加工劣质原油设备腐蚀与防护技术
石油炼制设备腐蚀及防护措施探讨
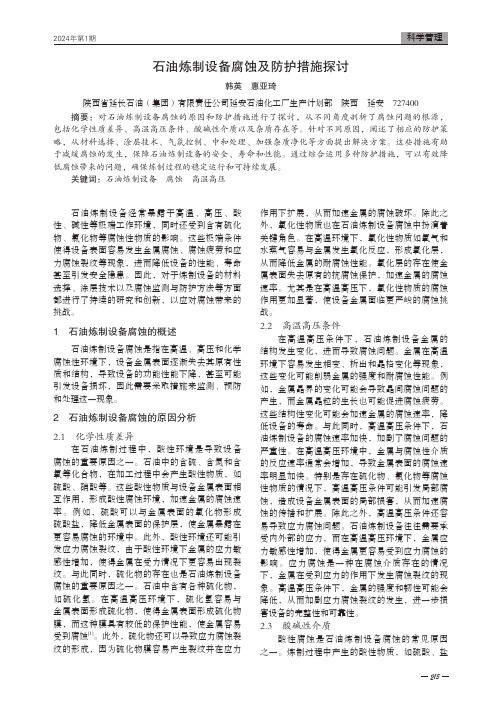
215石油炼制设备经常暴露于高温、高压、酸性、碱性等极端工作环境,同时还受到含有硫化物、氯化物等腐蚀性物质的影响。
这些极端条件使得设备表面容易发生金属腐蚀、腐蚀疲劳和应力腐蚀裂纹等现象,进而降低设备的性能、寿命甚至引发安全隐患。
因此,对于炼制设备的材料选择、涂层技术以及腐蚀监测与防护方法等方面都进行了持续的研究和创新,以应对腐蚀带来的挑战。
1 石油炼制设备腐蚀的概述石油炼制设备腐蚀是指在高温、高压和化学腐蚀性环境下,设备金属表面逐渐失去其原有性质和结构,导致设备的功能性能下降,甚至可能引发设备损坏,因此需要采取措施来监测、预防和处理这一现象。
2 石油炼制设备腐蚀的原因分析2.1 化学性质差异在石油炼制过程中,酸性环境是导致设备腐蚀的重要原因之一。
石油中的含硫、含氮和含氧等化合物,在加工过程中会产生酸性物质,如硫酸、硝酸等。
这些酸性物质与设备金属表面相互作用,形成酸性腐蚀环境,加速金属的腐蚀速率。
例如,硫酸可以与金属表面的氧化物形成硫酸盐,降低金属表面的保护层,使金属暴露在更容易腐蚀的环境中。
此外,酸性环境还可能引发应力腐蚀裂纹,由于酸性环境下金属的应力敏感性增加,使得金属在受力情况下更容易出现裂纹。
与此同时,硫化物的存在也是石油炼制设备腐蚀的重要原因之一。
石油中含有各种硫化物,如硫化氢。
在高温高压环境下,硫化氢容易与金属表面形成硫化物,使得金属表面形成硫化物膜,而这种膜具有较低的保护性能,使金属容易受到腐蚀[1]。
此外,硫化物还可以导致应力腐蚀裂纹的形成,因为硫化物膜容易产生裂纹并在应力作用下扩展,从而加速金属的腐蚀破坏。
除此之外,氧化性物质也在石油炼制设备腐蚀中扮演着关键角色。
在高温环境下,氧化性物质如氧气和水蒸气容易与金属发生氧化反应,形成氧化层,从而降低金属的耐腐蚀性能。
氧化层的存在使金属表面失去原有的抗腐蚀保护,加速金属的腐蚀速率。
尤其是在高温高压下,氧化性物质的腐蚀作用更加显著,使设备金属面临更严峻的腐蚀挑战。
原油加工过程氯的腐蚀与防治问题

原油加工过程氯的腐蚀与防治问题摘要:对于原油加工而言,腐蚀问题历来是管理重点和难题,其中氯化物的腐蚀最为突出,既影响了设备性能,也对炼厂安全构成了威胁,故必须加以有效防治。
对此,笔者阐述了原油加工中氯化物腐蚀的危害,并以其腐蚀机理为切入点提出了几点防治措施,希望对缓解原油加工中氯的腐蚀现状有所助益。
关键词:原油加工;氯化物腐蚀;防治近年来,原油重质化、劣质化问题日益严重,尤其是氯元素的不断增加,对设备性能和炼厂安全构成了极大的威胁,进而使得氯化物超标问题备受关注。
这就要求我们重视原油加工中氯腐蚀的高危害性,并立足实际采取切实有效的措施加以防治,通过减少氯的含量,促进原油加工朝着安全、高效、优质的方向发展。
一、原油加工过程中氯腐蚀的危害由于油田时常会遇到油井堵塞问题,制约了采油产量的提高,所以往往会加入含有氯代烷烃的清蜡剂、降凝剂、降粘剂、清解堵剂等诸多化学药剂来改善采收率,当其与原油一同进入炼油系统时,便会直接或间接的腐蚀炼油设备和装置。
具体的说,当化学药剂中的氯代烷烃经高温水解形成氯化物后会在蒸馏塔中严重腐蚀减压蒸馏装置、冷凝装置,使其难以安全生产,而且还可能引发管道阻塞、催化剂中毒等问题,如某炼油厂的常减压装置在氯化物的腐蚀下出现了多次泄露、塌陷、浮阀脱落问题,高压换热器和空冷也存在严重的腐蚀等等,二次加工装置也难以幸免。
故原油加工过程中氯的腐蚀无论是对炼油生产装置的安全运行使用寿命,还是企业的经济效益,均带来了巨大的不良影响,亟待改善。
二、原油加工过程中氯的腐蚀机理之所以在原油加工过程氯腐蚀的防治问题中分析氯的腐蚀机理,是因为只有了解其形成过程,才能对症下药提高防治措施的有效性,更好的解决氯腐蚀问题。
研究发现,原油加工过程中的氯主要分为有机氯化物和无机氯化物,虽然两者属性不同,但均会造成设备腐蚀以及催化剂中毒,而且腐蚀设备的过程都与 HCl有关。
无机氯化物可与水直接发生化学反应生成 HCl,而有机氯化物则难以发生水解,但当其到达减压塔时,经电脱盐处理后的水 PH 值会有所提升变为碱性,致使部分有机氯化物发生水解产生气体 HCl,并随油气流一同到达减压塔顶部,当其遇到水便会形成腐蚀性强的稀盐酸,最终腐蚀设备,同时少量的水蒸气达到冷凝系统变成冰时,气体 HCl 会溶于其中形成稀盐酸环境,进而对周围设备造成腐蚀[1]。
加工劣质原油腐蚀控制
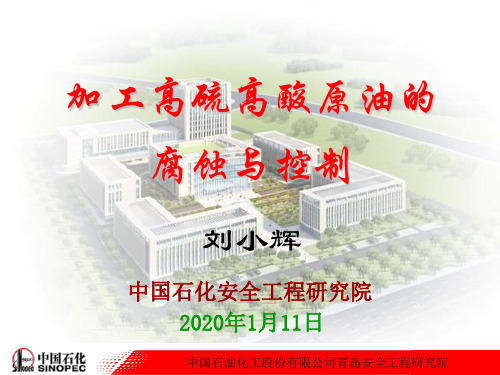
环烷酸腐蚀
经验表明,在一定温度范围内(通常指超过220℃), 存在一个临界酸值,高于此值,腐蚀速率明显加快。然 而,很难确定导致环烷酸腐蚀的临界酸值。例如,国外 有的学者认为,原油酸值超过0.5mgKOH/g 时才会引起 环烷酸腐蚀,而有的则认为临界酸值介于1.5-2mgKOH/g 之间,还有的则认为,含5%的环烷酸就可导致腐蚀发 生。这是因为实际腐蚀体系中影响环烷酸腐蚀的因素多 ,交互作用复杂,比如流速、材质、环烷酸的种类等都 与临界酸值有关。国内炼油厂普遍接受0.5mgKOH/g 为 导致环烷酸腐蚀的临界酸值。
加工高硫高酸原油的 腐蚀与控制
刘小辉
中国石化安全工程研究院 2020年1月11日
中国石油化工股份有限公司青岛安全工程研究院
课程内容
1 劣质原油及腐蚀应对技术现状 2 加工劣质原油的腐蚀风险所在 3 高酸原油的腐蚀与防护 4 高硫原油的腐蚀与防护
5 有机氯及高硫高酸腐蚀研究热√点问题
中国石油化工股份有限公司青岛安全工程研究院
11
中国石油化工股份有限公司青岛安全工程研究院
腐蚀应对技术现状
国内技术
第一:生产实践和科研中积累了一些 宝贵的经验,特别是沿海企业
第二:掺炼和单炼结合
第三:制定了一系列行业标准和管理规定
第四:寻找新的工艺路线,以此解决劣质 原油加工过程出现的严重腐蚀问题
中国石油化工股份有限公司青岛安全工程研究院
腐蚀应对技术现状
