熔模铸造毕业设计说明书
《玻璃专业熔制车间毕业设计》指导书

玻璃专业熔制车间毕业设计指导书一、说明书1.总论:容:生产方法概况、特点、设计指导思想以及设计原则。
2.玻璃的成分设计容:设计原则、成分确定及性质计算(熔化温度、温度-粘度曲线、退火温度和密度)3.总工艺计算容:(1)主要技术经济指标的确定;①年工作日:冷修年,310~320天;非冷修年365天。
②拉引速度:③玻璃原板宽度:2.5~4.5m。
④机组利用率:96~98%。
⑤总成品率:72~75%。
可达90~95%。
⑥碎玻璃损失率:0.5%。
(2)工艺平衡计算;①玻璃成品产量的计算:计算出各种规格产品的产量;各种规格产品的全年平均生产天数。
②玻璃液熔化量:③配合料需要量:4.熔窑设计容:(1)熔窑种类的确定;(2)熔窑结构设计;①熔化部设计:熔化率的初步确定:平板池窑:熔化率K=2.0~3.0(t/m2d);500吨窑,K=2.35(t/m2d);700吨窑,K=2.78(t/m2d);熔化部面积的初步确定:熔化面积:F m = Qk(m2)式中:Q —熔窑的产量(t/d)熔化部窑池的长度和宽度的确定:熔化区宽度的确定:平板池窑:B m = 0.75Х10-2Q + 6.75 (m)TOLETO公司的经验公式:B m = 95002.5Q/400 (m)熔化区长度的确定:l m = K1ХB m (m)式中:K1—熔化区的长宽比,一般为1.8~2.4。
l m = d1 + d2(n-1)+ 1.0式中:d1—1#小炉中心线到前脸墙的距离,一般为3~4m,900吨窑达6.8mm。
d2—小炉中心线间距,一般为2.8~3.5m。
n—小炉对数。
澄清区长度的确定:一般在8.3~19m。
熔化部窑池深度的确定:熔化部窑池深度为1.2m。
熔化部面积的调整和复核:熔化率的复核:熔化部窑池大碹股跨比的确定:大型窑为17.5~18,中小型窑为18~19。
大碹的厚度确定:熔化部胸墙的高度和厚度的确定:熔化部胸墙的高度:由燃料的种类、喷嘴的安装方式确定。
铸造工艺设计说明书

铸造工艺设计说明书一、引言铸造工艺设计是针对特定铸件的生产过程进行规划和安排的过程。
本文旨在详细介绍铸造工艺设计的内容,确保读者能够全面理解并掌握该过程的要点。
二、铸造工艺设计的目标铸造工艺设计的目标是实现高质量的铸件生产。
具体而言,主要包括以下几个方面:1. 确定适宜的材料:根据铸件的要求和使用环境,选择合适的铸造材料,确保其具备良好的机械性能和耐腐蚀性能。
2. 设计合理的结构:在铸造工艺设计中,需要考虑到铸件的结构特点,合理设计铸件的形状和尺寸,以确保在铸造过程中易于铸造和冷却。
3. 确定适宜的工艺参数:通过合理选择浇注温度、保温时间、浇注速度等工艺参数,以确保铸件的成形质量。
4. 确保铸件的表面质量:通过采用适当的除砂、除气和清洁工艺,确保铸件表面的光洁度和平整度符合要求。
三、铸造工艺设计的步骤铸造工艺设计的步骤可以分为以下几个阶段:1. 铸件设计分析:在铸造工艺设计之前,需要对铸件的结构和形状进行分析。
通过对铸件进行结构强度分析、模具结构分析以及热力学分析等,确定铸造工艺的基本要求和技术指标。
2. 模具设计:根据铸件的形状和尺寸要求,进行模具设计。
包括模具的整体结构设计、分型面设计、模腔和冷却系统的设计等。
3. 工艺参数确定:根据铸件的特点和模具设计,确定适宜的浇注温度、浇注速度、保温时间等工艺参数。
这些参数对于保证铸件成形质量和提高生产效率具有重要作用。
4. 检验和调整:在铸造工艺设计结束后,需要进行试验验证和工艺调整。
通过对铸件进行质量检验,查找潜在问题并进行相应的调整,以确保最终生产的铸件质量达到要求。
四、铸造工艺设计的注意事项在铸造工艺设计的过程中,需要特别注意以下几个方面:1. 材料特性:铸造工艺设计需要充分了解所选材料的特性和性能,确保其适用于特定的铸件要求。
同时,需要根据材料的熔化温度和流动性,合理选择浇注温度和浇注系统。
2. 模具设计:模具设计需要兼顾铸件的结构特点和生产效率。
熔模铸造毕业设计

熔模铸造毕业设计熔模铸造毕业设计熔模铸造是一种先进的金属铸造技术,也是我毕业设计的主题。
在这篇文章中,我将探讨熔模铸造的原理、应用以及我在毕业设计中的研究内容。
一、熔模铸造的原理熔模铸造是一种通过制作熔模来铸造复杂形状的金属零件的方法。
它的原理是先制作出一个与所需零件形状相同的模具,然后通过加热模具,使模具内的熔融金属填充进去,并冷却凝固,最后获得所需的零件。
熔模铸造的核心在于熔模的制作。
一般来说,熔模可以使用多种材料制作,如石膏、陶瓷、蜡等。
其中,蜡模是最常用的材料,因为它具有良好的可塑性和热稳定性。
通过制作蜡模,可以实现复杂形状的零件铸造。
二、熔模铸造的应用熔模铸造在工业生产中有广泛的应用。
它可以用于制造各种复杂形状的零件,如汽车发动机缸体、航空发动机叶片等。
相比于其他铸造方法,熔模铸造具有以下优势:1. 高精度:熔模铸造可以实现高精度零件的制造,因为模具的制作和熔模的填充过程可以控制得很精确。
2. 节约材料:相比于其他铸造方法,熔模铸造可以节约材料。
因为熔模铸造是通过填充熔融金属来制造零件,不需要额外的材料。
3. 良好的表面质量:熔模铸造可以获得良好的表面质量,因为熔模的表面光滑,可以直接影响到最终零件的表面质量。
三、我的毕业设计内容在我的毕业设计中,我选择了熔模铸造技术,并以某种特定的零件为研究对象。
我的研究内容主要包括以下几个方面:1. 熔模材料的选择:在研究中,我将对不同材料的熔模进行比较,包括蜡模、陶瓷模等。
通过对比它们的性能和成本,选择最适合的熔模材料。
2. 熔模制作工艺的优化:在研究中,我将对熔模的制作工艺进行优化,以提高熔模的质量和生产效率。
我将尝试不同的工艺参数,如温度、压力等,以找到最佳的制作工艺。
3. 铸造过程的模拟与分析:在研究中,我将使用计算机模拟软件对熔模铸造过程进行模拟与分析。
通过模拟,我可以预测铸造过程中可能出现的问题,如气孔、缩松等,并提前采取相应的措施。
4. 零件性能的测试与评估:在研究中,我将对熔模铸造获得的零件进行性能测试与评估。
毕业(设计)论文开题报告熔模铸造

南昌工程学院
10级毕业(设计)论文开题报告
机械与电气工程学院系(院)
材料成型及控制工程专业
南昌工程学院教务处订制
题目:导向器体精密铸件蜡模模具设计及其成型工艺
一、选题的依据及课题的意义
熔模铸造又称熔模精密铸造,是一种净行成型工艺。它是用可熔(溶)行一次模样和型芯使铸件成型的铸造方法。其可生产的各种合金精密、复杂、接近于零件最后形状的件,适与中小型精密铸件。
四、目标、主要特色及工作进度
目标:确定导向器体精密铸造模具设计和生产工艺。
主要特色:熔模铸造是一种尽形铸造技术,其生产铸件可为各种金属的精密、复杂、接近与零件最后形状的件,可不经过加工直接使用或少加工使用。本设计的产品通过软件三维造型获得二维造型,根据三维可以直接测量数据,方便快捷了解产品参数,提高产品从设计到工业化生产的效率,节约大量的时间和成本,让企业快速抢占市场,节约大量时间和成本。
