精益生产--LPS--精益生产的由来
精益生产系统管理概述

精益生产系统管理概述引言精益生产系统是由日本丰田汽车公司所引进并发扬光大的一种生产管理体系。
它的核心思想是通过消除浪费,提高生产效率和质量,从而实现企业的可持续发展。
本文将围绕精益生产系统的概念、原则和应用进行详细介绍,以帮助读者深入了解并灵活运用精益生产系统管理技术。
一、精益生产系统定义精益生产系统(Lean Production System,简称LPS)是一种以供应链为驱动,以价值流为导向,通过消除浪费、流程优化和员工参与等策略,实现生产效率和质量的全面提升的管理方法。
它的核心是通过持续改进来降低生产成本、减少库存、提高交付能力和顾客满意度。
二、精益生产系统原则1.价值流观念精益生产系统强调以顾客为导向,将价值流定义为一系列能够满足顾客需求并使顾客满意的活动。
通过细致的价值流分析,找出生产中的浪费环节,并采取相应措施进行改进。
2. 流程优化流程优化是精益生产系统的核心内容之一。
通过优化流程,减少浪费,提高生产效率和质量水平。
其中包括以下几个方面的内容:•连续流:追求生产过程的顺畅流动,减少停工等待时间,降低库存。
•小批量生产:以小批量生产为目标,减少库存压力,提高灵活性。
•快速交付:追求快速交付产品,减少等待时间,提高顾客满意度。
3. 人员参与精益生产系统强调员工的积极参与和创新意识的发挥。
通过培训和激励机制,激发员工的创造力和工作积极性,实现全员参与,不断改善。
4. 持续改进持续改进是精益生产系统的核心理念之一。
通过PDCA循环(Plan-Do-Check-Act),不断地进行问题分析、解决和改进,使生产过程更加优化和高效。
三、精益生产系统的应用精益生产系统可以应用到各种规模和行业的企业中,包括制造业、服务业和非营利组织等。
下面以制造业为例,介绍精益生产系统在实际应用中的一些常见方法:1. 5S工作法5S工作法是精益生产系统中的一个重要工具,它通过整理、整顿、清扫、清洁和素养的步骤,实现工作环境的改善和生产效率的提高。
LP-精益生产
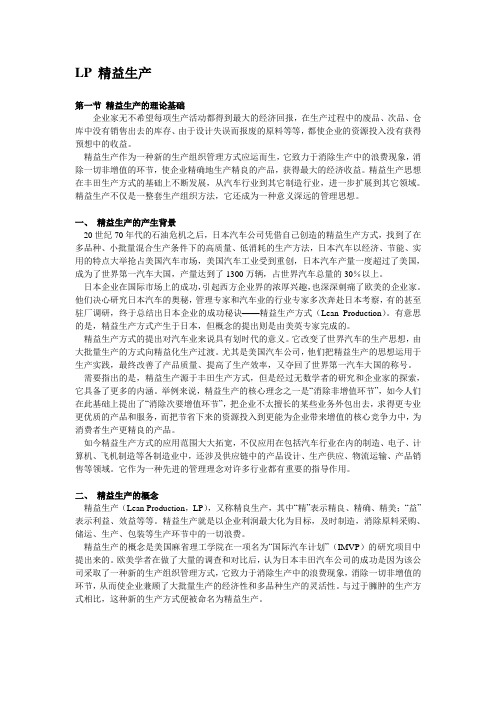
LP 精益生产第一节精益生产的理论基础企业家无不希望每项生产活动都得到最大的经济回报,在生产过程中的废品、次品、仓库中没有销售出去的库存、由于设计失误而报废的原料等等,都使企业的资源投入没有获得预想中的收益。
精益生产作为一种新的生产组织管理方式应运而生,它致力于消除生产中的浪费现象,消除一切非增值的环节,使企业精确地生产精良的产品,获得最大的经济收益。
精益生产思想在丰田生产方式的基础上不断发展,从汽车行业到其它制造行业,进一步扩展到其它领域。
精益生产不仅是一整套生产组织方法,它还成为一种意义深远的管理思想。
一、精益生产的产生背景20世纪70年代的石油危机之后,日本汽车公司凭借自己创造的精益生产方式,找到了在多品种、小批量混合生产条件下的高质量、低消耗的生产方法,日本汽车以经济、节能、实用的特点大举抢占美国汽车市场,美国汽车工业受到重创,日本汽车产量一度超过了美国,成为了世界第一汽车大国,产量达到了1300万辆,占世界汽车总量的30%以上。
日本企业在国际市场上的成功,引起西方企业界的浓厚兴趣,也深深刺痛了欧美的企业家。
他们决心研究日本汽车的奥秘,管理专家和汽车业的行业专家多次奔赴日本考察,有的甚至驻厂调研,终于总结出日本企业的成功秘诀——精益生产方式(Lean Production)。
有意思的是,精益生产方式产生于日本,但概念的提出则是由美英专家完成的。
精益生产方式的提出对汽车业来说具有划时代的意义。
它改变了世界汽车的生产思想,由大批量生产的方式向精益化生产过渡。
尤其是美国汽车公司,他们把精益生产的思想运用于生产实践,最终改善了产品质量、提高了生产效率,又夺回了世界第一汽车大国的称号。
需要指出的是,精益生产源于丰田生产方式,但是经过无数学者的研究和企业家的探索,它具备了更多的内涵。
举例来说,精益生产的核心理念之一是“消除非增值环节”,如今人们在此基础上提出了“消除次要增值环节”,把企业不太擅长的某些业务外包出去,求得更专业更优质的产品和服务,而把节省下来的资源投入到更能为企业带来增值的核心竞争力中,为消费者生产更精良的产品。
【实用资料】精益生产起源简介.doc

精益生产简介精益生产(Lean Production,简称LP)是美国麻省理工学院根据其在“国际汽车项目”研究中,基于对日本丰田生产方式的研究和总结,于1990年提出的制造模式。
目前,在众多的生产管理的新思想、新理论中,精益生产与MRPII(制造资源计划)的影响最为广泛,并进行过大量的实践。
在我国,精益生产与MRPII的应用也正广泛地展开。
此时,深入开展对精益生产与MRPII管理思想内核的研究,正是在实践中进一步有效推进工业工程的基础。
本文全面介绍精益生产。
1.精益生产的历史背景精益生产是起源于日本丰田汽车公司的一种生产管理方法。
其核心是追求消灭包括库存在内的一切“浪费”,并围绕此目标发展了一系列具体方法,逐渐形成了一套独具特色的生产经营管理体系。
