热冲压与液压成形零部件投产宝钢助力汽车实现轻量化
高强钢成形技术及其在汽车轻量化中的应用
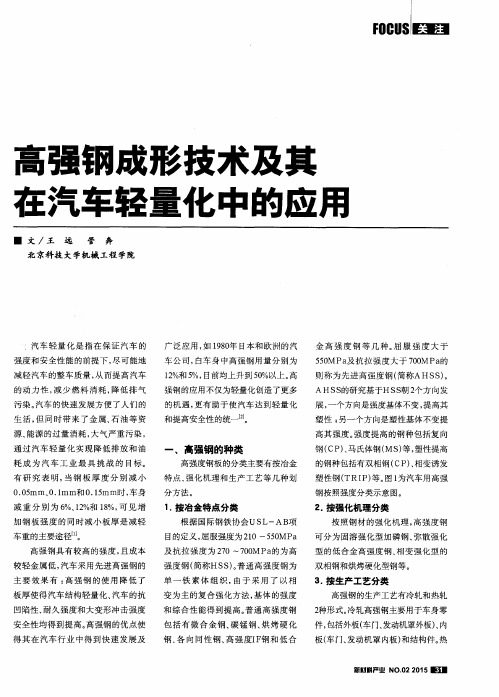
I t S I A: 高 强 度 低 合 金 钢 DF: 双相钢
C P: 复桕钢 TRI P: 相变诱 发性 钢
Ma r t : 马氏 体 钢 TW 1 I : 挛 品 诱 发 塑性 钢 S t a i n l e s s: 不 锈 钢 B S t e e l : 热 冲 压 用 钠
新和料产业 N O . 0 2 2 0 4 5圈
I I 圜 0 C U S
∞ m Βιβλιοθήκη 0 I r: 无 隙 原子 钢 Mi l d: 低 碳 铝 镇 静 钢 I I S S I F: 高强度1 F  ̄ 4 1 I { l I : 烘 烤 硬 化 钢 I s: 向 同性 钠
属H & 强 度 Mt a
图1 汽 车 用 高强 钢 按 照 强 度 分类 示 意 图
轧高强度钢板在载货 汽车上用量很 久,
不 良 为 了克服这 些 缺陷 , 欧 美及 L t
2 . 高强钢热冲压成形技术
当钢强度 超过 1 0 0 0 MPa 时, 一 些形 状 复杂 的零件 , 常 规 的冷冲 压 工 艺难 以成形 , 即使 可 以采 用冷冲 压工 艺, 所需 冲压 力大 、 成 型 件易 开裂 、 回
金高 强度钢等几 种。 屈 服 强 度 大 于 5 5 0 M Pa n t 抗 拉 强度 大于 7 0 0 MPa N 则称 为先 进 高 强度钢 ( 简 称AHS S ) 。
AHSS 的研 究基于 HS S 朝2 个方 向发
强度 和安 全性 能 的前提 下 , 尽可 能地 减轻 汽车 的整车 质量 , 从而 提高 汽车 的动 力 性 , 减少 燃 料 消 耗 , 降低 排 气 污染 。 汽 车 的快速 发展 方便 了人 们 的 生活 , 但 同 时 带来 了金 属 、 石 油 等 资 源、 能源 的过量 消 耗 , 大气 严重 污染 , 通 过 汽 车 轻量 化 实 现 降 低排 放 和 油 耗 成 为 汽 车 工 业 最 具 挑 战 的 目标 。 有研 究表 明, 当钢 板 厚 度 分 别 减 小 0 . 0 5 mm、 0 . 1 mm和 0 . 1 5 mm时 , 车身 减重 分别为 6 %、 l 2 %和 1 8 %, 可 见 增 加 钢 板 强度 的 同时 减小 板 厚 是 减 轻
国外汽车轻量化研究现状分析

国外汽车轻量化研究现状分析
康 受汽车安全性、燃油经济性以及排放标准提高的 制约,汽车轻量化成为当前钢铁行业研究重点之一。
有关行业协会和先进钢铁企业都在进行汽车轻量化用
斌 标杆车型减重了35%,在汽车生命周期内减排二氧化 碳70%。其中纯电动汽车的车身用钢比重见图1,用
钢品种见表1。
材及工程方面的研究,以提高钢材尤其是高强度钢材
2.安赛乐米塔尔S—i
n
motion项目
2010年,安赛乐米塔尔启动了为期2年的汽车 轻量化项目S—in motion(S是Steel、Saving
SaVlng cOst、 SustalnablIlt:
weight、
Safety、SerVice、
Strength、Solution这些词汇能 为汽车用户提供安全、轻量仳
和要求,见表4。
有研究表明2003年我国高强度汽车板的比重为 8%,2011年的比重为38%,整体呈直线上升趋势。 这表明我国汽车行业对高强钢的需求量越来越多,比 重越来越大。这要求钢铁企业尤其是汽车板生产企业 能够为汽车用户提供高强度汽车板,尤其是能从软 钢、高强钢、超高强钢全系列供应。 (1)根据自身产品结构全方位规划汽车用钢产品 我国大型联合钢铁企业一般都能生产板材和线 材,在重点发展汽车用高强度板材同时,还要根据自 身的设备能力发展汽车用高强度线材,实现汽车用板 线材齐头并进。如汽车用高强度帘线钢、弹簧钢、紧 固件用钢等(安赛乐米塔尔、浦项都有发展),国内 生产汽车板大型钢企普遍关注的是板材,而汽车用高 强度线材市场基本由特钢企业所占据。 在汽车全方位供材方面,浦项作了更为全面的研 究。在汽车轻量化研究中已经将汽车各类电机用无取 向硅钢列入轻量化指标。我国大型钢铁企业如宝钢、 武钢、鞍钢都能生产硅钢,也都具备一定实力。 (2)强化汽车工程研究实力和下游加工能力 从国外先进汽车板生产企业的经验来看,发展汽 车板,第一需要有强大的材料研发实力和生产能力, 能为汽车行业提供材料解决方案。第二需要有强大的 汽车工程实力,也就是汽车车身和零部件优化设计、 零部件选材的数值模拟等实力,通过应用提升汽车板 的使用。而目前我国钢铁企业在汽车板生产和产品研 发方面已具备一定实力,但在汽车工程能力的研发普 遍不足。第三需要具备一定汽车板下游加工能力,协 助汽车用钢的应用。如安赛乐米塔尔、蒂森克虏伯、 浦项、宝钢等在发展汽车板的同时,在汽车板激光拼 焊线、热成形线、液压成形线、辊压成形等方面都具 备了很强的实力。 因此,汽车用钢企业在大力发展汽车用钢产品方 面应有全局战略,除了在汽车用钢应用方面具备一定 的汽车工程实力,在汽车板下游加工应用方面也要具 备一定的配套能力,这样才能为汽车用户真正提供整 体解决方案,扩大市场占有率、提高盈利能力。蘩 (作者单位:武钢研究院)
