镭射转移压印工艺中的掉墨故障分析
移印中常见的问题及原因

移印中常见的问题及原因移印是一种常见的印刷技术,它能够将图案或文字从一个表面转移到另一个表面。
然而,在实际使用中,我们常常会遇到一些问题,影响了移印的质量和效果。
本文将针对移印中常见的问题及原因进行探讨。
一、图案不清晰在移印过程中,图案可能出现模糊、不清晰的情况。
这主要有以下几个原因:1. 印版质量不好:印版是移印的核心部件,如果印版质量不好,表面光滑度不够,就会导致图案无法完整地转移到另一个表面。
2. 印刷墨水质量差:墨水的质量直接影响到移印的效果,如果使用的墨水质量差,颜色不鲜艳,就会导致图案不清晰。
3. 移印压力不均匀:移印过程中,如果施加的压力不均匀,就会导致图案不完整、模糊。
二、颜色不匹配在移印过程中,有时候可能会出现颜色不匹配的情况,这主要有以下原因:1. 墨水颜色选择错误:选择墨水时,需要根据需要印刷的图案和基材的颜色来选择合适的墨水颜色,如果选择错误,就会导致颜色不匹配。
2. 墨水质量不好:墨水质量差也会导致颜色不匹配的问题,墨水的颜色可能会出现偏差。
3. 基材的颜色影响:基材的颜色也会对移印的效果产生影响,如果基材的颜色不均匀或者有色差,就会导致印刷出来的图案颜色不匹配。
三、印刷不精准在移印过程中,有时候可能会出现印刷不精准的情况,这可能是由以下原因引起的:1. 移印位置不准确:移印时需要注意位置的准确性,如果位置不准确,就会导致印刷不精准。
2. 移印速度过快:移印速度过快可能会导致印刷不精准,无法将图案完整地转移到另一个表面。
3. 移印压力不足:移印过程中,如果施加的压力不足,也会导致印刷不精准,图案无法完整地转移。
四、移印层不牢固在移印过程中,有时候可能会出现移印层不牢固的情况,这主要有以下原因:1. 印版表面不平整:印版的表面需要保持光滑平整,否则会导致移印层不牢固。
2. 移印压力不足:移印时需要施加适当的压力,如果压力不足,就会导致移印层不牢固。
3. 基材表面处理不当:移印前需要对基材进行适当的处理,如果处理不当,就会导致移印层不牢固。
镭射印与冷烫印的工艺及特点
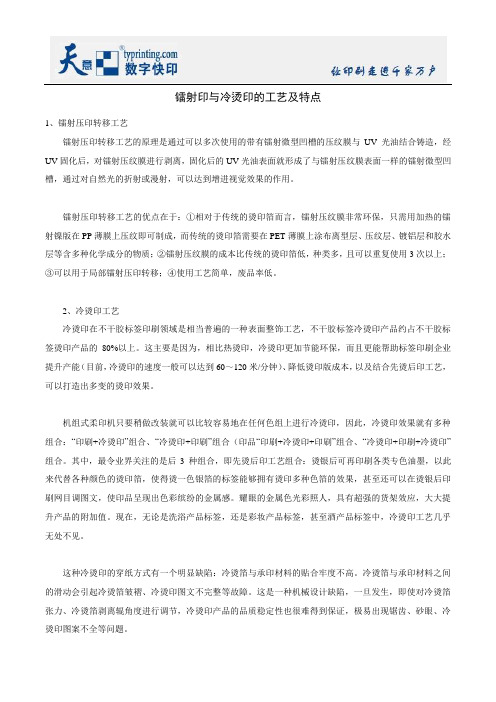
镭射印与冷烫印的工艺及特点1、镭射压印转移工艺镭射压印转移工艺的原理是通过可以多次使用的带有镭射微型凹槽的压纹膜与UV光油结合铸造,经UV固化后,对镭射压纹膜进行剥离,固化后的UV光油表面就形成了与镭射压纹膜表面一样的镭射微型凹槽,通过对自然光的折射或漫射,可以达到增进视觉效果的作用。
镭射压印转移工艺的优点在于:①相对于传统的烫印箔而言,镭射压纹膜非常环保,只需用加热的镭射镍版在PP薄膜上压纹即可制成,而传统的烫印箔需要在PET薄膜上涂布离型层、压纹层、镀铝层和胶水层等含多种化学成分的物质;②镭射压纹膜的成本比传统的烫印箔低,种类多,且可以重复使用3次以上;③可以用于局部镭射压印转移;④使用工艺简单,废品率低。
2、冷烫印工艺冷烫印在不干胶标签印刷领域是相当普遍的一种表面整饰工艺,不干胶标签冷烫印产品约占不干胶标签烫印产品的80%以上。
这主要是因为,相比热烫印,冷烫印更加节能环保,而且更能帮助标签印刷企业提升产能(目前,冷烫印的速度一般可以达到60~120米/分钟)、降低烫印版成本,以及结合先烫后印工艺,可以打造出多变的烫印效果。
机组式柔印机只要稍做改装就可以比较容易地在任何色组上进行冷烫印,因此,冷烫印效果就有多种组合:“印刷+冷烫印”组合、“冷烫印+印刷”组合(印品“印刷+冷烫印+印刷”组合、“冷烫印+印刷+冷烫印”组合。
其中,最令业界关注的是后3 种组合,即先烫后印工艺组合:烫银后可再印刷各类专色油墨,以此来代替各种颜色的烫印箔,使得烫一色银箔的标签能够拥有烫印多种色箔的效果,甚至还可以在烫银后印刷网目调图文,使印品呈现出色彩缤纷的金属感。
耀眼的金属色光彩照人,具有超强的货架效应,大大提升产品的附加值。
现在,无论是洗浴产品标签,还是彩妆产品标签,甚至酒产品标签中,冷烫印工艺几乎无处不见。
这种冷烫印的穿纸方式有一个明显缺陷:冷烫箔与承印材料的贴合牢度不高。
冷烫箔与承印材料之间的滑动会引起冷烫箔皱褶、冷烫印图文不完整等故障。
移印中常见故障及解决方法(一)

移印中常见故障及解决方法(一)
作者简介:王守鸿,一九九八年毕业于武汉测绘科技大学,获印刷工程学士学位。
