失效模式分析模板
注塑件过程失效模式及后果分析表模板(PFMEA)

6
包装破损
零件污染,客户投 诉
5
产品碰伤砸伤 客户投诉
6
装箱时确认不足 货物堆积过高
搬运不规范
2
无
3
试验后制定合理堆 积标准
2
无
100目测 100目测 100目测
5 60 5 75 4 48
标签贴错 发错货,客户投诉 5
标签与实物未核对 2
无
100目测
4 40
产品数量不正确
客户投诉
6
80-出货检验
关键尺寸超差
第 1 页,共 2 页
注塑件过程失效模式及后果分析表模板(PFMEA)
零件号
设计责任部门
FMEA 编号
零件名称
关键日期
编制人
车型/年份
系统/子系统/部件
编制日期
核心小组
序号
过程
潜在的失效模式
严 潜在的失效后果 重
度
级 别
潜在的失效原因/机理
频 度 数
现行预防性设计控 制
现行探测性设计控 制
探 测 度
5 60 5 75
建议措施
责任人和目标 完成日期
无
采取的措施
严频探 R 重度测 P 度数度 N
无
无
无
无
不同产品分区放置, 并做好标识
6
2 5 60
无
对纸箱进行固定 6 2 5 60
无
无
无
无
无
不同产品分区放置, 并做好标识
6
2 5 60
无
对纸箱进行固定 6 2 5 60
无
40-原材料烘料
烘料时间不对 烘料温度不对
表面料花 色差
失效分析报告模板

方
法
分 析 结 论
(检验规范) 改 (流程修改)
善
措 (设计更改)
施
(其他)
责任部门 责任部门 责任部门 责任部门
设 计 准 则
序号 仪 器 设 备
名称
型号
编号
测试工程师 签Βιβλιοθήκη 名年月日编制审核
批准 1
批准 2
年月 日
年月日
年月日
年月日
.
********失效分析
一 失效现象描述
宋体 小四 常规 单倍行距编写
二 样品背景资料描述 (附失效分析数据收集表即可)
三 分析过程
四 结论验证及结果
五 建议改善措施
精品文档
.
精品文档
**产品失效模式 分析报告
项目名称: 样品名称: 型号规格: 分析项目组: 编写日期:
报告编号 总页数
.
**产品失效模式分析报告
精品文档
项目名称
样品规格型号
样品提供部门
取样数目 (详细样品取样)
测试环境 温度:
湿度 :
产品名称 样品提交时间
供应商
气压:
分 析
宋体 五号 常规 单倍行距,此表格必须在一页上。
P-FMEA 过程潜在失效模式分析模板
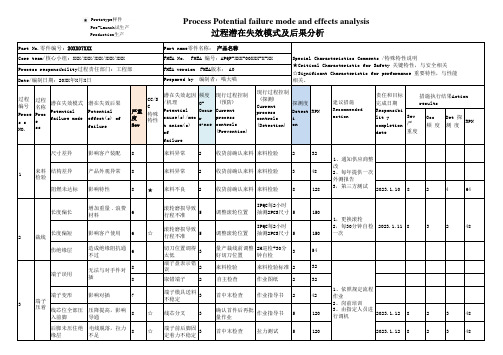
Pre-Launch 试生产 Production 生产Process Potential failure mode and effects analysisPart No.零件编号:Part name 零件名称:Special Characteristics Comments /特殊特性说明★Critical Characteristic for Safety 关键特性,与安全相关 ☆Significant Characteristic for performance 重要特性,与性能相关。
