PFMEA分析表
PFMEA 分析表

4.定期保养真空过滤棉时进行检查。
4
12
参阅《SMT设备保养计划》
1◎ 相机识别不清
3
每日保养对镜片进行擦拭,防止灰层,板 屑污染镜片,每日点检1次。 参阅《SMT设备点检记录表》
100%自检, IPQC抽检1次/天
4
12
1. 检查FEEDER MARK点识别坐标
1.供料器动作不到位; 2.Feeder取料中心位置偏移.
1、作业前按照标准设置4±0.5kgf.cm;
1、首件确认;
3
2、设置后实际测量,实际扭力需与标准一 致;
2、100%自检; 3、IPQC:2H/次
2
42
3、首件确认螺丝锁后是否锁紧及滑牙
抽检;
烧录
程序没烧录进芯 片
产品功能测试 失败
7 ● 烧录时程序调用错误
1.烧录前工程确认软件,确认无误后需先 1、首件确认;
7 ◎ 升温过快,导致器件两端受 3 升温斜率),参阅《回流焊炉温设定表 检; 2、IPQC抽 3 63
热不均匀;
》;
检2H/次
7
◎
回流焊升温区时间设定过 长;
3
根据炉温曲线设定SOP来设定炉温曲线的 各个参数,并参照锡膏规格书。
100%1、100%自 检; 2、IPQC抽 检2H/次
3
63
7 ◎ 作业员漏失;
3
湿敏元件的贮存环境进行控制,如温度、 湿度。参阅《温湿管理规范》。
行实时稽查。
3 63
锡膏存储 钢网管控
1.存储温度按照锡膏规格参数控制;
锡膏印刷品质 不良
存贮锡膏的冰箱温度不满足 锡膏存储条件。
2
2.对冰箱温度进行监控点检,2次/天; (参阅《锡膏存储使用规范》)
注塑件过程失效模式及后果分析表模板(PFMEA)

6
包装破损
零件污染,客户投 诉
5
产品碰伤砸伤 客户投诉
6
装箱时确认不足 货物堆积过高
搬运不规范
2
无
3
试验后制定合理堆 积标准
2
无
100目测 100目测 100目测
5 60 5 75 4 48
标签贴错 发错货,客户投诉 5
标签与实物未核对 2
无
100目测
4 40
产品数量不正确
客户投诉
6
80-出货检验
关键尺寸超差
第 1 页,共 2 页
注塑件过程失效模式及后果分析表模板(PFMEA)
零件号
设计责任部门
FMEA 编号
零件名称
关键日期
编制人
车型/年份
系统/子系统/部件
编制日期
核心小组
序号
过程
潜在的失效模式
严 潜在的失效后果 重
度
级 别
潜在的失效原因/机理
频 度 数
现行预防性设计控 制
现行探测性设计控 制
探 测 度
5 60 5 75
建议措施
责任人和目标 完成日期
无
采取的措施
严频探 R 重度测 P 度数度 N
无
无
无
无
不同产品分区放置, 并做好标识
6
2 5 60
无
对纸箱进行固定 6 2 5 60
无
无
无
无
无
不同产品分区放置, 并做好标识
6
2 5 60
无
对纸箱进行固定 6 2 5 60
无
40-原材料烘料
烘料时间不对 烘料温度不对
表面料花 色差
pfmea分析表
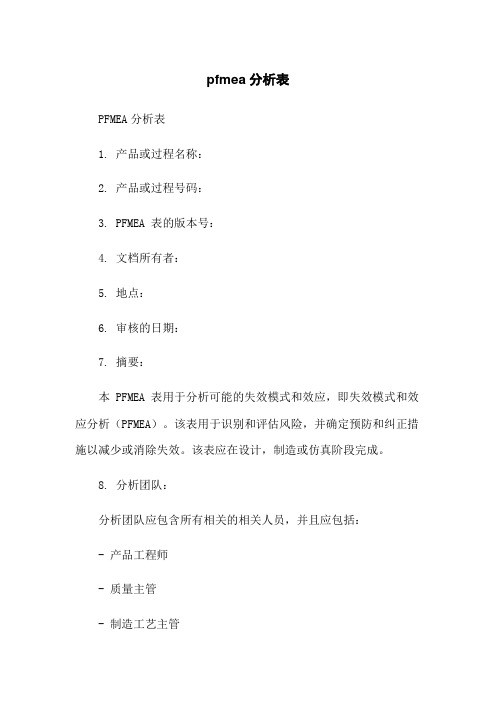
pfmea分析表PFMEA分析表1. 产品或过程名称:2. 产品或过程号码:3. PFMEA 表的版本号:4. 文档所有者:5. 地点:6. 审核的日期:7. 摘要:本 PFMEA 表用于分析可能的失效模式和效应,即失效模式和效应分析(PFMEA)。
该表用于识别和评估风险,并确定预防和纠正措施以减少或消除失效。
该表应在设计,制造或仿真阶段完成。
8. 分析团队:分析团队应包含所有相关的相关人员,并且应包括:- 产品工程师- 质量主管- 制造工艺主管- 安全主管- 故障分析师- 设计负责人- 制造工程师- 客户服务代表9. 步骤:步骤1:识别过程、组件或子组件- 识别过程、组件或子组件,该过程对产品性能,质量和可靠性的影响最大- 如果有多个过程,组件或子组件,请在单独的表中进行分析步骤2:确定失效模式- 对于每个识别的过程、组件或子组件,列出可能的失效模式步骤3:确定失效效应- 确定每种失效模式的影响,包括可能导致的产品或过程故障、风险和/或安全问题步骤4:确定失效严重性(S)- 确定失效对于产品功能和可靠性的影响严重性级别为S步骤5:确定失效发生概率(O)- 确定失效的发生概率级别为O步骤6:确定失效检出度(D)- 确定失效的检出度级别为D步骤7:计算风险优先级数(RPN)- 计算风险优先级数(RPN),即 RPN = S × O × D步骤8:制定预防和纠正措施- 针对高优先级数(RPN)的失效模式制定预防和纠正措施步骤9:跟踪措施有效性- 跟踪预防和纠正措施的实施,以确保其有效性。
10. 列举本文档所涉及简要注释如下:- 失效模式和效应分析(PFMEA):用于确定可能的失效模式和效应并采取纠正措施的过程。
- 风险优先级数(RPN): PFMEA 表中计算风险的指标。
RPN = S × O × D。
11. 列举如下本文档所涉及的法律名词及注释:无总结本文介绍了 PFMEA 分析表,该表用于识别和评估风险,并确定预防和纠正措施以减少或消除失效。
组装过程pfmea分析表
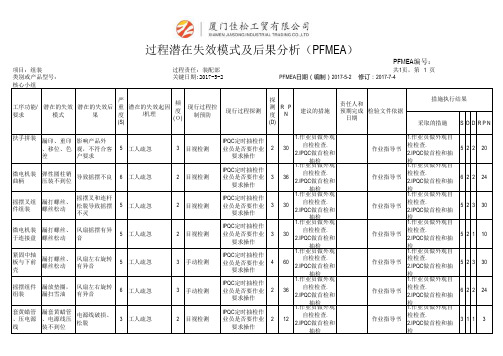
