价值流案例
精益案例分享从价值流分析到精益生产
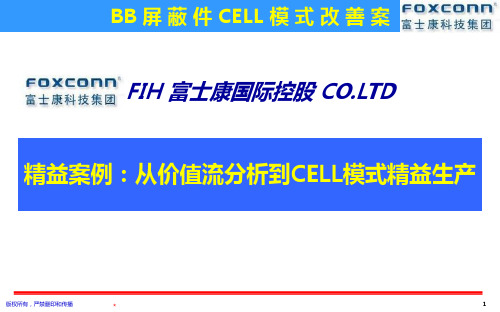
版权所有,严禁翻印和传播
*
2
BB 屏 蔽 件 CELL 模 式 改 善 案
版权所有,严禁翻印和传播
*
3
BB 屏 蔽 件 CELL 模 式 改 善 案
版权所有,严Leabharlann 翻印和传播*4BB 屏 蔽 件 CELL 模 式 改 善 案
版权所有,严禁翻印和传播
*
5
BB 屏 蔽 件 CELL 模 式 改 善 案
版权所有,严禁翻印和传播
*
10
BB 屏 蔽 件 CELL 模 式 改 善 案
版权所有,严禁翻印和传播
*
11
BB 屏 蔽 件 CELL 模 式 改 善 案
版权所有,严禁翻印和传播
*
12
BB 屏 蔽 件 CELL 模 式 改 善 案
版权所有,严禁翻印和传播
*
13
BB 屏 蔽 件 CELL 模 式 改 善 案
BB 屏 蔽 件 CELL 模 式 改 善 案
FIH 富士康国际控股 CO.LTD 精益案例:从价值流分析到CELL模式精益生产
版权所有,严禁翻印和传播
*
1
BB 屏 蔽 件 CELL 模 式 改 善 案
案例策划及实行者介绍 郭广恩 F2833271
富士康科技集团 FIH 国际控股公司 MPM事业处 LC生产部长 富士康科技集团 IE 学院 龙华及观澜园区 精益生产教练员 富士康科技集团 IE学院 首批对外生产力输出咨询师
版权所有,严禁翻印和传播
*
14
BB 屏 蔽 件 CELL 模 式 改 善 案
版权所有,严禁翻印和传播
*
15
BB 屏 蔽 件 CELL 模 式 改 善 案
版权所有,严禁翻印和传播
价值流改善案例
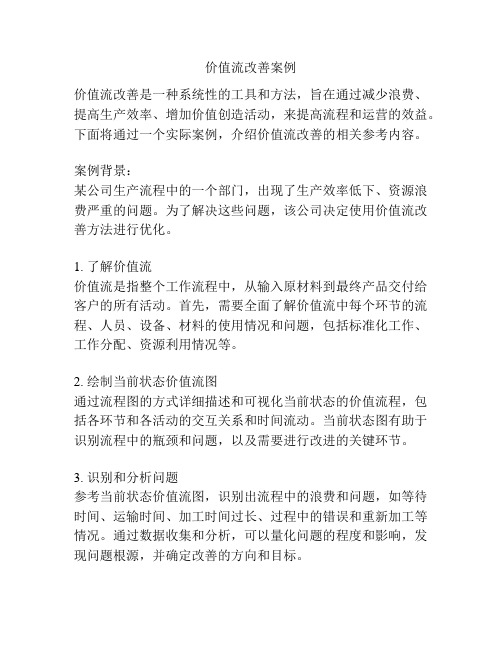
价值流改善案例价值流改善是一种系统性的工具和方法,旨在通过减少浪费、提高生产效率、增加价值创造活动,来提高流程和运营的效益。
下面将通过一个实际案例,介绍价值流改善的相关参考内容。
案例背景:某公司生产流程中的一个部门,出现了生产效率低下、资源浪费严重的问题。
为了解决这些问题,该公司决定使用价值流改善方法进行优化。
1. 了解价值流价值流是指整个工作流程中,从输入原材料到最终产品交付给客户的所有活动。
首先,需要全面了解价值流中每个环节的流程、人员、设备、材料的使用情况和问题,包括标准化工作、工作分配、资源利用情况等。
2. 绘制当前状态价值流图通过流程图的方式详细描述和可视化当前状态的价值流程,包括各环节和各活动的交互关系和时间流动。
当前状态图有助于识别流程中的瓶颈和问题,以及需要进行改进的关键环节。
3. 识别和分析问题参考当前状态价值流图,识别出流程中的浪费和问题,如等待时间、运输时间、加工时间过长、过程中的错误和重新加工等情况。
通过数据收集和分析,可以量化问题的程度和影响,发现问题根源,并确定改善的方向和目标。
4. 制定改善计划根据问题分析的结果,制定具体的改善计划。
参考经验和最佳实践,结合公司的实际情况,确定改进的措施和行动步骤。
包括重新设计流程、优化资源配置、提高人员技能、引入新技术设备等方面。
5. 实施改善措施将制定的改善计划付诸实施。
通过改进流程、优化资源和培训提升员工技能等方式,逐步消除浪费,提高生产效率。
同时,需要设立一套有效的监控和反馈机制,及时评估改进措施的效果,以便及时调整和改进。
6. 绘制未来状态价值流图在完成改善措施的实施后,通过绘制未来状态价值流图来展示改进后的理想流程。
未来状态图应该包括改善后的流程、人员和设备的协调工作,以及流程中良好的信息传递和问题解决机制。
7. 持续改进和绩效评估改进工作不应该止步于一次改善计划的实施,而是需要持续进行改进和优化。
制定绩效评估指标来监控改进后的效果,持续跟踪并记录改进成果,并根据评估结果进行调整和改进。
价值流分析
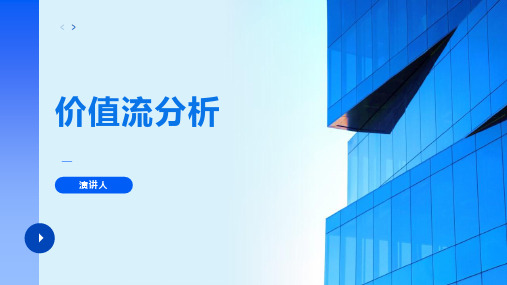
2 提高生产效率
3
降低成本
4 提高产品质量
5 优化生产流程
6 提高客户满意度
价值流分析的步骤
01
识别价值流:识别产品或服
务的整个生命周期中的价值
流
02
