现场改善IE案例
合集下载
现场IE改善案例分析--生产线平衡分析改善案例
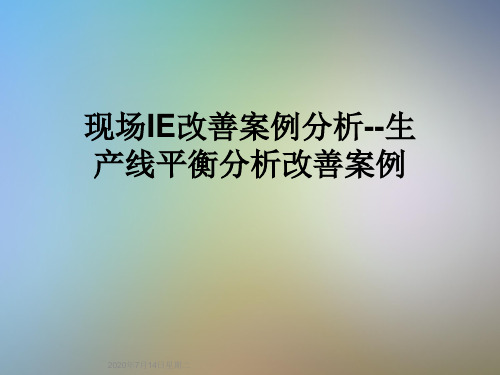
生产线平衡定义
对生产的全部工序进行均衡,调整作业 负荷和工作方式,消除工序不平衡和工 时浪费,实现“一个流”。
出料
入料
平衡生产线的意义
通过平衡生产线可以综合应用到程序分析、动作分析 、layout分析,搬动分析、时间分析等全部IE手法,提 高全员综合素质
在平衡的生产线基础上实现单元生产,提高生产应变 能力,对应市场变化实现柔性生产系统
(4) 4种增值的工作
站在客户的立场上,有四种增值的工作
1、使物料变形 2、组装 3、改变性能 4、部分包装
物料从进厂到出厂,只有不到 10% 的时间是增值的!
工序
符 号
内容
作业内容
分类
加工 作业
○
加工 作业
■产生附加价值的工序及作 业
卖得掉
检查
□
数量检查 ■虽然有必要,但需要进行 品质检查 改善的工序及作业
现场IE改善案例分析--生 产线平衡分析改善案例
2020年7月14日星期二
内容安排
一、线平衡定义 二、生产线平衡分析方法 三、B值、F值的定义与计算 四、线平衡案例分析
一、线平衡定义
生产线平衡定义
什么是生产线平衡
生产线平衡是指构成生产线各道工序所需的 时间处于平衡状态,作业人员的作业时间尽 可能的保持一致,从而消除各道工序间的时 间浪费,进而取得生产线平衡。
减少人手(1)
將工序3里的工作时 间分配至工序2﹑4 及5之內﹐从而工序 3里的人手可调配其 它生产线去
可行性﹕須工序 2﹐4及5內均有足夠 时间接受额外工作。
ቤተ መጻሕፍቲ ባይዱ
生产线平衡-例3﹕减少人手(2人)
降低线体速度,减少生产产量
工作時間
IE现场改善讲义《动作分析》

空手
抓
搬运
动作要素改善检查表
(1) 可否使用导轨或挡块进行定位? 修正位置 (2) 物品的角度、形状能否配合定位进行改变? (3) 可否通过设计使定位不会出错? (1) 是否可以使用固定装置或诱导装置方便组合? 组合 (2) 能否依次装配很多件? (1) 能否使用工具进行分解? 分解 (2) 可否一次分解很多件? (1) 工具的大小、形状、重量能否改变? 使用 (2) 工具的拿法拿的位置能否简单化? (3) 工具、仪器、设备的使用能否简单化?
拆卸(DA):将一物分解为两个以上目的物的动素。 它包括从物体被控制(握取),处于可拆卸状态的 一瞬间到完全拆开的瞬间。拆卸常在“握取”之 后以及“移动”或“放开”之前发生。
第一类动素说明
放开(RL):放下目的物的动素。它包括从手指开 始离开目的物的瞬间直至手指完全离开目的物的 瞬间。“开放”是与“握取”“抓”“持住”等 相反的动素,是所有动素中时间消耗最少的。当 用身体某一部份对物体控制的状态解除的一瞬间 也视为“放开。 检查(I):将目的物与规定标准相比较的动素。它 包括从眼睛开始寻找的一瞬间到目的物被发现的 瞬间。
基本动作要素分析
基本动作要素分析的基本思想是吉尔布雷斯奠定的, 他认为人所进行的作业是由某些基动作要素(简称动 素)按不同方式、不同顺序组合而成的。 为了探求从事某项作业的最合理的动作系列,必须 把整个作业过程中人的动作,按动作要素加以分解, 然后对每一项动素进行分析研究,淘汰其中多余的 动作,改善那些不合理的动作。
案例说明-1
案例说明-2
案例说明-3
案例说明-4
动作分析
沙布利克分析基本步骤 仔细观察作业过程,大体把握作业重点,最好 能在脑海中描绘出整个动作过程。 把整个动作过程分解成几个较大阶段性动作 (作业要素)。 按左右手、眼睛对阶段性动作进行动作要素分 解,把动作描述、相应的记号记入沙布利克分 析表。 将分析结果与实际动作进行对照,找出遗漏或 错误的地方进行修改。 应记得在表中填写单位名称、产品名、作业名 称、分析人、分析时间等使分析表完整。
现场改善IE案例
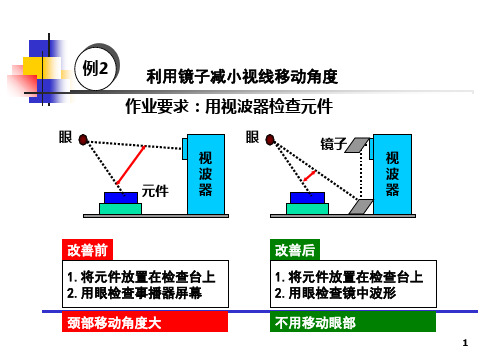
16
例17
辅助工具的应用
镊子
薄小零件
薄小零件
波纹板
改善前 用镊子把薄小零件夹起来 薄小零件易滑动
改善后 把薄小零件放在波纹板上
零件相对固定,夹取容易
17
例18
固定夹具 需长时间固定对象物时,可利用固定夹具
改善前
左手拿起螺栓, 右手将螺母拧上
改善后
左右手同时进行下述动作: 将螺栓放在固定夹具上, 再将螺母拧上
改善后 零件有序、对称放置, 双手同时、按顺序工作
12
例13
尽量缩小作业区域
传送带 工件 作业台
人
传送带 工件
人
★良好的照明有助于提高作业效率 ★适当的通风、正常的温度和湿度可以减轻疲劳 ★加强清扫和整理、合适的工作服可以避免工伤
13
例14
容器和器具
方形箱子
漏斗状/托盘状箱子
、、、、、、、、、
零件 过滤网 脏屑
9
例10
工具
改变材料和工具的存放状态
弹
夹
簧
工件
改善前
改善后
工具未固定
工具固定
取放距离不定
便于作业
10
例11பைடு நூலகம்作业场所的钳子放置
钳子
改善前 钳子放在桌子上, 拿起后要在手里倒一下
握法要调整
改善后 钳子放在漏斗状支架中
免去握法调整
11
例12 零件左右对称布置,便于双手作业
改善前