核心小组采取的措施S O D R P N扶手拼装漏印、重印、移位、色差影响产品外观,不符合客户要求5工人疏忽3目视检测IPQC定时抽检作业员是否要作业要求操作2301.作业员做外观自检检查.2.IPQC做首检和抽检作业指导书1.作业员做外观自检检查.2.IPQC做首检和抽检52220微电机装曲柄弹性圆柱销压装不到位导致摇摆不良6工人疏忽2目视检测IPQC定时抽检作业员是否要作业要求操作3361.作业员做外观自检检查.2.IPQC做首检和抽检作业指导书1.作业员做外观自检检查.2.IPQC做首检和抽检62224摇摆叉组件组装漏打螺丝、螺丝松动摇摆叉和连杆松脱导致摇摆不灵5工人疏忽2目视检测IPQC定时抽检作业员是否要作业要求操作3301.作业员做外观自检检查.2.IPQC做首检和抽检作业指导书1.作业员做外观自检检查.2.IPQC做首检和抽检52330微电机装于连接盘漏打螺丝、螺丝松动风扇摇摆有异音5工人疏忽2目视检测IPQC定时抽检作业员是否要作业要求操作3301.作业员做外观自检检查.2.IPQC做首检和抽检作业指导书1.作业员做外观自检检查.2.IPQC做首检和抽检52110紧固中轴板与下前壳漏打螺丝、螺丝松动风扇左右旋转有异音5工人疏忽3手动检测IPQC定时抽检作业员是否要作业要求操作4601.作业员做外观自检检查.2.IPQC做首检和抽检作业指导书1.作业员做外观自检检查.2.IPQC做首检和抽检52330摇摆组件组装漏放垫圈,漏扫雪油风扇左右旋转有异音6工人疏忽3手动检测IPQC定时抽检作业员是否要作业要求操作2361.作业员做外观自检检查.2.IPQC做首检和抽检作业指导书1.作业员做外观自检检查.2.IPQC做首检和抽检62224套黄蜡管、压电源线漏套黄蜡管、电源线压装不到位电源线破损、松脱3工人疏忽2目视检测IPQC定时抽检作业员是否要作业要求操作2121.作业员做外观自检检查.2.IPQC做首检和抽检作业指导书1.作业员做外观自检检查.2.IPQC做首检和抽检3113责任人和预期完成日期检验文件依据频度(O)现行过程控制预防现行过程探测探测度(D)R PN建议的措施类别或产品型号:关键日期:2017-5-2PFMEA日期(编制)2017-5-2 修订:2017-7-4措施执行结果工序功能/要求潜在的失效模式潜在的失效后果严重度(S)潜在的失效起因/机理过程潜在失效模式及后果分析(PFMEA)PFMEA编号:项目:组装过程责任:装配部共1页,第 1 页。
PFMEA评分表

PFMEA评分表PFMEA评分表》是一种常用的品质管理工具,用于进行潜在失效模式与效应分析(Process Failure Mode and Effects Analysis,简称PFMEA)。
它的目的是识别关键步骤或流程中的潜在失效模式,并评估其对产品或服务质量的影响程度。
PFMEA评分表可以帮助团队全面分析和评估可能发生的失效模式,并制定适当的预防和纠正措施,从而最大程度地降低产品或服务质量风险。
通过对各种失效模式和其效应的评估,可以提前发现潜在问题并采取相应的控制措施,以确保产品或服务质量的稳定和可靠。
在PFMEA评分表中,各个步骤或流程会被列出,并根据其对产品或服务的潜在失效的重要程度进行评分。
评分标准可以根据具体情况进行制定,但通常包括失效模式的严重性、发生频率和检测能力等方面的考量。
评分结果可以帮助团队确定哪些步骤或流程需要重点关注和改进,从而优化生产或服务流程,提高质量稳定性。
综上所述,《PFMEA评分表》是一种重要的品质管理工具,用于识别和评估潜在的失效模式,以确保产品或服务质量的稳定和可靠。
PFMEA评分表是一种用于进行过程故障模式与影响分析的工具。
它由以下几个组成部分构成,并且包含一些必填项。
1.项目信息在评分表的顶部,需要填写一些项目信息,以便对分析的过程进行标识和跟踪。
这些信息可能包括项目名称、项目编号、评分表编制人员等。
2.设计和工艺流程步骤在评分表中,需要列出与该过程相关的设计和工艺流程步骤。
这些步骤可以按照顺序进行排列,并且需要明确指出每个步骤的名称和内容。
3.故障模式与影响分析针对每个设计和工艺流程步骤,需要进行故障模式与影响分析。
这部分需要列出可能的故障模式,并对其进行评估。
评估可以基于指标如严重性、发生频率和可探测性等进行。
4.推理控制计划在评分表中,需要制定推理控制计划,以预防或控制故障模式对产品或过程的影响。
这部分需要明确列出控制措施、控制方式以及执行者。
2019新版PFMEA表格

1.对于上一较高级 别要素和/或终端 用户的失效影响
(FE)
失效 影响 的严 重度 (S)
ห้องสมุดไป่ตู้
2.关注要素的失效 模式(FM)
步骤四)
PFMEA风险分析(步骤五)
3.工作要素的失效 原因(FC)
当前的对失效起因 的预防措施(PC)
失效起 因的发 生频度 (O)
当前的失效起因/ 失效模式的探测措
施(DC)
素名称
3.过程工作要素 4M
1.过程名称的功能 系统、子系统、零 件要素或过程的功
能
项目: PFMEA开始日期: PFMEA修订日期:
跨职能团队:
PFMEA编号 : 过程负责人:
保密级别:
功能分析(步骤三)
失效分析(步骤四)
2.过程步骤的功能 和产品特性
(量值为可选项)
3.过程工作要素的 功能和过程特性
工作要素的失效原因fc当前的对失效起因的预防措施pc失效起因的发生频度o当前针对失效模式的探测措施dc失效分析步骤四pfmea风险分析步骤五当前针对失效起因的探测措施dc失效起因失效模式的探测度dpfmea措施优先级ap特殊特性筛选器代码可选预防措施探测措施责任人目标完成日期pfmea风险分析步骤五pfmea优化步骤六状态采取基于证据的措施完成日期严重度s发生度o探测度dap特殊特性备注pfmea优化步骤六公司名称
过程失效模式及影响分析(过程FMEA)
规划和准备(步骤一)
公司名称: 工厂地点: 顾客名称: 车型/平台:
持续改进
结构分析(步骤二)
PFMEA开始日期: PFMEA修订日期:
功能分析(步骤三
问 历史/变更 1.过程项目
2.过程步骤
新版PFMEA表格
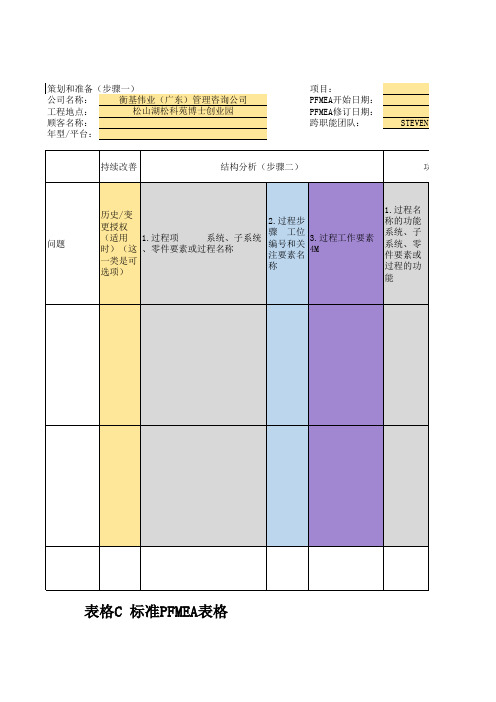
失效分析(步骤四)
PFMEA风险
2.过程步骤的功 能和产品特性 (量值为可选 项)
3.过程工 作要素的 功能和过 程特性
1.对于上
一较高级
2.关注
别要素和/ 失效影响的 要素的 3.工作要素的失效起因
或终端用 严重度(s) 失效模 (FC)
户的失效
式(FM)
影响(FE)
当前的 对失效 起因的 预防措 施(PC)
选)
施
A优化(步骤六)
频度 (O)
探测 度 (D)
DFME A措 施优 先级
筛选器代 码(可 备注 选)
策划和准备(步骤一)
公司名称:
衡基伟业(广东)管理咨询公司
