斗轮机培训教材
斗轮机 培训课件

内蒙古京能电力检修有限公司岱电维护项目部皮带一班04 月份培训课件京能电力检修岱电维护项目部燃料车间皮带一班二0一二年斗轮堆取料机设备简介:型号: DQL1000/1000·30型制造厂家:大连重工起重集团有限公司设计研究院主要参数:1、生产能力:取料:1000t/h 堆料:1000t/h2、物料:种料:煤料度:≤300mm 堆比重:0.9t/m³3、料场:堆料高度:轨上:12m 轨下:1.5m4、斗轮装置:型式:无格式斗轮直径:6m 转数:7r/min 轮数:8个斗容:0.4m5、悬臂皮带机:型式:双向可逆带宽:1200mm 带速:2.8m/s6、回转装置:回转半径:30m 回转速度: 0.06-0.18r/min7、走行装置:型式:四支点轨道中心距:6m 走行速度:7.5/30m/min 走行距离:约200m 最大轮压:250kn 钢轨:50kg/m8、俯仰机构:俯仰速度(水平位置斗轮中心处):4-5m/min 角度范围:+12º~-12º9、尾车:型式:活动双尾车功能:堆料/折返取料尾车皮带机型式:单向尾车皮带机带宽:1200mm 尾车皮带机速度:2.8m/s10、供电方式:型式:电缆卷筒卷取式11、电源:6000v 50HZ12、控制线:手动和PLC半自动控制13、装机容量:.apr.00kw一、主车机械设备1、减速器采用空心轴输出的减速器,所有减速器均为硬齿面减速器。
2、所有的驱动装置均装设合适的制动装置,电机功率在45KW与以上时配备液力联轴器。
3、外露的转动部件均设置防护罩,且便于拆卸。
人员易于达到的运动部位设置防护栏。
4、露天工作的电动机、减速器、制动器均设置防护、防雨罩并便于拆卸。
户外安装的电动机、减速器有防冻、防结露措施。
5、电动机、减速器重量在20kg与以上时设有带环形螺栓、吊钩或其它能安全起吊的装置。
6、液压系统与部件组装后密封良好、无冲击和漏油现象。
斗轮机教材
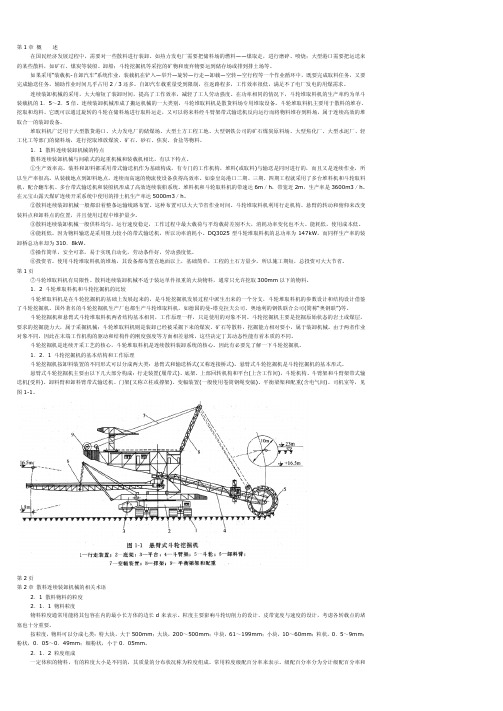
在国民经济发展过程中,需要对一些散料进行装卸。
如热力发电厂需要把储料场的燃料——煤取走,进行磨碎、喷烧;大型港口需要把运送来的某些散料,如矿石、煤炭等装船、卸船;斗轮挖掘机等采挖的矿物和废弃物要运到储存场或排到排土场等。
如果采用“装载机-自卸汽车”系统作业,装载机在铲入—举升—旋转—行走—卸载—空转—空行程等一个作业循环中,既要完成取料任务,又要完成输送任务,辅助作业时间几乎占用2/3还多。
自卸汽车载重量受到限制,往返路程多,工作效率很低,满足不了电厂发电的用煤需求。
连续装卸机械的采用,大大缩短了装卸时间,提高了工作效率,减轻了工人劳动强度。
在功率相同的情况下,斗轮堆取料机的生产率约为单斗装载机的1.5~2.5倍。
连续装卸机械形成了搬运机械的一大类别,斗轮堆取料机是散货料场专用堆取设备。
斗轮堆取料机主要用于散料的堆存、挖取和均料。
它既可以通过旋转的斗轮在储料场进行取料运走,又可以将来料经斗臂架带式输送机反向运行而将物料堆存到料场,属于连续高效的堆取合一的装卸设备。
堆取料机广泛用于大型散货港口、火力发电厂的储煤场、大型土方工程工地、大型钢铁公司的矿石煤炭原料场、大型焦化厂、大型水泥厂、轻工化工等部门的储料场,进行挖取堆放煤炭、矿石、砂石、焦炭、食盐等物料。
1.1 散料连续装卸机械的特点散料连续装卸机械与间歇式的起重机械和装载机相比,有以下特点。
①生产效率高。
装料和卸料都采用带式输送机作为基础构成,有专门的工作机构,堆料(或取料)与输送是同时进行的,而且又是连续作业,所以生产率很高。
从装载地点到卸料地点,连续而高速的物流使设备获得高效率。
如秦皇岛港口二期、三期、四期工程就采用了多台堆料机和斗轮取料机,配合翻车机、多台带式输送机和装船机形成了高效连续装船系统。
堆料机和斗轮取料机的带速达6m/h,带宽近2m,生产率是3600m3/h。
在元宝山露天煤矿连续开采系统中使用的排土机生产率达5000m3/h。