零件放置杂乱, 随即选择零件进行组装
14
例15
漏斗形容器的利用
加压
轴套 方形容器
改善前 从箱子中取轴套, 移动距离长,不好拿
漏斗形容器出口
例17
辅助工具的应用
镊子
薄小零件
薄小零件
波纹板
改善前 用镊子把薄小零件夹起来 薄小零件易滑动
改善后 把薄小零件放在波纹板上
零件相对固定,夹取容易
17
例18
固定夹具 需长时间固定对象物时,可利用固定夹具
改善前
左手拿起螺栓, 右手将螺母拧上
改善后
左右手同时进行下述动作: 将螺栓放在固定夹具上, 再将螺母拧上
改善后 零件有序、对称放置, 双手同时、按顺序工作
12
例13
尽量缩小作业区域
传送带 工件 作业台
人
传送带 工件
人
★良好的照明有助于提高作业效率 ★适当的通风、正常的温度和湿度可以减轻疲劳 ★加强清扫和整理、合适的工作服可以避免工伤
13
例14
容器和器具
方形箱子
漏斗状/托盘状箱子
、、、、、、、、、
零件 过滤网 脏屑
9
例10
工具
改变材料和工具的存放状态
弹
夹
簧
工件
改善前
改善后
工具未固定
工具固定
取放距离不定
便于作业
10
例11பைடு நூலகம்作业场所的钳子放置
钳子
改善前 钳子放在桌子上, 拿起后要在手里倒一下
握法要调整
改善后 钳子放在漏斗状支架中
免去握法调整
11
例12 零件左右对称布置,便于双手作业
改善前
零件放置杂乱, 随即选择零件进行组装
14
例15
漏斗形容器的利用
加压
轴套 方形容器
改善前 从箱子中取轴套, 移动距离长,不好拿
漏斗形容器出口
IE改善案例展示及学习
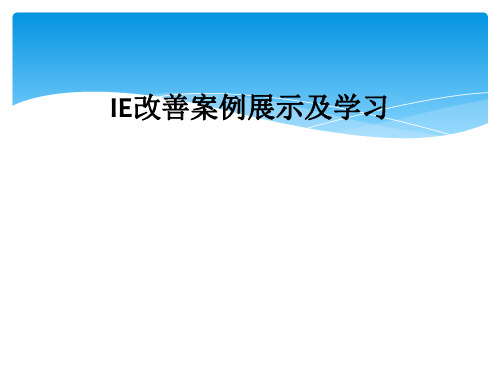
提效 王振凤
改善对象 改善日期
问题描述
商用公司370型号安装底脚工位员工没有工装,只能用手将底脚安装上,影响员工工作效率
商用公司 2012.07.28
改善措施
根据370底脚样式制作打底脚工装(如图所示),将此工装安在气枪上,把底脚安装好,即省了人力又减少操作时间10s
类别
改善前
改善后
对比照片
差异
员工打底脚时没有工装,用手操作,费时费力
--实验装置之间,而且,试验装 置在另一个房间,从而造成在这 两个房间之间频繁移动现象。
消除一点一滴的浪费是我们追求的目标
1.器皿的配置
作业量减少,操作更简单。简化
2.储水瓶
橡胶软管,橡胶栓种类减少,烧杯减少
3.过滤台(装置的配置台)
作业台减少,有效利用空间
消除一点一滴的浪费是我们追求的目标
改善方案
消除一点一滴的浪费是我们追求的目标
消除一点一滴的浪费是我们追求的目标
消除一点一滴的浪费是我们追求的目标
2.现场改善项目汇总
改善名称 改善部门 问题描述
刷漆工位接漆工装设计 IE办公室
改善类型 改善人
IE改善档案卡
质量改善 管伟琴
生产现场刷漆工位在刷漆过程中油漆经常滴落在压机底板上,影响产品质量
消除一点一滴的浪费是我们追求的目标
1)推进项目汇总表
3.物料模块化进度
项目
第一期 (商用公司)
已完成 7
推进中 0
第二期 (冷柜业务链)
3
4
第二期
(冰箱业务链)
2
5
澳洋
0
8
消除一点一滴的浪费是我们追求的目标
暂不实施 4 0 0 0
改善对象 改善日期
问题描述
商用公司370型号安装底脚工位员工没有工装,只能用手将底脚安装上,影响员工工作效率
商用公司 2012.07.28
改善措施
根据370底脚样式制作打底脚工装(如图所示),将此工装安在气枪上,把底脚安装好,即省了人力又减少操作时间10s
类别
改善前
改善后
对比照片
差异
员工打底脚时没有工装,用手操作,费时费力
--实验装置之间,而且,试验装 置在另一个房间,从而造成在这 两个房间之间频繁移动现象。
消除一点一滴的浪费是我们追求的目标
1.器皿的配置
作业量减少,操作更简单。简化
2.储水瓶
橡胶软管,橡胶栓种类减少,烧杯减少
3.过滤台(装置的配置台)
作业台减少,有效利用空间
消除一点一滴的浪费是我们追求的目标
改善方案
消除一点一滴的浪费是我们追求的目标
消除一点一滴的浪费是我们追求的目标
消除一点一滴的浪费是我们追求的目标
2.现场改善项目汇总
改善名称 改善部门 问题描述
刷漆工位接漆工装设计 IE办公室
改善类型 改善人
IE改善档案卡
质量改善 管伟琴
生产现场刷漆工位在刷漆过程中油漆经常滴落在压机底板上,影响产品质量
消除一点一滴的浪费是我们追求的目标
1)推进项目汇总表
3.物料模块化进度
项目
第一期 (商用公司)
已完成 7
推进中 0
第二期 (冷柜业务链)
3
4
第二期
(冰箱业务链)
2
5
澳洋
0
8
消除一点一滴的浪费是我们追求的目标
暂不实施 4 0 0 0
IE生产效率改善与流程优化案例

生产管理研修班专用培训教材
生产管理研修班专用培训教材
6大防错案例分析
生产管理研修班专用培训教材
案例应用:
1.鸡蛋之隔层装运盒减少搬运途中的损伤.(缓和原理)
2.设立多层之检查方法,考试后检查一次看看,有没有犯错的地方.(保险原理)
3.自动消防洒水系统,火灾发生了开始自动洒水灭火.(警告原理)
4.汽车之安全带,骑机车戴安全帽.(保险原理)
2、作业员责任很小,已够努力 如厕/休息仅各占5%左右 已是世界性宽放水准范围内
3、停工待料占11%,为何?