Core team/核心小组: XXX/XXX/XXX/XXX/XXX FMEA No. FMEA 编号:APQP-XXX-00XXX-X-XX Process responsibility 过程责任部门: 工程部 FMEA version FMEA 版本: A0 Date/编制日期:20XX 年X 月X 日Prepared by 编制者:喵大喵过程 编号 Proce s s NO.过程 名称 Proc e ss潜在失效模式 Potential failure mode潜在失效后果 Potential effect(s) of failureSevCC/S C 特殊 特性 潜在失效起因 /机理Potential cause(s)/mec h anism(s) offailure频度 O- Occur r e -nce 现行过程控制(预防) Current process controls (Prevention) 现行过程控制 (探测) Currentprocess controls (Detection)探测度 Detect i on RPN建议措施Recommended action责任和目标 完成日期 Responsibi lit ycompletion date措施执行结果Action results Sev 严重度 Occ 频 度 Det 探测 度RPN1来料 检验尺寸差异 影响客户装配 8 来料异常 2 收货前确认来料 来料检验 2 32 1、通知供应商整 改 2、每年提供一次 外测报告 3,第三方测试结构差异 产品外观异常 8来料异常 2 收货前确认来料 来料检验 3 48阻燃未达标影响特性8★来料不良2收货前确认来料 来料检验81282023.1.10 82 4 642裁线长度偏长增加重量﹐浪费材料6滚轮磨损导致行程不准5调整滚轮位置 IPQC 每2小时 抽测2PCS 尺寸 51501,更换滚轮2,每30分钟自检 一次2023.1.1183248长度偏短影响客户使用6☆滚轮磨损导致行程不准5调整滚轮位置IPQC 每2小时 抽测2PCS 尺寸 5150 伤绝缘层造成绝缘阻抗通不过6切刀位置调得太低3量产裁线前调整 好切刀位置 2H 巡检+30分钟自检 3543端子 压着端子误用无法与对手件对 插 8端子盘表示错误2 来料检验 来料检验标准 2 321、依照规定流程 作业2、岗前培训3、由指定人员进行调机8 取错端子 2自主检查 作业图纸 2 32端子变形影响对插7端子模具送料不稳定 3首中末检查作业指导书2 42线芯位全部压 入前脚 压降提高,影响导通 8☆ 线芯分叉3确认首件后再批量作业 作业指导书5 120 2023.1.12 82 3 48 后脚未压住绝 缘层 电线脱落,拉力不足8☆端子前后脚固定着力不稳定3首中末检查拉力测试51202023.1.12 82348Prototype 样件编制:审核:文件编号:XX-XX-XXX 版本:A0。
PFMEA模板

过程或产品名称:准备
者:
Page ____ of
____
职责:FMEA 日期(原始) ______________ (更改) _____________
流程输入潜在失效模式潜在失败影响S
E
V
潜在原因根源
O
C
C
D
E
T
R
P
N
推荐的行动Resp.
S
E
V
O
C
C
D
E
T
R
P
N
项目所涉及的流程项目的输入是什
么?在什么情况下这个
特征将失去其功
能?
对于客户的影响是什么(内部
的或外部的)?
对
于
客
户
的
影
响
有
多
严
重
?什么原因会失去功能?
原
因
或
失
败
模
式
发
生
的
频
率
是
多
少
?自主查侦系统查侦防呆
你
如
何
很
好
地
探
测
原
因
或
实
效
模
式
?减少发生要因,或改善探测需要
采取什么行动? 应该只针对具有
高RPN的部分采取行动,否则就
简单处理。
谁负责推荐的
行动?
