第一章铸造成型
第一章铸造成形工艺理论基础

⑵ 浇注温度
主要影响液态收缩。浇注温度提高,液态收缩
增加。
⑶ 铸型条件
铸件的实际收缩率要小于合金的自由线收缩率。
第一章 铸造成形工艺理论基础
24
材料成形工艺基础
几种铁碳合金的收缩率
合金 种类 碳素 铸钢 白口 铸铁
灰铸铁 5~8
1.08
球墨 铸铁
体收缩率/%
线收缩率/%
10~14
2.17
12~14
(1)热应力 概念:由于铸件壁厚不均匀以及散热条件的差异, 造成不同部位冷却速度不同,由此产生的铸造应力 称为热应力。
第一章 铸造成形工艺理论基础
35
材料成形工艺基础
形成过程 分布规律:铸件厚壁部分或心部存在拉应力,受拉应力的 部位变形时趋于缩短向内凹;薄壁部分或表面存在压应力, 受压应力的部位变形时趋于伸长向外凸。
第一章 铸造成形工艺理论基础
13
材料成形工艺基础
标 准 螺 旋 线 试 样
1-浇注系统;2-试样;3-出气口 ;4-试样凸台
第一章 铸造成形工艺理论基础
14
材料成形工艺基础
合金的化学成分 及结晶特点对流动 性的影响
第一章 铸造成形工艺理论基础
15
材料成形工艺基础
逐层凝固
中间凝固
糊状凝固
第一章 铸造成形工艺理论基础
16
材料成形工艺基础
液态金属在结晶状态下的 流动示意图
a)纯金属
b)结晶温度范围宽的合金
17
第一章 铸造成形工艺理论基础
材料成形工艺基础
2.浇注条件
1)浇注温度
浇注温度越高,流动性越好,充型能力越强。 但浇注温度不能过高,否则合金的吸气、氧化 现象严重,易产生气孔、夹渣等缺陷。
第一章铸造工艺基础

1-3铸造内应力、变形和裂纹
• 铸造内应力:铸件的固态收缩受到阻碍而引起的内应力。 • 残余内应力:一直保持到室温的铸造内应力 • 临时内应力:在冷却过程中暂存的铸造内应力 • 铸造内应力是铸件产生变形和裂纹的基本原因 • 按内应力产生原因不同分为热应力和机械应力 一、铸造内应力的形成 • 介绍热应力和机械应力的产生 1.热应力: • 1)定义:由于铸件的壁厚不均,各部分冷却速度不同,各部分收缩 不一致引起的内应力。 • 2)金属应力状态改变:(金属自高温至室温) • 金属在再结晶温度以上处于塑性状态,在再结晶温度以下处于弹性状 态,再结晶温度是分界点 • 塑性状态降温 弹性状态 • 弹性状态升温 塑性状态
流动性
二、浇注条件 • 1.浇注温度: “决定性”影响 浇温升高充型能力越强 • 实践中可利用此规律对薄壁铸件或流动性较差的合金可适当提高浇温, 提高充型能力 • 浇温也不宜过高,否则易产生缩孔、缩松等缺陷 • 2.充型压力 • 合金受压越大充型能力越强 三、铸型填充条件 • 1.铸型材料: • 铸型导热系数和比热容升高,合金充型能力下降 • 2.铸型温度: • 铸型温度升高减缓冷却速度,充型能力升高 • 3.铸型中气体: • 铸型中气体阻碍液体合金的充型,应减少之.
三、铸件的裂纹与防止 • 铸造内应力超过材料强度极限时产生裂纹 1.热裂 • (1)定义:在高温下形成的裂纹 • (2)形状特征:缝隙宽、形状曲折、缝内呈氧化色 • (3)形成原因:合金完全凝固前固态收缩已开始,晶粒间存在液体, 强度、塑性低 • (4)分布:一般分布在应力集中部位 • (5)主要影响因素:合金性质、铸型阻力 • (6)防止方法①使铸件结构合理②改善铸型和型芯的退让性③减少 浇、冒口对铸件收缩的机械阻碍④内浇口设置符合同时凝固原则⑤减 少合金中有害杂质含量。 2.冷裂 • (1)含义:在低温下形成的裂纹 • (2)形状特征:裂纹细小,呈连续直线状,缝内呈轻微氧化色 • (3)分布:常出现在形状复杂工件的受拉伸部分
材料成型技术基础知识点总结
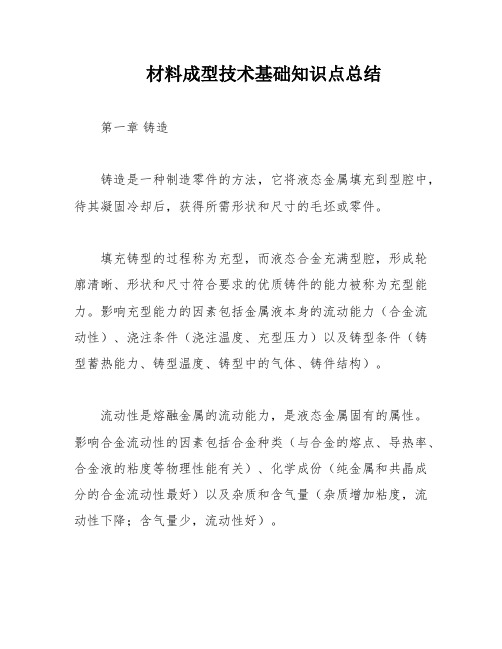
材料成型技术基础知识点总结第一章铸造铸造是一种制造零件的方法,它将液态金属填充到型腔中,待其凝固冷却后,获得所需形状和尺寸的毛坯或零件。
填充铸型的过程称为充型,而液态合金充满型腔,形成轮廓清晰、形状和尺寸符合要求的优质铸件的能力被称为充型能力。
影响充型能力的因素包括金属液本身的流动能力(合金流动性)、浇注条件(浇注温度、充型压力)以及铸型条件(铸型蓄热能力、铸型温度、铸型中的气体、铸件结构)。
流动性是熔融金属的流动能力,是液态金属固有的属性。
影响合金流动性的因素包括合金种类(与合金的熔点、导热率、合金液的粘度等物理性能有关)、化学成份(纯金属和共晶成分的合金流动性最好)以及杂质和含气量(杂质增加粘度,流动性下降;含气量少,流动性好)。
金属的凝固方式包括逐层凝固方式、体积凝固方式或称“糊状凝固方式”以及中间凝固方式。
收缩是液态合金在凝固和冷却过程中,体积和尺寸减小的现象。
收缩能使铸件产生缩孔、缩松、裂纹、变形和内应力等缺陷。
合金的收缩可分为三个阶段:液态收缩、凝固收缩和固态收缩。
液态收缩和凝固收缩通常以体积收缩率表示,是铸件产生缩孔、缩松缺陷的基本原因。
合金的固态收缩通常用线收缩率来表示,是铸件产生内应力、裂纹和变形等缺陷的主要原因。
影响收缩的因素包括化学成分(碳素钢随含碳量增加,凝固收缩增加,而固态收缩略减)、浇注温度(浇注温度愈高,过热度愈大,合金的液态收缩增加)、铸件结构(铸型中的铸件冷却时,因形状和尺寸不同,各部分的冷却速度不同,结果对铸件收缩产生阻碍)以及铸型和型芯对铸件的收缩也产生机械阻力。
缩孔和缩松是铸件凝固结束后常常在某些部位出现孔洞,按照孔洞的大小和分布可分为缩孔和缩松。
缩孔的形成主要出现在金属在恒温或很窄温度范围内结晶,铸件壁呈逐层凝固方式的条件下。
缩松的形成主要出现在呈糊状凝固方式的合金中或断面较大的铸件壁中,是被树枝状晶体分隔开的液体区难以得到补缩所致。
合金的液态收缩和凝固收缩越大,浇注温度越高,铸件的壁越厚,缩孔的容积就越大。
铸造课件论述