1.1管理技术背景二战以后,日本汽车工业开始起步,但此时统治世界的生产模式是以美国福特制为代表的大量生产方式。
这种生产方式以流水线形式生产大批量、少品种的产品,以规模效应带动成本降低,并由此带来价格上的竞争力。
具体而言:在当时,大量生产方式即代表了先进的管理思想与方法。
大量的专用设备、专业化的大批量生产是降低成本、提高竞争力的主要方式。
与此同时,全面质量管理在美国等先进的工业化国家开始尝试推广,并开始在实践中体现了一定的效益。
生产中库存控制的思想(以MRPII思想为主)也开始提出,但因技术原因未能走向实用化。
1.2丰田式生产方式发展的环境当美国汽车工业处于发展的顶点时,日本的汽车制造商们是无法与其在同一生产模式下进行竞争的。
丰田汽车公司从成立到1950年的十几年间,总产量甚至不及福特公司一天的产量。
与此同时,日本企业还面临需求不足与技术落后等严重困难,加上战后日本国内的资金严重不足,也难有大规模的资金投入以保证日本国内的汽车生产达到有竞争力的规模。
此外,丰田汽车公司在参观美国的几大汽车厂之后还发现,在美国企业管理中,特别是人事管理中,存在着难以被日本企业接受之处。
精益生产的起源
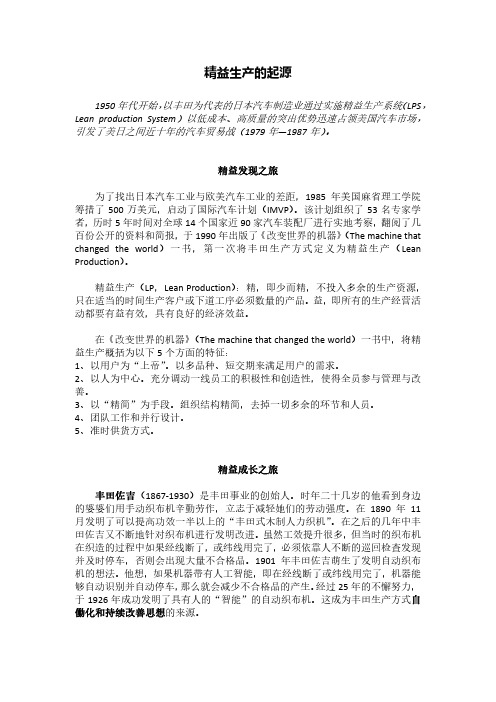
精益生产的起源1950年代开始,以丰田为代表的日本汽车制造业通过实施精益生产系统(LPS,Lean production System)以低成本、高质量的突出优势迅速占领美国汽车市场,引发了美日之间近十年的汽车贸易战(1979年—1987年)。
精益发现之旅为了找出日本汽车工业与欧美汽车工业的差距,1985年美国麻省理工学院筹措了500万美元,启动了国际汽车计划(IMVP)。
该计划组织了53名专家学者,历时5年时间对全球14个国家近90家汽车装配厂进行实地考察,翻阅了几百份公开的资料和简报,于1990年出版了《改变世界的机器》(The machine that changed the world)一书,第一次将丰田生产方式定义为精益生产(Lean Production)。
精益生产(LP,Lean Production):精,即少而精,不投入多余的生产资源,只在适当的时间生产客户或下道工序必须数量的产品。
益,即所有的生产经营活动都要有益有效,具有良好的经济效益。
在《改变世界的机器》(The machine that changed the world)一书中,将精益生产概括为以下5个方面的特征:1、以用户为“上帝”。
以多品种、短交期来满足用户的需求。
2、以人为中心。
充分调动一线员工的积极性和创造性,使得全员参与管理与改善。
3、以“精简”为手段。
组织结构精简,去掉一切多余的环节和人员。
4、团队工作和并行设计。
5、准时供货方式。
精益成长之旅丰田佐吉(1867‐1930)是丰田事业的创始人。
时年二十几岁的他看到身边的婆婆们用手动织布机辛勤劳作,立志于减轻她们的劳动强度。
在1890年11月发明了可以提高功效一半以上的“丰田式木制人力织机”。
在之后的几年中丰田佐吉又不断地针对织布机进行发明改进。
虽然工效提升很多,但当时的织布机在织造的过程中如果经线断了,或纬线用完了,必须依靠人不断的巡回检查发现并及时停车,否则会出现大量不合格品。
精益生产方式的历史发展过程

精益生产方式的历史发展过程精益生产是一种以减少浪费为核心的生产管理方法,它的发展经历了多个阶段。
本文将从精益生产的起源开始,逐步介绍其历史发展过程。
1. 起源精益生产起源于日本的丰田汽车公司。
20世纪50年代,日本汽车工业正处于起步阶段,丰田公司面临着生产效率低下、质量问题频发等困境。
为了改变这种局面,丰田公司邀请美国专家德鲁克来进行生产管理方面的指导。
德鲁克提出了“减少浪费”的理念,这成为了精益生产的核心。
2. 第一阶段:丰田生产方式丰田公司根据德鲁克的理念,开始进行生产流程的优化。
他们提出了“丰田生产方式”,强调通过精确的生产计划、合理的库存控制以及员工的积极参与来提高生产效率。
这一阶段的精益生产注重提高生产效率,减少不必要的浪费。
3. 第二阶段:丰田生产系统随着丰田公司逐渐摆脱了生产效率低下的困境,他们开始深入研究生产流程中的各个环节,并发展出了“丰田生产系统”。
这一阶段的精益生产注重优化生产流程,强调通过标准化、自动化和流程改进来提高生产效率。
丰田生产系统的核心原则是“Just-in-Time”(即时制),即在所需的时间和数量上实现生产和交付。
4. 第三阶段:精益生产精益生产是在丰田生产系统的基础上进一步发展起来的。
这一阶段的精益生产注重提高价值创造能力,将焦点放在满足客户需求和提供高质量产品上。
精益生产强调通过精确的需求预测、灵活的生产计划和快速的交付来实现客户价值的最大化。
5. 当前发展精益生产的理念和方法已经不仅局限于汽车行业,而是被广泛应用于各个领域。
在全球范围内,越来越多的企业开始采用精益生产方式来提高效率、降低成本、提高质量和客户满意度。
同时,随着数字化技术的发展,精益生产也与人工智能、大数据等技术相结合,为企业提供更加智能化和高效化的生产管理解决方案。
