PCB制程中金属化孔镀层空洞的成因及改善_程骄
PCB电镀镍工艺及故障原因与排除
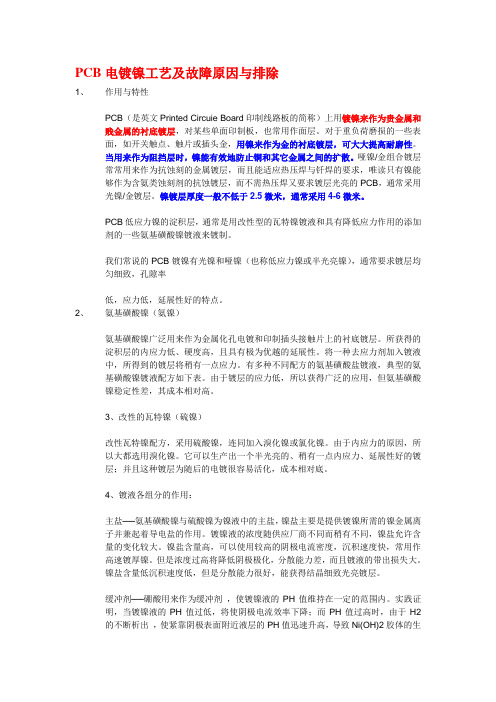
PCB电镀镍工艺及故障原因与排除1、作用与特性PCB(是英文Printed Circuie Board印制线路板的简称)上用镀镍来作为贵金属和贱金属的衬底镀层,对某些单面印制板,也常用作面层。
对于重负荷磨损的一些表面,如开关触点、触片或插头金,用镍来作为金的衬底镀层,可大大提高耐磨性。
当用来作为阻挡层时,镍能有效地防止铜和其它金属之间的扩散。
哑镍/金组合镀层常常用来作为抗蚀刻的金属镀层,而且能适应热压焊与钎焊的要求,唯读只有镍能够作为含氨类蚀刻剂的抗蚀镀层,而不需热压焊又要求镀层光亮的PCB,通常采用光镍/金镀层。
镍镀层厚度一般不低于2.5微米,通常采用4-6微米。
PCB低应力镍的淀积层,通常是用改性型的瓦特镍镀液和具有降低应力作用的添加剂的一些氨基磺酸镍镀液来镀制。
我们常说的PCB镀镍有光镍和哑镍(也称低应力镍或半光亮镍),通常要求镀层均匀细致,孔隙率低,应力低,延展性好的特点。
2、氨基磺酸镍(氨镍)氨基磺酸镍广泛用来作为金属化孔电镀和印制插头接触片上的衬底镀层。
所获得的淀积层的内应力低、硬度高,且具有极为优越的延展性。
将一种去应力剂加入镀液中,所得到的镀层将稍有一点应力。
有多种不同配方的氨基磺酸盐镀液,典型的氨基磺酸镍镀液配方如下表。
由于镀层的应力低,所以获得广泛的应用,但氨基磺酸镍稳定性差,其成本相对高。
3、改性的瓦特镍(硫镍)改性瓦特镍配方,采用硫酸镍,连同加入溴化镍或氯化镍。
由于内应力的原因,所以大都选用溴化镍。
它可以生产出一个半光亮的、稍有一点内应力、延展性好的镀层;并且这种镀层为随后的电镀很容易活化,成本相对底。
4、镀液各组分的作用:主盐──氨基磺酸镍与硫酸镍为镍液中的主盐,镍盐主要是提供镀镍所需的镍金属离子并兼起着导电盐的作用。
镀镍液的浓度随供应厂商不同而稍有不同,镍盐允许含量的变化较大。
镍盐含量高,可以使用较高的阴极电流密度,沉积速度快,常用作高速镀厚镍。
但是浓度过高将降低阴极极化,分散能力差,而且镀液的带出损失大。
PCB电镀填孔的机理分析及其影响因素

首先考虑抑制剂的抑制因子为 和光亮剂的 加速因子 相结合饱和的表面,吸附竞争动力学 简单的量化描述如下:
式(1)
由于在这些电解质溶液中,光亮剂SPS的浓
度
要远小于抑制剂PEG的浓度 ,因此可
以假定一个刚浸入到电解液的样品只被抑制剂浸
润。此外,在铜沉积过程中空气/水界面的抑制剂
关键词 填孔;曲率吸附机制;机理 中图分类号:TN41 文献标识码:A 文章编号:1009-0096(2018)09-0028-10
Analysis mechanism and effectors of Via-filling Plating for PCB
Liu Zhenquan Wu Peichang Lin Chunqin Chen Guangang Abstract CEAC play an important role for micro-via filling by electroplating, the organic additive can accelerate the electrical deposition rate of the blind hole bottom, also inhibit the electrical deposition rate of the suface and corner of blind hole to be filled. In this text, we carried on analysis about CEAC and function of organic additive for micro-via filling by electroplating detailed, got optimistic ratio of three kind organic additives for micro-via filling by electroplating at last, and inducted effectors of PCB boards during macrovia filling by electroplating. Key words Hole Filling; CEAC; Mechanism
详谈pcb钻孔孔壁镀铜开裂问题及解决方案-豆丁
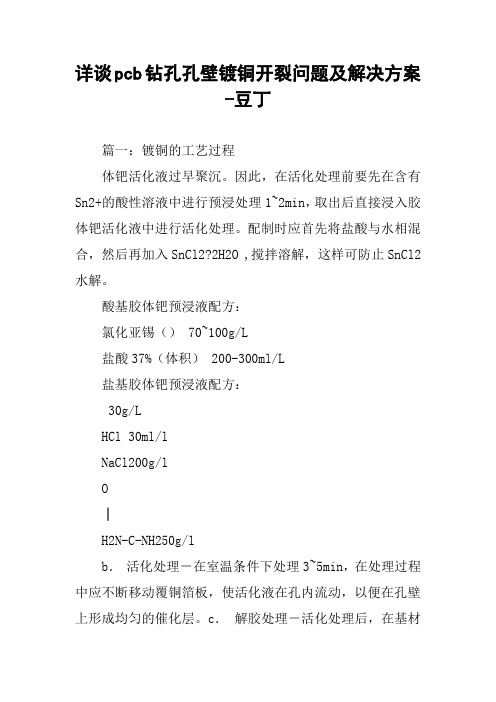
详谈pcb钻孔孔壁镀铜开裂问题及解决方案-豆丁篇一:镀铜的工艺过程体钯活化液过早聚沉。
因此,在活化处理前要先在含有Sn2+的酸性溶液中进行预浸处理1~2min,取出后直接浸入胶体钯活化液中进行活化处理。
配制时应首先将盐酸与水相混合,然后再加入SnCl2?2H2O ,搅拌溶解,这样可防止SnCl2水解。
酸基胶体钯预浸液配方:氯化亚锡() 70~100g/L盐酸37%(体积) 200-300ml/L盐基胶体钯预浸液配方:30g/LHCl 30ml/lNaCl200g/lO║H2N-C-NH250g/lb.活化处理-在室温条件下处理3~5min,在处理过程中应不断移动覆铜箔板,使活化液在孔内流动,以便在孔壁上形成均匀的催化层。
c.解胶处理-活化处理后,在基材表面吸附着以钯粒子为核心,在钯核的周围,具有碱式锡酸盐的胶体化合物。
在化学镀铜前,应将碱式锡酸盐去除,使活性的钯晶核充分暴露出来,从而使钯晶核具有非常强而均匀的活性。
经过解胶处理再进行化学镀铜,不但提高了胶体钯的活性,而且也显著提高化学镀铜层与基材间的结合强度。
常用的解胶处理液是5%的氢氧化钠水溶液或1%氟硼酸水溶液。
解胶处理在室温条件下处理1~2min,水洗后进行化学镀铜。
d.胶体铜活化液简介:明胶 2g/l/lDMAB(二甲胺基硼烷)5g/l水合肼 10 g/l钯20ppm配制过程:首先分别将明胶和硫酸铜用温水(40度C)溶解后将明胶加入至硫酸铜的溶液中,用25%H2SO4将PH值调至2..5当温度为45度C时,将溶解后DMAB在搅拌条件下缓慢加入上述的混合溶液中,并加入去离子稀释至1升,保温40~45度C,并搅拌至反应开始(约5~10分钟)溶液的颜色由蓝再变成绿色。
