PFMEA分析报告
过程失效模式及后果分析(PFMEA)

XXX汽车技术股份有限公司潜在失效模式及影响分析 PFMEA螺纹孔内无铝屑,机加工面边缘毛刺清理干净;螺纹孔内有铝屑,机加工面边缘未清理干净影响客户装配,客户抱怨61.丝锥损坏2.夹具松动3.切削液未正确喷淋,铝屑未吹掉31.首检记录表2.巡检记录表354None5XΦ0.341±0.01深0.55(英制)尺寸超差 1.毛坯不合格或尺寸变化大4XΦ0.232±0.01深0.5(英制)尺寸超差 2.夹具松动;3.程序错误2XΦ0.232±0.01深0.5(英制)尺寸超差 4.装夹失误2X4.34±0.02(英制)尺寸超差 1.毛坯不合格或尺寸变化大27.19±0.02(英制)尺寸超差 2.夹具松动;3.程序错误2X7.05±0.02(英制)尺寸超差 4.装夹失误2X11.72±0.02(英制)尺寸超差1.毛坯不合格或尺寸变化大1.25±0.02(英制)尺寸超差2.夹具松动;3.程序错误2.38±0.02(英制)尺寸超差 4.装夹失误1.56±0.02(英制)尺寸超差 1.毛坯不合格或尺寸变化大2.44±0.02(英制)尺寸超差 2.夹具松动;3.程序错误8XΦ0.118±0.01(英制)尺寸超差 4.装夹失误尺寸超差1.毛坯不合格或尺寸变化大2X45°±0.5°尺寸超差2.夹具松动;None3影响装配和功能7631.首检记录表2.巡检记录表3★3影响装配和功能7★31.首检记录表2.巡检记录表363NoneNone63影响装配和功能7★31.首检记录表2.巡检记录表3影响装配和功能7★31.首检记录表2.巡检记录表None影响装配和功能7★31.首检记录表2.巡检记录表36363None。
pfmea过程失效模式与后果分析报告

通过深入分析,我们确定了导致这些失效的潜在原因,包 括设备老化、操作规程不完善、员工培训不足、原材料质 量控制不严格以及工艺参数设置不合理等。
对未来工作的建议和展望
改进措施建议
持续改进计划
未来研究方向
基于PFMEA的结果,我们提出了一系 列改进措施,包括更新设备、优化操 作规程、加强员工培训、严格控制原 材料质量以及调整工艺参数等。这些 措施旨在减少失效发生的风险,提高 生产过程的可靠性和稳定性。
为了确保改进措施的有效实施,我们 制定了持续改进计划。该计划包括定 期评估改进效果、监测潜在问题的出 现以及调整改进措施等。通过持续改 进,我们期望能够不断优化生产过程 ,提高产品质量和客户满意度。
在报告的最后,我们提出了一些未来 可能的研究方向。这些方向包括进一 步探索失效模式与潜在原因之间的关 系、研究新的失效分析方法以及开发 更加智能化的失效预测模型等。通过 深入研究,我们期望能够为企业的持 续改进提供更有力的支持。
失效模式
汽车发动机性能下降
后果
影响汽车动力性能,可能导致油耗增加、排放超标
潜在原因
制造过程中材料、工艺、设备等方面的问题
风险评估
高风险,需采取措施进行改进
案例二:电子产品制造过程的PFMEA分析
失效模式
电子元件短路
潜在原因
制造过程中元件组装、焊 接等环节出现问题
后果
产品功能失效,可能引发 安全事故
提前发现和预防问
题
PFMEA是一种预防性的质量工具 ,它通过提前发现和预防潜在的 问题,减少后期修改和返工的成 本。
优化设计和过程
PFMEA分析结果可以为设计和过 程的改进提供指导,帮助企业优 化产品和过程的性能、可靠性和 安全性。
PFMEA风险分析评估范例

