撞击流气化炉内颗粒停留时间分布的随机模拟
运用马尔科夫链模拟气化炉停留时间分布
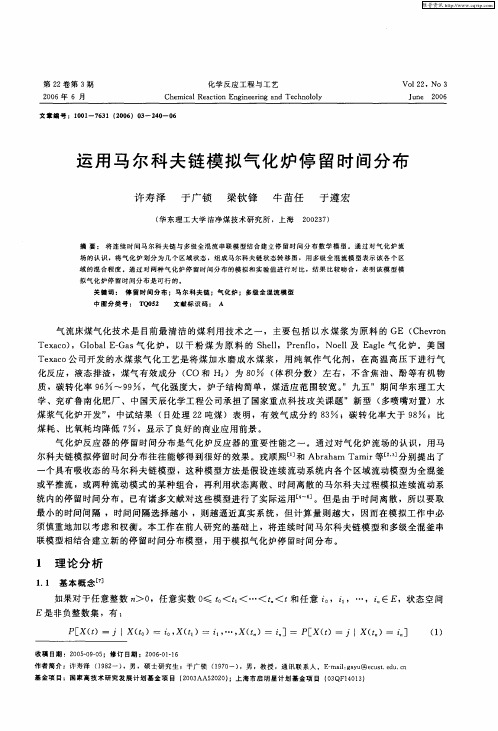
摘 要 : 将 连 续 时 间 马 尔 科 夫 链 与 多 级全 混 流 串联 模 型 结 合 建 立 停 留时 间分 布 数 学 模 型 。通 过 对 气 化 炉 流
场 的 认 识 , 将 气化 炉 划分 为 几 个 区域 状 态 ,组 成 马 尔科 夫 链 状 态 转 移 图 ,用 多 级 全 混 流 模 型 表 示 该 各 个 区 域 的混 合 程 度 。通 过 对 两种 气 化 炉 停 留时 间 分 布 的模 拟 和实 验 值 进 行 对 比 ,结 果 比 较 吻合 ,表 明 该 模 型 模 拟 气化 炉停 留 时 间分 布是 可 行 的 。
气化 炉反应 器 的停 留时 间分布 是气 化炉反 应器 的重 要性能 之 一。通 过对 气化 炉 流场 的认识 ,用 马
尔科夫 链模 拟停 留时 间分 布往 往能够 得 到很好 的效果 。戎顺 熙[ 和 Ab a a T mi等 [ ] 1 3 rh m a r 2 分别 提 出 了 。
一
T xc) e a o ,Glb l — a o a E G s气 化 炉 ,以 干 粉 煤 为 原 料 的 S el rnl ,No l 及 E ge气 化 炉。美 国 hl ,P e f o el al
T x c 公 司开发 的水 煤 浆气 化工 艺是 将煤 加 水磨 成 水煤 浆 ,用 纯 氧作 气 化 剂 ,在 高 温高 压 下进 行 气 eao
收稿 日期 :2 0—90 ;修 订 日期 :2 0—11 0 50 —5 0 60 —6 作 者 简 介 :许 寿 泽 (9 2 ) 1 8 - ,男 ,硕 士 研 究 生 ;于 广 锁 ( 90 ) 1 7 - ,男 .教 授 ,通 讯 联 系 人 。 Ema :su eute u c — i gy @ cs.d .n l 基 金项 目 :国 家 高 技 术 研 究 发 展 计 划 基 金 项 目 (0 3 2 0 AA5 0 0 ;上 海 市 启 明 星 计 划 基 金 项 目 (3 1 O ) 22) O QF 4 l 3
撞击流气固两相流动中曳力模型的分析
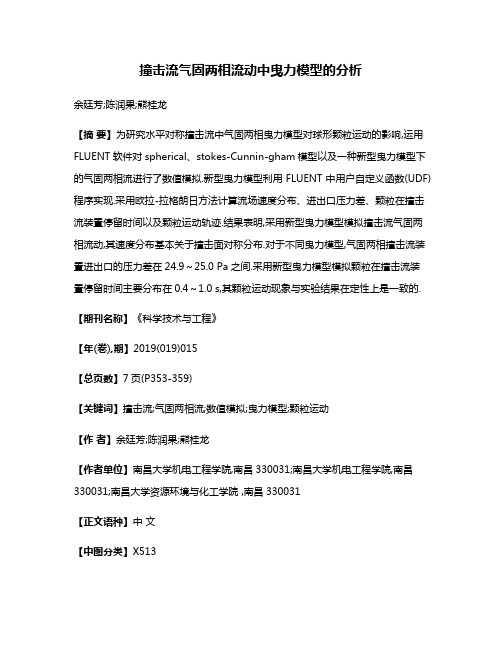
撞击流气固两相流动中曳力模型的分析余廷芳;陈润果;熊桂龙【摘要】为研究水平对称撞击流中气固两相曳力模型对球形颗粒运动的影响,运用FLUENT软件对spherical、stokes-Cunnin-gham模型以及一种新型曳力模型下的气固两相流进行了数值模拟.新型曳力模型利用FLUENT中用户自定义函数(UDF)程序实现.采用欧拉-拉格朗日方法计算流场速度分布、进出口压力差、颗粒在撞击流装置停留时间以及颗粒运动轨迹.结果表明,采用新型曳力模型模拟撞击流气固两相流动,其速度分布基本关于撞击面对称分布.对于不同曳力模型,气固两相撞击流装置进出口的压力差在24.9~25.0 Pa之间.采用新型曳力模型模拟颗粒在撞击流装置停留时间主要分布在0.4~1.0 s,其颗粒运动现象与实验结果在定性上是一致的.【期刊名称】《科学技术与工程》【年(卷),期】2019(019)015【总页数】7页(P353-359)【关键词】撞击流;气固两相流;数值模拟;曳力模型;颗粒运动【作者】余廷芳;陈润果;熊桂龙【作者单位】南昌大学机电工程学院,南昌330031;南昌大学机电工程学院,南昌330031;南昌大学资源环境与化工学院 ,南昌330031【正文语种】中文【中图分类】X513燃煤电厂大多采用了较为先进的除尘设备和湿法烟气脱硫设施,这些措施能够有效除去燃煤电厂烟气中的粗颗粒,但对细颗粒的脱除效率相对较低[1]。
因此,针对常规除尘技术难以有效脱除的细颗粒物,目前中外正在研究开发的控制技术主要有两种[2]:①团聚(凝并)促进技术:在常规除尘设备前加装处理设备,利用物理或化学作用使颗粒长大以便脱除;从原理上讲,应用外加声场[3]、磁场[4],光辐射[5]、电场[6]、吸附剂[7]、湍流[8]和蒸汽相变[9]对促进微粒长大均有一定作用。
②复合式除尘器:将不同的除尘机理相结合,使之共同作用以提高对细颗粒的脱除效果。
20世纪60年代初Elperin[10]提出撞击流理论(impinging tream)并进行相关研究,直到1975年俄罗斯学者Lainer开展了将撞击流技术应用于除尘领域的研究。
磁撞击流反应器内可磁化固体颗粒的磁力计算
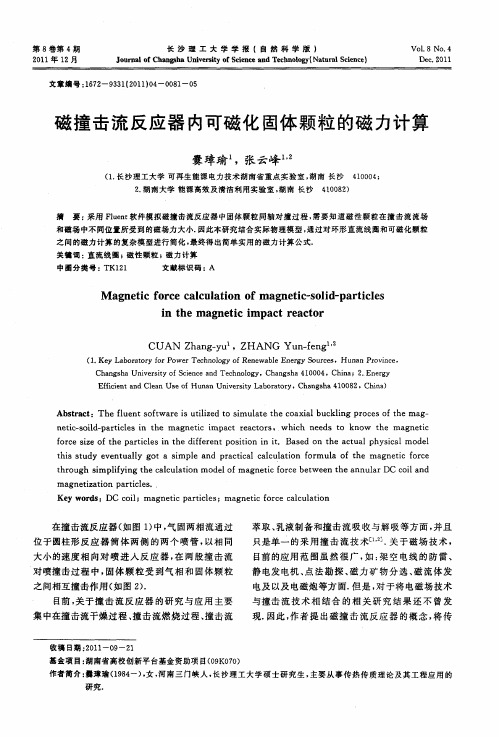
目前 的应 用 范 围 虽 然 很 广 , : 空 电线 的 防雷 、 如 架
静 电发 电机 、 法 勘 探 、 力 矿 物 分 选 、 流 体 发 点 磁 磁 电及 以及 电磁炮 等方 面 . 是 , 于将 电磁 场技 术 但 对 与撞击 流 技 术 相 结 合 的相 关 研 究 结 果 还 不 曾 发
对 喷撞击 过 程 中 , 固体 颗 粒 受 到 气 相 和 固体 颗 粒
之 间相互撞 击作 用 ( 图 2 . 如 )
目前 , 于撞 击 流 反 应 器 的 研 究 与 应 用 主 要 关
集 中在撞击 流干 燥过 程 、 击 流燃 烧磁 撞 击 流 反应 器 的概 念 , 传 将
F g Ma n t n u t n p o u e i.4 g ei id ci r d cd c o
b o la o n y Dc c i tp i t P
根据 毕奥 一 萨法尔 定律 可 知 , 段 电流 元 一 在 点 P 所产 生 的磁感应 强度 可 表示 为 : ‘
8 2
长 沙 理 工 大 学 学 报 (自 然 科 学 版 )
21 年 l 01 2月
统 的撞 击流 技术 与磁 场技 术 相 结合 , 即在 传 统 撞
击 流反 应器 外 缠 绕 通 有 直 流 电 的 线 圈 , 而 在 撞 从 击 流反 应器 周 围 产 生 磁 场 , 以达 到 强 化 撞 击 流 反 应 的作 用 . 型 中撞 击 流 反 应 器 外 加 磁 场 的分 布 模
直 流线 圈 磁 撞击 流反应 器 喷管
圈 4
正 漉 线 圈在 P 点 严 生 的磁 感 应 强厦
图 3 撞 击 流反 应 器 外部 磁 场 分 布 图
气流床气化炉内颗粒停留时间分布

离开床层。典型的气流床气化技术有Texaco水煤 浆气化技术、Shell粉煤气化技术和华东理工大学 开发的多喷嘴对置式水煤浆气化技术。
目前对气固两相流停留时间的研究主要集中于 循环流化床和固定床内颗粒停留时间分布。如 Harris等口11采用磷光示踪法系统研究了循环流化 床内颗粒停留时间分布,Barysheva等¨o采用光学