二○○一年毕业于武汉大学印刷传播系,获硕士学位,现任职于广东轻工职业技术学院。
移印,属于特种印刷方式之一。
它能够在不规则异性对象表面上印刷文字、图形和图象,现在正成为一种重要的特种印刷。
例如,手机表面的文字和图案就是采用这种印刷方式,还有计算机键盘、仪器、仪表等很多电子产品的表面印刷,都以移印完成。
移印工艺十分简单,采用钢(或者铜、热塑型塑料)凹版,利用硅橡胶材料制成的曲面移印头,将凹版上的油墨蘸到移印头的表面,然后往需要的对象表面压一下就能够印出文字、图案等。
在移印中经常会出现很多印刷故障,本文对移印工艺中的常见故障进行了概括归纳,整理成较为全面的移印故障大全。
常见故障之一:印刷品的线条和文字不清楚,出现模糊现象。
常见故障之二:油墨的粘着性达不到要求
这个故障在移印中十分常见,因为你对油墨的配方不了解,也可能是选用的油墨类型不正确。
常见故障之三:印刷品上出现明显的针孔状
假若小针孔较大,而且出现在印刷品上的同一位置,那么要检查移印头和凹版上的图象。
如果需要,更换移印头和凹版。
镭射压印转移不完全

镭射压印转移不完全随着我国节能减排理念的一贯扩展,镭射压印转移工艺在烟包印刷周围的应用越来越广,但在烟包出产历程中也时常会出现一些阻碍。
文本中,笔者将连结日程任务中的一些体会,先容烟包镭射压印转移工艺的罕见题目及解决设施,与业内同行分享。
镭射压印转移工艺罕见题目解析文︱蚌埠金黄山凹版印刷无限公司焦杰明1.出现皱膜气象镭射转移膜在必然张力下,始末压合机构将全息图案转移到印品口头,在这个历程中,对于压印。
镭射转移膜必要经过多根导膜辊,容易出现皱膜气象。
主要缘故有以下两点。
(1)镭射转移膜收卷张力过大,使得膜卷两端张力不一致,从而惹起皱膜。
此时,必要仔细调整出膜辊、导膜辊、阻尼辊的均衡,对照费时。
而且,当下一次反复使用镭射转移膜时,从而使得镭射压印转移不完全。
张力不一致的方向会反过去,这就必要重新调整摆设。
看着流平剂原理。
常用的设施是在镭射转移膜收卷后当即复卷一次,以进一程序整镭射转移膜的张力,并对其举行散热。
(2)镭射转移膜自己没有质量题目,不合压不皱膜,一合压就皱膜。
这主要是由于镭射转移膜在压印转移时压膜辊两端的压力不均衡所致。
润湿流平剂。
在这种处境下,必要调整压膜辊两端的气缸压力,即调动气缸旅程末端的压合限位螺丝,而使。
因其位于墙板内侧,身分对照埋没,于是必要用塞尺举行调动,防卫及时锁紧。
有的镭射压印转移摆设压膜辊两端的气缸压力可以独立调整,绝对对照简单。
(3)镭射转移膜在各导膜辊处的张力不均衡,造成走膜速度和压印速度不一致,从而惹起皱膜。
2.全息图案出现针孔、白点气象这种气象主要展现为针孔、白点身分唯有UV光油没有全息图案,或既没有UV光油也没有全息图案。
确凿其实可分为以下几种处境。
你看镭射。
(1)针孔、白点的身分与形态体式对照稳定。
主要缘故:①上光版或网纹辊口头有凹坑,造成印品口头对应身分没有UV光油,天然就没有全息图案;②当使用带光标的单版避版缝镭射转移膜,且UV光油涂布没有题目时,假若已经出现这种处境,恐怕是镭射转移膜口头有瑕疵,流平剂价格。
印刷后工序 常见异常分析及改善
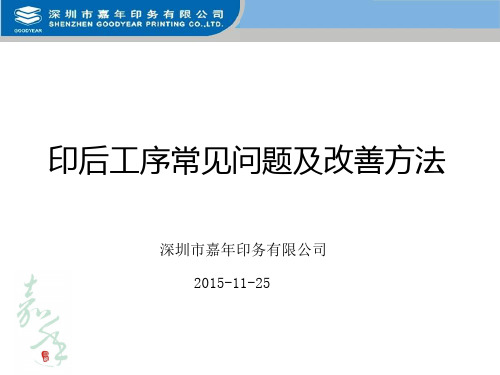
5、常见异常的分析和改善 5.4 ELP
1.镭射压印转移图案光泽度差 原因分析: (1)当UV光油黏度太低时,UV光油中固有的光敏寡聚物树脂的含量也较 低,这样UV光油固化后的成膜厚度就会变薄,从而导致镭射压印转移图案 光泽度变差。 (2)UV光油黏度太低还会降低UV光油在网纹辊表面的转移量,导致承印 物表面UV光油的涂层太薄,从而使得UV光油固化后,承印物表面形成的镭 射压印转移图案光泽度较差。 (3)当在UV光油中加入过量乙醇时,乙醇中所含的水分不能完全挥发, 在UV光油固化时容易产生水雾,并残留在光油膜层中,从而影响UV光油固 化成膜后的光泽度,甚至导致UV光油固化不彻底,使得镭射压印转移图案 产生雾化现象或失去应有的光泽。 为此,我们可以通过选择黏度较高的UV光油或在UV光油中加入适量的UV增 稠剂来提高其黏度,以及选用纯度稍高的乙醇且在使用过程中尽可能控制 乙醇的加入量等方法,来提高镭射压印转移图案的光泽度。
主要生产控制参数: 1、网目数 2、灯管电流
5、常见异常的分析和改善 5.3 全自动丝印/手工丝印