产品型号/Product Model: / 关键日期/ Key Date:2017年8月16日 FMEA日期 FEMA date:2017年8月16日修订revised by:2018年9月25日核心小组:XX,XXX,XXX,XXX,产品型号/Product Model: / 关键日期/ Key Date:2017年8月16日 FMEA日期 FEMA date:2017年8月16日修订revised by:2018年9月25日核心小组:XX,XXX,XXX,XXX,产、设备每日点检;备每日点检;产品型号/Product Model : / 关 键 日 期/ Key Date :2017年8月16 日 FMEA 日期 FEMA date :2017年8月16日 修 订revised by :2018年9月25日核心小组:XX,XXX,XXX,XXX,产、设备每日点检、上线前试产、设备每日点检专检验、上线前试产、设备每日点检产品型号/Product Model: / 关键日期/ Key Date:2017年8月16日 FMEA日期 FEMA date:2017年8月16日修订revised by:2018年9月25日核心小组:XX,XXX,XXX,XXX,产品型号/Product Model: / 关键日期/ Key Date:2017年8月16日 FMEA日期 FEMA date:2017年8月16日修订revised by:2018年9月25日核心小组:XX,XXX,XXX,XXX,产品型号/Product Model: / 关键日期/ Key Date:2017年8月16日 FMEA日期 FEMA date:2017年8月16日修订revised by:2018年9月25日核心小组:XX,XXX,XXX,XXX,产品型号/Product Model: / 关键日期/ Key Date:2017年8月16日 FMEA日期 FEMA date:2017年8月16日修订revised by:2018年9月25日核心小组:XX,XXX,XXX,XXX,产品型号/Product Model: / 关键日期/ Key Date:2017年8月16日 FMEA日期 FEMA date:2017年8月16日修订revised by:2018年9月25日核心小组:XX,XXX,XXX,XXX,产品型号/Product Model: / 关键日期/ Key Date:2017年8月16日 FMEA日期 FEMA date:2017年8月16日修订revised by:2018年9月25日核心小组:XX,XXX,XXX,XXX,功能不良不能达到产品的使用效果,消费者投诉原材料不合格,导致产品品质不合格,达不到预期用途;1严格按照原料标准采购原材料,定期进行产品检测。
失效模式与后果分析报告(PFMEA)控制程序

1.程序目的确定与产品生产过程相关的过程失效模式;评价和发现在各个生产过程中可能发生的失效模式的原因/机理,确定减少失效发生或找出失效条件的过程控制变量;为采取预防措施提供对策。
2.适用围适用于公司汽车钣金件产品冲压、焊接、表面处理等汽车零部件中新产品、产品的工程变更时的生产。
3.过程识别产品实现过程过程:产品策划过程过程活动:过程策划、设计与试制4.定义“PFMEA”是指由负责制造的多功能小组采用的一种分析技术,用来保证在可能的围已充分地考虑到并指明潜在失效及其相关的起因/机理。
5.主要职责和权限5.1 PFMEA多功能小组负责过程失效模式及后果分析、制定和跟踪措施。
5.2制造科等部门按策划的结果,实施和完善控制计划、作业指导书。
6.程序容6.1 由APQP多功能小组组长召集有关人员组成PFMEA多功能小组。
这个小组应包括与产品有关的技术、工艺、品质、生产、设备、营业等方面人员。
这个小组的主要执笔人应为负责本产品工艺的技术人员。
6.2 依据APQP策划中确定的过程(工艺)流程图,开展过程失效模式及后果分析(PFMEA),编写《过程失效模式及后果分析(PFMEA)表》。
客户若有特殊批准按客户要求和批准执行。
6.2.1写表头部分1)编号:按过程研究的顺序号编制。
2)项目名称:填写所分析产品/零件的正式名称。
3)过程责任部门:填写生产单位或生产班组名称。
4)编制人:填写主持编制本表人的、及所属部门名称。
5)零件号:填入要分析零件号。
6)关键日期:填写初次PFMEA预定完成的日期,该日期不应超过计划开始生产的日期。
7)PFMEA日期:填写编制PFMEA初稿日期及最新修改的日期。
8)主要参加成员:填写参与分析的多功能小组成员。
6.2.2 过程功能要求简单描述被分析的过程/工序,说明该过程/工序的目的,若某一过程/工序包括多个具有不同失效模式的过程/工序,应把这些过程/工序作为独立过程单列处理。
6.2.3 找出潜在失效模式1)潜在失效模式是指过程/工序中可能发生的不符合过程要求和/或设计意图的形式,是对具体过程/工序不符合要求的描述,它可能是引发下道过程/工序的潜在失效模式,也可能是上一道过程/工序潜在失效的后果。
PFMEA过程失效模式及后果分析报告