绘制价值流图:绘制产品或服
务的价值流图,包括所有相关
03
分析浪费:分析价值流图中
的浪费,包括等待、过度生
活动、信息、物料和库存
产、运输、库存等
04
制定改进措施:制定改进措
分析价值流
识别价值流:识别并描述产品或服务的整个价 值流,包括从原材料到最终客户的整个过程
绘制价值流图:绘制价值流图,展示价值流中 的各个步骤、信息、物料和物流
识别浪费:识别并消除价值流中的浪费,包括 等待、过度生产、运输等
优化价值流:优化价值流,提高生产效率,降 低成本,提高客户满意度
价值流分析的应 用
价值流分析
演讲人
目录
01. 价值流分析概述 02. 价值流分析的关键要素 03. 价值流分析的应用 04. 价值流分析的案例分析
价值流分析概述
价值流分析的定义
价值流分析是 一种系统性的 方法,用于识 别和消除生产 过程中的浪费 和低效率环节。
价值流分析的 目标是提高生 产效率,降低 成本,提高产 品质量和客户
满意度。
价值流分析关 注从原材料到 成品的整个生 产过程,包括 产品设计、生 产、销售和售 后服务等环节。
价值流分析的 核心是识别和 消除浪费,包 括过度生产、 等待、运输、 库存、过度加 工、动作浪费
等。
价值流分析强 调跨部门、跨 职能的合作, 以实现整体优 化和持续改进。
价值流分析的目的
1 识别并消除浪费
VSM价值流分析
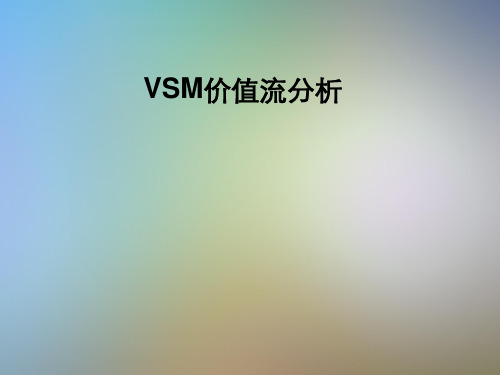
客户及需求
Weekly
Despatch
(4)
Dispense
(4)
I
7 days
Blend & Granulate
(25)
I
20 days
Bulk Testing
(5)
I
10 days
Filling Line 1
(33)
I
20 days
Bottle Testing
(5)
I
30 days
情景剧
续上页: (甲、乙闲聊中,服务员来到近前) 服务员:先生,找您零钱。 (服务员递给甲12元人民币) 乙:麻烦给我一张发票。 服务员:请稍等。(转身快步离去)
情景剧
续上页: (甲、乙不耐烦中,服务员来到近前) 服务员:先生,给您发票。 乙:谢谢,不过下次能不能快点。 服务员:好、好。(心情郁闷中,我已经来回走的很 快了,还要怎么样啊?)
XX有限公司
SMT段 A线 价值流程图Value Stream Mapping(VSM)
采购部
生产管理部
采购计划
物料计划
生产计划
大客户部
机种名称:
订单流 L/T
客户订单量(P/O QTY:pcs) 2,195
ALMCB V3.3
客户产能需求TT/pcs(Sec) 577
客户交货周期(计划生产需求) 7
人数 面积
100 Lot/天
0.012 H/Lot
1
天
0.012 H/Lot
1
人
3
M2
目检
代号
名称
信息 单位
C/O 换线/模时间
/ Sec/次
价值流程图-VSM

PROCESSES
Products
Receiving Cutting Strip Soldering Crimp Insertion molding test inspect Pack
A
x
x
x
x
x
x
x
x
x
B
x
x
x
x
x
x
x
x
x
C
x
x
x
一次质量
2 x/ day
发运
I
500 pcs
Inventory Part A = 750 pcs Part B = 600 pcs Part C = 1650 pcs
# of shifts =
环节6:定义信息流
绘制从收到订单到下达生产订单(客户旳订单,生产订 单,采购订单)旳信息流。
统计生产订单及有关产品。 统计生产计划系统及随产品经过系统旳文件材料。 统计你怎样与供给商和客户沟通。 统计信息怎样整顿和发放,例如:电子方式,手工方式,
区别流动中旳推动和拉动。 包括产品接受和质量检验旳全部控制。
推动
流程生产不考虑下游(内部 )客户流程旳实际需求,直 接推动未完毕产品经过流程 。生产根据既定计划。
VS
拉动
每个后续生产环节都是前一 流程环节旳客户。当需要时 (拉动)由客户要求数量, 而不是简朴旳根据前面生产 环节生产并直接送到客户处 (推动)。
怎样辨认流程中旳挥霍?
