动荷载和温度荷载等。
箱梁的设计需符合国家规范和桥梁设计标准,确保其刚度和稳定性。
设计过程中要考虑箱梁的整体性能,尽量减小桥梁的自重,提高整体刚度。
对箱梁的截面和布置筋进行优化设计,确保箱梁在各种荷载下的受力性能符合要求。
同时,还需考虑箱梁的施工性和维护性,确保其具有良好的使用性能和寿命。
2.制作箱梁的制作是桥梁建设中的重要环节,其质量直接关系到桥梁的安全和稳定。
在制作24米箱梁时,首先要选择优质的混凝土和钢筋材料,保证箱梁的材质符合设计要求。
然后,进行模板浇筑,采用专业的模板设备进行箱梁的浇筑,确保箱梁的几何尺寸和表面平整度。
在箱梁的制作过程中,要注意控制浇筑质量,严格按照设计要求进行施工,并对箱梁的浇筑过程进行监测和验收。
箱梁制作完成后,要进行质量检测和试验,确保箱梁的强度和稳定性符合设计要求。
3.安装箱梁的安装是桥梁建设的关键环节,直接影响到桥梁的使用和安全。
在安装24米箱梁时,首先要进行场地勘察和施工准备,确保箱梁的安装位置和设备符合要求。
然后,进行吊装和安装作业,采用专业的吊装设备和施工工艺进行箱梁的安装。
箱梁安装时要注意控制吊装质量,确保箱梁的安装位置和姿态正确,避免出现倾斜或错位现象。
在箱梁安装完成后,要进行检测和验收,确保箱梁的承载能力和稳定性符合要求。
同时,要对箱梁进行加固和防护,确保其具有良好的使用性能和寿命。
总之,24米箱梁的设计、制作和安装是桥梁建设中的重要工作,需要科学合理地规划和实施。
预应力张拉技术交底(三级)
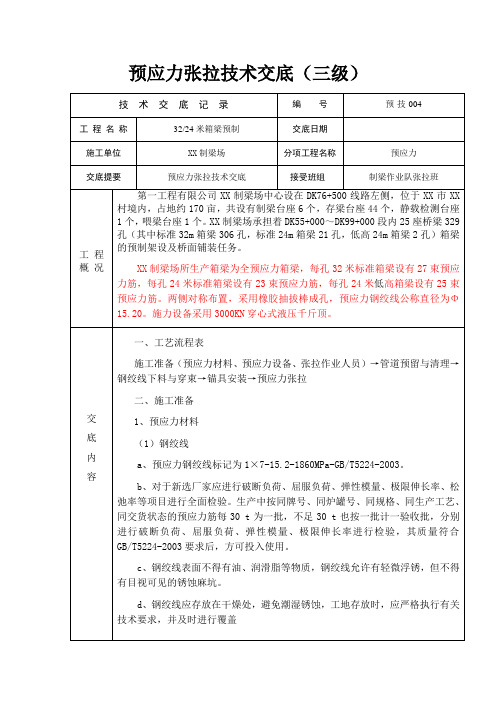
预应力张拉技术交底(三级)交底内容行调整。
正常生产后每100孔进行一次损失测试。
需测试的各项瞬时损失有:管道摩阻、锚口摩阻、锚垫板喇叭口摩阻、锚具回缩损失等。
2、梁体钢绞线束张拉程序:(1)预张拉:0→初应力0.2σk(作伸长值标记)→张拉至预张拉设计要求的控制应力(测伸长值)→回油、锚固(测量夹片外露量)。
(2)初张拉:0→初应力0.2σk(作伸长值标记)→张拉至初张拉设计要求的控制应力(测伸长值)→回油、锚固(测量夹片外露量)。
(3)终张拉:0→初应力0.2σk(作伸长值标记)→1.0σk(持荷5min)→补充到σk(测控制油压伸长量及工具夹片外露量)→回油、锚固(测量工作夹片外漏量)。
预应力筋布置详见下图。
张拉顺序及断面图通桥(2009)2229-Ⅳ预应力筋布置断面图预张拉:2N1b-2N6-2N2b初张拉:2N8-N1a-2N9-2N4-2N7终张拉:2N2b-2N10-N1a-2N2a-2N5-2N1b-2N3-2N6-2N9-2N4-2N7-2N2c-2N8;交底内容通桥(2009)2229-Ⅴ预应力筋布置断面图预张拉:N1a-2N5-2N2a初张拉:2N7-2N1b-2N3终张拉:N1a-2N4-2N2b-2N8-2N1b-2N6-2N5-2N7-2N2a-2N3;3、实际伸长量的量测及计算方法实际伸长值的量测采用量测千斤顶油缸活塞行程和夹片外露量的方法。
预应力筋张拉前,应先调整到初应力σ(取终张控制应力的20%),伸长量应从初应力时开始量测。
在σ应力下,量测油缸活塞行程δ油缸0、工具锚夹片外露量δ工具锚夹片0;在δk应力下, 量测油缸活塞行程δ油缸k、工具锚夹片外露量δ工具锚夹片k,则实际伸长值△L1的计算公式如下:△L1=δ油缸k+δ工具锚夹片k-δ油缸0-δ工具锚夹片04、梁体纵向钢绞线束张拉操作工艺:安放工作锚锚具,把夹片装入锚具内,再将钢管套在钢绞线上,沿着钢绞线把夹片整齐敲击进锚具内。
铁路24米双线箱梁模板设计制作及安装
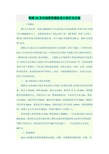
铁路24米双线箱梁模板设计制作及安装一、工程概况XX运专线是第一条按200Km/h行车速度设计的新建铁路,其客车最大时速可达250Km/h以上,是铁路建设史上的标志性工程。
XX桥梁厂承担了该线上XX特大桥的319孔箱梁的制造任务。
其中24m双线箱梁309孔,20m双线箱梁10孔。
XXX运专线后张法双线箱梁是我国首次在铁路上采用大截面、大体积结构。
因此,针对后张法双线箱梁,制定了《预制后张法预应力混凝土简支梁技术条件》、《桥梁制造与架设施工技术细则》、《XXX运专线桥梁工程质量检验评定标准》及《预制后张法预应力混凝土简支梁静载试验方法及评定标准》等。
这些标准和规范与原T梁箱比,具有设计和制造标准新,科技含量高,吊梁、运梁、存梁的精度要求高,检验验收标准严等特点。
因此,对箱梁模板的设计,制造与安装,提出了较高的要求。
二、24米箱梁的主要技术参数XXX运专线24m双线后张法预应力混凝土单箱简支梁,为单箱单室等高度箱梁。
梁全长24.6m;跨度24.0m;梁高为2.0m;桥面宽度为12.40m。
梁体腹板采用斜截面形式,其坡度为1:10。
箱梁底板宽度:中间部分为6.12m,梁端为6.52m。
顶板厚度为30cm,底板厚度25cm,梁端底板加厚至55cm。
腹板中段厚度为45cm,梁端加厚至85cm,箱梁内最大净空高度145cm。
梁端设横隔墙,隔墙上进人孔净高为90cm。
其跨中截面尺寸如图1.1:梁体混凝土强度等级为C48,弹性模量为35GPa,一片(孔)梁混凝土体积为204.3m3。
桥面防水层采用氯化聚乙烯防水卷材和聚氨脂防水涂料共同构成的TQF-I型防水层,桥面保护层采用C38纤维混凝土。
一片(孔)梁设计总重达567.1t。
三、箱梁模板24m双线整孔预制箱梁模板由底模、内模、外侧模和端模组成。
内模、外模、台座总体布置见图1.2。
(一)、制梁模板制造及安装要求模板应具有足够的强度、刚度和稳定性,确保箱梁在施工过程中,各部位尺寸及预埋件的准确,并在多次反复使用下不产生影响梁体外形的刚度。
预制箱梁施工方案(30m)
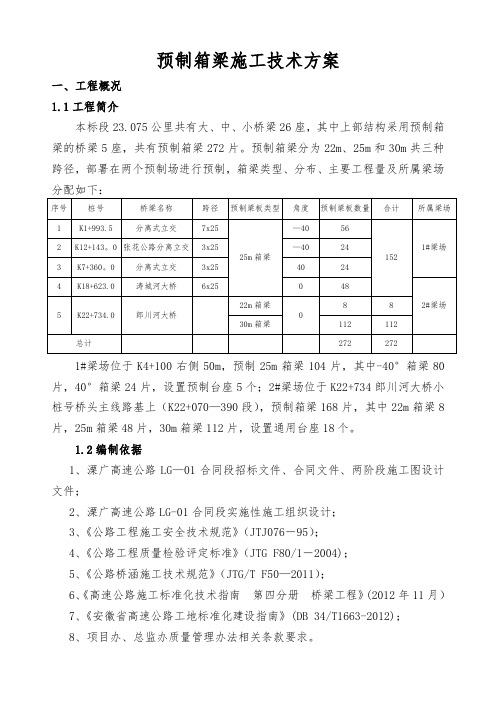
预制箱梁施工技术方案一、工程概况1.1工程简介本标段23.075公里共有大、中、小桥梁26座,其中上部结构采用预制箱梁的桥梁5座,共有预制箱梁272片。
预制箱梁分为22m、25m和30m共三种跨径,部署在两个预制场进行预制,箱梁类型、分布、主要工程量及所属梁场分配如下:1#梁场位于K4+100右侧50m,预制25m箱梁104片,其中-40°箱梁80片,40°箱梁24片,设置预制台座5个;2#梁场位于K22+734郎川河大桥小桩号桥头主线路基上(K22+070—390段),预制箱梁168片,其中22m箱梁8片,25m箱梁48片,30m箱梁112片,设置通用台座18个。
1.2编制依据1、溧广高速公路LG—01合同段招标文件、合同文件、两阶段施工图设计文件;2、溧广高速公路LG-01合同段实施性施工组织设计;3、《公路工程施工安全技术规范》(JTJ076-95);4、《公路工程质量检验评定标准》(JTG F80/1-2004);5、《公路桥涵施工技术规范》(JTG/T F50—2011);6、《高速公路施工标准化技术指南第四分册桥梁工程》(2012年11月)7、《安徽省高速公路工地标准化建设指南》(DB 34/T1663-2012);8、项目办、总监办质量管理办法相关条款要求。
1。
3适用范围本方案适用于指导溧广高速公路LG—01合同段预制箱梁施工。
二、预制箱梁首件概况、目的、计划进度、人员、设备投入情况2.1首件概况结合现场条件及施工准备情况,预制箱梁首件选择在K22+734郎川河大桥,该桥梁长682m共分4联,左幅为8x30m+22m+6x40m+6x30m,右幅为6x30m+22+2x30m+6x40m+6x30m,横坡为双向2%,设计交角0°,与老郎川河水流方向交角为15°,跨径分为22m、30m及40m,桥面宽2×12。
5m,上部结构跨老郎川河主河道采用6跨40m先简支后连续预应力混凝土T梁,引桥采用30m预应力混凝土先简支后连续箱梁,小桩号跨河堤处设22m调节跨,调节跨采用22m预应力混凝土先简支后连续箱梁。
高速铁路后张法预应力简支箱梁(24m低高度梁)技术交底

24m低高度梁技术交底一、工程概况贵溪制梁场位于贵溪市河潭镇丰田村,起讫里程为DK417+435~DK418+005,位于正线左侧,占地面积165896m2,约248.8亩,负责718片箱梁的预置和架设,其中32m箱梁654孔,24m普高梁46孔,24m低高梁18孔。
24m低高度梁分布在弋阳特大桥0#台与21#墩间,其中有3跨为连续梁。
