烧结工艺理论知识(全面)
烧结工艺介绍

烧结原料 三、回收料 在冶金及其它一些工业生产部门有不少副产 品,其含铁量都比较高,这些工业副产品如当作 废物抛弃,造成资源浪费而且导致环境恶化。烧 结配用这类工业副产品作为原料后,不仅可以降 低烧结成本,而且可以综合利用资源,保护环境 不被污染。烧结厂常用的工业副产品有: 1、瓦斯灰 瓦斯灰是高炉煤气带出来的炉尘,通常含铁40% 左右,它实际上是矿粉和焦粉的混合物。瓦斯灰 的粒度较细,呈深灰色,亲水性差。烧结料中加 入部分瓦斯灰,可节约铁料和燃料消耗。加上价 格低廉,还可以降低成本。进厂的瓦斯灰,要适 当加水润湿,以便运输和改善条件。
烧结工业的发展概况 2、工艺先进化,已被证实和利用的新工艺有: (1)改善原料中和(建立机械化和计算机控制的原料 场); (2)改善原料准备工艺(添加生石灰或消石灰,燃料分 加,分层布料,强化制粒等); (3)改进烧结技术(厚料层、高负压、高碱度、低燃耗, 混合料预热,富氧和热风烧结等) (4)强化烧结矿产品粒度。 (5)强调环境保护、资源综合利用烧结厂余热利用等。
烧结基本知识 二、烧结与炼铁的关系 烧结生产是炼铁生产的前工序,是整个钢铁工业生 产中的一个不可缺少的重要环节,也就是炼铁生产 的原料准备。烧结生产是为高炉服务的,所以烧结 矿的质量很大程度上决定了高炉生产的各项经济技 术指标和生铁质量。烧结生产的主要任务,是将铁 矿粉进行造块,为高炉冶炼提供优质的人造富矿。
技术质量处: 技术质量处:孙石磊
大纲
烧结基本知识 烧结工业发展概况 烧结原料介绍 烧结设备 烧结工艺流程 烧结矿的分类
一、为什么要进行烧结 在自然界中,金属状态的铁是极少见的。一般都和 其它元素结合成化合物。随着工业的发展,能直接 用于高炉冶炼的富矿越来越少,使得人们不得不开 采贫矿(品位25-40%)。但是贫矿直接入炉冶炼是 不经济的,所以,必须经过选矿处理,要选矿,就 必须对矿石进行破碎研磨。这样,选矿后的矿粉, 品位提高了,但其粒度(<0.043mm>90%)不符合 高炉冶炼要求,因此,对于开采出和筛选出来的矿 粉都必须经过造块后方可用于冶炼。
烧结基础知识

烧结基础知识烧结是把粉状物料转变为致密体,是一个传统的工艺过程。
那么你对烧结了解多少呢?以下是由店铺整理关于烧结知识的内容,希望大家喜欢!烧结的定义宏观定义:在高温下(不高于熔点),陶瓷生坯固体颗粒的相互键联,晶粒长大,空隙(气孔)和晶界渐趋减少,通过物质的传递,其总体积收缩,密度增加,最后成为具有某种显微结构的致密多晶烧结体,这种现象称为烧结。
微观定义:固态中分子(或原子)间存在互相吸引,通过加热使质点获得足够的能量进行迁移,使粉末体产生颗粒黏结,产生强度并导致致密化和再结晶的过程称为烧结。
烧结的方法及测量将试条放入烘箱内,在105~110℃下烘干至恒重。
在干燥器内冷却至室温后备用。
在天平上称取干燥后的试样重。
称取饱吸煤油后在煤油中试样重。
饱吸煤油后在空气中的试样重。
将称好重量的试样放入105~110℃烘箱内排除煤油,直至将试样中的煤油排完为止。
按编号顺序将试样装入高温炉中,装炉时炉底和试样之间撒一层薄薄的煅烧石英粉或Al2O3粉。
装好后开始加热,并按升温曲线升温,按预定的取样温度取样。
在每个取样温度点保温15min,然后从电炉内取出试样迅速地埋在预先加热的石英粉或Al2O3粉中,以保证试样在冷却过程中不炸裂。
冷至接近室温后,将试样编号,取样温度记录于表中,检查试样有无开裂、粘砂等缺陷。
然后放入105~110℃烘箱中烘至恒重。
取出试样放入干燥器内,冷却至室温。
将试样分成两批,900℃以下为第一批,测定其饱吸煤油后在煤油后在空气中重,900℃以上的试样为第二批,测定其饱吸水后在水中重及饱吸水后在空气重。
按公式算出各温度点的结果后,以温度为横坐标,气孔率和收缩率为纵坐标,画出收缩率和气孔率曲线,并从曲线上确定烧结温度和烧结温度范围。
烧结的意义烧结时的温度称为烧结温度,烧结温度和开始过烧温度之间的温度范围称为烧结温度范围,在烧结过程中若不确定烧结温度和烧结温度范围继续升温,则坯体开始变形、软化、过烧膨胀,造成烧结事故。
烧结生产工艺流程知识讲解
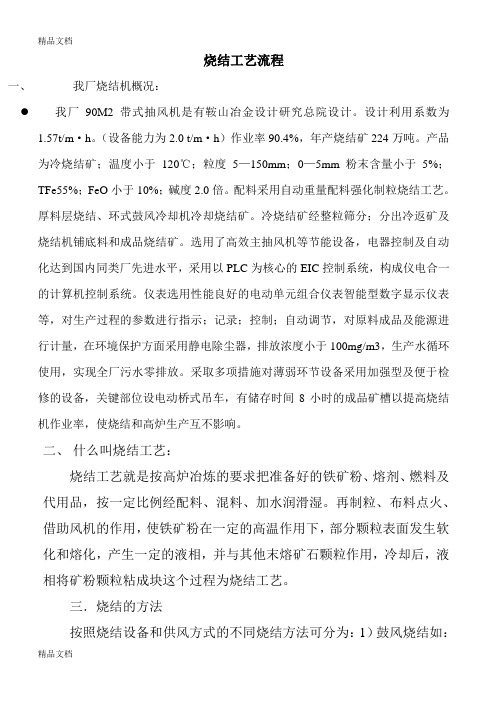
烧结工艺流程一、我厂烧结机概况:我厂90M2带式抽风机是有鞍山冶金设计研究总院设计。
设计利用系数为1.57t/m·h。
(设备能力为2.0 t/m·h)作业率90.4%,年产烧结矿224万吨。
产品为冷烧结矿;温度小于120℃;粒度5—150mm;0—5mm粉末含量小于5%;TFe55%;FeO小于10%;碱度2.0倍。
配料采用自动重量配料强化制粒烧结工艺。
厚料层烧结、环式鼓风冷却机冷却烧结矿。
冷烧结矿经整粒筛分;分出冷返矿及烧结机铺底料和成品烧结矿。
选用了高效主抽风机等节能设备,电器控制及自动化达到国内同类厂先进水平,采用以PLC为核心的EIC控制系统,构成仪电合一的计算机控制系统。
仪表选用性能良好的电动单元组合仪表智能型数字显示仪表等,对生产过程的参数进行指示;记录;控制;自动调节,对原料成品及能源进行计量,在环境保护方面采用静电除尘器,排放浓度小于100mg/m3,生产水循环使用,实现全厂污水零排放。
采取多项措施对薄弱环节设备采用加强型及便于检修的设备,关键部位设电动桥式吊车,有储存时间8小时的成品矿槽以提高烧结机作业率,使烧结和高炉生产互不影响。