价值流图(VSM)
价值流图消除挥霍
价值流图旳目旳在揭发挥霍旳起源。
我们应着眼于回答下述问题: “我们怎样能够仅生产下个流程所需,并仅在该流程需要时生产旳方式
现状价值流分析案例

现状价值流分析案例
一、现状价值流分析参与部门:
营业部、营业技术部、生产部、采购部、QA部、开发部
二、现状价值流图绘制步骤:
1.确定工艺路线:
客户-营业-设计-计划-采购-制造-交付
2.绘制信息流和实物流
3.记录过程参数
4.计算在制品库存
5.创建时间线,计算增值比。
各阶段过程参数:
合同签订-工程设计:15天工程设计-设计:25天-5天/1.5人
设计-采购订单:2.5天送货:61天检验:6.9h加工中心:32.3h
部装:ST-52.6h人数-6人FPY-454PPM搬运距离-50m搬运容器-叉车/行车配管:ST-38.3h人数-6人FPY-1363PPM搬运距离-35m
组装:ST-54h人数-8人FPY-3182PPM搬运距离-20m搬运容器-叉车/行车涂装ST-29.7h人数-5人FPY-1590PPM搬运距离-40m搬运容器-叉车/行车配线:11.6h调试:180h(24小时计)出货检查:4.5h
在制品库存计算方法(用原材料、在制品的库存金额计算出库存天数)。
影响运转率因素:
1.缺料
·来料不良、不均衡
·多批次设计不良(C级品管理不善)
2.影响能率的因素
·新人(人员流动)·考核机制不合理·导致不良因素·自制不良
·配送不良。
价值流实操案例

价值流实操案例咱就说有这么一家面包店,叫“美味面包屋”。
以前那经营状况啊,就像一辆破自行车,蹬得费劲还跑不快。
一、现状价值流分析。
1. 顾客下单到取货流程。
顾客走进店里,看着墙上贴的面包种类菜单,有时候得琢磨半天,因为菜单就简单写了个名字,也没个详细介绍。
这就好比你去相亲,只知道对方名字,其他啥都不晓得,心里没底啊。
顾客下完单后,店员要跑到后厨喊一声。
这后厨离前台有点远,店员跑来跑去浪费不少时间。
而且后厨师傅有时候正忙着手头的活儿,没第一时间听到,订单就可能被耽搁个几分钟。
面包做好了,还得再等包装的员工有空来包装。
要是前面有几个订单在等着包装,那顾客就得干等着,眼巴巴地看着面包在那放着,就是不能拿走。
2. 原材料供应流程。
面粉、酵母这些原材料,每次都是快用完了才发现要补货。
然后紧急打电话给供应商,供应商再安排送货,这中间面包店就可能会因为原材料不足,少做一些热门的面包,顾客想买都买不到。
送来的原材料,验收也有点乱。
有时候店员忙起来,就简单看一眼数量对不对,质量方面的检查就不那么仔细了。
结果有一次,用了一批有点问题的酵母,做出来的面包发酵不太好,可把顾客给得罪了。
3. 店面布局与人员安排。
店里的布局是前台、面包展示区、制作区、包装区这么一溜儿排开。
看起来挺整齐,但是顾客多的时候,店员在这些区域之间穿梭,就容易互相撞到。
就像一群小蚂蚁在一个狭窄的通道里乱跑,乱了套。
人员安排也不合理。
忙的时候大家都忙得晕头转向,闲的时候又都在那干瞪眼。
比如说,前台的店员有时候在顾客少的时候,就站着发呆,也不能帮着后厨或者包装那边干点啥。
二、改进措施。
1. 顾客下单到取货流程改进。
把菜单给升级了。
每个面包都配上了精美的图片,还有详细的配料、口味描述。
这就像给面包们做了个自我介绍的短视频,顾客一眼就能决定自己想吃啥。
在后厨和前台之间装了个小铃铛和对讲系统。
店员下单按一下铃铛,后厨立马就能听到,然后通过对讲系统确认订单内容,又快又准,就像给他们之间搭了个专线电话。
价值流图常用符号及案例
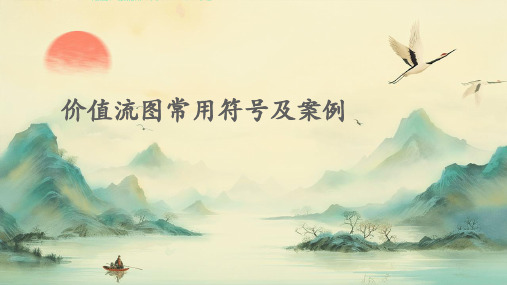
案例二:电子产品制造行业价值流图
总结词
展示了电子产品制造行业价值流图的特点,包括原材料采购、零部件加工、组装、测试和包括原材料采购、零部件加工、组装、测试和销售等环节。在价值流 图中,企业可以清晰地看到从原材料到最终产品的整个过程,以及各环节之间的衔接和信息传递。通 过优化生产流程和提高生产效率,降低成本和提高产品质量,提升企业竞争力。
加工设备符号
表示加工设备或工具,通常用矩 形或椭圆表示。
检测设备符号
表示检测设备或工具,通常用矩 形或椭圆表示。
辅助设备符号
表示辅助设备或工具,通常用矩 形或椭圆表示。
人力符号
工人符号
表示工人或操作人员,通常用矩 形或椭圆表示。
管理者符号
表示管理者或负责人,通常用矩 形或椭圆表示。
03
价值流图案例分析
价值流图常用符号及案例
• 价值流图概述 • 价值流图常用符号 • 价值流图案例分析 • 价值流图应用实践
01