该梁使用图纸主要为通桥(2008)2322A-I和通桥(2008)8388A,本技术交底主要参照以上两份图纸,并结合相关规范进行编制。
二、梁体结构介绍截面类型为单箱单室等高度简支箱梁,梁端顶板、底板、腹板局部向内侧加厚。
截面中心梁高2.45米,防护墙内侧净宽8.8米,桥上人行道钢栏杆内侧净宽11.9米,桥梁宽12米,建筑总宽为12.28米。
梁长为24.6米,跨度23.5米,横桥向支座中心距4.8米。
因18片低高度梁位于曲线设声屏障地段(声屏障位于梁体左侧),故预应力按二期恒载160~180KN/M布置,即N1a、N1b、N2c、N2d等7个孔道设9根预应力筋,使用80mm的抽拔管,其余16个孔道均为8根预应力筋,使用80mm抽拔管。
张拉计算时,锚口及喇叭口损失暂按控制应力的6%计算,管道摩阻系数和管道偏差系数暂按0.55和0.0015考虑。
梁体应预设反拱,跨中暂设为11mm,其他位置按二次抛物线过度;理论计算扣除自重后预应力产生的反拱为6mm,残余徐变为4mm;轨道铺设后梁体的徐变上拱值不得大于10mm。
梁体因混凝土干燥收缩及预应力作用下的理论平均压缩量上缘为4.20mm,下缘为9.24mm,梁体结构重心位于跨中截面梁体中心线,距跨中梁底1.541m~1.573m处。
三、使用的材料1、混凝土梁体混凝土强度等级为C50,封锚采用强度等级为 C50的干硬性补偿收缩混凝土,防护墙、遮板及电缆槽竖墙混凝土强度等级为C40;电缆槽盖板采用RPC混凝土。
各等级混凝土性能指标及采用的原材必须要符合《客运专线预应力混凝土简支梁暂行技术条件》、《客运专线高性能混凝土暂行技术条件》及其他相关规范的要求。
现浇箱梁工序操作手册
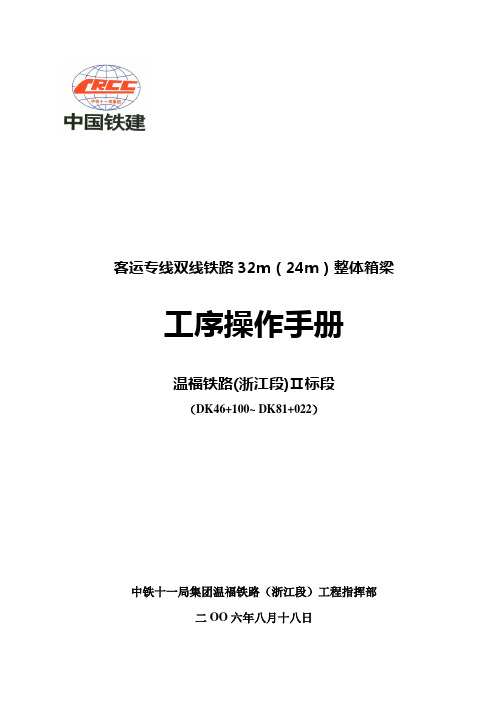
客运专线双线铁路32m(24m)整体箱梁工序操作手册温福铁路(浙江段)Ⅱ标段(DK46+100~ DK81+022)中铁十一局集团温福铁路(浙江段)工程指挥部二OO六年八月十八日支座安装工序操作手册支座的安装参照通桥(2005)8356进行,本简支箱梁采用4个KTPZ-I -6000(5000)型铁路客运专线桥梁盆式橡胶支座(括号外为32米梁采用型号、括号内为24米梁采用型号),分别有一个固定支座(GD)、横向活动支座(HX)、纵向活动支座(ZX)、多向活动支座(DX)。
(1)垫石在浇注过程中预留3cm,安装完后注浆;(2)支座采用预埋套筒和锚固螺栓方式连接,在墩台顶面支承垫石部位,深度为锚栓长度加预留螺栓孔,锚栓预留尺寸:直径为套筒直径加60+20-0mm60+20-0mm,预留锚栓孔中心及对角线位置偏差不得超过10mm;盆式橡胶支座控制项目(3)支座安装前,工地要检查支座连接状况是否正常,但不得任意松动上下支座连接螺栓;(4)凿毛支座就位部位的支撑垫石表面,清除预留螺栓孔中的杂物,安装灌浆用模板,并用水将支承垫石表面浸湿;(5)用钢楔块楔入支座四角,找平支座,并将支座底面调整到设计标高,严格调整支座水平,在支座底面与支承垫石之间应留有20~30mm间隙,安装灌浆用模板;(6)仔细检查支座中心位置及标高后,用无收缩、高强度灌注材料灌注,注浆材料性能要求如下(7)采用重力式灌浆方式,灌注支座下部及锚栓孔处孔隙,注浆过程应从支座中心部位向四周注浆,直至钢模与支座底板周边间隙观察到注浆材料全部注满为止,工人在旁边用钢筋或铁丝辅助捣实;支座正式注浆前要进行工艺试验;如下图钢模(8)注浆前,应初步计算所需浆体体积,注浆实用浆体数量不应与计算值产生过大误差,应防止中间缺浆;(9)注浆材料终凝后,拆除模板及四角钢楔块,检查是否有漏浆处,必要时对漏浆处进行补浆,并用砂浆填堵钢楔块抽出后的空隙,拧紧下支座板锚栓,待灌注梁体混凝土终凝后,及时拆除各支座上下支座连接钢板及螺栓,并安装支座钢围板(注意:各支座上下支座连接钢板及螺栓必须在张拉前拆除)。
箱梁梁体混凝土方量计算书
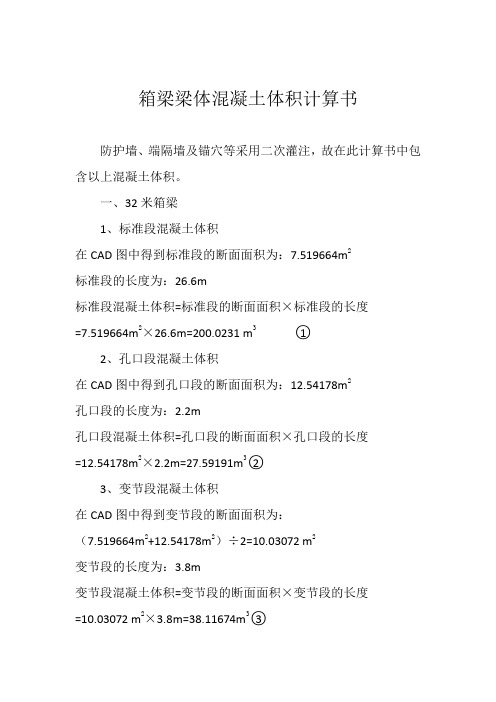
箱梁梁体混凝土体积计算书防护墙、端隔墙及锚穴等采用二次灌注,故在此计算书中包含以上混凝土体积。
一、32米箱梁1、标准段混凝土体积在CAD图中得到标准段的断面面积为:7.519664m2标准段的长度为:26.6m标准段混凝土体积=标准段的断面面积×标准段的长度=7.519664m2×26.6m=200.0231 m3○12、孔口段混凝土体积在CAD图中得到孔口段的断面面积为:12.54178m2孔口段的长度为:2.2m孔口段混凝土体积=孔口段的断面面积×孔口段的长度=12.54178m2×2.2m=27.59191m3○23、变节段混凝土体积在CAD图中得到变节段的断面面积为:(7.519664m2+12.54178m2)÷2=10.03072 m2变节段的长度为:3.8m变节段混凝土体积=变节段的断面面积×变节段的长度=10.03072 m2×3.8m=38.11674m3○34、顶板泄水孔混凝土体积在CAD图中得到两侧泄水孔的断面面积为:0.005026m2在CAD图中得到中线泄水孔的断面面积为:0.015393 m2两侧泄水孔的长度为:0.5m 数量为:16个中线泄水孔的长度为:0.55 m 数量为:8个顶板泄水孔混凝土体积=Σ(泄水孔的断面面积×泄水孔的长度×泄水孔数量)=0.005026m2×0.5m×16+0.015393m2×0.55 m ×8=0.11m3○45、底板泄水孔混凝土体积在CAD图中得到底板泄水孔的断面面积为:0.005026m2底板泄水孔的长度为:0.24m 数量为:32个顶板泄水孔混凝土体积=泄水孔的断面面积×泄水孔的长度×泄水孔数量=0.005026m2×0.24m×32=0.04m3○56、通风孔混凝土体积在CAD图中得到两侧通风孔的断面面积为:0.007853m2在CAD图中得到中线通风孔的断面面积为:0.07853 m2两侧通风孔的长度为:0.297m 数量为:16个中线通风孔的长度为:0.24m 数量为:8个顶板通风孔混凝土体积=Σ(通风孔的断面面积×通风孔的长度×通风孔数量)=0.007853m2×0.297m×16+0.007853m2×0.24 m ×8=0.052395m3○67、锚穴混凝土体积:0.61 m3○78、梁端检查孔混凝土体积在CAD图中得到底板检查孔的断面面积为:0.415008m2在CAD图中得到中腹板检查孔的断面面积为:0.2325m2底板厚度为:0.7m中腹板厚度为:0.5m检查孔孔混凝土体积=Σ(检查孔的断面面积×混凝土厚度)=(0.415008m2×0. 7m+0.2325m2×0.5m)×2=0.82m3○89、胶拔管占混凝土体积胶拔管的断面面积为:0.005024m2胶拔管的总长度为:830 m胶拔管占混凝土体积=胶拔管的断面面积×胶拔管的总长度=0.005024m2×830 m=4.17m3○910、梁体钢筋占的混凝土体积钢筋总重为:54.8t梁体钢筋占的混凝土体积为:54.8t÷7.85 t/ m3=6.98m3○1011、桥面吊装孔及端隔墙灌注预留孔占的混凝土体积预留孔的断面面积为:0.0113097m2预留孔的总长度为:5.88 m预留孔占混凝土体积=预留孔的断面面积×预留孔的总长度=0.0113097m2×5.88 m=0.066501m3○11因此32米梁体灌注时的混凝土总体积应为:○1+○2+○3-Σ(○4 +…..