锻件毛坯计算
机械制造工艺学毛胚尺寸确定(详解)

确定毛胚类型及制造方法毛胚的种类和制造方法常用的毛胚种类:铸件和锻件。
铸件毛胚,在成批生产条件下,采用砂型铸造,机器造型。
金属模造型。
锻件,可承受冲击载荷、交变载荷,在成批生产条件下,采用锻模。
加工余量的分类1、总余量和工序余量总余量是指某一表面毛胚尺寸与零件设计尺寸之差。
工序余量是指每道工序切除的金属层厚度,即相邻两道工序尺寸之差。
2、单边余量和双边余量工序余量有单边余量和双边余量之分。
对于非对称表面,工序余量是单边的,称单边余量。
对于外圆和内圆这样具有对称结构的对称表面,工序余量是双边的,称双边余量,即指相邻两工序的直径尺寸之差。
3、最大余量和最小余量由于各工序尺寸都有公差,所以各工序实际切除的余量值是变化的,因此工序余量有公称余量、最大余量、最小余量之分。
相邻两工序的基本尺寸之差即是公称余量。
公称余量的变化范围称为余量公差。
工序尺寸公差一般按“入体原则”标注。
即对被包容尺寸(轴径),上偏差为0,其最大尺寸就是基本尺寸;对包容尺寸(孔径、槽宽),下偏差为0,其最小尺寸就是基本尺寸。
一、铸件毛胚的余量铸件的尺寸公差与机械加工余量加工余量RMA:A、B、C、D、E、F、G、H、J、K共十级,其中常用的为C-K。
公差等级:CT1-CT16,常用的为CT4-CT13。
成批生产铸件机械加工余量等级注:第一行为单边余量,第二行为双边余量。
铸件公差及公差带公差带位置:对称标注最小圆角半径(mm)(1)铸件壁部连接处的内转角应有铸造圆角。
计算时热裂性较大的合金取较大值。
(2)算出数值后,应选取与其接近的机械制造业常用的标准尺寸(详见GB2822-81)。
为便于制造,半径应尽可能统一。
例如,对于砂型及金属型铸件,一般统一用R3或R5,对压铸件用R1或R2。
铸造最小孔径表3-19 起模斜度(根据JB/T 5105-91)用二、锻件毛胚的余量选择毛胚该零件材料为45钢。
由于该拨叉在工作过程中要承受冲击载荷,为增强拨叉的强度和冲击韧性,获得纤维组织,以使金属纤维尽量不被切断,毛胚选用锻件。
锻造模具设计说明书
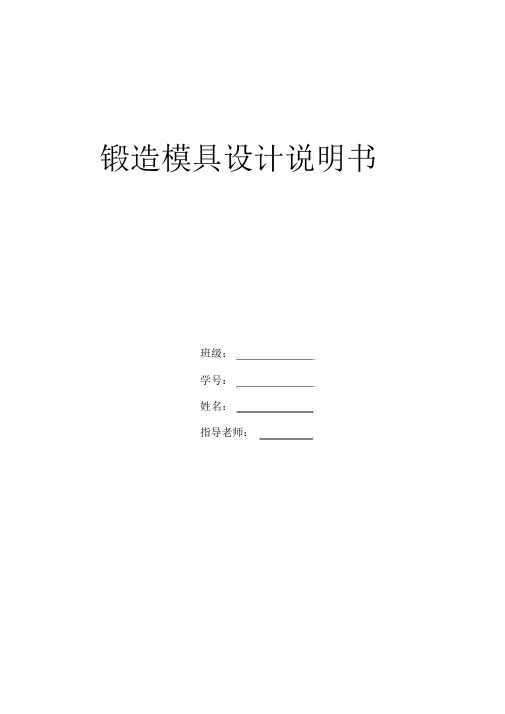
锻造模具设计说明书班级:学号:姓名:指导老师:目录1、绘制冷锻件图 (2)2、计算锻件主要参数 (3)3、确定锻锤吨位 (3)4、确定毛边槽形状和尺寸 (4)5、确定终锻型槽 (4)6、设计预锻型槽 (4)7、绘制计算毛坯图 (6)8、制坯工步选择 (8)9、确定下料尺寸 (8)9.1 坯料截面积 (8)9.2 坯料直径 (8)9.3 坯料体积 (9)9.4 坯料长度: (9)10、制坯型槽设计 (9)⑴滚挤型槽设计 (9)⑵拔长型槽设计 (10)11、锻模结构设计 (12)12、拔叉件模锻工艺流程 (12)13、附录 (13)参考文献 (14)1、绘制冷锻件图零件为接线盘拨叉,是汽车的主要零件之一,工作时在高速下运转,工作条件比较繁重,绘制锻件图过程如下:(1)确定分模位置根据零件形状,采用上下对称的直线分模。
(2)确定公差和加工余量估算锻件质量约为0.4kg,材料为45钢,密度7.85g/cm3,材质系数为M1 。
锻件的形状复杂系数:SW锻=630,为 4 级复杂系数S4。
W外廓包容=0.1518.3 3.4 8.4 7.85拔叉冷锻件图由有关手册查得:高度公差为0.6mm ;长度公差为0.9 mm;宽度公1.4 mm 1.9 mm差为 1.0.57mm mm。
(3)模锻斜度零件图上的技术条件已注明模锻斜度为7 。
(4)圆角半径锻件高度余量为 0.75+0.4=1.15mm;则需倒角的叉内圆角半径为 1.15+2=3.15mm;取 3mm,其余部位的圆角半径取1.5mm。
(5)技术条件:2、计算锻件的主要参数(1)锻件在平面上的投影面积 8000mm2 ;(2)锻件周边长度为 576mm;(3)锻件体积为 80255mm3 ;(4)锻件质量为 0.63Kg 。
