磨削技术的发展现状
高速磨削工艺特点及其发展现状

(1)高速主轴 ①高速主轴须有连续自动动平衡系统 属于自动控制技术,利用反馈调节模式,采用测量元件和控制元件进 行动平衡 ②保证主轴在高速状态下有足够的转矩用于切削 无功功率与转速和砂轮直径有关,在高速磨削状态下可通过选用直径 小的砂轮
(2)高速磨削砂轮
①砂轮基体(满足通用化,降低连接处应力,满足磨削时的强度和刚度 要求)
②锋利(也就是说,磨粒突出高度要大,以便能容纳大量的长切屑,一 般采用电镀结合砂轮)
③结合剂必须具有很高的耐磨性,以减少砂轮的磨损。(电镀结合砂轮, 多孔陶瓷结合剂砂轮)
10
高速磨削砂轮
11
(3)冷却润滑系统
2
3
Ⅱ工艺特点
一、磨削机理
①在高速超高速磨削加工过程中,在保持其它参数不变的条件下,随着 砂轮速度的大幅度提高,单位时间内磨削区的磨粒数增加,每个磨粒 切下的磨屑厚度变小,导致每个磨粒承受的磨削力大大变小,总磨削 力也大大降低。
②超高速磨削时,由于磨削速度很高,单个磨屑的形成时间极短。在极 短的时间内完成的磨屑的高应变率(可近似认为等于磨削速度) 形成过 程与普通磨削有很大的差别,表现为工件表面的弹性变形层变浅,磨 削沟痕两侧因塑性流动而形成的隆起高度变小,磨屑形成过程中的耕 犁和滑擦距离变小,工件表面层硬化及残余应力倾向减小。
15
结构形状优化后的高速砂轮
16
(4)优化冷却润滑系统 冷却润滑系统在高速磨削中有着极为重要的作用。除了要 注意冷却润滑液本身的化学构成外,其供给系统也十分重 要。因此,在研制高速磨床时,必须配置高压的冷却润滑 供给系统。
皮肤磨削术在皮肤科的应用进展

皮肤磨削术在皮肤科的应用进展引言随着现代科技的不断发展,皮肤磨削术在皮肤科的应用也不断取得了进展。
皮肤磨削术是一种通过机械、化学或激光等手段去除皮肤表面外层组织的方法,可以用于治疗皮肤疾病、改善皮肤质地、去除皱纹和色斑等。
本文将对皮肤磨削术的应用进展进行详细介绍,包括现有技术的发展、临床应用情况以及未来的发展趋势。
一、现有技术的发展1. 机械磨削术机械磨削术是最早出现的皮肤磨削技术,其原理是通过物理摩擦去除皮肤表面的角质层和表皮层,从而促进皮肤的再生和修复。
随着科技的进步,机械磨削术的设备和材料得到了不断改进,包括磨砂机、刨削器等工具的使用,有效提高了术后的效果和安全性。
化学磨削术是通过化学药物或化学制剂作用于皮肤表面,使其发生脱落和再生的方法。
目前常用的化学磨削剂包括果酸、水杨酸、尿素等,这些化学物质可以刺激皮肤代谢和再生,促进胶原蛋白的合成,从而改善皮肤质地和减轻皱纹。
激光磨削术是利用激光技术对皮肤进行磨削和去除,其优势在于精准、无创伤和恢复快。
目前常用的激光磨削术包括微钻激光、CO2激光、飞秒激光等,这些激光技术可以针对不同的皮肤问题进行治疗,包括痤疮疤痕、色斑、皱纹等。
二、临床应用情况1. 皮肤磨削术在疑难痤疮的治疗中的应用疑难痤疮是一种顽固性的慢性皮肤病,传统疗法难以有效治疗。
而通过机械磨削术、化学磨削术以及激光磨削术的应用,可以改善皮肤质地、促进炎症消退、减轻痘疤和色斑,显著改善患者的生活质量。
随着人口老龄化的加剧,皮肤老化问题日益突出。
机械磨削术、化学磨削术以及激光磨削术可以通过去除老化的皮肤组织、促进胶原蛋白的生成和皮肤再生,起到延缓皮肤老化、改善皱纹和松弛的作用。
色素沉着病变是一种常见的皮肤疾病,表现为色素沉着和色斑,严重影响患者的外貌和心理健康。
激光磨削术通过作用于色素颗粒和黑色素细胞,破坏色素颗粒的结构和代谢,以及促进色斑的脱落和再生,取得了显著的治疗效果。
三、未来的发展趋势1. 定制化治疗随着个体化医疗的发展,未来皮肤磨削术将更加趋向于个性化和定制化治疗。
陶瓷材料磨削加工的技术研究与发展现状
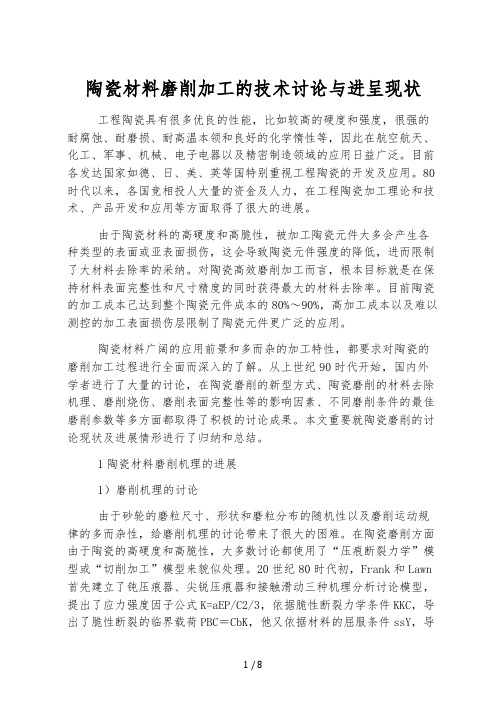
陶瓷材料磨削加工的技术讨论与进呈现状工程陶瓷具有很多优良的性能,比如较高的硬度和强度,很强的耐腐蚀、耐磨损、耐高温本领和良好的化学惰性等,因此在航空航天、化工、军事、机械、电子电器以及精密制造领域的应用日益广泛。
目前各发达国家如德、日、美、英等国特别重视工程陶瓷的开发及应用。
80时代以来,各国竞相投人大量的资金及人力,在工程陶瓷加工理论和技术、产品开发和应用等方面取得了很大的进展。
由于陶瓷材料的高硬度和高脆性,被加工陶瓷元件大多会产生各种类型的表面或亚表面损伤,这会导致陶瓷元件强度的降低,进而限制了大材料去除率的采纳。
对陶瓷高效磨削加工而言,根本目标就是在保持材料表面完整性和尺寸精度的同时获得最大的材料去除率。
目前陶瓷的加工成本己达到整个陶瓷元件成本的80%~90%,高加工成本以及难以测控的加工表面损伤层限制了陶瓷元件更广泛的应用。