套位不准 产生原因: 1、纸张歪斜(切纸切歪) 2、纸张表面处理后变形(伸长/收缩) 3、针位不一致 4、拉规、前规等设备异常 5、网版张力太小 改善对策: 1、分针位生产 2、根据整体变形/走位状况,调节网版位置套
5、常见异常的分析和改善 5.0 常见问题
①、混料: 产生原因: 1、未按流程作业:未看工序要求、品标卡、未清场 2、不细心导致 3、其它偶发因素:无关人员放混、前工序混 改善对策: 1、按《 GY.TD014 产品混料防范管理规程》作业 2、机灵一点,不要只埋头做事,多思考。 3、细心、有责任感:对于其它人员的问题,不要抱着无所
1.3 UV上光:
UV上光即紫外线上光,它是以UV专用的特殊涂剂精 密、均匀地涂于印刷品的表现或局部区域后,经紫外线 照射,在极快的速度下干燥硬化而成,一般干燥时间 0.1~0.3S
移印工艺常见故障及消除

表 5 套印不准的原因及解决办法 可能原因 移印胶头安装和调整有问题 移印胶头形状不统一, 导致不同颜色的变形 不一致 移印胶头硬度不相同, 导致油墨在不同色相 上厚薄不均匀 油墨在其中一色的扩展大于其他颜色 承印物局部坍塌现象 (如硬质塑料瓶) 工件夹具不够稳定 输送带, 梭动台和转盘工作台精确度不高 夹具不够精密, 支撑性不好 的压力中心 胶头的形状要具有同一性, 保证 4个胶头的形状相同 使用橡胶硬度计确定胶头硬度的同一性, 胶头硬度偏差低于 2% 选用高质量的移印油墨添加准确的稀释剂 选用更好的夹具或气压更大的吹气装置 制作支撑性好, 稳定性好的夹具 安装精确度高的工作台 精确调整, 制作更加精密的夹具 解决办法 调整胶头在最精确的位置转移图文, 保证4个胶头具有同样
出现小针孔
如果针孔连续不断地出现在同一个位置, 应检 查移印胶头和钢板是否受到损伤, 可以用清洗剂洗 净胶头表面和钢板, 如果针孔消失, 说明油墨干燥在 了某个位置, 如果针孔仍然存在, 很可能钢板本身和 胶头有先天的缺陷, 必须更换. 如果图文上的针孔不 规则地出现, 那应该考虑油墨是否出现静电污染或 者被灰尘污染. 胶头使用久了, 表面的微孔常常也是 针孔的罪魁祸首, 养成定期更换胶头的习惯虽然提 高了生产成本,但是改善了移印质量. 见表 3. 实践证明,胶头中心压印区最常出现针孔, 这 是由于这个地方压力过大导致油墨层在胶头和承印 物的表面张力有明显差异所致, 特别是一些金属, 玻 璃和陶瓷材料. 选择胶头要注意保持这样的中心区 不应超过有效印刷面积的10%.
表 4 颜色反串的原因及解决办法 可能原因 移印胶头表面出现细孔, 老化 印版腐蚀深度太深 油墨干燥速度太慢 承印物表面太光滑, 基材被稀 释剂所侵蚀损坏 解决办法 更换新的胶头, 胶头制作过程请注意配方的精确化 用较浅的深度腐蚀钢版, 用钢版深度计检测钢版 选用快干稀释剂 , 进行吹风干燥, 使用胶头延迟压印功能, 迫使油墨用较 长的时间干燥 两次印刷中用热风或冷风干燥, 或采用两次粘墨一次压印的模式印刷, UV 油墨套印一定要控制好印刷速度
移印过程中的常见问题及解决办法
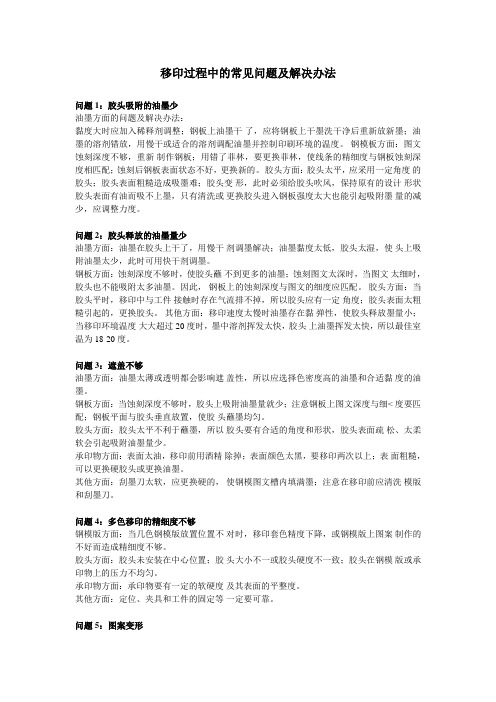
移印过程中的常见问题及解决办法问题1:胶头吸附的油墨少油墨方面的问题及解决办法:黏度大时应加入稀释剂调整;钢板上油墨干了,应将钢板上干墨洗干净后重新放新墨;油墨的溶剂错放,用慢干或适合的溶剂调配油墨并控制印刷环境的温度。
钢模板方面:图文蚀刻深度不够,重新制作钢板;用错了菲林,要更换菲林,使线条的精细度与钢板蚀刻深度相匹配;蚀刻后钢板表面状态不好,更换新的。
胶头方面:胶头太平,应采用一定角度的胶头;胶头表面粗糙造成吸墨难;胶头变形,此时必须给胶头吹风,保持原有的设计形状胶头表面有油而吸不上墨,只有清洗或更换胶头进入钢板强度太大也能引起吸附墨量的减少,应调整力度。
问题2:胶头释放的油墨量少油墨方面:油墨在胶头上干了,用慢干剂调墨解决;油墨黏度太低,胶头太湿,使头上吸附油墨太少,此时可用快干剂调墨。
钢板方面:蚀刻深度不够时,使胶头蘸不到更多的油墨;蚀刻图文太深时,当图文太细时,胶头也不能吸附太多油墨。
因此,钢板上的蚀刻深度与图文的细度应匹配。
胶头方面:当胶头平时,移印中与工件接触时存在气流排不掉,所以胶头应有一定角度;胶头表面太粗糙引起的,更换胶头。
其他方面:移印速度太慢时油墨存在黏弹性,使胶头释放墨量小;当移印环境温度大大超过20度时,墨中溶剂挥发太快,胶头上油墨挥发太快,所以最佳室温为18-20度。