②散料连续装卸机械一般都沿着整条运输线路布置。
万源斗轮机电气培训4
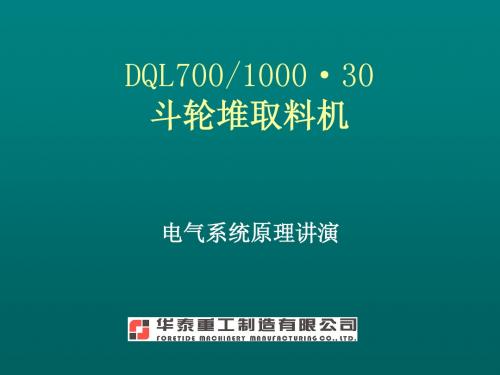
五.电气控制原理
电气分为:动力电源,走行,斗轮,皮带,臂变幅,回转,尾车变幅等主要部份. 1. 动力电源 • 机上动力电源为6000V,50HZ电源,由地面提供6000V电源到地面动力接线箱,再从 地面动力接线箱引出,经电缆卷盘上斗轮机箱式变电站,然后由箱式变电站低压接 线柜电气室内P1低压配电屏内的母排上。 • 机上动力电源断路器(+P1-QF1)给斗轮机各部份电动机提供三相380V动力电源,该 断路器安装在电气室P1屏内,操作方式为电动式。断路器分闸、合闸可以远距离(在 司机室)操作。
8. 尾车堆取料位置变换控制 • 尾车变换控制,一般在机旁操作箱P5上操作,先在司机室内左操纵台上 将控制方式选择+C1-SA6切换到“调整”位置(单动控制),然后将走行 台车与尾车之间的挂钩连接进行人工手动脱钩,脱钩后限位开关动作. • 然后按+P5-SB4大车前进按钮,台车向前行走,到位后台车停止前行。 • 然后根据堆料要求,按+P5-SB2“ 尾车上升”或者+P5-SB3“ 尾车下降” 按钮,控制尾车升降到位。尾车的上,下终端位置都有限位保护开关 • 尾车升降到位后,按+P5-SB4 “大车后退”按钮,台车向后退,到位后, 再进行手动挂钩.尾车堆取料位置变换完成.
二. DQL700/1000·30 斗轮堆取料机主要参数 斗轮堆取料机
• 取料为700吨/时,堆料为1000吨/时 • 斗轮机行走速度:快速30m/min,慢速5m/min • 臂架回转速度0.06-0.12r/min,回转角度±110°, 回转半径30m • 臂架变幅速度小于5m/min,臂架俯仰 角度-13.92°~ 12.22° • 装机总功率210Kw,单台电机最大功率55kW • 地面供电: 电缆卷筒6000V,50HZ • 操纵控制: 就地、手动(联锁)、半自动
斗轮机培训课件

斗轮机培训课件(一)按用途来分类分为斗轮取料机和斗轮堆料机。
前者只具有取料功能而不具备堆料功能,称为单一功能的斗轮机;而后者两种功能均具备,系多功能的斗轮机。
(二)按结构型式分类分为悬臂型、桥型、门型、圆型等,其中悬臂型应用最为广泛,其次为圆型,余下几种均为专用斗轮机。
其中悬臂型斗轮机又可分两种:悬臂斗轮取料机和悬臂斗轮堆取料机,目前国内电厂贮煤场大多采用堆、取合一的悬臂斗轮堆取料机。
一、结构特点及工作原理悬壁式斗轮堆取料机主要由金属构架、悬臂带式输送机、斗轮机构、仰俯机构、回转机构、行走机构、电器设备和操作室等组成。
(一)金属构架斗轮堆取料机的金属构架由前臂架、后配重架、主立柱,拉杆体系、回转平台、门座和尾车七大部分组成,各构件详述如下。
1、前臂架前臂架是用来安装胶带机和斗轮机构的主要构架,受力复杂,要承受转大的弯矩和压应力,故要求臂架要有足够的强度和刚度以及抗扭性能。
随着取料机出力加大,前臂架越来越长,有的可长达55m,这就给臂架的设计和制造以及运输带来较大的难度。
目前臂架结构型式有变截面箱型结构、管形结构、板梁结构和桁架结构几种。
臂架前端采用拉杆悬吊,后端通过绞座及主立柱或回转平台相连,臂架的两侧设有人行通道和跨越梯。
2、后配重架后配重架用来装设配重,平衡前臂架的倾覆力矩,提高斗轮机的稳定性。
该臂架受力虽较单纯,但承受载荷比较大。
在设计及制造时要给予足够的重视。
该臂架一般多用型钢制造或者用钢板焊制而成的箱体结构。
臂架的前端通过后座及主立柱相连,后端通过拉杆悬吊在主立柱的柱头上。
填装铁屑的混凝土配重箱或者悬挂混凝土的配重架均设在臂架的后端,借以获得较大的平衡力矩。
3、主立柱主立柱是回转平台上部的核心构件,通过它将前后臂架连接成为一整体,同时通过它把上部荷载传至回转平台上。
此外,该主立柱还要承受来自各个方向的力和力矩,因此要求主立柱必须有足够的强度和刚度。
大多采用较厚的钢板焊制两个大截面箱体立柱,尔后再用横梁和拉杆将两者连成一个坚固的整体。
