铝合金压铸件综合技术条件拉力
压铸国家标准对照
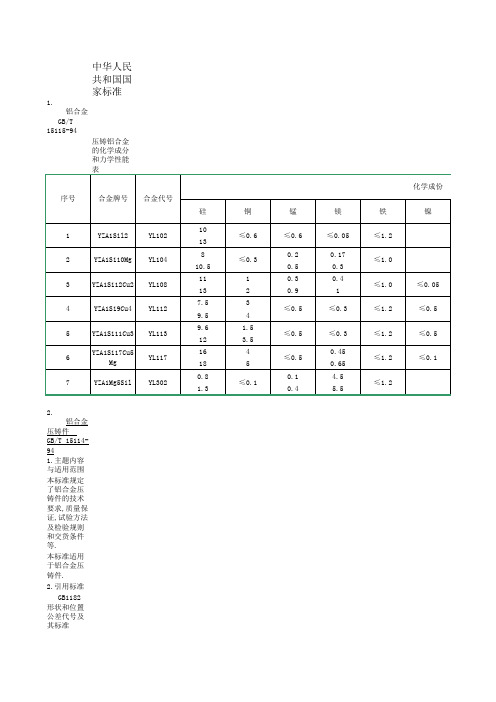
6.2 力学性能。
6.2.1 力学性能的检验频率应符合GB/T 13818中5.2.1有规定。
6.3 铸件表面质量应按3.2、4.5.2、4.5.3规定逐件检查。
6.4 铸件表面粗糙度按GB 6060.1的规定进行检测。
6.5铸果必须符合4.3的规定。
7 包装、运输、贮存
6.3压铸件的 包装,运输与 储存,由供需 双方商定.
(待续)
锌合金压 铸件1
1
主题内容与适用范围
本标准规定了锌合金压铸件分类、技术要求、试验方法、检验方法、检验规则、交货条件等。
本标准适用于锌合金铸件。
2
引用标准
GB 5678 铸造合金光谱分析取样方法
GB 6060.1
表面粗糙度比较样块 铸造表面
7.1 铸件的包装应保证在运输过程中和存放时间防止潮湿和机械损伤。
7.2 包装的标志应有:名称、数量、合金牌号、检验合印记和交付日记。
7.3 运输由双方商定。
附录A 锌合金压铸件铸造斜度(参考件)
Al 锌合金压铸件内腔的一般铸造斜度如下,铸件外壁铸造斜度为内腔度的1/2,见表Al。
表Al
内腔深度 (mm) 铸造斜度
3 承受国截荷 的零件和其 他零件
尺寸公差、 表面质量、 化学成分、 其它特殊要 求
表面质量、 化学成分、 尺寸公差
3.2 级别
铸件表面按使用范围分为三级(见表2)。
符号
使用范围 表面粗糙度
1 Y1
工艺要求高 Ra1.6
的表面:镀
、抛光、研
磨的表面相
对运动的配
合面,危险
应力区表面
2 Y2
要求在般或 Ra3.2
GB6060.5 表面粗糙度 比较样块
铝合金压铸技术要求
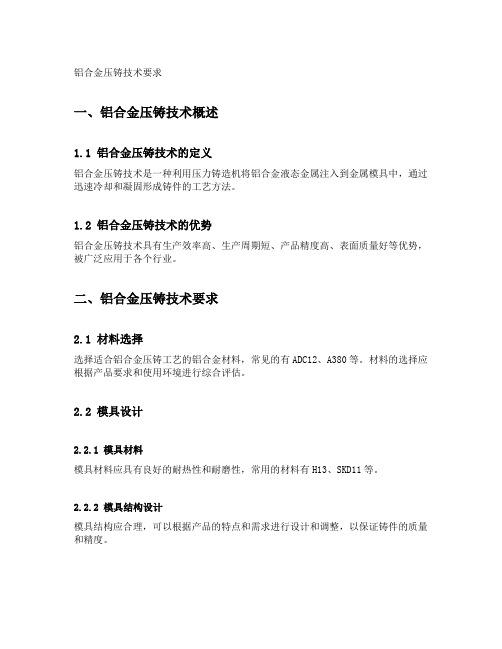
铝合金压铸技术要求一、铝合金压铸技术概述1.1 铝合金压铸技术的定义铝合金压铸技术是一种利用压力铸造机将铝合金液态金属注入到金属模具中,通过迅速冷却和凝固形成铸件的工艺方法。
1.2 铝合金压铸技术的优势铝合金压铸技术具有生产效率高、生产周期短、产品精度高、表面质量好等优势,被广泛应用于各个行业。
二、铝合金压铸技术要求2.1 材料选择选择适合铝合金压铸工艺的铝合金材料,常见的有ADC12、A380等。
材料的选择应根据产品要求和使用环境进行综合评估。
2.2 模具设计2.2.1 模具材料模具材料应具有良好的耐热性和耐磨性,常用的材料有H13、SKD11等。
2.2.2 模具结构设计模具结构应合理,可以根据产品的特点和需求进行设计和调整,以保证铸件的质量和精度。
2.3 注射设备2.3.1 压铸机选择根据产品的要求确定压铸机的型号和规格,包括锁力、注射压力等参数的选择。
2.3.2 注射系统注射系统包括注射缸、注射头、喷嘴等组成,其设计应合理,确保铝合金液态金属的注入和充填。
2.3.3 润滑系统润滑系统的设置对于铝合金压铸技术的稳定运行起着重要作用,应注意润滑剂的选择和使用。
2.4 工艺参数控制压铸工艺参数对于产品的质量和尺寸稳定性有很大的影响,应进行合理的控制和调整。
2.4.1 注射速度注射速度过快会导致铸件内部气孔、缺陷等问题,注射速度过慢会导致铝合金液态金属凝固不完全。
2.4.2 注射温度注射温度过高会导致铝合金液态金属粘度降低,流动性增强,但也会加快模具磨损。
注射温度过低则会导致液态金属凝固时间过长。
2.4.3 注射压力注射压力的控制对于铸件的密实性和表面质量有着重要影响,应根据产品要求进行精确控制。
2.4.4 注射时间注射时间应根据实际需要进行合理设置,以保证铝合金液态金属充填充实模腔。
2.5 热处理工艺铝合金压铸件在铸造成型后,经过热处理工艺可以改善其机械性能和物理性能,如固溶处理、时效处理等。
2.6 铸件表面处理铝合金压铸件的表面处理包括喷砂、喷涂、电镀等方法,以提高产品的外观质量和耐腐蚀性能。
DAZCZGYQ铝合金压铸件技术条件A
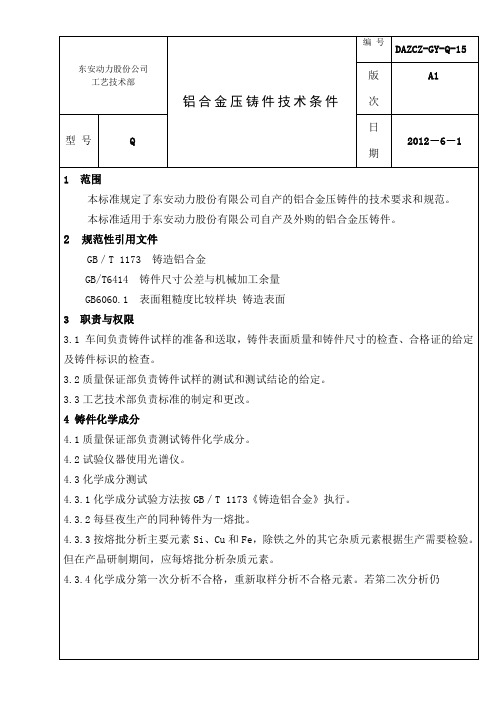
DABG-GY-6 1不合格,则铸件为不合格件。
4.3.5化学成分应符合表1要求。
表15 机械性能5.1质量保证部负责测试铸件机械性能。
5.2试验仪器使用拉伸试验机。
5.3机械性能测试5.3.1试验方法按按GB/T 1173《铸造铝合金》执行。
5.3.2每月取三根单铸试样测定合金机械性能,若有两根试样的机械性能符合表2规定时,则认为合格。
5.3.3第一次试验的三根试样中,若有两根试样的机械性能低于表2规定时,则认为不合格,但允许用加倍试样数量进行第二次试验。
第二次试验若有两根试样的机械性能不合格,但总平均值合格时,则认为合格;如不合格的试样多于两根,则机械性能不合格。
5.3.4允许用金属型铸造的标准试样测定合金的机械性能。
金属型试样的形状及尺寸应按GB/T 1173《铸造铝合金》的规定。
5.3.5每次试验后均允许采用压铸件本体试验,其指定部位切取试样的力学性能,不得低于单铸试样的75%。