工程地点:
松山湖松科苑博士创业园
顾客名称:
年型/平台:
项目: PFMEA开始日期: PFMEA修订日期: 跨职能团队:
STEVEN 13929414846
持续改善
结构分析(步骤二)
功能分析(步骤三
问题
历史/变
更授权
(适用 1.过程项
系统、子系统
时)(这 、零件要素或过程名称
一类是可
选项)
2.过程步
骤 工位 编号和关 注要素名
3.过程工作要素 4M
称
1.过程名 称的功能 系统、子 系统、零 件要素或 过程的功 能
表格C 标准PFMEA表格
STEVEN 13929414846 功能分析(步骤三)
过程失效模式及影响分析(过程FMEA)
PFMEA ID编号: 过程责任人: 保密级别: 加微信免费送案例及DFM分析(步骤五)
PFMEA优化(步骤六)
当前的
失效起 失效起
因/失效 模式的 频度
制程PFMEA分析表格
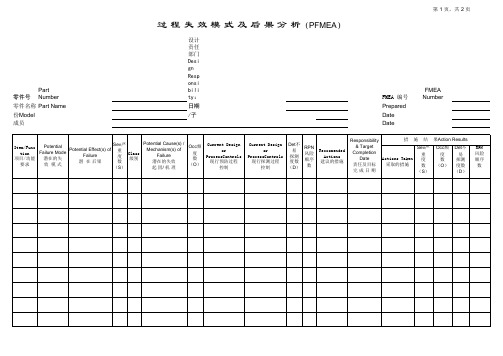
Occ频 度 数
(O)
Current Design or
ProcessControls 现行预防过程 控制
Current Design or
ProcessControls 现行探测过程 控制
Det不
易 探测 度数 (D)
RPN 风险 顺序 数
Reccomended Actions
建议的措施
Responsibility
措 施 结 果Action Results
& Target Completion
Date 责任及目标 完成日期
Actions Taken 采取的措施
Sev严 重 度 数
(S)
Occ频 度 数
(O)
Det不 易 探测 度数
(D)
RPN 风险 顺序
数
Part 零件号 Number
建议的措施
Responsibility
措 施 结 果Action Results
& Target Completion
Date 责任及目标 完成日期
Actions Taken 采取的措施
Sev严 重 度 数
(S)
Occ频 度 数
(O)
Det不 易 探测 度数
(D)
RPN 风险 顺序
数
FMEA Number
Item/Func tion
项目/功能 要求
Potential
Failure Mode 潜在的失 效 模式
Sev严
Potential Effect(s) of Failure
潜 在 后果
重 度 数
Class 级别
AIAG VDA PFMEA表格模板(自动计算AP)

1.对于上 一较高级 别要素和/ 或最终用 户的失效 影响 (FE)
失效 影响 2.关注要 的严 素的失效 重度 模式 (FM) (S)
3.下一较 低级别要 素或特性 的失效原 因 (FC)
对失效原 因的当前 预防控制
(PC)
失效 原因 的发 生度 (O)
对失效原 因 / 失效 模式的当 前探测控 制 (DC)
失效分析 (第4步)
PFMEA 风险分析 (第5步)
PFMEA 优化 (第6步)
问题#
1.过程项
历史/变 更授权 系统、子系 (适用时) 统、零件要
素或过程名 称
2.过程步 骤
工位编号和 关注要素名
称
3.过程工 作要素
4M类型
1.过程 名称的 功能
系统、子 系统、零 件要素或 过程的功
2.过程步 骤的功能 和产品特
PFMEA 优化 (第6步)
问题#
1.过程项
历史/变 更授权 系统、子系 (适用时) 统、零件要
素或过程名 称
2.过程步 骤
工位编号和 关注要素名
称
3.过程工 作要素
4M类型
1.过程 名称的 功能
系统、子 系统、零 件要素或 过程的功
2.过程步 骤的功能 和产品特
性
(量值为可 选项)
3.过程 工作要 素的功 能和过 程特性
(PC)
失效 原因 的发 生度 (O)
对失效原 因 / 失效 模式的当 前探测控 制 (DC)
失效原 因/失 效模式 的探测 度 (D)
AP
特殊 特性
筛选器 代码(选
填)
PFMEA 预防措
施
PFMEA 探测措
施
过程失效模式及后果分析(PFMEA)
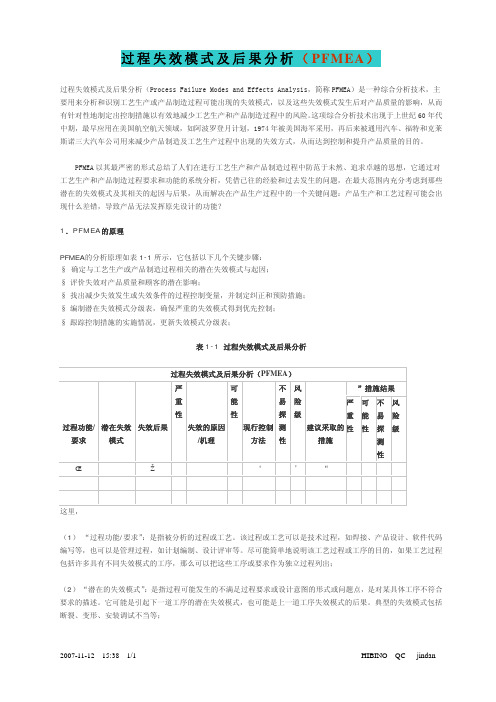
过程失效模式及后果分析(PFMEA)过程失效模式及后果分析(Process Failure Modes and Effects Analysis,简称PFMEA)是一种综合分析技术,主要用来分析和识别工艺生产或产品制造过程可能出现的失效模式,以及这些失效模式发生后对产品质量的影响,从而有针对性地制定出控制措施以有效地减少工艺生产和产品制造过程中的风险。
这项综合分析技术出现于上世纪60年代中期,最早应用在美国航空航天领域,如阿波罗登月计划,1974年被美国海军采用,再后来被通用汽车、福特和克莱斯诺三大汽车公司用来减少产品制造及工艺生产过程中出现的失效方式,从而达到控制和提升产品质量的目的。
PFMEA以其最严密的形式总结了人们在进行工艺生产和产品制造过程中防范于未然、追求卓越的思想,它通过对工艺生产和产品制造过程要求和功能的系统分析,凭借已往的经验和过去发生的问题,在最大范围内充分考虑到那些潜在的失效模式及其相关的起因与后果,从而解决在产品生产过程中的一个关键问题:产品生产和工艺过程可能会出现什么差错,导致产品无法发挥原先设计的功能?1.PFMEA的原理PFMEA的分析原理如表1-1所示,它包括以下几个关键步骤:§确定与工艺生产或产品制造过程相关的潜在失效模式与起因;§评价失效对产品质量和顾客的潜在影响;§找出减少失效发生或失效条件的过程控制变量,并制定纠正和预防措施;§编制潜在失效模式分级表,确保严重的失效模式得到优先控制;§跟踪控制措施的实施情况,更新失效模式分级表;表1-1 过程失效模式及后果分析过程失效模式及后果分析(PFMEA)”措施结果过程功能/要求潜在失效模式失效后果严重性失效的原因/机理可能性现行控制方法不易探测性风险级建议采取的措施严重性可能性不易探测性风险级ŒŽ‘ ’“这里,(1)“过程功能/要求”:是指被分析的过程或工艺。
