船用管子制通用工艺
管子加工呵安装通用工艺规范

管子加工呵安装通用工艺规范1.范围本标准规定了船舶管子内场加工及外场安装的工序内容和验收要求。
本标准适用于船舶管子的加工和安装。
2.引用标准CB*3083 弯管技术要求CB*/Z335 船用管子加工通用技术条件CB*/Z345 船舶管系布置和安装通用技术条件3.加工和安装前的准备3.1在新产品项目开工前,施工人员应用一定的时间熟悉产品名称、工程编号、分段号、项目号、项目内的各系统及安装部位。
3.2熟悉有关图纸资料,其内容包括各系统原理图、管子零件图、综放安装图、各类托盘表和开孔图及图纸中的技术要求和工艺说明。
3.3熟悉了解型宽、型深、肋距及梁拱高度和各构件高度,以及甲板间高度、舱室布置和木作绝缘厚度、地平敷料高度及各分段大合拢肋位线。
3.4正确使用工艺规定的各类型号、规格、数量的配套件,严格按图纸工艺要求施工。
4.内场制造4.1领料持领料单领取各种牌号、规格、数量的合格管材,并分别放置在料架上,Ⅰ、Ⅱ级管材应单独存放,并做出明显标记,标记应含检验号、规格。
管材领发必须建立台帐、做好记录、签名。
4.2下料4.2.1工序内容熟悉图纸资料及工艺文件,准备工护具,领取管材,按图划线、切割、用广告色或记号笔做标记,将管子放至指定地点。
4.2.2工艺步骤4.2.2.1按管子零件图要求,正确选用管材的牌号、规格和等级;检查管子有无明显凹陷、夹渣、分层、铜绿及其它腐蚀现象,白铁管还要检查接缝处有无开裂(直观或听敲击声判断),不符合质量的管材坚决不用,并及时反馈。
4.2.2.2按管子零件图下料尺寸,用色笔画出切割线,并加注“S”符号,规范书写分段号和零件号,尽可能套裁,短管可用于隔舱贯通件制作。
4.2.2.3切割管材DN125(含DN125以下全部机割,DN150以上允许气割,机割管去毛刺,气割管应去熔渣,管子端面和轴向垂直,允许偏差20~30。
有色管全部机割,去毛刺、锐边。
下料后的管子应置放到托架上,行车配合吊运到弯管机旁整齐堆放。
船用管子装配焊接工艺介绍
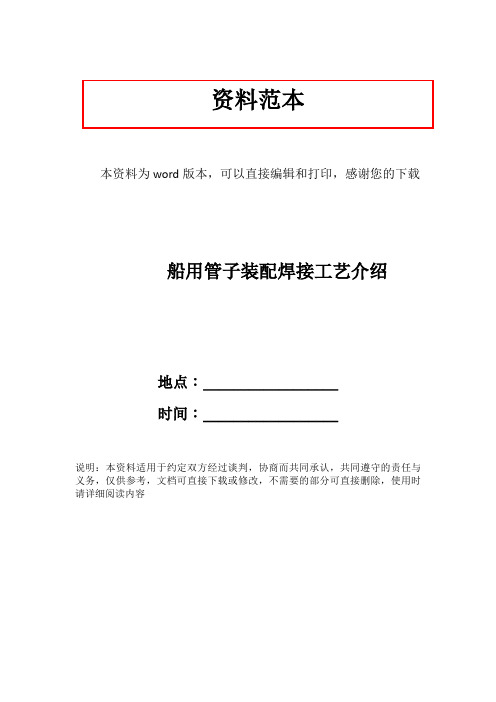
资料范本本资料为word版本,可以直接编辑和打印,感谢您的下载船用管子装配焊接工艺介绍地点:__________________时间:__________________说明:本资料适用于约定双方经过谈判,协商而共同承认,共同遵守的责任与义务,仅供参考,文档可直接下载或修改,不需要的部分可直接删除,使用时请详细阅读内容1 本工艺是管系施工工艺文件,是在考虑了本厂目前施工中的具体情况而编制的。
2 本工艺属于指导性文件,如设计图纸或专用工艺文件另有特殊规定或技术要求,则应按图纸或专用工艺文件执行。
3 本工艺不适用于主蒸汽、氧气和氮气等特殊管路及软管系统。
4 本工艺适用于内燃机动力船舶的常用管系。
范围本工艺主要规定了船用管子装配焊接通用工艺,适用于各类船舶材料满足规范要求的下列规格管子的装配焊接:外径在325mm以下的无缝钢管和合金钢管、180mm以下的铜管和铜合金管、70mm以下的铝管和铝合金管、42mm以下的双金属管和DN150mm以下的水煤气管。
对于其他类型或有特殊要求的管子应按设计要求另制定专门的焊接工艺。
1、管子与管子的焊接管子的焊接可以采用直接对焊、坡口对焊、衬圈对焊以及封底对焊等形式。
各种型式的技术要求见表一表一管子对焊型式及技术要求管子对接中心偏差均应≤1.0mm。
若管子对接时有壁厚差,则在较厚壁内侧削斜,其削斜长度不小于壁厚差的4倍。
管子经对接焊后,管子内外表面的焊渣和飞溅均应去除,如果采用气焊封底焊则焊缝内表面的修正可以省略。
2、法兰与管子的焊接2.1 钢管的法兰连接形式和适用范围见表22.2 法兰焊接应在支管和弯头焊接之后,以防止焊接变形。
焊接型式应严格按照所选用法兰标准的要求进行。
2.3 装焊时,法兰内壁与管子外表面最大间隙应不大于2mm,径向相对两点的间隙总和不得超过3mm;法兰与管子焊接的咬口深度应不大于0.2mm,超过此数值应予以修整。
焊接时不应使法兰密封平面碰电、损坏。
船舶管子焊接通用工艺
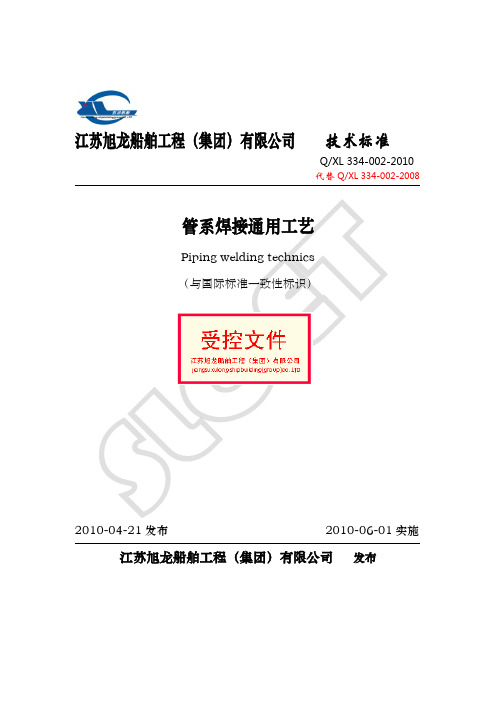
江苏旭龙船舶工程(集团)有限公司技术标准Q/XL 334-002-2010 代替 Q/XL 334-002-2008管系焊接通用工艺Piping welding technics (与国际标准一致性标识)2010-04-21 发布2010-06-01 实施 发布江苏旭龙船舶工程(集团)有限公司Q/XL 334-002-2010管系焊接通用工艺前言为确保公司承建船舶管路的焊接质量, 确保船舶使用和安全性能, 公司组织专业人员根 据造船规范和有关国家标准要求,再结合公司生产实际编制了本工艺。