切取部位未做规定时,由检验部门确定。
5.3.6若单铸试样不合格,铸件上切取的机械性能试样合格时,则该熔批铸件为合格件。
5.3.7由于试验本身的故障或试样上有目视可见的夹渣、气泡而造成试验结果不合格时,应补试样重新进行试验。
5.3.8机械性能应符合表2的规定。
6 硬度6.1检验员负责检测铸件硬度。
6.2试验仪器使用布氏硬度机。
6.3硬度试验方法按GB/T 1173《铸造铝合金》执行。
6.4硬度测试6.4.1按图纸的规定,对铸件进行硬度检查。
6.4.2铸件上检查硬度的部位,按毛坯图或控制计划中要求执行。
6.4.3按熔批对铸件硬度进行抽查,每熔批抽检不得少于2件。
6.4.4硬度值应符合表2规定。
6.4.5硬度检查不合格时,抽查数量加倍。
若再有不合格,铸件为不合格。
7压铸件尺寸7.1 质量保证部检查压铸件毛坯的尺寸。
7.2使用游标卡尺或其它简单、有效的自制工具。
7.3 使用测量工具对铸件尺寸进行检验。
7.4 压铸件尺寸7.4.1压铸件尺寸符合图样规定。
铝合金压铸技术要求

1、范围本标准规定了铝合金压铸件的技术要求、试验方法、检验规那么、交货条件等。
本标准适用于汽车发电机铝合金端盖压铸件。
2、引用标准GB6414铸件尺寸公差铝及铝合金化学分析方法GB288-87金属拉力试验法GB/T13822-92 压铸有色合金试样GB6060.5 外表粗造度比拟样块抛(喷)丸、喷吵加工外表3、技术要求3.1 压铸铝合金的牌号压铸铝合金采用UNS-A03800〔美国,日本ADC10〕可选用材料UNS-A03830 〔美国,日本ADC12〕化学成份见表1表1供给商可选择上述四种牌号的任何一种,如在生产过程中更换其它牌号,需重新进展样件鉴定。
一级回炉料:浇道、化学成份合格的废铸件,后加工次品等不含水分和油污。
二级回炉料:集渣包、坩埚底部剩料、退货废品、存放时间长〔超过10天〕的一级回炉料。
三级回炉料:飞边、溅屑、细小的碎料、带有油污的渣料、因化学成份报废的铸件、从铝渣中捡出的铝粒。
使用单一某级回炉料:一级回炉料最大使用量50%,二级回炉料最大使用量40%。
一级、二级回炉料混合使用:回炉料总量不超过40%,其中二级回炉料最大使用量20%。
三级回炉料:不能直接使用,必须经过重熔、精炼且化学成份分析合格后才能使用,其最大使用量10%,仅与铝锭混合使用。
小颗粒回炉料大块回炉料铝锭,如此循环。
3.2 力学性能采用单铸拉力试样检验,其力学性能应满足抗拉强度≥240Mpa,伸长率≥1%,HB85〔5/250/30〕。
试样尺寸及形状应符合GB/T 13822-92?压铸有色合金试样?的规定。
3.3 压铸件尺寸压铸件的几何形状和尺寸应符合铸件图的规定。
3.4 待加工外表用符号“〞标明,尖头指向被加工面。
例:0.5 表示该外表留有加工余量3.5 外表质量3.5.1 铸件清理后的外表质量铸件的浇口、飞边、溢流口、隔皮等应清理干净,但允许留有清理痕迹。
在不影响使用的情况下,因去除浇口、溢流口时所形成的缺肉或高出均不得超过壁厚的四分之一,并且不得超过1.5 mm。
QCT2721999汽车用铝合金铸件技术条件
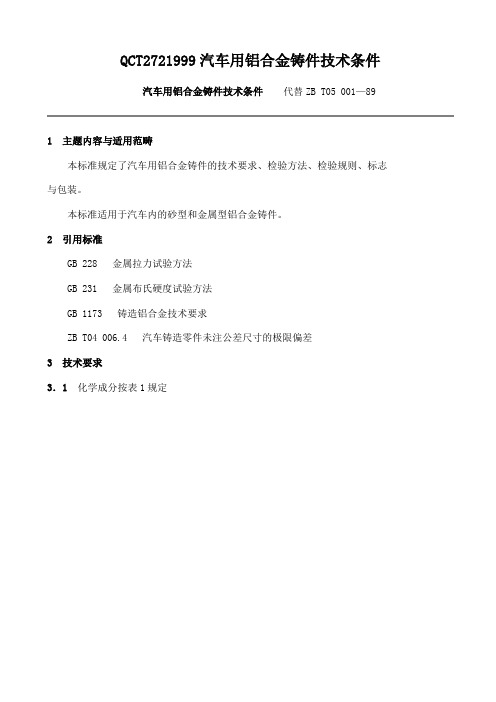
QCT2721999汽车用铝合金铸件技术条件汽车用铝合金铸件技术条件代替ZB T05 001—891 主题内容与适用范畴本标准规定了汽车用铝合金铸件的技术要求、检验方法、检验规则、标志与包装。
本标准适用于汽车内的砂型和金属型铝合金铸件。
2 引用标准GB 228 金属拉力试验方法GB 231 金属布氏硬度试验方法GB 1173 铸造铝合金技术要求ZB T04 006.4 汽车铸造零件未注公差尺寸的极限偏差3 技术要求3.1 化学成分按表1规定3.2 机械性能按表2规定3.3 铸件尺寸和几何形状应符合图样要求。
3.4 未注公差尺寸的极限偏差按ZB T04 006.4的规定。
3.5 表面质量3.5.1 砂型铸件表面粗糙度应不大于Ra25,金属型铸件应不大于Ra6.3,需经抛光阳极氧化处理的装饰性表面,粗糙度应不大于Ra1.6。
3.5.2 铸件表面应认真清理。
砂型铸件经修整后,除机械加工定位面外,允许有不高于1mm的浇口,凸瘤、毛刺等残痕。
3.5.3 铸件不承诺有欠铸、裂纹及机械加工时不能除去的缺陷。
3.5.4 铸件装饰表面不承诺有铸造模网状裂纹所形成的痕迹。
3.5.5 铸件不加工表面承诺存在和缺陷。
3.5.5.1 关于砂型铸造的铸件a.气孔和凹陷深度不大于1mm,其面积不大于10mm2。
b.铸件的最大轮廓尺寸不大于350mm时,气孔和缩孔深度不大于1mm,直径不大于3mm,数量不超过3处;当最大轮廓尺寸不大于350mm时,缺陷不超过6处,且在直径30mm范畴内不超过3处。
3.5.5.2 关于金属型铸造的铸件a.小缩孔和凹陷深度不大于0.25mm。
b.铸件分型面和滑动部分所形成的飞边不大于0.4mm,推杆痕迹不大于0.6mm。
