QSB中文版-防错验证
QSB+03检查及防错

检验工位
工程、监控和维护 识别出不符合项时,支持检验工位发出警报。
工厂经理(生产领导人) 建立检验工位流程。 启动和推进问题解决和防错。 参加检验工位每日汇报。 为团队提供支持,确保流程运行。
质量经理提供支持 检验工位每日会议。 问题解决及跟踪。
检验工位
描述,角色,职责 检验工位的目的是什么?
• 检验工位检查生产过程是否按照设计要求制造出产品。 • 通过报警系统,提供优先级最高的客户问题(问题解决报告类型的缺陷)的
工位提高 制造质量
通过消除变化 支持操作人员
反馈带来上游反应
线上下线全检 检验工位
查找 用户认可检查评估会 发现的内容
Байду номын сангаас
下线 客户认可检查评估
查找 客户会发现的内容
客户之声
资源: 客户线上抱怨 保修
13
检验工位
客户认可检查评估 保证客户不受不合格产品、不符合和错误标签的影响。
检验过程控制是否有效。 应用于客户满意度相关问题。
过程更改时向班组人员发出警报,并 知道何时、向谁求助。
问题发生时获得支持,将其解决。
防止缺陷被忽视。
确保班组人员在问题解决中的表现符 合范改围善:目标。 保生证产下操游作客户的信息反馈
装配区域
所有实施全检或遏制的区域。
职责: 责任归属 质量经理生产部门领导者 生产、工程、材料和质量部门领导和 员
工提供支持
未超出警报界限 >
在控制范围之内?
能力不足 11
过程图解
正向反馈
()
反馈
保修
用户认可检查 评估
客户
检验工位可以设置在过程中的任何地方。 过程的每个步骤中都应该应用警报升级。
副本副本QSB的SOS JES 防错、变更及风险降低的版本号 编号草案
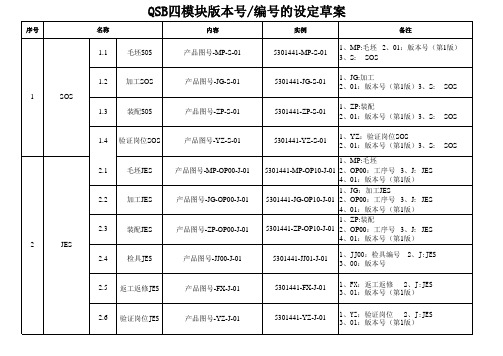
检具JES
产品图号-JJ00-J-01
2.5
返工返修JES
产品图号-FX-J-01
5301441-FX-J-01
1、FX:返工返修 2、J:JES 3、01:版本号(第1版) 1、YZ:验证岗位 2、J:JES 3、01:版本号(第1版)
2.6
验证岗位JES
产品图号-YZ-J-01
5301441-YZ-J00
BG-FG-12-001
5.1 5 风险降低 5.2
主动风险降低
产品图号-ZD-01
5301441-ZD-01
被动风险降低
BD00-01
BD01-01
编制:
审核:
单一产品
产品图号-FC-01
5301441-FC-01
4.1
水泵
BG-S-年-000
BG-S-12-001
4.2 4 变更管理 4.3 4.4
排气歧管 支架 飞轮壳
BG-P-年-000 BG-Z-年-000 BG-FK-年-000
BG-P-12-001 BG-Z-12-001 BG-FK-12-001
3.1 3 防错装置验证 3.2
共线产品
GX-FC-01
GX-FC-01
1、GX:共线产品 2、FC:防错装置验证 3、01:版本号(第1版) 1、FC:防错装置验证 2、01:版本号(第1版) 1、BG:变更管理 2、S:水泵 3、12:年 4、001:编号 1、BG:变更管理 2、P:排气歧管 3、12:年 4、001:编号 1、BG:变更管理 2、Z:支架 3、12:年 4、001:编号 1、BG:变更管理 2、FK:飞轮壳 3、12:年 4、001:编号 1、BG:变更管理 2、FG:阀盖 3、12:年 4、001:编号 1、ZD:主动风险降低 2、01:版本号(第1版) 1、BD00:被动风险降低编号 2、01:版本号(第1版) 批准:
QSB培训教材
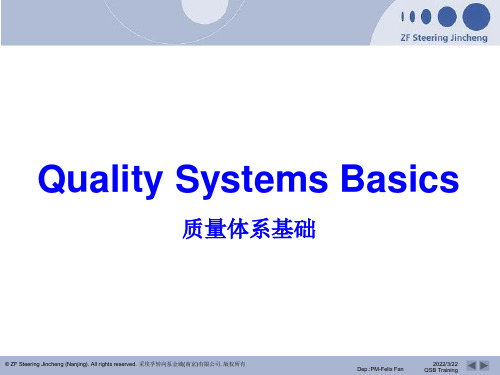
© ZF Steering Jincheng (Nanjing). All rights reserved. 采埃孚转向泵金城(南京)有限公司. 版权所有
Dep.:PM-Felix Fan
2022/3/22 QSB Training
快速反应
责任人的报告应包含以下几个方面的更新:
Dep.:PM-Felix Fan
2022/3/22 QSB Training
快速反应跟踪表 (举例)