随经济社会发展,制造行业迅速发展,不断提出新的要求,为了顺应我国机械工业、航空工业,以及满足国防工业的有关需求,熔模铸造随之发展起来,并从有余量发展到无余量熔模精密铸造。无余量熔模铸造显现出特有的优势,它有效地降低材料、制造和维修成本,缩短产品研制周期,延长使用寿命,提高整体性能,而且适合大批量生产或小批量生产各种结构、形状复杂的铸件,尺寸精度高,表面粗糙度小,合金材料不受限制,因此应用十分广泛。
铸钢齿轮熔模铸造工艺设计
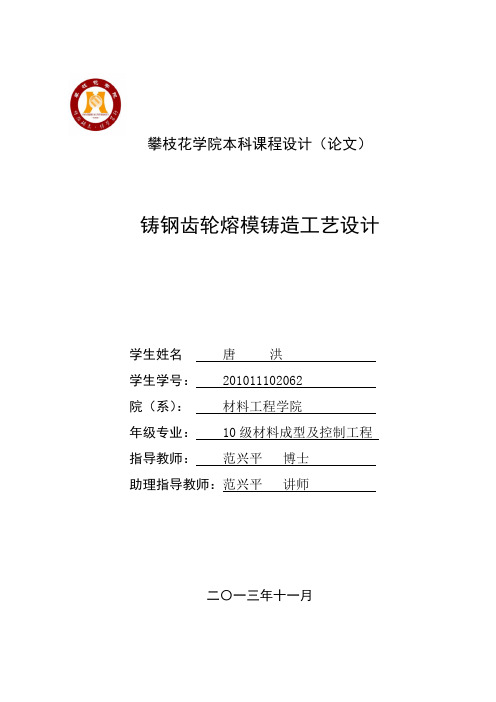
攀枝花学院本科课程设计(论文)铸钢齿轮熔模铸造工艺设计学生姓名唐洪学生学号: ************ 院(系):材料工程学院年级专业: 10级材料成型及控制工程指导教师:范兴平博士助理指导教师:范兴平讲师二〇一三年十一月攀枝花学院本科学生课程设计任务书课程设计(论文)指导教师成绩评定表摘要熔模铸造在我国具有悠久的历史。
它是一种少切削或无切削的铸造工艺,铸造行业中的一项优异的工艺技术,是一种无分型面的特种铸造方法。
熔模铸造是用一种易形成模样的材质如石蜡等做成零件的模型,然后在表面涂一层耐火材料和型砂形成一个模壳,经过脱蜡后对壳进行焙烧使壳具有一定的强度,然后进行浇注,经冷却落砂后生产出产品。
本课程设计主要是对齿轮的熔模铸造进行了设计,对齿轮的材料进行了分析,和在铸造中遇到的一系列问题,并一一进行处理。
在模料的选择中进行了分析并列举了制模的操作步骤等。
关键字:熔模铸造,齿轮,工艺设计目录摘要 (Ⅰ)1.零件分析 (1)1.1齿轮的形状分析 (1)1.2 齿轮材质分析 (1)2.选择基准面…………………………………………………………………………3.制模工部设计………………………………………………………………………3.1模料选择……………………………………………………………………………3.2制模设备与工艺…………………………………………………………………… 3.2.1制模设备………………………………………………………………………3.2.2蜡膏制备………………………………………………………………………3.2.3制模工艺………………………………………………………………………3.2.4压型制造………………………………………………………………………3.3蜡模修整………………………………………………………………………………4.制壳工部设计…………………………………………………………………………4.1 耐火材料选择………………………………………………………………………4.2涂料的配置及操作程序…………………………………………………………… 4.3 制壳………………………………………………………………………………4.4 脱蜡和型壳焙烧…………………………………………………………………5.熔炼工部设计…………………………………………………………………………5.1 熔炼操作步骤………………………………………………………………………6.浇注工部设计……………………………………………………………………………7.落纱清理及质检工部设计………………………………………………………………8.铸件表面处理方案的选择………………………………………………………………9.结束语……………………………………………………………………………………10.参考文献…………………………………………………………………………………1 零件分析1.1齿轮形状分析齿轮的外圆直径为φ258.26mm,宽为60mm,轮毂上有均匀分布的六个直径为φ40mm的孔,齿轮中心孔的直径为50mm。
铸造工艺毕业设计说明书

轮毂的铸造工艺及其热芯盒模具设计摘要随着社会的发展,机动车辆在生产和生活中的越来越广泛。
缸盖是机动车辆中的重要部件,其壳体的结构及加工精度直接影响轮毂的正常工作,因此研究轮毂的加工方法和工艺的编制是十分必要和有意义的。
本设计是对前轮毂零件进行铸造毛坯工艺设计。
根据零件的使用条件、结构特点、生产批量,结合工厂现有设备等进行铸造工艺分析,确定了铸造方法、造型及造芯方法、凝固原则及浇注位置、分型面、砂箱中铸件数量、砂型数量等,完成了砂芯、浇注系统、冒口及冷铁、相关工装设备等设计。
本设计采用壳芯盒法制芯,根据芯子的形状及重量选用763射芯机进行射芯,采用酚醛树脂砂作为制芯材料。
接着对壳芯盒本体进行设计,芯盒本体的设计主要包括芯盒的结构及分盒面的选择,射砂口的设计,芯盒材料的选择,芯盒中砂芯的数目,排气装置的设计以及芯盒顶出机构的设计。
关键字:砂型铸造,工艺分析,工艺设计,壳芯工装设计The Casting Technology and Hot Core BoxMold Design of HubABSTRACTAlong with social develop ment, motor vehicle used in production and life is increasingly wide. Hub is an important vehicle component and its interior structure and processing precisio n directly affect the hub normal work. Study hub cast processing methods and techniq ues of preparation is ne cessary and meaningful.This design is the casting techno logy design for front hub in vehicle. According to the application cond itions, structural features, production batch and existing equipment, it determines the method of casting, modeling, core making, solid ification principles and pouring position, parting surface, the quantity o f casting and mo ld etc. It comp letes the design of sand core, pouring system, riser, chill and related equipment etc.This design uses the shell core box mak ing core. According to the shape and weight it choose 763 shoot core machine shoot core and use phenolic resin sand as the core mak ing material. Then design the shell core box body, the