放置24小时颜色变成红黑色后加入水合肼。
篇二:PCB线路板镀铜表面粗糙问题原因分析PCB线路板镀銅表面粗糙问题原因分析可能原因如下:镀铜槽本身的问题1、阳极问题:成分含量不当导致产生杂质2、光泽剂问题(分解等)3、电流密度不当导致铜面不均匀4、槽液成分失调或杂质污染5、设备设计或组装不当导致电流分布太差…………当然作为镀铜本身来讲;以上问题导致粗糙的可能性不大前制程问题PTH制程带入其他杂质:1、活化成分失调钯浓度太高或者预浸盐残留板面2、速化失调板面镀铜是残有锡离子3、化学铜失调板面沉铜不均4、镀铜前酸洗不当导致板面残留杂质………………黑孔制程:微蚀不净导致残碳抗氧化不当导致板面不良烘干不良导致微蚀无法将板面碳剥除导致残碳电流输入输出不当导致板面不良…………篇三:化学镀铜常见故障和纠正方法-PCB工艺论文,SMT 技术文章-SMT专家网化学镀铜常见故障和纠正方法◎化学镀铜常见故障和纠正方法故障发生原因纠正方法化学镀铜空洞①钻孔粉尘,孔化后脱落①检查吸尘器,钻头质量,转速/进给等②加强去毛刺的高压水冲洗钻孔后孔壁裂缝或内层间分离检查钻头质量,转速/进给,以及层压板厚材料和层压工艺条件③除钻污过度,造成树脂变成海绵状,引起水洗不良和镀层脱落检查除钻污法工艺,适当降低去钻污强度④除钻污后中和处理不充分,残留Mn残渣检查中和处理工艺⑤清洁调整不足,影响Pd的吸附检查清洗调整处理工艺(如浓度、温度、时间)及副产物是否过量⑥活化液浓度偏低影响Pd吸附检查活化处理工艺补充活化剂⑦加速处理过度,在去除Sn的同时Pd也被除掉检查加速处理工艺条件(温度/时间/浓度)如降低加速剂浓度或浸板时间⑧水洗不充分,使各槽位的药水相互污染检查水洗能力,水量/水洗时间⑨孔内有气泡加设摇摆、震动等⑩化学镀铜液的活性差检查NaOH、HCHO、Cu2+的浓度以及溶液温度等⑾反应过程中产生气体无法及时逸出加强移动、振动和空气搅拌等。
pcb常见缺陷原因与措施

pcb常见缺陷原因与措施汇报人:日期:•孔洞和针孔•短路和断路•线路设计不良•基材不良目•环境因素影响•材料和工艺问题录孔洞和针孔孔洞孔的电镀质量不良,导致孔壁有颗粒或凸起。
孔壁上有异物,如金属屑、纤维或灰尘。
电镀过程中,液体内有气泡产生并滞留在孔壁上。
孔洞对孔进行清洁,去除异物和灰尘。
采用高质量的电镀液和电镀设备,提高电镀质量。
对孔径和孔深进行精确控制,确保电镀时能够完全覆盖。
预防措施孔洞在制作PCB时,对孔进行清洁和干燥,避免异物和灰尘的残留。
短路和断路原因分析解决方法预防措施线路设计不良布局不合理走线不规范未遵循最佳实践030201原因分析优化布局修正走线遵循最佳实践解决方法加强设计培训建立PCB设计的审核机制,确保设计的质量和可靠性。
强化审核机制增加技术投入预防措施基材不良基材质量不好基材储存不当原因分析使用高质量的基材储存环境控制解决方法对基材进行严格的质量控制在生产前对基材进行严格的质量检查,包括外观、物理性能和电气性能等指标。
储存环境监控定期对基材储存环境进行检查和维护,确保环境条件符合要求。
预防措施环境因素影响污染物空气中的微粒和有害气体可能污染PCB的表面和内部,导致缺陷。
温度和湿度过高或过低的温度和湿度可能影响PCB的制造过程和性能,导致缺陷的产生。
静电制造过程中的静电可能导致PCB上的微粒移动,产生缺陷。
原因分析控制温度和湿度空气净化静电防护解决方法定期检测空气质量培训员工定期检查和维护环境设备预防措施材料和工艺问题03压合工艺问题01板材选择不当02制造工艺问题原因分析1 2 3选用高质量板材优化制造工艺压合工艺优化解决方法严格控制材料质量对板材、胶片、铜箔等材料进行严格的质量控制,确保其符合制造要求。
加强工艺技术研究不断加强制造工艺技术的研究和开发,提高制造水平。
定期维护设备对制造设备进行定期维护和保养,确保其正常运行,提高制造效率。
预防措施感谢观看。
印制电路板镀层缺陷成因分析及其对策

印制电路板镀层缺陷成因分析及其对策1前言金属化孔质量与多层板质量及可靠性息息相关。
金属化孔起着多层印制线路电气互连的作用。
孔壁镀铜层质量是印制板质量的核心,不仅要求镀层有合适的厚度、均匀性和延展性,而且要求镀层在288℃热冲击10秒不能产生断裂。
因为孔壁镀铜层热冲击断裂是一种致命的缺陷,它将造成内层线路间和内层与外层线路之间断路;轻者影响线路断续导电,重者引起多层板报废。
目前,印制板生产中经常出现的金属化孔镀层缺陷主要有:金属化孔内镀铜层空洞、瘤状物、孔内镀层薄、粉红圈以及多层板孔壁与内层铜环连接不良等。
这些缺陷的绝大多数将导致产品报废,造成严重的经济损失,影响交货期。
2金属化孔镀层主要缺陷的产生原因及相应对策我们首先简单回顾一下多层印制板的制造工艺过程。
下料→制板→蚀刻→黑化→层压→钻孔→去沾污及凹蚀处理→孔金属化→全板电镀→制板→图形电镀→脱膜→蚀刻→丝印阻焊→热风整平→丝印字符本文将从钻孔工序、孔壁去树脂沾污及凹蚀处理工序、电镀及多层板层压工序等几个方面,分析金属化孔镀层的主要缺陷及产生原因,阐述如何优化工艺参数,进行严格的工艺及生产管理,以保证孔化质量。
2.1钻孔工序大多数镀层空洞部位都伴随出现钻孔质量差引起的孔壁缺陷,如孔口毛刺、孔壁粗糙、基材凹坑及环氧树脂腻污等。
由此造成孔壁镀铜层空洞,孔壁基材与镀层分离或镀层不平整。
下面,将对孔壁缺陷的成因及所采取的措施进行阐述:2.1.1孔口毛刺的产生及去除无论是采用手工钻还是数控钻,也无论是采用何种钻头和钻孔工艺参数,覆铜箔板在其钻孔过程中,产生毛刺总是不可避免的。
孔口毛刺对于金属化孔质量的影响历来不被人们所重视,但对于高可靠性印制板的金属化孔质量来讲,它却是一个不可忽视的因素。
首先,孔口毛刺会改变孔径尺寸,导致孔径入口处尺寸变小,影响元器件的插入。
其次,凸起或凹陷进入孔内的铜箔毛刺,将影响孔金属化过程中电镀时的电力线分布,导致孔口镀层厚度偏薄和应力集中,从而使成品印制板的孔口镀铜层在受到热冲击时,极易因基板热膨胀所引起的轴向拉伸应力造成断裂现象。
电镀填孔工艺影响因素
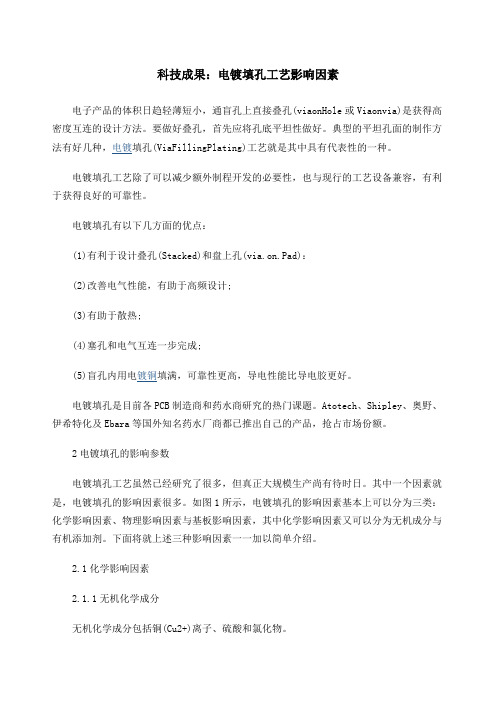