高酸原油。
中化泉州石化每 年可以加工1200 万吨高硫原油
中国石油化工股份有限公司青岛安全工程研究院
腐蚀应对技术现状
国外技术
McConomy曲线
Copper曲线
加工俄罗斯含硫原油的设备腐蚀与防护

e 膜被 迅 速 中刷破 坏 . 装 置 加 工含 硫 原 油提 供 最 佳 的工 艺操 作 形成 涡流 的部位 F S
指导 . 期最大程 度地减 少设备 的腐蚀 。 以
了 电脱 盐 装 置平 稳 操 作 降 低 原 油 脱 后 含 盐 量 外 要 对 初 馏塔 、 还 常压 塔 、 压 减 塔 进 行工 艺 防腐 , 在塔 顶 进 行 注 中和 即
1 低 . { _t - ¨ S+ Cl_ 0 l H
低 温 硫 腐 蚀 发 生 在 温 度 小 于 1 0C 。 5
的轻 油部 位 , 即初馏 塔 、 常压 塔和 减 压塔 塔 顶 油汽 挥 发线 及其 后 的冷 凝冷 却 系统 管 道 。 部 位 对 碳 钢 产 生均 匀腐 蚀 , 该 对 O r 钢也 有腐蚀 。 Cl 3
剂. 蚀 剂和 水 。 缓 () 中和 剂 : 分 馏 塔 顶 馏 出线 上 1注 在 注 中和 剂 。 和 剂 能 中和 H IHS 中 C 、 。 调 整
加 剧 了设 备 的腐 蚀 。 因此 , 叶轮 、 线 弯 管
头 、 嘴 等 部 位 首先 发 生 腐 蚀 减 薄 甚至 管
二 、含硫 原 油硫 腐蚀 的 形态 和腐 蚀 机理 穿 孔 。 原 油 中 的硫 以 多种 形 态 存 在 , 分 可 为 活 性硫 和 非 活性 硫 。 性 硫 是 指 可 以 三 、 防 护 措 施 及 结 论 活 直接 与金 属起 反 应的硫 化物 , 如单体 硫 、 硫 化 氢和 硫 醇 非活 性 硫 则 不 能 直 接 与
的升 高 顶低 温部 位设 备腐蚀 加大 腐 塔
蚀 的类型 主要 是HS H I ,腐蚀 。 + C+HO
0. 0 2%
.Hale Waihona Puke 塔 顶 冷 凝 冷 却系 统 的p 值 . 入 的 中和 H 注 1 改 进 工 防 腐 描 施 剂和缓 蚀 剂配 合 , 发挥 缓蚀 剂的作 用。 能 低 温轻 油 区 的腐蚀 主要 是 由无机 盐 中和 剂 的注入 量要 保证能 中和 全 部 的H I C 水 解 引起 的露 点 腐 蚀和 由有害 报 离 子引 和 HS 控 制 冷 凝 水 的 p 值 在 7 9 ,, H - 。 起 的 应 力腐 蚀 . 些都 与 电脱 盐 效 率 有 这 () 缓 蚀 剂 : 蚀 剂 在 其 分 子 内带 2注 缓 关 。因 此 , 进 工 艺 防 腐 措 施 . 高 脱 盐 改 提 有极 性基 因, 吸 附在金 属 表面形成保 护 能 率是 防止 低 温轻 油 区腐 蚀 的 有效 途 径 。 膜 , 腐 蚀 介质不 能与其 表 面接触 . 到 使 起 针对该 装 置情 况 主要 有 : 保 护 作 用。当p 值 低 ( H 小于2 ) 温 度高 ~3 . () 整 注 水 量 : 油 脱 盐 就 是 在 原 1调 原 ( 于2 0C) 缓蚀 剂会 失 效 。 大 3 。 时, 因此要求 油中注水 使油 水充 分混合 . 原油 中的盐 使 在 注 缓 蚀 剂 前 先 注 中和 剂 . 制 其 p 值 。 控 H 溶 于 水 中 随 水 一 起 脱 出 。 规 定 一 般 原 按 在 塔 顶低 温部 位 塔 顶 油 气 线 速 过 大 . 也 油 的 注 水 量 应 为原 油 的 3 ~5 % % 由于 俄 会 影 响 保 护膜 的形 成 , 般 缓 蚀 剂 的注 一 罗斯 原 油 的 含 盐 量 低 . 升 原 油 的 N C 每 aI 入 量控 制在馏 出物的 ( 一2 ) 0 既可 1 O X1~。 O 含 量 一 般 都 在2 mg 右 , 装 置 的注 水 0 左 故
关于石油炼制设备腐蚀的防治措施

关于石油炼制设备腐蚀的防治措施摘要:对于石化公司来说,石油精炼设备对其石油生产效率具有至关重要的影响。
当炼油厂发生严重腐蚀时,会影响炼油和石油生产的正常过程,阻碍石油企业的长期发展,甚至可能对石油生产商造成健康危害。
因此,中国石油企业必须对炼油厂的腐蚀现象采取一定的防护措施,使炼油设备能够长期使用。
基于此,对石油炼制设备腐蚀的防治措施进行研究,以供参考。
关键词:石油炼制设备;腐蚀;防腐措施引言为促进石油炼制设备安全运作能力的提升,提高石油企业生产效率,首要任务就是解决设备腐蚀问题,认真总结导致设备发生腐蚀的各项因素,在后续腐蚀防治工作中,加强耐高温、耐高压和耐腐蚀性新材料以及新型防腐技术的推广和使用力度,全面做好石油炼制设备腐蚀治理这项工作。
1腐蚀概念及相关介绍腐蚀是专业化学中常用的一个化学术语,它是一种用化学表达式改变物质基本性质的过程,它是通过与环境的接触而实现的,这一过程产生化学反应是由环境因素引起的,导致材料本身的性质和性能不可逆转的变化,当然,人们所描述的腐蚀通常是指金属材料,这种腐蚀主要是指环境中金属的一系列变化或化学反应,破坏金属本身特性的一般情况下,腐蚀不可避免地会影响到石油本身的材料本身,而石油本身经常被直接用于生产,需要一些炼油厂和加工厂制造原油时经常会出现在炼油厂生产原油的过程中,并且存在硫、酸等各种元素。
在化学上与炼油厂互动。
如果炼油厂使用时间长,这些元素会与设备一起使用,导致炼油厂的腐蚀时间越长,这些炼油厂的腐蚀就越大,对石油工业的生产和发展有很大影响,在严重情况下会损害相应的石油工业生产厂家。
炼油厂腐蚀的原因和类型可以是任何时候的化学反应,就像炼油厂的过程一样,炼油厂的化学反应会产生二氧化硫,如二氧化碳,这些化学反应会在这些化学物质及其溶液和设备材料之间产生化学反应,从而导致炼油厂腐蚀的原因和类型概述。
2石油炼制设备腐蚀原因2.1化学腐蚀化学腐蚀简单来讲,其指的是石油炼制设备与非电解质相接触,产生化学反应进而发生腐蚀的一种现象。
第四常减压蒸馏装置加工劣质原油常顶的腐蚀与防护