core box body design mainly includes the core box structure and box surface selectio n, sand jetting port core box design, choice of materials, core box of sand core in number, exhaust design and installation o f the core box lifting mechanism design.KEY WORDS:sand casting,technolo gy analysis,techno logy design,Shell core fixture design目录前言 (1)第一章铸造工艺设计 (2)§1.1 零件概述 (2)§1.1.1 零件信息 (2)§1.1.2 技术要求 (2)§1.2 铸造工艺方案的确定 (3)§1.2.1 造型、造芯方法及铸型种类的确定 (3)§1.2.2 浇注位置和分型面的确定 (3)§1.2.3 砂箱中铸件数目的确定 (6)§1.3工艺参数的选择 (7)§1.3.1 铸造收缩率 (7)§1.3.2 机械加工余量、铸件的尺寸和重量偏差 (7)§1.3.3 拔模斜度的确定 (8)§1.3.4 铸造圆角的确定 (8)§1.3.5 最小铸出口及槽 (8)§1.4 浇注系统的设计 (8)§1.4.1 浇注系统的概述 (8)§1.4.2 浇注系统类型的选择 (9)§1.4.3 浇注系统的设计与计算 (10)§1.4.4 出气孔的设计 (13)§1.5 砂芯的设计 (13)§1.5.1 砂芯的概述 (13)§1.5.2 砂芯数量的确定 (14)§1.5.3 芯头的设计 (14)§1.5.4 壳芯的制备 (15)§1.6 冒口及冷铁的设计 (15)§1.6.1 冒口的设计 (15)§1.6.2 冷铁的设计 (16)第二章铸造工艺装备设计 (17)§2.1 模板 (17)§2.1.1 模样的设计 (17)§2.1.2 模底板的设计 (17)§2.2 壳芯工装设计 (18)§2.2.1 壳芯的概述 (18)§2.2.2 壳芯工艺 (18)§2.2.3 壳芯盒的材料 (20)§2.2.4 壳芯工装设计 (20)结论 (25)参考文献 (26)致谢 (27)前言近年来,能源,环境和安全问题受到普遍关注,汽车行业尤为突出。
熔模铸造课程设计详细内容与要求
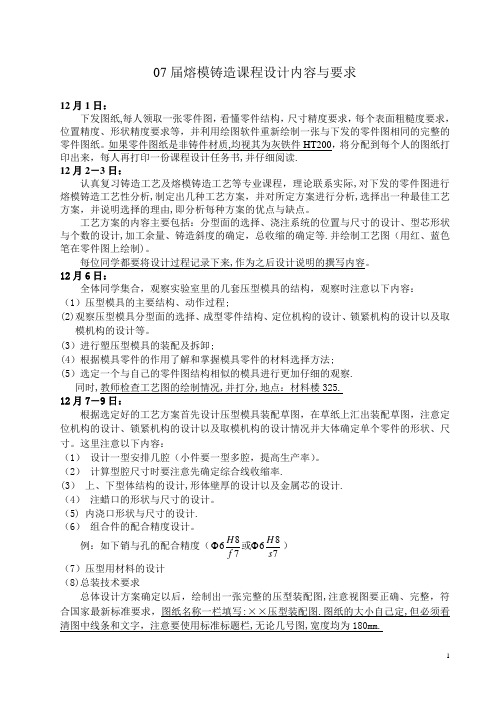
07届熔模铸造课程设计内容与要求12月1日:下发图纸,每人领取一张零件图,看懂零件结构,尺寸精度要求,每个表面粗糙度要求,位置精度、形状精度要求等,并利用绘图软件重新绘制一张与下发的零件图相同的完整的零件图纸。
如果零件图纸是非铸件材质,均视其为灰铁件HT200,将分配到每个人的图纸打印出来,每人再打印一份课程设计任务书,并仔细阅读.12月2-3日:认真复习铸造工艺及熔模铸造工艺等专业课程,理论联系实际,对下发的零件图进行熔模铸造工艺性分析,制定出几种工艺方案,并对所定方案进行分析,选择出一种最佳工艺方案,并说明选择的理由,即分析每种方案的优点与缺点。
工艺方案的内容主要包括:分型面的选择、浇注系统的位置与尺寸的设计、型芯形状与个数的设计,加工余量、铸造斜度的确定,总收缩的确定等.并绘制工艺图(用红、蓝色笔在零件图上绘制)。
每位同学都要将设计过程记录下来,作为之后设计说明的撰写内容。
12月6日:全体同学集合,观察实验室里的几套压型模具的结构,观察时注意以下内容:(1)压型模具的主要结构、动作过程;(2)观察压型模具分型面的选择、成型零件结构、定位机构的设计、锁紧机构的设计以及取模机构的设计等。
(3)进行塑压型模具的装配及拆卸;(4)根据模具零件的作用了解和掌握模具零件的材料选择方法;(5)选定一个与自己的零件图结构相似的模具进行更加仔细的观察.同时,教师检查工艺图的绘制情况,并打分,地点:材料楼325.12月7-9日:根据选定好的工艺方案首先设计压型模具装配草图,在草纸上汇出装配草图,注意定位机构的设计、锁紧机构的设计以及取模机构的设计情况并大体确定单个零件的形状、尺寸。
这里注意以下内容:(1) 设计一型安排几腔(小件要一型多腔,提高生产率)。
(2) 计算型腔尺寸时要注意先确定综合线收缩率.(3) 上、下型体结构的设计,形体壁厚的设计以及金属芯的设计.(4) 注蜡口的形状与尺寸的设计。
(5) 内浇口形状与尺寸的设计.(6) 组合件的配合精度设计。
毕业论文设计-电缆插头熔模铸造压型设计

前言熔模铸造又称"失蜡铸造",通常是在蜡模表面涂上数层耐火材料,待其硬化干燥后,将其中的蜡模熔去而制成型壳,再经过焙烧,然后进行浇注,而获得铸件的一种方法,由于获得的铸件具有较高的尺寸精度和表面光洁度,故又称"熔模精密铸造"。
可用熔模铸造法生产的合金种类有碳素钢、合金钢、耐热合金、不锈钢、精密合金、永磁合金、轴承合金、铜合金、铝合金、钛合金和球墨铸铁等。
熔模铸件的形状一般都比较复杂,铸件上可铸出孔的最小直径可达0.5mm,铸件的最小壁厚为0.3mm。
在生产中可将一些原来由几个零件组合而成的部件,通过改变零件的结构,设计成为整体零件而直接由熔模铸造铸出,以节省加工工时和金属材料的消耗,使零件结构更为合理。
摘要:本设计主要内容是熔模铸造的压型设计,针对给定的电缆插头进行综合分析,从而完成此零件的熔模压型设计。
确定铸件图及完成相关的准备工作后就可进行压型设计。
设计内容主要包括确定压型的结构、尺寸、型芯、排气系统和顶杆机构等。
设计的压型应力求结构简单,加工方便,选材合理,安全可靠。
运用cad,proe等作图软件,绘制压型的零件图和装配图。
关键词:熔模铸造,压型设计,制图Abstract:The design of the main contents of graduation is Investment Casting Design mold.For cable plug to make a comprehensive analysis,Parts of the mold to complete the pletion of the preparatory work such as casting plans, can Design mold.The design of the Content is to determine the structure of die, size,core, Exhaust System , Top of the body. Mold design should seek to simple structure, convenient processing, material selection reasonable, safe and e the mappingsoftware such as CAD and PROE, completion of the mold parts drawings