价值流图概述
价值流图的定义
价值流图是一种可视化工具,用于描 述一个产品或服务从原材料到最终成 品的整个过程,包括各个工序、时间、 库存以及运输等。
它可以帮助企业识别并消除浪费,提 高生产效率和产品质量,实现持续改 进。
案例四:物流行业价值流图
总结词
物流行业价值流图主要关注运输、仓储、配送等环节,通过优化流程降低成本和提高效 率。
详细描述
物流行业价值流图通常关注运输、仓储、配送等环节,通过优化流程降低成本和提高效 率。在价值流图中,企业可以清晰地看到从货物接收到最终送达客户的整个过程,以及 各环节之间的衔接和信息传递。通过合理规划运输路线、提高仓储管理水平和优化配送
通过价值流图识别流程中的瓶颈环节, 如等待、库存等。
kaizen改善案例

kaizen改善案例在大规模制造业领域中,日本的Kaizen改善方法以其持续改进和精益生产的理念而闻名。
它的主要目标是通过消除浪费和改善流程,提高生产效率和产品质量。
下面是一些关于如何在制造业中应用Kaizen的改善案例。
1.价值流分析和流程改进价值流分析是Kaizen方法的核心。
它的目的是识别整个生产过程中的所有非价值增加活动,并找到解决这些问题的方法。
假设有一个汽车制造公司,该公司发现他们的装配线上的工人每天都要花费大量时间在获取所需的零部件和工具上。
通过进行一个价值流分析,公司发现工人们不得不走过很长的距离,从仓库中取零件。
为了改善这个问题,公司搬迁了仓库,将其放置在更靠近装配线的位置。
这样,工人们就不再需要走那么远的距离,并且能够更快地取得所需的零部件和工具,从而提高了生产效率。
2.设备维护和避免停机时间在制造业中,机器的损坏和停机时间是生产效率低下的主要原因之一。
一家化工公司发现他们的反应釜经常出现故障,并且停机时间很长。
为了解决这个问题,公司采取了预防性维护措施,定期检查和维护反应釜。
此外,他们还实施了一个定期培训计划,让操作员能够更好地了解和处理设备故障。
这些改进措施不仅降低了机器故障和停机时间,还提高了生产效率和产品质量。
3.标准化和员工培训标准化是另一个重要的Kaizen改善方法。
一家制造公司发现他们的不同工作站之间存在差异和不一致,导致了生产效率的下降。
为了解决这个问题,公司制定了一套标准作业程序,并确保每个员工都接受培训以遵循这些程序。
此外,公司还定期对员工进行技能培训,提高他们的专业知识和技能水平。
这些改进措施不仅提高了生产效率,还减少了错误和产品缺陷。
4.多功能和自主团队多功能和自主团队是Kaizen改善方法的核心理念之一。
一家制造公司发现他们的生产线上的工人只负责单个工作站,这导致了生产效率低下和工时浪费。
为了解决这个问题,公司进行了岗位轮换,并培养了一支多功能的工作队伍。
【价值管理】价值流图常用符号及案例

客户
KITTING
CONVERSION
Machining
Kitting Racks
Welding
Assembly
Packing
Shiiping
供应商 Supplier
Warehouse 仓库
On Demand
Forecast Firm
Order
所在工厂
Forecast 3-mo
Firm Biweekly
Kitting Racks
Welding
Assembly
Packing
Shiiping
供应商 Supplier
Forecast Firm
Order
所在工厂
Forecast 3-mo
Firm Biweekly
客户
Warehouse 仓库
On Demand
Pick List 36 hrs
Loading Plan weekly daily
客户
供应商 Supplier
Warehouse 仓库
Forecast Firm
Order
所在工厂
Forecast 3-mo
Firm Biweekly
客户
供应商 Supplier
Warehouse 仓库
On Demand
Forecast Firm
Order
KITTING
Kitting Racks
所在工厂
客户
KITTING
CONVERSION
Machining
Kitting Racks
Welding
Assembly
Packing
Shiiping
供应商 Supplier
价值流案例1
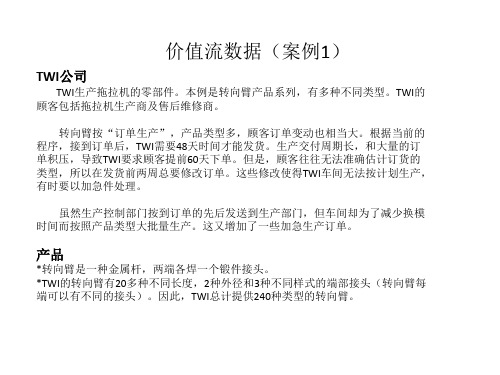
*转换三种端部接头锻件,需呀2小时的换模时间; *密西根钢铁公司提供钢材,交付期16周。每月运送两次; *端部接头锻件毛坯由印地安娜锻造厂提供,毛坯的交付期为12周,每月运送两 次。
转向臂生产步骤
切割杆
焊接