化学示踪法口¨、放射物质示踪法[1 21、颗粒提取 法[1 3|、荧光法[141和着色示踪法[151等。本实验采用 化学示踪法对气化炉内颗粒停留时间进行研究。
颗粒停留时间测量的准确性主要受示踪剂种 类、示踪剂加入方式和数据采集三方面的影响。本 实验使用的示踪剂是经饱和氯化钾溶液充分浸泡 (经过滤和干燥处理)的玻璃微珠颗粒,因此示踪 剂和实验颗粒具有相同的物理性质;采用精密的电
万方数据
‘56·
化
工
54 ·
·
化
工
学
报
第59卷
法研究了固定床内颗粒运动轨迹和逗留时间。对气 流床内颗粒停留时间分布的研究开展得很少,目前 的研究主要集中于气相系统,如于遵宏等睁63研究 了Texaco气化炉内气相停留时间分布,赵铁均‘7] 采用氢气脉冲法研究了多喷嘴气化炉内气体停留时 间分布,许寿泽等口。91采用马尔可夫链模拟了多喷 嘴对置式气化炉中气体停留时间分布。由于炉内流 体属气固多相流体系,气相的停留时问分布和混合 行为不能反映颗粒在气化炉内的停留时间分布及其 混合行为。而在工业运用中,煤粉颗粒的停留时间 对碳转化率和合成气组成具有十分重要的意义口…。 为此,本文采用一种合适的实验方法,对气流床气 化炉内颗粒停留时间分布进行研究。
2 结果与讨论
2.1实验方法可行性研究 气固两相流中固体颗粒停留时间的测量是一个
多喷嘴对置式气化炉内颗粒停留时间分布数学模拟研究
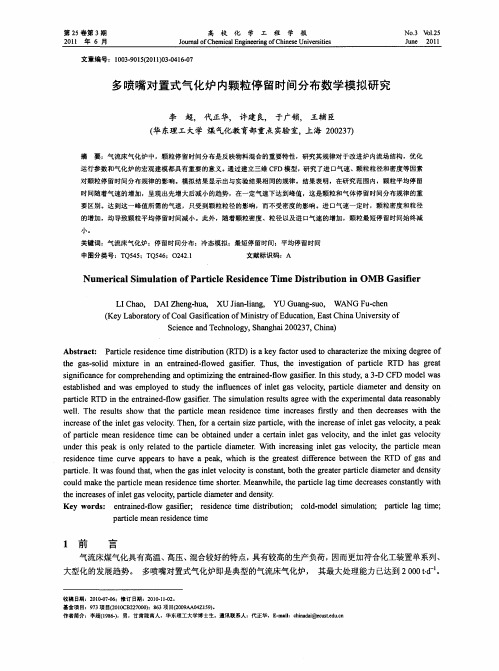
中图分类号 :T 4 ;T 4 ;0 4 . Q5 5 Q5 6 2 21 文献标识码:A
Nu e ia i ul to fPa tceRe i nc m eDit i to n O M B sfe m rc lS m a i n o r i l sde eTi s rbu i n i Ga i r i
LICh o, DAIZh n - u , XU in la g YU a g-U , W ANG u-h n a e gh a Ja -in , Gu n S O F ce
( y aoa r f o aict no nsyo d c i , at h a i r t o Ke b r oyo aG s ao f ir f ua o E i v sy f L t Cl i f i Mi t E t n s C n Un e i S i c d eh o g , h ga 2 0 3 , h a c n e n cn l y S a h i 0 2 7 C i ) e a T o n n
we1 l.Th e ul s o t a e patce m e n r sd nc i ic e s s frty n h n d c e s s w i e e r s t h w tt ril s h h a e i e e tme n r a e sl a d t e e r ae t t i h h
撞击流气化炉内气固两相流动与颗粒附壁沉积数值模拟
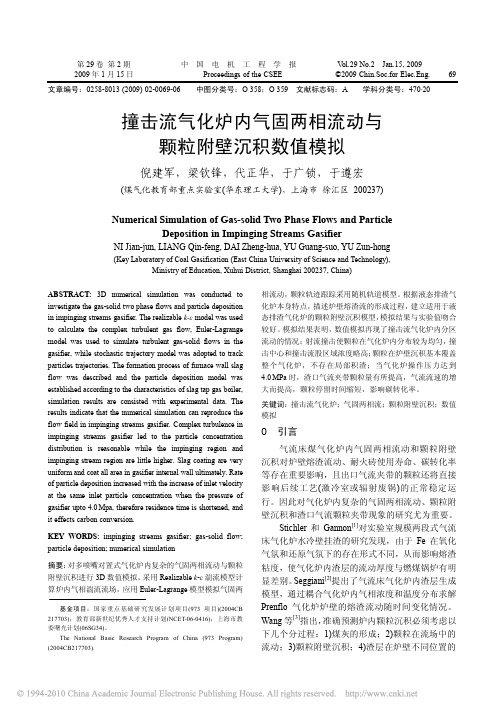
沉积 沉积
图 2 颗粒沉积和熔渣流形成过程 Fig. 2 Schematic of the development of particle
deposit and slag flow formation
性层上沉积形成结渣层;第 3 步,随着固态渣层的 不断增加,炉壁热阻增加,导致固态渣表面温度上
升,最终超过渣的相变温度,形成液态熔融层;最
η η+
] 5
;η
=Sk ε
;S
=
2Sij Sij ;
Yd 为流体可压缩影响因子;Sk 和 Sε为自定义影响 因子。
在湍流粘性系数的计算中,Cµ不再是常数,而 采用式(3)计算,即
式中:U * =Cµ=A0+
1 As
kU * ε
(3)
Si, j Si, j + Ωi, jΩi, j ; Ωi, j 是从角速度为
ABSTRACT: 3D numerical simulation was conducted to investigate the gas-solid two phase flows and particle deposition in impinging streams gasifier. The realizable k-ε model was used to calculate the complex turbulent gas flow, Euler-Lagrange model was used to simulate turbulent gas-solid flows in the gasifier, while stochastic trajectory model was adopted to track particles trajectories. The formation process of furnace wall slag flow was described and the particle deposition model was established according to the characteristics of slag tap gas boiler, simulation results are consisted with experimental data. The results indicate that the numerical simulation can reproduce the flow field in impinging streams gasifier. Complex turbulence in impinging streams gasifier led to the particle concentration distribution is reasonable while the impinging region and impinging stream region are little higher. Slag coating are very uniform and coat all area in gasifier internal wall ultimately. Rate of particle deposition increased with the increase of inlet velocity at the same inlet particle concentration when the pressure of gasifier upto 4.0 Mpa, therefore residence time is shortened, and it effects carbon conversion.