3、确定锻锤吨位总变形面积为锻件在平面上的投影面积与毛边面积之和,参考表 4-14 按 1t 模锻锤毛边槽考虑,假定毛边桥部宽度为23mm,总面积 F=8000+576*23=21248mm 2,按双作用模锻锤吨位确定的经验公式 G=(3.5~6.3)kF 确定锻锤吨位,取较大的系数 6.3,取k=1.0,于是G=6.3* 1.0* 212.48=1338Kg选用 1.5t 锤。
铸造、热处理、锻造工艺基础

5.2锻造比 • 锻造比是锻造时金属变形程度的一种表示方法。 锻造比以金属变形前后的横 断面积的比值来表示。不同的锻造工序,锻造比的计算方法各不相同。 • 1、拔长时,锻造比为y=F0/F1或y=L1/L0 • 式中F0,L0—拔长前钢锭或钢坯的横断面积和长度; • F1 ,L1—拔长后钢锭或钢坯的横截面积和长度。 • 2、镦粗时的锻造比,也称镦粗比或压缩比,其值为 • y=F1/F0或y=H0/H1 • F0, H0—镦粗前钢锭或钢坯的横截面积和高度; • F1, H1—镦粗后钢锭或钢坯的横截面积和高度。
三箱造型浇注位置和分型面
5/
2.3浇注位置选择原则
(1)铸件的重要加工面应朝下或侧立。因铸件的上表面容易产生砂眼、气孔、 夹渣等缺陷,组织也不如下表面致密; (2)铸件的大平面应朝下。大平面朝上容易产生夹砂缺陷 (3)为防止铸件薄壁部分产生浇不足或冷隔缺陷,应将面积较大的薄壁部分 置于铸型下部或使其处于垂直或倾斜的位置; (4)对于容易产生缩孔的铸件,应使厚的部分放在铸型的上部或侧面,以便 在铸件厚壁处直接安置冒口,使之实现自下而上的定向凝固。
两组数 铸铁选用
13/
4.1 PROCAST仿真简介 • Procast是为评价和优化铸造工艺与铸造产品而开发的专业CAE软件 • Procast是所有铸造模拟软件中集成化程度最高的 • 配备了功能强大的数据接口和自动网格划分工具 • 全部模块化设计,适合任何铸造过程的模拟 • 采用有限元技术,是目前唯一能对铸造凝固过程进行热——流动——应力完
24/
5.4锻造术语 • 锻件重量:锻件毛坯的实际重量 • 飞边重量:锻造过程中外轮廓分模面处多余的材料 • 料芯重量:锻造过程中内孔多余的材料 • 火耗重量: 锻件在锻打过程中的热损耗 • 下料重量(切料重量):锻打一件锻件所需要的钢坯重量 • 材料消耗定额:锻打一件锻件所需要的钢材消耗总重量
第五节、制坯工步的选择及制坯工步模膛的设计
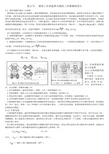
第五节、 制坯工步的选择及制坯工步模膛的设计1.1 圆饼类锻件制坯工步选择圆饼类(l ≈b ≈h 或l ≈b >h)锻件一般使用镦粗制坯,形状复杂的宜用成形镦粗制坯。
制坯的目的是为了避免终锻时产生折叠,还兼有除去氧化皮从而提高锻件表面质量和提高锻模寿命的作用。
为此确定盘形锻件中间坯料尺寸时,应选择恰当的d 和高度h ,否则会影响锻件成形效果,还可能出现充填不满或产生环状裂纹。
例如锻造套环类锻件,若制坯直径d 与锻件轮辐直径d 2的比值等于1,当锤击猛烈时,金属由中心向四周迅速外流,在冲头附近形成内凹,金属与轮缘模壁及模底接触后,便产生回流,结果在轮缘内侧转角处形成环状折纹(图6-37)。
当R 2减小或d 2/d 3减小,更能促使环状折纹的形成。
所以,对套环类锻件,中间坯料直径应为d=,即d 2<d <d 3。
对于齿轮类锻件,中间坯料尺寸应视轮毂高度尺寸大小分两种情况确定:1. 轮毂较矮的锻件。
这类锻件主要是要防止轮毂和轮缘过渡区产生折叠。
因此,中间坯料直径d 应在轮辐外径D 2和轮缘外径D 1之间,即D 2<d <D 1。
2. 轮毂较高的锻件。
当轮毂较高且又有较宽的轮缘和较深的内孔时,一方面要保证轮毂成形,另一方面又要防止产生折叠,中间坯料直径应在D 2<d <范围内。