自主查侦系统查侦防呆
00
00
00
00
00
00
00
00
00
00
00
00
00
当前控制方式采取的行动
过程失效模式分析
(FMEA)。
FMEA失效模式分析模板
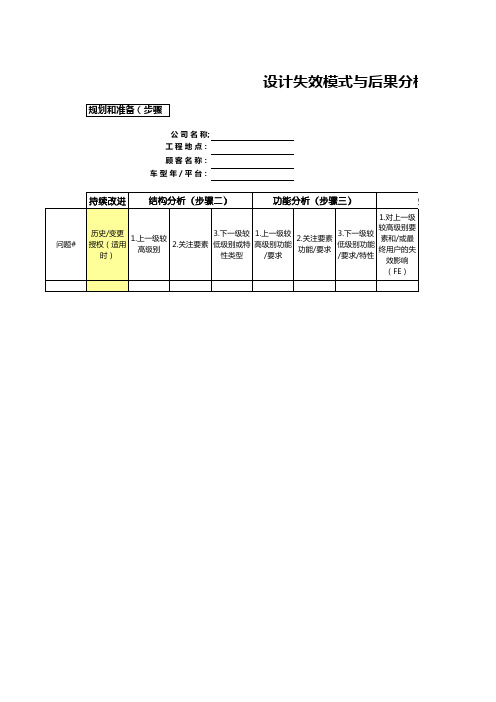
规划和准备(步骤
公 司 名 称; 工 程 地 点: 顾 客 名 称: 车 型 年 / 平 台:
问题#
持续改进 结构分析(步骤二)
功能分析(步骤三)
失效分析(步骤四)
1.对上一级
历史/变更 授权(适用
时)
1.上一级较 高级别
2.关注要素
3.下一级较 1.上一级较
低级别或特 高级别功能
3、下一级 较低要素或 特性的失效
原因 (FC)
当前对失效 原因(FC)的 预防措施
(PC)
失效原因 (FC)的 发生频度
(O)
当前失效原 因(FC)或失
效模式 (FM)的 探测措施
(DC)
失效原因
(FC)/失效
模式 (FM)的
DFMEA AP 筛选器代码
探测度
(D)
DFMEA编 号: 设 计 责 任: 保 密 级 别:
严重度(S) 频度(O)
优化(步骤6)
完
DFMEA 预防措施
DFMEA 探测措施
ቤተ መጻሕፍቲ ባይዱ
负责人姓名
目标完成日 期
状态
采取基于证 据的措施
成 日
期
探测度(D) DFMEA AP
筛选器代码 备注
性类型
/要求
2.关注要素 功能/要求
3.下一级较 低级别功能 /要求/特性
较高级别要 素和/或最 终用户的失
效影响
(FE)
后果分析(设计FMEA)
项 目: DFMEA开始日期: DFMEA修订日期:
跨 功 能 团 队:
失效分析(步骤四)
DFMEA风险分析(步骤五)
失效影响的 严重度 (S)
潜在过程失效模式及后果分析PFEMA(模板)

2
供应商管理
3
42
剪板2
少料
影响产品使用
6
2
开料前调整定 位或更换定位 定期调整、维护 装置 编制检验作业 检验员按检验作 指导书 业指导书检验 落料前检查定 位或更换定位 定期检查、维护 装置 编制检验作业 检验员按检验作 指导书 业指导书检验 针对失效原因 首、巡、未检验 采取措施 编制检验作业 检验员按检验作 指导书 业指导书检验 加强包装人员及 搬运人员管理与 培训 操作工每箱清点 数量,确定符合 包装要求后封 箱;
潜在过程失效模式及后果分析 (过程 FMEA)
项目名称: 车型年度/车辆类型: 过程责任部门: 生产部 关键日期: 核心小组: 编制者: FMEA日期
FMEA 编号: 页码: (编制) (修订) 措施执行结果
过程 功能 潜在 失效模式 潜在 失效后果 严重度 (S) 分类 潜在失效 起因/机理 频度(O) 现行预防 过程控制 现行探测 过程控制 探测度 (D) 风险顺 序数 R.P.N 建议 措施 责任和 目标完 成日期 采取的 措施 探 严 频 测 重 度 度 度 (O) (D) (S)
3
36
检验3
料宽偏大或偏 材料浪费或产品 小 缺料报废 少料 影响产品使用
6
2
3
36
落料4
6
2错检 成形尺寸不正 确 漏检、错检
影响后道工序
7
1
8
56
成型6 检验7 入成品库8
影响产品使用 影响装车,用户 不满意
6 7 4
3 1 2
2 8 5
36 56 40
入库时产品堆 产品包装箱挤压 码高度过高 变形
要求 根据领料单的规 格领料、领料人 与保管员共同确 认
失效件分析报告模板

失效件分析报告模板1. 引言本报告旨在对失效件进行分析,并找出导致失效的主要原因和可能的解决方案。
失效件分析对于提高产品质量和性能,减少故障率具有重要意义。
本报告将对失效件的失效模式、失效原因进行分析,并提出可行的改进措施。