该过程或工艺可以是技术过程,如焊接、产品设计、软件代码编写等,也可以是管理过程,如计划编制、设计评审等。
PFMEA分析标准表格模版

(过程PROCESS FMEA)
项目名称 Item: 主要参加人Core Team: 序号 NO. 过程功能要求 潜在的失效后果 潜在的失效模式 Process Function Potential Effect(S) of Potential Failure Mode Requirements Failure 严 级 重 别 度 Class Sev 潜在的失效原因/机理 Potential Cause(s)/ Mechanism(s) of Failure 频 现行过程预防控制 度 Current Process Controls 数 Prevention Occ 过程责任部门Process Responsibility: 关键日期Key Date:
准备人PrepareBiblioteka by审核Checked by
批准Approval by
1 of 1
工
现行过程检测控制 Current Process Controls Detection
措施结果Result 严 频 难 重 度 检 度 数 度 Sev Occ Det
风险 优先 指数 R.P.N.
out of 0.2 A spec.
偏小
版本 Rev. A0
变更内容Comment 新制/New
日期 Date
AND EFFECTS ANALYSIS
FMEA编号Number: 准备人Prepared By: FMEA日期Data(编制(orig): 责任及目标完 难 风险 建议的措施 成日期 检 优先 指数 Recommended Responsibility 度 Action(S) & Target Det R.P.N . Completion 页码Page:
3-1 PFMEA 表格-P16

探测措施
失效起因的频度(O)
过程FMEA措施优先级 特殊特性
筛选器代码(可选) 预防措施
负责人姓名 目标完成日期
状态 采取基于证据的措施
完成日期 (S)严重度 (O)发生度 (D) 探测度 特殊特性 措施优先级
备注
PFMEA 优化(步骤六)
过程失效模式及影响分析(PFMEA)表格
过程 FMEA 风险分析 (步骤五)
压装机
过程失效模式及影响分析(PFMEA)表格
功能分析 (步骤三)
1. 过程项的功能系统、 子系统、零件要素或过程 的功能
2. 过程步骤的功能和产 品特性(量值为可选)
3. 过程工作要素的功能 和过程特性
您的工厂:
运至工厂: 最终用户:
过程失效模式及影响分析(PFMEA)表格
功能分析 (步骤三)
最终用户:
升起和降下车窗
过程失效模式及影响分析(PFMEA)表格
失效分析(步骤四)
1.对于上一较高级别要素和/或最终用户 的失效影响(FE)
2.关注要素的失效模式(FM) 3.工作要素的失效原因(FC)
1.失效影响
2.过程步骤的失效模式 3.工作要素的失效原因(FC)
您的工厂: 发运至工厂: 最终用户:
1. 过程项的功能系统、 子系统、零件要素或过程 的功能
2. 过程步骤的功能和产 品特性(量值为可选)
3. 过程工作要素的功能 和过程特性
您的工厂:
将轴安装至电机壳总成内 发运至工厂: 将电机安装至车门上
压装烧结轴承,在每次压 装时实现 电机壳内的轴 向定位保留最大间隙
机器将烧结轴承压入电机 壳,实现轴向定位
PFMEAID编号:
顾客名称:
PFMEA分析表
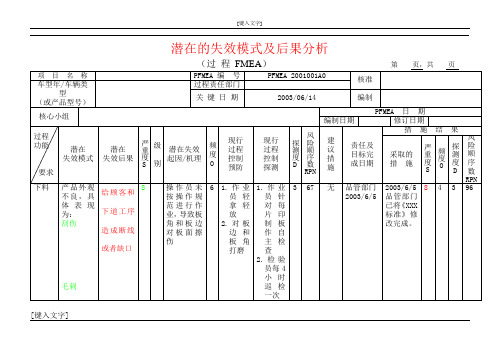
120
无
PP-705-2-01A0
XXX 有 限 公 司
过 程 F M E A 检 查 表
制定部门: 制定日期: 年 月 日
产品名称
规格/型号
顾客零件编号
问 题
是
否
所要求的意见 / 措施
负责部门/负责人
完成日期
1
是否使用克莱斯勒、福特和通用汽车公司的指南制定过程ห้องสมุดไป่ตู้MEA
2
所有影响配合、功能、耐久性、政府法规和安全性的操作是否已被识别并按顺序列出
潜在的失效模式及后果分析
(过程FMEA)第页,共页
项 目 名 称
PFMEA 编 号
PFMEA2001001A0
核准
车型年/车辆类型
(或产品型号)
过程责任部门
关 键 日 期
2003/06/14
编制
核心小组
PFMEA 日 期
编制日期
修订日期
过程
功能
要求
潜在
失效模式
潜在
失效后果
严
重
度
S
级
别
潜在失效
起因/机理
频
度
O
现行
过程
控制
预防
现行
过程
控制
探测
探测
度
D
风险
顺序
数RPN
建 议
措 施
责任及
目标完
成日期
措 施 结 果
采取的
措 施
严
重
度
S
频
度
O
探测
度
D
风险
顺序数
RPN
下料
产品外观不良,具体表现为:
FMEA分析量化评定参照表(失效模式分析)
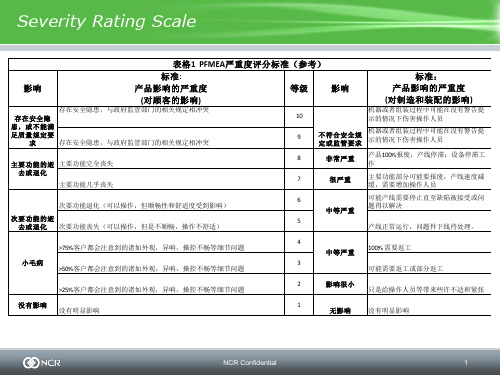
存在安全隐患,与政府监管部门的相关规定相冲突 存在安全隐 患,或不能满 足质量规定要 求 存在安全隐患,与政府监管部门的相关规定相冲突 主要功能的逝 主要功能完全丧失 去或退化 主要功能几乎丧失 次要功能退化(可以操作,但顺畅性和舒适度受到影响) 次要功能的逝 去或退化 次要功能丧失(可以操作,但是不顺畅,操作不舒适) >75%客户都会注意到的诸如外观,异响,操控不畅等细节问题 小毛病 >50%客户都会注意到的诸如外观,异响,操控不畅等细节问题 >25%客户都会注意到的诸如外观,异响,操控不畅等细节问题 没有影响 没有明显影响
5
中等水平
过程中监测
4
中等偏上
源头处监测
3
高
有部分防错手段
自动控制装置能自动检测到即将发生的失效并避免错误的发生
2
很高
有防错,不需要监测
夹具,机器或者产品设计本身具有放错功能,能够完全规避制作过程中可 能发生的失效
1
必然的(能被发 现)
NCR Confidential
3