陶瓷材料广阔的应用前景和多而杂的加工特性,都要求对陶瓷的磨削加工过程进行全面而深入的了解。
从上世纪90时代开始,国内外学者进行了大量的讨论,在陶瓷磨削的新型方式、陶瓷磨削的材料去除机理、磨削烧伤、磨削表面完整性等的影响因素、不同磨削条件的最佳磨削参数等多方面都取得了积极的讨论成果。
本文重要就陶瓷磨削的讨论现状及进展情形进行了归纳和总结。
1陶瓷材料磨削机理的进展1)磨削机理的讨论由于砂轮的磨粒尺寸、形状和磨粒分布的随机性以及磨削运动规律的多而杂性,给磨削机理的讨论带来了很大的困难。
在陶瓷磨削方面由于陶瓷的高硬度和高脆性,大多数讨论都使用了“压痕断裂力学”模型或“切削加工”模型来貌似处理。
20世纪80时代初,Frank和Lawn 首先建立了钝压痕器、尖锐压痕器和接触滑动三种机理分析讨论模型,提出了应力强度因子公式K=aEP/C2/3,依据脆性断裂力学条件KKC,导出了脆性断裂的临界载荷PBC=CbK,他又依据材料的屈服条件ssY,导出了塑性变形模式下临界载荷PYYC=s3/g3(或PYYC=H3Y/g3)。
磨削技术的发展趋势

磨削技术的发展趋势磨削技术作为一种重要的金属加工技术,一直以来都在不断地发展和完善。
随着科技的不断进步和工业领域的发展,磨削技术也呈现出一些明显的发展趋势。
首先,磨削技术的发展趋势之一是高效化。
随着生产效率要求的不断提高,传统的磨削工艺已经难以满足现代工业的需求。
因此,磨削技术正朝着高效化发展,通过改变磨削刀具的设计、改进磨削液的配方等手段,提高磨削过程的效率。
同时,磨削机床在自动化、智能化方面也得到了大幅度的提升,大大增强了生产的效率。
其次,磨削技术的发展趋势之二是精密化。
在一些高精度加工领域,如航空航天、光学仪器等领域,对零件的精密度要求非常高。
因此,磨削技术需要不断地提高精度,以满足这些需求。
目前,一些新型的磨削工艺和设备已经应用到了这些领域中,例如超精密磨削、超精密磨削等。
这些新技术和设备的应用可以使磨削加工达到更高的精度要求。
再次,磨削技术的发展趋势之三是绿色化。
随着环保意识的增强,磨削技术也在朝着绿色化的方向发展。
传统的磨削过程中,常常会产生大量的废液、废气和粉尘等工业污染物。
为了减少这些工业污染物对环境的影响,磨削技术需要采取一系列的措施,如改进磨削液的配方、研发新型的环保型磨削液等。
同时,磨削机床的设计和制造也需要考虑到节能、减排的要求,以减少其对能源资源的消耗。
最后,磨削技术的发展趋势之四是多功能化。
随着多品种、小批量生产的需求日益增加,传统的磨削技术已经不能满足现代工业的需求。
因此,磨削技术正朝着多功能化的方向发展,通过改进磨削工艺和磨削设备,使其具有更多的功能,能够适应不同产品的加工需求。
例如,磨削机床可以实现多轴、多道工序的加工,以提高生产效率和产品质量。
综上所述,磨削技术在高效化、精密化、绿色化和多功能化方面正朝着更加完善的方向发展。
随着科技的不断进步和工业的不断发展,相信磨削技术将会继续取得新的突破和进展,为现代工业的发展做出更大的贡献。
国内外激光磨削发展研究现状
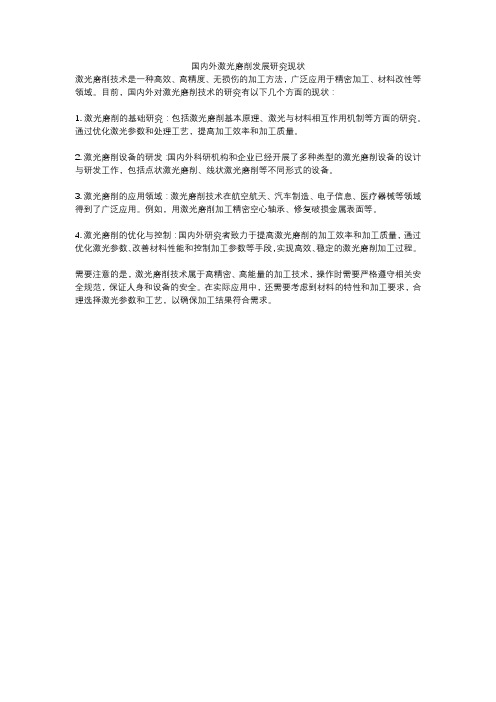
国内外激光磨削发展研究现状
激光磨削技术是一种高效、高精度、无损伤的加工方法,广泛应用于精密加工、材料改性等领域。
目前,国内外对激光磨削技术的研究有以下几个方面的现状:
1. 激光磨削的基础研究:包括激光磨削基本原理、激光与材料相互作用机制等方面的研究。
通过优化激光参数和处理工艺,提高加工效率和加工质量。
2. 激光磨削设备的研发:国内外科研机构和企业已经开展了多种类型的激光磨削设备的设计与研发工作,包括点状激光磨削、线状激光磨削等不同形式的设备。
3. 激光磨削的应用领域:激光磨削技术在航空航天、汽车制造、电子信息、医疗器械等领域得到了广泛应用。
例如,用激光磨削加工精密空心轴承、修复破损金属表面等。
4. 激光磨削的优化与控制:国内外研究者致力于提高激光磨削的加工效率和加工质量,通过优化激光参数、改善材料性能和控制加工参数等手段,实现高效、稳定的激光磨削加工过程。
需要注意的是,激光磨削技术属于高精密、高能量的加工技术,操作时需要严格遵守相关安全规范,保证人身和设备的安全。
在实际应用中,还需要考虑到材料的特性和加工要求,合理选择激光参数和工艺,以确保加工结果符合需求。
皮肤磨削术在皮肤科的应用进展

皮肤磨削术在皮肤科的应用进展皮肤磨削术是一种常见的皮肤整形手术,它在皮肤科领域有着广泛的应用。
随着科学技术的不断进步,皮肤磨削术在各个方面都有了很大的进展,成为了一种安全、有效的治疗方法。
本文将从皮肤磨削术的定义、历史、原理、技术和应用等方面进行介绍,以期为读者提供全面的了解。
