大跨度吊车梁制作方案
大跨度吊车梁分段安装工艺

避!塑,苎且大跨度吊车梁分段安装工艺周胜祥(中国二十冶集团有限公司浦东分公司,上海市201900)【I商要]本文结合湘钢宽厚板冷瓤顶目冷床工程项目介绍了大跨度吊车梁分段吊装、空中组拼、焊接的施工技术。
洪键词]大跨度;吊车梁;分段安装大跨度吊车梁分段吊装、空中组拼、焊接是我公司在湘钢宽厚板冷轧项目冷床工程施工中首次尝试。
按照常规的吊装方法是在地面组拼、焊接整体后双机抬吊,以往的做法不但对安装现场场地要求要足够大,而且需要专门的拼接平台,此外还要考虑两台百吨以上大吊机的占位和移动空间。
相比之下,我们采用的单机分段吊装、空中组拼、焊接的新工艺即有着更加“轻便灵活”的感觉,安装场地需求空间少、设备投入常规,既缩短了工期,又保证了安全、质量、经济等优势。
下面就大跨度钢吊车梁分段安装工艺在湘钢工程中的应用,及施工中安装方案设计、受力分析计算、焊接工艺、如何分段吊装、接口部位连接及保证其安装精度、安全方面采取的有效措施加以阐i也1概况简介湘钢宽擘板轧机工程冷床车间主厂房54米超长吊车梁由中冶赛迪技术股份有限公司煦计,我单位承建制安施工,吊车梁截面高度为5米,跨度54米,共计8根。
采用I形截面特厚钢板焊接,翼缘板厚度为45m m,腹板厚度为32m m,单重125t o每根吊车梁分三段进行制作、安装,中段最长为19.5m,两端长度各为1725m,每个对接接头用M24扭剪型高强螺栓进行连接,每段重量约40吨左右,在接口处采用高强螺栓及翼缘板多层焊接进行连接,每个接头共有高强螺栓计614套,所有的高强螺栓安装、翼板对接焊接均在高空作业完成,其安装情度、焊接质量要求之高,吊装难度之大,安全措施的保证,是本单项工程的最大难点。
2吊车、钢丝绳选择吊车、钢丝绳选择的是否合理,不但关系到整个吊装的成功与否,同时也关系到项目的成本,依据现场实际情况,在经过详细计算后,最终选择了L S一218R H一80T的履带吊,直径为56m m钢芯钢丝绳,即经济又合理。
浅谈常规设备制作大截面、大跨度吊车梁

2 4 1 作 原 因 : 1 吊运 和 拼 装 过 程 中 的 碰 撞 。 () 、、 操 () 2 吊装 孔 附近 混 凝 土被拔脱 。() 3 管片环发生扭转时, 千斤顶项在两块管片接缝处会导致 管片 端面崩角而破坏。 () 3千斤顶撑靴顶在管片上不正 ( 盾尾间隙不均匀 时) 会 使管片 内侧或外侧 的混凝土破损 。 2 4 2姿 态 控 制 上 : 1 盾 构 机 姿 态 调 整 时 , 急 于 纠 偏 造 成 受力 不 均 、、 () 匀 。() 构机姿态调整时, 2盾 千斤顶行程差过大而导致受力不均 出现管片损
工 程 科 学
浅谈常规设备制作大截面 、 大跨度吊车梁
秦慧 利
( 攀钢集 团冶金工程技术有限公司成都分公司 6 0 6) 1 0 1
【 搐Biblioteka 要】 介绍攀成钢 5 万 吨 / O 年高速线材生产线工程大截面、 大跨度 吊车梁 的制作工艺 , 特别对该种梁应用常规设备制作工艺及制作要求进 行详
2 工程难 点 钢 结构 制作厂的设备 多为满 足常规 吊车梁 的制 作而配备 ( 截面 高度
20 5 0以下 、 跨度 6 8 ) 而该工程 最大跨度 的吊车粱 为 3 2m 3 .m 常 ~1m , . 5X 09 , 规 设备 按 一 般 制 作 厂 工 艺无 法 制 作 , 场 制 作 精 度 又 不 易保 证 。 现 3 操作要点 31 . 材料检验 () 材 : 1主 吊车 梁 材 质 为 Q 4— c 钢 材 化 学 成 份 及 力 学 性 能 应 符 合 35 , G / 19 —l 9 B T 5 l 9 4中有 关规 定。由于截面高度 3 2 .5米 , 优先选用板宽 2 2 .× l b1 米 的热轧板 , 查来料 尺寸、 号、 O 1 检 牌 表面质量及不平度 ( 即不平度 不 大于 3mm 。 a r / ) () 接 材 料 : 弧 焊 接 时 , 用 H O n 2焊 埋 采 IM 2型 焊 丝 , 配 以相 应 的焊 剂 , 并 C 2气体保护焊 时,采用 E 5 — 0 R 0 2型焊丝 ,焊丝应符合 G / 1 9 7 1 9 、 B T 4 5- 94 -
吊车梁专项施工方案

1)施工工艺:
本工程地基基础设计等级为乙级,建筑场地类别为Ⅱ类,地震设防烈度为7度,框架抗震等级为三级,建筑物重要性类别属丙类,设计地震分组为第一组,设计基本地震加速度为0.1g。本次吊车梁系统起重机技术参数及所有构件如下两表所示
50/10t-28.5m(慢速)电动双梁式起重机主要技术参数一览表
参数类型
主起升机构
3.1.4、环境目标:消灭重大责任环境污染事件,水、气、声达标排放;固(液)废弃物处置符合法规和攀钢标准,创市级安全文明施工标准化工地。
3.2进度安排和空间组织
此次平台工程中主要分部工程分为吊车梁的钢筋笼绑扎,吊装,吊车梁的浇三步
钢筋安装绑扎→吊车梁吊装→垂直度校正→平面位置校正→吊车梁的最后固定模板支护→及埋件预埋→砼浇筑→模板拆除→构建养护。
《建筑地面工程施工质量验收规范》(GB50209-2002)
《火力发电厂土建结构设计技术规定》(DL5022-93)
《建筑地基基础设计规范》(GB50007-2002)
《建筑抗震设计规范》(GB50011-2001)(2008年版)
攀冶QEO文件
《项目策划控制程序》
《施工安全防护管理程序》
《固体废弃物管理控制程序》
6.4.1施工测量
1)、施工测量整体控制
本工程平面控制以厂房轴线为基准,根据平面布置图用钢尺丈量定位具体每根梁的安装位置及高度。结构工程施工阶段,用经纬仪将轴线投测到工作面,控制掉吊车梁位置
大跨度吊车梁吊装施工工艺
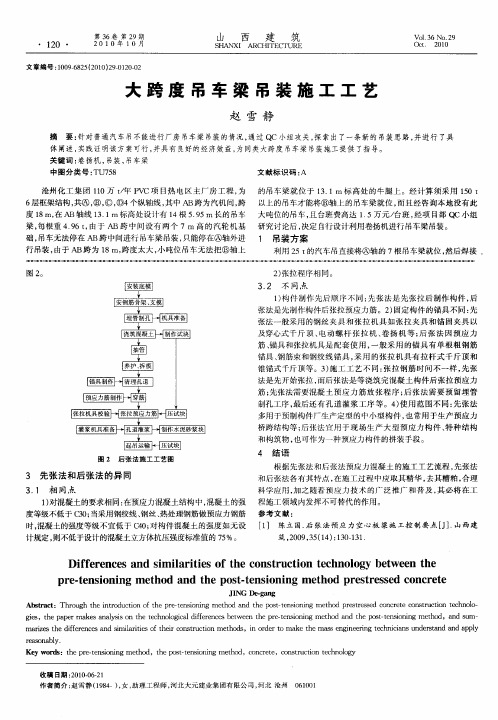
大 跨 度 吊 车 梁 吊 装 施 工 工 艺