科技股份有限公司作业文件文件编号:XXXX-XXXX.XX 版号:A/0(PFMEA)过程失效模式及后果分析作业指导书批准:审核:编制:受控状态:分发号:2016年01月15日发布2016年01月15日实施过程潜在失效模式及后果分析作业指导书(PFMEA)XXXX-XXXX.XX1目的过程潜在失效模式及后果分析,简称PFMEA。
是一种信赖度分析的工具,可以描述为一组系统化的活动,是对确定产品/过程必须做哪些事情才能使顾客满意这一过程的补充。
其目的是:(a)并评价产品/过程中的潜在失效以及该失效的后果;(b)确定能够消除或减少潜在失效发生机会的措施;(c)将全部过程形成文件。
2 范围:适用于公司用于零组件的所有新产品/过程的样品试制和批量生产。
适用于过程设计的风险性及后果的分析;适用于过程重复,周期性永不间断的改进分析。
3 术语和定义:1)PFMEA:指Process Failure Mode and Effects Analysis(过程失效模式及后果分析)的英文简称。
由负责制造/装配的工程师/小组主要采用的一种分析技术,用以最大限度地保证各种潜在的失效模式及其相关的起因/机理已得到充分的考虑和论述。
2)失效:在规定条件下(环境、操作、时间),不能完成既定功能或产品参数值和不能维持在规定的上下限之间,以及在工作范围内导致零组件的破裂卡死等损坏现象。
3)严重度(S):指一给定失效模式最严重的影响后果的级别,是单一的PFMEA范围内的相对定级结果。
严重度数值的降低只有通过设计更改或重新设计才能够实现。
4)频度(O):指某一特定的起因/机理发生的可能发生,描述出现的可能性的级别数具有相对意义,但不是绝对的。
5)探测度(D):指在零部件离开制造工序或装配之前,利用第二种现行过程控制方法找出失效起因/机理过程缺陷或后序发生的失效模式的可能性的评价指标;或者用第三种过程控制方法找出后序发生的失效模式的可能性的评价指标。
PFMEA分析范例
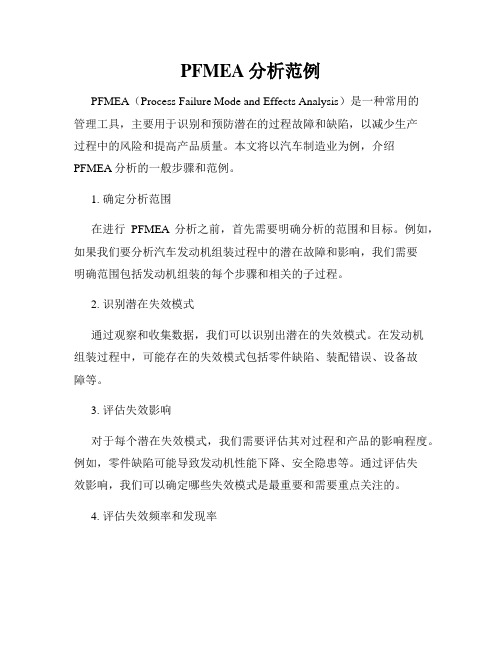
PFMEA分析范例PFMEA(Process Failure Mode and Effects Analysis)是一种常用的管理工具,主要用于识别和预防潜在的过程故障和缺陷,以减少生产过程中的风险和提高产品质量。
本文将以汽车制造业为例,介绍PFMEA分析的一般步骤和范例。
1. 确定分析范围在进行PFMEA分析之前,首先需要明确分析的范围和目标。
例如,如果我们要分析汽车发动机组装过程中的潜在故障和影响,我们需要明确范围包括发动机组装的每个步骤和相关的子过程。
2. 识别潜在失效模式通过观察和收集数据,我们可以识别出潜在的失效模式。
在发动机组装过程中,可能存在的失效模式包括零件缺陷、装配错误、设备故障等。
3. 评估失效影响对于每个潜在失效模式,我们需要评估其对过程和产品的影响程度。
例如,零件缺陷可能导致发动机性能下降、安全隐患等。
通过评估失效影响,我们可以确定哪些失效模式是最重要和需要重点关注的。
4. 评估失效频率和发现率在这一步骤中,我们需要评估潜在失效的频率和发现率。
频率指的是该失效模式在特定时间段内发生的次数,发现率指的是我们能在生产过程中或产品出厂之前检测到该失效模式的概率。
5. 确定风险优先级通过综合考虑失效影响、频率和发现率,我们可以确定每个失效模式的风险优先级。
通常采用风险优先数(RPN)计算方法,RPN = 失效影响 ×频率 ×发现率。
风险优先级高的失效模式意味着需要优先采取预防和纠正措施。
6. 制定预防和纠正措施根据风险优先级,我们可以制定相应的预防和纠正措施来降低潜在失效的风险。
例如,对于零件缺陷,我们可以建立更严格的质量控制流程,提高零件的检验和筛选标准。
7. 实施和监控措施制定好措施后,需要将其实施到实际生产过程中,并进行监控和评估。
通过不断追踪和更新PFMEA表格,我们可以及时发现并纠正新的失效模式,不断提升生产过程的稳定性和产品质量。
总结:本文以汽车制造业为例,介绍了PFMEA分析的一般步骤和范例。
吹塑、注塑产品pfmea报告
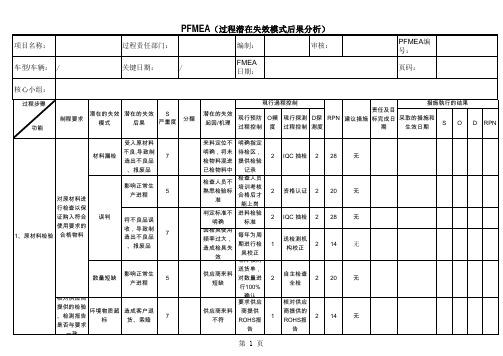
7
2
3 42
依据产品
料胚厚度不 足
标准书要 求,通过 吹塑机台
3
首检/自检 2
/巡检
42
无
厚薄控制
型胚气压过 大导致边料
过多
操作员根 据气压状 况适时调
整
3
自检
2 42
无
第3页
PFMEA(过程潜在失效模式后果分析)
项目名称:
过程责任部门:
用吹塑机通
车型/车辆: /过温度/时
间/空气压
3、产品成型 力把塑胶原
核心小组: 料吹胀成符
合规定尺寸
过程步骤
的制品
关键日期:
/
功能
潜在的失效 潜在的失效 S
制程要求
模式
后果
严重度 分類
编制:
FMEA 日期:
审核:
PFMEA编 号:
页码:
現行過程控制
措施執行的结果
责任及目
潜在的失效
现行预防 O頻 現行探测 D探 RPN 建议措施 标完成日 采取的措施和
、检测报告
7
标
货、索赔
是否与要求
一致
来料定位不 明确指定
明确,将未 待检区,
2 IQC 抽检 2 28
无
检物料混进 提供检验
已检物料中 记录
检查人员
检查人员不
培训考核
熟悉检验标
2 资格认证 2 20
无
合格后才
准
能上岗
判定标准不 进料检验
2 IQC 抽检 2 28
无
明确
标准
因检具使用
每年为周
频率过大,
17
比对色板验 收,保留色板
镭雕PFMEA失效模式分析

