精益生产之快速切换案例
精益生产与实际应用案例
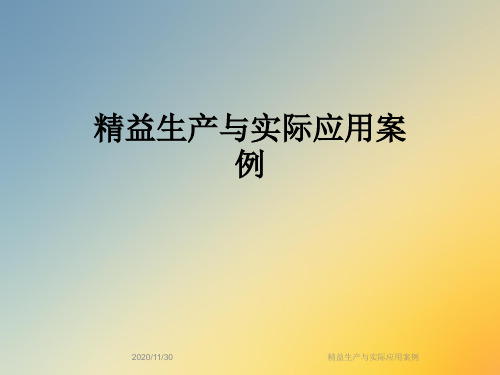
第二天内容 上午: 9:00---10:30 设备布局和标准作业 10:45—12:00 全员设备维护 下午: 1:00---2:00价值流 2:10---3:10 企业的改善案例 3:20---4:30 合理化改善提案活动的开展
精益生产与实际应用案例
第一模块: TPS对于成本的认识和诞生背景
精益生产与实际应用案 例
2020/11/30
精益生产与实际应用案例
精益生产与实际案例
讲师:巩怿(windy)
2008年8月
精益生产与实际应用案例
第一天内容 上午: 9:00---10:30 精益生产的诞生背景和基本理念 10:45—12:00 7大浪费和解决问题的方法、 下午: 1:00-2:00 精益生产的2大支柱 2:10—3:10 5S和目视化管理 3:20—4:30 设备的快速换产
销售额(亿美元) 1855 1290 1642
纯利润(亿美元) 38
101
5
戴—克 430 1600 6
大众 502 1050 13
精益生产与实际应用案例
Ⅰ.支持丰田生产方式経営的见解・想法
1. 企业目的
继续谋求与国际社会的調和、 (丰田将通过车辆供給实现)
完成社会的使命
・ 用文化来充实生活
・通过会社使地域活性化
丰田汽车经历了13年努力,到1952年共生产了2685辆 汽车,而福特的鲁奇厂一天就生产7000辆汽车。
▪ 日本国土很小,需求复杂,包括官员的豪华轿车,运货
的载重汽车,必以及须农使村用用的非小常型规客货的两方用法车。 ▪ 日本劳动力不愿意被作才为能可生变成存本!被不断变换。
▪ 经历了战争摧残的日本没有大量外汇去购买国外的新技术。 ▪ 世界大型汽车制造公司严格限制日本向他们的经济领域
精益生产-SMED(快速换模)
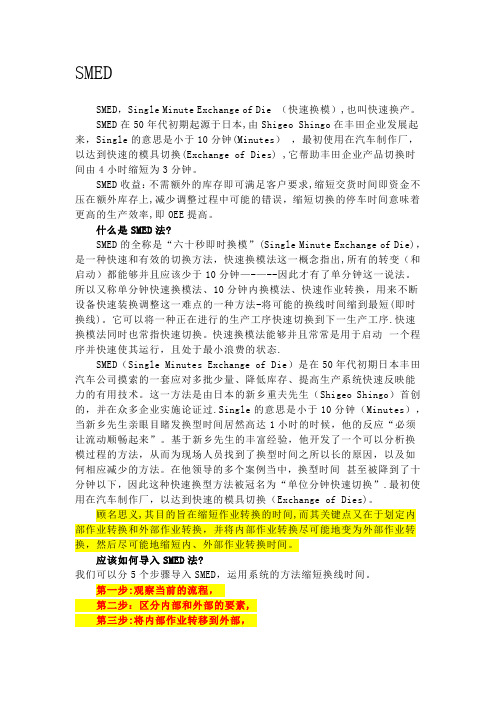
SMEDSMED,Single Minute Exchange of Die (快速换模),也叫快速换产。
SMED在50年代初期起源于日本,由Shigeo Shingo在丰田企业发展起来,Single的意思是小于10分钟(Minutes),最初使用在汽车制作厂,以达到快速的模具切换(Exchange of Dies) ,它帮助丰田企业产品切换时间由4小时缩短为3分钟。
SMED收益:不需额外的库存即可满足客户要求,缩短交货时间即资金不压在额外库存上,减少调整过程中可能的错误,缩短切换的停车时间意味着更高的生产效率,即OEE提高。
什么是SMED法?SMED的全称是“六十秒即时换模”(Single Minute Exchange of Die),是一种快速和有效的切换方法,快速换模法这一概念指出,所有的转变(和启动)都能够并且应该少于10分钟—-—--因此才有了单分钟这一说法。
所以又称单分钟快速换模法、10分钟内换模法、快速作业转换,用来不断设备快速装换调整这一难点的一种方法-将可能的换线时间缩到最短(即时换线)。
它可以将一种正在进行的生产工序快速切换到下一生产工序.快速换模法同时也常指快速切换。
快速换模法能够并且常常是用于启动一个程序并快速使其运行,且处于最小浪费的状态.SMED(Single Minutes Exchange of Die)是在50年代初期日本丰田汽车公司摸索的一套应对多批少量、降低库存、提高生产系统快速反映能力的有用技术。
这一方法是由日本的新乡重夫先生(Shigeo Shingo)首创的,并在众多企业实施论证过.Single的意思是小于10分钟(Minutes),当新乡先生亲眼目睹发换型时间居然高达1小时的时候,他的反应“必须让流动顺畅起来”。
基于新乡先生的丰富经验,他开发了一个可以分析换模过程的方法,从而为现场人员找到了换型时间之所以长的原因,以及如何相应减少的方法。
在他领导的多个案例当中,换型时间甚至被降到了十分钟以下,因此这种快速换型方法被冠名为“单位分钟快速切换”.最初使用在汽车制作厂,以达到快速的模具切换(Exchange of Dies)。
精益生产经典案例

精益生产改善案例生产管理追求无库存,就是要彻底改变以超量库存保发货的传统做法,变以造型为中心的推动式生产为以清理为起点的拉动式生产。
实行期量流或一个流生产方式,逐步扩大看板生产品种,造型生产线实行柔性生产,生产作业计划和生产统计应用计算机管理,大幅度地压缩工序、在制品和成品库存,最大限度地降低资金占用,提高生产组织管理水平。
质量管理追求无缺陷,就是要不断提高质量管理和产品质量水平。
质量管理要从“全面质量管理”转向“零缺点管理”,进一步减少不良损失,用精益思想研究和实施质量改进和攻关,提高产品的工艺水平。
落实质量责任制,严格厂内质量评审,严肃工艺纪律,使每个环节、每道工序、每名职工都切实做到精心操作,严格把关,确保产品内在质量和表面质量达到优质品标准。
设备管理追求无停台,就是要提高设备的可动率和开动率,提高工装的工艺水平和使用寿命。
要坚持以生产现场为中心,抓好现场巡检,现场维修,实行设备封闭管理。