赵 雪 静
摘 要 : 针对普通 汽车 吊不 能进行厂房 吊车梁 吊装 的情况 , 通过 QC小组攻关, 探索 出了一条新的 吊装思路 , 并进 行 了具
体 阐述 , 践 证 明该 方 案可 行 , 实 并具 有 良好 的经 济 效 益 , 同类 大 跨 度 吊车 梁 吊装 施 工 提 供 了指 导 。 为 关 键 词 : 扬机 , 卷 吊装 , 吊车 梁 中 图分 类 号 : U7 8 T 5 文 献标 识码 : A
・
10 ・ 2
第3 6卷 第 2 9期 2010年 10月
山 西 建 筑
S HANXI ARCHI TE( URE
Vo . 6 No. 9 I3 2 Oc . 2 0 t 01
文章编号 :0 96 2 (00)90 2 —2 10 —8 52 1 2 —100
沧州化工 集 团 10万 t年 P C项 目热 电区主 厂房工 程 , 1 / V 为 的 吊车 梁 就 位 于 1 . 标 高 处 的 牛腿 上 。 经 计 算 须 采 用 10t 3 1m 5 6层框架结构 , , , , 个纵轴线 , 中 A 共④ ⑤ ⑥ ⑩4 其 B跨为汽机 间, 跨 以上 的吊车才能将⑤轴上 的吊车梁 就位 , 而且 经咨询本地没有此
及穿心式千斤 顶 、 电动 螺杆 张拉 机 、 卷扬 机等 ; 张法 因预应 力 后 筋、 锚具 和张拉机具是 配套使 用 , 一般采用 的锚 具有单根粗 钢筋 锚具 、 钢筋束 和钢绞线 锚具 , 采用 的张拉机 具有 拉杆式千斤 顶和 锥锚式千斤顶等 。3 施 工工艺 不 同: ) 张拉钢 筋时 间不 一样 , 先张 法是先开始张拉 , 而后张法是等浇筑完混凝 土构件后张拉预应力 筋 ; 张法需要混凝 土预应力 筋放 张程序 ; 先 后张 法需要 预留埋管 制孑 工序 , L 最后还有 孔道灌 浆工 序等。4 使 用范 围不 同: 张法 ) 先 多用于预制构件厂生产定型的中小 型构件 , 常用于生产预应力 也
吊车梁吊装施工方案
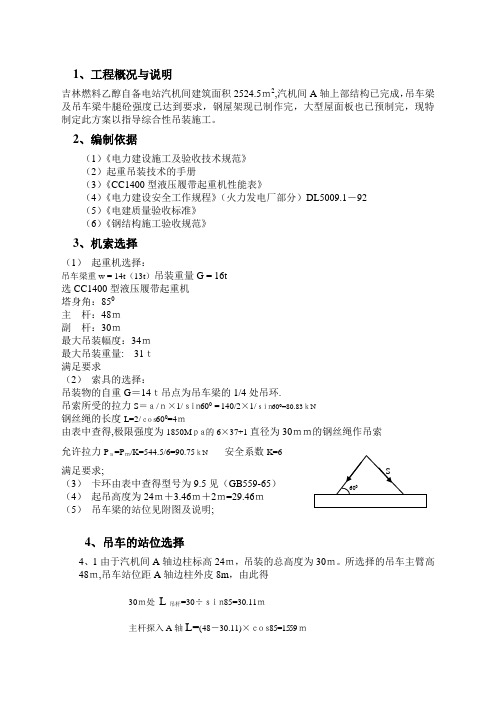
1、工程概况与说明吉林燃料乙醇自备电站汽机间建筑面积2524.5m2,汽机间A轴上部结构已完成,吊车梁及吊车梁牛腿砼强度已达到要求,钢屋架现已制作完,大型屋面板也已预制完,现特制定此方案以指导综合性吊装施工。
2、编制依据(1)《电力建设施工及验收技术规范》(2)起重吊装技术的手册(3)《CC1400型液压履带起重机性能表》(4)《电力建设安全工作规程》(火力发电厂部分)DL5009.1-92(5)《电建质量验收标准》(6)《钢结构施工验收规范》3、机索选择(1)起重机选择:吊车梁重w = 14t(13t)吊装重量G = 16t选CC1400型液压履带起重机塔身角:850主杆:48m副杆:30m最大吊装幅度:34m最大吊装重量: 31t满足要求(2)索具的选择:吊装物的自重G=14t吊点为吊车梁的1/4处吊环.吊索所受的拉力S=a/n×1/sin600=140/2×1/sin600=80.83kN钢丝绳的长度L=2/cos600=4m由表中查得,极限强度为1850Mpa的6×37+1直径为30mm的钢丝绳作吊索允许拉力Pa=Pm/K=544.5/6=90.75kN 安全系数K=6 Array满足要求;(3)卡环由表中查得型号为9.5见(GB559-65)(4)起吊高度为24m+3.46m+2m=29.46m(5)吊车梁的站位见附图及说明;4、吊车的站位选择4、1由于汽机间A轴边柱标高24m,吊装的总高度为30m。
所选择的吊车主臂高48m,吊车站位距A轴边柱外皮8m,由此得30m处L吊杆=30÷sin85=30.11m主杆探入A轴L=(48-30.11)×cos85=1.559m附图:8000故主杆可以满足吊装要求。
4、2吊车副杆根据现有工况为杆长30m,最大工作半径34m可以满足吊装附图:4、3行走及站位的地面处理:以现有安装铺设吊车行走道路处向西新铺设55m长;200mm厚路基石以保证大型吊车安全行走。
中、重型厂房结构设计-吊车梁的设计
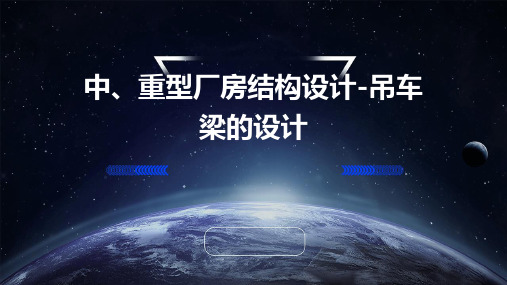
吊车梁的施工工艺流程
施工准备
根据设计图纸和施工要求,进行现场 勘查,确定吊车梁的安装位置和基础 结构。
01
02
基础制作
根据设计要求,进行吊车梁的基础制 作,包括混凝土浇筑、钢筋绑扎等。
03
吊车梁安装
将吊车梁按照设计要求进行安装,确 保其位置和标高符合设计要求。
质量检测
对吊车梁的安装质量进行检测,包括 其位置、标高、平整度等,确保符合 设计要求和相关规范。
吊车梁的功能
吊车梁的主要功能是支撑和固定吊车 的轨道,承受吊车的运行载荷,并将 载荷传递至厂房的承重结构上,确保 吊车的正常运行和使用安全。
吊车梁的类型与选择
吊车梁的类型
根据制作材料的不同,吊车梁可分为钢吊车梁、钢筋混凝土吊车梁等。根据使用场合和承载能力的不同,又可分 为轻型、中型和重型吊车梁。
吊车梁的选择
选择何种类型的吊车梁应根据厂房的跨度、高度、使用需求以及经济性等因素综合考虑。例如,钢吊车梁具有自 重轻、承载能力强、安装方便等优点,适用于大跨度、高净空的厂房;钢筋混凝土吊车梁则具有承载能力较高、 耐久性好、造价较低等优点,适用于中等跨度和高度的厂房。
吊车梁设计的原则与要求
吊车梁设计的原则
吊车梁设计应遵循安全可靠、经济合理、技术先进的原则, 确保吊车梁能够承受各种可能的载荷组合,满足厂房的正常 使用和安全性能要求。
04
吊车梁的抗震设计
吊车梁的抗震设防目标
防止吊车梁在地震中发生严重破坏,确保厂房的正常使用和 安全。
保证吊车在地震中的安全运行,防止因吊车梁破坏而引起的 设备损坏或人员伤亡。
吊车梁的抗震措施
选择合适的材料
采用高强度钢材,提高吊车梁的承载能力和抗变 形能力。
吊车梁安装施工方案