FMEA编号:页数:项目名称编制/日期: 核心小组:审核/日期过程责任部门修订日期变形产生不良品,造成制造成本浪费51、进货控制计划不详细,有漏项目;2、检验员粗心漏检项目。
21定期修改更新控制计划;2实行员工考核制度。
1、随时抽检报告和实物;2、操作者加工前自检。
440无错检产生不良品,造成成本浪费51、进货控制计划没及时更新;2、检验员检验错误。
21定期修改更新控制计划;3实行员工考核制度。
1、随时抽检报告和实物;2、操作者加工前自检。
440无材料上有灰尘影响产品外观5产品暴露在空气中2放入纸箱中保存目测100%控制220无尺寸不良影响后续加工6供应商加工控制错误2来料检查224无3领料领错料造成产品性能降低6原料放错位置1产品做定位摆放318雕错图案产品批量不良,造成成本浪费6图案相象,图案用错2样品图案进行控制1、随时抽检报告和实物;2、操作者加工前自检。
224无图案偏位产品组装后灯光照射会偏暗5产品摆放未放到位置4专用对位菲林对位控制1、随时抽检报告和实物;2、操作者加工前自检。
240无烧焦/未雕干净影响外观5镭射电流过大/过小4样品图案进行控制1、随时抽检报告和实物;3、操作者加工前自检。
240锯齿产品图案不流畅,影响外观5镭雕鼓调整精度不够4样品图案进行控制1、随时抽检报告和实物;2、操作者加工前自检。
240无5批号批号不清楚或没有不清楚产品的生产日期5工人忘记填写4目测检查目测100%控制240无外形图案不合格客户困难,造成停线7图案相象,图案用错2NA目测100%控制228无检验错误、漏检1、错判,不合格品流入客户,引起顾客抱怨;2、误报,成本浪费71、检验作业指导书不详细,不能起指导作用;2、检验员技能不足。
21定期修改检验作业指导书;2对检验员现场培训;3每天不合格零件进行评审。
质量工程师巡检或抽检456无限制性物质影响用户的健康9CC材料中含有有害物质1设计选择符合要求的材料327无包装不符合要求客户拒收或顾客抱怨6操作者未按照包装要求执行2包装规范发放到现场并培训操作者100%检验448无标识不正确发运错误,顾客抱怨6料箱上旧标识没有取出;操作者疏忽2操作者100%检验;检验员成品抽验448无8入库产品数量不正确影响后续发货6生产装箱多装或少装,取货无登记2培训操作者,做好库存记录操作者100%检验,定期盘点448无9发运产品数量不正确客户抱怨6装货的时候数量不足或多装2实行出货检再加以控制发货前清点数量448无10出货检错检、漏检1、错判,不合格品流入客户,引起顾客抱怨;2、误报,成本浪费71、检验作业指导书不详细,不能起指导作用;2、检验员技能不足。
汽车玻璃加工PFMEA分析范例