工装采取快速换模方法,满足小批量多品种生产的需求。
要通过采用一系列有效措施,不断提高设备工装的技术状态,为保证生产顺利进行和生产优质产品提供可靠的必要条件。
成本管理追求无浪费,就是要狠抓投入产出管理,做到少投入,多产出,优质低耗,降低成本。
深入开展三级经济核算,抓好产品收到率、原材料投入、成品产出率、清理合格率等环节的考核。
要整顿库房,对原材料、产成品、备品、备件等重新制定最高最低储备限额,做到用最低的储备满足生产的需要,大幅度地降低消耗,减少浪费,活化资金,降低产品成本。
优化生产,就是全厂每个生产环节都要达到整体优化标准,建立起以车间主任为首,以生产工人为主体,以生产现场为中心的现场“三为”管理机制。
实施生产要素一体化管理,强化现场“5S”管理和定置管理,现场工位器具标准化、改善生产现场环境,提高现场文明生产水平,使生产要素达到最佳状态。
优质服务,就是要强化科室为一线,后方为前方服务。
职能科室要切实转变工作作风,提高工作质量、服务质量和工作效率,充分发挥指导服务的职能。
精益生产推行之快速切换
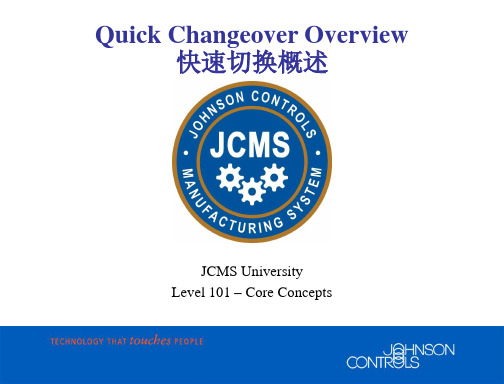
Quick Changeover is a structured process that: 快速改革是个结构过程用来
Reduces waste 减少浪费 Shortens lead times 减少时间 Improves manufacturing capacity, flexibility, and quality 提高生产能力,灵活性和质量.
Cleanup Waste Transportation Motion
Changeover Time =
Internal Changeover Time + External Changeover Time
11
QCO WSP - 6/25/03
CO
QUICK CHANGEOVER OVERVIEW
QCO WSP - 6/25/03
10
CO
QUICK CHANGEOVER OVERVIEW
Waste In Changeover Operations 在改革运作中的浪费
Waste in Changeover Operations
Waste in Internal Changeover
The goal is to reduce the time from “last good piece” to “first good piece,” down to customer takt time. 目标把从“最后一个好的零件”到 “第一个好的零件”的时间减少至客户的takt 时间
QCO WSP - 6/25/03 3
3
Implement Jigs
Internal Setup (Process is Down)
精益生产之快速换模SMED案例(分享)
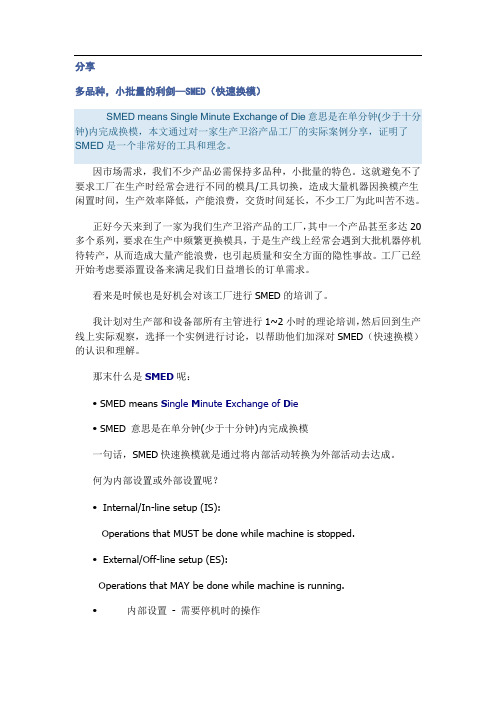
分享多品种,小批量的利剑—SMED(快速换模)SMED means Single Minute Exchange of Die意思是在单分钟(少于十分钟)内完成换模,本文通过对一家生产卫浴产品工厂的实际案例分享,证明了SMED是一个非常好的工具和理念。
因市场需求,我们不少产品必需保持多品种,小批量的特色。
这就避免不了要求工厂在生产时经常会进行不同的模具/工具切换,造成大量机器因换模产生闲置时间,生产效率降低,产能浪费,交货时间延长,不少工厂为此叫苦不迭。
正好今天来到了一家为我们生产卫浴产品的工厂,其中一个产品甚至多达20多个系列,要求在生产中频繁更换模具,于是生产线上经常会遇到大批机器停机待转产,从而造成大量产能浪费,也引起质量和安全方面的隐性事故。
工厂已经开始考虑要添置设备来满足我们日益增长的订单需求。
看来是时候也是好机会对该工厂进行SMED的培训了。
我计划对生产部和设备部所有主管进行1~2小时的理论培训,然后回到生产线上实际观察,选择一个实例进行讨论,以帮助他们加深对SMED(快速换模)的认识和理解。
那末什么是SMED呢:• SMED means S ingle M inute E xchange of D ie• SMED 意思是在单分钟(少于十分钟)内完成换模一句话,SMED快速换模就是通过将内部活动转换为外部活动去达成。
何为内部设置或外部设置呢?• Internal/In-line setup (IS):Operations that MUST be done while machine is stopped.• External/Off-line setup (ES):Operations that MAY be done while machine is running.•内部设置- 需要停机时的操作•例如/ Example: ---从冲压机里取出模,机器必须停止•外部设置–指那些机器运行时的操作有的也把它叫做在线和离线活动(In-Line Activities and Off-Line Activities),看你怎么翻译了,实质都一样。