机务培训教材

斗轮堆取料机培训手册长春发电设备技术服务前言本手册是为了用户对悬臂式斗轮堆取料机的运行、维护和检修更好的了解而编写的。
本手册可作为用户培训人员进行培训的教材,使培训人员能正确理解设计意图,认识设备特点和特性,掌握运行、维护和检修中要遵守的规则等方面的综合知识。
本手册着重阐述该设备的性能及主要技术参数、设备的构造、设备的组成、各机构的详细阐述、设备的作业方式及特点、设备的操作规程、设备的安全使用规则、设备的维护和保养及设备的常规故障和处理方法。
由于我们的编写水平有限,书中存在不妥之处,诚恳读者批评、指正。
目录第一章:绪论 (3)第1节斗轮机分类 (3)第2节设备的技术参数 (4)第二章:斗轮机主要机构 (7)第1节总体介绍 (7)第2节斗轮机构 (8)第3节回转机构 (13)第4节行走机构 (15)第5节悬臂胶带机 (18)第6节变幅机构 (20)第7节金属结构 (25)第9节附属机构 (29)第三章:设备的作业方式及特点 (38)第1节堆料作业 (38)第2节取料作业 (40)第3节分流作业 (41)第4节电气作业方式及特点 (42)第四章:设备的操作规程及安全使用规则 (46)第1节设备的操作规程 (46)第2节设备的安全使用规则 (47)第五章:设备的维护与保养 (50)表一:斗轮机使用油(脂)一览表 (52)表二:主要部件的磨损度 (53)表三:常见故障的处理 (54)附录I:斗轮堆取料机对走行轨道的要求 (62)附录Ⅱ主要机构的检查 (63)第一章:绪论悬臂式斗轮堆取料机是在斗轮挖掘机的基础上发展起来的,属于大型、连续、高效的散料装卸机械设备,广泛应用于火力发电厂、港口码头、水泥、钢铁、矿山等散料输送系统。
第1节斗轮机分类斗轮机为斗轮堆取料机、斗轮取料机、斗轮堆料机的总称。
1.斗轮堆取料机一种在贮料场上运行,通过斗轮进行取料,将物料从贮料场取走,又可以将物料堆积到贮料场的堆取合一的设备。
斗轮机教材(已加图)
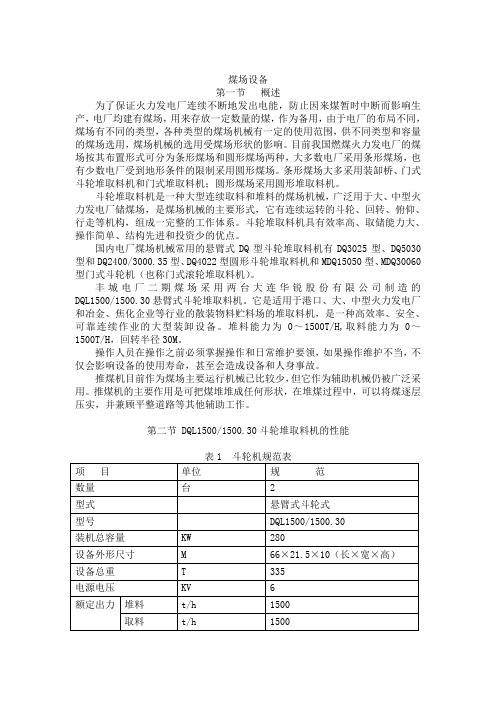
煤场设备第一节概述为了保证火力发电厂连续不断地发出电能,防止因来煤暂时中断而影响生产,电厂均建有煤场,用来存放一定数量的煤,作为备用,由于电厂的布局不同,煤场有不同的类型,各种类型的煤场机械有一定的使用范围,供不同类型和容量的煤场选用,煤场机械的选用受煤场形状的影响。
目前我国燃煤火力发电厂的煤场按其布置形式可分为条形煤场和圆形煤场两种,大多数电厂采用条形煤场,也有少数电厂受到地形条件的限制采用圆形煤场。
条形煤场大多采用装缷桥、门式斗轮堆取料机和门式堆取料机;圆形煤场采用圆形堆取料机。
斗轮堆取料机是一种大型连续取料和堆料的煤场机械,广泛用于大、中型火力发电厂储煤场,是煤场机械的主要形式,它有连续运转的斗轮、回转、俯仰、行走等机构,组成一完整的工作体系。
斗轮堆取料机具有效率高、取储能力大、操作简单、结构先进和投资少的优点。
国内电厂煤场机械常用的悬臂式DQ型斗轮堆取料机有DQ3025型、DQ5030型和DQ2400/3000.35型、DQ4022型圆形斗轮堆取料机和MDQ15050型、MDQ30060型门式斗轮机(也称门式滚轮堆取料机)。
丰城电厂二期煤场采用两台大连华锐股份有限公司制造的DQL1500/1500.30悬臂式斗轮堆取料机。
它是适用于港口、大、中型火力发电厂和冶金、焦化企业等行业的散装物料贮料场的堆取料机,是一种高效率、安全、可靠连续作业的大型装卸设备。
堆料能力为0~1500T/H,取料能力为0~1500T/H,回转半径30M。
操作人员在操作之前必须掌握操作和日常维护要领,如果操作维护不当,不仅会影响设备的使用寿命,甚至会造成设备和人身事故。
推煤机目前作为煤场主要运行机械已比较少,但它作为辅助机械仍被广泛采用。
推煤机的主要作用是可把煤堆堆成任何形状,在堆煤过程中,可以将煤逐层压实,并兼顾平整道路等其他辅助工作。