科技成果:电镀填孔工艺影响因素电子产品的体积日趋轻薄短小,通盲孔上直接叠孔(viaonHole或Viaonvia)是获得高密度互连的设计方法。
要做好叠孔,首先应将孔底平坦性做好。
典型的平坦孔面的制作方法有好几种,电镀填孔(ViaFillingPlating)工艺就是其中具有代表性的一种。
电镀填孔工艺除了可以减少额外制程开发的必要性,也与现行的工艺设备兼容,有利于获得良好的可靠性。
电镀填孔有以下几方面的优点:(1)有利于设计叠孔(Stacked)和盘上孔(via.on.Pad):(2)改善电气性能,有助于高频设计;(3)有助于散热;(4)塞孔和电气互连一步完成;(5)盲孔内用电镀铜填满,可靠性更高,导电性能比导电胶更好。
电镀填孔是目前各PCB制造商和药水商研究的热门课题。
Atotech、Shipley、奥野、伊希特化及Ebara等国外知名药水厂商都已推出自己的产品,抢占市场份额。
2电镀填孔的影响参数电镀填孔工艺虽然已经研究了很多,但真正大规模生产尚有待时日。
其中一个因素就是,电镀填孔的影响因素很多。
如图1所示,电镀填孔的影响因素基本上可以分为三类:化学影响因素、物理影响因素与基板影响因素,其中化学影响因素又可以分为无机成分与有机添加剂。
下面将就上述三种影响因素一一加以简单介绍。
2.1化学影响因素2.1.1无机化学成分无机化学成分包括铜(Cu2+)离子、硫酸和氯化物。
(1)硫酸铜。
硫酸铜是镀液中铜离子的主要来源。
镀液中铜离子通过阴极和阳极之间的库仑平衡,维持浓度不变。
通常阳极材料和镀层材料是一样的,在这里铜既是阳极也是离子源。
当然,阳极也可以采用不溶性阳极,Cu2+采用槽外溶解补加的方式,如采用纯铜角、CuO粉末、CuCO3等。
但是,需要注意的是,采用槽外补加的方式,极易混入空气气泡,在低电流区使Cu2+处于超饱和临界状态,不易析出。
值得注意的是,提高铜离子浓度对通孔分散能力有负面影响。
(2)硫酸。
pcB金属孔镀层缺陷
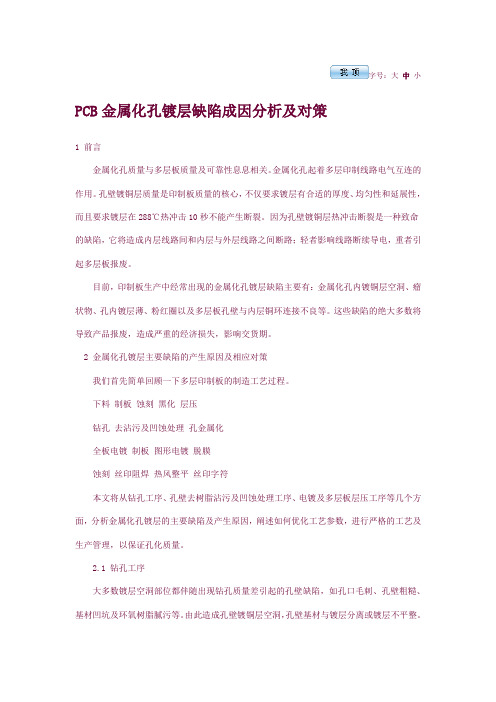
字号:大中小PCB金属化孔镀层缺陷成因分析及对策1 前言金属化孔质量与多层板质量及可靠性息息相关。
金属化孔起着多层印制线路电气互连的作用。
孔壁镀铜层质量是印制板质量的核心,不仅要求镀层有合适的厚度、均匀性和延展性,而且要求镀层在288℃热冲击10秒不能产生断裂。
因为孔壁镀铜层热冲击断裂是一种致命的缺陷,它将造成内层线路间和内层与外层线路之间断路;轻者影响线路断续导电,重者引起多层板报废。
目前,印制板生产中经常出现的金属化孔镀层缺陷主要有:金属化孔内镀铜层空洞、瘤状物、孔内镀层薄、粉红圈以及多层板孔壁与内层铜环连接不良等。
这些缺陷的绝大多数将导致产品报废,造成严重的经济损失,影响交货期。
2 金属化孔镀层主要缺陷的产生原因及相应对策我们首先简单回顾一下多层印制板的制造工艺过程。
下料制板蚀刻黑化层压钻孔去沾污及凹蚀处理孔金属化全板电镀制板图形电镀脱膜蚀刻丝印阻焊热风整平丝印字符本文将从钻孔工序、孔壁去树脂沾污及凹蚀处理工序、电镀及多层板层压工序等几个方面,分析金属化孔镀层的主要缺陷及产生原因,阐述如何优化工艺参数,进行严格的工艺及生产管理,以保证孔化质量。
2.1 钻孔工序大多数镀层空洞部位都伴随出现钻孔质量差引起的孔壁缺陷,如孔口毛刺、孔壁粗糙、基材凹坑及环氧树脂腻污等。
由此造成孔壁镀铜层空洞,孔壁基材与镀层分离或镀层不平整。
下面,将对孔壁缺陷的成因及所采取的措施进行阐述:2.1.1 孔口毛刺的产生及去除无论是采用手工钻还是数控钻,也无论是采用何种钻头和钻孔工艺参数,覆铜箔板在其钻孔过程中,产生毛刺总是不可避免的。
孔口毛刺对于金属化孔质量的影响历来不被人们所重视,但对于高可靠性印制板的金属化孔质量来讲,它却是一个不可忽视的因素。
首先,孔口毛刺会改变孔径尺寸,导致孔径入口处尺寸变小,影响元器件的插入。
其次,凸起或凹陷进入孔内的铜箔毛刺,将影响孔金属化过程中电镀时的电力线分布,导致孔口镀层厚度偏薄和应力集中,从而使成品印制板的孔口镀铜层在受到热冲击时,极易因基板热膨胀所引起的轴向拉伸应力造成断裂现象。
PCB制程中金属化孔镀层空洞的成因及改善_程骄

PCB制程中金属化孔镀层空洞的成因及改善程 骄 李卫明 刘敏然(广东东硕科技有限公司,广东 广州 510288)摘 要 文章从印制线路板的生产流程和工艺参数等方面,结合切片观察的手段,浅析了金属化孔镀层空洞的形成原因。
研究表明:半固化片的型号、含胶量及填料的比例与芯板质量有很大关联,影响着层压和钻孔工序的板件质量;沉铜和电镀工序的工艺参数、周边辅助设施的工作状况及加工过程中的时效是影响镀层空洞的主要因素。
针对每一个异常点,找到缺陷的形成原因,对工艺流程进行有效的改进,有的放矢的起到预防措施,最终达到改善镀层质量,提高产品的合格率,对提高线路板可靠性具有重要的意义。
关键词 空洞;化学沉铜;电镀;钻孔中图分类号:TN41 文献标识码:A 文章编号:1009-0096(2013)08-0021-03Research on the causes & control of through-holevoids for PCB processCHENG Jiao LI Wei-Ming LIU Min-RanAbstract Voids in plated through-holes are caused by many different processing problems. This paper will show how to identify rim voids by PCB production process & parameter with micro section observation. The results indicate that stronger correlation existed in core board between the proportion of rubber polymer to fi ller and type of PP, which could infl uence the quality of lamination and drill. The primary reason of VPTH formed was by process