气体热扩渗技术的发展现状
表面处理第七讲热扩渗
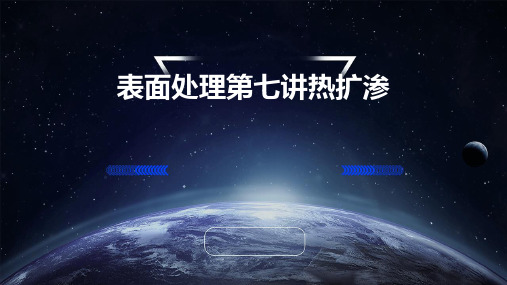
使用注意事项
选择合适的材料和工艺参数
在使用热扩渗技术时,需要根据工件的材料和性能要求选择合适的工 艺参数,以确保处理效果达到最佳。
控制环境污染
在热扩渗过程中,应采取有效的措施控制废气、废水和噪音等污染, 以符合环保要求。
专业操作和维护
热扩渗技术的操作和维护需要专业人员进行,以确保设备的正常运行 和使用效果。
安全操作规程
在热扩渗过程中,应遵守安全操作规程,防止发生意外事故。
05
热扩渗的未来发展
新材料的研究与应用
高性能陶瓷材料
研究具有优异耐热、耐磨、 耐腐蚀等性能的新型陶瓷 材料,拓展其在热扩渗领 域的应用。
纳米材料
利用纳米材料的特殊性质, 如高表面活性、高扩散性 等,提高热扩渗过程的效 率与效果。
复合材料
对基体材料的影响
热扩渗处理对基体材料的影响主要表现在对基体材料的硬 度和强度的提高。这是由于在热扩渗过程中,基体材料发 生塑性变形和相变,使材料的硬度和强度得到提高。
对基体材料的影响还包括对材料的热稳定性和抗疲劳性能 的提高。这些性能的提高可以提高零件的稳定性和可靠性 。
04
热扩渗的优缺点
优点
表面处理第七讲热扩渗
• 热扩渗原理 • 热扩渗工艺 • 热扩渗的效果与影响 • 热扩渗的优缺点 • 热扩渗的未来发展
01
热扩渗原理
热扩渗技术的定义
热扩渗技术是指在一定温度下,利用热激活的扩散作用,将一种或几种元素从固 体表面渗入内部,以改变材料表面的化学成分、组织结构和性能的一种表面处理 技术。
01
02
03
04
高效率
热扩渗技术能够在短时间内对 大量工件进行表面处理,提高
我国热处理的现状及先进热处理技术的发展和展望

我国热处理的现状及先进热处理技术的发展和展望热处理是指通过加热和冷却工艺,改变材料的组织结构和性能的一种工艺方法。
热处理广泛应用于钢铁、有色金属及其合金、塑料等材料的生产过程中,对提高材料的力学性能和使用寿命具有重要作用。
1.技术水平相对较低。
虽然我国热处理行业经过长期的发展已经取得了一定成就,但与国际先进水平相比还存在差距。
在技术设备和管理方面,我国热处理企业普遍存在缺乏投入和关注的问题。
2.信息化程度不高。
我国热处理行业在信息化方面的投入和应用较少,信息化程度相对较低,企业之间的信息共享和交流不够密切,影响了行业整体的发展。
3.环保意识不足。
我国热处理行业大部分企业在环境保护方面存在一定问题,热处理工艺中的废水、废气等排放未能得到有效处理和控制。
目前,我国热处理行业正积极推进先进热处理技术的发展,以提高产品质量、提升企业竞争力,并改善行业整体环境。
以下是我国先进热处理技术的发展和展望:1.先进的真空热处理技术。
真空热处理能够在无氧或低氧氛围中进行,减少材料表面氧化的问题,提高材料的耐腐蚀性和机械性能。
同时,真空热处理还能够实现材料的表面强化和改性,提高材料的使用寿命。
2.先进的低温热处理技术。
低温热处理技术主要包括低温渗碳、低温氮化等。
通过低温热处理可以实现材料的表面硬化和改性,提高材料的磨损和疲劳性能,同时减少材料的变形和裂纹。
3.先进的等离子体热处理技术。
等离子体热处理是一种通过等离子体化学反应实现材料表面改性的方法。
该技术具有温度低、速度快、效果好等优点,能够实现材料的表面强化和改性,提高材料的高温性能和抗腐蚀性。
展望未来,我国热处理行业在发展先进热处理技术的同时,应加强与国际接轨,提高品牌影响力和核心竞争力。
同时,还应注重培养热处理人才,推动热处理行业的技术创新和进步。
此外,还需要关注环保问题,推动热处理行业的绿色发展,减少对环境的影响。
总之,我国热处理行业在发展先进热处理技术方面还存在一定的差距,但随着技术的不断进步和应用的推广,相信我国热处理行业将会迎来更好的发展机遇。
2024年渗透汽化膜市场发展现状

2024年渗透汽化膜市场发展现状引言渗透汽化膜(Pervaporation Membrane)是一种高效的分离技术,广泛应用于化工、环保、食品等领域。
本文将探讨渗透汽化膜市场的发展现状,涵盖市场规模、应用领域、技术进展以及前景展望。
市场规模渗透汽化膜市场在过去几年间迅速发展,市场规模不断扩大。
据市场研究数据显示,2019年全球渗透汽化膜市场规模达到X亿美元。
预计到2025年,市场规模将达到Y亿美元,年复合增长率为Z%。
应用领域渗透汽化膜广泛应用于以下领域:化工行业化工行业是渗透汽化膜的主要应用领域之一。
渗透汽化膜在分离反应中可以实现高效的组分分离,特别适用于分离混合物中的有机溶剂。
它被广泛应用于石油化工、精细化工等领域。
渗透汽化膜在环保领域具有广阔的应用前景。
它可以有效地分离和回收有机物、水溶液中的重金属离子等。
通过应用渗透汽化膜技术,可以实现废水处理、有害气体治理等环保目标。
食品行业渗透汽化膜在食品行业中也得到了广泛应用。
它可以用于食品加工过程中的浓缩、提纯、除臭等操作。
渗透汽化膜可以更好地保留食品的口感、营养成分和风味,提高产品质量。
技术进展渗透汽化膜技术在过去几年间获得了显著的进展。
以下是几个重要的技术进展:新型材料研究人员不断开发新型渗透汽化膜材料,以提高膜的分离性能和稳定性。
聚酯、聚醚、聚酰胺等材料被广泛应用于渗透汽化膜制备中,提高了膜的渗透性和选择性。