本标准代替 Q/XL 334-002-2008 本标准是 Q/XL 334-002-2008 的重新修订本标准由 江苏旭龙船舶工程(集团)有限公司 提出 本标准由公司 技术部 归口本标准起草部门:工艺室 本标准主要起草人: 朱 军 本标准由总经理 周爱红 批准 本标准首次发布:2004 年 04 月 02 日zhujun2/9SLOETQ/XL 334-002-2010管系焊接通用工艺管系焊接通用工艺Q/XL 334-002-2010 1 范 围本规范规定了气体保护焊和氩弧焊用于管子焊接的焊前准备、人员要求、焊接程序、焊 接要求、和检验。
本规范适用于管子与管子、 管子与附件之间的对接和角接接头, 焊接时, 可采用纯 CO2 气体或 CO2+Ar 混合气体的 CO2 半自动或自动焊接, 也可采用钨极氩弧焊。
焊接位置为管 子水平转动位置和管子水平固定位置。
2 焊材和设备的要求2.1 焊条,焊丝和焊剂应符合有关标准的规定或验船部门认可。
2.2 焊条必须存放在干燥,通风良好的库房内,库房室温应大于5℃,相对湿度小开6℃, 严防焊条受潮变质。
焊条在使用前,需根据其万分,进行不同程度的烘干。
2.3 焊丝和焊剂应存放于干燥通风的室内。
严防焊丝生锈和焊剂受潮。
焊丝在使用前盘入焊 丝盘时,应清除螺丝上的油污,焊剂在使用前亦要进行烘干。
船用管子加工通常工艺标准
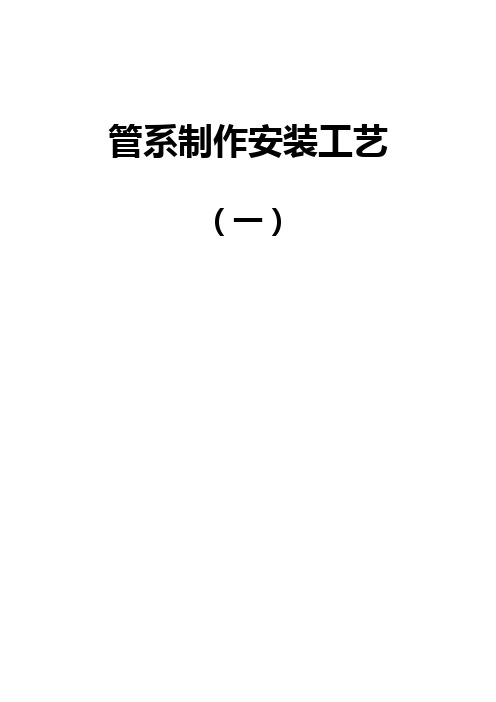
管系制作安装工艺(一)船用管子制作工艺本文件适用于各类船舶下列规格管子的加工:外径在500mm以下的无缝钢管和合金钢管、250mm以下的铜管和铜合金管(包括铜镍管)、6英寸以下的水煤气管及其它金属管。
本文件可供船舶管系施工设计时选用。
对于特殊要求的管子应按设计要求加工。
1、材料1.1 管子材料应符合我国造船规范要求和有关国家标准的规定。
出口船舶用管材须符合该船舶入级相应的船级社要求。
1.2 各种管材,必须具有制造厂的炉罐号和合格证书,如缺少证明时,应根据有关规定或订货要求补做试验,合格后方可使用。
1.3管子加工前,必须核对管子材料是否符合图纸要求。
1.4管子加工前,应对管材内外表面质量进行检查。
1.4.1无缝钢管和合金钢管,其内外表面不得有裂缝、折叠、分层、结疮、轧折、发纹等缺陷存在。
如有上述缺陷应予清除,清除部位壁厚的减薄不得超过该材料标准允许的负偏差。
1.4.2 焊接钢管内外表面不允许存在由于焊接引起的裂缝、咬口、飞溅、凹陷等缺陷。
1.4.3 有色金属管子,其表面应光滑清洁,不应有针孔、裂缝、气泡、分层、锈蚀等缺陷。
1.5碳素钢管、不锈钢管在订货时,应向制造厂提出退火处理要求。
1.6 法兰、套管、螺纹接头、异径接头、定型弯头等连接件,必须具有材质报告证件,方可使用。
2、管子弯曲加工2.1 弯管设备2.1.1 弯管机须经过设备管理部门检查验收,才能正式投入使用。
2.1.2 弯管模子、滑块或滑轮槽道和塞芯头部光洁和顺,切口处必须倒圆。
2.1.3 弯管模子和滑块的圆槽直径按表1。
2.1.4 有芯弯管机、芯棒头部的外径和长度按表2。
2.1.5 弯管机的工夹具/模具和附属设备应当定期检查和维修,以确保良好状态。
2.2 弯管技术要求2.2.1 管子的弯曲,一般采用冷弯的方法,在工厂缺少冷弯设备的情况下,允许采用热弯,但水煤气管不宜采用热弯,20号钢管不宜采用中频弯曲。
2.2.2 不锈钢管及合金钢管宜冷弯,如必须热弯时,不锈钢管加热应避免渗碳,而对淬硬倾向较大的合金钢管则不得浇水冷却。
1)船舶管系布置和安装通用工艺A

船舶管系布置和安装通用工艺
一、适用范围
1. 本工艺规定了船舶管系的布置、安装、管子支架、绝缘包扎、压力试验和清洁 投油等方面的工艺及其质量验收指标要求。
2. 本工艺适用于大中型钢质船舶管系的布置和安装,小型船舶可参照执行。 3. 本工艺属于指导性文件,如设计图纸或专用工艺文件另有特殊规定或技术要
T K
150 T K
150 T K
150
K≥T
图 10
3.1.3 法兰焊按座板可根据需要分别选用单面座板(图 11)或双面座板(图 12)。
座板在上船焊接前应先加工好螺孔,焊接时应对螺孔作适当保护以防飞溅损
伤。
单面座板
舱壁
管子 阀或配件