生产管理研修班专用培训教材
IE十大手法之七 — 搬运法
从到
料 件
搬运 者
容 器
用 车
重量
距 离
时间
次 数
改善 重点
生产管理研修班专用培训教材
IE十大手法之八 — 提案法(工作改善)
题目:油品加注 机的改善
程式时间
6
2
F5 开机
7
2 .9 7
取出M /B
8
4 .9 7
拆治具(C P U )
9
4 .2 2
目檢,SFIS
10
2 .5 5
盖测试章
11
1.3 7
放M /B 于输送帶
C ycle tim e(秒) (A ) 15 1.76
O P 时间(秒)
(B )
3 6 .9 2
人机比例
C = A /B
4 .11
观测事象 有效作业 准备作业 不良重制重修
休息 如厕/喝茶
交谈 停工待料 机台故障
比率% 29 20 14 4 5 5 11 4
生产管理研修班专用培训教材
现场改善及ie手法

THANK YOU
感谢聆听
时间研究
通过观察和测量作业人员完成某项任务所需的时间,制定合理的时 间标准。
作业标准化
将最优的作业方法和流程标准化,确保所有作业人员都能按照统一 的标准进行操作,提高生产效率和产品质量。
标准作业程序(SOP)制定
编写详细的标准作业程序,明确每一步骤的操作规范和要求,为作 业人员提供明确的指导。
生产线平衡与布局优化
运用各种计划和控制手段,确 保生产系统按照预定目标高效 运行。
IE手法在现场改善中的应用
流程优化
通过分析和改进工作流程,消除浪费、提高效率 。例如,减少不必要的操作步骤、简化工作流程 等。
设备改善
对生产设备进行改进和优化,提高设备效率和可 靠性。例如,采用自动化设备、改进设备维护计 划等。
物料管理
意义
现场改善是企业提高竞争力、实现可持续发展的重要手段之一。 通过现场改善,企业可以不断提高产品质量、降低生产成本、提 高生产效率、增强员工士气,从而赢得更多的市场份额和客户信 任。
现场改善的目标与原则
目标
现场改善的主要目标是提高生产效率、降低生 产成本、提高产品质量、增强员工士气等,以
实现企业的整体经营目标。
现场改善及IE手法
目
CONTENCT
录Hale Waihona Puke • 现场改善概述 • IE手法简介 • 现场改善的步骤与方法 • IE手法在现场改善中的具体应用 • 现场改善的实践案例 • 现场改善的挑战与对策
01
现场改善概述
现场改善的定义与意义
定义
现场改善是一种通过优化工作流程、提高工作效率和质量、降低 成本等方法,对生产现场进行持续改进的管理方法。
IE现场改善专案报告

2015年10月 2015年11月 2015年12月
李自岳/ 刘庆鹤
付国华/ 张文雅
计划 执行
2016年1月
付国华
IE
计划 执行
李自岳/ 刘庆鹤
赵永强
计划 执行
李自岳/ 刘庆鹤
赵永强
计划 执行
李自岳/ 刘庆鹤
赵永强
计划 执行
李自岳/ 刘庆鹤
赵永强
计划 执行
李自岳/ 刘庆鹤
赵永强
计划 执行
李自岳/ 刘庆鹤
一.成立背景及课题选定
1.2 课题选定之订单分析
根据10月份产能分析得,该型号订单量占公司总订订量的34.8%。
二.改善计划及目标设定
2.1 改善计划
内容
冲压A903车间LAYOUT布置
效果确认
A903改善48米流水线作业 改为30米作业(41人)
流程改善(山积表/平衡率 /IE七大手法)
A903改善(41人改为36 人,产能不变)
TT:22.4s
12
12
8
2 2
TT:19s
五.效果确认
5.1 各项指标数
41人
生
产
人
36人 数
:
减
少
改善前
改善后
5
人
400
350
面
300 200
220
积 :
减
100
少
13
0
0
改善前 改善后 M²
生 产 人 数 : 减 少 5 人
流 水 60
线 50
长 40
度 30
: 20
减 少
18
10 0
米
48米 改善前
现场IE改善(PPT47张)
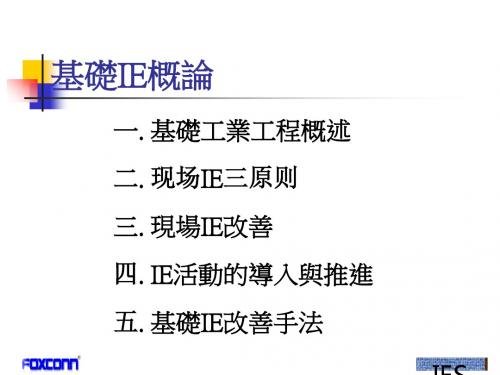
5、改善瓶颈岗位
(1)改善的4大原則
1)减少动作次数 2)同时使用双手 3)缩短移动距离 4)使动作变得轻松
(2) IE动作改善的4原则
ECRS原则 1、Eliminate 2、Combine 3、Rearrange 4、Simplify
——取消 ——合并 ——重排 ——简化
(3)ECRS法运用图示简介
四.基礎IE改善手法 1﹒何謂基礎IE手法
“基礎IE手法是以人的活動為中心 ﹐以事實為依據﹐用科學的分析方法對 生產系統進行觀察﹑記錄﹑分析﹐並對 系統問題進行合理化改善﹐最后對結果 進行標準化的方法”
IE手法一﹕動作改善法(作業標準化)