一、皮肤磨削术的定义皮肤磨削术是一种通过物理或化学手段将皮肤表面的老化角质层、色斑层、疤痕层进行去除,从而达到使皮肤表面更加光滑、细腻、富有弹性的美容整形手术。
整形外科医生利用激光或化学剂等手段,将皮肤的不规则部分磨平,从而改善皱纹、色素沉着、痤疮疤痕等问题。
早在公元前5000年,埃及人就已经开始使用物理方法去除皮肤表面的老化角质层,以求美容。
随着医学技术的不断进步,皮肤磨削术逐渐成为一种常见的美容整形手术。
20世纪70年代,随着激光技术的发展,激光磨削术逐渐成为了主流。
之后,随着激光技术的不断完善和进步,皮肤磨削术的效果也得到了进一步提升。
皮肤磨削术主要通过刺激皮肤细胞的再生和修复机制,从而改善皮肤的外观。
在皮肤磨削过程中,医生可以根据具体的情况选择化学剂或激光等手段,将皮肤表面的老化细胞去除,从而刺激胶原蛋白的再生,促进皮肤的新陈代谢,使皮肤表面更加光滑、细腻。
皮肤磨削术还可以通过破坏黑色素细胞,减少黑色素沉着,改善皮肤的色素沉着问题。
目前,常见的皮肤磨削术包括机械磨削术、化学磨削术和激光磨削术等。
机械磨削术是利用机械磨削工具将皮肤表面的老化细胞刮除,是一种比较传统的磨削术。
化学磨削术是通过涂抹化学剂,使其与皮肤细胞发生化学反应,从而去除老化细胞。
激光磨削术是利用激光能量破坏皮肤表面的老化细胞,从而实现磨削的效果。
1. 抗衰老:随着年龄的增长,皮肤细胞的再生速度逐渐减慢,皮肤表面的老化角质层也会逐渐增厚,从而使皮肤看上去更老化。
皮肤磨削术可以通过去除老化角质层,刺激胶原蛋白的再生,从而减缓皮肤的衰老过程。
2. 痤疮疤痕修复:痤疮是一种常见的青春痘疾病,留下的疤痕给患者带来了极大的困扰。
钛合金磨削技术研究现状

一、引言钛合金材料具备密度低、强度大、耐高温和耐热冲击的特性,因此作为航空航天发动机和汽车模具的高附加值行业被广泛应用,同时钛合金优异生物化学惰性也是其广泛应用于生物医疗,特别是植入人体的植入物,如钛合金支架、钛合金关节、钛合金固定板和骨钉等。
钛合金优异的机械物理性能也使得其加工非常困难。
钛合金工件的精密磨削加工中由于其具有磨削力大、磨削温度高以及砂轮磨损和粘附严重的特点,磨屑变形复杂形成层叠状挤裂切屑,表面易生成硬脆性变质层甚至烧伤或出现热裂纹,影响零件的加工精度、表面质量以及使用寿命,成为制约钛合金材料应用的关键因素之一。
统计资料显示钛合金磨削时,磨削加工的成本在整个加工过程中占比可达到90%;其中40%-70%属于砂轮磨损成本,磨削比G(工件去除体积/砂轮磨损体积)为30-50,只有普通钢的1/2到1/4。
因此钛合金的磨削技术使当今乃至未来数十年研究的难点和热点问题。
二、国内外钛合金材料磨削加工研究现状1.国内钛合金材料磨削加工研究现状湖南大学高效磨削工程技术研究中心研究团队对钛合金材料磨削机理的进行了深入的研究和探讨。
该团队研制了砂轮线速度超300 m/s超高速平面磨削实验平台,并对TC4钛合金工件进行了磨削测试。
研究结果表明,随着砂轮线速度增加,单科磨粒的最小未变形切深减小,砂轮单位面积上的磨削力下降。
在实验中,通过SEM显微照片观察发现,钛合金在Vs=150 m/s,Vw=6m/ min,ap=1 mm的工况下获得的工件表面粗糙度和光洁度较好。
消除了钛合金低速磨削表面质量差且以出现烧伤及裂纹的问题。
钛合金的强制冷磨削也是研究的热点之一。
在钛合金磨削过程中,采用压缩液氮冷却工件与砂轮及其磨削区。
由于液氮温度通常较低,在空气中挥发会从工件与砂轮及其磨削区吸收热量,使加工后的钛合金表面温度下降,减少了工件的热膨胀变形,抑制了磨削烧伤。
同时液氮持续排出,充盈在磨削区域,将周围的氧气排出,将氧气与加工的钛合金表面分离,避免了形成化学反应,抑制了钛合金表面组织结构的改变。
磨削加工的发展趋势

金属切削加工
宽砂轮磨削适合在大批大量中、用切入磨削法磨削较 短零件表面,尤其是成形表面。
多砂轮磨削适用于同时磨削多个表面,例如同时磨削 曲轴和凸轮轴的几个轴颈。这类磨床也适用于大批大量生 产中。
1.2 提高机床的自动化程度
近年来,普通磨床的自动化程度在不断提高。自动化 的措施有自动进给、砂轮的自动修整和补偿、自动分度、 自动装卸料和自动测量等。应用于中、小批生产的磨床, 其自动化的显著趋势是向数控磨床及适应控制方向发展。
高速磨削是指将砂轮的线速度从目前的35m/s提高到 50~60m/s(目前国外个别磨床的线速度已达120 m/s)。 提高了磨削效率和磨削质量,延长砂轮使用寿命。
强力磨削是指以大的磨削深度进行磨削,它可以代替 车和铣,直接将毛坯磨削到工件要求,可显著提高效率。 强力磨削在加工难切削材料方面效果特别显著。强力磨削 时磨削力很大,因此,强力磨削机床(尤其是主轴组件) 的刚度很高,而且砂轮电动机的功率也提高了好几倍。