管子
舱壁
图 11 阀或配件
Байду номын сангаас管子
阀或配件
舱壁
图 12 3.2 管子通过无水密要求的舱壁或平台时,其安装形式可参照表 3。
3.4.2 开孔的端部应尽量做到与横梁或纵桁穿过处的切口边缘等距离;开孔边缘 至纵桁或横梁面板的距离应小于其腹板高度的 40%。
3.4.3 开孔应有光滑的边缘和良好的圆角,且不应将开孔密集地布置在相邻的纵 骨间距内;离强横梁肘板趾部端 200mm 范围内的强横梁腹板上不得有任何 开孔。
-- 8 --
管子通用工艺-----船舶管系布置和安装工艺
3.4.4 凡开孔尺寸不能满足 5.4.1 款和 5.4.2 款的要求时,应予以补偿,补偿办法 利用复板搭焊于纵桁或横梁腹板上,复板的厚度应与腹板的厚度相等(见图 14)。
腹板
150 ~ 300
300 ~ 600
复板 图 14
3.4.5 在开孔处采用扁钢加强时,扁钢厚度不得小于腹板厚度,扁钢补偿围板外 表面应与开孔表面紧密接触,并采用双面连续焊,见图 15。
船舶液货不锈钢管制作安装工艺

船舶液货不锈钢管制作安装工艺
1. 材料选择,船舶液货不锈钢管的制作首先要选择合适的材料,通常选择316L、316、304等不锈钢材料,这些材料具有良好的耐腐
蚀性能和机械性能,适合在海洋环境下使用。
2. 制作工艺,制作船舶液货不锈钢管的工艺包括切割、弯曲、
焊接等步骤。
切割要求精准,保证管子的尺寸符合要求;弯曲需要
使用专业的弯管机进行,确保弯曲半径和角度符合要求;焊接工艺
要求高,通常采用TIG焊接,确保焊缝的质量和密封性。
3. 安装工艺,船舶液货不锈钢管的安装需要考虑船舶的特殊环境,包括船体的振动、海水腐蚀等因素。
安装时要保证管道的支撑
和固定,以减少振动对管道的影响;同时要做好防腐措施,保证管
道在海水环境下的长期使用。
4. 质量控制,制作和安装过程中需要严格控制质量,包括对材
料的质量检验、工艺过程的质量控制和最终产品的检验。
确保船舶
液货不锈钢管的质量符合相关标准和要求。
5. 安全考虑,船舶液货不锈钢管的制作和安装过程中需要充分
考虑安全因素,包括防火、防爆、防腐蚀等方面的安全措施,确保管道在使用过程中不会发生安全事故。
总的来说,船舶液货不锈钢管的制作和安装工艺需要综合考虑材料选择、工艺控制、质量检验、安全考虑等多个方面,确保管道的质量和安全可靠性。
希望以上回答能够满足你的要求。
船舶管子的拼接与弯制

2
1.5
0 ~1.5
⑶ 管子及弯头切割后,按坡口要求加工好坡 口。加工的方法最好采用机械(车床、镗床)加 工,无合适的机械设备时,用手工锉出。 ⑷ 装配前,对焊缝二边30mm范围内做好清洁 工作,去除管子内外表面的氧化物、油和水。清 洁工作的方法为: ① 用砂纸、铜丝刷、不锈钢丝刷和清洁的回 丝布擦洗; ② 用丙酮擦洗; ③ 用风动工具装布抛头抛光,此方法最有效。
3、装配
⑴ 法兰装配 将松套钢法兰套入管子, 有内倒角面对准内法兰,管 子与内法兰保持同轴线,按 装配坡口要求控制好间隙, 第一点定位焊,用法兰定规
检查管子与内法兰的垂直,
然后继续进行定位焊。
⑵ 三通、弯头、异径接头装配
① 管子与三通、弯头、异径接头保持同轴线对准,不能 有高低差,并按坡口要求控制好间隙,然后进行第一点定位 焊。对中时,可采用工夹具将需对中的二部分夹紧,工夹具 上留有点焊用的空隙 。 ②用角度尺、直尺检查各管段之间的夹角或直线度。 ③继续进行定位焊。
校管机校管
1、校管机校管的基本概念 校管机校管是在主管上安装搭焊式法兰的
一种方法。它是根据管子零件图的信息,将校
管机移动到适当的位置,并在模板上装上法兰, 法兰内放上厚度与焊接端距相同的钢环,然后 将成型管子的二端套进法兰,按图调整好管子 的位置,然后进行法兰的定位工作。
1
2 8 4
2、校管机结构及其 工作原理
A 螺栓 螺母 夹箍 管子 A向
图7.4.57 对中工夹具
4、焊接前的准备工作 采用氩弧焊工艺,焊接前做好以下工作: ⑴ 清除定位焊产生的氧化物。 ⑵ 用封板将管子所有端头封堵,封板中有一只 安装氩气接头,封板中橡胶封板的直径比管子内径 大3mm左右。 ⑶ 除需焊接的一条焊缝外,其余焊缝用胶带包 住,为防止胶带上的粘合剂涂上管子影响焊接,第 一层胶带反贴,即无粘合剂一面向着管子,再用第 二层胶带包复。
船舶管系工工艺

单,但扭矩较小,只 适宜弯制小直径管。
前夹头 后夹头 管子
图7.3.5 球形芯棒和前置量K示意图