作業員須每隔28秒轉 身一次﹐取身后的膠 帶﹐這樣每小時須做 150次轉身無效轉身取 膠帶動作
3600<H> 节拍<TT>= 目标产量
二. 现场IE改善<3>
2.现场IE三原则 a、划节距线<25-30cm>,根据标准工时 调整拉速节拍<TT>。 b、保证每个节距有一个产品。 c、每个岗位不准堆积。
生产线平衡计算
平衡率=
(各工序的作业时间总和) * 100% 瓶颈岗位时间*人数<工位数>
改变观念
1、观念改变 2、行动改变 则 则 行动改变 习惯改变
3、习惯改变
则
命运改变
团队与集团的区别
集体
目标不一致
团队
目标一致
Q&A time
本課程到此告一段落﹐請大家就有疑問 的部分踴躍提問﹐謝謝﹗
• • • • • • • • • • • • • • • • • • • • • • • • • • • • • • • • • • • • • • • • • • • • • • • • • • • • • • • • • • • • • • • • • • • • • • • • • • • • • • • • • • • • • • • • • • • • • • • • • • • •
现场改善四大原则
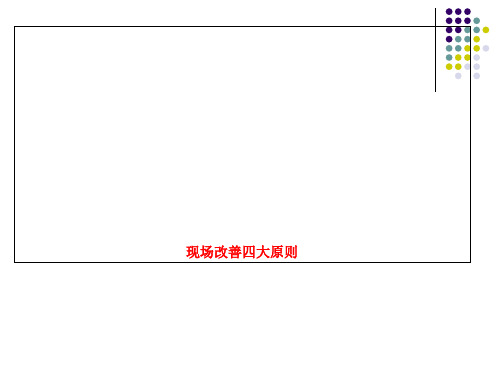
Peter Chen
2. Machine (機器設備方面) :
2-1.提高自動化/半自動化水平; 2-2.采用高效专用的工艺装备,减少辅助操作时间; 2-3.改变切削用量以减少机器作业时间;
--- 別把鐵杆磨成針 2-4.不切削空氣;
(進刀到加工物的距離過長,或上下模距離太遠)
2-5.盡量以足踏、夾具替代手的工作; 2-5.人機同步作業. 2-6.人機比合理配置.
件來件不良數
據后,提出取消
測試的建議,獲
得品管部支持,
風扇測試
喇叭測試
燈線測試
對大部分機種 取消測試,並督
促供應商加強
品質保証.
“ECRS”改善原则 – 合並
(2)合并(Combine)——对于无法取消而又有必要的,看是 否能够合并,以达到省时简化的目的。
改善案例:燈線測試改善.
測試導通
測試靜電
改善前: 一個治具測試燈線導通功能, 一個治具測試靜電,二工站 作業,共需2人.
(2)合并(Combine)——对于无法取消而又有必要的,看是 否能够合并,以达到省时简化的目的。
(3)重排(Rearrange)——经过取消、合并后,可再根据“ 何人、何地、何时”三个提问进行重排,使其能有最 佳的顺序、除去重复、办事有序。
(4)简化(Simple)——经过取消、合并、重排后的必要工作 ,就可考虑能否采用最简单的方法及设备,以节省人 力、时间及费用。
3. Material (材料方面) :
3-1.確保物料供應的及時性、準確性. 3-2.物料擺放位置、擺放方式合理化.避免
搬運距離過長、或需要彎腰、轉身拿 取物料. 3-3.同一工站不可使用易混淆的物料. 3-4.物料包裝合理化,減少拆卸的時間.
2. Machine (機器設備方面) :
2-1.提高自動化/半自動化水平; 2-2.采用高效专用的工艺装备,减少辅助操作时间; 2-3.改变切削用量以减少机器作业时间;
--- 別把鐵杆磨成針 2-4.不切削空氣;
(進刀到加工物的距離過長,或上下模距離太遠)
2-5.盡量以足踏、夾具替代手的工作; 2-5.人機同步作業. 2-6.人機比合理配置.
件來件不良數
據后,提出取消
測試的建議,獲
得品管部支持,
風扇測試
喇叭測試
燈線測試
對大部分機種 取消測試,並督
促供應商加強
品質保証.
“ECRS”改善原则 – 合並
(2)合并(Combine)——对于无法取消而又有必要的,看是 否能够合并,以达到省时简化的目的。
改善案例:燈線測試改善.
測試導通
測試靜電
改善前: 一個治具測試燈線導通功能, 一個治具測試靜電,二工站 作業,共需2人.
(2)合并(Combine)——对于无法取消而又有必要的,看是 否能够合并,以达到省时简化的目的。
(3)重排(Rearrange)——经过取消、合并后,可再根据“ 何人、何地、何时”三个提问进行重排,使其能有最 佳的顺序、除去重复、办事有序。
(4)简化(Simple)——经过取消、合并、重排后的必要工作 ,就可考虑能否采用最简单的方法及设备,以节省人 力、时间及费用。
3. Material (材料方面) :
3-1.確保物料供應的及時性、準確性. 3-2.物料擺放位置、擺放方式合理化.避免
搬運距離過長、或需要彎腰、轉身拿 取物料. 3-3.同一工站不可使用易混淆的物料. 3-4.物料包裝合理化,減少拆卸的時間.