精益生产-快速换型
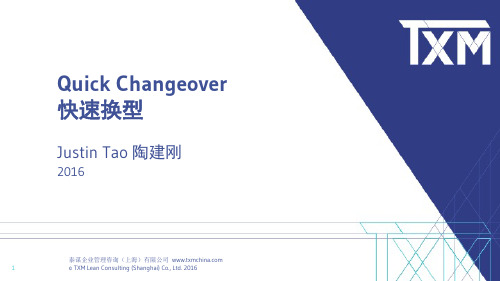
Quick Changeover 快速换型Justin Tao 陶建刚2016Produce Large Lot Size? 大批量生产?• It is a reality still used by many companies to produce, and the main objective is to smooth the setup time.事实上很多企业使用大批量生产方式进行生产,并且主要目标是使换型时间更加平稳• This is the key of the “Mass Production”, it means:这点是“大规模生产”意思的关键所在:– “Produce a large amount of a only product”“生产大批量的单一产品”Heijunka Process 均衡化进程Too early 过早,inventory 库存Too late 过晚,out of stock 缺货ChangeoverConsequence of Long Setup Time 长换型时间导致的结果All these factors increase the wastes in the workshop!!!所有这些因素都在车间中增加了浪费!!!Long Setup Time 长的换型时间Long Production Cycle time 长的生产周期 Large amount of WIP 大量的在制品Equipment to transport and to storage需要设备搬运和存储 Increase manpower need 增加所需人员Require space in the shop floor and area to storage 需要空间存储Definition of Setup Time and Its Structure换型时间的定义和构成:Setup time: The last qualified product in production run and the first qualified product in thenext production run换型时间:指介于一个生产作业的最后一件合格品和下一个生产作业的首件合格品之间的时间 Definition of setup in lean manufacturing: The last qualified product of one type to the firstqualified product of next type精益生产的换型定义:为从前一品种最后一个合格产品,到下一品种第一个合格产品之间的时间间隔。
精益生产经典案例

精益生产改善案例生产管理追求无库存,就是要彻底改变以超量库存保发货的传统做法,变以造型为中心的推动式生产为以清理为起点的拉动式生产。
实行期量流或一个流生产方式,逐步扩大看板生产品种,造型生产线实行柔性生产,生产作业计划和生产统计应用计算机管理,大幅度地压缩工序、在制品和成品库存,最大限度地降低资金占用,提高生产组织管理水平。
质量管理追求无缺陷,就是要不断提高质量管理和产品质量水平。
质量管理要从“全面质量管理”转向“零缺点管理”,进一步减少不良损失,用精益思想研究和实施质量改进和攻关,提高产品的工艺水平。
落实质量责任制,严格厂内质量评审,严肃工艺纪律,使每个环节、每道工序、每名职工都切实做到精心操作,严格把关,确保产品内在质量和表面质量达到优质品标准。
设备管理追求无停台,就是要提高设备的可动率和开动率,提高工装的工艺水平和使用寿命。
要坚持以生产现场为中心,抓好现场巡检,现场维修,实行设备封闭管理。
工装采取快速换模方法,满足小批量多品种生产的需求。
要通过采用一系列有效措施,不断提高设备工装的技术状态,为保证生产顺利进行和生产优质产品提供可靠的必要条件。
成本管理追求无浪费,就是要狠抓投入产出管理,做到少投入,多产出,优质低耗,降低成本。
深入开展三级经济核算,抓好产品收到率、原材料投入、成品产出率、清理合格率等环节的考核。
要整顿库房,对原材料、产成品、备品、备件等重新制定最高最低储备限额,做到用最低的储备满足生产的需要,大幅度地降低消耗,减少浪费,活化资金,降低产品成本。
优化生产,就是全厂每个生产环节都要达到整体优化标准,建立起以车间主任为首,以生产工人为主体,以生产现场为中心的现场“三为”管理机制。
实施生产要素一体化管理,强化现场“5S”管理和定置管理,现场工位器具标准化、改善生产现场环境,提高现场文明生产水平,使生产要素达到最佳状态。
优质服务,就是要强化科室为一线,后方为前方服务。
职能科室要切实转变工作作风,提高工作质量、服务质量和工作效率,充分发挥指导服务的职能。
精益生产之缩短作业转换时间 SMED
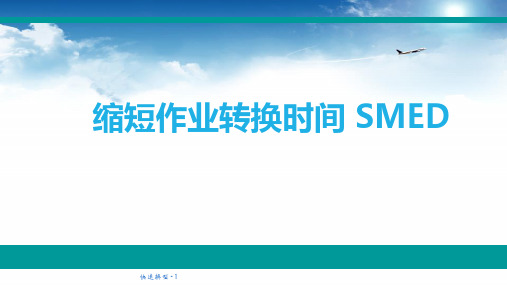
快速换型 - 1
外国两小时到一天,丰田一分钟以内!