汽车工业中热冲压成形工艺的应用
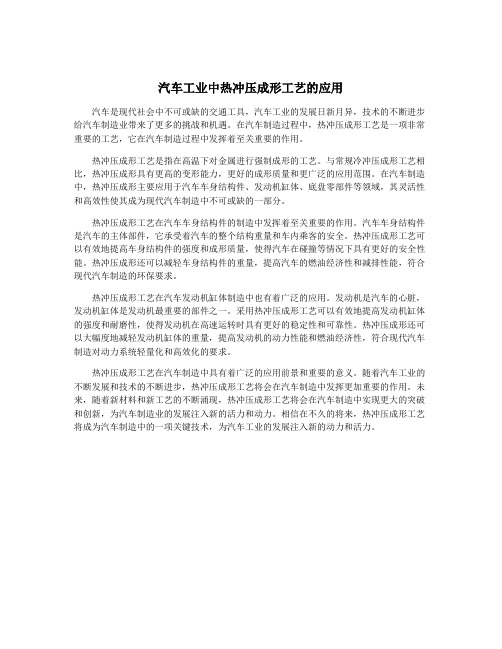
汽车工业中热冲压成形工艺的应用汽车是现代社会中不可或缺的交通工具,汽车工业的发展日新月异,技术的不断进步给汽车制造业带来了更多的挑战和机遇。
在汽车制造过程中,热冲压成形工艺是一项非常重要的工艺,它在汽车制造过程中发挥着至关重要的作用。
热冲压成形工艺是指在高温下对金属进行强制成形的工艺。
与常规冷冲压成形工艺相比,热冲压成形具有更高的变形能力,更好的成形质量和更广泛的应用范围。
在汽车制造中,热冲压成形主要应用于汽车车身结构件、发动机缸体、底盘零部件等领域,其灵活性和高效性使其成为现代汽车制造中不可或缺的一部分。
热冲压成形工艺在汽车车身结构件的制造中发挥着至关重要的作用。
汽车车身结构件是汽车的主体部件,它承受着汽车的整个结构重量和车内乘客的安全。
热冲压成形工艺可以有效地提高车身结构件的强度和成形质量,使得汽车在碰撞等情况下具有更好的安全性能。
热冲压成形还可以减轻车身结构件的重量,提高汽车的燃油经济性和减排性能,符合现代汽车制造的环保要求。
热冲压成形工艺在汽车发动机缸体制造中也有着广泛的应用。
发动机是汽车的心脏,发动机缸体是发动机最重要的部件之一。
采用热冲压成形工艺可以有效地提高发动机缸体的强度和耐磨性,使得发动机在高速运转时具有更好的稳定性和可靠性。
热冲压成形还可以大幅度地减轻发动机缸体的重量,提高发动机的动力性能和燃油经济性,符合现代汽车制造对动力系统轻量化和高效化的要求。
热冲压成形工艺在汽车制造中具有着广泛的应用前景和重要的意义。
随着汽车工业的不断发展和技术的不断进步,热冲压成形工艺将会在汽车制造中发挥更加重要的作用。
未来,随着新材料和新工艺的不断涌现,热冲压成形工艺将会在汽车制造中实现更大的突破和创新,为汽车制造业的发展注入新的活力和动力。
相信在不久的将来,热冲压成形工艺将成为汽车制造中的一项关键技术,为汽车工业的发展注入新的动力和活力。
汽车及零部件轻量化技术现状及研究方向

汽车及零部件轻量化技术现状及研究方向聂采顺【摘要】文章简要介绍了目前汽车轻量化技术的发展状况,包括轻量化设计内容、各种轻量化材料的性能及运用,从而阐述了汽车轻量化的实施途径及方法。
%This article introduced development of automobile lightweight technique, include lightweight design overview, material performance and application, elucidated implement ways and methods of automobile lightweight.【期刊名称】《汽车实用技术》【年(卷),期】2015(000)009【总页数】4页(P29-32)【关键词】汽车轻量化;实施途径【作者】聂采顺【作者单位】四川建安工业有限责任公司,四川雅安 625000【正文语种】中文【中图分类】U465.610.16638/ki.1671-7988.2015.09.011CLC NO.: U465.6 Document Code: A Article ID: 1671-7988(2015)09-29-04随着我国汽车保有量不断攀升,能源短缺、雾霾污染等等问题日益凸显,“节能减排”成为每个车企以及汽车零部件企业的最求目标,这使得轻量化技术受到越来越多的重视。
轻量化技术的发展,为中国汽车材料的发展提供了机遇,因为轻量化是优化设计、合理选材、先进的成形技术以及加工技术等各种专业优势的集成。
汽车的轻量化,就是在保证汽车的强度和安全性能的前提下,尽可能地降低汽车的整备质量,从而提高汽车的动力性,减少燃料消耗,降低排气污染。
汽车轻量化是汽车产业的发展方向之一,也是一个汽车厂商和国家技术先进程度的重要标志。
根据工信部1月23日发布的最新统计数据显示,2014年我国汽车产销量分别为2372.29万辆和2349.19万辆,同比增长7.3%和6.9%,产销量保持世界第一,如图1所示。
汽车铝压铸行业深度研究:一体化压铸、轻量化大市场初现峥嵘精选版

(:中信建投)一、汽车轻量化势在必行,铝压铸工艺优势显著1.1“碳中和”目标驱动汽车行业向绿色转型,轻量化助力实现节能降耗目标汽车尾气污染持续威胁环境,“碳中和”驱动节能减排势在必行。
截至 2021 年底,我国机动车保有量达 3.95 亿辆,同比增长 6.18%,年增量始终保持在两千万辆左右,中长期看仍具有较快增速。
高机动车保有量使得机动车尾气污染严重。
机动车排放的氮氧化物、挥发性有机物分别达 595/196 万吨,占全国排放总量的 33.3%与 19.3%。
因此,在“蓝天保卫战”和“双碳”政策驱动下,汽车减排、低碳化发展形势较为紧迫。
燃油乘用车整体降耗目标不断提升,新能源汽车助力节能减排潜力显著。
按照2020 年 10月正式发布的《节能与新能源汽车技术路线图 2.0》规划,2020-2035年我国乘用车百公里油耗年均降幅逐步提高,减排压力逐年增加。