Severity Rating Scale
表格 1 PFMEA 严重度评分标准(参考) 标准 : 产品影响的严重度 等级 影响 (对顾客的影响 )
10 9 8 7 6 中等严重 5 4 中等严重 3 2 1 影响很小
影响
标准: 产品影响的严重度 (对制造和装配的影响 )
机器或者组装过程中可能在没有警告提 示的情况下伤害操作人员
等级 10 9 8 7 6 5 4 3 2
1
NCR Confidential
2
Detection Rating Scale
可探测性表格
探测机会
没有机会探测到 任何阶段都好像不容 易探测到 问题探测总是滞后
PFMEA模板

PFMEA
修订次数版本修订人日期修改内容表单编号:
年份/平台
1.过程项
2.过程步骤
3.过程作业要素 1.过程项功能2.过程步骤的功
能和产品特性
3.过程作业要素的功能和过
程特性
1.失效影响FE
严重度
(S)
作业步骤的失效模
式
(FM)
作业要素的失效原因
(FC)
现行预防控制(PC)发生度(O)现行探测控制(DC)探测度(D)AP特殊特性预防控制探测措施责任人
目标完成
时间
状态
采取基于证据
的措施
实际完成
时间
S O D特殊特性AP备注
风险评估(第5步)改进措施(第6步)
失效分析(第4步)
结构分析(第2步)功能分析(第3步)
PFMEA 策划准备(第1步)
公司名称:项目:制造地址:PFMEA开始日期:顾客名称:PFMEA修订日期:
跨职能团队:。
PFMEA第五版表格模板 自己整理(带实例)--2020.2.3
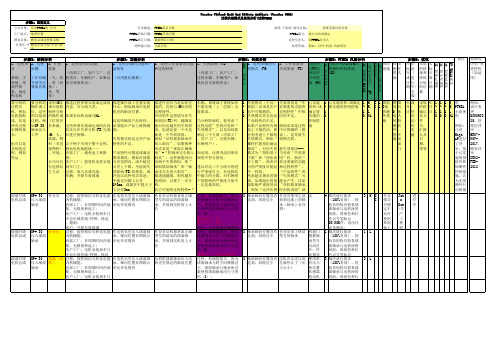
工厂地点: 地理位置
顾客名称: 顾客名或过程族名称 车型年/平 顾客车型年型/平台/款
台: 型
任务描述: PFMEA项目名称 PFMEA开始日期: PFMEA开始日期 PFMEA修订日期: 最新修订日期
跨职能小组: 小组名单
Process Failure Mode and Effects Analysis (Process FMEA) 过程失效模式及效果分析(过程FMEA)
# 批次放行要求
3 H C 作业 Joh 进
电机总成 压入球面
为机械能;
承,轴向位置在图纸公 型号的清洁的球面轴 球面轴承与转子间摩擦过 达到,间距过小 掉到过地上的轴
(100%有效),检
C 指导 n
行
轴承
内部工厂:在周期时间内装 差允许范围内
承,并放到压机的上止 大,球面轴承与轴承座过
承(轴承上有异
验员用检具检查球
书规 Doe 中
配,无报废和返工;
位
紧使得球面轴承内尺寸变
物)
面轴承与电机座的
定不 (生
客户工厂:电机安装到车门Fra bibliotek形(8);
间距,用绿色和红
允许 产
不会出现停线/停顿、拣选
内部工厂:无
色记号笔标记
使用 工
、遏制;
客户工厂:无;
OK/NOK件,再由作
掉到 程
用户:升降车窗玻璃
用户:车窗玻璃升降困难
为无需
0~3mm,或最多不能大于 析。
一定是最高的。
级影响严重度的话 “从料箱拿轴承
额外行
上公差3mm
其它可能的过程特性-“
制程PFMEA分析表格

第 1 页,共 1 页
FMEA 编号 FMEA Number 编制Prepared by: 编制日期Date (Orig.): 修订日期Date (Rev.):
Item/Func tion
项目/功能 要求
Potential
Failure Mode 潜在的失 效 模式
Sev严
Potential Effect(s) of Failure
Sev严 重 度 数
(S)
Occ频 度 数
(O)
Det不 易Βιβλιοθήκη 探测 度数(D)RPN 风险 顺序
数
潜 在 后果
重 度 数
Class 级别
(S)
Potential Cause(s) / Mechanism(s) of
Failure 潜在的失效 起 因/ 机 理
Occ频 度 数
(O)
Current Design or
ProcessControls 现行预防过程 控制
Current Design or
零件号 Part Number 零件名称 Part Name 车型/年份Model Year(s)/Vehicle(s) 核心小组成员Core Team Member
过 程 失 效 模 式 及 后 果 分 析(PFMEA)
设计责任部门Design Responsibility: 关键日期Key Date: 系统/子系统/部件System/Subsystem/Component
ProcessControls 现行探测过程 控制
Det不 易 探测 度数
(D)
RPN 风险 顺序 数
Reccomended Actions
建议的措施
Responsibility
塑料注塑成型PFMEA分析

等)N
度度度
射出机料管4定期清理料管模具日常保1次/30分464机台尽可能固定颜色生管/注塑
有黑斑养生产
缩水4保压过小2依照标准成型成型条件每批216
条件表点检表
8保压过小2依照标准成型成型条件每批232
条件表点检表
胶芯穿孔4模具灌点2零件寿命管制成型条件每批216
过大点检表
8模具灌点2零件寿命管制成型条件每批232
过大点检表
■
包装
混料6
未按照标准
作
2
依照制造通知
单填写
224标签贴错6
未按照标准
作业
2
依照制造通知
单填写
224功能丧失
无法组装
无法组装
外观不良
功能丧失
外观不良。
- 1、下载文档前请自行甄别文档内容的完整性,平台不提供额外的编辑、内容补充、找答案等附加服务。
- 2、"仅部分预览"的文档,不可在线预览部分如存在完整性等问题,可反馈申请退款(可完整预览的文档不适用该条件!)。
- 3、如文档侵犯您的权益,请联系客服反馈,我们会尽快为您处理(人工客服工作时间:9:00-18:30)。