表面粗糙度要求达到Ra<0.02~0.04μm。为 了达到上述高精度和高表面质量要求,在机床结构 中采取了一系列提高精度和抗振性的措施。其中主 要的措施有:采用高刚度和高旋转精度的新型主轴 轴承;提高整机及主要部件的动态特性,尤其是动 刚度及静刚度;采用精密微量进给机构;严格控制 机床的热变形;隔绝各种振源;采用各种高精度的 自动测量装置以及高效率的冷却液净化装置等。
1.3 精密及超精密磨削
目前,对磨削加工精度和表面质量要求越来越高,高 精度外圆磨削的圆度要求小于0.5μm;表面粗糙度要求达 到Ra<0.01~0.02μm;高精度内圆磨削的内孔6μm; 平面磨削的平行度及直线度要求小于5μm/m;
金属切削加工
磨削加工的发展趋势
磨削技术的新进展
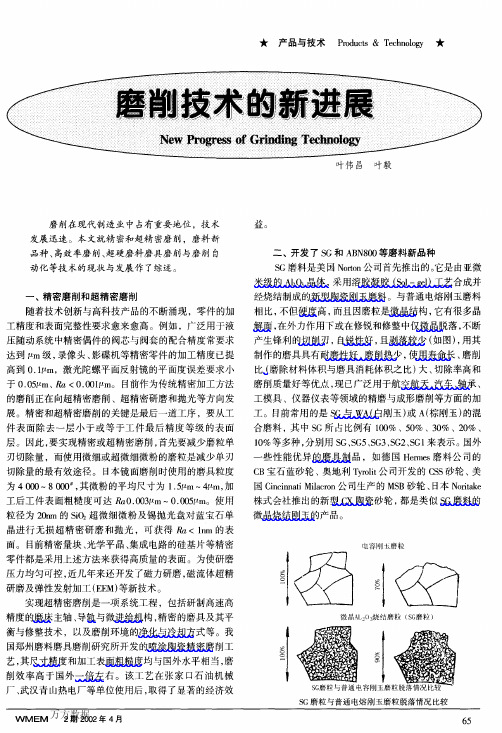
技术的发展,其中尤以高效点磨削新工艺更受人们的青 睐。
点磨削(Quickpoint Grinding)是由德国Junker公司首
先推出的。它是利用钎焊CBN薄砂轮(宽度只有几一)
和超高砂轮线速度(12嘶/s一18响/s,高的可达20嘶/s~ 25响/s)来实现的。加工时使砂轮轴线与工件轴线在水平 方向上形成一定倾斜角,以使砂轮与工件之间理论上的 线接触变成点接触。这样可大大减少磨削接触区面积,而 极高的磨削速度既可使磨屑变薄、磨粒负荷减轻,又可使 热量来不及传到工件和砂轮上,几乎都被磨屑所带走,提 高工件加工精度和表面质量。使用表明,点磨削的磨削比 大,砂轮寿命长,修整频率低,材料切除率高,同时由于它 采用和Nc车床一样的两坐标联动来实现复杂回转体零 件的表面磨削,一次安装能加工出外圆、锥面、曲面、螺 纹、台肩和沟槽等所有外形,比切入磨削有更大柔性,同 时冷却效果极佳,磨削温度低,甚至可以真正实现干磨 削,目前该工艺已在我国上海大众汽车有限公司桑塔纳 轿车生产线上使用,取得了显著的经济效益。
五、磨削技术发展方向 磨削当前除向超精密、高效率和超硬磨料方向发展 外,自动化也是磨削技术发展的重要方向之一。目前磨 削自动化在CNC技术日趋成熟和普及基础上,正在进一
眨箩
★产品与技术 PID(1ucts&Technology ★
步向数控化和智能化方向发展,许多专用磨削Nc软件 和系统已经商品化。磨削是一个复杂的多变量影响过 程,对其信息的智能化处理和决策,是实现柔性自动化和 最优化的重要基础。目前磨削中人工智能的主要应用包 括磨削过程建模、磨具和磨削参数合理选择、磨削过程监 测预报和控制、自适应控制优化、智能化工艺设计和智能 工艺库等方面。近几年来,磨削过程建模、模拟和仿真技 术有很大发展,并已达到实用水平。
高速磨削技术的现状及发展前景

高速磨削技术的现状及发展前景The Situ ation and Developing Vistas ofHigh-Speed G rinding T echnology荣烈润 摘 要:本文综述了高速磨削的概念、优势、关键技术、应用近况和发展前景。
关键词:高速磨削 动平衡 砂轮修整 精密高速磨削 高效深磨Abstract:This paper introduced concept,advantages,key technical points,application and developing vistas of high2speed grinding technology.K ey w ords:high2speed grinding dynamic balancing grinding wheel trim precision high2speed grind2 ing high2efficiency deep grinding0 引言人们一直对于提高磨削的砂轮速度所带来的技术优势和经济效益给予了充分的注意和重视。
但是在高速磨削过程中,工件受热变形和表面烧伤等均限制了砂轮速度的进一步提高,砂轮强度和机床制造等关键技术也使得高速磨削技术在一段时间内进展缓慢。
当20世纪90年代以德国高速磨床FS-126为主导的高速磨削(High-speed Grinding)技术取得了突破性进展后,人们意识到一个全新的磨削时代已经到来。
高速磨削技术是磨削工艺本身的革命性跃变,是适应现代高科技需要而发展起来的一项新兴综合技术,它集现代机械、电子、光学、计算机、液压、计量及材料等先进技术成就于一体。
随着砂轮速度的提高,目前磨削去除率已猛增到了3000mm3/ mm・s甚至更多,可与车、铣、刨等切削加工相媲美,尤其近年来各种新兴硬脆材料(如陶瓷、光学玻璃、光学晶体、单晶硅等)的广泛应用更推动了高速磨削技术的迅猛发展。
磨削加工的发展趋势论文
