浅谈长大隧道TBM拆卸洞施工技术
TBM在长隧道施工中存在的问题及发展趋势

2006 NO.2SCIENCE & TECHNOLOGY INFORMATION工 程 技 术火灾本层:各光标灯启动。
方向朝火警点的反方向闪动;各出口标志灯启动应急,关闭处于火警点的出口标志灯。
其他出口标志灯频闪,并语音广播。
火灾层上层:视火灾层火势、烟雾的具体走势而定。
在案例中,火警发生于楼道内,烟雾走向向右,因此火灾层右边的光标灯和出口灯就近指引,而上层右边的光标灯反向,出口灯关闭,因为该楼梯下面正是烟雾蔓延区。
火灾层的下一层及地下层:按默认方式启动应急,即启动应急各出口标志灯及其语音,疏散光流灯、可调向疏散指示标志灯就近指引。
所有底层设备都受控于中央主机,其工作状态,应急方案显示在操作界面上并记录于数据库中,异常状态有声光报警,同时打印输出。
6.结束语我们相信上述系统在具体应用中会不断地推陈出新,顺应市场和迎合客户的需要,凭借其自身的高端品质和开放的技术平台,实施针对每个工程的个性化设计,依据系统自身突出的网络优势和无限拓扑的特点,应用于各类建筑工程项目。
当然,随着科技的进步,建筑的新要求,在这一逃生领域中,还需在智能消防应急照明疏散指示逃生系统上做不断的完善,使其在火灾时发挥更大的作用。
参考文献[1] 建筑设计防火规范(GBJ16-1987). 北京:中国计划出版社. 1997[2] 火灾自动报警系统设计规范(GB50116). 北京:中国计划出版社. 1999[3] 智能建筑设计标准(GB/T50314-2000). 北京:中国计划出版社. 2000隧道掘进机英文名称是Tunnel Boring Machine,简称TBM。
隧道(洞)长度过长时,用常规钻爆法进行隧道施工将需要相当长的工期,隧道掘进机法施工则适合长隧道施工的需要。
根据国外实践证明:当隧道长度与直径之比大于600时,采用TBM进行隧道施工是经济的。
TBM法与钻爆法相比,其主要优点是掘进速度快,所以配套系统是满足连续快速掘进的关键因素,其运输布置、运输能力、供水、排水流量、通风方式及风压、风量以及喷锚、混凝土管片安装、豆砾石喷射、回填灌浆的速度,必须与掘进速度相匹配。
TBM洞内拆机方案
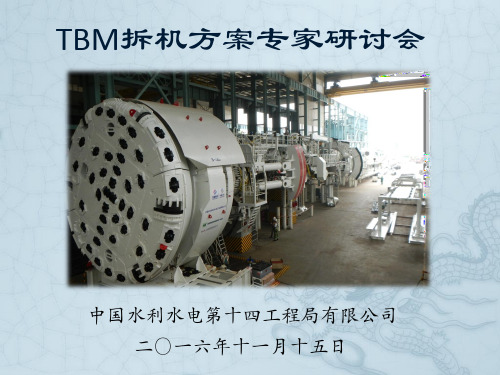
序号 结构名称
安放位置
备注
1 70mm厚滑动钢板 10395mm×4878mm,在铺底混凝土上
贯通面前
2
步3
进 系
4
统5
组6 成 构7
件8
提升支架 提升油缸 主梁提升托架 步进油缸 后支撑 撑靴部分支架 盾体支架
在滑板预留槽内移动 固定在提升支架与主梁提升托架之间
固定在主梁上 固定在滑板上
主梁尾端 水平撑靴处鞍架下方 主驱动下方固定在底护盾下
元(鞍架及撑靴油缸分别拆除)
分别在主梁上焊接钢结构,利用
10T纵向吊点和10T倒链进行拆
除,拆除放置于平板车上,从
3#洞方向运出,在检修间25T桥
主
机及平板车运到洞外存储场地。
驱
(6)主驱动拆卸
动 吊
拆除驱动电机后,安装吊耳、挂
耳
好钢丝绳,将钢丝绳刚好带紧,
及
利用液压张紧扳手对称拆除连接
翻
螺柱。将主驱动放置在翻身支架
(12)连接桥及电器设备拆卸
连接桥的拆卸遵循从后到前,先附属部件后主要部件的原则进 行。电器液压系统拆除时小的部件直接使用平板火车经3#洞运 出洞外,TBM第二层及较大的部件待2#皮带拆除完成后,在 TBM第二层布置门型架作为移动吊点进行拆除。
(13) 标识与包装咨询
根据TBM机械各部分的不同特点分别采取不同的标识方案。 但有一点是相同的,即除后配套等机械框架结构件外均用漆 字标识和挂标识牌(签)两种标识方式,并建立登记表备查。
指标
地勘指标
实际揭露指标
等级
Ⅱ类
Ⅲa
岩性
侏罗系林子头组下 部旋回酸性熔岩及 角砾熔岩,镶嵌结
构~次块状结构
隧道工程tbm技术方案

隧道工程tbm技术方案一、项目概况隧道是一种地下道路工程,是连接两个地点,穿越山脉、水域等地下地形的通道。
在现代城市建设和交通运输中,隧道工程起着重要的作用。
而盾构机(TBM)技术是当今最先进的隧道施工技术之一,其应用范围越来越广泛。
本文将结合实际情况,对某隧道工程中应用TBM技术的技术方案进行详细分析和介绍。
二、隧道工程TBM技术方案1. 项目背景该隧道工程位于某大城市的市区,是连接两个交通要道的重要通道。
由于地表交通拥堵,为了缓解交通压力,项目部决定采用TBM技术进行隧道施工,以便快速、高效地完成工程。
2. 项目技术特点该项目的技术特点主要包括以下几个方面:(1)地质条件复杂:隧道穿越的地质条件较为复杂,包括岩石、砂土、泥岩等多种地层。
(2)隧道长度较长:隧道全长约5公里,需要穿越多个地形。
(3)环保要求高:作为城市重要交通通道,对环境保护要求较高。
3. 技术方案(1)盾构机选型考虑到地质条件复杂、隧道长度较长等因素,决定选择直径6米的大型盾构机进行施工,以保证施工质量和效率。