二、什么叫烧结工艺:烧结工艺就是按高炉冶炼的要求把准备好的铁矿粉、熔剂、燃料及代用品,按一定比例经配料、混料、加水润滑湿。
再制粒、布料点火、借助风机的作用,使铁矿粉在一定的高温作用下,部分颗粒表面发生软化和熔化,产生一定的液相,并与其他末熔矿石颗粒作用,冷却后,液相将矿粉颗粒粘成块这个过程为烧结工艺。
三.烧结的方法按照烧结设备和供风方式的不同烧结方法可分为:1)鼓风烧结如:烧结锅、平地吹;2)抽风烧结:①连续式如带式烧结机和环式烧结机等;②间歇式如固定式烧结机有盘式烧结机和箱式烧结机,移动式烧结机有步进式烧结机;3)在烟气中烧结如回转窑烧结和悬浮烧结。
四.烧结矿的种类:CaO/SiO2小于1为非自熔性烧结矿;碱度为1-1.5是自熔性烧结.矿碱度为1.5~2.5是高碱度烧结矿;大于2.5是超高或熔剂性烧结矿。
[烧结工艺]烧结基础知识
![[烧结工艺]烧结基础知识](https://img.taocdn.com/s3/m/12d5a7ca0508763231121263.png)
[烧结工艺]烧结基础知识1、烧结的含义将含铁粉状料或细粒料进行高温加热,在不完全熔化的条件下烧结成块的过程。
铁矿粉烧结是一种人造富矿的过程。
2、烧结的方法(1)鼓风烧结:烧结锅,平地吹;(2)抽风烧结:a:连续式:带式烧结机和环式烧结机等;b:间歇式:固定式烧结机,如盘式烧结机和箱式烧结机;移动式烧结机,如步进式烧结机;(3)在烟气中烧结:回转窑烧结和悬浮烧结。
3、烧结生产的工艺流程一般包括:原燃料的接受、贮存,溶剂、燃料的准备,配料,混合,制粒,布料,点火烧结,热矿破碎,热矿筛分,热矿冷却,冷矿筛分,铺底料、成品烧结矿及返矿的贮存、运输等工艺环节。
机上冷却工艺不包括热矿破碎和热矿筛分。
现代烧结工艺流程不再使用热矿工艺,应使用冷矿工艺。
在冷矿工艺中,宜推广具有铺底料系统的流程。
4、烧结厂主要技术经济指标烧结厂的主要技术经济指标包括利用系数、作业率、质量合格率、原材料消耗定额等。
1>、利用系数每台烧结机每平方米有效抽风面积(m2)每小时(h)的生产量(t)称烧结机利用系数,单位为t/(m2*h)。
它用台时产量与烧结机有效抽风面积的比值表示:利用系数=台时产量(t/h)/有效抽风面积(m2)=总产量(t)/[总生产台时(t)×总有效面积(m2)]台时产量是一台烧结机一小时的生产量,通常以总产量与运转的总台时之比值表示。
这个指标体现烧结机生产能力的大小,它与烧结机有效面积的大小无关。
利用系数是衡量烧结机生产效率的指标,它与烧结机有效面积的大小无关。
2>、烧结机作业率作业率是设备工作状况的一种表示方法,以运转时间占设备日历时间的百分数表示:设备作业率=运转台时/日历台时×100%日历台时是个常数,每台烧结机一天的日历台时即为24台时。
它与台数、时间有关。
日历台时=台数×24×天数事故率是指内部事故时间与运转时间的比值,以百分数表示:事故率=事故台时/运转台时×100%设备完好率是衡量设备良好状况的指标。
烧结工艺理论知识(全面)
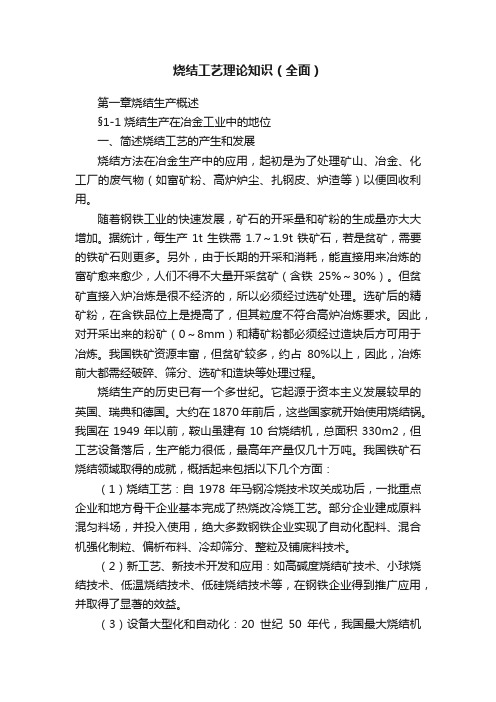
烧结工艺理论知识(全面)第一章烧结生产概述§1-1 烧结生产在冶金工业中的地位一、简述烧结工艺的产生和发展烧结方法在冶金生产中的应用,起初是为了处理矿山、冶金、化工厂的废气物(如富矿粉、高炉炉尘、扎钢皮、炉渣等)以便回收利用。
随着钢铁工业的快速发展,矿石的开采量和矿粉的生成量亦大大增加。
据统计,每生产1t生铁需1.7~1.9t铁矿石,若是贫矿,需要的铁矿石则更多。
另外,由于长期的开采和消耗,能直接用来冶炼的富矿愈来愈少,人们不得不大量开采贫矿(含铁25%~30%)。
但贫矿直接入炉冶炼是很不经济的,所以必须经过选矿处理。
选矿后的精矿粉,在含铁品位上是提高了,但其粒度不符合高炉冶炼要求。
因此,对开采出来的粉矿(0~8mm)和精矿粉都必须经过造块后方可用于冶炼。
我国铁矿资源丰富,但贫矿较多,约占80%以上,因此,冶炼前大都需经破碎、筛分、选矿和造块等处理过程。
烧结生产的历史已有一个多世纪。
它起源于资本主义发展较早的英国、瑞典和德国。
大约在1870年前后,这些国家就开始使用烧结锅。
我国在1949年以前,鞍山虽建有10台烧结机,总面积330m2,但工艺设备落后,生产能力很低,最高年产量仅几十万吨。
我国铁矿石烧结领域取得的成就,概括起来包括以下几个方面:(1)烧结工艺:自1978年马钢冷烧技术攻关成功后,一批重点企业和地方骨干企业基本完成了热烧改冷烧工艺。
部分企业建成原料混匀料场,并投入使用,绝大多数钢铁企业实现了自动化配料、混合机强化制粒、偏析布料、冷却筛分、整粒及铺底料技术。
(2)新工艺、新技术开发和应用:如高碱度烧结矿技术、小球烧结技术、低温烧结技术、低硅烧结技术等,在钢铁企业得到推广应用,并取得了显著的效益。
(3)设备大型化和自动化:20世纪50年代,我国最大烧结机75m2,60年代130 m2,80年代265m2,90年代宝钢二、三期和武钢等450m2烧结机相继投产,这些都是我国自行设计、自行制造,并实现自动化生产的。
烧结工艺知识点总结大全

烧结工艺知识点总结大全一、烧结原理1. 烧结是指将粉末材料在一定温度下加热,使其颗粒间发生结合,形成致密的块状产品。
烧结的基本原理是固相扩散,即热力学上的固相之间的扩散过程。
2. 烧结过程中主要有三种力学过程,分别为颗粒间的原子扩散、颗粒间的表面扩散和颗粒间的体扩散。