+ ○11)=252.6728 m3二、24米箱梁1、标准段混凝土体积在CAD图中得到标准段的断面面积为:7.519664m2标准段的长度为:18.6m标准段混凝土体积=标准段的断面面积×标准段的长度=7.519664m2×18.6m= 139.8658m3○12、孔口段混凝土体积在CAD图中得到孔口段的断面面积为:12.54178m2孔口段的长度为:2.2m孔口段混凝土体积=孔口段的断面面积×孔口段的长度=12.54178m2×2.2m=27.59191m3○23、变节段混凝土体积在CAD图中得到变节段的断面面积为:(7.519664m2+12.54178m2)÷2=10.03072 m2变节段的长度为:3.8m变节段混凝土体积=变节段的断面面积×变节段的长度=10.03072 m2×3.8m=38.11674m3○34、顶板泄水孔混凝土体积在CAD图中得到两侧泄水孔的断面面积为:0.005026m2在CAD图中得到中线泄水孔的断面面积为:0.015393 m2两侧泄水孔的长度为:0.5m 数量为:12个中线泄水孔的长度为:0.55 m 数量为:6个顶板泄水孔混凝土体积=Σ(泄水孔的断面面积×泄水孔的长度×泄水孔数量)=0.005026m2×0.5m×12+0.015393m2×0.55 m ×6=0.08m3○45、底板泄水孔混凝土体积在CAD图中得到底板泄水孔的断面面积为:0.005026m2底板泄水孔的长度为:0.24m 数量为:24个顶板泄水孔混凝土体积=泄水孔的断面面积×泄水孔的长度×泄水孔数量=0.005026m2×0.24m×24=0.029m3○56、通风孔混凝土体积在CAD图中得到两侧通风孔的断面面积为:0.007853m2在CAD图中得到中线通风孔的断面面积为:0.07853 m2两侧通风孔的长度为:0.297m 数量为:12个中线通风孔的长度为:0.24m 数量为:6个通风孔混凝土体积=Σ(通风孔的断面面积×通风孔的长度×通风孔数量)=0.007853m2×0.297m×12+0.007853m2×0.24 m ×6=0.039296 m3○67、锚穴混凝土体积:0.44 m3○78、梁端检查孔混凝土体积在CAD图中得到底板检查孔的断面面积为:0.415008m2在CAD图中得到中腹板检查孔的断面面积为:0.2325m2底板厚度为:0.7m中腹板厚度为:0.5m检查孔孔混凝土体积=Σ(检查孔的断面面积×混凝土厚度)=(0.415008m2×0. 7m+0.2325m2×0.5m)×2=0.82m3○89、胶拔管占混凝土体积胶拔管的断面面积为:0.005024m2胶拔管的总长度为:454m胶拔管占混凝土体积=胶拔管的断面面积×胶拔管的总长度=0.005024m2×454m=2.28m3○910、梁体钢筋占的混凝土体积钢筋总重为:43.9t梁体钢筋占的混凝土体积为:43.9t÷7.85 t/ m3=5.59m3○1011、桥面吊装孔及端隔墙灌注预留孔占的混凝土体积预留孔的断面面积为:0.0113097m2预留孔的总长度为:5.88 m预留孔占混凝土体积=预留孔的断面面积×预留孔的总长度=0.0113097m2×5.88 m=0.066501m3○11因此24米梁体灌注时的混凝土总体积应为:○1+○2+○3-Σ(○4+…..+ ○11)=196.2328m3综上所述:32米梁的混凝土灌注体积为:252.6728 m324米梁的混凝土灌注体积为:196.2328m3计算:ADMIN 复核:XXXX 日期:XXXX。
铁路客运专线24m后张法单线箱梁现场预制工法
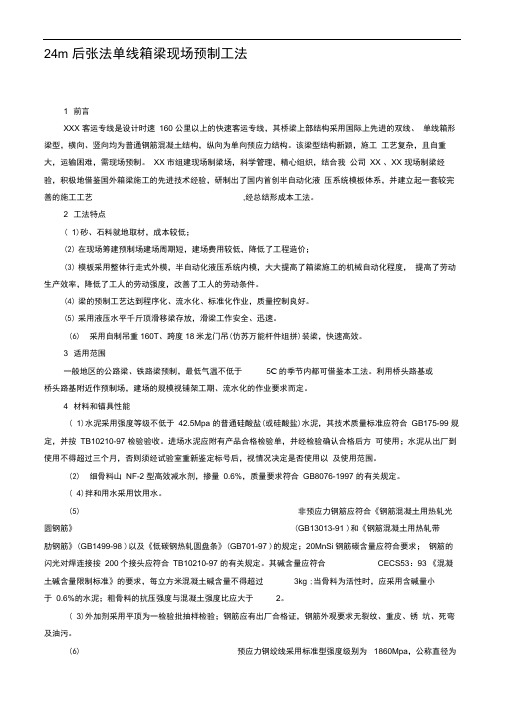
24m 后张法单线箱梁现场预制工法1 前言XXX 客运专线是设计时速160 公里以上的快速客运专线,其桥梁上部结构采用国际上先进的双线、单线箱形梁型,横向、竖向均为普通钢筋混凝土结构,纵向为单向预应力结构。
该梁型结构新颖,施工工艺复杂,且自重大,运输困难,需现场预制。
XX 市组建现场制梁场,科学管理,精心组织,结合我公司XX 、XX 现场制梁经验,积极地借鉴国外箱梁施工的先进技术经验,研制出了国内首创半自动化液压系统模板体系,并建立起一套较完善的施工工艺,经总结形成本工法。
2 工法特点( 1)砂、石料就地取材,成本较低;(2)在现场筹建预制场建场周期短,建场费用较低,降低了工程造价;(3)模板采用整体行走式外模,半自动化液压系统内模,大大提高了箱梁施工的机械自动化程度,提高了劳动生产效率,降低了工人的劳动强度,改善了工人的劳动条件。
(4)梁的预制工艺达到程序化、流水化、标准化作业,质量控制良好。
(5)采用液压水平千斤顶滑移梁存放,滑梁工作安全、迅速。
(6)采用自制吊重160T、跨度18米龙门吊(仿苏万能杆件组拼)装梁,快速高效。
3 适用范围一般地区的公路梁、铁路梁预制,最低气温不低于5C的季节内都可借鉴本工法。
利用桥头路基或桥头路基附近作预制场,建场的规模视铺架工期、流水化的作业要求而定。
4 材料和锚具性能( 1)水泥采用强度等级不低于42.5Mpa 的普通硅酸盐(或硅酸盐)水泥,其技术质量标准应符合GB175-99 规定,并按TB10210-97 检验验收。
进场水泥应附有产品合格检验单,并经检验确认合格后方可使用;水泥从出厂到使用不得超过三个月,否则须经试验室重新鉴定标号后,视情况决定是否使用以及使用范围。
(2)细骨料山NF-2 型高效减水剂,掺量0.6%,质量要求符合GB8076-1997 的有关规定。
( 4)拌和用水采用饮用水。
(5)非预应力钢筋应符合《钢筋混凝土用热轧光圆钢筋》(GB13013-91 )和《钢筋混凝土用热轧带肋钢筋》(GB1499-98 )以及《低碳钢热轧圆盘条》(GB701-97 )的规定;20MnSi钢筋碳含量应符合要求;钢筋的闪光对焊连接按200个接头应符合TB10210-97 的有关规定。
现浇箱梁预压方案

机场大道(江海大道-金通三大道)A标现浇箱梁模板支架预压专项方案编制:审核:审批:南通路桥工程有限公司机场大道(江海大道-金通三大道)工程A标项目经理部二○一七年七月目录一、编制依据及原则 (1)二、工程概况 (1)三、支架系统结构 (4)四、支架预压施工 (4)五、预压荷载计算 (5)六、支架预压应急措施 (6)七、预压安全注意事项 (7)八、环保及文明施工 (7)一、编制依据及原则1.1编制依据⑴《公路桥涵施工技术规范》(JTG/T F50-2011);⑵《建筑结构荷载规范》GB50009-2012;⑶《建筑施工高处作业安全技术规范》(JGJ 80—91);⑷《城市桥梁工程施工与质量验收规范》(CJJ2-2008);⑸《危险性较大的分部分项工程安全管理办法》(建质[2009]87号);⑹《公路桥涵地基与基础设计规范》(JTGD63-2007);⑺《建筑施工碗扣式钢管脚手架安全技术规范》(JGJ166-2016);⑻《钢管满堂支架预压技术规程》(JGJ/T194-2009);⑼设计图纸及相关文件1.2编制原则⑴安全第一、质量至上原则。
精心组织施工,合理安排工期。
坚持技术先进、方案优化、重信誉守合同、施工组织科学合理、按期优质安全高效、不留后患;⑵要求方案切实可行、经济合理、可操作性强。
⑶坚持用工制度的动态管理。
根据工作的需要,合理配置劳动力资源。
1.3编制目的检验支架及地基的强度及稳定性,消除支架的非弹性变形,消除地基的沉降变形,测量出支架的弹性变形。
二、工程概况1.主线桥本标段主线桥25.5m桥面采用等截面大悬臂单箱四室斜腹板箱梁,标准顶板宽度25.3m,标准底板宽度17.46m;翼缘板悬臂3.4m,外挑翼缘厚度22~50cm。
箱梁顶板厚度26cm,底板厚度25~35cm,腹板厚度40~70cm,梁高为1.8m、2.0m。
箱梁的支点设横梁,端横梁宽度1.8m,中横梁宽度2.5m。
主线桥箱梁标准断面图2.匝道桥A、B匝道桥面宽9.6 m采用等截面大悬臂单箱单室斜腹板箱梁,标准顶板宽度8.8m,标准底板宽度4.348m;翼缘板悬臂1.65m,外挑翼缘厚度22~36cm。
箱梁贝雷梁支架现浇施工方案

目录一、工程概况:............................................................................................................................................... - 3 -二、工程数量:............................................................................................................................................ - 3 -三、施工流程................................................................................................................................................ - 5 -四、施工技术方案........................................................................................................................................ - 5 -1、基础施工方案................................................................................................................................ - 5 -2、支架施工 ......................................................................................................................................... - 6 -3、支架预压 ......................................................................................................................................... - 7 -4、底模安装调整.................................................................................................................................. - 8 -5、钢筋和侧、内模安装...................................................................................................................... - 8 -6、混凝土施工.................................................................................................................................... - 10 -7、张拉 ............................................................................................................................................... - 11 -8、管道压浆、封端............................................................................................................................ - 11 -9、支架、模板拆除............................................................................................................................ - 12 -五、质量管理体系及保证措施.................................................................................................................. - 12 -1、质量目标 ....................................................................................................................................... - 12 -2、质量保证体系................................................................................................................................ - 13 -3、质量保证管理措施........................................................................................................................ - 13 -4、质量保证技术措施........................................................................................................................ - 13 -六、安全管理体系及保证措施.................................................................................................................. - 16 -1、安全目标 ....................................................................................................................................... - 16 -2、安全组织机构................................................................................................................................ - 16 -3、施工安全保证管理措施................................................................................................................ - 16 -4、施工安全保证技术措施................................................................................................................ - 17 -5、施工应急措施................................................................................................................................ - 18 -七、环境保证措施...................................................................................................................................... - 19 -1、环境目标 ....................................................................................................................................... - 19 -2、环境保护体系及组织机构............................................................................................................ - 19 -3、环境保护管理措施........................................................................................................................ - 19 -4、环境保护技术措施........................................................................................................................ - 19 -八、文明施工.............................................................................................................................................. - 20 -1、雨季施工措施................................................................................................................................ - 20 -2、文明施工措施................................................................................................................................ - 21 -九、其他保证措施...................................................................................................................................... - 23 -1、保护地下管线及周围构筑物措施................................................................................................ - 23 -2、防汛措施 ....................................................................................................................................... - 23 -3、文物保护措施................................................................................................................................ - 24 -4、消防措施 ....................................................................................................................................... - 24 -5、治安措施 ....................................................................................................................................... - 25 -6、防台风措施.................................................................................................................................... - 25 -24m现浇箱梁贝雷梁支架专项施工方案根据厦深铁路Ⅷ标的总体施工组织设计和现场的实际情况,由于部分桥梁处于两隧道之间无法运梁,并且数量比较少,建设桥梁预制厂经济不合理,切割后浇筑翼板受力有影响。
大桥0#块施工方案
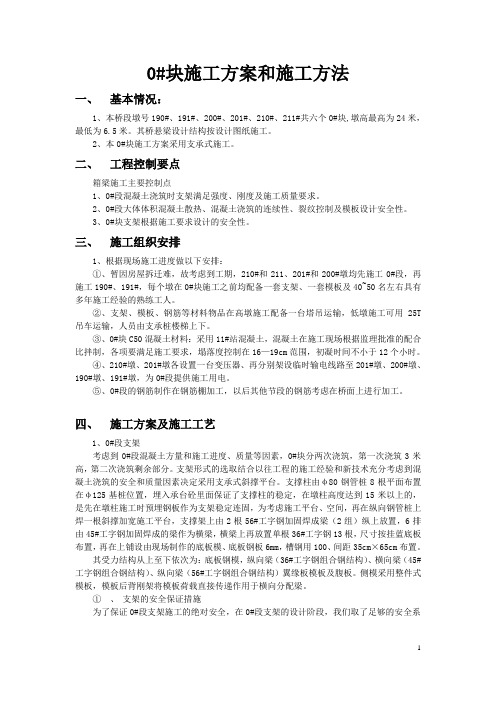
0#块施工方案和施工方法一、基本情况:1、本桥段墩号190#、191#、200#、201#、210#、211#共六个0#块,墩高最高为24米,最低为6.5米。
其桥悬梁设计结构按设计图纸施工。
2、本0#块施工方案采用支承式施工。
二、工程控制要点箱梁施工主要控制点1、0#段混凝土浇筑时支架满足强度、刚度及施工质量要求。
2、0#段大体体积混凝土散热、混凝土浇筑的连续性、裂纹控制及模板设计安全性。
3、0#块支架根据施工要求设计的安全性。
三、施工组织安排1、根据现场施工进度做以下安排:①、暂因房屋拆迁难,故考虑到工期,210#和211、201#和200#墩均先施工0#段,再施工190#、191#,每个墩在0#块施工之前均配备一套支架、一套模板及40~50名左右具有多年施工经验的熟练工人。
②、支架、模板、钢筋等材料物品在高墩施工配备一台塔吊运输,低墩施工可用25T 吊车运输,人员由支承桩楼梯上下。
③、0#块C50混凝土材料:采用11#站混凝土,混凝土在施工现场根据监理批准的配合比拌制,各项要满足施工要求,塌落度控制在16—19cm范围,初凝时间不小于12个小时。
④、210#墩、201#墩各设置一台变压器、再分别架设临时输电线路至201#墩、200#墩、190#墩、191#墩,为0#段提供施工用电。
⑤、0#段的钢筋制作在钢筋棚加工,以后其他节段的钢筋考虑在桥面上进行加工。
四、施工方案及施工工艺1、0#段支架考虑到0#段混凝土方量和施工进度、质量等因素,0#块分两次浇筑,第一次浇筑3米高,第二次浇筑剩余部分。
支架形式的选取结合以往工程的施工经验和新技术充分考虑到混凝土浇筑的安全和质量因素决定采用支承式斜撑平台。
支撑柱由φ80钢管桩8根平面布置在φ125基桩位置,埋入承台砼里面保证了支撑柱的稳定,在墩柱高度达到15米以上的,是先在墩柱施工时预埋钢板作为支架稳定连固,为考虑施工平台、空间,再在纵向钢管桩上焊一根斜撑加宽施工平台,支撑架上由2根56#工字钢加固焊成梁(2组)纵上放置,6排由45#工字钢加固焊成的梁作为横梁,横梁上再放置单根36#工字钢13根,尺寸按挂蓝底板布置,再在上铺设由现场制作的底板模、底板钢板6mm,槽钢用100、间距35cm×65cm布置。
移动模架施工工艺

移动模架施工工艺一、DXZ32/900下承自行式移动模架设计目的DXZ32/900下承自行式移动模架设计要紧目的是为了甬台温铁路客运专线中铁四局管段内双线32m及24m整孔箱梁原位现浇施工而设计的。
二、移动模架的使用范畴为了满足管段内32m、24m箱梁原位现浇,考虑工期安排要求,本标段工程共配置8台移DXZ32/900下承自行式移动模架适用于甬台温铁路中铁四局管段内32m和24m跨的简支箱梁原位现浇施工。
适用工作环境:1、环境温度:-20C°~ 50C°2、环境风力:移位时≤6级,浇注时≤8级,非工作时≤12级3、电源:380V、50Hz、4AC4、支承移动模架的桥墩基础必须平坦,现场无易燃、易爆、有毒等危险品及腐蚀性气体。
六、移动模架构造说明(郑州大方)七、移动模架首孔预压试验1、空载试验①.拉线测量两根箱梁轨底相对高差;操作边主梁竖直油缸,使整个模床差不多同步顶升120mm。
停15分钟;再拉线测量中主梁的相对下沉量。
然后分三次差不多同步下落于滑座上。
②.使两组模架向前移动过孔,并测量纵移速度,使两组主梁差不多同步向前移动。
③.回位后,用微调机构准确定位各梁的纵向位置。
④.顶升模床到浇筑位置。
⑤.在以上动作中,要同步检查电、液、机部分是否正常。
记录油压表的读数。
2、首孔堆载预压试验①.移动模架拼装后,在第一孔箱梁施工前要对移动模架进行预压试验。
预压的目的要紧有:a.检验移动模架主梁的实际抗弯能力。
b.排除移动模架的非弹性变形。
c.实测支点处的沉降值。
d.实测跨中的挠度值,与理论运算跨中挠度值对比,验证理论运算值准确性,为箱梁浇注预拱度设置提供体会数据。
②.拟采纳钢筋和钢绞线作为压重物进行移动模架预压。
依照等效原理,满足跨中最大弯矩相等,在跨中堆码钢筋及钢绞线,堆码重量约900t。
堆码尺寸详见下图:③.主梁上L/4、L/2、3/4处各选定1组测点,测量移动模架原始标高、挠度,压重后测移动模架的标高、挠度,6小时、12小时、24小时后均测出移动模架各测点变形值,卸载后测量移动模架各测点标高、挠度并做好记录。
箱梁架设施工方案

箱梁架设施工方案一:工程概况:省道高淄路岔河桥改建工程上部为35m+40m+35m预制箱梁,全桥共有24片箱梁,其中35m箱梁16片,40m箱梁8片。
40m跨径箱梁中梁重量为136T,边梁重量为145T。
我部按照40m边梁重量选用架桥机和运梁炮车。