parameter, the condition of assisting machine and processing time for electroless and electroplate process. The reason of defect was found for every abnormal board. Effective improvement measures not only had a defi nite object in view of prevention measures, but also improved quality and percent of certifi ed products, this measure had the vital signifi cance to improve reliability of printed circuit board.Key words Void PTH; Electroless Copper Plating; Electroplating; Drill现代印制电路板设计要求向高密度、细线条、微孔径的多层板发展,因此金属化孔质量将直接关系到线路板的质量及可靠性,而过孔不通会直接导致成品板的电气互连失败,从而使成品板件由于镀层空洞缺陷而报废。
PCB镀通孔发生_空洞_的根本原因和对策

PCB镀通孔发生“空洞”的根本原因和对策林金堵 吴梅珠摘 要 文章概述了多层板镀通孔发生“空洞”的根本原因与对策。
基材、钻孔、孔壁粗糙度、孔尺寸、化学镀铜和电镀铜等都会影响PTH的“空洞”问题。
关键词 镀通孔;镀层“空洞”;镀层附着力;高性能基材;孔壁表面状态;化学镀铜中图分类号:TN41 文献标识码:A 文章编号:1009-0096(2010)4-0031-06The Basic and Countermeasureof the Plated Through Hole Voiding in PCBLIN Jin-du WU Mei-zhuAbstract The paper describes the basic and countermeasure of the plated through hole voiding in PCB. The substrate material, drilling hole, hole-wall topography, hole size, electroless copper, and plated copper can signi fi cantly impact the hole-wall voids, adhesion, and reliability of the PTH.Key words PTH(Plated Through-Hole); hole-wall voids; hole-wall adhesion; high-performance substrate; hole-wall topography; electroless copper目前,多层板随着高密度化发展和无铅化焊接要求等条件下,层间连接的导通孔面临着产生“空洞”等缺陷,其可靠性方面面临着严厉而复杂的挑战。
这些挑战:(1)是导通孔高厚径比(孔微小化和高多层化)化和盲孔化等带来孔金属化与电镀的复杂困难度;(2)是无铅化要采用更高的T d 、T g 温度的CCL (高性能)材料所带来“导通孔”的加工新问题;(3)由于无铅化焊接要求有耐更高的焊接温度、更长的高温焊接时间和快速的冷却速度,因此,导通孔内的铜镀层,不仅要有更好的延展性,而且更重要地是要与孔壁有更好的结合力,才能经得起更高的焊接条件的考验;(4)是所制造的成品要经得起更高幅度的多次“热循环”、“热冲击”(更高温度和更长的高温停留时间)等的“老化(可靠性)”考验。
浅析印制电路板孔金属化及其工艺改进途径

浅析印制电路板孔金属化及其工艺改进途径摘要:PBC孔金属化技术被认为是印制电路板生产过程中的关键环节,本文将深入探讨这一技术的概念,并结合实际应用,提出有效的改善方案。
此外,本文还将探讨如何通过整平、氧化、催化和电镀等技术来提高PBC的性能,以及如何通过这些技术来实现PBC的长期可持续发展。
关键词:印制电路板。
孔金属化;工艺现状;优化方法引言:随着电子IT的飞速发展,印刷电路板(PBC)行业迎来了前所未有的机遇,而孔金属化则成为PBC生产过程中不可或缺的一部分。
随着PBC孔金属化技术的不断发展,其工艺已经变得越来越成熟,制造质量也越来越稳定,但仍然存在着复杂的工艺流程、昂贵的成本以及严重的环境污染问题。
因而,提升PBC孔金属化技术的效率与质量显得尤为重要,本文将从多方面探讨这一问题,以期达到更好的效果。
1 PBC孔金属化概念覆铜板(CCP)为PCB制造。
CCP是一种具有重要应用价值的基础材料,它可以通过精心设计的加工工艺,如电镀铜、刻蚀等,制作出具有良好导电性能的电路,从而实现高性能的PCB电路。
在PCB盘面上的每个孔都被完全封装之前,才能够将其与PCB电路连接起来,并安装相应的电子元器件。
从宏观视角来看,孔金属化技术指的是采用电化学镀、电镀或其他技术,将一层导电金属覆盖在PCB板孔壁上,以增强电路与电子元件之间的联系,以达到改善电路效率和电子元件耐久性的目的。
金属化是PCB制造过程中至关重要的一步,它需要确保金属化孔的机械强度和导电性能达到最佳水平。
此外,铜镀层的结构必须完善,分布均匀,厚度也应该适中(一般为25~30μm)。
同时,孔洞内部也应避免出现分层和气泡等缺陷,并且孔的电阻值应小于<1000MΩ。
近年来,随着高密度封装技术的普及,PCB结构的创新和发展得到了显著推动,成为工业界的一大亮点。
通过安装金属孔,可以有效地将不同电路连接起来,从而提高电子元件的性能和可靠性。
通过表面安装技术的应用,可以有效地缩小金属化孔空洞的尺寸,从而推动PCB制造技术的发展,实现微纳通孔和薄型化的生产。
浅析印制电路板孔金属化及其工艺改进途径

浅析印制电路板孔金属化及其工艺改进途径作者:苗奇来源:《科学与信息化》2019年第13期摘要孔金属化是印制电路板(PBC)生产制造工艺的核心,文章首先阐述了PBC孔金属化概念做出解析,其次从整平、氧化、催化与电镀等方面阐述了PBC孔金属化工艺显著,最后站在促进PBC孔金属化持续发展的角度,对优化工艺的方式方法做出研究。