膜制备技术膜制备技术是渗透汽化膜技术发展中的关键环节。
传统的制备方法包括溶液浸渍法、层析法等。
近年来,浸渍-交联法、层析-交联法等新的制备方法被提出,提高了膜的性能和稳定性。
多功能渗透汽化膜是近年来的研究热点。
多功能膜不仅具有渗透分离功能,还具有其他功能,如催化、吸附等。
这种多功能膜可以实现一步法的催化分离,提高分离效率和产品纯度。
前景展望渗透汽化膜市场未来有着广阔的发展前景。
随着全球化工、环保和食品行业的快速发展,对于高效分离技术的需求不断增加。
第五篇 热扩渗技术

名称 α相 γ相 含氮铁素体 含氮奥氏体 结构 体心 面心 面心 含氮 (wt%) 590℃:0.1 室温:0.004 ≤2.86 5.30~5.70 4.55~11.0 斜方 11.07~ 11.18 特性 有铁磁性 590℃共析转变, 慢冷: γ→α+ γ’ 铁磁相,硬度较高, 脆性小 铁磁相,650℃发生 共析: ε → γ+ γ’ 具有高脆性
热浸铝工艺影响因素
5.2 液体热扩渗
铝液成分、温度、时间 基体成分: ☆钢中C、Si含量增加,浸铝层厚度下降 ☆钢中的Cr、Mn元素,浸铝层厚度下降 ☆Si提高铝液流动性,降低合金层的厚度 和硬度
渗铝
渗铝的方法很多: 液态渗铝:工件浸入铝液 固体粉末渗铝:88%AlFe粉+10%石英粉 +2%NH4Cl2膏剂,涂在工件表面3~5mm厚, 在专用密封炉内加热,使铝渗入工件。 表面喷涂铝,再扩散退火渗铝:电弧喷涂 0.7~1.2mm铝层,在920~950℃进行4~6 小时扩散退火渗铝。
渗氮厚度与时间、温度的关系(95%N2+5%H2)
第五章 热扩渗技术
热扩渗工艺分类 按渗剂状态分:气体法、液体法、固体法 和等离子法。 按渗入元素分:渗碳、渗氮、渗硫、渗硼、 浸铝、浸锌、碳氮共渗、氮碳共渗等。 按工作温度分:高温( ≥910 ℃)、中温和 低温热(≤720 ℃)热扩渗。
5.1 气体热扩渗
第五章 热扩渗技术
热扩渗层的组织: 形成单相固溶体,如渗碳层中的α-Fe。 形成化合物,如渗氮层中的ε相(Fe2-3N), 渗硼层中的Fe2B等 。 形成固溶体和化合物的混合组织,并形成 梯度分布。
第五章 热扩渗技术
40CrNiMo钢 (a)渗碳:层深0.5mm 左右,表面碳势0.9 %。 表层为高碳马氏体+ 颗粒状碳化物+ 残留 奥氏体;心部为中碳 马氏体。 (b)渗氮:表层碳氮 化合物+ 含氮马氏体 + 残留奥氏体,心部 是回火索氏体。
热扩散的发展趋势
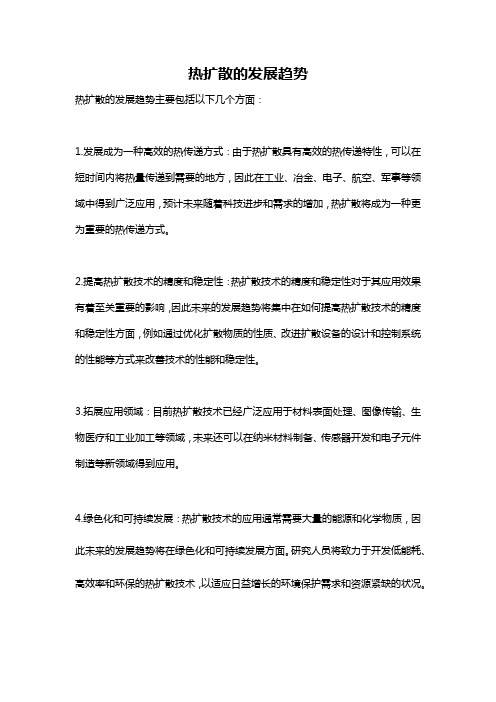
热扩散的发展趋势
热扩散的发展趋势主要包括以下几个方面:
1.发展成为一种高效的热传递方式:由于热扩散具有高效的热传递特性,可以在短时间内将热量传递到需要的地方,因此在工业、冶金、电子、航空、军事等领域中得到广泛应用,预计未来随着科技进步和需求的增加,热扩散将成为一种更为重要的热传递方式。
2.提高热扩散技术的精度和稳定性:热扩散技术的精度和稳定性对于其应用效果有着至关重要的影响,因此未来的发展趋势将集中在如何提高热扩散技术的精度和稳定性方面,例如通过优化扩散物质的性质、改进扩散设备的设计和控制系统的性能等方式来改善技术的性能和稳定性。
3.拓展应用领域:目前热扩散技术已经广泛应用于材料表面处理、图像传输、生物医疗和工业加工等领域,未来还可以在纳米材料制备、传感器开发和电子元件制造等新领域得到应用。
4.绿色化和可持续发展:热扩散技术的应用通常需要大量的能源和化学物质,因此未来的发展趋势将在绿色化和可持续发展方面。
研究人员将致力于开发低能耗、高效率和环保的热扩散技术,以适应日益增长的环境保护需求和资源紧缺的状况。
我国离子化学热处理技术的现状与展望概要

我国离子化学热处理技术的现状与展望一、概述离子化学热处理是置于低压容器内的工件,在辉光放电的作用下,带电离子轰击工件表面,使其温度升高,实现所需原子渗扩进入工件表层的一种化学热处理方法。
与常规化学热处理相比,离子化学热处理具有许多突出的特点:渗层质量好、工艺可控性强、工件变形小、处理温度范围宽、易于实现局部防渗;渗速快、生产周期短,可节约时间15%~50%;热效率高、工作气体耗量少,一般可节能30%以上、省气70%~90%;无烟雾、废气污染,处理后工件和夹具洁净,工作环境好;柔性好,便于生产线组合,实现自动化。
正因为如此,离子化学热处理一直是近几十年来热处理技术发展的一个热点,并在不太长的时间内迅速得到了推广应用。
20世纪30年代,德国学者B.Berghous首先发现了在辉光放电电场(即等离子区进行表面硬化的优越性,并采用此工艺进行了渗氮处理,取得了第一个离子渗氮发明专利;40年代,该技术在军事领域获得应用;50年代后,经原西德学者的进一步研究,KlöcknerIonon 公司(原西德于1967年实现工业应用。
60年代末期,我国开始了离子渗氮技术的研究,内容涉及工艺、设备、性能及基础理论等广泛的领域,并实现了试制设备到生产应用设备的过渡,到1980年,我国已拥有离子渗氮炉400余台,居世界第一。
目前,我国离子渗氮炉的保有量已超过1700台,并仍以每年60~80台的速度递增。
总的来讲,在离子化学热处理领域,我国已跻身于国际先进水平行列。