对于轮毂高且有内孔的锻件(图6-38),为保证锻件充填饱满,并便于坯料在终锻型槽中放平稳,宜用成形镦粗,中间坯料尺寸应符合下列条件:>H 1 ≤D 1 ≤d 02.1 长轴类锻件制坯工步选择2.1.1 长轴类锻件的制坯工步长轴类(l >b ≥h )锻件成形一般要采用拔长、滚挤、弯曲、卡压、成型等制坯工步,以及预锻、终锻和切断工步。
1. 直长轴线锻件,通常采用拔长、滚挤、卡压、成型等制坯工步。
2. 弯曲类锻件,制坯工步与直长轴线类锻件相同,但需增加一道弯曲工步。
3. 带枝芽的长轴件,这类锻件所用制坯工步大致与前两类锻件相同,但须增加一道成型制坯工步。
锻件成本的构成及其计算
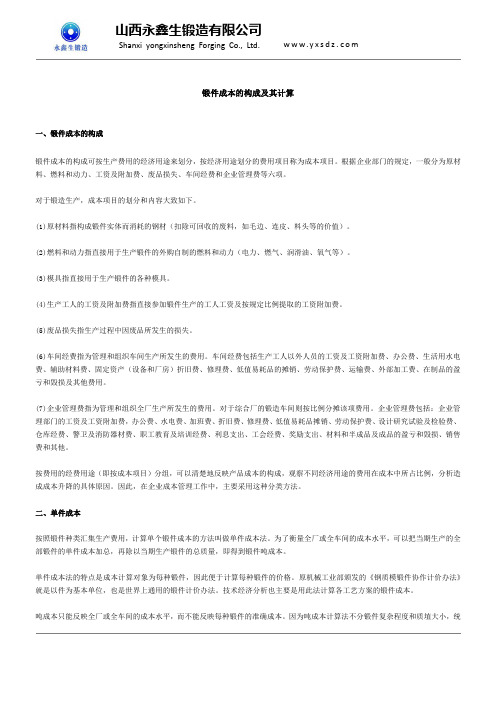
锻件成本的构成及其计算一、锻件成本的构成锻件成本的构成可按生产费用的经济用途来划分,按经济用途划分的费用项目称为成本项目。
根据企业部门的规定,一般分为原材料、燃料和动力、工资及附加费、废品损失、车间经费和企业管理费等六项。
对于锻造生产,成本项目的划分和内容大致如下。
(1)原材料指构成锻件实体而消耗的钢材(扣除可回收的废料,如毛边、连皮、料头等的价值)。
(2)燃料和动力指直接用于生产锻件的外购自制的燃料和动力(电力、燃气、润滑油、氧气等)。
(3)模具指直接用于生产锻件的各种模具。
(4)生产工人的工资及附加费指直接参加锻件生产的工人工资及按规定比例提取的工资附加费。
(5)废品损失指生产过程中因废品所发生的损失。
(6)车间经费指为管理和组织车间生产所发生的费用。
车间经费包括生产工人以外人员的工资及工资附加费、办公费、生活用水电费、辅助材料费、固定资产(设备和厂房)折旧费、修理费、低值易耗品的摊销、劳动保护费、运输费、外部加工费、在制品的盈亏和毁损及其他费用。
(7)企业管理费指为管理和组织全厂生产所发生的费用。
对于综合厂的锻造车间则按比例分摊该项费用。
企业管理费包括:企业管理部门的工资及工资附加费,办公费、水电费、加班费、折旧费、修理费、低值易耗品摊销、劳动保护费、设计研究试验及检验费、仓库经费、警卫及消防器材费、职工教育及培训经费、利息支出、工会经费、奖励支出、材料和半成品及成品的盈亏和毁损、销售费和其他。
按费用的经费用途(即按成本项目)分组,可以清楚地反映产品成本的构成,观察不同经济用途的费用在成本中所占比例,分析造成成本升降的具体原因。
因此,在企业成本管理工作中,主要采用这种分类方法。
二、单件成本按照锻件种类汇集生产费用,计算单个锻件成本的方法叫做单件成本法。
为了衡量全厂或全车间的成本水平,可以把当期生产的全部锻件的单件成本加总,再除以当期生产锻件的总质量,即得到锻件吨成本。
单件成本法的特点是成本计算对象为每种锻件,因此便于计算每种锻件的价格。
锻模设计(含实例)

继续压缩至上下模接触即打靠。
变形仅发生在分模面附近的区域内
,处于最强的三向压应力状态,变
形抗力也最大。此阶段的H 压下量小
16
于2mm,它消耗的能量却占总能量
H
17
二、终锻模膛设计
1、模膛尺寸计算
热锻件图依据冷锻件图绘制。
热锻件图上尺寸比冷锻件图
中尺寸加大一个收缩率,
即 Ll(1%)
式中:δ—终锻温度下的
主要内容是绘制热锻件图和确定飞 边槽形式与尺寸。
边槽主要起排泄和容纳多余金属
作用。
充填模膛的阻力作用相对次要。
锻件高度由压机行程保证。上下分 模面间保留一定间隙,不发生碰撞 。
间ቤተ መጻሕፍቲ ባይዱ大小根据飞边槽高度而定。
H
47
2)预锻工步设计
预锻工步图根据终锻工步图设计。总的原则是使预锻后
的坯料尽可能以镦粗方式进行。
dmin —计算毛坯的最小直径; d拐 —杆部与头部交接处的直径:
说明:
d拐1.13h拐M
α 值越大,流向头部的金属体积越多;
β 值越大,金属沿轴向流动的距离越长;
K 值越大,表明杆部锥度大,小头和杆部金属过剩;
G 值越大,制坯难度加大。
H
36
(4) 根据繁重系数确定制坯工序的初步 方案
长轴类锻件可根据计 算出的繁重系数在右示 经验图表中查出制坯工 序的初步方案,再依据 生产试验修改确定。