《IE现场优化改善》课件

展望
未来企业应进一步拓展IE现场优化改 善的领域,加强与其他管理方法的融 合,实现更高效、更灵活、更智能的 生产模式。
谢谢观看
《IE现场优化改善》PPT课件
目录
• IE现场优化改善概述 • IE现场优化改善方法 • IE现场优化改善案例分析 • IE现场优化改善的未来发展 • 结论与建议
01
IE现场优化改善概述
定义与目标
定义
IE现场优化改善是一种通过系统地分析和改进生产现场的布局、操作流程、设 备及工装夹具等,以提高生产效率、降低成本、提升质量的管理方法。
费,提升产品质量和客户满意度。
动作分析
01
动作分析的定义
通过对作业过程中动作的分析和研究,寻找最优的动作方法和顺序。
02
动作分析的工具
动素分析、动作经济原则。
03
动作分析在IE现场优化中的应用
通过动作分析,消除多余和无效的动作,提高作业效率和生产线的平衡
,降低成本和浪费,提升产品质量和客户满意度。
制定标准、宣传培训、执行落实、检查考 核、持续改进。
通过5S管理,优化现场布局,提高作业效 率和生产线的平衡,减少浪费和不良品, 保障员工安全和健康。
流程优化
流程优化的定义
对现有流程进行分析、改进和优化,提高流程效率和效果。
流程优化的原则
明确目标、关注瓶颈、整体优化、持续改进。
流程优化的方法
流程图绘制、流程分析、流程改进、流程再造。
时间研究
时间研究的定义
通过对作业过程中所需时间的分析和研究,制定标准作业时间。
时间研究的工具
时间测量表、工作抽样。
时间研究在IE现场优化中的应用
通过时间研究,制定合理的生产计划和排程,提高生产效率和产能,降低成本和浪费,提 升产品质量和客户满意度。
未来企业应进一步拓展IE现场优化改 善的领域,加强与其他管理方法的融 合,实现更高效、更灵活、更智能的 生产模式。
谢谢观看
《IE现场优化改善》PPT课件
目录
• IE现场优化改善概述 • IE现场优化改善方法 • IE现场优化改善案例分析 • IE现场优化改善的未来发展 • 结论与建议
01
IE现场优化改善概述
定义与目标
定义
IE现场优化改善是一种通过系统地分析和改进生产现场的布局、操作流程、设 备及工装夹具等,以提高生产效率、降低成本、提升质量的管理方法。
费,提升产品质量和客户满意度。
动作分析
01
动作分析的定义
通过对作业过程中动作的分析和研究,寻找最优的动作方法和顺序。
02
动作分析的工具
动素分析、动作经济原则。
03
动作分析在IE现场优化中的应用
通过动作分析,消除多余和无效的动作,提高作业效率和生产线的平衡
,降低成本和浪费,提升产品质量和客户满意度。
制定标准、宣传培训、执行落实、检查考 核、持续改进。
通过5S管理,优化现场布局,提高作业效 率和生产线的平衡,减少浪费和不良品, 保障员工安全和健康。
流程优化
流程优化的定义
对现有流程进行分析、改进和优化,提高流程效率和效果。
流程优化的原则
明确目标、关注瓶颈、整体优化、持续改进。
流程优化的方法
流程图绘制、流程分析、流程改进、流程再造。
时间研究
时间研究的定义
通过对作业过程中所需时间的分析和研究,制定标准作业时间。
时间研究的工具
时间测量表、工作抽样。
时间研究在IE现场优化中的应用
通过时间研究,制定合理的生产计划和排程,提高生产效率和产能,降低成本和浪费,提 升产品质量和客户满意度。
班组长管理训练之三--IE7大手法与现场改善

▪ 同时,必须把改善目标具体化。例如: 想更进一步提高效率,增 加每一个作业所负责的机械台数,以便达到省力化的目的。此例 提高机械的生产转动效率是第一个目标。
分析一周期作业
▪ 对于作业者及机械, 各自要针对一周期的作业内容, 制作一份工 程流动图。
制作人机分析图表
▪ 使用联合工程分析记号表示各个步骤, 再以“柱”的长度, 表示 所需要的时间, 更进一步为使时间一致化, 利用人机工程图表示 。
改善的四原則
原则
目标
例
取消 合并 重排 简化
不能取消吗? 取消又会变成如何?
检查的省略 配置变更的搬运省略
能否把两种以上的工程合而为一 ?
两种以上的加工,能否同时进 行作业 加工与检查同时进行
能否重排工程?
变更加工顺序,以便提高效率
不能更为简单吗?
作业的重新估计 自动化
取消
▪ 对程序图上的每一项工序都加以审查,确认其保留的必要性, 凡可取消者一律取消,例如:
加工 搬运 检查 停滞
使作业内容具体化
职务名称、人 机械名称、设备名 使作业场所 加工时间、 使加工次序具体化
数、个人名称 称、钻模名称、台 具体化
生产量
等
数等
使搬运内容具体化
同上
搬运设备(起重机、 从何地到何 搬运时间 台车、卡车、吊具) 处
一次的搬运个数、 装货、卸货方法等
使检查项目具体化
同上
检查设备、检查工 具等
▪ 工业工程的主要工作内容: ▪ 1 方法研究(改善工具): ▪ 程序分析 ▪ 作业分析 ▪ 动作分析 ▪ 2 时间研究(衡量标准): ▪ 作业标准和标准工时的测定
二、工业工程的原理
▪ 工作研究的实施步骤: ▪ 1 寻求最经济的工作方法(方法研究、工作改善); ▪ 2 工作方法、材料、工具及设备的标准化; ▪ 3 确定标准工作时间.
分析一周期作业
▪ 对于作业者及机械, 各自要针对一周期的作业内容, 制作一份工 程流动图。
制作人机分析图表
▪ 使用联合工程分析记号表示各个步骤, 再以“柱”的长度, 表示 所需要的时间, 更进一步为使时间一致化, 利用人机工程图表示 。
改善的四原則
原则
目标
例
取消 合并 重排 简化
不能取消吗? 取消又会变成如何?
检查的省略 配置变更的搬运省略
能否把两种以上的工程合而为一 ?
两种以上的加工,能否同时进 行作业 加工与检查同时进行
能否重排工程?
变更加工顺序,以便提高效率
不能更为简单吗?
作业的重新估计 自动化
取消
▪ 对程序图上的每一项工序都加以审查,确认其保留的必要性, 凡可取消者一律取消,例如:
加工 搬运 检查 停滞
使作业内容具体化
职务名称、人 机械名称、设备名 使作业场所 加工时间、 使加工次序具体化
数、个人名称 称、钻模名称、台 具体化
生产量
等
数等
使搬运内容具体化
同上
搬运设备(起重机、 从何地到何 搬运时间 台车、卡车、吊具) 处
一次的搬运个数、 装货、卸货方法等
使检查项目具体化
同上
检查设备、检查工 具等
▪ 工业工程的主要工作内容: ▪ 1 方法研究(改善工具): ▪ 程序分析 ▪ 作业分析 ▪ 动作分析 ▪ 2 时间研究(衡量标准): ▪ 作业标准和标准工时的测定
二、工业工程的原理
▪ 工作研究的实施步骤: ▪ 1 寻求最经济的工作方法(方法研究、工作改善); ▪ 2 工作方法、材料、工具及设备的标准化; ▪ 3 确定标准工作时间.