第二节 DQL1500/1500.30斗轮堆取料机的性能表2 斗轮技术规范表表3 悬臂皮带机规范表表4 悬臂回转机构规范表表5 行走机构规范表表6 悬臂变幅机构规范表表7 切换挡板规范表表8 尾车升降机构规范表表9 夹轨器机构规范表表10 电缆转盘规范表表11 斗轮机喷水系统规范表第三节斗轮堆取料机的主要结构DQL1500/1500.30型斗轮机主要由以下机构组成:斗轮装置、悬臂梁装置、悬臂皮带机、俯仰机构、门座架、回转钢结构、回转装置、走行装置、尾车、司机室、电气室、润滑系统、除尘、电气系统、液压系统及动力和控制电缆卷筒装置等部分构成。
斗轮机培训

斗轮机主要部件结构特征
• 俯仰机构 – 本机采用了整体俯仰形式即臂架上下俯仰与上部结构件一起连动,驱动系统采用 液压传动。主要由电机、油泵、油箱、油管、液压锁、各种控制阀、两个油缸等 组成。 – 油缸连接上部结构件上段与回转平台前端,电机及油泵油箱等安装在回转平台右 侧。 – 本机液压传动装置在斗轮机工作期间,臂架的俯仰由电磁转换阀控制,液压系统 采用液压锁和平衡阀的双重锁定,同步回路控制,俯仰时工作平稳可靠。
斗轮机主要部件结构特征
• 斗轮机构 – 斗轮机构是本机取料的执行机构。主要由斗轮、斗子、园弧挡料板、卸料板、斗 轮轴、轴承座、行星减速器、液力偶合器、电动机组成。 – 轮体结构为无格式,斗子与轮体材料为16Mn,斗子与轮体用销轴联接,装卸方便, 斗唇用碳化钨焊条堆焊,耐磨性高,斗齿与斗壳用螺栓连接,便于更换。
斗轮机操作
• 控制方式选择与操作 – 操作方式由SA111转换开关选择单动、手动、半自动三种方式,SA111转换开关 装设在司机室内右操作台上。 – 单动控制:把SA111旋到单动位置,PLC内部继电器工作,斗轮机电气控制处于单 动控制方式中,在司机室操纵台上可单独启动各机构运转,一般单动控制只用于 斗轮机检修、调试场合。
• •
斗轮机主要部件结构特征
• 回转机构 – 回转机构由电机、安全摩擦离合器、液压推杆制动器、减速器、交叉圆柱滚子轴 承、上下油封环、回转角度检测装置等组成。 金属结构 – 本机的主要金属结构件有前臂架、上部结构件、门座、尾车、回转平台等,为本 机的主要承力构件,其可靠性对整机正常安全运行有着十分重要的保证作用。
斗轮机主要部件结构特征
• 臂架带式输送机: – 在前臂架上设置了紧急拉绳装置,当遇紧急情况,用手拉双向开关的拉绳开关, 通过电信号控制,使臂架带式输送机停止作业,另设打滑检测装置,防止皮带在 打滑时工作,设溜料堵塞保护装置。 – 前臂架仰起堆料时,因故停电,可能出现物料带动皮带向中心漏斗处运动,而将 中心漏斗堵塞,为防止这一现象的产生在减速器的输入端装有制动器,一旦停电 制动器发生作用,驱动滚筒即被制动。
斗轮机电气培训课件05.10.13
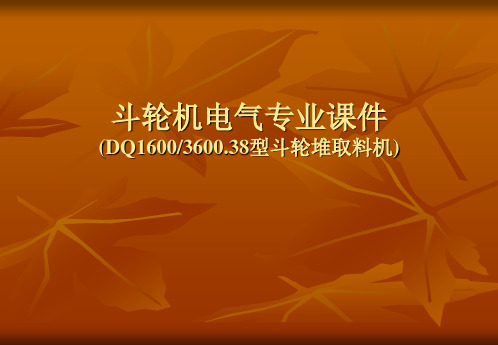
行走装置
各机构控制
(4)当大车行走至大车前进限位、极限或大车后退限位、极限时,大车将停止运行,在可编 程终端的”限位指示“画面上,相应的”大车前进限位“、”大车前进极限“、”大车后退限位 “、” 大车后退极限“指示灯亮,同时,左操作台上的”故障报警“有声光报警提示。此时,大车行 走只能向相反的方向运行。 (5)大车行走的过程中,进入可编程终端的”电流指示“画面,通过屏幕上的”大车行走电机电 流“电流表监视大车行走过程中电机的电流大小。 1.2、电缆卷筒单动控制 电缆卷筒的运行没有单独的开关控制,它随着大车行走同时运行。 1.3、洒水单动控制 (1)洒水系统的控制通过可编程终端完成。 (2)在可编程终端的”状态指示“画面上,”水箱水满“指示灯亮或”水箱缺水“指示灭时才可以 进 行洒水。 (3)进入可编程终端的”操作控制“画面,屏幕上的”喷水水泵运行“按钮和”喷水水泵停止“按 钮 可以实现喷水水泵电机运行和停止。在可编程终端的”状态指示“画面上,相应的”喷水水泵 运行“指示灯亮,此时方可操作水泵的堆料运行喷水和取料运行喷水。 (4)斗轮机堆料运行洒水时,进入可编程终端的”操作控制“画面,点击”堆料喷水“按钮,斗轮 机进行堆料喷水结束。 (5)斗轮机取料运行洒水时,进入可编程终端的”操作控制“画面,点击”取料喷水“按钮,斗轮 机进行取料喷水。取料喷水结束时,进入可编程终端的”操作控制“画面,点击”喷水停止“按 钮,斗轮机取料喷水结束。