H
43
东风汽车公司锻造厂用的热模锻压力机吨 位主要有1200、800、400、200MN(1MN =106 N)等。
2、平锻机吨位 经验公式:
F = 57.5kA,kN 。
式中
k —材料系数。 取 k = 1.0~1.3;
锻造毛坯放量

中华人民共和国冶金工业部部标准YB3213—80水压机锻件的余量与公差北京(1980)一、光滑轴类锻件的余量和公差:2、斜面角α≤15°3、L/D>20时,余量增加2~4㎜。
L/D>40时,余量增加5㎜。
二、矩形截面锻件。
注:余量和公差决定于零件长度和最大边长。
当平板B/A>4时,则“B”的尺寸余量减少10-15%。
当平板B/A<1.5时,斜角α≤20°当平板B/A>1.5时,斜角α≤30°三、带有台阶和凹档的圆形轴锻件、2、偏心轴可按表余量增大10-20%。
3、对于①用括号外的余量,对于②用括号内的余量。
四、实心圆柱,注:余量和公差在下列条件下有效。
1、方条尺寸,0.28A≤H≤1.5A(块类)2、圆柱和圆盘尺寸:0.28D≤H≤1.5D(并,柱类)3、当H<0.28D时,余量仍按此表规定,但允许有鼓形外形边缘。
4、锥形吸轮零件的余量与公差,按最大直径确定。
五、带孔圆并和方并锻件。
根据直径D、决定冲子的标准直径D2注:余量和公差在下列条件下有效。
1.圆形周边的高度H≤0.5D2.方形周边的高度B≤A≤1.5B,H≤0.5B.六、环形锻件。
1、d≥0.5D H<D2、薄壁圆环内径的余量根据具体情况可以增加10-20%.3、扩孔后无法进行高度方向端面平整时,其高度H的单面余量为0.6a.七、带孔圆柱锻件。
1 22、内径的加工余量根据芯棒的最大直径D2计算,但由于芯棒有锥度(1:100)允许余量增大3、若圆柱加工后的内径尺寸D1<180㎜时,则锻成实心圆棒。
八、模块2、如端部尺寸不够平整时,长度L的单面余量可为a。
十、单拐曲轴。
图见<锻工手册>注:1、曲拐斜面的角度≤15°2、切头斜面不得妨碍中心孔的位置。
3、余量a根据锻件最大断面部的标准放大20%。
十一、在同一个平面的拐曲轴。
锻件毛坯下料工艺守则

锻件毛坯下料工艺守则
锻件毛坯下料工艺守则
1 使用范围
本守则规定了用锯床下料的毛坯的各项质量要求。
适用于自由锻锤等设备上生产的钢质自由锻件的坯料,气割下料也可参照使用。
2 锻件毛坯的下料方法
2.1 锯切
2.2 气割
3 锻件毛坯下料质量要求
3.1 锯床下料按长度验收的坯料,其长度以两端面之间的短边为准,长度公差见表。
端面平整,倾斜角小于3度,公称尺寸大于表中所列时,长度偏差取±2.5mm。
4 锯切切口损耗约3~4mm,气割损耗约4~8mm。
5 检查内容
5.1 材料检查
根据对材料的技术要求确定检查项目、检查方法、检查百分比以及执行者。
5.2 毛坯下料质量检查
按毛坯下料质量要求确定检查项目、检查方法、检查百分比以及执行者。
6 质量记录
锻造明细表
锻件过程控制记录。
1。
锻造压力计算公式
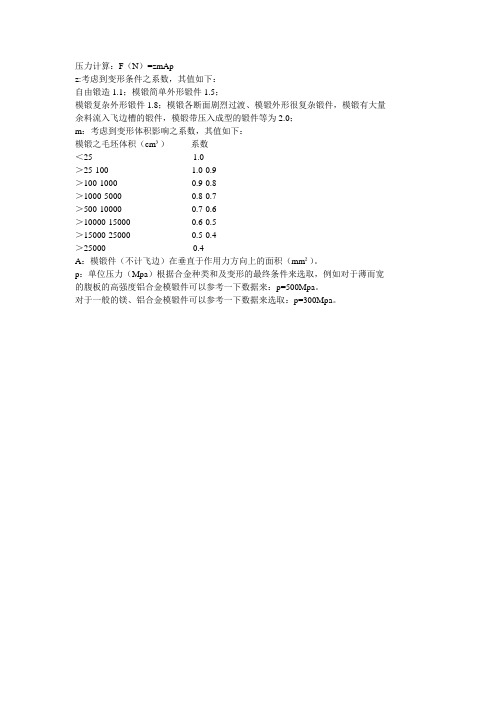
压力计算:F(N)=zmAp
z:考虑到变形条件之系数,其值如下:
自由锻造1.1;模锻简单外形锻件1.5;
模锻复杂外形锻件1.8;模锻各断面剧烈过渡、模锻外形很复杂锻件,模锻有大量余料流入飞边槽的锻件,模锻带压入成型的锻件等为2.0;
m:考虑到变形体积影响之系数,其值如下:
模锻之毛坯体积(cm³)系数
<25 1.0
>25-100 1.0-0.9
>100-1000 0.9-0.8
>1000-5000 0.8-0.7
>500-10000 0.7-0.6
>10000-15000 0.6-0.5
>15000-25000 0.5-0.4
>25000 0.4
A:模锻件(不计飞边)在垂直于作用力方向上的面积(mm²)。
p:单位压力(Mpa)根据合金种类和及变形的最终条件来选取,例如对于薄而宽的腹板的高强度铝合金模锻件可以参考一下数据来:p=500Mpa。