四喷嘴对置式气化炉停留时间分布的随机模型
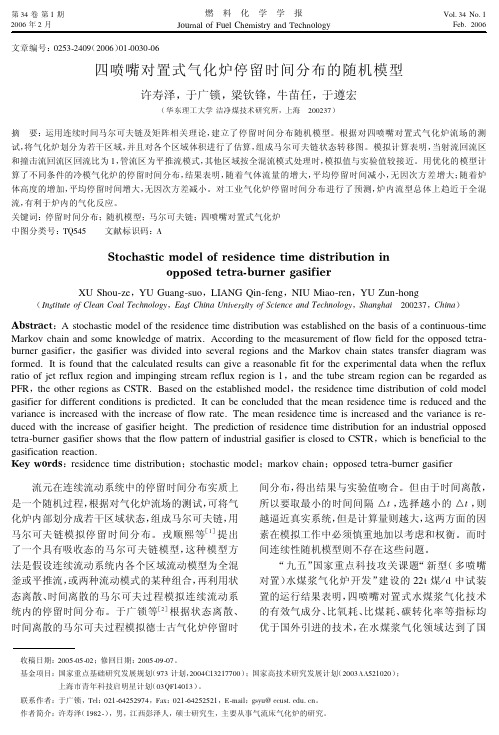
(7)
"# 理论分析
! $ !" 模型的建立 " 假定气化炉内任意一点流体流 型和速度分布不随时间变化。令随机变量 ! ( ")是 一可识别的流元在 " 时刻在气化炉内所处的位置 ( 区域状态) , 基于连续时间马尔可夫链的基本概 [ %] 念 可把{! ( ") }看成一个连续时间马尔可夫链, 并且认为这链是齐次的。 则 #( $% " )表示流元从状态 $ 经过时间 " 后转移到状态 % 的概率, #( 表示状态为 $ ") $ 的流元经过时间 " 后仍保留在原状态的概率, 可以 判断出 #( $% " )为标准转移概率。 如果 #( 即对任意 $, % " ’ 有: $% " )在 " & & 连续, "# 若 $ & % ’() #( (") $% " ) & "#& ( &# 若 $ $ % 假设气体流元{! ( ") , " % &} 在时刻 " 处于状态
, #( ] #( } /5 %% 5 ) $% " ) 性质, 有: / (" (#( $% " ) # $4 ( ") - 4% ’ 4 上式可写成矩阵方程形式: *6 ( ") & * ( ") 2 上式中: ( ") #"* ( ") #"" # ( ") #** ( ") * ( ") & *" # 3( ( " ") # 3 * ") 从式 (") 可得: " & * ( 7) & 8 & & & " & … … & … & & " … … & … & # $4 ( ") - 4% ’ 4$% (
《撞击流反应器流场数值模拟分析与氢氧化钙纳米粉体制备研究》
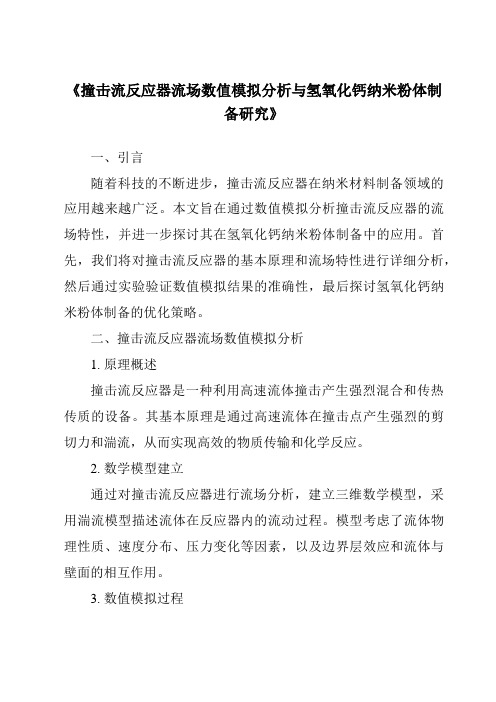
《撞击流反应器流场数值模拟分析与氢氧化钙纳米粉体制备研究》一、引言随着科技的不断进步,撞击流反应器在纳米材料制备领域的应用越来越广泛。
本文旨在通过数值模拟分析撞击流反应器的流场特性,并进一步探讨其在氢氧化钙纳米粉体制备中的应用。
首先,我们将对撞击流反应器的基本原理和流场特性进行详细分析,然后通过实验验证数值模拟结果的准确性,最后探讨氢氧化钙纳米粉体制备的优化策略。
二、撞击流反应器流场数值模拟分析1. 原理概述撞击流反应器是一种利用高速流体撞击产生强烈混合和传热传质的设备。
其基本原理是通过高速流体在撞击点产生强烈的剪切力和湍流,从而实现高效的物质传输和化学反应。
2. 数学模型建立通过对撞击流反应器进行流场分析,建立三维数学模型,采用湍流模型描述流体在反应器内的流动过程。
模型考虑了流体物理性质、速度分布、压力变化等因素,以及边界层效应和流体与壁面的相互作用。
3. 数值模拟过程采用计算流体动力学(CFD)软件进行数值模拟,对撞击流反应器内的流场进行求解。
通过设定不同的流体速度、流量和温度等参数,观察流场的变化,分析流体在反应器内的分布、混合和传热传质过程。
4. 结果分析数值模拟结果表明,撞击流反应器内流体具有较高的湍流强度和混合效率。
随着流体速度的增加,撞击点处的剪切力和湍流强度逐渐增大,有利于提高物质传输和化学反应速率。
同时,通过调整流体流量和温度等参数,可以实现对反应器内流场的优化控制。
三、氢氧化钙纳米粉体制备实验研究1. 实验材料与方法实验采用高纯度钙源和氢氧根源为原料,通过撞击流反应器制备氢氧化钙纳米粉体。
实验过程中,控制反应温度、反应时间和流体速度等参数,以获得理想的纳米粉体。
2. 实验结果与分析通过实验发现,利用撞击流反应器制备的氢氧化钙纳米粉体具有较高的纯度和良好的分散性。
随着反应温度和流体速度的增加,纳米粉体的粒径逐渐减小,表面积增大,有利于提高其应用性能。
同时,通过优化反应时间和流体流量等参数,可以实现氢氧化钙纳米粉体制备的规模化生产。
温度对撞击器内颗粒沉积粒径影响的研究
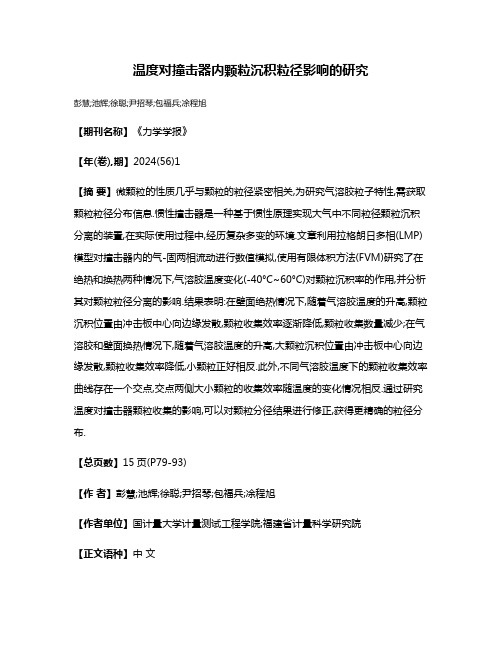
温度对撞击器内颗粒沉积粒径影响的研究
彭慧;池辉;徐聪;尹招琴;包福兵;凃程旭
【期刊名称】《力学学报》
【年(卷),期】2024(56)1
【摘要】微颗粒的性质几乎与颗粒的粒径紧密相关,为研究气溶胶粒子特性,需获取颗粒粒径分布信息.惯性撞击器是一种基于惯性原理实现大气中不同粒径颗粒沉积分离的装置,在实际使用过程中,经历复杂多变的环境.文章利用拉格朗日多相(LMP)模型对撞击器内的气-固两相流动进行数值模拟,使用有限体积方法(FVM)研究了在绝热和换热两种情况下,气溶胶温度变化(-40°C~60°C)对颗粒沉积率的作用,并分析其对颗粒粒径分离的影响.结果表明:在壁面绝热情况下,随着气溶胶温度的升高,颗粒沉积位置由冲击板中心向边缘发散,颗粒收集效率逐渐降低,颗粒收集数量减少;在气溶胶和壁面换热情况下,随着气溶胶温度的升高,大颗粒沉积位置由冲击板中心向边缘发散,颗粒收集效率降低,小颗粒正好相反.此外,不同气溶胶温度下的颗粒收集效率曲线存在一个交点,交点两侧大小颗粒的收集效率随温度的变化情况相反.通过研究温度对撞击器颗粒收集的影响,可以对颗粒分径结果进行修正,获得更精确的粒径分布.
【总页数】15页(P79-93)
【作者】彭慧;池辉;徐聪;尹招琴;包福兵;凃程旭
【作者单位】国计量大学计量测试工程学院;福建省计量科学研究院
【正文语种】中文
【中图分类】O359
【相关文献】
1.颗粒粒径对喷射沉积制备SiC颗粒增强铝硅合金复合材料显微组织及拉伸性能的影响
2.超声法纳米颗粒悬浮液粒径测量中温度影响的实验研究
3.撞击器法测定吸入粉雾剂空气动力学粒径分布颗粒反弹的研究
4.灰分沉积对DPF内颗粒沉积影响的试验研究
因版权原因,仅展示原文概要,查看原文内容请购买。
平面气固撞击流周期振荡的模拟分析
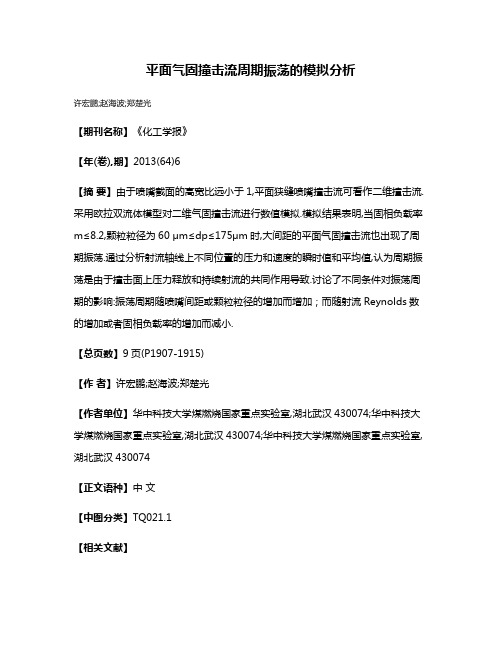
平面气固撞击流周期振荡的模拟分析
许宏鹏;赵海波;郑楚光
【期刊名称】《化工学报》
【年(卷),期】2013(64)6
【摘要】由于喷嘴截面的高宽比远小于1,平面狭缝喷嘴撞击流可看作二维撞击流.采用欧拉双流体模型对二维气固撞击流进行数值模拟.模拟结果表明,当固相负载率m≤8.2,颗粒粒径为60 μm≤dp≤175μm时,大间距的平面气固撞击流也出现了周期振荡.通过分析射流轴线上不同位置的压力和速度的瞬时值和平均值,认为周期振荡是由于撞击面上压力释放和持续射流的共同作用导致.讨论了不同条件对振荡周期的影响:振荡周期随喷嘴间距或颗粒粒径的增加而增加;而随射流Reynolds数的增加或者固相负载率的增加而减小.