设备与防腐齐鲁石油化工,2018,46 ( 1) :32 -36QILU PETROCHEMICAL TECHNOLOGY第四常减压蒸馏装置加工劣质原油常顶的腐蚀与防护张继辉1,杨析宗2(1.驻中国石化齐鲁分公司军事代表室,山东淄博255434,2.中国石化齐鲁分公司胜利炼油厂,山东淄博255434)摘要:齐鲁炼油厂因加工的髙硫髙酸原油劣质化,造成第四常减压蒸馏装置常顶循、常一线系统腐蚀严重,制约安 全生产。
常顶存在较为严重的结盐腐蚀,针对性的采取洗塔,改善电脱盐的操作,提出大检修装置技术改造及材质升级,最大限度的减轻了腐蚀,确保装置安全平稳运行。
关键词:常顶腐蚀电脱盐优化操作材质升级技术改造中图分类号:TE986 文献标识码:B文章编号:1009 -9859(2018)01 -0032 -051概述中国石化齐鲁分公司胜利炼油厂(简称齐鲁 炼油厂)第四常减压蒸馏装置于2010年3月底投 入生产运行,加工能力8.0M t/a。
装置设计加工 的原油为高硫高酸原油和胜利原油的混合原油,其中高硫高酸原油6.7 M/a,胜利原油1.3 M/a。
混合原油酸值(K0H)为1.685 m#g,硫含量(质 量分数)为1.97%,属高硫高酸一中间基原油。
因后续二次加工装置配套能力不足及胜利高 硫高酸原油配置不足,装置开工后的原料改为胜 利高硫高酸原油掺炼齐鲁炼油厂第二套第四常减 压蒸馏装置拔头后的沙重、伊重、索鲁士、扎库姆、奥瑞特、埃斯科兰特、玛雅等原油,掺炼比例(质 量分数)在30%左右,且装置一直在65% ~ 85% 的负荷运行。
2011年全年加工量6.53 M/其中 胜利高硫高酸原油4.81 M/第二常减压蒸馏装置 拔头油1.72 M/由于原油性质的复杂化及电脱 盐运行效果不好,导致脱后原油含盐、含水持续偏 高,即含盐平均值6.1m#L,含水(质量分数)平 均值0.51 %,均超过设计值,故电脱盐后续设备 腐蚀严重。
高酸原油加工的腐蚀与防护

高酸原油加工的腐蚀与防护引言随着原油资源的日益紧缺,高酸原油的加工及利用已成为当前炼油行业的一项重要工作。
然而,高酸原油会对加工设备产生腐蚀,从而对生产带来不利影响。
本文将探讨高酸原油加工过程中的腐蚀问题及其防护方法。
高酸原油的定义高酸原油是指含有较高酸值的原油。
一般来说,酸值越高,腐蚀性就越大。
在高酸原油中,主要的酸类成分是硫酸、硝酸、有机酸等。
此外,含有杂质和硫化物的原油也具有较高的腐蚀性。
高酸原油加工中的腐蚀问题由于高酸原油具有较强的酸性,其在加工中会对设备和管线产生严重的腐蚀问题,导致设备寿命缩短、性能下降、安全隐患增加等问题。
腐蚀类型高酸原油加工中常见的腐蚀类型如下:•粘附腐蚀:高酸原油中的酸类成分会粘附到金属表面上,形成一层薄膜,这层薄膜中的有机物和金属中的氧发生反应,从而引发腐蚀。
•晶间腐蚀:高酸原油中的酸性物质会促进晶间腐蚀的发生,从而使设备和管道产生脆化和断裂。
•点蚀腐蚀:高酸原油中的杂质和硫化物等物质会形成点蚀,从而导致设备表面出现小孔和凸起。
腐蚀影响高酸原油加工过程中的腐蚀问题会对设备和管线的使用寿命和性能造成不良的影响,具体表现如下:•设备寿命缩短:高酸原油加工对设备产生的腐蚀作用会导致设备寿命缩短,从而增加了生产成本。
•性能下降:高酸原油加工对设备的腐蚀作用会导致设备的性能下降,生产效率降低。
•安全隐患:高酸原油加工过程中,管道和设备的腐蚀会导致破裂和泄漏,可能会产生严重的安全隐患。
防腐保护技术在高酸原油加工中,防腐保护技术的应用非常重要。
以下是一些有效的防腐保护技术。
1. 涂层技术针对高酸原油的腐蚀问题,涂层技术是一种重要的防护方法。
所选涂层应具有耐酸蚀、耐磨损、耐高温等特点,并需经过专业检测。
将这些涂层应用于设备和管道表面,则能有效地防止高酸原油产生腐蚀作用。
2. 材料选择正确认识原油的酸性,根据酸值和组成选择适合的材料,如含锆或钛的合金结构,操作期间需要引起关注。
浅谈含硫原油的腐蚀及保护措施
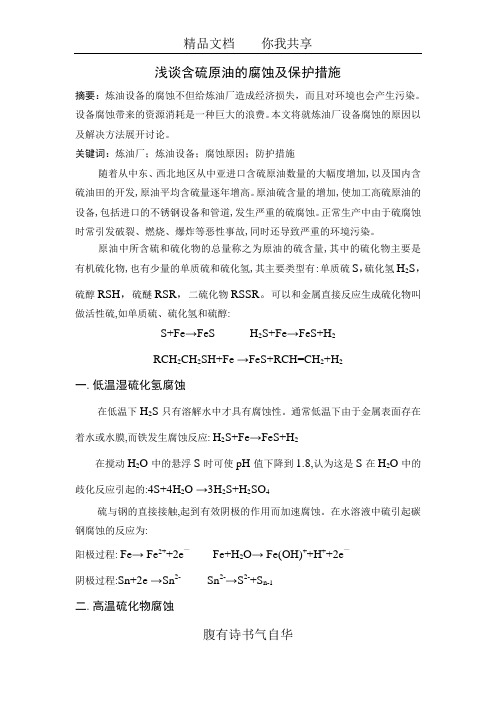
浅谈含硫原油的腐蚀及保护措施摘要:炼油设备的腐蚀不但给炼油厂造成经济损失,而且对环境也会产生污染。
设备腐蚀带来的资源消耗是一种巨大的浪费。
本文将就炼油厂设备腐蚀的原因以及解决方法展开讨论。
关键词:炼油厂;炼油设备;腐蚀原因;防护措施随着从中东、西北地区从中亚进口含硫原油数量的大幅度增加,以及国内含硫油田的开发,原油平均含硫量逐年增高。
原油硫含量的增加,使加工高硫原油的设备,包括进口的不锈钢设备和管道,发生严重的硫腐蚀。
正常生产中由于硫腐蚀时常引发破裂、燃烧、爆炸等恶性事故,同时还导致严重的环境污染。
原油中所含硫和硫化物的总量称之为原油的硫含量,其中的硫化物主要是有机硫化物,也有少量的单质硫和硫化氢,其主要类型有:单质硫S,硫化氢H2S,硫醇RSH,硫醚RSR,二硫化物RSSR。
可以和金属直接反应生成硫化物叫做活性硫,如单质硫、硫化氢和硫醇:S+Fe→FeS H2S+Fe→FeS+H2RCH2CH2SH+Fe →FeS+RCH=CH2+H2一.低温湿硫化氢腐蚀在低温下H2S只有溶解水中才具有腐蚀性。
通常低温下由于金属表面存在着水或水膜,而铁发生腐蚀反应: H2S+Fe→FeS+H2在搅动H2O中的悬浮S时可使pH值下降到1.8,认为这是S在H2O中的歧化反应引起的:4S+4H2O →3H2S+H2SO4硫与钢的直接接触,起到有效阴极的作用而加速腐蚀。
在水溶液中硫引起碳钢腐蚀的反应为:阳极过程: Fe→ Fe2++2e—Fe+H2O→ Fe(OH)++H++2e—阴极过程:Sn+2e →Sn2- Sn2-→S2-+S n-1二.高温硫化物腐蚀腹有诗书气自华高温下硫和硫化氢能直接与金属发生反应,生成金属的硫化物,其主要腐蚀反应过程为:S+Fe→FeS H2S+Fe→FeS+H2高温下H2S可发生分解,产生的元素硫具有很高的活性,与Fe发生反应极为强烈:H2S →H2+S S+Fe→ FeS原油中含的部分硫醇,在200℃以上也可以与铁直接发生反应产生硫化铁腐蚀产物:RCH2CH2SH+Fe→RCH2CH3+FeS+H2连多硫酸的形成及其腐蚀过程,如在催化裂化装置烟气管道中,高温部位(400~600℃)又有SO2和CO存在时:SO2+2CO →2CO2+S S+Fe→ FeS2SO2+O2→2SO3 SO3+H2O →H2SO4FeS+H2SO4→FeSO4+H2S H2S+H2SO4→4H2SxO6+S反应过程使在运行中形成的FeS膜破坏,腐蚀反应过程中形成的S和H2S又可参与金属的腐蚀过程,所以对材料的腐蚀具有自催化作用,过程中形成的亚硫酸,应力腐蚀开裂有诱发作用。