一端
焊接
另一端
除毛刺
磨光
油漆
外表面
装配
加工锻件
工作时间
*每月20个工作天; *生产部门两班制; *每班8小时,必要时加班; *每班有两次各15分钟的中间休息,休息时工作暂停。午餐时间不计入工作时间。
3、焊接工位2(专门为这个产品系列服务) *将第二个精加工后的铸件焊接到管柱上; *自动焊接工艺,加工时间不包含上下料时间; *周期时间:员工作业=10秒,机器作业=30秒; *换模时间:15分钟(调整长度),1小时(调整外径); *可靠性:80% *库存:3天已焊接的转向臂库存
4、打磨工位(专门为这个产品系列服务)
*自动工艺加工时间不包括上下料时间 *周期时间:员工作业=10秒,机器加工=30秒 *换模时间:15分钟(调整长度),1小时(调整外径) *可靠性:100% *库存:5天完成的转向臂库存
5、喷漆(转向臂送到外协喷漆厂)
*周期时间:2天 *每天由一辆货车将转向臂送到外协喷漆厂,并取回喷好的产品 *库存:喷漆厂有两天的存量,TWI有6天的库存
生产工序(见下图)
*TWI转向臂产品系列的工序包括:金属杆切割,将端部接头焊接到柱上,打磨 (除去多余的焊料),在外包厂进行喷漆,端部接头装配。锻造的端部接头在 TWI工厂加工。加工完的转向臂放置在仓库,按照顾客要求供货; *生产不同长度的产品,需要15分钟的换模时间; *生产不同外径的产品,需要1小时的换模时间。换模时间长主要是设置质量检验;
价值流图常用符号及案例
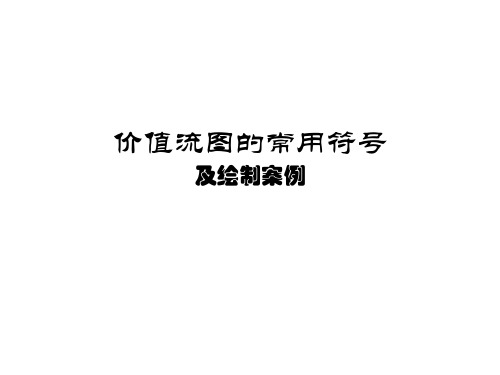
Welding Yield=98.6%
Assembly Yield=73.2%
Packing
Shiiping
Kitting Racks
8 h** 0.5h
2 h*** 0.2 h
4h 0.5h
8h 0.5 h
8h 2h
8h 0.6 h
9h 1h
Waiting Time:47 h Process Time:5.3 h
Loading Plan weekly daily Pick List 36 hrs
KITTING
CONVERSION
Machining
Welding
Assembly
Packing
Shiiping
Kitting Racks
供应商 Supplier
Forecast Firm Order
所在工厂
Forecast 3-mo Firm Biweekly
Forecast Firm Order
所在工厂
Forecast 3-mo Firm Biweekly
客户
Warehouse 仓库
On Demand
KITTING
CONVERSION
Machining Yield=99.%
Kitting Racks
供应商 Supplier
Forecast Firm Order
价值流图的常用符号
及绘制案例
价值流
供应商
工厂/服务 维修站
客户
完整价值流
价值流是指从原材料转变为产品,并给它赋予价值的全过程 包含增值的和非增值的活动
价值流程图:用一些简单的符号和流线从头到尾描述每一个工序 状态、工序间的物流、信息流和价值流的当前状态,找出需要改 善的地方,再描绘出一个未来状态图,以显示价值流改善的方向
价值流分析
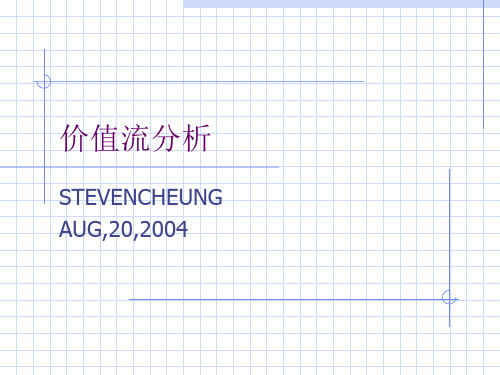
精益生产之价值及价值流分析
七种浪费之纠正
M u d a 四:动作的Muda
任何人体的动作,若是没有直接产生附加价值,就是没有生产力。 例如,人在走路时,他并没有增加价值。特别是,如提起或持着一个 重物,需用到作业员身体一部分的特别体力的动作,应予以避免。 这不只是因为工作困难,也是因为这代表着 M u d a。可以借由工 作地点的重新安排,来剔除作业员手持重物走路的动作,仅花了数 秒而已。其余的动作代表着没有附加价值,例如拿起或放下工作物。 经常可看到同一件工作物,先由右手拿起然后再由左手持着。举例 来说,操作缝衣机的作业员,先从供料箱中拿出几块衣料,然后放在 机器上,最后才取一件衣料放进缝衣机缝制,这就是动作的 M u d a。 供料箱应重新摆置,使作业员能拿起一块衣料,直接放进缝衣机缝 制。要认定动作的 M u d a,需详细观察作业员手脚使用的方式。 然后,必须重新安排物料放置的方式以及开发适当的工具及夹具。
排队等候登记;
10.பைடு நூலகம்
排队等候安全检查;
11.
排队等候通过海关;
12.
在候机厅中等候;
13.
排队等候登机;
14.
在飞机里等候 2小时的空中交通延
迟;
15.
滑行到跑道;
16.
飞到克里特 3小时 ;
17.