整体状态 遏制、围堵 PFMEA/控制计划 防错装置 标准化作业 分层审核 关闭日期
优化目视管理,将这个表格尽可能大的显示在会议室
( 如: 4’ x 8’ 可擦写的白板 )
Is s ue
Number 问题编号
。有些公司每班一次。 - 它是一个沟通会议,不是问题解决会议。该会议可以是 10-20分钟
在生产现场召开或在生产现场会议室进行的会议。 - 它是应由生产部负责审核的会议,质量部,工程部,设备维 修部等,给予支持。
在快速反应会议时,管理层必须:
- 就每一事项规定一个负责人 - 指定负责人在下次会议时汇报
2022/3/22 QSB Training
快速反应
• 快速反应是一个系统:
- 使应对重大的内/外部质量问题的反应标准化 - 通过每日例会加强沟通和管理 - 采用目视管理方法展示重要信息
为准备快速反应会议,每天开班时,质量部应找出过去24小时发生的重大质量事 故,包括:
- 客户关注的问题 - 供应商关注的问题 - 停线(内部/外部) - 发货审核 / 审核发现的问题 - 其它内部质量问题
Dep.:PM-Felix Fan
QSB(质量体系基础)介绍
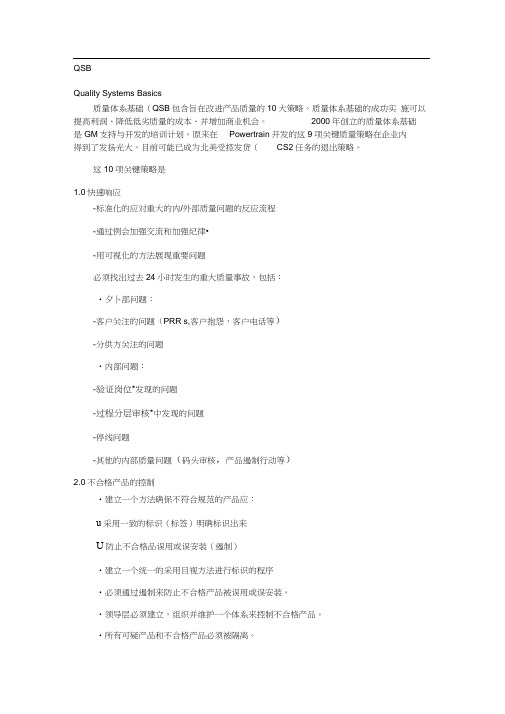
QSBQuality Systems Basics质量体系基础(QSB包含旨在改进产品质量的10大策略。
质量体系基础的成功实施可以提高利润、降低低劣质量的成本、并增加商业机会。
2000年创立的质量体系基础是GM支持与开发的培训计划。
原来在Powertrain开发的这9项关键质量策略在企业内得到了发扬光大,目前可能已成为北美受控发货(CS2任务的退出策略。
这10项关键策略是1.0快速响应-标准化的应对重大的内/外部质量问题的反应流程-通过例会加强交流和加强纪律•-用可视化的方法展现重要问题必须找出过去24小时发生的重大质量事故,包括:•夕卜部问题:-客户关注的问题(PRR s,客户抱怨,客户电话等)-分供方关注的问题•内部问题:-验证岗位*发现的问题-过程分层审核*中发现的问题-停线问题-其他的内部质量问题(码头审核,产品遏制行动等)2.0不合格产品的控制•建立一个方法确保不符合规范的产品应:u采用一致的标识(标签)明确标识出来U防止不合格品误用或误安装(遏制)•建立一个统一的采用目视方法进行标识的程序•必须通过遏制来防止不合格产品被误用或误安装。
•领导层必须建立,组织并维护一个体系来控制不合格产品。
•所有可疑产品和不合格产品必须被隔离。
3.0验证岗位验证岗位就是检查过程是否提供你所要的产品验证岗位也对频发的,低严重度不合格品提醒注意。
验证岗位最终减少缺陷零件数量,改善厂内一次合格率(FTQFirst time quality),直通率(Direct Run),从而在为顾客提供更好产品的同时也降低了成本。
•提供一个系统的方法减少过程变差。
•改善一次合格率(FTQ和提高过程能力:-迅速识别特殊原因变差。
-以数据做决定。
-系统地减少普通原因变差。
•警示操作员过程有变化。
•存在以下状况的任何过程或作业点:-高风险-PRR (顾客抱怨)-高RPN-低过程能力(Ppk, Cpk, FTQ) 任何Cpk或Ppk低于1.33的工序必须100% 检验。
QSB-质量基础体系
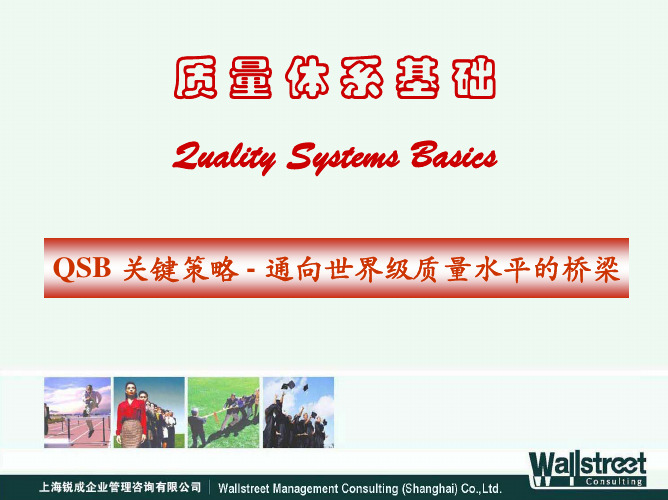
7: 分层过程审核
1
2
3
4
5
6
7
8
9 10
组织应该…
小 结
明确生产部门主导并执行分层审核 制定在分层审核过程中需验证的高风险项目表 设定审核频次(高风险项应至少一班审核一次) 审核适当的质量文件 跟踪和回顾分层审核的结果
8: 顾客接受的审核与评估
1
2
3
4
5
6
7
8
9 10
组织应该…
小 结
• 识别客户的满意项目 • 实施100%检验或相应的检验 • 直到永久性整改措施实施才能退出CARE. • 对不符项建立反应计划 • 评审C.A.R.E.结果
P24-P33
防错 验证
分层 审核
质量 验证
解决 问题
经验 教训
标识/ 遏制
操作员 培训验 证并记 录了吗
我们知 道风险 存在吗? 有防错 吗?