这三种扩散方式相互作用,共同促进颗粒间发生结合。
3. 烧结过程中温度、时间和压力是影响烧结效果的重要因素。
通过控制这些参数,可以使烧结过程更加均匀和有效。
二、烧结设备1. 烧结设备主要包括热处理炉、烧结炉、烧结机等。
不同的烧结设备适用于不同的烧结材料和工艺要求。
2. 烧结设备的主要部件包括燃烧室、加热炉、炉膛、热风循环系统、控制系统等。
这些部件共同作用,实现对粉末材料的加热和烧结作用。
3. 热处理炉是常见的烧结设备之一,主要通过电阻加热、气体燃烧等方式对粉末材料进行加热处理,适用于各种金属和非金属材料的烧结工艺。
三、烧结工艺控制1. 烧结工艺控制是烧结过程中的关键环节,可以通过控制温度、时间、压力等参数,实现对烧结过程的精确控制。
2. 烧结工艺控制的主要方法包括PID控制、自适应控制、模糊控制等。
这些控制方法通过对烧结过程中的各个参数进行实时监测和调整,以实现对烧结过程的精确控制。
3. 在实际生产中,烧结工艺控制可以通过计算机控制系统实现自动化,提高生产效率和产品质量。
四、烧结材料选型1. 烧结工艺适用于各种粉末材料,包括金属粉末、陶瓷粉末、粉末冶金材料等。
根据不同的材料性质和要求,选择合适的烧结工艺和设备。
2. 烧结材料的选型考虑因素包括原料种类、粒度、成分、形状等。
根据不同的要求,选择合适的烧结材料,可以有效提高产品质量和生产效率。
3. 在烧结材料选型过程中,也需要考虑成本、资源利用率和环境保护等方面的因素,以实现经济、环保和可持续发展。
五、烧结工艺的应用1. 烧结工艺广泛应用于金属、陶瓷、粉末冶金、电子材料等行业。
在金属制品生产中,烧结工艺可以用于制造各种粉末冶金制品、焊接材料、钎焊材料等。
烧结原理、工艺培训
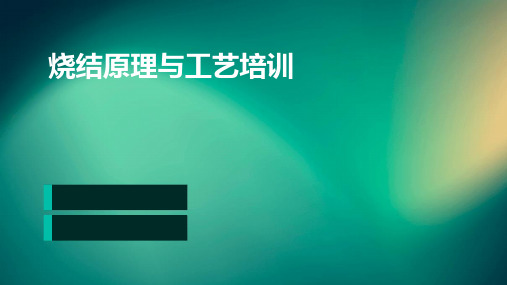
常见问题及解决方案
烧结温度过高或过低
产品性能不达标
调整烧结温度,优化加热速率和保温时间 。
优化原料配比,调整工艺参数,使用合适 的添加剂。
烧结过程中出现裂纹、变形等问题
环境污染与能耗问题
改进原料制备工艺,提高原料均匀性;优 化烧结工艺,降低烧结应力。
采用环保型烧结工艺,降低能耗,减少废气 、废水、废渣排放。
压力制度调整技巧
合理选择压力
根据产品的要求和原料的特性,选择 合适的压力制度,以保证产品的致密 度和强度。
分段加压
控制加压速度
加压速度过快可能导致产品开裂或变 形,因此应控制加压速度,确保产品 的稳定性。
在烧结过程中,可以采用分段加压的 方式,以适应不同烧结阶段的要求。
气氛控制策略
选择适当气氛
01
减少不合格品率
通过加强质量管理和员工培训,降低不合格 品率,提高生产效益。
提升客户满意度
关注客户需求和反馈,持续改进产品质量和 服务水平,提升客户满意度。
06 安全生产管理与环境保护 要求
安全生产管理体系建立
确定安全生产方针和目标
明确企业安全生产的方向和要达到 的预期结果。
建立安全生产责任制
明确各级人员、各部门在安全生产 中的职责和权限。
05 产品质量检测与评价标准
产品性能指标介绍
物理性能
包括产品的尺寸、形状、重量、密度、 孔隙率等。
化学性能
涉及产品的化学成分、矿物组成、氧 化物含量等。
力学性能
如产品的抗压强度、抗折强度、耐磨 性等。
热学性能
包括产品的热导率、热膨胀系数等。
质量检测方法
抽样检测
烧结工理论知识复习资料及参考答案

烧结工理论知识复习资料及参考答案一、判断题1.>成品筛二次筛分的筛孔为10mm。
( )答案:³2.>矿石品位指矿石中具有金属组份的含量百分数。
( )答案:√3.>烧结厂主要的耗电设备是烧结机。
( )答案:³4.>风机叶轮使用寿命与通过废气含尘量有直接关系。
( )答案:√5.>大烟道废气气流越高,降尘效率越好。
( )答案:³6.>烧结"终点"提前,总管负压升高。
( )答案:³7.>提高台车料厚,可以降低料层负压。
( )答案:³8.>磁铁矿主要是Fe2O3。
( )答案:³9.>烧结生产主要是还原气氛。
( )答案:³10.>烧结三碳指返中残碳、结矿中残碳及混合料含碳。
( )答案:√11.>物料残废存量即物料经过烧结排出水份和烧损为残存物量。
( )答案:√12.>精矿粒度要求控制8mm以下有利于烧结。
( )答案:√13.>返矿温度多少对混合料水分有较大影响。
( )14.>电除尘灰配比用不用细水长流,对主机参数无影响。
( )答案:³15.>点火器烘炉原则是快速将耐火材料中水份烘干。
( )答案:³16.>停机8小时以上,点火器不用灭火。
( )答案:³17.>点火燃料用量与机速无关。
( )答案:³18.>梭车布料均匀,关键是在两端换向时停留时间长,造成布料堆尘。
( )答案:√19.>烧结带温度越高,反应越复杂。
( )答案:³20.>燃料粒度对烧结无影响。
( )答案:³21.>烧结矿中MgO含量对改善高炉炉渣流动有影响。
( )答案:√22.>烧结对熔剂要求,SiO2+Al2O3越高越好。
( )答案:³23.>烧结矿中有害元素S、P,不影响炼铁。
烧结工艺介绍

烧结工艺的简单介绍目前,随着市场竞争的加剧,钢铁工业设备向大型化发展,对原料的要求日益提高,而高炉炼铁生产技术指标的提高,主要依靠入炉原料性质的改善,烧结矿是我国高炉的主要入炉料,因此,保证和提高烧结矿的质量,是保证钢铁工业稳定发展的重要手段。
一、烧结的概念烧结是钢铁生产工艺中的一个重要环节,它是将各种粉状含铁原料,配入适量的燃料和熔剂,加入适量的水,经混合和造球后在烧结设备上使物料发生一系列物理化学变化,将矿粉颗粒黏结成块的过程。