铸造成形的作用:
金属的液态成形是制造毛坯、零件的重要方法之一。按铸型材 料的不同,金属液态成形可分为砂型铸造和特种铸造(包括压力铸 造、金属型铸造等).其中砂型铸造是最基本的液态成形方法,所生 产的铸件要占铸件总量的80%以上.
铸造成型的优点
适于做复杂外形,特别是 复杂内腔的毛坯 对材料的适应性广,铸件 的大小 几乎不受限制
铸件在固态收缩时,因受到铸型、型 芯、浇冒口、砂箱等外力阻碍而产生 的应力。
内应力
机械应力
变形
残余热应力的存在,使铸件处在一种非稳定 状态,将自发地通过铸件的变形来缓解其应 力,以回到稳定的平衡状态。
裂纹
当热应力大到一定程度会导致出现裂纹。
热应力的形成过程演示
热应力的消除方法
铸件的结构:铸件各部分能自由收缩
(二)孕育铸铁
提高和改善普通灰铸铁 的力学性能的途径
改善基体组织 改变石墨形态、数量、 大小和分布
孕育处理:在浇注前往铁液中加入孕育剂,以产生大量人工晶核和 改善铁液的结晶条件,得到分布均匀的细小片状石墨和细珠光体基 体。常用的孕育剂是含Si量为75%的硅铁。
即将熔炼出的铁水在 浇铸前加入质量分数 为 0.25%~0.60%的孕育剂,孕育剂在铁水 中形成大量弥散的石墨结晶核心,使石墨化 作用显著提高,从而得到在细珠光体上 均匀分布着细片状石墨的组织。
灰铸铁的铸造性能:流动性好、
收缩小,铸造性能好,
具有自身补缩的能力。
铸造工艺特点:冲天炉熔炼(金属炉料、燃料、熔剂) 砂型铸造 常采用同时凝固原则,高强度采用顺序凝固
(三)球墨铸铁
向高温灰铸铁水中加入一定量的球化剂和 孕育剂,直接得到球状石墨的铸造合金。
要求含碳要高:3.6~4% 球化剂:金属镁或稀土镁 孕育剂:含Si量为75%或95%的硅铁
第一章 铸造成型工艺理论基础

① 热应力。热应力是由于铸件各部分冷却速度不同, 以致在同一时间内铸件各部分收缩不一致,导致相互约束 引起的内应力。
为了分析热应力的形成过程,首先应了解固态金属自 高温冷却到室温时力学状态的变化。固态金属在再结晶温
度(钢和铸铁为620~650℃)以上时,处于塑性状态,此
时在极小的应力作用下,便可发生塑性变形(即永久变
(2)缩孔与缩松的防止 ② 缩松的防止。缩松是细小分散的缩孔,它对铸件承 载能力的影响比集中缩孔要小,但它影响铸件的气密性,
使铸件渗漏。因此对气密性要求高的油缸、阀体等承压铸
件,必须采取措施来防止缩松。目前生产中多采用在热节
处安放冷铁,加大铸件的冷却速度;或加大结晶压力,以
破碎枝晶,减少金属液的流动阻力,从而达到部分防止缩
一、合金的充型
液态合金填充铸型的过程简称为充型。合金的充型能 力,是指液态合金充满铸型,获得轮廓清晰、形状准确的 铸件的能力。若液态合金的充型能力不足,铸件将产生浇 不到、冷隔等缺陷。影响充型能力的因素很多,其中主要 的是合金的流动性、浇注条件和铸型的充型条件。
1、合金的流动性
合金的流动性是指合金本身在液态下的流动能力,流 动性好,易获得轮廓清晰的薄壁复杂铸件。反之产生浇不 到、冷隔等缺陷。影响合金流动性其中的一个主要因素是 合
教学内容:该课程包括了除机械切削加工工艺以外的所有工 程材料的成形工艺,内容十分丰富,但由于学时有限,结合 我们的就业方向,讲授以铸、锻、焊和塑料成形为主,适当 兼顾别的内容。 教学目的:通过学习使学生能根据零件的使用性能和批 量大小正确的选择工程材料和正确的选择成形工艺、 通过借助设计资料能够进行成形工艺设计。 教学时数:40学时(理论36学时、实验4学时) 考核方式:闭卷 所用教材:材料成型工艺基础(华中科技大学出版社) 参考书目:材料成型基础、材料成型工艺、材料成型工 艺基础、冲压工艺学、塑料成形模具等等。
电子课件——机械制造工艺基础(第七版) 1第一章 铸造