涉及到离子化学热处理研究开发的内容较多,既有基础理论、组织和性能,也有设备开发;在工艺上的内容更多,几乎化学热处理中所需渗入的元素,都可在离子轰击条件下实现。
世界上不同的国家根据所处的工业状况和投资背景,在离子化学热处理的各个方面做了大量的工作。
据资料统计,前苏联、中国、美国、英国、德国、日本和法国的研究工作处于领先地位。
特别是美国和英国在离子渗碳、钛合金离子渗氮研究方而一路领先;前苏联在离子渗硼方面尤为突出;而我国在离子多元共渗、离子渗金属方面处于领先地位。
热扩渗技术

热扩渗技术
热扩渗是用加热扩散的方式使欲渗金属或非金属元素渗入模具 的表面,形成表面合金层,从而提高模具表面的耐磨性、耐腐蚀性 以及疲劳强度等性能。热扩渗技术又称为热渗镀技术或化学热处理 技术,其突出特点是扩渗层与基材之间是靠形成合金来结合的(即 所谓冶金结合),具有很高的结合强度,这是其他涂层方法如电镀、 喷镀或化学镀、甚至物理气相沉积技术所无法比拟的。
热扩渗可分为固体热扩渗、液体热扩渗、气体热扩渗。常用 的热扩渗技术有渗碳、渗氮、碳氮共渗等。
2020年12月29日星期二
返回目录
2020年12月29日星期二
1.1 固体热扩渗工艺及应用
1.固体渗碳 固体渗碳是将工件和固体渗碳剂装入渗碳箱中,用盖子和耐火泥封
好,然后放在炉中加热至900~950 ℃,保温足够长时间后,得到一定厚 度的渗碳层。固体渗碳剂通常2CO3)的混合物。木炭提供固体渗碳所需要的活性碳原子, 碳酸盐起催化作用。 2.固体渗硼
工件在密封的渗碳炉中,加热到900~950 ℃后,向炉内滴入易分解 的有机液体(如煤油、苯、甲醇等),或直接通入渗碳气体(如煤气、 石油液化气等),经一系列反应后产生活性碳原子,使钢件表面渗碳。
气体渗碳的特点是生产效率高,劳动条件好,渗碳过程中可以控制, 渗碳层的质量和机械性能较好。 2)气体渗碳后的热处理
固体渗硼可在650~1000 ℃内进行,常用于850~950 ℃,可保温 2~6 h,不同钢种可获得50~200 m深的固体渗硼层。固体渗硼工艺应用 较广,适用于几何形状复杂,包括带有小孔、螺纹和盲孔的零件。中、 小零件的固体渗硼采用粒状和粉末状介质,大件及其局部的渗硼采用膏 剂。这些介质均由供硼剂(B4C、B-Fe、非晶态硼粉)、催渗剂(KBF4、 NH4Cl、NH4F等)以及调节活性、支承工件的填料(Al2O3、SiC、SiO2)组 成。 3.固体渗铬
第10章 热扩渗技术-用

能进行热扩渗的材料包括:碳、氮、硼、锌、铝、铬、钒、铌、钛、硅、 硫等和这些元素的多元共渗。
10.1 热扩渗的基本原理 及分类
一、热扩渗层形成的基本条件
渗入元素的原子存在于扩渗层的形式:
与基体金属形成:固溶体或金属间化合物层,或固溶体+化 合物的复合层
形成渗层基本条件:
1.渗入元素必须能够与基体金属形成固溶体或金属间化合物。 2.欲渗元素与基材之间必须有直接接触。 3.被渗元素在基体金属中要有一定的渗入速度。 4.(对靠化学反应提供活性原子的热扩渗工艺)该反应必须满 足热力学条件。 (产生活性原子;反应平衡常数>1%。)
三、热扩渗速度的影响因素
热扩渗层的形成速度是由形成渗层的三个过程中最慢的一个来制约。 在初始阶段:化学介质分解化学反应速度 在中后期:扩散速度 能影响化学反应速度和扩散速度的因素,均将影响热扩渗层的形成速 度:增加反应物浓度、提高反应温度、加入适当催化剂等均能使反应 速度成倍提高。在扩散过程中,升高温度就更有效。
基材心部
10.1.2 热扩渗工艺的分类
按热扩渗温度:高温(高于910℃)、中温和低温(低于720℃)热扩渗 按渗入元素:非金属元素热扩渗、金属元素热扩渗、金属一非金属元素多元共渗、扩
散退火(均匀化退火)。
按渗剂在工作温度下物质状态:
气体热扩渗 液体热扩渗 固体热扩渗 等离子体热扩渗 复合热扩渗
热浸镀:
常见:钢铁制品的热浸锌、热浸铝、热浸锡等。 2. 特点:生产效率高。渗层厚度不易均匀,且只适于浸 渗熔点较低的金属。
1.
10.2.1
热浸镀原理
热浸镀时,被镀的基体材料与熔融金属的接触面上发生界面 反应,是一个冶金过程,按相应的相图形成不同相构成的合 金层,所以热浸镀层是由合金层和浸镀金属构成的复合镀层。 钢铁的热浸镀过程
国产燃料电池用气体扩散层材料关键技术研究及产业化
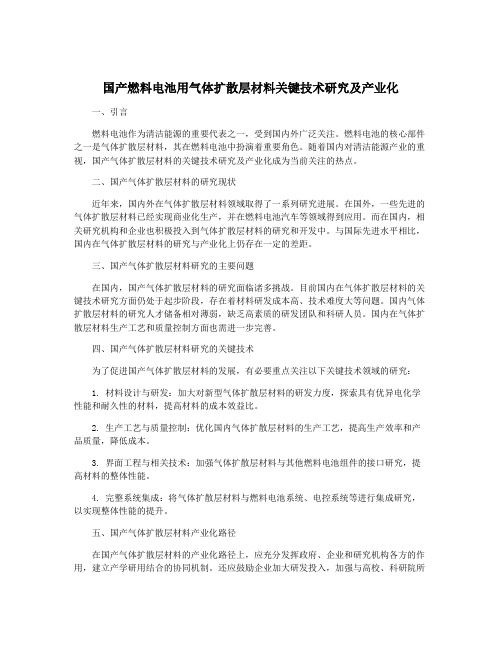
国产燃料电池用气体扩散层材料关键技术研究及产业化一、引言燃料电池作为清洁能源的重要代表之一,受到国内外广泛关注。
燃料电池的核心部件之一是气体扩散层材料,其在燃料电池中扮演着重要角色。
随着国内对清洁能源产业的重视,国产气体扩散层材料的关键技术研究及产业化成为当前关注的热点。
二、国产气体扩散层材料的研究现状近年来,国内外在气体扩散层材料领域取得了一系列研究进展。
在国外,一些先进的气体扩散层材料已经实现商业化生产,并在燃料电池汽车等领域得到应用。
而在国内,相关研究机构和企业也积极投入到气体扩散层材料的研究和开发中。
与国际先进水平相比,国内在气体扩散层材料的研究与产业化上仍存在一定的差距。
三、国产气体扩散层材料研究的主要问题在国内,国产气体扩散层材料的研究面临诸多挑战。
目前国内在气体扩散层材料的关键技术研究方面仍处于起步阶段,存在着材料研发成本高、技术难度大等问题。
国内气体扩散层材料的研究人才储备相对薄弱,缺乏高素质的研发团队和科研人员。