然而依据国家部委发布的 2016-2019 年度《中国乘用车企业平均燃料消耗量与新能源汽车积分核算情况表》,可计算得到 2016-2019年传统能源乘用车新车实际平均百公里油耗分别为 6.88L、6.77L、6.62L 及 6.46L,始终高于达标油耗 6.7L、6.4L、6L、5.5L。
但受新能源汽车销量持续提升影响,乘用车总体新车平均百公里油耗低于达标值,且拉动幅度越来越大。
由此可见,新能源汽车具有较大节能减排潜力,随着新能源汽车渗透率的逐步提高,可以进一步缓解汽车行业的节能减排压力。
技术路线图明确新能源发展目标,2035年节能与新能源汽车销量占比各 50%。
为进一步推动汽车低碳化进程,《节能与新能源汽车技术路线图(2.0 版)》提出“汽车产业碳排放总量先于国家碳排放承诺于 2028 年左右提前达到峰值,到 2035年排放总量较峰值下降 20%以上”和“新能源汽车逐渐成为主流产品,汽车产业实现电动化转型”等愿景目标。
具体里程碑目标如下:至2035 年,节能汽车与新能源汽车年销量各占50%,汽车产业实现电动化转型;氢燃料电池汽车保有量达到 100 万辆左右,商用车实现氢动力转型。
优化高强钢成形性能助力汽车实现轻量化

中国冶金报/2007年/1月/16日/第012版科技导航优化高强钢成形性能助力汽车实现轻量化热冲压技术介绍郭廷杰为防止全球变暖而签订的《京都协议书》中规定了二氧化碳的减排目标为6%。
从日本的现状看,完成这一目标具有一定的难度。
而且,即使已在该协议书上签字的国家能够完成规定的减排任务,那些未签字的发展中国家的二氧化碳排放量也很难得到控制。
因此,有关方面从保护全球环境的角度出发,开始加紧开发减排二氧化碳的各种技术。
高强度钢的应用带来的成形性问题在二氧化碳的排放量中,汽车尾气所占的比重最大,且其中80%~90%是在汽车行驶中排放的,故降低汽车油耗的技术对二氧化碳的减排而言至关重要。
使用高强度钢板制造车身以控制车体的总重量可以很好地降低汽车油耗。
但在高强度钢板的开发和应用中也存在着一些问题,如成形性能较差,表面形变明显,卡模具情况严重,冲压设备大型化,焊接性能变差以及模具磨损增加等。
成形性建立在一定的强度和延伸率的平衡范围内。
各种加工方法所使用钢材的平衡范围如下:软质冲压用钢,延伸率为44%~48%,抗拉强度为240兆帕~280兆帕;超深冲压用钢,延伸率为33%~42%,抗拉强度为320兆帕~440兆帕;一般固溶强化用钢,延伸率为26%~34%,抗拉强度为320兆帕~440兆帕;相变感生塑性钢,延伸率为28%~38%,抗拉强度为550兆帕~720兆帕;一般加工用析出强化钢,延伸率为15%~24%,抗拉强度为520兆帕~630兆帕;低屈服比双相钢,延伸率为14%~32%,抗拉强度为500兆帕~750兆帕;一般加工用相变钢,延伸率为3%~27%,抗拉强度为750兆帕~1450兆帕;超高强度钢,延伸率为25%~35%,抗拉强度为1000兆帕~1450兆帕。
强度的提升导致加工难度随之提高。
此外,即使延伸率和抗拉强度在平衡范围之内,也还存在伴随着高弹性而产生的回弹形变增大等问题。
由于以上问题很难从材料上解决,故只有从改进冲压技术上进行抑制。
2012 ECB(Euro Car Body)总结及2013ECB新材料应用展望
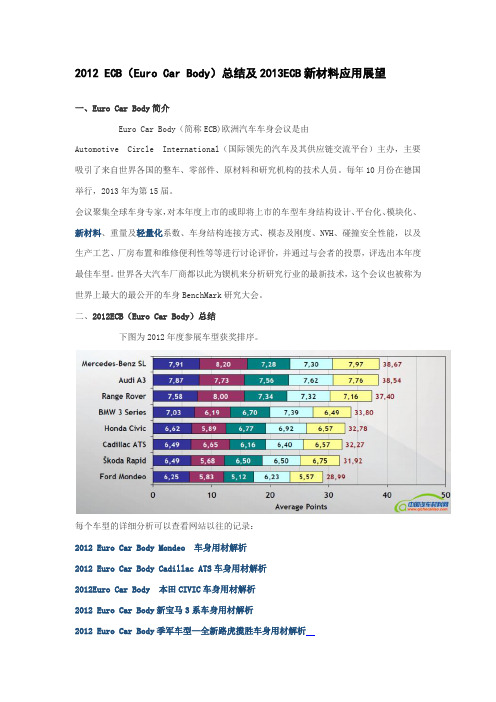
2012 ECB(Euro Car Body)总结及2013ECB新材料应用展望一、Euro Car Body简介Euro Car Body(简称ECB)欧洲汽车车身会议是由Automotive Circle International (国际领先的汽车及其供应链交流平台)主办,主要吸引了来自世界各国的整车、零部件、原材料和研究机构的技术人员。
每年10月份在德国举行,2013年为第15届。
会议聚集全球车身专家,对本年度上市的或即将上市的车型车身结构设计、平台化、模块化、新材料、重量及轻量化系数、车身结构连接方式、模态及刚度、NVH、碰撞安全性能,以及生产工艺、厂房布置和维修便利性等等进行讨论评价,并通过与会者的投票,评选出本年度最佳车型。
世界各大汽车厂商都以此为锲机来分析研究行业的最新技术,这个会议也被称为世界上最大的最公开的车身BenchMark研究大会。
二、2012ECB(Euro Car Body)总结下图为2012年度参展车型获奖排序。
每个车型的详细分析可以查看网站以往的记录:2012 Euro Car Body Mondeo 车身用材解析2012 Euro Car Body Cadillac ATS车身用材解析2012Euro Car Body 本田CIVIC车身用材解析2012 Euro Car Body新宝马3系车身用材解析2012 Euro Car Body季军车型—全新路虎揽胜车身用材解析2012 Euro Car Body亚军车型-- Audi A3车身用材解析2012 Euro Car Body参展车型用材解析(1)--冠军车型 Benz SL每个车型都有其特点,笔者从车身用材分布,新材料新工艺,结构设计和轻量化工程几个方面对2012 ECB做个简单的总结,便于各位读者去分析对比2013年 ECB最新的技术发展。