1 §1—1 概述 2 §1—2 砂型铸造 3 §1—3 特种铸造及铸造新技术
第一章 铸造
§1—1 铸造基础
一、 铸造及其分类
将熔融金属浇注、压射或吸入铸型型 腔中,凝固后获得具有一定形状、尺寸 和性能的毛坯或零件
砂型铸造
铸 造
特种铸造
熔模铸造 金属型铸造 压力铸造 离心铸造
§第1一—章1 铸铸造造基础
整模两箱造型
§第1—一2章 砂型铸铸造造
模样分成两 部分,分别 制造上型和 下型,型腔 则位于上型 和下型之间
分模两箱造型
§第1—一2章 砂型铸铸造造
2)脱箱造型 在可脱砂箱内造型,合型后浇注前脱去砂箱
§第1—一2章 砂型铸铸造造
3)挖沙造型 下型分型面挖成不平分型面(曲面、非平面)
§第1—一2章 砂型铸铸造造
气动微振压实造型机紧砂
§第1—一2章 砂型铸铸造造
3.造芯
制造型芯的过程称为造芯
手工造芯 机器造芯
芯盒造芯
§第1—一2章 砂型铸铸造造
4.合型
又称合箱,是将铸型的各个组元 组合成一个完整铸型的操作过程
5.熔炼
熔炼是使金属由固态转变为熔融状态的过程
§第1—一2章 砂型铸铸造造
6.浇注
(1)浇注工具
4.铸造圆角
相邻两表面的过渡圆角
§第1—一2章 砂型铸铸造造
5.芯头
在模样上:芯头是模样的凸出部分 在型芯上:芯头是型芯的外伸部分
§第1—一2章 砂型铸铸造造
6.浇注系统
(1)外浇口 (2)直浇道 (3)横浇道 (4)内浇道
7.冒口
§第1—一2章 砂型铸铸造造
三、砂型铸造的工艺过程
1.混砂
第一章铸造成形工艺理论基础

随着人们对金属材料(青铜、钢铁等)的使用,相应 地产生了铸造、锻造、焊接等金属成形加工技术。
20世纪以后,随着塑料和先进陶瓷材料的出现,这 些非金属材料的成形工艺得到了迅速发展;
在跨人21世纪后的今天,已进入了各种人工设计、 人工合成的新型材料层出不穷的新时代,各种与之 相应的先进的成形工艺也在不断涌现并大显身手。
第一章铸造成形工艺理 论基础
2020/12/1
第一章铸造成形工艺理论基础
在现代机械产品的制造过程中,一般是应用材料成 形的方法将材料制成毛坯,再经过机械加工方法制 成所需的零件。
材料成形工艺是指用于把材料从原材料的形态通 过加工而转变为具有所要求的形状及尺寸的毛坯
或成品的所有加工方法或手段的总称。
先进的技术装备等等。
我国成功地进行了耗用钢水达490t的轧钢机机架和 长江三峡电站巨型水轮机的巨型铸件的铸造,锻造 了196t汽轮机转子;
采用铸一焊组合方法制造了12000t水压机的立柱 (高18m)、底座和横梁等大型零、部件;
我国已成功地生产出了用于锻造大型锻件的12000t 水压机;
解决了30万吨级远洋油轮船体的焊接技术;
第一章铸造成形工艺理论基础
20世纪中期以后,随着计算机、微电子、信息和 自动化技术的迅速融入,在涌现出一大批新型的 成形技术的同时,材料成形加工生产已开始向着 优质化、精密化、绿色化和柔性化的方向发展。
第一章铸造成形工艺理论基础
我国材料成形技术的发展历史
我国的材料成形技术具有悠久的历史 明朝大科学家宋应星编著的《天工开物》一书中,
➢工艺过程----将原料或半成品加工成产品的 过程。
机械制造工艺基础课件第一章铸造

2.制造模样与芯盒的注意要点
(1)分型面——铸型组元间的接合面。
1—上型
2—分型面 3—型芯
4—支座型腔
5—芯头 6—下型
第十七页,共五十八页,2022年,8月28日
(2)收缩余量——为了补偿铸件收缩,模样比铸件图样尺 寸增大的数值。
(3)加工余量——为保证铸件加工面尺寸和零件精度, 在铸造工艺设计时预先增加而在机械加工时切去的金属层厚 度。
第十八页,共五十八页,2022年,8月28日
(4)起模斜度——为使模样容易从铸型中取出或型芯从芯盒
中脱出,在模样或芯盒上平行于起模方向所设的斜度。
一般α=0.5 ° ~3°
第十九页,共五十八页,2022年,8月28日
(5)铸造圆角——制造模样时,凡相邻两表面的交角,都 应做成圆角。
铸造圆角(r为铸造圆角半径)
第四十五页,共五十八页,2022年,8月28日
握包
抬包
吊包
第四十六页,共五十八页,2022年,8月28日
2.浇注温度与浇注速度
浇注温度(℃)——金属熔液浇入铸型时所测量到的温度 。
浇注速度(kg/s)——单位时间内浇入铸型中的金属熔液质量
。
第四十七页,共五十八页,2022年,8月28日
二、落砂和清理
四、 造芯 五、浇注系统及冒口 六、合型
第十页,共五十八页,2022年,8月28日
一、砂型和造型材料
1. 造型材料 2. 型砂和芯砂 3. 砂型
第十一页,共五十八页,2022年,8月28日
1.造型材料
造型材料——制造砂型和砂芯的材料。 1砂 2 黏土
3 黏结剂 4 附加物
第十二页,共五十八页,2022年,8月28日
第八页,共五十八页,2022年,8月28日
精选第一章铸造成形工艺理论基础