⑶ 液压、数控、冷弯弯管机(简称数控弯管机) 数控弯管机是应用电子数字控制技术的加工设 备。它能按照规定的程序和尺寸要求自动进行管子 弯制工作,实现管子弯管自动化,减轻劳动强度, 提高生产效率和管子弯管精度。
标准 范围 ――― ――― ――― ――― ――― ――― ――― ―――
允许极限 (%) ――― 20 25 10 20 5 15 5
备注
壁厚减薄率F F=(t-t1) / t X100 式中: 钢 t-原管壁厚, 管 mm t1-弯曲后的壁 厚,mm
3DW<R≤4DW
热弯 冷弯
R 为 弯 曲 半 径
项 目 R≤2DW 管子园度率E E=(a-b)/DWX100 式中: a-弯曲处截面最 大外径, mm; b-弯曲处截面最 小外径,mm; DW-管子实际外 径,mm 钢管 、 铜管 2DW<R≤3DW 3DW<R≤4DW R>4DW R≤2DW 铝黄 钢管 2DW<R≤3DW 3DW<R≤4DW
第四节 校管
一、校管机校管
1、校管机校管的基本概念
校管机校管是在主管上安装搭焊式法兰的
一种方法。它是根据管子零件图的信息,将校
管机移动到适当的位置,并在模板上装上法兰,
法兰内放上厚度与焊接端距相同的钢环,然后 将成型管子的二端套进法兰,按图调整好管子 的位置,然后进行法兰的定位工作。
1
2 8 4
部分进行冷却,因而会发生弯曲后产生裂
纹的现象,一般仅适用于弯制10号无缝钢
管。对于20号无缝钢管,弯曲后应作退火 处理。
(工艺技术)船舶管系制作安装工艺

(工艺技术)船舶管系制作安装工艺东海船舶修造有限公司船舶管系制作安装工艺技术科编制Lenovo User2008-9-1船舶管系制作安装工艺为现代造船的发展,规范管系制作及安装,保证管系制作和安装质量,使船舶建造更加规范化、正规化所编制。
本工艺参照各种相关船舶建造标准、规范及本公司实际而编制。
管系布置、预制及安装流程原则、规则。
一.管系布置原则1.管系布置要层次分明,顺序为先大口径管,后小口径管。
管子的排列应尽可能平直,成组成束并列,整齐和美观,以最短的距离连接,达到最佳目的,避免不必要的迂回和斜交叉。
2.管系的布置间距(1) 并行管或交叉管,邻近两根管子(包括管子附件),间距应在20mm 以上。
(2) 对于需要包扎绝缘的管子,包好绝缘后,其外缘与相邻管子、管系附件或船体结构件的间距在30mm以上。
(3) 下列管子与电缆的间距应在100mm以上。
a.蒸汽管子绝缘层外表。
b.非水隔层绝缘的排气管外表。
c.工作压力9.8MPa(100kg/cm2)以上的高压空气管。
3.位置应便于安装和操作,各种管子应尽量沿准船体结构或箱柜的附近布置。
4在通道拆装维修及检查等必要的空间内,不应设置管路,对机械拆装、维修、检查等必要的空间应根据设备详图,经阅校核后再做最后决定。
5.当电缆、管子和通风管道在同一位置时,最好由上至下,按照电缆-管子-通风管的顺序布置。
6淡水管不得通过油舱,油管不得通过淡水舱,如不能避免时,应在油密隧道或套管内通过,海水管也尽量避免通过淡水舱,其它管子通过燃油舱时,管壁按规范要求加厚,且不得有可拆接头。
7.燃油舱柜的空气管、溢流管、测量管和注入管应避免通过居住舱室,如必须通过时,则通过该类舱室的管子不得有可拆接头。
8.配电板及重要仪器上方及后面不得设置蒸汽管、油管、水管、排气管、油柜和水柜。
特殊情况下必须布置时,则不得设置管接头,并采取有效的防护措施。
9.锅炉、烟道、蒸汽管、排气管及消音器的上方应避免设置油管及油柜,如无法避免时,油管不得有接头,且应装设滴油盘或其他防护设备。
船舶管系制作安装工艺

船舶管系制作安装工艺为现代造船的开展,标准管系制作及安装,保证管系制作和安装质量,使船舶建筑更加标准化、正规化所编制。
本工艺参照各种相关船舶建筑标准、标准及本公司实际而编制。
管系布置、预制及安装流程原那么、规那么。
一.管系布置原那么1.管系布置要层次清晰,顺序为先大口径管,后小口径管。
管子的排列应尽可能平直,成组成束并列,整洁和美看,以最短的距离连接, 到达最正确目的,防止不必要的迂回和歪交叉。
2.管系的布置间距(1)并行管或交叉管,邻近两根管子〔包括管子附件〕,间距应在20mm 以上。
(2)关于需要包扎尽缘的管子,包好尽缘后,其外缘与相邻管子、管系附件或船体结构件的间距在30mm 以上。
(3)以下管子与电缆的间距应在100mm 以上。
a.蒸汽LenovoUser2021-9-1东海船舶修造船舶管系制作安装工艺技术科编制管子尽缘层外表。
b.非水隔层尽缘的排气管外表。