2. 失效件信息在本节中,首先列出失效件的详细信息,包括但不限于以下内容:- 失效件名称:[失效件名称]- 失效件型号:[失效件型号]- 失效件数量:[失效件数量]- 使用环境:[使用环境描述,例如温度、湿度、工作条件等]3. 失效模式分析在本节中,对失效件的失效模式进行分析和描述。
失效模式是指失效件在使用过程中出现的主要故障形式,常见的失效模式包括但不限于以下几种:1. 破裂失效2. 磨损失效3. 腐蚀失效4. 疲劳失效5. 温度过高失效6. 电压过高失效7. 电压过低失效根据实际情况,结合失效件的特点和使用环境,对失效件的失效模式进行综合分析和描述,以便更好地了解失效件出现故障的原因。
4. 失效原因分析在本节中,对失效件的失效原因进行深入分析。
失效原因是指导致失效件出现故障的主要原因,可能包括但不限于以下几种:1. 材料问题:材料质量不合格、材料选用不当等。
2. 制造工艺问题:制造过程中存在的问题,如焊接不良、装配不当等。
3. 设计问题:设计不合理、设计强度不足等。
4. 使用条件问题:使用环境过于恶劣、超负荷使用等。
对于每一种失效原因,展开详细的分析,包括失效原因的根本原因、对失效的影响程度以及可能导致失效的具体机制。
并且,根据分析结果提出相应的改进方案。
5. 改进措施基于对失效件失效原因的分析,本节将提出相应的改进措施,以解决失效件出现故障的问题。
改进措施应当具体、可行,并与失效件分析的结果相匹配。
根据不同的失效原因,改进措施可能包括但不限于以下几种:1. 优化材料选择:选择合适的材料,提高失效件的耐磨性、耐腐蚀性等性能。
2. 改进制造工艺:完善焊接工艺、装配工艺等,提高失效件的制造质量。
潜在过程失效模式及后果分析PFEMA(模板)教学文案

风险顺 探测度 序数
(D) R.P.N
建议 措施
责任和 目标完 成日期
进料1
材质不对 力学性能不符
7
剪板2
少料
影响产品使用
6
检验3
料宽偏大或偏 材料浪费或产品
小
缺料报废
6
落料4
少料
影响产品使用
6
检验5 漏检、错检 影响后道工序
7
成型6
成形尺寸不正 确
影响产品使用
6
检验7 漏检、错检
影响装车,用户 不满意
项目名称: 车型年度/车辆类型:
过程责任部门: 生产部 关键日期:
潜在过程失效模式及后果分析 (过程 FMEA)
编制者:
核心小组:
FMEA 编号: 页码:
FMEA日期 (编制) (修订)
过程 功能
要求
潜在 失效模式
潜在 失效后果
严重度 (S)
分类
潜在失效 起因/机理
频度(O)
现行预防 过程控制
现行探测 过程控制
.N
7
入成品库8
入库时产品堆 码高度过高
产品包装箱挤压 变形
4
包装9 包装数量不符 顾客抱怨
5
供应商代表签字:
根据领料单的规
☆
没有按领料单上规 格领料
2
供应商管理
格领料、领料人 与保管员共同确
3
42
认
剪板机定位装置磨 损或未调准
2
开料前调整定 位或更换定位 定期调整、维护
装置
3
36
检验员技能较差、 责任心不强
1
编制检验作业 检验员按检验作
指导书
业指导书检验
设计失效模式及后果分析表模板(DFMEA)
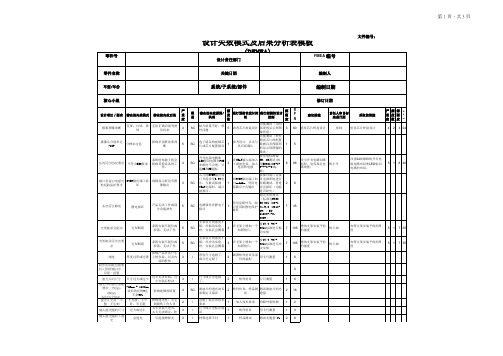
上支架的安装孔的 尺寸和厚度尺寸
尺寸不达标
无法与其他部件安 装;影响系统的厚
5
上支架的表面光滑 吗,无毛刺,无尖
不光滑,有毛 刺,有尖角
影响美观,以及安 装,使用的安全
6
角
下支架的安装孔的 尺寸和厚度尺寸
尺寸不达标
无法与其他部件安 装;影响系统的厚
5
下支架表面光滑, 不光滑,有毛 无毛刺,无尖角 刺,有尖角
61000-4-2:
2009)
SC
支架设计的强度不 够,在振动实验 时,安装孔会撕裂 。
3
在支架上增加一个 加固垫片。
按JT/T 7942011标准进行振 动实验
7
SC
支架设计的强度不 够,在冲击实验 时,安装孔会撕裂 。
