齿轮计算过程
齿轮计算公式

齿轮参数计算公式节圆柱上的螺旋角:基圆柱上的螺旋角:齿厚中心车角:销子直径:中心距离增加系数:一、标准正齿轮的计算(小齿轮①,大齿轮②)1.齿轮齿标准2.工齿齿形直齿3.模数 m4.压力角5.齿数6.有效齿深7.全齿深8.齿顶隙9.基础节圆直径10.外径11.齿底直径12.基础圆直径13.周节14.法线节距15.圆弧齿厚16.弦齿厚17.齿轮油标尺齿高18.跨齿数19.跨齿厚20.销子直径21.圆柱测量尺寸(偶数齿)(奇数齿)其中,22.齿隙 ?二、移位正齿轮计算公式(小齿轮①,大齿轮②)1.齿轮齿形转位2.工具齿形直齿3.模数4.压力角5.齿数6.有效齿深7.全齿深或8.齿隙9.转位系数10.中心距离11.基准节圆直径12.啮合压力角13.啮合节圆直径14.外径15.齿顶圆直径16.基圆直径17.周节18.法线节距19.圆弧齿厚20.弦齿厚21.齿轮游标尺齿高22.跨齿数23.跨齿厚24.梢子直径25.圆柱测量尺寸(偶数齿)(奇数齿)三、标准螺旋齿的计算公式(齿直角方式)(小齿轮①,大齿轮②)1.齿轮齿形标准2.齿形基准断面齿直角3.工具齿形螺旋齿4.模数5.压力角6.齿数7.螺旋角方向(左或右)8.有效齿深9.全齿深10.正面压力角11.中心距离12.基准节圆直径13.外径14.齿底圆直径15.基圆直径16.基圆上的螺旋角17.导程18.周节(齿直角)19.法线节距(齿直角)20.圆弧齿厚(齿直角)21.相当正齿轮齿数22.弦齿厚23.齿轮游标尺齿深24.跨齿数25.跨齿厚26.梢子直径其中,27.圆柱测量尺寸(偶数齿)(奇数齿)28.齿隙四、移位螺旋齿的计算公式(齿直角方式)(小齿轮①,大齿轮②)1.齿轮齿形移位2.齿形基准断面齿直角3.工具齿形螺旋齿4.模数(齿直角)5.压力角(齿直角)6.齿数7.螺旋方向8.有效齿深9.全齿深10.移位系数11.中心距离12.正面模数13.正面压力角14.相当正齿轮齿数15.齿直角啮齿压力角16.基准节圆直径17.外径18.啮齿节圆直径19.基圆直径20.基础圆柱上的螺旋角21.圆弧齿厚22.弦齿厚23.齿轮游标尺齿高24.跨齿数25.跨齿厚26.销子直径27.圆柱测量尺寸(偶数齿)注:齿隙 f=m 1.25以下 0.025-0.075m 1.25-2.5 0.05-0.10。
齿轮各参数计算公式
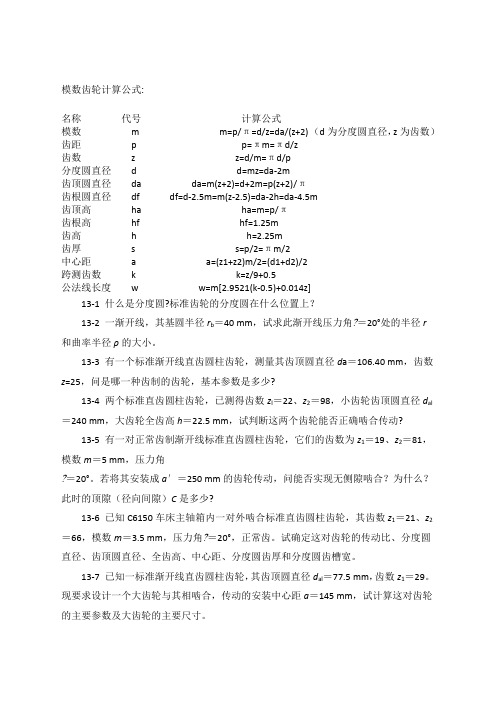
模数齿轮计算公式:名称代号计算公式模数m m=p/π=d/z=da/(z+2) (d为分度圆直径,z为齿数)齿距p p=πm=πd/z齿数z z=d/m=πd/p分度圆直径d d=mz=da-2m齿顶圆直径da da=m(z+2)=d+2m=p(z+2)/π齿根圆直径df df=d-2.5m=m(z-2.5)=da-2h=da-4.5m齿顶高ha ha=m=p/π齿根高hf hf=1.25m齿高h h=2.25m齿厚s s=p/2=πm/2中心距a a=(z1+z2)m/2=(d1+d2)/2跨测齿数k k=z/9+0.5公法线长度w w=m[2.9521(k-0.5)+0.014z]13-1 什么是分度圆?标准齿轮的分度圆在什么位置上?13-2 一渐开线,其基圆半径r b=40 mm,试求此渐开线压力角?=20°处的半径r和曲率半径ρ的大小。
13-3 有一个标准渐开线直齿圆柱齿轮,测量其齿顶圆直径d a=106.40 mm,齿数z=25,问是哪一种齿制的齿轮,基本参数是多少?13-4 两个标准直齿圆柱齿轮,已测得齿数z l=22、z2=98,小齿轮齿顶圆直径d al =240 mm,大齿轮全齿高h=22.5 mm,试判断这两个齿轮能否正确啮合传动?13-5 有一对正常齿制渐开线标准直齿圆柱齿轮,它们的齿数为z1=19、z2=81,模数m=5 mm,压力角?=20°。
若将其安装成a′=250 mm的齿轮传动,问能否实现无侧隙啮合?为什么?此时的顶隙(径向间隙)C是多少?13-6 已知C6150车床主轴箱内一对外啮合标准直齿圆柱齿轮,其齿数z1=21、z2=66,模数m=3.5 mm,压力角?=20°,正常齿。
试确定这对齿轮的传动比、分度圆直径、齿顶圆直径、全齿高、中心距、分度圆齿厚和分度圆齿槽宽。
13-7 已知一标准渐开线直齿圆柱齿轮,其齿顶圆直径d al=77.5 mm,齿数z1=29。
齿轮各参数计算公式

模数齿轮计算公式:名称代号计算公式模数m m=p/π=d/z=da/(z+2) (d为分度圆直径,z为齿数)齿距p p=πm=πd/z齿数z z=d/m=πd/p分度圆直径 d d=mz=da-2m齿顶圆直径da da=m(z+2)=d+2m=p(z+2)/π齿根圆直径df df=d-2.5m=m(z-2.5)=da-2h=da-4.5m齿顶高ha ha=m=p/π齿根高hf hf=1.25m齿高h h=2.25m齿厚s s=p/2=πm/2中心距 a a=(z1+z2)m/2=(d1+d2)/2跨测齿数k k=z/9+0.5公法线长度w w=m[2.9521(k-0.5)+0.014z]13-1 什么是分度圆?标准齿轮的分度圆在什么位置上?13-2 一渐开线,其基圆半径r b=40 mm,试求此渐开线压力角α=20°处的半径r和曲率半径ρ的大小。
13-3 有一个标准渐开线直齿圆柱齿轮,测量其齿顶圆直径d a=106.40 mm,齿数z=25,问是哪一种齿制的齿轮,基本参数是多少?13-4 两个标准直齿圆柱齿轮,已测得齿数z l=22、z2=98,小齿轮齿顶圆直径d al=240 mm,大齿轮全齿高h =22.5 mm,试判断这两个齿轮能否正确啮合传动?13-5 有一对正常齿制渐开线标准直齿圆柱齿轮,它们的齿数为z1=19、z2=81,模数m=5 mm,压力角α=20°。
若将其安装成a′=250 mm的齿轮传动,问能否实现无侧隙啮合?为什么?此时的顶隙(径向间隙)C是多少?13-6 已知C6150车床主轴箱内一对外啮合标准直齿圆柱齿轮,其齿数z1=21、z2=66,模数m=3.5 mm,压力角α=20°,正常齿。
试确定这对齿轮的传动比、分度圆直径、齿顶圆直径、全齿高、中心距、分度圆齿厚和分度圆齿槽宽。
13-7 已知一标准渐开线直齿圆柱齿轮,其齿顶圆直径d al =77.5 mm ,齿数z 1=29。
齿轮公式计算公式

齿轮计算公式计算公式:模数m = 分度圆直径d / 齿数z = 齿距p /圆周率π。
齿轮模数被定义为模数制轮齿的一个基本参数,是人为抽象出来用以度量轮齿规模的数。
在齿轮设计中,模数是决定轮齿大小的决定性元素。
不同国家对模数的定义方法有所区别,最典型的就是国际标准(除英国外,包括中国在内的其余国家的标准都与国际标准接轨)和英制标准。