P39-P51
防错制 具有验 证吗?
领导层 审核进 行了吗
符合客 户要求 的产品 质量验 证
P80-P92
结构化 的解决 产品质 量问题
利用成 功,少 走弯路
小 结
• 建立多功能小组用以开发及实施标准化操作 • 所有的操作工位均应张贴标准化操作指导 • 对相关的人员或新员工进行标准作业的培训 • 确保标准操作指导应包括作业要素, 操作员移动 及生产节拍 • 根据目前的质量状态持续改进和提高标准作业指 导书
4: 操作员培训的标准化
1
2
3
4
5
6
7
8
9
10
组织应该建立必要的文件和跟踪方法
质量体系基础
Quality Systems Basics
(完整版)GQS05-QSB中文版-验证岗位解析

• 验证岗位应由“下游”数据来验证。
FR&PS NCM VS LPA EPV WPO SWI (SOS)
QSB WORKSHOP REV. 111406
5
OI (JES) SOT(JIT)
Risk Reduct
(例)
缺陷流出验证岗位 ➢顾客 PR&R 抱怨 ➢顾客夜班口头抱怨。 ➢Q-终检l/GP-12/CS-1/CS-2 ➢一次合格率 FTQ & 废品趋势图 (随时间)
问题解决 – 驱动在过程中解 决问题 - 制造质量
➢每周问题解决会议 ➢根据柏拉图分析,选择新问 题
➢每个参加人都必须在信息板 上签字
FR&PS NCM VS LPA EPV WPO SWI (SOS)
验证岗位(VS)描述
• 验证岗位是一个使我们集中注意制造质量的过程。
• 操作员用标准化作业指导书检查零件并为小组成员提供反馈。 • 用趋势图跟踪不合格件
• 确认验证岗位是否有效工作。 • 由专职操作员进行操作。
• 通过检测和立即解决问题,防止质量不符件流出验证岗位。 • 对识别出的不合格品采取整改行动。
Risk Reduct
Contam
SCM
General Motors Corporation. All rights reserved.
验证岗位信息板
FR&PS NCM VS LPA EPV WPO SWI (SOS)
QSB WORKSHOP REV. 111406
7
OI (JES) SOT(JIT)
Contam
SCM
General Motors Corporation. All rights reserved.
_防错装置验证流程

50
技术/工艺工程师
1,记录包括:(见6.记录之章节)。
6.记录
防错装置验证清单
防错装置验证记录
防错装置验证月度统计
2,建立【防错装置验证记录】。可能时,可开发建立防错装置验证标准件等;必要时应在被验证/确认/计量合格。
2,按计量器具管理要求标识标准件并建档管理。
3,适宜定位放置,方便取放、保证质量而不失效。必要时应定期更换。
4,在工序进行标识防错验证点(装置编号)。
4.2各个工序制造工程师/班组长负责实施验证、记录等。
4.3多功能小组负责因防错装置验证失效后的问题解决及装置改进。
5.流程及重要说明
编号
核心子流程
权责单位
实施要点
10
技术/工艺工程师
1,参考PFMEA/PCP、按工序建立【防错装置验证清单】:防错装置名称、防错机理、装置编号、验证流程、OK/NG验证标准件、频次、担当、反应计划等。
适用于本组织内部需要进行验证的防错装置和工序。
3.定义或术语
3.1QSB:质量体系基础。
3.2防错装置:运用防错原理/机制的装置,分为预防型(不制造不合格)和探测型(不接收、不放行不合格)。一般需要按策划的频次进行验证,以确保该装置的有效性。
4.职责
4.1技术/工艺部负责防错装置验证流程策划、验证记录之统计分析和流程管理维护。
Revision history 修订记录
版本号
修订日期(年-月-日)
修订人
修订简述
过程绩效
项次
测量指标
测量方法
监视周期
目标值
01
防错验证合格率
防错验证合格次数/防错验证总次数×100%
通用QSB(质量系统基础)学习资料

QSB WORKSQHSOBPWREOVR.K0S9H13O0P4REV. 062705 11
11
QSB Workshop REV.10
Manufacturing 1
Manufacturing 2
Manufacturing Corrects
Correct Process?
Correct Tool?
D3 D4
遏制Contain 临时措施(快速解决)以防止问题在客
户端发生
识别根本原因 列出所有导致问题发生的事情,使用系统性
的方法来识别和验证其中的根本原因Root cause:实验设计 DOE, 鱼骨刺图法, Drill Deep Analysis, 7钻石法 7 Diamonds (包括蓝卡片 Blue Card)等.
QSB WORKSQHSOBPWREOVR.K0S9H13O0P4REV. 062705 1
1
QSB Workshop REV.10
QSB 关键策略
• 快速反应
快速解决质量问题的标准化反应模式
• 不合格品控制
标识/遏制
• 标准化操作
作业指导书应包括要素和操作员移动
• 操作员培训的标准化操作员培训验证并记录了吗?