(2)隧道路线设计根据地质勘察和设计要求,确定了隧道的最佳路线,并进行了全面的设计和布局方案。
(3)施工工艺流程采用封闭式盾构机施工工艺,具体分为切削系统、传输系统、混凝土浇筑系统等多个子系统,确保隧道施工质量。
(4)环保措施在隧道施工中,将采取降尘、降噪、污水处理等多项环保措施,保护周边环境。
(5)安全管理隧道施工过程中,将加强安全管理,严格落实安全生产措施,确保工程施工过程的安全。
三、方案实施1. 前期准备在正式进行隧道施工前,项目部将组织开展各项准备工作,包括设备调试、材料准备、人员培训等。
2. 施工实施根据技术方案,实施TBM盾构机施工工程,确保施工质量和进度。
3. 环境保护在施工过程中,严格执行环保措施,防止施工对环境造成不良影响。
4. 安全管理加强安全管理,定期进行安全检查和隐患排查,确保施工现场的安全。
四、技术方案优势1. 高效快速:TBM技术施工速度快,可以大大节省工期。
大断面TBM洞内组装施工工法
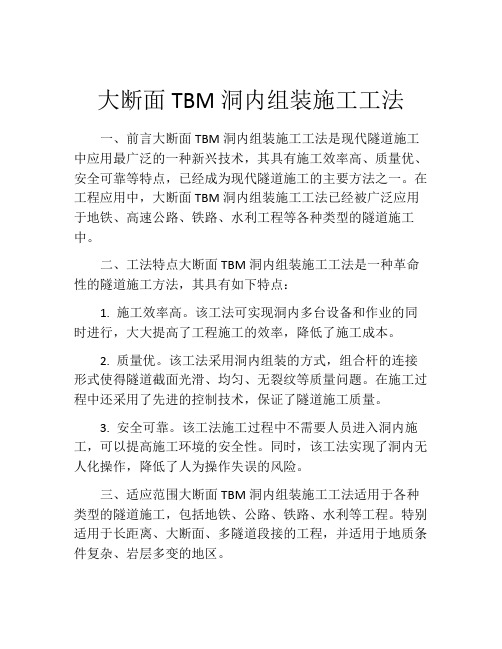
大断面TBM洞内组装施工工法一、前言大断面TBM洞内组装施工工法是现代隧道施工中应用最广泛的一种新兴技术,其具有施工效率高、质量优、安全可靠等特点,已经成为现代隧道施工的主要方法之一。
在工程应用中,大断面TBM洞内组装施工工法已经被广泛应用于地铁、高速公路、铁路、水利工程等各种类型的隧道施工中。
二、工法特点大断面TBM洞内组装施工工法是一种革命性的隧道施工方法,其具有如下特点:1. 施工效率高。
该工法可实现洞内多台设备和作业的同时进行,大大提高了工程施工的效率,降低了施工成本。
2. 质量优。
该工法采用洞内组装的方式,组合杆的连接形式使得隧道截面光滑、均匀、无裂纹等质量问题。
在施工过程中还采用了先进的控制技术,保证了隧道施工质量。
3. 安全可靠。
该工法施工过程中不需要人员进入洞内施工,可以提高施工环境的安全性。
同时,该工法实现了洞内无人化操作,降低了人为操作失误的风险。
三、适应范围大断面TBM洞内组装施工工法适用于各种类型的隧道施工,包括地铁、公路、铁路、水利等工程。
特别适用于长距离、大断面、多隧道段接的工程,并适用于地质条件复杂、岩层多变的地区。
四、工艺原理大断面TBM洞内组装施工工法的工艺原理是将TBM进行、预制隧道衬砌板进行组装和安装、旋挖钻井配合施工的一种隧道施工方式。
采用该工法施工需要进行如下技术措施:1. 预制隧道衬砌板的制作和加工。
在施工前,需要将隧道衬砌板进行制作和加工,以便后续进行组装施工。
2. TBM的洞内组装。
在施工过程中,通过将TBM进行洞内组装,可以有效减少施工现场尘土、噪音等环境污染。
在安装TBM过程中,需要进行计算机辅助设计和控制,以保证组装质量和施工进度。
3. 组合杆连接。
采用组合杆连接方式进行洞内组装,可以保证施工质量和施工效率。
需要在连接过程中加强检查和控制,以保障组合杆的连接紧密可靠。
4. 钻井配合施工。
在施工过程中,通过旋挖钻井的方式进行施工配合,使得施工过程更加高效、精准,保证了隧道施工效率。
隧道TBM施工关键技术应用
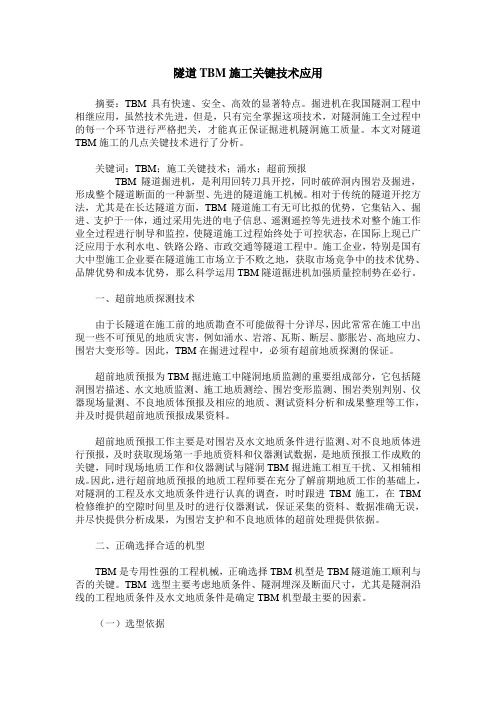
隧道TBM施工关键技术应用摘要:TBM具有快速、安全、高效的显著特点。
掘进机在我国隧洞工程中相继应用,虽然技术先进,但是,只有完全掌握这项技术,对隧洞施工全过程中的每一个环节进行严格把关,才能真正保证掘进机隧洞施工质量。
本文对隧道TBM施工的几点关键技术进行了分析。
关键词:TBM;施工关键技术;涌水;超前预报TBM隧道掘进机,是利用回转刀具开挖,同时破碎洞内围岩及掘进,形成整个隧道断面的一种新型、先进的隧道施工机械。
相对于传统的隧道开挖方法,尤其是在长达隧道方面,TBM隧道施工有无可比拟的优势,它集钻入、掘进、支护于一体,通过采用先进的电子信息、遥测遥控等先进技术对整个施工作业全过程进行制导和监控,使隧道施工过程始终处于可控状态,在国际上现已广泛应用于水利水电、铁路公路、市政交通等隧道工程中。
施工企业,特别是国有大中型施工企业要在隧道施工市场立于不败之地,获取市场竞争中的技术优势、品牌优势和成本优势,那么科学运用TBM隧道掘进机加强质量控制势在必行。
一、超前地质探测技术由于长隧道在施工前的地质勘查不可能做得十分详尽,因此常常在施工中出现一些不可预见的地质灾害,例如涌水、岩溶、瓦斯、断层、膨胀岩、高地应力、围岩大变形等。
因此,TBM在掘进过程中,必须有超前地质探测的保证。
超前地质预报为TBM掘进施工中隧洞地质监测的重要组成部分,它包括隧洞围岩描述、水文地质监测、施工地质测绘、围岩变形监测、围岩类别判别、仪器现场量测、不良地质体预报及相应的地质、测试资料分析和成果整理等工作,并及时提供超前地质预报成果资料。