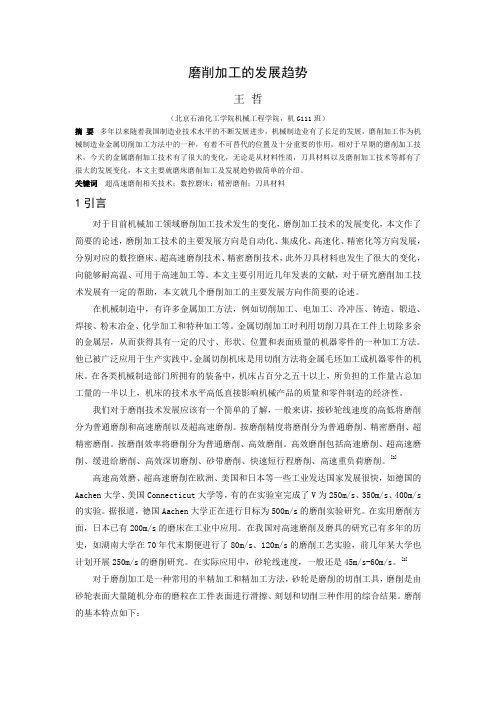
磨削加工的发展趋势王哲(北京石油化工学院机械工程学院,机G111班)摘要多年以来随着我国制造业技术水平的不断发展进步,机械制造业有了长足的发展,磨削加工作为机械制造业金属切削加工方法中的一种,有着不可替代的位置及十分重要的作用,相对于早期的磨削加工技术,今天的金属磨削加工技术有了很大的变化,无论是从材料性质,刀具材料以及磨削加工技术等都有了很大的发展变化,本文主要就磨床磨削加工及发展趋势做简单的介绍。
关键词超高速磨削相关技术;数控磨床;精密磨削;刀具材料1引言对于目前机械加工领域磨削加工技术发生的变化,磨削加工技术的发展变化,本文作了简要的论述,磨削加工技术的主要发展方向是自动化、集成化、高速化、精密化等方向发展,分别对应的数控磨床、超高速磨削技术、精密磨削技术,此外刀具材料也发生了很大的变化,向能够耐高温、可用于高速加工等。
本文主要引用近几年发表的文献,对于研究磨削加工技术发展有一定的帮助,本文就几个磨削加工的主要发展方向作简要的论述。
在机械制造中,有许多金属加工方法,例如切削加工、电加工、冷冲压、铸造、锻造、焊接、粉末冶金、化学加工和特种加工等。
金属切削加工时利用切削刀具在工件上切除多余的金属层,从而获得具有一定的尺寸、形状、位置和表面质量的机器零件的一种加工方法。
他已被广泛应用于生产实践中。
金属切削机床是用切削方法将金属毛坯加工成机器零件的机床。
在各类机械制造部门所拥有的装备中,机床占百分之五十以上,所负担的工作量占总加工量的一半以上,机床的技术水平高低直接影响机械产品的质量和零件制造的经济性。
我们对于磨削技术发展应该有一个简单的了解,一般来讲,按砂轮线速度的高低将磨削分为普通磨削和高速磨削以及超高速磨削。
按磨削精度将磨削分为普通磨削、精密磨削、超精密磨削。
按磨削效率将磨削分为普通磨削、高效磨削。
高效磨削包括高速磨削、超高速磨削、缓进给磨削、高效深切磨削、砂带磨削、快速短行程磨削、高速重负荷磨削。
磨削技术的发展现状及未来趋势分析

磨削技术的发展现状及未来趋势分析磨削技术是一种高精度、高效率的加工方法,广泛应用于机械制造、航空航天、汽车制造、电子设备等领域。
磨削技术的发展对制造业的提升和产品质量的改善起着重要作用。
本文将对磨削技术的发展现状及未来趋势进行分析。
近年来,磨削技术在国内外得到了快速发展。
一方面,随着高品质工件的需求不断增长,磨削技术逐渐成为高精度加工的主要方法之一。
在传统磨削技术的基础上,出现了多种新型磨削技术,如超声磨削、电化学磨削、电解腐蚀磨削等。
这些新技术不仅提高了工件的表面质量,还降低了加工成本和能耗。
另一方面,随着材料科学和机械制造技术的不断进步,磨削技术也在不断提高。
磨削刀具材料的研发使得切削效率得到了显著提升,磨粒性能的改善使得磨削加工得到了更好的控制,磨削液的优化使得磨削过程更加稳定和可靠。
这些技术进展让磨削技术在加工精度、表面质量和加工效率方面取得了巨大的进步。
未来,随着工业4.0和智能制造的快速发展,磨削技术将继续向着高精度、高效率和智能化方向发展。
首先,利用传感器和数据分析技术,实现磨削过程的监控和优化。
通过收集磨削过程中的各种数据,如刀具磨损情况、温度、振动等,可以实现对加工过程的实时监测和调整,提高加工效率和产品质量。
其次,磨削过程中的自动化和机器人技术将进一步推动磨削技术的发展。
自动化的磨削生产线可以实现对复杂形状工件的连续磨削加工,提高生产效率和稳定性。
机器人磨削系统可以实现对工件的全自动加工,减少人工干预,提高加工精度和一致性。
另外,磨削技术与其他加工技术的融合也将是未来的发展方向。
例如,磨削加工和3D打印技术结合,可以实现对复杂形状工件的加工;磨削加工和激光技术结合,可以实现对高硬度材料的加工。
这些新的磨削技术将进一步推动制造业的升级和创新。
此外,环保和节能也是磨削技术未来发展的重要方向。
随着能源和环境问题的日益突出,磨削工艺中的磨削液和废气处理将成为关注的焦点。
研发环保型磨削液和减少磨削过程中废气排放的技术不仅可以保护环境,还可以提高生产效率和降低成本。
磨削技术的历史、现状和展望

欧洲 高速 超 高速 磨 削技 术 的发展 起 步 比较 早 , 最初 在2 世纪 6 年 代末 期 就开 始进 行 高速 超 高速 磨 0 0 削 的基础 研 究 , 当时 实验 室 的 磨削 速度 就 已经达 到
2 0 2 0 / 。7 年 代 ,超 高速 磨 削开 始采 用C N 1 ~ 3 m S 0 B 砂 轮 。 l 8 年 德 国B e e 大 学 出 资 由 德 国 G h i g 93 rm n u r n
是否不 同?不 同之处在 哪里 ?原 因何在?
