丰田式现场管理改善技术
现场管理PDCA(丰田)

-- 精品--
5W2H
What When Where Why Who
(内容)……………… 做什么? (时间,期限)…何时进行,何时完成? (地点,担当部门)……在何处进行? (目的)…………… 为什么进行? (人物)……谁负责?和谁一起合作?
How
-- 精品--
交货期意识
有计划性、遵守期限
-- 精品--
考虑工作的重要性、紧急性(要求期 限)、实施期间,制定日程
1、需要定期做的工作、可以预先开展的工作,应该尽 可能地利用空闲时间处理,留出空间以应付突发工 作。
2、工作总是有期限的。必须有效地使用时间、遵守规 定期限。
3、在工作全部完成之后,必须认真确认、以防失误。 4、如果实在完不成的话,要事先向领导汇报或同老员
理想与现实的差距=需要改善的地方
如何解决问题?
使问题表面化,找出其真正的原因,对症下药。
-- 精品--
所谓有能力的人
意即善于解决问题的人 在日常工作中能自觉地发现可改善的地方, 并思考如何创造性地进行改善。
-- 精品--
协调意识
重视团队精神
-- 精品--
在工作中,团队协作很重要。 1、如果每个人都按照自己的模式各行其是的 话,整个团队就会混乱,丧失团队的力 量。因此,要与周围的人员保持经常性的 沟通,密切联系,相互配合开展工作。 2、如果手头有空的话,应该积极主动地询问 工作繁忙的人,看其是否需要帮助。
计划
(Plan)
实际操作 (Do)
考核
(Check)
应对
(Action)
(这四个步骤互为循环,也是就我们通常所说的PDCA) 从而完成成果报告。 在这个过程中,及时的报告,联络, 讨论都是必不可少的。
TPS丰田精益生产管理之6S现场改善和目视管理
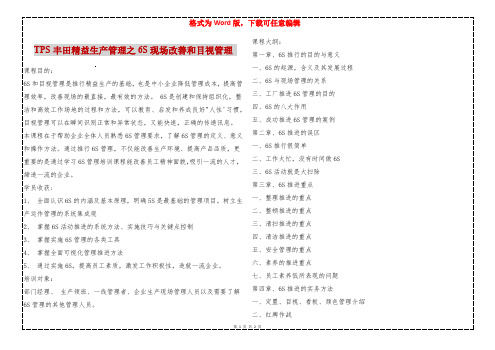
三、5W1H、思维方法及PDCA法
四、实景拍照及摄像前后对比法
第五章、6S推进组织及推进的步骤
一、推进组织结构及制度章程
二、推进小组工作目标及工作职责
三、推进小组人员素质要求
四、推进小组人员的培训
五、6S推进组织的工作内容
六、6S推进计划的策划及进度控制
七、推进6S的基本步骤
第六章、6S巡查与检讨
一、6S巡查的标准制定
二、6S巡查小组的建立及要求
三、巡查结果公开及透明化
四、如何将6S考核纳入绩效管理当中
五、如何提升员工的执行能力
最后:总结与探讨、问答与交流。
丰田现场管理方式(DOC 103页)

丰田现场管理方式(DOC 103页)丰田现场管理方式第一章利益的源泉来自制作方法作者: [日]门田安弘前言(1)———初版序言在最近数年经济增长低迷的情况下,产业界的关注点集中在了“丰田的现场管理”。
日本能率协会自昭和四十七年(1972)前后起,就在东京和大阪进行了几十次相关的研讨和演讲会,不论何时,听众都爆满。
当然这或许与讲师的阵容有关,他们是以丰田的大野耐一副社长为首的、开发“丰田的现场管理”并进行普及指导工作的生产管理部的管理人士。
为什么产业界非常需要这个研讨会呢?很荣幸,我几次都作为组织人员参加了研讨会,和大野副社长以及各个讲师们有过接触,从他们那里学来了不少东西,同时,通过他们和会场中的参加者热情的交流、回答质疑,我感到原因可能来自以下情况:各个企业对今后社会的经济状况都有顾虑,他们想摆脱现在严峻的经济态势,在竞争中获胜,更想从这个“丰田现场管理”的思想和实践中,探求一些真正的现场管理经验,并且通过其组织和运营,找到自信。
基于这样的认识,本书以日本能率协会举办的研讨会为基础,参考丰田提供的相关资料编辑而成。
我们的出版意图是,希望这本书能作为各个阶层的管理者和工作人员实践时可供参考的课本,也希望各位产业内的人士把大野语录作为座右铭去加以运用。
我最初接触“丰田现场管理”是二十年前,这期间,日本能率协会和丰田的密切关系已经相当久远了。
特别是关于“丰田现场管理”,我自身作为咨询顾问也受到强烈的吸引。
去年,我们举办了一个丰田现场视察研讨会,有三十多人参加,为期两天。
我们得出这样一个结论:在“丰田现场管理”严格发展的实践历史中,形成了真正的“实在”或者说是“纯粹”的思考方式。
让我们来看一看:经营过程是常有变动的,正是应对那种变化才是经营或管理。
为此,就需要在实践中形成企业的这种能力,要抓住变动中什么是异常情况,什么是重点,并在现场中进行实际看得到的管理。
不要隐藏问题和无益的东西,把它挖掘出来放到表面,特别是,要排除由于生产过剩而产生的一些隐患,越过这些隐患去发展企业是经营的罪恶。
《丰田式现场管理》课件

监控与反馈机制
监控与反馈机制是丰田式现场管理的重要环节。通过建立有效的监控和反馈系统,企业可以及时发现问 题、改进流程,并保持持续的学习和进步。
制定指标和目标
制定指标和目标是丰田式现场管理中的重要步骤。通过设定明确的指标和目 标,企业可以量化和监测绩效,并指导改进和决策。
建立标准化工作流程
建立标准化工作流程是丰田式现场管理的关键之一。通过规范和标准化工作流程,企业可以提高工作效 率、降低变异和错误。
丰田式现场管理在其他行业的 应用案例