c.在需磨光的表面上承诺有不阻碍工作性能的分散的多针孔。
d.铸件表面经清理后毛刺不大于±0.2mm。
e.经清理后毛孔刺不大于0.5mm,清理中所形成的痕迹深度不大于0.6mm。
DAZCZ-GY-Q-15铝合金压铸件技术条件(A)
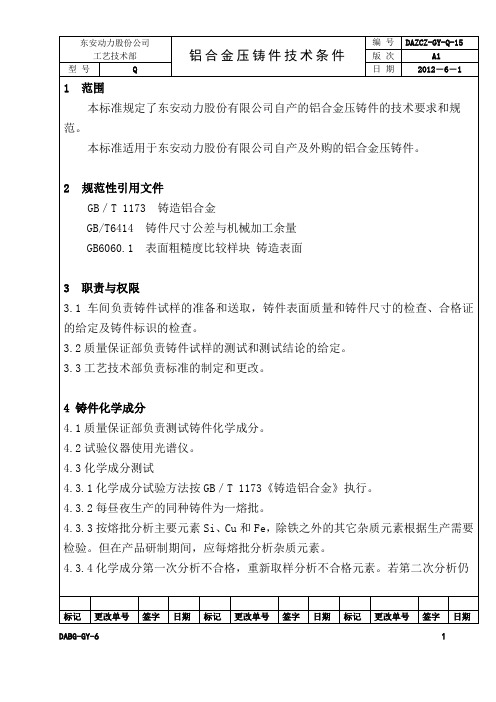
DABG-GY-6 1
不合格,则铸件为不合格件。
4.3.5化学成分应符合表1要求。
表1
5 机械性能
5.1质量保证部负责测试铸件机械性能。
5.2试验仪器使用拉伸试验机。
5.3机械性能测试
5.3.1试验方法按按GB/T 1173《铸造铝合金》执行。
5.3.2每月取三根单铸试样测定合金机械性能,若有两根试样的机械性能符合表2规定时,则认为合格。
5.3.3第一次试验的三根试样中,若有两根试样的机械性能低于表2规定时,则认为不合格,但允许用加倍试样数量进行第二次试验。
第二次试验若有两根试样的机械性能不合格,但总平均值合格时,则认为合格;如不合格的试样多于两根,则机械性能不合格。
5.3.4允许用金属型铸造的标准试样测定合金的机械性能。
金属型试样的形状及尺寸应按GB/T 1173《铸造铝合金》的规定。
5.3.5每次试验后均允许采用压铸件本体试验,其指定部位切取试样的力学性能,不得低于单铸试样的75%。
切取部位未做规定时,由检验部门确定。
5.3.6若单铸试样不合格,铸件上切取的机械性能试样合格时,则该熔批铸件为合格件。
5.3.7由于试验本身的故障或试样上有目视可见的夹渣、气泡而造成试验结
果不合格时,应补试样重新进行试验。
5.3.8机械性能应符合表2的规定。
表2。
压铸国家标准对照
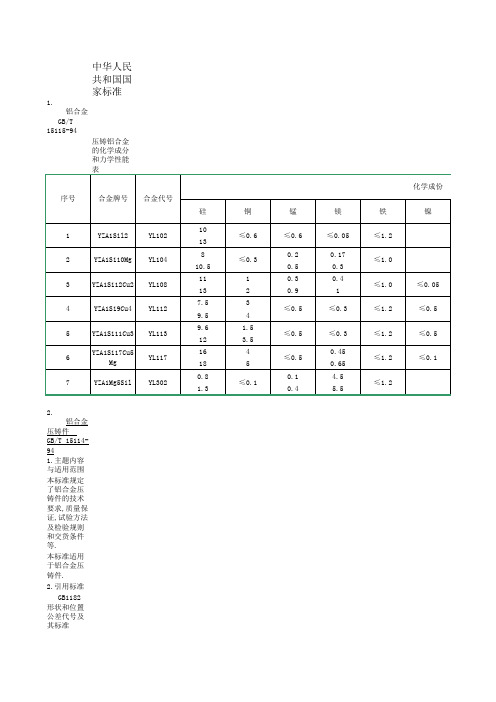
6.2 力学性能。
6.2.1 力学性能的检验频率应符合GB/T 13818中5.2.1有规定。
6.3 铸件表面质量应按3.2、4.5.2、4.5.3规定逐件检查。
6.4 铸件表面粗糙度按GB 6060.1的规定进行检测。
6.5铸件几何尺寸按批次抽验数量由供需双方商定,高验结果必须符合4.3的规定。
7 包装、运输、贮存
3.3.3压铸件 有形位公差 要求时,其标 注方法按 GB1182的规 定.
3.3.4压铸件 的尺寸公差 不包括铸造 斜度,其不加 工表面:包容 面以小端为 基准,有特殊 规定和要求 时,须在图样 上注明.
3.4压铸件需 要机械加工 时,其加工余 量按 GB/T11350的 规定执行.若 有特殊规定 和要求时,其 加工作量须 在图样上注 明.
中华人民 共和国国 家标准
1. 铝合金
GB/T 15115-94
压铸铝合金 的化学成分 和力学性能 表
序号
合金牌号 合金代号
1
YZA1Sil2
YL102
2
YZA1Si10Mg YL104
3
YZA1Si12Cu2 YL108
4
YZA1Si9Cu4 YL112
5
YZA1Si11Cu3 YL113
6
YZA1Si17Cu5 Mg
最大深度 铸造斜度
1°30´
9
14
18
1°20´
1°10´
1°
20
32
40
50
80
0°50´
0°45´
0°40´
0°30´
A3 锌合金压铸件的最小铸造斜度见表A3 表A3
铸件内腔 0°20´
铸件外壁 0°10´
压铸国家标准对照
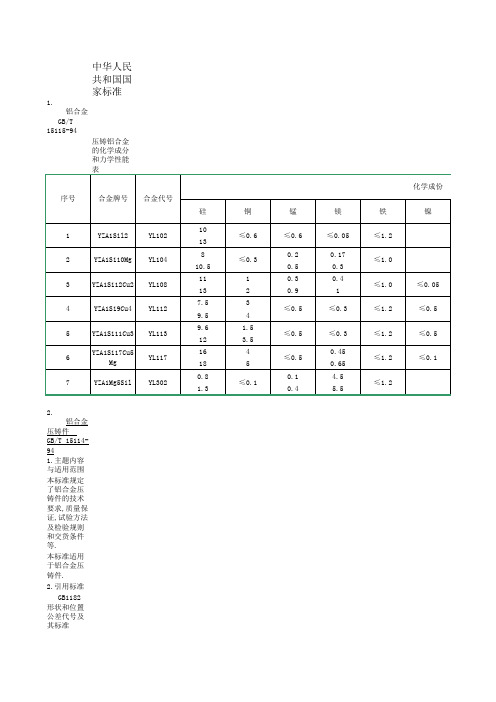
4.2根据压铸 生产特点,规 定一个检验 批量是指每 台压铸设备 在正常操作 情况下一个 班次的生产 量,设备,化 学成分,铸型 和操作连续 性的任何重 大变化都应 被认为是新 是一个批量 开始.
供方对每批 压铸件都要 随机或统计 地抽样检验, 确定是否符 合全部技术 要求和合同 或铸件图样 的规定要求, 检验结果应 予以记录.
附录B
表B 锌合金压铸件表面质量分级
序号
缺陷名称 检验范围 表面质量级别
1极
2极
1 花纹麻面有 色斑点
2 流痕
三者面积不 超过总面积 的百分数% 深度,mm
5 0.05
3极 25
0.07
说明 40 0.15
3 冷隔
≤ 面积不大于 总面积百分 数,% 深度,mm 不允许
≤
5
15
30
1/5壁厚
1/4壁厚
≤6 2°30´
>6-8 2°
>8-10 1°45´
>10-15 1°30´
>15-20 1°15´
>20-30 1°
>30-36 0°45´
A2 锌合金压铸件的铸孔直径与最大深度的关系及其铸造斜度的规定见表A2
表A2 孔的直径 ≤3
>3-4
>4-5பைடு நூலகம்
>5-6
>6-8
>8-10
>10-12 >12-16
4质量保证
4.1当供需双 方合同或协 议中有规定 时,供方对合 同中规定的 所有试验或 检验负责.合 同或协议中 无规定时,经 需方同意,供 方可以用自 已适宜的手 段执行本标 准所规定的 试验和要求, 需方有权对 标准中的任 何试验和检 验项目进行 检验,其质量 保证标准应 根据供需双 方之间的协 议而定.