对于一般的镁、铝合金模锻件可以参考一下数据来选取:p=300Mpa。
材料成型工艺考试复习题目及答案

1 充型能力的影响因素金属的流动性浇注条件铸型填充能力2 浇口杯的作用承接金属液防止和溢出减轻液流对型腔的冲击分离溶渣和气泡防止进入型腔增加充型压力头3 横浇道的作用(1)横浇道的稳流作用:收缩式浇注系统扩张式浇注系统(2)横浇道的流量分配作用:远离直浇道的流量大流量不均匀性克服不均匀性的措施:对称设置内浇道;横浇道断面沿液流方向逐渐缩小;设置浇口窝;采用不同断面内浇道。
(3)横浇道的排渣作用浇注系统主要排渣单元4冒口补缩的条件和要求1)冒口的凝固时间应大于或等于铸件(被补缩部分)的凝固时间。
2)冒口应有足够大的体积,以保证有足够的金属液补充铸件的液态收缩和凝固收缩3)在铸件整个凝固的过程中,冒口与被补缩部位之间的补缩通道应该畅通。
即使扩张角始终向着冒口。
5 浇注位置选择的原则①铸件的重要加工面应朝下或位于侧面:②铸件宽大平面应朝下:③面积较大的薄壁部分应置于铸型下部或垂直:④易形成缩孔的铸件,较厚部分置于上部或侧面:⑤应尽量减少型蕊的数量:⑥要便于安放型蕊、固定和排气:6 湿型砂的组成及性能要求原砂(或旧砂)100 粘土(膨润土)1-5% 煤粉少于8% 水分少于6% 以及其它附加物1) 紧实率和含水量湿型砂不可太干,因为干的型砂虽然流动性极好,但是型砂中膨润土未被充分润湿,性能较为干脆,起模困难,砂型易碎,表面的耐磨强度低,铸件容易生成砂孔和冲蚀缺陷。
型砂也不可太湿,否则型砂太粘,造型时型砂容易在砂斗中搭桥和降低造型流动性,还易使铸件产生针孔、气孔、呛火、水爆炸、夹砂、粘砂等缺陷。
一是紧实率,代表型砂的手感干湿程度;另一是含水量,代表型砂的实际水分含量。
2_) 透气率砂型的排气能力除了靠冒口和排气孔来提高以外,更要靠型砂的透气率。
因此砂型的透气率不可过低,以免浇注过程中发生呛火和铸件产生气孔缺陷。
3) 常温湿态强度湿型砂必须具备一定强度以承受各种外力的作用。
4)湿压强度一般而言,欧洲铸造行业对铸铁用高密度造型型砂的的湿压强度值要求较高。
锻件毛坯计算

锻件毛坯计算如图,根据零件图绘制锻件图;在1吨模锻锤上模锻,生产批量为成批生产,材料45钢;解:计算过程如下1、确定机械加工余量和公差1计算锻件质量m2计算锻件复杂系数SS 在0.32~0.63G C =范围内,所以复杂系数为2S 级;3材质系数M45钢含碳量c%=~%<%所以材质系数为1M 级;4由表2-2、表2-3查得零件加工余量锻件厚度尺寸100mm,余量~,取;锻件长度尺寸132mm,余量~,取;内孔直径尺寸46mm,余量;5根据锻件质量m 、复杂系数S 、材质系数M,由表2-4、2-6查公差锻件尺寸132mm,公差 2.11.13.2mm +-;锻件尺寸90mm,公差 1.90.92.8mm +-;厚度尺寸100mm,公差 2.70.93.6mm +-;厚度尺寸36mm,公差 1.90.62.5mm +-;内孔直径46mm,公差0.81.72.5mm +-;错差;残留飞边公差;表面缺陷,不允许超过1.2mm;2、确定模锻斜度由零件尺寸,查得,内表面拔模斜度10,外表面拔模斜度7;3、圆角半径外圆角半径r=余量+a=+2=,取r=5mm;内圆角半径R=2~3r,根据需要,取R=8mm;4、冲孔连皮当孔径为25~80mm 时,冲孔连皮厚度取4~8mm冲孔连皮:对于有内孔的模锻件,锤上模锻不能直接锻出通孔,必须在所锻成的盲孔内保留一层具有一定厚度的金属层;冲孔连皮形式:1平底连皮:用于d<,或25mm<d<60mm的孔;2斜底连皮:用于d>,或d>60mm的孔;3带仓连皮;4拱底连皮:用于内孔d>15h,且高度较小的锻件;连皮厚度0.450.6 6.6mmδ==取7mmδ=圆角半径150.150212R mm=+⨯+=综上得,锻件图如下;。
长轴类模锻件制坯工步确定.