国内在气体扩散层材料生产工艺和质量控制方面也需进一步完善。
四、国产气体扩散层材料研究的关键技术为了促进国产气体扩散层材料的发展,有必要重点关注以下关键技术领域的研究:1. 材料设计与研发:加大对新型气体扩散层材料的研发力度,探索具有优异电化学性能和耐久性的材料,提高材料的成本效益比。
2. 生产工艺与质量控制:优化国内气体扩散层材料的生产工艺,提高生产效率和产品质量,降低成本。
3. 界面工程与相关技术:加强气体扩散层材料与其他燃料电池组件的接口研究,提高材料的整体性能。
4. 完整系统集成:将气体扩散层材料与燃料电池系统、电控系统等进行集成研究,以实现整体性能的提升。
五、国产气体扩散层材料产业化路径在国产气体扩散层材料的产业化路径上,应充分发挥政府、企业和研究机构各方的作用,建立产学研用结合的协同机制。
还应鼓励企业加大研发投入,加强与高校、科研院所的合作,培育和引进高层次的研发人才。
气体渗透膜的研究和工业应用现状
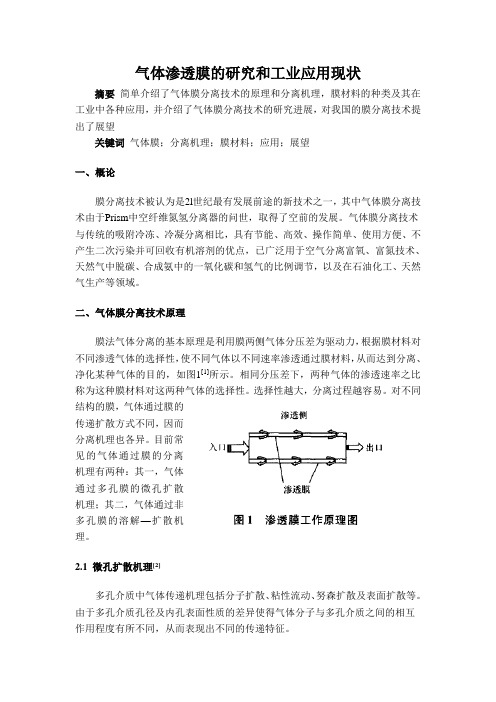
气体渗透膜的研究和工业应用现状摘要简单介绍了气体膜分离技术的原理和分离机理,膜材料的种类及其在工业中各种应用,并介绍了气体膜分离技术的研究进展,对我国的膜分离技术提出了展望关键词气体膜;分离机理;膜材料;应用;展望一、概论膜分离技术被认为是2l世纪最有发展前途的新技术之一,其中气体膜分离技术由于Prism中空纤维氮氢分离器的问世,取得了空前的发展。
气体膜分离技术与传统的吸附冷冻、冷凝分离相比,具有节能、高效、操作简单、使用方便、不产生二次污染并可回收有机溶剂的优点,已广泛用于空气分离富氧、富氮技术、天然气中脱碳、合成氨中的一氧化碳和氢气的比例调节,以及在石油化工、天然气生产等领域。
二、气体膜分离技术原理膜法气体分离的基本原理是利用膜两侧气体分压差为驱动力,根据膜材料对不同渗透气体的选择性,使不同气体以不同速率渗透通过膜材料,从而达到分离、净化某种气体的目的,如图1[1]所示。
相同分压差下,两种气体的渗透速率之比称为这种膜材料对这两种气体的选择性。
选择性越大,分离过程越容易。
对不同结构的膜,气体通过膜的传递扩散方式不同,因而分离机理也各异。
目前常见的气体通过膜的分离机理有两种:其一,气体通过多孔膜的微孔扩散机理;其二,气体通过非多孔膜的溶解—扩散机理。
2.1 微孔扩散机理[2]多孔介质中气体传递机理包括分子扩散、粘性流动、努森扩散及表面扩散等。
由于多孔介质孔径及内孔表面性质的差异使得气体分子与多孔介质之间的相互作用程度有所不同,从而表现出不同的传递特征。
混合气体通过多孔膜的传递过程应以分子流为主,其分离过程应尽可能满足下述条件:1,多孔膜的微孔孔径必须小于混合气体中各组分的平均自由程,一般要求多孔膜的孔径在(50~300)×10 -10m;2,混合气体的温度应足够高,压力尽可能低。
高温、低压都可提高气体分子的平均自由程,同时还可避免表面流动和吸附现象发生。
2.2 溶解—扩散机理[2]气体通过非多孔膜的传递过程一般用溶解一扩散机理来解释,气体透过膜的过程可分为三步:1.气体在膜的上游侧表面吸附溶解,是吸着过程;2.吸附溶解在膜上游侧表面的气体在浓度差的推动下扩散透过膜,是扩散过程;3.膜下游侧表面的气体解吸,是解吸过程。
气体热扩渗技术的发展现状
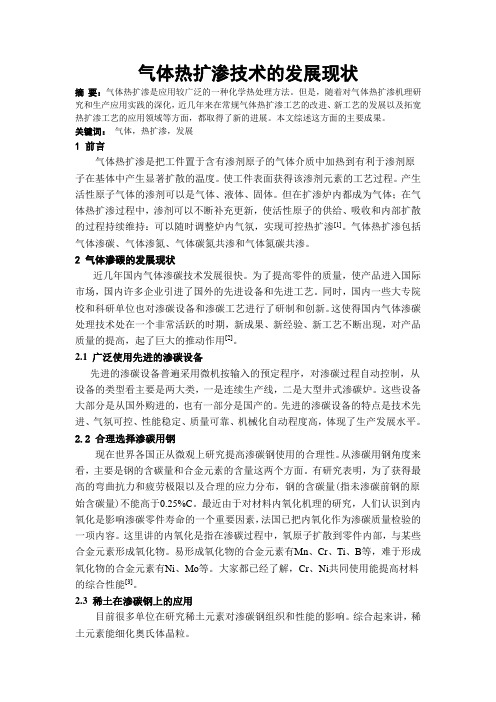
气体热扩渗技术的发展现状摘要:气体热扩渗是应用较广泛的一种化学热处理方法。
但是,随着对气体热扩渗机理研究和生产应用实践的深化,近几年来在常规气体热扩渗工艺的改进、新工艺的发展以及拓宽热扩渗工艺的应用领域等方面,都取得了新的进展。
本文综述这方面的主要成果。
关键词:气体,热扩渗,发展1 前言气体热扩渗是把工件置于含有渗剂原子的气体介质中加热到有利于渗剂原子在基体中产生显著扩散的温度。
使工件表面获得该渗剂元素的工艺过程。
产生活性原子气体的渗剂可以是气体、液体、固体。
但在扩渗炉内都成为气体;在气体热扩渗过程中,渗剂可以不断补充更新,使活性原子的供给、吸收和内部扩散的过程持续维持:可以随时调整炉内气氛,实现可控热扩渗[1]。
气体热扩渗包括气体渗碳、气体渗氮、气体碳氮共渗和气体氮碳共渗。
2 气体渗碳的发展现状近几年国内气体渗碳技术发展很快。
为了提高零件的质量,使产品进入国际市场,国内许多企业引进了国外的先进设备和先进工艺。
同时,国内一些大专院校和科研单位也对渗碳设备和渗碳工艺进行了研制和创新。
这使得国内气体渗碳处理技术处在一个非常活跃的时期,新成果、新经验、新工艺不断出现,对产品质量的提高,起了巨大的推动作用[2]。
2.1 广泛使用先进的渗碳设备先进的渗碳设备普遍采用微机按输入的预定程序,对渗碳过程自动控制,从设备的类型看主要是两大类,一是连续生产线,二是大型井式渗碳炉。
这些设备大部分是从国外购进的,也有一部分是国产的。
先进的渗碳设备的特点是技术先进、气氛可控、性能稳定、质量可靠、机械化自动程度高,体现了生产发展水平。
2.2 合理选择渗碳用钢现在世界各国正从微观上研究提高渗碳钢使用的合理性。
从渗碳用钢角度来看,主要是钢的含碳量和合金元素的含量这两个方面。
有研究表明,为了获得最高的弯曲抗力和疲劳极限以及合理的应力分布,钢的含碳量(指未渗碳前钢的原始含碳量)不能高于0.25%C。