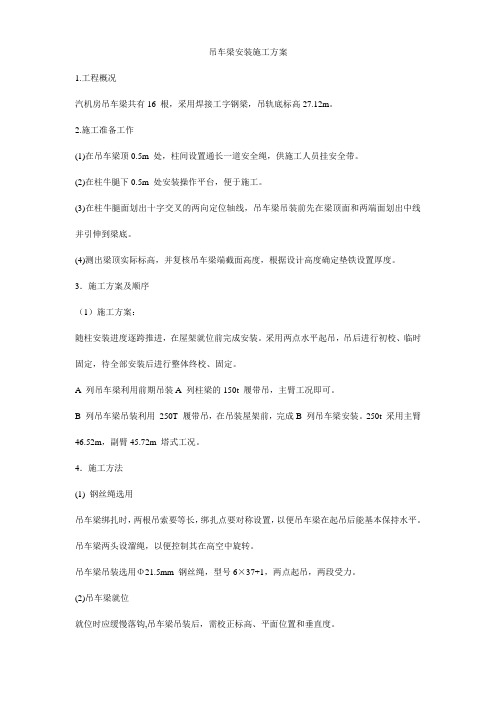
吊车梁安装施工方案1.工程概况汽机房吊车梁共有16 根,采用焊接工字钢梁,吊轨底标高27.12m。
2.施工准备工作(1)在吊车梁顶0.5m 处,柱间设置通长一道安全绳,供施工人员挂安全带。
(2)在柱牛腿下0.5m 处安装操作平台,便于施工。
(3)在柱牛腿面划出十字交叉的两向定位轴线,吊车梁吊装前先在梁顶面和两端面划出中线并引伸到梁底。
(4)测出梁顶实际标高,并复核吊车梁端截面高度,根据设计高度确定垫铁设置厚度。
3.施工方案及顺序(1)施工方案:随柱安装进度逐跨推进,在屋架就位前完成安装。
采用两点水平起吊,吊后进行初校、临时固定,待全部安装后进行整体终校、固定。
A 列吊车梁利用前期吊装A 列柱梁的150t 履带吊,主臂工况即可。
B 列吊车梁吊装利用250T 履带吊,在吊装屋架前,完成B 列吊车梁安装。
250t 采用主臂46.52m,副臂45.72m 塔式工况。
4.施工方法(1) 钢丝绳选用吊车梁绑扎时,两根吊索要等长,绑扎点要对称设置,以便吊车梁在起吊后能基本保持水平。
吊车梁两头设溜绳,以便控制其在高空中旋转。
吊车梁吊装选用Φ21.5mm 钢丝绳,型号6×37+1,两点起吊,两段受力。
(2)吊车梁就位就位时应缓慢落钩,吊车梁吊装后,需校正标高、平面位置和垂直度。
根据预测的牛腿顶标高和吊车梁自身尺寸,通过在牛腿面上加放钢垫片来调整。
根据牛腿面上的十字中心线和吊车梁上刻划的梁中心线,利用撬杠等工具,在吊车配合下,使两线对正,并临时固定(分别于梁中及梁端共三处用双股10#钢丝绳与A 列钢梁拉结)。
待吊车梁吊装完毕后,沿轴线绷通长钢丝,用线坠检查吊车梁顶面的轴线,误差较大的可利用倒链、千斤顶以钢柱为受力点进行调整。
当一列吊车梁调整完毕后,以该列为基准,用钢卷尺和弹簧秤在每根吊车梁两端及中间进行测量,利用倒链、千斤顶进行调整。
6.1.2.5 汽机房屋面钢梁安装1.屋架吊装(1)工程概况#1 汽机房共有9 榀轻型钢梁,结构安装顶标高33.0m。
钢吊车梁制作安装施工方案

第一章概况┈┈┈┈┈┈┈┈┈┈┈┈2 第一节编制说明┈┈┈┈┈┈┈┈┈┈┈┈2 第二节工程概况┈┈┈┈┈┈┈┈┈┈┈┈3 第二章施工准备┈┈┈┈┈┈┈┈┈┈┈┈3 第一节组织机构┈┈┈┈┈┈┈┈┈┈┈┈3 第二节主要机械及设备用量及计划┈┈┈┈┈┈┈4 第三章施工部署┈┈┈┈┈┈┈┈┈┈┈┈5 第一节工程施工目标┈┈┈┈┈┈┈┈┈┈┈┈5 第四章主要施工方法┈┈┈┈┈┈┈┈┈┈┈┈6 第一节焊接H型钢的制作┈┈┈┈┈┈┈┈┈┈┈┈6 第二节焊接过程及质量控制┈┈┈┈┈┈┈┈┈┈┈┈9 第三节钢结构构件安装工艺┈┈┈┈┈┈┈┈┈┈┈┈11 第四节吊车梁安装起重设备选择┈┈┈┈┈┈┈┈┈┈12 第五节吊车梁安装┈┈┈┈┈┈┈┈┈┈┈┈┈┈┈┈12 第六节安装检查验收┈┈┈┈┈┈┈┈┈┈┈┈┈┈┈14 第五章质量保证措施┈┈┈┈┈┈┈┈┈┈┈┈15 第一节质量管理┈┈┈┈┈┈┈┈┈┈┈┈15 第二节质量标准┈┈┈┈┈┈┈┈┈┈┈┈16 第六章安全及文明施工保证措施┈┈┈┈┈┈┈┈┈┈┈16 第一节钢结构施工安全要求┈┈┈┈┈┈┈┈┈┈┈17第二节施工现场防火措施┈┈┈┈┈┈┈┈┈┈┈┈17 第三节文明施工保证措施┈┈┈┈┈┈┈┈┈┈┈┈18第一章概况第一节编制说明本施工方案是根据柳州市东城投资开发有限公司柳东新区标准厂房C区I标段-5#楼/6#楼、施工图纸及参照图集<<钢吊车梁>>(03SG520-1)79页来编制的。
方案中着重考虑钢梁制作、吊装、焊接、等各工序的施工方法以及质量、环境、安全等保证措施,同时考虑钢结构工程配合土建等相关专业施工,确保质量及工期。
1.1编制依据施工图纸、图集<<钢吊车梁>>(03SG520-1)1.2执行的规范、规程、标准:《碳素结构钢》GB/T 700—2006;《焊接H型钢》YB3301-2005;《六角头螺栓--C级》GB/T5780-2000;《六角螺母--C级》GB/T41-2000;《平垫圈 C级》GB/T95-2002;《非合金钢及细晶粒钢焊条》GB/T5117-2012;《焊接用钢丝》GB/T14957-1994;《埋弧焊用碳钢焊丝和焊剂》GB/T5293-1999《钢结构工程施工质量验收规范》GB50205-2001;《气焊、焊条电弧焊、气体保护焊和高能束焊的推荐坡口》GB985.1—2008;《埋弧焊的推荐坡口》GB985.2—2008;《钢结构用高强度大六角螺栓》GB/T1228-2006;《混凝土结构工程施工质量验收》GB50204-2002;第二节工程概况2.1 工程概况:本工程为柳州市东城投资开发有限公司柳东新区标准厂房C区一标段-5#/6#厂房,地上三层建筑总长126.00m,宽48m,建筑总高度为21.60m,采用框架结构,基础采用独立柱基础。
超大跨度吊车梁制作方案
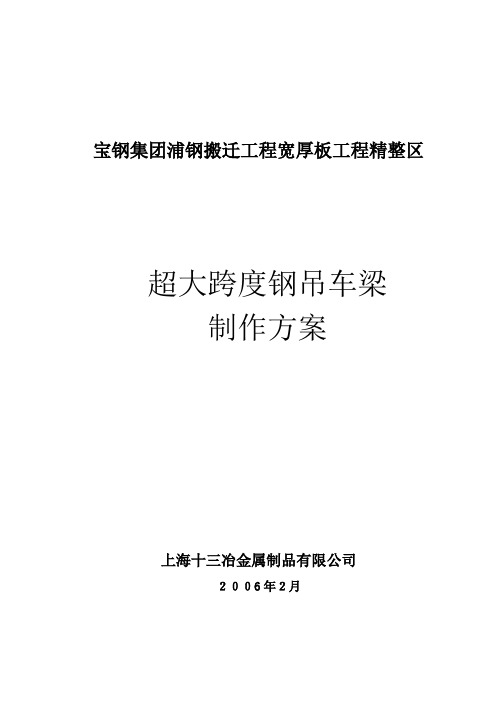
宝钢集团浦钢搬迁工程宽厚板工程精整区超大跨度钢吊车梁制作方案上海十三冶金属制品有限公司2006年2月目录1.总则 (1)2.工程概况及工程特点 (1)3.材料 (1)3.1钢材 (2)3.2焊接材料 (2)3.3涂装材料 (3)4.钢构件加工 (3)4.1制作机械设备 (3)4.2放样和号料 (3)4.3切割及刨平 (4)4.4矫正 (5)4.5接料及组装 (5)4.6焊接 (9)4.7制孔 (15)4.8抛丸、除锈和涂漆 (16)4.9构件标记 (17)4.10包装、发运 (17)4.11防护措施 (17)5.制作工艺流程 (17)6.质量保证措施 (17)7.安全技术措施 (18)附件一 (20)附件二 (21)1.总则1.1本工艺适用于宝钢集团浦钢搬迁工程宽厚板工程精整区钢结构的制作。