加工劣质原油装置大修腐蚀检查与分析

加工劣质原油装置大修腐蚀检查与分析1. 引言在石油加工行业中,原油是最基本的原料之一。
在一些情况下,我们可能需要处理劣质原油,这种原油常常含有高硫、高酸、高沥青质等成分,其腐蚀性较强。
为了确保加工劣质原油装置的安全运行和延长设备使用寿命,定期进行大修是必要的。
本文将重点介绍加工劣质原油装置大修过程中的腐蚀检查与分析。
2. 检查方法在进行加工劣质原油装置大修腐蚀检查时,可以采用以下几种方法:2.1 目视检查通过目视检查,可以观察设备表面是否出现腐蚀、锈蚀、凹陷等现象。
特别注意检查管道连接处、焊缝区域和设备接触介质的部位。
2.2 厚度测量通过使用超声波测厚仪或磁性质测厚仪等设备,可以测量设备壁厚,了解设备的腐蚀程度。
测量时需要选择代表性的测点,覆盖各个区域,同时考虑不同材质的厚度要求。
2.3 化学分析通过对设备内介质进行采样,并进行化学成分分析,可以判断介质中是否存在对设备腐蚀性较高的成分。
常见的化学分析方法包括红外光谱法、质谱法、电感耦合等离子体发射光谱法等。
3. 分析结果通过对加工劣质原油装置的腐蚀检查,可以得到以下几方面的分析结果:3.1 腐蚀程度根据厚度测量结果,可以评估设备的腐蚀程度。
腐蚀程度的评估可以参考国际标准或公司内部的经验指导,划分为轻微、中等和严重等级。
3.2 腐蚀类型根据目视检查的结果,可以确定设备上出现的腐蚀类型。
常见的腐蚀类型包括均匀腐蚀、点蚀腐蚀、晶界腐蚀等。
不同的腐蚀类型可能需要采用不同的修复方法。
3.3 腐蚀原因通过化学分析结果,可以确定设备腐蚀的原因。
可能的腐蚀原因包括介质的腐蚀性、温度、压力、含硫化氢等因素。
确定腐蚀原因有助于采取相应的措施,避免腐蚀问题再次发生。
4. 修复措施根据腐蚀检查与分析结果,我们可以制定相应的修复措施。
修复措施可能包括以下几个方面:4.1 表面修复对轻微的腐蚀问题,可以进行表面修复,如研磨、打磨、刷涂防腐漆等。
这些方法可以有效地防止进一步腐蚀,并延长设备的使用寿命。
关于石油炼制设备腐蚀的防治措施

关于石油炼制设备腐蚀的防治措施随着我国炼油加工量的不断增加,使得炼油装置设备的腐蚀程度越来越大,而且在不同的装置上,所腐蚀的形态也是各不相同,设备的腐蚀对于石油炼制企业来说,其危害性是非常大的,设备的腐蚀会影响到环境,直接地影响到人们的身体,严重的情况下还会引起火灾,甚至人身伤亡等重大的安全事故,造成巨大的经济损失。
本文主要分析石油设备腐蚀类型以及具体的防治措施。
标签:石油炼制;设备腐蚀;防治措施一、腐蚀类型(一)缝隙腐蚀缝隙腐蚀的位置基本上处于管板与管束之间的微小缝隙上,随着腐蚀程度不断加深,缝隙将会随之增大,最终对设备造成严重影响。
石油炼制设备的缝隙本身很难发生腐蚀,但在炼制石油的过程中,缝隙的存在为活性阴离子提供了便利的条件,当缝隙外部的活性阴离子(如氯离子)进人到缝隙内部之后,会与缝隙内部的阳性离子发生反应,从而发生腐蚀现象。
缝隙腐蚀具有极强的穿透力,很容易将腐蚀范围扩大,从而影响设备的运行。
(二)冲刷腐蚀石油炼制的过程中,会因为原油或原油产物的流动,对设备造成冲刷腐蚀。
冲刷腐蚀,顾名思义,就是对设备上的金属离子一遍又一遍的冲刷,从而使炼制设备的厚度越来越薄,最终出现渗漏。
(三)氢腐蚀在炼制石油的过程中,会产生极高的温度,氢分子在受到高温的影响后,会使炼制设备发生氢腐蚀。
正常状态下,设备是不会发生腐蚀现象的,但是在温度较高的环境中,高温会分解氢分子,从而变成离子吸附在炼制设备上,有的氢离子会进入到金属的内部,从而与设备发生化学反应,形成甲烷。
甲烷拥有极强凝聚力很难扩散,当金属中的甲烷积累到一定程度之后会使金属产生裂纹,从而导致石油炼制设备发生腐蚀。
(四)露点腐蚀石油炼制的过程非常复杂,需要经过层层炼制工序,才能够形成最终的石油。
在炼制工序中有一道蒸发脱水环节,这个环节会产生强酸,从而腐蚀炼制设备。
蒸发脱水会将NH4CL溶解在水中形成HCL,在高温的作用下HCL会发生化学变化形成强酸,而强酸对炼制设备具有很大的腐蚀作用,从而使得炼制设备腐蚀现象不断严重。
石油炼制设备腐蚀与防护措施

石油炼制设备腐蚀与防护措施摘要:随着当前我国经济建设的进步和各部件的快速发展,对各种热能的需求量越来越大,尤其是对汽油热能的需求量越来越大。
在炼油过程中,炼油装置的防腐质量直接关系到炼油的成败。
石油的性质产生了变化,其化学成分最终缓慢地从环烷酸化学成分转变为硫化物化学成分。
在此背景下将炼油厂作为搜索对象进行分析,本文首先对炼油装置的投入进行了分析。
关键词:石油、防护措施、腐蚀引言:装置腐蚀一直是炼油厂安全生产和长期运行的重要标志。
近年来,随着我国加工高硫精炼和高酸慢油的前景,该装置的损坏越来越严重。
在确认不同的作用后,腐蚀的形式和部位变得越来越复杂和多样化。
该装置的碰撞将导致设计强、自动化程度高、装置结构复杂、高温、高压、火焰、放大、碰撞和易值的炼油识别出现严重异常:该装置的碰撞程度将环绕环境,增加人类健康,增加损失,它导致无计划停工,甚至采取积极措施加强对腐蚀的控制和保护,确保安全生产和安全企业的长期运行,这是炼油厂必须始终做好的重要工作。
1.石油炼制企业典型的腐蚀环境1.电化学腐蚀环境电化学传感器腐蚀也是金属腐蚀中最普遍的表现形式之一。
其实质主要为金属原料和酸性电解质溶液碰撞,形成腐蚀的原电池,更多的活性金属失去电子并氧化。
在炼油企业,电化学的消解环境主要包括真空减压蒸馏设备顶部及其冷却系统,另外还有工作温度小于一百二十℃的腐蚀介质H2S+H20。