二、烧结矿的来源以及意义铁矿粉造块目前主要有两种方法:烧结法和球团法。
两种方法所获得的块矿分别为烧结矿和球团矿。
球团法通常在选贫矿的地区采用,尤其是北美地区。
而在有天然富矿可以开采使用的地方,烧结法则是一种成本较低的方法,在世界的其它地区被广泛采用。
虽然新的炼铁方法会不断出现,但是烧结矿的需求在很长一段时间内仍将保持在较高的水平。
在我国,高炉入炉的炉料90%以上都是靠烧结法提供的。
因此,铁矿石烧结对我国的钢铁工业有重大的意义。
三、烧结工艺流程介绍经烧结而成的有足够强度和粒度的烧结矿可作为炼铁的熟料。
利用烧结熟料炼铁对于提高高炉利用系数、降低焦比、提高高炉透气性保证高炉运行均有一定意义。
烧结生产的工艺流程如下图所示。
主要包括烧结料的准备,配料与混合,烧结和产品处理等工序。
目前生产上广泛采用带式抽风烧结工艺流程:1、烧结的原材料准备:含铁原料:含铁量较高、粒度<5mm的矿粉,铁精矿,高炉炉尘,轧钢皮,钢渣等。
一般要求含铁原料品位高,成分稳定,杂质少。
熔剂:要求熔剂中有效CaO含量高,杂质少,成分稳定,含水3%左右,粒度小于3mm的占90%以上。
在烧结料中加入一定量的白云石,使烧结矿含有适当的MgO,对烧结过程有良好的作用,可以提高烧结矿的质量。
燃料:主要为焦粉和无烟煤。
对燃料的要求是固定碳含量高,灰分低,挥发分低,含硫低,成分稳定,含水小于10%,粒度小于3mm的占95%以上。
烧结理论及工艺要求

烧结理论及工艺要求
一、烧结理论
烧结,它是一种特殊的金属加工方法,是将金属粉末或粒子因加热及
压实而聚结成固态或凝固态的工艺。
烧结过程一般分为三个阶段,疏松期、烧结期和结晶期。
烧结期包括加热期、热压期和持热期。
1、疏松期:粉末在温度小于熔点时,它的聚结能力较低,它的表面
比较滑,一般称为粉末状态,它既可以形成颗粒和宏观结构。
2、烧结期:当温度上升到金属熔点以上时,粉末微粒之间的聚结能
力增强,它的表面光滑,此时粉末形成了小的颗粒,并可以粘合在一起,
形成较大的烧结体。
3、结晶期:当温度上升到金属晶体化温度时,粉末发生晶体结构,
进一步烧结,形成金属晶体。
二、烧结工艺要求
1、烧结温度:烧结温度是控制烧结成果的重要参数,一般来说,烧
结温度应高于金属的熔点,低于其晶体化温度。
2、压力:压力也是影响烧结成果的重要参数。
如果压力太低,烧结
质量就会受到影响,这时就需要使用较高的压力,以保证烧结质量。
3、时间:在烧结过程中,烧结时间也是一个重要的参数,如果烧结
时间不足,就可能导致金属的结晶不匀,从而影响烧结的成果。
无机材料科学基础《烧结》知识点

(1)常压烧结:又称无压烧结。
属于在大气压条件下坯体自由烧结的过程。
在无外加动力下材料开始烧结,温度一般达到材料的熔点0.5-0.8即可。
在此温度下固相烧结能引起足够原子扩散,液相烧结可促使液相形成或由化学反应产生液相促进扩散和粘滞流动的发生。
常压烧结中准确制定烧成曲线至关重要。
合适的升温制度方能保证制品减少开裂与结构缺陷现象,提高成品率。
(2)热压烧结与热等静压烧结:热压烧结指在烧成过程中施加一定的压力(在10~40MPa),促使材料加速流动、重排与致密化。
采用热压烧结方法一般比常压烧结温度低100ºC左右,主要根据不同制品及有无液相生成而异。
热压烧结采用预成型或将粉料直接装在模内,工艺方法较简单。
该烧结法制品密度高,理论密度可达99%,制品性能优良。
不过此烧结法不易生产形状复杂制品,烧结生产规模较小,成本高。
作为陶瓷烧结手段,利用来自于表面能的表面应力而达到致密化的常压烧结法虽是一般常用的方法,但是,不依赖于表面应力,而在高温下借助于外压的方法,也是可以采用的。
这就是称为热压法的烧结方法。
广义来说,在加压下进行烧结的方法包括所有这类方法,超高压烧结和热等静压(HIP)烧结也属于这类方法。
不过,一般都作为在高温下施加单轴压力进行烧结的方法来理解。
其基本结构示于图1。
首先,制备粉体试料,置于模型中,在规定温度下加热、加压,获得烧结体。
由于下述原因而采用这种方法:(1)烧结温度降低;(2)烧结速度提高;(3)使难烧结物质达到致密化。
因为能够在颗粒成长或重新结晶不大可能进行的温度范围达到致密化,所以,可获得由微小晶粒构成的高强度、高密度烧结体。
图2所示,是热压对陶瓷致密化影响效果之一例。
将热压作为制造制品的手段而加以利用的实例有:氧化铝、铁氧体、碳化硼、氮化硼等工程陶瓷。
连续热压烧结生产效率高,但设备与模具费用较高,又不利于过高过厚制品的烧制。
热等静压烧结可克服上述弊缺,适合形状复杂制品生产。
(完整word版)烧结生产工艺完全版本
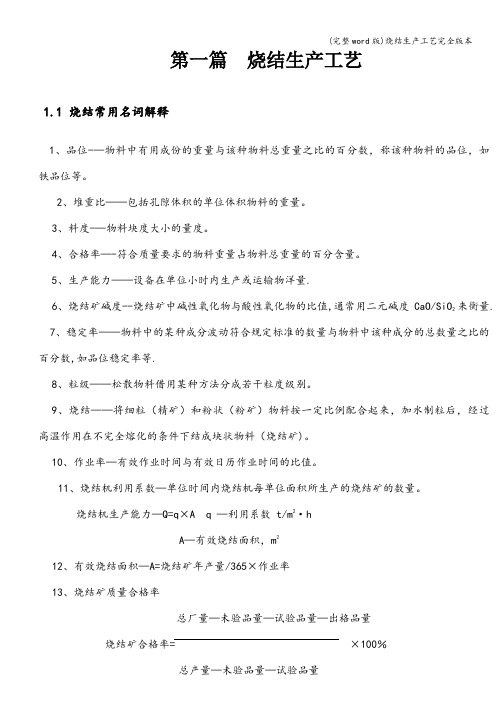
第一篇烧结生产工艺1.1 烧结常用名词解释1、品位-—物料中有用成份的重量与该种物料总重量之比的百分数,称该种物料的品位,如铁品位等。
2、堆重比——包括孔隙体积的单位体积物料的重量。
3、料度-—物料块度大小的量度。
4、合格率—-符合质量要求的物料重量占物料总重量的百分含量。
5、生产能力——设备在单位小时内生产或运输物洋量.来衡量.6、烧结矿碱度--烧结矿中碱性氧化物与酸性氧化物的比值,通常用二元碱度CaO/SiO27、稳定率——物料中的某种成分波动符合规定标准的数量与物料中该种成分的总数量之比的百分数,如品位稳定率等.8、粒级——松散物料借用某种方法分成若干粒度级别。