PFMEA分析表表单编号JZQ/QR703-42-A第页共页项目名称房山北延线PFMEA 编号JZQ-PF2017-002核准产品型号制动连接板座(BDZ07-110-003) 过程责任部门生产部关键日期编制核心小组张锦房立成郑芝龙周永锋李钧冯海彪张安富PFMEA 日期编制日期2015.12.11 修订日期2015.12.12过程功能要求潜在失效模式潜在失效后果严重度S级别潜在失效起因/机理频度O现行过程控制预防现行过程控制探测探测度D风险顺序数RPN建议措施责任及目标完成日期措施结果采取的措施严重度S频度O探测度D风险顺序数RPN1.原材料检验对原材料进行化学元素检验材料不符合要求产品不合格10 Z原材料供应商供货错误1检验员检验5 50无原材料内部存在缺陷1 5 102.下料下料尺寸Φ80X140±1毫米下料尺寸>Φ80X141造成材料浪费2作业员操作不规范4严格按工艺要求操作作业员自检,检验员巡检6 48无检测量具精度不够1检测量具周期检定计划5 10检测量具的检定周期过期1 5 10下料尺寸<Φ80X139造成锻件报废7 Z作业员操作不规范4严格按工艺要求操作作业员自检,检验员巡检6 1681.加强检查频次;2.加强人员培训锻造车间每次下料操作人员必须仔细测量下料尺寸7 1 3 21检测量具精度不够1检测量具周期检定计划5 35 无PFMEA分析表表单编号JZQ/QR703-42-A第页共页检测量具的检定周期过期1 5 353.锻造1.1加热温度1150-1180℃温度>1180℃过烧、晶粒度粗大7 Z作业员操作不规范5严格按工艺要求操作作业员自检,检验员巡检6 210严格按照工艺要求进行操作,控制加热温度锻造车间严格按照工艺要求,控制加热温度7 2 3 42加热炉仪表损坏3定期对仪表进行维护作业员日常点检5 105加强检验频次锻造车间班前对仪表要仔细检验7 2 3 42温度<1150℃锻打不易成型7Z作业员操作不规范5严格按工艺要求操作作业员自检,检验员巡检6 210严格按照工艺要求进行操作,控制加热温度锻造车间严格按照工艺要求,控制加热温度7 2 3 42加热炉仪表损坏3定期对仪表进行维护作业员日常点检5 105加强检验频次锻造车间班前对仪表要仔细检验7 2 3 42锻件报废8作业员操作不规范5严格按工艺要求操作作业员自检,检验员巡检6 240严格按照工艺要求进行操作,控制加热温度锻造车间严格按照工艺要求,控制加热温度7 2 3 42加热炉仪表损坏3定期对仪表进行维护作业员日常点检5 105加强检验频次锻造车间班前对仪表要仔细检验7 2 3 421.2锻造温度850-1180℃温度>1180℃过烧、晶粒度粗大7 Z作业员操作不规范5严格按工艺要求操作作业员自检,检验员巡检6 210严格按照工艺要求进行操作,控制加热温度锻造车间严格按照工艺要求,控制加热温度7 2 3 42加热炉仪表损坏3定期对仪表进行维护作业员日常点检5 105加强检验频次锻造车间班前对仪表要仔细检验7 2 3 42温度<850℃锻打不易成型7Z作业员操作不规范5严格按工艺要求操作作业员自检,检验员巡检6 210严格按照工艺要求进行操作,控制加热温度锻造车间严格按照工艺要求,控制加热温度7 2 3 42加热炉仪表损坏3定期对仪表进行维护作业员日常点检5 105加强检验频次锻造车间班前对仪表要仔细检验7 2 3 42锻件报废8作业员操作不规范5严格按工艺要求操作作业员自检,检验员巡检6 240严格按照工艺要求进行操作,控制加热温度锻造车间严格按照工艺要求,控制加热温度7 2 3 42PFMEA分析表表单编号JZQ/QR703-42-A第页共页加热炉仪表损坏3定期对仪表进行维护作业员日常点检5 105加强检验频次锻造车间班前对仪表要仔细检验7 2 3 422外观不得有欠肉、凹陷、氧化膜锻件有欠肉、凹陷、氧化膜影响后续加工2作业员操作不规范5严格按工艺要求操作作业员自检,检验员巡检6 60 无锻件报废8 Z作业员操作不规范5严格按工艺要求操作6 240加强人员培训锻造车间对操作人员进行培训,提高技能8 2 3 483.锻件不得裂痕锻件有裂痕锻件报废8 Z模具损坏 4模具周期验证作业员自检,检验员巡检6 192加强检验频次锻造车间班前及班后要仔细检验模具8 2 3 48模具设计不合理4模具入厂验证检验员入厂检验6 192设计人员更改设计方案锻造车间模具入厂使用前仔细检验8 2 3 485.控制锻件尺寸133+453+264+4128+344+40尺寸>137后续加工余量大3模具损坏 5 作业员自检,检验员巡检6 90无模具加工尺寸错误3 6 54尺寸<133后续加工余量不足7 Z模具损坏 5作业员自检,检验员巡检6 210加强检验频次锻造车间班前及班后要仔细检验模具8 2 3 48模具加工尺寸错误3 6 126加强模具验收标准,加强人员培训锻造车间对模具验收人员进行培训,提高技能8 2 3 48 尺寸>55后续加工余量大3模具损坏 5 作业员自检,检验员巡检6 90无模具加工尺寸错误3 6 54尺寸<53后续加工余量不足7 Z模具损坏 5作业员自检,检验员巡检6 210加强检验频次锻造车间班前及班后要仔细检验模具8 2 3 48模具加工尺寸错误3 6 126加强模具验收标准,加强人员培训锻造车间对模具验收人员进行培训,提高技能8 2 3 48 尺寸>68后续加工余量大3模具损坏 5作业员自检,检验员巡检6 90 无模具加工尺寸错误3 6 54尺寸<64后续加工余量不足7 Z 模具损坏 5作业员自检,检验员巡检6 210加强检验频次锻造车间班前及班后要仔细检验模具8 2 3 48PFMEA分析表表单编号JZQ/QR703-42-A第页共页模具加工尺寸错误3 6 126加强模具验收标准,加强人员培训锻造车间对模具验收人员进行培训,提高技能8 2 3 48尺寸>133 后续加工余量大3模具损坏 5作业员自检,检验员巡检6 90 无模具加工尺寸错误3 6 54尺寸<128 后续加工余量不足7 Z模具损坏 5作业员自检,检验员巡检6 210加强检验频次锻造车间班前及班后要仔细检验模具8 2 3 48模具加工尺寸错误3 6 126加强模具验收标准,加强人员培训锻造车间对模具验收人员进行培训,提高技能8 2 3 48尺寸>48 后续加工余量大3模具损坏 5作业员自检,检验员巡检6 90 无模具加工尺寸错误3 6 54尺寸<44 后续加工余量不足7 Z模具损坏 5作业员自检,检验员巡检6 210加强检验频次锻造车间班前及班后要仔细检验模具8 2 3 48模具加工尺寸错误3 6 126加强模具验收标准,加强人员培训锻造车间对模具验收人员进行培训,提高技能8 2 3 484热处理1.