合金的铸造性能: 充型能力收缩性吸气性
第二节 合金的铸造性能
合金的铸造性能是指在铸造过程中获得尺寸精确、结构完整的铸件的能力。
合金铸造性能是选择铸造金属材料,确定铸件的铸造工艺方案及进行铸件结构设计的依据。
铸造性能对获得合格的铸件有很大的影响。
一、合金的充型能力
充型能力:熔融合金充满铸型型腔,获得形状完整、轮廓清晰铸件的能力。
我国成功地进行了耗用钢水达490t的轧钢机机架和长江三峡电站巨型水轮机的巨型铸件的铸造,锻造了196t汽轮机转子;采用铸一焊组合方法制造了12000t水压机的立柱(高18m)、底座和横梁等大型零、部件;我国已成功地生产出了用于锻造大型锻件的12000t水压机;解决了30万吨级远洋油轮船体的焊接技术;CAD/CAE/CAM等计算机技术及机器人技术在材料成形技术中得到越来越广泛的应用,粉末冶金、高分子、陶瓷、复合材料制品的应用也日益扩大等等。
第一篇 金属的铸造成形工艺
铸 造
工艺基础
铸件生产
结构设计
铸造工艺
1
2
3
4
工艺性能
第一章 铸造成形工艺理论基础
定义:铸造(casting)是指将熔融态的金属(或合金)浇注于特定型腔的铸型中,冷却凝固后获得毛坯或零件的成形工艺。
铸造的基本过程:
第一节 铸造成形工艺的特点和分类
成分
温度
这种凝固方式犹如水泥凝固,先呈糊状而后固化,凝固前沿粗糙,对金属流动的阻力大,因而充型能力差,容易产生铸造缺陷。
特征
远离共晶点成分的合金,如锡青铜、球墨铸铁及高碳钢等
3. 中间凝固
介于逐层凝固和糊状凝固之间,大多数合金为此凝固方式。
温度
机械工艺第一章 铸造教案

授课 内容 授课 班级
第一章 第一节
铸造 铸造Байду номын сангаас础
授课 时间 第一周 第二学时 课程 类型 理论
授课 教师 授课 地点
王慧婷
了解铸造及其分类; 教学 了解铸造的特点; 目标 了解铸造的应用 了解铸造安全文明生产要求; 安 重 了解铸造及其分类; 全 教 点 了解铸造的特点;
学 重 点 难 点 难 点
〈课堂小结〉
1、明确学习目的,要有学好本课程的信心; 2、作风认真严肃,决不敷衍了事。 3、了解铸件及其分类 4、了解铸造的特点 5、了解铸造的应用 6、了解铸造安全文明生产要求 〈作业布置〉 课堂作业: 1、铸造的特点? 2、铸造安全文明生产要求? 课后作业:
1.? 2.?
教学 反思
通过课桌 上书本的 整理,强 化 6S 管 理。
2、 3、
操作人员必须按规定穿戴好劳动保护用品。 熔炼炉炉体及其附属设施完好,控制系统灵敏可靠,升 降起吊装置符合起重机械要求,炉坑干燥并设护栏或盖 板,炉料符合专门要求。
4、
铸造设备完好,操纵灵敏,安全防护装置齐全可靠,除 尘装置符合要求。
5、
压铸机压铸型区有防护装置并与压射程序联锁;制芯机 芯盒加热棒长短适中,线头连接可靠;混砂机防护罩牢 固可靠,检修门电器联锁;抛(喷)丸机密封良好,门 孔电器联锁。
二、 铸造的特点 1、 (1) 优点 可以生产出形状复杂,特别是具有复杂内腔的工件毛 坯,如各种箱体、床身、机架等。 (2) 产品的适应性广,工艺灵活性大,工业上常用的金属材 料均可进行铸造,铸件的质量可由几克到几百顿。 (3) 原材料大都来源广泛,价格低廉,并可直接利用废旧机 件,故铸造成本低。 2、 缺点 铸造组织疏松、晶粒粗大,内部容易产生缩孔、缩松、 气孔等缺陷,会导致铸件的力学性能特别是冲击韧度 低,铸件质量不稳定。 三、 铸造的应用 由于铸造具有上述特点,所以被广泛应用于机械工件的 毛坯制造。在各种机械和设备中,铸件质量占有很大的 比例,如拖拉机及其他农业机械中,铸件质量所占比例 达 40%~70%;在金属切削机床、内燃机中达 70%~80%, 在重型机械设备中则可高达 90%。但由于铸造易产生缺 陷,性能不高,因此多用于制造承受应力不大的工件 四、 铸造安全文明生产要求 1、 行铸造的工作人员必须有相应的上岗证和操作证,持证 上岗。
第一章 铸造成型工艺理论基础

40
铸件热裂纹的防止
为有效地防止铸件裂纹的发生,应尽可能采 取措施减小铸造应力; 金属在熔炼过程中,应严格控制有可能扩大 金属凝固温度范围元素的加入量及钢铁中的 硫、磷含量;
提高型砂的退让性。
41
②冷裂纹
冷裂纹是在较低的温度下,由于热应力和收 缩应力的综合作用,铸件的内应力超过金属 的强度极限而产生的。 冷裂纹出现在铸件受拉的部位,尤其是应力 集中的地方。 冷裂纹的特征是:裂纹细小,呈连续直线状, 裂缝内有金属光泽或轻微氧化色。
防止铸件变形的措施: 减小内应力 铸件结构设计成对称的; 采用反变形法; 时效处理:精度要求较高-粗加工后人工时 效和自然时效。
38
铸件的裂纹及其防止
铸件的内应力超过金属 的强度极限时,铸件便 产生裂纹。 ①热裂纹:热裂纹是铸 件凝固末期,在接近固 相线的高温下形成的。 热裂纹的特征是:裂纹 短,缝隙宽,形状曲折, 裂纹内呈氧化色。
合金流动性的好坏,通常以“螺旋形流动性 试样”的长度来衡量。
16
影响流动性的因素
合金的种类 不同种类的合金,具有不同的螺旋线长度, 即具有不同的流动性。 灰铸铁的流动性最好,硅黄铜、铝硅合金次 之,而铸钢的流动性最差。
17
影响流动性的因素
合金的化学成分 纯金属和共晶成 分的合金,流动 性好。 非共晶合 金,流动性差。 结晶温度范围越 宽,流动性越差。
35
机械应力
铸件的固态收缩受到铸型或型芯的机械阻碍 而形成的内应力。 其大小主要取决于铸型及型芯的退让性,落 砂后消失。
36
铸件的变形及其防止
铸件的变形包括铸件凝固后所发生的变形以 及随后的切削加工变形。 受拉的部位缩短; 受压的部位伸长; 杆件和板件最明显;
第一章 金属型铸造