国际标准定义模数的原理是:定义单个轮齿在分度圆(齿轮)/ 或线(齿条)出占有的圆弧(齿轮)/ 直线(齿条)的长度, 其长度为π * m,m 即为模数。
从这里可以看出,模数是有单位的,其标准单位为毫米(mm)。
很多人,习惯于模数简写,譬如,模数为1mm的齿轮,简写m=1;大家都逐渐接受这种写法,因此也是可以的。
但是,个别对齿轮模数理解不够深刻的同仁,认为模数没有单位,这个概念是错误的。
齿轮可按齿形、齿轮外形、齿线形状、轮齿所在的表面和制造方法等分类。
齿轮的齿形包括齿廓曲线、压力角、齿高和变位。
渐开线齿轮比较容易制造,因此现代使用的齿轮中,渐开线齿轮占绝对多数,而摆线齿轮和圆弧齿轮应用较少。
在压力角方面,小压力角齿轮的承载能力较小;而大压力角齿轮,虽然承载能力较高,但在传递转矩相同的情况下轴承的负荷增大,因此仅用于特殊情况。
而齿轮的齿高已标准化,一般均采用标准齿高。
变位齿轮的优点较多,已遍及各类机械设备中。
另外,齿轮还可按其外形分为圆柱齿轮、锥齿轮、非圆齿轮、齿条、蜗杆蜗轮;按齿线形状分为直齿轮、斜齿轮、人字齿轮、曲线齿轮;按轮齿所在的表面分为外齿轮、内齿轮;按制造方法可分为铸造齿轮、切制齿轮、轧制齿轮、烧结齿轮等。
齿轮的制造材料和热处理过程对齿轮的承载能力和尺寸重量有很大的影响。
20世纪50年代前,齿轮多用碳钢,60年代改用合金钢,而70年代多用表面硬化钢。
按硬度,齿面可区分为软齿面和硬齿面两种。
软齿面的齿轮承载能力较低,但制造比较容易,跑合性好,多用于传动尺寸和重量无严格限制,以及小量生产的一般机械中。
标准齿轮模数计算 齿数计算
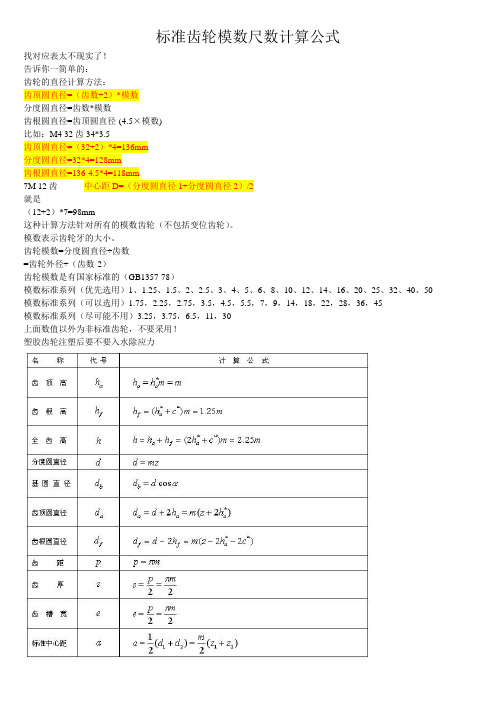
标准齿轮模数尺数计算公式找对应表太不现实了!告诉你一简单的:齿轮的直径计算方法:齿顶圆直径=(齿数+2)*模数分度圆直径=齿数*模数齿根圆直径=齿顶圆直径-(4.5×模数)比如:M4 32齿34*3.5齿顶圆直径=(32+2)*4=136mm分度圆直径=32*4=128mm齿根圆直径=136-4.5*4=118mm7M 12齿中心距D=(分度圆直径1+分度圆直径2)/2就是(12+2)*7=98mm这种计算方法针对所有的模数齿轮(不包括变位齿轮)。
模数表示齿轮牙的大小。
齿轮模数=分度圆直径÷齿数=齿轮外径÷(齿数-2)齿轮模数是有国家标准的(GB1357-78)模数标准系列(优先选用)1、1.25、1.5、2、2.5、3、4、5、6、8、10、12、14、16、20、25、32、40、50 模数标准系列(可以选用)1.75,2.25,2.75,3.5,4.5,5.5,7,9,14,18,22,28,36,45模数标准系列(尽可能不用)3.25,3.75,6.5,11,30上面数值以外为非标准齿轮,不要采用!塑胶齿轮注塑后要不要入水除应力精确测定斜齿轮螺旋角的新方法Circular Pitch (CP)周节齿轮分度圆直径d的大小可以用模数(m)、径节(DP)或周节(CP)与齿数(z)表示径节P(DP)是指按齿轮分度圆直径(以英寸计算)每英寸上所占有的齿数而言径节与模数有这样的关系: m=25.4/DPCP1/8模=25.4/DP8=3.175 3.175/3.1416(π)=1.0106模1) 什么是「模数」?模数表示轮齿的大小。
R模数是分度圆齿距与圆周率(π)之比,单位为毫米(mm)。
除模数外,表示轮齿大小的还有CP(周节:Circular pitch)与DP(径节:Diametral pitch)。
【参考】齿距是相邻两齿上相当点间的分度圆弧长。
2) 什么是「分度圆直径」?分度圆直径是齿轮的基准直径。
齿轮齿条设计计算公式

齿轮齿条设计计算公式齿轮和齿条是机械传动中常见的元件,用于传递动力和转速。
齿轮齿条的设计计算是设计师在进行齿轮齿条设计时所必须掌握的知识。
本文将介绍齿轮齿条设计计算的一些基本公式和原理。
一、齿轮设计计算公式1. 齿数计算公式齿数是齿轮设计中最基本的参数之一,可以通过以下公式计算:N = (π * D) / m其中,N为齿数,D为齿轮直径,m为模数。
2. 齿轮间距计算公式齿轮间距是指两个相邻齿轮之间的中心距离,可以通过以下公式计算:P = (N1 + N2) / 2 * m其中,P为齿轮间距,N1和N2分别为两个相邻齿轮的齿数,m为模数。
3. 齿轮传动比计算公式齿轮传动比是指两个相邻齿轮的转速之比,可以通过以下公式计算:i = N2 / N1其中,i为传动比,N1和N2分别为两个相邻齿轮的齿数。
4. 齿轮模数计算公式齿轮模数是指齿轮齿数和齿轮直径之间的比值,可以通过以下公式计算:m = D / N其中,m为模数,D为齿轮直径,N为齿数。
二、齿条设计计算公式1. 齿条模数计算公式齿条模数是指齿条齿数和齿条长度之间的比值,可以通过以下公式计算:m = L / N其中,m为模数,L为齿条长度,N为齿数。
2. 齿条传动比计算公式齿条传动比是指齿条的移动距离与齿轮转动角度之间的比值,可以通过以下公式计算:i = L / (π * D)其中,i为传动比,L为齿条的移动距离,D为齿轮的直径。
3. 齿条齿数计算公式齿条齿数是指齿条上的齿数,可以通过以下公式计算:N = L / m其中,N为齿数,L为齿条长度,m为模数。
三、齿轮齿条设计计算实例假设有一对齿轮,其中一个齿轮的齿数为20,直径为40mm,另一个齿轮的齿数为40,直径为80mm,模数为2mm。
我们可以通过上述公式进行计算。
根据齿数计算公式,可得第一个齿轮的齿数为20,第二个齿轮的齿数为40。
根据齿轮间距计算公式,可得齿轮间距为(20+40)/2*2=60mm。
齿轮传动系数计算方法

齿轮传动系数计算方法齿轮传动是一种常见的机械传动方式,在机械设计中具有广泛的应用。
齿轮传动系数是其中一个重要的计算参数,其用于评估传动效果和传动系统的可靠性。
接下来,将详细介绍齿轮传动系数的计算方法,并给出具体的计算步骤。
首先,我们需要了解齿轮传动系数的定义。
齿轮传动系数是指传动过程中损失的能量占输入功的比例。
通常用η表示,其计算公式如下:η=(P出-P进)/P进其中,P出为输出功率,P进为输入功率。
接下来,我们将具体介绍两种常用的齿轮传动系数的计算方法:基于齿轮模数和基于齿面接触疲劳寿命。
一、基于齿轮模数的齿轮传动系数计算方法:1.计算输入功率P进:P进=T进*ω进其中,T进为输入扭矩,ω进为输入角速度。
2.计算输出功率P出:P出=T出*ω出其中,T出为输出扭矩,ω出为输出角速度。
3.计算齿轮系数C:C=P出/P进4.计算齿轮传动系数η:η=1-(1-C)/i其中,i为传动比。
5.计算齿轮传动系数η':η'=η/(1-η)二、基于齿面接触疲劳寿命的齿轮传动系数计算方法:1.计算输入功率P进和输出功率P出,方法同上。