9、烧结——将细粒(精矿)和粉状(粉矿)物料按一定比例配合起来,加水制粒后,经过高温作用在不完全熔化的条件下结成块状物料(烧结矿)。
10、作业率—有效作业时间与有效日历作业时间的比值。
11、烧结机利用系数—单位时间内烧结机每单位面积所生产的烧结矿的数量。
烧结机生产能力—Q=q×A q —利用系数 t/m2·hA—有效烧结面积,m212、有效烧结面积—A=烧结矿年产量/365×作业率13、烧结矿质量合格率总厂量—未验品量—试验品量—出格品量烧结矿合格率= ×100%总产量—未验品量—试验品量1.2 生产工艺流程根据原料特性,选择相应的烧结方法、加工程序及工艺流程,以获得预期的产品,这一过程谓之烧结生产工艺选择过程。
选择生产工艺必须保证其技术上先进可靠、经济上合理,以获得先进的技术经济指标为目的。
在生产实践中,烧结生产工艺随原料条件,对产品质量要求和生产规模不同,其工艺流程也有差异。
图1—1所示为现行常用的烧结生产工艺流程。
烧结生产工艺流程通常由下列几部分组成:含铁原料、燃料和溶剂的接受和贮存;原料、燃料和溶剂的破碎筛分;烧结料的配制、混合制粒、布料、点火与烧结;烧结矿的破碎和筛分、冷却、整粒和铺底料。
烧结知识
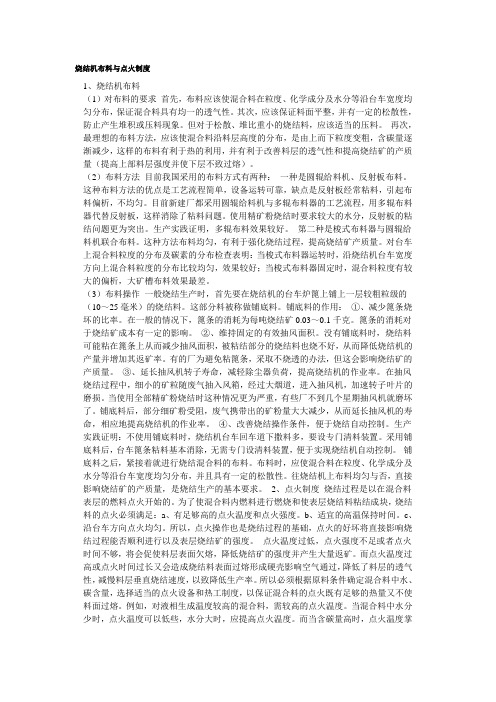
烧结机布料与点火制度烧结sintering ;firing1、在高温下,陶瓷生坯固体颗粒的相互键联,晶粒长大,空隙(气孔)和晶界渐趋减少,通过物质的传递,其总体积收缩,密度增加,最后成为具有某种显微结构的致密多晶烧结体,这种现象称为烧结。
2、制取无机固体材料的一种过程。
在利用固相反应制备无机固体化合物时,反应的速率由扩散过程控制,常常需要较高的温度才能使反应有效地进行。
另外一些固体化合物是固液相组成的化合物,在熔化时会发生分解反应,故烧结一般应在产物熔点以下进行,以保证得到均匀的物相。
但是烧结温度也不能太低,否则会使固相反应的速率太低。
在很多情况下,烧结需要在特定的气氛或真空中进行。
控制烧结过程的气相分压非常重要,特别是当研究的体系中含有价态可变的离子时,固相反应的气相分压将直接影响到产物的组成和结构。
例如,在铜系氧化物高温超导体的合成中,烧结过程必须在严格控制氧分压,以保证得到具有确定结构、组成和铜价态分布的超导材料。
3、是聚四氟乙烯(PTFE)加工过程中的一个重要步骤。
聚四氟乙烯预成型品必须通过烧结才能成为有用的制品。
烧结是将预成型品加热至熔点(327℃)以上,并在此温度下保持一定时间,使聚合物分子由结晶形逐渐转变为无定型,使分散的树脂颗粒通过相互熔融扩散黏结成一个连续的整体。
烧结全的预成型品由透明胶状体冷却成坚固的乳白色的不透明制品。
小球烧结简述小球团烧结技术烧结工艺技术进展烧结原料的准备及加工处理烧结球团的配料知识烧结球团的配料知识球团烧结工艺及设备核心技术高炉炼铁请问,有高人知道这方面的信息吗?高炉炉渣如何与转炉炉渣混合,再利用?谢谢! 冶金工程炼铁工艺知识360㎡烧结机工程的设计特点及生产实践烧结过程软测量建模综述关于铁水预处理新技术的研究铁水喷镁粒脱硫的特点KR法与喷吹法在铁水预脱硫中应用的比较。
烧结工艺精讲
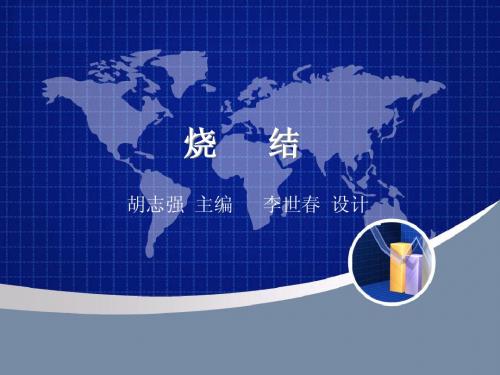
晶粒生长的影响因素
• 1.夹杂物如杂质、气孔等阻碍作用 • 晶界在移动时可能会遇到夹杂物,晶界为了通过夹杂物, 界面能就被降低,降低的量正比于夹杂物的横截面积。通 过障碍以后,弥补界面又要付出能量,结果使界面继续前 进能力减弱,界面变得平直,晶粒生长逐渐停止。 • 2.晶界上液相的影响 • 少量液相使晶界上形成两个新的固-液界面,从而界面移 动的推动力降低,扩散距离增加,因此少量液相可以起到 抑制晶粒长大的作用。但当坯体中有大量液相时,可以促 进晶粒的生长和出现二次再结晶。 • 3.晶粒生长极限尺寸 • 烧结达到气孔的体积分数为10%时,晶粒长大就停止了, 这也是普通烧结中坯体终点密度低于理论密度的原因。
影响烧结的因素
1.原始粉料的粒度 1.原始粉料的粒度 • 从烧结速率考虑:无论在固态或液态的烧结中,细颗粒由 于曲率半径小,从而增加的烧结的推动力—表面能之差, 缩短了原子扩散距离,提高了颗粒在液相中溶解度而导致 烧结过程的加速。 • 从防止二次再结晶考虑:起始颗粒粒径必须细而均匀,如 果细颗粒中有少量大颗粒存在,则易发生晶粒异常生长而 不利用烧结。 • 如果烧结速率与起始粒度的1/3次方成正比,从理论上计 算,当起始粒度从2μm减小到0.5μm,烧结速率将增加64 倍,这相当于粒度小的粉料烧结温度降低了150—300℃。 • 一般氧化物材料最适宜的粉末粒度为0.05—0.5μm。
严格控制温度即保温的重要性
• 当烧结达到晶界移动速率Vb=Vp时,烧结过程已接近完成。 严格控制温度是十分重要的,继续维持Vb=Vp,气孔易迅 速排除而实现致密化。此时烧结体应适当保温,如果再继 续升高温度,由于晶界的速率随温度呈指数增加,必然导 致Vb>>Vp,晶界越过气孔而向曲率中心移动,使气孔包入 晶粒内部,气孔一旦包入晶粒内部,只能通过体积扩散来 排除,而这是十分困难的。 • 随着烧结的进行,气孔逐渐缩小,而气孔内的气压不断增 大,当增加至2γ/r时,即气孔内气压等于烧结推动力, 烧结停止。如果继续升高温度,气孔内的气压继续增大, 这时气孔不仅不能缩小反而膨胀,对致密化不利。 • 烧结如果不采取特殊措施是不可能达到坯体完全致密化的, 如果要获得接近理论密度的制品,必须采用气氛或真空烧 结和热压烧结等方法。