1970年,丰田公司成功地把重达800吨的机罩用冲压机的作业转换时间 缩短到了三分钟。在丰田公司把这称为单一作业转换。“单一”(Single) 的意思是:作业转换时间,以分钟计仅为一位数,也就是9分59秒以内。 现在,在许多时候已将其缩短到了一分钟以内。这就是“快餐式”作业 转换。在欧美的公司,这种作业转换时间需要两小时到几小时的情况不 在少数。最长的甚至需要整整一天时间。
快速换型 - 2
即使设备的运转率低,也要优先保证库存最小
因为生产过剩会导致浪费,这被认为是比设备运转率低更糟糕的事情。 实现最小库存,面向订货生产的制造方式,对需求变化迅速的适应性, 都是“单一作业转换”最突出的优点。
快速换型 - 3
单一作业转换
“单一作业转换”是日本人在工业工程(IE)领域中发明的革新性概念之一。这一思路,是丰 田公司的顾问新乡重夫开发的,它给现在世界IE领域的理论与实践带来了思路上的转变。 “单一作业转换”,不应该认为是单纯的技术。这也是一个认为有必要转变一个工厂全体员工 态度的概念。在日本的公司,不仅通过IE工作人员,而且还通过被称为QC小组和ZD(零缺欠) 小组的现场员工的小集团活动来推进“缩短作业转换时间”。
快速换型 - 6
转换作业改善步骤
第一步:明确区分内部作业转换和外部作业转换 第二步:将内部作业转换B转化为外部作业转换 第三步:缩短内部作业转换C 第四步:缩短调整作业D 第五步:缩短外部作业转换A
总转换时间
外部作业转换 内部作业转换 调整作业
A
B
C
D
快速换型 - 7
作业转换改善体系 转换分析
内部 作业 转换
精益生产之快速切换案例
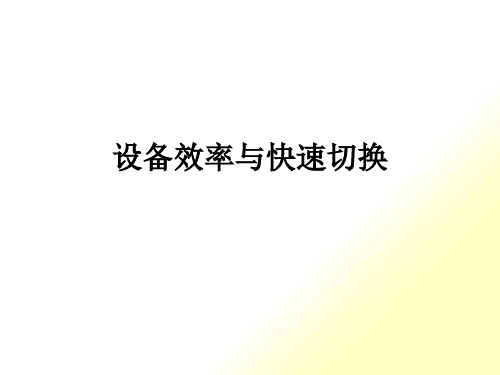
性能稼动=4率2.6=%有效稼动时间/稼动时间 〔200/400〕 设备的=生生产产率量=×设基备准综周合期效/〔率负×荷设时备间可-动停率止时间
现在1个月达成!!
在设计开发中进行品质预测
0.10
● NAD
0.08 ●
0.06
●
0.04
0.02 0.00
□
▲
□ ▲
准备阶段进1行品2
质预测
□ K/F
▲G
●
□▲
● □▲
● □▲
● □▲
3456
● □ ▲
7 量产时间
演讲完毕,谢谢观看!
生产制造过程中的快速转换技术
品种切换〔转换〕时间
SMED法有4个基本要求:
1〕 .严格区分“内部操作〞和“外部操作〞 ; 2〕 .将“内部操作〞转化为“外部换操作〞; 3〕 .缩短内部操作时间 . 4〕.彻底的5S管理
品质预测
异常表现
问题发生
预知 a
异常表现
感b知
c 爆发点
t时间
在C点前排除问题称预测
◇ 以“多品种、小批量〞为特征的均衡化生产是看板 管理和准时化生产方式的重要措施,而实现均衡化 生产,最关键的问题就是设备的快速装换调整问题.
◇ 缩短设备的装换与调整时间是减少瓶颈、降低成本、 改进产品质量和实现准时化生产方式的关键。
产品快速切换常用方法
精益生产成功案例

精益生产成功案例第一篇:精益生产成功案例精益生产网站案例1一家专业生产汽车刹车盘(鼓)美资公司,在中国设有2 家工厂,产品几乎覆盖了美国、欧洲、日本和韩国的所有车型。
同时水泵的可提供型号达到了500 种,主要是满足上面这几个国家主流车型的需要。
同时,借助市场调研和与一些客户的紧密合作,该公司装配线产品追溯性标示过程复杂,造成冗杂处理的浪费;手工打标记等不仅劳动强度大,而且容易造成疲劳错误。
铸造车间产品种类和生产区域无标示,将导致分检的时间损失及混淆。
-铸造现场、热处理车间5S 尚有较大改进空间,尤其是整顿、清洁和进一步的标准化工作。
、其他影响:同时,制造方式的变革也暴露出在原来的成批生产方式中隐藏至深的大量问题,如设备故障多发,维修速度慢以及缺乏保养;设备换模具时间长;刀具整备时间长;作业员技能单一等。
改善效果:经过三个月的维持与改善,同时辅以培训 , 一些主要问题得到明显的改善:·在不影响现有产出情况下,较大幅度降低成品库存总量。
总库存量减少了 4 0 %。
·按照用户的需求节拍,进行小批量多频次的生产和物料周转(目标:单件流),缩短生产周期。
生产提前期从 15 天缩短到 5 天。
·应用快速换模的项目方法(四步法)和技术手段,缩短生产线的换型时间。
·运用 IE 工程和看板管理,辅以必要的柔性生产布局设计及多技能员工培训,改善现有的工艺及流程,消除瓶颈限制,在制品减少 66 %,实现流畅化制造。
·全面生产性维护(TPM):对设备效能作了详细测定 , 并根据以往开机时间的历史纪录,分析总体生产效率(OEE),改进设备维护计划,提高运行效率, 在没有增加设备的前提下,月产量提高了30%,不良率由 8% 降到了 4%,OEE 从原来的 60% 提高到 85 %。
·现场的物流及 5S 改善,减少搬运、寻找、等待等浪费活动。
精益生产网站案例2一家美商独资生产硅胶和塑料按键产品的企业,产品广泛应用于手机、家用电器、工业电子设备等产品上。
精益生产改善方案案例分析

销售
9、要学生做的事,教职员躬亲共做; 要学生 学的知 识,教 职员躬 亲共学 ;要学 生守的 规则, 教职员 躬亲共 守。21 .6.1321 .6.13Su nday , June 13, 2021