2 24
管
客户型号: 厂内型号:TPK-9243A3
过程失效模式及后果分析报告
日期 编制:
版本 审核:
A1 核准:
负责部门:工程部
核心小组成员:
现行状况
措施结果
Severity (严重度) Occurrence (产生机率) Detection (不易测度)
RPN (风险数)
过程 步骤
功能
要求
潜在的失 失效模式 效模式 结果
2
2 20
每批次进行抽检,4收5退 2016.02.17 6 1 2 12
入库存 放
存放原料
外观
破损
强度不合 格
6
⊕ 玻璃碰撞导致破损
5 员工拿放手法不正确
2 60 原材轻拿轻放
2016.02.18 培训员工放置玻璃手法 2016.02.18 6 1 2 12
出库
运输到下 格工站
外观
破损
强度不合 格
过程失效模式及后果分析报告
日期 编制:
版本 审核:
A1 核准:
负责部门:工程部
核心小组成员:
现行状况
措施结果
Severity (严重度) Occurrence (产生机率) Detection (不易测度)
RPN (风险数)
过程 步骤
功能
要求
潜在的失 失效模式 效模式 结果
分类 潜在的失效起因/机理
3
16 无
1.检验来料,确保来料 覆有保护膜; 48 2.装夹前需清洁底座; 3.插篮使用间隔板,防 止前后玻璃接触;
1.及时添加/更换切削
72
液; 2.定义并管制砂刀寿
命;
平磨 (划伤
PFMEA过程风险分析评估

产品型号/Product Model: / 关键日期/ Key Date:2020年3月18日 FMEA日期 FEMA date:2020年3月18日修订revised by:2020年4月5日核心小组:xxx xxx xxx xxx产品型号/Product Model: / 关键日期/ Key Date:2020年3月18日 FMEA日期 FEMA date:2020年3月18日修订revised by:2020年4月5日核心小组:xxx xxx xxx xxx产、设备每日点检;备每日点检;产品型号/Product Model : / 关 键 日 期/ Key Date :2020年3月18 日 FMEA 日期 FEMA date :2020年3月18日 修 订revised by :2020年4月5日核心小组:xxx xxx xxx xxx产、设备每日点检、上线前试产、设备每日点检专检验、上线前试产、设备每日点检产品型号/Product Model: / 关键日期/ Key Date:2020年3月18日 FMEA日期 FEMA date:2020年3月18日修订revised by:2020年4月5日核心小组:xxx xxx xxx xxx产品型号/Product Model: / 关键日期/ Key Date:2020年3月18日 FMEA日期 FEMA date:2020年3月18日修订revised by:2020年4月5日核心小组:xxx xxx xxx xxx产品型号/Product Model: / 关键日期/ Key Date:2020年3月18日 FMEA日期 FEMA date:2020年3月18日修订revised by:2020年4月5日核心小组:xxx xxx xxx xxx产品型号/Product Model: / 关键日期/ Key Date:2020年3月18日 FMEA日期 FEMA date:2020年3月18日修订revised by:2020年4月5日核心小组:xxx xxx xxx xxx产品型号/Product Model: / 关键日期/ Key Date:2020年3月18日 FMEA日期 FEMA date:2020年3月18日修订revised by:2020年4月5日核心小组:xxx xxx xxx xxx产品型号/Product Model: / 关键日期/ Key Date:2020年3月18日 FMEA日期 FEMA date:2020年3月18日修订revised by:2020年4月5日核心小组:xxx xxx xxx xxx1、原则上每批订单量产前均应进行风险评估,根据工厂实际,产品较为固定,生产及相应工艺较为简单,人机料法环等因素也稳定,故暂定正常生产时针对每种类型产品每年评估一次;2、人机料法环等因素或其他因素发生变更时,则也应进行风险评估;3、新产品开发时应也应进行风险评估。
产品潜在失效模式及后果分析