and engineering drawings.Keywords:Investment casting、mold design、graphics目录1零件分析…………………………………………………………………………2选择基准面…………………………………………………………………………3模具结构类型与注蜡机的选择…………………………………………………4分型面的确定……………………………………………………………………5确定浇注口的位置…………………………………………………………………6型芯结构………………………………………………………………………7型腔结构………………………………………………………………………8设计合模机构和其它机构零件…………………………………………………9各尺寸的计算………………………………………………………………………10零件结构设计…………………………………………………………………11模具装配图…………………………………………………………12结论13致谢14参考文献1.零件分析本毕业设计所要完成的是电缆插头的熔模铸造的压型设计,电缆插头机构如图1所示。
毕业设计--熔模铸造工艺设计

目录中文摘要英文摘要一、概述 (3)1、定义 (3)2、特点 (3)3、发展历史 (3)4、应用 (4)二、熔模铸造工艺设计 (5)1、零件图 (5)2、铸件结构工艺性分析 (5)3、确定工艺方案和工艺参数 (6)4、设计浇注系统 (9)5、绘制铸件图 (12)三、压型设计 (13)1、压型设计的基本要求及参数选取 (13)2、成型部分形体结构部分设计 (14)3、压型工作图设计 (17)4、压型图 (20)四、熔模的制造 (22)1、模料的选取 (22)2、模料的配制 (23)3、制熔模 (23)4、制模组 (24)5、模组的除油和脱脂 (26)五、型壳的制造 (27)1、制造型壳用的材料 (27)2、涂料的配制 (28)3、涂挂涂料及撒砂 (32)4、型壳的干燥和硬化 (32)六、脱蜡与焙烧 (34)1、脱蜡 (34)2、脱蜡的工艺过程 (34)3、模料的回收处理 (34)4、焙烧 (35)七、熔炼与浇注 (36)1、黄铜的特性 (36)2、黄铜的牌号选用 (37)3、锰黄铜的熔炼准备 (37)4、中间合金 (38)5、熔剂 (39)6、配料 (39)7、熔炼工艺 (40)8、浇注 (41)八、铸件的后处理 (42)1、熔模铸件清理 (42)2、从铸件和金属浇注系统上清除新型壳 (42)3、铸件上残留耐火材料的清除 (42)参考文献 (44)致谢 (45)一、概述1、定义熔模铸造又称"失蜡铸造",通常是在蜡模表面涂上数层耐火材料,待其硬化干燥后,将其中的蜡模熔去而制成型壳,再经过焙烧,然后进行浇注,而获得铸件的一种方法,由于获得的铸件具有较高的尺寸精度和表面光洁度,故又称"熔模精密铸造"。
2、特点1)铸件尺寸精确一般可达CT4-62)可铸造形状复杂的铸件,特别可以铸造高温合金铸件3)不受铸件材料的限制4)铸件尺寸不能太大,重量也有限5)工艺过程复杂、工序繁多,使生产过程控制难度大增6)铸件冷却速度慢,铸件晶粒粗大压制熔模时,采用型腔表面光洁度高的压型,因此,熔模的表面光洁度也比较高。
(完整word版)铸造工艺课程设计说明书

铸造工艺课程设计说明书目录1 前言 (4)1。
1本设计的意义 (4)1.1.1 本设计的目的 (4)1.1。
2 本设计的意义 (5)1.2本设计的技术要求 (5)1。
3本课题的发展现状 (5)1.4本领域存在的问题 (6)1.5本设计的指导思想 (6)1。
6本设计拟解决的关键问题 (7)2 设计方案 (7)2。
1零件的材质分析 (8)2.2支座工艺设计的内容和要求 (9)2.3造型造芯方法的选择 (11)2。
4浇注位置的选择与分型面的选择 (12)2。
4.1 浇注位置的选择 (12)2.4.2 分型面的确定 (14)2.4.3 砂箱中铸件数目的确定 (15)3 设计说明 (17)3。
1工艺设计参数确定 (17)3。
1.1 最小铸出的孔和槽 (17)3.1.2 铸件的尺寸公差 (18)3。
1.3 机械加工余量 (19)3。
2铸造收缩率 (19)3。
2。
1 起模斜度 (20)3.2。
2 浇注温度和冷却时间 (21)3。
3砂芯设计 (22)3.3。
1 芯头的设计 (22)3。
3。
2 砂芯的定位结构 (23)3。
3.3 芯骨设计 (23)3.3.4 砂芯的排气 (23)3。
4浇注系统及冒口,冷铁,出气孔的设计 (24)3。
4.1 浇注系统的类型和应用范围 (24)3。
4。
2 确定内浇道在铸件上的位置、数目、金属引入方向 (24)3.5决定直浇道的位置和高度 (25)3.5.1 计算内浇道截面积 (25)3.5.2 计算横浇道截面积 (26)3。
5。
3 计算直浇道截面积 (27)3。
5.4 冒口的设计 (27)4 铸造工艺装备设计 (28)4。
1模样的设计 (28)4。
1.1 模样材料的选用 (28)4.1。
2 金属模样尺寸的确定 (29)4。
1。
3 壁厚与加强筋的设计 (29)4。
1。
4 金属模样的技术要求 (29)4.1。
5 金属模样的生产方法 (29)4.2模板的设计 (30)4。
2。
1 模底板材料的选用 (30)4.2。
熔模铸造毕业设计说明书
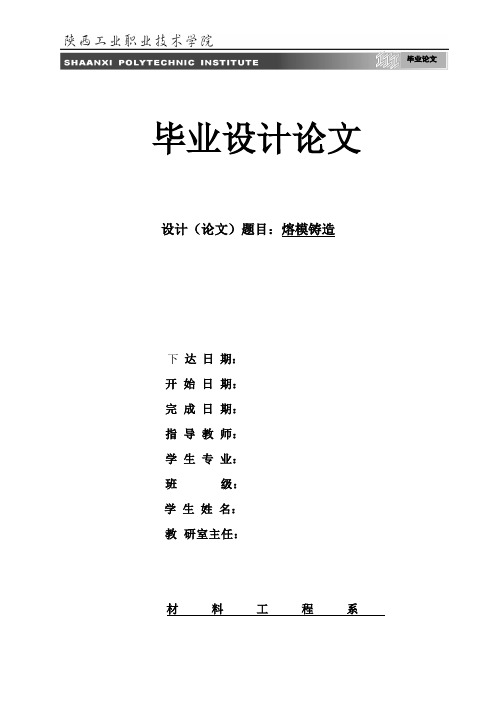
毕业论文毕业设计论文设计(论文)题目:熔模铸造下达日期:开始日期:完成日期:指导教师:学生专业:班级:学生姓名:教研室主任:材料工程系陕西工业职业技术学院毕业设计(论文)任务书一、设计(论文)内容及要求:(一)设计(论文)内容1. 撰写熔模技术发展现状的研究文章;2. 编制铸件(附零件图)铸造工艺规程,绘制铸造工艺图,填写铸造工艺过程卡片;3. 绘制铸件图和总装图;4. 设计熔模压型模具,绘制模具零件图;5. 撰写设计说明书(论文)。
(二)要求1.通过理论学习,熟悉熔模工艺过程,结合生产实际完成本次设计任务;2. 工程图用AutoCAD软件绘制并打印;3. 说明书(论文)按照学院统一格式,使用word文档并打印。
4. 提交资料包括:(1)毕业设计任务书;(2)熔模铸造技术发展现状的研究文章;(3)“四图一卡”,即绘制铸造工艺图;铸件图;零件图;铸型装配图;铸造工艺卡;(4)设计说明书(论文);所有提交的资料包括打印文件和电子文件。
二、技术指标:1.生产类型:大批大量生产2.生产及质量要求:满足产品图纸的各项技术要求;工艺出品率较高,废品率5%以下;生产效率高;对工人技术水平要求较低,操作简便。
3.生产工艺要求:熔模铸造;所用熔模模具自行设计;4.技术水平要求:尽量采用先进技术,创新项目应符合国家环保及安全生产要求。
陕西工业职业技术学院毕业设计(论文)任务书进程计划表摘要本设计是通过熔模铸造的方法来铸造管接头,先分析铸件,进行工艺设计,确定了主要参数,进行压型设计,绘制出铸件工艺图,进行熔模制造-型壳制造-脱蜡焙烧-熔炼浇注-后处理分析,结合具体零件,通过具体分析,最后有针对性的制定出材料为锡青铜的管接头熔模铸造工艺方案。