10、阅读一切好书如同和过去最杰出 的人谈 话。08:04:0808 :04:080 8:046/1 3/2021 8:04:08 AM
4、产品工序分析法 产品工序分析法的目的和目标 5、作业人员工序分析法
作业人员工序分析法的定义
5.2作业人员工序分析法的目的
1、是否有不必要的停滯 2、搬运的次数是否太多 3、搬运的距離是否太长 4、搬运的方法是否有问題 5、是否能同時实施加工及检查
工程分析案例:
1、优化生产线 自主改造装配线,实现HFC1020前桥混线装配
一个流生产:
自主设计制作本体流水装配线,在人员没有改变的前 提下,生产能力从加班日产200台提升到8小时产250 台;而且改变了长期以来落后的摆地摊装配方式。
推进精益生产:
1、现场是基础;
2、改善是手段。
库房的仓位
形迹管理
如图:通过不懈努力,所有工序的刀、辅、量具有 了“新家”,让它们也实现了定置
IE是英语industrial engineering 的缩写,即工业管理。
2、动作及动作分析法
定义:由人的身体各部位的运动所组成的行动、行为称之为 “动作”。
3、动作改善的目标和顺序
4、基本动作分析法与作业改善
4.1基本动作分析法的分析 方法
经过归纳将基本动作分 为以下三类:
Ⅰ第1类:作业进行时必 要的动作;
CT 设定
精益改善 生产 项目管理 规格
MRP
ERP 系统 设计 管理
精益生产经典案例

精益生产改善案例生产管理追求无库存,就是要彻底改变以超量库存保发货的传统做法,变以造型为中心的推动式生产为以清理为起点的拉动式生产。
实行期量流或一个流生产方式,逐步扩大看板生产品种,造型生产线实行柔性生产,生产作业计划和生产统计应用计算机管理,大幅度地压缩工序、在制品和成品库存,最大限度地降低资金占用,提高生产组织管理水平。
质量管理追求无缺陷,就是要不断提高质量管理和产品质量水平。
质量管理要从“全面质量管理”转向“零缺点管理”,进一步减少不良损失,用精益思想研究和实施质量改进和攻关,提高产品的工艺水平。
落实质量责任制,严格厂内质量评审,严肃工艺纪律,使每个环节、每道工序、每名职工都切实做到精心操作,严格把关,确保产品内在质量和表面质量达到优质品标准。
设备管理追求无停台,就是要提高设备的可动率和开动率,提高工装的工艺水平和使用寿命。
要坚持以生产现场为中心,抓好现场巡检,现场维修,实行设备封闭管理。
工装采取快速换模方法,满足小批量多品种生产的需求。
要通过采用一系列有效措施,不断提高设备工装的技术状态,为保证生产顺利进行和生产优质产品提供可靠的必要条件。
成本管理追求无浪费,就是要狠抓投入产出管理,做到少投入,多产出,优质低耗,降低成本。
深入开展三级经济核算,抓好产品收到率、原材料投入、成品产出率、清理合格率等环节的考核。
要整顿库房,对原材料、产成品、备品、备件等重新制定最高最低储备限额,做到用最低的储备满足生产的需要,大幅度地降低消耗,减少浪费,活化资金,降低产品成本。
优化生产,就是全厂每个生产环节都要达到整体优化标准,建立起以车间主任为首,以生产工人为主体,以生产现场为中心的现场“三为”管理机制。
实施生产要素一体化管理,强化现场“5S”管理和定置管理,现场工位器具标准化、改善生产现场环境,提高现场文明生产水平,使生产要素达到最佳状态。
优质服务,就是要强化科室为一线,后方为前方服务。
职能科室要切实转变工作作风,提高工作质量、服务质量和工作效率,充分发挥指导服务的职能。
精益生产之快速换线(精益)
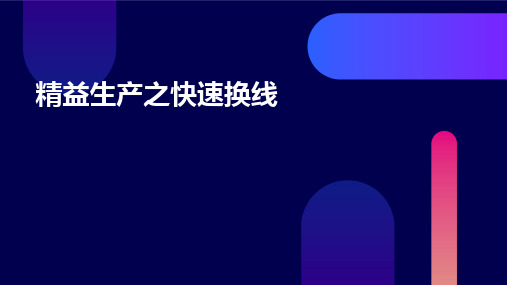
目 录
• 引言 • 快速换线的核心原则 • 快速换线的实施步骤 • 快速换线的挑战与解决方案 • 快速换线的成功案例 • 结论
01
引言
目的和背景
01
制造业的竞争日益激烈,快速响 应市场需求和降低生产成本成为 企业生存的关键。
02
传统的大批量生产模式难以满足 多样化、小批量生产的需求,精 益生产应运而生。
产品。
通过均衡化生产,企业可以避免 生产波动和浪费,提高生产效率
和设备利用率。
均衡化生产还可以帮助企业更好 地预测和计划生产,降低库存和
缺货风险。
单件流
01
单件流是指生产线上每个工序只生产一个或少数几个产品,并 保持连续流动的生产方式。
02
单件流可以减少在制品数量,降低库存成本,提高生产效率和
灵活性。
详细描述
设备故障可能是由于设备老化、维护不当或使用频率过高所致。为了解决这个问 题,企业应定期对设备进行维护和保养,确保设备处于良好状态。同时,建立设 备故障应急预案,以便在设备出现故障时能够迅速恢复生产。
员工技能不足
总结词
员工技能不足是影响快速换线效率的重要因素,它可能导致换线时间过长、操作不规范等问题。
公司C的案例
总结词
提升产品质量
详细描述
通过快速换线,公司C能够更快地适应 市场需求,提高产品质量的稳定性和 一致性,从而赢得了更多客户的信任 和订单。
06
结论
对快速换线的总结
快速换线是精益生产中的重要组成部分,通过减少换 线时间和提高生产效率,能够为企业带来显著的成本