2.1车身用材分布钢制车身的材料分布ECB的车身高强度钢应用比例是按照冶金学类型进行分类统计的,而不是屈服强度(详细分类请查看:汽车高强度钢应用手册V4.1),车身高强度钢比例最高达到70%。
[高强,汽车,技术]试论高强钢成形技术及其在汽车轻量化中的应用
![[高强,汽车,技术]试论高强钢成形技术及其在汽车轻量化中的应用](https://img.taocdn.com/s3/m/241a601289eb172dec63b703.png)
试论高强钢成形技术及其在汽车轻量化中的应用汽车轻量化是指在保证汽车的强度和安全性能的前提下,尽可能地减轻汽车的整车质量,从而提高汽车的动力性,减少燃料消耗,降低排气污染。
汽车的快速发展方便了人们的生活,但同时带来了金属、石油等资源、能源的过量消耗,大气严重污染,通过汽车轻量化实现降低排放和油耗成为汽车工业最具挑战的目标。
有研究表明,当钢板厚度分别减小0.05mm、0.1mm和0.15mm时,车身减重分别为6%、12%和18%,可见增加钢板强度的同时减小板厚是减轻车重的主要途径。
高强钢具有较高的强度,且成本较轻金属低,汽车采用先进高强钢的主要效果有:高强钢的使用降低了板厚使得汽车结构轻量化、汽车的抗凹陷性、耐久强度和大变形冲击强度安全性均得到提高。
高强钢的优点使得其在汽车行业中得到快速发展及广泛应用,如1980年日本和欧洲的汽车公司,白车身中高强钢用量分别为12%和5%,目前均上升到50%以上。
高强钢的应用不仅为轻量化创造了更多的机遇,更有助于使汽车达到轻量化和提高安全性的统一。
一、高强钢的种类高强度钢板的分类主要有按冶金特点、强化机理和生产工艺等几种划分方法。
1. 按冶金特点分类根据国际钢铁协会U S L - A B项目的定义,屈服强度为210 ~550MPa及抗拉强度为270 ~700M P a的为高强度钢(简称H S S)。
普通高强度钢为单一铁素体组织,由于采用了以相变为主的复合强化方法,基体的强度和综合性能得到提高。
普通高强度钢包括有微合金钢、碳锰钢、烘烤硬化钢、各向同性钢、高强度I F钢和低合金高强度钢等几种。
屈服强度大于550M P a及抗拉强度大于700M P a的则称为先进高强度钢(简称A H S S)。
A H S S 的研究基于H S S朝2个方向发展,一个方向是强度基体不变,提高其塑性;另一个方向是塑性基体不变提高其强度。
强度提高的钢种包括复向钢(C P)、马氏体钢(MS)等,塑性提高的钢种包括有双相钢(C P)、相变诱发塑性钢(T R I P)等。
关于宝钢钢板材料标准

0 0
BHSL BHSU
5
(b) B H = 40 M P a
50 0
-10 ε , %0
10
5
10
15
20
ε, %
15
20
25
30
35
ε. %
烘烤时间,min
60 50
BH,MPa
180BH自然时效8个月后的拉伸曲线
40 30 20 10 0 30 60 90 120 150 BHSL BHSU 180 210
内板
外板
白车身、悬挂件
常规冲压
滚压
热冲压
主要内容
1 汽车轻量化的技术路线 2 宝钢汽车轻量化用HSS的选用 3 宝钢HSS专用线产品及技术 4 我国汽车轻量化展望
HSS专用机组的主要产品
高强钢专用机组:产能规模20万t
产品规格: (0.5~2.1)×(700~1250mm) 品种大类:冷轧带钢、 热镀锌GI 高强钢产品种类: 冷轧DP钢 :590-1180MPa级 冷轧马氏体钢 :900-1500MPa级 冷轧TRIP钢 :590-980MPa级 热镀锌DP钢 :590-980MPa级 热镀锌TRIP钢 :590-780MPa级
1000
1200
• IF • Mi • HS • BH • IS • CM • HS • DP • CP • TR • Ma • TW • St •B
名称
级别
CR(EG)
GI
GA
Q/BQB 419-2008 低合金高强度冷连轧 钢板及钢带 Q/BQB 418-2008 双相高强度冷连轧钢 板及钢带
扩孔率λ=(df-d0)/d0,其中df为出现破断时的孔径,d0为初始孔径
科技成果——超高强汽车用钢的热金属气胀成形技术
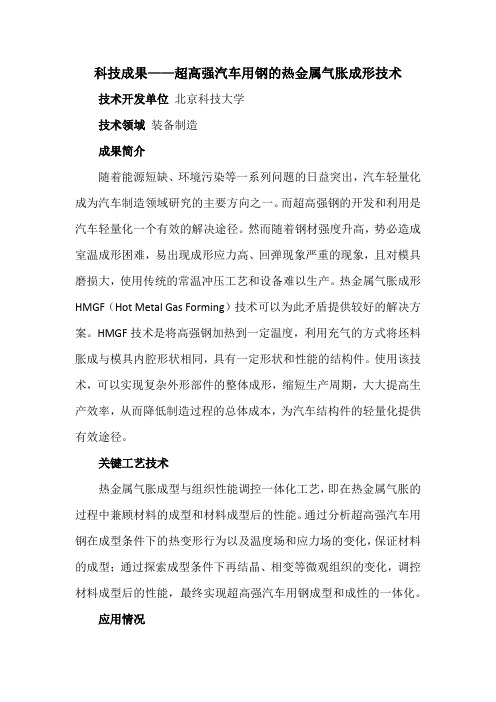
科技成果——超高强汽车用钢的热金属气胀成形技术技术开发单位北京科技大学技术领域装备制造成果简介随着能源短缺、环境污染等一系列问题的日益突出,汽车轻量化成为汽车制造领域研究的主要方向之一。
而超高强钢的开发和利用是汽车轻量化一个有效的解决途径。
然而随着钢材强度升高,势必造成室温成形困难,易出现成形应力高、回弹现象严重的现象,且对模具磨损大,使用传统的常温冲压工艺和设备难以生产。
热金属气胀成形HMGF(Hot Metal Gas Forming)技术可以为此矛盾提供较好的解决方案。
HMGF技术是将高强钢加热到一定温度,利用充气的方式将坯料胀成与模具内腔形状相同,具有一定形状和性能的结构件。