催化裂化装置可以在全系统高温下,通过吸附和稳定生成新的腐蚀环境HCN+H2S+H20(40;50{88451;)和高水条件下,氢过滤器系统和燃气燃烧设备中热交换器装置和空调设备的反应馏分的腐蚀环境,以及二级处理设备中的大量轻质油,如含有干空气的烃硫环境,催化裂化装置的热吸收和稳定部分,以及产品在精炼厂部分完全液化石油气系统的干法脱硫、酸提取装置中的汽提系统、碳氢化合物装置和碳氢化合物脱硫装置中的冷却、高压系统和下游装置的热分离;干空气、LPG自下而上系统和富rnH二的液体系统中(乙醇胺)+C02+H2S+H2O环境腐蚀(温度高于90 845NO)0.2MPA压力:连续多硫酸腐蚀环境,配备用于无水石山炼油系统施工的敏感设备。
加工进口劣质原油常减压腐蚀原因分析及防护措施

・
东
化工 ຫໍສະໝຸດ 4 ・ 2 S A D N H MIA D S R H N O G C E C LI U T Y N
21 0 0年第 3 9卷
加工进 口劣质原油常减压腐蚀原因分析及 防护措施
韩 红 亮
( 坊弘 润石 化助 剂有 限公 司 , 潍 山东 潍 坊 2 16 ) 6 0 1
Co .。L d.1 2Mt n 5Mt itl t n un t n lz d t e c ro i n me h n s o t s h rc a d t . /a a d 2. /a d si a i i.a ay e h o so c a im famo p e i n l o v c u d si ai n o r n p o o e me s r s o e u e he o r so o t s e i a d v c u a u m it l t t we a d r p s d l o a u e t r d c t c ro in f amo ph rc n a u m d si ain twe o e t n h rv y l . itl to o r t xe d t e d e c ce l i
( i n o gu e o hmi l d ivsC . Ld , i n 2 1 6 。C ia We a gH nrnP t c e c dt e o , t. We a g 6 0 1 hn ) f r aA i f
Ab t a t C u e o l it l t n tw rc ro in i e n r n f h mp r n e s n fa cd ns a d s r c : r d i d si a i e o r so n r f e y i o e o e i o t tra o so c i e t n l o o i S t a u p a n d d w t .C mb n d w t h o r s n s u t n o ef n n r n P t c e c l d t e n ln e o n i me o i e i te c ro i i a i f h o t o W i g Ho g u er h mia a o Ad i v s i
炼油设备腐蚀与防护
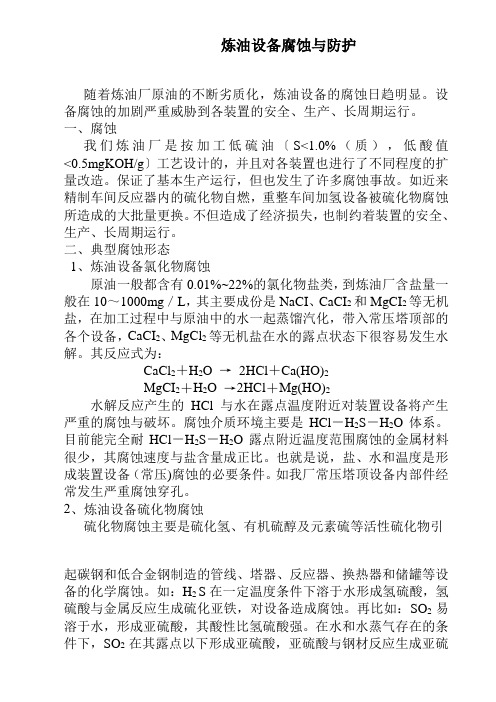
炼油设备腐蚀与防护随着炼油厂原油的不断劣质化,炼油设备的腐蚀日趋明显。
设备腐蚀的加剧严重威胁到各装置的安全、生产、长周期运行。
一、腐蚀我们炼油厂是按加工低硫油〔S<1.0%(质),低酸值<0.5mgKOH/g〕工艺设计的,并且对各装置也进行了不同程度的扩量改造。
保证了基本生产运行,但也发生了许多腐蚀事故。
如近来精制车间反应器内的硫化物自燃,重整车间加氢设备被硫化物腐蚀所造成的大批量更换。
不但造成了经济损失,也制约着装置的安全、生产、长周期运行。
二、典型腐蚀形态1、炼油设备氯化物腐蚀原油一般都含有0.01%~22%的氯化物盐类,到炼油厂含盐量一般在10~1000mg/L,其主要成份是NaCI、CaCI2和MgCI2等无机盐,在加工过程中与原油中的水一起蒸馏汽化,带入常压塔顶部的各个设备,CaCI2、MgCl2等无机盐在水的露点状态下很容易发生水解。
其反应式为:CaCl2+H2O →2HCl+Ca(HO)2MgCI2+H2O →2HCl+Mg(HO)2水解反应产生的HCl与水在露点温度附近对装置设备将产生严重的腐蚀与破坏。
腐蚀介质环境主要是HCl-H2S-H2O体系。
目前能完全耐HCl-H2S-H2O露点附近温度范围腐蚀的金属材料很少,其腐蚀速度与盐含量成正比。
也就是说,盐、水和温度是形成装置设备(常压)腐蚀的必要条件。
如我厂常压塔顶设备内部件经常发生严重腐蚀穿孔。
2、炼油设备硫化物腐蚀硫化物腐蚀主要是硫化氢、有机硫醇及元素硫等活性硫化物引起碳钢和低合金钢制造的管线、塔器、反应器、换热器和储罐等设备的化学腐蚀。
如:H2 S在一定温度条件下溶于水形成氢硫酸,氢硫酸与金属反应生成硫化亚铁,对设备造成腐蚀。
再比如:SO2易溶于水,形成亚硫酸,其酸性比氢硫酸强。
在水和水蒸气存在的条件下,SO2在其露点以下形成亚硫酸,亚硫酸与钢材反应生成亚硫酸铁(FeSO3),从而使设备严重腐蚀。
3、石油酸腐蚀石油酸是原油中各种酸性化合物的总称。
精选炼油设备的腐蚀与防护教材

中加入的溶剂及酸碱化学剂会形成腐蚀介质,也加
速设备的腐蚀。
第二节 原油中的腐蚀介质
❖ 一、硫化物的腐蚀 ❖ 原油中的硫化物主要包括:硫化氢,硫和硫醇;硫
醚,多硫醚,噻吩,二硫化物等。 ❖ 通常将含硫量在0.1%-0.5%的原油叫做低硫原油;含
硫量大于0.5%者为高硫原油。 ❖ 硫化物含量越高对设备腐蚀就越强。
六、我国原油的分类
❖ 据原油中含硫及酸值的高低,可将我国原油分为: ❖ (1)低硫低酸值原油 ❖ 原油含硫0.1%~0.5%,酸值≤0.5mgKOH/g,如大庆原油。 ❖ (2)低硫高酸值原油 ❖ 原油含硫0.1%~0.5%,酸值>0.5mgKOH/g,如辽河原油,