最近由于对材料内氧化机理的研究,人们认识到内氧化是影响渗碳零件寿命的一个重要因素,法国已把内氧化作为渗碳质量检验的一项内容。
气相渗铝现状研究报告

一、引言气相渗铝技术作为一种表面改性方法,广泛应用于金属材料的表面处理中,旨在提高其耐腐蚀性、耐磨损性和抗氧化性。
随着航空、汽车及能源等行业对材料性能要求的不断提升,气相渗铝工艺的研究与开发受到了极大关注。
本报告旨在概述当前气相渗铝技术的发展状况,分析其技术特点,探讨现有问题,并对未来的研究方向提出展望。
二、气相渗铝技术概述气相渗铝是通过将铝蒸气在高温下扩散渗入基体材料表层形成铝的富集层,从而改善材料表面的综合性能。
目前,常见的气相渗铝方法主要包括包裹法、气体运输法和真空蒸发沉积法等。
这些方法各有优势,但亦存在不同程度的局限性。
三、技术发展现状近年来,气相渗铝技术在设备、工艺优化以及应用范围拓展等方面取得了显著进展。
一方面,通过引入计算机控制系统,实现了渗铝过程的自动化和精确控制;另一方面,新型渗铝剂的研发降低了环境污染并提高了工艺安全性。
此外,针对特定材料和应用条件的定制化渗铝工艺研究,使得该技术更加灵活多样。
四、存在问题与挑战尽管气相渗铝技术已取得诸多成就,但仍面临以下挑战:1) 如何进一步提高渗层质量与均匀性;2) 降低高能耗和生产成本;3) 解决传统渗铝过程中可能产生的有害气体排放问题;4) 扩大其在极端环境下的应用范围,如高温、高压和强腐蚀条件。
五、未来发展方向面对现有问题,未来的研究可能会集中在以下几个方面:1) 开发新型高效环保渗铝剂,减少环境负担;2) 利用纳米技术改善渗层微观结构,提升材料性能;3) 探索低温渗铝工艺以节能降耗;4) 加强渗铝层的耐腐蚀和耐氧化机理研究,为工艺改进提供理论基础;5) 结合现代检测技术,实现渗铝过程的实时监控和质量控制。
六、结论气相渗铝技术作为一项重要的表面工程手段,在提升材料性能方面展现出巨大的潜力。
现阶段,该技术已在多个领域得到实际应用,并不断优化升级。
然而,仍需针对存在的技术难题进行深入研究,尤其要注重环保和可持续性。
展望未来,随着材料科学、化学工程及相关技术的交叉融合,气相渗铝技术有望实现更为广泛的应用,并为高性能材料的研发与制造提供有力支撑。
2023年扩散曝气设备行业市场发展现状

2023年扩散曝气设备行业市场发展现状1. 市场规模巨大,市场潜力巨大扩散曝气设备产业是水处理行业中不可或缺的重要部分。
随着全球水资源的日益短缺和市政给排水压力的增大,以及国家在环保方面的加大力度,扩散曝气设备行业市场前景非常广阔。
据不完全统计,全球扩散曝气设备市场规模达到120亿美元,且未来市场潜力巨大,特别是在中国等发展中国家。
2. 技术水平与产品质量有待提高当前,国内扩散曝气设备行业中,生产企业众多,技术水平参差不齐,大多采用传统生产工艺,产品质量难以保证。
市场上很多低成本、低质量的扩散曝气设备也在充斥市场,这不仅会影响消费者的购买满意度,同时也会影响扩散曝气设备行业整体形象。
3. 行业竞争日趋激烈随着扩散曝气设备行业市场的发展,行业竞争也日趋激烈。
除了企业之间的竞争外,新技术、新工艺不断涌现也加剧了竞争的程度。
加之国际经济形势的影响,市场价格也呈现下降趋势。
因此,各生产企业应在保持产品质量同时,注重创新,提高技术水平,不断发展新产品,以保持市场竞争优势。
4. 地域分布差异大扩散曝气设备市场的地域分布差异较大。
目前,国内扩散曝气设备行业主要集中在东南沿海地区,主要是由于该地区科技实力、工程项目的密度和水资源的状况相对较好。
而在西部地区和中西部地区,市场的开发还具有相当的潜力。
5. 公司品牌与厂家信誉逐渐成为影响购买的重要因素扩散曝气设备行业市场竞争激烈,品牌和信誉成为消费者选择的重要条件之一。
具备良好的品牌形象和企业信誉的企业在市场中有较强的竞争力。
消费者在购买扩散曝气设备时,常常会给予这些因素更多的考虑。
6. 环保标准的推行将推动市场进一步发展随着环保标准的不断提高和市场监管的加强,国家对于扩散曝气设备行业的要求也越来越高。
在此情况下,企业应适应环保标准的不断提高,加强技术创新和产品研发,生产环保、绿色、节能的产品和设备,以满足市场需求和政策要求,推动行业市场进一步发展。
气相渗铝工艺发展现状

气相渗铝工艺发展现状
气相渗铝工艺是一种表面处理技术,通过在铝材表面形成一层相对厚度较薄的氧化铝层,以提高铝材的耐蚀性、耐磨性和耐热性。
目前,气相渗铝工艺已经有了较大的发展和应用。
以下是该工艺的一些发展现状:
1. 工艺改进:随着技术的不断发展,气相渗铝工艺的操作程序不断改进,使得工艺变得更加稳定和高效。
例如,利用热电偶和气体控制系统来精确控制渗铝过程中的温度和气体流量,以获得更好的渗铝效果。
2. 材料研究:为了改善铝材的性能,研究人员还在不断探索新的渗铝材料和工艺。
例如,通过改变渗铝时使用的气氛成分,可以实现在铝表面形成不同的氧化物层,从而改变材料的性能。
3. 应用领域扩展:气相渗铝工艺已经在航空、汽车、船舶、电子等领域得到了广泛应用。
例如,在航空领域,气相渗铝可以提高铝件的耐磨性和耐腐蚀性,延长其使用寿命;在电子领域,气相渗铝可以提高铝基电路板的导热性能。
4. 环境友好型工艺:相比于传统的电镀等表面处理技术,气相渗铝工艺更加环境友好,因为在渗铝过程中无需使用有害的金属离子和有机溶剂等化学品。