使用该技术,可以实现复杂外形部件的整体成形,缩短生产周期,大大提高生产效率,从而降低制造过程的总体成本,为汽车结构件的轻量化提供有效途径。
关键工艺技术热金属气胀成型与组织性能调控一体化工艺,即在热金属气胀的过程中兼顾材料的成型和材料成型后的性能。
通过分析超高强汽车用钢在成型条件下的热变形行为以及温度场和应力场的变化,保证材料的成型;通过探索成型条件下再结晶、相变等微观组织的变化,调控材料成型后的性能,最终实现超高强汽车用钢成型和成性的一体化。
应用情况已投入研发费用200万元以上,目前处于中试阶段。
本项目已获得国家重点研发计划的资助,并在航宇智造(北京)工程技术有限公司和天津天汽模志通车身科技有限公司进行工业化推广。
市场前景可以推广到钢铁企业深加工业务领域的拓展方向,或给汽车零部件及主机厂进行推广。
投资估算和经济效益分析投资估算2000万元,预计3年收回投资。
成果亮点1、具有自主知识产权,研究成果已申请发明专利2项;2、技术先进性:本项目以开发新型成形工艺为手段,突破传统汽车零部件成形方式的局限,掌握超高强钢零部件成形与组织性能调控一体化工艺技术,形成具有自主知识产权的系列技术及应用,建立先进成型技术应用示范线。
合作方式技术许可、作价入股、合作开发。
机械设计中的轻量化技术如何应用

机械设计中的轻量化技术如何应用在当今的机械设计领域,轻量化技术已成为一个至关重要的研究方向。
随着科技的不断进步和市场需求的变化,减轻机械产品的重量不仅能够提高能源利用效率、降低运行成本,还能增强产品的性能和竞争力。
那么,轻量化技术在机械设计中究竟是如何应用的呢?首先,材料的选择是实现轻量化的基础。
高强度钢、铝合金、镁合金以及各种复合材料等在机械设计中得到了广泛的应用。
高强度钢具有较高的强度和良好的韧性,在保证结构强度的同时,可以通过减少材料的厚度来减轻重量。
铝合金和镁合金则具有密度小、比强度高的特点,常用于制造汽车零部件、航空航天部件等。
复合材料,如碳纤维增强复合材料(CFRP)和玻璃纤维增强复合材料(GFRP),具有优异的力学性能和轻量化优势,但成本相对较高,目前主要应用于高端机械产品。
以汽车行业为例,汽车的车身结构采用高强度钢和铝合金的混合材料,可以在保证碰撞安全性的前提下,显著减轻车身重量。
在航空航天领域,飞机的机翼、机身等部件大量使用碳纤维复合材料,不仅减轻了飞机的重量,还提高了飞机的燃油效率和飞行性能。
其次,结构优化设计是轻量化技术的核心。
通过合理的结构设计,可以在不增加材料的情况下提高结构的强度和刚度,从而实现轻量化。
常见的结构优化方法包括拓扑优化、形状优化和尺寸优化。
拓扑优化是在给定的设计空间内,寻找最优的材料分布形式,以达到最佳的力学性能。
例如,在设计一个机械支架时,可以通过拓扑优化确定材料的最优布局,去除多余的材料,从而实现轻量化。
形状优化则是通过改变零部件的外形来改善力学性能,如采用流线型的设计来减少空气阻力。
尺寸优化则是在确定的结构形状基础上,对零部件的尺寸进行优化,以达到轻量化的目的。
再者,制造工艺的改进也对轻量化技术的应用起到了重要的推动作用。
先进的制造工艺,如增材制造(3D 打印)、液压成形、热冲压成形等,可以实现复杂结构的制造,减少零部件的数量和连接,从而减轻重量。
高强度钢在汽车轻量化中的应用

组织 强化
490~1 180
利用将钢从高温的奥氏体急 冷时生成的硬质相马氏体和贝 氏体的强化机理
a.强度高且比较容易兼顾到成形性 b.根据硬质组织的种类、数量、形 态不同而具有多样性(DP钢、TRIP 钢、高扩孔性钢)
因此,高强度钢板能够大幅度增加零件的抗变形能
力,提高能量吸收能力和扩大弹性应变区。高强度钢
应用于汽车零件上,可以通过减薄零件厚度来减轻车
身质量;当钢板厚度分别减少0.05、0.10、0.15 mm
时车身可减重6%、12%、18%。车身用钢向高强度
化发展已经成为趋势。
2 高强度钢的强化机理与分类
2.1 高强度钢的强化机理 高强度钢的强化机制主要有固溶强化、析出强
国内汽车合资企业的技术直接来源于国外母公 司,高强度钢应用水平与国外汽车企业保持了相近的 水平。自主品牌汽车企业在高强度钢的应用方面整体 落后于国外汽车公司,正在快速追赶。最近两年,国内 自主品牌汽车开发的有些新车型,高强度钢质量占白 车身质量的比例已经达到45%以上。近年来,国内 钢铁企业积极开展了汽车用高强度纲的开发工作,目 前宝钢、武钢、鞍钢等可以生产一些等级的高强度IF
图3 TRIP780金相组织中约18%残余奥氏体
图1 DP600金相组织
图4 TRIP690金相组织中约10%残余奥氏体
图2 DP980金相组织 (5)相变诱导塑性钢(TRIP) 相变诱导塑性钢其金相组织为铁素体、贝氏 体、残余奥氏体,见图3、图4。在变形过程中,残余 奥氏体会发生诱导相变转化为马氏体,引起相变强 化和塑性增长。这类钢兼顾了较高的抗拉强度和良 好的成形性(见图5),比双相钢成形性更好,同样 具有BH钢性能,拥有更好的扩孔性(见图6)。目 前,此类钢板的主要牌号有TRIP590、TRIP690、 TRIP780和TRIP780HR等,在汽车行业尚没有得到 大规模应用。 (6)多相钢(CP) 多相钢组织与TRIP钢类似,基本上是在Mn-CrSi合金成分体系的基础上,依靠钛、铌、钒元素微合 金化产生的晶粒细化效应和析出强化效应,结合适当