总结起来,精益生产方式的历史发展经历了起源阶段、丰田生产方式阶段、丰田生产系统阶段以及当前的精益生产阶段。
这一发展过程不仅改变了丰田公司的生产管理方式,也对全球范围内的企业生产管理产生了深远的影响。
精益生产起源简介
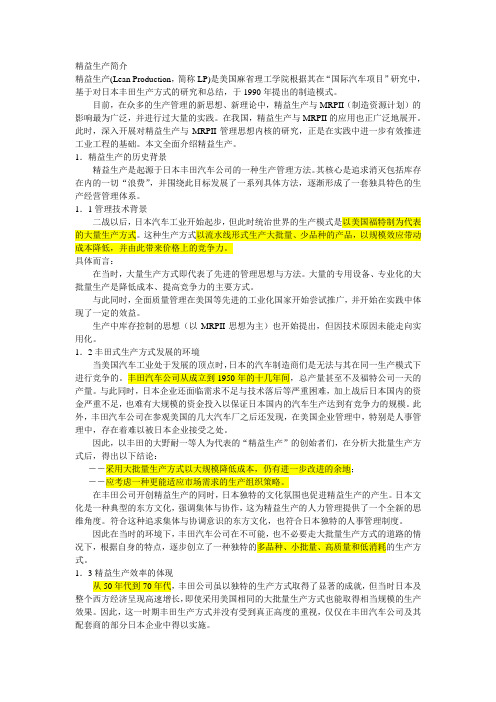
精益生产简介精益生产(Lean Production,简称LP)是美国麻省理工学院根据其在“国际汽车项目”研究中,基于对日本丰田生产方式的研究和总结,于1990年提出的制造模式。
目前,在众多的生产管理的新思想、新理论中,精益生产与MRPII(制造资源计划)的影响最为广泛,并进行过大量的实践。
在我国,精益生产与MRPII的应用也正广泛地展开。
此时,深入开展对精益生产与MRPII管理思想内核的研究,正是在实践中进一步有效推进工业工程的基础。
本文全面介绍精益生产。
1.精益生产的历史背景精益生产是起源于日本丰田汽车公司的一种生产管理方法。
其核心是追求消灭包括库存在内的一切“浪费”,并围绕此目标发展了一系列具体方法,逐渐形成了一套独具特色的生产经营管理体系。
1.1管理技术背景二战以后,日本汽车工业开始起步,但此时统治世界的生产模式是以美国福特制为代表的大量生产方式。
这种生产方式以流水线形式生产大批量、少品种的产品,以规模效应带动成本降低,并由此带来价格上的竞争力。
具体而言:在当时,大量生产方式即代表了先进的管理思想与方法。
大量的专用设备、专业化的大批量生产是降低成本、提高竞争力的主要方式。
与此同时,全面质量管理在美国等先进的工业化国家开始尝试推广,并开始在实践中体现了一定的效益。
生产中库存控制的思想(以MRPII思想为主)也开始提出,但因技术原因未能走向实用化。
1.2丰田式生产方式发展的环境当美国汽车工业处于发展的顶点时,日本的汽车制造商们是无法与其在同一生产模式下进行竞争的。
丰田汽车公司从成立到1950年的十几年间,总产量甚至不及福特公司一天的产量。
与此同时,日本企业还面临需求不足与技术落后等严重困难,加上战后日本国内的资金严重不足,也难有大规模的资金投入以保证日本国内的汽车生产达到有竞争力的规模。
此外,丰田汽车公司在参观美国的几大汽车厂之后还发现,在美国企业管理中,特别是人事管理中,存在着难以被日本企业接受之处。
精益导师考试指南

精益导师考试指南(Lean Production System, 简称LPS)是美国麻省理工学院数位国际计划组织的专家对日本“丰田JIT(Just In Time)生产方式的赞誉之称.起源于50年代的日本丰田汽车公司。
由美国国际汽车计划组织研究人员将之命名为精益生产。
●英文“LEAN”,是“瘦身”的意思。
中文取“精益”,其中“精”表示精良、精确、精美,即少而精;“益”表示利益、效益,即所有经营活动要有益有效,具有经济性。
●精益生产是一种系统的识别和剔除浪费的理念和方法。
●狭义的精益生产是生产系统的精益化。
广义的精益生产已超越了生产系统,就是企业的精益管理思想,精益管理思想的核心就是消灭一切浪费,为客户创造价值。
●精益生产的特点是剔除一切浪费、追求精益求精和尽善尽美,精简是它的核心.●精益生产的五个原则是指价值、价值流、流动、需求拉动、尽善尽美。
●精益生产系统的基础是5S、目视化管理、均衡化生产、料.设备.人力. 场地。
●通过及时生产,实现多品种、小批量的生产,消除生产现场中的无效劳动与浪费,最大限度地获取利润和效益●JIT基本要素:使用小巧、便宜的机器,设备. 逆时钟传送需求拉动定义“标准操作”并实施.(Beat)、“节奏”(Rhythm)或“速度” (Tempo).按节拍生产是精益生产的重要原则之一●节拍是指相继完成两件在制品或产品之间的时间间隔,通常以“秒”为单位,分为客户节拍及生产线节拍●节拍的计算是以客户的需求为基准●节拍计算公式:客户节拍=<净操作时间>/<客户需求量>●对生产线来讲,节拍就是完成一个产品的时间●节拍生产的规则:精益生产线必须按照设定的节拍生产每一个工位的员工都按照设定的相应的节拍生产.每个员工必须熟知自己所在生产线的生产线节拍和操作员节拍并达成节拍设定的生产进度,零件始终处于不停滞、不堆积、不超越,按节拍一个一个的流动的生产方法, 该方式可以消除库存的浪费并且及时发现异常.●所谓拉动生产,就是以客户需求为动力,以“看板”为链条,由后向前层层拉动每道工序的生产,从而达到按时按量提供所需产品。
精益生产简介
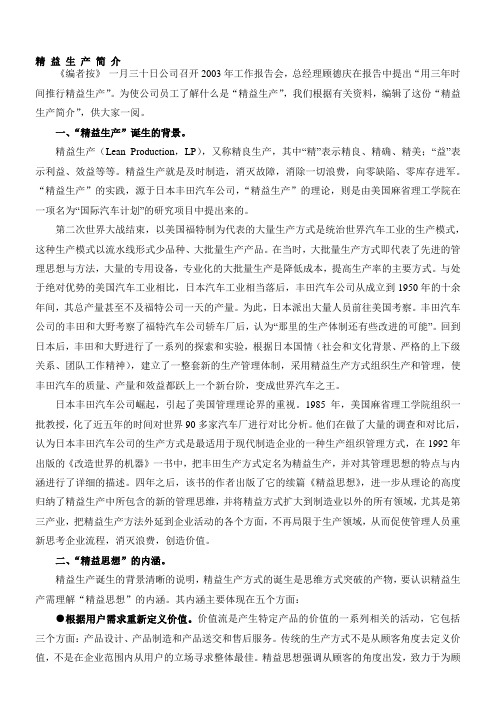
精益生产简介《编者按》一月三十日公司召开2003年工作报告会,总经理顾德庆在报告中提出“用三年时间推行精益生产”。
为使公司员工了解什么是“精益生产”,我们根据有关资料,编辑了这份“精益生产简介”,供大家一阅。
一、“精益生产”诞生的背景。
精益生产(Lean Production,LP),又称精良生产,其中“精”表示精良、精确、精美;“益”表示利益、效益等等。
精益生产就是及时制造,消灭故障,消除一切浪费,向零缺陷、零库存进军。