c.工作压力9.8MPa(100kg/cm2)以上的高压空气管。
3.位置应便于安装和操作,各种管子应尽量沿准船体结构或箱柜的四周布置。
4在通道拆装维修及检查等必要的空间内,不应设置管路,对机械拆装、维修、检查等必要的空间应依据设备详图,经阅校核后再做最后决定。
5.当电缆、管子和通风管道在同一位置时,最好由上至下,按照电缆-管子-通风管的顺序布置。
6淡水管不得通过油舱,油管不得通过淡水舱,如不能防止时,应在油密隧道或套管内通过,海水管也尽量防止通过淡水舱,其它管子通过燃油舱时,管壁按标准要求加厚,且不得有可拆接头。
7.燃油舱柜的空气管、溢流管、测量管和注进管应防止通过居住舱室,如必须通过时,那么通过该类舱室的管子不得有可拆接头。
8.配电板及重要仪器上方及后面不得设置蒸汽管、油管、水管、排气管、油柜和水柜。
特不情况下必须布置时,那么不得设置管接头,并采取有效的防护措施。
9.锅炉、烟道、蒸汽管、排气管及消音器的上方应防止设置油管及油柜,如无法防止时,油管不得有接头,且应装设滴油盘或其他防护设备。
船用管子制作通用工艺

管系制作通用工艺船用管子制作通用工艺一、目的及范围本工艺规定了船舶管子零件的材料、切割、装配、弯曲、表面处理、等方面的工艺及其质量验收指标要求。
本工艺适用于各类船舶下列规格管子的加工:外径在500mm以下的无缝钢管、焊接钢管和不锈钢管,250mm以下的铜管和铜合金管(包括铜镍管)、6英寸以下的水煤气管及其它金属管。
本文件可供船舶管系施工设计时选用。
对于特殊要求的管子应按设计要求加工。
二、引用标准下列标准所包含的条文,通过在本工艺中引用而构成本工艺的条文。
由于标准都会被修订,使用本工艺的各部门应探讨使用下列标准最新版本的可能性。
CB/T3790-1997 船舶管子加工技术条件CB/T3365-91 管子无余量下料工艺CB/Z94-68 黑色金属磷化技术条件CB*/Z343-84 热浸锌通用工艺船舶建造质量检验(CSQS)1998版中国船级社钢质海船入级和建造规范(CCS)2001版德国劳氏船级社钢质海船入级和建造规范(GL)1992版三、管子材料要求3.1 管子材料的机械性能和化学成分应符合有关国家标准、行业标准和我国造船规范要求。
出口船舶用管材须符合该船舶入级相应的船级社要求。
3.2 各种管材,根据其设计压力和设计温度分为三级,见表1。
对于I级、II级管,必须具有船舶检验部门的合格证书及制造厂的炉罐号。
III级管应具有制造厂的合格证书,如缺少证明时,应根据有关规定或订货要求补做试验,合格后方可使用。
四、管子的切割表1 管系等级1.Ⅰ级栏中的设计压力和设计温度两个参数,只要其中一个符合表中规定数值的,即为Ⅰ级管;Ⅱ级栏中的设计压力和设计温度两个参数,均达到表中规定数值的,即为Ⅱ级管。
2.除Ⅰ、Ⅱ级管外,其余的是Ⅲ级管。
3.表中其他介质是指空气、水、滑油或液压油等。
4.1 管子切割前,必须核对管子材料、规格是否符合图纸要求。
4.2 管子切割前,应对管材内外表面质量进行检查。
4.2.1无缝钢管和合金钢管,其内外表面不得有裂缝、折叠、分层、结疮、轧折、发纹等缺陷存在。
1)船舶管系布置和安装通用工艺A解析

船舶管系布置和安装通用工艺一、适用范围1. 本工艺规定了船舶管系的布置、安装、管子支架、绝缘包扎、压力试验和清洁投油等方面的工艺及其质量验收指标要求。
2. 本工艺适用于大中型钢质船舶管系的布置和安装,小型船舶可参照执行。
3. 本工艺属于指导性文件,如设计图纸或专用工艺文件另有特殊规定或技术要求,则应按图纸或专用工艺文件执行。
4. 本工艺不适用于氧气、氮气等特殊管系及软管、塑料管、风管等系统,也不适用于化学品货物管系及化学品处理管系。
5. 本工艺编写内容应能满足德国劳氏船级社钢质海船入级和建造规范(GL)、法国钢质船舶入级规范(BV)等国外船级社的规范要求,如有特殊情况不能满足规范要求时,由船厂、船检部门、船东共同协调解决。
二、引用标准2.1 下列标准及规范所包含的条文,通过在本工艺中引用而构成本工艺的条文。
由于标准及规范都会被修订,当修订后的新标准及规范与本工艺不相符时,使用本工艺的各有关部门应探讨使用下列标准最新版本的可能性。
a) 船舶管系布置和安装通用技术条件CB*/Z 345—85;b) 船舶管子加工技术条件CB/T 3790—1997;c) 船舶建造质量检验标准(QSCS)1998版;d) 中国船级社钢质海船入级规范(CCS)2001版;e) 德国劳氏船级社钢质海船入级和建造规范(GL)1992版。