现场管理与改善-IE手法的活用(PPT 167页)

中國大陸: 台合電子(廈門)、隆光音箱廠(深圳)、瑞泰電子(深圳)、加維公 司(大朗)等
2020/4/15
Page3
UNION POWER
課程大綱
壹、 現場的管理與改善 貳、 5W2H 參、 動作經濟原則 肆、 時間測定與標準時間 伍、 生產線平衡 附 錄: 工作衡量技法MOST的簡介
2020/4/15
2020/4/15
Page31
UNION POWER
三、 從自問開始
為什麼需要這樣做? 它做的目的是什麼? 在什麼地方進行最好? 應該在什麼時候做? 什麼人最適合去做? 用什麼方法做最好? 要花多少費用?
配合對項細目的自問檢討
材料,機器,設備,工具,設計,配置, 動作,安全,整理整顿
2020/4/15
2020/4/15
Page16
UNION POWER
七、改善的十大步驟
STEP 1
現場問題的發掘
2020/4/15
Page17
UNION POWER
八、 IE手法概要
IE手法是以人的活動爲中心,事實爲依據,用科學的分析方法, 對生産系統進行觀察、記錄分析,並對系統問題進行合理化改善, 最後對結果進行標準化的方法。
案例
例 : ●動作研究 (MOTlON STUDY)
生產線-工程(工作)-作業-動作-動素
(主要指標: 距離、時間、方法、人員)
●時間研究 (TIME STUDY)
工作抽查、工時測定、生產線平衡法
(主要指標: 時間、效率)
2020/4/15
Page25
UNION POWER
案例
●系統流程 (SYSTEMATIC LAYOUT)
前 言
【精益教材】第2节:现场改善IE七大手法(下)
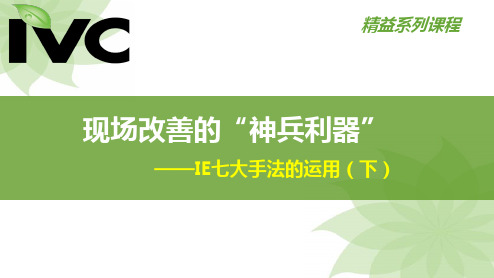
精益系列课程
现场改善的“神兵利器”
——IE七大手法的运用(下)
上节课程回顾
1、IE七大手法是什么?七大手法口诀? 答:“走(流)动的五个人抽双防烟” 流程法、动改法、五五法、人机法、抽查法、双手法、防呆法
2、防呆法的十大原则是什么?举例说明。 答:断根—隔离—警告—保险—相符—缓和—层别—
顺序—自动—复制。
流程程序图的分类
2、人型流程程序图
它是以人为研究对象,对他/她完成所有 工序的整个过程进行记录分析。
案例(发料):
工作内容:仓库发料员发料 开始:发料员坐在工作台旁 结束:发料员发完料坐到工作台旁
流程法的分析技巧
1个不忘:动作经济原则 4大原则:ECRS(取消、合并、重排、简化) 5个方面:加工、搬运、储存、检验、等待 5W1H技术:What/Where/When/Who/Why/How 6大步骤:选择、记录、分析、建立、实施、维护
案例:对制粒某机器作业率进行观测,估计该机器停机率为25%,需要观测
精度的绝对误差为0.01,可靠度为95%,求需观测的次数。(查表得正态分 布下的Z值为1.96)
答﹕P=0.25, 1-P=0.75, Z=1.96, E=0.01 由公式, n=P(1-P)Z2/E2 =0.25X0.75X1.962/0.012 =7203次
95.45%的可靠度,就是说实现预定 的抽样资料中有95.45%以上落入2 σ 的范围,仅有4.55%的误差。
抽查法的步骤
正态分布曲线
[P(1 P )] n
P-观测时间发生率 n-观测次数
抽查法的步骤
2、绝对精度和相对精度
使用抽查法时,会存在误差,所允许的误差用精确度来衡量。 精确度又分为绝对精确度E和相对精确度S
现场改善的“神兵利器”
——IE七大手法的运用(下)
上节课程回顾
1、IE七大手法是什么?七大手法口诀? 答:“走(流)动的五个人抽双防烟” 流程法、动改法、五五法、人机法、抽查法、双手法、防呆法
2、防呆法的十大原则是什么?举例说明。 答:断根—隔离—警告—保险—相符—缓和—层别—
顺序—自动—复制。
流程程序图的分类
2、人型流程程序图
它是以人为研究对象,对他/她完成所有 工序的整个过程进行记录分析。
案例(发料):
工作内容:仓库发料员发料 开始:发料员坐在工作台旁 结束:发料员发完料坐到工作台旁
流程法的分析技巧
1个不忘:动作经济原则 4大原则:ECRS(取消、合并、重排、简化) 5个方面:加工、搬运、储存、检验、等待 5W1H技术:What/Where/When/Who/Why/How 6大步骤:选择、记录、分析、建立、实施、维护
案例:对制粒某机器作业率进行观测,估计该机器停机率为25%,需要观测
精度的绝对误差为0.01,可靠度为95%,求需观测的次数。(查表得正态分 布下的Z值为1.96)
答﹕P=0.25, 1-P=0.75, Z=1.96, E=0.01 由公式, n=P(1-P)Z2/E2 =0.25X0.75X1.962/0.012 =7203次
95.45%的可靠度,就是说实现预定 的抽样资料中有95.45%以上落入2 σ 的范围,仅有4.55%的误差。
抽查法的步骤
正态分布曲线
[P(1 P )] n
P-观测时间发生率 n-观测次数
抽查法的步骤
2、绝对精度和相对精度
使用抽查法时,会存在误差,所允许的误差用精确度来衡量。 精确度又分为绝对精确度E和相对精确度S
工业工程(IE)现场改善方法_图文(精)

2、依1.的记录,加以质问,寻求改善之地方
3、用以比较改善前及改善后之差异情形
基本符号和应用符号
①加工:表示直接改变制品的物理和化学性质或处于分解装配中。
A35第五道加工工序
A制品的第3道加工工序
以加工为主,同时检验
直径3/8吋