Problem Description: ___________________________________________________ ___________________________________________________ ___________________________________________________
QSB WORKSQHSOBPWREOVR.K0S9H13O0P4REV. 062705 6
QSB【快速反应】 介绍

风险降低 (RPN)
主动式风险降低
跨部门团队应该: • 执行定期PFMEA审查
• 在完成审查之后,建立最高(RPN)风险降低机会列表
• 制定一个行动计划(或类似计划)来跟踪降低RPN级别的 进展情况
Why RPN? Risk and Prioritization
It is important to give fair and spread-apart ratings
确定组织内合格的培训人员
合格的培训人员: • 利用标准化培训记录和培训柔性图表来指导操作员 • 监控新操作员的行为,并在必要时对其进行重新培训,以遵 守确保标准化操作 • 将潜在故障告诉下游操作部门
受训操作员跟踪表
确定哪些受训人员需要被追踪: • 操作名称 • 受训人员和培训完成日期 • 培训最新版本
7– LAYER PROCESS AUDITS 分层审核
8– RPN REDUCTION 风险降低
降低各类缺陷的风险
工艺更改 质量指示
程序流程
PFMEA
控制计划
作业指导
对作业人员 提供指导
降低 RPN
风险降低(RPN)
主动式和被动式策略以利用PFMEA减低质量风险 PFMEA
Quality Systems Basics 质量系统基础
Key Strategies 关键战略
质量系统基础
质量系统基础是通过10个关键策略以达到改进质 量的目的
10个关键策略的实施
• • • • •
利用系统化方式即刻大幅度降低运营成本 将组织由被动模式快速转变成主动模式 通过分层审核保持制造/装配的完整性 促进沟通 改进你的ISO/TS 16949 (QS-9000)质量体系
QSB
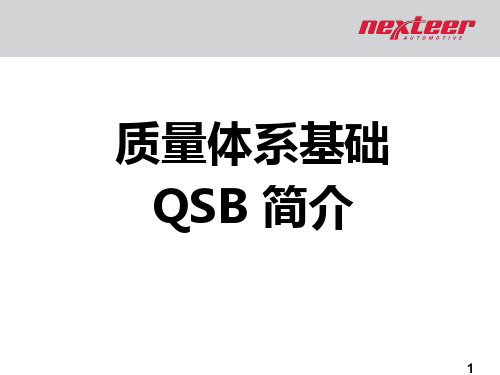
12
标准化作业的益处?
Without 没 有 Standardisation 标准作业 With 采 Standardisation 用标准作业
提供一个安全的工作环境
保持高质量水平 容易看到问到人力和设备的高利用率
13
标准化作业的三大模块
详细的动作步骤,怎样做, 为什么这样操 作。 操作主要步骤,每一步 骤所花时间 (平衡生产) 整洁、有序的工作 环境
29
10.0 供应链的管理
3级 供应商
2级 供应商
1级 供应商
Nexteer
OEM
客户热情
原材料 供应商
外协加工 服务
部件采购
供应链管理的目的:
提供一个管理整个供应链中各级供应商的标准化的程序。
您对供应商的期望是什么?
30
供应链管理要求
使用各种工具对其战略性分供方的特殊要求进行识别和 跟踪 开发一个衡量其所有分供方业绩的系统。包括对供应链各 级的评审 – QSB 审核,过程控制计划审核, PSA (潜在 供应商评审)等. 符合 ISO9001:2000 是达到目标的第一 步. 在供应链中交流 Nexteer 的期望和要求。使用管理工具, 如:对问题的反馈,业绩指标,供应活动的评审, 和问 题解决工具。 通过应用共同的原则,方法和系统来支持持续改善质量水 平, 降低PPM以及零件的故障产生的费用
维护保养的目的是什么?
目的: 保持各类设备在正常的工作条件下运行 提高设备的总运行效率 推动相关活动的风险管理 管理各种类型的维护保养 备品备件的管理
范围: 装配区域, 制造生产线, 维护区域, 所有生产区域
职责: 主管:设备维修经理 生产经理
SGM QSB 概述(1509)

SGM 质量系统基础概述
2015.9.7
共同打造有全球竞争力的供应链体系 Global Competitive Supply Chain Collaboration
1
QSB质量系统基础概述
什么是QSB? QSB------Quality Systems Basics,质量系统基础。
无重大质量问题 → 无PR/Rs → 0 PPM = 世界级质量
共同打造有全球竞争力的供应链体系 Global Competitive Supply Chain Collaboration
6
QSB质量系统基础概述
工具应用和分工: ( 已按部门优先级排序, 蓝色必须参加)