超前地质预报工作主要是对围岩及水文地质条件进行监测、对不良地质体进行预报,及时获取现场第一手地质资料和仪器测试数据,是地质预报工作成败的关键,同时现场地质工作和仪器测试与隧洞TBM掘进施工相互干扰、又相辅相成。
因此,进行超前地质预报的地质工程师要在充分了解前期地质工作的基础上,对隧洞的工程及水文地质条件进行认真的调查,时时跟进TBM施工,在TBM 检修维护的空隙时间里及时的进行仪器测试,保证采集的资料、数据准确无误,并尽快提供分析成果,为围岩支护和不良地质体的超前处理提供依据。
简述地铁隧道施工TBM工法应用策略

简述地铁隧道施工TBM工法应用策略摘要:文章针对隧道TBM工法进行研究,结合地铁隧道工程案例,指出TBM工法的破岩原理和技术优点,总结了TBM工法的施工应用。
实践表明:TBM是地铁隧道开挖施工的一种可行技术方案,具有效率高、安全性好、环境影响小等技术优点。
现场施工中严格规范操作、加强技术管理,才能进一步提高经济效益和社会效益,实现预期质控目标。
关键词:地铁隧道;TBM工法;破岩原理;施工方法TBM指的是全断面隧道掘进机(Tunnel Boring Machine),它将机、电、光、气、液等系统集成为一体,可实现掘进、支护、出渣等工序并连续作业,尤其适用于地理环境复杂的深埋长隧道工程[1]。
近年来,我国地铁建设工程数量增加,因施工地点位于市区,不仅地面交通繁忙、建筑物繁多,而且地下管线复杂,采用TBM工法具有较强的适应性。
以下结合实践,探讨了TBM工法在地铁隧道施工中的运用。
1.工程概况某城市地铁3号线,线路全长约24 km,其中正线21.6 km、连接线2.4 km,包括15个车站、15个区间、1个停车场和1座变电所。
土建工程主要有车站、区间、出入线段、停车场、既有线接口、人防工程等,采用TBM工法施工。
隧道断面内径、外径分别是5400 mm和6000 mm,管片宽度为1200~1500 mm,厚度为300 mm。
地质勘察结果显示,施工段岩土层从上到下分别是杂填土、素填土、砂卵石、强风化砂岩、中风化砂岩。
TBM掘进时,穿越砂卵石、强风化砂岩和中风化砂岩,其中强风化砂岩的单轴抗压强度为23.2~54.6 MPa,中风化砂岩的单轴抗压强度为3.8~19.2 MPa。
地表水对隧道施工影响不大,地下水来源于上层滞水和基层裂隙水,施工中重点考虑基岩裂隙水。
2.TBM工法的破岩原理和技术优点2.1 破岩原理刀具接触完整的岩石,在推力作用下切入岩体,岩石结合力薄弱处产生割痕裂纹;刀刃顶部的岩石产生压缩,随着刀盘回转、滚刀转动,岩石裂纹逐渐扩大;当不同部位的裂纹交汇在一起,岩石就会断裂、破碎,积聚在刀刃顶部范围内形成粉核区。
TBM及其洞内安装技术

塌严重,大部分时间消耗在初期支护和弃渣清理方面,此时
的重点任务是确保安全。本工程Ⅴ类围岩190m(1%),对工 程总工期影响较小,在极端情况下可考虑采用钻爆法处理后 再掘进通过。
六、TBM选型
根据各类型TBM的适用条件及前述岭南段地质条件,本 工程TBM主要是针对长距离高石英含量硬岩、以提高掘效率 为重点进行选型,因而采用敞开式TBM更经济、合理。 综合考虑国内国际TBM设备制造商生产能力及设备技术 水平,选择美国罗宾斯MB266-395型敞开式全断面隧道掘进
三、TBM施工优点
4、安全:用TBM施工,改善了作业人员的洞内劳动条件, 减轻了体力劳动量,避免了爆破施工可能造成的人员伤亡, 事故大大减少。 5、环保:TBM施工不用炸药爆破,施工现场环境污染小; TBM施工减少了长大隧道的辅助导坑数量,保护了生态环境, 有利于环境保护。 6、自动化、信息化程度高:TBM采用了计算机控制、传 感器、激光导向、测量、超前地质探测、通讯技术,是集机、 光、电、气、液、传感、信息技术于一体的隧道施工成套设 备,具有自动化程度高的优点。TBM具有施工数据采集功能, TBM姿态管理功能,施工数据管理功能,施工数据实时远传 功能,实现信息化施工。
设备,全套设备重达几千吨,最大部件重量达上百吨,拼装
长度最长达200多米。 5、设备购置及使用成本大:TBM施工需要高负荷的电力 保证、需要高素质的技术人员和管理队伍、前期购买设备的 费用较高,施工成本高。
五、TBM工作原理
通过一个短片来了解开敞式TBM工作原理。
六、TBM选型
1、TBM选型原则 ①根据工程特点选取合适类型的TBM。TBM按适用的工程 地质大致分为软岩TBM和硬岩TBM,不同生产商生产的同类的 TBM在结构上也有很大差别,各有优缺点,要根据工程特点 对照选型。
长距离大坡度隧洞开敞式掘进机(TBM)全断面施工工法(2)
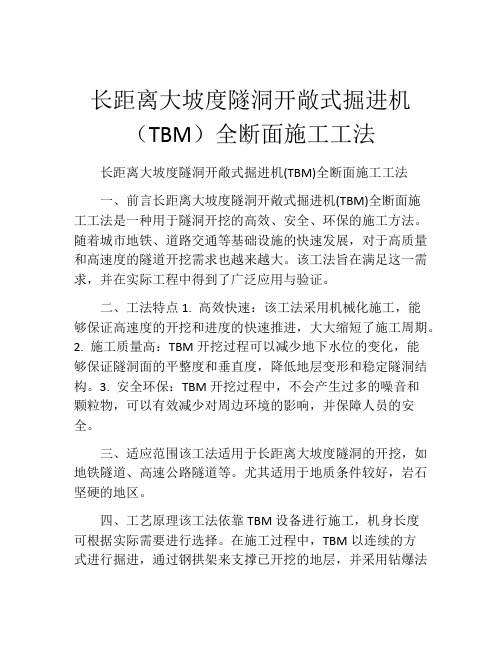
长距离大坡度隧洞开敞式掘进机(TBM)全断面施工工法长距离大坡度隧洞开敞式掘进机(TBM)全断面施工工法一、前言长距离大坡度隧洞开敞式掘进机(TBM)全断面施工工法是一种用于隧洞开挖的高效、安全、环保的施工方法。
随着城市地铁、道路交通等基础设施的快速发展,对于高质量和高速度的隧道开挖需求也越来越大。