【总页数】9页(P1907-1915)
【作者】许宏鹏;赵海波;郑楚光
【作者单位】华中科技大学煤燃烧国家重点实验室,湖北武汉430074;华中科技大学煤燃烧国家重点实验室,湖北武汉430074;华中科技大学煤燃烧国家重点实验室,湖北武汉430074
【正文语种】中文
【中图分类】TQ021.1
【相关文献】
1.大涡模拟二维气固两相平面射流 [J], 金晗辉;金涛;罗坤;樊建人;岑可法
2.移动床热煤气脱硫气固反应过程模拟:Ⅱ.错流移动床非催化气固反应过程模拟 [J], 曹晏; 张守玉; 张建民; 王洋; 张碧江
3.基于DSM湍流模型的气固圆湍撞击流模拟 [J], 耿察民;蒋骏;任少君
4.气固两相平面混合层的直接数值模拟 [J], 李文春;胡桂林;樊建人;岑可法
5.多腔室气-液-固三相床周期振荡操作的传质特性 [J], 刘天中;刘德华;欧阳藩
因版权原因,仅展示原文概要,查看原文内容请购买。
粉浆气化炉内流场分布数值模拟研究
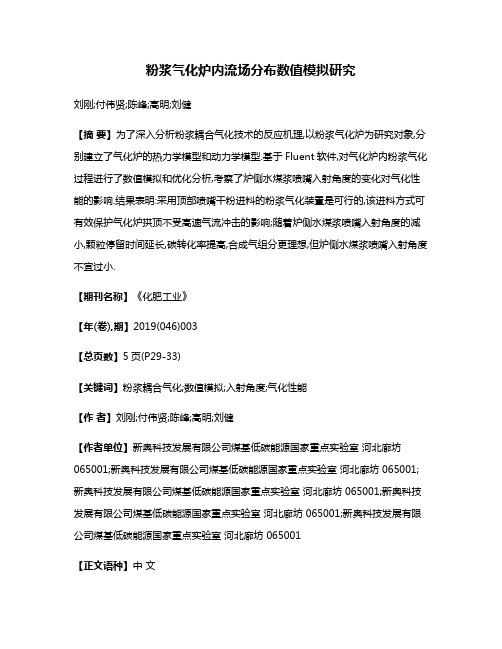
粉浆气化炉内流场分布数值模拟研究刘刚;付伟贤;陈峰;高明;刘健【摘要】为了深入分析粉浆耦合气化技术的反应机理,以粉浆气化炉为研究对象,分别建立了气化炉的热力学模型和动力学模型.基于Fluent软件,对气化炉内粉浆气化过程进行了数值模拟和优化分析,考察了炉侧水煤浆喷嘴入射角度的变化对气化性能的影响.结果表明:采用顶部喷嘴干粉进料的粉浆气化装置是可行的,该进料方式可有效保护气化炉拱顶不受高速气流冲击的影响;随着炉侧水煤浆喷嘴入射角度的减小,颗粒停留时间延长,碳转化率提高,合成气组分更理想,但炉侧水煤浆喷嘴入射角度不宜过小.【期刊名称】《化肥工业》【年(卷),期】2019(046)003【总页数】5页(P29-33)【关键词】粉浆耦合气化;数值模拟;入射角度;气化性能【作者】刘刚;付伟贤;陈峰;高明;刘健【作者单位】新奥科技发展有限公司煤基低碳能源国家重点实验室河北廊坊065001;新奥科技发展有限公司煤基低碳能源国家重点实验室河北廊坊 065001;新奥科技发展有限公司煤基低碳能源国家重点实验室河北廊坊 065001;新奥科技发展有限公司煤基低碳能源国家重点实验室河北廊坊 065001;新奥科技发展有限公司煤基低碳能源国家重点实验室河北廊坊 065001【正文语种】中文【中图分类】TQ546.2粉浆耦合气化技术是指在气化炉内同时喷入煤粉和水煤浆,通过调节粉浆投料比例和炉侧喷嘴的入射角度改变炉内气固流动情况及反应结果,实现煤粉和煤浆的高效共气化。
与水煤浆气化技术相比,该气化技术的煤种适应性更加广泛,单位产品原料煤耗、氧耗下降,有效气含量增加;与常规粉煤气化技术相比,可采用自有粉煤高压密相输送技术,可将气化压力提高至6.5 MPa。
如图1所示,粉浆耦合气化技术的特征炉型之一是在气化炉顶部设置煤粉喷嘴,并在距离顶部喷嘴一定位置的平面上设置4只水煤浆喷嘴,通过调节炉侧喷嘴的入射角度改变炉内气固流动情况及反应效果。
撞击流反应器的流场测量及数值模拟研究
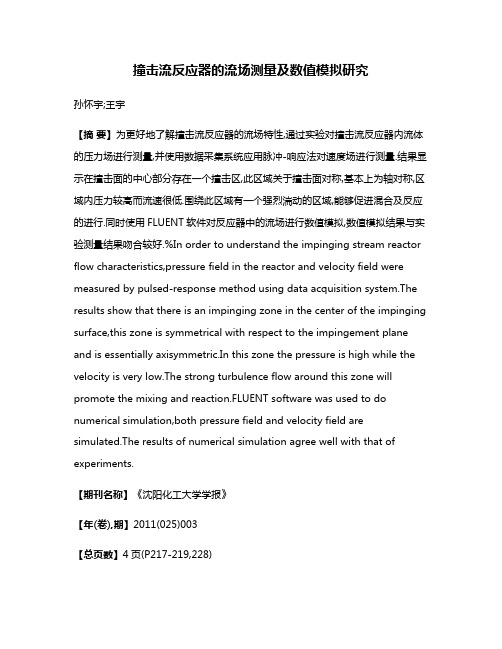
撞击流反应器的流场测量及数值模拟研究孙怀宇;王宇【摘要】为更好地了解撞击流反应器的流场特性,通过实验对撞击流反应器内流体的压力场进行测量,并使用数据采集系统应用脉冲-响应法对速度场进行测量.结果显示在撞击面的中心部分存在一个撞击区,此区域关于撞击面对称,基本上为轴对称,区域内压力较高而流速很低.围绕此区域有一个强烈湍动的区域,能够促进混合及反应的进行.同时使用FLUENT软件对反应器中的流场进行数值模拟,数值模拟结果与实验测量结果吻合较好.%In order to understand the impinging stream reactor flow characteristics,pressure field in the reactor and velocity field were measured by pulsed-response method using data acquisition system.The results show that there is an impinging zone in the center of the impinging surface,this zone is symmetrical with respect to the impingement plane and is essentially axisymmetric.In this zone the pressure is high while the velocity is very low.The strong turbulence flow around this zone will promote the mixing and reaction.FLUENT software was used to do numerical simulation,both pressure field and velocity field are simulated.The results of numerical simulation agree well with that of experiments.【期刊名称】《沈阳化工大学学报》【年(卷),期】2011(025)003【总页数】4页(P217-219,228)【关键词】撞击流反应器;压力场;数据采集系统;速度场;FLUENT;数值模拟【作者】孙怀宇;王宇【作者单位】沈阳化工大学化学工程学院,辽宁沈阳110142;沈阳化工大学化学工程学院,辽宁沈阳110142【正文语种】中文【中图分类】TQ051.19撞击流是使两股流体沿轴相向流动,并在中点处的撞击区域产生撞击.撞击流技术最早应追溯到1953年Koppers-Totsek粉煤气化炉的研发和应用[1].20世纪60年代初原苏联的 Elperin等学者率先开展了这一系统的研究[2].20世纪70年代末,以色列Tamir[3]及其领导的研究组从设备形式及应用上进行了较深入系统的研究.我国学者从20世纪90年代开始对撞击流进行研究.伍沅设计了用于制备超细粉体的浸没循环撞击流反应器[4].由流体的不同,撞击流分为以气相为连续相的撞击流及以液相为连续相的撞击流.近年来,撞击流领域的研究明显转向以液体为连续相.这种研究重点的转移是由于液体的密度和黏度分别比气体大3个和2个数量级,致使两股相向流体撞击时发生强烈的动量传递和流团间相互剪切、挤压作用,还在撞击区产生波动,其结果将有效地促进微观混合[5].本文主要研究撞击流反应器内流体的压力分布及流速分布,以便更好地了解流动情况,为反应器的放大设计及应用提供理论依据.同时应用FLUENT软件对流场进行数值模拟,更深入地解流场情况.1 实验部分1.1 反应器及实验方法使用有机玻璃制作撞击流反应器,设备尺寸为20 cm×10 cm×5 cm,上端开有10 cm×2 cm的长方形溢流口,两导流管为Φ0.75 cm×0.1 cm,管口间距为2 cm.定义以撞击面中心为坐标中心的三维坐标系,x轴与导流管轴线重合,y轴为垂直方向,y-z平面称为撞击面,x-z平面称为水平面,x-y平面称为垂直面.实验使用水为工质.实验流程如图1所示.图1 设备流程图Fig.1 Equipment flow chart1水槽 2泵 3调节阀 4转子流量计5撞击流反应器测量时用阀门调节两管流量.压力探头垂直插入液面下指定位置,使用双液倒U形管压差计(水和柴油做指示剂)对撞击流反应器内压力进行测量.用热电阻作为测温探头,使用PCI-1710数据采集卡建立数据采集系统,以1 kHz的采样率对探头处温度进行测量.在流动方向上放置2个间隔一定距离的探头,并在管出口处迅速加入一定量的热水,通过分析两探头测量得到温度脉冲峰的时间差,可得到两探头间的流体速度.1.2 实验结果与分析图2和图3分别是撞击速度u=0.4 m/s时x-z面的压力分布和流速分布.图2 u=0.4m/s时x-z面压力分布Fig.2 Pressure distribution on x-z plane when u=0.4 m/s从图2可以看出:压力分布关于撞击面基本对称,在撞击面的中心周围存在一个高压力区域,撞击面中心的压力最大,这是因为在两股流体撞击过程中部分动压头转换为静压头.而在此区域外的压力较低.图3 u=0.4m/s时x-z面流速分布Fig.3 Velocity distribution on x-z plane when u=0.4 m/s从图3可以看出:速度分布关于撞击面基本对称.撞击面中心周围存在一个低速区域,撞击面中心的速度基本为0.在此低速区域周围存在一个锥形的流速较高的区域.从流体力学角度分析,在低速区域周围的流动速度较高,而两侧的压力差又较大,所以在此区域流动的流体容易产生旋涡,并产生较强的混合及反应促进作用.2 使用FLUENT进行流体力学数值模拟使用FLUENT软件建立反应器模型[6],并对撞击流反应器的流场进行三维数值模拟.几何模型和网格模型使用前处理器GAMBIT完成,求解器选为FLUENT 5/6,利用Tgrid程序将包括入口管的反应器划分为四面体网格.设置两入水管出口为velocity-inlet边界条件,顶面长方形溢流口为outflow边界条件.