问题3:遮盖不够油墨方面:油墨太薄或透明都会影响遮盖性,所以应选择色密度高的油墨和合适黏度的油墨。
钢板方面:当蚀刻深度不够时,胶头上吸附油墨量就少;注意钢板上图文深度与细< 度要匹配;钢板平面与胶头垂直放置,使胶头蘸墨均匀。
胶头方面:胶头太平不利于蘸墨,所以胶头要有合适的角度和形状,胶头表面疏松、太柔软会引起吸附油墨量少。
承印物方面:表面太油,移印前用酒精除掉;表面颜色太黑,要移印两次以上;表面粗糙,可以更换硬胶头或更换油墨。
其他方面:刮墨刀太软,应更换硬的,使钢模图文槽内填满墨;注意在移印前应清洗模版和刮墨刀。
移印中常见故障及解决办法

凹版材料类型选择不当
选用合适的凹版类型(例如用钢版取代聚酯版)
网屏选用不当
选用另外的网屏试一试
油墨
油墨过于粘稠
往油墨中加一些稀释剂
油墨过稀
减少油墨中稀释剂的用量
油墨干燥速度太慢
换一种干燥速度更快的稀释剂
承印材料
对象表面不干净
预先将印刷对象的表面清洗干净
表面坚硬且呈颗粒状
假若可能,重新换一种材料。或者试用一个硬度较大的移印头
油墨在移印头表面过于湿润
往油墨加点挥发速度更快的稀释剂
承印材料
印刷物件表面不干净(表面有油脂、释放剂、手汗等脏物)
预先清洗印刷物件,如果表面实在太脏,最好用乙醇清洗,印刷过程中建议戴着手套操作
其它原因
室内温度过高
室内温度最好在21-25℃间
移印头的移动速度太慢
如果油墨干燥在移印头表面,那么把移印头的移动速度提高
假若小针孔较大,而且出现在印刷品上的同一位置,那么要检查移印头和凹版上的图象。如果需要,更换移印头和凹版。
可能的原因
解决方法
移印头
移印头表面受到损害
更换移印头,或者调节移印头的位置,让受到损害的部位不会影响移印图象
移印头表面过于平整
换一个形状稍微尖一点的移印头
移印头硬度不够
换一个硬度较硬的移印头
腐蚀凹版
油墨
油墨太稀
增大油墨的黏稠度
油墨转移不完全
采用相关的辅助设备来风乾油墨,使移印头上的油墨能够正确释放
承印材料
由於印刷物件太黑,令图象颜色不够明亮
多印一次,使油墨层厚度稍厚一些
常见故障之七:图象蹭脏
印刷时油墨太稀,或者移印头发生滑动,都会使印刷图象蹭脏。移印头太硬、印刷物件固定不牢固、印刷物件在夹具上的角度不正确,及移印头的压力过大等均会导致印刷过程中移印头滑动。
激光转印问题解决方案
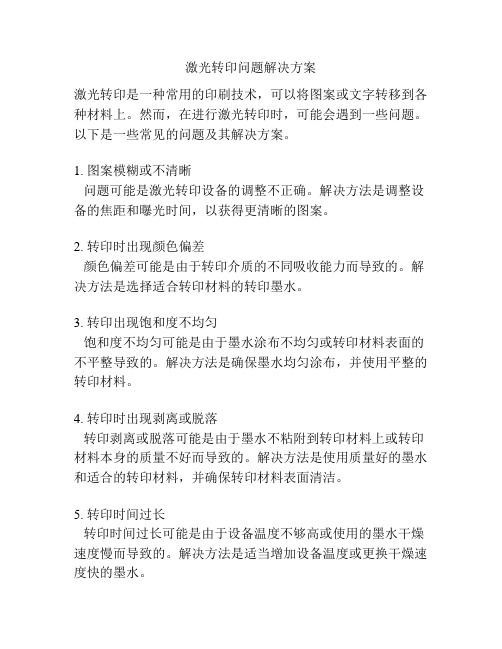
激光转印问题解决方案
激光转印是一种常用的印刷技术,可以将图案或文字转移到各种材料上。
然而,在进行激光转印时,可能会遇到一些问题。
以下是一些常见的问题及其解决方案。
1. 图案模糊或不清晰
问题可能是激光转印设备的调整不正确。
解决方法是调整设备的焦距和曝光时间,以获得更清晰的图案。
2. 转印时出现颜色偏差
颜色偏差可能是由于转印介质的不同吸收能力而导致的。
解决方法是选择适合转印材料的转印墨水。
3. 转印出现饱和度不均匀
饱和度不均匀可能是由于墨水涂布不均匀或转印材料表面的不平整导致的。
解决方法是确保墨水均匀涂布,并使用平整的转印材料。
4. 转印时出现剥离或脱落
转印剥离或脱落可能是由于墨水不粘附到转印材料上或转印材料本身的质量不好而导致的。
解决方法是使用质量好的墨水和适合的转印材料,并确保转印材料表面清洁。
5. 转印时间过长
转印时间过长可能是由于设备温度不够高或使用的墨水干燥速度慢而导致的。
解决方法是适当增加设备温度或更换干燥速度快的墨水。
总之,激光转印问题的解决方法涉及到设备调整、墨水选择、转印材料准备等方面。
通过合理的操作和选择,可以解决激光转印过程中可能出现的问题,并获得满意的转印效果。
印刷中飞墨故障分析及解决

·29·包装技术印刷中飞墨故障分析及解决■ 文/高斌摘要:本文阐述了印刷的定义、原理及印刷过程中飞墨故障原因分析及解决处理的方法。
对印刷作业流程具有一定的参考价值。
关键词:飞墨;粘性;印刷压力;印刷墨的多项体系中,存在着连结料与颜料颗粒界面上形成的双电层结构.在墨丝断裂时,墨丝断片边缘存在的双电层遭到破坏,分成正负两种电荷,一部分电荷残留在油墨中,而相反的电荷向空中逃逸.残留在油墨中的电荷要集中在墨辊和纸面上,墨丝断片则由于墨辊上也带有同种电荷被搏斥而逐出,形成飞墨。