2.计算齿轮模数m:m=√(T进/(K*σ*m2*b))其中,K为齿数系数,σ为弯曲疲劳强度,m2为齿轮模数,b为齿宽。
3.计算齿面接触疲劳寿命Lh:Lh=((C*Yθ*m*b)/(Cm*Zv))^10^6其中,C为载荷系数,Yθ为添加修正系数,Cm为齿面载荷修正系数,Zv为应力修正系数。
4.计算齿轮传动系数η:η=1-(1/(1.1*(Lh/Lh0)^(1/7)))其中,Lh0为齿面接触疲劳寿命标准值。
综上所述,齿轮传动系数的计算方法包括基于齿轮模数和基于齿面接触疲劳寿命两种方法。
根据实际情况选择合适的计算方法,并按照以上步骤进行计算。
计算得到的齿轮传动系数可以用于评估传动系统的可靠性和传动效果,为机械设计和选型提供重要的依据。
齿轮基本计算公式

16. 基圆上的螺旋角
sin β g = sin β0 ⋅ cosαn
17. 导程
L1 = π ⋅ d 01 ⋅ cot β 01
18. 周节(齿直角)
t0n = π ⋅ mn
19. 法线节距(齿直角) ten = π ⋅ mn ⋅ cosα n
20.
圆弧齿厚(齿直角)
S0n
=
π
⋅ mn 2
21. 相当正齿轮齿数
1. 齿轮齿形 2. 工具齿形 3. 模数 4. 压力角 5. 齿数 6. 有效齿深 7. 全齿深 8. 齿隙 9. 转位系数 10. 中心距离 11. 基准节圆直径
12. 啮合压力角
13. 啮合节圆直径
14. 外径 15. 齿顶圆直径 16. 基圆直径 17. 周节 18. 法线节距
转位 直齿 m
⋅
cos(
90° ) Ζ1
+
d1
(奇数齿)
28. 齿隙
invφ1
=
Ζ1
di ⋅ m ⋅ cosα 0
π −(
2 ⋅ Ζ1
− invα 0 ) +
2 ⋅ x1 ⋅ tan α 0 Ζ1
f
移位螺旋齿的计算公式(齿直角方式)(小齿轮①,大齿轮②)
1. 齿轮齿形 2. 齿形基准断面 3. 工具齿形
4. 模数(齿直角)
S0 = π ⋅ m / 2
Sj
=
Ζ
⋅ m ⋅ sin(
π 2⋅Ζ1
)
π
hj
= (Ζ ⋅ m / 2) × (1 − cos
) 2⋅Ζ
+
m
Ζ m = (α0 ⋅ Ζ / 180 )×0.5
19. 跨齿厚 20. 销子直径 21. 圆柱测量尺寸
齿轮计算表(包含直齿轮和斜齿轮)
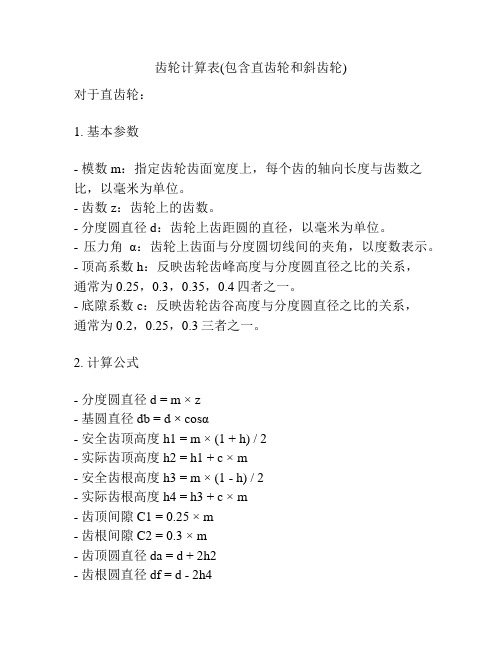
齿轮计算表(包含直齿轮和斜齿轮)对于直齿轮:1. 基本参数- 模数m:指定齿轮齿面宽度上,每个齿的轴向长度与齿数之比,以毫米为单位。
- 齿数z:齿轮上的齿数。
- 分度圆直径d:齿轮上齿距圆的直径,以毫米为单位。
- 压力角α:齿轮上齿面与分度圆切线间的夹角,以度数表示。
- 顶高系数h:反映齿轮齿峰高度与分度圆直径之比的关系,通常为0.25,0.3,0.35,0.4四者之一。
- 底隙系数c:反映齿轮齿谷高度与分度圆直径之比的关系,通常为0.2,0.25,0.3三者之一。
2. 计算公式- 分度圆直径d = m × z- 基圆直径db = d × cosα- 安全齿顶高度h1 = m × (1 + h) / 2- 实际齿顶高度h2 = h1 + c × m- 安全齿根高度h3 = m × (1 - h) / 2- 实际齿根高度h4 = h3 + c × m- 齿顶间隙C1 = 0.25 × m- 齿根间隙C2 = 0.3 × m- 齿顶圆直径da = d + 2h2- 齿根圆直径df = d - 2h4- 对啮合线上的齿距p'求法:p' = π / m- 一个齿的圆弧长度L(计算齿轮外径):L = mπ = πd / z- 第二齿轮的基本参数公式与计算方法同第一齿轮,只需根据需要调整其齿数即可。
同时,可以根据需要定义两个齿轮的齿数比,即z1 / z2 = i。
3. 示例- 假设需要计算模数为2mm,齿数为30的直齿轮参数:分度圆直径d = m × z = 2 × 30 = 60mm基圆直径db = d × cosα = 60 × cos20° = 56.985mm安全齿顶高度h1 = m × (1 + h) / 2 = 2 × (1 + 0.25) / 2 = 2.5mm 实际齿顶高度h2 = h1 + c × m = 2.5 + 0.2 × 2 = 2.9mm安全齿根高度h3 = m × (1 - h) / 2 = 2 × (1 - 0.25) / 2 = 1.5mm实际齿根高度h4 = h3 + c × m = 1.5 + 0.2 × 2 = 1.9mm齿顶间隙C1 = 0.25 × m = 0.5mm齿根间隙C2 = 0.3 × m = 0.6mm齿顶圆直径da = d + 2h2 = 60 + 2 × 2.9 = 65.8mm齿根圆直径df = d - 2h4 = 60 - 2 × 1.9 = 56.2mm一个齿的圆弧长度L = mπ = πd / z = π × 60 / 30 = 6.28mm对于斜齿轮:1. 基本参数- 模数m:同直齿轮。
斜齿轮设计(史上最详细的计算过程,有图有表有计算)

例题:已知小齿轮传递的额定功率P=95 KW,小斜齿轮转速n1=730 r/min,传动比i=3.11,单向运转,满载工作时间35000h。
1.确定齿轮材料,确定试验齿轮的疲劳极限应力参考齿轮材料表,选择齿轮的材料为:小斜齿轮:38S i M n M o,调质处理,表面硬度320~340HBS(取中间值为330HBS)大斜齿轮:35S i M n, 调质处理, 表面硬度280~300HBS(取中间值为290HBS)注:合金钢可提高320~340HBS由图16.2-17和图16.2-26,按MQ级质量要求选取值,查得齿轮接触疲劳强度极限σHlim及基本值σFE:σHlim1=800Mpa, σHlim2=760MpaσFE1=640Mpa, σFE2=600Mpa2.