工作原理
本设备采用手动、手动联锁、半自动进行堆料和取料作业。 堆料作业时,系统胶带机送来的煤经尾车胶带机(系统胶带机)、尾车 头部落料斗转运到中部料斗(含分流装置),经分流有二种工况:a来煤通 过悬臂胶带机输送全部抛向储煤场;b来煤经过分流,把系统来煤分流出 1600t/h,直接送至上煤系统,另外部分抛向储煤场。整机的上仰和下俯 可实现高、低位的堆料回转实现左右煤场及煤场宽度的堆料;大车行走 则实现轨道长度方向的堆料。 取料作业是按分层取料的工艺进行的,必要时也可以进行斜坡取 料。取料作业时,斗轮机构上的斗子挖取上来的煤卸至悬臂胶带机上, 再上悬臂胶带机抛向中部料斗,经尾车胶带机(系统胶带机)输出。整机的 上仰和下俯可实现高、低位的取料;整机回转实现左右煤场及煤场宽度 的取料;大车行走则实现轨道长度方向的取料,禁止只靠大车行走取 料。
斗轮机培训教材
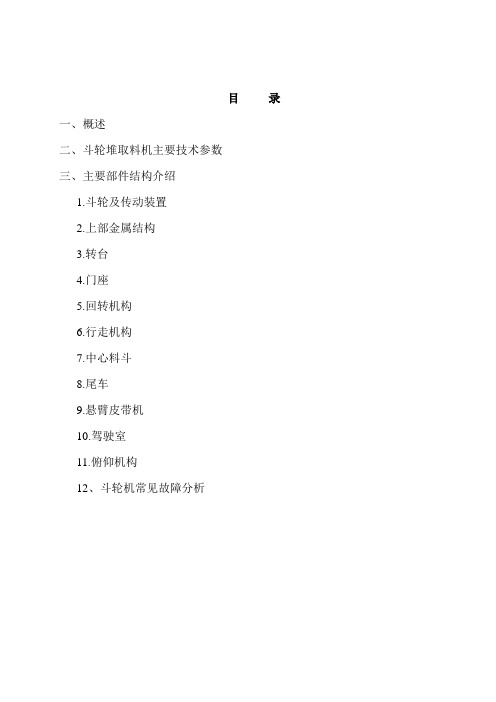
目录一、概述二、斗轮堆取料机主要技术参数三、主要部件结构介绍1.斗轮及传动装置2.上部金属结构3.转台4.门座5.回转机构6.行走机构7.中心料斗8.尾车9.悬臂皮带机10.驾驶室11.俯仰机构12、斗轮机常见故障分析一、概述1.DQ1500/1500.35型斗轮堆取料机(图一),可用于堆和取粒度小于350mm的煤炭;其大车行走、回转、俯仰、斗轮传动、胶带机等传动机构之间有连锁保护。
二、斗轮堆取料机的主要技术参数2.生产能力:堆料最大生产率1500t/h(煤炭)取料最大生产率1500t/h(煤炭)3.堆料范围:长度:沿轨道方向延伸宽度::回转半径35m,两轨的规距为7m。
除去路基影响可堆取净宽为62m。
4.堆料高度:堆料高14m(其中轨面上为12m:轨面下为1.5m)5.取料机构:形式:无格式斗轮斗轮直径D=7000mm斗容V=0.52斗数Z=9只斗轮转速vn=6.8r/min驱动方式:机械传动,减速机ZHP5.34-k (ZOLLERN 公司) i=217.26.变幅机构:俯仰油缸参数:活塞直径D=250mm,活塞杆直径D=140mm行程L=1370mm,液压缸型号:A2F028,工作压力:9.8M 流量:40L/min上升速度:v斗上=3.4m/min下降速度:v斗下=5m/min变幅范围:上仰13.5°,下俯9°.驱动方式:采用双作用油缸,液压传动6. 回转机构:回转半径:35m回转速度:工作速度0.03~0.12r/min(6.6~26m/min)最大转速:0.128r/min(28.5m/min)回转角度:左右各110°驱动方式:采用机械传动和VVVF不变频调速装置,能自动控制回转取料速度减速器:型号ENFRSYN SG—XP220 i=65转矩联轴器:型号:YWZ3B—315/25—12.5极限转矩联轴器:转矩=100—170N电动机功率:P=11×2KW(Y160M-4),n=1460r/min7. 行走机构:行走速度:7.5~30m/min车轮直径:、D=500mm最大轮压:230KN轨道载荷:50kg/m减速装置:三级卧式减速器加开式传动,传动比i=33.028×2=76.625减速器MC3RLHF02(SEW公司)车轮数:主动轮12,从动轮12个车轮直径:500mm驱动轮数:8个电动机功率:P=11×6KW(Y160M-4),n=1460r/min夹轨器形式:液压弹簧夹轨器锚定装置形式:为手动机械式锚定8.悬臂皮带机参数:带宽:1.4m带速:2.75m/s皮带层数:Z=6(耐寒带)电动机功率:P=75KW(Y280S-4)驱动方式:机械传动,减速箱MC3RJHF05H (SEW 公司)传动比i=22.758,液力偶合器型号:YOXNZ45050-90KW,减速器型号:MC3RLHF05H,制动器:YWZ3B-315/45-16拉紧方式:重锤式,拉紧重量=4.9t,拉紧行程=820mm,配重铁丸3100kg,头尾滚筒间距=37250mm9.