丰田式现场管理不仅在汽车制造行业得到广泛应用,还在其他行业取得了成 功。通过案例研究,我们可以了解不同行业如何借鉴丰田式现场管理,实现 运营优化和绩效提升。
丰田式现场管理的起源和发展
丰田式现场管理起源于日本丰田汽车公司,并在20世纪50年代发展成为丰田 生产方式。这种管理方法得到了广泛应用,并对现代生产管理产生了重大影 响。
现场管理的重要性和优点
现场管理对于企业的运营和效益具有重要影响。它可以提高生产效率、减少浪费、提升质量、加强员工 参与和团队合作,从而实现更高水平的绩效和竞争力。
《丰田式现场管理》PPT 课件
这是一份关于丰田式现场管理的课件,通过讲述丰田式现场管理的起源、发 展和重要性,以及相关的管理原则和案例,帮助您了解并应用丰田式现场管 理的核心概念和代表的现代生产管理方法。它注重强调 实施现场改进、质量管理和人员参与,以提高效率、降低成本和提升质量。
空间管理
空间管理是丰田式现场管理中的关键环节。通过合理规划和优化空间布局,企业可以提高工作效率、减 少浪费和提升生产能力。
成本管理
成本管理是丰田式现场管理中的重要指标之一。通过优化生产流程和减少浪 费,企业可以降低成本,提高利润率和竞争力。
丰田现场管理技能水平提升培训标准作业
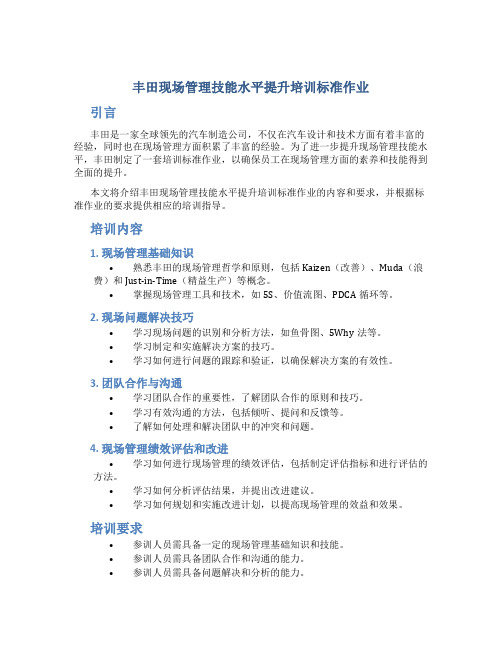
丰田现场管理技能水平提升培训标准作业引言丰田是一家全球领先的汽车制造公司,不仅在汽车设计和技术方面有着丰富的经验,同时也在现场管理方面积累了丰富的经验。
为了进一步提升现场管理技能水平,丰田制定了一套培训标准作业,以确保员工在现场管理方面的素养和技能得到全面的提升。
本文将介绍丰田现场管理技能水平提升培训标准作业的内容和要求,并根据标准作业的要求提供相应的培训指导。
培训内容1. 现场管理基础知识•熟悉丰田的现场管理哲学和原则,包括 Kaizen(改善)、Muda(浪费)和Just-in-Time(精益生产)等概念。
•掌握现场管理工具和技术,如5S、价值流图、PDCA循环等。
2. 现场问题解决技巧•学习现场问题的识别和分析方法,如鱼骨图、5Why法等。
•学习制定和实施解决方案的技巧。
•学习如何进行问题的跟踪和验证,以确保解决方案的有效性。
3. 团队合作与沟通•学习团队合作的重要性,了解团队合作的原则和技巧。
•学习有效沟通的方法,包括倾听、提问和反馈等。
•了解如何处理和解决团队中的冲突和问题。
4. 现场管理绩效评估和改进•学习如何进行现场管理的绩效评估,包括制定评估指标和进行评估的方法。
•学习如何分析评估结果,并提出改进建议。
•学习如何规划和实施改进计划,以提高现场管理的效益和效果。
培训要求•参训人员需具备一定的现场管理基础知识和技能。
•参训人员需具备团队合作和沟通的能力。
•参训人员需具备问题解决和分析的能力。
培训指导1. 现场管理基础知识培训•提供丰田现场管理哲学和原则的相关资料,组织参训人员进行学习和讨论。
•提供现场管理工具和技术的培训教材和实例,指导参训人员进行实践操作。
2. 现场问题解决技巧培训•提供现场问题解决技巧的培训材料和案例,引导参训人员进行实际问题的分析和解决。
•组织参训人员进行团队合作的训练和实践演练,提升其问题解决和团队合作的能力。
3. 团队合作与沟通培训•提供团队合作与沟通技巧的培训教材和案例,引导参训人员进行团队合作和沟通的练习和演练。
现场管理的卓越实践与标杆案例

现场管理的卓越实践与标杆案例引言现场管理是指对现场工作进行有效控制和监督的一种管理方法。
在各个行业中,现场管理被视为保证生产效率和顺利进行的重要因素之一。
卓越的现场管理实践可以帮助企业有效地提高工作效率、降低成本、提升产品质量以及改善员工安全和满意度。
本文将介绍一些在现场管理方面取得卓越实践的企业,并分析其标杆案例。
案例一:丰田汽车的现场管理实践丰田汽车是全球知名的汽车制造商,其现场管理实践一直被视为行业标杆。
丰田汽车在现场管理方面采用了“精益生产”(Lean Production)的方法,以最大限度地提高生产效率和产品质量。
丰田汽车注重员工参与和持续改进。
他们通过培养员工的创新和质量意识,鼓励员工积极参与现场管理,提出改善建议,并持续优化工作流程。
丰田汽车还实行了“错误防止”(Poka-yoke)的原则,通过在生产过程中引入自动化装置和检测设备,减少了人为错误,提高了产品质量。
另外,丰田汽车在供应链管理方面也取得了卓越的成果。
他们与供应商建立了紧密的合作伙伴关系,通过共享信息和资源,实现供应链的协同管理。
这种合作的方式不仅提高了供应链的敏捷性和灵活性,还降低了库存成本和交货周期。
案例二:沃尔玛的现场管理实践沃尔玛是世界最大的零售商之一,其现场管理实践也备受瞩目。
沃尔玛在现场管理方面注重供应链的协调和优化,以及仓储和物流的高效运作。
沃尔玛利用信息技术和数据分析工具来实现供应链的协同管理。
他们通过实时跟踪和监控销售数据和库存情况,以及与供应商进行紧密的合作,实现了快速响应市场需求和准确配送商品的目标。
沃尔玛还通过优化仓储和物流流程,实现了即时补货和最低库存的管理目标,降低了运营成本,并提升了顾客满意度。
此外,沃尔玛还注重员工的培训和参与。