Hale Waihona Puke QSB QSB-1 QSB-2 QSB-3 QSB-4 QSB-5 QSB-6 模块名称 快速响应 不合格品控制 防错验证 标准化操作 标准化操作工培训 分层审核 执行内容和职责分工简述 跟踪内部问题解决(占多数)----制造,跟踪外部问题解决---质量 制造过程中的不合格品控制---制造,客户质量抱怨和遏制—制造/质 量 制造过程中的防错装置的有效性检查---制造, 制造过程员工的操作要求、步骤和方法的标准化---制造 制造过程操作员工的标准化培训方法---制造 制造过程的符合性审核----制造
4. 供应商应用SGM QSB模块,是对其自身体系的完善和补充,应用的型式以体系融合为主 ,不拘泥于表面形式,不以建立一个全新的模式为目的; 5. 供应商会面临各个主机厂的不同要求,QSB是融合并完善这些要求,最终使TS16949质 量体系的要求得到充分、有效地满足; 6. 质量体系的建设和完善是一个长期的过程,QSB的应用也需要长期的坚持,最终融入并
QSB防错验证流程图

目的:不生产不传递不良品,为保证公司能够持续提高产品质量,降低成本,并积极的制造创新
责任部门/人
输入
防错验证流程
设备部
需要建立防错的原则
作业前准备
生产部
设备防错操作规范
生产部
作业指导书
设备防错点检NLeabharlann 通过Y产品加工
生产部
暂停生产
管理编号: YTSB002
输出 防错装置清单
责任部门/人 设备部
防错完好率柱状图
第三方支持性文件: 快速反应原则 作业指导书 报警流程
质量部
设备部
设备部
设备部 设备部
高层
设备点检表
设备部
报警流程
质量部
生产部
设备点检表
快速反应
停产整修
维修人员 防错验证
防错统计
防错维修记录及升 级汇报流程与紧急
措施
设备点检表
防错失效统计表
设备部
设备防错失效表
防错改进
防错改进报告
结束
支持性文件: 防错装置清单(仅指出哪个工位哪台设备哪个部分有防错) 防错验证操作指导(图文并茂,阐述清楚流程性标准步骤,以及相关耗时) 设备点检表(不做任何的分析与评价,只是如实记录表中涉及的点检内容) 设备维修清单(设备维护人员根据失效形式进行相关的处理及记录不做任何分析) 防错失效统计表(设备工程师对每个设备建立防错失效档案,便于分析统计) 防错改进报告(高层要定期审核)
防错验证
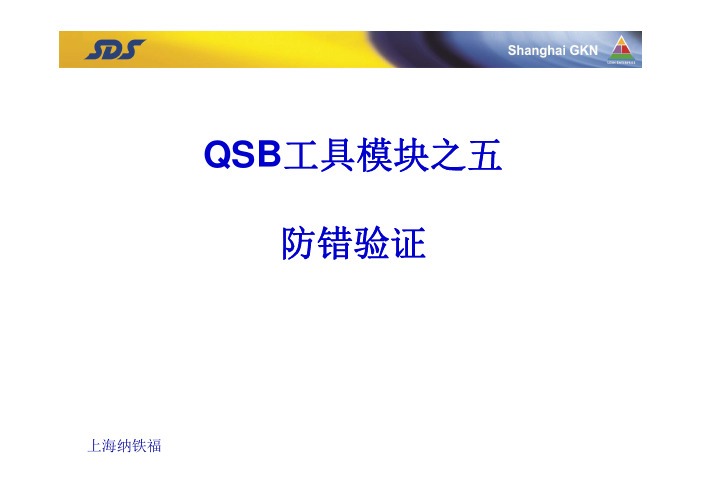
QSB工具模块之五防错验证上海纳铁福上海纳铁福2内容◆防错验证的目的和定义◆防错验证的要求◆防错验证的策划准备◆防错验证的实施和结果报告◆防错验证关键要点◆防错验证相关文件和记录保存上海纳铁福3防错验证的目的•确保防错/错误探测装置正常工作•防止制造中传递不合格品•为每台防错装置建立历史档案以指示何时需要对其进行预防性维护或维修•在整个过程中培养良好的行为规范上海纳铁福4防错验证的定义•所有可能的失效、磨损、移位或超出调整范围的防错、探测装置,每班必须最少验证一次,首选的方法是在开班前或在生产过程中由生产线操作员工/生产线班长来实现防错验证•防错装置--(不制造)--防止加工或装配不合格品产品的装置•错误探测装置—(不传递或不接受)--防止传递不合格品的装置(如100%在线检测设备)•防错验证不是校准量具,而是将一个已知的好/坏的零件分别通过防错装置,以确认装置功能有效。
防错验证的要求上海纳铁福5上海纳铁福6防错验证的策划准备•防错/错误探测装置的清单:明确识别码(编号)、名称、功能、分布、相应标准操作规程编号•标准操作规程:定义调整、点检、维护、反应计划•为每台防错/错误探测装置制作日常点检记录•培训操作员工、班长、现场质量员•按标准化作业培训要求培训防错装置作业指导书•如增加或更新防错装置,需同时评估清单、操作规程、记录、标准化作业培训的更新需求上海纳铁福7防错验证的实施和结果报告•操作员工按防错装置点检记录实施点检并记录•现场质量监督人员对防错装置实施周抽查•对于点检时发现问题或防错装置使用过程发现的问题按反应计划执行•现场质量工程师汇总防错装置验证结果并报告•领导层检查和评审防错验证的结果防错验证实施要点上海纳铁福8防错验证记录的保存•防错装置点检记录•防错装置异常情况统计表•防错装置验证结果汇总表•防错装置不合格时的反应计划执行情况记录上海纳铁福9防错验证实施案例•TULIP1#防错装置标准操作规程•TULIP1#防错装置点检记录上海纳铁福10谢谢!上海纳铁福。
QSB质量系统基础课程大纲
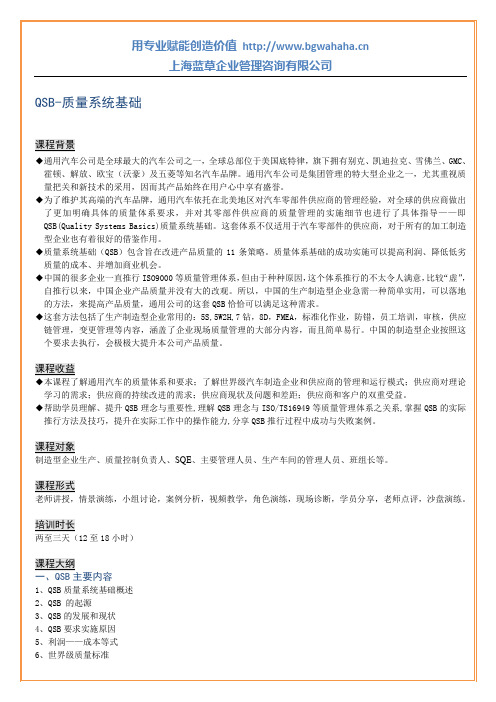
6、经验教训总结——经验总结、验矩阵
7、有效问题解决方法实践
8、七颗钻石法
9、8D报告
10、5W2H
三、不合格产品控制
1、停止灯控制
2、不合格产品标识
3、隔离区
4、遏制表单
5、与顾客沟通
四、验证岗位
1、为什么需要验证岗位
2、哪些区域应该设立验证岗位
3、如何设立验证岗位
4、验证岗位工作内容
3、培训记录
4、培训要求
5、培训灵活单
七、防错验证
1、为什么要防错验证
2、防错验证定义