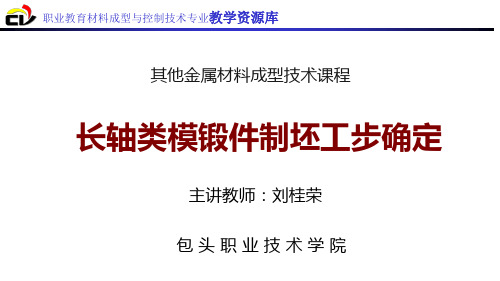
其他金属材料成型技术课程
长轴类模锻件制坯工步确定
主讲教师:刘桂荣 包头职业技术学院
职业教育材料成型与控制技术专业教学资源库
目
1 1 2 3
录
绘制计算毛坯的截面图和直径图
制坯工步选择各种参数介绍
长轴类模锻件制坯工步概述
其他金属材料成型技术课程
职业教育材料成型与控制技术专业教学资源库
根据计算毛坯的截面积可以得到计算毛坯直径:
d 计=
4
F计
计算毛坯的直径图是以模锻件轴线对称轴,计算毛
坯的半径为纵坐标绘出的对称曲线。
其他金属材料成型技术课程
职业教育材料成型与控制技术专业教学资源库
(4)计算毛坯图的组成
一张完整的计算毛坯图包 括三个部分,即模锻件的 主视图、截面图和直径图。
别代入图中查找,得出制
坯工步的初步方案。图中
“开滚”指开式滚挤制坯,
ห้องสมุดไป่ตู้
“闭滚”指闭式滚挤制坯。
长轴类锻件制坯工步选用图
其他金属材料成型技术课程
2.计算工艺过程繁重系数
制坯工步的基本任务是完成金属的轴向分配,该任务 的难易可用金属变形工艺过程繁重系数描述: (1)金属流入头部的繁重系数
;
(2)金属沿轴向变形的繁重系数 ; (3)计算毛坯的杆部斜率K ;
其他金属材料成型技术课程
职业教育材料成型与控制技术专业教学资源库
d max d均
弯曲
成形
滚压
拔长
卡压
其他金属材料成型技术课程
职业教育材料成型与控制技术专业教学资源库
拔长
使坯料某部分轴向长度增加,截面减小的 制坯工步。
第十章 自由锻造工艺

二.拔长
使毛坯横截面减小而长度增加的锻造工序。
作用: 成形轴杆类锻件; 改善锻件内部质量。
(1)拔长变形特点: 拔长前变形区的长、宽、高分别为:l0、b0、h0。
拔长后变形区的长、宽、高分别为:l、b、h。
送进量l0 相对送进量l0/h0 压下量Δh=h0-h 展宽量Δb=b-b0, 拔长 量Δl=l- l0
理论计算法:根据塑性成形原理建立的公式,算出锻件成形 所需的最大变形力(或变形功),按此选取设备吨位。
经验类比法:在统计分析生产实践数据的基础上,整理出经 验公式、表格或图线,根据锻件某些主要参数(如质量、尺 寸、接触面积),直接通过公式、表格或图线选定所需锻压 设备吨位。
五、制订自由锻工艺规程卡
锻造工艺规程卡上需填写工艺规程制定的所有内容。它包括: 下料方法 工序 火次 加热设备 加热及冷却规范 锻造设备 锻件锻后处理。
第四节
胎模锻造简介
一.胎模锻及工艺特点:
在自由锻设备上采用活动模具成形锻件的方法称为胎模锻。 主要工艺特点:
1.与自由锻比,可以得到较高的锻件精度和较高的生产率; 2.与模锻比,不需要专用的模锻设备,可以在自由锻锤上生产模锻件, 胎模的制造简单、成本低; 3.采用人力操作胎模,劳动强度大; 4.适于小型锻件小批或中批生产。
变形程度表示: 压下量ΔH 镦粗比KH=H0/H
图10-2 平砧镦粗
(1)平砧镦粗:指毛坯在上下两个平砧之间的镦粗
根据镦粗后网格的变形程度分为三个变形区: 区域Ⅰ:难变形区; 区域Ⅱ:大变形区; 区域Ⅲ:小变形区,变形程度介于区域Ⅰ与区域Ⅱ之间。
变形结果:变 形不均匀,易 出现缺陷。
齿轮坯自由锻造工艺流程
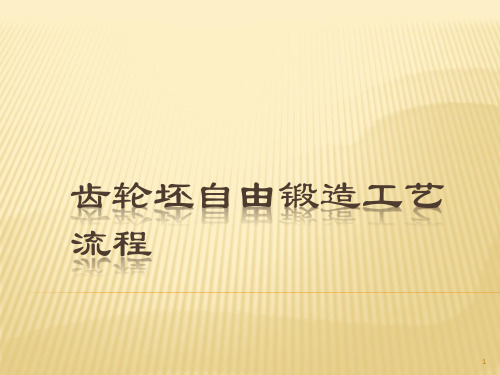
具体设计方法与步骤
(2) 冲孔 冲孔应使冲孔芯料损失小,同时扩 孔次数不能太多,冲孔直径d冲应小 于或等于D/3即 d冲≤D/3=213/3=71mm,实际选用d=60mm (3) 扩孔 总扩孔量为锻件孔径减去冲孔直径, 即(131-60)=71mm,一般每次扩孔量为 25~30mm,分配各次扩孔量为21mm、25mm、25mm。 (4) 修整锻件 按锻件图进行修整
6
具体设计方法与步骤
1.设计绘制锻件图 该零件材料为40Cr,生产批量小,采取自由锻锻造齿轮坯。齿轮上 的齿形,圆周小凹槽,凸肩以及8×φ30mm通孔等部分,采用自由 锻方法很难成形这些部位,因此考虑到技术上的可行性和经济性, 决定不与锻出,并采用附加余块简化锻件外形,以利于锻造。锻造 出齿轮坯后可以进一步进行切削加工,最后成形。 根据零件图的尺寸规格,对照表所列中零件的高度和直径范围,可 以查出齿轮锻件加工余量和 公差。D=289,h=52,查得的加工余量 及公差为锻件水平方向a=10±4,锻件 高度方向b=9±3,内孔的双边c=13±5, 然后按查得的公差数值,便可绘出凸肩 齿轮的锻件图。