李长河教 授 :我 国和世 界各 国磨 削加工的发展重 点基本相 同,但在高速/ 高效磨削加工方面世界各国略
有不 同。
小切 削工具 。磨 削过程就 是 由这些成千 上万个磨粒 微
小切 刃 共 同连 续 完 成 的 。
M M :磨削加工 的发展 方向?为什么确 TT 立这样 的方向?
李长 河教授 :磨削技术 的历史非 常悠久 。人类 的祖 先最早用砂岩磨砺 燧 石工具 ,还用磨料将石 头磨 成饮食工具 。用于建造埃及金字塔 的巨大石 块也是用 原始 的磨料 工具切割而成,并用 砂岩磨 光他们 的表面 。
金 属 磨 削 始 于 公 元 前 2 0 年 的 古 埃 及 , 主 要 用 于 磨 锐 工 具 和 光 整 饰 00
高效磨 削工艺及装 备 的关键 实现技术和基 础理论 ,石
‘ l ‘ 等等 十
率 。美 国C n e t c t o n c iu 大学磨削研究与发展 中心 的无心 外 圆磨床 ,最 高磨削速度 2 0 m s 0 0 5 / 。2 0 年美 国马萨诸 塞州立大学 的S M l i 等人, 以1 9 m s .a k n 4 / 的砂轮速度 , 使用 电镀金 刚石砂轮通 过磨 削氮化硅 ,研究砂轮 的地
磨削技术现状与新进展
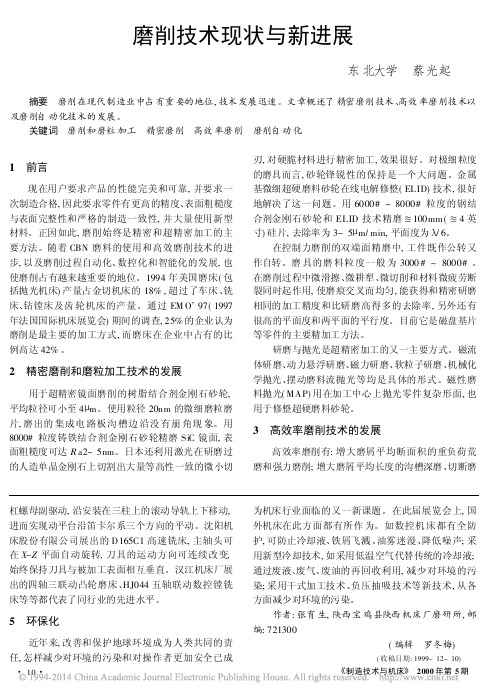
磨削技术现状与新进展东北大学蔡光起摘要磨削在现代制造业中占有重要的地位,技术发展迅速。
文章概述了精密磨削技术、高效率磨削技术以及磨削自动化技术的发展。
关键词磨削和磨粒加工精密磨削高效率磨削磨削自动化1前言现在用户要求产品的性能完美和可靠,并要求一次制造合格,因此要求零件有更高的精度、表面粗糙度与表面完整性和严格的制造一致性,并大量使用新型材料。
正因如此,磨削始终是精密和超精密加工的主要方法。
随着CBN磨料的使用和高效磨削技术的进步,以及磨削过程自动化、数控化和智能化的发展,也使磨削占有越来越重要的地位。
1994年美国磨床(包括抛光机床)产量占金切机床的18%,超过了车床、铣床、钻镗床及齿轮机床的产量。
通过EM O.97(1997年法国国际机床展览会)期间的调查,25%的企业认为磨削是最主要的加工方式,而磨床在企业中占有的比例高达42%。
2精密磨削和磨粒加工技术的发展用于超精密镜面磨削的树脂结合剂金刚石砂轮,平均粒径可小至4L m。
使用粒径20nm的微细磨粒磨片,磨出的集成电路板沟槽边沿没有崩角现象。
用8000#粒度铸铁结合剂金刚石砂轮精磨SiC镜面,表面粗糙度可达R a2~5nm。
日本还利用激光在研磨过的人造单晶金刚石上切割出大量等高性一致的微小切刃,对硬脆材料进行精密加工,效果很好。
对极细粒度的磨具而言,砂轮锋锐性的保持是一个大问题。
金属基微细超硬磨料砂轮在线电解修整(ELID)技术,很好地解决了这一问题。
用6000#~8000#粒度的钢结合剂金刚石砂轮和ELID技术精磨Á100mm(Á4英寸)硅片,去除率为3~5L m/min,平面度为K/6。
在控制力磨削的双端面精磨中,工件既作公转又作自转。
磨具的磨料粒度一般为3000#~8000#。
在磨削过程中微滑擦、微耕犁、微切削和材料微疲劳断裂同时起作用,使磨痕交叉而均匀,能获得和精密研磨相同的加工精度和比研磨高得多的去除率,另外还有很高的平面度和两平面的平行度。
磨削加工技术的现状
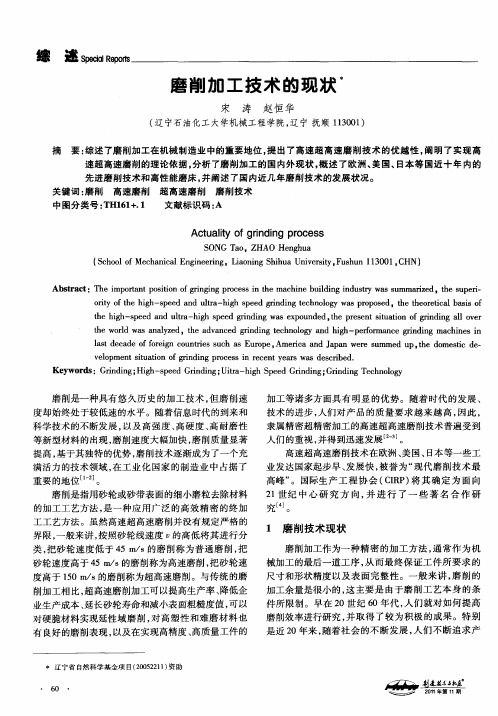
先进磨 削技术 和 高性 能磨床 , 阐述 了国 内近 几年磨 削技术 的发展 状 况。 并
关键 词 : 削 高速磨 削 超 高速磨 削 磨 削技术 磨
中图分 类号: H1 1 . T 6 +1 文 献标识 码 : A Ac u l fg id n r c s t ai o r ig p o e s t y n
满 活力 的技 术领 域 , 工 业 化 国家 的制 造 业 中 占据 了 在
重 要 的地位 。
加工等诸多方面具有明显的优势 。随着 时代 的发展 、
技 术 的进步 , 人们 对 产 品的 质量 要 求 越 来 越 高 , 因此 , 隶 属精 密超 精密 加工 的高 速超 高速磨 削 技术普 遍 受 到 人 们 的重视 , 并得 到迅 速发 展 q。 高 速超 高速磨 削 技术 在欧 洲 、 国、 美 日本 等一 些工 业 发达 国家起 步早 、 发展 快 , 誉 为 “ 代磨 削 技 术 最 被 现 高 峰” 国际生 产 工 程 协 会 ( I P 将 其 确 定 为 面 向 。 CR ) 2 世 纪 中 心 研 究 方 向 , 进 行 了 一 些 著 名 合 作 研 1 并