3、防错验证的要求
4、防错验证检查表
5、防错验证结果
八、分层审核
1、为什么做分层审核
2、分层审核定义
3、分层审核的要求
4、分层审核检查清单
5、分层审核的频率
6、分层审核的整改
九、风险降低流程
1、为什么实施风险降低
2、降低质量风险定义
◆这套方法包括了生产制造型企业常用的:5S,5W2H,7钻,8D,FMEA,标准化作业,防错,员工培训,审核,供应链管理,变更管理等内容,涵盖了企业现场质量管理的大部分内容,而且简单易行。中国的制造型企业按照这个要求去执行,会极极大提升本公司产品质量。
课程收益
◆本课程了解通用汽车的质量体系和要求;了解世界级汽车制造企业和供应商的管理和运行模式;供应商对理论学习的需求;供应商的持续改进的需求;供应商现状及问题和差距;供应商和客户的双重受益。
QSB-质量系统基础
课程背景
◆通用汽车公司是全球最大的汽车公司之一,全球总部位于美国底特律,旗下拥有别克、凯迪拉克、雪佛兰、GMC、霍顿、解放、欧宝(沃豪)及五菱等知名汽车品牌。通用汽车公司是集团管理的特大型企业之一,尤其重视质量把关和新技术的采用,因而其产品始终在用户心中享有盛誉。
QSB防错建立的基本准则
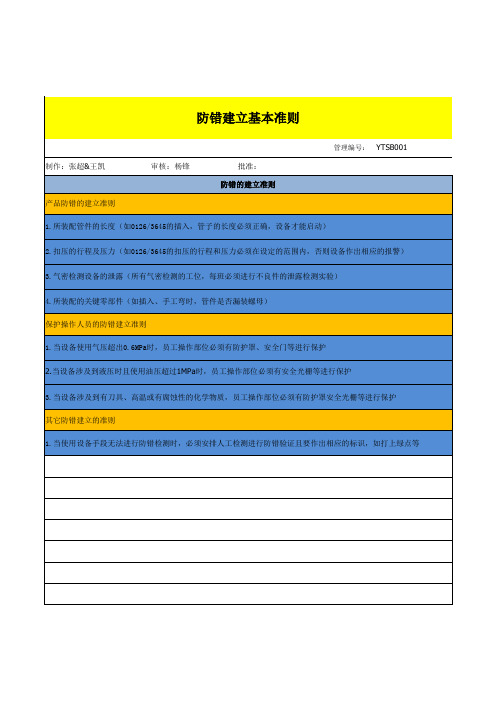
4.所装配的关键零部件(如插入、手工弯时,管件是否漏装螺母) 保护操作人员的防错建立准则 1.当设备使用气压超出0.6MPa时,员工操作部位必须有防护罩、安全门等进行保护
2.当设备涉及到液压时且使用油压超过1MPa时,员工操作部位必须有安全光栅等进行保护
3.当设备涉及到有刀具、高温或有腐蚀性的化学物质,员工操作部位必须有防护罩安全光栅等进行保护 其它防错建立的准则 1.当使用设备手段无法进行防错检测时,必须安排人工检测进行防错验证且要作出相应的标识,如打上绿点等
防错建立基本准则
制作:张超&王凯 产品防错的建立准则
审核杨锋
批准: 防错的建立准则
管理编号: YTSB001
1.所装配管件的长度(如0126/3645的插入,管子的长度必须正确,设备才能启动)
2.扣压的行程及压力(如0126/3645的扣压的行程和压力必须在设定的范围内,否则设备作出相应的报警)
3.气密检测设备的泄露(所有气密检测的工位,每班必须进行不良件的泄露检测实验)
QSB实施程序

1.范围:本程序合用于汽车用无缝钢管产品。
2. 目的:实现质量体系基础关键策略,确保汽车零部件满足顾客要求。
一、 快速反应程序1.术语:快速反应:通过每日例会加强沟通和管理,采用目视管理方法展示重要信息,使应对重大的内、外部质量问题的反应标准化。
问题解决:一个系统化的用来识别、分析和消除现状和现行标准或者期望之间的差距,并预防根本原因再 次发生的过程。
经验总结:利用成功经验,防止错误重复浮现。
2.职责: (1)创造部负责快速反应会议,质量部,技术部,设备部等赋予支持。
(2)问题负责人负责采用 8D 等方法、运用相应工具解决问题。
(3)各负责部门负责其相应经验教训活动,总经办负责文件归档和发布。
3.快速反应会议:3.1 开会时间:每天一次,每次 10~15 分钟,会上只对质量问题进行沟通。
3.2 开会地点:生产现场看板前或者生产现场办公室。
3.3 参会人员:所有部门(财务部外)的第一责任人,因故不在候补出席。
3.4 会议主题:应对每天的具体重大质量问题。
3.5 会议准备:每天质量部每天找出过去 24 小时发生的重大质量问题,开会前详细描述在白板上。
具体问题包括:(1)客户关注的问题; (2)供应商关注的问题; (3)停线(内部或者外部); (4)重复发生的质量问题;(5)除调车废品以外班废品率超过综合废品率目标; (6)验证岗位中发现的问题; (7)分层审核中发现的问题; (8)其它内部质量问题。
3.6 会议内容:(1)会议主席协调各方意见,确定新问题的责任人和关闭日期。
(2)旧问题负责人提交相关报告,报告具体进度,紧抓问题退出标准,由预会人员确认关闭。
(3)会议主席根据当天情况,标明具体问题和日 Q 图的状态。
3.7 会后工作:问题负责人运用 8D 等方法、相关工具解决问题,总结形成报告。
3.8 其他定期工作:快速反应跟踪表应记录所有产生的问题。
文件名称 质量体系基础关键策略实施程序共 9 页发行日期第 1 页每月汇总发布问题发生数趋势图。
QSB标准理解

QSB标准理解一、不良品对于不良品呢,我们要坚决的采取围堵和遏制措施,任何一种物料都需要进行标识(合格品,转序品,不合格品),且标识不容易掉落。
物料存储区域采用红绿黄进行区域标识,很明显的,当我们看到红色时,就会立即想到这是不良品,减少不良品错拿流转的风险。
在不良品隔离区,需要进行封闭上锁,无关人员不得进入,这也是一种控制不良品错拿流转的手段。