锌合金、铜合金、铝合金压铸件技术条件

中华人民共和国第一机械工业部部标准锌合金、铝合金、铜合金压铸件技术条件JB 2702—80北京1981中华人民共和国第一机械工业部部标准JB 2702—80 锌合金、铝合金、铜合金压铸件技术条件本标准适用于机电、仪表、汽车、拖拉机等机械工业产品的锌合金、铝合金、铜合金压铸件(以下简称铸件)。
对有特殊要求的铸件,经商议后应在图样中注明。
一、铸件分类及级别1.铸件按使用要求分为两类,见表1。
2.铸件表面质量按使用范围分为三级,见表2。
3.铸件的类别和表面质量的级别应在图样中注明,表示方法如下:Ⅱ-∽铸件表面质量级别铸件分类类别铸件标准代号如有更高要求的部位应在图样中有关面处分别注明。
4.未注明铸件类别、级别和尺寸精度者,均按本标准相关的最低级别处理。
二、尺寸精度5.铸件线性尺寸公差才选用中华人民共和国第一机械工业部发布 1 9 8 1 年 1 月 1 日实施一机部沈阳铸造研究所提出上海电器压铸三、上海电表厂等起草共11页第2页 JB 2702—80⑴铸件的基本尺寸公差按表3选用。
铸件受分型面或模具活动部位影响的尺寸应按表4、表5规定,在基本尺寸公差上再加附加公差。
铸件基本尺寸公差表3线性尺寸受分型面影响时的附加公差表4线性尺寸受模具活动部位影响时的附加公差表5注:一模多铸时,铸件分型面上的投影面积为各铸件投影面积之和附加公差应用示例:JB 2702—80 共11页第3页1 铝合金压铸件的尺寸A为3+0.12mm(基本公差按7级精度),模具活动部位由成形滑块构成,其投影面积为34cm2,由表5查得其附加公差为0.20mm,则A的尺寸公差应为0.12+0.20=0.32(mm) 。
2 在同一铸件上尺寸B为2.5+0.12mm(基本公差按7级精度),模具活动部位由滑块型芯构成,型芯直径为20mm,则其投影面积为3.14cm2,由表5查得其附加公差为0.15mm,则B处的尺寸公并为+0.12/-0.15。
⑵尺寸公差带的位置a.不加工的配合尺寸,孔取正(+),轴取负(-)。
铝合金压铸件综合技术条件(拉力)

1? 主题内容与适用范围? 本标准根据GB 1173及GB 9438的相关内容,规定了铝合金铸件的分类和铸件的外观质量、内在质量以及铸件修补等内容的技术要求与检验规则等。
? 本标准适用于铝硅系合金铸件的砂型铸造、特种铸造(不含压力铸造)。
2? 一般规定2.1 合金牌号2.1.1 铸造铝合金牌号由铝及主要合金元素的化学成分符号组成。
主要合金元素后面跟有表示其名义百分含量的数字(名义百分含量为该元素的平均百分含量的修约化整值)。
如果合金化元素的名义百分含量不小于1,该数字用整数表示;如果合金化元素的名义百分含量小于1,一般不标数字,必要时可用一位小数表示。
? 在合金牌号前面冠以字母“Z”(“铸”字汉语拼音第一个字母)表示属于铸造合金。
2.1.2 若合金化元素多于两个,除对表示合金的本质特性是必不可少的外,不必把所有的合金化元素都列在牌号中。
2.1.3 杂质含量较一般合金低、性能高的优质合金,在其牌号后面附加字母“A”。
2.1.4 在牌号中主要合金化元素按名义百分含量的递减次序排列,当名义百分含量相等时,按其化学符号字母顺序排列。
2.2 合金代号? 本标准中合金代号由字母“Z”、“L”(它们分别是“铸”、“铝”的汉语拼音第一个字母)及其后面的三个阿拉伯数字组成。
“ZL”后面第一个数字表示合金系列,其中“1”表示铝硅系列合金,第二、三两个数字表示顺序号。
优质合金,在其代号后面附加字母“A”。
引用顾客提供的材料标准时,其代号按原用代号不变。
2.3 合金铸造方法、变质处理代号? S——砂型铸造? J——金属型铸造? R——熔模铸造? K——壳型铸造? B——变质处理2.4 合金状态代号? F——铸态? T1——人工时效? T2——退火? T4——固溶处理+自然时效? T5——固溶处理+不完全人工时效? T6——固溶处理+完全人工时效? T7——固溶处理+稳定化处理T8——固溶处理+软化处理2.5 数字修约规则? 合金牌号中合金化元素的名义百分含量、合金化学成分、合金性能等数字修约按GB 1.1中附录C规定。
压铸件通用验收技术条件

压铸件通用验收技术条件(试行)定义:压铸件—指金属材料在一定的温度、压力条件下,通过专用压力机以液体或高粘流态压入成型模具,经一定时间的冷却后成形的零件。
本文件为指导性技术文件。
常用材料及牌号:1.镁合金:AZ91D、YM52.铝合金:A360、 YL108、YL104、YL112成型后铸件的验收技术条件:1.曲翘度:≤0.2/100mm2.有外观要求的零件表面要求:① 无明显熔接痕(允许有看得见摸不出的痕迹)② 不允许有鼓泡、凹痕、针孔、沙眼、冷料块、夹渣③ 不允许有裂痕、毛刺、缺口、裸露的气泡④ 未注边角倒角0.5*45°⑤ 浇口位置应修锉平整肉眼看不出明显的浇口特征⑥ 所有顶杆痕不允许凸出表面,但允许深入表面≤0.2mm,其周边不允许有飞边⑦ 光洁度要求高于Ra1.6以上的应用0#砂纸及400#金相砂纸分别打磨到图纸要求⑧ 未注表面粗糙度:铝合金Ra3.2—6.3镁合金Ra1.6—3.23.无外观要求的零件表面要求:按各类压铸件表面质量(JB2702—80)2级质量标准执行4.螺纹的处理:内外螺纹允许后加工做出(但必须做出底孔)5.未注公差:按GB6414—86铸件尺寸公差CT5级执行6.未注形位公差的要求:① 铸件未加工前的平面度公差:≤25为0.1、≤60为0.15、≤100为0.2、≤160为0.25、≤250为0.3、≤400为0.4② 铸件未加工前的平行度公差:≤25为0.15、≤60为0.2、≤160为0.3、≤250为0.45、≤400为0.65③ 铸件未加工前的同轴度公差:≤25为0.15、≤60为0.25、≤160为0.35、≤250为0.45、≤400为0.65、7.铸件加工后的形位公差按图要求执行8.零件上不加工孔类要素的尺寸一律指小端,轴类要素的尺寸一律指大端9.表面处理后技术要求:定义:—表面处理:指完成压铸后的零件经机械修正后进行的下列加工:① 氧化处理② 电镀处理③ 非金属喷涂④ 表面喷漆或电泳漆9.1.镀(涂)、或氧化层外观要求:① 色泽均匀、无明显色差、流痕、气泡、针孔、剥落、露底② 异物、杂质:影响外观的零件表面不允许存在,非重要表面每250mm距离内≤0.6mm的异物、杂质少于5点可视为合格③ 未注镀(涂)、或氧化层厚度≤0.03mm9.2.镀(涂)、或氧化层的附着力要求:① 每批次做一块附着力检测样板(厚度=1-2mm 100*40随被检测的批次零件同时表面处理经检测镀(涂)、或氧化层厚度合格后作为合格检测样板备用② 在样板的一个角离边缘5mm、15*15范围内用美工刀间隔1mm井字形划线(必须划穿镀(涂)、或氧化层)后用指甲盖或橡皮擦来回刮檫20次无剥落、露底则为合格③ 在样板的1/2处为界限折弯90°镀(涂)、或氧化层无开裂、剥落为合格9.3.耐腐蚀要求:用刷子蘸Kodak冲卷、冲纸的彩显、漂白药水刷于(涂)、或氧化层表面1小时后用水清洗檫干,检查镀(涂)、或氧化层应无龟裂、鼓泡但允许有轻微变色10.标志及包装:10.1.零件用硬纸盒包装,并用密封塑料袋及干燥剂作为内包装,盒上应有零件编号、规格、合格证,并与盒内零件相一致。