按齿面接触强度初步确定中心距,并初选主要参数:按公式表查得:a≥476(u+1)√KT1φa σHP2u3 1)小齿轮传递扭矩T1:T1=9550×Pn1=9549×95730=1243N.m2)载荷系数K:考虑齿轮对称轴承布置,速度较低,冲击负荷较大,取K=1.63)查表16.2-01齿宽系数φα:取φα=0.44)齿数比u=Z2/Z1=3.115)许用接触应力σHP:σHP =σHlimS Hmin查表16.2-46,取最小安全系数s Hmin=1.1,按大齿轮计算σHP2=σHlim2S Hmin2=7601.1MPa=691MPa6)将以上数据代入计算中心距公式:a≥476(3.11+1)√ 1.6×12430.4×6912×3.113=292.67mm取圆整为标准中心距a =300mm7)确定模数:按经验公式m n=(0.007~0.02)α=(0.007~0.02)x300mm=2.1~6mm 取标准模数m n=4mm8)初选螺旋角β=9°,cosβ= cos9°=0.9889)确定齿数:z1=2acosβm n(u+1)=2×300×0.9884×(3.11+1)=36.06Z2=Z1i=36.03×3.11=112.15 Z1=36,Z2=112 实际传动比i实=Z2/Z1=112/36=3.111 10)求螺旋角β:cosβ=m n(Z1+Z2)2a =4×(36+112)2×300=0.98667,所以β=9°22’11)计算分度圆直径:d1=m n Z1cosβ=4×360.98667=145.946mmd2=m n Z2cosβ=4×1120.98667=454.053mm12)确定齿宽:b=Фα×a =0.4×300=120mm 13)计算齿轮圆周速度:V=πd1n160×1000=π×145.946×73060×100=5.58m/s根据齿轮圆周速度,参考表16.2-73,选择齿轮精度等级为8-7-7 (GB10095-2002)3.校核齿面接触疲劳强度根据σH=Z H Z E Zεβ√F1bd1u+1uK A×K V×K Hβ×K Ha1)分度圆上的圆周F1:F1=2T1d1=2×1243×103145.946=17034N2)使用系数K A:查表16.2-36,K A=1.5 3)动载荷系数K V:K V=1+(K1K A F1b+K2)Z1V100√u21+u2查表16.2-39得K1=23.9,K2=0.0087代入上式得K V =1+(23.91.5×17034120+0.0087)36×5.58100√ 3.1121+3.112 =1.234)接触强度计算的齿向载荷分布系数K H β,根据表16.2-40,装配时候检验调整:K Hβ=1.15+0.18×(b d 1)2+0.31×10−3×b=1.15+0.18×(120145.946)2+0.31×10−3×120=1.2695)齿间载荷分配系数K H α:查表16.2-42,得:K A F t b=1.5×17034120=213 N/mm 2,K H α=1.16)节点区域系数Z H ,查图16.2-15,Z H =2.477)弹性系数Z E ,查表16.2-43,Z E =189.8√MPa8)接触强度计算的重合度与螺旋角系数Zεβ:当量齿数:Z V1=Z1COS3β=360.986673=37.5Z V2=Z2COS3β=1120.986673=116.6当量齿轮的端面重合度εav:εav=εaI+εaII ,查图16.2-10,分别得到εaI=0.83,εaII=0.91,εav:εav=εaI+εaII=0.83+0.91=1.74按 φm=bm =1204=30, β=9°22’,查图16.2-11,得εβ=1.55按εav= 1.74,εβ=1.55,β=9°22`,查图16.2-16,得Zεβ=0.76 9)将以上数据代入公式计算接触应力σH=2.47×189.8×0.76×√17034120×145.946×3.11+13.11× √1.5×1.23×1.27×1.1=649MPa10)计算安全系数S H根据表16.2-34,S H=σHlimZ HT Z LVR Z W Z XσH寿命系数Z NT:按式16.2-10N1=60n1K h=60×730×1×35000=1.533×109N2=N1i=1.533×1093.11=4.93×108对调质钢(允许有一点的点蚀),查图16.2-18,Z NT1=0.98,Z NT2=1.04滑油膜影响系数Z LVR ,:按v=5.58m/s选用220号齿轮油,其运动粘度V40=220mm2/s查图16.2-19, Z得LVR =0.95工作硬化系数Z W,:因小齿轮未硬化处理,齿面未光整,故Z W=1尺寸系数Z X:查图16.2-22,Z X =1 将各参数代入公式计算安全系数S HS H1=σHlim1Z NT1Z LVRσH Z w Z X=800×0.98×0.95×1649=1.13S H2=σHlim2Z NT2Z LVRσH Z w Z X=760×1.04×0.95×1649=1.16根据表16.2-46,一般可靠度S Hmin=1~1.1,S H>S Hmin,故安全。
齿轮的设计计算过程
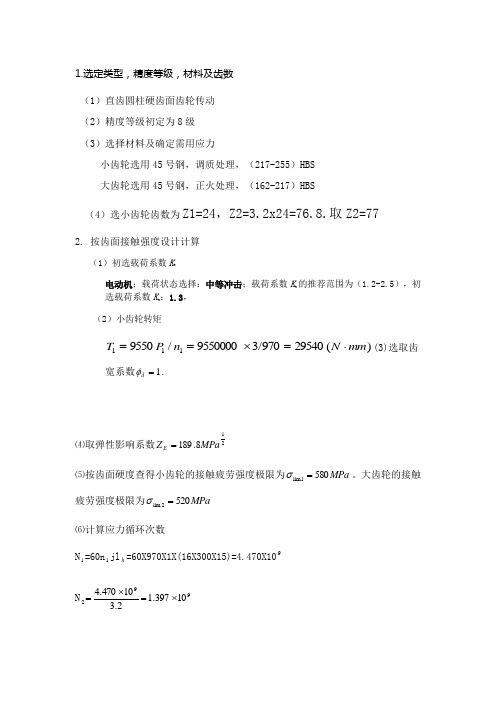
1.选定类型,精度等级,材料及齿数 (1)直齿圆柱硬齿面齿轮传动 (2)精度等级初定为8级 (3)选择材料及确定需用应力小齿轮选用45号钢,调质处理,(217-255)HBS 大齿轮选用45号钢,正火处理,(162-217)HBS (4)选小齿轮齿数为Z1=24,Z2=3.2x24=76.8.取Z2=772. 按齿面接触强度设计计算(1)初选载荷系数K t电动机;载荷状态选择:中等冲击;载荷系数K t 的推荐范围为(1.2-2.5),初选载荷系数K t :1.3, (2)小齿轮转矩)(29540/97039550000/9550111mm N n P T ⋅=⨯==(3)选取齿宽系数1=d φ.⑷取弹性影响系数218.189MPa Z E =⑸按齿面硬度查得小齿轮的接触疲劳强度极限为MPa 5801lim =σ。
大齿轮的接触疲劳强度极限为MPa 5202lim =σ ⑹计算应力循环次数N 1=60n 1jl h =60X970X1X(16X300X15)=4.470X109N 99210397.12.310470.4⨯=⨯=⑺取接触疲劳寿命系数K .89.0,88.021==HN HN K⑻计算接触疲劳许用应力 取失效概率为1%,安全系数S=1[]a HN H MP MPa SK 4.5105709.01lim 11=⨯==σσ[]a HN H MP MPa SK 8.46253095.02lim 22=⨯==σσ⑼按齿面接触强度设计计算 ①试算小齿轮分度圆直径mm Z u u T K d H E d t t 248.56)8.4628.189(2.32.4110954.28.132.2)][(132.23243211=⨯⨯⨯=+〉σφ②计算齿轮圆周转速v 并选择齿轮精度 s m n d V t /48.2100060970248.5610006011=⨯⨯⨯=⨯=ππ③计算齿轮宽度bmm d b t d 248.56248.5611=⨯=⨯=φ④计算齿轮宽度b 与齿高h 之比 模数 mm mm Z d m t 033.22272.44111===齿高 mm mm m h 574.4033.225.225.21=⨯==67.10=hb⑤计算载荷系数根据v=2.27m/s 。
标准齿轮计算公式