②搬运:表示材料从一处移到另一处。
或
③检验:进行数量或质量的检验。表示数量检验表示质量检验表示数量和质量同时检验,以质量检验为主
•在纸上采用适当的间隔分开人与机,作出垂线。最左方为工人操作时的动作单元及垂线,在此垂线上按所取的时间比例,由上向下记录工人每一动作单元所需时间。当工人操作时用实线(或其它方式表示,空闲用虚线(或其它方法表示,机器同样。•待人与机器的操作时间均已记录之后,在此图的下端将工人与机器的操作时间、空闲时间及每周期人工时数予以统计,供分析时参考。
联合作业分析研究对象:两个或两个以上操作者所进行的分析联合作业分析研究目的:发掘空闲与等待时间,使工作平衡,減少周期時間,获得最大的机器利用率。
联合作业分析研究工具:联合作业图
联合作业图的构成:表头、图表、统计。示例
联合作业图的特点:机器的作业情况画在图表的最左栏
操作者的作业情况画在图表的右栏
利用联合作业图分析的基本原则:
工作A工作A工作A
工作B
工作B
工作B
4h4h
4h
3h
3h
3h 1h
等待
8h 7h
使各个对象的工作进度协调,取消空闲和等待时间,缩短周期。
结论:
1消除工作中的等待,可以有效的缩短工作的周期时间
2如果有多项工作,则同时开展工作,周期时间最短
人机操作图的构成
•以适当的线段的长短代表时间比例。
3、用以比较改善前及改善后之差异情形
基本符号和应用符号
①加工:表示直接改变制品的物理和化学性质或处于分解装配中。
A35第五道加工工序
A制品的第3道加工工序
以加工为主,同时检验
直径3/8吋
②搬运:表示材料从一处移到另一处。
或
③检验:进行数量或质量的检验。表示数量检验表示质量检验表示数量和质量同时检验,以质量检验为主
•在纸上采用适当的间隔分开人与机,作出垂线。最左方为工人操作时的动作单元及垂线,在此垂线上按所取的时间比例,由上向下记录工人每一动作单元所需时间。当工人操作时用实线(或其它方式表示,空闲用虚线(或其它方法表示,机器同样。•待人与机器的操作时间均已记录之后,在此图的下端将工人与机器的操作时间、空闲时间及每周期人工时数予以统计,供分析时参考。
联合作业分析研究对象:两个或两个以上操作者所进行的分析联合作业分析研究目的:发掘空闲与等待时间,使工作平衡,減少周期時間,获得最大的机器利用率。
联合作业分析研究工具:联合作业图
联合作业图的构成:表头、图表、统计。示例
联合作业图的特点:机器的作业情况画在图表的最左栏
操作者的作业情况画在图表的右栏
利用联合作业图分析的基本原则:
工作A工作A工作A
工作B
工作B
工作B
4h4h
4h
3h
3h
3h 1h
等待
8h 7h
使各个对象的工作进度协调,取消空闲和等待时间,缩短周期。
结论:
1消除工作中的等待,可以有效的缩短工作的周期时间
2如果有多项工作,则同时开展工作,周期时间最短
人机操作图的构成
•以适当的线段的长短代表时间比例。
改善案例(八大浪费)

库存的危害: ☆ 额外的搬运储存成本 ☆ 造成空间浪费 ☆ 资金占用(利息及回报损失) ☆ 物料价值衰减 ☆ 造成呆料废料 ☆ 造成先进先出作业困难 ☆ 掩盖问题,造成假象
制造过多/过早
浪
费
制造过多/过早造成浪费: ☆ 造成在库 ☆ 计划外/提早消耗 ☆ 有变成滞留在库的风险 ☆ 降低应对变化的能力
浪
费
多余动作 增加强度降低效率
常见的12种浪费动作: ① 两手空闲 ② 单手空闲 ③ 作业动作停止 ④ 动作幅度过大 ⑤ 左右手交换 ⑥ 步行多
动作
⑦ 转身角度大 ⑧ 移动中变换动作 ⑨ 未掌握作业技巧 ⑩ 伸背动作 ⑾ 弯腰动作 ⑿ 重复/不必要动作
啟動開關獨立地防止地面易
01
備碰﹑觸發生工業安全﹐且
02
人須彎腰按動開關易疲勞
03
將啟動開關定置在控制面板上
04
保障安全且人不須彎腰按動開
05
關動作經濟化
06
IE手法三﹕防呆法
01
手動固定工件產生品質無
03
利用治具定位精度准﹐品質
02
保障﹑精度不准
04
高﹐效率得到提升
IE手法三﹕防呆法
01
準確掌握生產活動的實際狀態﹔ 盡快地發現浪費﹑不合理﹑不可靠的地方﹔ 對生產活動的改善和標準化進行系統的管理﹒
02
從來沒有這樣做過; 人家已經用過了不行; 這個方法已經用了10年; 我們現在已經做的夠好; 這個方法不適合我們; 老板不會感興趣﹔ 他們都說不可能﹔
4.現場IE活動的21種抵抗情緒(1)
個個方法行不通﹔ 沒有預算﹔ 那是件遙遠的事情﹔ 這事情超過我們的權限﹔ 不是我的工作﹔ 沒有時間﹔ 客戶不會接受﹔
制造过多/过早
浪
费
制造过多/过早造成浪费: ☆ 造成在库 ☆ 计划外/提早消耗 ☆ 有变成滞留在库的风险 ☆ 降低应对变化的能力
浪
费
多余动作 增加强度降低效率
常见的12种浪费动作: ① 两手空闲 ② 单手空闲 ③ 作业动作停止 ④ 动作幅度过大 ⑤ 左右手交换 ⑥ 步行多
动作
⑦ 转身角度大 ⑧ 移动中变换动作 ⑨ 未掌握作业技巧 ⑩ 伸背动作 ⑾ 弯腰动作 ⑿ 重复/不必要动作
啟動開關獨立地防止地面易
01
備碰﹑觸發生工業安全﹐且
02
人須彎腰按動開關易疲勞
03
將啟動開關定置在控制面板上
04
保障安全且人不須彎腰按動開
05
關動作經濟化
06
IE手法三﹕防呆法
01
手動固定工件產生品質無
03
利用治具定位精度准﹐品質
02
保障﹑精度不准
04
高﹐效率得到提升
IE手法三﹕防呆法
01
準確掌握生產活動的實際狀態﹔ 盡快地發現浪費﹑不合理﹑不可靠的地方﹔ 對生產活動的改善和標準化進行系統的管理﹒