箱梁的架设使用步履式SDL B型双导梁架桥机,架桥机纵向长度为90米,主梁高度:起重部分高2.5m,长为65m,附支过孔部分为25米,高度为1.8米,设计吊装重量为170T,纵横移动方便,性能良好,特别是架桥机的过孔,采用架桥机自带导梁的过孔方式,简单快捷,安全性能良好;此架桥机曾成功架设长度50米重量160多吨的T梁。
运梁车为推、拉双方向皆能行驶的专用运梁炮车,前、后设计有方向控制,设计运输能力为180T,为新购车辆,性能良好。
预制场在高淄路小清河大桥的北面路基上,运梁时能方便的进入主路线,预制梁在梁场装车时采用2台80T的龙门吊车。
二:使用的机械设备及人员安排:在预制梁安装中使用的主要机械设备如下:1、龙门吊车2台,每台的起吊重量为80T。
2、运梁炮车1台,设计运输能力为180T。
3、双导梁架桥机1台,设计起重能力为170T。
4、其它配套使用的小型机具一宗。
人员安排:安装负责人:1、前台安装:张京华;2、后台装梁:潘福忠;3、技术负责人:武海波;现场技术负责人:白长峰;4、安全负责人:张珂;起吊装车:8人;运输:3人;安装10人;专职安全人员:3人。
三:安装顺序及工期安排:1、安装顺序为:首先安装右幅箱梁,从淄博方向(第三孔)向高青方向(第一孔)进行,安装时先安装每孔的外边梁,然后由外向内依次进行梁板安装。
安装完成第三孔后,再安装第二孔,最后安装第一孔(见下图)。
右幅桥:2008年5月10日—2008年6月10日左幅桥:2008年7月20日—2008年8月10日四:架设方案做好箱梁架设的准备工作,在路基上拼装架桥机,并进行试运行及报请验收;由于本桥的箱梁安装重量较大,为了保证运输中的安全,将左侧的现有道路上的坑槽等不平的地方提前整平并压实。
24米贝雷片计算(070312)

支架拼设方案检算说明1、该方案采用贝雷片拼设的支架进行现浇梁体的施工。
2、贝雷片上方铺设工字钢作为分配梁,工字钢上方直接铺设定型钢模板。
3、现浇梁内模支架通过底板泄水孔内安放Φ80mm的实体铁棒或填筑满砼的钢管伸出铁板层,然后在铁柱上安放纵向的工字钢,在工字钢上拼设内模支架。
4、为确保模板顺利拆除,在钢管桩顶设置Φ=500mm的钢砂箱。
5、为加快支架安装的速度,所有分配梁、钢管桩、砂箱均统一使用同一规格。
6、在确定是否采用单支墩还是双支墩,主要从以下几方面考虑:(1)如果采用单支墩,为保证贝雷梁的[Q]、[M]满足要求,需增加贝雷片、分配梁等材料的数量。
(2)如果采用双支墩,虽然增加了基底处理的工程量,但减少了贝雷梁、分配型钢的数量而且从控制挠度、支架受力等方面均比设单支墩效果好。
设2排钢管桩立柱结构拼设检算成果书一、检算过程中用到的各种参数钢材E=2.1×105MPa=2.1×108KPa单排单层贝雷片I=250497.2cm4, W=3578.5 cm3[M]=788.2KN.m; [Q]=245.2KN贝雷片自重305/3=102kg/m=1.02KN/m22号工字钢I=3400cm4, W=309 cm3, 每延米自重q=42kg/m。
20号工字钢I=2370cm4, W=239 cm3, 每延米自重q=27.9kg/m。
28号工字钢I=7110cm4, W=508 cm3, 每延米自重q=43.4kg/m。
32号工字钢I=11620cm4, W=726 cm3, 每延米自重q=57.7kg/m。
二、腹板部分,设3排贝雷片钢材E=2.1×105MPa=2.1×108KPa3排单层贝雷片力学参数I=250497.2×3=751491.6cm4,W=10735.5 cm3[M]=2364.6KN.m; [Q]=735.6KN检算过程所应考虑的各种荷载:1、贝雷片自重q1=915/3=305kg/m=3.05KN/m2、施工人员荷载q2=2.5×2.75×1=6.875 KN/m3、振捣荷载q3=2.0×2.75=5.5KN/m4、模板荷载(在腹板附近处)q4=腹板处模板重量+内模标准架+内模绗架+内模模板系+内模支架系+底模系=(81.08×4.0/2/32/(2.5+3.3)+0.1+0.11+0.312(内模暂考虑30t)+0.3+24.779/32/5×2.75)×10=20.21KN/m5、梁体自重腹板q5=(2.5+2.5+0.4)×0.45×1/2×25=30.375KN/m顶板q6=(0.65×0.45×1+(0.65+0.3)/2×2.75)×25=39.97KN/m底板q7=1×0.28×2.75×25=19.25KN/m6、分配型钢(暂按2根32号工字钢间距2m)q8=5×2×0.042×2.75/2=0.5775KN/m贝雷片所受荷载q= q1+ q2 + q3 + q4 + q5 + q6 + q7 + q8 =(6.875+5.5)×1.4+(3.05+20.21+30.375+39.97+19.25+0.5775)×1.2=153.447KN/m,贝雷梁跨径按6.5m进行检算,检算时按三跨连续梁受均布荷载进行简化计算M=0.1×ql2=0.1×153.447×6.52=648KN.m<[M]=2364.6KN.m满足要求Q=0.6ql=0.6×153.447×6.5=598.44<[Q]×1.2=882.72KN(剪力在临时结构中可不考虑荷载分项系数,而且可考虑应力提高系数1.2,在进行Q检算过程中如果将荷载分项系数不进行考虑,即能满足结构受力特性,不需考虑应力提高系数)满足要求f=0.677ql4/(100EI)=0.677×153.447 ×6.54/(100×2.1×108×500994.4×10-8)=0.0018m=1.8mm<[f]=l/400=6500/400=16.25mm三、底板箱梁中心位置处设双排贝雷片双排单层贝雷片I=500994.4cm4, W=7157 cm3[M]=1576.4KN.m; [Q]=490.4KN检算过程所考虑的荷载:1、贝雷片自重q1=710/3=203.3kg/m=2.033KN/m2、施工人员荷载q2=2.5×2.75×1=6.875 KN/m3、振捣荷载q3=2.0×2.75=5.5KN/m4、模板荷载q4=底板荷载+内模标准架+内模绗架+内模模板系+内模支架系=(24.779/32/5×2.75+0.1+0.11+0.312(内模暂考虑30t)+0.3)×10=20.21KN/m6、梁体自重顶板q5=(0.65+0.3)/2×2.75)×25=32.66KN/m底板q6=1×0.28×2.75×25=19.25KN/m7、分配型钢(2根32号工字钢间距2m)q7=5×2×0.042×2.75/2=0.5775KN/m贝雷片所受荷载q= q1+ q2 + q3 + q4 + q5 + q6 + q7 =(6.875+5.5)×1.4+1.2×(2.03+20.21+32.66+19.25+0.5775)=106.3KN/m,贝雷梁跨径按9m进行检算,检算时按三跨连续梁受均布荷载进行简化计算M=0.1×ql2=0.1×106.3×6.52=449.1KN.m<[M]=1576.4KN.m满足要求Q=0.6ql=0.6×106.3×6.5=414.57<[Q]×1.2=588KN(剪力在临时结构中可不考虑荷载分项系数,而且可考虑应力提高系数1.2,在进行Q检算过程中如果将荷载分项系数不进行考虑,即能满足结构受力特性,不需考虑应力提高系数)满足要求f=0.677ql4/(100EI)=0.677×106.3 ×6.54/(100×2.1×108×751491.6×10-8)=0 .0012m=1.2mm<[f]=l/400=6500/400=16.25mm四、翼缘板距箱梁中心6.75m的位置处设双排贝雷片钢材E=2.1×105MPa=2.1×108Kpa, I=500994.4cm4, W=7157 cm3[M]=1576.4KN.m; [Q]=490.4KN贝雷片自重305/3=102kg/m=1.02KN/m检算过程所考虑的荷载:1、贝雷片自重q1=710/3=203.3kg/m=2.033KN/m2、施工人员荷载q2=2.5×2.0×1=5 KN/m3、振捣荷载q3=2.0×2.0=4.0KN/m4、模板荷载q4=侧模=(81.08×4/5.85)×10=55.44KN/m5、梁体自重顶板q5=(0.2+0.3)/2×2×25=12.5KN/m6、分配型钢(2根32号工字钢间距2m)q6=5×2×0.042×2.0/2=0.42KN/m贝雷片所受荷载q= q1+ q2 + q3 + q4 + q5 + q6 =(5+4)×1.4+1.2×(55.44+2.033+12.5+0.42)=97.071KN/m 贝雷梁跨径按9m进行检算,检算时按三跨连续梁受均布荷载进行简化计算M=0.1×ql2=0.1×97.071×6.52=410.1KN.m<[M]=1576.4KN.m满足要求Q=0.6ql=0.6×97.071×6.5=378.6<[Q]×1.2=588KN(剪力在临时结构中可不考虑荷载分项系数,而且可考虑应力提高系数1.2,在进行Q检算过程中如果将荷载分项系数不进行考虑,即能满足结构受力特性,不需考虑应力提高系数)满足要求f=0.677ql4/(100EI)=0.677×97.071 ×6.54/(100×2.1×108×500994.4×10-8)=0.0011m=1.1mm<[f]=l/400=6500/400=16.25mm五、钢管立柱顶横梁各种参数设计1、跨中检算跨中的钢管立柱尽量布置在纵向贝雷梁的附近,以减少工字钢横梁上弯矩和剪应力,具体检算如下:将作用在工字钢上的荷载简化为集中荷载,根据现场实际受力情况,横梁简化成4跨不等跨连续梁,将钢管立柱尽量布置在贝雷梁在下方,除箱梁中心线处和距箱梁中心线4.75m处对横梁跨中有弯矩外,其他位置的贝雷梁均在钢管立柱正上方。