该工法旨在满足这一需求,并在实际工程中得到了广泛应用与验证。
二、工法特点1. 高效快速:该工法采用机械化施工,能够保证高速度的开挖和进度的快速推进,大大缩短了施工周期。
2. 施工质量高:TBM开挖过程可以减少地下水位的变化,能够保证隧洞面的平整度和垂直度,降低地层变形和稳定隧洞结构。
3. 安全环保:TBM开挖过程中,不会产生过多的噪音和颗粒物,可以有效减少对周边环境的影响,并保障人员的安全。
三、适应范围该工法适用于长距离大坡度隧洞的开挖,如地铁隧道、高速公路隧道等。
尤其适用于地质条件较好,岩石坚硬的地区。
四、工艺原理该工法依靠TBM设备进行施工,机身长度可根据实际需要进行选择。
在施工过程中,TBM以连续的方式进行掘进,通过钢拱架来支撑已开挖的地层,并采用钻爆法将岩石破碎。
采用全断面开挖方式可以保持隧道的整体稳定,降低地下水位的变化。
五、施工工艺1. 施工前准备:包括场地平整、道路清理和设备调试等。
2. 施工洞口控制:通过设置合理的洞口尺寸和控制洞口进水来保证施工的顺利进行。
3. TBM设备配置:根据隧洞的实际情况,选择合适的TBM设备,并对设备进行调试和检测。
4. 施工开挖:TBM进行连续开挖,同时进行岩石破碎和排土,通过传输带将土方运出隧道。
5. 支护加固:在TBM掘进的同时,设置临时支护结构来保证隧洞的稳定性和安全性。
6. 排水处理:根据地下水位情况,采取合适的排水措施来保证隧道的干燥。
7. 清洁维护:定期对TBM设备进行清洁和维护保养,确保设备正常运行。
六、劳动组织在施工中需要建立合理的劳动组织,包括工地管理、人员调配和队伍培训等。
长距离大坡度隧洞开敞式掘进机(TBM)全断面施工工法

长距离大坡度隧洞开敞式掘进机(TBM)全断面施工工法长距离大坡度隧洞开敞式掘进机(TBM)全断面施工工法一、前言隧洞工程在现代交通、水利、能源等基础设施建设中占据重要地位。
长距离大坡度隧洞的施工面临着诸多挑战,如地质复杂、工期紧张等。
为了满足这些挑战,长距离大坡度隧洞开敞式掘进机(TBM)全断面施工工法应运而生。
本文将详细介绍该工法的特点、适应范围、工艺原理、施工工艺、劳动组织、机具设备、质量控制、安全措施以及经济技术分析。
二、工法特点长距离大坡度隧洞开敞式掘进机(TBM)全断面施工工法具有以下特点:1、高效快速:TBM采用现代化设备和自动化技术,能够实现连续掘进、支护和后续施工工序,施工效率高,工期可缩短。
2、安全可靠:TBM作业面封闭,能够有效控制尘埃、噪音和恶劣环境对施工人员的影响,提供安全保障。
3、质量可控:TBM采用先进的定位和导向系统,能够准确控制隧道的偏差和纵横断面的尺寸,保证施工质量。
4、环保节能:TBM施工过程中产生的废弃物、尘埃等污染物能够得到有效管理,节约能源。
5、适应性强:TBM可以适应各种地质条件和施工要求,可用于挖掘各种断面形状的长距离大坡度隧洞。
三、适应范围长距离大坡度隧洞开敞式掘进机(TBM)全断面施工工法适用于以下场景:1、交通隧道:如公路、铁路、地铁等。
2、水利隧洞:如水库溢洪道、输水隧洞等。
3、电力隧道:如输电隧道、升压站隧洞等。
4、资源开发隧道:如矿山开采、石油、天然气等。
5、城市地下综合管廊。
四、工艺原理长距离大坡度隧洞开敞式掘进机(TBM)全断面施工工法的工艺原理主要包括施工工法与实际工程之间的联系和采取的技术措施:1、地质调查和分析:通过地质调查了解隧洞工程的地质条件,包括地层分布、岩石性质、巷道构造等,为施工工艺的确定提供基础。
2、设备选型:根据隧洞工程的长度、倾角、断面形状等特点,选择合适的TBM型号和配套设备。
3、开始施工:首先进行掘进端的开挖和初期支护,然后启动TBM掘进,控制进尺和隧道纵横断面的尺寸。
深埋长隧道TBM施工关键问题探讨
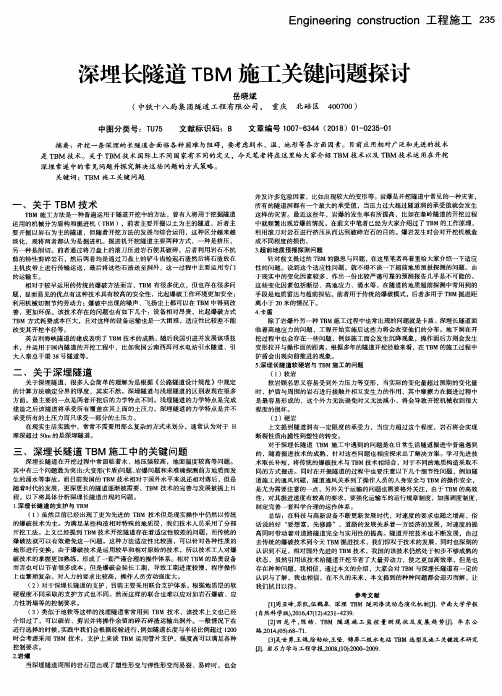
二 、 关 于 深 埋 隧 道
关 于深埋 隧道 ,很多人会简单 的理解 为是根据 《公路隧道设计规 范》中规定 的计算方法 确定分界的厚度 ,其 实不然 。深埋隧道与浅埋隧道 的区别 表现在很多 方面 。最主要的一点是两者 开挖 后的力学特点不同 。浅埋 隧道 的力学特点是完成 建造 之后该 隧道将承受所有覆 盖在其 上面的土压力 ,深埋 隧道 的力 学特点是并不 承受所有 的土压力 而只承受一部 分的土压力 。
关键 词 :TBM 施 工 关 键 问 题
一 、 关 于 TBM 技 术
TBM 施工方法是一种普遍运用于隧道开挖 中的方法 ,曾有人将用 于挖掘隧道 运用的机械分 为盾 构和掘进机 (TBM ),前者主要开掘 以土为主的隧道 ,后者 主 要开掘 以岩石 为主的隧道 ,但随着开挖方法 的发展 与综合运用 ,这种 区分越来越 淡化 ,现将两者都认 为是掘进机 。掘进机开挖 隧道 主要两种方式 ,一种是挤压 , 另一种是削切 。前 者通过将刀盘上的滚刀压进 岩石使 其破碎 ,后者利用岩石不抗 剪的特性剪碎岩 石 ,然后两者均是通过刀盘 上的铲 斗齿捡起石渣然后将 石渣放在 主机皮带上进行 传输运送 ,最后将这些石渣送 至洞外 ,这一过程 中主要 运用专 门 的 运 输 车 。