Absr c t a t:Th mpot n o iin o rn i g p o e s i h c i e b idng i d s ̄ wa u ei ra tp sto fg i gn r c s n t e ma h n u l i n u t ss mma ie rz d,t e s p r- h u e i o iy o h ih—s e d a d u ta i h s e rn n e h oo y wa o o e rt ft e h g p e n l -h g pe d gi di g tc n lg sprp s d,t h o e ia sso r he t e r tc lba i f
金属加工机械磨削技术

金属加工机械磨削技术一、前言与背景金属加工机械磨削技术作为机械加工领域的一个重要分支,起源于工业革命时期,随着工业生产的不断发展,金属加工技术也在不断进步和完善。
磨削技术作为金属加工中常见的一种加工方式,其通过对金属材料进行磨削,可以达到提高表面光洁度、尺寸精度和减小表面粗糙度的目的。
研究金属加工机械磨削技术具有重要意义,首先,提高磨削效率和加工质量可以有效降低生产成本,提高企业竞争力。
其次,磨削技术的发展推动了金属加工行业的技术进步,促进了新材料的应用和发展。
此外,磨削技术在航空、航天、汽车等领域的应用也日益广泛,对经济社会的发展产生了积极影响。
二、金属磨削技术的核心概念与分类1. 核心概念金属磨削技术是指利用磨削工具对金属材料进行切削,以提高表面质量、尺寸精度和减小表面粗糙度的加工方法。
磨削过程中涉及到的主要参数包括磨削速度、进给速度、切削深度等。
2. 分类及特征(1)按照磨削方式分类:外圆磨削、内圆磨削、平面磨削、曲面磨削等。
(2)按照磨削对象分类:黑色金属磨削、有色金属磨削、复合材料磨削等。
(3)按照磨削工具分类:磨粒磨削、陶瓷磨削、碳化物磨削等。
各类磨削技术具有不同的特征和应用领域,例如,外圆磨削适用于轴类零件的加工,平面磨削适用于板类零件的加工等。
3. 应用领域及市场潜力金属磨削技术广泛应用于航空、航天、汽车、精密仪器等领域,随着制造业的快速发展,市场需求不断提高,磨削技术市场潜力巨大。
三、金属磨削技术的关键技术及创新成果1. 关键技术金属磨削技术的关键技术主要包括磨削参数优化、磨削工具材料、磨削液选用等。
2. 创新成果(1)高速磨削技术:提高磨削速度,降低加工成本,提高加工效率。
(2)数控磨削技术:实现磨削过程的自动化和精确控制,提高加工精度。
(3)智能化磨削技术:利用和大数据技术,实现磨削参数的优化和自动调整。
3. 影响新技术的应用和性能提升对金属磨削技术的竞争格局和市场格局产生了积极影响,提高了企业的竞争力,推动了行业的快速发展。
凸轮轴磨削加工的发展与现状
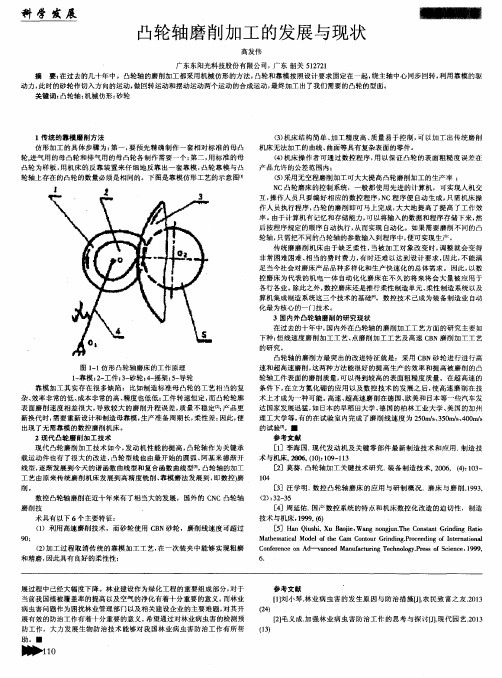
( 3 ) 机床结构简单 、 加 工精度高 、 质量 易于控制 , 可 以加 工出传统磨削 机床无法加工 的曲线 、 曲面等具有复杂表 面的零件 。 ( 4 ) 机床操作者可通 过数控程序 , 用 以保证 凸轮的表面粗 糙度误差在 产品允许 的公差 范围内; ( 5 ) 采 用无空程磨削加工可大大提 高凸轮 磨削加工 的生产率 : N C凸轮磨床 的控制系统 ,一般都使用先进的计算机,可实现人机交 互, 操作人员只要编好相 应的数控程序 , N C程序便 自动生成 , 只需机床操 作人员执行程序 , 凸轮 的磨削 即可马上完成 , 大大地提 高了提 高了工作 效 率。由于计算机有记忆和存储 能力, 可 以将输入的数据和程序存储 下来 , 然 后按程序规定的顺序 自动执行 , 从而实现 自动化 。如果需要磨 削不 同的凸 轮轴, 只需把 不同的凸轮轴 的参数输入 到程序 中, 便可实现生产 。 传统磨磨削机床 由于缺乏柔性 , 当被加工对象改变 时, 调整就会变得 非常 困难困难 、 相 当的费时费力 , 有 时还难 以达到设计要求 , 因此 , 不 能满 足当今社会对磨床产 品品种多样化和生产快速化的总体需求。 因此 , 以数 控磨床为代表 的机 电一体 自动化化 磨床 在不久的将来将会 大量被应 用于 各行各业。 除此之外, 数控磨床还是推行柔性制造单元、 柔性制造系统以及 算机集成制造系统这三个技术 的基础 。数控技术 己成为装备制造业 自动 化 最 为 核 心 的一 门技 术 。 3国内外 凸轮轴磨削的研究现状 在过去的十年 中, 国内外在 凸轮轴的磨削加工工艺方面 的研究主 要如 下种: 恒线速度磨削加工工艺、 点磨削加工工艺及高速 C B N磨 削加工 工艺 的研究。