新疆原油。 ❖ (3)高硫低酸值原油 ❖ 原油含硫>0.5%,酸值≤0.5mgKOH/g,如胜利原油。 ❖ (4)高硫高酸值原油 ❖ 原油含硫>0.5%,酸值>0.5mgKOH/g,如孤岛原油和“管
❖ (4)340℃﹤t ≤400℃,H2S开始分解为H2和S,此 时对设备的腐蚀反应式为:
❖ H2S → H2 + S Fe + S → FeS ❖ R-S-H(硫醇) + Fe → FeS + 不饱和烃 ❖ (5)420℃﹤t ≤430℃,高温硫对设备腐蚀最快; ❖ (6)t﹥480℃,硫化物近于完全分解,腐蚀率下降。 ❖ (7)t﹥500℃,不是硫化物腐蚀范围,此时为高温
第一节 概述
❖
在石油炼制过程中存在着一系列腐蚀问题。
它直接影响着生产装置的长周期,安全、稳定,满
负荷及优质的运转;并降低工厂开工率,提高工厂
维护费用;消耗大量化学药剂。因而增加工厂成本,
降低工厂的整体效益。近年来由于我国原油变重,
关于石油炼制设备腐蚀的防治措施

关于石油炼制设备腐蚀的防治措施发布时间:2021-11-22T01:28:03.769Z 来源:《工程管理前沿》2021年6月第18期作者:邢连栋[导读] 近年来,随着社会的发展,各行各业不断发展,石油已经成为我国工业发展中的主要能源,更是促进经济稳定发展的基础。
邢连栋中石化股份有限公司天津分公司天津 300270摘要:近年来,随着社会的发展,各行各业不断发展,石油已经成为我国工业发展中的主要能源,更是促进经济稳定发展的基础。
石油提炼过程是比较复杂的,其中的各种化工产品会腐蚀相关的设备。
因此,在新时期,需要对石油炼制设备腐蚀控制措施进行分析,然后结合其中的材料性能和防腐内容,完善控制和防护方案。
关键词:石油炼制;设备;腐蚀;防治措施引言石油炼制企业出现设备腐蚀问题的几率是比较高的,需要引起高度重视并加大解决对策。
若是设备出现腐蚀,会影响其使用年限和功能,甚至会造成人身伤亡,不利于企业发展。
因此,石油炼制企业要根据腐蚀产生的原因,采取有效的应对措施,并且还需要分析总结经验,采用先进的防腐技术,才能保证生产的安全运行,从而实现石油炼制企业的长远发展。
1石油炼制设备腐蚀的原因 1.1炼油装置腐蚀为了促进石油炼化企业在社会中的持续发展,对国内原油现状进行了分析,在原油加工中出现了比较明显的问题,这会导致原油腐蚀程度不断增加。
同时,国内的各大炼化企业原油一般包括大庆原油、吐哈原油和青海原油等产出的原油,但是相关企业并没有对各地区油品进行合理化应用,并且受到原油差异化腐蚀作用的影响,装置设备的实际腐蚀情况比较严重,如果不对其进行有效处理,就会加剧腐蚀程度。
1.2设备自身的原因一般来说,石油炼制设备材料会造成腐蚀问题的产生,尤其是金属设备更容易出现腐蚀。
石油炼制设备材料主要是金属材质的,同时不同金属材质产生腐蚀的情况也不一样。
然而在实际生产中,我国大部分石油炼制企业为追求经济效益,往往采购便宜的材料,这些材料晶粒直径较大,没有抗腐蚀性。
炼油设备的腐蚀与防护
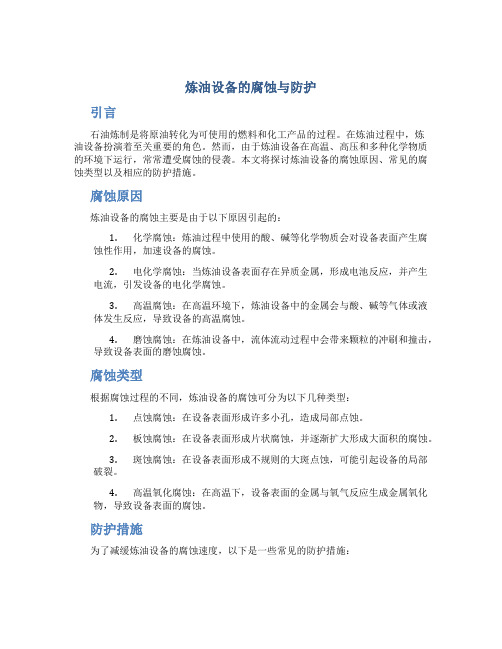
炼油设备的腐蚀与防护引言石油炼制是将原油转化为可使用的燃料和化工产品的过程。
在炼油过程中,炼油设备扮演着至关重要的角色。
然而,由于炼油设备在高温、高压和多种化学物质的环境下运行,常常遭受腐蚀的侵袭。
本文将探讨炼油设备的腐蚀原因、常见的腐蚀类型以及相应的防护措施。
腐蚀原因炼油设备的腐蚀主要是由于以下原因引起的:1.化学腐蚀:炼油过程中使用的酸、碱等化学物质会对设备表面产生腐蚀性作用,加速设备的腐蚀。
2.电化学腐蚀:当炼油设备表面存在异质金属,形成电池反应,并产生电流,引发设备的电化学腐蚀。
3.高温腐蚀:在高温环境下,炼油设备中的金属会与酸、碱等气体或液体发生反应,导致设备的高温腐蚀。
4.磨蚀腐蚀:在炼油设备中,流体流动过程中会带来颗粒的冲刷和撞击,导致设备表面的磨蚀腐蚀。
腐蚀类型根据腐蚀过程的不同,炼油设备的腐蚀可分为以下几种类型:1.点蚀腐蚀:在设备表面形成许多小孔,造成局部点蚀。
2.板蚀腐蚀:在设备表面形成片状腐蚀,并逐渐扩大形成大面积的腐蚀。
3.斑蚀腐蚀:在设备表面形成不规则的大斑点蚀,可能引起设备的局部破裂。
4.高温氧化腐蚀:在高温下,设备表面的金属与氧气反应生成金属氧化物,导致设备表面的腐蚀。
防护措施为了减缓炼油设备的腐蚀速度,以下是一些常见的防护措施:1.材料选择:选择适用于炼油条件的高耐蚀性材料,如不锈钢、镍合金等。
在选材时要考虑设备的工作环境和所需的物理性能。
2.防蚀涂层:在设备表面涂覆防蚀涂层,如耐蚀漆、耐酸碱涂层等,以提供额外的保护层。
3.阳极保护:对于容易发生电化学腐蚀的设备,可以采用阳极保护技术,通过外加电流形成保护电场,减少设备的电化学腐蚀。
4.清洗与维护:定期对设备进行清洗和维护,及时清除设备表面的杂质和腐蚀产物,以延缓腐蚀的发生。
5.腐蚀监测:使用腐蚀监测技术对设备进行实时监测,及时发现腐蚀情况,采取相应的防护措施。
结论炼油设备的腐蚀是炼油过程中不可避免的问题,但通过合理的防护措施,可以减缓腐蚀速度,延长设备的使用寿命,提高炼油效率。
浅谈高硫原油加工设备的硫腐蚀与防护

浅谈高硫原油加工设备的硫腐蚀与防护摘要:随着经济的发展,国内高硫原油的加工比例不断增大,硫化物在原油加工过程中对设备的腐蚀是工业上的一大难题。
随着炼制进口中东高硫原油数量的增加,炼制高硫原油中出现的问题也越来越突出,基于此本文介绍了炼油装置在炼制高硫原油后设备腐蚀的主要类型、腐蚀部位及腐蚀机理,并在此基础上提出了相应的防护措施。
关键词:高硫原油;设备腐蚀;防护措施前言随着石油的开采深度逐渐加大,含硫和高硫原油逐年增加,已占原油总量的50%以上,尤其是中东地区的原油,大部分为高硫原油。
虽然在价格上高硫原油相比于低硫原油有着明显的优势,但高硫原油在加工过程中对设备造成的腐蚀却是个棘手的难题。
因此,深入了解加工高硫原油设备的腐蚀与防护技术对于石油加工企业有着非常重要的意义。
1、硫化物形态的腐蚀类型根据原油中各形态含硫化合物的性质不同可划分为活性硫、中性硫和非活性硫。