这使得气相渗铝工艺在可持续发展的背景下变得更加受欢迎。
总的来说,气相渗铝工艺在改进工艺、材料研究、应用领域拓展和环境友好型方面都取得了一定的发展。
随着技术的进一步成熟和应用广泛,气相渗铝工艺有望在更多领域得到推广和应用。
气体热扩渗的原理特点应用
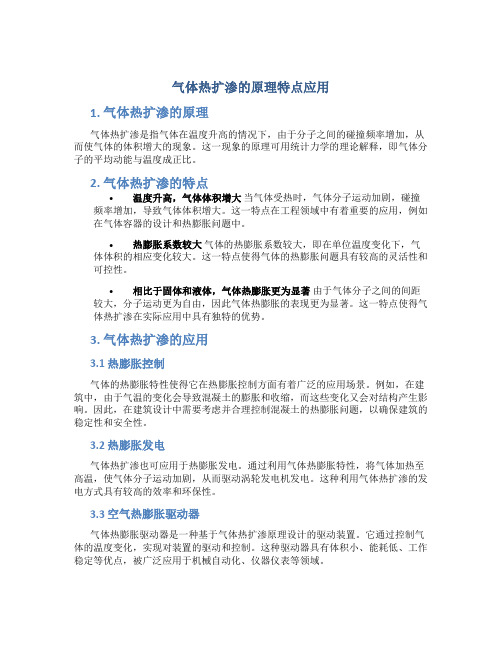
气体热扩渗的原理特点应用1. 气体热扩渗的原理气体热扩渗是指气体在温度升高的情况下,由于分子之间的碰撞频率增加,从而使气体的体积增大的现象。
这一现象的原理可用统计力学的理论解释,即气体分子的平均动能与温度成正比。
2. 气体热扩渗的特点•温度升高,气体体积增大当气体受热时,气体分子运动加剧,碰撞频率增加,导致气体体积增大。
这一特点在工程领域中有着重要的应用,例如在气体容器的设计和热膨胀问题中。
•热膨胀系数较大气体的热膨胀系数较大,即在单位温度变化下,气体体积的相应变化较大。
这一特点使得气体的热膨胀问题具有较高的灵活性和可控性。
•相比于固体和液体,气体热膨胀更为显著由于气体分子之间的间距较大,分子运动更为自由,因此气体热膨胀的表现更为显著。
这一特点使得气体热扩渗在实际应用中具有独特的优势。
3. 气体热扩渗的应用3.1 热膨胀控制气体的热膨胀特性使得它在热膨胀控制方面有着广泛的应用场景。
例如,在建筑中,由于气温的变化会导致混凝土的膨胀和收缩,而这些变化又会对结构产生影响。
因此,在建筑设计中需要考虑并合理控制混凝土的热膨胀问题,以确保建筑的稳定性和安全性。
3.2 热膨胀发电气体热扩渗也可应用于热膨胀发电。
通过利用气体热膨胀特性,将气体加热至高温,使气体分子运动加剧,从而驱动涡轮发电机发电。
这种利用气体热扩渗的发电方式具有较高的效率和环保性。
3.3 空气热膨胀驱动器气体热膨胀驱动器是一种基于气体热扩渗原理设计的驱动装置。
它通过控制气体的温度变化,实现对装置的驱动和控制。
这种驱动器具有体积小、能耗低、工作稳定等优点,被广泛应用于机械自动化、仪器仪表等领域。
3.4 热膨胀传感器基于气体热扩渗原理设计的热膨胀传感器在工业自动化中有着重要的应用。
这种传感器通过检测气体的热膨胀变化,实现对温度和压力等指标的测量。
这种传感器具有灵敏度高、响应快等优点,在自动化生产过程中起到了至关重要的作用。
4. 总结气体热扩渗作为气体物理学的重要内容之一,具有独特的原理特点和广泛的应用场景。
最新的供气供热技术进展和创新趋势
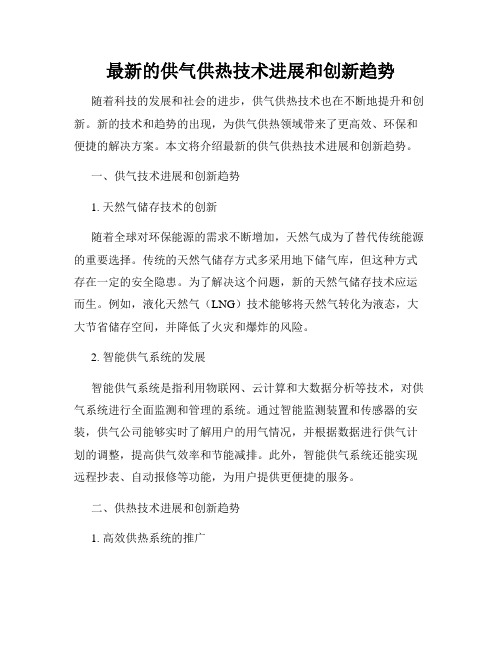
最新的供气供热技术进展和创新趋势随着科技的发展和社会的进步,供气供热技术也在不断地提升和创新。
新的技术和趋势的出现,为供气供热领域带来了更高效、环保和便捷的解决方案。
本文将介绍最新的供气供热技术进展和创新趋势。
一、供气技术进展和创新趋势1. 天然气储存技术的创新随着全球对环保能源的需求不断增加,天然气成为了替代传统能源的重要选择。
传统的天然气储存方式多采用地下储气库,但这种方式存在一定的安全隐患。
为了解决这个问题,新的天然气储存技术应运而生。
例如,液化天然气(LNG)技术能够将天然气转化为液态,大大节省储存空间,并降低了火灾和爆炸的风险。
2. 智能供气系统的发展智能供气系统是指利用物联网、云计算和大数据分析等技术,对供气系统进行全面监测和管理的系统。
通过智能监测装置和传感器的安装,供气公司能够实时了解用户的用气情况,并根据数据进行供气计划的调整,提高供气效率和节能减排。
此外,智能供气系统还能实现远程抄表、自动报修等功能,为用户提供更便捷的服务。
二、供热技术进展和创新趋势1. 高效供热系统的推广传统的供热系统存在热量损失高、运行效率低的问题。
为了提高供热系统的效率,新的供热技术逐渐被推广。
例如,采用地源热泵和空气源热泵技术,可以利用地下和空气中的热能进行供热,达到更高的效果。
另外,采用分布式供热系统也能够减少输送和散热损失,提高供热效率。
2. 温控技术的创新温控技术是指通过智能温控设备对供热系统进行调节和控制的技术。
传统的温控设备多采用手动调节,不仅不方便,而且容易造成能源的浪费。
新的温控技术通过智能温控器和传感器的配合,可以根据室内温度和用户需求自动调节供热系统的工作状态,达到更舒适和节能的效果。
此外,温控技术还可以与智能家居系统和手机APP相结合,实现远程控制和智能化管理。
三、供气供热技术的未来发展随着科技的不断进步,供气供热技术还将不断发展和创新。
以下是未来发展的几个趋势:1. 新能源的应用:随着新能源技术的进步,太阳能、风能等可再生能源有望广泛应用于供气供热系统,实现更清洁和可持续发展。
气体扩散层行业指标
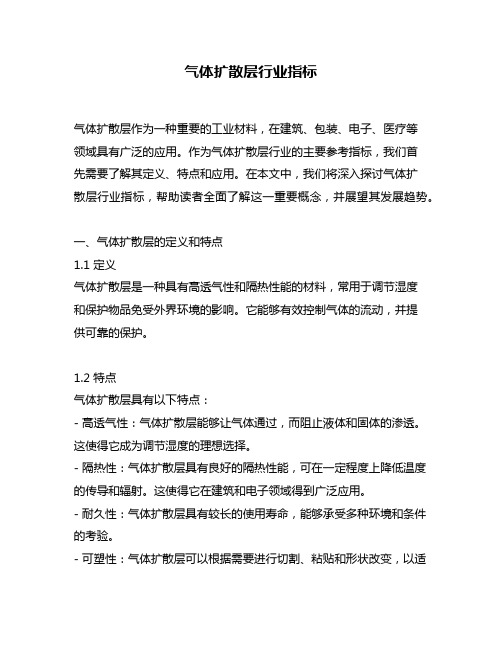
气体扩散层行业指标气体扩散层作为一种重要的工业材料,在建筑、包装、电子、医疗等领域具有广泛的应用。
作为气体扩散层行业的主要参考指标,我们首先需要了解其定义、特点和应用。
在本文中,我们将深入探讨气体扩散层行业指标,帮助读者全面了解这一重要概念,并展望其发展趋势。
一、气体扩散层的定义和特点1.1 定义气体扩散层是一种具有高透气性和隔热性能的材料,常用于调节湿度和保护物品免受外界环境的影响。
它能够有效控制气体的流动,并提供可靠的保护。