2)水平分型金属型 如图1-19所示,铸型主体由上、 下两半型组成,下半型固定在工作台面上,上半型 作开(合)型动作。可以配置各种型芯,抽芯及顶 出。砂芯安放方便,但不便于设计浇、冒口系统, 排气条件差。适用于轮盘类铸件。
金属型的预热方法主要有: 1)用煤气或天然气火焰预热。该方法简单、 方便,但金属型上温度分布不均匀。 2)采用电加热方法。在模具背面设置电加热 管,浇注开始前将金属型预热到指定的温度。 该方法同上述1)方法一样,简单方便,但温 度不是很均匀。也可烘箱加热。 3)将金属型放入加热炉中预热,可获得均匀 一致的温度,但仅限于小金属型。 4)采用浇注金属液的方法预热。该方法一般 不推荐,因为一是浪费金属液,二是缩短金 属型使用寿命。小型铸型。
涂料组成:
1)耐火材料:氧化锌、滑石粉、锆砂粉、硅藻 土粉等。 2)粘结剂:水玻璃、糖浆、纸浆废液等。
3)溶剂:水等。
4)附加物
从上面的一些分析可知,确定金属型浇 注工艺规范时,应铸件材质、形状大小、复 杂程度等考虑以下三点原则:
• (1)保证铸件全部表面能得到清晰的外形, 没有冷隔和浇不足的现象,也就是希望冷却 慢些,要求有较高的浇注温度和金属型温度。 • (2)保证铸件变形小,不发生扭曲和裂纹, 要求金属型温度高而浇注温度低。 • (3)保证铸件组织细密,力学性能好,希望 快速冷却,要求较低的金属型温度和浇注温 度。
• 缺点:
(1) 金属型制造成本高。
(2) 金属型急冷、不透气,而且无退让性,易造成 铸件浇不足、冷隔、开裂或铸铁件白口等缺陷。
(3) 铸型的工作温度、合金的浇注温度和浇注速度, 铸件在铸型中停留的时间以及所用的涂料,对 铸件质量的影响敏感,控制难度大。 近年来,为了防止浇注时金属液流动过程中形成紊 流,减少氧化夹渣及卷气等缺陷,采用倾转式 浇注已成为金属型铸造的主流方式,见图1-1。
第一章 铸造

消除缩孔类缺陷的途径
1)实现顺序凝固,用冒口补缩。
使铸件各部分按规定方向从一部分到另一部分铸件凝固
如图阶梯形铸件。
2)使铸件实现同时凝固
同时凝固原则不需冒口,节约金属且工艺简单;铸件冷却均匀, 不易形成应力、变形和裂纹等缺陷。
5、固态收缩缺陷
铸造应力、变形和裂纹 在铸件的凝固以及以后的冷却过程中,随温度的不断降低, 收缩不断发生,如果这种收缩受到阻碍,就会在铸件内产生 应力,引起变形或开裂,这种缺陷的产生,将严重影响铸件 的质量。 (1) 铸造应力的产生 铸造应力按其产生的原因可分为三种: a)热应力 铸件在凝固和冷却过程中,不同部位由于不均衡 的收缩而引起的应力。 b)固态相变应力 铸件由于固态相变,各部分体积发生不均 衡变化而引起的应力。 c)收缩应力 铸件在固态收缩时,因受到铸型、型芯、浇冒 口、箱挡等外力的阻碍而产生的应力。 铸件铸出后存在于铸件不同部位的内应力称为残留应力。
4、凝固收缩缺陷
(1)缩孔 当合金在恒温下或窄温度范围内凝固,铸件壁断 面逐层凝固方式时易形成缩孔。 缩孔总是出现在铸件上部或最后凝固的部位,其外形特征是: 内表面粗糙,形状不规则,多近于倒圆锥形。通常缩孔隐藏于铸件 的内部,有时经切削加工才能暴露出来。缩孔形成的主要原因是液 态收缩和凝固收缩。缩孔形成过程见图。
2. 铸件中的气孔和合金的吸气 (1)侵入性气孔 侵入性气孔是由于铸型表面聚集的气体侵入金 属液中而形成的孔洞。多位于铸件的上表面附近,尺寸较大,呈 椭圆形或梨形,孔壁光滑,表面有光泽或有轻微氧化色。 (2)析出性气孔 析出性气孔是溶解在金属液中的气体,在凝固 时由金属液中析出而未能逸出铸件所产生的气孔。其特征是尺寸 细小,多而分散,形状多为圆形、椭圆形或针状,往往分布于整 个铸件断面内。 (3)反应性气孔 浇入铸型中的金属液与铸型材料、型芯撑、冷 铁或溶渣之间,因化学反应产生气体而形成的气孔,统称反应性 气孔。这种气孔经常出现在铸件表面层下1mm-2mm处,孔内表面光 滑,孔径1mm-3mm。
第一章铸造成形工艺理论基础(李)

课程的主要目的
• 《材料成形工艺基础》是机械类或近机械类专
业的一门学科基础课,学习本课程的主要目的是 使学生比较全面系统的获得机械制造中铸造、压 力加工、粉末成形、焊接、塑料、橡胶、陶瓷以 及有关模具设计、加工、制造方面的专业知识。 其主要任务是介绍以下内容: • 1)制定铸造过程图,了解合金的熔炼与浇注过 程的基本知识以及砂型铸造、特种铸造等; • 2)制定锻造过程图,了解材料塑性变形基本规 律;了解粉末成形、塑料、橡胶、陶瓷成型过程 和板料冲压成形过程; • 3)了解常用金属材料焊接过程基本知识;
➢ 熔融凝固制备技术
原材料
熔融 精炼
凝固
坯料
常用于金属、无机非金属化合物、半导体材料坯锭和 玻璃制品的制备。
第一章铸造成形工艺理论基础(李)
➢ 粉末冶金制备技术
原料 粉末
混合
压制
烧结
这是陶瓷材料、水泥以及硬质合金以及铁基合金等材 料的主要成材途径。
第一章铸造成形工艺理论基础(李)
➢ 单体聚合制备技术
发展起来。
熔模铸造 传统的熔模铸造一般称失蜡、出蜡或捏
蜡、拨蜡。它和用来制造汽轮机叶片、铣刀等精密铸件
的现代熔模铸造,无论在所用蜡料、制模、造型材料、
工艺方法等方面,都有很大不同。但是,它们的工艺原
理是一致的,并且现代的熔模铸造是从传统的熔模铸造
发展而来的。
•
第一章铸造成形工艺理论基础(李)
• 金属型铸造 铸型材料从石和泥、砂改用金属,从 一次型经多次型又改进成为耐用性更高的所谓“永久” 型(金属型),在铸造技术的历史发展上具有重要的意 义。1953年河北兴隆铁范的发现,证明我国早在战国时 期已经用白口铁的金属型浇注生铁铸件。这批铁范包括 锄、镰、斧、凿、车具等类共87件,大部完整配套。其 中,镰和凿是一范两件,锄和斧还采用了金属芯。它们 的结构十分紧凑,颇具特色。范的形状和铸件相吻合, 使壁厚均匀,利于散热:范壁带有把手,以便握持,又 能增加范的刚度。可以说是创造了一种中国风格的金属 型,并且在那个时候已经大体定型了。近年来,在河南 南阳、郑州、镇平和河北满城、山东莱芜等地又陆续出 土汉代铁范许多件,品种比战国时期显著增多,型式却 基本相同。河南泥池汉魏铁器窖藏中还有铸造成形铁板 和矢镞的铁范以及长达半米的大型铁犁范。
第二篇铸造第一章铸造工艺基础演示文稿