他们通过提供培训和发展机会,激励和激发员工的工作激情和创造力。
沃尔玛鼓励员工积极参与现场管理,提出改进建议,并采取措施来实施这些改善措施。
以上介绍的丰田汽车和沃尔玛是在现场管理方面取得了卓越实践的企业,并成为行业的标杆。
丰田精益管理 现场管理与改善(图解版)

当问题发生时,现场管理者首先要做的事就是去现场,因为现场是所有信息的来源。问题发生后,现场管理 者能够随时掌握现场第一手的情况,观察事情的进展,并及时处理或向上级报告。
5S是管理的基础,是管理合理化的前提。它不但可以强化组织规范运作,将一个混乱的企业整理得井然有序
第1节现场安全教 育与培训
第3节现场事故处 理流程
1.1日常安全教业人员安全教育
2.1事故防范的工程技术措施 2.2事故防范的管理措施
3.1现场工伤事故的处理 3.2现场火灾的处理 3.3突发事件应急处理流程 3.4事故后的调查与改善
第2节持续改善的 工具
《丰田精益管理:现场管理与改善(图解版)》采用丰田精益管理的思想,为企业现场的改善与管理工作 提供了八项措施,具体包括5S现场管理法、现场目视管理、现场人员管理、现场设备管理、现场作业改善管理、 现场品质管理、现场安全管理和持续改善管理,目的是帮助企业消除浪费、提升产品和服务的质量,以获得利润, 实现企业健康、稳定、长远的发展。
精彩摘录
精益管理相对传统粗放式管理模式,就是要将具体的量化标准渗透到企业管理的各个环节中。精简冗余的消 耗,没有冗余的机构设置和产业流程,对企业的人力、物力和财力资源进行最大化的利用,以最小的成本投入实 现企业效益的最大化,为客户提供高附加值的产品或服务
丰田精益管理对企业在硬件方面的投入要求并不多,最主要的是时间的投入以及坚持正确的方式、方法。
第2节现场品质管 理工具
第1节现场品质管 理流程
第3节现场品质改 善方法
1.1事前控制 1.2事中控制 1.3事后控制
2.1亲和图法 2.2 PDPC法 2.3矩阵数据分析法 2.4关联图法 2.5矩阵图法 2.6系统图法 2.7箭线图法
丰田模式精益制造的14项管理原则

丰田模式精益制造的14项管理原则丰田模式,又称精益制造,是日本汽车制造商丰田公司在生产中积累的一套管理原则和方法论。
这套管理原则起源于丰田在20世纪80年代经历的危机时期,针对生产效率低下、质量问题和滞销等困境进行和优化。
经过多年的实践,丰田模式已经在全球范围内得到推广和应用。
丰田模式的核心思想是通过消除浪费,不断提高价值创造能力和质量水平,实现制造业的持续改善和优化。
这套管理原则包括14项原则,每个原则都涉及到企业的组织结构、流程设计、团队合作、持续改进等方面。
下面是丰田模式中的14项管理原则:1.长期质量优先:丰田公司将质量放在首位,追求零缺陷和完美品质。
2.以拉动方式而非推动方式进行生产:根据需求合理制定生产计划,避免过度生产和库存积压。
3.平衡生产:通过平衡各个生产环节和工作岗位的工作量,避免产能过剩或不足。
4.现场创新:鼓励员工提出改善建议,推动现场创新和问题解决。
5.人力积极发挥和培养:充分发挥员工的潜能,提供培训和发展机会,建立学习型组织。
6.标准化工作:制定标准化工作程序和作业指导书,提高工作质量和效率。
7.清理生产线:保持生产场地整洁有序,提高工作效率和品质水平。
8.花费创造价值的时间:减少非生产性活动,使员工的工作时间都用于创造价值。
9.使用可靠技术和设备:使用可靠的工具和设备,提高工作效率和质量。
10.组织层面的持续改进:建立改进的机制和流程,持续追求卓越和进步。
11.目标管理:设定明确的目标和标准,评估和改善绩效。
12.全员参与和团队合作:鼓励员工参与决策和管理,增强团队合作意识。
13.及时问题解决:立即解决生产中的问题,避免问题扩大化和延误。
14.指导性领导:领导者要起到激励和指导的作用,为员工提供支持和指导。
这些原则是丰田公司在生产实践中总结出来的,是一套科学且实用的管理手段。
丰田模式的核心目标是提高企业组织和流程的效率和质量,实现生产体系的优化和持续改进。
这套模式已经被广泛应用于制造业和服务业,成为现代管理的经典案例。
丰田的现场管理具体案例

丰田的现场管理具体案例
丰田汽车公司以其高效的现场管理而著称。
本文将介绍一个具体案例,展示丰田在现场管理方面的成功经验。
在这个案例中,丰田公司面对着一个生产线上的问题。
生产线上的一个关键零件出现了质量问题,导致整个生产线的停工。
丰田立即采取了行动,以确保生产线的顺利运行。
首先,丰田的现场管理团队立即成立了一个应急小组,由各个部门的专家组成。
小组成员迅速分析了问题的根本原因,并提出了解决方案。
这个小组确保了问题能够快速得到解决,避免了生产线停工时间的延长。
接下来,丰田采取了一系列措施来确保问题不再发生。
他们对生产线进行了全面的检查,并制定了更严格的质量控制标准。
丰田还加强了员工的培训和教育,以提高他们对质量的意识和责任感。
这些措施确保了质量问题得到了根本性的解决,并避免了类似问题再次出现。
此外,丰田还注重对现场管理的持续改进。
他们不断收集并分析生产数据,以找出潜在的问题和改进的机会。