尾车:尾车型式为全功能主尾车、折返通过式9.1主尾车9.1.1主尾车为固定式9.1.2主.尾车皮带机参数:带宽:1.4m带速:2.75m/s皮带层数:Z=6(耐寒型)电动机功率:P=55KW(Y250S-4),n=1480r/min驱动方式:机械传动,减速箱MC3REHF04+1(SEW公司)带逆止器,i=23.171,输出轴转速:63.87r/min,头尾滚筒间隙=22862mm拉紧方式:重锤式,拉紧重量=2.1t,拉紧行程=800mm,重18块共837kg9.2付尾车:9.2.1系料场皮带,皮带宽度1.4m,带速2.5m/s9.2.2变位方式:液压缸升降10.液压系统:包括主机与尾车两个液压系统。
- 1、下载文档前请自行甄别文档内容的完整性,平台不提供额外的编辑、内容补充、找答案等附加服务。
- 2、"仅部分预览"的文档,不可在线预览部分如存在完整性等问题,可反馈申请退款(可完整预览的文档不适用该条件!)。
- 3、如文档侵犯您的权益,请联系客服反馈,我们会尽快为您处理(人工客服工作时间:9:00-18:30)。
斗轮机培训材料一、目的保证生产设备正常运作,延长机器设备使用寿命,最大程度提高装卸效率,加强司机设备操作、巡检的规范化意识,避免因设备操作、巡检不当而引发机器损伤及工伤事故。
二、范围本规范适用于本公司1#斗轮机、2#斗轮机。
三、操作、巡检人及职责1、各班班长及设备使用人员为机器设备负责人。
2、职责范围包括机器设备的操作、巡检、定期试验等。
3、责任人员负责设备的操作与巡检,并作记录。
四、操作规范内容及注意事项1、斗轮机巡检1.1、斗轮机的构造、参数和行走的组成和检查1.1.1斗轮机的构造和主要组成部分:由斗轮机构、悬臂胶带机、俯仰钢结构、行走机构、俯仰机构、回转机构、中部料斗、附属结构、尾车、机电保护装置、洒水除尘系统、润滑装置、液压系统、电缆卷筒、电气室、司机室、电气系统、配重等组成。
1.1.2行走机构组成:行走电机、制动器、减速机、电机风扇、驱动轮、行走轮、清轨器、接地靴、电缆、水缆的拉紧保护、防跑制动器、防风系缆、行走锚定、声光报警装置、大车前后停止限位、防撞缓冲器、大车润滑、就地操作箱、检修箱。
1.1.3查轨道有无障碍物,沿线无关人员是否撤离,检查轨道沉降情况。
1.1.4行走轮完好,无裂纹、啃轨等缺陷,轮子与轨道应平行,下轮面应轨道紧密接触。
1.1.5驱动轮的电动机外观完好,接线完好,连接螺栓无松动,进线盒封堵完好。
1.1.6大车行走制动器完好,工作正常,制动片不会磨到传动轴。
1.1.7大车减速机无漏油,油位、温度正常。
1.1.8斗轮机两个终端限位保护完好,无弯曲、歪斜等损坏现象1.1.9操作箱开关是否都在停止位或零位,防风系缆和锚定是否都抬起。
1.1.10前后停止限位开关是否有效,无弯曲、歪斜等损坏现象。
是否能与限位支架触碰。
1.1.11接地靴与轨道接触良好,用手扳动有一定下压力。
1.1.12防跑制动器外观完好,接线完好,大车行走时会自动抬起。
1.1.13润滑管线接头完好,无漏油、压扁、鼓包现象。
1.1.14上机前要试验电缆限位开关是否动作。
卷筒拉紧限位是否有卡住、卷筒是否会变形外观无明显积尘、积灰。
电机外观、接地完好,地脚螺栓无松动,进线盒封堵完好。
1.2、喷淋水系统1.2.1喷淋水系统组成:各种水阀(总阀、进水阀、出水阀、再循环阀、溢流阀、排气阀)的作用、水位计、压力表、多级离心泵(扬程82.8M)、各个洒水点(悬臂皮带头部抛料点、尾车头部料斗、悬臂皮带尾部导料槽,斗轮卸料槽、中部料斗、地面皮带导料槽)1.2.2水箱水位应在1.4M-1.6M之间,低于1.4M时交班者应进行补水,水泵外观完好,地脚螺栓紧固无松动。
检查水箱水位,喷淋头有无堵塞。