坑。动画演示。 ◆收缩率↑,浇注温度↑,铸件愈厚,则缩孔↑。
现在是16页\一共有20页\编辑于星期五
2)缩松:分散在铸件某区域内的细小缩孔,称为缩松。缩松分为宏 观缩松和纤维缩松。动画演示
(2)铸型温度: 铸型的温度↑ 充型能力↑∴铸型可先预热。
(3)铸型中气体: 砂型铸造产生大
量气体,排气能力差,型腔中气压↑流 动阻力↑充型能力↓,所以铸型要留出
排气口。
四、铸件结构条件
铸件结构对充型能力的影响。
折算厚度: 折算厚度也叫当量厚度或模数,是铸件体积与铸件表面积之比。折算厚度 越大,热量散失越慢,充型能力就越好。铸件壁厚相同时,垂直壁比水平壁更容
二、铸件合金的收缩 合金从浇注、凝固直至冷却到室温,其体积
或尺寸缩减的现象,称为收缩 - 收缩是多种铸造
缺陷产生的根源。(如:缩孔、缩松、裂纹、
变Байду номын сангаас等)。
◆合金的收缩经历有三个阶段:
1)液态收缩、2)凝固收缩 、3)固态收缩
现在是14页\一共有20页\编辑于星期五
◆合金的收缩过程: 液态合金冷却
合金收缩 固态合金冷却
越小,则流动性越好。铸件晶粒组织
◆由图亚共晶铸铁随含碳量的增加,结晶温度范围减小,流动性提高。
实验证明铸铁的流动性好,
铸钢的流动性差
。
现在是9页\一共有20页\编辑于星期五
◆合金流动性对充型能力的影响
合金流动性的决定因数:
1)合金种类: 合金不同,流动性不同
2)化学成分:同种合金中成分不同的合金具有不同的结晶特点, 流动性也不同。
第一章铸造成型

上一页 下一页 返回
第二节 砂型铸造详解
(2)起模方法常用的起模方法有顶箱、漏模、翻转三种。图 1-15为顶箱起模方法。 随着生产的发展,新的造型设备会 不断出现,从而使整个造型和制芯过程逐步地实现自动化, 并逐步提高生产效率为制芯。型芯的主要作用是用来获得铸 件的内腔,但有时也可作为铸件难以起模部分的局部铸型。 浇注时,由于型芯受金属液的冲击、包围和烘烤,因此,与 砂型相比,型芯必须具有较高的强度、耐火度、透气性、退 让性和溃散性。满足上述性能主要是依靠合理配制芯砂和正 确的制芯工艺来保证的。在制芯过程中,应采取下列一些措 施:
型芯上的延伸部分称为芯头,用于安放和固定型芯。型芯头 位于砂型的型芯座上。型芯中设有通气孔,用于排出型芯在 受热过程中产生的气体。型腔的上方开设出气口,用于排出 型腔中的气体。另外,利用通气针在砂型中还扎有多个通气 孔。金属液从浇口杯中浇入,经直浇道、横浇道、内浇道流 入型腔中。
四、两种造型方法
上一页 下一页 返回
第五节铸件结构工艺性
2.铸件应具有最少的分型面,并尽量使分型面呈平面 图1-34 (a)所示铸件因侧壁凹入,有两个分型面,需 采用三箱造型,造型效率低,而且易产生错型缺陷。在不影 响使用性能的前提下,改为图1-34 (b)所示结构后,只 有一个分型面,可采用两箱造型。 3.铸件应有起模斜度 为了起模方便,在模样或芯盒的出模方向留有一定斜度, 以免损坏砂型或砂芯。这个在铸造工艺设计时所规定的斜度 称为起模斜度。
二、造型材料和工具
1.造型材料 制造铸型用的材料称为造型材料。造型材料主要包括型砂 和芯砂。型砂和芯砂主要由原砂、黏结剂(多用黏土和膨润 土,有时也用水玻璃、植物油、树脂等)、附加物毛坯(煤 粉或木屑等)、旧砂和水组成。
第一章 铸造成型