所有的产品都不得混装,产品和各类物资等都必须定置定位摆放二、分层审核①我们的分层审核必须要确保我们的领导层参与,不能浮于形式,在八大质量管理原则中,明确的提到领导的带头作用,只有领导重视质量,亲力亲为,基层员工就会逐渐养成质量意识,自主加强品质控制。
②我们的分层审核不仅要包括一般性检查,工位上的人机料法环测啊,还要从客户的角度增加客户要求(就是顾客关注项),例如PRR里面的问题反馈,客户的特殊要求等等。
③分层审核发现的问题要上升到快速反应会议,立即解决。
分层审核是一个最简单的基础,我们的要求就是做到不接受,不制造,不传递不良品的三不原则。
三、四过程失效模式及其后果分析PFMEA降低风险和年度复查①必须按照AIAG美国汽车工业协会第四版PFMEA的内容和要求进行我们的过程失效模式及后果分析,PFMEA的格式文本结构正确,符合要求。
②要关注SOD评分,S为严重度,O为发生频度,D为探测度,每一项的打分都必须符合具体给分原则,例如在涉及到人的探测度打分时,只能给7分。
③对RPN风险降低活动进程,我们需要进行一个月度评审。
④PFMEA呢是一种用来持续改进,减少风险的工具,还不是当问题发生后才记录进去。
⑤RPN现在不为GM采用,GM现在现在采用一种图表的表示方法,GM要求对PFMEA进行更新,但仍可以保留RPN的判断方式。
925744五、设备、设施更换管理①在所有生产GM产品的设备中,我们要事先识别哪一台机器可能停机并导致影响生产GM产品,要时时掌控设备的情况,并列出一个清单,识别这些机器设备的情况②要指定哪些设备可以进行代替生产GM产品,要有一个替代预案。
质量体系基础(QSB)

五、标准化的操作员培训
➢对组织的要求: ✓确保通过“操作员培训跟踪表”跟踪员工
的培训 ✓在每一操作工位张贴“操作员培训跟踪表” ✓通告下游工序新员工操作可能产生的潜在
失效
✓培训近三个月内未进行过该岗位操作的后 备人员
六、风险降低程序
满足顾客要求(时间、步骤、沟通等) ✓领导层必须对产品遏制问题进行审核
四、验证岗位
➢定义: ✓是一个通过预防、探测和遏制异常情况的
在线制造质量系统。 ✓检查过程是否提供你所要的产品
四、验证岗位
➢验证岗位的描述:
验证岗位是一个使我们集中注意制造质量的过程 操作员通过标准化的作业方式检查零件并为小组
➢两种类型:
主动式:
✓ RPN降低流程 ✓ 降低潜在质量失效的风险
被险降低程序
➢过程失效模式及后果分析(PFMEA)的定 义:
是对每一个过程步骤进行分析的技术,以识别: ✓ 过程可能达不到要求的情形 ✓ 对内部/外部顾客的影响(严重度) ✓ 失效可能发生的频率(发生频度) ✓ 当前控制的效果(预防和可探测度) ✓ 原因和结果的等级(风险顺序数)
五、标准化的操作员培训
➢操作员培训四步法: ✓第一步:成员准备 ✓第二步:演示、示范 ✓第三步:试操作 ✓第四步:跟踪
五、标准化的操作员培训
五、标准化的操作员培训
➢要求:
✓ 培训师必须以既定的频次检查受训员工的操作质 量以确保达到所有的操作标准
✓ 操作员培训必须被跟踪记录在“操作员培训跟踪 表”里
一、快速反应程序
➢对组织的要求(2): ✓责任人必须在快速反应会议上更新和汇报
进展状态 ✓建立明确的问题解决流程来识别和消除发
- 1、下载文档前请自行甄别文档内容的完整性,平台不提供额外的编辑、内容补充、找答案等附加服务。
- 2、"仅部分预览"的文档,不可在线预览部分如存在完整性等问题,可反馈申请退款(可完整预览的文档不适用该条件!)。
- 3、如文档侵犯您的权益,请联系客服反馈,我们会尽快为您处理(人工客服工作时间:9:00-18:30)。
November 200his presentation was developed by General Motors Corporation Worldwide Purchasing. All rights reserved. No part of this material may be reproduced in any form, or by any method, for any purpose, without written permission of General Motors Worldwide Purchasing.
•建立防错验证失效及对失效进行的整改的记录 •建立表格,以通知不符合项及逐级汇报不符合反应行动。。 • 将以上信息做为经验积累存档
工厂管理层必须要定期回顾验证记录.
•确定收集相关信息的方法 •确定哪些信息需要公布/展示
FR&PS NCM VS LPA EPV WPO SWI (SOS)
QSB WORKSHOP REV. 111406
4
OI (JES) SOT(JIT)
Risk Reduct
Contam
SCM
General Motors Corporation. All rights reserved.