为简化计算,假设撞击流反应器内流体的时均运动为稳定流动;流体为连续、不可压缩牛顿流体;反应器与外界无热量交换;不考虑重力影响;壁面为无滑移光滑界面.选用标准k-ε双方程作为流体力学模型,此模型可对湍流发展非常充分的流体进行计算.通过模拟计算,得到指定流速下反应器中的压力场及速度场.3 实验与模拟结果比较分析图4和图5为撞击速度u=0.4 m/s、中心水平面x=0时沿z轴压力和速度的实验结果与模拟结果比较.图4 u=0.4 m/s时z轴压力模拟值与实验值的比较Fig.4 Simulation compared with the experimental values of pressure on z-axis when u=0.4 m/s在入口流速相同情况下,数值模拟与实验所得z轴上压力分布和速度分布基本一致.表明使用数值模拟软件对此反应器中的流场进行模拟可行.但实验值与模拟值存在一定的差别,说明使用流体力学模型在模拟撞击流时还有一定的误差,这方面有待于在流体力学模型方面进行进一步的研究及改进.数值模拟得到的在u=0.4 m/s时x-y平面和y-z平面的压力分布和速度分布如图6~图9所示.图5 u=0.4 m/s时z轴速度模拟值与实验值的比较Fig.5 Simulation compared with the experimental values of velocity on z-axis when u=0.4 m/s图6 u=0.4 m/s时x-y面压力分布Fig.6 Pressure distribution on x-y plane when u=0.4 m/s图7 u=0.4 m/s时y-z面压力分布Fig.7 Pressure distribution on y-z plane when u=0.4 m/s图8 u=0.4 m/s时x-y面流速分布Fig.8 Velocity distribution on x-y plane when u=0.4 m/s图9 u=0.4 m/s时y-z面流速分布Fig.9 Velocity distribution on y-z plane when u=0.4 m/s从图6~图9可进一步证实,在撞击面的中心有一个高压力低流速区域,区域关于撞击面对称,基本为轴对称.流体在进行撞击时,绕这个区域进行流动,在区域的周围产生强烈的湍流,这个强烈的湍流区域对混合过程及反应过程有很强的促进作用.4 结论(1)通过实验得到撞击流反应器内的压力分布及速度分布.证明在撞击面中心部分存在一个撞击区,此区域关于撞击面对称,基本上轴对称.区域内压力较高,流速很低,围绕此区域有一个强烈湍动的区域,会促进混合及反应的进行.(2)使用FLUENT对反应器建模,使用k-ε方程进行流体力学模拟计算,得到的模拟结果与实验结果基本一致.参考文献:【相关文献】[1] Tamir A.撞击流反应器——原理和应用[M].伍沅,译.北京:化学工业出版社,1996:172-173.[2] Elperin I T.Heat and Mass Transfer in Opposing Currents[J].J Engng Physics,1961(6):62-68.[3]伍沅.撞击流性质及其应用[J].化工进展,2001,20(11):8-13.[4]伍沅.浸没循环撞击流反应器:中国,CNZL002303264[P].2000-07-06.[5]伍沅.撞击流中连续相研究重点的转移[J].化工进展,2003,22(10):1066-1071. [6]于勇.Fluent入门与进阶教程[M].北京:北京理工大学出版社,2008:1-2.。
气流床气化炉内气体浓度的分布规律
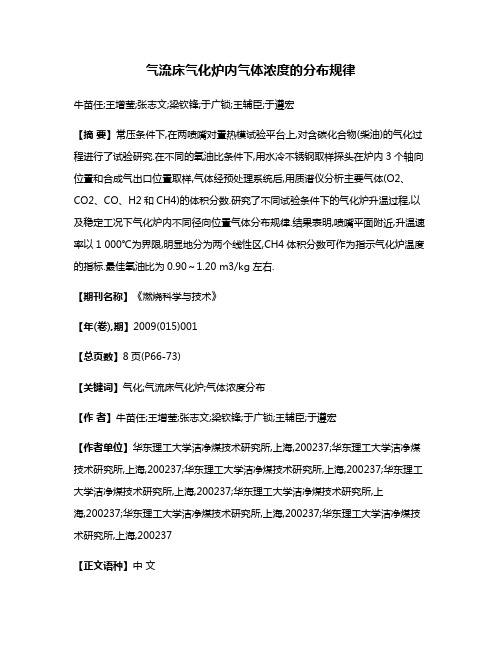
气流床气化炉内气体浓度的分布规律牛苗任;王增莹;张志文;梁钦锋;于广锁;王辅臣;于遵宏【摘要】常压条件下,在两喷嘴对置热模试验平台上,对含碳化合物(柴油)的气化过程进行了试验研究.在不同的氧油比条件下,用水冷不锈钢取样探头在炉内3个轴向位置和合成气出口位置取样,气体经预处理系统后,用质谱仪分析主要气体(O2、CO2、CO、H2和CH4)的体积分数.研究了不同试验条件下的气化炉升温过程,以及稳定工况下气化炉内不同径向位置气体分布规律.结果表明,喷嘴平面附近,升温速率以1 000℃为界限,明显地分为两个线性区,CH4体积分数可作为指示气化炉温度的指标.最佳氧油比为0.90~1.20 m3/kg左右.【期刊名称】《燃烧科学与技术》【年(卷),期】2009(015)001【总页数】8页(P66-73)【关键词】气化;气流床气化炉;气体浓度分布【作者】牛苗任;王增莹;张志文;梁钦锋;于广锁;王辅臣;于遵宏【作者单位】华东理工大学洁净煤技术研究所,上海,200237;华东理工大学洁净煤技术研究所,上海,200237;华东理工大学洁净煤技术研究所,上海,200237;华东理工大学洁净煤技术研究所,上海,200237;华东理工大学洁净煤技术研究所,上海,200237;华东理工大学洁净煤技术研究所,上海,200237;华东理工大学洁净煤技术研究所,上海,200237【正文语种】中文【中图分类】TQ546.2撞击流基本构思是使两股气体-颗粒或滴沥两相流沿同轴相向流动撞击.由于惯性,颗粒穿过撞击面渗入反向流做减幅振荡运动,颗粒经历相间相对速度极高的条件,并延长了在气流中的停留时间,这种方法对强化热、质传递过程非常有效,在许多领域已有广泛的研究和应用[1-4].大型四喷嘴对置冷模装置的测试结果表明,气化炉内流场可划分成射流区、撞击区、撞击流股区、回流区、折返流区和管流区.对于热态试验,炉内温度高,气体含尘量大,要测量合成气浓度相当困难,再加上燃烧规律复杂,因此无论在理论分析、试验研究或是现场实测方面,已做过的研究工作都很少,可查到的有关文献资料也甚少.以含碳物质(柴油)为原料,纯氧为气化剂,经过部分氧化生成合成气,是一个极其复杂的反应过程.就化学反应而言,同时存在柴油的高温裂解、燃烧和气化反应,因返混而造成的可燃组分(主要是CO和H2)与氧的燃烧反应,气体组分同炭黑之间的反应以及变换和甲烷蒸气转化反应.柴油中含有多种元素,除了主要元素C、H 以外,还含有S、N等其他元素.在高温气化过程中,S生成H2S和COS,别的化合物如SOx或CS2基本不存在,合成气中S主要以H2S形式存在(93%~95%),其余为COS,由于COS很难除去,所以用专门的催化剂把COS转变为H2S再除去.HCN、NH3和NOx等主要来自原料中的N,不是来自N2,因为N—H,N—C比≡N弱好多[5].H2S、COS、HCN、NH3和NOx等体积分数都很少,本文只分析主要气体(O2,CO2,CO,H2和CH4)的体积分数.1 反应机理柴油气化主要出现两种不同类型的化学反应:放热的一次反应(燃烧)和吸热的二次反应.气化炉内某一区域主要发生哪种反应依赖于此区域的流动性质和混合过程.图1给出了煤和生物质气化的反应过程,对于柴油气化,由于包含的几乎全是高温分解物质,过程稍微有些不同.柴油进入高温气化炉内,受到快速加热,与氧化剂迅速反应,生成气体.基于反应和流动行为,气化炉内可分成3个区[6]:一次反应区,二次反应区,一次反应和二次反应共存区.图1 煤和生物质气化的反应过程[5]1.1 一次反应区撞击流本身和它的扩展区域构成了一次反应区.一次反应区中以挥发分、CO和H2的燃烧反应为主,高温分解产物、CO和H2的燃烧速率极快,其时间尺度在2~4 ms[7],远小于炉内微观混合的时间尺度(0.6 s).在混合过程中,燃料将发生高温分解,并形成游离残碳,残碳的燃烧反应主要出现在一次反应区.Masdin等[8]的研究表明,残碳的燃烧速率较低,因此,残碳在一次反应区中的燃烧与其他高温分解产物的燃烧相比是次要的.概括地讲,一次反应区中的反应如式(1)~式(5)所示.高温分解产物+O2→CO2+H2O(1)2CO+O2→2CO2(2)2H2+O2→2H2O(3)CH4+2O2→CO2+2H2O(4)2C+O2→2CO(5)1.2 二次反应区二次反应区包括平推流区和折返流区.在此区域内,一次反应区的产物将进行二次反应:C+CO2→2CO(6)C+H2O→CO+H2(7)CH4+H2O→CO+3H2(8)CH4+CO2→2CO+2H2(9)CO2+H2→CO+H2O(10)在900~1 500 ℃范围内,C与H2的反应速率比C与CO2或H2O的反应速率低了2个数量级.一般来讲,可用反应速率常数的倒数1/k表征反应时间尺度,反应(6)的时间尺度为10 s左右[9].众所周知,反应(7)速度比反应(6)快,反应(8)~(10)为均相反应,在高温下其速率高于反应(6)和(7).碳与H2O和CO2反应的时间尺度均大于微观混合的时间尺度,即化学反应是残碳气化反应的控制步骤.1.3 一次与二次反应共存区一次反应与二次反应共存区主要出现在回流区,因射流的卷吸作用和湍流扩散,回流区与射流区将进行质量交换.尽管共存区中也出现二次反应,但多数反应可以看作一次反应.此区域所有反应过程,除了残碳与H2O和CO2反应以外,都由微观扩散步骤控制.2 试验撞击式气流床气化炉试验流程如图2所示.试验在常压下进行,用氧气作为氧化剂,柴油作为气化介质.气化炉内衬为刚玉管,外部为不锈钢外壳,中间隔有硅酸铝保温棉.炉内径为300 mm,长度为2 200 mm;炉侧面开孔,以便于进行观察和测量.