磨削技术的发展趋势

磨削技术的发展趋势磨削技术是一种使用磨削工具对材料进行加工的机械加工方法。
随着现代制造技术的发展,磨削技术也在不断演进和改进。
下面将从材料需求、磨削工具、磨削工艺以及磨削设备四个方面来讨论磨削技术的发展趋势。
首先,随着对材料性能要求的不断提高,磨削技术面临着更高的材料需求。
传统的磨削主要针对金属材料,如铸铁、钢等。
但随着新材料的不断涌现,如高温合金、陶瓷材料、复合材料等,这些新材料具有很高的硬度、韧性和耐热性,传统的磨削工具无法满足对这些材料的加工需求。
因此,需要研发出新型的磨削工具来适应不同材料的加工。
其次,磨削工具的发展也是磨削技术发展的重要方面。
传统的磨削工具主要包括磨轮、磨石等,在加工过程中容易出现磨损和断裂的问题。
为了解决这些问题,需要开发出更加耐磨、耐高温的新型磨削工具。
例如,金刚石磨削工具具有很高的硬度和耐磨性能,可以适应对硬脆材料的加工需求。
同时,还可以利用纳米材料、复合材料等新材料来制备高性能磨削工具,以提高磨削效率和加工质量。
再次,磨削工艺的发展也对磨削技术的提升起到重要作用。
传统磨削工艺主要采用单点平面磨削,容易出现加工精度低、表面质量差的问题。
为了提高工件的加工精度和表面质量,需要采用多点磨削或者非接触磨削工艺。
多点磨削可以提高对材料的磨削效率和加工精度,而非接触磨削可以避免对工件表面产生划伤和烧伤等缺陷。
因此,在磨削工艺方面,需要进一步研究和开发新的工艺方法和技术。
最后,磨削设备的发展也是磨削技术改进的重要方面。
传统的磨削设备主要包括平面磨床、中心磨床等。
然而,随着对加工效率和精度要求的不断提高,传统的磨削设备已经无法满足需求。
因此,需要研发出新型的磨削设备,如数控磨削机床、自动磨削系统等,以提高加工效率和加工精度。
同时,磨削设备还需要具备高速、高稳定性和低能耗等特点,以适应现代制造业的需求。
总之,磨削技术的发展趋势主要体现在材料需求、磨削工具、磨削工艺和磨削设备方面。
- 1、下载文档前请自行甄别文档内容的完整性,平台不提供额外的编辑、内容补充、找答案等附加服务。
- 2、"仅部分预览"的文档,不可在线预览部分如存在完整性等问题,可反馈申请退款(可完整预览的文档不适用该条件!)。
- 3、如文档侵犯您的权益,请联系客服反馈,我们会尽快为您处理(人工客服工作时间:9:00-18:30)。
磨削技术的发展现状
磨削技术是一种将工件表面精确加工为所需形状和尺寸的机械加工方法。
随着现代制造业的发展,磨削技术也在不断进步和完善。
首先,磨削技术的机械设备得到了极大的改进和发展。
传统的磨床已经不再能够满足工艺要求,取而代之的是高速、精密、自动化的磨床。
这些先进的磨床设备具有更高的加工精度和效率,能够处理更复杂和精细的工件。
其次,使用的磨削工具也得到了改进。
传统的磨石逐渐被高硬度、高韧性的刚性磨削磨料所取代。
这些磨料能够更好地满足精密磨削的要求,并且能够提高加工效率和降低成本。
此外,磨削技术的自动化程度也在不断提高。
现代磨床配备了先进的数控系统,可以实现自动化的加工过程。
操作人员只需设定加工参数并监控加工过程,在大部分情况下无需直接干预。
这样不仅提高了加工效率和稳定性,还减少了人工操作错误的可能性。
此外,磨削技术在实现工艺的同时也注重环保和能源的节约。
一方面,磨削加工可以减少物料的浪费。
传统的切削加工通常会产生大量的切屑,而磨削加工则可大大减少切屑。
另一方面,磨削工具的设计也越来越注重能源的节约。
例如,通过优化磨削参数和减少磨削路径的方式,可以大大降低能源的消耗。
此外,磨削技术也逐渐向无损工艺方向发展。
传统的切削加工
往往会对工件表面产生变形和残余应力,而磨削加工则可以减少或避免这些问题。
因此,磨削技术在航空航天、汽车、船舶等高精度产品行业得到广泛应用。
总的来说,磨削技术在机械设备、磨削工具、自动化程度、环保性能和应用范围等方面都取得了显著的发展。
随着科技的不断进步和制造业的高速发展,磨削技术将继续迎来新的突破,以满足不断增长的工艺需求。