3
在支架上增加一个 加固垫片。
按JT/T 7942011标准进行冲 击实验
7
60 优化芯片焊盘设计
制
控制
测 度
R P N
建议措施
责任人和目标 完成日期
采取的措施
严频探 R 重度测 P 度数度 N
SC
贴片质量不好,软 件问题
5
功能测试(用肉 改善芯片封装设计 眼观察显示屏图
像质量)
3
功能测试(软件
SC
选了错误的视频芯 片或芯片配置错误
1
参考设计,以及与 供应商确认
测试芯片的配置 数据以及肉眼判 断显示屏图像的
张钊
5
改小开关电路回路 96 面积。电容靠近电 胡小军
路放置。
6
35
105
增加支架安装平面 的强度
杨玉福
105
增加支架安装平面 的强度
DFMEA设计潜在失效模式及后果分析表模板

8
Designer wrong input dimension data 设计人员标错尺寸
1. According design SOP (XJ-SJ-SOP-001)
3
2. Design leader re-check design 依照设计SOP参考,双人确认图档无误后,主管
Check Key dimension in CAD file
1. According design SOP (XJ-SJ-SOP-001)
0
2. Design leader re-check design
Remove shrinkage ratio to recheck
依照设计SOP参考,双人确认图档无误后,主管 3D dimension
1
确认
0
Team leader approve 设计开发部负责人审核确认
CNC加工
Electrode discharge allowance does Tooling dim. issue and product dim.
not match
failure
电机放电余量不符
影响模具尺寸,产品超尺寸公差
7
1. Gate desige/loacation issue 浇口方式不合理
Tooling Design 模具设计
Shrinkage issue 产品缩水率错误
Scrap mold core 模仁报废
Wrong dimension issue 尺寸标准错误
1.Fail to production 2.Fail to meet tooling schedule 3.Add tooling cost 模具不能量产/交期滞后/增加成本
产品潜在失效模式及后果分析(PFEMA)--报告模板

5
90
第 5 页,共 228 页
潜在失效模式及后果分析
GLP1007 ◎首次提交 ○OTS提交更新 ○PPAP提交更新 ○生产更新
版本号:5
○DFMEA ◎PFMEA
供应商代码/名称 100036
编号:
零件号码:01727609
零件名称:GPS主机-MP5
核心小组:PE-毛积钧、唐庆姚、廖正江 、黄业旺 SQE - 吴冲 ,ME - 郭业亮 ,新进-梁 小华,叶振超 PM -温闻,田梦棠
潜在失效模式及后果分析
GLP1007 ◎首次提交 ○OTS提交更新 ○PPAP提交更新 ○生产更新
版本号:5
○DFMEA ◎PFMEA
供应商代码/名称 100036
编号:
零件号码:01727609
零件名称:GPS主机-MP5
核心小组:PE-毛积钧、唐庆姚、廖正江 、黄业旺 SQE - 吴冲 ,ME - 郭业亮 ,新进-梁 小华,叶振超 PM -温闻,田梦棠
编制人:毛积钧
编制日期:2014-04-15
设计项目或过程功 能要求
潜在失效模式
失效的潜在后果
S
特性分 类
失效的潜在起因
○
现有设计或过程控制
D RPN
二维条形码贴装
条形码纸翘起或是中间 凸起
外观不良
3
条形码纸贴装完后没 有用手抹平贴纸
3
条形码纸贴装完用手指将胶 纸抹平贴紧.