汽车轻量化-文献综述
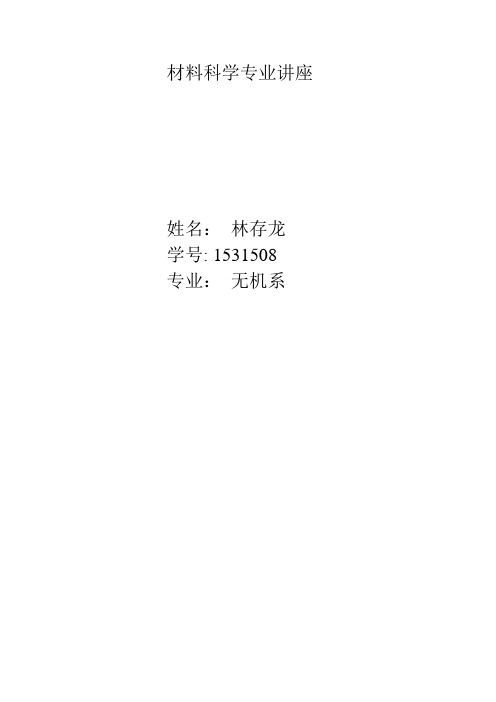
材料科学专业讲座姓名:林存龙学号: 1531508专业:无机系材料在汽车轻量化中的应用及发展摘要:由于汽车工业的迅速发展,汽车产量和保有量的增多,带来了油耗、排放和安全三大问题。
论述了汽车节能减排是汽车工业发展的必然趋势,轻量化是汽车节能减排的直接而有效的手段;介绍了汽车轻量化意义和轻量化工程的实施方法。
采用轻量化材料,如高强钢、铝合金、镁合金、塑料、复合材料等重点介绍了轻量化材料及先进的制造工艺在汽车轻量化中的应用现状,综述了轻量化领域中新材料、新工艺的最新研究进展。
总结了目前国内外研究的热点、难点问题.基于目前的研究现状,提出了未来汽车轻量化技术的发展趋势。
关键词:汽车;轻量化The Application and Development of Materials in Automotive Weight LightingAbstract: The brief condition of development of China automotive industry was reviewed。
Three problem:oil consumption,emission,safety were brought about due to the rapid development of auto industry , the production output and vehicle stock in China。
Energy saving and emission reduction is necessary trend of auto industry development。
Affective and direct method and way is Auto lightweight。
The concept ,significance implementation methods have been introduced. Use the lightweight materials of high strength steel, aluminum alloy,plastics composites, etc。
宝钢上汽携手攻关汽车用钢“轻量化”

与性 能 改进 条 件下 , 过结 构 设 通
维修 大 厅 及航 线 大楼 组 成 , 度 跨
达 4 l 总建 筑 面积 21 8/, q .8万 m 。 作 为 虹 桥 交 通 枢 纽 区域 内 首 个 大 型航 线 机 库 ,该 机 库 可 同 时 维 修 2架 波 音 7 7飞 机 和 1 4 架 A2 3 0客机 , 而有 效提 升东方航 从 空 公 司 在 该 区域 的 机 务 维 修 和 地 面保 障能力 。
度 大 ,面积达 9 . m ,相 当于 4万 1 3个标 准足球 场那 么 大 , 质量 总
屋 架 , 日整体 提升 到 3 .m 的 近 75 高度 就位 。
该 工 程 位 于 虹 桥 国 际 机 场 东航 基 地 机务 维 修 区 内 , 由机 库
大生 产 和 消费 国 , 量 化 已成 轻 个 重 要课 题 。 如何 在 成本 控 制
为 我 国汽 车 工 业 可 持 续 发 展 的
一
约 8 0 。 此 大 规模 、 体 量 、 0t如 0 大
高难 度 的高 空 网架 在 国内罕见 。 据 工程 技 术人 员 介 绍 , 面 总 积近 l 0万 r 的 屋 盖 将 被 分 成 l l 9块 网架单元 , 别 拼装 、 装到 分 安 指 定 位 置 后 再 连 成 整 个屋 盖 网
立 柱 的顶 端 搭 建 4条 “ 中轨 空 道 ” 利 用 轨 道 把 一 个 个 网架 单 ,
4 i 5mn车程 内前 往各 比赛 场馆参 加 比赛 , 可 避 开市 中心交 品 的轻 量 化 设
计 应用 , 升宝 钢 股份 汽车轻 量 提 化 材 料 研 发 水 平 和解 决 方 案 的
行 业 信息
热冲压成形技术及发展前景

热冲压成形技术及发展前景王辉;葛锐;周少云;陈寅;潘利波【摘要】Based on the characteristics of thermal forming technology and current development both at home and abroad ,the paper gives a description of thermal forming technology development of steel plant , die arrangement design ,key equipment of process ,and machine parts design and analyzes the prospects in the future .%世界汽车工业汽车轻量化技术的可持续发展带动了热成形技术的快速发展,并成为汽车制造领域的热门技术。