三、工艺内容1管系布置原则1.1 管系布置的先后顺序是先大口径后小口径管,管子的排列应尽可能地平直、成组成束并列、整齐和美观,避免不必要的迂回和斜交。
1.2 管系的布置间距1.2.1 并列管或交叉管,邻近两根管子(包括管子附件),间距应在20mm以上,参照图1。
图 11.2.2 对于需要包扎绝缘的管子,包好绝缘后,其外缘与相邻管子、管系附件或船体结构件的间距应在30mm 以上。
1.2.3 下列管子与电缆的距离应在200mm 以上。
a) 蒸汽管子绝缘层外表; b) 非水隔层绝缘的排气管外表;c) 工作压力9.8Mpa (100kgf/cm 2)以上的高压空气管。
船舶管系通用工艺

船舶管系通用工艺(厂标)南京蛟龙船舶有限公司技术部编制目录(1) 总则----------------------------------------------3(2) 管子等级、材料与规格------------------------------3(3) 管子布置原则与要求--------------------------------5(4) 管子的加工技术要求--------------------------------7(5) 管子的连接形式与要求-----------------------------12(6) 管路安装-----------------------------------------18(7) 管子通过船体结构的安装要求-----------------------20(8) 管子支架-----------------------------------------24(9) 管子试验-----------------------------------------31 附管路垫片使用表-------------------------------------331总则1.1.为了缩短船舶船台建造周期,确保船舶管系制作安装的可靠性、准确性、结合本公司实际施工状况特制定本工艺。
1.2.本工艺适用于我公司船舶设计的管系设计与管子加工、布置、安装。
对有特殊要求的管子加工、安装以图纸要求为准或者另编单船专用工艺。
1.3.本工艺规定了船舶管系加工、布置、安装要求及检验规则。
1.4.本工艺是南京蛟龙船舶有限公司企业标准,其内容与规范或者设备资料有矛盾时,应按规范或者设备资料要求执行。
2.管子等级、材料与规格2.1.管系等级2.1.1.船舶耐压管系按其设计压力与温度,通常分为Ⅰ、Ⅱ、Ⅲ三级见表1。
具体管子等级应根据所入级船级社规范而定。
表1 管系等级2.2.材料与规格2.2.1.无缝钢管的规格优先选用表2。
- 1、下载文档前请自行甄别文档内容的完整性,平台不提供额外的编辑、内容补充、找答案等附加服务。
- 2、"仅部分预览"的文档,不可在线预览部分如存在完整性等问题,可反馈申请退款(可完整预览的文档不适用该条件!)。
- 3、如文档侵犯您的权益,请联系客服反馈,我们会尽快为您处理(人工客服工作时间:9:00-18:30)。
管系制作通用工艺船用管子制作通用工艺一、目的及范围本工艺规定了船舶管子零件的材料、切割、装配、弯曲、表面处理、等方面的工艺及其质量验收指标要求。
本工艺适用于各类船舶下列规格管子的加工:外径在500mm以下的无缝钢管、焊接钢管和不锈钢管,250mm以下的铜管和铜合金管(包括铜镍管)、6英寸以下的水煤气管及其它金属管。
本文件可供船舶管系施工设计时选用。
对于特殊要求的管子应按设计要求加工。
二、引用标准下列标准所包含的条文,通过在本工艺中引用而构成本工艺的条文。
由于标准都会被修订,使用本工艺的各部门应探讨使用下列标准最新版本的可能性。
CB/T3790-1997 船舶管子加工技术条件CB/T3365-91 管子无余量下料工艺CB/Z94-68 黑色金属磷化技术条件CB*/Z343-84 热浸锌通用工艺船舶建造质量检验(CSQS)1998版中国船级社钢质海船入级和建造规范(CCS)2001版德国劳氏船级社钢质海船入级和建造规范(GL)1992版三、管子材料要求3.1 管子材料的机械性能和化学成分应符合有关国家标准、行业标准和我国造船规范要求。
出口船舶用管材须符合该船舶入级相应的船级社要求。
3.2 各种管材,根据其设计压力和设计温度分为三级,见表1。
对于I级、II级管,必须具有船舶检验部门的合格证书及制造厂的炉罐号。
III级管应具有制造厂的合格证书,如缺少证明时,应根据有关规定或订货要求补做试验,合格后方可使用。