丰田还积极借鉴其他公司的最佳实践,以进一步提高他们的现场管理能力。
通过这个案例,我们可以看到丰田在现场管理方面的成功经验。
他们能够快速地应对问题,并采取适当的措施来解决问题。
丰田还注重预防,以确保问题不再发生。
他们的持续改进和学习的态度使得他们的现场管理能力不断地提高。
总结起来,丰田的现场管理具体案例展示了他们在应对问题、质量控制和持续改进方面的成功经验。
这些经验对其他企业来说也具有借鉴意义,可以帮助他们提高生产效率和质量。
丰田模式 精益制造的14项管理原则
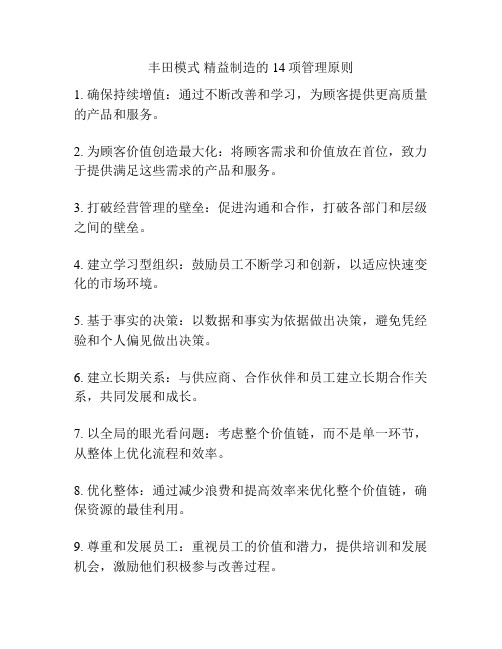
丰田模式精益制造的14项管理原则
1. 确保持续增值:通过不断改善和学习,为顾客提供更高质量的产品和服务。
2. 为顾客价值创造最大化:将顾客需求和价值放在首位,致力于提供满足这些需求的产品和服务。
3. 打破经营管理的壁垒:促进沟通和合作,打破各部门和层级之间的壁垒。
4. 建立学习型组织:鼓励员工不断学习和创新,以适应快速变化的市场环境。
5. 基于事实的决策:以数据和事实为依据做出决策,避免凭经验和个人偏见做出决策。
6. 建立长期关系:与供应商、合作伙伴和员工建立长期合作关系,共同发展和成长。
7. 以全局的眼光看问题:考虑整个价值链,而不是单一环节,从整体上优化流程和效率。
8. 优化整体:通过减少浪费和提高效率来优化整个价值链,确保资源的最佳利用。
9. 尊重和发展员工:重视员工的价值和潜力,提供培训和发展机会,激励他们积极参与改善过程。
10. 靠近现场解决问题:在现场发现和解决问题,避免问题的传导和误解。
11. 标准化工作方法:建立标准化的工作方法和流程,确保质量和效率的稳定性。
12. 反思和改进:不断反思和改进工作方式和方法,追求卓越和完美。
13. 充分利用技术和创新:利用先进的技术和创新的工具,提高生产效率和产品质量。
14. 突显领导力:培养和推崇有远见、能够激励员工并推动组织发展的领导力。
丰田现场的改善实例

☆丰田现场的改善实例 实例一实例二小点滴汇成大智慧丰田公司从创立至今,一直没有停止改善的步伐。
改善是丰田人最熟知的字眼,也是丰田公司永恒不变的话题。
今天的丰田,改善不断进化,已经很难找到效果在1分钟以上的问题点。
丰田公司对浪费已经“计较”到了每一个动作。
“一步一秒一日元”,这是对动作和成本最直接的诠释。
多走动一步,就多浪费一秒,就等于扔了一日元。
把浪费直接换算成金额,非常直观。
正是基于这个观点,丰田公司把改善一步一步做到极致。
员工的眼光已经关注到几秒,甚至零点几秒的问题点上。
别小看了这零点几秒,一次操作零点几秒,累加起来,一天就是几分钟,以丰田一分钟一台车的节拍来看,几分钟的浪费,就已经影响几台车的产出!正如图中所示,这些改善看起来都是很小的点的改善,但是正因为有了这样一个一个的点,才能最终汇集形成线、形成面、形成体,从而最终变成企业强大的力量。
在企业精益生产推动过程中,改善提案活动是激活员工智慧,推动全员参与、持续改进的有力武器。
国内很多企业,也都认识到了改善提案活动的重要性,大多会有一个部门或者科室专门负责统计改善提案。
公司想出了种种激励措施,来鼓励员工积极创新,多提改善建议。
但是到了年底一看统计数字,往往都是失望的。
甚至有些部门一年的人均改善提案才零点零几。
与丰田公司人均12条以上的差距,不言而喻。
这个差距究竟是怎么产改善前:要取的件掉在盒子里。
盒子空间有限,伸手进去拿,费力不好拿。
改善后:用两根托钩取代了原来的盒子。
零件滑落下来,掉在托钩上,伸手就能轻松拿到!改善效果:1.0秒改善前:开关太小,每次按的时候都要仔细分辨,不容易操作。
改善后:开关加大,容易操作了。
改善效果:0.5秒8实例三实例四生的呢?这与我们对待提案的态度有关。
总觉得既然是提案,一定是要为公司创造几万甚至几十万的效益才行。
几秒钟,也就是动动手、挪挪位置的改善,往往都被忽略了。
不单单是操作者有这样的想法,就连审查改善建议书的管理层也有这样的想法。
精益管理方法—丰田式改善培训课件
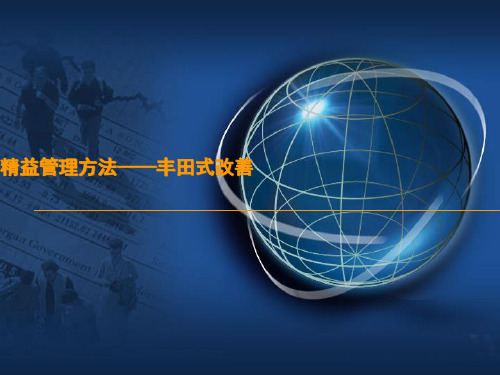
6. 彻底地思考和执行
再三思考、怀着“决不放弃”的强大 意志和坚忍不拔的精神,将工作进行 到最后
7. 速度・时机
迅速对应客户需求,贯彻实施对策。
如果对策的实施尚需要一定时间,可采取适当措施, 以免错失良机
8. 诚实・正直(实事求是)
进阶篇
在处理新业务或范围广的业务、或制定方 针时所需要的工作的“经验技巧”
丰田工作方法的开发背景
海外
随着丰田汽车事业的国际化, 为使其价值观可视化,制定了 《Toyota way 2001》
日本
针对年轻员工工作能力低下,从 2000年开始加强丰田工作方法的 培训
尽管“Toyota way”目前已在全世界 的事业体中广为人知。 但仍然有很多员工,甚至是管理层 都不知道如何才算真正实践了 Toyota Way
问题发生在哪个环节?
问题发生的环节
为什么一定要确定 问题发生的环节呢?
是为了有效率地 分析真因。
Step 2.分解问题
Process 3. “现地现...