(例)
防错验证检查表
是否有卡环
工序#
以下项目必须每天检查
OP 30 4 在左/右卡环安装工装上不装卡环-工件是否被拒收?
OP 30 5 灯柱上的红灯是否亮 ? (左&右)
防错装置被验证过吗?
FR&PS NCM VS LPA EPV WPO SWI (SOS)
QSB WORKSHOP REV. 111406
2
OI (JES) SOT(JIT)
Risk Reduct
Contam
SCM
General Motors Corporation. All rights reserved.
OP 30 6 被拒收的工件是否仍然在工作台内? (左&右)
OP 30 7 按灯报警器是否响起?(左&右)
OP 40 8 在小卡环安装工装上不装卡环-工件是否被拒收?
9 灯柱上的红灯是否亮 ? (小卡环)
10 被拒收的工件是否仍然在工作台内? (小卡环)
11 按灯报警器是否响起?(小卡环)
12 当手动确认工具上红色拒收灯亮起时,工件是否仍然在工位内?
错误检测设备 -(不传递或不接受)-防止传递不合格产品的装置
(如100%在线检测设备)
FR&PS NCM VS LPA EPV WPO SWI (SOS)
QSB WORKSHOP REV. 111406
3
OI (JES) SOT(JIT)
Risk Reduct
Contam
SCM
General Motors Corporation. All rights reserved.
防错装置必须至少每天验证一次。 防错装置的位置必须被记录在案。 必须制定防错装制失效的应对计划。 必须记录防错验证结果。 领导层必须检查和评审防错验证的结果.
FR&PS NCM VS LPA EPV WPO SWI (SOS)
QSB WORKSHOP REV. 111406
8
OI (JES) SOT(JIT)
JAN
FEB
MAR
APR
MAY
JUNE
JUL
AUG
SEP
OCT
NOV
DEC
% IN COMPLIANCE: # OF ITEMS ON CHECKLIST:
# OF VERIFICATIONS TOTAL # OF ITEMS VERIFIED: # OF ITEMS IN COMPLIANCE:
JAN
班次:
日期:
编号 YES NO 4 5 6 7 8 9 10 11
182 15 12 13 14
YES NO
总计
问题描述
所有不符合项目必须由主管评审,或复印一份检查表交给主管。
防错验证的完成情况必须被记录并展示在工位上。防错装置的验证 状态必须被清楚的被所有人看到。
FR&PS NCM VS LPA EPV WPO SWI (SOS)
FR&PS NCM VS LPA EPV WPO SWI (SOS)
QSB WORKSHOP REV. 111406
1
OI (JES) SOT(JIT)
Risk Reduct
Contam
SCM
General Motors Corporation. All rights reserved.
ERROR PROOFING VERIFICATION 防错验证
必须要记录防错验证的结果, 这样可以对防错装置失效做出迅速的反应.
• 明确定义防错装置失效时的反应计划 • 当如果防错装置不能检测出残次品,什么时候停机? • 遏制计划? (100% 检验,等.) • 可疑品是否 需重新通过防错装置? • 怎样/什么时候防错装置需要维修?
•在防错装置确认之间生产的产品的批量数量 • 用过程的历史记录决定验证的频率 • 过程是否稳定 • 可疑品的遏制是否有效
6
OI (JES) SOT(JIT)
Risk Reduct
Contam
SCM
General Motors Corporation. All rights reserved.
防错验证
益 处:
• 确保防错装置/检测设备按照设定的功能正常工作。 • 防止不合格产品被制造或被传递。 • 为每个防错装置建立历史数据记录, 为是否需要进行预防性维护和 必要的维修提供基础. • 逐步强化纪律。
Risk Reduct
Contam
SCM
General Motors Corporation. All rights reserved.
防错验证
所有的防错装置必须被验证, 相关防错装置的位置应该被记录.
• 防错装置在主控文件中应有识别号和位置 • 确认防错验证频率 • 确定标准样件(好的/坏的)以及检查的时效模式
当 防 错 装 置 被 查 证 出 失 效 时 ,应 该 必 须 马 上 启 动和跟踪相应的反应计划.
防错装置必须每天至少验证一次.
13 是否可看到小卡环?
14 当小卡环安装工具出现故障,备份检具是否可用?
15 如果没有安装小卡环,备份检具是否可拒收工件?
16 红色指示灯是否亮? (小卡环备份安装工具)
主管: ______________________________
检查人: _________________________________ 当标为黄色的项目不合格时,必须立即通知主管。
FR&PS NCM VS LPA EPV WPO SWI (SOS)
QSB WORKSHOP REV. 111406
7
OI (JES) SOT(JIT)
Risk Reduct
Contam
SCM
General Motors Corporation. All rights reserved.
防错验证小结
防错验证
所有可能失效,磨损,移位或超出调整范围的防错/检测设备,每天必须 最少检验一次。 首选的方法是在开班前或在生产过程中由生产线作业员/ 生产线班组长来实施防错验证。
注:防错装置不是校准一个量具 (如:调零位),而是将一个已知的好/ 坏零件分别通过防错装置,以确认防错功能是否有效。
定 义:
防错装置 -(不制造)-防止加工或装配不合格产品的装置
QSB WORKSHOP REV. 111406
5
OI (JES) SOT(JIT)
Risk Reduct
Contam
SCM
General Motors Corporation. All rights reserved.
(例)
部门.____________
防错验证结果
100% 90% 80% 70% 60% 50% 40% 30% 20% 10% 0%
FEB
MAR APR MAY JUNE
JUL
AUG SEP
OCT NOV DEC
ITEMS NOT IN COMPLIANCE
NUMBER OF ITEMS NOT IN COMPLIANCE
FR&PS NCM VS LPA EPV WPO SWI (SOS)
QSB WORKSHOP REV. 111406