烧结过程的理论基础

烧结过程的理论基础烧结是一种通过高温和压力将细粉状材料压制成成型体的加工方法。
在烧结过程中,粉末颗粒之间发生了部分熔融、扩散、结合和收缩现象,最终形成了密实的、具有一定机械强度和结构稳定性的成型体。
烧结过程的理论基础主要涉及燃烧理论、传热理论、材料科学等方面的知识。
1.燃烧理论烧结过程中常用的燃烧方式包括气相燃烧、固相燃烧和液相燃烧。
在燃烧过程中,燃料与氧化剂反应产生高温高能的燃烧产物,为烧结提供了必要的热能。
燃烧产物的温度越高,烧结过程中的热传递效果越好,有利于颗粒间的结合和收缩。
2.传热理论热传递是烧结过程中的一个重要环节。
热传递可以通过传导、对流和辐射等方式进行。
传导是指热量通过颗粒之间或颗粒内部的分子振动和传递,对于高温下的烧结过程尤为重要。
对流是指在气体或液体中,通过流体的对流传导热量,对于烧结中的气体流动和温度分布具有重要影响。
辐射是指物体表面的热能以电磁波的形式辐射出去,对于高温烧结具有显著效果。
3.材料科学烧结过程中,粉末颗粒之间的结合主要是通过扩散和熔融发生的。
扩散是指原子或分子在固体中由高浓度区向低浓度区传递的过程,是粉末颗粒烧结过程中结合的主要方式。
熔融是指粉末颗粒在高温下部分熔化,形成液相,通过液相的黏结作用形成连续的成型体。
材料科学中的物理化学性质、晶体学、材料力学等知识对于理解和控制烧结过程中的结合机制和力学性能具有重要意义。
总之,烧结过程的理论基础涉及燃烧理论、传热理论和材料科学等多个方面的知识。
这些理论和原理的深入研究和应用,可以帮助理解烧结过程中颗粒的结合机制、热传递现象以及成型体的力学性能,为烧结工艺和材料应用提供理论指导。
烧结生产知识

烧结生产知识一、铁矿石烧结知识(原料条件)1、天然矿粉与烧结1)天然矿粉包括富矿粉和贫矿粉,其中天然矿粉含铁量在45%以上的通常称为富矿粉,含铁量低于45%的通常称为贫矿粉。
45%这个界限随着冶炼技术的发展是会变化的。
2)铁矿粉烧结是重要的造块技术之一。
由于开采时产生大量的铁矿粉,特别是贫铁矿富选促进了铁精矿粉的生产发展,使铁矿粉烧结成为规模最大的造块作业。
烧结矿比天然矿石有许多优点,如含铁量高、气孔率大、易还原、有害杂质少、含碱性熔剂等。
2、铁矿石分类:按照铁矿物不同的存在形态,分为磁铁矿、赤铁矿、褐铁矿、菱铁矿四大类。
1)磁铁矿:磁铁矿化学式为Fe3O4,也可以视为Fe2O3与FeO的固溶体。
比密度为4.9--5.2t/m3,硬度为5.5--6.5,难还原和破碎,有金属光泽,具有磁性。
其理论含铁量为72.4%。
磁铁矿晶体为八面体,组织结构较致密坚硬,一般成块状和粒状,表面颜色由钢灰色到黑色,条痕均是黑色,俗称青矿。
2)赤铁矿:赤铁矿俗称“红矿”,化学式为Fe2O3,其矿物成份是不含结晶水的三氧化二铁,密度为4.8—5.3,硬度不一,结晶完整的赤铁矿硬度为5.5—6.0,理论含铁量70%。
赤铁矿由非常致密的结晶组织到很分散的粒状,结晶的赤铁矿外表颜色为钢灰色和铁黑色,其它为暗红色,但条痕均为暗红色。
3)褐铁矿:褐铁矿石(mFe2O3. nH2O)是一种含结晶水的Fe2O3,按结晶水含量不同,褐铁矿分为五种,其中以2Fe2O3. 3H2O形式存在的较多。
4)菱铁矿:菱铁矿石的化学式为FeCO3,理论含铁量为48.2%。
自然界中常见的是坚硬致密的菱铁矿,外表颜色为灰色和黄褐色,风化后变为深褐色,条痕为灰色或带黄色,由玻璃光泽。
菱铁矿的比重为3.8吨/米3,无磁性。
3、铁矿粉分类:1)精矿粉:也称选粉。
是天然矿石经过破碎、磨碎、选矿等加工处理,除去一部分脉石和杂质,使含铁量提高后的极细的矿粉叫精矿粉。
烧结理论知识培训课件

烧结理论知识培训课件烧结是一种重要的金属加工工艺,它指的是将细小的金属粉末通过高温压制和烧结过程将其转化为具有一定强度和形状的金属零件。
烧结技术在航空航天、汽车、电子、化工等领域有着重要的应用。
因此,为了满足市场需求和提高企业竞争力,我们需要深入了解烧结理论知识。
一、烧结的基本原理与步骤烧结的基本原理是通过高温和压力将细小的金属粉末烧结成一定形状和尺寸的金属零件。
其步骤包括:1.混合:将不同材料的金属粉末按照一定比例混合均匀。
2.成型:将混合均匀的金属粉末按照设计要求进行成型,如挤压成型、注射成型等。
3.烧结:将成型后的金属粉末在高温环境下进行烧结处理,使其成为整体零件。
4.加工:根据实际需要,对烧结成的零件进行加工或者表面处理,如车削、磨削、喷涂等。
二、烧结的特点1.能够制造高强度和高精度的金属零件。
2.可制造各种不规则和复杂的形状。
3.烧结生产工艺简单、流程短,可以提高生产效率和节约生产成本。
4.可以使用多种不同材料的金属粉末进行混合烧结,获得具有良好性能的合金材料。
5.在烧结过程中,可以控制粉末的成分和密度,获得不同的结构和性能。
三、烧结的应用及前景1.航空航天领域:烧结技术被广泛应用于航空航天领域,用于制造发动机部件、轮毂轴承、航天器外壳及燃料结构等。
2.汽车领域:烧结技术可以用于制造汽车零件,如制动器、发动机缸体等。
3.电子领域:烧结技术可以制造具有特殊性能的电子元器件,如热敏电阻、电阻器等。
4.医疗领域:烧结技术可以用于制造人体骨骼植入物、假牙、人工关节等医疗器械。