产品潜在失效模式及后果分析目录1. 产品潜在失效模式及后果分析概述 (2)1.1 研究目的 (3)1.2 研究方法 (4)1.3 研究范围 (5)2. 失效模式分类及描述 (7)2.1 设计失效模式 (8)2.1.1 设计缺陷 (9)2.1.2 设计不合理 (10)2.1.3 设计错误 (11)2.2 制造失效模式 (12)2.2.1 材料失效 (13)2.2.2 工艺失效 (14)2.2.3 装配失效 (16)2.3 使用失效模式 (18)2.3.1 操作不当 (19)2.3.2 维护不当 (20)2.3.3 环境因素影响 (21)3. 潜在失效模式分析方法 (22)3.1 FMEA(失效模式及后果分析)方法 (23)3.1.1 定义和目的 (25)3.1.2 步骤和流程 (26)3.1.3 结果和改进措施 (27)3.2 CBET(控制基于工程的方法)方法 (28)3.2.1 定义和目的 (29)3.2.2 步骤和流程 (30)3.2.3 结果和改进措施 (31)4. 具体案例分析 (32)4.1 案例一 (32)4.2 案例二 (33)4.3 案例三 (34)5. 结果与讨论 (35)5.1 FMEA结果报告示例 (36)5.2 CBET结果报告示例 (38)5.3 结果讨论与改进建议 (38)1. 产品潜在失效模式及后果分析概述产品潜在失效模式及后果分析(PFMEA)是一种分析工具,用于识别产品在设计、制造和生命周期各个阶段的潜在失效模式。
它旨在预测和预防潜在的产品失效,以及评估和减少产品对用户造成的不利后果。
本文档概述了如何实施产品潜在失效模式及后果分析的过程和方法,旨在提高产品质量和安全性。
产品潜在失效模式及后果分析是质量管理和风险管理的一种技术,用于评估产品或过程可能发生的失败以及这种失败可能导致的后果。
PFMEA可以帮助识别产品设计中的潜在问题,以及制造过程中的潜在缺陷,从而提高产品的可靠性、安全性和性能。
汽车塑料部件PFMEA分析

PO
against Invoice.
接收的材料,批号与定单一致
供应商发错料
2. Correct packing and Labeling 正确的包装与标签
Torn Bags & No or wrong identification on bags. 损坏的包装,没有或错误的 标签
3.Received Correct quantity 数量与送货单上的一致
2..inproper inspection method 不合理的检查方法
paint rejected / incorrect results 涂料拒收/不正确的报告
3.Dameaged or
uncalibration measurement machine 损坏或未经检验的测量仪
incorrect inspection result 错误的检验结果
POTENTIAL FAILURE MODE AND EFFECT ANALYSIS ( PROCESS FMEA )制程FMEA
PROJECT项目 : Part Number 零件号 : Part Name 零件名称:
APPROVED BY审核:
GRILLE SWDO DEFROGGER OUTLET
Variation in Quantity. 数量不足
Not able to plan for production. 无法按计划生产
Material contamination & material
mix up
材料污染
混料
Not able to plan for production. 无法按计划生产
PROCESS RESP制程责任.
触摸屏PFMEA分析报告