预制箱梁施工作业指导书
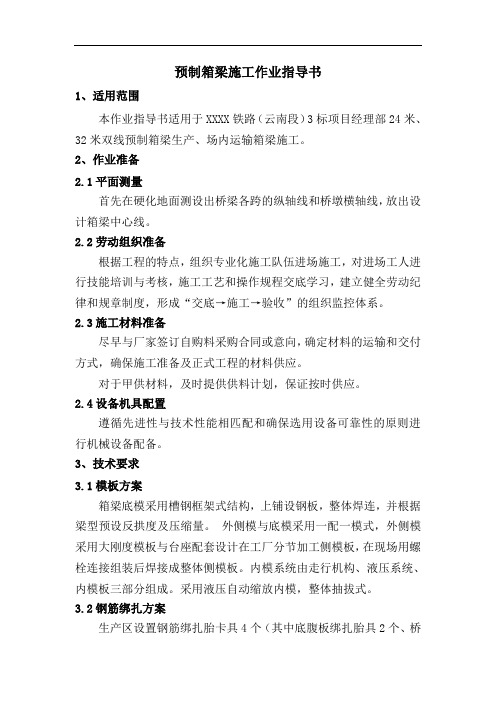
预制箱梁施工作业指导书1、适用范围本作业指导书适用于XXXX铁路(云南段)3标项目经理部24米、32米双线预制箱梁生产、场内运输箱梁施工。
2、作业准备2.1平面测量首先在硬化地面测设出桥梁各跨的纵轴线和桥墩横轴线,放出设计箱梁中心线。
2.2劳动组织准备根据工程的特点,组织专业化施工队伍进场施工,对进场工人进行技能培训与考核,施工工艺和操作规程交底学习,建立健全劳动纪律和规章制度,形成“交底→施工→验收”的组织监控体系。
2.3施工材料准备尽早与厂家签订自购料采购合同或意向,确定材料的运输和交付方式,确保施工准备及正式工程的材料供应。
对于甲供材料,及时提供供料计划,保证按时供应。
2.4设备机具配置遵循先进性与技术性能相匹配和确保选用设备可靠性的原则进行机械设备配备。
3、技术要求3.1模板方案箱梁底模采用槽钢框架式结构,上铺设钢板,整体焊连,并根据梁型预设反拱度及压缩量。
外侧模与底模采用一配一模式,外侧模采用大刚度模板与台座配套设计在工厂分节加工侧模板,在现场用螺栓连接组装后焊接成整体侧模板。
内模系统由走行机构、液压系统、内模板三部分组成。
采用液压自动缩放内模,整体抽拔式。
3.2钢筋绑扎方案生产区设置钢筋绑扎胎卡具4个(其中底腹板绑扎胎具2个、桥面顶板绑扎胎具2个)。
梁体和桥面钢筋在胎卡具上人工绑扎,再利用50吨龙门吊吊装到台座上进行安装。
3.3混凝土拌制采用自动计量,微机控制强制式搅拌机系统的泵送混凝土施工工艺。
3.4箱梁养护混凝土养生采用自然养生直到梁体出场。
3.5箱梁场内运输梁场提梁机将箱梁吊放至运梁车上,由运梁车运至架设桥位,架桥机架设安装。
4、主要施工程序1、底板钢筋提前绑扎,验收并整体吊装,底板预应力孔道定位,抽拔管的安装定位2、腹板钢筋提前绑扎,验收并整体吊装,腹板预应力孔道定位,抽拔管的安装定位3、内板整体安装、调位与验收4、顶板钢筋提前绑扎,验收并整体吊装,顶板预应力孔道定位,抽拔管的安装定位及验收5、预埋件定位安装、定位及验收6、混凝土浇注、养生7、待到混凝土强度到达设计强度,抽出抽拔管,并进行初张拉,终张拉,压浆封锚5、施工工序及工艺流程施工工艺流程框图5.1 预埋、预留工程施工5.1.1梁体钢配件的加工(1)钢配件包括:支座板、防落梁支架预埋板和预埋螺杆、伸缩缝预埋件、一般接触网支柱预埋板、下锚支柱预埋板、下锚拉线预埋板、泄水管固定螺母、综合接地螺母、梁体接地螺母、防撞墙、电缆槽竖墙、人行道挡板等,在相应位置将预埋钢筋及预埋件与梁体钢筋一同绑扎、安装,以保证预埋筋与梁体的连接。
通桥(2221)模板技术文件

模板设计方案5.1.项目概况:根据贵方《招标函》的要求,以及与贵方在技术细节上的过程沟通,我们做出了相应的设计方案。
本方案在设计上即保证了模板结构的合理性、强度和刚度,同时又注重模板的外观质量、使用的便利性、通用性和操作效率等。
为用户着想,尽可能提高模板的通用性,降低制造成本。
厦深铁路32米箱梁模板的设计方案是:外模固定不纵移,采用端包侧的形式。
内模采用整体式液压内模,内模拼装完成后,整体滑入台座钢筋笼,拆模时,整体滑出。
5.2.模板主要构造及工作性能:5.2.1、侧模32米侧模标准侧模在梁长方向分为四块,中间两块长8米,两端两块长8.3米。
侧模有腹板模、翼模及桁架。
标准侧模可满足31.5米普高粱(通桥[2008]2221A-Ⅱ/Ⅶ)。
拆除中间一块8米侧模、移模及桁架,可满足23.5米普高梁(通桥[2008] 2221A -Ⅳ)。
32米高梁与24米、20米低梁共用模板需特制,即将侧模在断面方向分为三块,并配特制桁架。
其他与标准侧模相同。
这套侧模在满足31.5米普高粱(通桥[2008] 2221A -Ⅱ/Ⅶ)的同时,在重新调整安装后可满足24米、20米低梁(通桥[2008] 2221A -Ⅵ)。
侧模采用无上拉杆受力结构设计,由外模板、外模桁架、桁架支撑等组成。
梁体底板弧度由侧模完成。
与底模一对一的配置,联结方式简单可靠。
侧模的面板采用8mm钢板,在面板背后采用槽钢作支撑与桁架相连,外模板与底模间的垂直高度可通过外模桁架底部手动千斤顶调节,外模板的翼模部分与外模桁架之间采用调节螺杆支撑,用于调整模板平直度及线型。
为便于施工在翼模外侧加宽1m,可在侧模上部安装钢轨,作为养护棚车、工作平台车、提浆抹平机的轨道,同时还可用于布置振动桥走道、人行走道及栏杆,两端设有供施工人员上下的扶梯,每端设置两个。
外模桁架由型钢组成的两片主桁架及上、下平联组成。
外模桁架的作用是作为骨架以保证整个外模板形状的稳定。
在外模桁架下部的每个节点处均设有手动千斤顶用于调整外模的安装高度和脱模。
- 1、下载文档前请自行甄别文档内容的完整性,平台不提供额外的编辑、内容补充、找答案等附加服务。
- 2、"仅部分预览"的文档,不可在线预览部分如存在完整性等问题,可反馈申请退款(可完整预览的文档不适用该条件!)。
- 3、如文档侵犯您的权益,请联系客服反馈,我们会尽快为您处理(人工客服工作时间:9:00-18:30)。
24米箱梁模板设计下面是下面给大家带来关于24米箱梁模板设计的相关内容,以供参考。
一、工程概况沈客运专线是我国第一条按200Km/h行车速度设计的新建铁路,其客车最大时速可达250Km/h以上,是我国铁路建设史上的标志性工程。
中铁大桥局谷城桥梁厂承担了该线上月牙河特大桥的319孔箱梁的制造任务。
其中24m双线箱梁309孔,20m双线箱梁10孔。
秦沈客运专线后张法双线箱梁是我国首次在铁路上采用大截面、大体积结构。
因此,针对后张法双线箱梁,铁道部制定了《预制后张法预应力混凝土简支梁技术条件》、《桥梁制造与架设施工技术细则》、《秦沈客运专线桥梁工程质量检验评定标准》及《预制后张法预应力混凝土简支梁静载试验方法及评定标准》等。
这些标准和规范与原T 梁箱比,具有设计和制造标准新,科技含量高,吊梁、运梁、存梁的精度要求高,检验验收标准严等特点。
因此,对箱梁模板的设计,制造与安装,提出了较高的要求。
二、24米箱梁的主要技术参数秦沈客运专线24m双线后张法预应力混凝土单箱简支梁,为单箱单室等高度箱梁。
梁全长24.6m;跨度24.0m;梁高为2.0m;桥面宽度为12.40m.梁体腹板采用斜截面形式,其坡度为1:10.箱梁底板宽度:中间部分为6.12m,梁端为6.52m.顶板厚度为30cm,底板厚度25cm,梁端底板加厚至55cm.腹板中段厚度为45cm,梁端加厚至85cm,箱梁内最大净空高度145cm.梁端设横隔墙,隔墙上进人孔净高为90cm.其跨中截面尺寸如图1.1:梁体混凝土强度等级为C48,弹性模量为35GPa,一片梁混凝土体积为204.3m3.桥面防水层采用氯化聚乙烯防水卷材和聚氨脂防水涂料共同构成的TQF-I型防水层,桥面保护层采用C38纤维混凝土。
一片梁设计总重达567.1t.三、箱梁模板24m双线整孔预制箱梁模板由底模、内模、外侧模和端模组成。
内模、外模、台座总体布置见图1.2.、制梁模板制造及安装要求模板应具有足够的强度、刚度和稳定性,确保箱梁在施工过程中,各部位尺寸及预埋件的准确,并在多次反复使用下不产生影响梁体外形的刚度。