8
72
Z刮浆
拉尖、锡孔、短路、少 丝印不良,回流焊接后产生
设计项目或过程功 能要求
潜在失效模式
失效的潜在后果
S
特性分 类
失效的潜在起因
○
现有设计或过程控制
潜在失效模式分析(PFMEA)样板-1
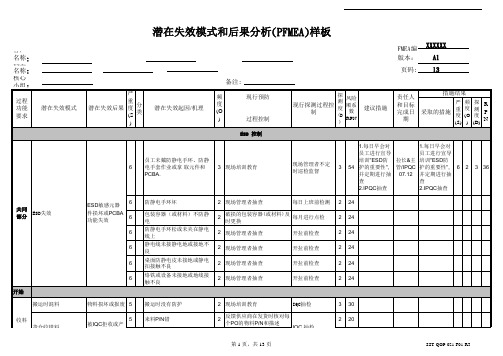
1.不同的Model 之间有相似 的的钢网设计 2.钢网上的P/N标示错误或没 标示 1.印刷速度或刮刀压力设置 不当 2.钢网孔堵塞或漏开孔 3.刮刀两边红胶收拢不及时 4.PCB板表面清洁度不够 5.红胶开封时间太长或过期 1.印刷速度或刮刀压力设置 不当 2.红胶开封时间太长或过期 3.印刷偏移位 1.钢网孔偏位 2.程序设定偏位
1.定期培训员 工"电子元件 基础知识"并 实践考核 2.每站物料上 6 线时依BOM 描述需要测量 其阻容值并记 PIE 录 /操作员 3.开线换线后 Dec-07 由技术员确认 所有方向性器 件的"方向标 示"并贴装首 6 件确认 4.换料时由两 人互检确认 5.IPQC 抽验
2
3 36
2
3 36
2
3 36
共同 ESD失效 部分
ESD敏感元器 件损坏或PCBA 功能失效
6 6 6 6 6 6
防静电手环坏 包装容器(或材料)不防静 电 防静电手环松或未夹在静电 线上 静电线未接静电地或接地不 良 桌面防静电皮未接地或静电 扣接触不良 烙铁或设备未接地或地线接 触不良
2 现场管理者抽查 2
每日上班前检测
潜在失效模式和后果分析(PFMEA)样板 样板 潜在失效模式和后果分析
FMEA编号: XXXXXX 客户名称: 机型名称: 核心小组:
严 重 分 潜在失效后果 度 类 (S ) 频 度 (O )
XXXXXX XXXXXX
过程责任部门:SMT&MI&TEST
编制者:
版本: 页码:
A1 13
备注:
现行预防
2 2 2 2 2 2
破损的包装容器(或材料)及 每月进行点检 时更换 开拉前检查
新版第五版 设计失效模式及后果分析模板

FM(失效模式)
FC(失效原因)
LCD显示对比度不足 玻璃面电阻过高 LCD显示对比度不足 PI层厚度过高 LCD显示对比度不足 液晶阈值电压 LCD显示对比度不足 偏光片角度设计不对
FE(失效影响) FM(失效模式) FC(失效原因) ← FE(失效影响) FM(失效模式) FC(失效原因)
0 0
FE(失效影响)
0 0 0 0
← FM(失效模式) FC(失效原因)
0 0 0 0
DFMEA中的“失效原因”一般为“选材不 当”“公差错误”“计算错误”…… 而不应该是“来料不良”“加工不良”“操作失
←玻璃 ←PI ←液晶 ←偏光片
← ← ← ←
失效分析瀑布表
FE(失效影响) FM(失效模式) FC(失效原因)
娱乐系统无法工作 显示模组失效 显示模组失效 画面显示不清晰 ←多媒体娱乐系统
FE(失效影响) FM(失效模式)
画面显示不清晰
FC(失效原因)LCD显示对比度不足源自←液晶显示模组FE(失效影响)
画面显示不清晰 画面显示不清晰 画面显示不清晰 画面显示不清晰
过程失效模式及后果分析模板(PFMEA)

潜在失效模式
严
潜在失效后果
重 度
级 别
S
潜在失效原因机理
频 度 O
现行控制
探 测 度 D
R P N
建议采取的措施
责任人 完成日期
措施结果 验证 S O D RPN
长度超出上限 下限 报废
4
员工计算失误
4
员工计算失误
6 首件检验 2 首件检验
板材开裂
2
折弯
外型扭曲
报废 报废
4
周转/搬运碰到