Engineering construction 工 程 施 工 235
深埋长隧道 TB M施工关键问题探讨
岳 晓 斌 (中铁 十八局 集团隧道 工程有 限公 司, 重庆 北碚 区 400700)
TBM施工技术
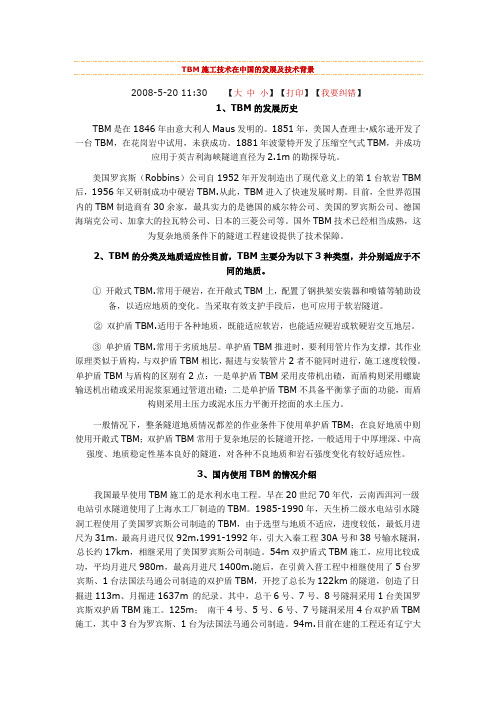
TBM施工技术在中国的发展及技术背景2008-5-20 11:30【大中小】【打印】【我要纠错】1、TBM的发展历史TBM是在1846年由意大利人Maus发明的。
1851年,美国人查理士·威尔逊开发了一台TBM,在花岗岩中试用,未获成功。
1881年波蒙特开发了压缩空气式TBM,并成功应用于英吉利海峡隧道直径为2.1m的勘探导坑。
美国罗宾斯(Robbins)公司自1952年开发制造出了现代意义上的第1台软岩TBM 后,1956年又研制成功中硬岩TBM.从此,TBM进入了快速发展时期。
目前,全世界范围内的TBM制造商有30余家,最具实力的是德国的威尔特公司、美国的罗宾斯公司、德国海瑞克公司、加拿大的拉瓦特公司、日本的三菱公司等。
国外TBM技术已经相当成熟,这为复杂地质条件下的隧道工程建设提供了技术保障。
2、TBM的分类及地质适应性目前,TBM主要分为以下3种类型,并分别适应于不同的地质。
①开敞式TBM.常用于硬岩,在开敞式TBM上,配置了钢拱架安装器和喷锚等辅助设备,以适应地质的变化。
当采取有效支护手段后,也可应用于软岩隧道。
②双护盾TBM.适用于各种地质,既能适应软岩,也能适应硬岩或软硬岩交互地层。
③单护盾TBM.常用于劣质地层。
单护盾TBM推进时,要利用管片作为支撑,其作业原理类似于盾构,与双护盾TBM相比,掘进与安装管片2者不能同时进行,施工速度较慢。
单护盾TBM与盾构的区别有2点:一是单护盾TBM采用皮带机出碴,而盾构则采用螺旋输送机出碴或采用泥浆泵通过管道出碴;二是单护盾TBM不具备平衡掌子面的功能,而盾构则采用土压力或泥水压力平衡开挖面的水土压力。
一般情况下,整条隧道地质情况都差的作业条件下使用单护盾TBM;在良好地质中则使用开敞式TBM;双护盾TBM常用于复杂地层的长隧道开挖,一般适用于中厚埋深、中高强度、地质稳定性基本良好的隧道,对各种不良地质和岩石强度变化有较好适应性。
3、国内使用TBM的情况介绍我国最早使用TBM施工的是水利水电工程。
TBM法掘进机拆卸、运输及存放工艺

TBM法掘进机拆卸、运输及存放工艺4.10.1工艺概述TBM 完成区间隧道施工,到达拆卸洞或步进至敞开段进行拆除。
4.10.2作业内容作业内容:TBM 拆卸、TBM 运输及存放4.10.3工序步骤及质量控制说明一、TBM 拆卸工作准备TBM 的拆卸是一项系统的工作。
实施前各项准备工作充分与否,不仅关系到拆卸是否顺利进行的问题,而且更关系到 TBM 重复使用的状态与寿命等问题,影响 TBM 的使用效能。
编制详细的 TBM 拆卸施组,从劳动、物资、机具上做好准备,先对各分项设备技术鉴定加上- 422 -工标识牌,主机洞内拆卸,拖车运至洞外拆卸。
1.洞内拆卸工艺(1)TBM 拆机工作分三个主要阶段,准备工作阶段、拆机作业阶段、拆毕整理阶段。
图4.10.3-1 拆机的几个主要阶段(2)TBM 拆机的主要流程分为三个步骤,主要为连续皮带机、后配套、主机。
(3)TBM 拆机人员主要分为三个小组,分别为运输、连续皮带机的拆卸、TBM 的拆卸。
2.硬件配套工程准备该准备工作包括风水电及土建工程完成情况,以及拆机设备、工具和材料准备落实情况等。
(1)洞内拆卸的配套工程这是一项庞大的工程。
既有拆卸洞室的庞大土建工作,同时也包括预装起重吊点的布置分布情况,及另行配置的风水电等。
各种预埋、预埋制作件、设备、工具及非标加工件等。
(2)拆卸洞室根据 TBM 规格尺寸确定拆卸洞室尺寸。
以大伙房输水工程为例,TBM 直径为 8m,洞内的拆卸洞室的围岩为四类,岩性为混合岩,拆卸洞断面设计为蘑菇形,此作业面主要是拆卸主机以及设备桥,刀盘处设计洞室平面:L×W=5×10m,剩下拆机洞室平面为:L×W=31×9m,净空高度:H=11m。
设计洞室的总长为 36m,拆卸洞内的拖车轨面施工成嵌入轨。
(3)吊机的安装①拆卸洞安装一台双梁 10T 电动葫芦。
②后配套 15#拖车尾部安装两台单臂梁 10T 电动葫芦。
TBM洞内拆卸方案
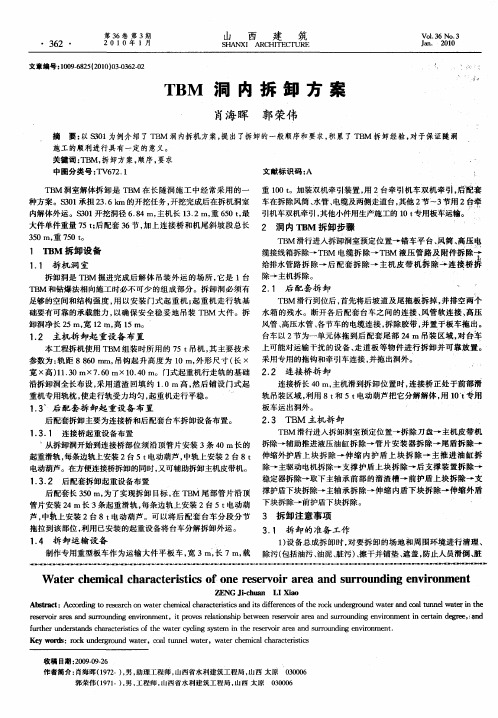
芦, 中轨上安装 2 8t 台 电动 葫芦。可 以将后 配套 台车分段 分节 3 拆 卸注意 事项
拖 拉 到该 部 位 , 用 已 安装 的起 重设 备将 台 车分 解 拆 卸 外 运 。 利
3 1 拆卸 的 准备 工作 .