理想状态
差距=问题
现状
对所承担的业务怀有高度的问题意识
要点 1) 自己工作的基本功要扎实; 2) 明确自己工作的目的; 3) 站在客户角度考虑问题; 4) 对变化敏感; 5) 了解竞争对手水平 。
…etc.
摒弃“有问题是坏事”的意识
• 丰田并不认为“有问题”是件坏事。
有划痕的车辆
不好的切入点
好的切入点
1班
2班
底盘
前装
轿车
箱车
后装
Step 2.分解问题
Process 2.确定自身要着手解决的问题
丰田管理模式TPS技法

二、看板管理
看板管理方法是在同一道工序或者前后工序之间进行物流或信息流的传递。
看板种类:
1.工序内看板 工序内看板是指某工序进行加工时所用的看板。这种看板用于装配线以及既 使生产多种产品也不需要实质性的作业更换时间(作业更换时间接近于零) 的工序,例如机加工工序等。典型的工序内看板如表。
二、看板管理
2.加工的浪费 加工的浪费也叫过分加工的浪费,主要包含两层含义:第一是多余的加工和 过分精确的加工,例如实际加工精度过高造成资源浪费;第二是需要多余的 作业时间和辅助设备,还要增加生产用电、气压、油等能源的浪费,另外还 增加了管理的工时。
一、七大浪费
3.动作的浪费 动作的浪费现象在很多企业的生产线中都存在,常见的动作浪费主要有以下 12种:两手空闲、单手空闲、作业动作突然停止、作业动作过大、左右手交 换、步行过多、转身的角度太大,移动中变换“状态”、不明技巧、伸背动作、 弯腰动作以及重复动作和不必要的动作等,这些动作的浪费造成了时间和体 力上的不必要消耗。
4.搬运的浪费 从JIT的角度来看,搬运是一种不产生附加价值的动作,而不产生价值的工作 都属于浪费。搬运的浪费具体表现为放置、堆积、移动、整列等动作浪费, 由此而带来物品移动所需空间的浪费、时间的浪费和人力工具的占用等不良 后果。 国内目前有不少企业管理者认为搬运是必要的,不是浪费。因此,很多人对 搬运浪费视而不见,更谈不上去消灭它。也有一些企业利用传送带或机器搬 运的方式来减少人工搬运,这种做法是花大钱来减少工人体力的消耗,实际 上并没有排除搬运本身的浪费。
“一个流”生产的概念 所谓“一个流”生产,是指将作业场地、人员、设备(作业台)等进行合理 配置,使产品在生产时,每道工序最多只有一个在制品或成品,从生产开 始到完成之前,没有在制品放置场地及入箱包装的作业。为了实现“一个 流”生产,必须将设备的布置进行调整,不是按类型布置,而是根据加工 工件的工序进行布置(称为垂直布置),形成相互衔接的生产线。
丰田巨额利润的秘密科学的现场管理

丰田巨额利润的秘密科学的现场管理丰田汽车公司是全球汽车行业的领导者之一,其取得的巨额利润一直是业内瞩目的焦点。
众所周知,丰田的成功得益于其科学的现场管理方法,这正是其利润高企的秘密所在。
本文将探讨丰田巨额利润的背后,揭示其科学的现场管理所扮演的关键角色。
1. 现场管理的重要性现场管理是指企业在生产过程中,对工人和设备进行调度和管理,以确保生产效率最大化的一种管理方法。
丰田秉持着“现场是真理”的原则,将现场视为改善和提高效率的关键驱动力。
通过科学的现场管理,丰田成功地实现了生产线的高度流动性、员工的高效协作以及缺陷的最小化。
2. JIT生产系统的应用丰田首创了“Just-In-Time(JIT)”生产系统,通过减少库存和生产过程中的浪费,实现了生产的精益化。
丰田将自己视为“生产者而非商人”,致力于在客户下单后尽快交付产品,以实现库存的最小化。
这种精准的生产调度和库存控制使得丰田能够避免过剩的库存和降低生产成本,从而实现了巨额利润的增长。
3. Jidoka原则的落实Jidoka原则是丰田生产方式的重要组成部分,它强调在生产过程中实现自动化和自检测,以避免缺陷的产生。
丰田引入了人工智能和自动化设备,通过机器监测和识别生产中的异常情况,并立即触发停机,以避免缺陷产品的进一步制造。
这种自动化和自检测的原则不仅提高了产品质量,也降低了成本,为丰田带来了巨额利润。
4. Kaizen持续改善的文化丰田注重持续改善的文化,通过Kaizen(改善)活动来推动全员参与的持续改善。
丰田鼓励员工主动发现问题、提出改进意见,并通过小步快走的方式实施改变。
丰田坚信,持续改进是实现卓越的关键,只有通过持续的改善才能保持竞争优势和不断创新。
这种注重改善的文化使得丰田能够提高生产效率、优化流程,从而改善利润水平。
5. 人力资源管理的关键作用除了科学的现场管理方法,丰田还注重人力资源管理的重要性。
丰田致力于培养员工的技能和专业知识,通过培训和提升机制,建立员工与企业共同成长的关系。
丰田管理方法
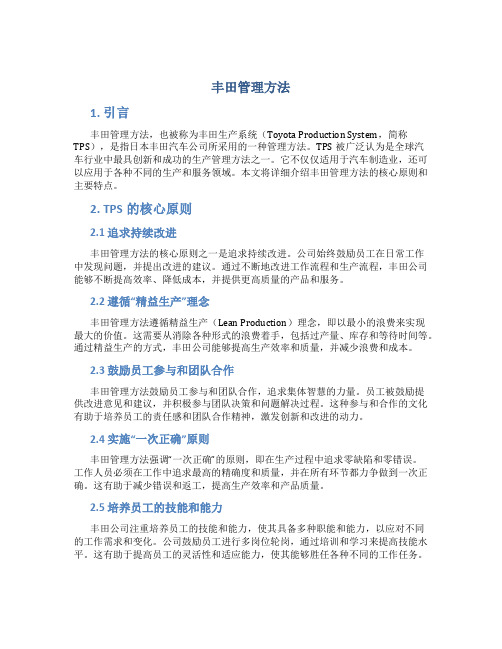
丰田管理方法1. 引言丰田管理方法,也被称为丰田生产系统(Toyota Production System,简称TPS),是指日本丰田汽车公司所采用的一种管理方法。
TPS被广泛认为是全球汽车行业中最具创新和成功的生产管理方法之一。