其中活性硫主要包括单质硫、硫化氢、二氧化硫和硫醇等;中性硫主要包括硫醚、二硫醚和二甲基硫醚等;非活性硫主要包括噻吩及其同系物等。
含硫化合物对设备的腐蚀是造成高硫原油加工设备腐蚀的主要原因,而其中的活性硫化物对碳钢和低合金钢材质的加工设备的腐蚀最为活跃。
硫腐蚀机理的不同而十分复杂,大部分情况下,腐蚀程硫化物对加工设备的腐蚀过程因活性硫与非活性度随着温度的上升而加深,因此,一般以240℃界定低温硫腐蚀和高温硫腐蚀,并以此判别硫化物腐蚀类型。
1.1、低温硫腐蚀1.1.1低温轻油腐蚀低温轻油腐蚀常见于温度低于200℃的常减压装置塔顶冷凝冷却系统,对碳钢设备可以形成均匀腐蚀、点蚀及湿硫化氢应力腐蚀开裂,其中H2S-HCI-H2O型和H2S-H2O型是2大主要的硫腐蚀类型。
有机氯及少量未脱除的无机盐随油品温度升高在塔内分解,产生大量的HCI气体,同时油品的活性硫成分在塔内生成H2S,干燥环境下的HCI和H2S对金属无腐蚀作用,当塔顶冷凝器将水蒸气冷凝成小水滴时,便为形成一个强烈的酸腐蚀环境提供了条件,因此高硫原油馏分中存在的H2S、HCl和H2O相互促进会加速对设备的腐蚀。
- 1、下载文档前请自行甄别文档内容的完整性,平台不提供额外的编辑、内容补充、找答案等附加服务。
- 2、"仅部分预览"的文档,不可在线预览部分如存在完整性等问题,可反馈申请退款(可完整预览的文档不适用该条件!)。
- 3、如文档侵犯您的权益,请联系客服反馈,我们会尽快为您处理(人工客服工作时间:9:00-18:30)。
加工劣质原油设备腐蚀与防护技术齐鲁石化公司胜利炼油技术研究所近年来,国内炼油行业进展专门快,以山东省为例,不包括国有大中型炼油厂,仅地点炼油企业,年总加工能力差不多超过两千万吨。
炼油企业加工能力的增加,必定会带来原油资源和炼油技术的竞争,优化资源、降本增效成为企业生存进展的要紧手段。
国有炼油厂国家原油配置指标较为充足,炼制的原油品种较为单一。
而地点炼油企业由于缺乏国家原油配置指标,原油来源比较复杂,有时不得不炼制部分劣质原油(包括高硫、高酸、高含盐、高含水等原油)。
同时由于价格优势,加工劣质原油也成为国内炼油企业战略进展的重要方向之一。
加工劣质原油不仅会造成生产工艺的波动,还会造成设备的腐蚀,给安全生产带来隐患,严峻时甚至会导致装置停工和人身伤亡事故。
如二十世纪七十年代,国内某炼油厂焦化装置因设备腐蚀导致爆炸着火,并造成人员伤亡事故,经济缺失庞大。
2001年某炼油厂加氢装置空冷器腐蚀泄漏,造成装置部分停工抢修,经济缺失达数百万元。
因此,炼油企业必须充分重视劣质原油加工过程中的设备腐蚀问题,加强腐蚀监控和腐蚀防护,保证生产装置的长稳安运行,为企业制造更多的经济效益。
11加工劣质原油的设备腐蚀问题加工劣质原油面临的腐蚀问题要紧是由于原油中的盐、硫、酸及水含量高所引起的,这些原油组分在加工过程中通过分解、转化及相互作用,形成各种腐蚀环境,对设备造成腐蚀。
1.1 盐含量高带来的腐蚀问题在原油加工过程中,原油中无机盐水解会对设备造成严峻的腐蚀。
原油中的无机盐(要紧是氯化钠、氯化镁、氯化钙)在一定温度下水解生成盐酸,在常减压蒸馏装置塔顶循环冷凝冷却系统及温度低于露点温度的部位冷凝下来,形成低温HCl+H2S+H2O腐蚀环境。
该环境一样在气相部位腐蚀比较轻微,而液相部位腐蚀较重,气液相变的部位即露点部位腐蚀最为严峻。
在这种腐蚀环境中,HCl腐蚀为主,H2S起促进作用,它和HCl相互促进,形成腐蚀循环,造成设备失效。
此外,盐含量高还会造成装置设备的结垢以及催化剂中毒等问题。
1.2 硫含量高带来的腐蚀问题原油中硫要紧以元素硫、硫化氢、硫醇、硫醚、二硫化物、噻吩等形式存在,由于在原油加工过程中,非活性硫不断向活性硫转变,导致硫的腐蚀贯穿在整个炼油过程中。
通常在炼油厂,硫的腐蚀环境要紧有以下几种:a)HCl+H2S+H2O腐蚀环境,要紧发生在分馏塔顶冷凝冷却系统;b)H2S+HCN+H2O腐蚀环境,要紧发生在催化裂化装置稳固吸取系统;c)RNH2(乙醇胺)+H2S+CO2+H2O腐蚀环境,要紧发生在干气及液化气脱硫的再生塔底部系统及富液管线系统(温度高于90℃,压力约0.2MPa);d)S+H2S+RSH高温硫腐蚀环境(温度在240℃以上),要紧发生在蒸馏装置常减压塔下部及塔底管线、常压重油和减压渣油换热器、催化裂化分馏塔下部、延迟焦化分馏塔下部等部位;e )H2+H2S腐蚀环境,要紧发生在加氢裂化和加氢精制等临氢装置温度超过240℃的部位,如加氢裂化装置反应器、加氢脱硫装置反应器及催化重整装置石脑油加氢精制反应器;f)连多硫酸(H2SxO6)应力腐蚀开裂,要紧发生在装置停工期间的不锈钢或高合金材料制造的设备上,例如高温高压含氢环境下的反应器器壁及其衬里和内构件、储罐、换热器、管线等,专门是加氢脱硫、加氢裂化、催化重整等系统的奥氏体钢设备管线;g)高温烟气硫酸露点腐蚀,多发生在炼油厂加热炉空气预热器和烟道以及废热锅炉的省煤器和管道上。
是由于加热炉燃烧含硫瓦斯气或燃料油生成的SO2和SO3所引起的。
1.3 酸含量高带来的腐蚀问题原油中的酸包括环烷酸、芳香酸、脂肪酸等,通常以酸值或酸度来表示。
一样来说,原油中的酸腐蚀是指由环烷酸引起的高温腐蚀。
环烷酸是原油中有机酸的总称,是原油中要紧的酸性氧化物,其腐蚀要紧为化学腐蚀。
由于腐蚀生成的环烷酸铁能够溶解在油中,金属表面相对光洁,使腐蚀不断进行。
环烷酸腐蚀要紧发生在炼油装置高温部位。
常减压装置要紧部位有常压转油线、减压转油线、常压炉出口、减压炉出口、常减压塔进料段塔壁、减三线等;催化和焦化装置要紧部位有高温重油管线、加热炉管、分馏塔及相应的换热器等。
2 设备腐蚀给生产造成的危害设备腐蚀的过程是一个潜移默化的过程,而且设备腐蚀所造成的危害往往是间接表达出来的,因此腐蚀的危害往往容易被人们所忽视。