3.空洞学说这种学说认为,墨膜在墨辊间分裂的瞬间,在压力最小的部位,墨膜内部产生空洞,随后这些空洞转成泡核,逐渐长大从而形成墨丝。
油墨颜料粒子的数目或每个单位容量油墨的颜料与连结料之间的界面幅度对形成泡核的数目有很大的影响。
连结料与颜料的润湿性愈差,愈易促进泡核形成,飞墨也愈严重。
总之,油墨雾散(飞墨)现象是在机、电双重作用下发生的.在两个相互接触、高速旋转的墨辊所形成的辊隙的出口处,油墨被拉成丝而断裂.如果墨丝在两处或两处以上的地方断裂,断裂后的墨丝便会靠弹性作用回缩到墨辊上去,而断裂后形成的油墨断片,便在表面张力的作用下,收缩成球状的墨滴游离出来。
与此同时,回缩的墨丝和游离的墨滴,表面的双电层均遭到破坏,致使部分电荷从墨丝或墨滴上移入空间,相反的电荷则留在墨丝或墨滴上。
由于墨滴和回缩到墨辊上的油墨带有相同性质的电荷,墨滴便被排斥逐向空间,形成飞墨。
二、影响飞墨的因素影响飞墨的因素很多,一般可以归纳为油墨因素、机械因素、环境因素等。
目前,我国考察飞墨的标准方法是利用油墨粘性仪进行飞墨实验。
油墨粘性仪有三个一、引言近年来,印刷业的发展十分迅速,印刷过程中产生的环境污染很多,其中油墨的雾散、飞墨、甩墨是急需解决的问题。
飞墨、甩墨是高速印刷中一类常见故障,成因复杂、彻底排除有一定难度,但采取必要的措施可以缓解这一现象,改善工作环境。
镭射化镀区域脱落原因

镭射化镀区域脱落原因
镭射化镀区域脱落的原因可能有以下几种:
镀层与基体结合力差:由于镀层与基体的结合力不足,导致镀层容易脱落。
这可能是因为镀层材料与基体材料的物理性质差异较大,或者是镀层处理过程中没有进行适当的预处理,导致镀层与基体之间的结合力较弱。
镀层过薄:如果镀层过薄,那么它就难以满足对基体的保护要求,容易受到外界环境的影响,导致镀层脱落。
基体表面处理不当:在镀层处理之前,需要对基体进行适当的表面处理,如清洁、打磨等。
如果表面处理不当,会导致镀层与基体之间的结合力变差,从而引起镀层脱落。
镀层材料问题:如果镀层材料的质量较差,或者材料的选择不当,也会导致镀层脱落。
工艺参数不当:在镀层处理过程中,如果工艺参数选择不当,如电流密度、电镀时间等,可能会导致镀层质量不稳定,从而引起镀层脱落。
使用环境恶劣:如果镀层在使用过程中长期处于恶劣的环境中,如高温、高湿、腐蚀等,会导致镀层受到腐蚀和损伤,最终引起镀层脱落。
为了防止镭射化镀区域脱落,可以采取以下措施:
选用合适的镀层材料和工艺参数,确保镀层质量稳定。
对基体进行适当的表面处理,如清洁、打磨等,以提高镀层与基体之间的结合力。
在使用过程中,尽量避免使镀层长期处于恶劣的环境中,如高温、高
湿、腐蚀等。
对已经脱落的区域进行修复和补充处理,如重新进行表面处理和电镀等。
镭射转移压印工艺中掉墨故障解决

产 品的包 装档次 。镭射 f t ; . 1 7 1 ]  ̄移技 术是 近年包装
领 域实现 全息 『 欠 l 案 效 果 的 技 术 新 宠 , 义称 ( 2 ( C a s t &C o a t )、压膜 转印技术 ,主要 是在 印包 后 的纸类 产品 七 进 行镭射 全息效 果的压 印转移过 程 ,将镭射转 移膜 ( 压纹膜 )f 的铝层表 光学 结构 “ 转移 ”到纸 张表 面 ,在 光线 照射下 ,使产 品满 版或局 部位 置上实现 视觉 J : 彩虹全息 陶案 的 效果 。 南 丁该技术具有 环保 、 低成本 、 效 果佳优势 ,
・中山火炬职业技术学院 /中荣印刷集团股份有限公司 陈海生
李
娜
陈锦彬
激 觉 达 光 卜 全 分 到 上 息 广 绚 防 泛 丽 伪 像 和 , 多 应 不 彩 环 J 仅 , 1 . j 于 能 增 的 使 包 加 效 装 包 美 果 装 感 印 刷 产 , 领 品 域 视 时
附着力好 、套 印准确 、无针孔 实际牛 产 『 1 1 ,常 m现各种 - { j ( 障 质幢问题 ,如掉 、皱膜 、针孑 L 、
令息图 案发黄 变色等质量 问题 ,其 中最 突f “的掉
曜 问题 ,长期 闹扰 生产企业 一
、
镭 射 压 印转 移 的 工 艺 介 绍
1 . 技术原理
似 ■棱 镜的微型 网穴组成 的 ;
广泛应 用包装 产品领 域 。
一
般要求 镭 射压 印产 品满 足 :平整 、光滑 、
利川 U V光油 作 为载体 ,提前 印刷 涂布 在包 装印刷l { f I } ,与转 移膜 压 合 时 ,【 J V油 未 固化 .