它不仅仅适用于汽车制造业,还可以应用于各种不同的生产和服务领域。
本文将详细介绍丰田管理方法的核心原则和主要特点。
2. TPS的核心原则2.1 追求持续改进丰田管理方法的核心原则之一是追求持续改进。
公司始终鼓励员工在日常工作中发现问题,并提出改进的建议。
通过不断地改进工作流程和生产流程,丰田公司能够不断提高效率、降低成本,并提供更高质量的产品和服务。
2.2 遵循“精益生产”理念丰田管理方法遵循精益生产(Lean Production)理念,即以最小的浪费来实现最大的价值。
这需要从消除各种形式的浪费着手,包括过产量、库存和等待时间等。
通过精益生产的方式,丰田公司能够提高生产效率和质量,并减少浪费和成本。
2.3 鼓励员工参与和团队合作丰田管理方法鼓励员工参与和团队合作,追求集体智慧的力量。
员工被鼓励提供改进意见和建议,并积极参与团队决策和问题解决过程。
这种参与和合作的文化有助于培养员工的责任感和团队合作精神,激发创新和改进的动力。
2.4 实施“一次正确”原则丰田管理方法强调“一次正确”的原则,即在生产过程中追求零缺陷和零错误。
工作人员必须在工作中追求最高的精确度和质量,并在所有环节都力争做到一次正确。
这有助于减少错误和返工,提高生产效率和产品质量。
2.5 培养员工的技能和能力丰田公司注重培养员工的技能和能力,使其具备多种职能和能力,以应对不同的工作需求和变化。
公司鼓励员工进行多岗位轮岗,通过培训和学习来提高技能水平。
这有助于提高员工的灵活性和适应能力,使其能够胜任各种不同的工作任务。
3. TPS的主要特点3.1 供应链管理丰田管理方法不仅仅关注内部的生产和运营,还注重整个供应链的管理。
(丰田管理)丰田式管理
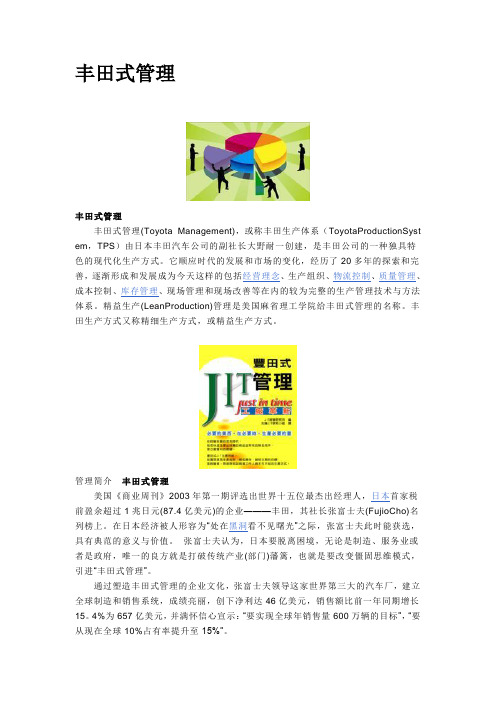
丰田式管理丰田式管理丰田式管理(Toyota Management),或称丰田生产体系(ToyotaProductionSyst em,TPS)由日本丰田汽车公司的副社长大野耐一创建,是丰田公司的一种独具特色的现代化生产方式。
它顺应时代的发展和市场的变化,经历了20多年的探索和完善,逐渐形成和发展成为今天这样的包括经营理念、生产组织、物流控制、质量管理、成本控制、库存管理、现场管理和现场改善等在内的较为完整的生产管理技术与方法体系。
精益生产(LeanProduction)管理是美国麻省理工学院给丰田式管理的名称。
丰田生产方式又称精细生产方式,或精益生产方式。
管理简介丰田式管理美国《商业周刊》2003年第一期评选出世界十五位最杰出经理人,日本首家税前盈余超过1兆日元(87.4亿美元)的企业———丰田,其社长张富士夫(FujioCho)名列榜上。
在日本经济被人形容为“处在黑洞看不见曙光”之际,张富士夫此时能获选,具有典范的意义与价值。
张富士夫认为,日本要脱离困境,无论是制造、服务业或者是政府,唯一的良方就是打破传统产业(部门)藩篱,也就是要改变僵固思维模式,引进“丰田式管理”。
通过塑造丰田式管理的企业文化,张富士夫领导这家世界第三大的汽车厂,建立全球制造和销售系统,成绩亮丽,创下净利达46亿美元,销售额比前一年同期增长15。
4%为657亿美元,并满怀信心宣示:“要实现全球年销售量600万辆的目标”,“要从现在全球10%占有率提升至15%”。
TPS的由来20世纪后半期,世界汽车工业进一个市场需求多样化的新阶段,而对质量的要求也越来越高,这就给制造业提出了这样一个新课题:只有有效地组织多品种、小批量生产,避免生产过剩所引起的设备、人员、库存、资金等一系列资源浪费,以保持企业竞争能力。
在这种历史背景下,从丰田相佐诘开始,经丰田喜一郎及大野耐一等人的共同努力,综合了单件生产和批量生产的特点和优点,创造了一种多品种、小批量混合生产条件下高质量、低消耗的生产方式。
丰田车的管理模式
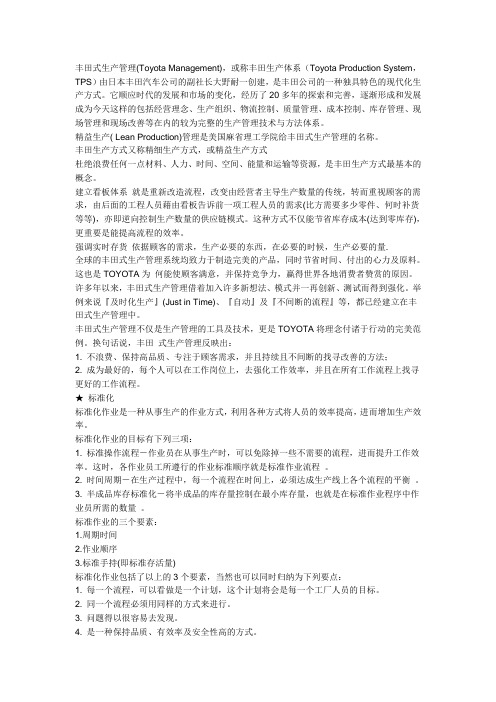
丰田式生产管理(Toyota Management),或称丰田生产体系(Toyota Production System,TPS)由日本丰田汽车公司的副社长大野耐一创建,是丰田公司的一种独具特色的现代化生产方式。
它顺应时代的发展和市场的变化,经历了20多年的探索和完善,逐渐形成和发展成为今天这样的包括经营理念、生产组织、物流控制、质量管理、成本控制、库存管理、现场管理和现场改善等在内的较为完整的生产管理技术与方法体系。
精益生产( Lean Production)管理是美国麻省理工学院给丰田式生产管理的名称。
丰田生产方式又称精细生产方式,或精益生产方式杜绝浪费任何一点材料、人力、时间、空间、能量和运输等资源,是丰田生产方式最基本的概念。
建立看板体系就是重新改造流程,改变由经营者主导生产数量的传统,转而重视顾客的需求,由后面的工程人员藉由看板告诉前一项工程人员的需求(比方需要多少零件、何时补货等等),亦即逆向控制生产数量的供应链模式。
这种方式不仅能节省库存成本(达到零库存),更重要是能提高流程的效率。