关键词印制电路板;孔金属化;工艺现状;优化方法在电子信息技术的促动下,印制电路板(PBC)行业获得巨大发展空间,孔金属化是PBC 生产制造的关键一环。
当下国内PBC孔金属化技术工艺日趋成熟、制造质量相对稳定,但还存在工艺流程繁杂、造价成本高及环境污染严重等特征。
故而加强PBC孔金属化工艺改造完善具有很大现实意义,本文基于此做出相关研究与分析。
1 PBC孔金属化概念覆铜板(CCP)为PCB制造。
的基础材料之一,以CCP为载体,在其上部有目的性的进行加工,电镀铜,刻蚀等操作,进而获得导电图形电路并构建PCB。
只有确保PCB盘面上通孔进入化后,方可和PCB电路衔接与安设电子零部件。
从宏观的角度上分析,孔金属化实质上就是采用电化学镀与电镀等方法,在PCB板孔绝缘孔壁上镶镀一层导体金属,其目的在于促使制印导线之间的连通性。
在PCB生产制造期间,孔金属化是核心工艺流程,在具体生产中要求金属化孔具备优良的机械韧性与导电性能、铜镀层结构完整、分布均匀、厚度适中(通常为25~30μm),孔洞内部可有分层、气泡等不良现象,孔电阻指标最近几年中,高密度封装技术在工业领域中有广泛应用,带动了PCB结构的创新发展进程。
在安装插孔过程中,金属孔设置目的是有效连接不同电路,并促进各个电子元件功能正常发挥。
在表面安装技术的协助下,金属化孔空洞内径应适量减少,同时助力于PCB制造技术朝着为微纳通孔、薄型化生产进程。
2 PBC孔金属化工艺研究在孔金属化生产工艺期间,直接采用导电性有机聚合物的方法称之为dms2工艺,其可以划分为前处理,形成导电性聚合物膜以及硫酸铜电镀三阶段,在板面、板面图形及整体图形电镀领域中均有广泛应用,且取得的效果较为优良,本文如下的主要工艺流程做出阐述:(1)整平。
电路板(PCB)制造出现各种问题及改善方法

电路板(PCB)制造出现各种问题及改善方法(一)一、电路板工程设计制作1.1CAM制作的基本步骤每一个PCB 板基本上都是由孔径孔位层、DRILL 层、线路层、阻焊层、字符层所组成的,在CAM350 中,每载入一层都会以不同的颜色区分开,以便于我们操作。
1.1.导入文件首先自动导入文件(File-->Import-->Autoimport),检查资料是否齐全,对齐各层(Edit-->Layers-->Align)并设定原点位置(Edit-->Change-->Origin-->Datum Coordinate),按一定的顺序进行层排列(Edit-->Layers-->Reorder),将没用的层删除(Edit-->Layers-->Reorder)。
1.2.处理钻孔当客户没有提供钻孔文件时,可以用孔径孔位转成Flash(Utilities-->Draw-->Custom,Utilities-->Draw-->Flash-->Interactive)后再转成钻孔(钻孔编辑状态下,Utilities-->Gerber to Drill);如果有提供钻孔文件则直接按制作要求加大。
接着检查最小钻孔孔径规格、孔边与孔边(或槽孔)最小间距(Analysis-->Check Drill)、孔边与成型边最小距离(Info-->Measure-->Object-Object)是否满足制程能力。
1.3.线路处理首先测量最小线径、线距(Analysis-->DRC),看其是否满足制程能力。
接着根据PC 板类型和基板的铜箔厚度进行线径补偿(Edit-->Change-->Dcode),检查线路PAD 相对于钻孔有无偏移(如果PAD 有偏,用Edit-->Layers-->Snap Pad to Drill 命令;如果钻孔有偏,则用Edit-->Layers-->Snap Drill to Pad 命令),线路PAD 的Ring 是否够大(Analysis-->DRC),线路与NPTH 孔边、槽边、成型边距离是否满足制作要求。
空洞的来因
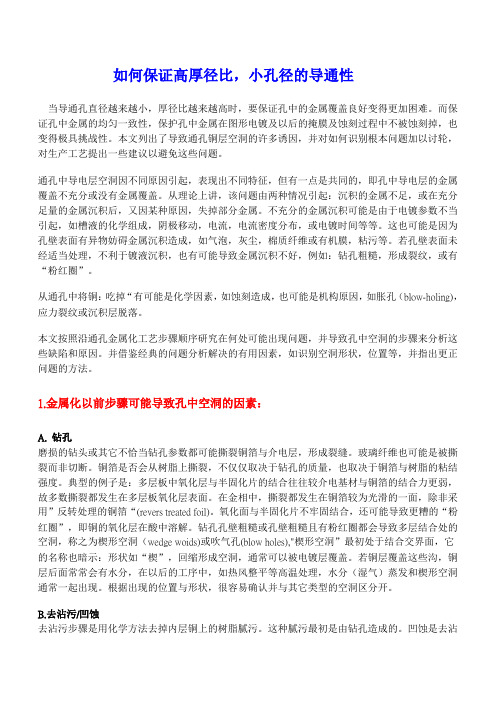
如何保证高厚径比,小孔径的导通性当导通孔直径越来越小,厚径比越来越高时,要保证孔中的金属覆盖良好变得更加困难。
而保证孔中金属的均匀一致性,保护孔中金属在图形电镀及以后的掩膜及蚀刻过程中不被蚀刻掉,也变得极具挑战性。
本文列出了导致通孔铜层空洞的许多诱因,并对如何识别根本问题加以讨轮,对生产工艺提出一些建议以避免这些问题。
通孔中导电层空洞因不同原因引起,表现出不同特征,但有一点是共同的,即孔中导电层的金属覆盖不充分或没有金属覆盖。
从理论上讲,该问题由两种情况引起:沉积的金属不足,或在充分足量的金属沉积后,又因某种原因,失掉部分金属。
不充分的金属沉积可能是由于电镀参数不当引起,如槽液的化学组成,阴极移动,电流,电流密度分布,或电镀时间等等。
这也可能是因为孔壁表面有异物妨碍金属沉积造成,如气泡,灰尘,棉质纤维或有机膜,粘污等。
若孔壁表面未经适当处理,不利于镀液沉积,也有可能导致金属沉积不好,例如:钻孔粗糙,形成裂纹,或有“粉红圈”。
从通孔中将铜:吃掉“有可能是化学因素,如蚀刻造成,也可能是机构原因,如胀孔(blow-holing),应力裂纹或沉积层脱落。
本文按照沿通孔金属化工艺步骤顺序研究在何处可能出现问题,并导致孔中空洞的步骤来分析这些缺陷和原因。
并借鉴经典的问题分析解决的有用因素,如识别空洞形状,位置等,并指出更正问题的方法。
1.金属化以前步骤可能导致孔中空洞的因素:A. 钻孔磨损的钻头或其它不恰当钻孔参数都可能撕裂铜箔与介电层,形成裂缝。
玻璃纤维也可能是被撕裂而非切断。
铜箔是否会从树脂上撕裂,不仅仅取决于钻孔的质量,也取决于铜箔与树脂的粘结强度。
典型的例子是:多层板中氧化层与半固化片的结合往往较介电基材与铜箔的结合力更弱,故多数撕裂都发生在多层板氧化层表面。
在金相中,撕裂都发生在铜箔较为光滑的一面,除非采用”反转处理的铜箔“(revers treated foil)。
氧化面与半固化片不牢固结合,还可能导致更糟的“粉红圈”,即铜的氧化层在酸中溶解。
孔无铜
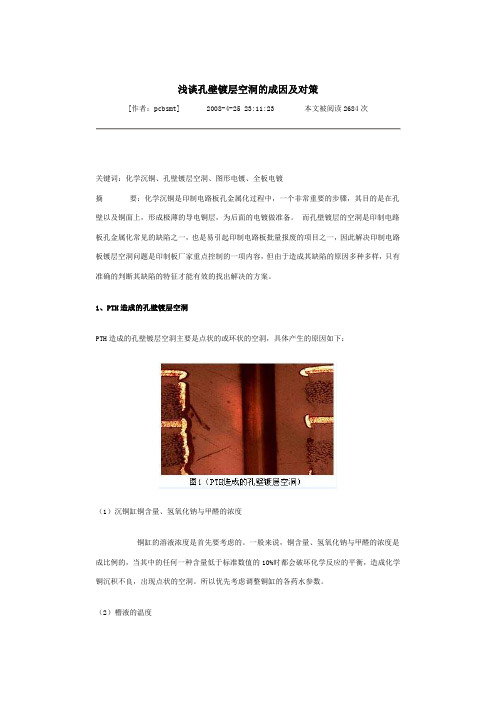