1.2主要引用标准及资料1.2.1本工程的钢结构施工图(中冶京诚工程技术有限公司)1.2.2低合金结构钢技术条件GB/T1591-941.2.3《钢结构设计规范》GB50017-20031.2.4《钢结构工程施工质量验收规范》GB50205-20011.2.5《建筑工程施工质量验收统一标准》GB50300-20011.2.6《建筑钢结构焊接技术规程》JGJ81-20021.3钢结构制作过程中,应严格遵守此工艺和我厂工程质量管理的规定,使本工程质量符合GB50205-2001合格标准。
并满足业主、项目部和监理单位对钢结构质量精品的要求。
1.4本工程特殊过程为一级焊缝和涂装工程。
1.5本工程结构安全等级为二级。
2.工程概况及工程特点2.1工程概况:2.1.1宝钢集团浦钢搬迁工程宽厚板工程精整区工程中,有6根超大型工字形实腹梁,其长、宽、高分别为57.5m×1.3m×6m,单件重约164t左右。
另有跨度43m、截面高度为4.5 m大梁6根,最重的构件约93t,也参照此方案施工。
该工程制作的整体思路:整体制作-分段焊接-最后拼成整体。
大跨梁施工方案范文

大跨梁施工方案范文一、项目概况本工程为大跨度梁的施工方案,梁长30米,跨度为25米。
梁体采用钢筋混凝土结构,梁面宽度为1.5米,高度为2.5米。
施工区域位于高速公路上,交通繁忙。
施工目标是确保施工安全,控制质量,保证进度。
二、施工准备1.做好施工前的准备工作,包括收集相关设计图纸、施工规范和标准、物资采购和人员组织等。
2.完成临时设施的搭建,包括施工场地的平整化、易懂标识的设置、安全防护设备的安装等。
三、施工流程1.基础工程a.按设计图纸和规范要求,清理基础区域,并进行标高定位。
b.搭建基础模板,确保模板材料无杂物,规格符合设计要求。
c.安装主筋和配筋,按要求进行连接和固定。
d.倒模施工,包括模板调整、定型、喷脱模剂等工作。
e.混凝土浇筑,包括材料配比、搅拌、运输、倒料、振捣等工作。
f.浇筑完成后,进行养护处理,包括湿养护、覆盖保温等。
2.梁体施工a.梁体模板搭建,按设计图纸和规范要求进行。
b.钢筋安装,包括主筋和配筋的布置和连接。
c.预埋件处理,包括设置方桩、定位块等。
d.安装模板防倾杆,确保定位准确。
e.浇筑混凝土,按要求进行振捣和浇注。
f.梁体养护,根据混凝土到达设计强度的时间进行养护处理。
3.梁浇筑a.设计施工方法和控制措施,确保施工安全。
b.梁浇筑前的准备工作,包括设备检查、混凝土浇注量和浇注工艺计划等。
c.设计支架和支柱,确保浇筑过程中的稳定性。
d.建造模板,确保模板的定位和水平度。
e.梁浇筑施工,包括混凝土的搅拌、运输、均匀浇筑、充实和振捣等。
f.根据混凝土到达设计强度的时间进行养护处理。
四、质量控制1.施工前,对材料进行质量检测,确保符合标准。
2.按要求进行混凝土的配合比和浇筑作业,保证混凝土的强度和均匀性。
3.对施工过程中的各个环节进行检查,确保施工质量符合要求。
4.梁浇筑完成后,进行质量验收和检测,并制作相关报告。
五、安全措施1.设立施工安全管理员,负责施工现场的安全管理工作。
吊车梁吊装方案

目录 (4)1.编制依据国家及部颁有关现行标准、规范、规定2002;GB50205-2001;图纸见汽机房吊车梁,卷册号37-FC14811S-T0310;2.工程概况及主要工程量工程概况±标高相当于绝对标高;2机吊车梁中心线距A轴为900mm,距B轴为1400mm,A、B排柱间距为30m,吊车梁中心线跨度为,柱间距为9m,共计18根吊车梁;吊装顺序为8a轴→17轴;主要工程量起重设备工况表D800-42平臂吊60M臂长4倍率吊车性能如下表吊钩及绳索按2T计QY50K-1型汽车吊性能表如下3.主要施工方法吊装作业前要在8a轴和17轴处汽机吊车梁外侧的连系梁上挂爬梯用于吊装作业人员上下;制作吊篮挂在吊车梁牛腿外侧连系梁上,用于吊装人员清理牛腿基面、就位吊车梁并进行焊接;在+处8a轴和17轴间A、B排外侧各拉一根安全绳用于吊装人员作业;对钢吊车梁进行测量放线,确定吊车梁的中心线;对钢吊车梁牛腿进行纵向、横向放线和标高的放线,可放在同一标高的柱子上;吊车梁及轨道吊装考虑选用D800-42T平臂吊及50t汽车吊进行吊装,D800-42t平臂吊负责吊装B排11轴到17轴吊车梁及轨道的吊装,50t汽车吊车责A排8b~17轴、B排8b~11轴吊车梁及轨道的吊装;汽机吊车梁的吊装:当钢吊车梁至设计位置离支座20cm时,用人力扶正,使梁中心线与支承面中心线或已安装相邻的中心线对准,并使两端搁置长度相等,然后缓慢落下,如有偏差,稍吊起用撬杠拨正,如支座不平,用斜铁垫平,当梁校正之后脱钩之前需先将吊车梁与柱连接板焊接完成并用8线将梁捆于柱上,以防倾倒;吊车梁就位后在汽机房钢屋架牛腿应焊出支架用来悬挂斤不落,吊车梁就位后用斤不落找正;吊车梁找正后,开始焊接钢梁固定件,固定件焊牢后开始铺钢轨及其它连接件;吊车梁与轨道安装时选用M20普通螺栓及三面直角焊缝,连接孔为;轨道联接连接时螺栓为M22;钢车档与吊车梁的连接孔为φ,螺栓为M16,L=90 mm;伸缩缝接头的边接孔为φ,螺栓为M22,L=160mm;其它未注明的螺栓为M20,孔径为φ;钢吊车梁、支座板、及钢车档焊缝见图纸标注,未注明贴角焊缝厚度为8mm,未注明长度的焊缝一律满焊;吊车梁轨道连接采用鱼尾板连接,螺栓孔采用M24磁座钻钻孔;4.质保措施材料的品种、规格、性能及质量符合设计要求和规范规定,对进入现场的材料应检查其材质单或合格证;施工用计量器具必须经计量检定、校准合格后方可使用;在吊车梁安装前,在柱子牛腿上弹出两个方向的中心线,在吊车梁安装、找正过程中使吊车梁中心线与柱子对齐,在牛腿附近弹出标高线作为控制吊车梁标高的依据,若牛腿标高偏低,则安装时垫入垫铁;若牛腿上表面与吊车梁底座间有缝隙,则用楔铁塞满;所有螺栓及螺母拧紧后,用电焊将丝扣点死,防止螺栓松动;构件安装完毕后,应将预留的未涂底漆部分或运输过程中碰坏的涂漆部分补刷底漆,最后再涂刷中间漆及面漆;油漆的涂装及颜色应符合设计要求;5.安全文明施工措施安全施工技术措施严格按电力建设安全工作规程上的规定进行施工,工器具严格执行其操作规程,遵守上级部门颁发的有关安全文件,施工人员经安全措施交底后方可施工;文明施工技术措施并设标识,注明名称、品种、规格等; 环保技术措施6.人力配置7.工器具及机械配置表42T平臂吊作业半径示意图。