强调实时存货依据顾客的需求,生产必要的东西,在必要的时候,生产必要的量.全球的丰田式生产管理系统均致力于制造完美的产品,同时节省时间、付出的心力及原料。
这也是TOYOTA为何能使顾客满意,并保持竞争力,赢得世界各地消费者赞赏的原因。
许多年以来,丰田式生产管理借着加入许多新想法、模式并一再创新、测试而得到强化。
举例来说『及时化生产』(Just in Time)、『自动』及『不间断的流程』等,都已经建立在丰田式生产管理中。
丰田式生产管理不仅是生产管理的工具及技术,更是TOYOTA将理念付诸于行动的完美范例。
换句话说,丰田式生产管理反映出:1. 不浪费、保持高品质、专注于顾客需求,并且持续且不间断的找寻改善的方法;2. 成为最好的,每个人可以在工作岗位上,去强化工作效率,并且在所有工作流程上找寻更好的工作流程。
- 1、下载文档前请自行甄别文档内容的完整性,平台不提供额外的编辑、内容补充、找答案等附加服务。
- 2、"仅部分预览"的文档,不可在线预览部分如存在完整性等问题,可反馈申请退款(可完整预览的文档不适用该条件!)。
- 3、如文档侵犯您的权益,请联系客服反馈,我们会尽快为您处理(人工客服工作时间:9:00-18:30)。
没有在制品闲置,含入箱包装作业
之前。 它的含义包括:
1) 每道工序加工完一个工件后立即流到下一工序;
2)
制件的运动不间断、不超越、不落地;
七.丰田生产方式的动态自我完善机制--11
十三、现场管理的两大基础--------33 十四、彻底的现场5S管理----------34 十五、定置定位改善--------------37 十六、目视管理------------------38 十七、看板管理------------------39 十八、污染源改善----------------40 十九、干部的影子----------------21 二十、改善是现场管理的核心------42 二十一、提高现场管理能力的基本步骤--45 二十二、学习管理工具------------50 二十三、改善是一门技术----------51 二十四、全员管理提升------------53
丰田生产方式的 动态自我完善机制
---丰田及时化生产方式的过 人之处,就是在于它本身具有一种内在 的不断自我完善机制“强制性揭露问题, 暴露隐患”而这种强制性的手段就是看 板管理。看板管理迫使生产系统中存在 的问题和隐患在不平稳中显露出来,如 设备保养不善,加工能力不均衡,作业 人员技能差异,工序作业衔接不良等。 通常 这些问题和隐患都被过量的在制 品储备所掩盖了当这些问题和隐患显露 出来之后,现场管理人员和作业人员就 针对问题提出改善的设想与措施,来消 除问题,使生产系统达到新水平的稳定。
最大的浪费
上面提到库存是万恶之源,而制造过多或提早完成,在丰田则被视为最大的浪费. 丰田生产方式所强调的是"适时生产",也就是在必要的时候,做出必要的数量的必要的东西。此外 都属于浪费。而所谓必要的东西和必要的时候,就是指客户已决定要买的数量与时间。假设客户只要 100个,而每个1元,如果生产了150个,这售价却不会是150元,因为多余的50个并没有卖出去,仅是 变成库存,因此利润也就无从产生,换句话说,多做了是浪费。而制造过早同样也是浪费,但为什么 有很多工厂会一而在地过多与过早制造呢?最大的原因在于他们不明白这是一种浪费,反而以为多做 能提高效率,提早做好能减少产能损失(不做白不做,机器还不是一样停着?),显然这是一种极大 误解。认为制造过多与过早能够提高效率或减少产能的损失,是见树不见林的看法,因为真利润的产 生,是从销售而来而不是效率与产能。为了看到更多的效率与产能,制造过多与过早而销售量并没增 加,仅是增加了库存量,你说这合算吗?因此丰田生产方式强调,绝不允许制造过多(早),因为, 只有浪费,无任何益处!
时间分析的主要用途
1.作为改善生产效率的重要手段. 工厂内的生产活动因为各种原因会产生时间的浪费,通过对时间使用及效果 进行定量测量,把不合理的地方找出来进行改善,使生产效率提到提升. 2.作为设定标准工时的重要依据. 通过时间分析,可以掌握各项作业所需时间的基本资料,再根据标准工时的设 定方法,定出标准工时. 3.作为制造系统规划和改善的依据. 掌握作业时间的基本资料后,通过计算可以为制造系统的规划设计和改善提 供很大的帮助,可体现在:①生产线平衡分析与改善.②联合作业方法的设定.③ 设备投资安排规划.④生产布局的设计.⑤决定一名操作者操作机械设备的台数. 4.作为评价作业者技能和工程管理水平的依据. 有了基准,就可以作为评价的工具.作业者生产相同产品的时间比基准时间 长,则说明作业者熟练程度不够或时间安排不合理,需要加以教育及指导. 5.作为成本分析的重要依据. 成本分析如果使用事后分析,则往往出入很大,而且不利于成本控制.目前一 般是把单位产品所包含的材料耗用,制造工资支出,设备分摊,管理费用等予以 标准化,定出标准成本,作为管理目标.而时间分析为此提供了方便.