XXX 2019/3/2 XXX 2019/3/2 XXX 2019/3/2 XXX 2019/3/2 XXX 2019/3/6 XXX 2019/3/6 XXX 2019/3/6 XXX 2019/3/6 XXX 2019/3/6 XXX 2019/3/7 XXX 2019/3/7 XXX 2019/3/9 XXX 2019/3/9 XXX 2019/3/9
4
周转/搬运碰到
4 巡检 1次/2hr 2 巡检 1次/2hr
孔径规格不符 影响装配
8
钻孔设备精度不够 2 巡检 1次/2hr
3
钻孔 尺寸超差
影响装配
7
钻头定位不准
2 首件检验
位置不对中心 影响装配
7
钻头定位不准
2 首件检验
焊渣飞溅
影响外观
设备调试不良
3 巡检 1次/2hr
3
毛刺未及时磨掉
4 巡检 1次/2hr
过程失效模式及后果分析(PFMEA)
Process Failure Modes and Effects Analysis
产品名称: XXXXXXXXXXXXXXX 小组成员: XXX(开发)、XXX(生产)、XX(品质)、XXX(技术)…
D-FMEA 模板

1 9 焊接参数
1 12
2 16
2 56
4 56
2 48
8 48 做破坏性试验
page 1 of 1
公司名 称: 编制部门/ 人员: 编制日 期:
责任目标/
措施结果
完成日期 采取的措施 S O D RPN
2011/3/30 制作模具
2011/3/30 制作工装 2011/4/5 技术验证
2011/4/5 试验
2
2
折弯 板材裂开
报废
4
304材料内应力大 4
外型扭曲
报废
4
折弯时与刀具不垂 直
2
3
做孔 孔径不符
影响装配
8
工艺孔错或精度不 够
2
尺寸超差
影响装配
7
定位不准确
2
位置不对中 影响装配
7
定位不准确
2
4
焊接 焊渣飞溅
影响外观
3
设备调试不良
3
毛刺未及时打磨
4
焊缝尺寸高 影响外观
4
作业不良
2
位置不对中 影响装配
7
定位不准确
4
外型扭曲
影响装配
7
定位不准确
2
焊缝错(漏) 影响产品寿命 6
作业不良
4
焊接不牢固 影响产品寿命 6
虚焊
1
现行控制
预防 √ √
ቤተ መጻሕፍቲ ባይዱ√ √
√
探测 √ √
√ √ √ √ √ √
√ √ √
探
测 度
RAN
D
建议的措施
4 96 设计制做圆头模具
18
1 16
2 16
D-FMEA 模板

2
2
折弯 板材裂开 报废
4
304材料内应力大 4
外型扭曲 报废
4
折弯时与刀具不垂 直
2
3
做孔 孔径不符 影响装配
8
工艺孔错或精度不 够
2
尺寸超差 影响装配
7
定位不准确
2
位置不对中 影响装配
7
定位不3
设备调试不良
3
毛刺未及时打磨
4
焊缝尺寸高 影响外观
4
作业不良
2
位置不对中 影响装配
7
定位不准确
4
外型扭曲 影响装配
7
定位不准确
2
焊缝错(漏) 影响产品寿命 6
作业不良
4
焊接不牢固 影响产品寿命 6
虚焊
1
现行控制
预防 √ √
√ √
√
探测 √ √
√ √ √ √ √ √
√ √ √
探 测 度 RAN
D
建议的措施
4 96 设计制做圆头模具
18
1 16
2 16
4 64 设计制做定位工装
4 56
2 28
1 9 焊接参数
1 12
2 16
2 56
4 56
2 48
8 48 做破坏性试验
page 1 of 1
公司名 称: 编制部门/ 人员: 编制日 期:
责任目标/
措施结果
完成日期 采取的措施 S O D RPN
2011/3/30 制作模具
2011/3/30 制作工装 2011/4/5 技术验证
2011/4/5 试验
失效模式及后果分析
Failure Mode and Effects Analysis (DFAME)