“精益生产”的实践,源于日本丰田汽车公司,“精益生产”的理论,则是由美国麻省理工学院在一项名为“国际汽车计划”的研究项目中提出来的。
第二次世界大战结束,以美国福特制为代表的大量生产方式是统治世界汽车工业的生产模式,这种生产模式以流水线形式少品种、大批量生产产品。
在当时,大批量生产方式即代表了先进的管理思想与方法,大量的专用设备,专业化的大批量生产是降低成本,提高生产率的主要方式。
与处于绝对优势的美国汽车工业相比,日本汽车工业相当落后,丰田汽车公司从成立到1950年的十余年间,其总产量甚至不及福特公司一天的产量。
为此,日本派出大量人员前往美国考察。
丰田汽车公司的丰田和大野考察了福特汽车公司轿车厂后,认为“那里的生产体制还有些改进的可能”。
回到日本后,丰田和大野进行了一系列的探索和实验,根据日本国情(社会和文化背景、严格的上下级关系、团队工作精神),建立了一整套新的生产管理体制,采用精益生产方式组织生产和管理,使丰田汽车的质量、产量和效益都跃上一个新台阶,变成世界汽车之王。
日本丰田汽车公司崛起,引起了美国管理理论界的重视。
1985年,美国麻省理工学院组织一批教授,化了近五年的时间对世界90多家汽车厂进行对比分析。
他们在做了大量的调查和对比后,认为日本丰田汽车公司的生产方式是最适用于现代制造企业的一种生产组织管理方式,在1992年出版的《改造世界的机器》一书中,把丰田生产方式定名为精益生产,并对其管理思想的特点与内涵进行了详细的描述。
精益生产知识简介

精益生产知识简介一、精益生产的产生及基本概况:1、精益生产的产生------精益生产(lean production, LP)是美国麻省理工学院因政府要求,组织14个国家的专家、学者历时5年对日本丰田汽车公司生产方式的研究,花费500万美元,在一项名为“国际汽车计划”的研究项目中提出来地,他们在做了大量的调查和对比后认为日本丰田汽车公司的生产方式是适用于现代化制造企业的一种生产管理方式,称之为精益生产。
2、精益生产的定义-----精益生产致力于在客户关系、产品设计、供应网络和工厂管理等各个方面全面消除浪费。
其目标是以最少的人员、最低的库存、最短的时间,高效、经济地生产出高质量的产品,对顾客需求做出最迅速的响应。
同时精益生产还可理解为:精益生产就是及时制造;消除一切浪费;努力实现零缺陷;零库存;零故障理想目标。
它综合了大量生产与单件生产方式的优点,力求在大量生产中实现多品种,少批量的“价廉物美”,即高品质低成本生产。
3、精益生产的相关概念:①、精益生产的前身准时化生产:即以最小的成本在准确的时间生产准确的数量的准确产品,这里所有的“准确”都是由客户(包括外部和内部)决定。
用户所关注的正是精益生产要解决的问题,它们是功能质量、价格和交期,对制造商来说就是设计、质量、成本、和交期。
产的核心是消除一切浪费,它的思想基础是“库存是祸根,以人为本”。
②、精益生产常用工具:目视管理(VM)、标准化作业(SOP)、防差错(POKA YOKE)快速换模(SMED)、看板管理(KANBAN)、U型布局、IE工程、多能工、质量控制等。
精益生产工具背后的四项基本原则是:“规范所有活动”、“明确所有客户供应商关系”、“流程简单明确”、“在尽可能低的层次发现并解决问题”向理想状态过渡。
4、精益生产基本概况------精益生产要求企业的各项活动都必须运用“精益思维”(Lean Thinking)。
精益思维的核心就是以最小的资源投入,包括人力、资金、材料、时间和空间,创造出尽可能多的价值,为顾客提供新产品和及时的服务。
精益生产系统
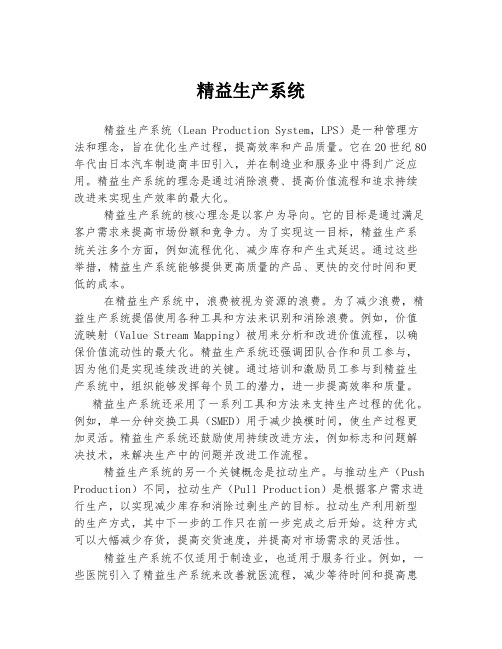
精益生产系统精益生产系统(Lean Production System,LPS)是一种管理方法和理念,旨在优化生产过程,提高效率和产品质量。
它在20世纪80年代由日本汽车制造商丰田引入,并在制造业和服务业中得到广泛应用。
精益生产系统的理念是通过消除浪费、提高价值流程和追求持续改进来实现生产效率的最大化。
精益生产系统的核心理念是以客户为导向。
它的目标是通过满足客户需求来提高市场份额和竞争力。
为了实现这一目标,精益生产系统关注多个方面,例如流程优化、减少库存和产生式延迟。
通过这些举措,精益生产系统能够提供更高质量的产品、更快的交付时间和更低的成本。
在精益生产系统中,浪费被视为资源的浪费。
为了减少浪费,精益生产系统提倡使用各种工具和方法来识别和消除浪费。
例如,价值流映射(Value Stream Mapping)被用来分析和改进价值流程,以确保价值流动性的最大化。
精益生产系统还强调团队合作和员工参与,因为他们是实现连续改进的关键。
通过培训和激励员工参与到精益生产系统中,组织能够发挥每个员工的潜力,进一步提高效率和质量。
精益生产系统还采用了一系列工具和方法来支持生产过程的优化。
例如,单一分钟交换工具(SMED)用于减少换模时间,使生产过程更加灵活。
精益生产系统还鼓励使用持续改进方法,例如标志和问题解决技术,来解决生产中的问题并改进工作流程。
精益生产系统的另一个关键概念是拉动生产。