时间分析概述 效率以时间为基准来衡量的
古往今来,不知有多少先贤曾感叹过时光易逝,韶华难追.懂得利用时间 的人觉得时间很宝贵,一分一秒都不让他白过.不懂得利用时间的人觉得 时间很无情,总在时间消逝之后来追悔自己无作为. 对于追求投资回报的企业来说,“时间就是金钱”不同的企业利用时间 的能力也参差不齐,这是企业成败的一大关键!在同样的时间里,谁的产 出多,谁的效率就高,谁就掌握竞争优势,这是毋庸置疑的. 许多企业都知道要提高效率,却总是以定性的方法来进行,结果许多 时间在不知不觉中浪费掉了却不感到可惜.须知,效率是以时间为基准来 衡量的.对时间和产出进行定量的分析才是提高效率的堂堂正正之道. 所谓时间分析,就是针对时间及产出做定量的分析,找出时间利用不 输工序合为一体; 4) 只有合格的产品才允许往下道工序流.
“自动化” Jidoka)
---“自动化”是丰田及时化生产体系质量保证的重 要手段,日语中的Jidoka(自动化)有两种涵义。 ---“自动化”的意思,表示用机器来代替人工,这样的自动工 作机器没有发现加工质量缺陷的能力,也不会在出现加工质量缺陷 时停止工作,依然有可能会产出大量的不合格制品。 ---丰田公司强调的是Jidoka的另一个涵义,即“自动化缺陷控 制”并称为“带有人字旁的自动化”或“具有人类判断力的自动化” 「自働化」完整的说是一种发现异常质量缺陷的技术手段,一旦机 器在动作时发现不良产生时,机器会自动停止工作。 ---丰田公司的“自动化缺陷制”主要通过三个主要的技术手段 来实现的,就是异常情况的自动化检测,异常情况下的自动化停机, 异常情况的自动化报警。
公式二:
(供应<需求)
它是一种基于成本的定价方法,称之为成本主义 .
利润=售价-成本
(供应>需求)
它的经济意义是价格由市场决定,企业要获得利润就要学会降低成本 丰田公司采用后一公式,即汽车的售价是按市场行情定的,这样, 为了获得利润,就要尽量降低成本,这就是产生利润的源泉 .
利益的源泉来自制作现场与方法
没有管理的紧张感,阻碍改善的活性化
---库存量一多,机械故障不会马上有大的影响,故对策可以 慢慢来,不良品产生也一样,对策可以慢慢来。同样的,换模时 间也永远不会排在优先解决之列,而变成没有什么需要了。
前面一片平静 似乎没问题
不设 良计
机 械 故 障
产 品 不 良
材 料 不 良
庫存多就 如水位高 将暗礁 (问题) 隐藏住了。 不产 均能 过人 多员
商业企业,把购进的商品加上一定的盈利,定出销售价格.
工业企业,把制造出的产品定出价格,销售出去赚钱. 利润永远都是售价与成本之差.获得利润无非是要么提高售价,要么降 低成本,要么两者都用
企业经营观比较
所谓成本主义,是指认为在制造产品时花费了一定的成本,所以售 价应是成本加上适当的利润, 公式一:
售价=成本+利润
---丰田公司为了实现 “少人化”和“省人化”, 在各个工作场所只配备最低 限度的作业人员,全体作业 人员加班已经成了平常的事 了,如果需求减少了,或者 是引进了机器人的话,就可 以不用解雇作业人员或让其 停职,而是减少加班了。
什么是TPS?
---TPS(Toyota Production System)是丰田生产方式的简 称,是为实现企业对员工、社会和产品负责的目的,以彻底杜绝浪费 为目标,在持续改善的基础上,采用准时化、自働化方式与方法, 追求制造产品合理性的一种生产方式。 ---是战后日本汽车工业遭到“资源稀缺”和“多品种、 少批量”的市场制约的产物,它是从丰田佐吉开始,经丰田喜一郎 及大野耐一等人的共同努力才逐步完善的一种生产方式。 ---TPS既是一种以最大限度地减少企业工厂所占用的资源 和降低企业管理及运营成本为主要目标的生产方式,同时它又是一 种理念,一种文化.实现TPS就是决心追求完美的历程,也是追求卓 越的过程,它是支撑个人与企业生命的一种精神力量,也是在永无 止境的学习过程中获得自我满足的一种境界.其目标是精益求精, 永无止境地追求尽善尽美.
丰田式现场管理改善技术
目录
一.前言---------------------------1 二.工业利润来自制造现场-----------3 三.什么是TPS?--------------------5 四.丰田生产方式支撑架构-----------6 五.认识七大浪费-------------------7 六.常见三种现象-------------------8
丰田生产方式支撑架构
TPS
工时观测法 工程别能力表(L/T) 山积表(T/T) 表准作业组合票(C/T) 标准作业票(C/T=T/T) 多能工技能评价与培训 (省人化) (柔性化)
平准化
J
I
T
必 要 种 类
自働化
补充架构
必 要 时 间
必 要 数 量
品 质 保 证
丰田生产方式的技术体系核心
---丰田生产方式是一个包容了多 种制造技术和管理技术的综合技术体系, 要实现“彻底降低成本”这一基本目标, 就必须彻底杜绝过量生产及由此而产生的 在制品过量和人员过剩等各种直接浪费和 间接浪费,因此“及时化生产”这种手段 是丰田生产方式的核心。
流线化生产(one piece flow)
常见三种现象
工作能力 工作能力
有能力而未给予充分的工作量;
工作量时多时少;
工作能力
超负荷生产:精神、体力、安 全、品质、效率很难提升。
库存是万恶之源
● 库存:一切暂时不用的资源.●为满足未来需要的而准备的原材料;
● 加工过程中的在制品; ●未销售的成品;
由於库存量的存在,设备能力不平衡时也看不出(库存越多,越不容易看出来)。人员是否过剩, 也无法了解。由於有较多的库存,供应部门需要增加人员,制造一线需要更多的人员来生产产品 用於补充库存,需要增添设备来保证生产库存所需要的设备能力,从而形成新一轮的浪费。 到底为什么要有库存量,最大的理由是"怕出问题"——出现故障怎么办?会不会因部分设备出问题, 而影响整条生产线或工厂的生产呢?於是乎为了不使影响扩大,库存便成了必要,衆多的问题也被隐 藏起来,所以进步、赚钱的步调自然变慢了。无怪乎丰田生产方式称库存为万恶之源,绝对不允许它 存在,如果现在已经有了库存,也要想尽一切办法,将之降低,力争零库存。(尽量减到最少的必要 的程度。)