进、出口阀门是否已在开启状态。
平衡管应无漏水现象。
1.3、回转机构组成和检查1.3.1回转机构组成:回转终始角度保护、回转电机、行星减速机、制动器、转盘轴承、回转防撞缓冲器、回转润滑(与俯仰铰轴、悬臂皮带驱动滚筒、改向滚筒共用)、回转禁区。
1.3.2回转润滑压力不得超过21Mpa。
1.3.3检查齿轮的润滑情况以及齿轮内是否有杂物。
齿轮外观应完整。
1.3.4检查回转电机外观完好,外壳接地完好,地脚螺栓无松动。
进线盒封堵完好。
减速机螺栓无松动,脱落,油位在1/2-2/3之间,角度限位开关的支架外观完好,接线无脱落现象。
1.3.5查看回转减速机油位。
油位应在1/2-2/3之间,油质良好。
需用内六角转开。
1.3.6润滑管线、配油器完好、无漏油、无鼓包现象,润滑油站的油脂量在1/2-2/3之间,油站内压力表、油管接头完好,无漏油现象。
油站内部无积料、积灰。
1.3.7检查回转大轴承处积料情况,应及时清理,在积料不严重的情况下可每船清理一次。
1.3.8回转防撞缓冲器无变形、开裂,与回转机构交接处无脱胶、开裂。
1.4、俯仰机构的组成和检查1.4.1俯仰机构组成:俯仰上下限位保护、俯仰液压油站电动机、冷油器、流量表、温度表、俯仰油缸、波纹罩。
1.4.2液压站的油位在1/2-2/3之间,温度不能超过65℃。
1.4.3油泵电动机运转正常,温度及振动不超限,无异味,无异响。
各油管无鼓包、漏油现象。
1.4.4液压活塞杆密封环处漏油现象,波纹罩无破列、损坏现象。
1.4.5俯仰限位是否有效。
1.4.6俯仰工作安全压力为200Bar最大工作压力为180Bar,堆取料挡板最大工作压力为150 Bar。
1.5、中心料斗、尾车、上部金属结构的组成和检查:1.5.1中心料斗、尾车组成:尾车料斗、分料料斗、出料料斗、导料槽、尾车液压系统、检修箱、压带轮、安全通行桥。
1.5.2上部金属结构组成:悬臂前段、悬臂后段、塔架、塔架拉杆、前拉杆、平衡臂、后拉杆、悬臂架防碰撞保护、配重。
1.5.3检查料斗是否被砸穿变形,是否有积料,耐磨衬板无松动,螺丝无松动、掉落。
1.5.4液压油站安全工作压力为150 Bar。
温度不得超过65℃,油泵电动机运转正常,温度及振动不超限,无异味,无异响。
各油管无鼓包、漏油现象。
1.5.5检查尾车接料板处是否有积料和杂物,如有须及时清理,防止磨到回程皮带或托棍。
1.6、悬臂皮带机系统的组成和检查:1.6.1悬臂胶带机的组成:调芯托棍、槽型托辊、清扫托辊、平行托辊、缓冲床、空段清扫器、电子皮带称、速度检测开关、跑偏开关、拉绳开关、防撕裂开关、电机、减速机、制动器、皮带张紧装置、悬臂皮带尾部导料槽、液压站、就地操作箱。
1.6.2检查悬臂皮带尾部导料槽是否到位,限位开关是否有效。
1.6.3滚筒轴承座无异响。
轴承座无漏油。
轴承座温度不得超过80℃。
轴承座螺丝无松动脱落。
1.6.4滚筒表面橡胶无大面积的脱胶现象。
震动情况及是否有异响,滚筒是否有物料及异物卷入,重锤积料情况。
1.6.5检查皮带清扫器完好,与皮带之间的间隙适当。
两端的导料槽防溢裙板完好,不漏料。
托辊外观完好,无变形,弯曲。
1.6.6检查皮带无明显撕破、脱胶、断裂、起皮、起泡现象。
上工作面和下层皮带均无杂物。
皮带秤上因无积料,螺丝无松动,外观完好,数值准确。
1.6.7检查拉绳和跑偏开关动作是否灵敏,位置是否正确。
1.6.8检查电机震动值在规定范围内,振动达0.1毫米时应加强监视,达0.15毫米时应停止运行。
轴承温度达65℃时应加强监视,超过85 ℃时应停止运行油位不得高于液力偶合器的1/3,无漏油现象,螺栓无松动脱落、无裂痕。
1.6.9检查悬臂下方横梁上的积料是否磨到悬臂皮带,若有需要立即清理后才能继续运行。
1.7、斗轮机构及悬臂头部导料槽的组成和检查:1.7.1斗轮机构组成:驱动电机、风机、减速机、液力偶合器、油泵、圆弧挡料板、斗轮轴、滑料槽、导料槽、斗轮体、轴承座、斗子、斗轮轴承润滑油站(与悬臂皮带头部滚筒轴承共用)。