气化炉两个双通道喷嘴水平对置,喷嘴结构如图3所示.氧气由氧气钢瓶提供,并由气体质量流量计控制计量后经喷嘴外通道进入气化炉炉膛内.柴油由齿轮泵计量输送,经喷嘴内通道进入炉膛内,氧气与柴油在炉内进行剧烈的对撞气化燃烧,生成的合成气经激冷室冷却后放空.采用工业电视系统拍摄气化火焰图像,对炉内情况进行监控.取样及分析系统主要由3个部分构成.(1) 气体采集装置采用水冷不锈钢探头,从高温高粉尘的环境中连续取样,其结构如图4所示.探头可从不同轴向位置取样,对同一轴向位置,探头可从炉壁伸到轴线中心,即在不同辐射位置取样.为了比较全面地对炉内气体进行分析,本系统的取样位置安装在如图2所示的C、D、F和G四个位置,采用氩气定时吹扫以防止取样探头堵塞.同时在A、B和E三个位置安装热电偶,来观察炉内温度变化情况. (2) 气体净化装置中气体分析预处理,使其达到质谱仪的进样要求.其流程如图5所示,气体样品由水冷探头取出后,首先进行过滤,滤去大部分炭黑,接着进行干燥、精密过滤进入取样泵,然后进入压缩机制冷器冷凝,冷凝水经三通、针阀,由排水口排出;冷凝后的气体再经干燥器干燥、流量计计量后进入质谱仪.(3) 采用英国HIDEN公司生产的HPR20QIC型气体分析质谱仪进行在线、实时、定量分析.分析一组数据的时间为16~20 s,响应时间快,分析精度高.由于受湍流波动、取样时间等的限制,为了能获得足够的信息,在每一位置处取样时间至少为10 min.1—柴油储槽;2—氧气瓶;3—氩气瓶;4—齿轮泵;5—气体质量流量计;6—喷嘴;7—涡街流量计;8—排渣口;9—气体预处理系统;10—质谱仪;11—计算机;12—火焰检测器图2 试验流程示意(单位:mm)图3 喷嘴结构示意图4 水冷取样探头(单位:mm)图5 气体预处理系统3 结果与讨论3.1 烘炉过程气化炉内的温度是一个非常重要的参数,它应低于耐火衬里的使用温度,高于维持快速反应需要的温度.烘炉过程是指从气化炉点火开始至炉内各位置热电偶温度基本不发生变化为止,是气化炉趋于平稳的过程.这一过程类似于工业开车过程,故研究烘炉过程温度变化情况.以此为基础,烘炉过程条件不变,在C位置取样,取样探头与炉内壁相切.烘炉条件见表1.条件2稳定时炉内升温情况见图6.B位置热电偶约90 min升到1 000 ℃,约195 min升到1 300 ℃.温度随时间基本上呈线性增加,在刚开始的1 h内,升温速度很快,约9 ℃/min,而后升温速度逐渐变慢,约2 ℃/min.从图6也可以看出,A位置和B位置热电偶的温度在1 000 ℃左右有一个拐点,升温速率明显地分为两个线性区.图6 炉内升温情况表1 烘炉条件条件1号柴油/(k g·h-1)2号柴油/(kg·h-1)1号O2/(m3·h-1)2号O2/(m3·h-1)氧油比/(m3·kg-1)B位置升到1 000 ℃时间/ minB位置升到1 300 ℃时间/min12.101.922.562.571.2810022522.002.002.732.841.399019532.002.002.7 82.911.428018042.222.463.513.701.5475150在气化过程中,气化炉温度主要与氧油比(每小时进料氧气体积与柴油质量之比,m3/kg)、柴油进料量、气化反应进行的深度以及热损失有关.O2和水蒸气是控制气化炉温度的气体,还有一些其他降低炉温的方法,比如:在O2中加入N2或CO2,或者间接把热量移走等.由于停留时间很短,所以控制过程非常复杂.在气化炉运行过程中,如果最重要的调节参数O2突然增加,会使气化炉内衬受到严重的损坏,经验表明,如果O2的量超出气化炉正常运行所需O2量的50%,几分钟之内,气化炉温度就会升到1 550 ℃以上.3.2 稳定燃烧气化过程稳定燃烧气化过程是指试验条件固定,从点火开始约4 h到炉内各位置热电偶的温度基本保持不变为止,即认为达到了热平衡.在C、D、F三个轴向位置取样,每个轴向位置,以取样探头与炉内壁相切为基准,分别测量距离炉内壁0 cm、3 cm、6 cm、9 cm、12 cm、15 cm (炉膛中心) 6个辐射位置的气体组成,试验条件见表2.3.2.1 位置C各物质不同径向位置体积分数分布不同氧油比条件下,位置C各物质不同径向位置体积分数分布如图7所示,从图7可以看出:① H2在接近炉中心处体积分数下降,CO在接近炉中心处体积分数上升;② CO2体积分数先降低后升高,不同径向位置,O2体积分数依然很低,没有大的变化,说明在高温下,炉内反应进行的很快;③ 越接近炉中心,CH4体积分数越高,在炉中心位置有一最低值,因为炉中心温度最高;理论上越接近于炉中心,离火焰越近,温度越高;CH4体积分数应该越低,但实际测量值升高,直到炉中心最高温度时,体积分数才最低,说明炉内气体发生了不同程度的混合;④ Ar体积分数约在径向位置6 cm处有一最高值,然后越接近炉中心,体积分数越低;这是因为Ar用来保护火焰检测器镜头,从炉顶吹入,由于双喷嘴对撞,形成一个撞击面,Ar很难进入炉中心.表2 实验条件条件1号柴油/(kg·h-1)2号柴油/(kg·h-1)1号O2/(m3·h-1)2号O2/(m3·h-1)Ar/(m3·h-1)氧油比/(m3·kg-1)11.952.041.7471.8140.8180.89321.952.041.8922.0380.7160.98532.011.982 .0372.1880.6731.05942.082.042.2142.3880.1191.11752.001.982.3232.496-1.21162.002.002.4872.6200.7161.27772.02.002.7852.9110.8091.424(a) 氧油比0.893 m3/kg,T=1 290 ℃(b) 氧油比1.059 m3/kg,T=1 308 ℃(c) 氧油比1.211 m3/kg,T=1 360 ℃(d) 氧油比1.424 m3/kg,T=1 380 ℃图7 位置C各物质不同径向位置体积分数3.2.2 位置D各物质不同径向位置体积分数分布不同氧油比条件下,位置D各物质不同径向位置体积分数分布如图8所示.从图8可以看出,各物质体积分数基本上为一条水平直线,在不同径向位置差别不大.说明在D位置处各物质体积分数混合已比较均匀,在F位置也有类似规律,说明在喷嘴平面下部20 cm处,合成气已混合比较均匀.表3给出了各物质径向6个位置的体积分数均值.图9为位置D各物质体积分数随氧油比变化图,从图9可以看出,随氧油比增大,气化炉温度升高,碳转化率增大,CO2体积分数增大,CO基本不变,H2体积分数下降,CH4体积分数下降,O2体积分数基本为零.(a) 氧油比0.893 m3/kg,T=1 282 ℃(b) 氧油比1.059 m3/kg,T=1 290 ℃(c) 氧油比1.211 m3/kg,T=1 360 ℃(d) 氧油比1.424 m3/kg,T=1 390 ℃图8 位置D各物质不同径向位置体积分数(a) CO2,CO,H2(b) CH4,O2图9 位置D各物质体积分数随氧油比变化表3 位置D各物质体积分数径向均值氧油比/(m3·kg-1)φ(CO2)/%φ(CO)/%φ(H2)/%φ(CH4)/%φ(O2)/%0.8937.59645.76744.4232.0 570.0310.98510.37749.45838.7511.2290.0311.05910.23849.51838.5721.508 0.0311.11714.14648.35336.8410.4900.0401.21113.86951.67234.1480.1600.0 401.27715.77751.50232.5250.0310.0211.42421.76251.47426.61900.021 3.2.3 位置F各物质不同径向位置体积分数分布表4给出了不同氧油比条件下位置F各物质体积分数径向均值,图10为位置F各物质体积分数随氧油比变化图.从图10可以看出,随氧油比增大,CO2体积分数增大,CO体积分数基本不变,H2体积分数下降,CH4体积分数下降,O2体积分数基本为零.表4 位置F各物质体积分数径向均值氧油比/(m3·kg-1)φ(CO2)/%φ(CO)/%φ(H2)/%φ(CH4)/%φ(O2)/%0.8938.05046.78742.9072.1 110.0100.98511.64947.79539.1201.1880.0521.05911.29948.77238.9630.770 0.0411.11715.76647.31736.2660.4300.0401.21114.72950.18034.7710.1500.0 401.27718.40848.91632.4700.0210.0211.42424.34747.05528.41100.021(a) CO,H2,CO2(b) CH4,O2图10 位置F各物质体积分数随氧油比变化3.2.4 位置G各物质体积分数表5给出了不同氧油比条件下位置G各物质体积分数径向均值.对气化反应来说,氧油比过低,将使气化温度降低,碳转化率降低;氧油比过高,将使合成气品质降低.从图11可以看出:随氧油比增大,CO2体积分数增大,CO体积分数基本不变,H2体积分数下降,CH4体积分数下降,O2体积分数基本为零.