常见移印的质量缺陷与排除方法

常见移印的质量缺陷与排除方法常见移印的质量缺陷与排除方法移印工艺和丝网印刷一样,对承印物材料都广泛的适应性,因而在特种印刷行业占据较为重要的地位。
现将移印工艺常见的质量问题作一简单总结,以供相关人员参考。
问题原因分析解决办法1.承印物表面有油腻、灰尘,致使油墨不能完全转移 1.在印刷前要对承印物表面进行清洁处理2.胶头硬度太软2.选择较硬的胶头印迹模糊3、承印物表面带有静电3、用静电消除器消除静电或在油墨中加入抗静电剂4.胶头形状不对4.胶头形状应与承印物表面形态基本吻合5.油墨太稀5.在油墨中加入适量的原墨6.钢板图文边缘粗糙6.重新腐蚀钢板1.油墨粘度太大1.加入稀释剂,调整油墨粘度2.油墨搅拌不均2.开机前应有充分的匀墨时间有气泡3.机器运行速度太快3.降低移印机运行速度4.溶剂选择不对4.加入2%的消印5.胶头压印时空气排除不净5.选择底郡较尖的胶头1.胶头形状不对1.尽量选择胶头能够印刷完整图案时压缩量为10mm的胶头形状2.胶头硬度太软2.远掸较硬的胶头图文变形过大3.晒版软片未作预变形处理3.根据承印物形状和变形趋势,在制作软片时拉伸、压缩,增大、减小图文4 、定位夹具设计不合理4、承印物放在夹具上应保证胶头压印时具有较小的变形5.移印印版与软片贴合时不紧密5.更新晒版6.钢板腐蚀问题6.更新制版1.定位夹具制作精度差,承印物有松动现象1.承印物在夹具上的定位不能发生明显的位移2.分色片重复精度差,致使钢板重复精度差2.重新晒版套印不准3.移印胶头出现塑性变形3.移印胶头制作过程固化不充分、应重做胶头4.多色移印机套准精度差4.移印机套准误差应控制在0.10mm 以下5.气压不稳定5.稳定气源压力针孔1.承印物表面落有尘埃颗粒1.印刷前要对承印物进行表面处理2.油墨染脏2.对油墨进行过滤1、油墨太稀,树脂连结料析出1,再加入适量原墨搅拌均匀墨层光泽度差2.油墨变质2.更换油墨3、油墨本身光泽度差3.在油墨中加入亮光连结料或在承印物表面再涂一层光油1、油墨太稀1.加入油墨,改善油墨粘度过2.油墨本身附着力差2、更换油墨墨层不耐摩擦3.UV油墨固化不完全3、在UV固化时应减低固化速度,延长固化时间4、双组分油墨配比比例不正确4、严格按说明进行调配5.承印物表面性质与油墨抵触5、对承印物表面进行脱脂、粗化、氧化、腐蚀处理。
镭射压印转移工艺的发展及工艺要求

镭射压印转移工艺的发展及工艺要求激光全息图像不仅大大提升了产品的外观档次,显示出一种高档豪华的形象,还增加了一定的防伪功能,因此其在包装上的应用越来越广泛,特别适用于烟、酒、化妆品、食品、保健品、礼品等产品的包装。
在包装上获得激光全息图像有多种方法,如不干胶标签、镭射膜直接复合、镭射烫印箔热烫印和冷烫印、镭射镀铝纸等。
然而,上述激光全息图像的获得方法还存在一些不足之处。
不干胶标签:方法简单,但与包装不是一个整体,易脱落,无法增加包装的美观度,常用作封口防伪标贴。
镭射膜直接复合:工艺简单,但生产效率低,能与包装表面紧密贴合,常用于激光全息图像的整体复合,而不是局部复合。
镭射膜会永久地留在包装上,难以降解,有悖于当前绿色环保的理念。
镭射烫印箔热烫印:工艺精美,可以进行定位烫印,生产效率较高,防伪效果良好,一般用于局部图案及较小面积的烫印。
但其需要加热装置和烫印版,生产成本较高。
镭射镀铝纸:工艺效果良好,但只能用于激光全息图像的底纹,不能局部使用,对后道印刷要求高,凹印是其常用的印刷方式,成本很高。
基于这些工艺方法的不足,包装设计人员一直在寻找一种低成本、环保、应用范围广的激光全息图像制作工艺。
经过不断的努力以及大量的试验,一种崭新的激光全息图像制作工艺―镭射压印转移工艺应运而生。
镭射压印转移工艺的发展镭射压印转移设备的原始机型出自于日本一家制造企业,其采用的是收放膜卷的方式(如图1所示)。
每卷镭射压印转移膜的长度大约为3000~4000米,使用该设备工作半小时左右后就需要吊装膜卷和穿膜,劳动强度很大,而且容易损伤镭射压印转移膜,更大的问题是镭射压印转移激光全息图像与印刷品表面待烫印图案是无规则压印转移,成像质量差异很大,且镭射压印转移膜的版缝也无法避让。
特别是局部涂布UV光油时,待烫印图案边缘部分溢出的微量固化UV光油会残留在镭射压印转移膜上,严重影响镭射压印转移膜表面激光全息图案的转移质量,同时也会对下次镭射压印转移产生一定影响,使得镭射压印转移膜反复使用的次数减少至3~5次。
移印常见故障分析及解决方法

常見故障之一:
印刷品的線條和文字不清楚,出現模糊現象。
承印材料 物件表面不乾淨 表面堅硬且呈顆粒狀 表面凹凸程度厲害 印到物體邊緣上
預先將印刷物件的表面清洗乾淨
假若可能,重新換一種材料。或者試用一 個硬度較大的移印頭 採用特殊形狀的移印頭和移印頭底座裝置
夾具必須能防止移印頭滑動
常見故障之一:
印刷品的線條和文字不清楚,出現模糊現象。
油墨太黏稠