1 4 拆卸运 输设备 .
1 设备 总成 拆卸时 , ) 对要拆 卸的场地 和周围环境进行 清理 、 制作专用重型板车作 为运输大件 平板 车 , 3m, 7m, 宽 长 载 除污( 包括油污 、 油泥、 脏污 )擦 干并铺垫 、 、 遮盖 , 防止人员滑倒 、 脏
i ’‘
内解体外运 。S 0 3 1开挖 洞径 6 8 , .4i 主机长 1 . 重 6 0t最 引机车双机牵 引, n 3 2m, 5 , 其他小件用生产施工的 1 专用板车运输。 0t
大件单 件重量 7 ; 5t后配套 3 , 6节 加上连接桥 和机尾斜 坡段总 长 2 洞 内 T M 拆 卸步 骤 B
T M 滑行到位后 , B 首先将后坡道 及尾拖板拆 掉 , 空两个 并排
风管 、 高压水管 、 各节 车的电缆连接 , 拆除胶带 , 置于板车拖 出。 并 台车以 2 为一单元 体拖到后 配套尾 部 2 吊装 区域 , 台车 节 4m 对
风 高压 础要有可靠的承载能力 , 以确保 安全稳 妥地 吊装 T M 大件。拆 水箱 的残水 。断开各 后配套 台车之间 的连 接 、 管软连接 、 B
30m, 7 0t 5 重 5 。
T M滑行进入拆卸洞室预定位置一错车平台、 B 风筒、 高压电
缆接线 箱拆 除一 T M 电缆 拆除一 T 液 压管路 及附件 拆除 B I
1 T M 拆 卸设备 B
1 1 拆 机 洞 室 .
tbm洞内拆机工作总结
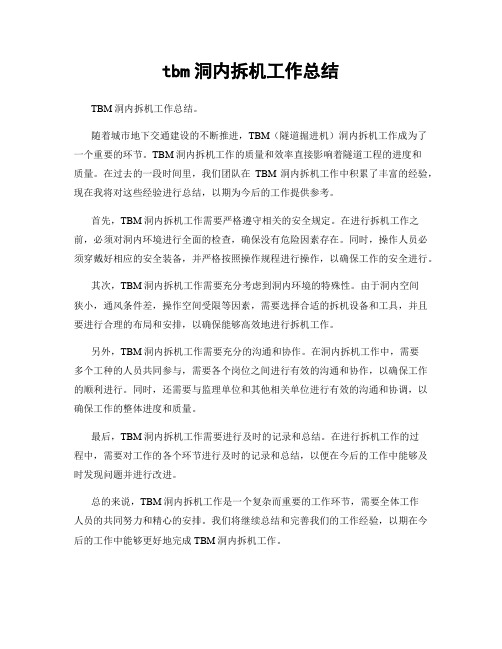
tbm洞内拆机工作总结
TBM洞内拆机工作总结。
随着城市地下交通建设的不断推进,TBM(隧道掘进机)洞内拆机工作成为了一个重要的环节。
TBM洞内拆机工作的质量和效率直接影响着隧道工程的进度和
质量。
在过去的一段时间里,我们团队在TBM洞内拆机工作中积累了丰富的经验,现在我将对这些经验进行总结,以期为今后的工作提供参考。
首先,TBM洞内拆机工作需要严格遵守相关的安全规定。
在进行拆机工作之前,必须对洞内环境进行全面的检查,确保没有危险因素存在。
同时,操作人员必须穿戴好相应的安全装备,并严格按照操作规程进行操作,以确保工作的安全进行。
其次,TBM洞内拆机工作需要充分考虑到洞内环境的特殊性。
由于洞内空间
狭小,通风条件差,操作空间受限等因素,需要选择合适的拆机设备和工具,并且要进行合理的布局和安排,以确保能够高效地进行拆机工作。
另外,TBM洞内拆机工作需要充分的沟通和协作。
在洞内拆机工作中,需要
多个工种的人员共同参与,需要各个岗位之间进行有效的沟通和协作,以确保工作的顺利进行。
同时,还需要与监理单位和其他相关单位进行有效的沟通和协调,以确保工作的整体进度和质量。
最后,TBM洞内拆机工作需要进行及时的记录和总结。
在进行拆机工作的过
程中,需要对工作的各个环节进行及时的记录和总结,以便在今后的工作中能够及时发现问题并进行改进。
总的来说,TBM洞内拆机工作是一个复杂而重要的工作环节,需要全体工作
人员的共同努力和精心的安排。
我们将继续总结和完善我们的工作经验,以期在今后的工作中能够更好地完成TBM洞内拆机工作。
TBM及其洞内安装技术

六、TBM选型
区域断层。 ②地质适应性分析:敞开式TBM在Ⅱ、Ⅲ类围岩中,能 够发挥较好的掘进效率,综合上述本标段的围岩情况,Ⅱ、 Ⅲ类围岩总长度达到14947m,占80%,如果设备状态良好、 施工组织合理,平均月进尺可达到500~600m;Ⅰ类围岩条
件下,初期支护和弃渣清理工作量极小,但TBM破岩效率较
设备,全套设备重达几千吨,最大部件重量达上百吨,拼装
长度最长达200多米。 5、设备购置及使用成本大:TBM施工需要高负荷的电力 保证、需要高素质的技术人员和管理队伍、前期购买设备的 费用较高,施工成本高。
五、TBM工作原理
通过一个短片来了解开敞式TBM工作原理。
六、TBM选型
1、TBM选型原则 ①根据工程特点选取合适类型的TBM。TBM按适用的工程 地质大致分为软岩TBM和硬岩TBM,不同生产商生产的同类的 TBM在结构上也有很大差别,各有优缺点,要根据工程特点 对照选型。
输移动较困难,施工准备和辅助施工的配套系统较复杂,加
工制造工期长,对于短隧道和中长隧道很难发挥其优越性。
四、TBM施工缺点
3、断面适应性较差:断面直径过小时,后配套系统不
易布置,施工较困难;而断面过大时,又会带来电能不足、 运输困难、造价昂贵等种种问题。较适宜采用TBM施工的隧 道断面直径在3m~l 2m。 4、运输困难,对施工场地有特殊要求:TBM属大型专用
四、TBM施工缺点
1、地质适应性较差:TBM对隧道的地层最为敏感,不同 类型的TBM适用的地层也不同,一般的软岩、硬岩、断层破
碎带,可采用不同类型的TBM辅以必要的预加固和支护设备
进行掘进,但对于大型的岩溶暗河发育的隧道、高地应力隧 道、软岩大变形隧道、可能发生较大规模突水涌泥的隧道等 特殊不良地质隧道,则不适合采用TBM施工。 2、不适宜中短距离隧道的施工:由于TBM体积庞大,运