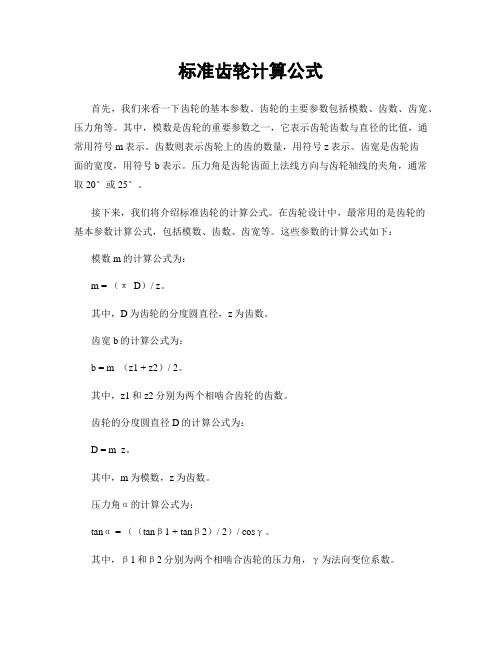
标准齿轮计算公式首先,我们来看一下齿轮的基本参数。
齿轮的主要参数包括模数、齿数、齿宽、压力角等。
其中,模数是齿轮的重要参数之一,它表示齿轮齿数与直径的比值,通常用符号m表示。
齿数则表示齿轮上的齿的数量,用符号z表示。
齿宽是齿轮齿面的宽度,用符号b表示。
压力角是齿轮齿面上法线方向与齿轮轴线的夹角,通常取20°或25°。
接下来,我们将介绍标准齿轮的计算公式。
在齿轮设计中,最常用的是齿轮的基本参数计算公式,包括模数、齿数、齿宽等。
这些参数的计算公式如下:模数m的计算公式为:m = (π D)/ z。
其中,D为齿轮的分度圆直径,z为齿数。
齿宽b的计算公式为:b = m (z1 + z2)/ 2。
其中,z1和z2分别为两个相啮合齿轮的齿数。
齿轮的分度圆直径D的计算公式为:D = m z。
其中,m为模数,z为齿数。
压力角α的计算公式为:tanα = ((tanβ1 + tanβ2)/ 2)/ cosγ。
其中,β1和β2分别为两个相啮合齿轮的压力角,γ为法向变位系数。
以上是标准齿轮的基本参数计算公式,通过这些公式可以计算出齿轮的各项参数,为齿轮传动系统的设计提供基础数据。
除了基本参数的计算外,齿轮传动系统中还需要考虑齿轮啮合的几何参数。
齿轮啮合的几何参数包括齿顶高、齿根高、齿顶圆直径、齿根圆直径等。
这些参数的计算公式如下:齿顶高h的计算公式为:h = m。
其中,m为模数。
齿根高hf的计算公式为:hf = 1.25 m。
其中,m为模数。
齿顶圆直径da的计算公式为:da = m (z + 2)。
其中,m为模数,z为齿数。
齿根圆直径df的计算公式为:df = m (z 2.5)。
其中,m为模数,z为齿数。
通过以上公式的计算,可以得到齿轮啮合的几何参数,进一步完善齿轮传动系统的设计。
总结一下,本文介绍了标准齿轮计算的基本原理和方法,包括齿轮的基本参数计算公式和齿轮啮合的几何参数计算公式。
这些公式为齿轮传动系统的设计提供了重要的参考数据,希望能对读者有所帮助。
齿轮计算公式
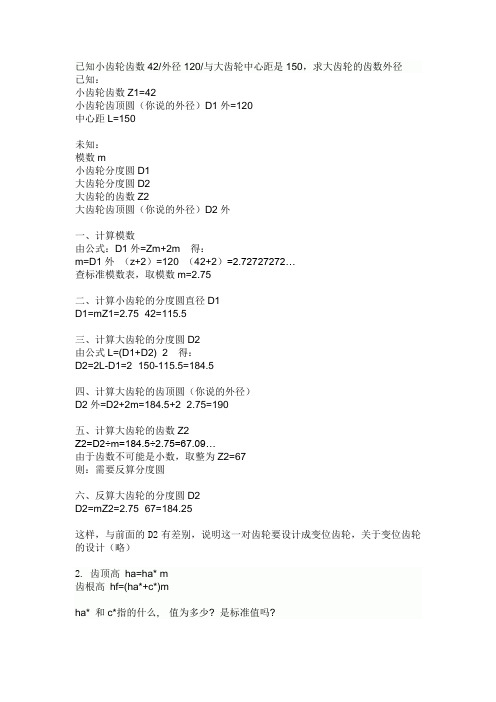
已知小齿轮齿数42/外径120/与大齿轮中心距是150,求大齿轮的齿数外径已知:小齿轮齿数Z1=42小齿轮齿顶圆(你说的外径)D1外=120中心距L=150未知:模数m小齿轮分度圆D1大齿轮分度圆D2大齿轮的齿数Z2大齿轮齿顶圆(你说的外径)D2外一、计算模数由公式:D1外=Zm+2m 得:m=D1外÷(z+2)=120÷(42+2)=2.72727272…查标准模数表,取模数m=2.75二、计算小齿轮的分度圆直径D1D1=mZ1=2.75×42=115.5三、计算大齿轮的分度圆D2由公式L=(D1+D2)÷2 得:D2=2L-D1=2×150-115.5=184.5四、计算大齿轮的齿顶圆(你说的外径)D2外=D2+2m=184.5+2×2.75=190五、计算大齿轮的齿数Z2Z2=D2÷m=184.5÷2.75=67.09…由于齿数不可能是小数,取整为Z2=67则:需要反算分度圆六、反算大齿轮的分度圆D2D2=mZ2=2.75×67=184.25这样,与前面的D2有差别,说明这一对齿轮要设计成变位齿轮,关于变位齿轮的设计(略)2.齿顶高ha=ha* m齿根高hf=(ha*+c*)mha* 和c*指的什么, 值为多少? 是标准值吗?问题补充:还问一下~如果模数是1 那齿轮的齿顶高不就是1了吗,??? 这不对呀, 不知道我哪里算错了齿顶高系数:ha* =1齿顶间隙系数:c*=0.25以上是标准齿轮、正常齿高的两个系数,是标准值。
对于非标准齿轮(变位齿轮),以上两个参数会有变化,并且有时变化的程度还很大。
问题补充:还问一下~如果模数是1 那齿轮的齿顶高不就是1了吗,??? 对啊。
此时齿顶高就是1毫米啊。
齿根高是1.25毫米。
齿全高是2.25毫米。
齿轮各部分计算公式
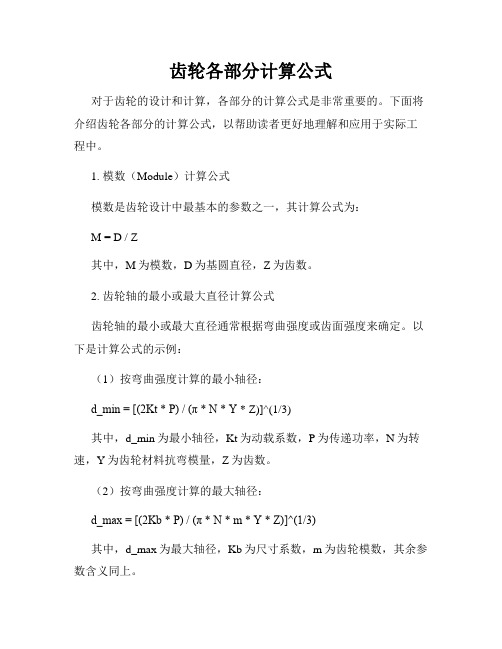
齿轮各部分计算公式对于齿轮的设计和计算,各部分的计算公式是非常重要的。
下面将介绍齿轮各部分的计算公式,以帮助读者更好地理解和应用于实际工程中。
1. 模数(Module)计算公式模数是齿轮设计中最基本的参数之一,其计算公式为:M = D / Z其中,M为模数,D为基圆直径,Z为齿数。
2. 齿轮轴的最小或最大直径计算公式齿轮轴的最小或最大直径通常根据弯曲强度或齿面强度来确定。
以下是计算公式的示例:(1)按弯曲强度计算的最小轴径:d_min = [(2Kt * P) / (π * N * Y * Z)]^(1/3)其中,d_min为最小轴径,Kt为动载系数,P为传递功率,N为转速,Y为齿轮材料抗弯模量,Z为齿数。
(2)按弯曲强度计算的最大轴径:d_max = [(2Kb * P) / (π * N * m * Y * Z)]^(1/3)其中,d_max为最大轴径,Kb为尺寸系数,m为齿轮模数,其余参数含义同上。
3. 齿宽计算公式齿宽是齿轮上两齿间的宽度,其计算公式为:b = m * z其中,b为齿宽,m为模数,z为齿数。
4. 齿顶高计算公式齿顶高是齿轮齿形中顶面的高度,其计算公式为:ha = 0.5m * (α + β)其中,ha为齿顶高,m为模数,α为压力角,β为顶隙角。
5. 齿根高计算公式齿根高是齿轮齿形中根面的高度,其计算公式为:hf = 1.25 * ha其中,hf为齿根高,ha为齿顶高。
6. 齿根圆直径计算公式齿根圆直径是齿轮齿形中根部的圆直径,其计算公式为:df = D - 2hm - 2hf其中,df为齿根圆直径,D为基圆直径,hm为齿顶高。
以上是几个常用的齿轮各部分的计算公式。
通过这些公式,可以更好地进行齿轮设计和计算,确保齿轮的准确性和可靠性。
在实际工程中,根据具体需求和材料特性,还可以进行进一步的调整和优化。
齿轮尺寸计算

齿轮尺寸计算《齿轮尺寸计算》
一、螺旋齿轮尺寸计算
1、计算齿轮模数:
齿轮模数=齿轮外径÷齿数。
2、计算齿轮基圆:
齿轮基圆=模数×齿数。
3、计算齿顶圆:
齿顶圆=齿轮基圆+2×模数。
4、计算齿根圆:
齿根圆=齿轮基圆-2×模数。
5、计算齿宽:
齿宽=模数×0.7071。
二、圆柱齿轮尺寸计算
1、计算齿轮模数:
齿轮模数=齿轮外径÷齿数。
2、计算齿厚:
齿厚=模数÷2。
3、计算齿顶圆半径:
齿顶圆半径=模数×0.5。
4、计算齿根圆半径:
齿根圆半径=模数×0.5。
三、立锥齿轮尺寸计算
1、计算齿轮模数:
齿轮模数=齿轮顶径÷齿数。
2、计算齿厚:
齿厚=模数÷2。
3、计算齿根母线夹角:
齿根母线夹角=180°÷齿数+顶隙角度。