根据现实生产的应用,表明:熔模铸造适用于实际生产中管接头的铸造。
关键词:熔模铸造,锡青铜,工艺流程ABSTRACTThis design is through investment casting methods to cast pipe joints, first analysis of castings, for process design, to determine the main parameters for pressure-type design, the casting process to map out plans to carry out melt-mold making - Shell Manufacturing - Dewaxing roasting - Melting Pouring - post-processing analysis of specific parts, through a specific analysis, and finally to develop targeted materials bronze fittings of Investment Casting Process.Applications based on the realities of production, indicating that: the application of investment casting in the actual production of the control valve body casting.Key word:Melt mold casting, gun metal, technical process目录毕业设计任务书中文摘要英文摘要一、概述 (1)1、定义 (1)2、熔模铸造的特点 (1)3、发展历史 (2)4、应用范围 (2)二、熔模工艺设计 (4)1、零件图 (4)2、铸件结构工艺性分析 (4)3、确定工艺方案和工艺参数 (5)4、浇注系统 (7)5、绘制铸造工艺图 (10)三、压型设计 (11)1、装配图 (11)2、压型分类 (11)3、分型面选择 (12)4、型体设计 (13)5、压型排气 (16)6、压型冷却 (17)7、压型工作图设计 (17)8、注蜡孔的设计 (19)四、熔模的制造 (20)1、熔模 (20)2、模料的选取和配制 (20)3、制熔模 (21)4、制模组 (23)五、型壳的制造 (26)1、型壳服役性能的要求 (26)2、制造型壳的耐火材料及黏结剂 (26)3、制造型壳用涂料及配制 (27)4、制壳工艺 (31)六、脱蜡与焙烧 (34)1、脱蜡 (34)2、焙烧 (35)七、熔炼与浇注 (36)1、材料的选择 (36)2、选择炉型 (37)3、熔炼准备 (38)4、配料 (40)5、熔炼工艺 (42)八、铸件的后处理 (44)1、型壳的清理 (44)2、切割浇冒口 (46)参考文献 (47)致谢 (48)一、概述1、定义熔模铸造又称“失蜡铸造”,通常是在可熔模样的表面涂上数层耐火材料,待其硬化干燥后,加热将其中模样熔去,而获得具有与模样形状相应空腔的型壳,再经过焙烧,然后在型壳温度很高的情况下进行浇注,而获得铸件的一种方法,由于获得的铸件具有较高的尺寸精度和表面光洁度,故又称“熔模精密铸造”。
熔模铸造说明书
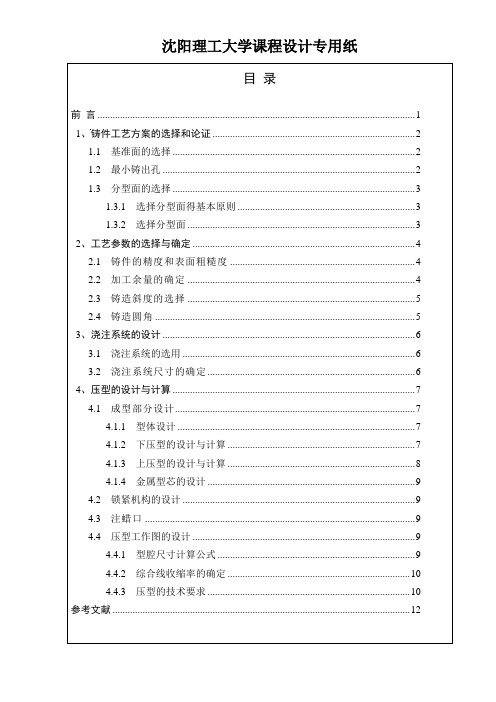
目录前言 (1)1、铸件工艺方案的选择和论证 (2)1.1 基准面的选择 (2)1.2 最小铸出孔 (2)1.3 分型面的选择 (3)1.3.1 选择分型面得基本原则 (3)1.3.2 选择分型面 (3)2、工艺参数的选择与确定 (4)2.1 铸件的精度和表面粗糙度 (4)2.2 加工余量的确定 (4)2.3 铸造斜度的选择 (5)2.4 铸造圆角 (5)3、浇注系统的设计 (6)3.1 浇注系统的选用 (6)3.2 浇注系统尺寸的确定 (6)4、压型的设计与计算 (7)4.1 成型部分设计 (7)4.1.1 型体设计 (7)4.1.2 下压型的设计与计算 (7)4.1.3 上压型的设计与计算 (8)4.1.4 金属型芯的设计 (9)4.2 锁紧机构的设计 (9)4.3 注蜡口 (9)4.4 压型工作图的设计 (9)4.4.1 型腔尺寸计算公式 (9)4.4.2 综合线收缩率的确定 (10)4.4.3 压型的技术要求 (10)参考文献 (12)前言熔模铸造又称"失蜡铸造",通常是指在易熔材料制成模样,在模样表面包覆若干层耐火材料制成型壳,再将模样熔化排出型壳,从而获得无分型面的铸型,经高温焙烧后即可填砂浇注的铸造方案。
由于模样广泛采用蜡质材料来制造,故常将熔模铸造称为“失蜡铸造”。
可用熔模铸造法生产的合金种类有碳素钢、合金钢、耐热合金、不锈钢、精密合金、永磁合金、轴承合金、铜合金、铝合金、钛合金和球墨铸铁等。
熔模铸件的形状一般都比较复杂,铸件上可铸出孔的最小直径可达0.5mm,铸件的最小壁厚为0.3mm。
在生产中可将一些原来由几个零件组合而成的部件,通过改变零件的结构,设计成为整体零件而直接由熔模铸造铸出,以节省加工工时和金属材料的消耗,使零件结构更为合理。
熔模铸件的质量大多为几十克到几千克,太重的铸件用熔模铸造法生产较为麻烦,但目前生产的熔模铸件的质量已达1000kg左右。
熔模铸造工艺设计(3篇)

第1篇摘要:熔模铸造是一种精密铸造方法,具有精度高、表面光洁、尺寸稳定性好等优点。
本文介绍了熔模铸造的基本原理、工艺流程、材料选择、熔模制作、浇注系统设计、冷却系统设计、质量检测等方面的内容,以期为熔模铸造工艺设计提供参考。
一、熔模铸造基本原理熔模铸造是利用蜡或塑料等可熔化材料制作成具有复杂形状的熔模,然后将熔模放入型壳中,通过加热使熔模熔化,金属液体充填熔模所形成的空腔,冷却凝固后取出型壳,得到与熔模形状相同的金属铸件。
熔模铸造工艺具有以下特点:1. 精度高:熔模铸造的精度可达0.1mm,表面光洁度可达Ra0.1~0.2μm。
2. 材料广泛:可用于各种金属材料的铸造,如不锈钢、铝合金、铜合金、钛合金等。
3. 可铸性优良:熔模铸造适用于形状复杂、尺寸精度要求高的铸件。
4. 生产周期短:熔模铸造工艺流程短,生产周期短,可满足大批量生产的需求。
二、熔模铸造工艺流程1. 设计与工艺分析:根据铸件要求,进行铸件设计、材料选择、工艺参数确定等。
2. 熔模制作:采用蜡或塑料等可熔化材料制作熔模,熔模形状与铸件相同。
3. 型壳制作:将熔模放入型壳中,通过加热使熔模熔化,金属液体充填熔模所形成的空腔。
4. 浇注系统设计:根据铸件要求,设计合理的浇注系统,确保金属液体充填铸件空腔。
5. 冷却系统设计:设计合理的冷却系统,保证铸件冷却均匀,避免产生缩孔、裂纹等缺陷。
6. 铸造:将金属液体浇注到型壳中,经过冷却凝固后取出型壳,得到铸件。
7. 后处理:对铸件进行打磨、抛光、热处理等工序,提高铸件质量。