四、管子的切割表1 管系等级注:1.Ⅰ级栏中的设计压力和设计温度两个参数,只要其中一个符合表中规定数值的,即为Ⅰ级管;Ⅱ级栏中的设计压力和设计温度两个参数,均达到表中规定数值的,即为Ⅱ级管。
2.除Ⅰ、Ⅱ级管外,其余的是Ⅲ级管。
3.表中其他介质是指空气、水、滑油或液压油等。
4.1 管子切割前,必须核对管子材料、规格是否符合图纸要求。
4.2 管子切割前,应对管材内外表面质量进行检查。
4.2.1无缝钢管和合金钢管,其内外表面不得有裂缝、折叠、分层、结疮、轧折、发纹等缺陷存在。
如有上述缺陷应予清除,清除部位壁厚的减薄不得超过该材料标准允许的负偏差。
4.2.2 焊接钢管内外表面不允许存在由于焊接引起的裂缝、咬口、飞溅、凹陷等缺陷。
4.2.3 有色金属管子,其表面应光滑清洁,不应有针孔、裂缝、气泡、分层、锈蚀等缺陷。
4.3 碳素钢管、不锈钢管在订货时,应向制造厂提出退火处理要求。
4.4 法兰、套管、螺纹接头、异径接头、定型弯头等连接件,必须具有材质报告证件,方可使用。
4.4 管子的切割与开孔4.4.1 有色金属管、水煤气管和外径不超过32mm的钢管,应用机械方法切割和开孔;对外径超过32mm钢管允许使用气割开孔;合金钢管切割和开孔的方法应根据材料成分决定。
4.4.2 管子上开孔和切割后,切口必须修整光顺,氧气渣和毛剌必须全部清除干净。
4.4.3 管子切割后,管端面和管子外表面的垂直度公差Δ,应符合表2所规定的要求。
表 2 mm4.5 管子焊接坡口的切割4.5.1 以下状况可以允许焊接不开坡口钢管总管开孔、钢管壁厚δ≤6mm的支管、钢管壁厚δ≤5mm的管子对接焊处,以及钢管与其他附件搭焊处如图一图一4.5.2 钢管开坡口在没有开坡口设备的情况下,一般采用气焊切割或打磨成型。
当壁厚等于或大于6mm,并当主管直径大于或等于2.5倍支管直径时,在整个支管顶端开坡口;当主管直径小于2.5倍支管直径时,可在支管端面沿主管轴线方向左右部位,局部开坡口。
所有坡口型式及尺寸具体参照管子焊接通用工艺(YF-XXX-2004)。
五、管子弯曲加工5.1 管子弯制前,必须核对管子材料是否符合图纸要求。
5.2 弯管设备5.2.1 弯管机须经过设备管理部门检查验收,才能正式投入使用。
5.2.2 弯管模子、滑块或滑轮槽道和塞芯头部光洁和顺,切口处必须倒圆。
5.2.3 弯管模子和滑块的圆槽直径按表3。
5.2.4 有芯弯管机的芯棒头部外径和长度按表4。
5.2.5 弯管机的工夹、模具和附属设备应当定期检查和维修,以确保良好状态。
表3弯管模子和滑块的圆槽直径 mm表4 芯棒头部外径和长度 mm5.3 弯管技术要求5.3.1 管子的弯曲,一般采用冷弯的方法,在工厂缺少冷弯设备的情况下,允许采用热弯,但水煤气管不宜采用热弯,20号钢管不宜采用中频弯曲。
5.3.2 不锈钢管及合金钢管宜冷弯,如必须热弯时,不锈钢管加热应避免渗碳,而对淬硬倾向较大的合金钢管则不得浇水冷却。
紫铜管冷弯前应采取局部退火处理。
5.3.3 管子弯曲半径,一般不小于3倍管子通径,在管路布置比较紧凑的地方,在保证弯管质量前提下,允许小于3倍管子外径,较小弯曲半径的管子,应采用定型弯头。
5.3.4 弯管操作者,应熟悉弯管设备的结构、性能及其操作程序和规则。
5.3.5 对有芯弯管机,管子内径与塞芯工作部分,应涂适量的润滑油。
5.3.6对有芯弯管机,弯管时芯棒的端头圆柱截面位置应超过与其垂直的模具中心线,其超前值一般根据试验来决定,新安装和调试的弯管机可参照表5选取。
表 5注:表中D及d分别代表管子的外径和内径。
5.3.7 弯曲焊接钢管和水煤气管时,应尽量将焊缝安置在因弯曲而引起弯形的最小方位上,如图2所示。
在弯立体弯头时,亦应考虑焊缝的位置。
焊缝位置图25.3.8 弯制铜管、铝管时,必须小心地清除管子内外表面及机械设备与管子相接触部分所粘附的硬质杂物(如铁屑、砂土等)。
不允许在管子表面刻线,可]用铅笔或粉笔在管子表面划标记。
弯制时,应加少许润滑油以防止管材内外表面拉伤。
5.3.9 管子热弯时,加热应缓慢均匀和热透,且应防止过热,弯制每个弯头的加热次数应越少越好,这要取决于加热的渗透性和弯管操作的熟练程度,加热温度参照表6。
表6管子加热温度℃5.3.10 采用冷弯进行弯曲的铜和铜合金管,在弯曲后应进行退火处理,退火温度为500~700°C。
5.3.11 合金钢管和外径大于120mm碳素钢蒸气管,经弯曲后,应进行退火处理,碳素钢管加热至600~650°C,壁厚小于或等于25mm,保持时间至少1小时,然后在平静空气中缓慢冷却,合金钢管的热处理根据成分决定。