5)蠕墨铸铁—碳以蠕虫状石墨 ) 蠕虫状石墨形式存在,介于片状和球 蠕虫状石墨
状石墨之间。
根据铸铁的化学成分: 根据铸铁的化学成分:
普通铸铁 合金铸铁(加入一些合金元素,如Cr、Cu、Al、B等。 Cr、 合金铸铁 Cr Cu、Al、
组织: );F 组织:F + G (片); + P + G (片); P + G (片); 片; 片; 性能:抗压不抗拉;耐磨、消振性好;缺口敏感性低、 性能 抗压不抗拉;耐磨、消振性好;缺口敏感性低、
切削加工性好等。 切削加工性好等。
1.3 铸造合金
牌号: 数字”表示。“HT”表示“灰铁”,后 牌号:用“HT+数字 数字 后
控制调整成分
浇注
凝固 出模 清理、 清理、检验等
1.1 概述
齿圈
钢锭
退火罩
古铜钱
西安秦皇陵出土的铜马车
古代十八般武器和编钟
1.1 概述
铸造特点: 优点:投资小、生产周期短、 优点:投资小、生产周期短、能制造形状复杂零件 缺点:内部组织疏松、晶粒粗大,易产生缩孔、缩松等; 缺点:内部组织疏松、晶粒粗大,易产生缩孔、缩松等;
上砂箱 浇口棒 分型面
轮罩
下砂箱
模样
1.2 砂型铸造的基本工艺
整模造型
1.2 砂型铸造的基本工艺
分模造型 分模造型 特点:模样在最大截面处分开,模样一分二, 特点:模样在最大截面处分开,模样一分二,制作模样麻
烦,易偏箱和错箱。 易偏箱和错箱。
应用:最大截面在中部的铸件,常用于回转体类等铸件。 应用:最大截面在中部的铸件,常用于回转体类等铸件。
- 1、下载文档前请自行甄别文档内容的完整性,平台不提供额外的编辑、内容补充、找答案等附加服务。
- 2、"仅部分预览"的文档,不可在线预览部分如存在完整性等问题,可反馈申请退款(可完整预览的文档不适用该条件!)。
- 3、如文档侵犯您的权益,请联系客服反馈,我们会尽快为您处理(人工客服工作时间:9:00-18:30)。
二、砂型组成
如图1-5所示,型砂被舂紧在上砂箱和下砂箱中,连同砂 箱一起,分别称为上砂型和下砂型。从砂型中取m模样后形 成的空腔称为型腔,在浇注后形成铸件的外部轮廓。上砂型 和下砂型的分界面称为分型面。图中有阴影线的部分表示型 芯,型芯用于形成铸件的孔。
上一页 下一页 返回
第二节 砂型铸造详解
上一页 下一页 返回
第二节 砂型铸造详解
(2)起模方法常用的起模方法有顶箱、漏模、翻转三种。图 1-15为顶箱起模方法。 随着生产的发展,新的造型设备会 不断出现,从而使整个造型和制芯过程逐步地实现自动化, 并逐步提高生产效率。
三、制芯
制造型芯的过程称为制芯。型芯的主要作用是用来获得铸 件的内腔,但有时也可作为铸件难以起模部分的局部铸型。 浇注时,由于型芯受金属液的冲击、包围和烘烤,因此,与 砂型相比,型芯必须具有较高的强度、耐火度、透气性、退 让性和溃散性。满足上述性能主要是依靠合理配制芯砂和正 确的制芯工艺来保证的。在制芯过程中,应采取下列一些措 施:
上一页 下一页 返回
第四节金属的铸造性能
(3)铸造应力、变形和裂纹的形成与防止铸件在凝固和冷却 过程中由于受阻收缩、热作用和相变等因素而引起的内应力 称为铸造应力。铸造应力分为收缩应力、热应力和相变应力。 收缩应力是由于铸型、型芯等阻碍铸件收缩而产生的内应力; 热应力是由于铸件各部分冷却、收缩不均匀而引起的;相变应 力是由于固态相变,造成各部分体积发生不均衡变化而引起 的。 为了防止铸件产生收缩应力,应提高铸型和型芯的退让性, 如在型砂中加入适量的锯末或在芯砂中加入高温强度较低的 特殊钻结剂等,都可以减小其对铸件收缩的阻力。
1.造型材料 制造铸型用的材料称为造型材料。造型材料主要包括型砂 和芯砂。型砂和芯砂主要由原砂、黏结剂(多用黏土和膨润 土,有时也用水玻璃、植物油、树脂等)、附加物毛坯(煤 粉或木屑等)、旧砂和水组成。
下一页 返回
第二节 砂型铸造详解
为了获得合格的铸件,造型材料应具备一定的强度、可塑性、 耐火度、透气性、退让性和溃散性等性能。 2.造型工具 制造铸型用的T具称为造型T具。造型常用的T具是砂箱及 底板、砂舂、通气针、起模针、皮老虎、镘刀、秋叶、提钩、 半网等,如图1-3和图1 -4所示。
上一页 下一页 返回
第二节 砂型铸造详解
五、熔炼
金属熔炼质量的好坏对能否获得优质的铸件有着重要的影 响。如果金属液的化学成分不合格,会降低铸件的力学性能 和物理性能。常用的熔炼设备有冲天炉(适合于熔炼铸铁)、 电炉(适合于熔炼铸钢)、琳竭炉(适合于熔炼非铁金属)。
六、合型(合箱)
将铸型的各个组元如上砂型、下砂型、型芯、浇口杯等组合 成一个完整铸型的操作过程称为合型。合型后要保证铸型型 腔几何形状、尺寸的准确性和型芯的稳固性。型芯放好并经 检验后,才能扣上上砂型和放置浇口杯。
上一页 下一页 返回
第五节铸件结构工艺性
2.铸件应具有最少的分型面,并尽量使分型面呈平面 图1-34 (a)所示铸件因侧壁凹入,有两个分型面,需 采用三箱造型,造型效率低,而且易产生错型缺陷。在不影 响使用性能的前提下,改为图1-34 (b)所示结构后,只 有一个分型面,可采用两箱造型。 3.铸件应有起模斜度 为了起模方便,在模样或芯盒的出模方向留有一定斜度, 以免损坏砂型或砂芯。这个在铸造工艺设计时所规定的斜度 称为起模斜度。
上一页 下一页 返回
第二节 砂型铸造详解
十、检验
铸件清理后,应进行质量检验。检验可通过肉眼观察(或 借助尖嘴锤)找出铸件的表面缺陷,如气孔、砂眼、黍占砂、 缩孔、浇不足、冷隔等。对于铸件内部的缺陷可进行耐压试 验、超声波探伤等。
上一页 返回
第三节铸造工艺图
一、浇注位置的选择