4、计算齿顶面夹角:
齿顶面夹角=180°÷齿数-顶隙角度。
5、计算齿宽:
齿宽=模数×0.5。
齿轮计算程序(附带跨帮距转换为公法线)
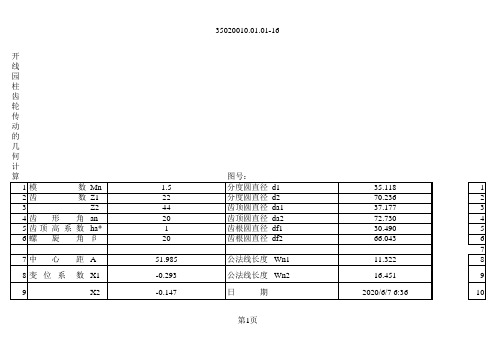
相 目公 式计 算结 果齿轮已知参数齿数Z122齿数Z244模数Mn 1.5中心距A51.985齿面宽B21100螺旋角β0.3490658520齿高系数ha*1齿形角an0.3490658520齿顶系数cn*0.25 1分度圆直径d1d1=Mn*Z1/COSΒ35.1178664935.118分度圆直径d2d2=Mn*Z2/COSΒ70.2357329870.236 2未变位时中心距Ad Ad=Mn*(Z1+Z2)/2COSΒ52.6767997452.677 3中心距变动系数Yn Yn=(A-Ad)/Mn-0.461199825-0.461 4啮合角a t'tgat=tgan/COSΒ0.3873290330.387 at=arctgat0.36953563421.173COSat'=Ad/A*COSat0.9449045140.945at'=arccosawt'0.33349354319.108 5总变位系数Xn invawt=tgawt-awt0.0129394340.013 invat=tgat-at0.01779340.018Xn=(Z1+Z2)*(invawt-invat)/(2*tgan)-0.440093307-0.440 6变位系数分配Xn1 Xn2Xn1 取值-0.29265-0.293 Xn2=Xn-Xn1-0.147-0.147 7齿顶高变动系数ΔYnΔYn=Xn-Yn0.0210.021 8齿顶高ha1 ha2ha1=(ha*+Xn1-ΔYn)*Mn 1.029365223 1.029 ha2=(ha*+Xn2-ΔYn)*Mn 1.247175262 1.247 9齿根高hf1 hf2hf1=(ha*+cn*-Xn1)*Mn 2.313975 2.314 hf2=(ha*+cn*-Xn2)*Mn 2.096164961 2.096 10齿高 h1 h2h1=ha1+hf1 3.343 3.343h2=ha2+hf2 3.343 3.343 11齿顶圆直径da1 da2da1=d1+2*ha137.1765969437.177 da2=d2+2*ha272.7300835172.730 12齿根圆直径df1 df2df1=d1-2*hf130.4899164930.490 df2=d2-2*hf266.0434030666.043 13公法线计算Wn1 Wn2当量齿数 Z*1 Z*2Z*1=Z1*invat/invan26.2644075926.264 Z*2=Z2*invat/invan52.5288151852.529跨测齿数 K1 K2(1+2*Xn/Z*)*(1+2*Xn/Z*)0.9559267940.9560.9888039010.989COSan*COSan0.8830222220.883SQRT0.2700084680.2700.3252409570.325K1 2.8454069763 K2 6.037974214 W*1 W*2W*=COS(PI(K-0.5)+Z**INVan)7.7481757637.74811.0681543711.068Wn1 Wn1=(W*1+2*Xn1*SINan)*Mn11.3219870611.322 Wn2Wn1=(W*2+2*Xn2*SINan)*Mn16.4509458216.451量棒直径dp 1.65*Mn 2.475 2.475实际量棒直径dp44invαMt invαMt=invαt+dp/Mn/Z/COSαn-3.1415926/2/Z+2*Xn*tg(αn)/Z0.065701550.041747475αMt24.1141偶数齿M137.1830305876.71131093偶数齿M276.71131093奇数齿M1奇数齿M22、根据C12数值选择C13单元参数(一般C12≯1,C13=0.5、或C13=0.5C12)3、C7单元参数输入角度数值4、该程序适用于外啮合齿轮的传动计算。
齿轮轴计算过程

倒档器锥齿轮计算因为转向器没有设置传动比 我选用两个材料和尺寸大小一样的锥齿轮 1)选择齿轮材料,确定许用应力由机械设计书表6.2选两齿轮材料为: 小齿轮40Cr 调质 HBS1=260 HBS大齿轮 45 正火 HBS2=210 HBS 许用接触应力[]H σ 由[]H σ=limminH N H Z S σg接触疲劳极限lim H σ查机械设计 图6-4 lim1H σ=700N/mm2接触强度寿命系数N Z 应力循环次数N lim2H σ=550N/mm N=60njL h =6080001(103004)⨯⨯⨯⨯⨯ N=5.76910⨯ 查图机械设计6-5(如没有特殊说明图表都来源于机械设计书)得N ZN Z =1接触最小安全系数lim H S lim H S =1[]1H σ =700 1/1⨯ []1H σ =700N/mm 2[]25501/1H σ=⨯ []2H σ =550N/ mm 2许用弯曲应力[]F σ 由式[]limminF F N X F Y Y S σσ=弯曲疲劳极限lim F σ 查图6-7 lim1F σ=540N/mm 2, 2lim 2420/F N mm σ= 弯曲强度寿命N Y 查图6-8 12N N Y Y ==1弯曲强度尺寸系数X Y 查图6-9(设模数m 小于5) X Y =1 弯曲强度最小安全系数min F S min F S =1.4 则[]1F σ=54011/1.4⨯⨯ []1F σ=450 N/mm 2 []2F σ= 42011/1.4⨯⨯ []2F σ=300 N/mm 2 2)齿面解除疲劳强度设计计算确定齿轮传动精度等级,估取圆周速度7/t m s υ=,参考表6-7 、6-8选取∏公差等级组7级锥齿轮分度圆直径d(1d ≥+齿宽系数dm ψ 查表6.14 dm ψ=0.3 小齿轮齿数1z =13 1z =13 那么 大齿轮齿数211z z i ==18.2圆整 2z =18 齿数传动比u=1.385 u=1.385 传动比误差为/u u V /(1.4 1.385)/1.40.01070.05u u =-=<V 倒档器输入轴扭矩1T1119550/T P n ==10050 N m g 1T =10050N •mm 载荷系数K= A V K K K βA K ——使用系数 查表6.3 A K =1.1 V K ——动载系数 由推荐值 1.05-1.4 V K =1.2 K β——齿向载荷分布系数 由推荐值1.0-1.2 K β=1.1载荷系数 