围绕热成形技术的特点对热冲压成形技术国内外现状进行了介绍,重点从热成形钢板开发、热成形模具设计技术、热成形工艺关键装备技术、以及热成形零件设计技术等方面详细探讨了热成形技术的技术发展,并对热成形技术的未来前景进行了分析与展望。
【期刊名称】《武汉工程职业技术学院学报》【年(卷),期】2014(000)003【总页数】4页(P52-55)【关键词】热成形;轻量化;超高强钢;汽车板【作者】王辉;葛锐;周少云;陈寅;潘利波【作者单位】武汉钢铁集团公司研究院湖北武汉430080;武汉钢铁集团公司研究院湖北武汉430080;武汉钢铁集团公司研究院湖北武汉430080;武汉钢铁集团公司研究院湖北武汉430080;武汉钢铁集团公司研究院湖北武汉430080【正文语种】中文【中图分类】TG3860 引言随着能源危机和环境问题的日益加剧,汽车轻量化已经成为世界汽车工业可持续发展的必然道路。
车身高强化,既可以减轻车身重量,又能提高安全性,是同时实现车身轻量化和提高碰撞安全性的最好途径。
影响高强钢汽车板发展的主要问题及其对策

影响高强钢汽车板发展的主要问题及其对策发表日期:2007-3-23 阅读次数:458摘要:随着我国汽车工业的快速发展以及汽车保有量的不断增长,汽车减重、节能、小型化、安全、环保等受到人们的普遍关注,高强钢汽车板将是今后汽车板发展的主流,大量使用高强钢是解决汽车减重、节能、安全、环保的重要途径。
为此,介绍了高强钢汽车板在钢厂各工序生产中存在的主要问题和汽车厂使用高强钢中存在的主要问题,并对加快发展中国高强钢汽车板提出了相应的解决措施。
关键词:汽车板高强钢生产对策1 前言进入21世纪以来,中国汽车工业的发展呈加速发展态势。
从1992年到2000年,中国汽车年产量从100万辆增加到200万辆,而从200万辆/年增加到300万辆/年只用了不到两年的时间。
2002年之后,汽车产量平均每年约增加100万辆。
随着我国汽车工业的快速发展以及汽车保有量的不断增长,道路、停车场、交通安全和燃油紧张等问题也日趋突出。
因此,汽车的减重、节能、小型化、安全、环保等备受人们普遍关注,而高强钢汽车板的大量采用对解决上述问题都有帮助。
研究结果表明,汽车板抗拉强度从220MPa提高到700MPa,材料厚度从1.8mm减小到1.4mm,而材料可吸收冲击能指数则基本保持不变。
汽车减重也与材料强度密切相关。
研究表明,材料抗拉强度从300MPa左右提高到900MPa左右,汽车减重率则从25%左右提升到40%左右。
近10年来,汽车用高强钢的发展速度很快。
为了适应汽车板高强化的发展趋势,世界各国纷纷开展了高强钢的研发并取得了令人瞩目的进展。
2 汽车用高强钢板的研究发展20世纪90年代初,欧洲试生产了全铝汽车。
由于可以减轻车重,降低油耗,铝材有跻身汽车行业取代钢材的可能。
1994年,国际钢铁学会(简称“IISI”,International Iron&steel Institute)组织主要由北美和西欧35家钢厂和汽车厂组成的联合攻关课题,开展了超轻钢车身项目ULSAB(ultra Light Steel Auto Body)的研究。
做轻量化“逐风者”,让“玛克系”开枝散叶!
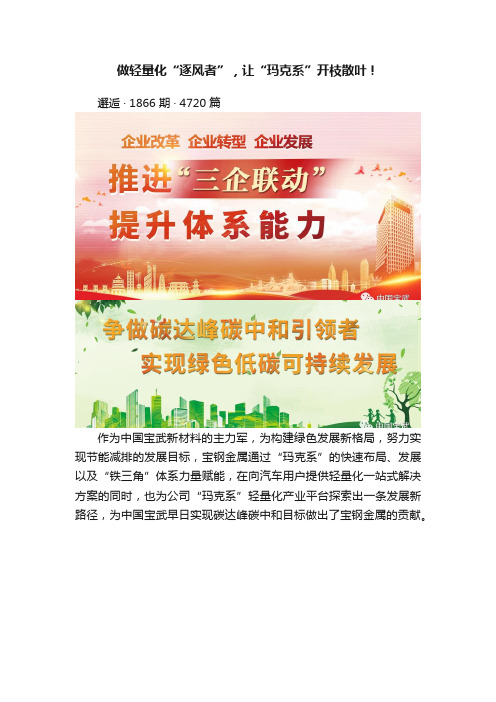
做轻量化“逐风者”,让“玛克系”开枝散叶!邂逅· 1866期· 4720篇作为中国宝武新材料的主力军,为构建绿色发展新格局,努力实现节能减排的发展目标,宝钢金属通过“玛克系”的快速布局、发展以及“铁三角”体系力量赋能,在向汽车用户提供轻量化一站式解决方案的同时,也为公司“玛克系”轻量化产业平台探索出一条发展新路径,为中国宝武早日实现碳达峰碳中和目标做出了宝钢金属的贡献。
打造宝玛克品牌“玛克系”开枝散叶当前,在国家实施碳达峰碳中和的背景下,汽车减重已成为大势所趋。
新能源汽车减重既可以节省能源消耗,也可以提高续航里程,因此新能源汽车对轻量化的需求更加迫切。
为实现“轻量化解决方案领军者”的愿景使命,2016年以来,宝钢金属开始积极探索汽车轻量化之路。
2017年,宝钢金属全球布局,控股意大利宝玛克集团,整合海外宝玛克40多年的车身设计和制造经验,协同开发中国市场,为客户提供轻质材料开发和应用的一揽子解决方案。
期间,宝钢金属科学谋划,围绕城市规划、汽车厂商进行战略布局,“玛克系”逐步在国内生根发芽、开枝散叶,宝钢金属合肥宝玛克分公司、沈阳宝玛克分公司、宝玛克(合肥)科技有限公司、武汉宝玛克分公司先后成立。
作为首家落地的企业,宝钢金属合肥宝玛克分公司(以下简称“合肥宝玛克分公司”)自成立以来,始终与意大利宝玛克高效协同,将其多年在铝制部件和高强钢零部件的设计、制造和服务经验迅速落地。
同时,宝钢金属“玛克系”业务以强大的同步设计开发能力为基础,以开放的姿态积极与国内各大汽车商、高校和产业链相关机构展开合作,共同以新材料量产应用为目的进行技术开发与合作,得到了广大汽车用户的认可和赞许。
目前,合肥宝玛克分公司已经获得蔚来汽车、吉利汽车、路特斯汽车、华晨雷诺、爱驰汽车、零跑汽车、海马汽车等多款车型订单。
坚持自主创新占领技术制高点要成为轻量化解决方案领军者,技术领先是关键。