浇注位置是指浇注时铸型分型面所处的位置。可归纳为 “三下一上”,即: (1)铸件的重要加工面或主要工作面应朝下 其确定原则因为气体、渣子、沙粒等易上浮,铸件上部质量 较差。 (2)铸件的大平面应朝下这样可以防止大平面上产生气孔、 夹砂等缺陷,如图1-23所示。 (3)具有大面积的薄壁铸件,应将薄壁部分放在铸型下部这 是为了防止薄壁部分产生浇不足、冷隔等缺陷,如图1-24 所示。
1.手工造型 全部用手或手动工具完成的造型工序称为手工造型。手工造 型的特点是操作灵活,适应性强,模型制作成本低,生产准 备时间短。
上一页 下一页 返回
第二节 砂型铸造详解
但造型效率低,劳动强度大,劳动环境差,主要用于单件小 批量生产。造型时如何将木模顺利地从砂型中取出,而又不 致破坏型腔的形状,是一个很关键的问题。因此,围绕如何 起模这一问题,就形成了各种不同的造型方法。 (1)整体模造型 (2)分开模造型 (3)挖砂造型 (4)假箱造型 (5)活块造型 (6)三箱造型 (7)刮板造型
三、绘制铸造工艺图
在确定了铸件浇注位置、分型面、型芯结构、浇冒口系统 及有关参数等内容后,即可用表1-1所列的工艺符号及其表 示方法绘制铸造工艺图。
上一页 返回
第四节金属的铸造性能
一、流动性
流动性是指熔融金属的流动能力。它是影响熔融金属充型 能力的主要因素之一。 液态金属流动性好,充型能力就强,就容易获得尺寸准确、 外形完整和轮廓清晰的铸件,避免产生冷隔和浇不足等缺陷。 也有利于金属液中非金属夹杂物和气体的排出,避免产生夹 渣和气孔等缺陷。同时,金属的流动性好,也有利于补充在 凝固过程中所产生的收缩,避免产生缩孔和缩松等缺陷。
上一页 下一页 返回
第二节 砂型铸造详解
八、落砂
用手工或机械使铸件和型砂、砂箱分开的操作称为落砂。 落砂时铸件的温度不得高于500℃,如果过早取出,则会产 生表面硬化或发生变形、开裂。
九、清理
铸件由铸型取出后,还需要进一步清理表面的钻砂。手工 清除时一般用钢刷或扁铲加工,这种方法劳动强度大,生产 率低,且妨害健康。因此,现代化生产主要是用震动机和喷 砂喷丸设备来清理表面。所谓喷砂和喷丸就是用砂子或铁丸, 在压缩空气作用下,通过喷嘴射到被清理工件的表面进行清 理的方法。
下一页 返回
第四节金属的铸造性能
二、收缩性
金属在液态凝固和冷却至室温过程中,产生体积和尺寸减 小的现象称为收缩。收缩是铸造金属本身的物理性质,是铸 件中产生缩孔、缩松、裂纹、变形、残余内应力的基本因素。 1.收缩的三个阶段 金属液从浇注温度冷却到室温要经过液态收缩、凝固收缩、 固态收缩三个阶段。
上一页 下一页 返回
第二节 砂型铸造详解
七、浇注
将熔融金属从浇包注入铸型的操作称为浇注。在浇注过程中 必须掌握以下两点: (1)浇注温度的高低对铸件的质量影响很大。 (2)较高的浇注速度,可使金属液更好地充满铸型,铸件各 部温差小,冷却均匀,不易产生氧化和吸气。但速度过高, 会使铁液强烈冲刷铸型,容易产生冲砂缺陷。实际生产中, 薄壁件应采取快速浇注;厚壁件则应按慢一快一慢的原则浇注。
第一章铸造成型
第一节 铸造工艺基础 第二节 砂型铸造详解 第三节铸造工艺图 第四节金属的铸造性能 第五节铸件结构工艺性 第六节特种铸造
第一节 铸造工艺基础
一、铸造成型特点
1.成本低廉,设备简单、周期短 2.成型方便,工艺灵活性大 3.砂型铸件的力学性能较差,质量不够稳定 4.砂型铸造成型生产劳动强度大,生产条件差
上一页 返回
第五节铸件结构工艺性
一、铸造性能对铸件结构的要求
1.铸件应有合理的壁厚 为保证液态合金充满铸型,铸件壁厚不能小于金属允许的 最小壁厚。否则,易产生浇不足、冷隔等缺陷。 2.铸件壁厚应力求均匀 铸件壁厚不均匀,会产生冷却不均匀,引起较大的内应力, 从而使铸件产生变形和裂纹,同时,还会因金属局部积聚, 产生缩孔。
下一页 返回铸件壁与壁的连接应合理 铸件壁的连接应平缓、圆滑,避免直角处产生应力集中和 金属积聚,铸件厚壁与薄壁间的连接要逐步过渡,做到减少 应力集中,防止裂纹产生。 4.铸件应避免收缩受阻 铸件收缩受阻是产生内应力、变形和裂纹的根本原因。铸 件结构设计时,应尽量使其能够自由收缩,以减少内应力, 避免变形和裂纹。如图1-32(a)中的轮辐,往往由于内应力 大使轮辐产生裂纹,改为图1-32 ( b )所示的弯曲轮可借 助轮辐的微量变形来自行减少内应力。
下一页 返回
第三节铸造工艺图
(4)易形成缩孔的铸件,浇注时应把厚的部分放在分型面附 近的上部或侧面,这样便于在铸件厚处直接安置冒口,保证 铸件自下而上顺序凝固,使冒口充分发挥补缩作用。
二、工艺参数的选择
绘制铸造工艺图时应考虑的主要工艺参数是加工余量、起 模斜度、铸造圆角、收缩率和芯头等。
上一页 下一页 返回
第五节铸件结构工艺性
5.铸件应尽量避免有过大的水平面 铸件的大水平面,易产生浇不足等缺陷。同时,平面型腔 的上表面,由于受液体金属长时间烘烤,易产生夹砂,而且 大水平面也不利于气体和非金属夹杂物的排除。所以,应把 铸件的大水平面设计成倾斜结构形式,如图1-33所示。 二、铸造工艺对铸件结构的要求 1.铸件外形应力求简单 铸件外形尽可能采用平直轮廓,尽量少用曲面,尤其是非圆 曲面,以便于制造模样。
上一页 下一页 返回
第二节 砂型铸造详解
2.机器造型 用机器全部地完成或至少完成紧砂操作的造型工序称为机 器造型。机器造型的实质就是机器代替了手工紧砂和起模, 它是现代化铸造车间的基本造型方法。特点是生产率高,铸 件尺寸精度高和表面质量好,改善了劳动条件,很适合于成 批大量生产铸件。 (1)紧砂方法常用的紧砂方法有震实、压实、振压、抛砂、 压射等几种形式。其中以振压式应用最广,图1-14为振压 式紧砂方法。