大跨度吊车梁制作方案

大跨度吊车梁制作方案编制说明:本方案是宝钢宽厚板轧机车间超长跨度吊车梁制作方案,如此超大、超长、超重吊车梁在我国冶金建设史上是空前的,此梁的施工是该工程众多施工难题之首。
本方案是针对超长吊车梁的制作而编制的,是确保超长吊车梁合理科学,优质、安全、高效完成制作任务的重要技术文件。
1、概况及特点:1.1 概况:宝钢宽厚板轧机车间超长吊车梁,采用H型钢实腹梁,截面尺寸6m×1m×57.5m,材质Q345c,最厚板厚δ=50mm,单件重约130t,共有8根,总重量约1040t。
纵横双方均有加劲肋,主焊缝为一级熔透焊缝,梁与柱、梁与制动板均采用高强螺栓的连接形式,构件喷射除锈Sa2.5级。
1.2 工程特点:1.2.1 梁体超长、超重、超高拼装组对难度较大。
1.2.2 工艺复杂,厚板拼接、焊接、矫正难度大。
1.2.3 单件长,变形难以控制,梁体倒运和运输对制作厂区道路要求高。
1.2.4 单件重,翻转难,行车要有足够的起吊能力。
1.2.5 焊缝多且质量要求高,必须有正确的焊接工艺。
1.2.6 8根梁构造基本相同,可形成流水生产。
2、施工及验收规范:2.1(GB50205-2001)<<钢结构工程施工质量验收规范>>2.2(GB/T1591-94)<<低合金高强度结构钢>>2.3(YG9254-95)<<钢结构制作安装施工规程>>2.4(J GJ81-91)<<建筑钢结构焊接规程>>2.5(GB50224-95)<<建筑防腐蚀工程质量检验评定超标准>>3、施工方案:3.1 施工准备:利用富冶露天跨配置两台60t龙门吊车作为此吊车梁的加工场地,该宽28m,长120m,可以露天跨同时摆放4根吊车梁,详见制作场地平面图。
3.2 工艺流程:技术、材料准备→抛丸除锈→车间底漆→接板、下料→钻孔→组对→主缝焊接→矫正→二次组对→焊接、打磨→涂装→编号出厂。
大跨度梁施工方案
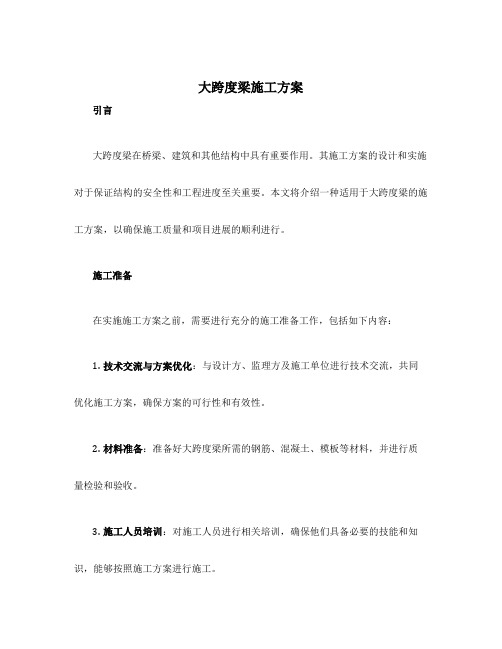
大跨度梁施工方案引言大跨度梁在桥梁、建筑和其他结构中具有重要作用。
其施工方案的设计和实施对于保证结构的安全性和工程进度至关重要。
本文将介绍一种适用于大跨度梁的施工方案,以确保施工质量和项目进展的顺利进行。
施工准备在实施施工方案之前,需要进行充分的施工准备工作,包括如下内容:1.技术交流与方案优化:与设计方、监理方及施工单位进行技术交流,共同优化施工方案,确保方案的可行性和有效性。
2.材料准备:准备好大跨度梁所需的钢筋、混凝土、模板等材料,并进行质量检验和验收。
3.施工人员培训:对施工人员进行相关培训,确保他们具备必要的技能和知识,能够按照施工方案进行施工。
4.施工设备准备:准备好大跨度梁施工所需的起重机械、模板支架等设备,并进行检修和调试。
5.施工现场准备:清理施工现场,确保施工场地安全整洁,为施工方案的实施提供良好的施工条件。
施工步骤大跨度梁的施工可分为以下步骤:1.梁箱制作:根据设计图纸,制作梁箱模板,并进行检查和调整,确保模板的尺寸和质量达到要求。
然后,在模板内布置预埋件和钢筋,最后浇筑混凝土,待混凝土养护完全后,拆除模板。
2.梁段架设:使用起重机械将制作好的梁段吊装到拟定位置,并采取临时支撑措施使其保持稳定。
调整梁段的位置和水平度,然后进行固定。
3.梁体拼接:根据施工图纸的要求,将各个梁段按照连接方式进行拼接。
拼接方式可以采用焊接、螺栓连接等方法,确保梁体的整体性和稳定性。
4.梁体加固:根据设计要求,在梁体的关键部位进行加固处理,如在梁底部加设加劲肋,提高梁体的承载能力和稳定性。
5.伸缩缝处理:根据需要,在梁体的伸缩缝处进行处理,以适应结构的变形和温差的影响。
常用的处理方式有橡胶板铺设、金属伸缩缝等。
6.梁体防护:为了保护梁体免受外界的侵蚀和损害,可以在梁体表面进行防护处理,常用的方式有喷涂防腐、涂抹防水等。
施工安全措施在大跨度梁的施工过程中,需要严格遵守相关安全规范,采取有效的安全措施以确保施工人员和施工设备的安全,包括:1.施工现场安全:设置必要的警示标志,随时清理施工现场,确保施工环境的安全整洁。
吊车梁设计【范本模板】

一、吊车梁所承受的荷载吊车在吊车梁上运动产生三个方向的动力荷载:竖向荷载、横向水平荷载和沿吊车梁纵向的水平荷载。
纵向水平荷载是指吊车刹车力,其沿轨道方向由吊车梁传给柱间支撑,计算吊车梁截面时不予考虑。
吊车梁的竖向荷载标准值应采用吊车最大轮压或最小轮压。
吊车沿轨道运行、起吊、卸载以及工件翻转时将引起吊车梁振动。
特别是当吊车越过轨道接头处的空隙时还将发生撞击。
因此在计算吊车梁及其连接强度时吊车竖向荷载应乘以动力系数.对悬挂吊车(包括电动葫芦)及工作级别A1~A5的软钩吊车,动力系数可取1。
05;对工作级别A6~A8的软钩吊车、硬钩吊车和其他特种吊车,动力系数可取为1。
1。
吊车的横向水平荷载由小车横行引起,其标准值应取横行小车重量与额定起重量之和的下列百分数,并乘以重力加速度:1)软钩吊车:当额定起重量不大10吨时,应取12%;当额定起重量为16~50吨时,应取10%;当额定起重量不小于75吨时,应取8%。
2)硬钩吊车:应取20%。
横向水平荷载应等分于桥架的两端,分别由轨道上的车轮平均传至轨道,其方向与轨道垂直,并考虑正反两个方向的刹车情况。
对于悬挂吊车的水平荷载应由支撑系统承受,可不计算.手动吊车及电动葫芦可不考虑水平荷载。