由此可见,烧结技术在未来的制造业中具有重要的应用前景和市场需求。
- 1、下载文档前请自行甄别文档内容的完整性,平台不提供额外的编辑、内容补充、找答案等附加服务。
- 2、"仅部分预览"的文档,不可在线预览部分如存在完整性等问题,可反馈申请退款(可完整预览的文档不适用该条件!)。
- 3、如文档侵犯您的权益,请联系客服反馈,我们会尽快为您处理(人工客服工作时间:9:00-18:30)。
烧结工艺理论知识(全面)第一章烧结生产概述§1-1 烧结生产在冶金工业中的地位一、简述烧结工艺的产生和发展烧结方法在冶金生产中的应用,起初是为了处理矿山、冶金、化工厂的废气物(如富矿粉、高炉炉尘、扎钢皮、炉渣等)以便回收利用。
随着钢铁工业的快速发展,矿石的开采量和矿粉的生成量亦大大增加。
据统计,每生产1t生铁需1.7~1.9t铁矿石,若是贫矿,需要的铁矿石则更多。
另外,由于长期的开采和消耗,能直接用来冶炼的富矿愈来愈少,人们不得不大量开采贫矿(含铁25%~30%)。
但贫矿直接入炉冶炼是很不经济的,所以必须经过选矿处理。
选矿后的精矿粉,在含铁品位上是提高了,但其粒度不符合高炉冶炼要求。
因此,对开采出来的粉矿(0~8mm)和精矿粉都必须经过造块后方可用于冶炼。
我国铁矿资源丰富,但贫矿较多,约占80%以上,因此,冶炼前大都需经破碎、筛分、选矿和造块等处理过程。
烧结生产的历史已有一个多世纪。
它起源于资本主义发展较早的英国、瑞典和德国。
大约在1870年前后,这些国家就开始使用烧结锅。
我国在1949年以前,鞍山虽建有10台烧结机,总面积330m2,但工艺设备落后,生产能力很低,最高年产量仅几十万吨。
我国铁矿石烧结领域取得的成就,概括起来包括以下几个方面:(1)烧结工艺:自1978年马钢冷烧技术攻关成功后,一批重点企业和地方骨干企业基本完成了热烧改冷烧工艺。
部分企业建成原料混匀料场,并投入使用,绝大多数钢铁企业实现了自动化配料、混合机强化制粒、偏析布料、冷却筛分、整粒及铺底料技术。
(2)新工艺、新技术开发和应用:如高碱度烧结矿技术、小球烧结技术、低温烧结技术、低硅烧结技术等,在钢铁企业得到推广应用,并取得了显著的效益。
(3)设备大型化和自动化:20世纪50年代,我国最大烧结机75m2,60年代130 m2,80年代265m,90年代宝钢二、三期和武钢等450m烧结机相继投产,这些都是我国自行设计、自行制造,并实现自动化生产的。
(4)烧结生产指标及产品质量:近年来我国烧结矿质量显著提高,目前多数企业烧结矿含铁品位达到55%以上,有的达到58%;SiO2含量降到5%,有的还低于5%,实现了低硅烧结。
烧结矿FeO在8%~10%之间,转鼓指数明显提高,还原性提高。
此外,烧结矿固体燃料消耗也有较大幅度的降低。
(5)炉料结构趋于合理:20世纪70年代前我国绝大部分企业高炉炉料结构是以单一自熔性烧结矿为主,近年来我国新建球团矿生产设备逐年增加,酸性球团烧结矿工艺工业生产成功,酸性炉料产量逐年增加(包括进口部分块矿),这样使得酸性料配加高-1-22碱度烧结矿的合理炉料结构比例逐年增加,为高炉增铁节焦创造了条件。
(6)复合矿造块工艺过关:攀钢、包钢、酒钢所用的三种铁矿石,是我国三大特殊类型复合铁矿石,比普通铁矿石的造块难度更大。
多年来,在企业及科研单位、高等院校的共同努力下,分别解决了这三大类型复合矿石的烧结工艺及技术难题。
此外,宝钢等企业采用了近期开发的信息技术,自动化控制水平得到提高。
烧结厂的环境治理及余热回收方面也取得较大的进展。
建国50年来,我国烧结领域取得了可喜的成就,但是我们也要清楚地看到我国烧结矿技术与国外先进国家比较还存在不小的差距,主要是品位低、质量差,不少厂的产品成分波动大、能耗高,环境治理尚有差距,微机控制技术较为落后。
二、铁矿粉烧结的意义和作用铁矿粉烧结是最重要的造块技术之一。
由于开采时产生大量铁矿粉,特别是贫铁矿富选促进了铁精矿粉的生产发展,使铁矿粉烧结成为规模最大的造块作业。
其物料的处理量约占钢铁联合企业的第二位(仅次与炼铁生产),能耗仅次于炼铁及轧钢而居第三位,成为现代钢铁工业中的重要生产工序。
铁矿粉烧结要求烧结矿有很好的物理、冶金性能。
由于现代炼铁设备的大型化,炉料倒运次数多,落差大,要求烧结矿有高的冷强度,如耐压强度等。
烧结矿经历冶炼中的高温过程,要求一定的热强度,即在高温还原气氛下耐压、耐磨及耐急热爆裂性能;烧结矿在高炉内经历物理化学反应,要求它具有良好的冶金性能,如还原性、软化性、熔滴性等。
铁矿粉烧结技术的困难还在于追求合理的经济效果,因此,铁矿粉烧结是一门技术复杂的专门学科。
在长期的生产实践中,人们发现经过选矿、烧结处理后的人造富矿能进一步地使矿物富集和去除有害杂质,因而使高炉生产率提高,焦比下降,其经济效果比天然矿好,见表1-1。
表1-1 烧结矿对炼铁生产的影响原料变化条件磁铁矿加入10%的烧结矿赤铁矿加入10%的烧结矿降低焦比/% 3~6 2~4 提高产量/% 3~6 2~4 原料变化条件烧结矿含铁量增加1% 烧结矿碱度增加0.1 降低焦比/% 2 3.8 提高产量/% 3 3.8“精料”的研究工作也越来越深入,烧结矿朝着品位高、成分稳定、粒度均匀、强度高、冶金性能好的方向发展。
在烧结料中加入一定数量的石灰石或生、消石灰,可生产出具有一定碱度的自熔性烧结矿、高碱度烧结矿。
高炉冶炼这种原料时可不加或少加熔剂,从而进一步降低焦比,提高生产率。