和竞争优势。
输标02入题
快速换线需要跨部门协作和持续改进的精神,通过不 断优化流程、提高员工技能和采用先进的生产技术, 可以进一步缩短换线时间、提高生产效率。
精益生产全集_快速切换_QCO_CN
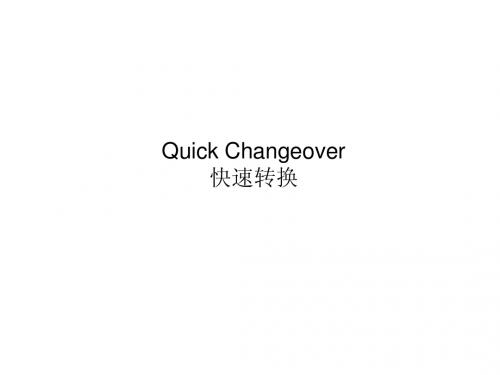
•内部时间:必须在设备停机的状态下才可执行的工作
–移开、插入工具或坏掉的传送链
•外部时间:可在设备运行同时进行的准备或清理工作
–工具和/或模具的运输 –每次运行必须做的书面工作
22
区分内外部
QCO步骤1(续)
过程:
内部转外部 运用夹具
消除调节
标准化 并行操作 机械改进
产品时间表 一个月
A B C
50 100 150
每月生产一次以上(小批量)
9
平衡生产与大批量
批量生产
生产理论 产出理论
平衡生产
市场导向理论
生产方式
大批量
周期时间
达到效率的方法
针对每个单独的工序
针对整条线提高效率 (系统焦点) 中等速度,用途单一, 体积小,价格低
关于设备
高速,广用途,体积大并且价格高
• 工具整和 – 是否每件工具都是必要的? 工具的性能是 可以合并,减少或取消?
• 专业化 – 改进手推车、工具和其他的设备以缩短转换 时间。
5S 能够在安装调试阶段实现很大的节约而又不耗费任何成本!
19
改进的关键——TPM
• TPM 可以看作为“对设备的5S” • 它提供了严格的有规律的过程,这些过程改进了 重复性并确保证设备最大的正常运行时间。 • 如果设备情况不可预测,不可能进行真正有意义 的转换时间降低。 • 通过TPM可以预测设备的运行情况,通过快速转换 实现的节约是可以持续的
使操作标准化并消除调节
• 定位 – 制定定位和夹紧定制的标准。 • 夹紧 – 每次按同样的顺序、相同的扭矩夹紧和拧紧 螺丝。 • 设置档块 – 如果必需垫片,要使用标志清楚、伸手 可及的专用间隔档块。
精益生产经典案例

精益生产改善案例生产管理追求无库存,就是要彻底改变以超量库存保发货的传统做法,变以造型为中心的推动式生产为以清理为起点的拉动式生产。
实行期量流或一个流生产方式,逐步扩大看板生产品种,造型生产线实行柔性生产,生产作业计划和生产统计应用计算机管理,大幅度地压缩工序、在制品和成品库存,最大限度地降低资金占用,提高生产组织管理水平。
质量管理追求无缺陷,就是要不断提高质量管理和产品质量水平。
质量管理要从“全面质量管理”转向“零缺点管理”,进一步减少不良损失,用精益思想研究和实施质量改进和攻关,提高产品的工艺水平。
落实质量责任制,严格厂内质量评审,严肃工艺纪律,使每个环节、每道工序、每名职工都切实做到精心操作,严格把关,确保产品内在质量和表面质量达到优质品标准。
设备管理追求无停台,就是要提高设备的可动率和开动率,提高工装的工艺水平和使用寿命。
要坚持以生产现场为中心,抓好现场巡检,现场维修,实行设备封闭管理。
工装采取快速换模方法,满足小批量多品种生产的需求。
要通过采用一系列有效措施,不断提高设备工装的技术状态,为保证生产顺利进行和生产优质产品提供可靠的必要条件。
成本管理追求无浪费,就是要狠抓投入产出管理,做到少投入,多产出,优质低耗,降低成本。
深入开展三级经济核算,抓好产品收到率、原材料投入、成品产出率、清理合格率等环节的考核。
要整顿库房,对原材料、产成品、备品、备件等重新制定最高最低储备限额,做到用最低的储备满足生产的需要,大幅度地降低消耗,减少浪费,活化资金,降低产品成本。
优化生产,就是全厂每个生产环节都要达到整体优化标准,建立起以车间主任为首,以生产工人为主体,以生产现场为中心的现场“三为”管理机制。
实施生产要素一体化管理,强化现场“5S”管理和定置管理,现场工位器具标准化、改善生产现场环境,提高现场文明生产水平,使生产要素达到最佳状态。
优质服务,就是要强化科室为一线,后方为前方服务。
职能科室要切实转变工作作风,提高工作质量、服务质量和工作效率,充分发挥指导服务的职能。
精益生产中的SMED
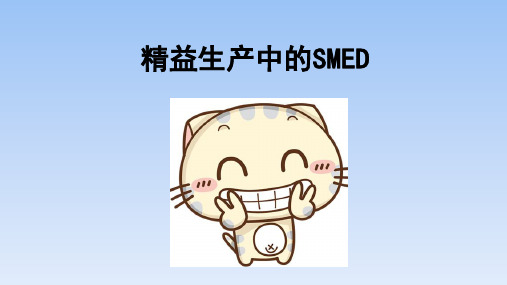
精益生产中的SMEDSMED简介1 什么是SMED2 SMED概述3 快速换模的境界SMED的全称是“六十秒即时换模”(Single Minute Exchange of Die),是一种快速和有效的切换方法。
SMED系统是一种能有效缩短产品切换时间的理论和方法。
SMED 有些企业和学者也称为 QCD (Quick Die Change)●SMED在20世纪50年代初期起源于日本;SMED(Single Minutes Exchange of Die)是在50年代初期日本丰田汽车公司摸索出的一套应对多批少量、降低库存、提高生产系统快速反映能力的有用技术。
●由Shigeo Shingo(新乡重夫)在丰田企业发展起来;●Single的意思是小于10分钟(Minute);●最初是用在汽车制造厂,以达到快速的模具切换;●它帮助丰田企业产品切换时间获得极大地缩短。
快速换模创始人:新乡重夫日本工程师,出身于佐贺县,工业工程(IE)领域世界著名的品质管理专家,著名的丰田生产体系创建人。