浅谈孔壁镀层空洞的成因及对策[作者:pcbsmt] 2008-4-25 23:11:23 本文被阅读2684次关键词:化学沉铜、孔壁镀层空洞、图形电镀、全板电镀摘要:化学沉铜是印制电路板孔金属化过程中,一个非常重要的步骤,其目的是在孔壁以及铜面上,形成极薄的导电铜层,为后面的电镀做准备。
而孔壁镀层的空洞是印制电路板孔金属化常见的缺陷之一,也是易引起印制电路板批量报废的项目之一,因此解决印制电路板镀层空洞问题是印制板厂家重点控制的一项内容,但由于造成其缺陷的原因多种多样,只有准确的判断其缺陷的特征才能有效的找出解决的方案。
1、PTH造成的孔壁镀层空洞PTH造成的孔壁镀层空洞主要是点状的或环状的空洞,具体产生的原因如下:(1)沉铜缸铜含量、氢氧化钠与甲醛的浓度铜缸的溶液浓度是首先要考虑的。
一般来说,铜含量、氢氧化钠与甲醛的浓度是成比例的,当其中的任何一种含量低于标准数值的10%时都会破坏化学反应的平衡,造成化学铜沉积不良,出现点状的空洞。
所以优先考虑调整铜缸的各药水参数。
(2)槽液的温度槽液的温度对溶液的活性也存在着重要的影响。
在各溶液中一般都会有温度的要求,其中有些是要严格控制的。
所以对槽液的温度也要随时关注。
(3)活化液的控制二价锡离子偏低会造成胶体钯的分解,影响钯的吸附,但只要对活化液定时的进行添加补充,不会造成大的问题。
活化液控制的重点是不能用空气搅拌,空气中的氧会氧化二价锡离子,同时也不能有水进入,会造成SnCl2的水解。
(4)清洗的温度清洗的温度常常被人忽视,清洗的最佳温度是在20℃以上,若低于15℃就会影响清洗的效果。
在冬季的时候,水温会变的很低,尤其是在北方。
由于水洗的温度低,板子在清洗后的温度也会变的很低,在进入铜缸后板子的温度不能立刻升上来,会因为错过了铜沉积的黄金时间而影响沉积的效果。
所以在环境温度较低的地方,也要注意清洗水的温度。
(5)整孔剂的使用温度、浓度与时间药液的温度有着较严格的要求,过高的温度会造成整孔剂的分解,使整孔剂的浓度变低,影响整孔的效果,其明显的特征是在孔内的玻璃纤维布处出现点状空洞。
通孔铜层空洞的原因和解决方法

通孔铜层空洞的原因和解决方法通孔中导电层空洞的原因大概有两种:沉积的金属不足,或在充分足量的金属沉积后,又因某种原因,失掉部分金属。
不充分的金属沉积可能是由于电镀参数不当引起,如槽液的化学组成,阴极移动,电流,电流密度分布,或电镀时间等等。
本文按照导通孔金属化工艺步骤顺序研究在何处可能出现问题,并导致孔中空洞的步骤来分析这些缺陷和原因。
并借鉴经典的问题分析解决的有用因素,如识别空洞形状,位置等,并指出更正问题的方法。
1、金属化以前步骤可能导致孔中空洞的因素:A、钻孔磨损的钻头或其它不恰当钻孔参数都可能撕裂铜箔与介电层,形成裂缝。
玻璃纤维也可能是被撕裂而非切断。
铜箔是否会从树脂上撕裂,不仅仅取决于钻孔的质量,也取决于铜箔与树脂的粘结强度。
典型的例子是:多层板中氧化层与半固化片的结合往往较介电基材与铜箔的结合力更弱,故多数撕裂都发生在多层板氧化层表面。
在金板中,撕裂都发生在铜箔较为光滑的一面,除非采用”反转处理的铜箔“(revers treated foil)。
氧化面与半固化片不牢固结合,还可能导致更糟的“粉红圈”,即铜的氧化层在酸中溶解。
钻孔孔壁粗糙或孔壁粗糙且有粉红圈都会导致多层结合处的空洞,称之为楔形空洞(wedge woids)或吹气孔(blow holes),"楔形空洞”最初处于结合交界面,它的名称也暗示:形状如“楔”,回缩形成空洞,通常可以被电镀层覆盖。
若铜层覆盖这些沟,铜层后面常常会有水分,在以后的工序中,如热风整平等高温处理,水分(湿气)蒸发和楔形空洞通常一起出现。
根据出现的位置与形状,很容易确认并与其它类型的空洞区分开。
B、去沾污/凹蚀去沾污步骤是用化学方法去掉内层铜上的树脂腻污。
这种腻污最初是由钻孔造成的。
凹蚀是去沾污的进一步深化,即将去掉更多的树脂,使铜从树脂中“突出”,与镀铜层形成“三点结合”或“三面结合”,提高互联可靠性。
高锰酸盐用于氧化树脂,并“蚀刻”之。
首先需要将树脂溶胀,以便于高锰酸盐处理,中和步骤可以去掉锰酸盐残渣,玻璃纤维蚀刻采用不同的化学方法,通常是氢氟酸。
化孔镀层缺陷成因分析及对策
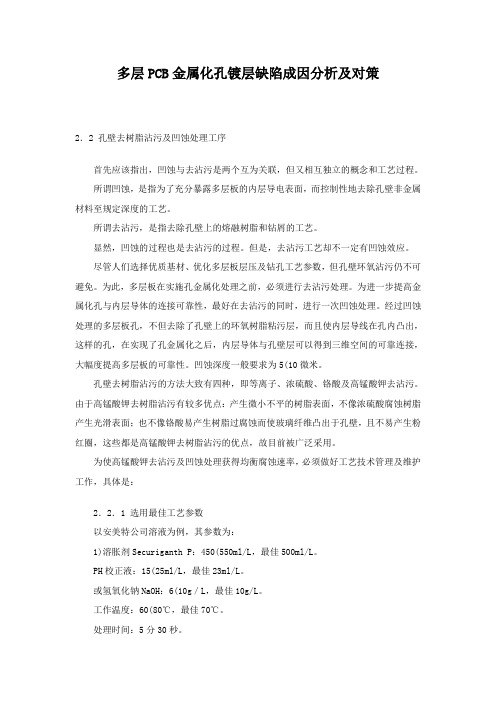
多层PCB金属化孔镀层缺陷成因分析及对策2.2 孔壁去树脂沾污及凹蚀处理工序首先应该指出,凹蚀与去沾污是两个互为关联,但又相互独立的概念和工艺过程。
所谓凹蚀,是指为了充分暴露多层板的内层导电表面,而控制性地去除孔壁非金属材料至规定深度的工艺。
所谓去沾污,是指去除孔壁上的熔融树脂和钻屑的工艺。
显然,凹蚀的过程也是去沾污的过程。
但是,去沾污工艺却不一定有凹蚀效应。
尽管人们选择优质基材、优化多层板层压及钻孔工艺参数,但孔壁环氧沾污仍不可避免。
为此,多层板在实施孔金属化处理之前,必须进行去沾污处理。
为进一步提高金属化孔与内层导体的连接可靠性,最好在去沾污的同时,进行一次凹蚀处理。
经过凹蚀处理的多层板孔,不但去除了孔壁上的环氧树脂粘污层,而且使内层导线在孔内凸出,这样的孔,在实现了孔金属化之后,内层导体与孔壁层可以得到三维空间的可靠连接,大幅度提高多层板的可靠性。
凹蚀深度一般要求为5(10微米。
孔壁去树脂沾污的方法大致有四种,即等离子、浓硫酸、铬酸及高锰酸钾去沾污。
由于高锰酸钾去树脂沾污有较多优点:产生微小不平的树脂表面,不像浓硫酸腐蚀树脂产生光滑表面;也不像铬酸易产生树脂过腐蚀而使玻璃纤维凸出于孔壁,且不易产生粉红圈,这些都是高锰酸钾去树脂沾污的优点,故目前被广泛采用。
为使高锰酸钾去沾污及凹蚀处理获得均衡腐蚀速率,必须做好工艺技术管理及维护工作,具体是:2.2.1 选用最佳工艺参数以安美特公司溶液为例,其参数为:1)溶胀剂Securiganth P:450(550ml/L,最佳500ml/L。
PH校正液:15(25ml/L,最佳23ml/L。
或氢氧化钠NaOH:6(10g/L,最佳10g/L。
工作温度:60(80℃,最佳70℃。
处理时间:5分30秒。
2)高锰酸钾KMnO4:50(60g/L,最佳60g/L。
氢氧化钠NaOH: 30(50g/L,最佳40g/L。
工作温度:60(80℃,最佳70℃。
处理时间:12分。