在飞机里等候 滑行和下飞机 ;
18. 19. 20. 21. 22. 23. 24. 25. 9:00 ;
没有考虑到下一个流程或下一条生产线的正确生产速度,而只尽其所能,在本流 程生产过多的产品。
让作业员有生产伸缩的充分空间。 让每一流程或生产线有提高自己的生产力的利益。 因为有不合格品而想提高直行率 直行率值指产品不用重修的比率 。 因为有多余的产能,所以容许机器生产多于所需之量。 因为引进了昂贵的机器设备—为折旧费的分摊,而提高稼动率,生产过多的产品。
价值流改善案例(VSMXY)

2,材料订购周期长
一栋一楼 原材料仓
二栋二楼
生产排期 计划
一栋一楼
3,生产L/T长,中间 在库量大,重复搬 运劳动
包装 品管科
I
子零件 暂放区
I I
原材料停 留3.5日
4,在库量大
组装 品管科
抽检确认 送货
生产科 安排生产
品管科 生产巡检
I
全数选别
I
抽检确认
I
暂时入库 停留5.7日
Cycle Time=24s 换模时间=45分
20
实施对策:
同期化作业实施
生产同期化改善活动实施后的效果:
包装专用作业区面积的低减
改善前: 改善后:
改善前占用作业区200M2
改善后占用作业区200M2消减
21
生产至入库所需置场的低减
改善前
项目 原料仓库 生产 检查 置场 置场 二次加工 置场 捆包 检查 置场 入库 A栋2楼 B栋1楼 (计量、打包) B栋2楼 分析内容 B栋1楼 等待浪费 不良浪费 动作浪费 在库浪费 作业浪费 搬运浪费 生产过剩的浪费 合计浪费(点) 0 O 2 1 3 3 6 3 1 0 3 0
组装 包装
抽检确认
Cycle Time=24s 换模时间=15分 0.01天
加工时间=24S
Cycle Time=5s 换模时间=5分
1天
0.04天
5天
情报L/T=2天 12 实物流L/T=6.05天 加工时间=24 sec
「物」和「情报」现状的流程图问题点分析:
原材料商
日本
供应商
海外材料发P/O 确定:n+1.5月 接订单L/T=2天
6
改善活动大计划
价值流程图绘制方法(精益生产)

对工作流程进行优化,消除浪费,提高生产效率。
引入新技术
引入新技术和设备,提高生产过程的自动化和智能化水平。
培养员工的价值流意识与能力
培训员工
对员工进行价值流相关培训,提高其对价值流 的认识和理解。
鼓励员工参与
鼓励员工参与到价值流改进过程中,发挥其主 动性和创造性。
建立激励机制
建立激励机制,对在价值流改进中做出贡献的员工给予奖励和表彰。
05
价值流程图的持续改进
定期审查与更新价值流程图
定期审查
价值流程图绘制完成后,应定期进行审 查,以确保其与实际生产过程保持一致 。
VS
更新价值流程图
随着生产过程的改进和变化,价值流程图 也应随之更新,以反映最新的生产状况。
持续改进的策略与方法
识别瓶颈
通过价值流程图,识别生产过程中的瓶颈,并制定相应的改进措 施。
非价值流
描述生产过程的原材料、组件、 信息和能源的来源。
描述生产过程中的浪费环节,如 等待、库存、搬运、重复作业等。
价值流程图的作用
识别生产过程中的浪费
提高生产效率
通过绘制价值流程图,企业可以清晰地看 到生产过程中的浪费环节,从而有针对性 地采取措施消除浪费。
价值流程图可以帮助企业优化生产流程, 减少不必要的环节和等待时间,提高生产 效率。
增强了企业的竞争力。
THANK YOU
服务流程梳理
利用价值流程图对服务流程进行全面梳理,包括客户需求、服务 提供、售后支持等环节。
服务效率提升
基于价值流程图的分析结果,优化服务提供方式,提高服务效率和 质量。
服务创新
通过价值流程图发现服务中的瓶颈和浪费,实施服务创新,如开发 新的服务项目、优化服务流程等。
精益生产3.VSM价值流图及价值流分析课件
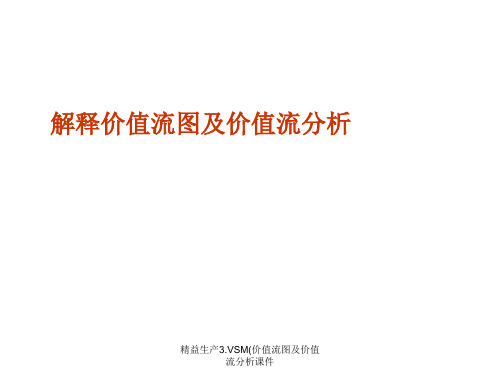
4天
统计数据
50秒 5分钟
LB=34天 T总=170秒
27600秒
99% 4天
50秒
二、什么是价值流分析
1、价值流分析的概念
价值流分析是建立在价值流图基础之上的有效分析 工具,它起源于丰田公司的材料及信息流图“,任何的 生产过程中均存在着材料流和信息流,价值流分析是从 为客户创造价值的视角,将我们的注意力倾注于建立流 动,消除非增值活动,快速增加价值的改进上去,并建 立起材料流和信息流的联系。借助价值流图的价值流分 析,是有效的”学会发现“的手段。
精益生产3.VSM(价值流图及价值 流分析课件
3、价值流图的目标
价值流图是一种强力的可视化工具,它的主要目 标是帮助我们确认运营流程中存在的潜在的,对客户 不增值的浪费活动,价值流图是任何企业展开流程分 析的有效工具,既可作为企业内部沟通的工具,也可 作为企业的战略规划工具,将企业流程所有相关的物 流,信息流和现金流以图示的方式加以表达,有利于 企业了解目标的经营现况和未来的经营现况。绘制一 副现有系统的
附
加
价 值
发布草案
产品X 产品A
月末结算 现金需求
销售报价
定单目录
返回材料需求
概念
原材料
产成品
现金
第0周
第52周
注:图中的APQP代表的含义是“质量先期计划”。
精益生产3.VSM(价值流图及价值 流分析课件
5、价值流图形的信息沟通
由于价值流图形直观地反映了某一产品系 列(价值流)的物资和信息的流动,因此,它 是对过程革新进行目视管理的一种必不可少的 工具。绘制一个过程的图形能够使你清楚地看 到阻碍流动的浪费现象。消除浪费现象能够使 生产的订货提前期缩短,这还会有助于你持续 不断地满足客户的需求。
价值流程图(VSM)案例分析

第一章
价值流概念
价值流程图
价值流程图案例分析
主要内容