与推动生产(Push Production)不同,拉动生产(Pull Production)是根据客户需求进行生产,以实现减少库存和消除过剩生产的目标。
拉动生产利用新型的生产方式,其中下一步的工作只在前一步完成之后开始。
这种方式可以大幅减少存货,提高交货速度,并提高对市场需求的灵活性。
精益生产系统不仅适用于制造业,也适用于服务行业。
例如,一些医院引入了精益生产系统来改善就医流程,减少等待时间和提高患者满意度。
在餐饮业中,精益生产系统可以通过提高厨房流程和减少浪费来提高效率和质量。
精益生产的来历
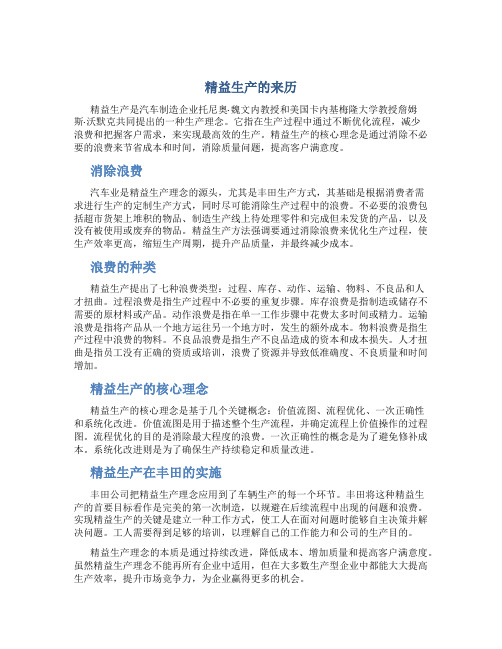
精益生产的来历精益生产是汽车制造企业托尼奥·魏文内教授和美国卡内基梅隆大学教授詹姆斯·沃默克共同提出的一种生产理念。
它指在生产过程中通过不断优化流程,减少浪费和把握客户需求,来实现最高效的生产。
精益生产的核心理念是通过消除不必要的浪费来节省成本和时间,消除质量问题,提高客户满意度。
消除浪费汽车业是精益生产理念的源头,尤其是丰田生产方式,其基础是根据消费者需求进行生产的定制生产方式,同时尽可能消除生产过程中的浪费。
不必要的浪费包括超市货架上堆积的物品、制造生产线上待处理零件和完成但未发货的产品,以及没有被使用或废弃的物品。
精益生产方法强调要通过消除浪费来优化生产过程,使生产效率更高,缩短生产周期,提升产品质量,并最终减少成本。
浪费的种类精益生产提出了七种浪费类型:过程、库存、动作、运输、物料、不良品和人才扭曲。
过程浪费是指生产过程中不必要的重复步骤。
库存浪费是指制造或储存不需要的原材料或产品。
动作浪费是指在单一工作步骤中花费太多时间或精力。
运输浪费是指将产品从一个地方运往另一个地方时,发生的额外成本。
物料浪费是指生产过程中浪费的物料。
不良品浪费是指生产不良品造成的资本和成本损失。
人才扭曲是指员工没有正确的资质或培训,浪费了资源并导致低准确度、不良质量和时间增加。
精益生产的核心理念精益生产的核心理念是基于几个关键概念:价值流图、流程优化、一次正确性和系统化改进。
价值流图是用于描述整个生产流程,并确定流程上价值操作的过程图。
流程优化的目的是消除最大程度的浪费。
一次正确性的概念是为了避免修补成本。
系统化改进则是为了确保生产持续稳定和质量改进。
精益生产在丰田的实施丰田公司把精益生产理念应用到了车辆生产的每一个环节。
丰田将这种精益生产的首要目标看作是完美的第一次制造,以规避在后续流程中出现的问题和浪费。
实现精益生产的关键是建立一种工作方式,使工人在面对问题时能够自主决策并解决问题。
工人需要得到足够的培训,以理解自己的工作能力和公司的生产目的。
精益生产方式的来源、概念与内涵
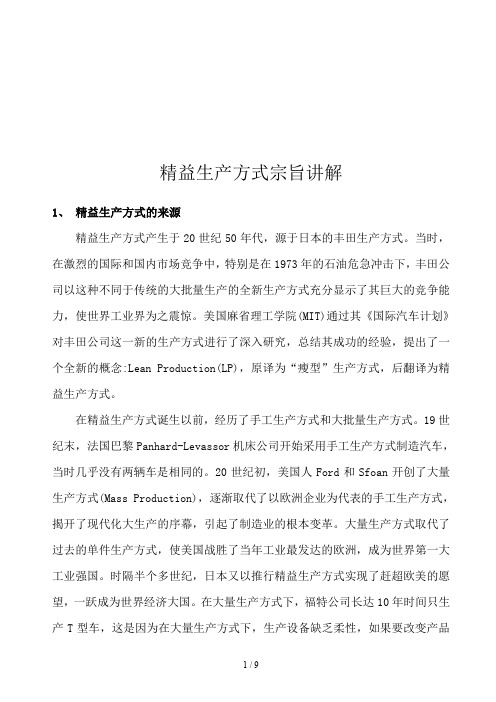
精益生产方式宗旨讲解1、精益生产方式的来源精益生产方式产生于20世纪50年代,源于日本的丰田生产方式。
当时,在激烈的国际和国内市场竞争中,特别是在1973年的石油危急冲击下,丰田公司以这种不同于传统的大批量生产的全新生产方式充分显示了其巨大的竞争能力,使世界工业界为之震惊。
美国麻省理工学院(MIT)通过其《国际汽车计划》对丰田公司这一新的生产方式进行了深入研究,总结其成功的经验,提出了一个全新的概念:Lean Production(LP),原译为“瘦型”生产方式,后翻译为精益生产方式。
在精益生产方式诞生以前,经历了手工生产方式和大批量生产方式。
19世纪末,法国巴黎Panhard-Levassor机床公司开始采用手工生产方式制造汽车,当时几乎没有两辆车是相同的。
20世纪初,美国人Ford和Sfoan开创了大量生产方式(Mass Production),逐渐取代了以欧洲企业为代表的手工生产方式,揭开了现代化大生产的序幕,引起了制造业的根本变革。
大量生产方式取代了过去的单件生产方式,使美国战胜了当年工业最发达的欧洲,成为世界第一大工业强国。
时隔半个多世纪,日本又以推行精益生产方式实现了赶超欧美的愿望,一跃成为世界经济大国。
在大量生产方式下,福特公司长达10年时间只生产T型车,这是因为在大量生产方式下,生产设备缺乏柔性,如果要改变产品品种,不仅耗资巨大,而且要停产1年之久。
而丰田公司以其准时化、高柔性、模块化和并行设计的精益生产方式,开创了以适应消费者多样化的个性需求为中心的生产,迅速崛起于世界汽车工业。
我国卷烟生产也同样经历了手工(或由简单机械设备手动)生产阶段、大量生产阶段。
解放前国内卷烟生产基本属于手工生产阶段,生产力水平很低。
解放以后很长一段时间里,市场供应紧张,各工厂几乎都是采用大批量生产方式,这个时期普遍采用增加设备,增加人员的方法扩大规模,生产效率也不高,因是计划经济时期,产品不愁销路,无改良品种的需要。
精益生产体系介绍

一.何为精益生产精益生产(Lean Production,简称LP)是美国麻省理工学院数位国际汽车计划组织(IMVP)的专家对日本“丰田JIT(Just In Time)生产方式”的赞誉之称,精,即少而精,不投入多余的生产要素,只是在适当的时间生产必要数量的市场急需产品(或下道工序急需的产品);益,即所有经营活动都要有益有效,具有经济性。