pcb常见缺陷原因与措施

阻焊桥连的预防措施
调整阻焊剂的配方和涂覆工艺,避免阻焊剂残留在孔口 或线路之间。 控制好线路之间的间距,避免过近导致阻焊剂涂覆时产 生桥连。
在制作过程中及时清理残留物,避免影响阻焊效果。
焊盘脱落的预防措施
优化焊盘设计,确保焊盘大小和厚度合理。 选择合适的焊接材料,确保焊接强度和稳定性。
措施
加强线路板制作工艺控制,避免不同导电路径之 间的短路。
断路
原因
线路板制作过程中,导电路径出现断裂或开路现象。
影响
电气连接中断,导致电路功能失效。
措施
加强线路板制作工艺控制,确保导电路径完整无缺。
03
预防和改进措施
Chapter
孔铜不足的预防措施
01
确保孔壁光滑,避 免孔内有毛刺或杂 质。
02
孔铜不足通常是由于PCB制造过程中孔铜沉积不足或电镀不充分所导致。这种缺陷可能导 致电气连接性能下降,甚至在某些情况下可能导致电路板短路或断路。
措施
为避免孔铜不足的问题,可以采取以下措施:确保PCB制造过程中孔铜沉积和电镀环节的 质量控制,加强来料检验和质量控制,以及在后续使用过程中定期检查和维护PCB板。
影响
电气连接不稳定,容易引 发短路或断路。
措施
加强钻孔过程中的质量控 制,确保铜箔完全覆盖钻 孔。
孔铜过度
原因
在沉铜过程中,铜箔过量 沉积在钻孔中,导致孔内 铜箔过厚。
影响
电气连接过于紧密,影响 信号传输质量。
措施
调整沉铜工艺参数,控制 铜箔沉积厚度。
阻焊桥连
原因
阻焊剂涂覆不均匀,导致部分区 域出现桥连现象。
短路
- 1、下载文档前请自行甄别文档内容的完整性,平台不提供额外的编辑、内容补充、找答案等附加服务。
- 2、"仅部分预览"的文档,不可在线预览部分如存在完整性等问题,可反馈申请退款(可完整预览的文档不适用该条件!)。
- 3、如文档侵犯您的权益,请联系客服反馈,我们会尽快为您处理(人工客服工作时间:9:00-18:30)。
PCB制程中金属化孔镀层空洞的成因及改善程 骄 李卫明 刘敏然(广东东硕科技有限公司,广东 广州 510288)摘 要 文章从印制线路板的生产流程和工艺参数等方面,结合切片观察的手段,浅析了金属化孔镀层空洞的形成原因。
研究表明:半固化片的型号、含胶量及填料的比例与芯板质量有很大关联,影响着层压和钻孔工序的板件质量;沉铜和电镀工序的工艺参数、周边辅助设施的工作状况及加工过程中的时效是影响镀层空洞的主要因素。
针对每一个异常点,找到缺陷的形成原因,对工艺流程进行有效的改进,有的放矢的起到预防措施,最终达到改善镀层质量,提高产品的合格率,对提高线路板可靠性具有重要的意义。
关键词 空洞;化学沉铜;电镀;钻孔中图分类号:TN41 文献标识码:A 文章编号:1009-0096(2013)08-0021-03Research on the causes & control of through-holevoids for PCB processCHENG Jiao LI Wei-Ming LIU Min-RanAbstract Voids in plated through-holes are caused by many different processing problems. This paper will show how to identify rim voids by PCB production process & parameter with micro section observation. The results indicate that stronger correlation existed in core board between the proportion of rubber polymer to fi ller and type of PP, which could infl uence the quality of lamination and drill. The primary reason of VPTH formed was by process parameter, the condition of assisting machine and processing time for electroless and electroplate process. The reason of defect was found for every abnormal board. Effective improvement measures not only had a defi nite object in view of prevention measures, but also improved quality and percent of certifi ed products, this measure had the vital signifi cance to improve reliability of printed circuit board.Key words Void PTH; Electroless Copper Plating; Electroplating; Drill现代印制电路板设计要求向高密度、细线条、微孔径的多层板发展,因此金属化孔质量将直接关系到线路板的质量及可靠性,而过孔不通会直接导致成品板的电气互连失败,从而使成品板件由于镀层空洞缺陷而报废。
影响板内孔壁质量的因素很多,印制电路板或多或少的都存在着空洞,IP-6012C-《刚性印制板的鉴定及性能规范》标准3.3.3条规定:对于2级的铜板材,在不多于孔总数5%的孔中,每个孔允许有一个空洞;但对于更高级的3级铜板材,不允许有任何的孔空洞,所以按照行业的标准,虽然2级可以接受部分镀层空洞的板件,但对应高级的3级是不接受镀层空洞的板件。
因此金属化孔品质的好坏,对于品质要求高的印制板来说显得尤为重要。
本文根据我们在该行业积累的大量经验,浅谈影响成品板件镀层品质的因素,研究这些缺陷的形成原因,改善工艺参数,对提高镀层可靠性具有重要的意义。
1 印制电路板PTH孔镀层空洞的成因1.1 层压及相关工序层压工序主要与基材的类型有着紧密的联系。
目前,使用较多的板材包括不同型号的FR-4、PTFE 、PI 、陶瓷基材料等,每种材料都具有特定的加工参数和使用条件。