铝合金压铸件一般技术要求

铝合金压铸件一般技术要求铝合金压铸件是利用铝合金熔体通过高压注射进入金属模具中,通过自身的凝固过程形成的零件。
它具有良好的综合性能,广泛应用于各个领域,如汽车、航空航天、电子等。
为了保证铝合金压铸件的质量和可靠性,有一系列一般技术要求需要遵守。
首先,铝合金压铸件的设计要合理。
合理的设计能保证零件的结构和尺寸满足使用要求,避免因结构设计不当而导致的铝合金压铸件质量问题。
设计时应考虑铝合金材料的特性和成型工艺,合理布置加强筋和放大壁厚等措施,确保压铸件有足够的强度和刚度。
其次,材料的选择要合适。
铝合金压铸件一般采用高强度、高导热性的铝合金材料,如ADC12、A380等。
材料的选择要符合使用环境的要求,具有良好的耐热、耐腐蚀、耐磨损和耐腐蚀性能。
材料的选择还需要考虑成本因素,以保证生产的经济性。
第三,模具的制造要精确。
模具的精度和质量对铝合金压铸件的成型质量起着重要的影响。
模具制造应严格按照设计要求进行,尺寸精度应达到零件的使用要求。
模具材料一般选用精密,耐磨耐热的材料,如合金钢、硬质合金等,以保证模具的耐用性和寿命。
第四,操作工艺要规范。
铝合金压铸件的压铸过程需要控制压铸机的参数,如注射速度、注射压力和注入时间等。
同时,还需要注意合金的热处理和退火工艺,以提高原材料的性能和细化晶粒。
此外,还需要对压铸件进行后处理,如除霜、抽调、清洗和表面处理等,以保证铝合金压铸件的表面质量和使用寿命。
最后,质量检查要全面。
对铝合金压铸件进行全面的质量检查是确保产品质量的重要手段之一、常用的检查方法有外观检查、尺寸检查、物理性能测试、金相组织分析等。
通过严格的质量检查,可以及时发现和纠正问题,保证产品的合格率和一致性。
综上所述,铝合金压铸件的一般技术要求涉及设计、材料、模具、操作工艺和质量检查等方面,通过科学的设计和精确的制造工艺,可以生产出质量可靠的铝合金压铸件,满足不同领域的使用需求。
铝合金压铸件一般技术要求
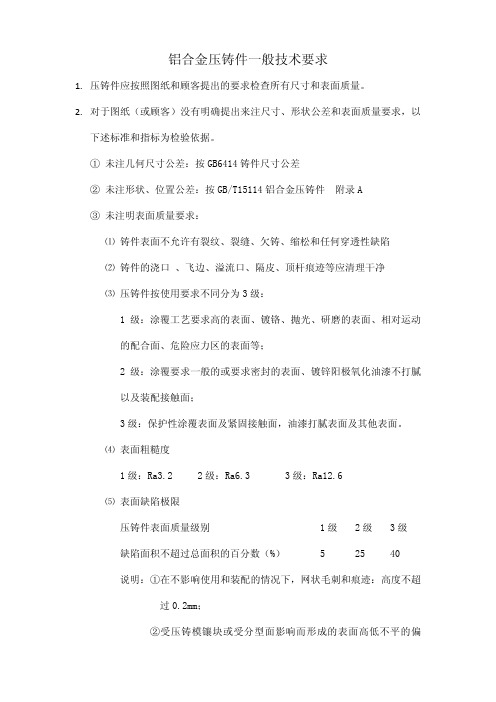
铝合金压铸件一般技术要求1.压铸件应按照图纸和顾客提出的要求检查所有尺寸和表面质量。
2.对于图纸(或顾客)没有明确提出来注尺寸、形状公差和表面质量要求,以下述标准和指标为检验依据。
①未注几何尺寸公差:按GB6414铸件尺寸公差②未注形状、位置公差:按GB/T15114铝合金压铸件 附录A③未注明表面质量要求:⑴铸件表面不允许有裂纹、裂缝、欠铸、缩松和任何穿透性缺陷⑵铸件的浇口 、飞边、溢流口、隔皮、顶杆痕迹等应清理干净⑶压铸件按使用要求不同分为3级:1级:涂覆工艺要求高的表面、镀铬、抛光、研磨的表面、相对运动的配合面、危险应力区的表面等;2级:涂覆要求一般的或要求密封的表面、镀锌阳极氧化油漆不打腻以及装配接触面;3级:保护性涂覆表面及紧固接触面,油漆打腻表面及其他表面。
⑷表面粗糙度1级:Ra3.2 2级:Ra6.3 3级:Ra12.6⑸表面缺陷极限压铸件表面质量级别 1级 2级 3级缺陷面积不超过总面积的百分数(%) 5 25 40说明:①在不影响使用和装配的情况下,网状毛刺和痕迹:高度不超过0.2mm;②受压铸模镶块或受分型面影响而形成的表面高低不平的偏差,不超过相关的公差尺寸;③推杆痕迹表面凸出或凹入铸件表面的深度,一般为±0.2mm;⑹表面质量要求(见附表)⑺挫痕:目视挫痕应均匀、一致,不允许有明显的凹凸。
经锉加工的表面和未经锉加工的表面允许有角度,但角度应在10°以内;⑻变形:压铸件成型后,如有变形应进行调整,经调整后的压铸件表面不允许有明显的打击痕迹。
调整部分的平面度:0.2mm;⑼对于顾客的特殊要求,要形成相应的工艺文件,规定其相关的工艺过程和检验方法。
总工办2003年4月附表: 缺陷名称 缺陷范围表面质量级别 备注 1级2级 3级 流痕深度(mm )≤ 0.05 0.07 0.15 面积不超过总面积的百分数515 30冷隔深度(mm )≤ 不允许1/5壁厚 1/4壁厚 1. 在同一部分对应出不允许同时存在 2. 长度是指缺陷流向的展开长度长度不大于铸件的最大轮廓尺寸的(mm ) 1/101/5所在面上的不允许超过的数量 2处 2处 离铸件边缘距离(mm )≥ 4 4 两冷隔间距(mm )≥10 10 拉伤深度(mm )≤ 0.05 0.1 0.25 除一级表面外,浇道部位允许增加一倍 面积不超过总面积的百分数35 10 凹陷 凹入深度(mm ) 0.10.3 0.5 粘附物痕迹整个铸件缺陷不允许超过 不允许1处 2处 占带缺陷的表面面积的百分比5 10气泡平均直径≤3mm1.每100cm 2缺陷个数不超过 不允许 1 2 允许两种气泡同时存在,但大气泡不超过3个,总数不超过10个。
铝合金压铸件一般技术要求

铝合金压铸件一般技术要求铝合金压铸件这玩意儿,在咱们的日常生活和工业生产里那可真是太常见啦!小到一个精致的手机外壳,大到汽车发动机的零部件,都可能有它的身影。
咱先来说说铝合金压铸件的材质要求吧。
这铝合金啊,可不能是随随便便的材料。
它得有足够的强度和韧性,就像一个强壮又灵活的运动员,既能承受住压力,又不会轻易折断。
比如说,有一次我在一个工厂里看到师傅们在检测铝合金的成分,那叫一个仔细!拿着各种仪器,一点点分析,就怕有一点点杂质影响了最终的质量。
再说说尺寸精度吧。
这可太重要啦!要是尺寸不对,那整个零件可能就没法用了。
就好比你盖房子,砖头的大小不合适,那这房子能结实吗?我曾经看到过一个因为压铸件尺寸偏差导致组装不顺利的情况,工人们在那着急得直挠头,真是让人印象深刻。
表面质量也是不容忽视的。
这表面得光滑平整,不能有气孔、砂眼之类的缺陷。
想象一下,你买了个漂亮的铝合金制品,结果表面坑坑洼洼的,多闹心啊!有一回我看到一个精美的铝合金工艺品,那表面简直就像镜子一样光滑,让人爱不释手。
还有啊,铝合金压铸件的内部组织也得均匀致密。
不然的话,在使用过程中就容易出现裂缝或者疲劳损坏。
这就好像是一块蛋糕,如果里面有的地方松软,有的地方硬邦邦,一掰就断啦。
另外,对于铝合金压铸件的力学性能也有一定的要求。
它得有足够的硬度和抗拉强度,这样才能在各种环境下正常工作。
我记得有一次看到一个测试铝合金压铸件硬度的实验,那个测试仪器压下去的瞬间,真让人紧张,就盼着能达到标准。
总之,铝合金压铸件的一般技术要求那是相当严格的。
每一个环节都不能马虎,只有这样,才能生产出高质量的铝合金压铸件,为我们的生活和工作提供可靠的保障。
所以啊,不管是生产厂家还是使用者,都得对这些技术要求心里有数,才能让铝合金压铸件发挥出它们最大的作用!。
铝合金压铸件的标准
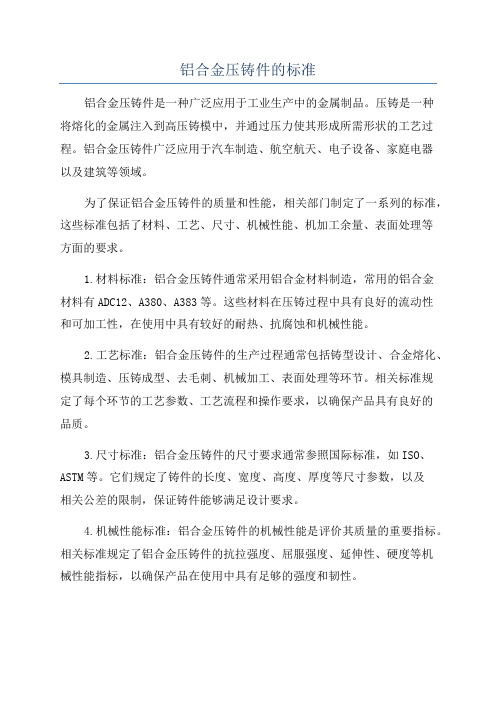
铝合金压铸件的标准铝合金压铸件是一种广泛应用于工业生产中的金属制品。