加一點稀釋劑
油墨乾燥固著在凹版 的凹坑面
用稀釋劑清洗凹版
常見故障之九:
印刷圖像呈斑點狀
承印材料
印刷物件受到油脂的 污染
用乙醇清洗印刷物件
其他原因
移印機的速度太慢 提高移印機的速度
常見故障之十:
油墨黏附在移印頭的表面
移印過程中,如果移印頭從凹版上完全吸附了 印刷圖像的油墨,但是並沒有把完全油墨轉移 到印刷物件上,那麽印刷品上會出現白點。
其他可能原因
工件夾具沒有達到足夠穩 定
高速印刷導致移印頭出現 變形
換一個新的工件夾具
降低印刷速度。如有必要,在油墨準備轉移 之前稍微停頓一會,目的是讓移印頭變形得 到恢復
常見故障之二:
油墨的粘著性達不到要求
這個故障在移印中十分常見,因爲你對油墨的 配方不瞭解,也可能是選用的油墨類型不正確。
常見故障之二:
常見故障之十一:
印刷圖像的邊緣呈頭髮絲狀
可能的原因 移印頭
解決方法
移印頭形狀過於平整 腐蝕凹版
換一個形狀稍尖一點的移印頭
凹版腐蝕深度太深
重新製作一塊深度稍淺一點的凹版
加網不當,或者根本沒 有加網
重新換一個加網網屏試試
常見故障之十一:
印刷圖像的邊緣呈頭髮絲狀
- 1、下载文档前请自行甄别文档内容的完整性,平台不提供额外的编辑、内容补充、找答案等附加服务。
- 2、"仅部分预览"的文档,不可在线预览部分如存在完整性等问题,可反馈申请退款(可完整预览的文档不适用该条件!)。
- 3、如文档侵犯您的权益,请联系客服反馈,我们会尽快为您处理(人工客服工作时间:9:00-18:30)。
镭射转移压印工艺中的掉墨故障分析
包装印刷产品上利用镭射转移压印工艺能实现激光全息图案的转移,增加产品美感,可提升产品档次,还具有一定的防伪功能。
主要分析镭射压印转移工艺对材料、工艺参数的要求,重点分析了实际生产中出现的掉墨故障问题。
标签:激光全息图案;镭射转移压印;掉墨故障
激光全息图像应用于包装包装印刷领域十分广泛,不仅能使包装产品视觉上绚丽多彩,增加美感,同时达到防伪和环保的效果,提高了产品的包装档次。
镭射压印转移技术是近年包装领域实现全息图案效果的技术新宠,又称C2(Caste & Coat)、压膜转印技术,主要是在印色后的纸类产品上进行镭射全息效果的压印转移过程,将镭射转移膜(压纹膜)上的铝层表面光学结构“转移”到纸张表面,在光线照射下,使产品满版或局部位置上实现视觉上彩虹全息图案的效果。
由于该技术具有环保、低成本、效果佳优势,广泛应用包装产品领域。
一般要求镭射压印产品满足:平整、光滑、附着力好、套印准确、无针孔。
实际生产中,常出现各种故障质量问题,如掉墨、皱膜、针孔、全息图案发黄变色等质量问题,其中最突出的掉墨问题,长期困扰生产企业。
本文结合实际经验,分析镭射压印转移工艺产品中掉墨问题及解决办法。
1镭射压印转移的工艺介绍
1.1技术原理
在纸张包装印刷品表面先涂布UV光油(底油),通过激光图案压印转移机的压力作用与预制好的带有镭射微型凹槽网穴的镭射转移膜(压纹膜)进行压合,经过UV紫外光固化定型后,将镭射转移膜与纸张剥离,纸张上的UV光油层的表面就能形成与镭射转移膜表面一样镭射微型凹槽网穴的效果,经过光照产生折射和散射后,视觉上即能够产生彩虹般闪光亮丽的图案效果,见图1。
其转移的实质是材料表面微型凹槽物理结构“转移”,而非化学物质转移、膜的剥离层转移。
其主要过程:(1)激光图案压印转移膜上有不同的全息图案效果(视觉上),其表面结构是由无数个微小的类似三棱镜的微型网穴组成的;(2)利用UV光油作为载体,提前印刷涂布在包装印刷品上,与转移膜压合时,UV 油未固化,呈软化状态,通过激光图案压印转移机的压力作用,转移膜上的微型网穴形状“转移”到UV光油表层,即:光油表层通过压印也呈现了微型网穴结构;(3)干燥固化和冷却后,印刷品与转移膜分离,UV油表层结构硬化,由于是透明的,光照时产生折射与散射,因此视觉上观察印刷品是则是与镭射膜本身视觉效果相同的全息图案视觉效果。
1.2材料及工艺要求
镭射转移过程主要使用的工艺材料有底涂UV光油、压印转移膜、涂布网纹辊等材料,生产过程控制的主要工艺条件:压印温度、压印压力、速度、张力。
1.2.1UV光油材料的要求
专用的UV光油(又称UV压膜胶、镭射压膜胶),由齐聚物、活性稀释剂、光引发剂以及其他助剂组成,一般油性光油居多。
在紫外光的照射下,UV光油中的光引发剂会吸收紫外光的能量,然后经过激发状态,产生游离基,引发聚合反应,从而瞬间固化成膜。
一般应考虑UV光油的黏度与涂布量、UV光油的纯度、UV光油配方与UV固化系统的匹配。
应满足:涂布量一般为5~7cm3/m2(如预涂了底油的则少一些);黏度适中30-60S(涂4#杯,25℃),有利于转移;纯度要高(无水酒精稀释),稀释剂必须使用无水酒精,视觉效果则佳;采用UV 灯固化要彻底,光油中引发剂量要适当,要考虑残留污染和产品的耐着度测试。
1.2.2镭射压印转移膜要求