02
從來沒有這樣做過; 人家已經用過了不行; 這個方法已經用了10年; 我們現在已經做的夠好; 這個方法不適合我們; 老板不會感興趣﹔ 他們都說不可能﹔
4.現場IE活動的21種抵抗情緒(1)
個個方法行不通﹔ 沒有預算﹔ 那是件遙遠的事情﹔ 這事情超過我們的權限﹔ 不是我的工作﹔ 沒有時間﹔ 客戶不會接受﹔
- 1、下载文档前请自行甄别文档内容的完整性,平台不提供额外的编辑、内容补充、找答案等附加服务。
- 2、"仅部分预览"的文档,不可在线预览部分如存在完整性等问题,可反馈申请退款(可完整预览的文档不适用该条件!)。
- 3、如文档侵犯您的权益,请联系客服反馈,我们会尽快为您处理(人工客服工作时间:9:00-18:30)。
精品课件
20
例20
利用重力和机械力取送材料 利用斜架缩短搬运的距离
60cm
精品课件
21
改善前 分别在两处盖章
改善后 只要盖1次章
动作多,盖章位置难确定
动作少,盖章位置易确定
精品课件
3
例4
双手同时作业
小零件
固定作业
改善前 左手拿零件 右手将零件固定 单手作业
小零件
改善后
左手拿零件并将之固定 右手同时进行相同作业
对称作业
精品课件
4
例5
双手同时作业
改善前 一件一件地检查
改善后 一次检查两件
进行组装零部件,作业者不弯
够得着的近处 ●减少屈身、弯腰等躯干动作
腰——高度约85cm
精品课件
8
例8
眼睛的移动 眼睛→颈部→躯干 ●尽可能将零件、工具 放在看得见的近处
精品课件
9
例9 减小移动距离 作业要求:将盖板固定在产品上
产品
传送带
人
人
改善前
盖板放在一边, 取到盖板后固定在产品上
改善后
盖板放在传送带上, 取到盖板后固定在产品上
手移动40cm
手移动15cm
精品课件
10
例10
工具
改变材料和工具的存放状态
弹
夹
簧
工件
改善前
改善后
工具未固定
工具固定
取放距离不定
便于作业
精品课件
11
例11 作业场所的钳子放置
钳子
改善前 钳子放在桌子上, 拿起后要在手里倒一下
握法要调整
支 架
改善后
钳子放在漏斗状支架中
免去握法调整
精品课件
12
例12 零件左右对称布置,便于双手作业
例1 将工具固定减少动作数量
作业要求: 将元件焊在基板上
元件 基板
焊料
电烙铁
改善前
左手 1.取材料 2.拿焊料 3.焊接 4.放焊料 5.材料入箱
右手 (等待) 拿电烙铁
放电烙铁 (等待)
改善后
左手 1.取材料 2.焊接 3.材料入箱
右手 拿焊料
拿焊料
每次都要取放电烙铁
将电烙铁固定在工作台前
精品课件
改善前
左手拿起螺栓, 右手将螺母拧上
改善后
左右手同时进行下述动作: 将螺栓放在固定夹具上, 再将螺母拧上
★利用夹具、导轨等限定运动路线 ★利用夹具、导轨等使定位更容易
精品课件
19
利用重力和其它力取送材料 例19
利用斜槽缩短完成品搬运的距离
60cm
20cm
作业台
工件箱
其它力:磁力、气压、油压、弹力、点滴装置
改善后
双手将垫圈插入专用夹具, 用手指使之弯折90°
双手协调动作
精品课件
7
例8
使用身体最佳部位
手的移动
手指→手→前臂→上臂
→肩→躯干→腰部
使作业位置高度达到最佳状态: ●缩短手臂的移动距离
★坐在椅子上,前臂水平伸出时 ●尽可能不动全臂
——高度约60cm
●只做凭前臂、手腕或手指即 可完成的动作
★臂肘防灾作业台上,眼睛平视 ●尽可能将零件、工具放在手
精品课件
5
例6 双手同时反向和对称移动
左手
非协调性动作 右手 左手 右手 左手
协调性动作 右手 左手 右手
左手 右手 左手 右手 左手 右手 左手 右手
材料工具不对称,肩部或躯干要移动, 易失去平衡,易疲劳
容易做到
不能做到
能,但不协调
精品课件
6
例7
使用双手可同时完成动作的夹具
ቤተ መጻሕፍቲ ባይዱ
改善前
左手拿垫圈, 右手握夹使之弯折90°
方形箱子
漏斗状/托盘状箱子
、、、、、、、、、
零件 过滤网 脏屑
精品课件
15
例15
漏斗形容器的利用
加压
轴套 方形容器
改善前 从箱子中取轴套, 移动距离长,不好拿
漏斗形容器出口
改善后 从漏斗形容器出口取轴套
取用方便
精品课件
16
例16 辅助工具的应用
小零件
小零件
手指
作业台
海绵垫
改善前
小零件放在作业台上, 用指尖拿起来
改善后 小零件放在海绵垫上
取用时小零件易滑掉
取用更容易
★工具、设备的把手做成易握、易抓的形状
精品课件
17
例17
辅助工具的应用
镊子
薄小零件
薄小零件
波纹板
改善前 用镊子把薄小零件夹起来
改善后 把薄小零件放在波纹板上
薄小零件易滑动
零件相对固定,夹取容易
精品课件
18
例18
固定夹具 需长时间固定对象物时,可利用固定夹具
1
例2
利用镜子减小视线移动角度
作业要求:用视波器检查元件
眼
眼
镜子
视
视
波
波
元件 器
器
改善前
1.将元件放置在检查台上 2.用眼检查事播器屏幕
改善后
1.将元件放置在检查台上 2.用眼检查镜中波形
颈部移动角度大
不用移动眼部
精品课件
2
例3 将两个以上动作合并 作业要求:盖日期印和合格印
定位
日合 期格
日合 期格
改善前
零件放置杂乱, 随即选择零件进行组装
改善后
零件有序、对称放置, 双手同时、按顺序工作
精品课件
13
例13
尽量缩小作业区域
传送带 工件 作业台
人
传送带 工件
人
★良好的照明有助于提高作业效率
★适当的通风、正常的温度和湿度可以减轻疲劳
★加强清扫和整理、合适的工作服可以避免工伤
精品课件
14
例14
容器和器具