5.3.12 管子热弯后,应清除表面的氧化皮.5.3.13 采用塞砂弯管时,应选用河沙,但也允许用铁砂或石英砂。
河沙、石英砂的直径一般约为2~5mm,铁砂直径约为1mm。
砂子颗粒要干净、无杂质、无锐角,特别要无木质、煤屑和油类等有机物,要筛去细泥,选好的砂子经150~500℃烘干筛选,然后保存在专用的容器内,防止混入杂质或受潮。
填砂可用抖动或敲击的方法填实,一般每灌300~400mm即用锤在管外壁自下而上不断敲打,直到填满为止。
敲击时只允许用木锤,砂子填实后,用干燥木塞住管口。
六、管子装配及制作本工艺所提及的管子装配系指管子的搭焊6.1 钢管总管与支管装配6.1.1钢管支管型式一般如图3中a、b、c、d四种。
图 36.1.2 角尺支管和Y型支管应尽量少用。
6.1.3 支管宜设在总管法兰近端,以便清除焊渣和毛剌。
6.1.4 支管不允许插入总管中,马鞍口应与总管很好吻合,其焊接尺寸要求见管子焊接通用工艺(YF-XXX-2004)。
6.1.5 总管上支管孔应同轴,其不同轴度不得大于±1mm。
6.1.6 支管高度在确保法兰连接螺丝安装方便下尽量缩短。
6.2 铜管总管与支管的装配6.2.1 铜管支管型式一般如图4中A、B两种。
6.2.2 当总管内径大于支管内径时采用图4中A型,当总管内径等于支管内径时采用图4中B型。
6.2.3 A型支管插入端不得超过领口最底点。
6.2.4 B型支管与总管交接处应相贯。
6.2.5 铜管支管也可以采用三通接头。
6.2.6 总管上支管孔应同轴,其不同轴度不得大于±1mm。
6.3 与法兰的装配6.3.1 钢管法兰连接型式和适用范围按表7。
6.3.2 铜法兰连接型式和适用范围见表 8。
6.3.3 装配法兰时,法兰内孔与管子外表面之间的最大间隙在任何一点均不应超过2mm,径向相对两点的间隙总和不得超过3mm。
对于DN≥300mm 的管子,其间隙可适当放宽。
6.3.4 凡安装支管和弯头等配件的管子,宜将支管和弯头等配件焊完后,再装焊法兰,以防止焊接变形。
表7钢管法兰连接型式和适用范围表7钢管法兰连接型式和适用范围续(完)注:(1)“不限”系指在造船规范所允许各系统管路使用的最高压力或最高温度范围内。
(2)B型法兰应用于蒸汽系统当压力大于1.6Mpa或温度大于300°C时,管子外径不得大于150mm。
6.4 与螺纹接头装配6.4.1 符合于国家标准或部标准的螺纹接头,可用于各种管子的连接,但应根据管路介质压力去选用各种型式的螺纹接头;装配技术要求符合所用螺纹接头国家标准或部标准。
6.5 与卡套装配6.5.1 符合于国家标准或部标准的卡套接头,可用于各种管子的连接,但应根据管路介质压力去选用各种型式的卡套接头;装配技术要求符合所用卡套国家标准或部标准。
6.6 钢管的套管连接3.6.1 套管连接的结构形式和技术要求见表9。
表9套管连接的结构形式和技术要求6.6.2 套管连接不得用于有可能发生疲劳、严重腐蚀或裂缝腐蚀之处,套管材料应与管路材料相同,严重腐蚀处可采用双套管连接方式。
6.6.3 垂直位置的套管,如用于淡水、海水系统,应将下管端外套管内孔部位进行封底焊接,如是用于水平方向则可省略。
6.7钢管的对接装配6.7.1 管子对接有直接对焊、坡口对焊、衬圈对焊以及封底对焊等形式。
各型式的装配枝术要求见表10。
表10 钢管的对接装配枝术要求表10钢管的对接装配枝术要求续(完)6.7.2 异径管子的连接装配6.7.2.1 异径接头装配有三种形式如图5,其接头的技术要求参照表10。
a.同心型b.异心型c.锥形图 56.7.2.2 异径法兰连接:形式如图6所示。
应严格控制工作介质流向,只许由小口径流向大口径。
图 66.7.3 管子与定型弯头连接的技术要求参照表10。
6.8 铜管的对接装配铜管的对接有直接对接、扩管搭接、套管搭接等形式,其装配形式和适应范围见表11。
6.9 通舱管件6.9.1 当管子通过船舶各种水密、油密的隔舱、甲板,或船体加强梁结构时,应按表12各种型式通舱管件选用:表11 铜管的对接装配形式和适应范围表12 通舱管件型式表12 通舱管件型式续(完)6.9.2 通舱管件壁厚应大于或等于连接管子壁厚的1.25倍。
6.10 虾壳式焊接弯管(斜接焊弯管)装配型式船舶管路不能采用机械冷弯及定型弯头时,可采用虾壳式焊接弯管,这种弯管一般适用于船舶的主副机大口径排气管,锅炉烟道及其他低压力管路等,其材料可用船用钢板或无缝钢管,其结构型式如图7所示。