计算重级工作制吊车梁及其制动结构的强度、稳定性以及连接(吊车梁、制动结构、柱相互间的连接)的强度时,由于轨道不可能绝对平行、轨道磨损及大车运行时本身可能倾斜等原因,在轨道上产生卡轨力,因此钢结构设计规范规定应考虑吊车摆动引起的横向水平力,此水平力不与小车横行引起的水平荷载同时考虑。
二、吊车梁的形式吊车梁应该能够承受吊车在使用中产生的荷载。
竖向荷载在吊车梁垂直方向产生弯矩和剪力,水平荷载在吊车梁上翼缘平面产生水平方向的弯矩和剪力。
吊车的起重量和吊车梁的跨度决定了吊车梁的形式。
吊车梁一般设计成简支梁,设计成连续梁固然可节省材料,但连续梁对支座沉降比较敏感,因此对基础要求较高.吊车梁的常用截面形式,可采用工字钢、H 型钢、焊接工字钢、箱型梁及桁架做为吊车梁.桁架式吊车梁用钢量省,但制作费工,连接节点在动力荷载作用下易产生疲劳破坏,故一般用于跨度较小的轻中级工作制的吊车梁.一般跨度小起重量不大(跨度不超6米,起重量不超过30吨)的情况下,吊车梁可通过在翼缘上焊钢板、角钢、槽钢的办法抵横向水平荷载,对于焊接工字钢也可采用扩大上翼缘尺寸的方法加强其侧向刚度.对于跨度或起重量较大的吊车梁应设置制动结构,即制动梁或制动桁架;由制动结构将横向水平荷载传至柱,同时保证梁的整体稳定。
大跨度吊车梁设计
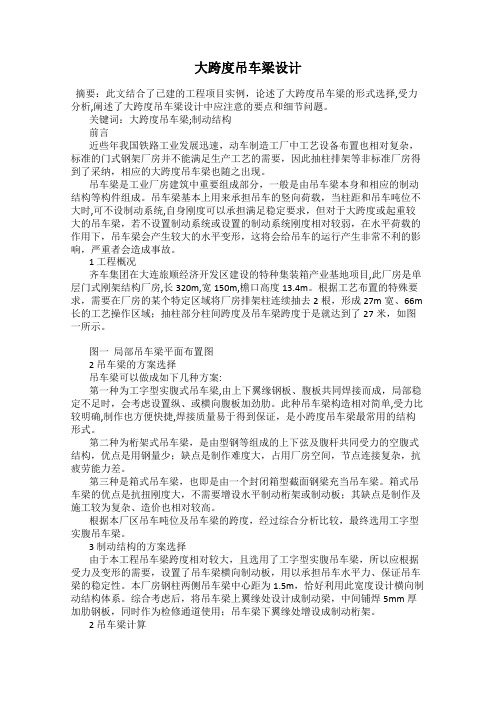
大跨度吊车梁设计摘要:此文结合了已建的工程项目实例,论述了大跨度吊车梁的形式选择,受力分析,阐述了大跨度吊车梁设计中应注意的要点和细节问题。
关键词:大跨度吊车梁;制动结构前言近些年我国铁路工业发展迅速,动车制造工厂中工艺设备布置也相对复杂,标准的门式钢架厂房并不能满足生产工艺的需要,因此抽柱排架等非标准厂房得到了采纳,相应的大跨度吊车梁也随之出现。
吊车梁是工业厂房建筑中重要组成部分,一般是由吊车梁本身和相应的制动结构等构件组成。
吊车梁基本上用来承担吊车的竖向荷载,当柱距和吊车吨位不大时,可不设制动系统,自身刚度可以承担满足稳定要求,但对于大跨度或起重较大的吊车梁,若不设置制动系统或设置的制动系统刚度相对较弱,在水平荷载的作用下,吊车梁会产生较大的水平变形,这将会给吊车的运行产生非常不利的影响,严重者会造成事故。
1 工程概况齐车集团在大连旅顺经济开发区建设的特种集装箱产业基地项目,此厂房是单层门式刚架结构厂房,长320m,宽150m,檐口高度13.4m。
根据工艺布置的特殊要求,需要在厂房的某个特定区域将厂房排架柱连续抽去2根,形成27m宽、66m 长的工艺操作区域;抽柱部分柱间跨度及吊车梁跨度于是就达到了27米,如图一所示。
图一局部吊车梁平面布置图2 吊车梁的方案选择吊车梁可以做成如下几种方案:第一种为工字型实腹式吊车梁,由上下翼缘钢板、腹板共同焊接而成,局部稳定不足时,会考虑设置纵、或横向腹板加劲肋。
此种吊车梁构造相对简单,受力比较明确,制作也方便快捷,焊接质量易于得到保证,是小跨度吊车梁最常用的结构形式。
第二种为桁架式吊车梁,是由型钢等组成的上下弦及腹杆共同受力的空腹式结构,优点是用钢量少;缺点是制作难度大,占用厂房空间,节点连接复杂,抗疲劳能力差。
第三种是箱式吊车梁,也即是由一个封闭箱型截面钢梁充当吊车梁。
箱式吊车梁的优点是抗扭刚度大,不需要增设水平制动桁架或制动板;其缺点是制作及施工较为复杂、造价也相对较高。
钢吊车梁的制作施工方案
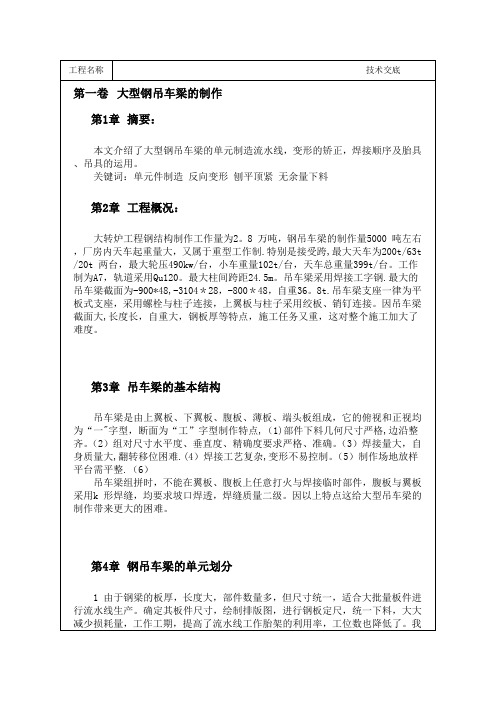
b. 反变形控制钢板组对时,在焊缝处反向垫高,反向变形控制。
腹板与上、下翼板采用坡口焊接,使用组对胎具如图1.胎具的角度可根据梁的高度而定,胎具上的腹板与腹板拼按的角度>90 度(具体角度根据实验数据与现场操作经验数据而定,如腹板28mm、翼板48mm 的天车梁,插入选用拼接角度为97 度,翼板与腹板焊缝采用埋弧自动焊,反面气刨清根自动焊接。
c. H 型钢及单元件的矫正因吊车梁自重大,截面大,采用两台天车进行起吊,采用如图2 机具,使施工工序减少,安全性系数高,施工简便,又便于H 型钢的翻身,因H 型钢截面大,通过天车吊住H 型钢、进行矫正机矫正.三角形火焰烘烤矫正,对于单元件的小部位矫正、钢板的侧弯矫正,利用热胀冷缩的原理,因钢板冷缩的变形量大于热涨的变形量,三角形加温点的分布多少应视弯曲变形的轻重而异,如图3:某吊车梁腹板厚28mm,长度25。
176m,切割下料后宽弯10mm,但温度一定要控制在650℃~900℃之间.如图3 编号1 加温在85 0°,2 加温在780°,3 加温在750°,4 加温在700°,5 加温在650°。
经过加温烘烤,自然冷却后宽弯曲值Δ=±1mm。
第5章钢吊车梁的组对与焊接:1 H 型钢如图1 进行组对,矫正后在平台上进行筋板与端板的组对,操作平台要求水平度精确,严格掌握焊接顺序是吊车梁变形控制的关键,整个吊车梁的焊接顺序是:端头重点段焊——筋板与上、下翼板、腹板的角焊。
2 吊车梁的起拱L≤18m,吊车梁不要求具体起拱数值,但制作时应采用合适的焊接顺序,使吊车梁产生向上的上拱趋势。
因≤18m 吊车梁腹板与上翼缘采用K 型焊缝,腹板与下翼缘采用角焊缝,因此,先焊腹板与上翼缘焊缝,再焊下翼缘与腹板的角焊,自然起拱。
L>18m 的吊车梁采用1/1000 跨度起拱,在自动切割下料时,按计算得的起拱数值划线切割,焊接顺序与L≤18m 以下的吊车梁一样。
10t吊车梁的设计参数
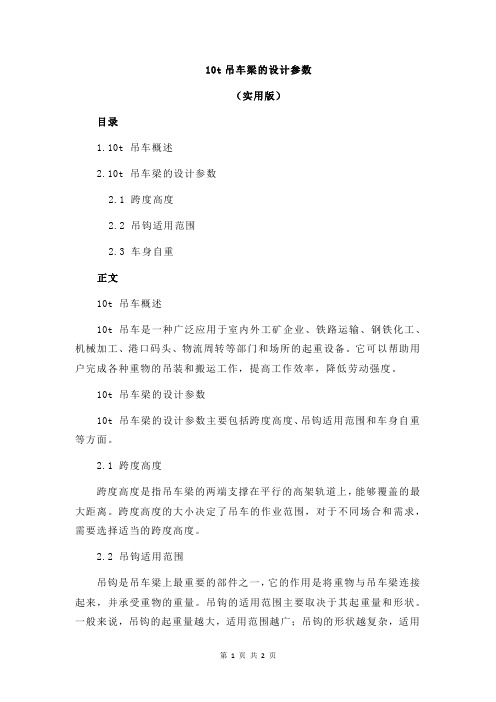
10t吊车梁的设计参数
(实用版)
目录
1.10t 吊车概述
2.10t 吊车梁的设计参数
2.1 跨度高度
2.2 吊钩适用范围
2.3 车身自重
正文
10t 吊车概述
10t 吊车是一种广泛应用于室内外工矿企业、铁路运输、钢铁化工、机械加工、港口码头、物流周转等部门和场所的起重设备。