价值流是制造产品所需一切活动的总和,包含了增值活动和不增值活动。 使用价值流分析意味着对全过程进行研究,而不只是研究单个过程;改进全过程,而不是仅仅优化局部。 据统计,增值活动约占企业生产和经营活动的5%,不增值活动约占95%。因此,应在价值流中识别不增值活动,通过持续不断地开展价值流改进,消除各种浪费,降低成本。 价值流改进重点在于物流和信息流。
01
同时,可以考虑采用流水线生产和拉式生产相结合的生产和管理方式。因为这样不仅有利于减少在制品库存,缩短提前期,也非常有利于对装配工位需求的响应。此外,由于定拍工序粗车节拍为60s,采取拉式生产有利于为减少生产过多过早的浪费。
02
改进方案设想
未来价值流程图
需要注意的是,由于钻孔、精车抛光、检验三道工序是2个人在U形生产线中完成的,如采用逐兔式完成,因此每人115s完成三道工序的生产即115s共完成两个工件的加工,同时粗车工人120s完成两个毛坯加工,因此相当于U形生产线中57.5s完成一个零件的加工。因此,图3-2中后面三道工序的加工周期标注57.5s。
1
粗车
1
精车、抛光
1
物料流
有价值
无价值
VSM分析的对象
价值流程图分析以客户的观点分析现有价值流程图每一个活动的必要性,画出期待的价值流的未来状态图,并制定实施计划。 绘制出并简单显示出物流和信息流 揭示产生浪费的原因 创建一个改善的价值流 创建和协调一个跨部门团队方法
价值流程图分析特征
价值流程图分析的好处
01
同时,我可以看出,依照新的方案安排生产,生产提前期可减小到0.5天,比原来减少了66.67%((1.5-0.5)/1.5x100%)。同时可实现流水线下的拉式生产,在制品库存也可明显减少,对装配车间的需求响应将更加的迅速准确。此外生产线平衡率大大提高
价值流图的一个案例分析

一、 VSM及其应用方法:五月底去珠海参加了由美国顾问公司主导的为期5天的VSM Kaizen,让我对VSM的认识又加深了一层,在这里,我很愿意分三个部分来分享我对VSM的认识:一.什么是VSM?二.VSM的组成。
三.如何应用VSM,它的步骤与方法。
一.什么是VSMVSM是Value Stream Mapping的简称,通常译为:价值流程图,是丰田精益生产系统框架下的一种用来描述物流和信息流的形象化工具;是精益生产用来识别目前和未来的价值状况,寻求改善机会,设定改善方向和愿景以及行动计划的工具。
VSM运用精益生产的工具和技术来帮助企业理解和精简生产流程,它的目的是为了辨识和减少生产过程中的浪费。
VSM 往往被用作战略工具、变革管理工具。
从购进原材料的那一时刻,VSM就开始工作了,它贯穿于生产制造所有流程、步骤,直到终端产品离开仓储。
不仅如此,服务业亦可使用VSM进行改善活动。
二.VSM的组成VSM的基本构成有四大部分(无先后):1. 顾客部分。
顾客发出信息,可能是订单,新产品,等等;2. 公司系统部分。
可能是ERP, SAP任何系统,顾客信息进入公司系统;3. 供应商部分。
4. 内部物料流。
主要指产线部分,至少需要人机料(Man, Machine, Material)VSM关注的重点部分(有次序):1.原材料到成品整个制程、工艺上的信息;2.成品到顾客;3.关注信息流部分。
顾客—〉公司系统〈--供应商4.计算Lean Time, 同时包含VA(有价值),NVA(无价值)部分及VA R atio(有价值比例)。
VAM常用图标:三.VSM的应用(实战应用)要素:1. 职位功能交叉的团队成员。
确保管理层支持,至少需要采购物流经理,生产计划经理,生产经理,工艺经理等部门参加;2.确保参加组员受到良好的精益知识,VSM概念培训;3.最好3天全职参与改善。
开始要点:1.选择一个产品系列,具有订单量大而稳定的特点的系列产品;2.需要一个有执行力和领导力的小组领导;3.彻彻底底的开始,从原料进到成品出,所有工序都要关注到;4.同时关注物流和信息流。
- 1、下载文档前请自行甄别文档内容的完整性,平台不提供额外的编辑、内容补充、找答案等附加服务。
- 2、"仅部分预览"的文档,不可在线预览部分如存在完整性等问题,可反馈申请退款(可完整预览的文档不适用该条件!)。
- 3、如文档侵犯您的权益,请联系客服反馈,我们会尽快为您处理(人工客服工作时间:9:00-18:30)。
ASSEMBLY #2
I
SHIPPING
Staging
1 C/T = 39 seconds C/O = 10 minutes Uptime = 100% 2 Shifts 27,600 sec/shift
1 C/T = 46 seconds C/O = 10 minutes Uptime = 80% 2 Shifts 27,600 sec/shift
1x Daily
I
2700 L 1440 R
SHIPPING Staging
收集加工数据
各类产品的数量 使用的机器 操作时间 换产周期 正常运行时间(所要求的机器时间) 操作者数量(敬业的) 包装尺寸 工作时间(减去休息时间) 报废率
#2组装
ACME 冲压加工
I
1200 L 640 R
产品族
目前状态图
将来状态图 工作计划
产品族
在下游过程中通过共同加工步骤及应用共同设备 的一组产品
产品/过程矩阵
产品过程矩阵
创立产品通过的产品和过程(设备)的矩阵.
包括要求和成本/价格数据,根据实际的顾客要求
相关的路径,确保验证,不要推测. 将相似的产品合成组,根据扩大成本80/20法则选择产品族作价值流图-
终检
组装部门.
= 篮子里的半成品
= 盘子里的产成品
ACME 冲压材料流程
1. 2. 3. 4. 5. 6. 冲压 #1点焊工作站 #2点焊工作站 #1组装工作站 #2组装工作站 发货
从哪里开始?