晶粒度≥5级晶粒度<5级产品报废8 Z作业员操作不规范5严格按工艺要求操作金相检验 6 240加强人员培训热处理车间对热处理操作人员进行培训,提高技能8 3 3 72原材料不合格3 6 144加强原材料进厂检验质量部对原材料检验人员进行培训,提高技能8 3 3 722.σs≥345MPaσs<345MPa产品报废作业员操作不规范5严格按工艺要求操作机械性能检验6 240加强人员培训热处理车间对热处理操作人员进行培训,提高技能8 3 3 72原材料不合格3 6 144加强原材料进厂检验质量部对原材料检验人员进行培训,提高技能8 3 3 72PFMEA分析表表单编号JZQ/QR703-42-A第页共页3.σb ≥520MPaσb<520MPa产品报废作业员操作不规范5严格按工艺要求操作6 240加强人员培训加强原材料进厂检验热处理车间对热处理操作人员进行培训,提高技能8 3 3 72原材料不合格3 6 144 质量部对原材料检验人员进行培训,提高技能8 3 3 724.δs≥21% δs<21% 产品报废作业员操作不规范5严格按工艺要求操作6 240加强人员培训加强原材料进厂检验热处理车间对热处理操作人员进行培训,提高技能8 3 3 72原材料不合格3 6 144 质量部对原材料检验人员进行培训,提高技能8 3 3 725. AKU≥34J AKU<34J 产品报废作业员操作不规范5严格按工艺要求操作6 240加强人员培训加强原材料进厂检验热处理车间对热处理操作人员进行培训,提高技能8 3 3 72原材料不合格3 6 144 质量部对原材料检验人员进行培训,提高技能8 3 3 725.抛丸表面无氧化皮,喷丸均匀表面残留氧化皮影响后续加工2作业员操作不规范5严格按工艺要求操作作业员自检,检验员巡检6 60无机器故障 3 6 36 喷丸不均匀影响产品外观作业员操作不规范5严格按工艺要求操作6 60无机器故障 3 6 366.机加工1立铣上下面,控制尺寸60±0.2尺寸>60.2余量过大,影响后续加工3作业员操作不规范4严格按工艺要求操作作业员自检,检验员巡检6 72无加工设备精度不够3 6 54检测量具精度不够1检测量具周期检定计划6 18检测量具的检定周期过期1检测量具周期检定计划6 18PFMEA分析表表单编号JZQ/QR703-42-A第页共页尺寸<59.8 产品报废7 Z 作业员操作不规范4严格按工艺要求操作作业员自检,检验员巡检6 168加强人员培训生产车间对操作人员进行培训,提高技能7 3 3 63加工设备精度不够3 6 126加强检验频次,加强人员培训生产车间每月对设备记性一次检查,对维修人员进行培训,提高技能7 3 3 63检测量具精度不够1检测量具周期检定计划6 42无检测量具的检定周期过期1检测量具周期检定计划6 422.立铣D端面,控制尺寸52 尺寸>52.3余量过大,影响后续加工3作业员操作不规范4严格按工艺要求操作作业员自检,检验员巡检6 72 无加工设备精度不够3 6 54检测量具精度不够1检测量具周期检定计划6 18检测量具的检定周期过期1检测量具周期检定计划6 18尺寸<51.7 产品报废7 Z作业员操作不规范4严格按工艺要求操作作业员自检,检验员巡检6 168加强人员培训生产车间对操作人员进行培训,提高技能7 3 3 63加工设备精度不够3 6 126加强检验频次,加强人员培训生产车间每月对设备记性一次检查,对维修人员进行培训,提高技能7 3 3 63检测量具精度不够1检测量具周期检定计划6 42 无检测量具的检定周期过期1检测量具周期检定计划6 423.卧铣D、E端面,控制尺寸129±尺寸>129.2余量过大,影响后续加工3作业员操作不规范4严格按工艺要求操作作业员自检,检验员巡检6 72 无PFMEA分析表表单编号JZQ/QR703-42-A第页共页0.2 加工设备精度不够3 6 54检测量具精度不够1检测量具周期检定计划6 18检测量具的检定周期过期1检测量具周期检定计划6 18尺寸<127.8 产品报废7 Z 作业员操作不规范4严格按工艺要求操作作业员自检,检验员巡检6 168加强人员培训生产车间对操作人员进行培训,提高技能7 3 3 63加工设备精度不够3 6 126加强检验频次,加强人员培训生产车间每月对设备记性一次检查,对维修人员进行培训,提高技能7 3 3 63检测量具精度不够1检测量具周期检定计划6 42 无检测量具的检定周期过期1检测量具周期检定计划6 423.数铣成型一,控制尺寸124、35、40、41.5 尺寸>124.3余量过大,影响后续加工3作业员操作不规范4严格按工艺要求操作作业员自检,检验员巡检6 72 无加工设备精度不够3 6 54检测量具精度不够1检测量具周期检定计划6 18检测量具的检定周期过期1检测量具周期检定计划6 18尺寸<123.7 产品报废7 Z作业员操作不规范4严格按工艺要求操作作业员自检,检验员巡检6 168加强人员培训生产车间对操作人员进行培训,提高技能7 3 3 63加工设备精度不够3 6 126加强检验频次,加强人员培训生产车间每月对设备记性一次检查,对维修人员进行培训,提高技能7 3 3 63PFMEA分析表表单编号JZQ/QR703-42-A第页共页检测量具精度不够1检测量具周期检定计划6 42 无检测量具的检定周期过期1检测量具周期检定计划6 42尺寸>35.3 余量过大,影响后续加工3作业员操作不规范4严格按工艺要求操作作业员自检,检验员巡检6 72 无加工设备精度不够3 6 54检测量具精度不够1检测量具周期检定计划6 