5
工艺规程的制定
5.确定锻造温度及规范造温度及规范 (1).确定锻造的温度范围 各类合金钢的锻造温度范围可以从表中查出,基本的原 则是确保钢在锻造温度范围内具有良好的塑性和较低的 变形抗力,能够锻造出优质锻件,且较宽的锻造温度范 围和较少的加热次数,以及较高的生产率。 (2).确定加热及冷却范围 对于导热性好,直径小于150~200mm的碳素结构钢小件, 采用一般加热规范,一般高温装炉,炉温控制在 1300℃~1350℃。当坯料加热至始锻温度后,立即出炉 锻造。 (3). 确定冷却方法及规范 根据要求选择空冷、坑冷或 炉冷。中小型碳钢和低合金钢锻后均采取冷却速度较快 的空冷方法。碳素工具钢、合金工具钢及轴承钢,锻后 先空冷鼓风或喷雾等快速冷到200℃,然后把锻件放入 坑中或炉中缓冷。
锻件余量和材料消耗计算基本原则
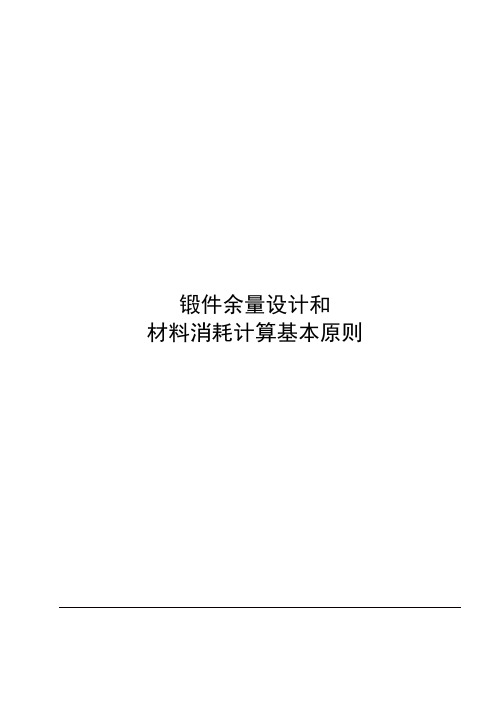
锻件余量设计和材料消耗计算基本原则锻件余量设计和材料消耗计算基本原则1 范围本标准规定了滚动轴承(包括轮毂单元、凸缘等)套圈所有热锻锻件的设计基本方法,锻件重量、飞边重量、料芯重量、火耗重量、下料重量、材料消耗重量的基本计算方法。
本标准适用于滚动轴承(包括轮毂单元、凸缘等)套圈所有热锻锻件。
2 规范性引用文件下列文件中的条款通过本标准的引用而成为本标准的条款。
凡是注日期的引用文件,其随后所有的修改单(不包括勘误的内容)或修订版均不适用于本标准,然而,鼓励根据本标准达成协议的各方研究是否可使用这些文件的最新版本。
凡是不注日期的引用文件,其最新版本适用于本标准。
GB/T 12361 钢质模锻件通用技术条件GB/T 12362 钢质模锻件公差及机械加工余量CSBTS TC98.25 滚动轴承套圈锻件技术条件3 术语和定义锻件重量:锻件毛坯的实际重量飞边重量:锻造过程中外轮廓分模面处多余的材料料芯重量:锻造过程中内孔多余的材料火耗重量:锻件在锻打过程中的热损耗下料重量(切料重量):锻打一件锻件所需要的钢坯重量材料消耗定额:锻打一件锻件所需要的钢材消耗总重量4 锻件设计基本原则4.1 锻件余量设计基本原则4.1.1 法兰盘/单元外圈/轴承座/凸缘等锻件余量设计基本原则径向余量2.2mm,外径公差+1.0mm,内径公差-1.0mm;当直径超过φ100mm时,径向余量2.5 mm,外径公差+1.2mm,内径公差-1.2mm。
(注:在保证法兰盘两端厚度C1、C2最小壁厚不小于5mm的前提下)法兰大外径D径向余量2.5mm,外径公差+1.2mm。
轴向余量2.5mm, 两端轴向余量每端各2mm,一般外轮廓公差+1.0mm,内轮廓公差-1.0mm。
法兰内孔深度一般为h1小于等于10mm,h2小于等于18mm,具体可视产品情况而定。
料芯厚度:单元外圈料芯厚度一般按8mm设计。
图一4.1.2 挡环余量设计基本原则径向余量2.5mm。
材料定额的计算(新)最新版

材料比重= (1)圆钢 外圆直径(mm) 42 (2)扁钢(方钢/板材) 宽度(mm) 厚度(mm) 长度(mm) 139 毛坯 数量 1 毛坯 数量 1 每毛坯 加 工件数 1 每毛坯 加 工件数 10 每毛坯 净重kg 1.348 每毛坯 净重kg 8.653 每毛坯 净重kg 1.01 每毛坯 净重kg 0.0616 每毛坯 毛重kg 1.4154 每毛坯 毛重kg 9.08565 每毛坯 毛重kg 1.0605 每毛坯 毛重kg 0.06468 7.85 千克/立方分米 毛坯 数量 1 每毛坯 加 工件数 1 毛重系数= 1.05 乘系数后毛重kg 长度(mm) 37 每毛坯 净重kg 0.402 每毛坯 毛重kg 0.4221
毛坯 数量 1
每ቤተ መጻሕፍቲ ባይዱ坯 加 工件数 1
1.0605
每工件 毛重kg
长度(mm) 28
毛坯 数量 1
每毛坯 加 工件数 1
0.06468
一般毛重系数为1.05 锻件毛重系数为1.15 气割毛重系数为1.20
单件重量 件数 总重量
计算。
锻件毛重按(残料系数5%+火耗系数10%)= 15%
乘系数后毛重kg 每台件 数 20 每台件 数 每台量 重kg 8.442 每台量 重kg 0.000 每台件 数 每台量 重kg 0.000 每台量 重kg 0 每台量 重kg 0 毛 毛 毛 毛
每工件 毛重kg
0.422
每工件 毛重kg