综上所述,烧结具有如下重要意义:(1)为高炉提供化学成分稳定、粒度均匀、还原性好、冶金性能高的优质烧结矿,为高炉优质、高产、低耗、长寿创造了良好的条件;-2-(2)可去除有害杂质,如硫、锌等;(3)可利用工业生产的废弃物,如高炉炉尘、轧钢皮、钢渣等;(4)可回收有色金属如稀有、稀土金属。
三、烧结矿质量对高炉冶炼的影响(1)烧结矿含铁品位下降1%,高炉焦比上升2%,产量下降3%。
(2)烧结矿的FeO变动1%,影响高炉焦比1%~1.5%,影响产量1%~1.5%。
FeO同时影响烧结矿的还原性和软熔性能。
(3)烧结矿的碱度(CaO/SiO2)在1.2以下,每变动0.1,影响高炉焦比和产量3%~3.5%。
(4)烧结矿的强度和高炉冶炼也有一定的影响,强度不够时,容易破碎成粒度小于5mm的粉矿,而粉矿含量变动1%,影响高炉焦比0.5%,影响高炉产量0.5%~1.0%。
(5)烧结矿的饿还原性对焦比和产量的影响:烧结矿在高炉内的直接还原度(rd)增加10%,焦比上升8%~9%,产量下降8%~9%。
烧结矿试样在60min、1000℃条件下的间接还原度每提高5%,高炉煤气中的CO利用率提高0.66%。
(6)烧结矿的低温还原强度(RDI)每提高5%,煤气中CO利用率降低0.5%,产量下降1.5%,焦比上升1.55%。
(7)荷重软化性能对高炉操作的影响:据意大利的皮昂比诺公司4号高炉于1980年的统计,含铁原料的荷重软化温度由1285℃提高到1335℃,高炉的透气性△P由5.2kPa 降低到4.75kPa,产量提高16%。
(8)熔融滴落性能对高炉操作的影响:烧结矿的熔滴性能是冶金性能最重要的性能,大量研究检测表明,含铁炉料熔滴带的阻力损失占整个高炉阻力损失的三分之二以上,熔滴性能直接影响高炉内熔滴带的位置和厚度,影响Si、Mn等元素的直接还原,从而影响生铁的成分和高炉技术经济指标。
§1-2 烧结方法分类及生产工艺流程一、烧结过程及烧结矿的特性将各种粉状含铁原料,配入一定数量的燃料和熔剂,均匀混合制粒,然后放到烧结设备上点火烧结。
在燃料燃烧产生高温度一系列物理化学反应下,混合料中部分易熔物质发生软化熔化,产生一定数量的液相,并润湿其它未熔化的矿石颗粒,当冷却后,液相将矿石颗粒粘结成块,这个过程为烧结,所得矿块叫烧结矿。
烧结矿比天然矿石有许多优点,如含铁量高、气孔率大、易还原、有害杂质少、含碱性熔剂等,且对原料要求不像球团矿那么严格,所以烧结生产发展得十分迅速,在世-3-界上得到了广泛应用。
二、烧结方法分类按照烧结设备和供风方式的不同烧结方法可分为:(1)鼓风烧结:烧结锅,平地吹。
这是小型厂的土法烧结,逐渐被淘汰。
(2)抽风烧结:①连续式:带式烧结机和环式烧结机等;②间歇式:固定式烧结机,如盘式烧结机和箱式烧结机;移动式烧结机,如步进式烧结机。
(3)在烟气中烧结:回转窑烧结和悬浮烧结。
三、烧结生产工艺流程烧结生产的工艺流程,无混合料场时,一般包括:原燃料接受,储存及熔剂、燃料的准备,配料,混合,布料,点火烧结,热矿破碎,热矿筛分及冷却,冷矿筛分及冷矿破碎,铺底料,成品烧结矿的储存及运出,返矿储存等工艺环节。
有混匀料场时,原、燃料的接受、储存放在料场,有时筛分熔剂、燃料的准备也放在料场。
是否设置热矿筛,应根据具体情况或试验结果,经技术经济比较后确定。
机上冷却工艺不包括热矿破碎和热矿筛分。
烧结工艺流程不再使用热矿工艺,应使用冷矿工艺,宜推广具有整粒、铺底料系统的流程。
§1-3 烧结厂主要技术经济指标烧结厂的主要技术经济包括:烧结机利用系数、作业率、质量合格率、原料消耗等。
1、烧结机利用系数:指1台烧结机每平方米有效抽风面积(m2)每小时(h)的生产量(t)。
它用台时产量与烧结机有效抽风面积的比值表示:利用系数[t/(m2h)]=台时产量(t)/有效抽风面积(m2)或利用系数=总产量(t)/[总生产台时(h)总有效面积(m2)]2、台时产量是1台烧结机1h的生产量,通常以总产量与运转的总台时之比值表示。
这个指标体现烧结机生产能力的大小,它与烧结机有效面积的大小有关。
烧结机利用系数是衡量烧结机生产效率的指标,它与烧结机有效面积大小无关。
3、烧结矿出矿率(%)=成品烧结矿量(t)/原料配料总量(干基)(t) 4、作业率是描述设备工作状况的一种表示方法,以运转时间占设备的日历时间的百分数表示:设备作业率(%)=100%×烧结机运转台时/日历台时日历台时是个常数,每台烧结机一天日历台时即为24小时。
它与台数、时间有关。
日历台时=台数×24×天数-4-运转台时是按台计算的设备运转时间。
事故率是指内部事故时间与运转时间的比值:事故率(%)=100%×事故台时/运转台时设备完好率是衡量设备良好状况的指标,指全厂完好设备的台数与设备总台数的比值:设备完好率(%)=100%×完好设备总数/设备总台数扣外作业率(%)=烧结机运转台时/(日历台时-外部影响台时) 5、质量合格率是衡量烧结矿质量好坏的综合指标:质量合格率(%)=100%×[总产量(t)-未验品量(t)-试验品量(t)-合格品量(t)]/[ 总产量(t)-未验品量(t)-试验品量(t)]6、生产成本是指生产1t烧结矿所需的费用,由原料费及加工费两部分组成。
加工费是指生产1t烧结卡所需的加工费用(不包括原料费),包括辅助材料费(如燃料、润滑油、胶带、炉蓖条、水、动力费),工人工资,车间经费(包括设备折旧费、维修费等)。
劳动生产率是指每人每年生产烧结矿的吨数。
这个指标反映了工厂的管理和生产技术水平,它又称全员劳动生产率(全员包括工人和干部)。