压铸是一种将熔化的金属注入到高压铸模中,并通过压力使其形成所需形状的工艺过程。
铝合金压铸件广泛应用于汽车制造、航空航天、电子设备、家庭电器以及建筑等领域。
为了保证铝合金压铸件的质量和性能,相关部门制定了一系列的标准,这些标准包括了材料、工艺、尺寸、机械性能、机加工余量、表面处理等方面的要求。
1.材料标准:铝合金压铸件通常采用铝合金材料制造,常用的铝合金材料有ADC12、A380、A383等。
这些材料在压铸过程中具有良好的流动性和可加工性,在使用中具有较好的耐热、抗腐蚀和机械性能。
2.工艺标准:铝合金压铸件的生产过程通常包括铸型设计、合金熔化、模具制造、压铸成型、去毛刺、机械加工、表面处理等环节。
相关标准规定了每个环节的工艺参数、工艺流程和操作要求,以确保产品具有良好的品质。
3.尺寸标准:铝合金压铸件的尺寸要求通常参照国际标准,如ISO、ASTM等。
它们规定了铸件的长度、宽度、高度、厚度等尺寸参数,以及相关公差的限制,保证铸件能够满足设计要求。
4.机械性能标准:铝合金压铸件的机械性能是评价其质量的重要指标。
相关标准规定了铝合金压铸件的抗拉强度、屈服强度、延伸性、硬度等机械性能指标,以确保产品在使用中具有足够的强度和韧性。
5.机加工余量标准:铝合金压铸件通常需要进行进一步的机械加工,比如铣削、切割、钻孔等。
相关标准规定了机加工余量的限制,以确保在机加工过程中不会影响铝合金压铸件的尺寸和性能。
6.表面处理标准:铝合金压铸件在生产后通常需要进行表面处理,以提高其耐腐蚀性、耐磨性和美观度。
常用的表面处理方法包括喷涂、阳极氧化、电泳涂装等。
相关标准规定了表面处理的方法、工艺和要求,以确保产品具有所需的表面性能。
总结起来,铝合金压铸件的标准涵盖了材料、工艺、尺寸、机械性能、机加工余量和表面处理等方面的要求,以确保产品的质量和性能。
这些标准不仅适用于压铸生产厂家,也为用户提供了选择和评估铝合金压铸件的指导依据。
铝合金压铸件检验标准
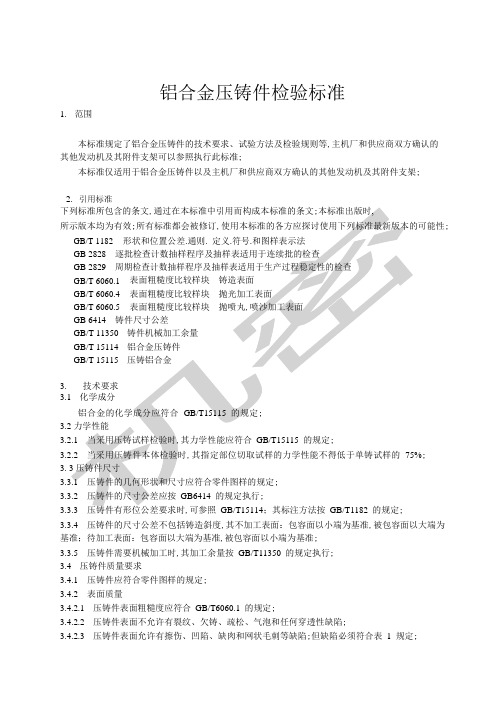
铝合金压铸件检验标准1.范围本标准规定了铝合金压铸件的技术要求、试验方法及检验规则等,主机厂和供应商双方确认的其他发动机及其附件支架可以参照执行此标准;本标准仅适用于铝合金压铸件以及主机厂和供应商双方确认的其他发动机及其附件支架;2.引用标准;3.;3.3.4压铸件的尺寸公差不包括铸造斜度,其不加工表面:包容面以小端为基准,被包容面以大端为基准;待加工表面:包容面以大端为基准,被包容面以小端为基准;3.3.5压铸件需要机械加工时,其加工余量按GB/T11350的规定执行;3.4压铸件质量要求3.4.1压铸件应符合零件图样的规定;3.4.2表面质量3.4.2.1压铸件表面粗糙度应符合GB/T6060.1的规定;3.4.2.2压铸件表面不允许有裂纹、欠铸、疏松、气泡和任何穿透性缺陷;3.4.2.3压铸件表面允许有擦伤、凹陷、缺肉和网状毛刺等缺陷;但缺陷必须符合表1规定;表1压铸件表面质量要求3.4.4.1 压铸件机械加工螺纹的头两扣不允许有任何缺陷,其余部分螺纹不允许有表3所规定的孔穴缺陷;表3机械加工螺纹规定的孔穴缺陷范围3.4.4.2 压铸件不铸底孔加工后的螺纹表面质量见表4的规定;表4不铸底孔加工后的螺纹表面质量3.4.5 压铸件机械加工孔加工后表面的孔穴规定范围见表5;3.4.7 其它性能要求应符合GB/T15114的规定;4试验方法及检验规则4.1化学成分4.1.1铝合金化学成分的检验方法,检验规则和复检应符合GB/T15115的规定;4.1.2化学成分的试样也可取自压铸件,但必须符合GB/T15115的规定;4.2力学性能4.2.1力学性能的检验方法,检验频率和检验规则应符合GB/T15115的规定;4.2.2采用压铸件本体为试样时,切取部位的尺寸、测试形式由供需双方商定;4.3压铸件几何尺寸的检验可按检验批量抽检或按GB2828、GB2829的规定进行,检验结果应符合本标准3.3的规定;4.4压铸件表面质量的出厂检验应逐件检查,检验结果应符合本标准的规定;4.5压铸件表面粗糙度按GB/T6060.1的规定执行;4.6压铸件需抛光加工的表面按GB/T 6060.4的规定执行;4.7压铸件需喷丸、喷沙加工的表面按GB/T 6060.5的规定执行;4.8压铸件内部质量的试验方法及检验规则可以包括:X射线照片、无损探伤试验、金相图片和5。
有色金属压铸件技术条件1

编号:GC/JS058-2003中山国驰摩托车实业有限公司1主题内容与适用范围本技术条件规定了摩托车用铝合金、锌合金的压铸件的分类、牌号、化学成分、机械性能、尺寸、外观缺陷等。
本技术条件适用于摩托车、轻便摩托车用铝合金、锌合金的压铸件的铸造与检验,其它有色金属的压铸件亦应参照使用。
2引用标准GB 1173 铸造铝合金技术条件GB 1175 铸造锌合金GB 2828 逐批检查计数抽样程序及抽样表(适用于连续批的检查)GB 6414 铸件尺寸公差3分类3.1 铸件按使用要求分为三类,其类别的划分与各类的检验项目应符合表1。
3.2 铸件的类别应在图纸中注明,凡未注明类别的均按Ⅲ类处理。
4牌号、化学成分、机械性能编号:GC/JS058-2003中山国驰摩托车实业有限公司铝合金应符合GB 1173,锌合金应符合GB 1175之规定。
有特殊要求者需在图样中注明。
5尺寸5.1 铸件的尺寸应符合产品图样或铸件图样的规定。
5.2 铸件的尺寸公差应在产品图样或铸件图样中注明,凡未注明的尺寸公差均按GB 6414 GT6。
5.3 凡产品图样或铸件图样中未注明的拨模斜度按表2表25.6 拨模斜度的取法按以下原则处理:a 待加工面增大壁厚,内表面控制大端尺寸,外表面控制小端尺寸。
b 非加工面增大壁厚,内表面控制小端尺寸,外表面控制大端尺寸。
c 铸件因拨模斜度影响装配要求时,应放加工余量。
5.7 模具镶嵌块引起的凹凸不平和模具错型必须在尺寸公差内。
6外观缺陷3.26.1 铸件需进行外观缺陷检查,铸件的表面粗糙度为6.2 铸件的顶杆和浇冒口不得设在暴露面上。
6.3 顶杆痕迹在非加工表面只允许凹下,其值不大于0.5mm,在加工表面应符合铸件图样的要求。
6.4 浇冒口应切除,其方法不限,但采用气割时应在热处理前进行。
浇冒口余根在非加工面上应打磨齐平,允许打磨部位比原表面有平缓的凸起或凹下,其值不大于0.5mm,在加工面上应符合铸件图样的规定。
铝合金拉力试验标准

铝合金拉力试验标准铝合金是一种常见的金属材料,具有较高的强度和轻量化的特点,因此在工业制造领域得到广泛应用。
而铝合金的拉力试验是评价其机械性能的重要指标之一,对于制定合理的拉力试验标准具有重要意义。
首先,铝合金拉力试验的标准需要明确试验的目的和要求。
通过拉力试验可以评估铝合金的抗拉强度、屈服强度、延伸率等性能指标,因此标准需要明确这些指标的测定方法和要求。
同时,标准还应包括试验样品的制备、试验设备的选择和校准、试验过程的操作规程等内容,以确保试验结果的准确性和可比性。