精益生产是当前工业界最佳的一种生产组织体系和方式。
精益生产既是一种以最大限度地减少企业生产所占用的资源和降低企业经管和运营成本为主要目标的生产方式,同时它又是一种理念,一种文化。
实施精益生产就是决心追求完美的历程,也是追求卓越的过程,它是支撑个人与企业生命的一种精神力量,也是在永无止境的学习过程中获得自我满足的一种境界。
其目标是精益求精,尽善尽美,永无止境的追求七个零的终极目标。
精益生产方式的优越性及其意义与大量生产方式相比,日本所采用的精益生产方式的优越性主要表现在以下几个方面:1. 所需人力资源--无论是在产品开发、生产系统,还是工厂的其他部门,与大量生产方式下的工厂相比,均能减至1/2;2. 新产品开发周期--可减至l/2或2/3;3. 生产过程的在制品库存--可减至大量生产方式下一般水平的1/10;4. 工厂占用空间--可减至采用大量生产方式工厂的1/2;5. 成品库存--可减至大量生产方式工厂平均库存水平的1/4;6. 产品质量--可提高3倍;精益生产经管方法上的特点(1)拉动式(pull)准时化生产(JIT)--以最终用户的需求为生产起点。
--强调物流平衡,追求零库存,要求上一道工序加工完的零件立即可以进入下一道工序。
--组织生产线依靠看板(Kanban)的形式。
即由看板传递工序间需求信息(看板的形式不限,关键在于能够传递信息)。
--生产中的节拍可由人工干预、控制,保证生产中的物流平衡(对于每一道工序来说,即为保证对后工序供应的准时化)。
--由于采用拉动式生产,生产中的计划与调度实质上是由各个生产单元自己完成,在形式上不采用集中计划,但操作过程中生产单元之间的协调则极为必要。
精益生产的历史概述

服务业
餐饮业:通过减少浪费、提高效率、优化服务流程等方式提高顾客满意度 零售业:通过减少库存、提高陈列效果、优化购物体验等方式提高销售额 医疗行业:通过减少等待时间、提高诊断准确率、优化医疗流程等方式提高医疗服务质量 教育行业:通过减少资源浪费、提高教学效果、优化教育流程等方式提高教育质量
起源:20世纪40年代
精益生产概念提出:1986 年
精益生产的发展:持续改进 和全球推广
起源国家
日本 美国 欧洲 中国
精益生产的发展历程
初步发展阶段
初步发展阶段的时间和背景
初步发展阶段的成果和影响
添加标题
添加标题
初步发展阶段的代表企业
添加标题
添加标题
初步发展阶段面临的挑战和困难
成熟发展阶段
精益生产方法在全球范围内 推广
持续改进
通过不断优化生产流程、提 高生产效率和质量来降低成 本
精益生产的核心思想之一是 持续改进
强调全员参与,鼓励员工提 出改进意见
持续改进是精益生产不断发 展的动力源泉
精益生产的应用领域
制造业
精益生产在制造业中的应用 制造业中的浪费与精益生产 精益生产在制造业中的优势 制造业中实施精益生产的案例
添加项标题
全球化发展:加强国际合作和交流,引进国际先进技术和经验, 推动精益生产的全球化发展,提高企业国际竞争力。
可持续性精益生产
绿色制造和可持 续发展
精益生产与可持 续性相结合
未来趋势:数字 化、智能化和绿 色化
实现可持续性精 益生产的途径和 措施
YOUR LOGO
THANK YOU
汇报人: 汇报时间:20X-XX-XX
提高效率
减少浪费:精益生产的核心思想之一是消除生产过程中的浪费,包括时间、人力、材料等方面 的浪费。
精益生产的由来
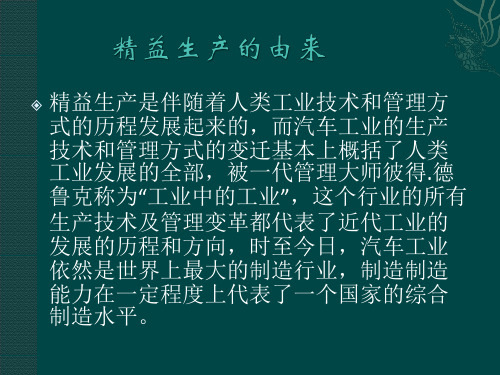
美国
-1896年杜里埃兄弟制造 并销售了13辆四轮汽车
-1908年共有485家汽车 制造商
-1914年福特汽车实现了 汽车流水线生产
-1928年通用公司雪佛兰 汽车年产量达到120万辆
丰田
-1896年丰田汽车的创始人丰田佐 吉刚刚发明了“丰田式木制织机”
-1930年丰田喜一郎刚刚开始研究 开发汽车发动机
在北美的日 本企业
其他
在北美的美 国企业
0.2
1.6
2.9
60.0
65.0
82.3
5.7
9.1
7.8
4.1
4.9
12.9
16.8
21.2
25.1
69.3
71.3
17.3
11.9
8.7
67.1
380.3
370.0
46.4
61.6
1.4
0.4
5.0
4.8
11.7
3.0
2.7
0.9
整个欧洲
2.0 97.0 7.8 14.4 36.2 0.6 14.8 173.3 0.4 12.1
丰田生产系统(TPS) •JIT生产(按客户需求品种和数量准时生产) •拉动生产 •强调生产数量和库存数量与市场匹配 •按照客户需求定制产品
二十世纪初以福特为代表的北美和欧洲汽 车大批量生产方式已经非常成熟
日本汽车业在研究了美国汽车大批量生产 生方式后,结合自己的情况,利用自己的 生产方式,不断赢得更多的市场份额
理念一 ———— 零浪费
所有不必要的浪费都能消除 简而言之,完美的目标
22
对七个“零”目标理解:
☆ 零切换
☆ 零库存
零 7个“
精益生产起源简介