18检测量具的检定周期过期1检测量具周期检定计划6 18尺寸<34.7 产品报废7 Z 作业员操作不规范4严格按工艺要求操作作业员自检,检验员巡检6 168加强人员培训生产车间对操作人员进行培训,提高技能7 3 3 63加工设备精度不够3 6 126加强检验频次,加强人员培训生产车间每月对设备记性一次检查,对维修人员进行培训,提高技能7 3 3 63检测量具精度不够1检测量具周期检定计划6 42 无检测量具的检定周期过期1检测量具周期检定计划6 42尺寸>40.3 余量过大,影响后续加工3作业员操作不规范4严格按工艺要求操作作业员自检,检验员巡检6 72 无加工设备精度不够3 6 54检测量具精度不够1检测量具周期检定计划6 18检测量具的检定周期过期1检测量具周期检定计划6 18PFMEA分析表表单编号JZQ/QR703-42-A第页共页尺寸<39.7 产品报废7 Z 作业员操作不规范4严格按工艺要求操作作业员自检,检验员巡检6 168加强人员培训生产车间对操作人员进行培训,提高技能7 3 3 63加工设备精度不够3 6 126加强检验频次,加强人员培训生产车间每月对设备记性一次检查,对维修人员进行培训,提高技能7 3 3 63检测量具精度不够1检测量具周期检定计划6 42 无检测量具的检定周期过期1检测量具周期检定计划6 42尺寸>41.8 产品报废7 Z 作业员操作不规范4严格按工艺要求操作作业员自检,检验员巡检6 168加强人员培训生产车间对操作人员进行培训,提高技能7 3 3 63加工设备精度不够3 6 126加强检验频次,加强人员培训生产车间每月对设备记性一次检查,对维修人员进行培训,提高技能7 3 3 63检测量具精度不够1检测量具周期检定计划6 42 无检测量具的检定周期过期1检测量具周期检定计划6 42尺寸<41.2 余量过大,影响后续加工3作业员操作不规范4严格按工艺要求操作作业员自检,检验员巡检6 72 无加工设备精度不够3 6 54检测量具精度不够1检测量具周期检定计划6 18检测量具的检定周期过期1检测量具周期检定计划6 184.数铣成型二,控制尺寸尺寸>20.3余量过大,影响后续加工3作业员操作不规范4严格按工艺要求操作作业员自检,检验员巡检6 72 无PFMEA分析表表单编号JZQ/QR703-42-A第页共页20、49 加工设备精度不够3 6 54检测量具精度不够1检测量具周期检定计划6 18检测量具的检定周期过期1检测量具周期检定计划6 18尺寸<19.7 产品报废7 Z 作业员操作不规范4严格按工艺要求操作作业员自检,检验员巡检6 168加强人员培训生产车间对操作人员进行培训,提高技能7 3 3 63加工设备精度不够3 6 126加强检验频次,加强人员培训生产车间每月对设备记性一次检查,对维修人员进行培训,提高技能7 3 3 63检测量具精度不够1检测量具周期检定计划6 42 无检测量具的检定周期过期1检测量具周期检定计划6 42尺寸>49.3 余量过大,影响后续加工3作业员操作不规范4严格按工艺要求操作作业员自检,检验员巡检6 72 无加工设备精度不够3 6 54检测量具精度不够1检测量具周期检定计划6 18检测量具的检定周期过期1检测量具周期检定计划6 18尺寸<48.7 产品报废7 Z 作业员操作不规范4严格按工艺要求操作作业员自检,检验员巡检6 168加强人员培训生产车间对操作人员进行培训,提高技能7 3 3 63加工设备精度不够3 6 126加强检验频次,加强人员培训生产车间每月对设备记性一次检查,对维修人员进行培训,提高技能7 3 3 63PFMEA分析表表单编号JZQ/QR703-42-A第页共页检测量具精度不够1检测量具周期检定计划6 42 无检测量具的检定周期过期1检测量具周期检定计划6 425.数铣倒角,控制尺寸C5 尺寸>C5余量过小,影响后续加工3作业员操作不规范4严格按工艺要求操作作业员自检,检验员巡检6 72 无加工设备精度不够3 6 54检测量具精度不够1检测量具周期检定计划6 18检测量具的检定周期过期1检测量具周期检定计划6 18尺寸<C5余量过大,影响后续加工3作业员操作不规范4严格按工艺要求操作作业员自检,检验员巡检6 168加强人员培训生产车间对操作人员进行培训,提高技能7 3 3 63加工设备精度不够3 6 126加强检验频次,加强人员培训生产车间每月对设备记性一次检查,对维修人员进行培训,提高技能7 3 3 63检测量具精度不够1检测量具周期检定计划6 42 无检测量具的检定周期过期1检测量具周期检定计划6 427.探伤产品进行100%探伤产品有裂纹产品报废8 G原材料不合格3作业员自检,检验员巡检6 144加强原材料进厂检验质量部对原材料检验人员进行培训,提高技能8 3 3 72热处理工艺参数不规范3进行工艺评审、验证6 144加强工艺评审及验证8 3 3 72作业员操作不规范3严格按工艺要求操3 72加强作业人员技能培训对作业人员进行技能培训PFMEA分析表表单编号JZQ/QR703-42-A第页共页8.压标识按图纸指定位置处打“JZQ Txx年月及序列号,7号字压标识位置不正确影响产品外观2作业员操作不规范3严格按工艺要求操作作业员自检,检验员巡检6 36 无标识内容不正确影响产品追溯4作业员操作不规范3严格按工艺要求操作作业员自检,检验员巡检6 72 无标识字体不正确影响产品追溯2作业员操作不规范3严格按工艺要求操作作业员自检,检验员巡检6 36 无9.入库产品清洗干净,涂防锈油,包装入库清洗不干净影响后道工序5作业员操作不规范3严格按工艺要求操作作业员自检,检验员巡检6 90 无未涂防锈油导致产品生锈5作业员操作不规范3严格按工艺要求操作作业员自检,检验员巡检6 90 无包装不符合要求导致产品运输过程中损坏5作业员操作不规范 3严格按工艺要求操作作业员自检,检验员巡检6 90 无存放位置不符合要求不方便库房管理2作业员操作不规范 4严格按工艺要求操作作业员自检,检验员巡检6 48 无。