其次,标准需要规定试验样品的制备方法。
铝合金拉力试验的样品通常为平行长度为200mm,宽度为20mm的试样,标准需要规定试样的制备方法、尺寸公差要求、表面处理要求等内容,以确保试样的质量和一致性。
另外,标准还需要规定试验设备的选择和校准要求。
拉力试验机是进行铝合金拉力试验的关键设备,标准需要规定试验机的选择原则、技术指标要求、校准方法和周期等内容,以确保试验机的准确性和可靠性。
此外,标准还需要明确试验过程的操作规程。
试验过程中的操作规程直接影响试验结果的准确性,标准需要规定试验前的准备工作、试验过程中的操作要求、数据记录和处理方法等内容,以确保试验过程的可控性和可重复性。
最后,标准还需要规定试验结果的表达和分析方法。
标准需要规定试验结果的表达形式、数据处理方法、结果分析和判定标准等内容,以便工程师和设计师能够准确理解试验结果并进行合理的应用。
综上所述,铝合金拉力试验标准的制定需要考虑试验目的和要求、试验样品的制备、试验设备的选择和校准、试验过程的操作规程以及试验结果的表达和分析方法等内容,以确保试验结果的准确性和可比性。
只有制定合理的试验标准,才能有效评估铝合金材料的机械性能,为工程设计和生产提供科学依据。
压铸铝合金构件技术条件

压铸铝合金构件技术条件他那脸啊,被车间里的灯光照得明晃晃的,脸上的皱纹像是被岁月用刻刀精心雕琢过,一道一道的。
每次他检查构件的时候,眉头就紧紧皱着,就像两座小山丘挤到了一块儿。
嘴里还嘟囔着:“这压铸铝合金构件啊,技术条件可是一点都不能含糊。
”我就问他:“老伙计,这技术条件到底咋个讲究法呢?”他就开始跟我唠起来了。
他说啊,这压铸铝合金构件首先材料就不能马虎。
就好比做饭,你得先选好食材一样。
那铝合金的纯度啊,配比啊,都得按照严格的标准来。
稍微差一点,这构件就可能出大问题。
他一边说一边拿起来一个构件,对着灯光仔细地瞧。
他说:“你看这表面,得光滑平整,不能有啥瑕疵。
要是有个小坑洼或者凸起,那在实际使用的时候,就可能是个大隐患。
”我凑近了看,那构件在灯光下反射着光,真就像一面镜子似的,稍微有点毛病都能瞅出来。
还有啊,这构件的尺寸那也是精确到不能再精确了。
他拿着个小尺子,在构件上量来量去,眼睛都快贴到尺子上了。
他说:“差一毫米都不行,这就像人的衣服,大一点小一点穿着都不得劲。
”我就好奇了,又问他:“老伙计,这技术条件这么严格,是不是特别难搞啊?”他把构件小心翼翼地放好,直起腰来,捶了捶背说:“可不是嘛,这就像走钢丝,每一步都得稳稳当当的。
但是呢,这也有乐趣。
每次做出一个完全符合技术条件的构件,就像自己生了个大胖小子一样高兴。
”他在这个车间里待了大半辈子了,对这些构件就像对自己的孩子一样。
他说:“这压铸铝合金构件啊,是有灵魂的。
只要按照技术条件一丝不苟地做,这构件就能在它该发挥作用的地方好好干活。
”我听着他的话,也好像能看到那些构件在各种各样的设备里欢快地工作着,像一个个听话的小士兵一样。
- 1、下载文档前请自行甄别文档内容的完整性,平台不提供额外的编辑、内容补充、找答案等附加服务。
- 2、"仅部分预览"的文档,不可在线预览部分如存在完整性等问题,可反馈申请退款(可完整预览的文档不适用该条件!)。
- 3、如文档侵犯您的权益,请联系客服反馈,我们会尽快为您处理(人工客服工作时间:9:00-18:30)。
1 主题内容与适用范围本标准根据GB 1173及GB 9438的相关内容,规定了铝合金铸件的分类和铸件的外观质量、内在质量以及铸件修补等内容的技术要求与检验规则等。
本标准适用于铝硅系合金铸件的砂型铸造、特种铸造(不含压力铸造)。
2 一般规定2.1 合金牌号2.1.1 铸造铝合金牌号由铝及主要合金元素的化学成分符号组成。
主要合金元素后面跟有表示其名义百分含量的数字(名义百分含量为该元素的平均百分含量的修约化整值)。
如果合金化元素的名义百分含量不小于1,该数字用整数表示;如果合金化元素的名义百分含量小于1,一般不标数字,必要时可用一位小数表示。
在合金牌号前面冠以字母“Z”(“铸”字汉语拼音第一个字母)表示属于铸造合金。
2.1.2 若合金化元素多于两个,除对表示合金的本质特性是必不可少的外,不必把所有的合金化元素都列在牌号中。
2.1.3 杂质含量较一般合金低、性能高的优质合金,在其牌号后面附加字母“A”。
2.1.4 在牌号中主要合金化元素按名义百分含量的递减次序排列,当名义百分含量相等时,按其化学符号字母顺序排列。
2.2 合金代号本标准中合金代号由字母“Z”、“L”(它们分别是“铸”、“铝”的汉语拼音第一个字母)及其后面的三个阿拉伯数字组成。
“ZL”后面第一个数字表示合金系列,其中“1”表示铝硅系列合金,第二、三两个数字表示顺序号。
优质合金,在其代号后面附加字母“A”。
引用顾客提供的材料标准时,其代号按原用代号不变。
2.3 合金铸造方法、变质处理代号S——砂型铸造J——金属型铸造R——熔模铸造K——壳型铸造B——变质处理2.4 合金状态代号F——铸态T1——人工时效T2——退火T4——固溶处理+自然时效T5——固溶处理+不完全人工时效T6——固溶处理+完全人工时效T7——固溶处理+稳定化处理T8——固溶处理+软化处理2.5 数字修约规则合金牌号中合金化元素的名义百分含量、合金化学成分、合金性能等数字修约按GB 中附录C规定。
3 铸件分类根据工作条件、用途以及在使用过程中如果损坏,所能造成的危害程度,来确定铸件的类别。
3.1 铸件分三类,其定义及检验项目见表1:表1 铸件分类的定义及检验项目3.2 铸件类别由顾客在图样或有关文件中规定。
对于未注明类别的铸件,视为Ⅲ类铸件。
材料标记包括:所用的合金牌号或代号、铸造方法、铸件的供应状态、铸件的类别以及所执行的标准号等。
标记示例:ZL104-SB-T6Ⅱ-GB9438—954 技术要求4.1 化学成分合金的化学成分根据GB 1173的规定,应符合表2及表3的规定。
4.1.1 在海水环境中使用时,ZL101合金中铜含量不大于%。
4.1.2 ZL105合金中当铁含量大于%时,锰含量应大于铁含量的一半。
4.1.3 为提高机械性能,在ZL101、ZL102合金中允许含钇(Y)%~%。
此时,它们的铁含量应不大于%。
4.1.4 与食物接触的铝合金制品,不允许含有铍(Be);砷含量不大于%;锌含量不大于%;铅含量不大于%。
4.1.5 当使用杂质总和来表征杂质含量时,如无特殊规定,其中每一种未列出的元素含量不大于%。
4.2 状态4.2.1 铸件的供应状态,由顾客在图样中规定。
4.2.2 铸件按表4的规定,呈铸态或热处理状态供应。
表2 铸造铝合金化学成分注:在保证合金机械性能前提下,可以不加铍(Be)。
表3 铸造铝合金杂质允许含量注:1)表中“(1)”内容为每种,共;2)熔模铸造的主要元素及杂质含量按表2和表3中砂型指标检验;3)“CF 105002”合金其它杂质元素总量应不大于。
表4 铸造铝合金机械性能4.3 机械性能4.3.1 每批铸件应按其类别检验机械性能。
4.3.2 合金及其铸件的机械性能应符合表4的规定。