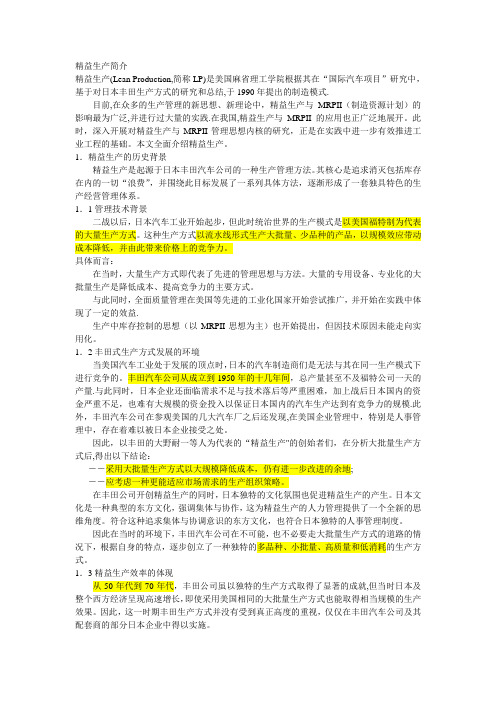
精益生产简介精益生产(Lean Production,简称LP)是美国麻省理工学院根据其在“国际汽车项目”研究中,基于对日本丰田生产方式的研究和总结,于1990年提出的制造模式.目前,在众多的生产管理的新思想、新理论中,精益生产与MRPII(制造资源计划)的影响最为广泛,并进行过大量的实践.在我国,精益生产与MRPII的应用也正广泛地展开。
此时,深入开展对精益生产与MRPII管理思想内核的研究,正是在实践中进一步有效推进工业工程的基础。
本文全面介绍精益生产。
1.精益生产的历史背景精益生产是起源于日本丰田汽车公司的一种生产管理方法。
其核心是追求消灭包括库存在内的一切“浪费”,并围绕此目标发展了一系列具体方法,逐渐形成了一套独具特色的生产经营管理体系。
1.1管理技术背景二战以后,日本汽车工业开始起步,但此时统治世界的生产模式是以美国福特制为代表的大量生产方式。
这种生产方式以流水线形式生产大批量、少品种的产品,以规模效应带动成本降低,并由此带来价格上的竞争力。
具体而言:在当时,大量生产方式即代表了先进的管理思想与方法。
大量的专用设备、专业化的大批量生产是降低成本、提高竞争力的主要方式。
与此同时,全面质量管理在美国等先进的工业化国家开始尝试推广,并开始在实践中体现了一定的效益.生产中库存控制的思想(以MRPII思想为主)也开始提出,但因技术原因未能走向实用化。
1.2丰田式生产方式发展的环境当美国汽车工业处于发展的顶点时,日本的汽车制造商们是无法与其在同一生产模式下进行竞争的。
丰田汽车公司从成立到1950年的十几年间,总产量甚至不及福特公司一天的产量.与此同时,日本企业还面临需求不足与技术落后等严重困难,加上战后日本国内的资金严重不足,也难有大规模的资金投入以保证日本国内的汽车生产达到有竞争力的规模.此外,丰田汽车公司在参观美国的几大汽车厂之后还发现,在美国企业管理中,特别是人事管理中,存在着难以被日本企业接受之处。
- 1、下载文档前请自行甄别文档内容的完整性,平台不提供额外的编辑、内容补充、找答案等附加服务。
- 2、"仅部分预览"的文档,不可在线预览部分如存在完整性等问题,可反馈申请退款(可完整预览的文档不适用该条件!)。
- 3、如文档侵犯您的权益,请联系客服反馈,我们会尽快为您处理(人工客服工作时间:9:00-18:30)。
二次世界大战时美国人在太平洋战场上击败了日本,而日本全心的模仿了美国,以至于美国人出专 用资金和派遣大批的学者研究日本
5/14/2015
7
精益生产方式的5个特征
工厂组织、产品设计、供货环节、顾客和企业管理;理解成对外以用户为上帝,对内以“人”为中
心,在组装机构上以“精简”为手段,在工作方法上采用“Team Work”(综合工作组)和并行设计
制造成本组成
利润Profit 行政管理费用 G&A
Direct Material 直接材料费用 Direct labor 直接人工費用 Indirect 间接費用
价格
总成本 Total Cost
Cost of Goods Sold
PRICE
制造成本
企业的经营理念
可分为三种 成本中心型 、售价中心型和利润中心型 1.成本中心型 以计算或实际的成本为中心,加上预先设定好的利润而得出的售价,这种经营理念称之为成本中 心型。 售价=成本+利润 例如:生产成本100元,利润设定20元那么售价就为120元。这是供不应 求时,垄断产品,例如:油、电、气、通信等甚至火车票都是,这个也是用文化大革命时期计划经 济 2.售价中心型 在供大于求是,以售价为中心,当市场降低的时候利润也随之降低。 利润=售价-成本 例如:目前小挖供不应求时,我们说多少就是多少,可是到今天济宁遍地都 是小挖,那么有些缺乏改善和竞争力的企业,采用降价,那么成本不变的情况下,利润就降下来了 。慢慢降降,当售价接近或是低于成本的时候,企业就走不动了,下一步面临的将是停产 3.利润中心型 以利润为中心,当市场售价降低时,成本也必须降低,使获得的利润不会减少 即,成本=售价-利润 这是现代企业追寻的目标。 其实数学角度来看这些都是一样的,但是理念的不同,最终的结果却大相径庭。
人员组建的做功能设计组,对产品的开发和生产具有很强的指导和集成能力。综合负责的一个产品
型号的开发和生产,包括设计、工艺设计、编制预算、材料购置、生产部准备及投产等方面,并根 据实际情况调整原有对计划和设计。
5.准时供货 最小的库存,最少的在制品
6.“零”缺陷 对质量问题的“零”容忍,最低的成本、最好的质量、无废品、零库存与产品多样
单件手工生产
1776
1920
1950
1990
(年份)
第一次工业革命 18世纪60年代-19世纪70年代;第二次工业革命—20世纪初 这个阶段都隶属于到批量生产方式,这个历史上我们都学过
5/14/2015
5
丰田生产模式(TPS,Toyota Production System)