传统的FR-4材料由于受到T g (玻璃化温度)温度和CTE (热膨胀系数)的影响,在高温高压的条件下,基材内部易形成分层或者微空隙,厂家通常加入一些特殊的填料或具有特殊功能的分子链段,提高T g 温度、降低CTE 系数,改善材料固有的热缺陷,降低加工过程中残余应力。
各种特殊填料的加入,在改变材料特性的同时也增加了相应的加工难度,在真空条件下高温压合,如不控制好加工参数或者内层芯板前处理不良,树脂与内层铜箔的结合不良会对后续的加工埋下隐患。
因此,选择合适的PP 型号、稳定工艺流程和调整适宜的加工参数,在层压工序是改善镀层空洞的主要方法。
1.2 钻孔工序PTH 孔壁质量与钻孔的加工参数有着紧密的关系,钻孔引起毛刺、爆孔、余胶等各种缺陷会提高镀层空洞出现程度。
钻孔时基材的热膨胀会使孔径收缩,孔壁对钻头的摩擦力增大,从而导致钻头在进、退刀时形成了大量的环氧树脂钻污;另外一方面,加工参数的不恰当会导致板件生产过程中,在铜箔与树脂、树脂与玻纤布之间造成“撕裂”的缝隙,后工序加工过程中引起空洞(图1)的缺陷,影响PTH 导通孔的质量。
选择合适的钻头型号以及适宜的加工参数,规范钻头的加工寿命是保证孔壁质量的必要因素之一。
研究表明:随着钻孔转数的提高或采用较细纤维束的基材,可以降低撕裂引起的空洞;规范钻头的寿命、磨次,定期检测钻孔后孔壁的质量,是保证金属化孔无空洞等缺陷的前提。
图1 钻孔时孔未钻穿造成的空洞1.3 孔化工序金属化孔的质量好坏,除了要有好的钻孔质量为前提条件保证外,化学镀铜和电镀铜的质量也密切相关。
对于化学镀铜来说,孔内空洞的产生与下列因素有关:1.3.1 异物堵孔造成的金属化空洞钻孔粉屑残留过多,孔化前处理不净。
产生的原因除改善钻孔条件外,还与沉铜前处理有关,包括刷板参数、去钻污方式及加工参数等。
孔壁余胶及粉屑的未及时去除,由于其“松散”的状态,在孔化和电镀过程中,往往受到外界因素“松动”而脱落离去,从而形成镀层空洞,并随着板件厚径比的增加,这种影响更为明显。
针对这些异常,加工过程中需要定期对刷板机的刷辊、喷嘴的压力及工作状况进行点检和维护,确保板件加工过程中设备运行正常,对于厚径比大于10:1的板件,建议增加线外超声波水洗的方式来提供孔壁的润湿性和排除孔内的异物。
1.3.2 除油、活化、解胶等流程造成的金属化孔空洞除油的目的一方面清除微表面及深孔内的油污,另外一方面改变基材表面的极性,便与吸附钯胶体,因此除油槽的槽液温度、过滤循环搅拌不良等,都得不到良好的电荷转移和清洁的效果,适当的电震和摇摆可以有良好的协同作用。
活化、解胶工艺流程药水浓度、温度以及槽体之间在空气中或者水槽中的停留时间过久,一方面会破坏钯层的致密度,导致沉铜不上,另一方面药水浓度和温度异常造成钯胶体吸附能力变弱导致水解后的钯层薄,在水洗槽或者沉铜槽中,易受到外界的因素脱附开来,引起镀层空洞。
1.3.3 沉铜槽组分、温度等异常造成的镀层空洞(1)化学沉铜是一个自催化氧化还原反应,伴随着晶核的生成和生长过程,两者之间需要一个平衡,当生成大于生长速度时,铜离子堆积速度快,除了沉铜层的厚度较厚外,会有大量的铜原子直接在双电子层区域直接聚集形成“铜粒”,这样镀层的结合力就变差,也比较疏松;当生长速度大于生成速度时,部分区域可能直接没有铜原子的存在,电镀后直接出现镀层空洞的现象。
所以,维持化学反应过程的一个平衡极为重要,这种平衡与沉铜药水的组成、生产过程中的温度、各组分的含量控制有密切的联系。
(2)沉铜到电镀之间的加工时效,由于沉铜层的厚度只有0.25 μm ~ 0.5 μm ,沉铜后的板件在空气中或者水槽中过久,都会造成沉铜层的破坏,影响PTH 孔的电镀效果。
(3)沉铜槽挂篮中的板件摆放方式,目前常见的挂篮卡数为24齿~28齿,对于加工普通的板件来说,装有相同数量的板件时可以满足生产的,但是对于厚板或者盲孔板件来说,一般需要采用间隔装板或时打斜装板;另外板件的在摆放过程中用卡梳固定好,防止由于震动等原因造成板件叠放在一起,挂蓝需要定期的维护检修。
1.3.4 沉铜气泡造成的孔内空洞在沉铜和电镀中很容易产生由气泡引起的镀层空洞,这也是最为常见的缺陷(图2)。
沉铜中的气泡一方面是板件厚径比高,孔口小,残留气泡残留在孔壁中不易排出;另一方面是副产物氢气没有及时排除造成的。
对于该缺陷,考虑从周边设备来着手解决,包括电震强度、摇摆频率,提高孔壁的润湿性等措施来防止该种缺陷的产生。
图2 孔化时气泡造成的沉铜不良1.3.5 特殊材料的沉铜方式目前,线路板都朝着高频高速的方式发展,传统的去钻污及活化方式已不能满足其生产的需求,等离子去钻污及各种特殊的活化剂应用而生。
等离子去钻污是气氛在高压真空的条件下,利用离子高速撞击板材来清洁表面达到去钻污的目的,并且采用氢气来改善板材的亲水性,使材料表面会形成较多亲水基基团,提高孔壁的润湿性,促进交换。
另外,柔性板加工过程中通常需要用到PI 材料,传统的除油调整剂和活化剂不能满足此种材料的生产,会产生大面积的空洞,市场上针对柔性板的活化不上,开发有不同的调整药水,用来改善板材的极性,提高板材的润湿性,增强对活化钯的吸附,改善镀层的可靠性。
1.4 电镀工序金属化孔经过化学沉铜后,会在孔壁形成一层致密均匀的铜镀层,电镀工序产生的空洞主要与加工时效、辅助设备、干膜覆盖等有关。
一般沉铜到电镀的加工时效为4个小时,沉铜后的板件为防止氧化需要浸泡在水槽中,板件在水槽中停留时间过久会造成电镀后“铜粉”和“空洞”的形成。
另外,沉铜层的厚度有限,在预浸槽、水洗槽停留时间超时,进入铜缸中未及时输入电流等,都会造成“空洞”的形成,这主要是沉铜层厚度较薄被咬蚀的关系,因此控制沉铜电镀的时效,跟进板件进槽后的加工状况是工序生产中必须遵守的一个重要环节。
孔壁中气泡的生产,不仅与沉铜有关系,还与电镀有关联,包括外界溢入孔壁的气泡,镀铜/镀锡过程中产生的气泡,不及时的排除,前期残留的气泡会造成镀层空洞,后期产生的气泡会造成镀层凹陷,尤其是高厚径比的板件小孔中很容易残留气泡而影响镀层(图3)。
对于这类的气泡,可通过以下措施来解决:(1)增强孔壁的润湿性;(2)通过摇摆、喷流、鼓气、电震等方式,迫使溶液交换加快,排除孔壁的气泡;(3)铜缸中药水组分、工艺参数的设定与控制。