1.2 特点气体扩散层具有以下特点:- 高透气性:气体扩散层能够让气体通过,而阻止液体和固体的渗透。
这使得它成为调节湿度的理想选择。
- 隔热性:气体扩散层具有良好的隔热性能,可在一定程度上降低温度的传导和辐射。
这使得它在建筑和电子领域得到广泛应用。
- 耐久性:气体扩散层具有较长的使用寿命,能够承受多种环境和条件的考验。
- 可塑性:气体扩散层可以根据需要进行切割、粘贴和形状改变,以适应不同的应用场景。
二、气体扩散层行业指标为了评估气体扩散层的性能和质量,行业内制定了一系列指标来对其进行衡量。
以下是其中几个重要的指标:2.1 透湿度透湿度是指气体扩散层在单位时间内透过湿度差的能力。
它可以衡量气体扩散层的调湿性能,越高的透湿度意味着更好的调湿效果。
2.2 密度密度是指单位体积内气体扩散层包含的质量。
较低的密度意味着更轻薄、更透气的气体扩散层,适用于需求更高透气性的场景。
2.3 密度波动密度波动是指气体扩散层内部质量分布的均匀性。
较小的密度波动意味着气体扩散层内部结构更加均一,性能更为稳定可靠。
2.4 抗拉强度抗拉强度是指气体扩散层在受力情况下的抵抗能力。
较高的抗拉强度意味着气体扩散层具有更好的耐久性和使用寿命。
这些指标不仅能够评估气体扩散层的质量和性能,也为相关行业提供了参考依据。
通过对这些指标的综合评估,可以选择出适合不同应用场景的气体扩散层产品,提高工艺效率和产品质量。
三、气体扩散层行业的发展趋势随着科技的进步和人们对环境保护的不断重视,气体扩散层行业也在不断发展和创新。
- 1、下载文档前请自行甄别文档内容的完整性,平台不提供额外的编辑、内容补充、找答案等附加服务。
- 2、"仅部分预览"的文档,不可在线预览部分如存在完整性等问题,可反馈申请退款(可完整预览的文档不适用该条件!)。
- 3、如文档侵犯您的权益,请联系客服反馈,我们会尽快为您处理(人工客服工作时间:9:00-18:30)。
气体热扩渗技术的发展现状
摘要:气体热扩渗是应用较广泛的一种化学热处理方法。
但是,随着对气体热扩渗机理研究和生产应用实践的深化,近几年来在常规气体热扩渗工艺的改进、新工艺的发展以及拓宽热扩渗工艺的应用领域等方面,都取得了新的进展。
本文综述这方面的主要成果。
关键词:气体,热扩渗,发展
1前言
气体热扩渗是把工件置于含有渗剂原子的气体介质中加热到有利于渗剂原子在基体中产生显著扩散的温度。
使工件表面获得该渗剂元素的工艺过程。
产生活性原子气体的渗剂可以是气体、液体、固体。
但在扩渗炉内都成为气体;在气体热扩渗过程中,渗剂可以不断补充更新,使活性原子的供给、吸收和内部扩散的过程持续维持:可以随时调整炉内气氛,实现可控热扩渗[1]。
气体热扩渗包括气体渗碳、气体渗氮、气体碳氮共渗和气体氮碳共渗。
2气体渗碳的发展现状
近几年国内气体渗碳技术发展很快。
为了提高零件的质量,使产品进入国际市场,国内许多企业引进了国外的先进设备和先进工艺。
同时,国内一些大专院校和科研单位也对渗碳设备和渗碳工艺进行了研制和创新。
这使得国内气体渗碳处理技术处在一个非常活跃的时期,新成果、新经验、新工艺不断出现,对产品质量的提高,起了巨大的推动作用[2]。
2.1广泛使用先进的渗碳设备
先进的渗碳设备普遍采用微机按输入的预定程序,对渗碳过程自动控制,从设备的类型看主要是两大类,一是连续生产线,二是大型井式渗碳炉。
这些设备大部分是从国外购进的,也有一部分是国产的。
先进的渗碳设备的特点是技术先进、气氛可控、性能稳定、质量可靠、机械化自动程度高,体现了生产发展水平。
2.2合理选择渗碳用钢
现在世界各国正从微观上研究提高渗碳钢使用的合理性。
从渗碳用钢角度来看,主要是钢的含碳量和合金元素的含量这两个方面。
有研究表明,为了获得最高的弯曲抗力和疲劳极限以及合理的应力分布,钢的含碳量(指未渗碳前钢的原始含碳量)不能高于0.25%C。
最近由于对材料内氧化机理的研究,人们认识到内氧化是影响渗碳零件寿命的一个重要因素,法国已把内氧化作为渗碳质量检验的一项内容。
这里讲的内氧化是指在渗碳过程中,氧原子扩散到零件内部,与某些合金元素形成氧化物。
易形成氧化物的合金元素有Mn、Cr、Ti、B等,难于形成氧化物的合金元素有Ni、Mo等。
大家都已经了解,Cr、Ni共同使用能提高材料的综合性能[3]。
2.3稀土在渗碳钢上的应用
目前很多单位在研究稀土元素对渗碳钢组织和性能的影响。
综合起来讲,稀土元素能细化奥氏体晶粒。
2.4真空渗碳
在真空炉中进行的渗碳是一种高温气体渗碳工艺,由于渗碳是在真空高温状态下进行,因此具有净化零件表面,金相组织均匀,消除渗碳过程中内氧化等优点,并且渗碳时间比一般渗碳时间缩短一半。
2.5离子渗碳
离子渗碳过程简述如下,零件在真空炉中被加热到920℃,然后导入丙烷或丙烯,并在零件上加以10KV/cm的电场,使炉内气体发生辉光放电,产生碳离子,碳离子向零件表面轰击引起碳原子向零件内部的扩散。
离子渗碳具有渗碳速度快、渗碳质量易控制、不产生内氧化等优点。
2.6中温气体渗碳
为了减少零件的变形、延长设备的使用寿命、提高生产率,国内许多厂家研制并开始使用中温气体渗碳工艺。
所谓的中温气体渗碳工艺是在催渗剂的作用,渗碳过程在860~900℃温度下完成。
其工艺具有渗碳组织细小,淬火变形小、节约电能、延长设备使用寿命等优点。
陕西机械学院研制成功的《微氮中温渗碳技术》已获国家专利。