65 19 (3)空心管(无缝钢管) 外圆(mm) 102 (4)空心套 外圆(mm) 115 (5)六角钢 每米重量 2.2
1.4154
每工件 毛重kg
壁厚(mm) 长度(mm) 16 255
毛坯的选择

过定位
例2 箱体定位中将一面两销中的菱形销改用短圆 形销:
右边的短圆销不仅约束 ,而且与左边的 r r 短圆销一起同时约束两个自由度 X , Y ,引 起变形和误差。
) Z
例3 加工连杆用长圆销,支承板及挡销进行 定位的情况。 左边的长圆销约束了工件连杆四个自由度 ; 支承板相当于三点定位,应该约束了工件的三 ) ) r 个自由度 X , Y , Z ;挡销为一点定位,约束了工 ) 件的一个自由度 Z 。这样和被长圆销和支承 板重复限制。即过定位。 说明: 正确对待过定位 实属不许-----产生变形、误差 实属不许-----产生变形、误差 可用则用
3)为了保证重要表面的余量均匀,选重要表面 3)为了保证重要表面的余量均匀,选重要表面 为粗基准。
4)粗基准表面(几何原则) 4)粗基准表面(几何原则) ①面积大(是指力学面积) ②重心低 ③平整光洁(易于清理) ④尽可能同箱,同模面。(下箱面更好) ⑤夹紧刚度尽可能好
5)粗基准应避免重复使用,在同一尺寸方向 5)粗基准应避免重复使用,在同一尺寸方向 上(即同一自由度方向上),通常只允许使 用一次。
工序余量 本道工序基本尺寸
上道工序基本尺寸
T1—上道工序尺寸公差 T2—本道工序尺寸公差
- 1、下载文档前请自行甄别文档内容的完整性,平台不提供额外的编辑、内容补充、找答案等附加服务。
- 2、"仅部分预览"的文档,不可在线预览部分如存在完整性等问题,可反馈申请退款(可完整预览的文档不适用该条件!)。
- 3、如文档侵犯您的权益,请联系客服反馈,我们会尽快为您处理(人工客服工作时间:9:00-18:30)。
锻件毛坯计算
如图,根据零件图绘制锻件图。
在1吨模锻锤上模锻,生产批量为成批生产,材料45钢。
解:计算过程如下
1、确定机械加工余量和公差
(1)计算锻件质量m
()2223313290463610036100107.8510222m kg πππ--⎡⎤⎛⎫⎛⎫⎛⎫=⨯⨯+⨯⨯--⨯⨯⨯⨯⨯⎢⎥ ⎪ ⎪ ⎪⎝⎭⎝⎭⎝⎭⎢⎥⎣⎦
5.76kg =
(2)计算锻件复杂系数S
()2222132904636100361002220.5361321002S ππππ⎡⎤⎛⎫⎛⎫⎛⎫⨯⨯+⨯⨯--⨯⨯⎢⎥ ⎪ ⎪ ⎪⎝⎭⎝⎭⎝⎭⎢⎥⎣⎦=
=⎛⎫⨯⨯ ⎪⎝⎭
S 在0.32~0.63G C =范围内,所以复杂系数为2S 级。
(3)材质系数M
45钢含碳量c%=0.42~0.50%<0.65%
所以材质系数为1M 级。
(4)由表2-2、表2-3查得零件加工余量
锻件厚度尺寸100mm ,余量2.0~2.5mm ,取2.5mm 。
锻件长度尺寸132mm ,余量2.0~2.5mm ,取2.5mm 。
内孔直径尺寸46mm ,余量2.6mm 。
(5)根据锻件质量m 、复杂系数S 、材质系数M ,由表2-4、2-6查公差
锻件尺寸132mm ,公差 2.11.13.2mm +
-;
锻件尺寸90mm ,公差 1.90.92.8mm +
-;
厚度尺寸100mm ,公差 2.70.93.6mm +
-;
厚度尺寸36mm ,公差 1.90.62.5mm +
-;
内孔直径46mm ,公差0.81.72.5mm +
-;
错差1.2mm ;
残留飞边公差1.2mm ;
表面缺陷,不允许超过1.2mm 。
2、确定模锻斜度
由零件尺寸,查得,内表面拔模斜度10,外表面拔模斜度7。
3、圆角半径
外圆角半径r=余量+a=2.5+2=4.5mm ,取r=5mm 。
内圆角半径R=(2~3)r ,根据需要,取R=8mm 。
4、冲孔连皮(当孔径为25~80mm 时,冲孔连皮厚度取4~8mm)
冲孔连皮:对于有内孔的模锻件,锤上模锻不能直接锻出通孔,必须在所锻成的盲孔内保留一层具有一定厚度的金属层。
冲孔连皮形式:
(1)平底连皮:用于d<2.5h,或25mm<d<60mm的孔。
(2)斜底连皮:用于d>2.5h,或d>60mm的孔。
(3)带仓连皮。
(4)拱底连皮:用于内孔d>15h,且高度较小的锻件。
连皮厚度100
0.45460.2550.650 6.6
2mm
δ=⨯-⨯-+⨯=取7mm
δ=
圆角半径
150.150212
R mm
=+⨯+=
综上得,锻件图如下。