三、材料选择1. 熔模材料:蜡、塑料等可熔化材料,具有良好的可塑性、熔点适中、表面光洁度高。
2. 型壳材料:耐火度高、导热性好、强度高的材料,如耐火土、硅砂等。
3. 金属液体:根据铸件材料要求,选择合适的金属液体,如不锈钢、铝合金、铜合金等。
四、熔模制作1. 熔模设计:根据铸件形状、尺寸、精度要求,设计合理的熔模结构。
2. 熔模制造:采用蜡或塑料等材料,采用手工或机械加工方法制作熔模。
铸造工艺设计说明书

铸造工艺设计说明书一、铸造工艺设计的目的和意义铸造是将液态金属浇注到与零件形状、尺寸相适应的铸型型腔中,待其冷却凝固,以获得毛坯或零件的生产方法。
铸造工艺设计则是根据零件的结构特点、技术要求、生产批量等因素,确定铸造方法、铸型分型面、浇注系统、冒口和冷铁等工艺参数,以保证获得高质量的铸件,并提高生产效率、降低成本。
良好的铸造工艺设计具有重要意义。
首先,它能够保证铸件的质量,减少铸造缺陷的产生,如气孔、缩孔、夹渣等。
其次,合理的工艺设计可以提高生产效率,降低生产成本,缩短生产周期。
此外,还能为后续的机械加工提供良好的基础,减少加工余量,提高材料利用率。
二、零件分析1、零件结构对需要铸造的零件进行结构分析,包括形状、尺寸、壁厚均匀性等。
例如,形状复杂的零件可能需要采用复杂的分型面和浇注系统;壁厚不均匀的零件容易产生缩孔、缩松等缺陷,需要合理设置冒口和冷铁。
2、技术要求明确零件的技术要求,如材质、力学性能、表面质量等。
不同的材质和性能要求会影响铸造工艺的选择和参数的确定。
3、生产批量生产批量的大小直接影响铸造方法的选择。
大批量生产时,通常采用金属型铸造、压力铸造等高效率的铸造方法;小批量生产则多采用砂型铸造。
三、铸造方法的选择1、砂型铸造砂型铸造是应用最广泛的铸造方法,其优点是成本低、适应性强,可生产各种形状和尺寸的铸件。
但砂型铸造的生产效率较低,铸件的表面质量相对较差。
2、金属型铸造金属型铸造的生产效率高,铸件的精度和表面质量好,但模具成本高,适用于大批量生产形状简单、尺寸较小的铸件。
3、压力铸造压力铸造能生产出形状复杂、薄壁的高精度铸件,但设备投资大,主要用于生产大批量的有色金属铸件。
4、熔模铸造熔模铸造适用于生产形状复杂、精度要求高、难以机械加工的小型零件。
根据零件的结构、技术要求和生产批量,综合考虑选择合适的铸造方法。
四、铸型分型面的选择分型面的选择直接影响铸型的制造、造型操作的难易程度以及铸件的质量。
铸造设计说明书
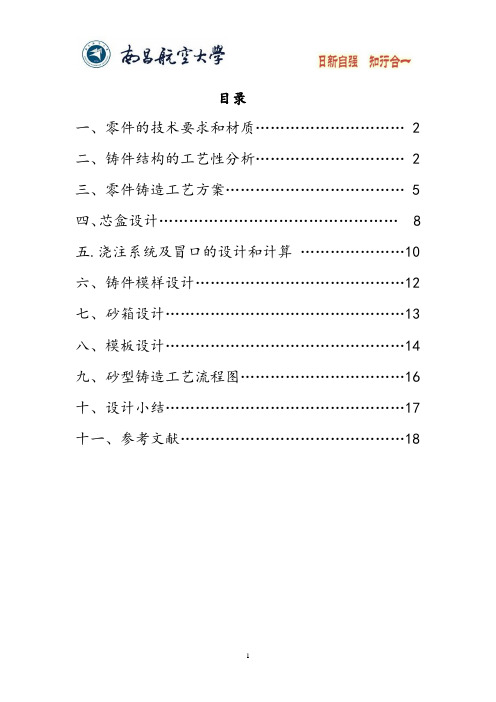
目录一、零件的技术要求和材质 (2)二、铸件结构的工艺性分析 (2)三、零件铸造工艺方案 (5)四、芯盒设计 (8)五.浇注系统及冒口的设计和计算 (10)六、铸件模样设计 (12)七、砂箱设计 (13)八、模板设计 (14)九、砂型铸造工艺流程图 (16)十、设计小结 (17)十一、参考文献 (18)设计内容、设计步骤、公式及计算备注一、零件的技术要求及材质零件名称:铝支座1.零件的技术要求铸件尺寸公差按GB6414 - 86 CT102.零件的材质分析铸件成型材料为ZL102,其化学成分如下:表一 ZL102化学成分Si Cu Mg Mn Al10.0-13.0 ≤0.30(杂质) ≤0.10 ≤0.5(杂质)余量由于ZL102成分在共晶点左右,故在铝硅二元系中,铸造性能最好强度也较高,致密度较好,但塑性较低。
具有良好的抗蚀性,耐磨性和耐热性。
必须进行热处理,提高力学性能。
适用于薄壁复杂铸件及对气密性要求较高的铸件以及压铸件。
二.铸件结构的工艺性分析从铸造工艺角度,结合零件结构特征对铸造生产方法进行选择。
本设计采用砂型造型方法。
小批量生产。
ZL102砂型铸造小批量生产1.铸件壁厚铸件的壁厚要力求均匀,壁的后、薄不宜相差悬殊,在保证能浇注成型的条件下尽量采用最小壁厚;尽量避免采用大的薄壁平面,若必需采用大的薄壁平面时,则设有铸孔或加强筋。
ZL102砂型铸造中的最小壁厚为3mm。
盖的零件图如图所示,壁厚基本均匀,主要壁厚10mm,最小壁厚10mm,最大壁厚10mm,为一小型铸件;铸件除满足几何尺寸精度及材质方面的要求外,无其他特殊技术要求。
2.壁的连接铸件的连接应圆滑过度,并应尽量避免铸件有厚大的热节点,尤其是三个以上断面集结于一点或一根线上,都是比较难于铸造的。
最小壁厚 10mm三.铸造工艺方案的设计铸造工艺方案设计的内容主要有铸造工艺方法的选择,铸件浇注位置及分型面的选择,铸件初加工基准面的选择,铸造工艺设计有关工艺参数的选择等。
熔模铸造毕业设计

摘要箱体类零件的成形,许多工厂采取铆焊拼接或砂型铸造的方法。
前者制造过复杂,生产成本高,而且延长生产周期。
后者尺寸精度低,表面质量差。
随着科学技术的不断发展和生产水平的不断提高以及人类社会生活的需要,对铸造生产提出了一系列新的、更高的要求,熔模铸造正发挥着越来越重要的作用。
熔模铸造就是在蜡模的表面涂多层耐火材料,待硬化干燥后,加热将蜡模熔去,从而获得具有与蜡模形状相应空腔的型壳,再经,焙烧之后进行浇注而获得铸件的一种方法。
工艺流程的特点:使用易熔模,无分型面;用涂料浆制型壳,涂层对易熔模复印性好;热壳浇注金属液充型好。
因此,熔模铸造可生产尺寸精确、表面粗糙度低的复杂件,既适用于大批生产,也适用于小批生产,甚至单件生产。
它的产品精密、复杂,接近于零件最后的形状,可不加工或很少加工就可直接使用,被称为近净成型的一种先进工艺。
关键词:箱体类零件;熔模铸造;工艺流程AbstractBox part of forming, many factories adopt sand casting splicing or welding method. The former made complex, high production costs, and prolong production cycle. The latter dimension accuracy, low quality of surface. Along with the science and technology unceasing development and production to improve the level of social life and human needs, puts forward a series of casting, new and higher requirements for casting is playing an increasingly important role. Investment casting is in search of the wax models with multilayer fire-proof material, after drying, heat to hardening modulus, wax melting to be obtained with wax mould cavity shape corresponding the