它可以帮助用户完成各种重物的吊装和搬运工作,提高工作效率,降低劳动强度。
10t 吊车梁的设计参数
10t 吊车梁的设计参数主要包括跨度高度、吊钩适用范围和车身自重等方面。
2.1 跨度高度
跨度高度是指吊车梁的两端支撑在平行的高架轨道上,能够覆盖的最大距离。
跨度高度的大小决定了吊车的作业范围,对于不同场合和需求,需要选择适当的跨度高度。
2.2 吊钩适用范围
吊钩是吊车梁上最重要的部件之一,它的作用是将重物与吊车梁连接起来,并承受重物的重量。
吊钩的适用范围主要取决于其起重量和形状。
一般来说,吊钩的起重量越大,适用范围越广;吊钩的形状越复杂,适用
范围也越广。
2.3 车身自重
车身自重是指吊车本身的重量。
车身自重的大小会影响吊车的稳定性和运输成本。
一般来说,车身自重越轻,吊车的稳定性越好,但运输成本也会相应增加;反之,车身自重越重,吊车的稳定性越差,但运输成本会相应减少。
- 1、下载文档前请自行甄别文档内容的完整性,平台不提供额外的编辑、内容补充、找答案等附加服务。
- 2、"仅部分预览"的文档,不可在线预览部分如存在完整性等问题,可反馈申请退款(可完整预览的文档不适用该条件!)。
- 3、如文档侵犯您的权益,请联系客服反馈,我们会尽快为您处理(人工客服工作时间:9:00-18:30)。
大跨度吊车梁制作方案编制说明:本方案是宝钢宽厚板轧机车间超长跨度吊车梁制作方案,如此超大、超长、超重吊车梁在我国冶金建设史上是空前的,此梁的施工是该工程众多施工难题之首。
本方案是针对超长吊车梁的制作而编制的,是确保超长吊车梁合理科学,优质、安全、高效完成制作任务的重要技术文件。
1、概况及特点:1.1 概况:宝钢宽厚板轧机车间超长吊车梁,采用H型钢实腹梁,截面尺寸6m×1m×57.5m,材质Q345c,最厚板厚δ=50mm,单件重约130t,共有8根,总重量约1040t。
纵横双方均有加劲肋,主焊缝为一级熔透焊缝,梁与柱、梁与制动板均采用高强螺栓的连接形式,构件喷射除锈Sa2.5级。
1.2 工程特点:1.2.1 梁体超长、超重、超高拼装组对难度较大。
1.2.2 工艺复杂,厚板拼接、焊接、矫正难度大。
1.2.3 单件长,变形难以控制,梁体倒运和运输对制作厂区道路要求高。
1.2.4 单件重,翻转难,行车要有足够的起吊能力。
1.2.5 焊缝多且质量要求高,必须有正确的焊接工艺。
1.2.6 8根梁构造基本相同,可形成流水生产。
2、施工及验收规范:2.1(GB50205-2001)<<钢结构工程施工质量验收规范>>2.2(GB/T1591-94)<<低合金高强度结构钢>>2.3(YG9254-95)<<钢结构制作安装施工规程>>2.4(J GJ81-91)<<建筑钢结构焊接规程>>2.5(GB50224-95)<<建筑防腐蚀工程质量检验评定超标准>>3、施工方案:3.1 施工准备:利用富冶露天跨配置两台60t龙门吊车作为此吊车梁的加工场地,该宽28m,长120m,可以露天跨同时摆放4根吊车梁,详见制作场地平面图。
3.2 工艺流程:技术、材料准备→抛丸除锈→车间底漆→接板、下料→钻孔→组对→主缝焊接→矫正→二次组对→焊接、打磨→涂装→编号出厂。
3.3 排版下料:吊车梁拼接焊缝应避开跨中1/3区域范围,且上下翼板与腹板的拼接焊缝必须错开200mm以上,在满足此两项要求的前提下进行排版,并对原材料定尺。
钢材进厂后检查表面平直度并对超差部分进行矫正,保证钢钢材表面平直度符合规范要求。
因此梁成形后移动难度大,拟采用原材料抛丸的方法,抛丸使用的磨料为铁丸,铁丸直径为 1.6~0.63毫米,压缩空气压力为0.5~0.6MP a。
处理后的钢材表面无可见的油脂和污垢,氧化皮、锈和油漆涂层等附着物,任何残留的痕迹应仅是点状或条状的轻微色斑,达到质量等级Sa2.5级的要求。
号料时依据工艺要求预留焊接收缩余量及切割、刨边和铣平等的加工余量一般以50mm为宜。
焊接收缩值为0.8mm/m。
切割截面与钢材表面不垂直度不应大于钢材厚度的10%,且不得大于2.0mm。
刨边的零件,其刨边线与号料线的允许偏差为±1.0mm;铣平表面的粗糙度不得大于0.03mm。
零件的切割线与号料线的允许偏差应符合下列规定:3.4 组装,3.4.1 吊车梁组装采用平躺法。
顺序:将腹板放在专用胎架上定位→先焊接纵缝、后焊接横缝→翼缘板分别立于腹板两侧→用契打底→埋弧焊接(说明:点焊块调整好组对间隙→点焊→CO210/500)。
3.4.2 吊车梁上下翼缘板、腹板上均不得焊接本施工图以外的任何零配件,在制作过程中亦不得焊接临时固定件等,亦不得随意在主材上用电焊引弧或打火。
3.4.3 吊车梁横向加劲肋的上端应与上翼缘刨平项紧后焊接,必须保证支座加劲板与腹板的垂直度以及支座加劲板下端刨平的水平度3.4.4 钢吊车梁支座加劲肋的下端应刨平,在与梁焊接时,必须保证支座加劲肋与腹板的垂直度和支座加劲肋下端刨平的水平度。
3.4.5 组装工序基本结束后检查所有点焊部位,发现有裂纹等必须及时补修。
3.5 焊接,3.5.1 焊工必须持证上岗。
焊接设备必须有参数稳定、调节灵活、安全可靠的性能来满足焊接要求。
并要求编制切实可行的焊接工艺。
3.5.2 吊车梁对接焊缝、腹板与上翼缘板T型连接焊缝、腹板与下翼缘T型连接每端部不小于梁跨度的1/8焊缝长度处焊接质量要求均为I级。
3.5.3 所有焊接材料必须有相应的质量保证书,焊缝的强度屈服点、冲击韧性等指标不低于母材。
不符合设计要求及焊接工艺的焊接材料严禁使用。
焊材的选用:焊条、焊剂烘干温度:严剂。
3.5.4 焊接工程量统计表(按照排版图统计)33.5.5.1 钢板对接采用小车直流埋弧焊机(DZ1250)8台。
气体保护焊16台(打底),小车直流埋3.5.5.2 主焊缝采用CO2弧焊机16台。
气体保护焊18台;交流电弧焊机3.5.5.3 筋板焊接采用CO228台。