K1.1 1.2 1.1A V K K K K β==⨯⨯ K=1.452材料弹性系数E Z 查6.4E Z 节点区域系数 H Z 查图6-3 H Z =2.5计算得d1≥44.74 mm d1≥44.74mm 齿轮模数m m=d1/z1=3.44 圆整 m=3.5 小齿轮大端分度圆直径 d1=mz1=3.5⨯13 d1=45.5mm 大齿轮大端分度圆直径 d2=mz2=3.5⨯18 d2=63mm 齿轮平均分度圆直径d m =/(1dd1m =45.5/(1+d 1m =38.7mmd2m ) d 2m =53.59mm圆周速度1m υ=3.141/60000m d n I 1m υ=16.2m/s 2m υ=3.1422/60000m d n2m υ=18.84m/s齿宽b b1=dm ψd 1m =11.61mm 圆整 b1=12mm b2=dm ψd 2m =16.007mm 圆整 b2=16mm 3)齿根弯曲疲劳强度校核计算 由式[]212(1F Fa Sa F KT Y Y bdm σσ=≤当量齿数v z11/cos 3016.04v z z δ===1v z =16.04221z z u υυ==30.75 2z υ=30.75 齿形系数Fa Y 应力修正系数Sa Y 查表 6.5 1Fa Y =3.21,2 2.91Fa Y =1Sa Y =1.46,2Sa Y =1.53计算弯曲疲劳强度1F σ=197.17<[]H σ 所以齿根弯曲强度满足 4)齿轮其他主要尺寸计算 分度锥角1cos δ=0.8107 1δ=35.83o锥距255.1R ==R=55.1mm齿顶高 3a a h h m mm *==齿根高 () 3.6f a h h c m mm **=+=齿顶圆直径2cos 82.24a a d d h mm δ=+=齿根圆直径 2cos 72.9f f d d h mm δ=-=齿顶角 arctan(/) 3.1a a h R θ== 齿根角 arctan(/) 3.7f f h R θ== 4)结构设计及绘制齿轮零件图花键连接强度计算花键轴的内径为20mm,轴与发动机轴用凸缘联轴器连接;选取花键规格N d D B ⨯⨯⨯为620245⨯⨯⨯;因为花键是连接发动机输出轴和转向器轴,因此,他们是动连接。
齿轮宽度 计算
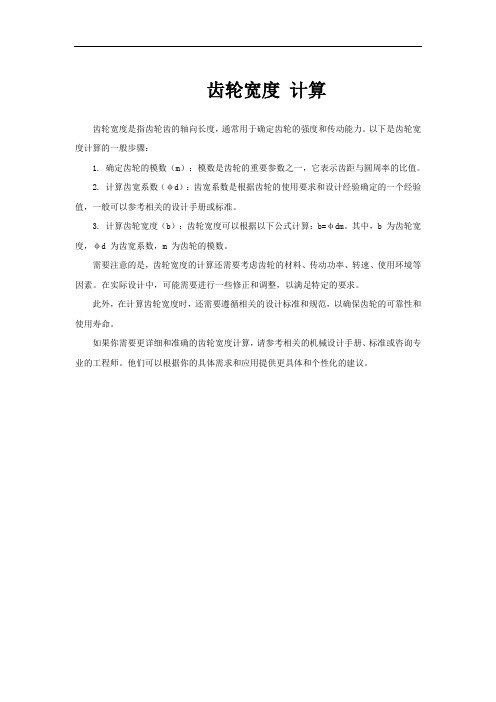
齿轮宽度计算
齿轮宽度是指齿轮齿的轴向长度,通常用于确定齿轮的强度和传动能力。
以下是齿轮宽度计算的一般步骤:
1. 确定齿轮的模数(m):模数是齿轮的重要参数之一,它表示齿距与圆周率的比值。
2. 计算齿宽系数(φd):齿宽系数是根据齿轮的使用要求和设计经验确定的一个经验值,一般可以参考相关的设计手册或标准。
3. 计算齿轮宽度(b):齿轮宽度可以根据以下公式计算:b=φdm。
其中,b 为齿轮宽度,φd 为齿宽系数,m 为齿轮的模数。
需要注意的是,齿轮宽度的计算还需要考虑齿轮的材料、传动功率、转速、使用环境等因素。
在实际设计中,可能需要进行一些修正和调整,以满足特定的要求。
此外,在计算齿轮宽度时,还需要遵循相关的设计标准和规范,以确保齿轮的可靠性和使用寿命。
如果你需要更详细和准确的齿轮宽度计算,请参考相关的机械设计手册、标准或咨询专业的工程师。
他们可以根据你的具体需求和应用提供更具体和个性化的建议。
- 1、下载文档前请自行甄别文档内容的完整性,平台不提供额外的编辑、内容补充、找答案等附加服务。
- 2、"仅部分预览"的文档,不可在线预览部分如存在完整性等问题,可反馈申请退款(可完整预览的文档不适用该条件!)。
- 3、如文档侵犯您的权益,请联系客服反馈,我们会尽快为您处理(人工客服工作时间:9:00-18:30)。
计算过程[解] 1.选定齿轮类型、精度等级、材料及齿数(1)按图10-26所示的传动方案,选用直齿圆柱齿轮传动,压力角取为20°。
(2)带式输送机为一般工作机器,参考表10-6,选用7级精度。
(3)材料选择。
由表10-1,选择小齿轮材料为40Cr(调质),齿面硬度280HBS,大齿轮材料为45钢(调质),齿面硬度240HBS。
(4)选小齿轮齿数z1=24,大齿轮齿数z2=uz1=4.5×24=108,取z2=108。
2.按齿面接触疲劳强度设计(1)由式(10-11)试算小齿轮分度圆直径,即d1t≥√2K Ht T1φd∙u+1u∙(Z H Z E Zε[σH])231)确定公式中的各参数值○1试选K Ht=1.3。
○2计算小齿轮传递的转矩。
T1=9.55×106Pn1=9.55×106×7.5970N∙mm=7.384×104N∙mm○3由表10-7选取齿宽系数φd=1。
○4由图10-20查得区域系数Z H=2.5。
○5由表10-5查得材料的弹性影响系数Z E=189.8MPa1/2。
○6由式(10-9)计算解除疲劳强度用重合度系数Zε。
αa1=arccos[z1cosα/(z1+2ℎa∗)]=arccos[24×cos20°/(24+2×1)]=29.841°αa2=arccos[z2cosα/(z2+2ℎa∗)]=arccos[108×cos20°/(108+2×1)]=22.690°εα=[z1(tanαa1−tanα′)+z2(tanαa2−tanα′)]2π=[24×(tan29.841°−tan20°)+108×(tan22.690°−tan20°)]2π=1.731Zε=√4−εα3=√4−1.7313=0.870○7计算解除疲劳许用应力[σH]。
由图10-25d查得小齿轮和大齿轮的解除疲劳极限分别为σHlim1=600MPa、σHlim2= 550MPa。
由式(10-15)计算应力循环次数:N1=60n1jLℎ=60×970×1×(2×8×300×15)=4.190×109N2=N1u=4.190×109108/24=9.311×108取失效概率为1%、安全系数S=1,由式(10-14)得[σH]1=K HN1σHlim1S=0.90×6001MPa=540MPa[σH]2=K HN2σHlim2S=0.98×5501MPa=539MPa取[σH]1和[σH]2中较小者作为该齿轮副的解除疲劳许用应力,即[σH]=[σH]2=539MPa2)试算小齿轮分度圆直径d1t≥√2K Ht T1φd∙u+1u∙(Z H Z E Zε[σ])23=√2×1.3×7.384×1041×(10824)+1(10824)×(2.5×189.8×0.87539)23mm=51.763mm(2)调整小齿轮分度圆直径1)计算实际载荷系数前的数据准备。
○1圆周速度v。
v=πd1t n160×1000=π×51.632×97060×1000m/s=2.6m/s○2齿宽b。