关于炼油厂来说,腐蚀的危害性要紧表达在以下几个方面:a)炼油装置关联性专门强,某台设备的腐蚀问题会造成装置部分停工或降量生产,严峻时会导致整个生产装置的停产,使生产周期缩短,企业经济效益降低;b)设备腐蚀会造成爆炸着火和产品泄漏,导致人员伤亡和环境污染事故的发生;c)设备腐蚀生成的腐蚀产物会造成催化剂中毒等事故,阻碍产品深度加工;d)部分腐蚀产物进入产品,使产品带有杂质、异味或变色,造成产品质量不合格;e)腐蚀产物沉积在换热设备表面形成垢层,降低了热效率,增加能源消耗;f)腐蚀导致设备使用寿命降低,检修理费用和检修时刻增加,增加了装置的运行成本。
3 胜利炼油厂加工劣质原油设备腐蚀防护技术胜利炼油厂是国内高硫高酸原油要紧加工基地之一,自1967年建厂以来,先后加工过胜利原油、陆上混合原油、高硫高酸原油及多种含硫量高的外油品种。
这些原油的盐、硫、酸含量都比较高,给设备带来了严峻的腐蚀问题。
为了解决那个问题,炼油厂于建厂初期成立了设备防腐研究室,开展设备腐蚀与防护技术研究。
1990年设备防腐室和工艺研究室合并成立胜利炼油厂研究所,即现在的齐鲁石化胜利炼油技术研究所(以下简称研究所)。
通过多年的研究探究和现场应用,开发了腐蚀监检测成套技术、腐蚀失效分析、GL渗铝钢、防腐药剂(缓蚀剂、中和剂、破乳剂等)、防腐涂料等技术产品,在全国炼油系统领先应用“一脱四注”工艺防腐技术,专门是在劣质原油加工设备防腐方面,从腐蚀监检测、工艺防腐、材料防腐、防腐治理等方面入手,解决了大量制约炼油厂生产的设备腐蚀难题。
3.1 设备的腐蚀监检测技术腐蚀监检测是炼油厂防腐的重点工作,胜利炼油厂目前采纳的腐蚀监检测方法要紧有腐蚀挂片、电阻探针腐蚀在线监测系统、pH在线监测系统、定点测厚、腐蚀介质分析等。
a)腐蚀挂片腐蚀挂片是腐蚀监测最差不多的方法之一。
目前胜利炼油厂采纳的腐蚀挂片技术要紧有两种方式。
一是采纳现场腐蚀挂片监测技术,在装置停工检修期间将腐蚀试片挂入装置设备内,监测装置整个运行周期的腐蚀情形。
该方法监测周期通常为2到4年。
第二种方法是采纳挂片探针技术,在装置运行过程中,对重点腐蚀部位进行监测,监测周期通常为一到二个月。
随着装置开工周期的延长,挂片探针技术在炼油厂的应用更加广泛。
b)电阻探针腐蚀在线监测系统电阻探针腐蚀监测通过测量金属元件在工艺介质中腐蚀时的电阻值的变化,运算金属在工艺介质中的腐蚀速度。
研究所94年在国内首家开发了电阻探针腐蚀监测仪,该仪器能够实现在线多点监测。
随着装置生产自动化程度的提高,2001年研究所在原先的电阻探针监测技术的基础上又开发成功了电阻探针腐蚀在线监测系统,并在胜利炼油厂第三套常减压装置投用。
该系统利用运算机操纵技术,对电阻探针腐蚀信号进行在线采集、数据转换、远程传输、数据处理,不仅实现了腐蚀数据在线采集运算,使操作人员在室内即可观测,而且将腐蚀数据实时绘成曲线,大大减轻了劳动强度,提高了监测精度。
腐蚀在线监测系统示意图见图1,腐蚀监测操纵软件界面见图2。
图1 现场自动腐蚀监测流程图图2 腐蚀监测操纵软件界面①pH在线检测系统常减顶系统冷凝水的pH值是腐蚀操纵的重要指标,通常采纳人工用pH试纸现场放水的检测方法,费时费劲,精确度不高。
由于监测间断进行,不能及时发觉pH偏低的情形,造成设备腐蚀的发生。
研究所2001年开发了pH在线检测系统,通过酸度计远程采集信号,能够连续在线检测pH值变化情形,并通过DCS系统实时显示,如此能够及时发觉问题并调整注剂,最大限度地减轻常减顶系统的腐蚀。
该系统流程示意图见图3。
②定点测厚定点测厚技术是炼油厂运行中设备管线腐蚀监测的重要手段之一。
该技术采纳专用超声波测厚仪,可检测500℃以下的炼油设备及管管壁厚。
目前胜利炼油厂全厂定点测厚点数量差不多超过5 000个,下一步要达到1到2万个点。
近年来通过设备及管线定点测厚工作,胜利炼油厂发觉多处腐蚀减薄严峻的部位,包括焦化炉炉管弯头、焦化大瓦斯线、减三线系统(包括减一中管线及泵入口过滤器大小头)、高温换热器管箱接管、减顶增压器、常顶馏出线等,有关单位采取了包盒子等处理措施,有效地防止了腐蚀事故的发生。
图3 pH在线测试系统原则流程图③腐蚀介质分析为了监控设备的腐蚀情形,胜利炼油厂还托付研究所加强了腐蚀介质分析,包括常减顶冷凝水分析、加氢装置酸性水分析、脱硫装置再生塔顶酸性水分析、常减压侧线油活性硫及总硫分析、常减压侧线油酸值(度)分析、加热炉烟气热效率及露点腐蚀检测等常规分析项目,此外还有减压侧线油铁离子分析、催化烟气粉尘检测等临时分析项目。
通过腐蚀介质分析能够判定被监测部位总的腐蚀情形,以便于及时调整工艺操作,减轻腐蚀。
此外,腐蚀介质分析还能够用于监测、评判工艺防腐措施的使用成效。
④腐蚀产物分析在装置运行或检修期间,由研究所负责对腐蚀设备进行腐蚀产物取样分析,通过定性和定量分析,判定腐蚀产物组成,为腐蚀机理的确定提供关心。
⑤装置停工腐蚀检查在装置停工检修期间,研究所负责对所有停工装置进行腐蚀检查,对腐蚀严峻的部位进行照相,并采集腐蚀产物进行分析。
关于检修中发觉的腐蚀问题,有关部门要及时采取防护措施。
检修终止后,研究所要提交各装置的腐蚀调查报告。
此外,研究所还开发了氢腐蚀监测探针、腐蚀监测旁路、内窥镜腐蚀检测、埋地管线泄漏检测等技术,以监测炼油厂专门环境下的腐蚀状况。
3.2 工艺防腐技术假如通过腐蚀监检测发觉设备存在腐蚀隐患,就需要采取一定的防腐措施加以预防操纵。
炼油厂常用的腐蚀防护措施能够分为两种:工艺防腐和材料防腐。
关于低温部位的腐蚀,胜利炼油厂通常采纳电脱盐、注缓蚀剂、注中和剂等方法加以操纵,并开发形成了系列技术产品。
①原油低温破乳脱盐技术1999年到2001年期间,胜利炼油厂炼制陆上混合原油时经常显现原油乳化严峻、脱后含盐高等现象,给下游设备带来了严峻的腐蚀和结垢问题。
为此,研究所开发了SYW-3型低温破乳剂及相应的原油罐区低温破乳脱盐技术,通过实际应用,成功地解决了原油乳化及含盐高给电脱盐装置带来的阻碍,保证了脱后原油的含盐含水量。
②电脱盐工艺优化电脱盐成效的好坏直截了当关系着整个炼油厂的设备腐蚀,研究所采纳静态电脱盐评判设备和动态电脱盐评判装置,对电脱盐工艺参数(如温度、电场强度、注水性质、混合强度等)和破乳剂等进行优化选择,多次为炼油厂电脱盐工艺优化提供方案,解决电脱盐运行难题。