shell, after roasting, pouring and a method of castings.The process features: use the fusible mode, no parting surface, Paint, coating slurry system of fusible shell mould good copy, Hot filling liquid metal shell casting. Therefore, the investment casting production size can be accurately, surface roughness low complexity, applies both to mass production, also suitable for small batch production, even single production. Its product precision, complex, close to the final shape, parts processing or rarely processing can be used directly, called the net-shape forming an advanced technology.Keywords: box part, Investment casting, Process目录1 绪论 (5)1.1熔模铸造的概述 (5)1.1.1 熔模铸造的历史 (5)1.1.2 熔模铸造的基本原理和特点 (6)1.1.3 熔模铸造工艺过程 (7)1.1.4 我国熔模铸造发展概况 (8)1.1.5 国外熔模铸造发展概况 (8)1.2箱体零件概述 (9)1.3选题的目的和意义 (10)2 熔模铸造壳型材料对熔融合金化学稳定性研究 (12)3 箱体零件的工艺流程设计 (14)3.1模具的设计与制造 (14)3.1.1 模具的设计 (14)3.1.2 模具的制造 (15)3.2压蜡 (18)3.2.1 压蜡 (18)3.2.2 修蜡 (19)3.2.3 组树 (19)3.3制壳 (20)3.3.1硅溶胶涂料 (21)3.3.2 模组清洗 (21)3.3.3 制壳 (21)3.4浇注 (22)3.4.1 脱蜡 (22)3.4.2 焙烧 (22)3.4.3 熔炼和化性分析 (23)3.4.4 熔模铸件浇注 (23)3.4.5 熔模铸件的清理 (24)3.5后处理 (24)3.5.1 抛丸 (24)3.5.2 喷砂 (24)3.5.3 酸洗 (25)3.5.4 修正(机加工) (26)3.5.5 热处理 (26)3.5.6 抛光 (27)3.6检验 (28)3.7入库 (28)4 结论 (29)参考文献 (30)致谢 (31)1 绪论1.1 熔模铸造的概述1.1.1 熔模铸造的历史熔模铸造的历史可以追溯到4000年前,最早发现的国家有埃及、中国和印度,然后才传到非洲和欧洲的其它国家。
- 1、下载文档前请自行甄别文档内容的完整性,平台不提供额外的编辑、内容补充、找答案等附加服务。
- 2、"仅部分预览"的文档,不可在线预览部分如存在完整性等问题,可反馈申请退款(可完整预览的文档不适用该条件!)。
- 3、如文档侵犯您的权益,请联系客服反馈,我们会尽快为您处理(人工客服工作时间:9:00-18:30)。
毕业论文毕业设计论文设计(论文)题目:熔模铸造下达日期:开始日期:完成日期:指导教师:学生专业:班级:学生姓名:教研室主任:材料工程系陕西工业职业技术学院毕业设计(论文)任务书一、设计(论文)内容及要求:(一)设计(论文)内容1. 撰写熔模技术发展现状的研究文章;2. 编制铸件(附零件图)铸造工艺规程,绘制铸造工艺图,填写铸造工艺过程卡片;3. 绘制铸件图和总装图;4. 设计熔模压型模具,绘制模具零件图;5. 撰写设计说明书(论文)。
(二)要求1.通过理论学习,熟悉熔模工艺过程,结合生产实际完成本次设计任务;2. 工程图用AutoCAD软件绘制并打印;3. 说明书(论文)按照学院统一格式,使用word文档并打印。
4. 提交资料包括:(1)毕业设计任务书;(2)熔模铸造技术发展现状的研究文章;(3)“四图一卡”,即绘制铸造工艺图;铸件图;零件图;铸型装配图;铸造工艺卡;(4)设计说明书(论文);所有提交的资料包括打印文件和电子文件。
二、技术指标:1.生产类型:大批大量生产2.生产及质量要求:满足产品图纸的各项技术要求;工艺出品率较高,废品率5%以下;生产效率高;对工人技术水平要求较低,操作简便。
3.生产工艺要求:熔模铸造;所用熔模模具自行设计;4.技术水平要求:尽量采用先进技术,创新项目应符合国家环保及安全生产要求。
陕西工业职业技术学院毕业设计(论文)任务书进程计划表摘要本设计是通过熔模铸造的方法来铸造管接头,先分析铸件,进行工艺设计,确定了主要参数,进行压型设计,绘制出铸件工艺图,进行熔模制造-型壳制造-脱蜡焙烧-熔炼浇注-后处理分析,结合具体零件,通过具体分析,最后有针对性的制定出材料为锡青铜的管接头熔模铸造工艺方案。
根据现实生产的应用,表明:熔模铸造适用于实际生产中管接头的铸造。
关键词:熔模铸造,锡青铜,工艺流程ABSTRACTThis design is through investment casting methods to cast pipe joints, first analysis of castings, for process design, to determine the main parameters for pressure-type design, the casting process to map out plans to carry out melt-mold making - Shell Manufacturing - Dewaxing roasting - Melting Pouring - post-processing analysis of specific parts, through a specific analysis, and finally to develop targeted materials bronze fittings of Investment Casting Process.Applications based on the realities of production, indicating that: the application of investment casting in the actual production of the control valve body casting.Key word:Melt mold casting, gun metal, technical process目录毕业设计任务书中文摘要英文摘要一、概述 (1)1、定义 (1)2、熔模铸造的特点 (1)3、发展历史 (2)4、应用范围 (2)二、熔模工艺设计 (4)1、零件图 (4)2、铸件结构工艺性分析 (4)3、确定工艺方案和工艺参数 (5)4、浇注系统 (7)5、绘制铸造工艺图 (10)三、压型设计 (11)1、装配图 (11)2、压型分类 (11)3、分型面选择 (12)4、型体设计 (13)5、压型排气 (16)6、压型冷却 (17)7、压型工作图设计 (17)8、注蜡孔的设计 (19)四、熔模的制造 (20)1、熔模 (20)2、模料的选取和配制 (20)3、制熔模 (21)4、制模组 (23)五、型壳的制造 (26)1、型壳服役性能的要求 (26)2、制造型壳的耐火材料及黏结剂 (26)3、制造型壳用涂料及配制 (27)4、制壳工艺 (31)六、脱蜡与焙烧 (34)1、脱蜡 (34)2、焙烧 (35)七、熔炼与浇注 (36)1、材料的选择 (36)2、选择炉型 (37)3、熔炼准备 (38)4、配料 (40)5、熔炼工艺 (42)八、铸件的后处理 (44)1、型壳的清理 (44)2、切割浇冒口 (46)参考文献 (47)致谢 (48)一、概述1、定义熔模铸造又称“失蜡铸造”,通常是在可熔模样的表面涂上数层耐火材料,待其硬化干燥后,加热将其中模样熔去,而获得具有与模样形状相应空腔的型壳,再经过焙烧,然后在型壳温度很高的情况下进行浇注,而获得铸件的一种方法,由于获得的铸件具有较高的尺寸精度和表面光洁度,故又称“熔模精密铸造”。
2、熔模铸造的特点1)铸件尺寸精确,一般可达CT4~7,有时尺寸公差可小于±0.005cm/cm,故可使铸件达到少切削,甚至无余量的要求。
2)可铸造形状复杂的铸件。
铸件壁厚最小可达0.5mm,铸出最小孔径为0.5mm。
在生产中可将一些原来由几个零件组合而成的部件,通过改变零件的结构,设计成为整体零件而直接由熔模铸造铸出,以节省加工工时和金属材料的消耗,使零件结构更为合理。
3)不受铸件材料的限制。
可用熔模铸造法生产的合金种类有碳素钢、合金钢、耐热合金、不锈钢、精密合金、永磁合金、轴承合金、铜合金、铝合金、钛合金和球墨铸铁等。
4)铸件尺寸不能太大,重量也有限制。
5)工艺过程复杂,工序繁多,使生产过程控制难度大增。
6)铸件冷却速度慢,铸件晶粒粗大。
压制熔模时,采用型腔表面光洁度高的压型,因此,熔模的表面光洁度也比较高。
此外,型壳由耐高温的特殊粘结剂和耐火材料配制成的耐火涂料涂挂在熔模上而制成,与熔融金属直接接触的型腔内表面光洁度高。
所以,熔模铸件的表面光洁度比一般铸造件的高,一般可达Ra.1.6~3.2μm。
熔模铸造最大的优点就是由于熔模铸件有着很高的尺寸精度和表面光洁度,所以可减少机械加工工作,只是在零件上要求较高的部位留少许加工余量即可,甚至某些铸件只留打磨、抛光余量,不必机械加工即可使用。
由此可见,采用熔模铸造方法可大量节省机床设备和加工工时,大幅度节约金属原材料。
3、发展历史熔模铸造又称失腊法。
失腊法是用腊制作所要铸成器物的模子,然后在腊模上涂以泥浆,这就是泥模。
泥模晾干后,在焙烧成陶模。
一经焙烧,腊模全部熔化流失,只剩陶模。
一般制泥模时就留下了浇注口,再从浇注口灌入铜液,冷却后,所需的器物就制成了。
我国的失腊法至迟起源于春秋时期。
河南淅川下寺2号楚墓出土的春秋时代的铜禁是迄今所知的最早的失腊法铸件。
此铜禁四边及侧面均饰透雕云纹,四周有十二个立雕伏兽,体下共有十个立雕状的兽足。
透雕纹饰繁复多变,外形华丽而庄重,反映出春秋中期我国的失腊法已经比较成熟。
战国、秦汉以后,失腊法更为流行,尤其是隋唐至明、清期间,铸造青铜器采用的多是失腊法。
失腊法一般用于制作小型铸件。
用这种方法铸出的铜器既无范痕,又无垫片的痕迹,用它铸造镂空的器物更佳。
中国传统的熔模铸造技术对世界的冶金发展有很大的影响。
现代工业的熔模精密铸造,就是从传统的失腊法发展而来的。
虽然无论在所用腊料、制模、造型材料、工艺方法等方面,它们都有很大的不同,但是它们的工艺原理是一致的。
四十年代中期,美国工程师奥斯汀创立以他命名的现代熔模精密铸造技术时,曾从中国传统失蜡法得到启示。
1955年奥斯汀实验室提出首创失蜡法的呈请,日本学者鹿取一男根据中国和日本历史上使用失蜡法的事实表示异议,最后取得了胜诉。
熔模铸造适用于形状复杂、难以用其他方法加工的成形的精密铸件的生产,如航空发动机的叶片、叶轮,复杂的薄壁框架,雷达天线,带有很多散热薄片、柱、销轴的框架,齿套等。
用这种方法铸出的铜器既无范痕,又无垫片的痕迹,用它铸造镂空的器物更佳。
中国传统的熔模铸造技术对世界的冶金发展有很大的影响。
4、应用范围熔模铸造适用于形状复杂、难以用其他方法加工的成形的精密铸件的生产,如航空发动机的叶片、叶轮,复杂的薄壁框架,雷达天线,带有很多散热薄片、柱、销轴的框架,齿套等。
用这种方法铸出的铜器既无范痕,又无垫片的痕迹,用它铸造镂空的器物更佳。
中国传统的熔模铸造技术对世界的冶金发展有很大的影响。
现代熔模铸造技术是在金属义齿铸造基础上,于20世纪40年代的第二次世界大战期间发展起来的。
随着现代工业的发展,熔模铸造技术也在不断的获得提高和更新,并扩大它的应用范围。
除了航空制造业和兵器工业以外,在机械制造、电子、石油、化工、核能、交通运输、纺织、医疗器械、泵、阀等制造工业中,都得到了广泛的应用。
在艺术铸造业中,熔模铸造也是传布的很广的。
二、熔模工艺设计1、零件图图2-1为管接头零件图,材料为锡青铜,牌号ZCuSn6Zn6Pb3,锡青铜具有较高的耐磨性、耐蚀性及良好的切削性,广泛的使用于阀体管件的制造。
图2-1 零件图2、铸件结构工艺性分析熔模铸件的结构工艺性是指,从熔模铸造生产工艺角度出发,对零件结构提出的要求。
也就是在满足工作要求的前提下,希望零件结构能兼顾到熔模铸造的工艺特点,使之尽量与熔模铸造的工艺要求相吻合。
铸件结构是否合理,对铸件质量、生产工艺的可行性和简易性以及生产成本等影响很大。
熔模铸件的结构应当符合熔模铸造的生产特点。
⑴铸件壁厚由于熔模铸造的型壳内表面光洁,并且一般为热型壳浇注,因此熔模铸件壁厚允许设计得较薄。
表2-2铜合金的熔模铸件的最小壁厚推荐值和可能铸出的最小值。
对于局部尖锐部位,可以铸出更薄的壁厚(可比表中最小值小30%—50%的壁厚)表2-2熔模铸件的最小壁厚(单位mm)本次设计为一管接头,见图2-1。
由上表得铜合金熔模铸造最小壁厚为 2.5mm。
根据此结论和实际要求得出最佳壁厚为10mm。
⑵铸件结构整个铸件中,没有工艺肋结构,有孔槽结构。
熔模铸件一端面为方台因为有配合要求,要求加工粗糙度为0.8,两端均有凹台,采用机械加工成形,铸件两端的法兰盘和方台上各分部有4个直径为ø10的通孔,其配合要求为H7/f7,所有的通孔都是直接铸造出来的。
铸件材料为ZCuSn6Zn6Pb3,收缩率为1.03%。
该铸件全部尺寸均为标注公差。
按图中要求,熔模铸件铜合金公差为IT4~6级。
3、确定工艺方案和工艺参数⑴铸孔熔模铸件上细而长的孔,由于制壳时的内部不易上涂料和撒砂,所以一般孔径d<2.5~3.0 mm、孔高与孔径比h/d>5的通孔和h/d>2.5~3.0的不通孔不予铸出。