在品质管理方面作出重大贡献,在美国出版了不少有关品质方面的著作。
他还根据自己20年事业生涯中的系统性方法和精心笔记,著有18部书和无数管理文章。
他指出,“零损坏”就是品质要求的最高极限。
被尊称为“纠错之父”。
在众多的成就中其中有两项最被人称道:1、快速换模(SMED, Single Minute Exchange of Dies,一分钟换模法):是日本人在工业工程(IE)领域中发明的革新性概念之一。
2、丰田生产系统(Toyota Production System)的精益生产系统。
新乡重夫(Shigeo Shingo,1909年-1990年)“ ……很多公司建立了一套完善的提高工人技能水平的政策和方针,但很少有公司执行降低换模本身所需要的技能水平的策略。
”——新乡重夫( Shigeo Shingo )3.快速换模的境界●境界一:No concept of Quick Changeover 没有快速换模观念●境界二:Single Minutes Exchange Die 单分钟换模●境界三:Zero Exchange Die 零换模●境界四:One Touch Exchange Die 一触换模●境界五:One Cycle Exchange Die 一周换模●境界六:No Need Exchange Die 无需换模传统换模介绍1 传统换模的十个步骤 3 换模的七大浪费4 传统换模的时间分配2 传统换模存在的问题1.传统换模活动的十个步骤●1.机台停机● 2.旧产品零部件撤离现场● 3.换模人员和工具准备● 4.清洁机台和模具● 5.拆卸旧模具● 6.搬运新模具及检查保养● 7.装配新模具● 8.通知前工序准备新零部件试产● 9.搬运新零部件准备生产● 10.运行调整2.传统换模活动存在的问题1.在机台停机后物料才开始移动●成品被送到下一个工位●原材料在设备停止后才移走●新模具、各种配件运到机台2.机台准备运行时才发现缺陷和缺少的配件●换模开始后才开始修复缺陷配件,需要调整或更换设备配件●微调开始后才发现缺陷产品3.机台开动后,才发现不良的加工,夹具设定和仪器设定●内部作业开始后,操作者才发现缺陷的设备2.传统换模活动存在的问题4.缺少标准化的安装调整流程和技术要求●每个调模工根据他们自己经验,按照他们认为合适的方式进行安装和调整,缺少标准;●没有2个调模工以同样的方式安装和调整;●每个班次都觉得上个班次的调整达不到要求,要重新调整;●一些人认为安装和调整时间越长产品质量会更好。
精益生产快速换模改善案例(经典作品) 精品
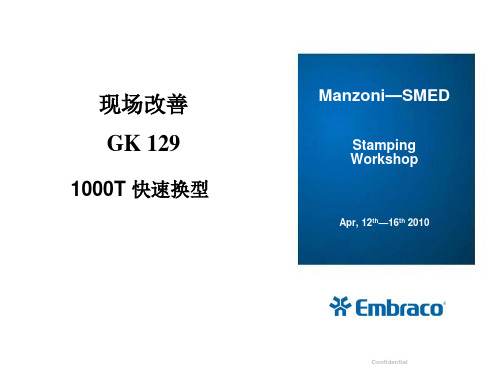
Objective and Goal 目的与目标
•降低1000T换型时间 ==》从35分钟至20分钟
Decrease the setup model time (1000T) ==》 From 35mins to 20 mins
•人因工程改善 ==》1项
Ergonomic Improvement ==》1 Item
Internal Work: Operations which have to happen when the machine is not running 外部工作:机器没有运作时要进行的工作
External work: The operations which can take place when the machine is running 内部工作:机器运作时要进行的工作
将内部工作与外部工作分开
• Work to be done after stopping 停机后要做的工作
Study of the actual situation 研究实际情况
Register and classified all the necessary working elements 将所有必要的工作进行登记和分类
2
Confidential
The source of the GK 项目来源 1. VSM 价值流程图
Kaizen 改善 SMED
2. 860项目组 Capacity Expansion project 8.6 M/y
Presentation's Title
3
Confidential
Objectives and Goal 目的 与目标
0
0 00:00:45
- 1、下载文档前请自行甄别文档内容的完整性,平台不提供额外的编辑、内容补充、找答案等附加服务。
- 2、"仅部分预览"的文档,不可在线预览部分如存在完整性等问题,可反馈申请退款(可完整预览的文档不适用该条件!)。
- 3、如文档侵犯您的权益,请联系客服反馈,我们会尽快为您处理(人工客服工作时间:9:00-18:30)。
螺丝只需转一圈即可拧下
小螺母U-形 垫圈梨形孔
此改善点表明:只需转一圈即可拧下螺丝。 虽然大多数螺丝的螺纹每英寸有12至20圈,但只有最后 一圈起固作用,其它的均属浪费。
现场案例:辅导后某客户《机加工现场》 一个流生产(LEAN生产的一种)
设备效率与快速切换
设备效率提升
常见的浪费设备无效使用的现象有哪些?