汽车模具行业属于高壁垒行业,对于汽车零部件配套企业来说,模具制造技术水平的高低,不仅是衡量制造水平高低的重要标志,更在很大程度上决定着这个企业所产出的产品的质量、效益及其新产品开发能力。
- 1、下载文档前请自行甄别文档内容的完整性,平台不提供额外的编辑、内容补充、找答案等附加服务。
- 2、"仅部分预览"的文档,不可在线预览部分如存在完整性等问题,可反馈申请退款(可完整预览的文档不适用该条件!)。
- 3、如文档侵犯您的权益,请联系客服反馈,我们会尽快为您处理(人工客服工作时间:9:00-18:30)。
火液折光读数与冷却速度进行检 测修正 ,回火 与淬火时
间问隔不 能超过 1 ” 的规定 。 h
这里加热与冷却之 间有 0 5 的间隔 ,目的是让加热 .s 部位 达到温度均匀 ;由于主轴颈 、连 杆颈与止 推面的淬 火是 由不 同的感应器完成 ,淬火 的顺 序以各部位 淬火不
相互影 响为准 。
从 20 0 8年 4月份至今 已有 8 2条 曲轴装机使用 ,还 有近 2 曲轴 在制 。在这 两年 的生产 过程 中 ,我们 遇 0条 到 了很多问题 ,大部 分都跟热处理有关 。
车轻 量 化 的 重要 技 术 途 径 。 宝钢 热 冲 压 和 液 压 成 形 项 目
的顺利投产 ,标 志着宝钢汽车零部件产业化发展进入 了
严格控制 曲轴工序质量 ,是解决这一问题 的根热处理 质量 ,我们成 立 了由技术 、管
理 、生产一线人员组 成 的攻 关型 Q c小组 ,对 曲轴 的热 处理进行全过程 控制 ,裂纹与 硬度不均 的问题 已彻底解
决 ,淬火变形 问题还有进一 步改进的空 间。该 大型船用 中速柴油机曲轴 国产化 的成 功 ,填补 了国内空 白,打破
等 。 宝钢 液 压 成 形 一 期 的 产 能 计 划 为 5 万 件 , 总投 资 0
22亿 元 。 主 要 产 品 是 液 压 成 形 零 部 件 、相 关 模 具 、 夹 . 具 、 配套 部 件 和 总 成 。 热 冲 压 和 液 压 成 形 技 术 是 实 现 汽
五 、曲轴热处理 中遇 到的问题及应对措施
趟 赠
了该类 曲轴完 全依赖进 口的局面 。MW (0078 2 10 1)
0
热 冲压 与 液压 成 形 零 部 件投 产
时间r / h
宝钢助 力汽车 实现轻量化
近 日 ,宝 钢 热 冲 压 零 部 件 有 限公 司 、 宝钢 液 压 成 形 零 部件 有 限 公 司正 式 投 产 。 宝钢 热 冲压 一 期 工程 计 划 产 能 lO万 件 , 总 投 资 2 3亿 元 。 主 要 产 品 是 汽 车 安 全 O .
所 示
样 ,而感应器变形问题 ,需做工装 ,在每次淬火 后对
感应器进行检测修正。
( ) 淬 火变 形 这 里 所 说 “ 形 ” 为 “ 加 变 3 变 附 形”,即附加 力引起 的变形 ,主要 由机床结 构所致 ,也
与 曲轴淬火前 的加工状 况有 关。进 一步优 化机 床结构 ,
生过大的组织应 力 ;或 者 回火 不及 时 ,回火 温度 过低 ,
在后 续的磨 削中 ,磨 削力与 内应 力叠加 ,超过 材料 的强
度极 限而产生裂纹 。
() C 主轴 颈 淬火 曲线 () 杆颈 淬火 曲线 d连
为了避免 以上 问题 的发生 ,我们 制定 了 “ 定期对淬
图 1 零件各部位淬火 曲线
He tT e t n a ra me t
L处 垫 里圜 -
( ) 曲轴磨削后探伤发现裂纹 曲轴磨削后 出现裂 1
纹 ,除了与磨 削进 给量及冷却 等因素有关 外 ,跟感应淬
火及 回火也有很大的关 系 ,如淬火液浓 度测量不 准,致 使使用的淬火液 3 0C冷 速过大 ,马氏体转 变过快 ,产 0 ̄
( )淬火表面硬度不均匀 其原 因 :一是淬火液浓 2
度太 高,粘度增大 ,冷却时喷淋不 均匀 ;二是感应 器变 形造成加热不均匀 。淬火液浓度高跟浓 度低的解决 方法
一
四、曲轴 的回火
通过控制淬火时的冷却时间 ,淬火液 喷淋冷却 结束 时,曲轴的温度大约为 10~10C,这部分热量 可使曲 5 7 ̄ 轴进行 白回火 。为 了使组织转变彻底 ,最 大限度地 消除 曲轴整体 的内应力 ,将 曲轴送入 回火 炉 回火 。回火 温度 以能保证精加工后 曲轴硬度合格为 限度 ,在硬度合 格的 前提下 ,回火温度越高 ,内应力去除越彻 底 ,对后续 磨 削越有利。通过大量试验 ,最后 确定 的 回火 工艺如 图 2
件 , 包括 A柱 、B柱 、 C柱 、 车 门 防撞 杆 、前 后 保 险 杠
图 2 曲轴的 回火曲线
目 ,由于 曲轴淬 火 时还 不能 达到 完全 “ 前 自由” ,
对 变形超 过限 度 的 曲轴在 回火 时进行 校 正 ,即所谓 的
“ 热定型” 热定型 ”在 目前 的生产 中起 到 了很大 的挽 。“ 救 曲轴 的作用。
一
个崭新 的起点 ,成 为宝钢 为汽车用户提供全 方位 、 系
统 化 解 决方 案 的 重要 支撑 。
参磊 工热 工 处 铸m et 1年 ng1950.cor 加 热 锻 造 2wor第2 n 0 ki 1 o 期 WWW. al