隧道掘进机(TBM)在工程施工中的应用研究

隧道掘进机(TBM)在工程施工中的应用研究摘要:隧道掘进机是一种专门用于开挖地下通道工程的大型高科技施工装备,它具有开挖快、优质、安全、经济、有利于环境保护和降低劳动强度的优点。
掘进机技术体现了计算机、新材料、自动化、信息化、系统科学、管理科学等高新技术的综合和密集,反映了一个国家的综合国力和科技水平。
本文主要探讨隧道掘进机在工程施工中的应用。
关键词:隧道掘进机工程施工应用一、隧道掘进机(TBM)在工程施工中的应用(一)隧道掘进机在国外的应用情况隧道掘进机在3km以上的长洞中应用较多。
具有代表性的是连接英法两国的英吉利海峡隧道,3条洞总长87KM(单洞长50.5km),采用11台掘进机施工,只用了三年半就全部贯通(全部工程完工只用了8年,1986-1993年),月平均进度从340m增加到840m,最高月进尺,在法国则为1232m,英国则高达1716m,无一人因掘进事故而死亡。
而日本青函隧道,全长53.85km,使用钻爆法施工,花12年才贯通(全部完工用了24年,1964-1988年),伤亡100多人。
(二)隧道掘进机在国内的应用情况我国水利、电力、铁路、煤炭、矿山、交通及城市地下等工程的建设中,长隧洞已开始采用TBM施工,并取得了良好的效果。
如甘肃省引大入秦引水工程30A隧洞,全长11.649KM,采用TBM施工,1990年月12月开工,1992年元月贯通建成,平均月成洞进尺860m,最高月成洞进尺1300m;38#隧洞洞长4947.6m,仅用4.5个月就完工,平均月成洞进尺1100m,最高月成洞进尺1400m,创造了当时我国的最高记录和达到了世界先进水平。
山西省隧道掘进机(TBM)的施工,始于引黄入晋工程的建设。
引进美国ROBBINS制造的1811-256型双护盾硬岩掘进机,首次用于山西引黄工程总干6#/7#/8#隧洞施工,平均月进尺610m-680m。
之后,引黄南干线隧洞工程也采用TBM施工,平均月进尺660-1100m。
- 1、下载文档前请自行甄别文档内容的完整性,平台不提供额外的编辑、内容补充、找答案等附加服务。
- 2、"仅部分预览"的文档,不可在线预览部分如存在完整性等问题,可反馈申请退款(可完整预览的文档不适用该条件!)。
- 3、如文档侵犯您的权益,请联系客服反馈,我们会尽快为您处理(人工客服工作时间:9:00-18:30)。
浅谈长大隧道TBM拆卸洞施工技术
摘要:某长大隧道TBM拆卸洞设在Ⅱ级围岩地段,对拆卸洞分三部四区段开挖完成。
鉴于该隧道特点,本文对的特大断面II类围岩对TBM拆卸洞室施工进行探讨,总结出该工程所采用的成功经验,为今后类似工程提供借鉴及管理成功的实例。
关键词:隧道施工拆卸洞TBM施工隧洞开挖
1 工程概况
某隧道TBM拆卸洞设在Ⅱ级围岩地段,拆卸洞全长60 m,边墙为直墙,拱部为曲墙,下部开挖宽度为13.1 m,上部最大开挖宽度为16.12 m,开挖总高度为18.81 m。
托梁及下部直墙衬砌采用C30钢筋砼,拱部段衬砌均采用C30素砼。
2 拆卸洞开挖施工技术
拆卸洞分三部四区段开挖完成,第一步:到达拆卸洞前15 m施作预留平台,利用现有开挖台架在分界断面处开始向上挑挖,向上挑挖15 m后到达TBM拆卸洞顶部(见图1),之后分三台阶开挖上部Ⅰ、Ⅱ区、Ⅲ区,台阶长度3~5 m,每循环进尺为2.5 m,拱部Ⅰ区采用搭设临时活动支架进行作业,开挖一段支护一段。
水平向前直至挖出上部断面。
第二步:当至TBM端上部Ⅰ、Ⅱ区、Ⅲ区段开挖完成后反向施工钻爆端的上部断面,直至所有上部断面全部开挖成型,上部反向开挖时
在台架上可加设临时平台确保台架的高度满足开挖要求。
第三步:最后开挖底部Ⅳ区段。
后段拱部初支:上挑洞顶须进行临时支护措施,根据围岩情况在拱部局部可设φ22砂浆锚杆,锚杆长2.0 m,喷射C25砼,厚度3~5 cm。
拆卸洞初支:托梁上2米范围、以下3 m 范围内边墙锚杆间距0.5×0.5 m,L=4 m,梅花型布置;其余部位锚杆间距1.0×1.0 m,L=3.5 m,梅花型布置,锚杆均采用R32N自进式锚杆并径向注浆,浆液采用水泥浆。
边墙及拱部用C25喷射砼,砼喷射厚度为13~15 cm(见图2)。
TBM拆卸洞出碴采用ZL50C装载机及CAT330挖掘机装碴,斯太尔自卸汽车运输。
3 拆卸洞砼衬砌
本工程砼衬砌施工作业顺序采取如下:铺底→下部边墙→托梁→上部直墙段→拱墙段砼。
3.1 铺底施工技术
拆卸洞铺底砼标号为C20砼,铺设厚度30 cm。
砼采用分段全幅施工一次浇注长度30 m,分两次完成。
无轨灌车运输,泵送砼入模。
3.2 直边墙段施工技术
直边墙段施工施工序:安装脚手架→铺设土工布及防水板→安装
边墙钢筋→立模板→浇筑砼。
直边墙段采用脚手架作为施工平台,脚手架作业面平台上设木板作为行走过道。
脚手架沿边墙搭设三排至墙顶,砼浇注后脚手架纵横每隔3~4 m与边墙预埋筋进行连接加固。