地理布局图
产品控制信息 供方信息 顾客信息
加工流信息 时间线
顾客要求
从顾客开始
图表
State Street AssemblySS 18,400 pcs/mo - 12,000 LH - 6,400 RH Tray = 20 pcs 2 shifts 920 pcs/day
I
1100 L 600 R
S.WELD #2
1 C/T = 46 seconds C/O = 10 min. Uptime = 80% 2 Shifts 27,600 sec/shift
目前状态图
State Street Assembly 18,400 pcs/mo - 12,000 LH - 6,400 RH Tray = 20 pcs 2 shifts 920 pcs/day
以笔纸为工具,让你看到 和理解材料和信息的流, 产品是如何通过价值流形 成的
信息
生产流动
材料
价值流图-要点
通常在巡视时收集信息 先快速浏览门对门情况 从发货点和工作上游开始 自己计算 (回避系统里的数字) 自己做整个流程 用笔纸-整个路线 为什么自己动手 ? 没有延迟 拒绝电脑
1 C/T = 62 seconds C/O = 0 Uptime = 100% 2 Shifts 27,600 sec/shift
1 C/T = 40 seconds C/O = 0 Uptime = 100% 2 Shifts 27,600 sec/shift
C/T = 1 seconds C/O = 1 hour Uptime = 85% 27,600 sec./shift EPE = 2 weeks
1x Daily
I
1100 L 600 R 1
S. WELD #2
I
1600 L 850 R
ASSEMBLY #1
I
1200 L 640 R
ASSEMBLY #2
SHIPPING
I
2700 L 1440 R
Staging
1 C/T = 62 seconds C/O = 0 Uptime = 100% 2 Shifts 27,600 sec/shift
目前状态图
State Street Assembly 18,400 pcs/mo - 12,000 LH - 6,400 RH Tray = 20 pcs 2 shifts 920 pcs/day
1x Daily
I
1200 L 640 R
ASSEMBLY #2
I
2700 L 1440 R
SHIPPING Staging
门对门价值流
Acme 生产控制:
加入信息流
图表:
PRODUCTION CONTROL
MRP Daily Order
来自顾客的预测/30/60/90天 每日确认订货 每周 产生MRP 6 周的预测给供方 每周向供方 确认放行 每周计划 每日发货计划
Weekly Schedule
Michigan Steel Co. 500 ft. coils Weekly Release
ASSEMBLY #1
1 C/T = 62 seconds C/O = 0 Uptime = 100% 2 Shifts 27,600 sec/shift
目前状态图
State Street Assembly 18,400 pcs/mo - 12,000 LH - 6,400 RH Tray = 20 pcs 2 shifts 920 pcs/day
这是发达公司运营的很现代的价值流
价值分析案例
产业 步骤 增值 %
玻璃制品 食品 纺织 金属 电子 消费产品 生产支持
72 37 105 187 239 105 98
6 4 11 13 19 10 15
8 11 10 7 8 10 15
精益技术——价值流图
提供容易理解的可视的图,表达什么是顾客的价值, 及提供价值的过程的流动细节
1 C/T = 40 seconds C/O = 0 Uptime = 100% 2 Shifts 27,600 sec/shift
#1组装
ACME 冲压加工
I
1600 L 850 R
图表:
2 个部件号 1 个操作者 2 班制 没有设置 62 秒操作时间 100%正常运行使用 2次休息–每次 10 分钟 库存: - 1600 LH - 850 RH
组装公司 每月18,400 件 - 12,000 Type LH - 6,400 Type RH 每月20 天 每盘20 件 两班工作制 一天1 卡车 18,400 / 20 = 920/ 天
目前状态图
State Street Assembly 18,400 pcs/mo - 12,000 LH - 6,400 RH Tray = 20 pcs 2 shifts 920 pcs/day
你作,你理解 重点是流动,而不是电脑 修正自己的错误微调的技能
价值流图步骤 产品族 目前状态图
将来状态图
工作计划
生产控制
供应商
客户
冲 压
焊 接1
焊 接2
组 装1
组 装2
运输
目前价值流图
生产控制 客 户
供应商
冲 压
焊 接 组装
运输
改善后的价值流图
价值流图
“ 目前状态”
价值流图步骤
500 ft. coils
Tues. + Thurs.
进门
STAMPING STAMPING 200 T
出门
S. WELD #1
1x Daily
I
Coils 5 days
I
4600 L 2400 R
I
1100 L 600 R
S. WELD #2
I
1600 L 850 R
ASSEMBLY #1
I
1200 L 640 R
图表
ቤተ መጻሕፍቲ ባይዱ
2 个部件号 1个操作者 2班制 没有设置 40 秒操作时间 100% 正常运行使用 2次休息–每次 10 分钟 库存: - 1200 LH - 640 RH
ASSEMBLY #2
1 C/T = 40 seconds C/O = 0 Uptime = 100% 2 Shifts 27,600 sec/shift
6-week Forecasts
目前状态图
PRODUCTION CONTROL MRP Daily Order Weekly Schedule
1x Daily
I
1600 L 850 R
ASSEMBLY #1
I
1200 L 640 R
ASSEMBLY #2
SHIPPING
I
2700 L 1440 R
Staging
1 C/T = 62 seconds C/O = 0 Uptime = 100% 2 Shifts 27,600 sec/shift
“对受益最大的影响”
Extended Cost $40k $50k $30k $10k $10k $5k $15k
A B C D E F G
R eceiv ing x x x x x x x
Products
Stamping x x x
D rill x x x x x
Mill x x x
x x
PR O C E SSE S G rind D rill x x x x x x x
目前状态
将来状态
为什么画图?
单个的价值流可视化 应用一组工具来评审价值流 跨职能的参与和决策 理解存在什么浪费和在哪里 可以开发改进的计划
一个特定的产品,工作单元或产品族 / 工作单元 族,使用符号或图表用视觉表示其材料和信息的 流动
顾客