第二汽车制造厂模具分厂已把这项技术应用生产,收到了较好的经济效益[4]。
其实稀土渗碳工艺也是中温渗碳技术。
3气体渗氮的发展现状
近年来,由于气体渗氮温度低、变形小、工序少等诸多优点,在精密齿轮的制造中,渗氮处理已逐渐取代了传统的气体渗碳淬火处理[5]。
现今发展起来的有快速深层渗氮工艺,在快速深层渗氮工艺利用稀土催渗,快速渗氮新技术包括表面预氧化,表面预变形,表面纳米化预处理,激光表面氮化及其他新技术。
各种快速渗氮技术都能在一定程度上提高渗氮速度。
渗氮优化工艺能在20h以内使渗氮层厚度达0.8mm,较普通渗氮时间缩短了2/3;若能将不同的优化渗氮工艺的方法与各种新技术相结合,那么一定能进一步缩短渗氮时间,增加渗氮层的厚度。
若能进一步缩短深层渗氮的时间,那么将大大降低精密齿轮的加工成本,提高经济效益,为齿轮加工业的发展创造更广阔的前景[6-7]。
4气体碳氮共渗发展现状
气体碳氮共渗是在20世纪60年代被大量研究,70年代得到广泛使用的一项传统热处理技术。
该技术由于氮的渗入使钢的临界点(A1、A3)下移,可以适当降低淬火温度,提供了进一步减少淬火变形的可能。
氮的渗入还使淬透性增加,所以除合金钢外,碳素钢也可以实施碳氮共渗及油淬处理,从而提高硬度和表面耐磨性,这两个特点也正是该技术被广泛应用的原因。
20世纪末到本世纪初以来,出现了一种预抽真空式碳氮共渗技术。
从C、N 来源和使用渗剂方法来看,共渗机理、结果和气体碳氮共渗是一样的,渗剂中仍有含氧介质。
渗层组织中仍有表面晶界氧化层,并无法杜绝。
不过此法由于使用
了真空排气和密封技术,不仅工艺过程缩短,效率提高,渗剂使用量略有减少,而且晶界氧化层深度也有所减轻。
本世纪以来,H.Altena和F.Schrank介绍了往真空炉中通入丙烷、氨气的新技术来提高合金钢和非合金钢的表面硬度,借助真空中工艺过程的控制来影响金属表层碳、氮浓度及渗层的深度,说明了碳、氮渗入的过程和影响因素,报道了关于设备的构想。
2004年日本专利公开,该专利提到的新技术特征:在真空炉内,工件被加热至渗碳温度,通入渗碳气体进行渗碳、扩散,然后降低温度,再向真空状态的炉内通入渗氮气体,进行渗氮。
碳钢或表面硬化钢用这种新技术都可以得到要求的表面硬度、层深和韧性[8]。
5气体氮碳共渗的发展现状
气体氮碳共渗的应用范围仅次于气体渗碳。
以日本为例,在日本工业中,氮碳共渗占了化学热处理市场总量的30%。
随着应用范围的进一步扩广,气体氮碳共渗将进一步得到发展[9]。
5.1气体稀土氮碳共渗
稀土元素在化学热处理中的应用研究起始于80年代初期,但发展很快。
稀土元素对气体氮碳共渗的影响80年代末、90年代初人们进行了大量的研究。
研究结果表明:无论稀土化合物还是稀土单质当添加量适当时,对氮碳共渗有明显的催渗作用,可提高渗速30%左右,适量稀土能有效提高氮碳共渗后的硬度、耐磨性、冲击韧性和抗腐蚀性能。
应用于自行车冷作模具,其使用寿命比常规氮碳共渗提高35%以上。
5.2气体铁素体合金化氮碳共渗
气体铁素体合金化氮碳共渗(简称合金化渗氮)是一种新的表面硬化技术。
它在渗氮(碳)同时,使工件表面渗人所添加的元素(如Al、Cr、Ti和V等)其实它是低温金属元素一氮一(碳)共渗。
合金化渗氮可形成高硬度(比常规气体氮碳共渗高l00~500HV)、低脆性(I级)和致密的渗层;渗速比气体氮碳共渗高10~20%。
本技术解决了铁素体氮碳共渗后表面硬度不够高的问题。
在合金化渗氮基础上西安理工大学又进行了室温形变合金化渗氮研究,结果表明:(l)室温形变使合金化渗氮层深度随形变量增加而增加,当形变量超过一定值(该值随材质而异)后,渗氮层探度随形变量增加而减小。
(2)合金化渗氮硬度随形变量增加而增加。
5.3加压气体氮碳共渗
南昌航空工业学院试验研究了加压气体氮碳共渗的工艺特性,结果表明,铁素体氮碳共渗随着炉压的增加,渗层的表面硬度、化合物层和扩散层厚度均有所增加。
奥氏体氮碳共渗采用加压脉冲工艺,在680℃工艺温度下,能将氨分解率控制在75%左右,容易实施以氨为渗剂的奥氏体氮碳共渗,并且加压奥氏体氮碳共渗后化合物层较致密,基本上无疏松[10]。
参考文献:
[1]钟厉,孙艳鹏.热扩渗工艺的研究应用及进展[J].热加工工艺,2007,(22)
[2]夏期成.渗碳工艺的发展和应用[J].山西机械,1996,(01)
[3]横濑敬二,蔡千华.渗碳技术的进展[J].国外机车车辆工艺,2007,(04)
[4]张伯英.气体渗碳技术发展概况[J].内燃机配件,1996,(03)
[5]陈玮,王蕾,周磊,王君.钢的快速渗氮技术研究现状[J].武汉科技大学学报(自然科学
版),2006,(03)
[6]周上祺,范秋,林任勤,胡振纪.快速深层渗氮工艺的设计[J].金属热处理,1998,(03)
[7]孟力凯,齐义辉.快速气体渗氮工艺[J].辽宁工学院学报(自然科学版),2002,(06)
[8]安峻岐,刘新继,何鹏.渗碳与碳氮共渗催渗技术的发展与现状[J].金属热处理,2007,(05)
[9]A.kurz,SHU UIm,D.Joritz,曾国屏.用一体化全自动氮碳共渗设备进行可控气体渗氮的经
验[J].国外金属热处理,2004,(05)
[10]石淑琴.气体氮碳共渗的发展[J].高等职业教育-天津职业大学学报,1999,(03)。