我们的设备效率是如何计算?是多少?
设备损耗计算
稼动时间=运行时间
(某一日)
工作时间 475分
负荷时间
稼动时间 460分
400分
15 管理停止时间(早晚令、5S等) 分 故障停止 20分 60分 LOSS停止时间 品种切换 20分 品质故障停止 20分
第四次 时间 3分49秒
3分22秒
3分05秒
4分11秒
4分30秒
第N次改善
大家各自换摸
液压定位,不用螺栓\螺母
换模准备
保证安全前提下:双手换模
模具放置
换模车没有任何准备 此时换模时间为40分钟
换模准备
模具放置
换模车有了准备,但准备不专业 此时换模时间为30分钟
类别(含调试) 钣金冲压300T以下 塑胶换型300T左右 塑胶换型700T左右 装配线换型 一般企业 30分钟左右 世界级 5分钟以内 5~10分钟 差距 6倍 5~8倍 10~15倍 6~8倍 10倍以上
钣金冲压1000T左右 40~50分钟
110~150分钟 10分钟左右 150~200分钟 25分钟左右 10~30分钟 0~60秒
120 80 有效稼动时间 200分 点点停32次(5分锺以下) (生产量) 分 分 400个/日 速度低下耗费(基准周期0.5分/个; 价值稼动时间 196分 4 实际周期0.8分/个) (最终良品) 392个/日分 不良废弃品耗费(8个)
设备综合效率计算(续1)
按1日的负荷时间460分计,设定生产良品数应为: 460分/ 0.5(分/个)=920个, …但实际生产良品数仅为392个 . 设备综合效率:设备在负荷时间内的产出效率 =价值稼动时间 / 负荷时间 =196/460=42.6% (=实际良品数/设定良品数 =392/920=42.6%.)
下批生产 模具放置
上批换下 模具放置
零件料号 B0772772 DC11换B0772778 DC11 B0772772DH11换 B0772778DH11 B0772772 DF21换B0772778 DF211
第三次 时间 3分39秒
零件料号 B0772778 DC11换B0771786 DC11 B0772778DC11换 B0771786DP11 B0772778 DC11换B0771786 DN11
设备的10大浪费
设备故障浪费 点点停的浪费 转换调试准备浪费 制造不良
维修的浪费
启动浪费 夹具模具浪费 物流慢浪费
速度低下浪费
品质故障浪费
设备停机记录及效率
设
NO
备
运
行
状
况
记录者 备 注
停机开始~恢复开机
: : : : : : ~ ~ ~ ~ ~ ~ : : : : : :
停机时间
停止的要因描述
吉利汽车
• 冲压切换从45分→15分(5个月) • 15分→10分(2个月) • 将来10分→ 5分
快速换摸案例演示
瓶颈设备管理—— 快速转换、与日常保养
模具放置
设备装置为生产核心的车间 -----设备效率\换模与调模时间
2
3
4
5
6
7
8
9
10
11
12
13
14
15
16
17
18
19
20
◇ 以“多品种、小批量”为特征的均衡化生产是看板 管理和准时化生产方式的重要措施,而实现均衡化 生产,最关键的问题就是设备的快速装换调整问题.
◇ 缩短设备的装换与调整时间是减少瓶颈、降低成本、
改进产品质量和实现准时化生产方式的关键。
产品快速切换常用方法
设备损耗计算(续2)
• 设备综合效率不能够反映出各类LOSS 的影响各有多大,以及一项改善活动在什 么方面产生了作用;为了找出造成设备综 合效率低下的各类原因及其影响度,导 入以下公式:
设备综合效率=时间稼动率 × 性能稼动率 ×良 品 率 停止LOSS 速度LOSS 不良LOSS
设备损耗计算(续3)
换模车有了充分的准备,准备非常专业 在附之于其它改善,此时换模时间为15分钟
提前移出下批模具
所有员工动手
卸下模具暂放
口哨联络
分工合作
内換模改善(辅导他公司事例)
事例 : 改善清理机台時間
改善前: 废料清理
换型时一般企业同世界级企业差距
:
~
:
设备停机记录及效率
设备名称: №: 1 2 3 4 5 6 7 8 9 10 11 12 13 14
项 目
设备编号:
计时单位:(h)
1
换模时间 调试时间 检查待判定时间 缺料停机时间 无生产计划停机 设备保养/修理 模具修理停机 质量问题停机 生产中异常停机 其他原因停机 总停机时间 实际开机时间 当日可开机时间 设备稼动率
时间稼动率=稼动时间/负荷时间 设备综合效率=价值稼动时间/负荷时间 (196/460) = (负荷时间—停止时间)/负荷时间 =时间稼动率 ×— 性能稼动率 = (460 60)/460= ×良 87% 品 率 =(400/460) × (200/400) ×(196/200) 停止LOSS = 87% × 50% × 98% =42.6% 性能稼动率 =有效稼动时间/稼动时间 (200/400) 设备的生产率 =设备综合效率×设备可动率 =生产量×基准周期 /(负荷时间-停止时间 (设备的效率) 42.6% ×460/475 0.5/ ( 460-60 )= 50% 速度 LOSS =400 × = =41.3% 我们呢? 良 品 率 =良品数 /生产量(392/400) = 98% 不良LOSS
• SMED
精益生产实践 快速生产切换法
-------「一分钟换模」
品种切换(转换)时间
SMED法有4个基本要求:
1) .严格区分“内部操作”和“外部操作” ; 2) .将“内部操作”转化为“外部换操作”;
3) .缩短内部操作时间 .
4).彻底的5S管理
快速切换(不是转换)
例1:减少拧下和紧固螺丝的工作量