模板的支撑必须支承在可靠的基础上,做好基底的防水和防冻措施,模板及支撑的弹性压缩和下沉度必须满足设计要求。
后张梁应根据设计要求及制梁的实际情况设置反拱。
根据秦沈客运专线预制后张法预应力混凝土简支梁技术条件和桥梁工程质量检验评定标准规定的模板安装允许偏差如下:a、全长:±10mm;b、高度:±5mm;c、上翼缘内外侧偏离设计位置:+10mm,-5mm;d、底板、顶板厚度:+10mm,0;e、腹板厚度:+10mm,-5mm;f、腹板中心偏离设计位置:10mm;g、底板平整度:2mm;h、模板垂直度:3mm;I、相邻模板错台:2mm;j、模板表面平整度:3mm;k、模板接缝处缝隙:≤1mm;l、支座板位置处任意两点高差:≤1mm;m、四支座中心相对高差:≤2mm;n、底板反拱度:±2mm;o、端模预留孔道偏离设计位置:≤3mm.、底模箱梁一次灌注混凝土重量达530多吨,加上梁体模板重达90多吨和每平方米1.5KN的施工荷载,底模每延米荷载达27吨以上。
为使底模板刚度大且满足受力均匀的要求,底模面板采用12mm厚的钢板与槽钢组成井字型整体焊接结构,利用钢结构底横梁将底模受力传递到台座基础。
井字型结构分段制作,便于调整其平整度和底模的反拱度。
底模的反拱设置根据底模的分段呈折线布置,同时为了将模板受力均匀地传递给基础,采用了三点支撑的工字型底横梁,与混凝土地基有效地结合成整体,既增加了底模的刚度,也增加了混凝土条形地基的横向刚度,同时节约了钢材的用量。
横梁的间距为800mm.底模板断面见图1.3.底模与侧模的密封采用燕尾橡胶条进行密封,底模与端模的密封采用海绵橡胶条进行密封。
、外模箱梁的梁高2m,上翼板悬挑宽度达3m,侧模板同时承受灌注混凝土的侧向压力和上翼板混凝土的竖向压力以及施工荷载。
为保证混凝土的密实,还须在侧模上设置振动器。
为保证梁体混凝土外侧的平整和光滑,采用刚度较大的整体侧模。
侧模由面板、面板加劲槽钢、面板加劲立带、侧模支腿、调节支撑和调节拉杆组成。
模板加劲立带的设置,确保了侧模双向受力的刚度;面板加劲槽钢的采用,节约了钢材的用量,还增加了侧模的纵向刚度;侧模立腿的使用,改变了侧模上翼的悬挑受力为简支受力的受力方式。
考虑到侧模刚度大,侧模立腿受力不匀,为保证在上翼板混凝土灌注时侧模不发生变形,增设立腿调节支撑和调节拉杆,通过调节支撑来保证侧模立腿的支撑高度,通过调节拉杆来对侧模立腿预施荷载压力,来保证侧模在混凝土灌注施工时的双向受力稳定。
外模结构见图1.4.外侧模板的分块和安装:为减少模板拼装时间,外侧模两端变截面4.3m段做成一段,中间16m作一节,不再拆除。
只在梁体起吊前,将外侧模立腿调节支撑松掉,模板向外略倾斜,使模板脱离梁体混凝土面。
待梁体张拉、吊运后外侧模复位,复位时不再用吊机,只需用立腿支撑调节,打紧钢楔,模板即安装到位。
端部变截面4.3m段因梁体张拉压缩,变截面模板须脱开混凝土面,以免造成梁体混凝土外观克损,其方法是将横梁上支承侧模板的活动刀口铁的销轴抽掉,使活动刀口铁向下转动,即可使模板完全脱离梁体。
模板复位只需用千斤顶将模板顶起,转动活动刀口铁,插上销轴后模板落位,然后调节支腿高度,打紧钢楔,模板即安装到位。
侧模面板端部采用刨光,使模板接缝密合。
模板接缝外侧用海绵橡胶条加木板条,木楔进行密封。
外模特点:1、外侧模采用了整体连接的方式,施工方便快捷。
减少了侧模之间的连接工作量,缩短了立模、拆模工序作业时间。
避免了连接件易丢失的现象。
2、降低了工人的劳动强度,消除了原分块模板缝易漏浆等质量问题,因而改善了梁体外观。
3、外侧模立柱撑杆的使用,使立模、拆模更加方便,模板的垂直度、高度等调节更加快速,并精确度高。
4、采用了刀口铁与钢楔联合组件,避免了跑模的问题。
5、侧模面两端刨光,使模板之间的接缝均小于1mm,并且采用燕尾橡胶条和海绵橡胶条密封,使箱梁表面基本上没有漏浆、接缝及错台。
箱梁表面质量较好。
、内模24m箱梁的中间段箱室高度为1450mm,箱室净宽却达5500mm,箱顶混凝土高度达387mm,箱室底宽为4670mm;梁端箱口高度为900mm,梁端箱口净宽为4070mm,箱室截面尺寸变化大,中间17.4m 为等截面段,梁端3.6m段为变截面段,同时秦沈客运专线预制后张法箱形梁技术条件规定:模板的最大变形不大于2mm,箱梁底板、顶板厚度的误差+10,0mm,腹板为+10,-5mm,因此给内模制造和安装带来很大困难。
现场采用两种内模方案。
1、液压式内模液压式内模有二种。
一种是液压整体收缩抽拔式内模。
其方案是设立内模纵梁,把整个内模按顶板和侧模铰接为三大块或多块,利用液压顶伸缩完成内模支模和拆模,利用整体内模床来支撑内模。
它的优点是:钢模整体性好;整体刚度大;表面平整光洁;混凝土表面平整、美观;容易保证梁体外观尺寸;支模和拆模时可一次整体完成,减少劳动用工和减轻工人的劳动强度。
其缺点是:由于精度高,带来加工制造困难,用钢量大,使用维修难度大,模板投资大,其箱体内油顶设置多,难以保持同步运动,因而使内模易变形,模板变形后难以修复;由于箱梁的两端带有隔墙,其整体内模脱模时须完全折叠,造成内模竖向刚度减小,移动时若支点不匀容易产生变形;因为箱室净空低,加上内模的油顶和支撑,减小了箱室的空间,给箱底混凝土灌注带来困难;立模时,只能在台座上完成,其工序时间较长。
一种是分段液压拼装式内模。
其方式是不设内模纵梁,按梁体的长度和箱室的变截面段把内模分成数段,内模的横截面与整体内模相同,顶板和侧模铰接为三大块或多块,采用可与内模分离的液压内模车来完成内模的支模和拆模。
其优点同液压整体抽拔式内模。
因内模纵向分段,解决了内模折叠的竖向刚度问题,减少了内模纵梁,但也产生了模板纵向拼接接缝多,易错台,在灌注时受混凝土挤压内模变形大,容易产生箱梁内箱尺寸误差超标;还存在用钢量大,生产人员增加,使用维修难度大,模板投资较大。
同时,立模时其工序时间较长。
2、拼装式内模工具式拼装内模:其方法是采用工字型断面的钢梁及节点板拼成环形骨架,以螺旋支撑杆组成稳定的三角体系,消除环形骨架拼装接点的微量变形;面板采用工具式钢模板拼装,在环形钢结构骨架上形成整体内模。
拼装式内模安装使用方法:先拼装骨架,后铺设面板。
骨架的拼装精度直接影响内模的整体精度。
拼装时控制好四个点的位置准确,上下两条线互相平行即可保证骨架精度,为此,先特制了四种骨架的拼装胎具。
骨架分段吊运,对位好后,用正反丝杆调节骨架。
这样做的优点:快速、方便、精度高。
内模拼装在拼装台位上拼装,拼装台位按箱梁底板变截面坡度设置相同高度的支承台位,在台位上首先固定相应变截面位置的内模骨架,以骨架来控制内模横截面的结构尺寸,在骨架上拼装工具式内模板块,以工具式内模板块来控制内模的纵向尺寸,内模采用一次拼装,整体成形,用整体来保证内模的刚度。
在侧模、梁体钢筋、端模安装完后,将内模整体吊装至制梁台位安装。
内模在台座上的安装对位:由两台10t门吊抬吊内模至制梁台位上,门吊初步对准台位,内模缓缓下落,当内模快要到位时,吊钩停止下落,检查纵向及横向位置,纵向以一端的端模为基准,调整另一端内模安装尺寸。
横向以一侧侧模为基准,对角进行调整,以保证精确对位。
内模与外侧模的相对位置利用通风孔穿M28螺栓拉结,以确保内模与外模的相对位置不变。
内模在底模上的固定,利用预制的混凝土垫块支承内模,其垫块中间预留孔洞以便穿螺栓,使内模与底模连结防止内模上浮。
拼装内模的特点:模板在分块上,考虑箱内施工的劳动强度和结构形式,把转角处模板分块减小,平、侧面模板分块的原则是,单块重量不超过35Kg,分块尺寸统一,可以互换。
由此带来制造加工快而且方便,钢结构用料少,造价低,便于梁体换型。
拼装式内模制造费用低廉,只相当于液压式整体内模的1/5~1/10.施工时可在台座外拼装成整体后吊运至制梁台位整体安装,占用台座的工序时间短,容易维修。
缺点是投入劳动力多,工人的劳动强度大。
与液压内模相比,箱梁内室表面接缝多,混凝土表面不太平整、不太光滑。
、箱梁模板安装顺序箱梁的立模顺序为:检查、维修底模→安装侧模→安装支座板→涂脱模剂→吊装梁体钢筋骨架→安装端模→穿制孔胶管→吊装内模→吊装桥面板钢筋→吊装桥面联结系。
四、立模注意事项1、模板应清理干净,脱模剂应涂刷均匀,不能漏刷或多涂。
2、模板的接缝应平顺,其错台不大于1mm,要严密不漏浆。
3、安装底模时应在底模上准确标出梁体的中轴线,并调整底模的反拱度。
4、安装外模时,要保证箱梁底板、腹板及腹板的倾斜度、隔墙的尺寸误差。