直墙段从TBM端向钻爆端施工。
防水板施工时,本工程防水板采用自爬动焊机焊接,搭接宽度不小于15 cm,接头距砼施工缝距离不小于1 m。
一次铺设高度6 m,长度12 m。
边墙钢筋为φ16筋,内外共设两层,钢筋现场绑扎。
直边墙模板采用定制钢模板,面板采用5 mm钢板,高1.5 m×宽1.0 m,加工40块。
一次安装长度为10 m,模板分成两组,边墙左右两侧同时施工。
模板的定位通过螺旋钢顶撑、调节拉杆、预埋筋及葫芦实现。
预埋筋每浇注层设5根,水平间距2 m,预埋筋设置有两种方法,方法1:采用φ14螺纹钢外套φ30PVC管定位于模板上口适当位置,拆模后转动钢筋通过调节拉杆与脚手架紧固;方法2:采用φ18螺纹钢,端头车φ16的丝杆,在模板适当位置钻φ30孔,丝杆穿过模板定位于模板上口适当位置,拆模后预埋筋通过调节拉杆与脚手架拉紧,模板就位后模板的下口用螺旋钢顶撑顶紧加固,上口亦用螺旋钢顶撑顶紧加固。
每层浇注完成后,模板通过手动葫芦实现拆、装。
浇筑混凝土时,对于托梁以下直边墙砼浇注总高度为12.36 m,共分9次完成,每层浇注高度从第一层自下往上依次分别为1.5 m、1.45 m、1.45 m、1.45 m、1.45 m、1.45 m、1.45 m、1.45 m、0.71 m。
砼采用无轨灌车运输,泵送砼入模,砼强度达到8 Mpa 后开始拆模。
3.3 托梁施工技术
本工程托梁设钢筋,钢筋在现场绑扎;托梁顶部预埋43号钢轨,钢轨用钢筋焊接固定牢固,与另侧轨距精确控制在12.8 m,标高控制在±10 mm;经检查合格后方可关模。
3.4 拱部施工技术
拱部砼采用移动台车作为施工平台,移动台车由专业厂家设计制作,现场拼装。
台车采用液压或螺旋设计,竖向升降行程在20 cm,通过轨道用手动葫芦实现前后移动。
防水板采用自爬动焊机焊接,搭接宽度不小于15 cm,接头距砼施工缝距离不小于1 m。
当直边墙施工15 m 后,开始安装移动台车骨架,安装台车时脚手架作业平台计划一次搭设8 m长,台车骨架安装完成后先作为防水板作业平台,一次性将60 m防水板全部铺设完成,之后拼装台车面板。
本工程一次砼浇注长度6 m,砼方量55 m3,砼采用无轨灌车运输,泵送砼入模,砼强度达到24 Mpa 后开始拆模。
4 开挖施工技术措施
(1)控制超欠挖措施。
控制好超欠挖可以保证开挖成型、保证初期支护质量、有利于提高围岩本身的承载力、利于砼的喷射以及利于防水板的铺设等诸多优点,因此,采取以下措施严格控制超欠挖:①正
确标示开挖轮廓线。
在爆破前画开挖轮廓线时考虑施工误差,并考虑预留围岩变形和画线误差等因素,采用全站仪极坐标放样法准确的放出开挖轮廓线。
②保证钻孔质量。
炮孔间距符合钻爆设计。
周边眼间距的误差不大于5 cm,辅助眼间距的误差不大于10 cm,严格控制周边眼的外插角。
除掏槽眼、周边眼、底板眼外的其它眼孔方向与隧道方向平行,要求孔底在同一平面上。
钻孔结束后要清孔,炮眼用炮泥堵塞,确保单孔装药质量。
定人定位,明确分工,明确责任,不得混岗乱位。
③光爆。
首先合理选定钻爆参数,不断优化爆破设计。
实现光面爆破的最佳效果,使开挖轮廓圆顺,线性超挖及炮眼痕迹保存率合乎光爆技术要求。
④优化爆破设计。
根据隧道地质情况采用不同参数的光面控制爆破技术。
正确选用周边眼装药结构。
为保证爆破质量,周边眼采用小药卷炸药,间隔装药,并加强炮泥的堵塞质量。
非电毫秒雷管起爆。
按设计装药,并顺序起爆。
不断总结、修正爆破参数以达到最佳效果。
⑤采用先进的仪器进行开挖断面检查。
采用TC402全站仪进行爆破质量检查,及时提供超欠挖实测图。
根据提供的实测断面图,进行分析,及时处理,认真分析超欠挖的原因,以便采取对策。
⑥建立严格的激励、约束机制。
实行超欠挖奖罚制度,将奖罚数量与炮眼残留痕迹、超欠挖范围、超欠挖数量、炸药用量等直接挂钩,形成一套强有力的超欠挖管理办法。
(2)喷锚、量测。
及时支护,及时量测,及时反馈,及时修正。
同时在开挖后及时初喷,出碴后及时安装锚杆、复喷砼。
当围岩等级与设计不符时,特别是围岩变软弱时及时提出设计变更,加强支护,以确保围
岩的稳定。
5 结语
文章通过结合某隧道施工实例,针对该隧洞Ⅱ级围岩地段采取TBM拆卸洞,拆卸洞全长60 m,详细地总结出该施工技术,从拆卸洞开挖以及混凝土衬砌等施工环节来进一步探讨,同时针对长大隧道拆卸洞施工的安全性,结合实践经验,总结出开挖施工时的控制技术措施,有效地保证了拆卸洞施工过程的质量以及安全性,为今后进一步推广该技术提供借鉴。
参考文献
[1]范以田,章跃林,王彦峡.特大断面Ⅳ类围岩TBM拆卸洞室设计与施工技术研究[C]//和谐地球上的水工岩石力学——第三届全国水工岩石力学学术会议论文集.2009(25):30-31.
[2]梁文灏,刘赪.铁路特长隧道设计中的几点体会[J].铁道建筑,2006(21):28-34.
[3]李德武.秦岭隧道TBM拆卸洞室的稳定性分析[J].铁道建筑,2005(2):115-117.。