斗轮取料过载保护料位高度检测。
1.7.2检查斗轮电机完好,外壳接地完好,地脚螺栓无松动,进线盒封堵完好。
1.7.3斗轮轴承座螺栓无松动,脱落。
1.7.4润滑油站外观完好,油管接头完好,无漏油、压扁、鼓包现象,油位应保持在1/2-2/3之间。
1.7.5斗子与斗轮体连接螺栓无松动,斗子无变形。
1.7.6检查滑料槽是否有积料,需及时清理以及磨损情况。
1.7.7导料槽不漏料,外观完整,导料槽防溢裙板完好,不漏料。
液压推杆无磨损、漏油现象,波纹罩无破裂、损坏现象。
1.7.8检查电机震动值在规定范围内,振动达0.1毫米时应加强监视,达0.15毫米时应停止运行。
轴承温度达65℃时应加强监视,超过85 ℃时应停止运行油位不得高于液力偶合器的1/3,无漏油现象,螺栓无松动脱落、无裂痕。
1.7.9检查圆弧挡料板外观完好,无松动、脱落。
轴承座螺丝无松动,震动值正常。
1.8、高、低压电气室的检查:1.8.1电气室各配电柜的开关在合闸位置,表计显示正常,照明正常。
1.8.2监控计算机显示各机构状态正常,无故障报警。
1.8.3高压室主、辅变压器工作正常,无超温报警。
1.8.4电气室无异味,空调工作正常,温度设定为25℃。
1.8.5空调单元和过滤器是否正常。
1.8.6电气室各配电柜排气扇运行正常1.8.7各盘柜门、电气室门关好。
2、定期检查与维护:2.1、每班工作结束后,应对下列部位进行清理后方可交班。
2.1.1清理斗轮平台,悬臂皮带周围等处的积煤及异杂物。
2.1.2清理各落料点及档板上的积料及异杂物。
2.1.3司机室、电气房、液压站打扫干净。
2.1.4回转大轴承内部积料清理。
2.2、每月按清洁责任区划分,各班对管辖斗轮机全面打扫二次(10号及25号前后),对电动机、减速箱、制动器等设备进行清理,要求设备见本色。
2.3、每船检查:2.3.1减速箱,电机、液力偶合器、液压系统漏油情况。
2.3.2输送胶带的损伤及跑偏情况。
2.3.3信号、主要限位(水缆、电缆拉紧限位,上下俯仰限位,头部导料槽限位)和照明灯具完好性。
2.3.4各平台上和悬臂皮带周围的积料是否清理。
2.4、每周、月检查:2.4.1制动闸瓦,销轴,制动轮磨损情况。
2.4.2金属结构变形,弯曲,裂纹情况。
2.4.3各部位螺栓紧固情况,各支腿,底座有无脱焊,松动。
2.4.4挤到轴承外面的润滑脂中有无金属磨下的粉末。
2.4.5控制柜,电动机和其它电气元件的绝缘情况。
2.4.6各限位开关和安全装置的动作情况。
(见附件一)2.4.7制动轮、联轴器、轴、滚筒有无裂纹。
2.4.8各润滑点润滑情况。
(见附件二)2.5、每季、年检查:2.5.1校准各种仪表精度。
2.5.2减速箱中油液污垢程度,确属需要,滤清或更换油液。
(见附件三2.5.3电动机、接头有无松动。
2.5.4衬板、易损件磨损情况。
2.5.5检查大车行走轨道精度是否在管理限界内。
2.5.6制动器的动作可靠性。
2.5.7检查各减速器齿轮,滚动轴承,联轴器内外齿磨损情况,清洗各减速箱,更换新油。
2.5.8检查结构锈蚀情况,视情况可在2~3年重新漆一次。
3、斗轮机手动取料方法:3.1、取料说明:3.1.1在取料时,由斗轮挖取的物料经溜料板滑到悬臂皮带机上,再通过中心料斗的下半部转运到料场主胶带机系统中。
3.1.2取料时斗轮每转一次切割的断面呈月牙形,大车每前进一段距离就是斗轮的吃进深度,而前臂架每下降一单位距离就是斗轮的切削高度。
3.1.3从前臂架平行于轨道到垂直轨道,进行回转取料时,前臂架回转每单位转角时的物料被斗轮的挖取量是不等的,即物料挖取量由最多将到零。
3.1.4在臂架平行于轨道时切进深度等于大车前进的一段距离,在垂直于轨道时切深等于零。
3.1.5要取料稳定,就必须在大车行走,悬臂回转上去控制。
3.2、变速取料法(图1)3.2.1开始取料前将斗轮放至离料堆最近端(即A点)1米处,斗轮挖取的高度应≤4米。
3.2.2如挖取高度为4米时,装船量为3000t/h,装火车量为1300 t/h。