1
15
无
1)裁切尺寸不对
1)尺寸同设计尺寸 大片膜不符
3
作业人员操作失误
2
2
12
无
1)烘烤温度不对
影响材料的电阻、和 缩水。
8
认为设定出错或设备故障
2
3
48
பைடு நூலகம்
无
根据文件要 2 求,对材料进 行缩水处理, 避免后续加工 中材料收缩。
耐酸油墨印刷
2)烘烤时间不对
影响材料的电阻、和 缩水。
8
认为设定出错或设备故障
蚀刻不净
蚀刻区域内部分ITO 残留。
8
设备温度异常,温度过低 。
2
2
32
无
蚀刻完成后材料表面 存在水迹、污迹等。
5
设备风刀压力不足、风刀 堵孔、风刀过滤芯损坏。
2
2
20
无
银线印刷
印刷偏位
根据文件要求 5 在产品上印刷 导电银浆油 墨,实现导电 功能。
印刷位置不固定,位 置有偏移,严重的造 成不导通和绝缘不良 。
过程失效模式及后果分析(Process FMEA)
产品项目(客户型号): 项目名称 (产品型号): 核心小组:
序 号 工程功能 / 要求事项 ITO膜裁切 失效模式 失效影响 严重 程度 R 失效原因 发生 频率 P 目前过程的控制措施 可测 度 N R P N 推荐的改进措施 改进措施结果 负责人及 完成时间 推荐措施改进 严重 发生 可测 效果的跟进及 度 频率 度 下一步建议 R P N
1
16
无
蚀刻残留短、断路
功能不良
8
激光蚀刻时能量不稳定;
2
1、sensor全检;
注塑PFMEA分析范例
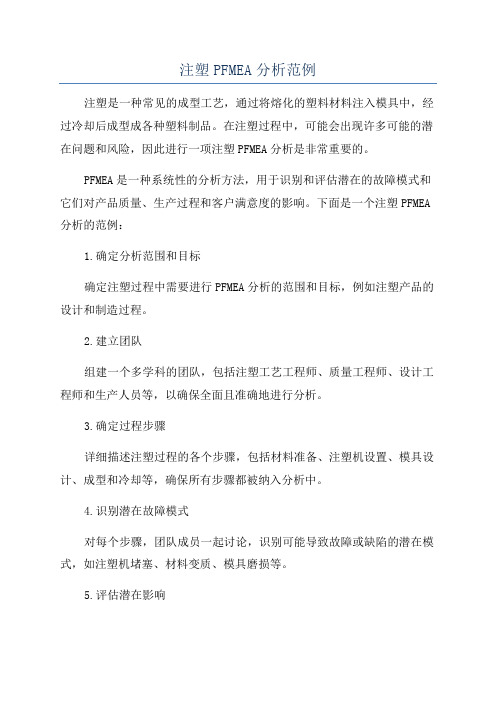
注塑PFMEA分析范例注塑是一种常见的成型工艺,通过将熔化的塑料材料注入模具中,经过冷却后成型成各种塑料制品。
在注塑过程中,可能会出现许多可能的潜在问题和风险,因此进行一项注塑PFMEA分析是非常重要的。
PFMEA是一种系统性的分析方法,用于识别和评估潜在的故障模式和它们对产品质量、生产过程和客户满意度的影响。
下面是一个注塑PFMEA 分析的范例:1.确定分析范围和目标确定注塑过程中需要进行PFMEA分析的范围和目标,例如注塑产品的设计和制造过程。
2.建立团队组建一个多学科的团队,包括注塑工艺工程师、质量工程师、设计工程师和生产人员等,以确保全面且准确地进行分析。
3.确定过程步骤详细描述注塑过程的各个步骤,包括材料准备、注塑机设置、模具设计、成型和冷却等,确保所有步骤都被纳入分析中。
4.识别潜在故障模式对每个步骤,团队成员一起讨论,识别可能导致故障或缺陷的潜在模式,如注塑机堵塞、材料变质、模具磨损等。
5.评估潜在影响对每个潜在模式,团队成员评估其对产品质量、生产效率和客户满意度的潜在影响。
例如,注塑机堵塞可能导致不良制品数量增加、生产停止和客户投诉等。
6.确定当前控制措施列出当前已经采取的控制措施,用于降低每个潜在模式的风险。
例如,使用可靠的注塑机和模具、定期保养和维护等。
7.评估现有控制措施的有效性对每个潜在模式,评估当前控制措施的有效性和可靠性。
如果发现当前控制措施无法有效降低风险,则需要提出改进措施。
8.提出改进措施对于无法满足要求的控制措施,团队成员一起提出改进建议。
例如,更换注塑机、改进模具设计、更换材料供应商等。
9.评估改进措施的效果对提出的改进措施进行评估,并根据实际效果进行相应的调整和改进。
这有助于确保改进措施的有效性和可行性。
10.编写PFMEA报告汇总所有分析结果和改进措施,编写PFMEA报告。
确保报告清晰、具体,并包含所有必要的信息,以便于团队成员和其他相关人员参考。
通过进行注塑PFMEA分析,可以及时识别潜在的故障模式,并采取相应的改进措施,降低质量问题和生产风险,提高客户满意度和产品质量。
吹塑注塑产品pfmea报告

项目名称:
过程责任部门:
编制:
审核:
PFMEA编号:
车型/车辆:
/
关键日期:
/
FMEA日期:
页码:
核心小组:
过程步骤 功能
现行过程控制
措施执行
制程要求
潜在的失 效模式
潜在的失 效后果
S 严重度
分类
潜在的失
效起因/机 现行预防过
理
程控制
O频 度
现行探 测过程 控制
2
首检/自 检/巡检
2
28
无
模具冷却 上下模后清
水道堵塞
理
5
自检
生产过 程中每 3 105 十二小 时检查 水道
工程课 2015-9-1
生产过程中每 十二小时检查 水道,《制程 参数检查表》
2015-9-1
第3页
PFMEA(过程潜在失效模式后果分析)
项目名称:
过程责任部门:
编制:
审核:
PFMEA编号:
措施执行的结果 S O D RPN
第 17 页
在失效模式后果分析)
措施执行的结果 S O D RPN
第 18 页
过程步骤 功能
现行过程控制
措施执行
制程要求
潜在的失 效模式
潜在的失 效后果
S 严重度
分类
潜在的失
效起因/机 现行预防过
理
程控制
O频 度
现行探 测过程 控制
D探 RPN 测 度
建议措 责任及目标完成
施
日期
采取的措施和
生效日期
穿孔
7
粘胶
客户不可 接受粘胶 7
制程失效模式和影响分析报告PFMEA