b=φd d1t=1×51.632mm=51.632mm3)计算实际载荷系数K H。
○1由表10-2查得使用系数K A=1。
○2根据v=2.6m/s、7级精度,由图10-8查得动载系数K v=1.08。
○3齿轮的圆周力。
F t1=2T1d1t=2×7.384×10451.632N=2.86×103NK A F t1 b =1×2.86×10351.632N/mm=55.4N/mm<100N/mm查表10-3得齿间载荷分配系数K Hα=1.2。
○4由表10-4用插值法查得7级精度、小齿轮相对支承非对称布置时,得齿向载荷分布系数K Hβ=1.421。
由此,得到实际载荷系数K H=K A K v K HαK Hβ=1×1.08×1.2×1.421=1.844) 由式(10-12),可得按实际载荷系数算得的分度圆直径d 1=d 1t √K H K Ht 3=51.632×√1.841.33=57.971mm 及相应的齿轮模数m =d 1z 1⁄=57.97124⁄mm =2.415mm 3.按齿根弯曲疲劳强度设计(1)由式(10-7)试算模数,即m t ≥√2K Ft T 1Y εφd z 12∙(Y Fa Y sa [σF ])31) 确定公式中的各参数值○1试选K Ft =1.3。
○2由式(10-5)计算弯曲疲劳强度用重合度系数。
Y ε=0.25+0.75εα=0.25+0.751.731=0.683 ○3计算 Y Fa Y sa σF 。
由图10-17查得齿形系数Y Fa1=2.65、Y Fa2=2.23。
由图10-18查得应力修正系数Y sa1=1.58、Y sa2=1.76。
由图10-24c 查得小齿轮和大齿轮齿根弯曲疲劳极限分别为σFlim1=500MPa 、σFlim2=380MPa由图10-22查得弯曲疲劳寿命系数K FN1=0.85,K FN2=0.88。
取弯曲疲劳安全系数S=1.4,由式(10-14)得[σF ]1=K FN1σFlim1=0.85×500MPa =303.75MPa [σF ]2=K FN2σFlim2S =0.88×3801.4MPa =238.86MPa Y Fa1Y sa1[F ]1=2.65×1.58=0.0138 Y Fa2Y sa2[σF ]2=2.23×1.76238.86=0.0164 因为大齿轮的 Y Fa Y sa σF 大于小齿轮,所以取 Y Fa Y sa [F ]=Y Fa2Y sa2[F ]2=0.0164 2) 计算模数m t ≥√2K Ft T 1Y εφd z 12∙(Y Fa Y sa [σF ])3=√2×1.3×7.384×104×0.6831×242×0.01643mm =1.551mm(2)调整齿轮模数1)计算实际载荷系数前的数据准备。
○1圆周速度v 。
d 1=m t z 1=1.551×24mm =37.224mmv =πd 1n 160×1000=π×37.224×97060×1000m/s =1.89m/s ○2齿宽b 。
b =φd d 1=1×37.224mm =37.224mm○3宽高比。
h =(2ℎa ∗+c ∗)m t =(2×1+0.25)×1.551mm =3.49mmb h =37.2243.49=10.67 3) 计算实际载荷系数K F 。
○1根据v=1.89m/s ,7级精度,由图10-8查得动载系数K v =1.04。
○2由F t1=3.967×103N ,K A F t1b ⁄=107N mm >100N mm ,查表10−3得齿间载荷分配系数K Fα=1.0。
○3由表10-4用插值法查得K Hβ=1.417,结合b h =10.67查图10−13,得K Fβ=1.34。
则载荷系数为K F =K A K v K FαK Fβ=1×1.04×1.0×1.34=1.394) 由式(10-13),可得按实际载荷系数算得的齿轮模数m =m t √K F K Ft 3=1.551×√1.391.33=1.586mm 对比计算结果,由齿面接触疲劳强度计算的模数m 大于由齿根弯曲疲劳强度计算的模数,由于齿轮的模数m 的大小主要取决于弯曲疲劳强度所决定的承载能力,而齿面接触疲劳强度所决定的承载能力,仅与齿轮直径有关,可取由弯曲疲劳强度算得的模数.586mm 并就近圆整为标准值m=2mm ,按接触疲劳强度算得的分度圆直径d 1=57.971mm ,算出小齿轮齿数z 1=d 1m ⁄=28.99。
取z 1=29,则大齿轮齿数z 1=uz 2=4.5×29=130.5,取z 2=131,z 1与z 2互为质数。
4.几何尺寸计算(1)计算分度圆直径d 1=z 1m =29×2mm =58mmd 2=z 2m =131×2mm =262mm(2)计算中心距a =(d 1+d 2)/2=(58+262)/2mm =160mm(3)计算齿轮宽度b =φd d 1=1×58mm =58mm考虑不可避免的安装误差,为了保证设计齿宽b 和节省材料,一般将小齿轮略为加宽(5~10)mm ,即b 1=b +(5~10)mm =63~68mm取b 1=65mm ,而使大齿轮的齿宽等于设计齿宽,即b 2=b =58mm 。
5.圆整中心距后的强度校核(1)齿面接触疲劳强度校核按前述类似做法,先计算式(10-10)中的各参数。
K H =1.86,T 1=7.384×104N ∙mm ,φd =1,d 1=58mm ,u =4.5,Z H =2.5,Z E =189.8MPa 1/2,Z ε=0.864。
将它门代入式(10-10),得到σH =√2K H T 1φd d 13∙u +1∙Z H Z E Z ε=√2×1.86×7.384×1041×583∙4.5+14.5∙2.5×189.8×0.864MPa =538MPa <[σH ]齿面接触疲劳强度满足要求,并且齿面接触应力比标准齿轮有所下降。
(3)齿根弯曲疲劳强度校核按前述类似做法,先计算式(10-6)中的各参数。
K F =1.46,T 1=7.384×104N ∙,Y Fa1=2.65、Y Fa2=2.23,Y sa1=1.58、Y sa2=1.76,Y ε=0.676,φd =1,m =2mm ,z 1=29。
将它门代入式(10−6),得到σF1=2K F T 1Y Fa1Y sa1Y εφd m 3z 12=2×1.58×7.384×104×2.65×1.58×0.6761×8×292=98<[σF ]1 σF2=2K F T 1Y Fa2Y sa2Y εφd m 3z 12=2×1.58×7.384×104×2.23×1.76×0.6761×8×292=92<[σF ]1 齿根弯曲疲劳强度满足要求,并且大齿轮抵抗弯曲疲劳破坏的能力大于小齿轮。