表5 位置G各物质体积分数氧油比/(m3·kg-1)/%φ(CO2)/%φ(CO)/%φ(H2)/%φ(CH4)/%φ(O2)/%0.8939.78943.88843.8882.3040.0470.98510.73649.13838.8141.1450.0421.05911.50348.89038.4140.9 390.0521.11716.02147.96435.5470.3140.0491.21115.00649.72134.9150.150 0.0581.27719.09948.00732.6240.0210.0501.42424.47646.46328.8320.0030.0 653.3 计算结果主要计算参数是每千克柴油冷煤气效率和有效气产率,具体计算过程见文献[10].试验条件见表3,对位置G进行计算,计算结果见表6.(a) CO,H2,CO2(b) CH4,O2图11 位置G各物质体积分数表6 位置G的一些计算参数氧油比/(m3·kg-1)有效气产率/(m3·kg-1)冷煤气效率/%碳转化率/%合成气量/(m3·h-1)0.8932.51777.66393.13511.3350.9852.31470.72195.82311.9341.0592.285 80.12196.94212.1131.1172.08577.78497.51312.3151.2112.09479.10298.177 12.4321.2771.92876.95398.50612.4971.4241.70474.60499.02412.574冷煤气效率为(11)每千克柴油有效气产率为(12)式中:ni为合成气中i组分的物质的量,mol;Y为冷气体效率,%;mi为合成气中i组分的质量,kg;md为柴油的进料量,kg/h;ΔHi为i组分的燃烧热;PCO+H2为每千克柴油有效气产率,m3/kg.由表6数据可知,最佳氧油比数值应为0.90~1.20 m3/kg,此时CO+H2体积分数达到最大值,且冷煤气效率最高.4 结论(1) 烘炉过程温度随时间线性增加,接近喷嘴位置的热电偶,从点火开始1 h内,升温速度很快,约9 ℃/min,而后升温速度逐渐变慢,约2 ℃/min.温度在1 000 ℃左右有一个拐点,升温速率分为两个线性区.CH4体积分数可作为指示气化炉温度的指标.(2) 喷嘴平面位置的各物质体积分数有不同程度的变化.从炉壁至径向6 cm之间,各物质体积分数变化很小,基本为一水平直线.从径向6 cm至炉中心15 cm处,CO、CO2体积分数基本为上升趋势,在炉中心处达最大值;H2、Ar体积分数基本上为下降趋势,在炉中心处达最小值;越接近炉中心,CH4体积分数越高,在炉中心位置有一最低值;不同径向位置,O2体积分数依然很低,没有大的变化,说明在高温下,炉内反应进行得很快.(3) 氧油比增加,燃烧反应加强,系统温度升高,气化进程加快.CO2体积分数增大,CO体积分数基本不变,H2体积分数下降,CH4体积分数下降,O2体积分数基本为零.最佳氧油比为0.90~1.20 m3/kg.参考文献:[1] Berman Y,Tamir A.Experimental investigation of phosphate dust collection in impinging streams (IS) [J].Canadian Journal of Chemical Engineering,1996,74(6):817-821.[2] Berman Y,Tanklevsky A,Oren Y,et al.Modeling and experimental studies of SO2 absorption in coaxial cylinders with impinging streams (I)[J].Chemical Engineering Science,2000,55(5):1009-1021.[3] Berman Y,Tanklevsky A,Oren Y,et al.Modeling and experimental studies of SO2 absorption in coaxial cylinders with impinging streams (II)[J].Chemical Engineering Science,2000,55(5):1023-1028.[4] Dehkordi A M.Application of a novel-opposed-jets contacting device in liquid-liquid extraction [J].Chemical Engineering and Processing,2002,41(3):251-258.[5] Chris Higman,Maarten van der Burgt.Gasification [M].USA:Elsevier Science,2003.[6] 王辅臣.射流携带床气化过程研究[D].上海:华东理工大学资源与环境工程学院,1995.Wang Fuchen.The Gasification Process Investigation for Jet-Entrained Gasifier [D].Shanghai:School of Resource and Environmental Engineering,East China University of Science and Technology,1995(in Chinese).[7] Smoot L D,Smith P J.Coal Combustion and Gasification[M].New York:Plenum Press,1985.[8] Masdin E G,Thring M bustion of single droplets of liquid fuel [J].Journal of the Institute of Fuel,1962,35(257):251-260.[9] 孙学信,陈建原.煤粉燃烧物理化学基础[M].武汉:华中理工大学出版社,1991.Sun Xuexin,Chen Jianyuan.Physical Chemistry Basis of Coal Fines Combustion [M].Wuhan:Huazhong University of Science and Technology Press,1991 (in Chinese).[10] 王辅臣,龚欣,吴韬,等.渣油气化炉工艺分析[J].大氮肥,1996,19(5):321-328.Wang Fuchen,Gong Xin,Wu Tao,et al.Technology analysis for residual-oil gasifier [J].Large Scale Nitrogenous Fertilizer Industry,1996,19(5):321-328 (in Chinese).。
催化裂化汽提器内颗粒停留时间分布的数值模拟
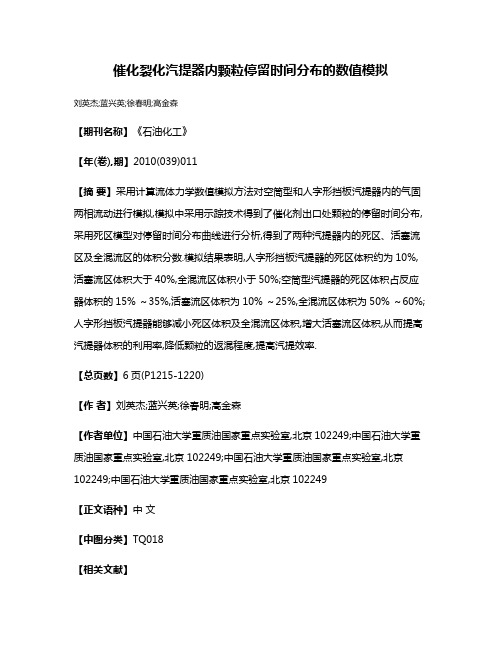
催化裂化汽提器内颗粒停留时间分布的数值模拟刘英杰;蓝兴英;徐春明;高金森【期刊名称】《石油化工》【年(卷),期】2010(039)011【摘要】采用计算流体力学数值模拟方法对空筒型和人字形挡板汽提器内的气固两相流动进行模拟,模拟中采用示踪技术得到了催化剂出口处颗粒的停留时间分布,采用死区模型对停留时间分布曲线进行分析,得到了两种汽提器内的死区、活塞流区及全混流区的体积分数.模拟结果表明,人字形挡板汽提器的死区体积约为10%,活塞流区体积大于40%,全混流区体积小于50%;空筒型汽提器的死区体积占反应器体积的15% ~35%,活塞流区体积为10% ~25%,全混流区体积为50% ~60%;人字形挡板汽提器能够减小死区体积及全混流区体积,增大活塞流区体积,从而提高汽提器体积的利用率,降低颗粒的返混程度,提高汽提效率.【总页数】6页(P1215-1220)【作者】刘英杰;蓝兴英;徐春明;高金森【作者单位】中国石油大学重质油国家重点实验室,北京102249;中国石油大学重质油国家重点实验室,北京102249;中国石油大学重质油国家重点实验室,北京102249;中国石油大学重质油国家重点实验室,北京102249【正文语种】中文【中图分类】TQ018【相关文献】1.催化裂化沉降器旋流快分器内气体停留时间分布的数值模拟研究 [J], 孙凤侠;卢春喜;时铭显2.工业催化裂化汽提器内气固停留时间的数值模拟 [J], 刘英杰;蓝兴英;刘旭阳;徐春明;高金森3.提升管CSVQS系统预汽提段颗粒速度和停留时间分布 [J], 赵爱红;鄂承林;王芬芬;卢春喜4.旋流反应器内颗粒停留时间分布的CFD模拟 [J], 黄峰;孙治谦;王振波;王亮;张玉春;金有海5.新型内构件填充床反应器数值模拟——Ⅰ.气相流场和停留时间分布 [J], 张学佳;程易;韩明汉因版权原因,仅展示原文概要,查看原文内容请购买。
流态化炉内物料停留时间分布的数学模型
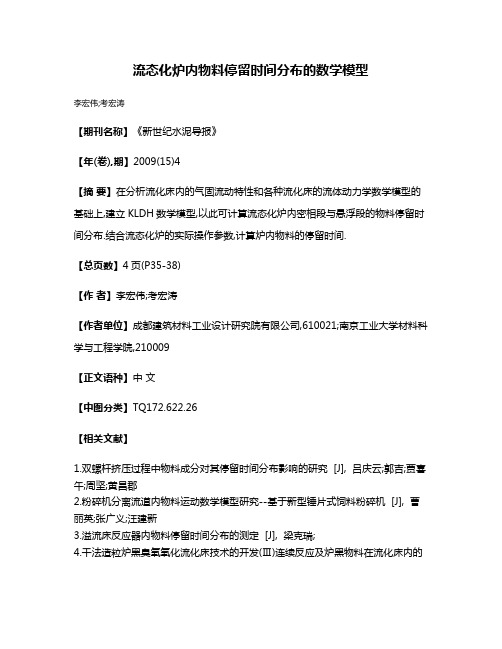
流态化炉内物料停留时间分布的数学模型
李宏伟;考宏涛
【期刊名称】《新世纪水泥导报》
【年(卷),期】2009(15)4
【摘要】在分析流化床内的气固流动特性和各种流化床的流体动力学数学模型的基础上,建立KLDH数学模型,以此可计算流态化炉内密相段与悬浮段的物料停留时间分布.结合流态化炉的实际操作参数,计算炉内物料的停留时间.