3.5.5.4 部分要求焊透的角焊缝采用硅整流直流弧焊机12台。
3.5.6 焊接方法3.5.6.1 钢板对接:采用埋弧自动焊。
a)采用X形70度坡口、无钝边,组对间隙2mm。
b)在焊缝两侧加(100×100mm)工件厚度的引弧板和熄弧板,坡口形式与工件相同。
3.5.6.2 腹板与翼缘板角焊缝的焊接:采用埋弧自动焊。
a)采用双边600坡口。
b)在焊缝两侧加(100×100mm)工件厚度的引弧板和熄弧板,坡口形式与工件相同。
3.5.6.3 筋板与翼缘板、腹板的焊接a)采用CO2气体保护焊,焊丝为H08Mn2si,ф1.2mm。
b)焊缝必须封口。
3.5.7 焊接顺序3.5.7.1 吊车梁主焊缝的焊接先焊接下翼缘与腹板的脚缝。
3.5.7.2 长度方向筋板的焊接顺序:从中间向两侧间断跳焊。
3.5.7.3 详见焊接顺序附图。
3.5.8 焊接过程中应注意如下问题:3.5.8.1 焊接的电流不宜过大、电压需稳定,并要求焊工选用的电流、速度、手法基本相同,一经施焊必须连续焊完同一部位。
焊缝端头应进行包角焊。
3.5.8.2 焊接过程中必须严格执行焊接工艺评定所确定的工艺参数。
3.5.8.3 点焊高度,不宜超过设计焊缝高度的1/2;定位焊不得有裂缝、气孔、夹渣、焊瘤等缺陷,否则应处理改正。
3.5.8.4 严禁在焊缝区以外的母材上打火引弧。
在坡口内起弧的局部面积应熔焊一次,不得留下弧坑。
低合金结构钢在同一处的返修不得超过两次。
3.5.8.5 因降雨或雪使相对湿度>80%时,焊接部分应进行加热、去潮措施。
3.5.8.6 气温在00C以下,距离焊缝100mm以内的母材部分加气体保护焊应进行热至360C以上。
环境风速>2米/秒时,采用CO2挡风措施。
3.6 涂装3.6.1 原材料抛丸预处理后,涂刷车间涂装底漆一道,待整个构件制作完后,按设计要求涂刷油漆,涂料必须附有产品质量保证书。
3.6.2 刷油4小时内严防淋雨,每道涂层测定漆膜厚度要达到两个90%。
3.6.3 连接板摩擦面抗滑移系数≥0.55,摩擦面严禁油污且不得涂漆,并进行贴纸保护。
3.6.4 涂装方法主要采用高压无气喷涂,不便于采用高压无气喷涂的部位采用手刷、滚刷等方法结合。
作业前要了解当天和第二天乃至其后一周雨日、风力等情况。
3.6.5 涂装场地环境温度,相对湿度必须符合涂料产品说明书的要求和其他相关规定,构件表面有结露时不得涂装。
涂膜干燥前应防止雨水、灰尘、垃圾等污染。
涂装应均匀,无明显起皱、流挂,附着性良好。
3.7 构件质量控制标准3.3.3.8装车运输构件检查符合要求,涂层干燥后,配合装车将吊车梁运至安装现场,装车必须保证构件不变形、不损坏、不散失。
拟用两台龙门吊车装车,将吊车梁抬起后将运输汽车倒进加工场,调整好车位将吊车梁缓缓落下。
当汽车承受吊车梁80~90%重量后停止下落,此时开始加固、封车,加固封车必须确保汽车行走安全。
4、技术措施:4.1材料定尺由于此吊车梁跨度大,普通规格钢板根本无法满足拼接焊缝避开跨中1/3的要求,因此必须先排版确定材料尺寸后,对有些材料要作为特供材料直接厂家订货。
使主材在满足拼接焊缝避开跨中1/3要求的同时将材料损耗降至最低。
4.2材料抛丸该吊车梁成型后单件超重,而且超长,构件倒运、翻转难度均很大,且抛丸车间起吊能力有限。
因此拟采用改变原传统成品抛丸除锈的方式为原材料抛丸除锈,原材料抛丸处理合格后涂刷底漆一道。
在构件组装过程中,钢材表面产生的局部浮锈,采用机械除锈的方式进行处理。
4.3焊缝排版初步统计此吊车梁有焊缝3800多米,且焊肉高,大部分焊缝均不能一次焊接成型,如果焊缝集中势必造成焊接应力集中。
因此在材料排版的同时要考虑拼接焊缝和加劲板焊缝尽量分散,避免造成局部应力集中。
4.4设置胎具组装吊车梁前预先制作组装胎具,胎具的宽度大于H型钢梁的宽度并且具有一定刚度,具备吊车梁最大静荷载的抗压、抗弯而不产生较大变形。
组装胎具应根据吊车梁预起拱数值设置,并用水平仪调节标高。
每根吊车梁制作胎架宽度7米,长度为57.5米,具体组装胎架形式见附图。
4.5吊具设计大型构件在施工中为加快施工进度和确保施工安全,通常加焊专用吊点。
此吊车梁属特大型构件,除专安装专用吊点外还须借助特设专用吊具来完成制作任务。
专用吊具详见附图。
4.6支顶装置吊车梁H型钢焊接时,为保证角焊缝450角均匀分布,焊体角焊缝需按450角摆放。
因为H型钢截面高,且无加劲板,传统的两点支撑方法必然导致H型钢腹板产生较大变形,因此施焊前必须对H型钢焊体的腹板加以支撑,保证焊体在无任何变形的情况下进行焊接,支顶方式详见附图。
4.7加固装置焊接过程中,需将焊体翻转后对另一焊缝施焊,H型钢此时尚未成型,且其本身超长、超高,H型钢不能承受其翻转时产生的冲击力。
因此焊体翻转前必须对其进行加固,加固装置每间距3600mm 设置一套,并要求此加固装置拆装方便、可重复利用,焊体翻转后能及时拆除,不影响焊机正常作业。
固装置详见附图。
5、质量保证措施:5.1建立质量保证体系建立质量体系,成立项目部,责任落实到每个管理人员,保证每一个施工环节都有专人负责。
实施质量三级管理,一级专检的管理制度,实施全过程质量控制,设置停点检查。
严格控制质量通病,以预防为主。
严格执行本公司管理科学、技术先进、施工精心、产品优良、顾客满意的质量方针。
确保实现本公司分项工程合格率100%,分项工程优良率80%以上,主体工程、关健部位均符合优良等级的质量目标。
质量保证资料真实、完整、规范、及时、符合规定。
5.2原材料质量控制措施牢固树立“质量第一”的思想,严把质量关。
几在本工程上使用的主材、辅材必须按规范要求进行检查验收,要求抽样复检的必须抽样送检。
经检查验收不符合要求的材料严禁使用。
5.3组装质量控制措施材料下料时必须按设计要求起拱,组装前检查胎架起拱度,组装过程中弹线辅助控制起拱度,确保吊车梁成型起拱度符合设计要求。