4.4 外观质量4.4.1铸件在进行表面粗糙度、表面缺陷、尺寸等外观质量检验之前,应清理干净、平整。
4.4.1.1 非加工表面的浇冒口,应清理到与铸件表面齐平;待加工表面的浇冒口残留量应不大于3mm。
4.4.1.2 清除飞翅、夹砂等多肉类缺陷,铸件的内外表面型砂、芯砂应清除干净。
4.4.1.3 根据顾客图样或技术文件的要求,铸件表面可进行喷砂处理。
4.4.1.4 铸件上作为基准用的部位应平整。
4.4.2 铸件尺寸应符合图样的要求。
尺寸公差应符合表5的规定。
有特殊要求时,应在图样上注明。
4.4.2.1铸件尺寸公差不包括由于拔模斜度而引起的尺寸增减,但必须保证铸件的最小极限尺寸。
4.4.2.2 铸件壁厚公差一般可降一级选用。
即图样上的一般尺寸公差为CT10,则壁厚尺寸公差为CT11。
4.4.2.3 错型必须位于表5规定的公差值之内。
当需进一步限制错型值时,则应在图样上注明,其值从表5或表6中选取较小的值,且不得与表5中所列值相加。
表5 铸件尺寸公差数值表6 错型值4.4.2.4 成批和大量生产铸件的尺寸公差等级按表7的规定选取:表7 成批和大量生产铸件的尺寸公差等级4.4.2.5 小批和单件生产铸件的尺寸公差等级按表8的规定选取:表8 小批和单件生产铸件的尺寸公差等级4.4.3 铸件非加工面的粗糙度由顾客在图样中规定。
4.4.4 铸件上不允许有冷隔、裂纹、穿透性缺陷及严重的残缺类缺陷(浇不到、未浇满、机械损伤等)的存在。
4.4.5 铸件待加工表面上,允许有经加工可去掉的任何缺陷。
4.4.6 在金属型铸件的非加工表面上,允许铸件有分型、顶杆及排气塞等痕迹。
但凸出表面不大于1mm 或凹下表面不超过0.5mm。
4.4.7 铸件表面的字母、数字、文字及花纹等应清晰、平整、美观、无缺漏现象。
4.4.8 砂型、金属型、壳型铸件的非加工表面和加工表面在清理干净后,允许存在下列孔洞:4.4.8.1 单个孔洞的最大直径不大于3mm,深度不超过壁厚的1/3,在安装边上,不超过壁厚的1/4,且不大于1.5mm。
在上述缺陷的同一截面的反面,对称部位不得有类似缺陷。
4.4.8.2 成组孔洞:对于Ⅰ、Ⅱ类铸件,最大直径不大于1.5mm,深度不超过壁厚1/3,且不大于1mm。
对于Ⅲ类铸件,最大直径不大于2mm,深度不超过壁厚1/3,且不大于1.5mm。
上述缺陷的数量、边距等应符合表9规定:表9 铸件表面孔洞数量及边距注:在非加工面上最大直径小于1mm,在加工面上最大直径小于0.5mm 的单个孔洞不予计算。
铸件表面按a、b、c、d四个级别验收。
验收级别由顾客在图样中规定。
4.4.9 对铸件的非加工表面上最大直径小于1mm,在加工表面上最大直径小于0.5mm的单个孔洞,参照4.5.1和条执行。
4.4.10 当图样上对一个铸件的不同表面规定不同级别要求时,各表面允许缺陷数量的总和,不得超过图样规定的最低等级表面所允许的缺陷数量。
4.4.11 图样上未注明级别时,加工表面为c级,非加工表面为d级。
4.4.12 由砂型、金属型、壳型浇注的液压、气压件的非加工面上经清理干净后,其单个孔洞按4.4.8条的规定。
加工面上允许有最大直径不大于1.5mm,且深夜不大于1mm的孔洞,这些孔洞的数量、边距等应符合表10的规定:表10 加工面的孔洞数量及边距4.4.13 液压、气压件的砂型、金属型、壳型铸件的加工表面上,允许2级针孔,局部允许3级针孔,但一般不得超过受检面积的25%。
当满足顾客对致密性的技术要求时或对其他砂型、金属型、壳型铸件允许按低一级的针孔度验收。
4.4.14 熔模铸件的非加工表面和加工表面,经清理干净后允许有:4.4.14.1 最大直径不大于1mm、深度不大于0.5mm的单个孔洞,在3cm×3cm面积上数量不多于3个,且边距不小于10mm,在一个铸件的非加工表面上孔洞总数不多于5个,加工表面上不多于3个(直径和深度不大于0.3mm的单个孔洞不计)。
4.4.14.2 直径和深度不大于0.3mm的密集小孔,其分布区域面积不得超过铸件受检面积的10%。
4.4.15 螺纹孔内、螺丝旋入四个牙距之内不允许有缺陷。
四个牙距之外,是否允许有缺陷以及允许缺陷的大小、数量按图样规定。
4.5 内部质量4.5.1 铸件内部针孔,当用低倍试验方法检验时,对Ⅰ类铸件或液压、气压件应按2级验收,允许局部有3级针孔,但不得超过受检面积的25%,Ⅱ类铸件按低一级针孔度验收。
4.5.2 针孔等级评定:低倍检验按GB 10851的规定进行,当有争议时按表11的规定:表11 各针孔级别的针孔数、大小及所占的比例4.5.3 铸件内部疏松、偏析,按专用技术标准进行验收。
4.5.4 铸件内部气泡、夹杂,当无特殊规定时,按下列要求验收:4.5.4.1 单个气泡或夹杂的最大尺寸不大于3cm,且不超过壁厚的1/3,在安装边上不超过壁厚的1/4,在10cm×10cm面积上的数量不多于3个,边距不小于30mm。
4.5.4.2 成组气泡或夹杂最大尺寸不大于1.5mm,且不超过壁厚的1/3,在3cm×3cm的面积上数量不多于3个,组与组间的距离不小于50mm。
4.5.4.3 尺寸小于0.5mm的单个气泡或夹杂不计。
4.5.4.4 气泡或夹杂距铸件边缘和内孔边缘的距离不小于夹杂或气泡最大尺寸的2倍。
4.5.4.5 上述缺陷所对应的(同一截面)表面,不得有类似缺陷。
4.5.5 铸件内不允许有裂纹。
4.5.6 铸件固溶处理不允许过烧。
4.6 铸件修补及矫正:4.6.1 可用打磨的方法清除任何缺陷,但打磨后的尺寸应符合铸件尺寸公差的要求。
4.6.2 变形的铸件允许用机械方法矫正,矫正后全部检查有无裂纹。
4.6.3 除另有规定外,铸件可用焊补的方法修复。
4.6.4 当采用钨极氩弧焊焊补时,焊补面积、焊补最大深度应符合表12的规定。
表12 铸件焊补的规定注:1)焊补面积是指扩修后的面积;2)焊补面积小于2cm2 的焊区不计入焊补数。
4.6.5 同一处焊补不超过三次,焊区边缘间距(包括反面的焊区)不得小于两相邻焊区直径之和。
4.6.6 凡以热处理状态供应的铸件,焊补后需按原状态进行热处理,热处理后的铸件按和条检验机械性能。
当氩弧焊区面积小于2cm2,焊区间距不小于100 mm,可不经热处理。
但在一个铸件上,不得多于五处。
4.6.7 焊补区不得有裂纹、分层、未焊透,在任何一焊区中允许有最大直径不大于2 mm,且不超过壁厚的1/3的气泡或夹杂三个,边距不小于10 mm。
直径小于0.5 mm的分散气泡或夹杂不计。
4.6.8 在腐蚀介质或气氛中工作的铸件,焊补时不允许使用焊药。
4.6.9 除另有规定外,允许对要求致密性的铸件进行渗补处理。
5 试验方法及检验规则5.1 化学成分5.1.1 合金的化学成分检验按GB 1198《铝化学分析方法》进行,在保证分析精度的条件下,允许使用其他方法。
5.1.2 对Ⅰ、Ⅱ类铸件,根据其重要程度,每月作为一个批次,每批随机抽查五个熔炼炉次,对主要元素和主要杂质Fe进行分析,其余杂质仅在有必要时或工艺检验时进行分析。