丰田生产方式是由丰田公司的第一任总经理丰田喜一郎根据日本市场的需求创造出来的,经丰田公 司原总经理大野耐一在近20年得以完善的生产方式。主要是二战以后 ,日本经济萧条,生产效率 低下,日本的汽车行业生产效率只有美国的1/9—1/8要想发展不可能全面引进美国的设备,丰田喜 一郎引进了福特的传送带技术,加以改造,而后来大野耐一根据美国的自由超市的启迪,发明了拉 动式生产同时开发了看板等一系列的管理工具。因此早期的大野管理模式。直到1962年才被正式 命名为TPS,到1974年才公布于世。
3.以“精简”为手段 去掉一切多余环节,将层次细分工,横向打破部门障碍,管理模式平行网络,减
少非直接员工作业,采用管理工具最大限度的减少库存,减少场所、设备等,减少工艺复杂性,提 供多样产品。
5/14/2015
8
4. Team Work和并行设计 精益生产强调的是以Team Work工作方式的并行设计。是由各部门专业
精——少而精 ,不投入多余的生产要素,只要在适当的时间生产必要
数量的市场急需产品(或是下一道工序急需的产品)
益——所有经营活动都要有效有益,具有经济效益
5/14/2015
*接下来就是精益生产的发展史
4
精益生产的发展其实社会生产方式的演变
1990 1955 1913
精益生产
丰田生产方式
大批量生产方式
5/14/2015
利润 售 价 成 本
利润
成 本
售 价
1. 成本型:售价= 成本 + 利润
利润
售 价
3.利润型.:成本= 售价—利润
成 本
5/14/2015
2.售价型:利润= 售价—成本
14
丰田的管理模式 很多都源于日本的生活我们这一代是看着《蜡笔小新》长大的,里面的很多故事情节还有日本大地 震以后日本人的有序安置等
5/14/2015
6
丰田生产模式 向精益生产模式的演变
到20世纪80年代末—美国的市场份额被日本慢慢吞噬,这样很多的美国人就去研究日本的经济,并
尝试借鉴。1985年美国麻省理工学院—制定了-{国际汽车计划}-用了近5年53位专家和学者对14个国
家90家汽车装配厂实地考察,对比分析后,1990年出版了《改变世界的机器》将丰田模式定名为: 精益生产方式,这里将丰田生产模式从生产制造领域扩展到产品研发、协作配套、销售服务、财务 管理等各个领域,贯穿企业生产经营活动的全部过程。(熟悉汽车的都知道目前的销售冠军是通用,
最盈利的是丰田,财务管理成本最低的汽车制造业)
5/14/2015
3
什么是精益生产 精益生产(Lean Production System) :是通过系统结构、人员组织、 运行方式和市场等方面的变革,是生产系统能够很快的使用用户的需 求的不断变化,并能使一切生产过程中取用、多余的东西被简化,最
终达到包括市场供销在内的生产各方面最好的结果。
(我们在做想要一个详细的定义,这个定义是我们国人北京航空航天大学的一个教授给 定义的,我们理解下面的就行)
,在供货方式上采用“JIT”方式,在最终目标方面“零缺陷”
1.以用户为上帝 生产的东西就是销售给客户的 , 多产品面向不同客户优良的品质、快速的交货、优质 的服务 2.以“人”为中心 人是企业的主体,所有的活动都有人为展开,积极发挥员工的积极性和创造性。管 理层下放部分权利,使人人有权,人人有责(现在中央都进行权利下放了),满足员工的学习新知 识和实现价值的愿望,一定形成具有竞争意识的的企业文化团队。催进度忙的一团糟 不合格品就像水中的葫芦此起彼伏 新员工老是出问题 人手从来不够用 物料随处可见却找不到自己想要的 生产效率一直上不去
不要着急!我们一 起分析。来吧!
5/14/2015
2
不管当前如何,部门里的人都会说一句 “忙”,可是等你要结果的时候,他还是 一句很效率的话“忙,还没有出来
5/14/2015
10
第二章 精益生产基本思想
1、生产成本的真谛
成本!成本!还是成本!!!! 效率!效率!还是效率!!!! 市场竞争的激烈与产品同质化压力,制造型企 业要获取生存空间,降低成本成为主要渠道。
无论是什么样的企业,都是以盈利为目的。那什么是盈利呢?在商业上,盈利是只对 购进的商品以购进价格加上一定比率进行的销售,这个比率即是商人的盈利;我们 制造业的赢利是指购进生产加工的原材料,用自己的继续设备,雇佣工人进行生产加工 ,使原材料的附加值在生产中增值,让后卖给消费者,以获取生产过程中的增加部分 要想赢利有两种方法 1.提高产品的销售价格 2.降低产品的生产成本
性。这是每一家企业最求的目标。
(到这里是不是打消掉一些人心中的疑问,精益生产不就是生产中的事情吗,跟我们非生产部门有 什么管理呢?如果到这里你的疑问还不能消除,那看下面的)
5/14/2015
9
生产方式的特点比较
生产方式特点比较 项目 手工生产方式 大批量生产方式 精益生产方式 产品特点 完全按照顾客要求 标注化、产品单一 品种多样化、系列化 设备和工装 零活、便宜 专用、高效、昂贵 柔性高、效率高 作业分工与 粗略、丰富 细致、简单、重复 ∩粗略、多技能、丰富 作业内容 对操作工人 懂设计制造、有较 不需要专业技能 多技能 的要求 高操作技能 库存水平 高 高 低 制造成本 高 低 更低 产品质量 低 高 更高 所适应的市 极少量需求 物质缺乏、供不应求 买方市场 场时代