Root Cause
OCC
DET
RPN
Corrective Principal/Dept finished 采取措施
function / Requireme
Mode
Failure
预防 Prevention
探测 Detection
measures
date
Performed actions
严重度 (SEV)
文件版本 Rev.
品质工程 Quality Engr.
制造工程 Manuf Engr.
产品工程 Prod Engr.
编制日期 修订日期
拟制 Prepared By:
审核 Checked By:
文件编 号:
核准 Approved By:
备注:1) SEV/OCC/DET的评分标准参见《PFMEA作业指导书》EN-3-006; 2) 当 RPN≥90 或 S≥8 时,执行纠正/预防措施。 Note: 1) SEV/OCC/DET Evaluating Principle, refer to RD-3-006 FMEA Control Criterion; 2) For those components with high RPN≥100 or S*O≥25 failure mode, perform corrective/preventive measures, improved plan.
项目名称: Project Name
PFMEA小组成员 Team member:
研发部 R&D Dept.
产品型号: Product Number
可靠性及失效分析 Reliability & FA
XXX电子有限公司
触摸屏PFMEA分析报告

导电银浆油墨,实现导电功能。
根据文件要求
要求:FPC位置符
1)产品漏点胶1)点胶工序“5S”划分不
清,产品出现混淆
2
1)点胶工序区域有明确的“5S”定
制。
2)点胶与未点胶的产品摆放不
一样,未点胶的产品是坚首摆放,点
过胶的产品是横着摆放。
228
2)点胶不完整2)人员点胶速度过快;
3)胶体未完全固化,被转
序误触。
2
1)每片产品点胶后要求全部自检。
2)点胶后记录点胶时间,下一工序
按照规定时间差再行制作。
228
3)点胶过量3)有可能造成产品
装配时与机壳干涉。
1)针头过粗;
2)人员点胶速度过慢
3
1)作业指导书有明确要求点胶的进
量。
2)每片产品点胶后要求全部自检。
3)后道工序外观有要求检验点胶效
果,如发现不良将考核点胶人员绩效。
4)根据文件要求选用合适针头,
同时与封样件比对
242 7
FPC点胶可靠性隐患
15。
PCB来料检查PFMEA分析范例

项目Item:FMEA 编号FMEA No.采取的措施action adoptedS O DR P N铜面凹陷、褶皱、擦花等。
Cupped,cockle andscrape etc on the copper surface 部分产品需要报废6来料问题Issueoccur before enter the storage 1每批来料按AVL=0.65进行抽样检查目视检查板材外观,必要时使用放大检查。
742板料空洞、杂质、气泡、白斑、白点部分产品需要报废6来料问题Issueoccur before enter the storage 1每批来料按AVL=0.65进行抽样检查蚀刻后目视检查基材情况742板料尺寸不够laminate size not enough 影响后工序生产效率,部分产品需要挑选5来料问题Issue occur before enter the storage 25张/每批进行尺寸测量使用卷尺进行抽样测量550板料超厚或太薄laminate thicknessover or under部分产品需要报废6来料问题Issue occur before enter the storage 25张/每批(每张四个边各取一个点值),使用千分尺进行厚度测量使用千分尺进行抽样测量560底铜超厚或太薄thebottom copper thickness over or under部分产品需要报废6来料问题Issueoccur before enter the storage25张/每批,用CMI165进行铜厚测量用CMI165进行抽样测量560Potential Failure Mode and Effect Analysis过程潜在失效模式及后果分析(PFMEA)类型type:PCB关键日期Key Date:版本content Version:B2审批Approval by:双面板/多层板double-side/multi-layers PCBFMEA-IQC-01编制日期Pepare date:2015-5-24编制Prepare by:过程责任Responsibility:IQC 修订日期:Modify Date:工厂批准plant approval :核心小组core team:1.如果客户有指定产品及过程特性符号,按客户要求标识;2.客户没有指定,则按如公司规定标识。