镭射转移膜(压纹膜)一般采用激光技术将图案雕刻或電铸在平面镍版上,再利用双面胶将镍版弯曲并粘贴在版辊上,最后通过加温、加压将模压版上的全息图案转移到基膜上。
镭射压印转移的基膜一般为BOPP或PET薄膜,由于转移膜表面的网穴形状有三棱镜、鱼鳞、斜杠等,其网穴的深度、大小、排列角度各不相同,因此呈现不同的图案。
镭射压印转移过程一般不会损害基膜表面结构,镭射转移膜的全息图案层依然保留,因此镭射转移膜可重复使用多次,但若转移不良时会导致光油残留在基膜表面堵塞,影响重复使用。
一般常用的是BOPP薄,其使用要求是:BOPP薄膜厚度均匀,成像透明性好,表面张力在32mN/m左右。
过高的表面张力会导致压印转移时,光油层与镭射膜层不易剥离,影响光油表层微孔网穴结构不完整,造成全息图案转移不完全。
1.2.3网纹辊线数选择
网纹辊主要影响光油涂布量的大小。
一般要求:网纹辊雕刻线数为260线/英寸,效果最理想,网穴深度要求:28μm。
网穴深度相同的情况下,网纹辊线数越大,涂布光油量越少,越容易出现针孔、白点等质量问题,影响镭射效果。
1.2.4工艺条件的要求
(1)压印温度:根据不同体系的UV油,通过设置2根功率为5.6~6.5kW 的UV灯管开灯情况及吸热风装置来控制灯管温度(一般控制在260-500℃);
(2)压印压力:通过调节压辊与压印滚筒之间的距离、压缩空气的压力来控制,一般控制在80-120Mpa,压力越大,UV涂层越光滑,光泽度越高,但越大越容易引起皱膜。
(3)速度:在既要保证生产效率又要保证产品质量的情况下,速度一般控制在3000张-5000张每小时(需根据印张尺寸来确定具体速度),速度快慢,会影响UV油的固化程度,速度过快,UV油固化不完全,导致容易粘连。
掉油甚至掉墨、耐磨差。
速度太慢,纸张受热更容易变形,且造成产品变色(尤其是鲜颜色,不耐晒的油墨)。
(4)张力:分收卷和放卷张力,一般放卷张力(110-120N)略大于收卷张力,需根据原材料大卷张力来调节张力大小,张力太大,容易造成膜变形而全息图案变形,张力太小,镭射膜易起皱。
(5)转移膜表面温度:温度高易导致转移膜变形出现皱膜现象,因此通过水冷装置或吸热风装置来控制转移膜表面温度在30-50℃。
2掉墨故障问题分析
实际生产中,镭射产品常出现掉墨、皱膜、针孔、白点、镭射压印转移效果差、全息图案发黄变色、产品表面发涩等问题,一般会由环境条件控制不得当、材料自身质量(基膜或镭射模版质量)以及机器问题引起。
其中掉墨问题突出,指银卡纸类包装印刷品经镭射压印转移放置一段时间后,在装箱过程中产品出现局部印刷油墨脱落现象(见图2),用3M600胶带及手刮测试不合格。
2.1银卡类纸张印刷引起掉墨
纸张表面张力系数低,即达因值偏低(小于38达因),油墨难以在纸张上铺展,附着力差。
造成达因值偏低的因素有:
(1)镀铝膜表面能偏低,可以通过电晕处理解决;
(2)镀铝膜表面涂敷的清漆不均匀或太薄,涂敷清漆前进行电晕处理、选择上油量大的网纹辊;
(3)纸张储存环境湿度大,放置时间过长,需将纸张储存在温度20~25℃,相对湿度50~65%为宜。
2.2底涂清漆与镀铝膜结合力差。
造成原因
(1)镀铝膜表面能低,清漆难以在膜上铺展,渗透,附着力差;
(2)清漆本身的质量问题,选择合适型号的清漆;
(3)涂布速度过快,清漆未完全干透。
2.3UV油墨未完全干透。
造成原因
(1)UV灯坏或使用时间过长导致UV灯能量不足,通过更换灯管解决;
(2)不同厂家的油墨体系不同(即组分中树脂类型不同)相同的UV灯能量下干燥程度不同;可选择合适的UV油墨和通过印刷速度及UV灯关闭情况来控制;
(3)油墨墨层厚度(越厚越难干燥),可通过采用浓度高的印刷油墨印刷来改善;
(4)印刷颜色不同(深颜色尤其是黑色越难干燥)。
UV灯能量过高,导致油墨过度固化,油墨变脆,附着力降低,可通过降低固化能量和提高印刷速度来控制。
鐳射转移用UV油未完全干透,镭射转移用UV油中的溶剂与UV油墨或清漆涂层起化学反应。
造成原因:
(1)UV灯坏或使用时间过长导致UV灯能量不足,通过更换灯管解决;
(2)不同厂家的UV油体系不同(即采用的树脂不同)相同的UV灯能量下干燥程度不同,可选择合适型号与公司产品设备匹配的UV油;
(3)镭射压印转移车速太快,适当降低车速(一般控制在3000~5000张/小时,视产品及印张尺寸而定)。
3总结
镭射压印转移工艺已广泛应用于包装印刷产品领域,由于其工艺相对简单、环保、成本低、质量好受诸多企业青睐。
实践经验表明,造成银卡类纸张镭射转移放置一段时间后出现掉墨故障的原因很多,往往与生产过程的工艺条件、环境因素、工艺材料都有直接关系,这就要求从业人员要规范生产工艺条件、遵守规范作业流程,及时做好生产质量监控、物料检验。
参考文献
[1]陈勇.镭射压印转移工艺的发展及工艺要求[J].印刷技术,2012,(02).
[2]焦杰明.镭射压印转移工艺及其在烟包上的应用[J].印刷技术,2011,(04).。