【总页数】4页(P35-38)
【作者】李宏伟;考宏涛
【作者单位】成都建筑材料工业设计研究院有限公司,610021;南京工业大学材料科学与工程学院,210009
【正文语种】中文
【中图分类】TQ172.622.26
【相关文献】
1.双螺杆挤压过程中物料成分对其停留时间分布影响的研究 [J], 吕庆云;郭吉;贾喜午;周坚;黄昌郡
2.粉碎机分离流道内物料运动数学模型研究--基于新型锤片式饲料粉碎机 [J], 曹丽英;张广义;汪建新
3.溢流床反应器内物料停留时间分布的测定 [J], 梁克瑞;
4.干法造粒炉黑臭氧氧化流化床技术的开发(Ⅲ)连续反应及炉黑物料在流化床内的
停留时间分布 [J], 彭辉;孙东凯;王锦凤;张济宇;刘振宇
5.注塑螺杆计量段物料的停留时间分布 [J], 于宇;马秀清;王之磊;王鹄
因版权原因,仅展示原文概要,查看原文内容请购买。
停留时间可控的撞击流反应器的设计与研究的开题报告
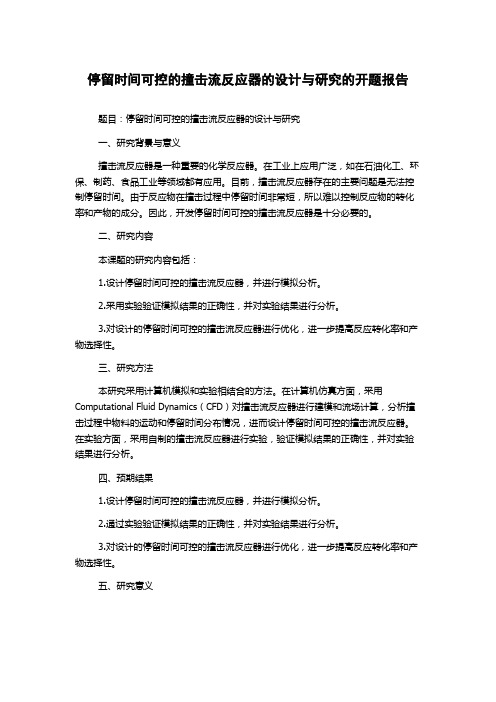
停留时间可控的撞击流反应器的设计与研究的开题报告题目:停留时间可控的撞击流反应器的设计与研究一、研究背景与意义撞击流反应器是一种重要的化学反应器。
在工业上应用广泛,如在石油化工、环保、制药、食品工业等领域都有应用。
目前,撞击流反应器存在的主要问题是无法控制停留时间。
由于反应物在撞击过程中停留时间非常短,所以难以控制反应物的转化率和产物的成分。
因此,开发停留时间可控的撞击流反应器是十分必要的。
二、研究内容本课题的研究内容包括:1.设计停留时间可控的撞击流反应器,并进行模拟分析。
2.采用实验验证模拟结果的正确性,并对实验结果进行分析。
3.对设计的停留时间可控的撞击流反应器进行优化,进一步提高反应转化率和产物选择性。
三、研究方法本研究采用计算机模拟和实验相结合的方法。
在计算机仿真方面,采用Computational Fluid Dynamics(CFD)对撞击流反应器进行建模和流场计算,分析撞击过程中物料的运动和停留时间分布情况,进而设计停留时间可控的撞击流反应器。
在实验方面,采用自制的撞击流反应器进行实验,验证模拟结果的正确性,并对实验结果进行分析。
四、预期结果1.设计停留时间可控的撞击流反应器,并进行模拟分析。
2.通过实验验证模拟结果的正确性,并对实验结果进行分析。
3.对设计的停留时间可控的撞击流反应器进行优化,进一步提高反应转化率和产物选择性。
五、研究意义本研究将开发停留时间可控的撞击流反应器,解决了该领域存在的主要问题,对于提高反应效率和产物成分的选择性具有重要意义。
同时,本研究还可为相关领域的发展提供新思路和新方法,促进该领域的发展。
- 1、下载文档前请自行甄别文档内容的完整性,平台不提供额外的编辑、内容补充、找答案等附加服务。
- 2、"仅部分预览"的文档,不可在线预览部分如存在完整性等问题,可反馈申请退款(可完整预览的文档不适用该条件!)。
- 3、如文档侵犯您的权益,请联系客服反馈,我们会尽快为您处理(人工客服工作时间:9:00-18:30)。
第59卷第3期 2008年3月
Journal
化
of Chemical
工
Industry
学
报
and Engineering(China)
V01.59 No.3 March 2008
撞击流气化炉内颗粒停留时间分布的随机模拟
倪建军,郭庆华,梁钦锋,于遵宏,于广锁 (华东理工大学资源与环境工程学院,煤气化教育部重点实验室,上海200237)
1.2颗粒的运动特性
气固两相流体在气化炉内的颗粒的碰撞行为具 有下列基本特点[1 6。:①颗粒在撞击区存在颗粒一
Table 1
表1冷模气化炉各个区域估算体积分数
Estimated volume fraction of every region for cold model gasifier
万方数据
冷模装置可以划分成4个射流区、4个射流回 流区、1个撞击区、2个撞击流股区、2个撞击流 回流区、1个折返流区和1个管流区。马波[151对连 续相流体做了整体的区域划分工作。而非连续相颗 粒流在气化炉中的撞击流动具有如下特点。
(1)射流区 由于射流速度很大,射流两侧颗 粒被卷吸回射流中形成射流回流区。
1 气化炉内流场分析
1.1气化炉流场划分 气化炉内颗粒流动是时间和状态都连续的马尔
可夫过程,运用该模型需要对状态和时间进行离 散。4个工艺喷嘴在同一水平面A上,相邻喷嘴轴 线夹角为90。,4股射流撞击。四喷嘴对置式气化 炉冷模装置的结构尺寸和流场结构见文献[15], 根据四喷嘴对置式气化炉流场的测试,可将气化炉 内部划分为若干区域状态。
过时间出后仍保留在原状态的概率。
因此,对于全混流反应器(CSTR)有
Pi—exp(一At/t。)
(i=1,2,…,N)
(10)
PF一半(1一A)(i,歹=1,2,…,N)(11)
厶q口
f≠j
对于平推流反应器(PFR),它的一步转移概
率Pd可表达为
f1
应器必定需要不同的时间。对离开反应器的流体, 上述时间的分布称为停留时间分布。同时进入反应 器的N个流体质点中,停留时间介于t与t+dt间
的质点所占分率导为E(f)出。因此,根据此定
义Ⅲ],停留时间分布密度函数具有归一化性质
,一
Ji E(t)dt=1
(4)
对于平推流反应器,由于所有流元在反应器中的停
摘要:根据多喷嘴对置式气化炉流场测试,将气化炉划分为若干区域,运用时间离散、状态离散的马尔可夫链
随机模型,模拟了气化炉内颗粒相的停留时间分布(RTD)。当颗粒在撞击区和射流区间的回流比为0.5,向下
撞击流股区和管流区为平推流模型,其他区域按全混流模型处理时,模拟值与实验值吻合较好。随着进料流量
的增大,平均停留时间减小,量纲1方差减小;随着回流比的增加,平均停留时间增大;气固两相平均停留时 间接近,但RTD存在一定差异。
Key words:residence time distribution;particle flow;Markov chain;gasifier
士
丘
在实际工业反应器中,反应器出El物料是所有
具有不同停留时间物料的混合物,反应器的实际转 化率是这些物料的平均值。为了准确地测定出口物 料的反应转化率,就必须准确地描述出口物料的停
第3期
倪建军等:撞击流气化炉内颗粒停留时间分布的随机模拟
‘569·
颗粒的碰撞,以及因碰撞导致的颗粒振荡运动;② 颗粒与气化炉炉壁存在碰撞;③颗粒间存在间隙 而并非充满整个流动空间。颗粒在撞击区的运动过 程如图1所示。
兰一x
Fig.1
图1撞击流中颗粒的运动 Particle moving in impinging region
Received date:2007—05—06. Corresponding author:Prof.YU Guangsuo.E--mail:gsyu@ ecust.edu crl Foundation item:supported by the National Basic Research Program of Ch如a(2004CB217703),Program for New Century Excellent Talents in University(NCET-06—0416),Shanghai Shuguang Training Program for the Talents(06SG34).
关键词:停留时间分布;颗粒流;马尔可夫链;气化炉
中图分类号:TQ 022
文献标识码:A
文章编号:0438—1157(2008)03一0567一07
Stochastic modeling of particle residence time distribution in impinging-streams gasifier
2007一05一06收到初稿,2007—10一25收到修改稿。 联系人:于广锁.第一作者:倪建军(1983一),男,硕士研 究生。 基金项目:国家重点基础研究发展计划项目 (2004CB217703),教育部新世纪优秀人才支持计划项且(NCET. 06—0416)l上海市教委曙光计划项目(06SG34).
(2)撞击区 相向流体撞击时,由于速度高, 时间短,部分颗粒将在撞击区发生碰撞,部分颗粒 直接溢出撞击区,或在后续流体的作用下做减幅振 荡[1引,振荡颗粒经若干次振荡后将离开撞击区进 入撞击流股区。
(3)撞击流股区 在保持连续流体流型的基础 上,向上流股由于与炉顶发生撞击,少量颗粒反弹 回撞击区形成振荡运动,部分进入折返流区;向下 流股直接进入管流区,两流股均有不同程度的卷吸 回流区。
Engineering,East China University of Science and Technology,Shanghai 200237,China)
Abstract:According to the flow field of opposed multi—burner gasifier,the gasifier was divided into several regions.The particle residence time distribution(RTD)in the gasifier was investigated with a stochastic model based on discrete time and state Markov chain.The results showed that the calculated results could give a reasonable fit to the experimental data when reflux ratio between jet stream region and impinging region was 0.5,the tube stream region and the downward impinging-stream region were regarded as plug flow reactor(PFR),others were considered as continuous stirred tank reactor(CSTR).Mcan residence time and dimensionless variance decreased with the increase of flow rate,while mean residence time increased with the increase of reflux ratio.Mean residence time was similar between gaseous phase and solid phase.
利用状态空间中获得的信息,即单步转移概率
矩阵P和初始概率向量s(O),就可以由下列公式
计算体系经过优+1步转移(跃迁)后处于状态_『
的概率
三 si(m+1)一艺8i(m)Po
(m=1,2,3,…) (2)
其中矩阵和向量的元素应满足下列条件
∑是(优)一1,∑P。一1
(3)
2.2状态向量与停留时间分布的关系 取不同路径并以不同方式运动的流体元通过反
NI Jianjun,GUO Qinghua-LIANG Qinfeng。YU Zunhong,YU Gaangsuo (Key Laboratory of Coal Gasification,Ministry of Education,School of Resource and Environmental
2模型建立
2.1马尔可夫链 设一随机序列{s。,咒≥0}的状态空间E是整
数集的某一子集(通常取E为所有非负整数集 合)。如果对于任意非负整数和任意i。,…,i。一。, i和_『∈E,有
力(s科1一J 50—io,…,Sn-1=i,卜1,晶=i)=
夕(5H1=j l如一i)
(1)
称之为离散时间尔可夫链m]。
万方数据
·568·
化
工
学
报
第59卷
留时间分布(RTD)。许多学者曾提出各种流动系 统的RTD显式数学表达式,大多采用确定型方 法[1],而对于复杂的流动系统,很难获得确定型的显 式数学表达式,有时甚至是不可能的。Danckwerts[z] 早在1953年就提出流元在连续流动系统中的停留 时间及其分布实质上是一随机过程,Alex等嘲运 用马尔可夫链验证了该结论。因此可以通过假设连 续流动系统内各个区域流动模型为理想全混流反应 器(CSTR)或平推流反应器(PFR),或两种流 动模式的某种组合,再进行随机模拟。很多学者对 复杂系统中物料停留时间分布的随机模拟做了大量 的研究,范良政等H1提出一个具有吸收态的马尔可 夫链模型,该模型为状态离散、时间离散的马尔可 夫过程,用于模拟连续流动系统内的RTD;Yu 等[5]采用该模型模拟了Texaco气化炉的RTD,得 出结果与实验值吻合;许寿泽等[6。3根据状态离散、 时间连续的马尔可夫链模型模拟了四喷嘴对置式气 化炉和Texaco煤气化炉的连续流动系统的RTD; Tamir等od妇提出的状态离散、时间离散的马尔可 夫链随机模型,模拟了两喷嘴对置撞击和切向撞击 的流元RTD。随机模拟多相流中颗粒RTD的研究 在流化床和填料床反应器中也得到了大量应用n21。 Hoffmann等[13]用马尔可夫链模型模拟了连续流化 床内的颗粒RTD;Mohan等[14]用马尔可夫链模型 研究了填料床中流元的停留时间和接触时间分布。